Design features of coal mines ventilation using a room-and-pillar development system
- 1 — Ph.D. Professor NUST MISIS, Mine institute ▪ Elibrary ▪ Scopus ▪ ResearcherID
- 2 — vice chief Mines Rescue Service of Republic of Khakassia Mines Rescue Service of Republic of Khakassia
Abstract
The safety of mining operations in coal mines for aerological factors depends on the quality of accepted and implemented ventilation design solutions. The current “Design Manual of coal mine ventilation” do not take into account the features of room-and-pillar development systems used in Russia. This increases the risk of explosions, fires, and gassing. The detailed study of foreign experience in designing ventilation for the considered development systems e of coal deposits allowed to formulate recommendations on the ventilation scheme organization for coal mines using a room-and-pillar development system and the procedure for ventilation during multi-entry gateroad development. Observations have shown that the use of the existing Russian procedure for airing mining sites with a room-and-pillar development system complicates the emergency rescue operations conduct. Low speeds and multidirectional air movement, difficult heat outflow, and the abandonment of coal pillars increase the risk of occurrence and late detection of endogenous fire. The results of numerical modeling have shown that the installation (parallel to the drifts) of ventilation structures in inter-chamber pillars will increase the reliability of ventilation by transferring the ventilation scheme from a complex diagonal to a complex parallel. It will also reduce the amount of air required for the mine site and the total aerodynamic drag. The research made it possible to formulate requirements for the design procedure for coal mines ventilation using a room-and-pillar development system, which consist in the order of working out blocks in the panel, and also the additional use of ventilation structures (light brattice clothes or blowing line brattice).
Introduction. Currently, there are several coal mines in Russia that use a room-and-pillar development system (for example, the Denisovskaya-Tsentralnaya mine and the Mezhegeyugol mine). These development systems are common in the extraction of non-combustable minerals. During coal mining, a number of issues arise to ensure aerological safety in terms of choosing rational schemes and modes of ventilation, ventilation structures, and the procedure for monitoring the mine atmosphere parameters. These issues are closely related to the order of mining operations and development. At the same time, there are no regulatory requirements, methodological documents for the design and control of ventilation for such systems developed in Russia. To ensure the safety of mining operations and also mine rescue operations, taking into account the upcoming significant changes in the regulatory framework and the “regulatory guillotine” criteria [7], research on the ventilation parameters of coal mines using a room-and-pillar system is needed.
Formulation of the problem. The room-and-pillar mining system at coal mines is actively used in the USA and Australia [14, 14]. The mine field is divided into panels, which, in turn, are worked out by tunneling machines, hauling is usually carried out by self-propelled cars and conveyors. Pillars mined out by a reverse motion with the use of self-propelled supports. Ventilation of such mining sites is carried out by dividing the panel into two or three parts (Fig.1). Air is supplied through some mine workings, and an outgoing air stream is issued through others, while it is allowed to maintain several workings in a “neutral” ventilation state, without a certain direction of air movement, while observing the minimum air speed equal to 250 FPM (1.27 m/s) [9].


The peculiarity of such ventilation schemes is to provide air to the bottom-hole area by using partition walls (Fig.2, a) or by installing booster fans (BF) in the immediate vicinity (Fig.2, b). At the same time, there is a clear directional movement of fresh and outgoing air jets. According to calculations by W.R.Kennedy [14] this scheme reduces the aerodynamic drag of the mining site by nine times from 0.09 to 0.01 km. The aerodynamic scheme is represented by a complex parallel connection and is reciprocating. Mining and tunneling operations are combined and have a single front.
In Russian coal mines, the ventilation scheme has a number of significant differences:
1. First, the mining site (the extraction pillar or panel) is cut with one or two paired drifts. The site is divided into blocks that are randomly worked out by tunneling machines, while there is no single front for mining operations.
2. Air is supplied to the face by directing the main jet to the mined out block by installing ventilation windows in the drifts or by air feed pipe with booster fans installed in the drifts.
To determine the reliability and efficiency of ventilation schemes used in Russia for the roomand-pillar development system, field studies and mathematical modeling were conducted to assess the level of aerological safety with further development of scientifically based recommendations.
