Improvement of energy efficiency of ore-thermal furnaces in smelting of alumosilicic raw materials
Abstract
The issues of energy saving in pyrometallurgical production during processing of mineral raw materials in ore-thermal furnaces are particularly important for the development of new energy-efficient technologies. The reduction of the specific power consumption during melting at different stages of heating and melting of charge materials when modeling is related to obtaining kinetic curves in the process of kyanite concentrate regeneration in polythermal conditions. Based on practical data of carbo-thermal reduction the mathematical modeling of reduction processes from alumosilicic raw materials – kyanite was carried out. In this work, the nonisothermal method based on a constant rate of charge heating (i.e. a linear dependence between time and temperature) was used for the reduction of kyanite charge, which saves electrical energy. The experiments were carried out on a high-temperature unit with a heater placed in a carbon-graphite crucible. Based on the obtained kinetic dependences of nonisothermal heating of enriched kyanite concentrates in plasma heating conditions we obtained a number of kinetic anamorphoses of the linear form which point to the possibility of describing the reaction rate using the modified Kolmogorov – Erofeev equation for given heating conditions and within a narrow temperature range. The complex of mathematical modeling makes it possible to create a control algorithm of technological process of reduction of kyanite concentrate to a metallized state within the specified temperature range for the full flow of reaction exchange and to reduce the specific power consumption by 15-20 %. With the help of the received kinetic dependences, taking into account the thermodynamics of processes and current state of the art it is possible to create a universal thermal unit for the optimal carbothermal reduction of charge to a metallized state (alloy) with minimum power inputs compared to existing technologies.
Introduction
Energy saving in production during processing of metallurgical and anthropogenic raw materials is paramount for solving both local [1, 2], and global environmental problems [3, 4]. So the development of new technologies based on fundamental scientific approaches is of great practical importance for the strategic energy-efficient development of the metallurgical industry [5-7]. The development strategy for ferrous and non-ferrous metallurgy of the Russian Federation until 2030 includes a large complex of measures for energy saving and the reduction of specific energy intensity of products, resource intensity, and emissions of harmful substances. The national mining and metallurgical complex [8-10] has already taken a number of measures to improve the energy efficiency of production. However, shortages of some resources or partial inaccessibility lead to significant economic and industrial problems [11-13] and risks [14-16], as well as to the reduced efficiency in the use of fuel and energy resources, sometimes complete losses in the supply of enterprises [17-19].
The production of aluminum silicon alloys, the most popular type of aluminum alloys, requires the organization of primary aluminum production in electrolysis cells, while the production of silicon requires the carbothermic method of reduction from quartz raw materials in ore-thermal furnaces [20-22]. In the production of primary aluminum, only alumina is used as an aluminum-containing raw material, and in Russia there are significant difficulties in providing enterprises with their own raw materials due to a shortage of high quality bauxite [23, 24]. The shortage of alumina for electrolytic production, which has developed as a result of the shutdown of some plants and the reduction in the share of exports for political reasons, leads to a search for innovative, energy-saving technologies for aluminum and aluminum silicon alloy production from alternative raw materials, which could be kyanite [25, 26]. After the reduction of unprofitable capacity and the mothballing of several plants with obsolete electrolysis cells, raw material shortages amount to approximately 45 % of all alumina production in the Russian Federation [27-29].
Systematic research is being conducted using aluminum and silicon industries wastes [10-15] in order to provide new types of aluminum-containing raw materials [30, 31]. Ore reserves of aluminum-silicon raw materials are studied as well in order to use them in processing [31, 32]. The end products of these technologies satisfy only a certain narrow demand of the industries due to the specific properties of the raw material and technological solutions. However, these studies are not focused on one of the promising areas, the direct production of aluminum silicon alloys, containing aluminum and silicon oxides by means of carbothermic reduction.
At present, the use of kyanite ores in various branches of industry is a highly topical issue due to the considerable number of reserves and simplicity of their development [33] in the Urals [36] and Keivy [34, 35] Mountains. Besides the production of refractories and ceramics, this type of raw materials can be used for production of alumina and silicon oxide after beneficiation and separation of the concentrate [37-39]. However, calculations show that the technology of kyanite disintegration is economically unprofitable in current conditions of traditional alumina production by the method of Bayer-sintering [40, 41].
