Study of Aluminum Influence on the Adhesion of Stainless Steel in Flame Spraying
- 1 — Ph.D. docent Peter the Great Saint Petersburg Polytechnic University
- 2 — assistent Peter the Great Saint Petersburg Polytechnic University
- 3 — assistent Peter the Great Saint Petersburg Polytechnic University
Abstract
This paper is dedicated to a study of aluminum influence on the improvement of surface adhesion strength. The main purpose of this work is to investigate the strength of adhesion to the substrate by mixing flame spray powder with aluminum, which not only possesses high corrosion resistance and conductivity, but also provides additional strength, as it combines and reacts with other components of the powder. Research results of sandblasting dependence on surface roughness parameter Ra are demonstrated. The paper describes authors’ original device for a measuring instrument “Profilometer”, which was also used for measuring roughness parameter in order to obtain comparative results. Authors present results of adhesion measurements given obtained values of surface roughness by mixing nominal chemical composition of PR-30X13 powder, used as a testing material, with aluminum, which reacts with oxides on the surface of steel substrates, imparts strength to the bonding between the coating and the substrate, protects the base metal due to a combination of chemical components of the powder and creates a layer of dense surface coating. These dependencies are analyzed and parameters, exerting the greatest influence on their values, are identified. Taking into account the results obtained through numerical modeling, authors propose a mathematical model of a dependency between adhesion strength and certain values of surface roughness for different chemical compositions of flame spray powder. These studies will help in the development of certain material types for spraying and hardening of steel parts and products in order to improve their durability.
Introduction. The stage of preproduction engineering is a rather labor intensive process. High labor intensity of this process stage is largely observed in individual and small-scale production, distinctive features of which include a wide variety of workpieces with low production volume, absence of specialized workplaces, high labor intensity and a long cycle of products manufacturing [7].
Therefore, taking into account fast development rates of mechanical engineering industry, a growing number of requirements is imposed on contact surfaces, which maximally actualizes the main tasks of mechanical engineering, i.e. increasing wear-resistance of workpieces. One of the ways to solve this problem is to apply thermal spray coating, each type of which possesses universal properties and exerts an individual effect on the metal.
Literature review demonstrated that the most important property, which defined the possibility of using thermal spraying, was the strength of adhesion to the substrate [1, 3, 5, 6, 8, 10, 11, 14, 15].
However, in a number of cases the required strength of adhesion between wear-resistant sprayed coating and acting surface of the workpiece can be obtained by means of a justified selection of abrasive blast machining modes [5].
In order to improve the quality of sprayed coatings after using abrasive blast cleaning and to manage their properties in the process of spraying and subsequent machining, there are several methods of combining coating both with other technologies, and with other compositions of spray powder.
One of these combining methods is described in the current paper: the use of aluminum (Al), a chemical component, which is not a part of the nominal composition of the studied PR-30X13 stainless steel powder, in the spraying process. Aluminum does not introduce any significant changes to the process flow, maintains microhardness, homogenous chemical and phase composition, structural stability, allows to investigate adhesive strength and helps to improve coating properties, increasing wear-resistance and reliability of products under combined exposure to high temperatures and aggressive media.
Setting of research goals and objectives. The goal of this paper is to develop a method to increase adhesion in the process of sand blasting, using several types of spray powder chemical compositions.
In the context of reaching this goal, the following objectives need to be addressed:
• measurement of surface roughness parameter on the selected sample surfaces after removing various traces of contamination and rust by means of sand blasting;
• activation of workpiece surface by flame spraying of each sample using several chemical compositions of spray powder, measurement of adhesion;
• construction of a direct dependency between adhesion strength of the coating and spray powder composition by means of numerical modeling and derivation of a rational linear function.
Research methodology. Research was performed on two workpieces made of 30X13 steel, which is used to manufacture cutting and measuring tools, springs, carburetor needles, piston compressor rods, internal parts of devices and other parts, working to the point of exhaustion in mildly aggressive media up to 450 °С.
The samples possessed identical characteristics: length 500 mm, diameter 30 mm (Fig.1). General layout of testing samples made of 30X13 steel is presented in Fig.1.
In order to obtain the most complete and reliable results, each testing sample was divided into four parts – for doing this, an Optimum TH 4210 DPA V lathe circumferentially marked their surfaces with four 1.5 mm-deep stripes; the marked surfaces underwent measurements of surface roughness parameters and, after restoring the workpieces by means of flame spraying, measurements of adhesion strength between the base material and the surface.
