Estimation of ore contour movements after the blast using the BMM system
- 1 — Ph.D. research fellow Research Institute of Comprehensive Exploration of Mineral Resources, Russian Academy of Sciences
- 2 — Global Consultant Manage Blast Movement Technologies PTY Ltd Company AB Hexagon
- 3 — Ph.D. Technical Consultant for Russia and the CIS Blast Movement Technologies PTY Ltd Company AB Hexagon
Abstract
Measurement of ore movements by blast is one of the key components of the quality control system at any mining enterprise, which allows to obtain the accuracy necessary for determining the location of ore contours. About 15 years ago, a monitoring system was developed in Australia that allows mine personnel to make three-dimensional measurements of ore blocks movement at each blast. Studies have shown that ore blocks movement is extremely variable, and it characterized by a complete absence of a deterministic component. The consequence is that modeling ore contour movements during the blast will be inaccurate, and the best results for the mining enterprise can only be achieved by directly measuring the movement. The technology of measuring ore contours movements considered in the article is based on three-dimensional movement vectors obtained in different parts of the blasted block, characterized by different movements. It is obvious that the accuracy of determining the ore contours position after the blast is proportional to the number of measurements made on the block. Currently, the movement control technology based on the BMM system is actively used by global mining companies, its use reduces losses and dilution of ore. In 2017, the pilot implementation of the BMM system was started at the Olympiadinsky GOK, and the system is being implemented in several Russian mining companies.
Introduction. The BMM system of movement monitoring during the blast was commercialized after being developed by several researchers at the University of Queensland (Australia). It was found that modeling of ore contour movement after a blast does not provide the accuracy required for quality control. In [8], the developers of the system note that modeling of ore contour movement during a blast is potentially useful, for example, for training or solving problems that do not require high accuracy.
In 2001, the mining company Placer Dome (now Barrick), together with research scientists at the University of Queensland, tried to develop a predictive model for estimating the variability of vector movements after the blast, in order to use vectors for ore blocks movements and minimize ore loss, dilution and misclassification [9]. When it was determined that the used models were not able to achieve the accuracy required for quality control, scientists began to develop a system for monitoring movements during the blast, which was later commercialized. As a result, BMT (Blast Movement Technologies PtyLtd Australia) was formed in 2005.
The BMM system is widely used in gold mining enterprises and it is recognized as the world standard for tracking the ore movement after the blast [3, 4, 10, 13]. The system is used in more than 150 enterprises worldwide. Six of the ten largest gold producers are currently using this technology effectively. In Russia, a pilot project to implement BMM systems was launched in 2017 at the Olympiadinsky GOK. Currently, the technology is being implemented and the experience of its application is being replicated in Polyus company at the Verninskoye, Natalkinskoye, and Kuranakhskoye deposits. Other Russian companies are also working on implementing the system. The current number of users worldwide and in Russia is increasing, which confirms the relevance of this technology for improving the efficiency of mining and processing of ore raw materials.
Description of the monitoring system. The BMM system (Fig.1) consists of sensors that are activated by a special activator before the blast and installed on the area of the blasting block in predrilled "empty" holes. The correct placement of sensors on the block is an important component of success in obtaining reliable movement data. After the blast and their movement in the collapse of the blasted rock mass, sensors are detected, and their coordinates are determined using a special detector. The collected information is then processed in the specialized BMM Explorer software. Brief description of BMM system components:
• activator – a remote control that turns on each sensor and programs it;
• sensors-installed in specially drilled holes on the block, the location of which is fixed by the surveyor;
• a special detector is used to determine the position of the BMM sensor after the blast;
• the developed software calculates three-dimensional movement vectors of each BMM sensor, the data obtained is processed and stored in a database.
The process of working with the BMM system is clearly shown in Fig.2 and consists of 7 steps. It should be noted that the position of the ore blocks contours after the blast to reflect their movement and thereby reduce ore losses and dilution is determined within 1-2 hours after the blast, which indicates the ease of the BMM system use.