Several attempts to study kyanite ores of the Kola Peninsula were made during the 20th century. The first study carried out by V.S.Artamonov, P.A.Borisov, and N.A.Volotovskaya dates back to 1929. The Mekhanobr Institute received preliminary data on beneficiation of kyanite-quartz material in 1939. All-Russian Aluminium-Magnesium Institute tested kyanite ore to produce kyanite concentrate by the flotation method in industrial conditions in 1949. In parallel, the geological aspects of kyanite deposits were studied, and 27 deposits were identified. A preliminary assessment of ore reserves showed 966 million tons located at depths of up to 100 m. The total volume of the deposits was 11 billion tons. Favorable geological conditions of ore occurrence make it possible to develop them by open-pit mining with high performance.
In this regard, the studies on the issues of direct reduction of the kyanite charge for the production of hypereutectic aluminum silicon alloys are of high scientific and practical interest (28 % of silicon in the final alloy). There are studies on the carbothermal reduction of alumina for production of aluminum [42-45]. Thus, calculations of technical and economic indicators in the work [43] confirmed the promising nature of this technology. The environmental analysis carried out in this work indicates a low ecological impact by the production of aluminum and its alloys compared to the current production. The analysis of the literature shows that methods of direct processing of charge materials [41, 46] without the use of fluorine-containing and carcinogenic substances (as in the electrolysis of molten salts according to Hall – Eru method) are promising, which is certainly a favorable positive factor. On the other hand, the carbothermal method of aluminum production had many difficulties in the implementation of the technological process in the 1970s and 1980s due to the formation of carbide compounds. The presence of these compounds reduces aluminum yield and with an increase of silicon content the production process was more active from the thermodynamic point of view. The low level of technology, insufficient study of the issues associated with reduction of charge, and the use of inadequate thermal aggregates could not have created the conditions for a wide distribution of industrial carbothermal production of aluminum.
Despite the existing scientific background and practical experience in the studies of the reduction of aluminosilicate charges, the issues of the direct reduction of the charge to the metallized state remain unresolved. There are no data on the kinetics and mechanism of interaction in the Si-Al-O-C system, which is an important technological factor and scientific justification for the implementation of the carbothermal process of aluminum silicon alloy production from kyanite concentrates or similar charge materials. The solution of this problem is especially important for improving the energy efficiency of the production of basic aluminum alloys.
Methods
Metallurgical processes based on the reduction of metals from their compounds by carbon and carbon-containing materials take place in ore-thermal furnaces at elevated temperatures and have highenergy losses (part of the heat is waste, partly spent in the assembly units and on the reduction of impurity elements and incorrectly composed charge material). In the course of this work we considered a method that allows us to study more extensively the chemistry of the carbothermal reduction of kyanite charge materials when producing aluminum silicon alloy and eliminate energy losses in the metallurgical process. A non-isothermal method was used for the reduction of the kyanite charge in this work. The method is usually based on a constant heating rate of the charge, i.e., in the presence of a linear relationship between time and temperature, the following equations are valid
where m – heating rate, °С/min; а – degree of conversion the metallic phase (reactivity).
The experiments were carried out on a high-temperature unit with a carbon-graphite heater with an additional element – a directed arc. A directed plasma arc is required for intensive heating and implementation of the non-isothermal method of processing the kianite charge to the specified temperatures (2000-2300 °C).
A sample of beneficiated kyanite concentrate with a minimum content of titanium oxide and iron (Table 1) with a molar ratio of SiO2:Al2O3 = 0.73 was used in the conducted experiments. The carbon content in the sample was 110 % of the theoretically required amount for the reduction of oxides to metal (aluminum silicon alloy). The reduction was carried out using a directed plasma arc (controlled plasma flow) at heating rates of 10, 20, and 40 °C/min in the temperature range from 1100 to 2200 °C. The total heating rate and process kinetics were estimated by the rate of gas releasing during the reduction reaction (Fig.1) and by the amount of carbon dioxide registered by the MGL-98 gas analyzer. The temperature data were recorded by the WRe-5/20 tungsten-rhenium thermocouple connected to the OVEN TRM1 thermostat.
