Повышение энергоэффективности малотоннажного производства метанола путем применения микротурбодетандерных установок
- 1 — канд. техн. наук доцент Балтийский государственный технический университет «ВОЕНМЕХ» им. Д.Ф.Устинова ▪ Orcid
- 2 — канд. техн. наук доцент Санкт-Петербургский горный университет ▪ Orcid
- 3 — канд. техн. наук доцент Санкт-Петербургский горный университет ▪ Orcid
- 4 — старший преподаватель Балтийский государственный технический университет «ВОЕНМЕХ» им. Д.Ф.Устинова ▪ Orcid
- 5 — инженер-конструктор АО «ОДК-Климов» ▪ Orcid
Аннотация
Рассматривается вопрос повышения энергоэффективности контейнерных газохимических установок для производства метанола в промысловых условиях. Актуальность направления обуславливается необходимостью освоения удаленных арктических месторождений углеводородов. Объектом исследования является энергоэффективное преобразование энергии отходящих газов и излишков тепловой энергии в малотоннажном комплексе производства метанола с использованием технологии получения синтез-газа путем некаталитического парциального окисления природного газа. Рассмотрены подходы к дизайну и анализу конструкционных решений микротурбодетандерных установок. Предложена методика, сочетающая традиционные подходы к расчету оборудования и моделирование методом конечных элементов в ПК ANSYS. Разработанная методика облегчает расчет конструктивных параметров микротурбодетандеров и позволяет учесть особенности рабочей среды, термобарических условий и расходные характеристики газа.
Введение
Решение проблемы обеспечения растущего мирового спроса в энергоресурсах за счет развития энергоэффективных и низкоуглеродных технологий является актуальной задачей. Но компенсировать рост энергопотребления только за счет энергии ветра и солнца, на которых основаны стратегии декарбонизации ряда развитых экономик, на развивающихся рынках в ближайшие десятилетия не представляется возможным. Среди углеродсодержащего сырья углеводородный газ представляется одним из самых энергоэффективных и экологически чистых источников энергии [1]. В связи с истощением зрелых месторождений углеводородов для обеспечения целей устойчивого развития российской экономики возникает острая необходимость в освоении трудноизвлекаемых и труднодоступных месторождений, находящихся, в том числе и в Арктике [2, 3].
При проектировании и строительстве инфраструктуры арктических нефтегазовых объектов принятие решения о внедрении газохимических технологий обеспечит выполнение требований природоохранного законодательства в области утилизации попутного нефтяного газа (ПНГ) и низконапорного газа, а также повысит рентабельность производства [4-6]. Это особенно актуально для освоения удаленных, труднодоступных и малых месторождений нефти и газа, в которых в совокупности сосредоточено более 50 % российских разведанных запасов углеводородного сырья [7, 8]. Кроме утилизации ПНГ предлагаемый к рассмотрению газохимический комплекс может быть использован для вовлечения в хозяйственный оборот метана угольных и сланцевых пластов, а также био- и свалочного газов.
Рассматриваемый газохимический комплекс разработан под задачи утилизации ПНГ, так как данная задача стоит очень остро во всем мире. Согласно данным международной инициативы по полному прекращению сжигания ПНГ Zero Routine Flaring by 2030, представленной Всемирным банком, ежегодно в мире сжигается около 150 млрд м3 попутного газа [9].
Сжигание газа на факелах способствует возникновению парникового эффекта. Например, российская нефтегазовая промышленность является одним из крупнейших источников выбросов CO2 в стране. Его доля в общих выбросах углекислого газа РФ составляет около 26 % [10].
Для утилизации ПНГ в промысловых условиях наиболее широко используются генерация электрической энергии и переработка с разделением на сухой газ, пропан-бутановую смесь и газовый бензин. Оба метода актуальны и в конкретных случаях позволяют полностью утилизировать газ [8, 11]. Однако потребности месторождений углеводородов в энергии могут различаться в зависимости от их географического положения, доступа к централизованным энергосистемам, наличия топлива для энергоблоков и т.д. Существующие способы утилизации ПНГ зачастую реализуемы только в случаях их применения на крупных месторождениях в промышленно развитых регионах. На удаленных объектах нецелесообразно строить протяженный газопровод для транспорта ПНГ или его компонентов до рынков сбыта, а получаемая из ПНГ электроэнергия может быть не востребована в имеющихся объемах [12, 13].
Для обеспечения задач рационального природопользования целесообразно создание контейнерных малотоннажных газохимических установок на базе процессов: GTL (Gas-to-liquids – на основании процесса Фишера – Тропша) и GTC (Gas-to-chemicals – на основании процессов переработки синтез-газа в метанол, диметиловый эфир, синтетические углеводороды и др). GTL и GTC установки можно интегрировать в процессы утилизации ПНГ нефтегазовых промыслов, включая добывающие морские платформы. Установки могут быть адаптированы под различные композиции углеводородных газов, чтобы получить синтез-газ с заданным составом, который необходим для различных целевых продуктов: синтетических углеводородов, ароматики, диметилового эфира и метанола [14, 15]. Для удаленных газовых месторождений и некоторых арктических нефтяных объектов получаемый метанол может использоваться для ингибирования образования газовых гидратов в насосно-компрессорных трубах и обвязки наземной инфраструктуры [16, 17]. В России производится и транспортируется на удаленные месторождения более 500 тыс. т метанола в год. Необходимость специального обращения с метанолом при его транспортировке, хранении и использовании способствует значительному удорожанию мероприятий по борьбе с гидратообразованием.
