Intelligent monitoring of the condition of hydrocarbon pipeline transport facilities using neural network technologies
- 1 — Ph.D., Dr.Sci. Associate Professor Tyumen Industrial University ▪ Orcid ▪ Elibrary ▪ Scopus
- 2 — Ph.D. Associate Professor Tyumen Industrial University ▪ Orcid ▪ Elibrary ▪ Scopus
- 3 — Ph.D., Dr.Sci. Professor Tyumen Industrial University ▪ Orcid ▪ Elibrary ▪ Scopus ▪ ResearcherID
Abstract
The national strategic goal of the Russian Federation is to ensure the safety of critical technologies and sectors, which are important for the development of the country's oil and gas industry. The article deals with development of national technology for intelligent monitoring of the condition of industrial facilities for transport and storage of oil and gas. The concept of modern monitoring and safety control system is developed focusing on a comprehensive engineering control using integrated automated control systems to ensure the intelligent methodological support for import-substituting technologies. A set of approved algorithms for monitoring and control of the processes and condition of engineering systems is proposed using modular control robotic complexes. Original intelligent models were developed for safety monitoring and classification of technogenic events and conditions. As an example, algorithms for monitoring the intelligent safety criterion for the facilities and processes of pipeline transport of hydrocarbons are presented. The research considers the requirements of federal laws and the needs of the industry.
Introduction
Relevance of the task of digitalization, intellectualization of key industries and development of modern technologies for controlling the processes and facilities is mentioned in the latest research papers [1-3] and a number of federal documents: the national program “Digital Eco-nomy of the RF” (approved by the Presidium of the Council under the President of the RF for Strategic Development and National Projects, Protocol N 7 dated 04.06.2019), Strategy for the Development of the Information Society in the Russian Federation for 2017-2030 (Decree of the President of the RF N 203 dated 09.05.2017), National Strategy for the Development of Artificial Intelligence for the Period until 2030 (Decree of the President of the RF N 490 dated 10.10.2019), Resolution of the Government of the RF “On conducting an experiment on the implementation of a remote control system for industrial safety” (dated 31.12. 2020 N 2415) and other documents on safety and ecology, industry programs [4, 5].
The Department of Hydrocarbon Resources Transportation of the Tyumen Industrial University proposed an essentially new concept of the system of intelligent neural network engineering control, forecasting, and preventing technogenic events, emergencies, incidents, accidents and optimizing engineering solutions in control of the technological processes of hazardous production facilities (HPF) of pipeline transport of oil and gas [6-8]. The strategic goal of creating such a system is to ensure the effective control of pipeline transport facilities as one of the most important sectors of national industry which, in turn, will require the solution of serious and significant tasks related to the deve-lopment of methodology, a set of procedures and algorithms, and software implementation. In addition, in the conditions of modern economy, the problem of import substitution is pressing. In global practice, there are some developments dealing with resolving the certain problems when constructing models with an intelligent component: to assess the reliability of petroleum products supply [6, 7]; identification of defects in the assessment of the engineering condition [8, 9]; evaluation of the dynamics of corrosion processes [9-11]; predicting the hydraulic characteristics of flows [12-14], hydraulic machines [15] as well as the design position of structures [16-18]. However, a single concept of integrated intelligent safety control in oil and gas industry is not presented or is shown fragmentarily [19].
Many Russian research papers [20-22] deal with the problems of creating systems for monitoring the reliability and safety of hydrocarbon transport processes by the main pipelines, but the question of providing an operational automated predictive monitoring of technogenic events and conditions during oil and gas transport is still open. To consider various security threats and factors reducing the reliability in the system of main oil and gas pipelines, a rather wide range of diagnostic monitoring tools is used and developed [23-25] including those for real-time operation [24-26] as well as models for predicting the mode parameters, leaks, and losses [27-29]. In papers [30-32] the scientific problems of an intelligent assessment of the parameters of hydrocarbon transport systems are resolved; however, the models known in the industry are not applicable for monitoring the condition and universal solution of safety control problems.
According to the official reports of Rostekhnadzor, in recent years, there occurred a steady decrease in the accident rate at the facilities of the main transport and storage of oil and gas (Fig.1); however, incidents occur, and accidents can reach the scale of a national catastrophe (diesel fuel spill near Norilsk on May 29, 2020). This points to the necessity not only to monitor the background risks [20], but also to create the systems of automated predictive monitoring with functions of control and prevention of technogenic events and their development based on modern models consi-dering all the threats. The development and application of a universal intelligent approach in combination with available scientific developments for solving the tasks, and its systemic application in control [33-35] makes it possible to create a system for managing the condition of facilities of the new generation.