Table 1
Results of X-ray spectral analysis of kyanite samples, %
Fraction |
Na2O |
MgO |
Al2O3 |
SiO2 |
P2O5 |
S |
K2O |
CaO |
TiO2 |
MnO |
Fe2O3 |
Non-magnetic |
0.2 |
< 0.01 |
51.33 |
37.63 |
0.12 |
0.013 |
0.5 |
0.05 |
0.6 |
< 0.01 |
0.18 |
Magnetic |
0.25 |
0.21 |
50.98 |
35.64 |
0.19 |
0.029 |
0.49 |
0.25 |
0.67 |
0.054 |
1.85 |
For thermodynamic calculation of the process in a given temperature range, possible reactions are considered in wider values of 1400-1900 °C according to the following group of equations:

Fig.1. The kinetic curves of the reduction of kyanite concentrate in polythermal conditions 1 – 10 °С/min; 2 – 20 °С/min; 3 – 30 °С/min
where equations (3) and (4) refer to the interaction of oxides with fine fractions of carbon in the graphite environment of the furnace, and the rest of the equations refer to the interaction of oxides with solid carbon in the charge.
The kinetics of reduction of silicon dioxide in the given temperature range of 1100-1900 °C was studied at a constant heating rate of 20 °C/min. The studied sample was quenched every 100 °C, then the change in mass was determined, and the chemical analysis of the resulting material was carried out (Table 1).
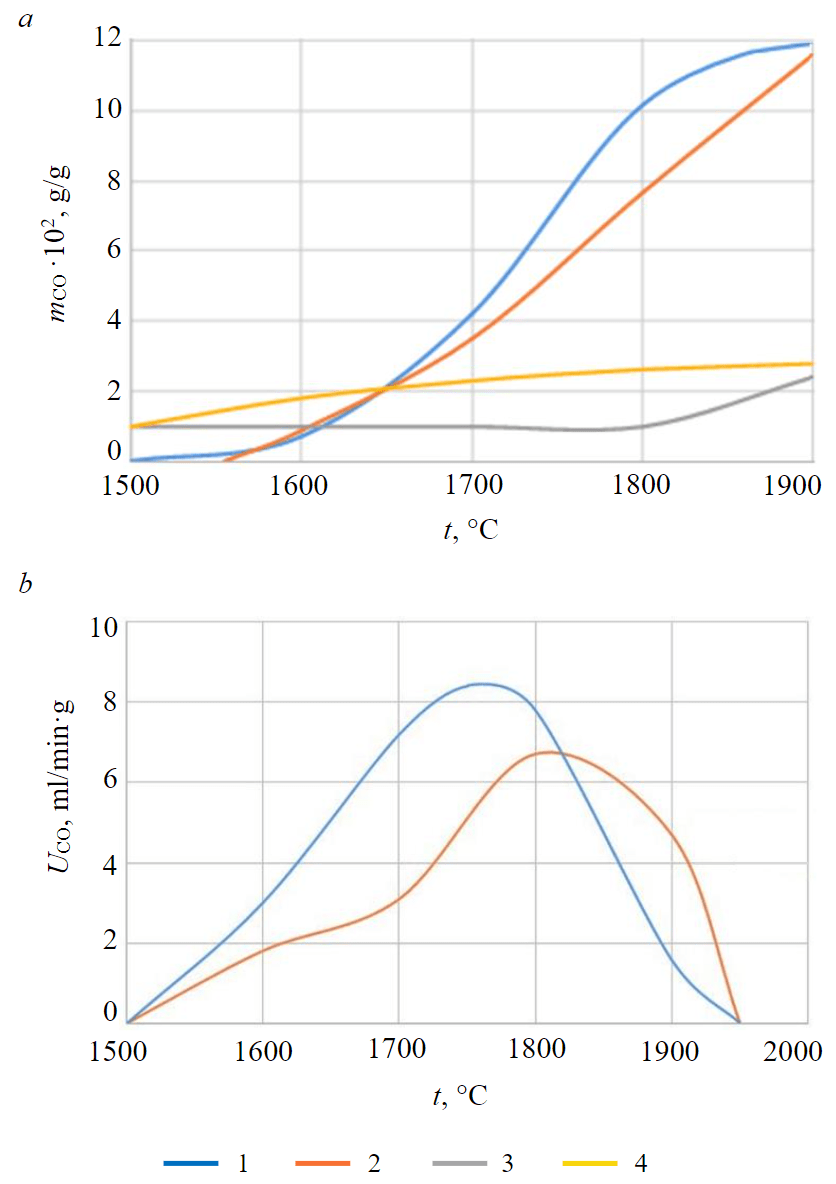
Fig.2. The dependences of the amount of carbon monoxide, evolved by reactions (1), (2), (4) and (5) (a) and gas release rate for reaction (1) and (2) (b) on temperature at a heating rate of kyanite charge 20 °C/min 1 – reaction (2); 2 – reaction (1); 3 – reaction (4); 4 – reaction (5)
The results of calculations are shown in Fig.2, as well as in Table 2. The flow of reactions in the temperature range 1400-1900 °С according to the analysis of waste gases was not recorded.