Одна из целей проекта – разработка концепций технически реализуемых и экономически рентабельных технологических цепочек конверсии ПНГ в синтетические топлива или высококачественные химические продукты в полевых условиях. Ключевым процессом материального использования ПНГ является его конверсия в синтез-газ при высокотемпературных условиях (основные компоненты СО и Н2) [18].
Следует отметить, что CO2, образующийся в технологических процессах месторождений углеводородов, можно эффективно утилизировать путем его закачки в продуктивный пласт для повышения нефтеотдачи. В работах [19, 20] исследуются характеристики смесей с углекислым газом и эффективность их применения в различных пластовых условиях. Методы повышения нефтеотдачи с использованием СО2 важны для дальнейшего снижения выбросов парниковых газов в атмосферу и уменьшения углеродного следа производимой продукции. Полученный синтез-газ предлагается преобразовать в различные продукты с использованием подходящих процессов: водород для химической или нефтехимической промышленности; аммиак для производства удобрений; метанол, этилен или пропилен в качестве основных химикатов для химической промышленности, а также в бензин, дизельное топливо или керосин в качестве синтетических жидких топлив. Интеграция методов GTC в инфраструктуру нефтяных месторождений может снизить углеродный след от добычи нефти и газа, что повысит их конкурентоспособность на рынках ЕС и АТР [8, 21].
Существует ряд технологий получения метанола из осушенного природного газа, но в России есть только три блочно-модульных завода, работающих в условиях удаленного арктического месторождения. Это заводы дочерних обществ ПАО «НОВАТЕК»: ООО «НОВАТЭК-ЮРХАРОВНЕФТЕГАЗ» – установки ИОПУ-12,5 (производительность 12500 т метанола в год) и УПМ-40 (40 000 т метанола в год); ОАО «АРКТИКГАЗ» – установка УПМ-50 (50 000 т метанола в год). Установки работают на низконапорном газе, поступающем от установки комплексной подготовки газа. Углеводородный газ по технологии каталитического парового риформинга преобразуется в синтез-газ, который поступает в реактор синтеза метанола на медьцинкалюминиевых катализаторах. Затем отходящие газы утилизируются, а метанол отделяется от воды и направляется в систему подачи ингибитора гидратообразования инфраструктуры.
В процессе эксплуатации трубчатых реакторов каталитического парового риформинга низконапорного газа, который содержит значительное количество C3-C5 компонентов, периодически возникают сложности, вызванные тем, что трубки реактора, заполненные катализатором, забиваются частицами твердого углерода. На периодическую очистку катализатора водяным паром тратится до 10 % рабочего времени. При продувке паром происходит газификация частиц углерода с образованием CO2, который затем отводится в атмосферу. Перспективной инновационной технологией для малотоннажного производства метанола является парциальное некаталитическое окисление углеводородного газа воздухом с получением азотсодержащего синтез-газа, подаваемого в проточный каскад реакторов каталитического синтеза метанола. Использование воздуха в качестве окислителя позволяет проектировать модульные транспортабельные, безопасные в эксплуатации и энергонезависимые установки. Однако для их промышленного внедрения необходимо создание опытных установок с целью экспериментальной проверки расчетных материальных балансов и детальной технико-экономической оценки проектов.
Недостатком рассматриваемой схемы являются значительные энергозатраты на компримирование углеводородного газа и воздуха до 6 МПа. При этом в процессе получения синтез-газа выделяется значительное количество потенциальной тепловой энергии, которая может быть использована для генерации энергии посредством микротурбодетандерных установок [22].
Анализ существующих моделей микротурбодетандерных установок
На российском рынке представлены турбодетандерные агрегаты среднего давления типа ДТ (например, ДТ 1,5/4), производимые компаниями ОАО «НПО «ГЕЛИЙМАШ» и ООО «Кислородмаш» [23]. Данный тип турбодетандеров работает в широком диапазоне давлений. Но получаемая мощность на валу гораздо меньше заданного значения, а наибольшая эффективность работы (изоэнтропный КПД менее 87 %) осуществляется при отрицательных температурах.
Также интерес представляют детандеры компании Rotoflow [24]. Оборудование отличается надежностью и простотой в эксплуатации и обслуживании. К особенностям можно отнести обеспечение изоэнтропного КПД до 91 %. Но турбодетандеры данного типа работают в диапазоне температур от –200 до 150 °C. С учетом того, что диапазон температур на выходе рассматриваемого малотоннажного комплекса производства метанола составляет 250-300 °C, такие детандеры не могут использоваться.
На китайском рынке турбодетандеры среднего давления производит компания Suzhou Wintek Machinery Engineering. Представленный модельный ряд детандеров PLPK (например, PLPK-25.83/14.2-5.35) работает в подходящем диапазоне температур и давлений. Но из-за низкого качества используемых материалов изоэнтропный КПД менее 80 %, что не удовлетворяет условию эффективного преобразования рабочего тела.
Компания Capstone Turbine Corporation представляет микротурбинные установки с мощностями от 35 кВт до 1 МВт. Данные турбины работают на оборотах до 96000 об/мин [25]. Однако рабочим телом выступают газы, которые поступают из камеры сгорания топлива, с более высокими температурами и сильно отличающимся компонентным составом.