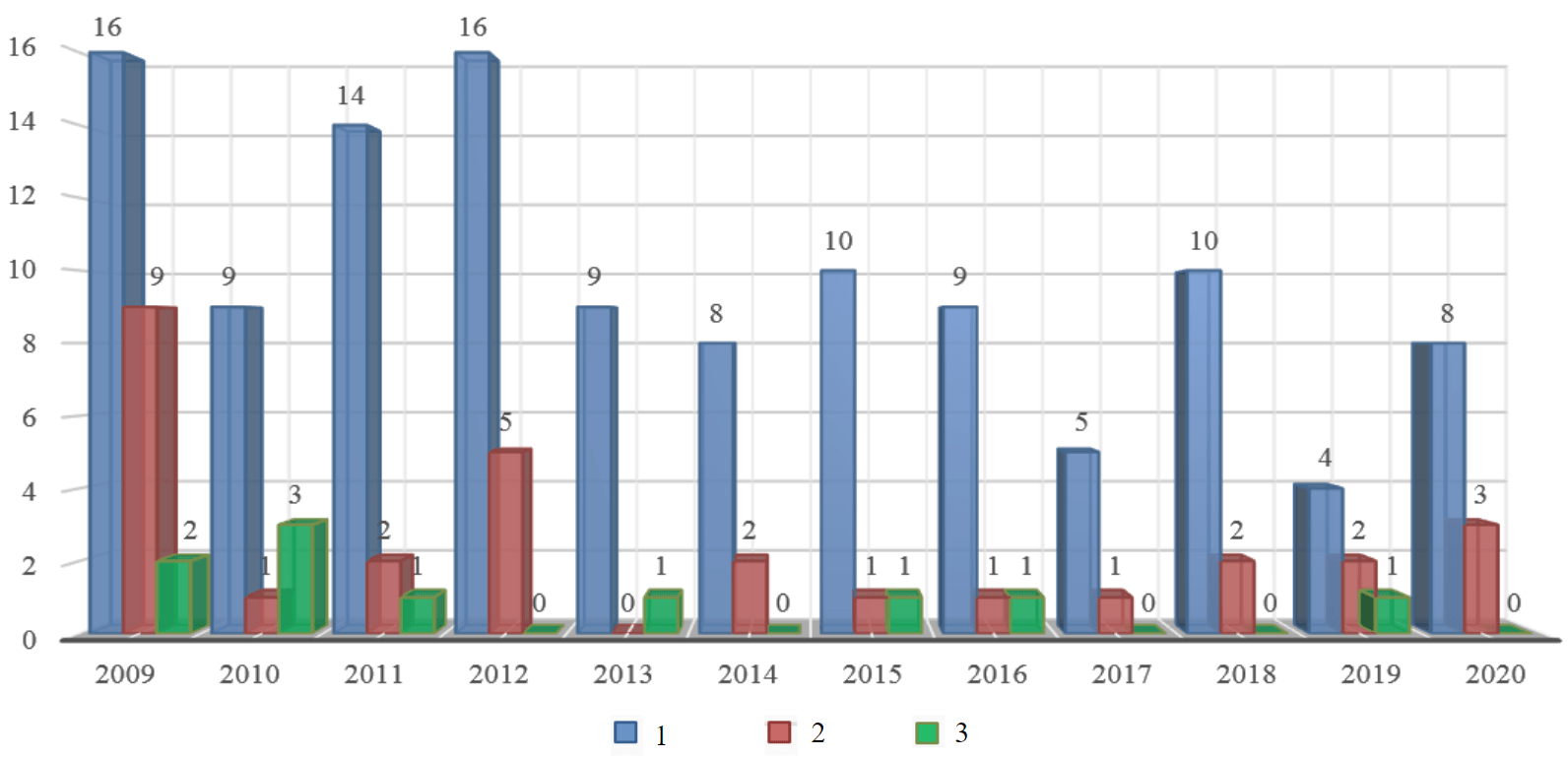
Fig.1. Dynamics of accidents at the facilities of the main pipeline transport 1 – gas pipelines; 2 – oil pipelines; 3 – oil product pipelines
Despite a new wave of scientific interest to neural networks due to increasing power of compu-ters and modelling tools, overgrown bases of neural network architectures for various purposes, certain experience in implementing when solving the problems of controlling the efficiency and safety [31, 32] of gas and oil pipeline trunk facilities, the task of creating universal systems for predictive monitoring of the safety of condition and processes is currently of high priority.
Methods
The developed system is original and aimed at ensuring independence from foreign suppliers and information safety of control technologies. The article considers some features of the author's methodological support for the development of predictive intelligent safety monitoring systems. The task of real-time monitoring is different in that it is necessary to consider regular updates of regulatory documentation at the federal level, which is still focused on assessing the safety taking into account the up-to-date information on reliability and ensuring the efficiency of the processes. The methodological approach implies the use of the scientific base available in the industry and developed over generations using neural network technologies. The criterial approach is applied, and a set of criteria is proposed reflecting the properties of oil and gas pipeline facilities as a technical object. Thus, for example, when ensuring safety, not only the criteria specific to complex sets of engineering and technical structures are taken into account, but also the internal and external threats, reliability, efficiency of the technological processes, factors of interaction with technogenic, anthropogenic and natural environments.
A systematic analysis of the requirements of current regulatory and technical documentation and the results of scientific developments in the field of reliability, safety, and the practice of monitoring oil and gas pipelines showed that in production they are limited to assessing the performance, technical condition, and residual life. The tasks of assessing and monitoring safety are reduced to decla-ring, and reliability assessment – to calculating point estimates of indicators and fixing them for a certain period.
Thus, to create a universal control system, but specialized in accordance with properties of the facilities, a base of point control models and real-time models is required. Despite the availability of large databases at enterprises, each module of the control system should be clearly structured and provided with a methodological basis for processing the data flow, for example, on oil and gas transport modes, operating modes of process equipment, engineering status, energy consumption, labour costs, repairs accomplished, and resources expended, volumes of spare parts and materials, quality of work, service life, etc. The tasks of predicting the condition of hazardous production faci-lities and their subsystems are very difficult from the physicotechnical point of view but can be partially solved using the intelligent approach.
To solve the problems of controlling the intelligent methods, the authors developed a universal methodology by creating neural network models for monitoring the safety of oil and gas pipeline transport facilities (Fig.2). The advantage of the procedure is that depending on the tasks set at the first stage, an individual solution algorithm can be formed. The methodology for creating a model provides for eight main stages, at each of which a scientific decision is taken supported by the technological features of the production processes, facilities, a systemic approach to the goal and tasks of monitoring, mathematical methods of solution and the potential of neural networks.
At the first stage, the key task of monitoring is set. Thus, for example, the classification of technogenic events (according to Safety Guide N 29 approved by the Order of Rostekhnadzor dated 24.01.2018) corresponds to paragraph 1.2 (Fig.2), and the task of predictive monitoring corresponds to paragraph 1.4. When setting the mathematical models, taking into account the capabilities of the diagnostic base, an optimal neural network model is formed with hyperparameters, type of learning, and, thus, an individual trajectory is developed that allows solving the problem. Let us consider an example of implementing neural network models for classifying the technogenic events and predicting the intelligent safety criterion.
