Study on the rheological properties of barite-free drilling mud with high density
Abstract
Improved drilling and reservoir penetration efficiency is directly related to the quality of the drilling mud used. The right choice of mud type and its components will preserve formation productivity, stability of the well walls and reduce the probability of other complications. Oil and gas operators use barite, less often siderite or hematite weighting agent as a weighting component in the composition of drilling muds for the conditions of increased pressure. But the use of these additives for the penetration of the productive formation leads to the reduction of filtration characteristics of the reservoir, as it is almost impossible to remove them from the pore channels. Therefore, barite-free drilling mud of increased density based on formic acid salts with the addition of carbonate weighting agent as an acid-soluble bridging agent is proposed. The results of experimental investigations on rheological parameters of barite-free solutions are given and the obtained data are analyzed. Based on the comparison of results it is recommended to use high-density drilling mud on the basis of formic acid salts (sodium and potassium formate) and with the addition of partially hydrolyzed polyacrylamide with molecular mass of 27 million.
Introduction
Well drilling and development of oil and gas fields often takes place under complicated mining, geological and climatic conditions. In addition to ensuring environmental safety in the area of drilling operations, the technical requirements on the choice of an optimal drilling mud must also be met: high temperature stability; required rheological and filtration characteristics for preserving the reservoir properties; effective inhibiting capacity; high transport ability (especially in inclined and horizontal wellbore sections); resistance to contamination; compatibility with formation fluids and recirculation capability.
Offshore wells are characterized by specific complications associated with the narrow allowable pressure window, defined by pore pressure and fracturing pressure gradient. This narrow window is usually the result of abnormally high pore pressure and/or low fracturing pressure due to rock layers being additionally pressurized by the seawater column, which requires a larger number of casing strings than wells of similar depth constructed onshore. Therefore, under such conditions, one of the key factors for drilling success is equivalent circulation density (ECD) management [1-3]. Factors influencing the final ECD value include: static density; rheological parameters of the fluid; well design and profile; drilling mode; drill pipes used and bottomhole assembly; bit type (number and cross-section of each hydraulic nozzle); temperature profile of the well; chemical composition of the mud [4-7].
If flushing fluids containing barite as a weighting agent are used, a thick filter cake will form on the wellbore wall. If circulation is stopped for a long period of time and the static shear stress (SSS) is not adequate, barite may be precipitated and, consequently, the backpressure in the wellbore decreases (increasing the probability of gas and water influx) [8-10].
High ECD of the circulating drilling mud weighted with barite can be a cause of fracturing, especially if there is a narrow operating window between pore and fracturing pressure. Inorganic and organic salts (chlorides, bromides, formates) are used as bases to create barite-free drilling mud with high density. Values of density for technological fluids based on salts may vary – density of potassium chloride brine is 1160 kg/m3, sodium chloride – 1200 kg/m3. With bromides density of 2500 kg/m3 can be achieved (for zinc bromide) and with sodium and potassium formate up to 1320 and 1590 kg/m3 respectively [11-13].
Zinc bromide based solutions can provide the highest density among other salts (up to 2520 kg/m3), but are more corrosive than chloride and formate based solutions and have disposal limitations [14-16]. Brine flushing fluids are a good alternative to clay solutions and solutions containing significant amounts of solids. The formulation usually consists of a base brine, a pH control additive, a structure former (usually a biopolymer), a filtrate reducer and a bridging agent. Such combination of reagents provides beneficial rheological and filtration characteristics. Salt solutions allow the creation of a drilling system with high density and low solids concentration, which minimizes damage to reservoir properties and leads to a reduction in plastic viscosity. Application of barite-free water-based drilling fluids ensures lower ECD in the well, which improves the drilling efficiency [11, 17].
Thus, the relevant trend in deepwater drilling is the development of water-based mud formulations, which should have not only high density, thermal stability, low corrosivity, but also optimal rheological properties. Modernization of the formulation should be based not only on reducing the concentration of solids in high-density mud, but also on finding a combination of polymeric reagents, providing pseudoplastic and transporting properties.
Rheology is the science of studying the deformation and flow of fluids, which is necessary for solving various theoretical and practical problems [18-20]. Rheological properties of drilling fluids influence almost all processes and indicators related to well construction, so they are among the most important [21-23].
Most drilling muds are non-Newtonian fluids [24-26]. Therefore, this study aims at investigating non-linear behavior of rheological parameters of the mud (how the rheological curve changes when polymers of different molecular mass are added to drilling mud) and the influence of component composition of high-density drilling mud on this change.
In the conditions of offshore fields, it is necessary to use environmentally friendly flushing systems [27-29]. For this reason, a formate-based drilling mud, characterized by high density without or low solid phase content, has been selected for the investigation. It will provide lower rheological parameters, EDC and pressure losses in the well compared to traditionally used hydrocarbon-based mud. This contributes to improved drilling efficiency*, especially in conditions of a narrow safe range of density [1, 30]**. The analysis of scientific literature proves that formate drilling systems are compatible with formation fluids, and it creates prerequisites for increasing mechanical penetration rate and decreasing near-bottomhole zone contamination due to low filtration index [31, 32]. Such solutions in combination with polymer reagents have good inhibiting ability in relation to unstable clay sediments [21, 33, 34].