Для повышения энергоэффективности и экологичности малотоннажного производства метанола необходимо использовать микротурбодетандерные установки с различной конструкцией в зависимости от термобарических условий в конкретном блоке установки получения метанола. Поэтому целью работы является разработка схемы малотоннажной установки получения метанола с системой утилизации потенциальной энергии отходящих газовых потоков, для чего также необходимо обосновать методологию проектирования турбины микротурбодетандерных установок.
Методы
Рассмотрим малотоннажную систему производства метанола с использованием технологии получения синтез-газа путем некаталитического парциального окисления природного газа [26]. На схеме (рис.1) углеводородный газ (CхHy), отделенный на нефтяном или газовом промысле на сепарационной установке, поступает на прием газового компрессора. Воздух засасывается из атмосферы и компримируется на первой ступени воздушного компрессора 1. При этом одна часть воздушного потока направляется в котел-утилизатор отходящих газов, а остальная часть дожимается до требуемого давления на второй ступени воздушного компрессора 1. Компримированный до требуемого давления углеводородный газ и воздух смешиваются и подаются в смесительную головку высокотемпературного реактора, где протекает реакция парциального окисления с образованием синтез-газа. Вместе с газом и воздухом в реактор для протекания реакции подается деминерализованная вода через инжектор.
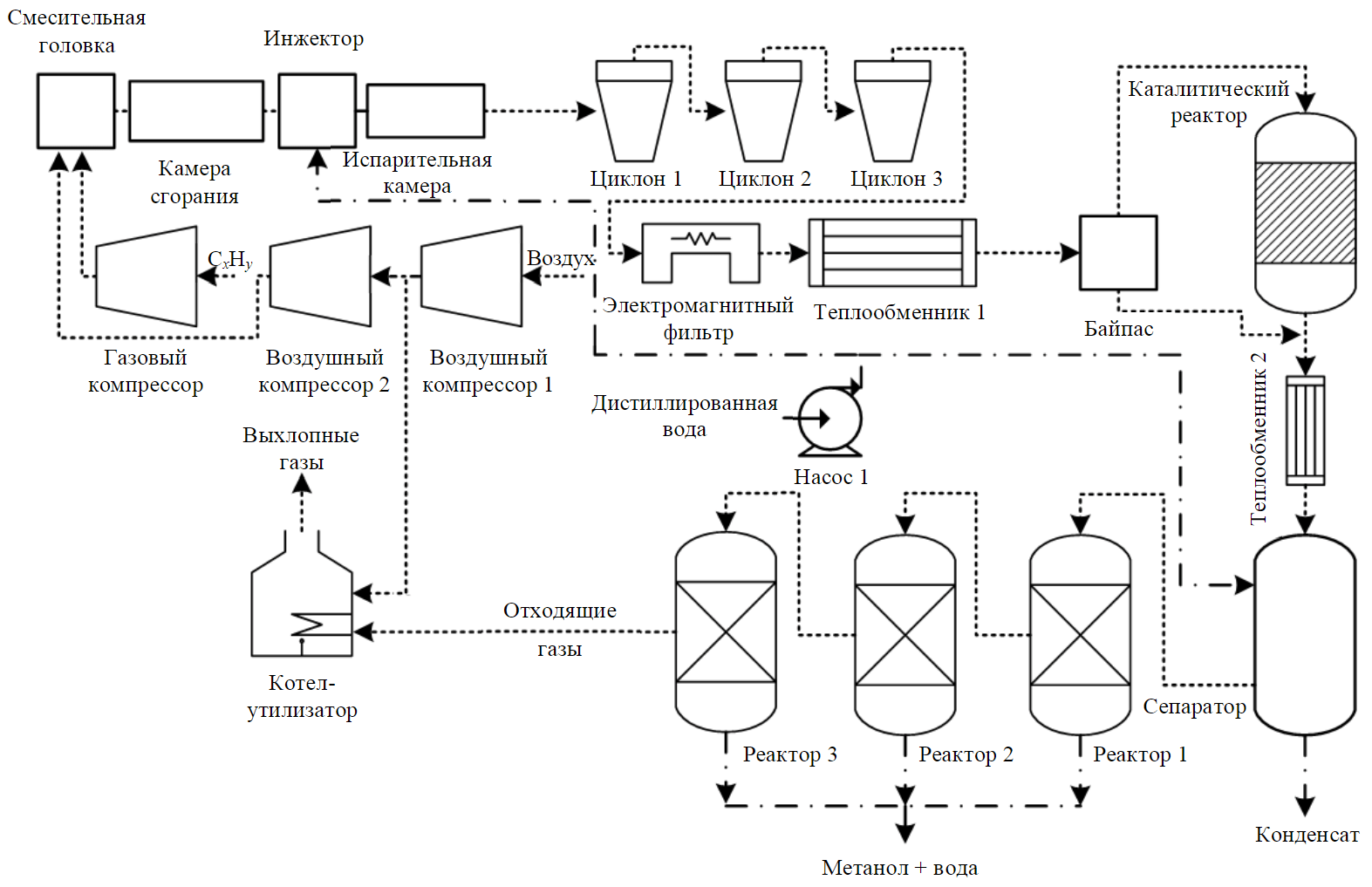
Рис.1. Процесс производства метанола
Синтез-газ, полученный парциальным окислением на установке, проходит очистку от сажи на трех циклонах (1, 2 и 3 на рис.1), электромагнитном фильтре и теплообменнике 1. Часть синтез-газа направляется байпасом на каталитический реактор, в котором проходит реакция CO-сдвига с добавлением воды и преобразованием CO в CO2, за счет чего в потоке увеличивается молярная доля H2. Осушенный газ подается в теплообменник 2 для охлаждения и далее на сепаратор для отделения из потока воды. После сепаратора синтез-газ подается в реактор 1 (входящий в каскад реакторов 1, 2 и 3), в котором получают метанол в присутствии катализатора. Из-за балластных газов использовать один реактор с рециклингом не целесообразно. В предложенной схеме три реактора использованы для повышения процента конверсии, так как в синтез-газе присутствует значительное количество азота. Полученный в реакторе 1 метанол направляется на теплообменный аппарат, в котором охлаждается и поступает в сепаратор для отделения непрореагировавшего синтез-газа от полученного метанола и воды. Метанол с водой собирается в емкости, а оставшийся синтез-газ направляется на вторую и третью ступени каскада в реакторы 2 и 3. Непрореагировавший газ отправляется в котел-утилизатор, в котором дожигается и через систему фильтров отводится в атмосферу.