Formulation of the problem. The experience of using a BMM system in mining enterprises shows that the ore contours movement after the blast within a single block is extremely variable and depends on many factors. To determine the movement vector of the entire ore contour, it is not enough to install the sensor at any point of the blasting block (for example, in the center of one of the directional movement sites) and then interpret it for the entire directionally displaced site. This will not be enough to get reliable information about the entire ore contour movement, especially if there are several ore contours on the block. The results of the work of BMT specialists and other researchers demonstrate [3, 4, 10, 13], that the variability of horizontal ore contours movement during any blast can reach from 50 to -50 % of the average. The direction of movement can also be extremely variable and depends on the surface mounting schemes of the blast.
In addition, note that the required accuracy of estimating the ore contours movements after the blast cannot be achieved by modeling, which at the current stage of development of software and hardware complexes has received some progress. The reliability of the modeling results is not representative: due to the inaccuracy of the input data, which cannot be obtained for objective reasons, it is impossible to foresee all the nuances that affect the blasting process (inaccuracies of modeling algorithms). Experience has shown, they often differ significantly from instrumental measurements of movements, including using the BMM system.
Obviously, for effective ore quality management, the ore contours marked on the bench should be as accurate as possible (±0.2 m for some mines). In this regard, the selection of special methods for using the BMM system is required. The correct approach will ensure the required accuracy in estimating the ore contours movement within the blasted block. Research aimed at studying and highlighting these issues is relevant and will improve production efficiency.
Research methodology. Fig.3, a shows the distribution of horizontal movements determined using the BMM system for blasts conducted at four deposits that differ in mining and geological conditions for mining gold-bearing mineral reserves (Olympiadinskoe, Kuranakhskoe, Verninskoe and Natalkinskoe). For a comparative analysis of the results of using the BMM system, a three-month period was adopted. As can be seen from Fig.3, a, all deposits show high variability of horizontal movements in the same range of specific explosive consumption.
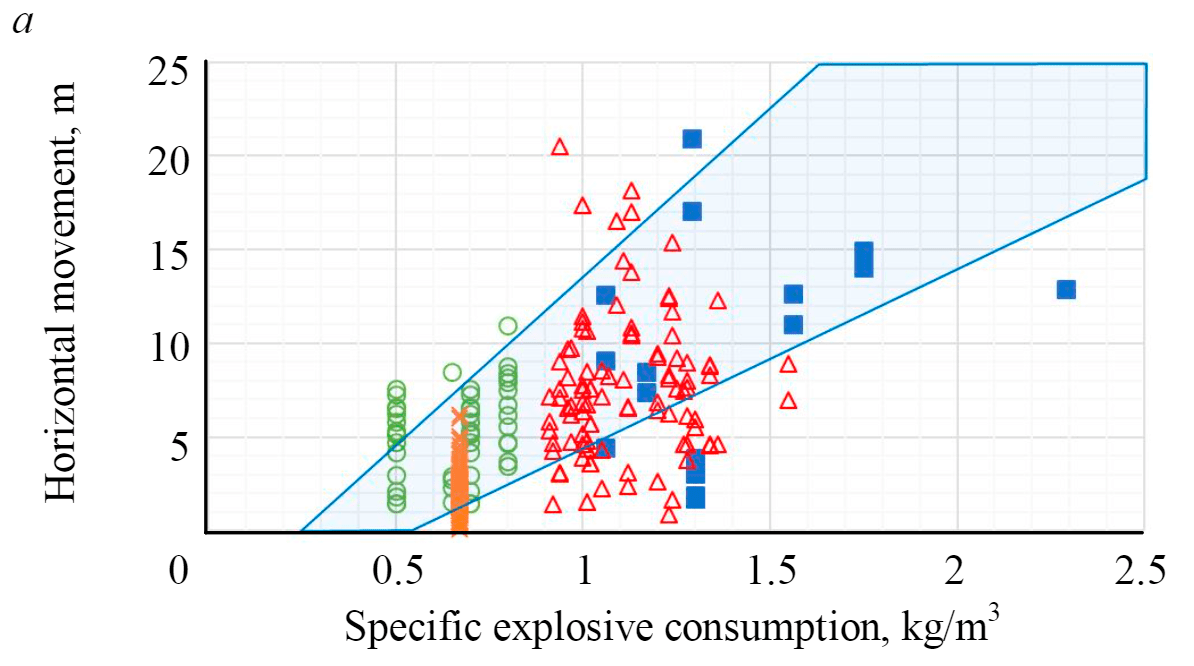
84 BMM sensors were used at the Olympiadinskoye deposit. Horizontal movements were recorded from 0.8 to 17.3 m, the average value was 7 m. 58 BMM sensors were used at the Kuranakhskoe deposit. Horizontal movements of ore blocks recorded by BMM sensors varied from 1.4 to 11 m. The average value was 5.1 m. At the Verninskoe deposit, 25 BMM sensors were used, the recorded horizontal movements of the blasted ore mass varied from 1.7 to 20.9 m, and the average value was 10 m. 132 BMM sensors were used at the Natalkinskoe deposit. The movements of the ore blocks varied from 0.1 to 6.2 m, with an average value of 2.2 m.