The aim of the study is to determine the effect of the molecular mass of partially hydrolyzed polyacrylamide (PHPA) on the rheological properties of the developed formate drilling mud and substantiate its optimum composition, taking into account the non-linearity of the rheological parameters of the fluid.
Methodology
Rheological models of modern drilling muds
Drilling muds can be classified according to their rheological behaviour. Fluids whose viscosity remains constant as the shear rate changes are called Newtonian. But most drilling muds are non-Newtonian-their shear stress is not directly proportional to the shear rate.
The rheological parameters of drilling mud are used for [35, 36]: calculation of friction loss in the pipe or annular space; determination of ECD; determination of flow regime in annular space; evaluation of wellbore cleaning efficiency; determination of drilling cuttings sedimentation rate in vertical wells. The selection accuracy of drilling mud rheological model minimizes the errors of calculated technological parameters during oil and gas wells drilling. This is why the problem of optimal model selection is especially relevant. However, it should be taken into account that there is no rheological model that would give the necessary accuracy of approximation over the whole range of shear rate corresponding to circulation of drilling mud in the well [11, 37, 38].
A large number of rheological models (more than 30) are available to predict the rheological behaviour of modern drilling systems over a wide range of shear rate. The most commonly used by drilling fluid engineers are the following models: Newton, Bingham – Shvedov, Ostwald – de Waale (power law), Herschel – Bulkley (modified power law) and Schulman – Casson [20, 39, 40]. The equation of Bingham rheological model is as follows:
where σ – shear stress; σ0 – ultimate dynamic shear stress; ηpl – plastic viscosity;
The flow of these muds begins only after the tangential stress exceeds a threshold value, which is called the dynamic shear stress (DSS). For tangential stresses exceeding the threshold stress, the stress is proportional to the shear rate with a coefficient of proportionality called plastic viscosity [41, 42]. The common use of the Bingham – Shvedov model is justified by its simplicity, however, a significant drawback is that it describes the rectilinear part of the rheological curve, which does not allow predicting the actual behaviour of the fluid at low shear rates. Also the yield point is often overestimated by several times.
The power model is another widely used rheology model for shear-thinning drilling muds. The model uses a power relationship between shear stress and shear rate; hence, in logarithmic coordinates, the relationship is plotted as a straight line. The values of parameters n and K of this law can be determined from observations at any two values of velocity. The power law equation is as follows:
where K – consistency coefficient; n – non-linearity index.
The model can be applied to shear-thinning fluids (pseudoplastic) at n < 1, to Newtonian fluids at n = 0 or to shear-thickening fluids (dilatant) at n > 1. The more the index of degree n differs from the 1, the more the fluid differs from the Newtonian fluid.
The Herschel – Bulkley model is also widely used in the oil and gas industry to describe thinning or pseudoplastic solutions. This model is called a modified power law because it is a combination of the Bingham and power law models, i.e. the relationship between shear stress and shear rate is expressed as a power function, taking into account the ultimate dynamic shear stress that must
be exceeded for the fluid to begin to flow. The equation of the Herschel – Bulkley rheological model is:
The American Petroleum Institute (API) recommends predicting fluid behaviour using a modified power model (Herschel – Bulkley). One part predicts fluid behaviour at low shear rates and the other at high shear rates. Figure 1 shows a graphical representation of the described rheological models [39].
The object of the study is a basic ecologically clean, barite-free drilling mud with high density (1.45 g/cm3) based on formic acid salts (sodium and potassium formate) for drilling a directional well with a horizontal ending, located on the Arctic shelf of the Russian Federation. The composition of the base mud is shown in Table 1.
Table 1
Component composition of the formate-based solution
Component |
Concentration |
Functions |
Xanthan, g/l |
4 |
Structure former |
Starch, g/l |
12 |
Filtration reducer for normal and high temperature HTHP (high temperature and high pressure) |
HPAN, g/l |
4 |
Filtration reducer HT |
K2CO3 (potassium carbonate), g/l |
10 |
Buffer рН |
HCOONa (sodium formate (dry), g/l |
800 |
Mud base |
HCOOK (potassium formate (liquid), % |
30 |
Mud base, inhibitor |
CaCO3 MEX-CARB F, g/l |
50 |
Bridging agent |
CaCO3 MEX-CARB M, g/l |
20 |
Bridging agent |
CaCO3 MEX-CARB VF, g/l |
10 |
Bridging agent |
Complicated conditions are associated with a narrow safe drilling window in terms of mud density and the presence of unstable clay deposits in the geological section, causing problems with wellbore stability.