The most expedient way to carry out kinetic studies of the reactions (1) and (2) in conditions of polythermal heating (prompt-burst plasma heating) is to apply the generalized Kolmogorov – Erofeev topokinetic equation [8]:
where k and n are constants and Erofeev, respectively, and the rate constant can be calculated by the ratio
Results and discussion
Since the reduction occurs in a narrower temperature range at a relatively high temperature, the most preferable option is to set heating temperature Ts so that at
The graphs a = f (T) and υa = f (T) were plotted based on the obtained kinetic dependencies for the reaction (1) and (2) and defined as, Ts и υas. The calculated kinetic parameters n, E и K0 prove that the reaction is valid and the production of metallic charge (hypereutectic aluminum silicon alloy) is possible.
Table 2
The results of the reduction of the kyanite sample at the constant heating rate of 20 °C/min
Final temperature, °С |
Sample mass, g |
СО, g |
Chemical analysis of residues, % |
|||||
Before test |
After test |
SiO2gen |
Al2O3gen |
Al2O3sol |
SiC |
C |
||
1100 |
– |
– |
– |
25.92 |
42.32 |
– |
– |
28.62 |
1500 |
8.85 |
8.69 |
0.185 |
25.98 |
41.81 |
1.56 |
– |
28.46 |
1600 |
8.93 |
8.60 |
0.305 |
26.29 |
45.42 |
1.34 |
– |
28.08 |
1700 |
9.05 |
8.11 |
0.861 |
38.73 |
48.2 |
0.77 |
5.33 |
24.83 |
1800 |
8.87 |
6.96 |
1.737 |
30.37 |
53.50 |
1.30 |
1.87 |
21.04 |
1900 |
8.49 |
6.29 |
2.081 |
31.28 |
58.33 |
0.56 |
17.3 |
18.33 |
By substituting the expression for K0, we obtain the equation and the dependence shown in Fig.3:
The equation (7) is the equation of anamorphosis of the kinetic curve modified for conditions of linear polythermal heating by controlled plasma arc. Therefore, the graph of the dependence ln[–ln(1 – a)] depends on θ or Т, and results in the linear relationship based on the equation θ = Т – Тs with the slope of
Thus, the linear form of the kinetic anamorphoses (Fig.3) indicates the possibility of describing the reaction rate in considered heating conditions and in a narrower temperature range by the modified Kolmogorov – Erofeev equation. This has a positive effect on the overall energy consumption of the unit – there is the most efficient use of the heat received, both in terms of process time and in absolute values of energy consumption.
The obtained mathematical model provides data for development of an algorithm for controlling the technological process of reduction of kyanite concentrate to a metallized state in the set temperature range for the complete cycle of the reaction ex-change and creates prerequisites for the justification and development of the modern energy efficient technology.
It is possible to create a universal thermal unit using the obtained dependencies and considering the thermodynamics of the processes and current technological level in order to optimize the process of carbothermal reduction of the charge to a metallized state (alloy).
