Изучение влияния алюминия на адгезию нержавеющей стали при газопламенном напылении
- 1 — канд. техн. наук доцент Санкт-Петербургский политехнический университет Петра Великого
- 2 — ассистент Санкт-Петербургский политехнический университет Петра Великого
- 3 — ассистент Санкт-Петербургский политехнический университет Петра Великого,
Аннотация
Данная работа посвящена исследованию влияния алюминия на повышение прочности сцепления с поверхностью. Основной целью работы является исследование прочности сцепления с подложкой при добавлении в порошок для газопламенного напыления алюминия, который обладает не только высокой коррозионной стойкостью и хорошей проводимостью, но и придает дополнительную прочность при комбинировании и взаимодействии с другими компонентами порошка. Показаны результаты исследований зависимости пескоструйной обработки от параметра шероховатости поверхности Ra . В работе описывается авторское устройство для контрольно-измерительного прибора «Профилометр», на котором также для получения сравнительных результатов проводились измерения параметра шероховатости. Представлены результаты измерений адгезии при полученных значениях шероховатости поверхности путем добавления в номинальный химический состав применяемого в качестве опытного материала порошка ПР-30Х13 алюминия, который вступает в химическую реакцию с оксидами на поверхности стальных субстратов , придавая связи покрытия с субстратом особую прочность, а также защищает базовый металл за счет комбинации составляющих химического состава порошка и создает слой плотного поверхностного покрытия. Произведен анализ данных зависимостей и определены параметры, оказывающие наибольшее влияние на их значения. С учетом полученных результатов на основе численного моделирования предлагается математическая модель зависимости прочности сцепления от определенных значений шероховатости поверхности при различном химическом составе порошка для напыления. Данные исследования помогут в разработке определенных видов материала для напыления и упрочнения деталей и изделий из стали, повышая их долговечность
Введение. Этап технологической подготовки производства является достаточно трудоемким процессом. Высокая трудоемкость данного этапа производственного процесса в значительной степени ощущается в условиях единичного и мелкосерийного производства, отличительными особенностями которых являются широкая номенклатура деталей с малым объемом выпуска, отсутствие специализированных рабочих мест, высокая трудоемкость и длительный производственный цикл изготовления изделий [7].
В связи с этим, учитывая быстрые темпы развития машиностроительного производства, выдвигается все больше требований к контактным поверхностям, что максимально актуализирует одну из главных задач в машиностроении – повышение износостойкости деталей. Одним из путей решения этой задачи является нанесение на деталь газотермического покрытия, каждый вид которого обладает универсальными свойствами и индивидуально воздействует на металл.
Анализ литературных источников показал, что важнейшим свойством, определяющим возможность применения газотермического напыления, является прочность сцепления с подложкой [1, 3, 5, 6, 8, 10, 11, 14, 15].
Однако, в ряде случаев, необходимая прочность сцепления износостойкого напыляемого покрытия рабочей поверхности изделий может быть обеспечена обоснованным выбором режимов струйно-абразивной обработки [5].
С целью повышения качества напыляемых покрытий после применения струйно-абразивной очистки и управления их свойствами при напылении и последующей обработке существует несколько способов комбинирования покрытий как с другими технологиями, так и с другими составами порошков для напыления.
Один из способов комбинирования описывается в данной работе: применение при напылении одного из химических компонентов – алюминия (Al), не входящего в номинальный состав исследуемого порошка для нержавеющей стали ПР-30Х13. Алюминий не вносит в схему процесса существенных изменений, сохраняет микротвердость, однородность по химическому и фазовому составу, структурную устойчивость и позволяет исследовать адгезионную прочность, помогает улучшить свойства покрытия, повышая долговечность и надежность изделий в условиях совместного воздействия высоких температур и агрессивных сред.
Постановка цели и задач исследования. Целью работы является разработка методики повышения адгезии при пескоструйной обработке с применением нескольких видов химических составов порошка для напыления.
В рамках достижения поставленной цели необходимо решить следующие задачи:
• измерение параметра шероховатости поверхности на выбранных опытных поверхностях образцов после удаления с их поверхности следов различных загрязнений и следов ржавчины с помощью пескоструйной обработки;
• активирование поверхности деталей при нанесении на каждый образец газопламенного напыления с применением нескольких химических составов порошка, измерение адгезии;
• выведение прямой зависимости прочности сцепления покрытия от состава порошка для напыления методом численного моделирования с нахождением рациональной линейной функции.