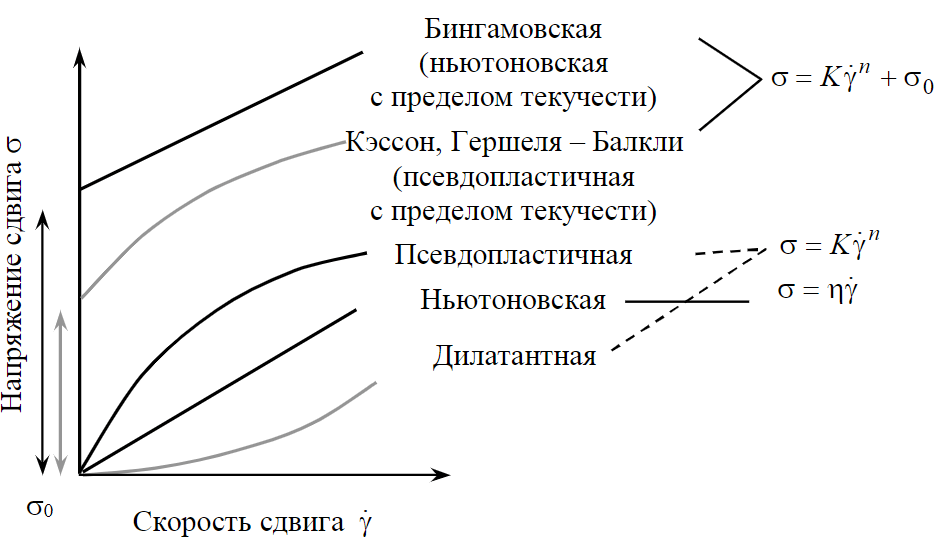
Fig.1 Flow curves of fluids obeying different flow models [39]
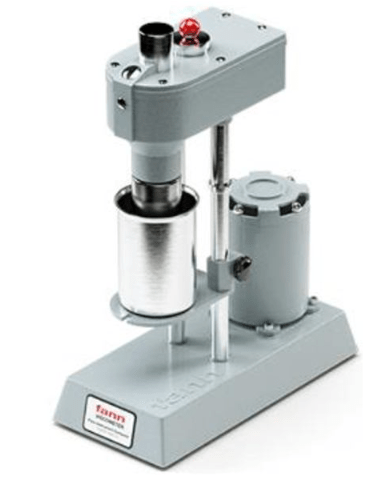
Fig.2. Rotational viscometer Fann
Experimental investigations were carried out by the authors of the article in laboratory of drilling fluids at Saint Petersburg Mining University. To establish a rheological flow model for various developed formulations, an experiment has been carried out on a Fann 35A six-speed viscometer (Fig.2), at rotor rotational speed of 3, 6, 100, 200, 300 and 600 rpm. The results have allowed to define the rheological parameters of studied solutions and to construct rheograms in Cartesian coordinates.
The plastic viscosity in centipoise is calculated as the difference between the Fann viscometer reading (θ) at 600 and 300 rpm:
where θ600, θ300 – values of the viscometer scale angles at rotor rotation speed, equal to 600 and 300 min–1 respectively, degrees.
The dynamic shear stress in lb/100 ft2 is calculated from Fann viscometer data using the formula [17, 43]:
where θ300 – device readings at 300 rpm.
According to API standard, Gel10 s/10 min (or SSS) system values are obtained on a rotary viscometer, at a speed of 3 rpm after 10 s and 10 min.
For further analysis it is necessary to convert the results obtained to a standard form: rpm converted to shear rate (s–1), shear stress converted from lb/100 ft2 to Pa. Viscometer speeds are standardized, therefore 3, 6, 100, 200, 300, 600 rpm in shear rate will be 5.1, 10.2, 170, 340, 511, 1021 s–1, respectively. The conversion coefficient to convert lb/100 ft2 to Pa is 0.48.
Discussion of the results
Partially Hydrolyzed Polyacrylamide (PHPA) of different molecular mass (12 000 000-27 000 000) has been proposed to improve the basic formulation as a substitute for hydrolyzed polyacrylonitrile (HPAN). The concentration of PHPA in each solution is 1 g/l. When increasing PHPA concentration up to 2 g/l, the Weissenberg effect was observed (the mud was coiled up on the stirring element), so it was decided to reduce the amount of PHPA. The main parameters of the developed drilling muds are presented in Table 2.