The standard deviation of horizontal ore contours movements from the average for the Olympiadinskoye deposit was 3.1 m, Kuranakhskoye – 2.3 m, Verninskoye – 5.7 m, and Natalkinskoye – 1.1 m.
Fig.3, b shows the distribution of vertical movements of BMM sensors on the objects under consideration for the same period. Note that vertical movements, along with horizontal ones, are also characterized by significant variability. Negative vertical movements are typical for areas located in the immediate vicinity of the so-called "break line" of the block and in the immediate vicinity of the free surface. Taking into account vertical movements of ore contours, along with horizontal ones, will certainly have a positive impact on the quality of the mined ore.
Discussion. Analysis of the obtained data allows to conclude that both horizontal and vertical movements have a significant spread of values not only between deposits, but also within the one deposit. Regardless of the movement amplitude of the ore contours, this variation is typical for these conditions, according to BMT statistics. The explanation for this is a number of factors that influence the size and direction of ore contours movement during the blast. Among them, the most significant are:
• design parameters of drilling and blasting operations (type and specific consumption of the explosive, borehole depth and charge height, presence and type of stemming, initiation scheme and deceleration intervals, distance between rows and holes, etc.);
• properties of the rock mass (physical and mechanical properties, strength, fracturing, water cut, presence of fractured zones, etc.);
• boundary conditions (conducting a blast in a nipped environment or on a free surface, the width and length of the block, etc.).
One should also note the possible factors that may affect the processes occurring during the blast and the direction of contours movement of the blasted rock mass (variable quality indicators of the blast, the means of initiation accuracy, the design parameters accuracy of the blast, etc.). Let us consider only the most significant factors.
Design parameters of drilling and blasting operations – the blast project controls the distribution of its energy through the block in space and time. The bench height, the distance between rows of boreholes, between boreholes, loaded length, length of stemming and its material, the borehole length and its diameter controls the distribution in space and the slowdown between each individual blasting boreholes – distribution in time. All of this is an example of a complex interaction, when the rock mass volume, exposed to blasting energy, changes dynamically during the blast, since rock masses move due to the action of the blasting forces on them [8].
The properties of the rock masses have the greatest influence on the movement’s variability, being at the same time the most difficult parameter to measure. The properties of the rock mass are determined by their structural configuration (for example, the size of blocks, characteristics of tectonic disturbances seams, their filling) and mechanical characteristics (for example, compressive strength, tensile strength, elasticity modulus and Poisson's ratio). Due to the randomness of these values in any ore body, they can never be measured accurately, but only statistically estimated based on a limited number of experiments. The ability to perform a wide range of measurements is limited in any block due to the availability of only a small part of it for measurements. For example, in a 200 × 100 × 10 m stoping block with a free surface, the available surface area is only 22,000 m2 for a block with volume of 200,000 m3. If the volume of the block, on which its strength characteristics were measured, was 0.5 m3, and its dimensions were 0.8 × 0.8 × 0.8 m, respectively, only 9 % of the total volume of the blasting block was available for such measurements [8].
Determining the boundary conditions for a blasting block is the final stage of determining the input data. They have a significant impact on the rock mass movement near the boundaries of the block, and also affect the shape of the rock mass collapse on its surface. For the blasts with a free surface and a corresponding slowdown, the movements will be mostly horizontal. If the free surface of the blasting block is limited, for example, in its lower part, by previously blasted material, the rock mass from the upper part of the blasting block will tend to fill the space above the left rock mass, shifting in the horizontal direction [8].