Методология исследования. Исследования проводились на двух заготовках из стали 30Х13, которая используется при изготовлении режущего, мерительного инструмента, пружин, карбюраторных игл, штоков поршневых компрессоров, деталей внутренних устройств аппаратов и других деталей, работающих на износ в слабоагрессивных средах до 450 °С.
Образцы имеют одинаковые характеристики: длину 500 мм, диаметр 30 мм (рис.1). Общий вид опытных образцов из стали 30Х13 представлен на рис.1.
Для получения наиболее полных и достоверных результатов каждый опытный образец был разделен на четыре части, для чего на их поверхностях на станке Optimum TH 4210 DPA V были нанесены по четыре риски глубиной 1,5 мм по всей окружности, на выделенных поверхностях проводились измерения параметров шероховатости поверхности, и, после восстановления деталей методом газопламенного напыления, измерения прочности сцепления основного материала с поверхностью.
При напылении на поверхностях деталей не должно быть следов ржавчины и загрязнений, раковин, трещин, обнаруживаемых визуально. Поэтому перед нанесением покрытия опытные образцы были подвергнуты пескоструйной обработке (степень очистки поверхности Sa 2,5) для придания металлу текстурной поверхности, так как шлифование и полирование не всегда эффективны для удаления окалины, ржавчины и т.п. [2, 9]. Такой метод очистки поверхности, основанный на принципах абразивного воздействия, не только придает необходимую шероховатость и насечку, существенно увеличивающие долговечность покрытия, но и очищает поверхность и выводит ее из состояния термодинамического равновесия со средой, освобождая межатомные связи поверхностных атомов, т.е. химически активирует подложку [12, 13].
Так как после очистки степень подготовки определяется оптимальными для нанесения покрытия параметрами текстуры поверхности, то для исследования адгезии материала необходимо учитывать показатели шероховатости поверхности [13]. В соответствии с ГОСТ Р ИСО 4287-2014, после очищения детали, были исследованы параметры шероховатости полученной поверхности. Поверхности обоих образцов были измерены прибором «Профилометр TR100».
В исследовании параметра шероховатости поверхности описывается запатентованное устройство для контрольно-измерительного прибора. Измерения проводились двумя способами: без использования устройства и с помощью него [4]. Окончательные, усредненные значения параметра шероховатости поверхности Ra были получены после пяти измерений на каждой из четырех исследуемых поверхностей каждого образца. Данные средних значений параметра Ra представлены в табл.1.
Таблица 1
Результаты измерения параметра шероховатости поверхности
Геометрия поверхности | Опытная поверхность | Средние значения параметра шероховатости поверхности Ra, мкм | |
Без применения устройства для контрольно-измерительного прибора | С применением устройства для контрольно-измерительного прибора | ||
Образец № 1 после пескоструйной обработки | 1 | 3,2 | 2,7 |
2 | 3,8 | 3,2 | |
3 | 4,0 | 3,4 | |
4 | 3,5 | 3,2 | |
Образец № 2 после пескоструйной обработки | 1 | 3,8 | 3,2 |
2 | 3,8 | 3,2 | |
3 | 4,2 | 3,5 | |
4 | 3,6 | 3,0 |
Описание устройства. Устройство для контрольно-измерительного прибора «Профилометр» предназначено для максимальной фиксации детали – в корпусе и контрольно-измерительного прибора – в отверстии, что существенно снижает как субъективную погрешность измерения, так и погрешности внешних влияний. Оно включает в себя корпус 3, состоящий из двух частей, скрепленных между собой болтовым соединением 2, причем габаритные размеры корпуса могут меняться в зависимости от длины и диаметра измеряемых деталей (рис.2). Верхняя часть корпуса содержит отверстие 4 для фиксации контрольно-измерительного прибора, его размеры также могут корректироваться под фиксируемую часть прибора. В верхней части устройства располагаются винты вертикальной подачи 5, служащие для корректировки вертикального подвода детали к контрольно-измерительному прибору. В нижней части корпуса располагаются винты горизонтальной подачи 7, закрепленные в отверстиях на ползунах 6 и имеющие на концах призматические губки 1, фиксирующие детали.