The research was conducted at the Mezhegeyugol mine, which is located in the Republic of Tyva. The mined bed has an inclined dip, which causes its opening with inclined pillars. One of the distinctive features of this mining company is that it was designed by the Australian company Snowden, whose specialists proposed a room-and-pillar development system. The deposit at this stage of development is mined out by four inclined shafts, while the general ventilation scheme is central – flank. The mine uses a pressure system ventilation (Fig.3).
According to geological surveys, the deposit has several zones with coal burned due to spontaneous combustion. This is due to the inclined dip of the formation, its output to the surface and the presence of an aerodynamic connection with the surface. In case of a complete collapse, the number of cracks connecting coal seams to the surface can be significantly increased, which will significantly increase the risk of endogenous fires [8, 17].There is one main ventilation fan in operation ВО-A22- 14ВР, the air is supplied through the western ventilation shaft. The outgoing stream from the mine is issued through the western conveyor, western transport and western flank shafts. The methane content of the mined bed with the depth of mining operations increases from 4 to 11 m3/t. At the same time, ventilation of the mined out blocks is provided at the expense of a mine ventilating pressure drop. Additionally, booster fans are used for ventilation of blind parts of workings with a total length of more than 10 m. They are installed on drifts that outline the mining site (Fig.3).
The conditional aerodynamic scheme (Fig.4) allows to visually estimate the number of zones with difficult to predict air direction. Inside the blocks, mine workings are ventilated at low air speeds. Field measurements have shown that the air velocity is less than 0.25 m/s. Periodically, in a short period of time, the air flow-back occurs in the inter-chamber pillars. This is due to the auxiliary transport used for the delivery of people (Driftrunner vehicles) and cargo (CL210 loading and delivery vehicles, DMZ50F diesel manipulator). Driving into the workings of the mine site and block, they overlap part of the cross-section, which leads to an increase in aerodynamic drag due to aerofoil drag.

It should also be noted that in order to increase the coal mining productivity, panel mining is sometimes worked out simultaneously in several blocks (see Figure 3). This does not exclude the possibility of mine workings gassing due to methane ingress through the conveyor drift, where gas control is carried out in accordance with the federal rules and regulations (FRaR) only on the outgoing jet from the site and at booster fans installed on the ventilation drift. The change in the control procedure was reported earlier [3, 12], but for schemes with a room-and-pillar development system such proposals were not submitted for discussion.
An additional factor in assessing the aerological safety state of coal mines using a room-andpillar development system is endogenous fire hazard. Leaving pillars in a supported worked out space, taking into account low air speeds, significantly increases the risk of fire. The presence of a complex diagonal connection complicates the conduct of rescue operations in terms of detecting, locating and eliminating accidents.
On August 5, 2017, a fire with smoke from the mine workings occurred at the Mezhegeyugol mine. 93 people were brought to the surface. Due to the complex airing scheme, position 17 was initially activated (fire in conveyor drift 2-2), but after an investigation, it turned out that the fire occurred in track 3-15. It took 89 minutes from the start of the accident to the fire detection. The fire was caused by a conveyor belt ignition. The smoke spread to all the mine workings, which made it difficult to find the fireplace. However, the rescuers managed to localize the fire spread and prevent the ignition of coal pillars in the worked out space.
Taking into account the existing methods of predicting emergency situations, the most optimal is three-dimensional computer modeling, which makes it possible to calculate the coordinates of the fire source with a high probability, but this requires complex preliminary work on collecting initial data and building a virtual analog of an underground aerogasodynamic system [4].
Methodology and analysis of research results. To assess the effectiveness of ventilation and ensure safety by the aerological factor for complex diagonal schemes that represent the mine sites, specialized software tools “Ventilyacia 2.0” and “VentPLA” were used, and verification was also performed by conducting full-scale measurements. [9].
Based on the ventilation scheme, a simplified standard scheme was used (Fig.5), which allowed to determine the main characteristics of the mine ventilation network. It is established that the tracks and drifts (the main elements of the mine site) are located in a complex diagonal connection, the air movement direction in which depends on the resistance of the upper and lower conveyor drifts. Calculations have shown that a change in the resistance in any of the defining drifts can lead to air flow-back inside the block.
Calculations have established that in a number of tracks and subdrifts inside the block, the air velocity is less than the permissible values (0.25 m/s) or equal to zero, which is confirmed by measurements in the mine.