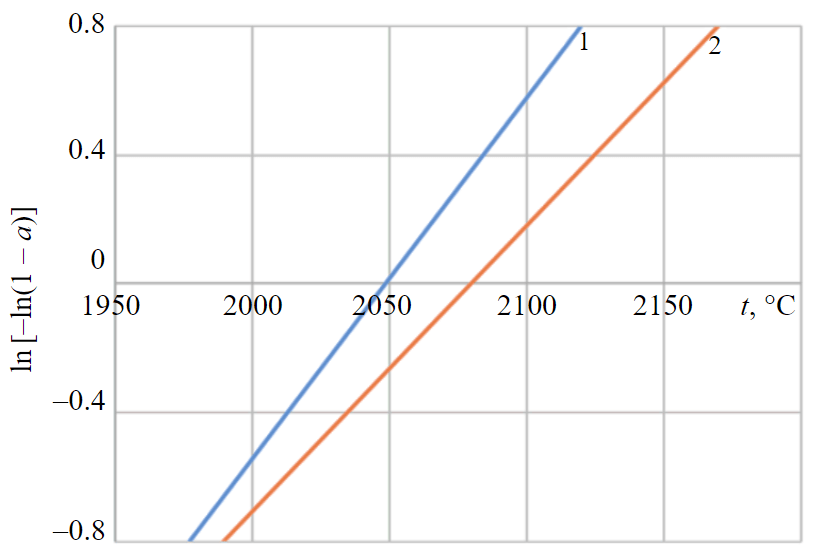
Fig.3. The anamorphoses of the kinetic curves for reactions (1) and (2) and heating rate 1 – reaction (2); 2 – reaction (1)
Description of the reaction rate using the modified Kolmogorov – Erofeev equation has an in-depth character of increasing the efficiency of aluminum silicon alloys production. General technical and economic comparative characteristics with the existing methods of aluminum silicon alloy production are not mentioned, since there is no need to produce aluminum and silicon separately. It enables to decrease considerably energy consumption for aluminum silicon alloy production, operating costs, and capital expenses. The advantages of the method of direct processing of silicon-aluminum ores for aluminum silicon alloy production are the following:
- combining energy-intensive aluminum and silicon production in a single smelter and the ability to process raw materials with high Al and Si content (up to 60-70 % in total), in particular, kyanite;
- in comparison with industrial electrolysis cells, orethermal or plasma furnaces are characterized by a substantially higher specific capacity, low capital and operating costs, and high environmental friendliness.
Conclusion
The non-isothermal method was used for the reduction of kyanite charge in the ore-thermal furnace, which is based on a constant rate of charge heating, i.e. with a linear relationship between time and temperature, which greatly saves electrical energy.
The expediency of using kyanite raw materials for energy-saving production of aluminum- and silicon-based alloys and aluminum silicon alloy has been substantiated.
The research on the kinetics and interaction mechanism in the Si-Al-O-C system was carried out on a high-temperature installation with a graphite heater in conditions of controlled plasma flow with symmetrical heating, focused on stabilization and energy losses reduction. A sample with the molar ratio of SiO2:Al2O3 = 0.73 was used in the experiments. The carbon content in the sample was 90 % of the amount theoretically required for the reduction of the mineral oxide to metal. The sample consisted of kyanite ore subjected to electromagnetic separation and a complex reduction agent. The reduction was carried out at heating rates of 10, 20, and 40 °C/min in the temperature range from 1100 to 2200 °C. Calculations and obtained dependencies indicate a favorable operating mode of the furnace at the temperature of 1450 to 1650 °C.
The non-isothermal method was used for the reduction of kyanite charge.
The linear type of kinetic anamorphosis testifies to the possibility of describing the reduction reaction rate in the process of carbothermic reduction of aluminosilicon ore required for energy-saving technological melting regimes. This makes it possible to reduce specific power consumption for reduction smelting of kyanite ore by 15-20 % as compared to the existing indicators for ore-thermal furnaces. The solution of this problem is especially important for increasing the energy efficiency of the production of basic aluminum alloys.
A promising direction for the development of the aluminum industry is the use of plasma flow in the carbothermic reduction of pre-enriched kyanite concentrate. A large volume of kyanite deposits in the Murmansk region, the existing infrastructure, and an excess of cheap electric power create favorable logistics for organizing large-scale production of aluminum alloys.
A positive factor is the presence of the Kandalaksha aluminum smelter (United Company “RUSAL”), the only aluminum smelter in the world producing primary aluminum, located beyond the Arctic Circle, which, unlike the productions of the Western division, has maintained the full production volumes.
The development of technologies for deep, environmentally safe, and energy-efficient processing of kyanite ore in high-tech melting plants and furnaces is of great scientific and technical interest. These technologies ensure a high degree of aluminum silicon alloys extraction and obtaining multi-purpose commercial products, which will increase the competitiveness of the aluminum industry.