Table 2
Parameters of the investigated drilling muds
Solution |
Parameters |
|||||
Density, |
Conditional viscosity, s/quarter |
Plastic viscosity, |
DSS, |
SSS (10 s/10 min), lb/100 ft2 |
Filtration, ml/30 min |
|
1 (HPAN) |
1.45 |
47 |
19 |
11 |
5/8 |
3.6 |
2 (РНРА 12) |
1.45 |
40 |
16 |
11 |
5/8 |
3.0 |
3 (РНРА 15) |
1.45 |
41 |
16 |
14 |
5/8 |
2.6 |
4 (РНРА 20) |
1.45 |
43 |
16 |
17 |
5/8 |
2.4 |
5 (РНРА 27) |
1.45 |
44 |
16 |
20 |
5/8 |
2.1 |
The analysis of the results shows that by replacing HPAN with PHPA, it was possible to reduce the water loss of the mud, and with increasing molecular mass of partially hydrolyzed polyacrylamide, the filtration index decreases, which helps to reduce the probability of differential pipe sticking. This mud is also capable of forming a thin, impermeable filter cake (0.2 mm), which will prevent filtrate penetration into the formation. Increasing the molecular mass of the PHPA increases the DSS, but does not affect the value of plastic viscosity. Obtained values of SSS show that the structure of studied solutions is evident after 10 s of staying at rest and changes by 3 lb/100 ft2 after 10 min of staying at rest.
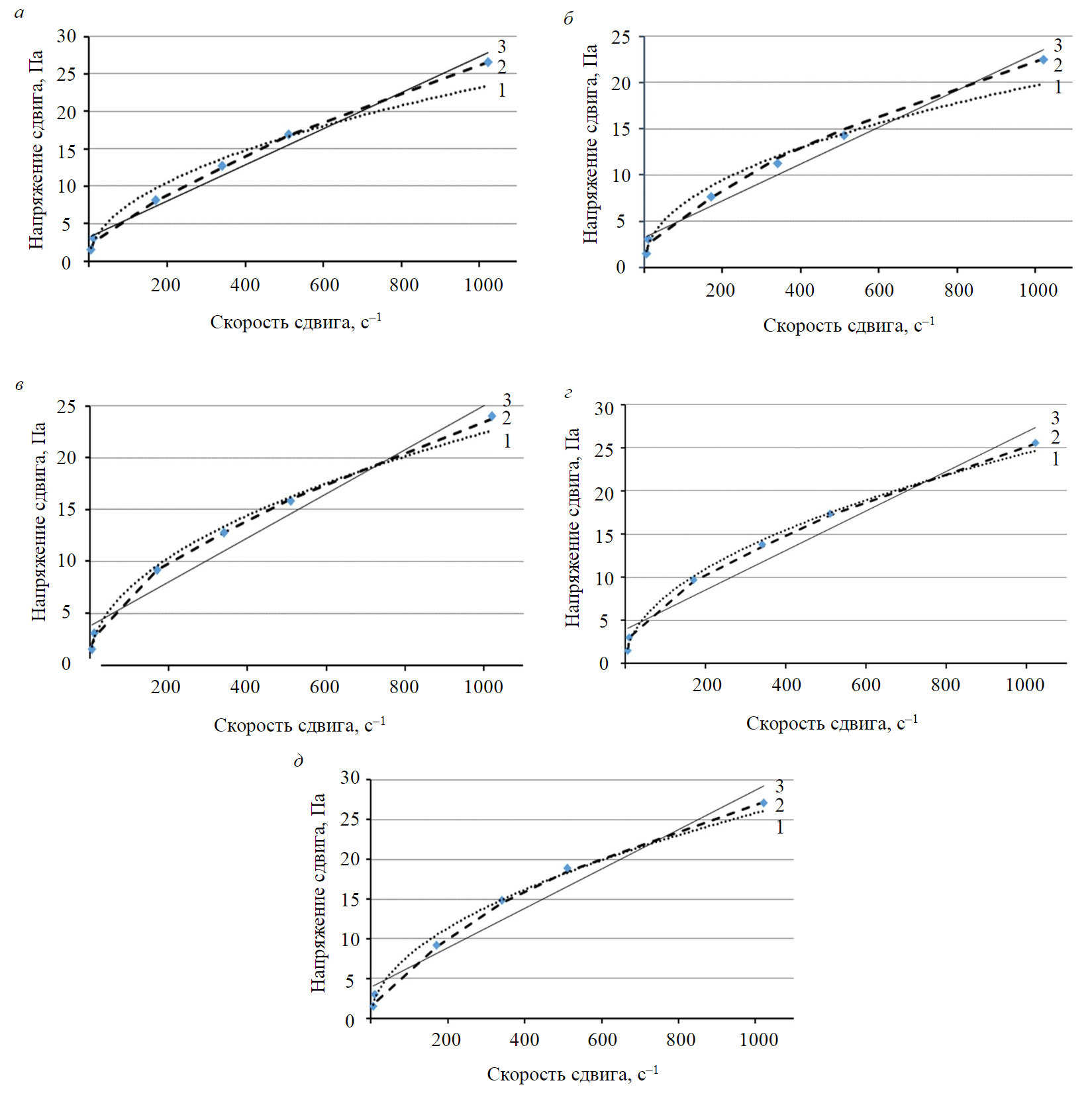
Fig.3. Selection of rheological models for solutions: а – 1; b – 2, ММ РНРА = 12 mln; c – 3, ММ РНРА = 15 mln; d – 4, ММ РНРА = 20 mln; e – 5, ММ РНРА = 27 mln Models: Ostwald – de Waale (1); Herschel – Bulkley (2); Bingham – Shvedov (3)
Selection of a rheological model for the drilling mud
Experimental data were analysed by approximation. Accuracy of approximation for flow curves of real water-based fluids by these models does not exceed 10-11 %, which is enough for engineering practice solution. Obtained dependencies of shear stress on shear rate and method of optimal rheological model selection are shown in Fig.3 and Table 3.