Для различных термобарических условий в элементах установки производства метанола невозможно подобрать готовое решение, так как параметры среды и процесса будут меняться не только при масштабировании параметров процесса, но и при изменении состава перерабатываемого углеводородного газа в зависимости от множества других характеристик. С учетом этого для реализации системы необходимо разрабатывать элементы таких турбодетандеров исходя из конкретных условий.
Вырабатываемая турбодетандером механическая энергия используется для привода компрессора, подающего воздух (окислитель) в смеситель, после чего газы поступают в реактор для дальнейшей рекуперации. Реализация данной схемы имеет существенные ограничения из-за малых размеров установки, поэтому проектируемая установка должна иметь малые массогабаритные характеристики и низкие эксплуатационные расходы.
Чтобы эффективно использовать отходящие газы (массовое соотношение элементов газов, %: 87,16 N2; 1,44 Н2; 5 CO2; 4,99 CO; 1,41 CH3OH), следует установить турбодетандер, который будет иметь малые массогабаритные характеристики и отвечать заданным параметрам: температура на входе/выходе – 260/139 °C; давление на входе/выходе – 4,915/1,46 МПа; массовый расход – 5112 кг/ч; объемный расход – 4768 нм3/ч; мощность на валу – 200 кВт.
Необходимо рационально и эффективно использовать свободное место, так как главной особенностью разрабатываемой малотоннажной установки получения метанола являются малые габариты и размещение множества габаритных элементов в одном 20-футовом контейнере.
При малых габаритах и заданном расходе рабочего тела необходимо учитывать неизбежное увеличение оборотов ротора и окружных скоростей с уменьшением диаметра рабочего колеса. С этим условием принято решение разработки центростремительного турбодетандера, представляющего радиально-осевую лопаточную машину. Выбор такой схемы определен простотой и надежностью центростремительного колеса, которое можно выполнить единой отливкой, что расширяет области рабочих оборотов и возможные теплоперепады, допустимые по прочностным характеристикам.
В итоге разрабатываемый турбодетандерный агрегат преобразует энергию расширения отходящих газов в механическую энергию вращения вала детандера, с которого можно получать полезную работу. Отходящие газы представляют собой смесь азота, водорода, монооксида и диоксида углерода, метанола. Параметры смеси газа определялись расчетом с помощью справочника [26].
На первом этапе проектирования выбраны методики А.Н.Шерстюка и А.Е.Зарянкина, Е.М.Бамбушека и И.А.Сакуна, а также В.И.Епифанова. В проведенном анализе предложенных методов расчета и на основе анализа статей [27, 28] в качестве основной выбрана методика А.Н.Шерстюка и А.Е.Зарянкина. На ее основе проведен предварительный термогазодинамический расчет турбодетандера, число лопаток рассчитывалось по методике [27] и выбиралось минимальное нечетное их количество для минимизации потерь на трение и уменьшения потенциальной вибрации ротора. Заданный расчетный диаметр из условия малых габаритов D1 = 80 мм, при этом предельное допустимое значение окружной скорости на входе в рабочее колесо u1max ∼ 500 м/c. Условие окружной скорости исходит из условия прочностных характеристик материалов, из которых производят рабочие колеса [29, 30]. Угол на входе β1 задается 90° из условия безударного входа потока и технологичности конструкции лопатки рабочего колеса. Для минимизации закрутки потока на выходе из рабочего колеса и уменьшения потерь в последующих элементах проточной части угол α2 задается 90°. По условию приведенной скорости потока на выходе из соплового аппарата λ ≤ 1 заданная степень реактивности ρ = 0,5.
Построение геометрии рабочей ступени турбодетандера
Существует множество методов профилирования периферийного и втулочного ободов рабочего колеса: по окружностям, эллиптические и параболические кривые, кривыми Безье и т.д., основанные на исследовательской базе и опыте проектировщиков. Построение меридионального профиля на данном этапе проводилось при помощи окружностей. Толщина лопаток и угол заострения выбирались так, чтобы толщина узкой части кромки была не менее 1 мм по технологическим соображениям [31, 32]. Влияние ширины рабочего колеса на его эффективность исследовано в [28]. Слишком малая ширина колеса может привести к образованию отрывных зон на рабочих режимах, поэтому на данном этапе ширина принималась как B = 0,25D1. Для сохранения постоянства угла выхода по всей высоте профиля на выходе из рабочего колеса угол профиля лопатки β2 изменялся по закону tg(β2)R2 = = const [27].