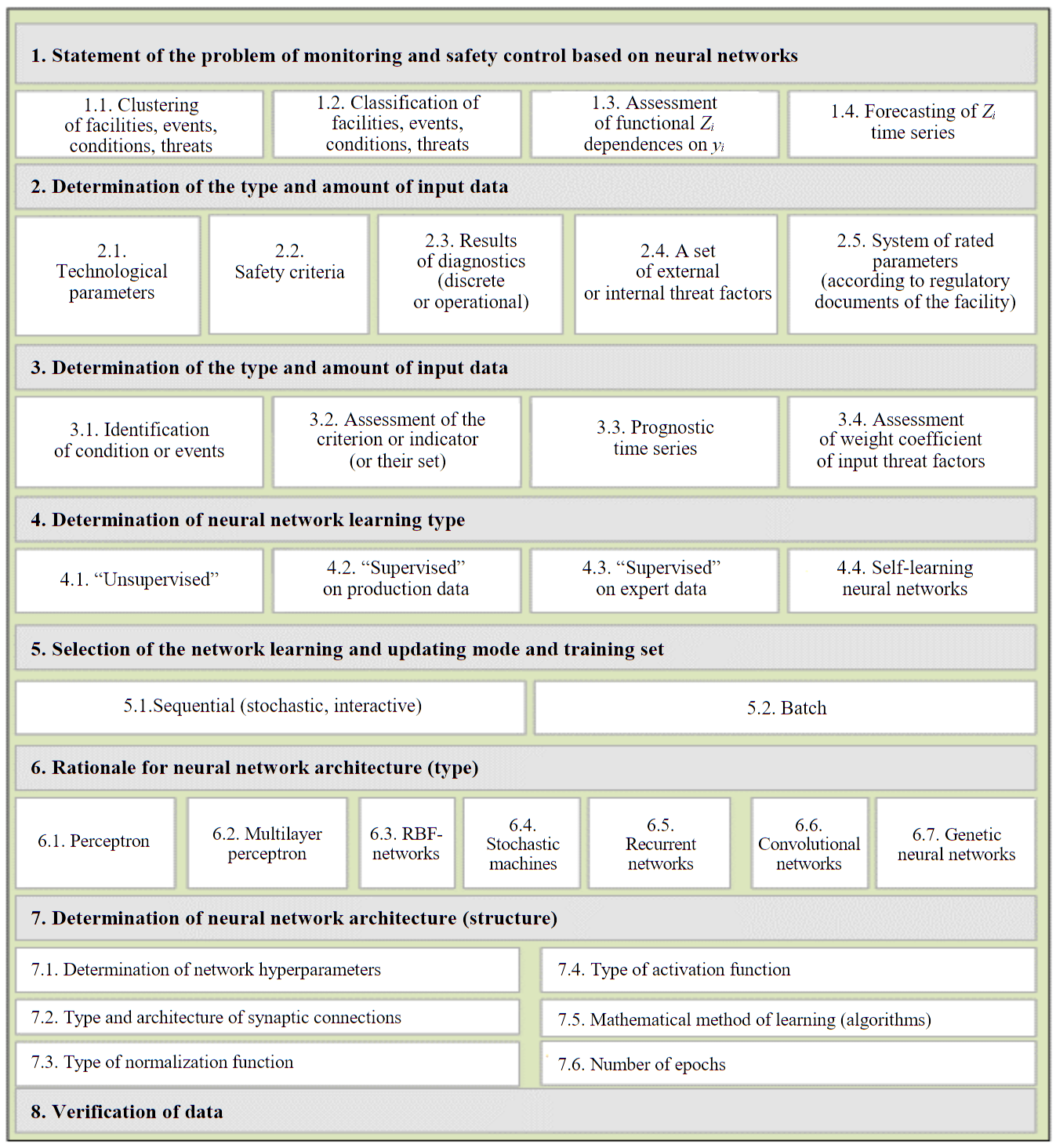
Fig.2. Algorithm for implementing the methodology for creating a neural network model for the facility safety monitoring system (Zi – safety indicator; yi – parameter scanned by the monitoring system)
Currently, risk assessment is applied according to the system of indicators. The criterial approach proposed by Professor N.A.Makhutov [1, 4] is particularly relevant for the development of real-time monitoring systems. Based on the criterial approach, the authors of the article proposed to introduce the concept of a complex intelligent safety criterion
where Ksv1, Ksv2, … Ksvm are safety criteria according to the system of signs and by groups established by federal laws (mechanical (FZ N 384), informational (FZ N 149), fire (FZ N 123), ecolo-gical (FZ N 7), national (FZ N 390) etc.); vi – type of safety; i – serial number, i ∈ [1; m].
Functional dependence for assessing the intelligent safety criterion (upper-level criterion) will have the following form:
where OUTt(Ksv1, Ksv2, … Ksvm) is output signal of a neural network of arbitrary architecture for facility t.
Safety criterion of the next hierarchical level is determined by the set of input safety criteria of the input level or characteristics of the facility (process)
where Zvi1, Zvi2, Zvi3, … Zvin are basic level safety criteria (estimated by the parameters of processes and systems scanned by diagnostic and dispatching systems).
Boundary conditions for applying the safety assessment model
initial conditions are determined by the maximum value at the start of operation Kis0= 1, at the time of launching the monitoring system at an arbitrary point in time (actual value):
When classifying the technogenic events (for example, into five groups (according to Safety Guide N 29 approved by the Order of Rostekhnadzor dated 24.01.2018), the condition should be met at which:
where Е1+, Е2+, Е3+, Е4+ are a set of conditions each of which is a group of technogenic events of hazard level 1, 2, 3, 4; Е5+ – condition of safe operation in the absence of deviations and threats.
We set the threshold values Kis4, Kis3, Kis2, Kis2 for the subsequent intelligent evaluation of the weight coefficients of factors or significance coefficients of synaptic connections for subsequent intelligent calculation of threshold values.
To initiate a neural network according to the mathematical and technical basis [36], a heuristic analysis of the situation should first be performed. The analysis of possibilities of diagnostic apparatus determines the number of sensors – the number of neurons in the input layer, the number of scanned properties – the number of hidden layers. Thus, for instance, when monitoring the modes the number of sensors will be identical to that of scanned process parameters; when assessing the technical status – to the number of characteristics evaluated during diagnostics; when evaluating the resource – to the number of scanned parameters of the corrosion process, the stress-strain state and degradation factors, technical condition of the line part of the pipeline – based on the results of diagnostics with regard for the thickness measurement, profiling, defect characteristics, etc. As a result, from the systemic point of view, a certain set of source data corresponds to a certain conclusion which the neural network should identify, and which can be expressed as an integrated assessment or condition.
To assess the dynamics, the authors introduced the concept of the coefficient of change in the safety criterion during operation
where Ks.pr is a complex safety criterion of a facility with design properties; Ks.ac – a complex safety criterion of a facility with actual properties in the operating mode; Ks.pr = Ks.ac = 1 is design value for a new facility; С ∈ (0;1] Ks.ac ∈ (0;1] – area of functions definition.