The statistical approach is applied to the choice of optimal model, in which rheology of drilling mud is characterized by indicators of the model that describes its rheological behaviour most accurately (with less error). On the basis of the obtained dependencies and results, it is possible to conclude that the Herschel – Bulkley model describes rheological behaviour of the investigated drilling mud more accurately than the Ostwald – de Waale model and the Bingham – Shvedov model. Analyzing graphical materials, it is possible to state, that the modified power law reflects the behaviour of investigated muds in all range of shear rate with 99 % reliability.
Table 3
Rheological parameters of the investigated drilling muds
Rheological parameters |
Rheological model |
|||
Bingham – Shvedov |
Ostwald – de Waale |
Herschel – Bulkley |
||
Solution 1 (HPAN) |
||||
Regression equation |
y = 0.024x + 3.2401 |
y = 0.7813x0.4906 |
y = 0.541 + 0.1654x0.708 |
|
R2 |
0.9787 |
0.9799 |
0.9991 |
|
τy, Pa |
2.985 |
1.416 |
1.279 |
|
μ, mPa×s |
23.5 |
9.68 |
18.53 |
|
n |
– |
0.506 |
0.722 |
|
K, Pa×sn |
– |
0.717 |
0.163 |
|
Solution 2 (РНРА 12) |
||||
Regression equation |
y = 0.0199x + 3.2356 |
y = 0.8389x0.4568 |
y = 1.23 + 0.1218x0.712 |
|
R2 |
0.9735 |
0.9778 |
0.9989 |
|
τy, Pa |
2.889 |
1.471 |
1.354 |
|
μ, mPa×s |
19.88 |
6.71 |
14.69 |
|
n |
– |
0.472 |
0.734 |
|
K, Pa×sn |
– |
0.761 |
0.148 |
|
Solution 3 (РНРА 15) |
||||
Regression equation |
y = 0.0212x + 3.7829 |
y = 0.8177x0.4793 |
y = 0.992 + 0.3431x0.689 |
|
R2 |
0.9535 |
0.9866 |
0.9988 |
|
τy, Pa |
3.511 |
1.402 |
0.985 |
|
μ, mPa×s |
21.46 |
9.74 |
13.71 |
|
n |
– |
0.496 |
0.619 |
|
K, Pa×sn |
– |
0.741 |
0.318 |
|
Solution 4 (РНРА 20) |
||||
Regression equation |
y = 0.0226x + 3.6466 |
y = 0.7129x0.5072 |
y = 0.689 + 0.559x0.598 |
|
R2 |
0.9523 |
0.997 |
0.9993 |
|
τy, Pa |
3.9964 |
1.178 |
0.715 |
|
μ, mPa×s |
22.51 |
12.94 |
14.91 |
|
n |
– |
0.536 |
0.596 |
|
K, Pa×sn |
– |
0.704 |
0.415 |
|
Solution 5 (РНРА 27) |
||||
Regression equation |
y = 0.0247x + 3.9506 |
y = 0.7653x0.5093 |
y = 0.289 + 0.441x0.575 |
|
R2 |
0.9483 |
0.9873 |
0.9992 |
|
τy, Pa |
3.6169 |
0.821 |
0.294 |
|
μ, mPa×s |
24.71 |
13.92 |
16.13 |
|
n |
– |
0.534 |
0.587 |
|
K, Pa×sn |
– |
0.578 |
0.439 |
Notе. R2 – approximation reliability; τy – dynamic shear stress, Pa; μ – plastic viscosity, mPa×s.
Experience in directional and horizontal well construction shows that flushing fluids exhibiting pseudoplastic properties have ideal rheological behaviour – at the exit from bit nozzles the fluid acquires viscosity close to that of water, and when moving in the annular space it increases its viscosity to retain the drilled rock.
The indices of non-linearity n and consistency K of the drilling mud characterize the behaviour of the system both at low and at high shear rate. When xanthan polymer is added to the mud, the fluid acquires pseudoplastic properties. Xanthan helps to increase viscosity of drilling muds due to its long branched structure and relatively weak hydrogen bonds of side groups. The functional groups are represented by hydroxyl (–OH), carboxyl (–COH), carbonyl (C = O) and other groups, which give this polymer its thickening properties.
The pseudoplasticity of the solution is evaluated by a non-linearity index in the range from 0 to 1. All solutions are characterized by a non-linearity index in the range of 0.587-0.722. At the same time, there is a decrease in n with increasing molecular mass of РНРА, i.e. solution 5 exhibits pseudoplastic properties to a greater extent. Low value of non-linearity index will assist in equalization of flow velocities in annular space, thus avoiding undesirable migration of cuttings to the well walls. In addition, solution 5 has the lowest value of ultimate shear stress, which will reduce the amplitude of pressure fluctuations when starting and stopping pumps and performing tripping operations, as well as the probability of formation of dead zones with accumulation of drilled rock in them.