По предварительным расчетам малотоннажной установки получения метанола скорость потока отходных газов на выходе из реакторов перед турбодетандером составляет 20-30 м/с. С учетом расчетной степени реактивности и скоростей на входе в рабочее колесо принято решение использовать сопловую решетку для достижения необходимых параметров и заданного угла.
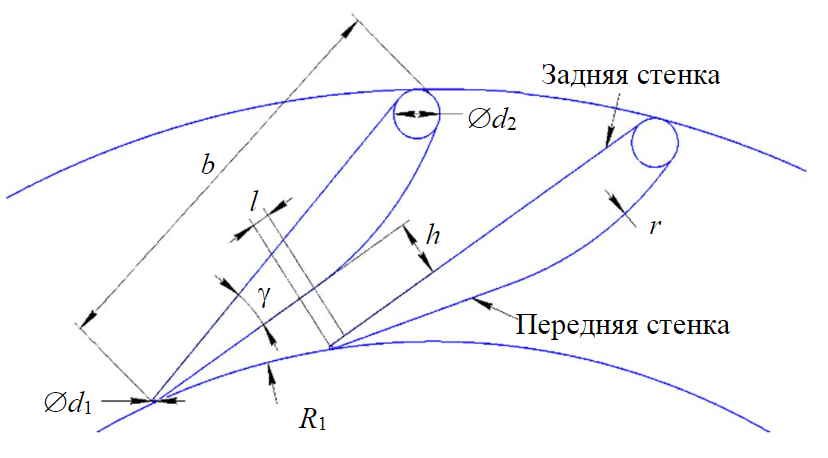
Рис.2. Профиль проектируемой сопловой решетки: d1, d2 – диаметры скруглений на выходной и входной кромках; R1 – внутренний радиус, равный сумме радиуса рабочего колеса и зазора; h – ширина горла канала; r – радиус скругления передней стенки; l – ширина прямолинейного участка горла; γ – угол раскрытия лопатки, определялся как γ = 360/zл; zл – число лопаток соплового аппарата (принято 24)
Построение геометрии сопловой решетки
Существует множество профилей сопловых решеток в виде лопаток и канальных сопловых аппаратов. Для малогабаритных турбодетандерных установок применяются крыловидные профили с параллельными смежными стенками, так как при малых размерах лопаток их эффективность не отличается от профилированных, а проектируются и изготавливаются гораздо легче [27, 29, 33]. Для малых углов входа потока заднюю стенку искривляют, чтобы достичь оптимального угла.
Основные геометрические параметры профиля и ширина горла рассчитаны на основе методики [31] и с учетом рекомендаций [34, 35]. Кривая область передней стенки задается радиусом окружности. Построенный крыловидный профиль представлен на рис.2.
Оптимальная форма подбиралась изменением длины лопатки и длины участка горла, подбор которой обусловлен обеспечением выравнивания поля скоростей на выходе из канала. Диаметр выходной кромки задавался минимально возможным для уменьшения кромочного следа и принимался 0,1 мм [33]. Расчет подобных входных устройств представляет собой сложную задачу из-за сложных условий течения [31, 32]. Для оценки предварительных габаритных размеров использована методика [32].
Построение входных аппаратов турбодетандера
Входные аппараты турбодетандеров обычно выполняют в виде кольца или улитки с прямым или угловым подводом рабочего тела для равномерного распределения потока по окружности рабочего колеса [27]. Подвод потока проводится как одним патрубком, так и несколькими. Способ подвода потока во входной аппарат во многом зависит от компоновочных соображений и требуемого распределения усилий на рабочее колесо турбины. Также применяются безлопаточные направляющие сопловые аппараты, объединяющие функции соплового аппарата и входного устройства при небольших расходах и значениях приведенной скорости [36].
Обсуждение результатов
Недостаток схемы, в которой используется атмосферный воздух вместо чистого кислорода, – компримирование воздуха и углеводородного газа до 6 МПа, что является наиболее энергозатратной частью процесса. Для повышения энергоэффективности процесса и сокращения углеродного следа синтезируемой продукции предлагается использовать несколько микротурбодетандерных установок с различными характеристиками и геометрией для снятия:
- излишков давления отходящих газов до котла-утилизатора – позволит утилизировать энергию потока после реакторов синтеза метанола;
- давления дымовых газов после котла-утилизатора – после разогрева потока за счет дожигания реакционных газов позволит разместить еще одну микротурбину;
- давления водяного пара в высокотемпературном контуре – позволит утилизировать излишки высокопотенциальной тепловой энергии;
- давления паровой фазы низкокипящей жидкости в низкотемпературном контуре – позволит утилизировать излишки низкопотенциальной тепловой энергии и охлаждать потоки перед сепарацией жидкой фазы (воды, метанола).