References
- Litvinenko V.S., Tsvetkov P.S., Molodtsov K.V. The social and market mechanism of sustainable development of public companies in the mineral resource sector. Eurasian Mining. 2020. N 1, p. 36-41. DOI: 10.17580/em.2020.01.07
- Litvinenko V., Bowbrick I., Naumov I., Zaitseva Z. Global guidelines and requirements for professional competencies of natural resource extraction engineers: Implications for ESG principles and sustainable development goals. Journal of Cleaner Production. 2022. Vol. 338. N 130530. DOI: 10.1016/j.jclepro.2022.130530
- Litvinenko V.S., Petrov E.I., Vasilevskaya D.V. et al. Assessment of the role of the state in the management of mineral Journal of Mining Institute. 2023. Vol. 259, p. 95-111. DOI: 10.31897/PMI.2022.100
- Yurak V.V., Dushin A.V., Mochalova L.A. Vs sustainable development: scenarios for the future. Journal of Mining Institute. Vol. 242, p. 242-247. DOI: 10.31897/PMI.2020.2.242
- Shklyarskiy Ya.E., Shklyarskiy A.Ya., Zamyatin Е.О. Analysis of distortion-related electric power losses in aluminum industry. Tsvetnye metally. N 4, p. 84-91 (in Russian). DOI: 10.17580/tsm.2019.04.11
- Timonina V.I. Energy conservation and efficiency as indicators for achieving energy security in the country. Teoreticheskaya ekonomika. 2022. N 1, p. 111-119 (in Russian). DOI: 10.52957/22213260_2022_1_111
- Turysheva A.V., Gulkov Y.V., Krivenko A.V. Improving energy performance of the oil and gas industry by applying technologies for the use of associated petroleum gas. Topical Issues of Rational Use of Natural Resources. CRC Press, 2019. Vol. 1, p. 442-447. DOI: 10.1201/9781003014577-56
- Kopteva A., Kalimullin L., Tcvetkov P., Soares A. Prospects and Obstacles for Green Hydrogen Production in Russia. Energies. 2021. Vol. 14. Iss. 3. N 718. DOI: 10.3390/en14030718
- Cherepovitsyn A., Solovyova V. Prospects for the Development of the Russian Rare-Earth Metal Industry in View of the Global Energy Transition – A Review. Energies. 2022. Vol. 15. Iss. 1. N 387. DOI: 10.3390/en15010387
- Zhukovskiy Yu.L., Kovalchuk M.S., Batueva D.E., Senchilo N.D. Development of an Algorithm for Regulating the Load Schedule of Educational Institutions Based on the Forecast of Electric Consumption within the Framework of Application of the Demand Response. Sustainability. 2021. Vol. 13. Iss. 24. N 13801. DOI: 10.3390/su132413801
- Catalán-Vázquez M., Riojas-Rodríguez H., Cortez-Lugo M. et al. Social representations of mining activity after an environmental improvement program in the manganese district of Molango, in Mexico, and their implications for risk management. Journal of Environmental Planning and Management. 2019. Vol. 62. Iss. 10, p. 1714-1735. DOI: 10.1080/09640568.2018.1512475
- Abramkin S.E., Shisterov G.A., Dushin S.E. et al. The problems of complex algorithms development for gas industy objects. Automation, telemechanization and communication in oil industry. N 5 (550), p. 27-32 (in Russian). DOI: 10.33285/0132-2222-2019-5(550)-27-32
- Zinovieva O.M., Kolesnikova L.A., Merkulova A.M., Smirnova N.A. Environmental risk management at mining enterprises. Ugol'. N 3, p. 76-80 (in Russian). DOI: 10.18796/0041-5790-2022-3-76-80
- Zgheib H. Concept of environmental risk management in the system of sustainable environmental economics. Proceedings of BSTU. Iss. 5. Economics and Management. N 2, p. 111-115.
- Litvinenko V.S. Technological Progress Having Impact on Coal Demand Growth. XVIII International Coal Preparation Congress, 28 June – 01 July 2016, Saint-Petersburg, Russia. Cham: Springer, 2016, p. 3-16. DOI: 10.1007/978-3-319-40943-6_1
- Abramkin S.E., Dushin S.E., Ilyushin Yu.V. et al. Automation and control of technological processes: status and prospects. Problems of Training of Specialists. Pyatigorsk: Izd-vo Pyatigorskogo instituta (filiala) Severo-Kavkazskogo federalnogo universiteta, 2019, p. 140 (in Russian).