According to mine design data, 6,25 m3/s of air is required to ventilate one face. A panel consisting of blocks (up to seven in a panel) is divided into drifts (up to seven in a block) and tracks (up to nine in a block). Supported mine workings (without brattice clothes), represented by a single network, must be ventilated taking into account the minimum air speed. The required amount of air is Qblock = n(VS) = (9 + 7) 0,25·21 = 84 m3/s. Taking into account the simultaneous operation of four faces, the air consumption will be equal to Qpan = 84 + 6,25∙4 = 109 m3/s. Currently, the air in a single panel block is supplied in a smaller volume.
The next step was to assess the effect of increasing the total length of mine workings in the panel on the total aerodynamic drag as the main element of the mine ventilation network (MVN), the change of which affects the aerological safety. Mathematical modeling was used to calculate the value of the aerodynamic friction drag (without taking into account local and airfoil drags). At the same time, it was assumed that at each stage one track with adjacent sites of intra-block drifts is fully worked out (Fig.5). The calculation data is shown in the table with the graph in Fig.6.


From the obtained results, it can be concluded that with an increase in the number of workings, the total aerodynamic drag under this scheme decreases slightly (by 1.02 times), while the total length of mine workings increases significantly (by more than 1000 m). The decrease in aerodynamic drag occurs in a linear relationship with a very close to zero angular coefficient (Fig.6, b), however, when using existing specialized software (“Ventilyacia 2.0” and “VentPLA”), airfoil and local drags are not taken into account, which does not allow to fully assess the impact of the applied development system on aerological safety. Research can only be continued using three-dimensional computer modeling, which is widely used in leading universities and research organizations [2, 10, 15, 16]. This issue requires further research, and according to current data, it can be concluded that with an increase in the total length of mine workings in the applied scheme, the total aerodynamic drag increases slightly.
Recommendations for schemes and modes of ventilation. Based on the research, the following recommendations are made for measures to improve the reliability of the ventilation system when using a room-and-pillar development system:
1. Organization of a united front for mining operations. According to the results of the analysis of room-and-pillar systems used abroad for the coal deposits development, it is noted that there are schemes for airing the entire mine site on the principle of a complex parallel connection. At the same time, all mining faces are located within two adjacent tracks. It turns out a single front for mining development, which increases the reliability of ventilation (from a complex diagonal ventilation scheme, we move to a complex parallel scheme), and also reduces the cost of ventilation due to a decrease in the number of supported mine workings that require separate ventilation.
2. Installation of rapidly erected ventilation structures of the blowing line brattice type (Fig.7, b and 8, a), and also the changes in the technology for preparing the mine panel, will allow to switch from a complex diagonal to a complex parallel scheme for airing the site. This solution will ensure the safety rules compliance in terms of ventilation due to the blind ends diffusion (formed due to the installation of a brattice clothes in the breakthrough between the drifts). It will also reduce the amount of air needed to ventilate supported mine workings. The introduction of the proposed parallel ventilation scheme will eliminate the possibility of air flow-back, which, according to observations, occurs in a complex diagonal scheme. Air regulation between drifts can be carried out using blowing line brattices. The amount of air required to ventilate one block (seven drifts, including the nine tracks excluded from the MNV) will be Q = n(VS) = 7·0,25·21 = 36,75 m3/s (excluding the introduction of a parallel ventilation scheme, the flow rate is 84 m3/s).
3. Installation of booster fans should be carried out on a fresh air stream before the first face or before the main front of mining operations (Fig.8, b). This measure will prevent methane from entering existing mine workings due to a possible air flow-back.
4. To increase the level of aerological safety, it is also necessary to consider a set of works on ventilation and degassing, which is described in detail in [5, 6].