Разработанная схема по повышению энергоэффективности и снижению углеродного следа процесса получения метанола представлена на рис.3. На рис.3, а представлен алгоритм работы турбодетандеров 1 и 2. Метанол, который выделяется из потоков, выходящих из трех реакторов в каскаде, собирается и используется на нужды промысла. При этом для решения задач ингибирования образования гидратов не требуется полная очистка метанола от воды. Отходящие газы, выделенные после третьего реактора, находятся под значительным избыточным давлением (до 5 МПа), которое используется для привода турбодетандера 1. Затем синтез-газ, оставшийся после прохождения реакторного каскада и первого детандера, сжигается в котле-утилизаторе, который представляет собой герметичный сосуд со встроенной запальной горелкой. В горелке отходящие газы смешиваются с обогащенным компримированным воздухом, поступающим после воздушного компрессора 1. После котла-утилизатора дымовые газы отправляются на турбодетандер 2 для заключительной стадии утилизации энергии потока. Затем дымовые газы через фильтры отводятся в атмосферу или на установку захвата CO2 (на схеме не показаны).
На рис.3, б представлен алгоритм работы турбодетандеров 3 и 4. Для отвода избытка тепла, выделяющегося после высокотемпературного реактора на теплообменнике 1, используется вода. Циркуляция хладагента (воды) осуществляется в высокотемпературном контуре при помощи насосной станции, а регулировка давления на входе в каждый теплообменный аппарат проводится с помощью регулировочных клапанов. Забрав тепло, вода переходит в пар, который вращает турбодетандер 3. Отвод тепла и конденсация пара осуществляется на едином холодильном центре, в состав которого входит контур органического цикла Ренкина с низкокипящей средой для утилизации энергии низкопотенциального тепла на турбодетандере 4. Низкотемпературный контур используется для охлаждения технологических потоков перед сепараторами, чтобы разделять воду, метанол и синтез-газ. При этом все турбодетандеры в разработанной схеме используются в качестве привода генераторов для производства электроэнергии.
Анализ результатов расчетов по проектированию турбины микротурбодетандерных установок
Расчет проводился в специальной программе на языке Python 3. Применение таких расчетов перспективно для их дальнейшей автоматизации и автоматического конструирования элементов в прикладных программных пакетах, поддерживающих скрипты на данном языке.
Поскольку основные углы заданы из конструктивных соображений, а угол β2 определяется результатом расчета из условия α2 = 90 , то задаваемым параметром остается α1. Необходимо исследовать его влияние на изоэнтропный КПД турбинной ступени. Так как расчетные мощности ограничены, нужно упростить расчетную модель. Одним из вариантов является расчет только одной лопатки с частью области течения вокруг нее. В этом случае граничные области течения делаются периодическими, что позволяет провести расчет только с одной областью.
Геометрия сопловой лопатки создана в SolidWorks и импортирована в ANSYS Design Modeler. Расчетная сетка построена в модуле TubroGrid (рис.4). Количество ячеек в сетке составило ~510000. Поверочный расчет проводился в модуле CFX.
Смесь газов задавалась как Pure Substance, термодинамическая модель – идеальный газ. Параметры смеси задавались исходя из расчета по справочникам. Расчет проводился как стационарная задача. Задаваемые граничные условия: на входе полная температура T0* = 533 К и расход газовой смеси G = 1,42 кг/c; на выходе статическое давление P1 = 2,817 МПа, предварительно определенное из результатов термогазодинамического расчета. В качестве модели турбулентности выбрана SST-Ментора, которая способна обеспечить необходимую точность решения подобных задач [33, 37]. Результат расчета приведен на рис.5.
Наблюдается зона отрыва потока на передней стенке при переходе в область горла. Для исключения подобных явлений нужно продолжить подбор такого радиуса окружности, который позволит гладко переходить потоку по кривой профиля, или применять иные способы построения кривой, такие как кривая Безье.
При малом угле подвода потока к сопловому аппарату задняя стенка заменяется кривой, обеспечивающей благоприятный подвод потока. После получения геометрии сопла проводится совместный расчет с рабочим колесом (как и в случае с сопловым аппаратом). Задаваемые граничные условия: на входе полная температура T0* = 533 К и расход газовой смеси G = 1,42 кг/c; на выходе статическое давление P2 = 1,46 МПа.