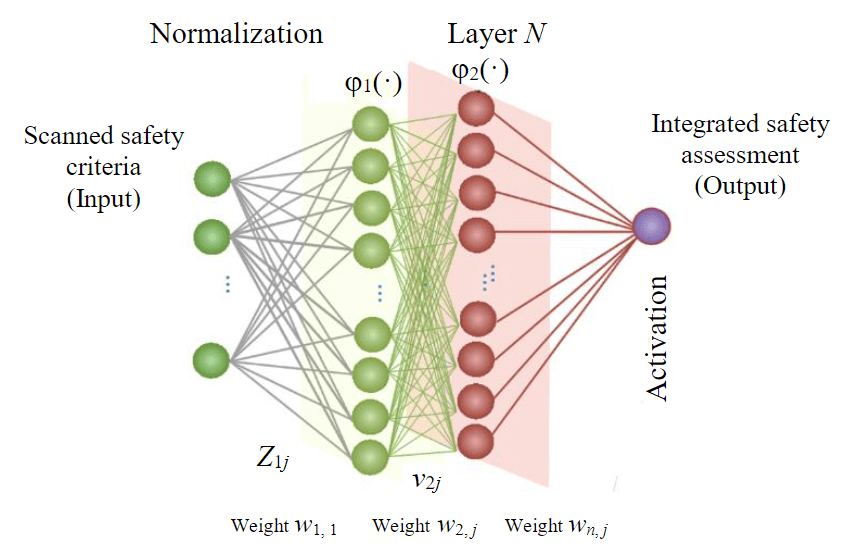
Fig.3. Universal scheme of a neural network for integrated assessment with regard for the relevance of input criteria
Thus, the regulated risk approach can be synchronized and supplemented with an intelligent approach considering various properties of the facility. For example, according to the authors, to consider the actual technical condition and reliability of oil and gas pipelines, it is advisable to calculate risk indicators taking into account the intelligent criterion of mechanical safety
where Zm1, Zm2, Zm3, …Zmn are zero-level mechanical safety criteria at a specific industrial facility (each of the criteria should reflect actual change in technical condition of the facility in relation to the design one; when substantiating compliance – to the normative one).
For a comprehensive assessment of the safety of hydrocarbon transport modes (or any operation), the safety criterion for the technological process is proposed according to the function (Fig.3) depending on the system of variables:
where Zr1, Zr2, Zr3, …Zrn are safety criteria of basic zero level (obtained on the basis of measured and formalized parameters of processes and systems).
Let us consider, as an example, how the models can be implemented to assess the safety of the technological process at an oil pumping station. The developed algorithms and models can be applied in an arbitrary programming environment that provides algorithms for the operation of neural networks or the mathematical apparatus of machine learning. Let us consider some features of implementation and verification of models for assessing safety and identifying conditions in the Matlab environment.
Control sample of the identification network contained a data bank of over 1,000 examples scanned during dispatching control and control of technological modes of oil transport using the example of the main pumping station in various loading options. The neural network was trained on a retrospective sample on the dynamics of a set of parameters corresponding to technogenic events 1, 2, 3, 4 and normal operation in condition 5 according to the current classification of technogenic events for hazardous production facilities. The structure of the training sample reflected actual operating conditions, when the facility is in normal operation mode most of the time, i.e., in condition 5; and at initial deviations from the optimal parameters of the processes – in condition 4. Sample size of being in condition 3, 2, 1 is identified from the emergency parameters of equipment. There were no accidents or incidents during the operation process in accordance with safety requirements; threshold values of identifiers were set by expertise based on a retrospective analysis of events and requirements of regulatory documents on the operation oil pumping station facilities.
To assess the condition of the system and identify technogenic events in terms of hazard level, an intelligent model was initiated based on a multilayer perceptron of direct propagation with the number of neurons equal to (and a multiple of) the number of sensors on the input neuron layer, namely, the number of scanned mode parameters. Thus, at the input, a data flow for nine neurons was obtained equal to the dimension of the input matrix. The input data matrix contained zero-level safety criteria based on parameters of the technological process of pipeline transport of hydrocarbons, at the output there were five conditions according to the hazard level of technogenic events, the architecture is a two-layer perceptron (Fig.4, a). It should be noted that a two-layer perceptron is the optimal basic architecture that allows to provide the speci-fied identification accuracy. In some cases, it is necessary and reasonable to complicate the model, increase the number of layers and neurons in a layer; however, there is a risk of retraining error characteristic of neural networks; an analysis of learning indicators is required to ensure maximum convergence and minimum error. For the illustrated mo-dels, optimization of network hyperparameters was accomplished, and the most appropriate architectures were shown. Thus, the neural network model was tested in the Matlab programming environment using the Levenberg – Marquardt gradient optimization method [36]. It was ascertained that when modelling threshold values it is necessary to establish critical values and rules at which the values of coefficients will corres-pond to the threshold ones. According to the authors, two methods of accepting threshold values are reasonable – normalization and calculation by the neural network.