In most enterprises, only some of the characteristics presented above are known in advance, while others, such as the characteristics of a rock mass, may vary even within the limits of a single blasting block. As an example, consider a block where ore blocks movements were measured using the BMM system at the Verninskoye deposit. The block used a diagonal initiation scheme (Fig.4). 6 BMM sensors were installed, of which only 5 were detected after the blast. The horizontal and vertical movements recorded by the BMM sensors after the test are shown in the table. Note that within only this blast, the horizontal movements of the sensors ranged from 11.8 to 24.8 m, with an average movement of 17.8 m. It is obvious that in this case the use of systems that allow modeling the ore blocks movement after the blast would lead to significant ore losses, dilution and also its erroneous classification, which, ultimately, would negatively affect the economic performance of the enterprise. That is why mining companies are implementing the BMM system for tracking the ore blocks movement, which is an effective tool for ore control. Collapse modeling is being developed in some enterprises and it is an addition for obtaining information about movements [1, 2, 6, 7].
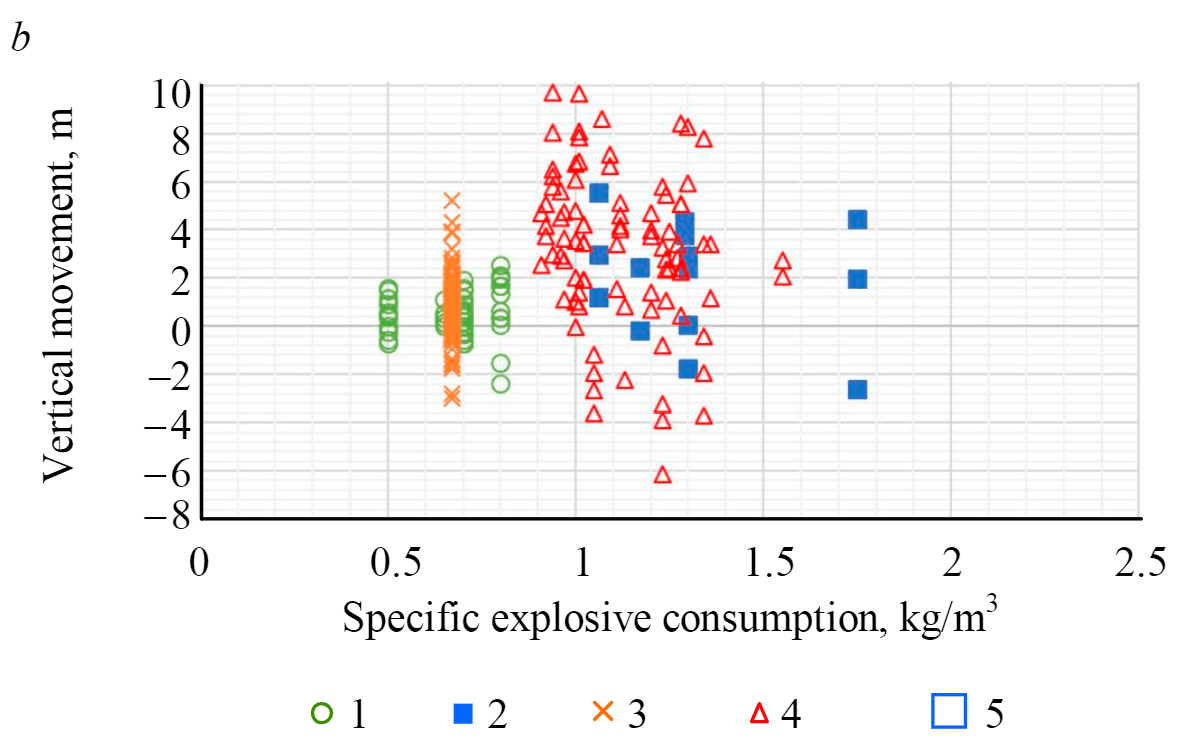
A similar variability in the ore blocks movement is typical for all mining enterprises without exception [5, 11, 12]. For example, in [5], the average ore contours movements (5.3 m) were compared with those measured at three blasts. Based on the obtained results (Fig.5), it is shown that the used pattern actually indicates movements close to the average, but it does not correspond to any available empirically obtained data.