The consistency index K represents the viscosity of the fluid (the higher the K value, the more viscous the mud), which can be increased to achieve complete cuttings removal with a simultaneous reduction in the non-linearity index. When drilling mud is treated with РНРА, the consistency index increases with increasing molecular mass, which is due to the elastic properties and increased viscosity of the partially hydrolyzed polyacrylamide.
Conclusion
РНРА of different molecular mass, which is not only an inhibitor but also an encapsulant (creating prerequisites for improved cleaning quality), is proposed as a replacement for HPAN, and its optimum concentration is determined.
Based on the results of the experimental data approximation and the comparison of the results obtained, it is recommended to use a high density, barite-free drilling mud on the basis of formic acid salts (sodium and potassium formate) and PHPA additive with a molecular mass of 27 million.
Different rheological models are considered. Modified power law reflects the behaviour of investigated solutions in the whole range of shear rates with high reliability, which allows to calculate pressure loss in annular space and ECD more accurately in the next stage of the research. High-density formate drilling muds are a good alternative to polymer flushing fluids with barite as a weighting agent. But further research is needed, including full evaluation of filtration, inhibiting and lubricating characteristics of these muds.
* API RP 13B-1-2019. Recommended Practice for Field Testing Water-based Drilling Fluids: Second Edition. Washington, USA: Norm of American Petroleum Institute, 2019, 132 p.
** API RP 13D. Rheology and Hydraulics of Oil-well Drilling Fluids. Washington, USA: Norm of American Petroleum Institute, 2006, 98 p.
References
- Alcázar L.A., Cortés I.R. Drilling fluids for deepwater fields: an overview. Recent Insights in Petroleum Science and Engineering. London: IntechOpen, 2017, p. 67-89. DOI: 10.5772/intechopen.70093
- Litvinenko V.S., Bowbrick I., Naumov I.A., Zaitseva Z. Global guidelines and requirements for professional competencies of natural resource extraction engineers: Implications for ESG principles and sustainable development goals. Journal of Cleaner Production. 2022. Vol. 338. N 130530. DOI: 10.1016/j.jclepro.2022.130530
- Litvinenko V.S., Dvoynikov M.V., Trushko V.L. Elaboration of a conceptual solution for the development of the Arctic shelf from seasonally flooded coastal areas International. Journal of Mining Science and Technology. 2021. Vol. 32. Iss. 1, p. 113-119. DOI: 10.1016/j.ijmst.2021.09.010
- Dvoynikov M.V., Kuchin V.N., Mintzaev M.S. Development of viscoelastic systems and technologies for isolating water-bearing horizons with abnormal formation pressures during oil and gas wells drilling. Journal of Mining Institute. 2021. Vol. 247, p. 57-65. DOI: 10.31897/PMI.2021.1.7
- Gao C.H. A Survey of Field Experiences with Formate Drilling Fluid. SPE Drill & Compl. 2019. Vol. 34. Iss. 4, p. 450-457. DOI: 10.2118/195699-PA
- Grigoriev B.S., Eliseev A.A., Pogarskaya T.A., Toropov E.E. Mathematical Modeling of Rock Crushing and Multiphase Flow of Drilling Fluid in Well Drilling. Journal of Mining Institute. 2019. Vol. 235, p. 16-23. DOI: 10.31897/PMI.2019.1.16
- Palyanitsina A., Tananykhin D., Masoud R. Strategy of water-flooding enhancement for low-permeable polymictic reservoirs. Journal of Applied Engineering Science. 2021. Vol. 19. N 2, p. 307-317. DOI: 10.5937/jaes0-29693
- Mardashov D.V., Rogachev M.K., Zeigman Y.V., Mukhametshin V.V.Well killing technology before workover operation in complicated conditions. Energies. 2021. Vol. 14. Iss. 3. N 654. DOI: 10.3390/en14030654
- Mohamed A., Al-Afnan S., Elkatatny S., Hussein I. Prevention of barite sag in water-based drilling fluids by a urea-based additive for drilling deep formations. Sustainability. 2020. Vol. 12. Iss. 7. N 2719. DOI: 10.3390/su12072719
- Van Thang Nguyen, Rogachev M.K., Aleksandrov A.N. A new approach to improving efficiency of gas-lift wells in the conditions of the formation of organic wax deposits in the Dragon field. Journal of Petroleum Exploration and Production Technology. 2020. Vol. 10, p. 3663-3672. DOI: 10.1007/s13202-020-00976-4