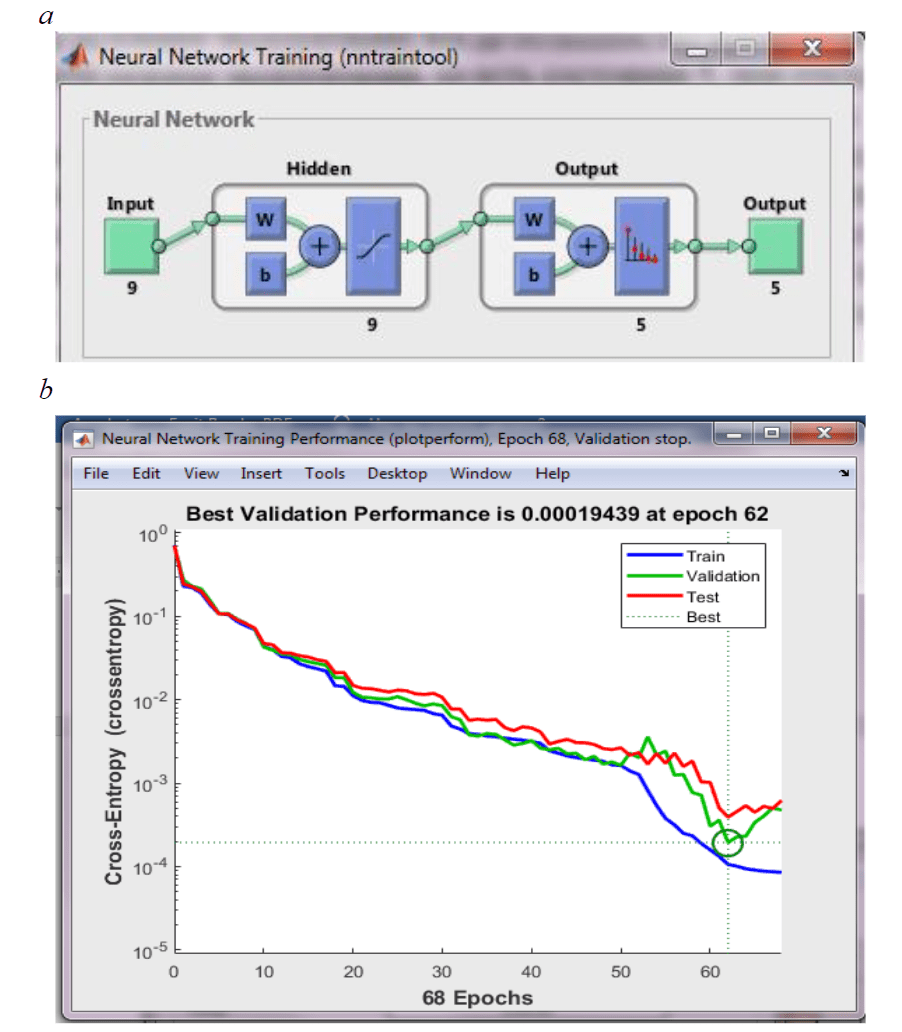
Fig.4. An example of neural network operation for identifying conditions: a – architecture of a neural network with nine hidden neurons and two hidden layers in the Matlab environment; b – optimization of learning indicators – validation
It is known from the production practice that the same deviation of certain mode parameters from optimal or normative parameters in different combinations can be both safe and fatal. It is for such cases that complete production experience, expert assessments, model samples should be considered when forming the database. Databases updated by the batch or sequential procedure should consider all possible cases that can lead to an incident, accident, catastrophe and, of course, predict such events at an early stage. Thus, a neural network fully trained on actual and normative data identifies the input condition of the system in real time mode according to the set of input data placing a unit in the position in the matrix corresponding to the technogenic condition of a certain hazard level. Extraction of synaptic connections in a fully connected neural network can be performed for any layer of the network.
Results
The results of optimizing the neural network model for the sample showed the convergence of the neural network at epoch 68 with a learning rate of 0.711 and a starting gradient of 0.602. From the validation curve graph (Fig.4, b) it is seen that the minimum value of cross-entropy is achieved at the number of epochs – 62; subsequent increase in the number of epochs can lead to an overfitting error, thus, the training parameters are optimized: cross-entropy and classification error are minimized. Thus, the network error percentage is minimized (equal to zero) (Fig.5), i.e., there are no classification errors. The shapes of the ROC (Receiver Operator Characteristic) identification truth curves testify to the high accuracy of the model (Fig.5), the classifier errors are minimal. Identification errors in this model can occur when examples of conditions unknown to the intelligent system appear in the data flow. In case of a high-quality formation of the training sample taking into account the preliminary systemic multivariate analysis of the engineering system, possible scenarios for the development of technogenic events as well as timely batch or sequential updates, identification errors are practically eliminated.
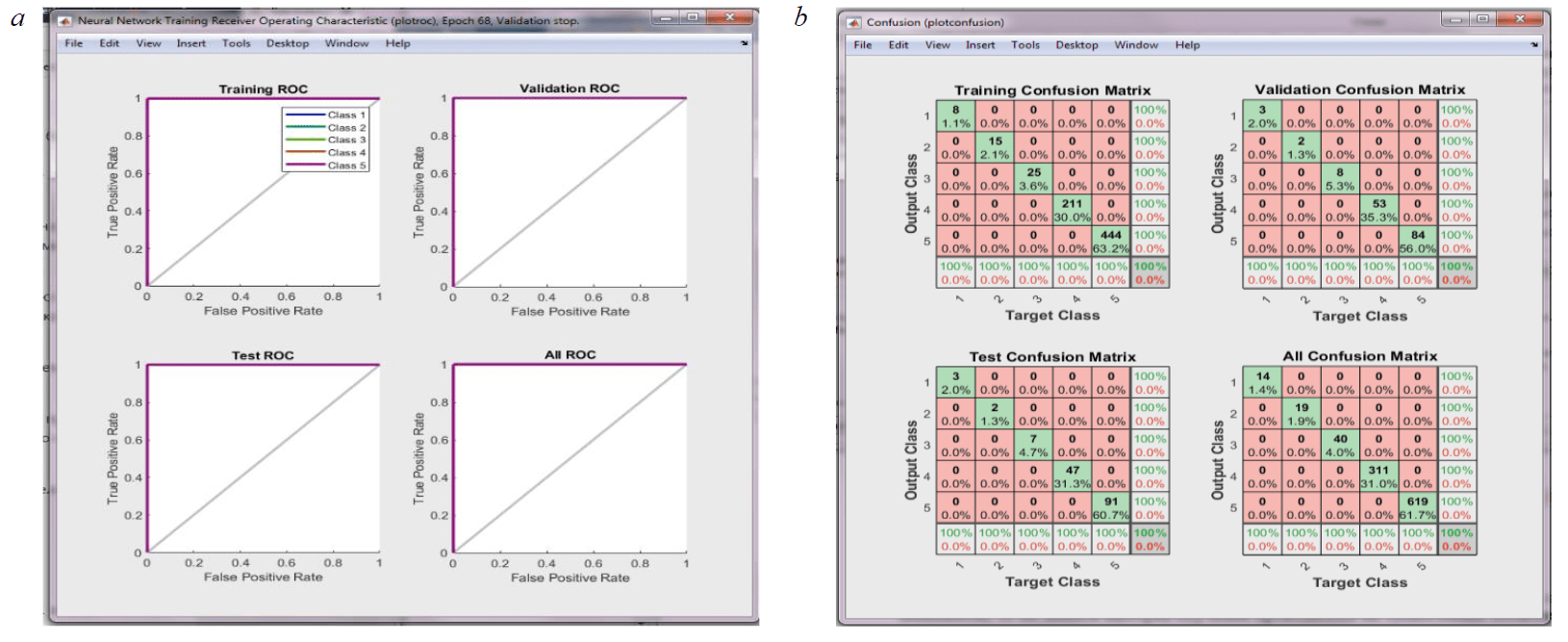
Fig.5. Training results of the identification neural network: a – identification truth lines; b – classifier errors (red squares)
Let us consider an example of another possible function of neural network analysis which is necessary for both comparing the safety level, and for making decisions and ranking the facilities. For a comprehensive safety assessment, a neural network was initiated for the model with one computed output. For an intelligent comprehensive assessment of the safety criterion, the architecture of a multilayer perceptron with the number of sensors equal to the number of scanned parameters and threat factors was adopted. To train the model, the number of input parameters was taken equal to nine features (indicators of the facility operation mode), in the layer – two. Network convergence for this model was achieved at epoch 158 with a training rate of 2.0 and gradient 4.29, high regression coefficient (0.999), no validation errors, with rms learning error 2.98·10–11, testing error 1.29·10–2 and learning error 2.98·10–11, which is a high indicator.