- Iakovleva E., Guerra D., Tcvetkov P., Shklyarskiy Ya. Technical and Economic Analysis of Modernization of Solar Power Plant: A Case Study from the Republic of Cuba. Sustainability. 2022. Vol. 14. Iss. 2. N 822. DOI: 10.3390/su14020822
- Shklyarskiy Ya.E., Batueva D.E. Operation mode selection algorithm development of a wind-diesel power plant supply complex. Journal of Mining Institute. Vol. 253, p. 115-126. DOI: 10.31897/PMI.2022.7
- Pyagay I.N., Kremcheev E.A., Pasechnik L.A., Yatsenko S.P. Carbonization processing of bauxite residue as an alternative rare metal recovery process. Tsvetnye metally. N 10, p. 56-63 (in Russian). DOI: 10.17580/tsm.2020.10.08
- Shklyarskiy Y., Skamyin A., Vladimirov I., Gazizov F. Distortion Load Identification Based on the Application of Compensating Devices. Energies. 2020. Vol. 13. Iss. 6. N 1430. DOI:3390/en13061430
- Boduen A.Ya., Petrov G.V., Kobylyansky A.A., Bulaev A.G. Sulfide leaching of high-grade arsenic copper concentrates. Obogashchenie rud. N 1, p. 14-19 (in Russian). DOI: 10.17580/or.2022.01.03
- Sizyakov V.M., Kononenko E.S., Snegurova A.I. Intensification of carbon aluminates technology of superdeep desilication on the basis of the catalytic properties of the hydro granate sludge. Journal of Mining Institute. Vol. 202, p. 27-30 (in Russian).
- Shepelev I.I., Sakhachev A.Yu., Zhyzhaev A.M. et al. Extraction of valuable components from alumosilicate natural and technogenic materials under alumina production by sintering. Proceedings of Irkutsk State Technical University. Vol. 22. N 4, p. 203-214 (in Russian). DOI: 10.21285/1814-3520-2018-4-202-214
- Dubovikov O.A., Yaskelyainen E.E. Processing of low-quality bauxite feedstock by thermochemistry-Bayer method. Journal of Mining Institute. Vol. 221, p. 668-674. DOI: 10.18454/PMI.2016.5.668
- Pasechnik L.A., Medyankina I.S., Yatsenko S.P. Scandium extraction from multicomponent systems by crystallization of complex sulfates. IOP Conference Series: Materials Science and Engineering. 2020. Vol. 848. N 012064. DOI: 10.1088/1757-899x/848/1/012064
- Koteleva N.I., Zhukovskiy Y.L., Valnev V. Augmented reality technology as a tool to improve the efficiency of maintenance and analytics of the operation of electromechanical equipment. Journal of Physics: Conference Series. 2021. Vol. 1753. N 012058. DOI: 10.1088/1742-6596/1753/1/012058
- Mann V., Buzunov V., Frantsev Y. et al. The Development of RUSAL’s Prebake Anode Production in Support of the Company’s Green Initiatives. Light Metals 2022. Cham: Springer, 2022, p. 890-900. DOI: 10.1007/978-3-030-92529-1_117
- Brough D., Jouhara H. The aluminium industry: A review on state-of-the-art technologies, environmental impacts and possibilities for waste heat recovery. International Journal of Thermofluids. 2020. Vol. 1-2. N 100007. DOI: 10.1016/j.ijft.2019.100007
- Farjana S.H., Huda N., Parvez Mahmud M.A. Impacts of aluminum production: A cradle to gate investigation using life-cycle assessment. Science of the Total Environment. 2019. Vol. 663, p. 958-970. DOI: 1016/j.scitotenv.2019.01.400
- Nemchinova N.V., Mineev G.G., Tyutrin A.A., Yakovleva A.A. Utilization of Dust from Silicon Production. Steel in Translation. 2017. 47. Iss. 12, p. 763-767. DOI: 10.3103/S0967091217120087
- Kuzmin M.P., Ivanov N.A., Kondratev V.V. et al. Preparation of aluminum-carbon nanotubes composite material by hot pressing. Metallurgist. 2018. Vol. 61. N 9-10, p. 815-821. DOI: 10.1007/s11015-018-0569-2