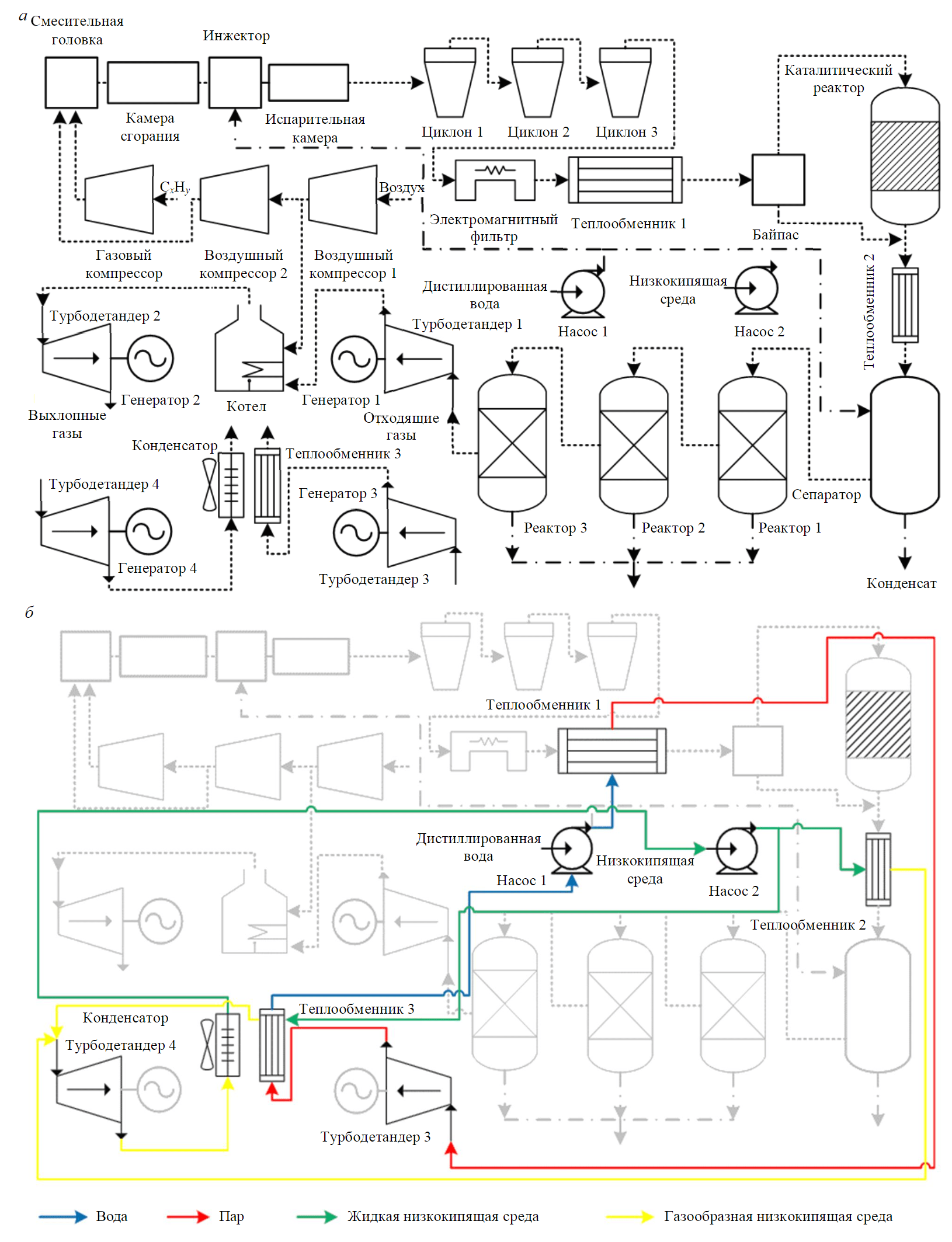
Рис.3. Схема материальных (а) и энергетических потоков (б) в системе утилизации энергии малотоннажного производства метанола
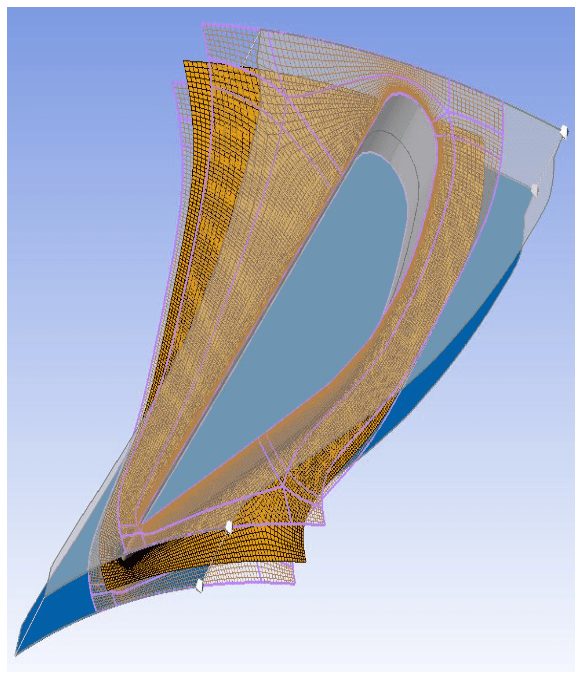
Рис.4. Расчетная сетка в межлопаточном канале соплового аппарата