Let us consider the following function, which is of particular importance for the prediction of parameters, condition and prevention of undesirable events, emergencies, incidents, and accidents. To solve these problems, a neural network for forecasting the time series and conditions of oil and gas pipelines based on a recurrent neural network of the NARX architecture (non-linear autoregressive with exogenous inputs model) was scientifically substantiated and initiated.
The constructed real-time forecasting model based on the time series is a recurrent neural network with one input and an offset. The specific feature of this model is that the signal vector applied to the sensor layer of the multilayer perceptron is the data of the input signal of arbitrary origin charac-terizing the condition of the system and of the output signal of the function at previous points in time. In such models, for minimizing the error and ensuring convergence of the series, the number of layers and their dimension increase in comparison with classification and approximation networks. When substantiating the structure, with increasing number of layers, a decrease in prediction errors occurs. A specific feature of the NARX architecture is a possibility of supplying an auxi-liary series both with a lag and with reinforcement (additional information for forecasting). Neural networks with reinforcement are of particular importance for solving the tasks of ensuring monitoring of the efficiency of technological processes taking into account not only the structure of transport flows, but also their economic and technological gainings and losses, which is particularly important for creating the optimal paths on decision graphs for process control, maintenance, repair of technological equipment, line part.
As an example, let us consider the results of training a neural network to predict the time series of the process safety criterion in arbitrary non-stationary operation modes of the liquid hydrocarbon transport system (the abscissa shows the hours from the start of monitoring and formation of the training sample). As can be seen from the graph (Fig.6), with a smooth change in indicators, the model prediction accuracy is correlationally significant: high regression coefficients, low values of autocorrelation error 6∙10–5. The histogram of errors is maximum at an error modulus of 0.003-0.005.
The analysis of technological processes and dispatching operations shows that at stationary processes, the accuracy of forecasting is extremely high, and response deviation values are maximum at points of mode change due to deterministic interference in the operation of the system or the human factor, which cannot be predicted. From the physicotechnical point of view, the neural network remembers the behaviour of the system as a whole in various situations and based on the dynamics of a set of parameters, predicts the following possible scenarios for the development of the event forecasting the hazard level. The architecture of the expert system provides that the safety manager sees not only the target graph but can also analyse the behaviour of subsystems (Fig.7).
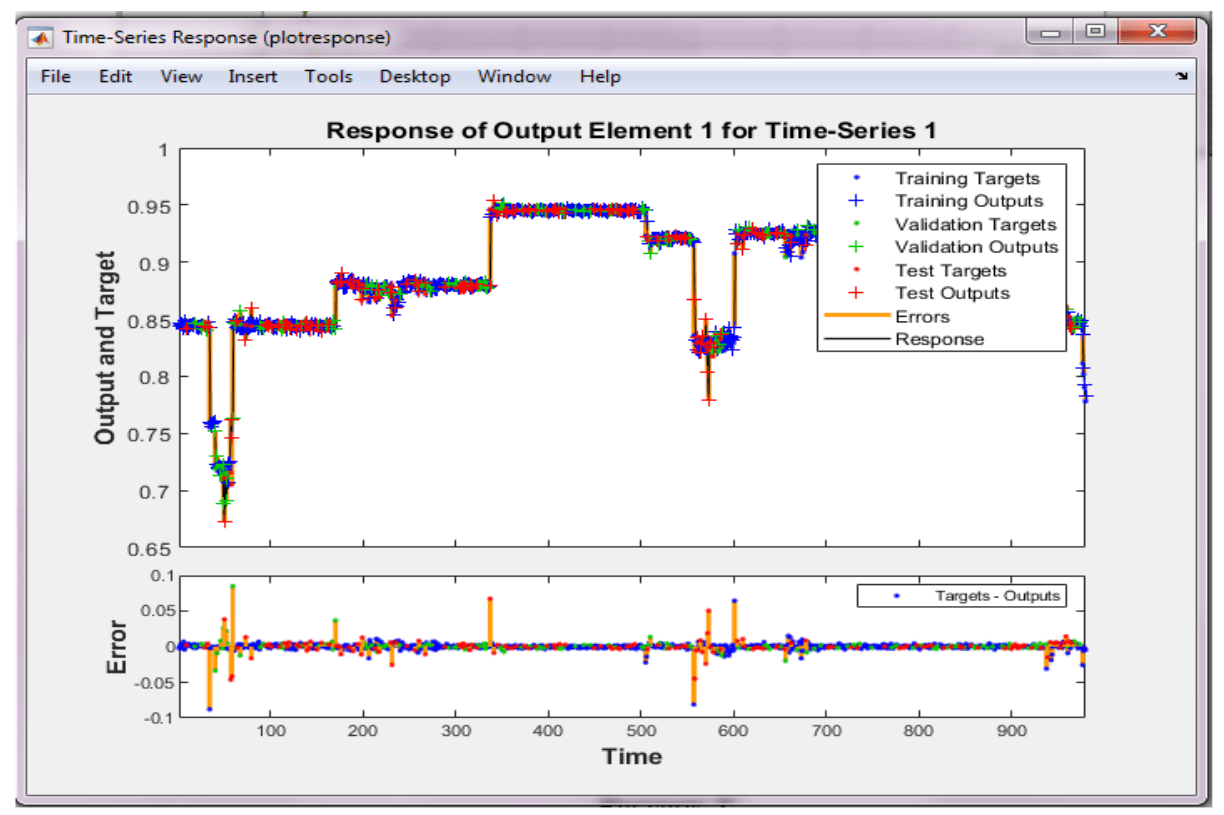
Fig.6. Neural network response and response error in time series forecasting

Fig.7. An example of graphic presentation of a fragment of predicting the process safety criterion by a recurrent neural network 1 – neural network forecast; 2 – actual series
Thus, it is possible to predict the values of safety parameters for a set of parameters for a certain time period in advance. Such forecasts will, undoubtedly, help the operational dispatch personnel in taking decisions, especially under emergency. Practice shows that it is advisable not only to consider and convey the experience of skilled operational dispatch personnel, but also to use it for robotization, digitalization and development of decision support systems in specialized modular expert systems. The author's neural network assessment model allows performing the intelligent predictive online monitoring based on the system of criteria.