- Byrne M., Patey I., Liz G. et al. Formate Brines: A Comprehensive Evaluation of Their Formation Damage Control Properties Under Realistic Reservoir Conditions. SPE International Symposium and Exhibition on Formation Damage Control, 20-21 February 2002, Lafayette, Luisiana, USA. OnePetro, 2002. SPE-73766-MS. DOI: 10.2118/73766-MS
- Howard S.K., Downs J.D. Formate Brines for HPHT Well Control – New Insights into the Role and Importance of the Carbonate/Bicarbonate Additive Package. SPE International Symposium on Oilfield Chemistry, 20-22 April 2009, Texas, USA. OnePetro, 2009. SPE-121550-MS. DOI: 10.2118/121550-ms
- Nutskova M.V., Rudiaeva E.Y., Kuchin V.N., Yakovlev A.A. Investigating of compositions for lost circulation control. Youth Technical Sessions Proceedings of the 6th Youth Forum of the World Petroleum Council – Future Leaders Forum, 23-28 June 2019, Saint Petersburg, Russia. CRC Press, 2019, p. 394-398. DOI: 10.1201/9780429327070-55
- Champeau M., Xia Wei, Jackson P. et al. Alternative High Density Brines. SPE Offshore Europe Conference and Exhibition, 3-6 September 2019, Aberdeen, UK. OnePetro, 2019, p. 544-554. DOI: 10.2118/195743-MS
- Pashkevich M.A., Alekseenko A.V., Petrova T.A. Application of polymeric materials for abating the environmental impact of mine wastes. International Conference “Complex equipment of quality control laboratories”, 14-17 May 2019, Saint-Petersburg, Russian Federation. Journal of Physics: Conference Series, 2019. Vol. 1384. N 012039. DOI: 10.1088/1742-6596/1384/1/012039
- Ryabtsev P., Khomutov A., Korolev V. The First Experience of Formate Based Drilling Fluids Application in Russia. SPE Russian Petroleum Technology Conference, 15-17 October 2018, Moscow, Russia. OnePetro, 2018. SPE-191503-18RPTC-MS. DOI: 10.2118/191503-18RPTC-MS
- Howard S., Kaminski L., Downs J. Xanthan stability in formate brines – Formulating non-damaging fluids for high temperature applications. SPE European Formation Damage Conference, Proceedings, EFDC, 3-5 June 2015, Budapest, Hungary. OnePetro, 2015. SPE-174228-MS. DOI: 10.2118/174228-ms
- Hamed S.B., Belhadri M. Rheological properties of biopolymers drilling fluids. Journal of Petroleum Science and Engineering. 2009. Vol. 67, p. 84-90. DOI: 10.1016/j.petrol.2009.04.001
- Tianle Liu, Leusheva E., Morenov V. et al. Influence of Polymer Reagents in the Drilling Fluids on the Efficiency of Deviated and Horizontal Wells Drilling. Energies. 2020. Vol. 13. Iss. 18. N 4704. DOI: 10.3390/en13184704
- Vipulanandan C., Mohammed A.S. Hyperbolic rheological model with shear stress limit for acrylamide polymer modified bentonite drilling muds. Journal of Petroleum Science and Engineering. 2014. Vol. 122, p. 38-47. DOI: 10.1016/j.petrol.2014.08.004
- Blinov P.A., Dvoynikov M.V. Rheological and filtration parameters of the polymer salt drilling fluids based on xanthan gum. Journal of Engineering and Applied Sciences. 2020. Vol. 15. Iss. 2, p. 5661-5664.
- Melekhin A.A., Chernyshov S.E., Turbakov M.S. Expanding Compositions of Cement Slurries for Lost Circulation Control under Cementing of Casing of Producing Wells. Oil Industry. 2012. N 3, p. 50-52
- Moradi S.S.T., Nikolaev N.I., Chudinova I.V. Geomechanical Analysis of Wellbore Stability in High-pressure, High-temperature Formations. Proceedings of the Eage Conference & Exhibition, 12-15 June 2017, Paris, France. European Association of Geoscientists & Engineers, 2017, p. 1-3. DOI: 10.3997/2214-4609.201701463
- 24. Bui B.T., Tutuncu A.N. A Generalized Rheological Model for Drilling Fluids With Cubic Splines. SPE Drill & Compl. 2016. Vol. 31. Iss. 1, p. 26-39. DOI: 2118/169527-MS
- Litvinenko V.S., Nikolaev N.I. Development of the weighted biopolimer drilling mud for workover. Journal of Mining Institute. 2012. Vol. 199. 375-378 (in Russian).
- Raupov I.R., Shagiakhmetov A.M. The results of the complex rheological studies of the cross-linked polymer composition and the grounding of its injection volume. International Journal of Civil Engineering and Technology. 2019. Vol. 10. Iss. 2, p. 493-509.