BMM sensors movement after a blast
BMM | Installation depth, m | Horizontal movement, m | Vertical movement, m |
1-O | 5,0 | The sensor was not detected | |
2-O | 5,0 | 15,3 | 11,7 |
3-O | 5,0 | 19,0 | –1,6 |
4-O | 5,2 | 18,0 | 10,1 |
5-O | 5,1 | 11,8 | 1,3 |
6-O | 5,5 | 24,8 | 3,5 |
In the study [5], three blasts were analyzed. The three blasting blocks that were used for the research were located on the same bench, on the same open-pit, and under the similar geological conditions. For each of the blasting blocks, similar initiation schemes were used, and the specific explosive consumption was the same. Despite this, the BMM sensors movements for each blast are different from each other. Although the total average measured ore contours movement was approximately 5.5 m, which is close to the results of studies conducted in 2009 (5.4 m), the ore contours movements in each blast differ significantly from the average. The main conclusion of the research is that the ore contours movement by blast cannot be estimated by the pattern on the average value even if all the controlled input parameters remain constant and known. If the total ore contours movement in the blasting block matches the pattern, there may be a random deviation of the movements within a single blast. If in practice a pattern or a movement model is used instead of continuous monitoring, the risks associated with their application should be studied and evaluated. The benefits of direct monitoring far exceeded the costs. The return on investment (ROI) for only two blasts (9480-47 and 9480-52) was 14.5 in the real situation and 20.4 in the presented scenario. Thus, the benefit of using the BMM system in comparison with modeling in only these two blasts was approximately $ 42,000. This means that the BMM system will fully pay for itself in six blasts, after which it will only bring the company a net profit [5].
It can be concluded that the measurement of ore contours movements during blasting operations should be recognized as an effective element of the quality management system at the mining enterprise. The amplitude and direction of BMM sensors movements are determined by the initial data, which are fully taken into account; the inherent variability of ore contours movements is measured. Note that there are still no exact formulas for calculating movements that provide the accuracy required for quality management.
Measurement of ore movements by blast is one of the key components of a quality control system for any mining enterprise, as it allows to obtain the accuracy necessary for determining the location of ore contours and thereby increase the efficiency of mining and processing.
Conclusion. This article discusses the use of the BMM system for monitoring the movement of ore contours on the example of gold mining enterprises that have implemented and are using this system. The main purpose of the article was to prove the fact that in order to solve the problems of ore quality management, it is necessary to take into account the ore contours movements, which are characterized by significant variability in the blasting blocks. The BMM system allows to do this efficiently and with the necessary accuracy.
The ore contours movement in the considered deposits is variable and depends on a set of initial data, which is often impossible or ineffective to account. The ore contours movement at the current stage cannot be modeled with the necessary accuracy for quality control. The obtained data about movements in the framework of the study are not typical for enterprises even in similar mining and geological conditions. Direct measurements of the ore contours movement are currently the only accurate method. Due to the inherent variability of movements, a larger number of monitoring sites will lead to more accurate delineation of ore contours boundaries. The choice of such monitoring sites should be made at enterprises according to their mining and geological conditions based on the results of analysis of movement statistics at the conducted blasts.
Measurements of movements from the blast at several gold mining open pits showed that horizontal movements ranged from 0.1 to 20.9 m. For some open-pits in comparable conditions of drilling and blasting parameters, such movements within one block can vary by 15-18 m. Variation of horizontal ore contours movement when conducting of a blast can be up to ±50 % from the average. Reliable estimation of ore contours movements in such conditions is possible only with a sufficient and correctly selected number of points for measuring ore contours movements. If an insufficient number of sensors are installed on the blasting block, the ore contours movement in the selected positions may differ from the actual movement of the entire ore contour.
The results of the study prove that under certain circumstances, there may be situations when the open pit actually loses more ore, extracting it without taking into account the movement factor from the contours displaced by the blast. Instrumental measurement of ore contours movements by blast is an important component of the mining process, which minimizes such losses.