In the spraying process, workpieces had to be clean from visually detectable traces of rust and contamination, cavities and fractures. Therefore, before spraying, testing samples were subject to sand blasting (surface preparation grade Sa 2,5) in order to give the metal a textured surface, as grinding and polishing are not always capable of removing scale, rust, etc. [2, 9]. This method of surface cleaning, based on the principles of abrasive effect, not only produces required roughness and ribbing, significantly prolonging operating life of the coating, but also abrades the surface and upsets its thermodynamic equilibrium with the environment, releasing interatomic bonds of surface atoms, i.e. performs chemical activation of the substrate [12, 13].
As after cleaning, the preparation grade is defined by optimal spraying parameters of the surface texture, the study of material adhesion requires taking into account the indicators of surface roughness [13]. After cleaning the workpiece, roughness parameters of the obtained surface were studied in accordance with GOST R ISO 4287-2014 (Russian National Standard, identical to ISO 4287). Surfaces of both samples were measured with a Profilometer TR100.
The study of surface roughness parameter describes a patented device for a measuring instrument. Measurements were performed in two ways: with and without the device [4]. Resulting average values of surface roughness parameter Ra were obtained after five measurements on each of the four examined surfaces of each sample. Data on the average Ra values are presented in Table 1.
Table 1
Results of measuring surface roughness parameter
Surface geometry | Testing surface | Average values of surface roughness parameter Ra, μm | |
Without the device for a measuring instrument | With the device for a measuring instrument | ||
Sample N 1 after sand blasting | 1 | 3,2 | 2,7 |
2 | 3,8 | 3,2 | |
3 | 4,0 | 3,4 | |
4 | 3,5 | 3,2 | |
Sample N 2 after sand blasting | 1 | 3,8 | 3,2 |
2 | 3,8 | 3,2 | |
3 | 4,2 | 3,5 | |
4 | 3,6 | 3,0 |
Device description. A device for a measuring instrument “Profilometer” is designed for maximum fixation of the workpiece in the housing and a measuring instrument in the opening, which significantly reduces both human error and observational error due to external factors. It consists of the housing 3, made of two parts connected with a bolt joint 2, provided that overall housing dimensions can vary depending on the length and diameter of measured workpieces (Fig. 2). Upper part of the housing has an opening 4 for holding a measuring instrument, its size can also be adjusted to fit the tool. Upper part of the housing contains vertical feed screws 5, which serve to adjust vertical approach of the workpiece to the measuring instrument. In the lower part of the housing there are horizontal feed screws 7, attached to the sliding bars 6 and ending with prismatic jaws 1 for clamping workpieces.
The principle of measuring roughness parameter with the described device is in clamping the testing samples in the prismatic jaws and in adjusting vertical feeds screws so that the samples approach the measuring instrument, which is also clamped in the fixation opening. By adjusting these screws, the values were measured for all surfaces of both samples.
Then, in the course of three hours (GOST R ISO 8501-1-2014) after cold abrasive machining and surface roughness control, in order to study adhesion at given roughness values, the testing samples were subject to flame spraying using powders of different chemical composition, with preliminary degreasing and heating of the surface to 100 °C. After that, as required by the study procedure, surface adhesion strength was measured for each surface of samples N 1 and N 2 with an adhesion tester PosiTest AT-A in accordance with the type of powder used for flame spraying, followed by derivation of mathematical dependencies between surface adhesion strength and the composition of spray powder, using numerical modeling in order to find the rational linear function.
Planning of the experiment and the results. At the initial stage of research, sand blasting of the testing samples was performed with an ejector-type sandblasting machine Aeroblasting A-90E, intended for processing metal and concrete surfaces with dry sand of any type up to 3.5 mm in size. The cleaning was carried out using a 6-mm nozzle with an average flow of approximately 30 m3 h. Operating pressure equaled 3.5 kg/cm2, air flow rate was 1.2 m3/min, abrasive material consumption was 122 kg/h, rounded silica sand 0.4-0.8 mm in size was also used in the process.
Magnified fragments of testing sample surfaces after sand blasting are presented in Fig.3.
The surface quality after sand blasting was measured with Profilometer TR100, which had the following characteristics: measured roughness parameters Ra, Rz, scanning length 6 mm, permissible intrinsic error ± 15 %, a diamond stylus with a radius 5 ± 1 μm, stylus tip angle 900 (+ 50 или –100).
Results of measuring surface roughness parameter demonstrated a decrease in Ra parameter of the sample N 2, the values of which were obtained using the device for a measuring instrument. The difference between measurements was approximately 16 %. Based on the obtained values, for further research, this study will present the results of measuring the roughness using the device for a measuring instrument.
Measurement results of surface roughness parameter, obtained using two described methods, are presented in Table 1.