Принцип измерения параметра шероховатости с помощью описываемого устройства состоит в закреплении опытных образцов в призматических губках и подведении винтами вертикальной подачи их к контрольно-измерительному прибору, который также закреплен в отверстии для его фиксации. С помощью регулирования данных винтов были измерены значения на всех поверхностях обоих образцов.
Далее в течении трех часов (ГОСТ Р ИСО 8501-1-2014) после холодной абразивной обработки и контроля качества поверхности для исследования адгезии при полученных значениях шероховатости на опытные образцы было нанесено газопламенное напыление порошками с различным химическим составом, с предварительным обезжириванием и подогревом поверхности до 100 °C. Затем, в соответствии с исследованиями, с помощью адгезиметра PosiTest AT-A проводились измерения прочности сцепления с поверхностью на каждой из исследуемых поверхностей образцов № 1 и № 2 в соответствии с видом применяемого при газопламенном напылении порошка, после чего были выведены математические зависимости прочности сцепления покрытия от состава порошка для напыления методом численного моделирования, с нахождением рациональной линейной функции.
Планирование эксперимента и результат. На начальном этапе исследований для пескоструйной обработки поверхностей опытных образцов был применен пескоструйный аппарат эжекторного типа «Аэробластинг А-90Э», который предназначен для обработки металлических и бетонных поверхностей сухим песком любого вида фракцией до 3,5 мм. Для очистки использовалось сопло 6 мм, которое достигает средней мощности струи приблизительно 30 м3 в час. Рабочее давление при этом составило 3,5 кг/см2, расход воздуха 1,2 м3/мин, расход абразива 122 кг/ч, также использован кварцевый окатанный песок с фракцией 0,4-0,8 мм.
Увеличенные фрагменты поверхностей опытных образцов после применения пескоструйной обработки представлены на рис.3.

Качество поверхности после пескоструйной очистки контролировалось с помощью прибора «Профилометр TR100», со следующими основными характеристиками: измеряемые параметры шероховатости Ra, Rz, длина трассы сканирования 6 мм, допускаемая основная погрешность ± 15 %, алмазная игла с радиусом 5 ± 1 мкм, угол вершины щупа 900 (+ 50 или –100).
В результате измерений параметра шероховатости поверхности было выявлено уменьшение параметра Ra образца № 2, значения которого были получены при помощи устройства для контрольно-измерительного прибора. Разница в результатах измерений составила примерно 16 %. На основании полученных значений для дальнейших исследований в работе будут представлены данные результатов измерения шероховатости с применением устройства для контрольно-измерительного прибора.
Результаты измерений параметра шероховатости поверхности, полученные двумя описываемыми способами, представлены в табл.1.
В соответствии с постановкой задач исследования, далее опытные образцы были подвергнуты газопламенному напылению. Для напыления опытного образца № 1 был применен самофлюсующийся порошок нержавеющей стали ПР-30Х13, полученный распылением расплава металла газом (сферическая форма частиц) и отличающийся пониженной пористостью при напылении.
Затем в используемый порошок, имеющий следующий химический состав: Fe 87, Cr 13 %, для напыления образца № 2 в качестве металлической компоненты смеси был добавлен алюминий в размере 5 %, а содержание железа было уменьшено на 5 %.
Газопламенное напыление производилось при дистанции напыления в пределах 200 мм горелкой «Автоген ГН-2 BRIMA», которая предназначена для наплавки изношенных поверхностей деталей машин и механизмов, со смесью рабочих газов – кислорода и ацетилена.
Основные режимы и характеристики при нанесении газопламенного напыления: давление воздуха 0,5 МПа, давление кислорода 0,7 МПа, расход кислорода 58 л/мин, давление ацетилена 0,4 МПа, расход ацетилена 30 л/мин, размер зерен порошка 50 мкм, толщина первоначальный подслоя (на одну сторону) 0,2, основного слоя – 0,5 мм.
Далее с помощью цифрового адгезиметра PosiTest AT-A, который имеет диапазон нагружения 0,3-70 МПа, точность установки давления отрыва ±1 % от полной шкалы, методом отрыва, с применение упора 14 мм (максимальная прочность сцепления при данном упоре 40 МПа), были измерены и получены результаты зависимости параметров прочности сцепления с основным материалом (табл.2) при полученной шероховатости поверхности.