Discussion of results
It was ascertained that neural networks can be used with a high degree of efficiency to predict the technogenic events and process parameters. The architecture, hyperparameters of the neural network depend on the character of the investigated process, the volume and quality of training samples, and functional connections within the technical system. With appropriate setting of the model and programming, the training results of the models are characterized by high regression coefficients (0.99), low mean square learning error (10–4-10–3), low classification (0 %) and validation ((5-8)∙10–3) errors. It is advisable to use the original intelligent models for predicting safety criteria for pipeline transport processes using recurrent neural networks in real time mode taking into account the flow of incoming information. The analysis of the results of the work indicates that when creating each intelligent analytical system, to ensure the accuracy of forecasting, the conditions for forming a sample, rationale for the neural network architecture for each problem solved taking into account the individual properties of systems and processes are important.
It is shown that the developed approach makes it possible to implement at least three functions: safety assessment, prediction of estimates and parameters, identification of current and future conditions. The intelligent system allows identifying the condition of the facility based on actual and predictive data estimating the predicted time of occurrence of the technogenic event taking into account the incoming threats, degradation factors and diagnostic results that make up the sensor layer of the neural network on any time scale.
Conclusion
The authors have developed a set of multifactorial models for identification, prediction, and classification of technogenic events constructed on a systemic neural network analysis of the data flow of sensory neurons of multilayer direct propagation perceptrons with learning.
The results of model testing at station facilities and line parts of the main hydrocarbon transport make it possible to perform intelligent monitoring of technogenic events promptly in real time mode. It is possible to implement and optimize the decision on the maintenance strategy based on the actual condition at a high technological level, and most importantly, to identify and prevent emergencies, incidents, and accidents of any scale without delay. Implementation of the author's methodological approach in construction of modular systems for controlling the condition of oil and gas transportation facilities makes it possible to increase the efficiency and validity of decision-making on safety control of production processes with maximum efficiency.
References
- Makhutov N.A., Cherepanov A.P., Lisanov M.V. Tasks of the development and implementation of enterprise industrial safety management system when operating technical devices. Occupational Safety in Industry. 2021. N 2, p. 15-19 (in Russian). DOI: 10.24000/0409-2961-2021-2-15-19
- Lisin I.Yu., Korolenok A.M., Kolotilov Yu.V. System approach to the formation of integrated energy systems on the platform of intelligent information technology solutions. Neftyanoye khozyaystvo. 2020. N 3, p. 36-40 (in Russian). DOI: 10.24887/0028-2448-2020-3-36-40
- Revazov A.M., Lezhnev M.A. The impact of accidents at the facilities of pipeline transport of oil and petroleum products on the environment. Environmental protection in oil and gas complex. 2021. N 6 (303), p. 12-17 (in Russian). DOI: 10.33285/2411-7013-2021-6(303)-12-17
- Makhutov N.A., Gadenin M.M., Ivanov V.I. Scientific and methodological base for technical diagnostics of potentially ha-zardous production facilities. Occupational Safety in Industry. 2021. N 6, p. 7-14 (in Russian). DOI: 10.24000/0409-2961-2021-6-7-14
- Lisanov M.V., Sumskoy S.I., Shvyryayev A.A. Uncertainties of the quantitative emergency risk assessment at oil-gas facilities. Vesti gazovoy nauki. 2018. N 2 (64), p.125-134 (in Russian).
- Huai Su, Jinjun Zhang, Enrico Zio et al. An integrated systemic method for supply reliability assessment of natural gas pipeline networks. Applied Energy. 2018. Vol. 209, p. 489-501. DOI: 10.1016/j.apenergy.2017.10.108
- Qian Chen, Lili Zuo, Changchun Wu et al. Short-term supply reliability assessment of a gas pipeline system under demand variations. Reliability Engineering & System Safety. 2020. Vol. 202. N 107004. DOI: 10.1016/j.ress.2020.107004
- Wan Yong,Wang Yongzhi, Yang Yong et al. Intelligent identification and classification methods of oil and gas pipeline defects by fluxgate magnetometry. Journal of Harbin Engineering University. 2021. Vol. 42. Iss. 9, p. 1321-1329. DOI: 10.11990/jheu.202005049
- Hayward N., Portugal M. Machine Learning Image Analysis for Asset Inspection. SPE Offshore Europe Conference and Exhibition, 3-6 September 2019, Aberdeen, UK. SPE-195773-MS. DOI: 10.2118/195773-MS
- Wasim M., Djukic M.B. External corrosion of oil and gas pipelines: A review of failure mechanisms and predictive preventions. Journal of Natural Gas Science and Engineering. 2022. Vol. 100. N 104467. DOI: 10.1016/j.jngse.2022.104467
- Stubelj I.R., Ruschmann H., Wold K., Gomnaes J.O. Pipeline Predictive Analitics Trough On-Line Remote Corrosion Monitoring. Corrosion 2019, 24-28 March 2019, Nashville, Tennessee, USA. N NACE-2019-12899.
- Brünenberg K., Vogt D., Ihring M. Additional Functionalities Of Model Based Leak Detection Systems To Improve Pipeline Safety And Efficiency. Pipeline Technology Journal. 2020. Iss. 1, p. 38-44.