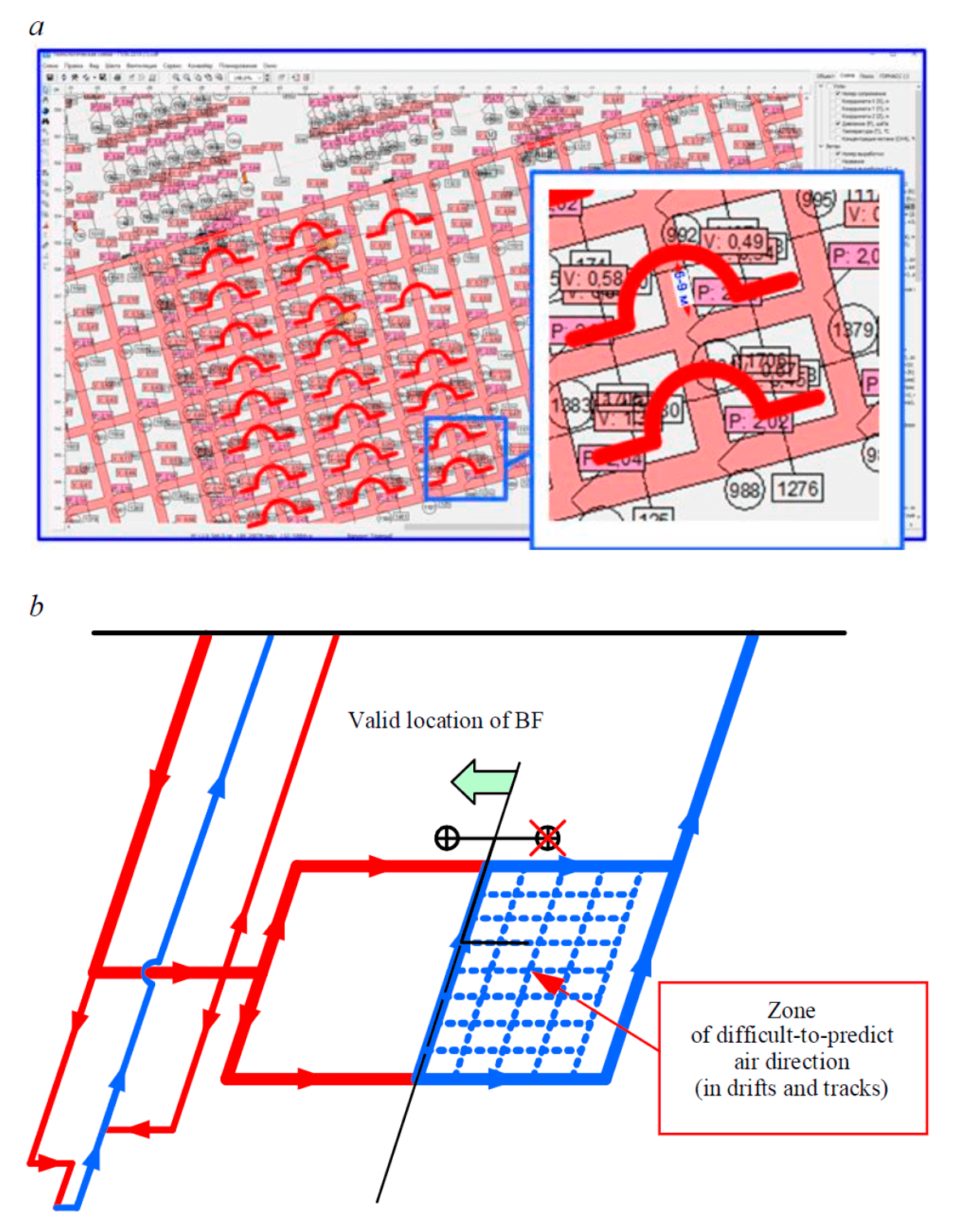
Conclusion. Determining the airing parameters of coal mines that use a room-and-pillar development system requires scientific justification at a higher level than for ore mines. This is due to the danger of methane accumulation in the mine workings of the mine panel, and also the presence of a large amount of coal (mainly in the pillars), which at low air speeds will contribute to the difficulty of heat outflow and further self-heating with the risk of endogenous fires.
Based on the conducted research, the main characteristics of the mine ventilation network were determined. It is established that the tracks and drifts are located in a complex diagonal connection, the air movement direction in which depends on the drag of a large number of mine workings of the block.
Analysis of the computer simulation results showed that a change in the drag in any of the defining drifts can lead to air flow-back inside the panel. Calculations and field measurements found that in a number of tracks inside the panel, the air velocity is less than the permissible 0.25 m/s or even zero, which leads to a violation of the FRaR.
The conducted research can be used in the development of a regulatory framework based on the “regulatory guillotine” criteria [7], and also a riskbased approach in the development of methods for predicting the coal mine explosion safety of mine sites [1] and in the development of new technologies for the mining of gas-bearing coal seams [13].