- Romanov A.D., Romanova E.A., Vilkov I.V. et al. Technology for Producing Aluminum-Matrix Composite Material Reinforced with Multi-Wall Carbon Nanotubes. Metallurgist. 2022. Vol. 66, p. 681-687. DOI: 10.1007/s11015-022-01376-1
- Evans K. The History, Challenges, and New Developments in the Management and Use of Bauxite Residue. Journal of Sustainable Metallurgy. 2016. Vol. 2, p. 316-331. DOI: 1007/s40831-016-0060-x
- Akcil A., Akhmadiyeva N., Abdulvaliyev R. et al. Overview On Extraction and Separation of Rare Earth Elements from Red Mud: Focus on Scandium. Mineral Processing and Extractive Metallurgy Review. 2018. Vol. 39. Iss. 3, p. 145-151. DOI: 1080/08827508.2017.1288116
- Voytyuk I.N., Pantyushin I.V. Automated Measurement of Oil-gas-water Mixture Component Composition in Pipeline. 3rd International Conference on Control Systems, Mathematical Modeling, Automation and Energy Efficiency (SUMMA), 10-12 November 2021, Lipetsk, Russian Federation. IEEE, 2021, p. 935-939. DOI: 10.1109/SUMMA53307.2021.9632165
- Grishin N.N., Ivanova A.G., Neradovskii Yu.N., Kalinnikov V.T. Integrated recovery of kyanite ore from the Keivskoye deposit. Tekhnologiya metallov. 2013. N 7, p. 3-9 (in Russian).
- Salama E.I., Abbas A., Esawi A.M.K. Preparation and properties of dual-matrix carbon nanotube-reinforced aluminum composites. Composites Part A: Applied Science and Manufacturing. 2017. Vol. 99, p. 84-93. DOI: 10.1016/j.compositesa.2017.04.002
- Kuskov V.B., Lvov V.V., Yushina T.I. Increasing the recovery ratio of iron ores in the course of preparation and processing. CIS Iron and Steel Review. 2021. Vol. 21, p. 4-8. DOI: 10.17580/cisisr.2021.01.01
- Qing-chun Yu, Hai-bin Yuan, Fu-long Zhu et al. Carbothermic reduction of alumina with carbon in vacuum. Journal of Central South University. 2012. Vol. 19. Iss. 7, p. 1813-1816. DOI: 10.1007/s11771-012-1213-0
- Baisong Guo, Xinming Zhang, Xi Cen et al. Enhanced mechanical properties of aluminum based composites reinforced by chemically oxidized carbon nanotubes. Carbon. 2018. Vol. 139, p. 459-471. DOI: 10.1016/j.carbon.2018.07.026
- Khairul M.A., Zanganeh J., Moghtaderi B. The composition, recycling and utilisation of Bayer red mud. Resources, Conservation and Recycling. 2019. Vol. 141, p. 483-498. DOI: 10.1016/J.RESCONREC.2018.11.006
- Vozniakovskii A.A., Kidalov S.V., Koltsova T.S. Development of composite material aluminum-carbon nanotubes with high hardness and controlled thermal conductivity. Journal of Composite Materials. 2019. Vol. 53. Iss. 21, p. 2959-2965. DOI: 10.1177/0021998319829894
- Choate W., Green J. Technoeconomic Assessment of the Carbothermic Reduction Process for Aluminum Production. Essential Readings in Light Metals. Cham: Springer, 2016, p. 1070-1075. DOI: 10.1007/978-3-319-48156-2_156
- Qingchun Yu, Yong Deng, Yuebin Feng, Ziyong Li. Phase Transformation of Alumina, Silica and Iron Oxide during Carbothermic Reduction of Fly Ash for Ceramics Production. Metals. 2021. Vol. 11. Iss. 8. N 1165. DOI: 10.3390/met11081165
- Litvinova T., Kashurin R., Lutskiy D. Complex Formation of Rare-Earth Elements in Carbonate-Alkaline Media. 2023. Vol.16. Iss.8. N 3140. DOI: 10.3390/ma16083140
- Bazhin V.Yu., Masko O.N., Martynov S.A. Automatic burden balance monitoring and control in the production of metallurgical silicon. Tsvetnye metally. 2023. N 4, p. 53-59. DOI: 10.17580/tsm.2023.04.07