- Ghorbani B., Ziabasharhagh M., Amidpour M. A hybrid artificial neural network and genetic algorithm for predicting viscosity of Iranian crude oils. Journal of Natural Gas Science and Engineering. 2014. Vol. 18, p. 312-323. DOI: 10.1016/j.jngse.2014.03.011
- Hankun Wang, Yunfei Xu, Bowen Shi et al. Optimization and intelligent control for operation parameters of multiphase mixture transportation pipeline in oilfield: A case study. Journal of Pipeline Science and Engineering. 2021. Vol. 1. Iss. 4, p. 367-378. DOI: 10.1016/j.jpse.2021.07.002
- Tao Zhang, Hua Bai, Shuyu Sun. Intelligent Natural Gas and Hydrogen Pipeline Dispatching Using the Coupled Thermodynamics-Informed Neural Network and Compressor Boolean Neural Network. Processes. 2022. Vol. 10. N 2. DOI: 10.3390/pr10020428
- Kraidi L., Shah R., Matipa W., Borthwick F. An investigation of mitigating the safety and security risks allied with oil and gas pipeline projects. Journal of Pipeline Science and Engineering. 2021. Vol. 1. Iss. 3, p. 349-359. DOI: 10.1016/j.jpse.2021.08.002
- 17. Li Xin, Bai Mingzhou, He Bohu et al. Safety analysis of landslide in pipeline area through field monitoring. Journal of Testing and Evaluation. 2022. Vol. 50. Iss. 6. DOI: 10.1520/JTE20200751
- Suzhen Li, Chen Wei, Xinghua Peng. Safety Monitoring of Buried Pipeline with Socket Joints Subjected to Ground Deformation Using MEMS Inclinometers. Journal of Pipeline Systems Engineering and Practice. 2019. Vol. 10. Iss. 2. N 04019008. DOI: 10.1061/(ASCE)PS.1949-1204.0000380
- Mohd Nazmi bin Mohd Ali Napiah, Hambali bin Chik. Revolutionising Pipeline Safety: Intelligent Weldment Inspection Decision Support System. Pipeline Technology Journal. 2019. Vol. 2, p. 38-42.
- Grazhdankin A.I., Pecherkin A.S., Samuseva E.A. et al. On the background levels of emergency hazards at hazardous production facilities. Occupational Safety in Industry. 2019. N 10, p. 50-56 (in Russian).
- Revazov A.M., Savushkina V.N. Improving methods of trunk pipelines anti-terrorist security. Proceedings of Gubkin University. 2019. N 4 (297), p. 127-137 (in Russian). DOI: 10.33285/2073-9028-2019-4(297)-127-137
- Belostotsky M.A., Kunlin Li, Korolenok A.M., Korolenok V.A. Formation of intelligent repair management system on the linear part of main oil pipelines. Science & Technologies: Oil and Oil Products Pipeline Transportation. 2022. Vol. 12. N 4, p. 368-375 (in Russian). DOI: 10.28999/2541-9595-2022-12-4-368-375
- Vasilyev G.G., Dzhalyabov A.A., Leonovich I.A. Deformation monitoring of oil and gas construction structures on permafrost soils. Science & Technologies: Oil and Oil Products Pipeline Transportation. 2020. N 5-6, p. 34-39 (in Russian). DOI: 10.24411/0131-4270-2020-6-34-39
- Rudianov G.V., Krapivsky E.I., Daniliev S.M. Evaluation of Signal Properties When Searching for Cavities in Soil Under Concrete Slabs by Radio Detection Stations of Subsurface Investigation. Journal of Mining Institute. 2018. Vol. 231, p. 245-253. DOI: 10.25515/PMI.2018.3.245
- Usmanov R.R., Chuchkalov M.V., Romanov I.A. et al. Practical aspects of using the mobile digital radiography systems. Gazovaya promyshlennost. 2022. N 8 (836), p. 66-74 (in Russian).
- Gorban N.N., Vasiliev G.G., Salnikov A.P., Shitov S.I. Development of a layout of scanner stations for ground-based laser scanning of tanks, taking into account the requirement; for the deviation in measurement results. Neftyanoye khozyaystvo. 2020. N 2, p. 74-78 (in Russian). DOI: 10.24887/0028-2448-2020-2-74-78
- Vasilyev G.G., Leonovich I.A., Levin S.N., Pisarevskiy V.M. Potential Risks of Oil Product Losses during Storage and Analysis of Ways for Reducing Them. Occupational Safety in Industry. 2020. N 5, p. 87-93 (in Russian). DOI: 10.24000/0409-2961-2020-5-87-93
- Lure M.V. Mathematical modelling of the processes of pipeline transport of oil, oil products and gas. Moscow: Neft i Gaz, 2003, p. 336 (in Russian).
- Nikolaev A.K., Fetisov V.G., Lykov Y.V. Application investigation of gas flotation metering during emergency leak at a segment of line pipe. Truboprovodnyy transport: teoriya i praktika. 2017. N 2 (60), p. 14-17 (in Russian).
- Alekperova S.T., Revazov A.M. Practical Application of Artificial Intelligence Technologies in Planning Measures to Ensure the Safety of Hydrocarbon Production and Transportation Facilities. Oil and Gas Territory. 2022. N 1-2, p. 40-44.
- Shammazov I.A. Determination of indicators of technical condition of gas compressor units using neural networks. Transport i khranenie nefteproduktov i uglevodorodnogo syrya. 2012. N 2, p. 34-37 (in Russian).
- Tokarev D.V. Development of the theory and methods of industrial safety control at hydrocarbon pipeline transport facilities: Avtoref. dis. … d-ra tekhn. nauk. Ufa: Institut problem transporta energoresursov, 2011, p. 46 (in Russian).
- Zemenkova M.Yu. Methods for reducing technological and environmental risks in transport and storage of hydrocarbons. Tyumen: Tyumenskii industrialnyi universitet, 2019, p. 397 (in Russian).
- Moiseev B.V., Zemenkov Yu.D., Chekardovskii M.N. et al. Aspects of reliability and diagnostics of oil-and-gas facilities. Tyumen: Tyumenskii industrialnyi universitet, 2019, p. 423 (in Russian).
- Zemenkova M.Yu. System analysis and technological monitoring of reliability and safety in transport and storage of hydrocarbons. Tyumen: Tyumenskii industrialnyi universitet, 2017, p. 252 (in Russian).
- Khaikin S. Neural networks. Moscow: Vilyams, 2018, p. 1104 (in Russian).