Результаты численного моделирования. После сопоставления имеющихся данных прочности сцепления и параметра шероховатости каждого опытного образца были сделаны выводы о наличии прямой зависимости и увеличении адгезии не только с увеличением параметра шероховатости, но и с добавлением в порошок для газопламенного напыления алюминия.
Таблица 2
Результаты исследования зависимости прочности сцепления от параметров шероховатости поверхности
Геометрия поверхности | Опытная поверхность | Средние значения параметра шероховатости поверхности Ra с применением устройства для контрольно-измерительного прибора, мкм | Значения прочности сцепления σ, МПа |
Образец № 1 с применением порошка для газопламенного напыления без добавления алюминия | 1 | 2,7 | 24,47 |
2 | 3,2 | 25,5 | |
3 | 3,4 | 25,82 | |
4 | 3,2 | 25,48 | |
Образец № 2 с применением порошка для газопламенного напыления при добавлении алюминия | 1 | 3,2 | 27,38 |
2 | 3,2 | 27,34 | |
3 | 3,5 | 28,17 | |
4 | 3,0 | 26,79 |
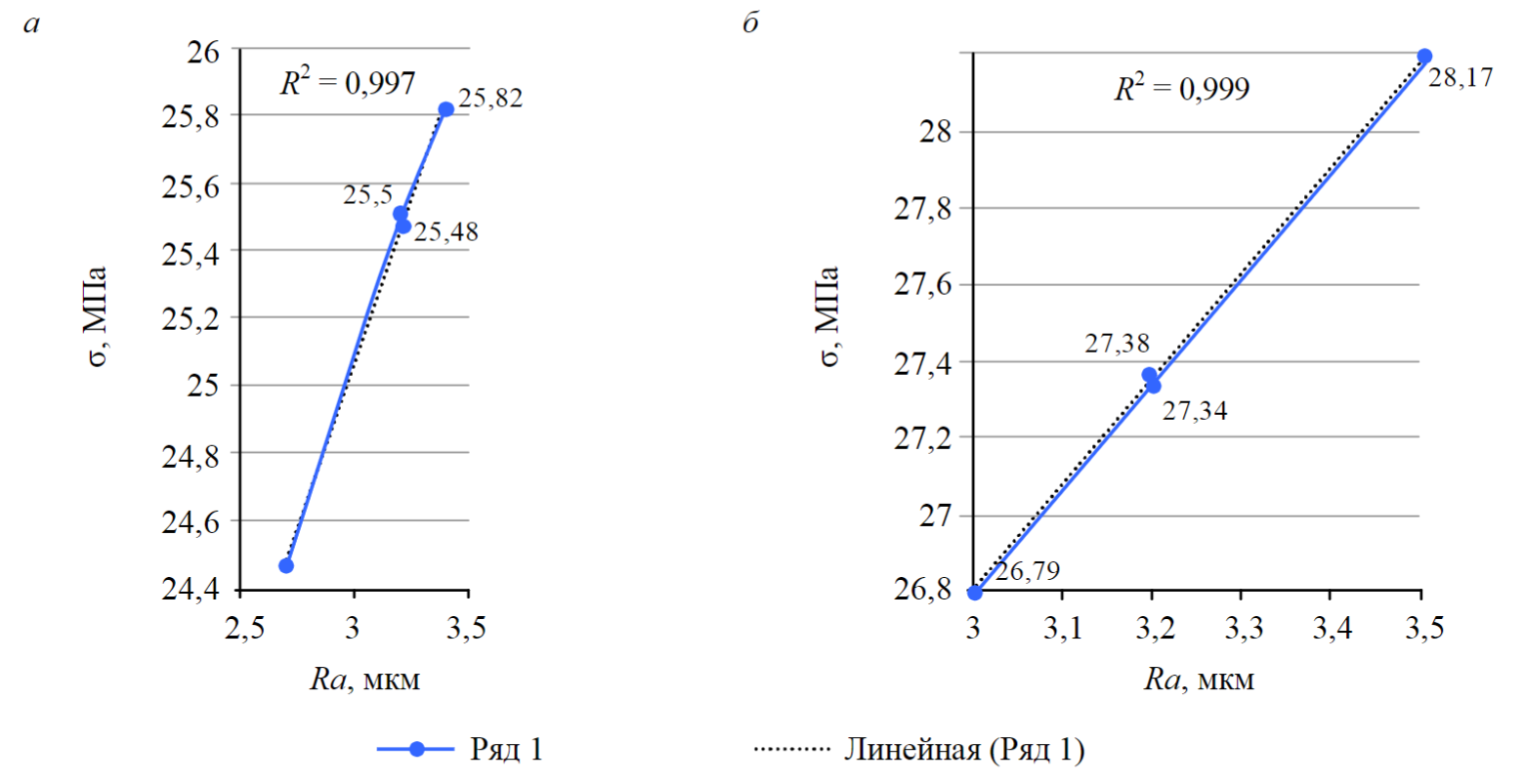
Исходя из этого, можно предположить, что связь между признаками прямая, и ее можно описать линейным уравнением регрессии при наличии величины достоверности аппроксимации R, построив поле корреляции для каждого случая.