- Akpan E.U., Enyi G.C., Nasr G.G. Enhancing the performance of xanthan gum in water-based mud systems using an environmentally friendly biopolymer. Journal of Petroleum Exploration and Production Technology. 2020. Vol. 10, p. 1933-1948. DOI: 10.1007/s13202-020-00837-0
- Chunping Deng, Guoyong Du, Xingchun Li et al. Effect of high temperature and high pressure on the biodegradability and biotoxicity of typical additives in drilling fluid. Journal of Petroleum Science and Engineering. 2022. Vol. 208. Part E. N 109773. DOI: 10.1016/j.petrol.2021.109773
- Davarpanah A., Mirshekari B. Effect of formate fluids on the shale stabilization of shale layers. Energy Reports. 2019. Vol. 5, p. 987-992. DOI: 10.1016/j.egyr.2019.07.016
- Strizhenok A.V., Korelskiy D.S. Improvement of the system of industrial environmental monitoring of atmospheric air in the area of anthropogenic arrays impact. International Conference “Complex equipment of quality control laboratories”, 14-17 May 2019, Saint-Petersburg, Russian Federation. Journal of Physics: Conference Series. 2019. Vol. 1384. N 012052. DOI: 10.1088/1742-6596/1384/1/012052
- Zhou Hui, Chesnee D., Jay D. et al. Hydraulic Modeling Helps Designing Ultralow ECD Nonaqueous Fluids to Meet Narrow ECD Windows. Abu Dhabi International Petroleum Exhibition & Conference, 12-15 November 2018, Abu Dhabi, UAE. OnePetro, 2018. N SPE-192951-MS. DOI: 10.2118/192951-MS
- Jain R., Mahto V. Evaluation of polyacrylamide/clay composite as a potential drilling fluid additive in inhibitive water based drilling fluid system. Journal of Petroleum Science and Engineering. 2015. Vol. 133, p. 612-621. DOI: 10.1016/j.petrol.2015.07.009
- Berg P.C., Pederson E.S., Lauritsen A. Drilling and Completing High-Angle Wells in High-Density, Cesium Formate Brine – The Kvitebjorn Experience. SPE Drill & Completion. Vol. 24. Iss. 1, p. 15-24. DOI: 10.2118/105733-PA
- Blkoor S.O., Norddin M.M., Ismail I. et al. Amphipathic anionic surfactant modified hydrophilic polyethylene glycol-nanosilica composite as effective viscosifier and filtration control agent for water-based drilling muds. Arabian Journal of Chemistry. 2022. Vol. 15. Iss. 4. N 103741. DOI: 10.1016/j.arabjc.2022.103741
- Krivoshchekov S.N., Melekhin A.A., Turbakov M.S. et al. Development of a Telemetric System for Monitoring Downhole Parameters in the Course of Wells Construction. Oil Industry. 2017, p. 86-89 (in Russian). DOI: 10.24887/0028-2448-2017-9-86-88
- Myslyuk M.A. On the interpretation of drilling fluids rotational viscometry data. Oil Industry. 2018. Vol. 2018. Iss. 10, p. 50-53. DOI: 10.24887/0028-2448-2018-10-50-53
- Adewale J., Lucky A.P., Abioye P. et al. Selecting the most appro-priate model for rheological characterization of syntheticbased drilling mud. International Journal of Applied Engineering Research. 2017. Vol. 12. N 18, p. 7614-7629.
- Winiowski R., Skrzypaszek K., Maachowski T. Selection of a Suitable Rheological Model for Drilling Fluid Using Applied Numerical Methods. Energies. 2020. Vol. 13. Iss. 12. N 3192. DOI: 10.3390/en13123192
- Heath G., Okesanya T., Levey S. A Practical Study of the Influence of Drill Solids on the Corrosion of Downhole Tubulars When Using Brine Based Drilling Fluids. SPE Western Regional Meeting, 20-22 April 2022. OnePetro, 2021. SPE-200886-MS. DOI: 10.2118/200886-MS
- Kelessidis V.C., Maglione R., Tsamantaki C., Aspirtakis Y. Optimal determination of rheological parameters for Herschel–Bulkley drilling fluids and impact on pressure drop, velocity profiles and penetration rates during drilling. Journal of Petroleum Science and Engineering. 2006. Vol. 53, p. 203-224. DOI: 10.1016/j.petrol.2006.06.004
- Kupavykh K.S., Kupavykh A.S., Morenov V.A.Analysis of Implementation Effectiveness of Two Working Fluids Characterized by Different Viscoelastic Characteristics at Hydrodynamic Impact on the Borehole Bottom Zone. Science & Technique. 2019. Vol. 18. N 2, p. 164-170. DOI: 10.21122/2227-1031-2019-18-2-164-170
- Mahto V., Sharma V.P. Rheological study of a water based oil well drilling fluid. Journal of Petroleum Science and Engineering. 2004. Vol. 45. Iss. 1-2, p. 123-128. DOI: 10.1016/j.petrol.2004.03.008
- Xianbin Huang, Kaihe Lv, Jinsheng Sun et al. Enhancement of thermal stability of drilling fluid using laponite nanoparticles under extreme temperature conditions. Materials Letters. 2019. Vol. 248, p. 146-149. DOI: 10.1016/j.matlet.2019.04.005