According to the statement of research problem, afterwards the testing samples were subject to flame spraying. In case of the testing sample N 1, the spraying was done with a self-fluxing stainless steel powder PR-30X13, obtained by spraying molten metal by gas (spherical shape particles) and characterized by reduced coating porosity.
Then the utilized powder with the chemical composition of Fe 87 %, Cr 13 % was modified for coating sample N 2: 5 % of aluminum was added as a metallic component of the mixture, and iron content was reduced by 5 %.
Flame spraying was performed at a spraying distance of 200 mm with a gas torch «Avtogen GN-2 BRIMA», intended for weld deposition of worn-out surfaces of machine parts and mechanisms using a mixture of active gases – oxygen and acetylene.
The main operation modes and characteristics in the process of flame spraying were the following: air pressure – 0.5 MPa, oxygen pressure – 0.7 MPa, oxygen flow rate – 58 l/min, acetylene pressure – 0.4 MPa, acetylene flow rate – 30 l/min, powder grain size – 50 μm, thickness of the initial sublayer (on one side) – 0.2 mm, thickness of the basic layer – 0.5 mm.
Afterwards, measurements were made using a digital adhesion tester PosiTest AT-A with a loading range 0.3-70 MPa, accuracy of pull-off pressure measurement ±1 % of the full scale, by using pull-off method and a 14 mm dolly (maximum adhesion strength for this dolly equaled 40 MPa), there were measured and derived the results of the dependency of the parameters of adhesion strength with the base material (Table 2) with the resulting surface roughness.
Results of numerical modeling. After comparing adhesion strength and roughness parameter values of each testing sample, the conclusions were drawn on the presence of a direct dependency and an increase in adhesion not only with an increase of roughness parameter, but also with the addition of aluminum to the powder for flame spraying.
Table 2
Study results of the dependency between adhesion strength and surface roughness parameters
Surface geometry | Testing surface | Average values of surface roughness parameter Ra using the device for a measuring instrument, μm | Value of adhesion strength σ, MPa |
Sample N 1 using flame spray powder without aluminum | 1 | 2,7 | 24,47 |
2 | 3,2 | 25,5 | |
3 | 3,4 | 25,82 | |
4 | 3,2 | 25,48 | |
Sample N 2 using flame spray powder with added aluminum | 1 | 3,2 | 27,38 |
2 | 3,2 | 27,34 | |
3 | 3,5 | 28,17 | |
4 | 3,0 | 26,79 |
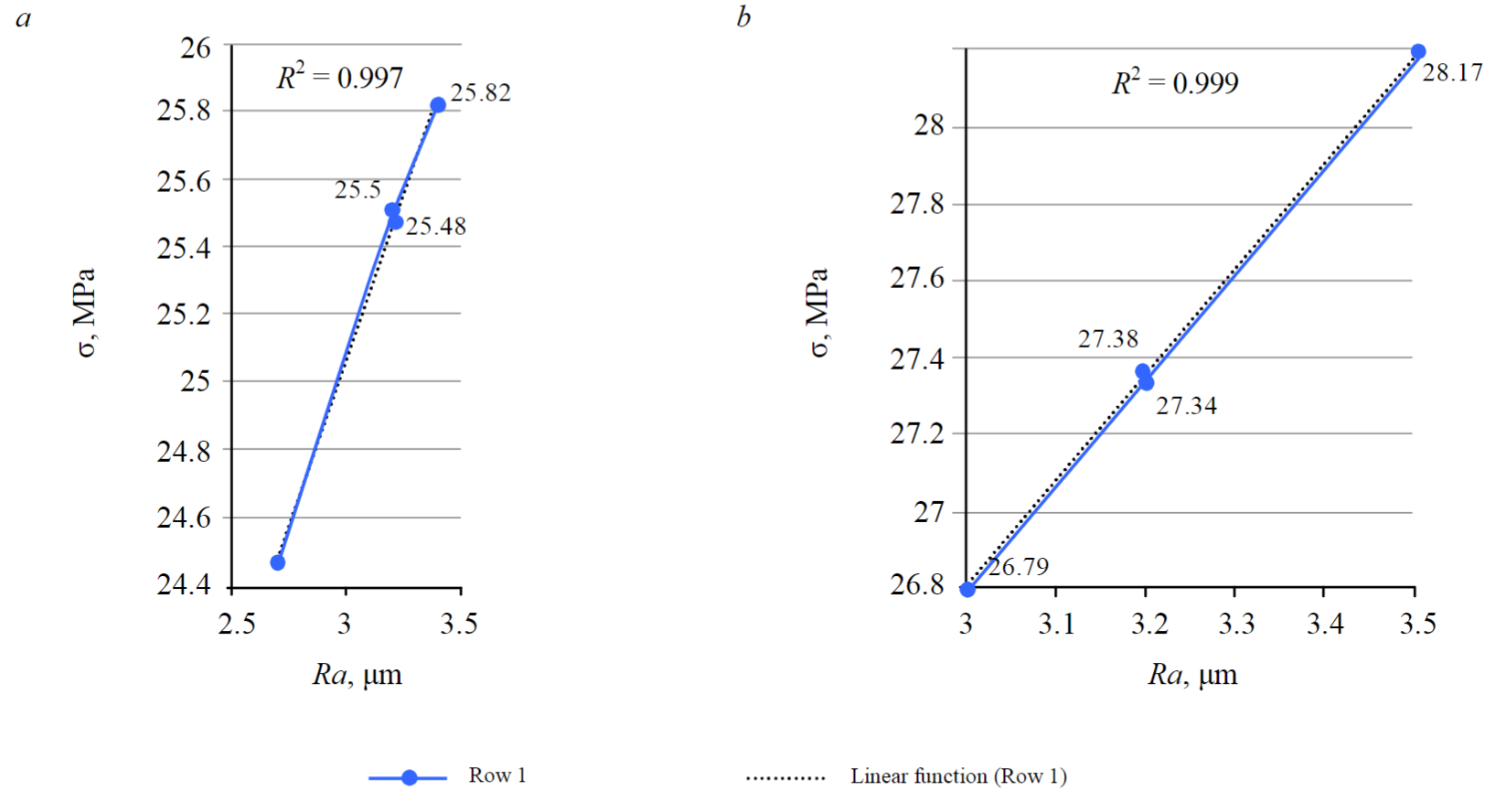
Therefore, it can be assumed that there is a direct dependency between these features, and that it can be expressed in a linear regression equation, given value of determination coefficient R2, by plotting a correlation field for each case.
Analysis of the data in the correlation fields allows to draw a conclusion that the highest value of determination coefficient corresponds to the linear function, as all the points in both correlation fields are located as close as possible to the straight line.
Graphic display of experimental data approximation is presented in Fig.4.