Анализируя данные в полях корреляции, можно сделать вывод о том, что ближе всего к поиску величины достоверности подходит линейная функция, так как точки на обоих полях расположены максимально близко к прямой линии.
Графическое представление аппроксимации экспериментальных данных показано на рис.4.
В соответствии с построенным полем корреляции можно видеть, что величина достоверности аппроксимации полученных значений адгезии без добавления в используемый порошок алюминия (рис.4, а) R2 = 0,997, а на рис.4, б, при добавлении в используемый порошок алюминия, R2 = 0,999, что указывает на максимальное совпадение расчетной прямой с исходными данными.
Из рис.4, б видно, что в качестве аппроксимирующей функции для обоих случаев можно выбрать многочлен первой степени. Для удобства дальнейших расчетов примем обозначения данных в поле корреляции с коэффициентом достоверности R2 = 0,997,X1, Y1, а также обозначения коэффициентов аппроксимирующей функции a1,b1. Данные поля корреляции с коэффициентом достоверности R2 = 0,999 и коэффициентами аппроксимирующей функции a2,b2, X2, Y2. Тогда линейная функция для каждого случая (φ1, φ2) будет описана уравнениями, которые выражают наблюдаемые значения:
Сумма квадратов отклонений опишется выражениями:
Далее, используя метод наименьших квадратов, найдем значения коэффициентов аппроксимирующей функции a и b. Для этого вычислим минимум функции S (a и b). Система с условием для существования минимума данной функции для двух опытных случаев будет описана выражениями:
Затем были введены обозначения данных обоих полей корреляции, и система приняла вид:
Далее была выведена система уравнений:
Из уравнений (8) находим выражения, которые будут описывать коэффициент a для обоих исследуемых случаев:
Формулы для расчета коэффициента b для обоих исследований выражены в:
На основании выведенных формул для расчета коэффициентов аппроксимирующей функции a и b при полученных в результате исследований опытных данных значения данных коэффициентов для обоих случаев будут равны: a1 = 1,96; a2 = 2,79; b1 = 19,2; b2 = 19,5.
При полученных коэффициентах значения линейной функции (1) и (2) приобретут вид для случая исследования прочности сцепления с порошком для напыления без применения алюминия
для случая исследования адгезии с порошком для напыления с применением алюминия
В результате расчетов были получены функции, выведенные на основе данных значений полей корреляции обоих опытных случаев, которые точнее всего описывают зависимость прочности сцепления с поверхностью при полученной шероховатости в зависимости от химического состава порошка для напыления с применением математического моделирования.
1. Параметр шероховатости поверхности уменьшился приблизительно на 16 % при использовании устройства для контрольно-измерительного прибора за счет максимальной фиксации в нем как опытных образцов, так и самого измерительного прибора.
2. Опытным путем было доказано, что присутствие алюминия в напыляемом порошке ПР-30Х13 повысило параметр адгезии в среднем на 3 МПа по сравнению с составом того же порошка, но без алюминия.
3. На основе численного моделирования были получены функции, которые описывают зависимость адгезионной прочности от параметра шероховатости поверхности в двух исследуемых случаях.
Таким образом, на примере проведенных исследований было доказано, что существенное влияние на адгезионную прочность оказывает качество текстуры поверхности, а присутствие в составе порошка для напыления ПР-30Х13 такого элемента как алюминий повышает адгезионную прочность и, следовательно, существенно повышает долговечность детали и дает основания к уменьшению финансовых затрат и повышению экономической выгоды.