According to the plotted correlation field, it can be seen that the value of determination coefficient of the obtained adhesion values without adding aluminum to the used powder (Fig.4, a) R2 = 0,997, whereas in Fig.4, b, in case of adding aluminum to the powder it makes, R2 = 0,999, which indicates the maximum coincidence of the calculated straight line with the input data.
As seen from Fig.4, b, a first-degree polynomial can be chosen as an approximation function for both cases. For convenience of calculation, let us denote the data in the correlation field with a determination coefficient R2 = 0,997,X1, Y1, and the coefficients of the approximation function as a1,b1. Data in the correlation field with a determination coefficient R2 = 0,999 and coefficients of a2,b2, X2, Y2. Then a linear function for each case (φ1, φ2) will be described by equations, which express the observed values:
A sum of squared deviations is described by expressions:
Then, using the least square method, let us calculate coefficients of the approximation function a and b. In order to do this, let us estimate the minimum of S function (a and b). A set of equations with the condition for a minimum of this function for the two testing cases will be expressed as follows:
Then the denotations for data in both correlation fields are introduced, and the set of equations is written as:
Then the set of equations is derived:
From equations (8) let us find expressions, which describe the coefficient a for both cases:
Formulas to calculate the coefficientb for both cases are expressed as follows:
Basing on the derived formulas to calculate coefficients of the approximation function a and b given the testing data, obtained in the process of research, the values of these coefficients for both cases will be: a1 = 1,96; a2 = 2,79; b1 = 19,2; b2 = 19,5.
Given the calculated coefficients, linear functions (1) and (2) will be written as follows, for the case of adhesion strength study with a spray powder without aluminum:
for the case of adhesion strength study with a spray powder with added aluminum:
As a result of calculations and mathematical modeling, the functions were obtained, which were derived from the data in correlation fields of both testing cases and were the closest fit for the dependencies between surface adhesion strength and obtained roughness values, taking into account chemical composition of spray powder.
1. The surface roughness parameter was reduced approximately by 16% due to the use of the device for a measuring instrument, which enabled secure clamping of testing samples and the measuring instrument.
2. It was empirically confirmed that the presence of aluminum in PR-30X13 sprayed coating increased adhesion on the average by 3 MPa compared to the composition of the same powder without aluminum.
3. By means of numerical modeling, functions were obtained, which described a dependency between adhesion strength and surface roughness parameter for two studied cases.
Hence, the example of the described experiments confirms that adhesion strength is significantly influenced by the quality of surface texture, and the presence of aluminum in the composition of PR-20X13 spray powder increases adhesion strength and, consequently, greatly improves durability of the workpiece and allows to reduce financial costs and to increase economic benefits.