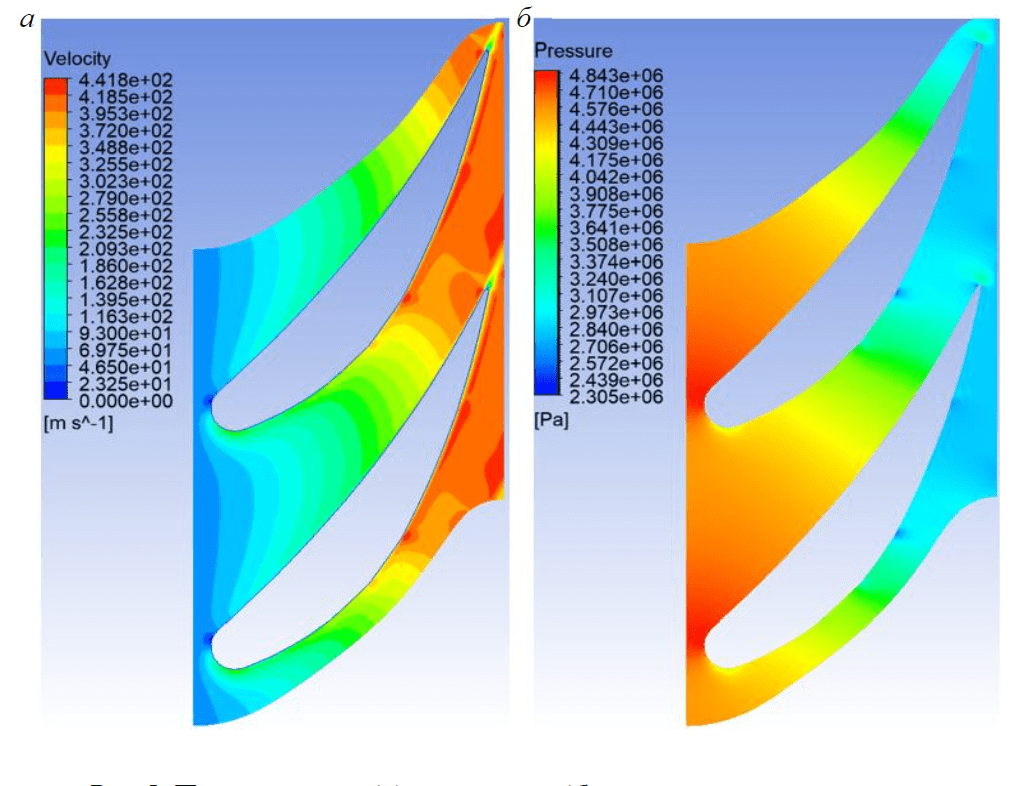
Рис.5. Поля скорости (а) и давления (б) в канале соплового аппарата
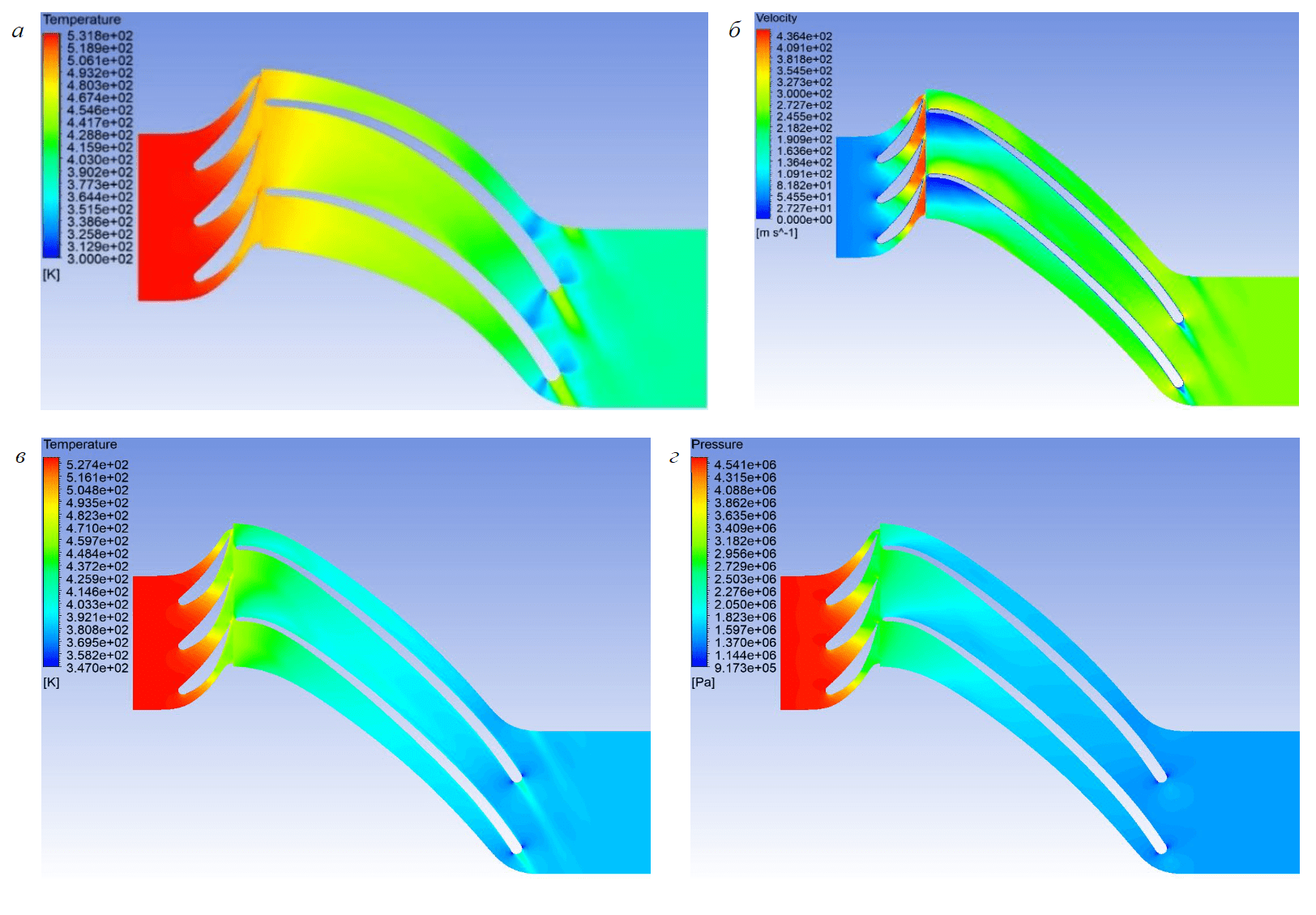
Рис.6. Поле распределения температуры (а), скоростей (б), статической температуры (в), статического давления (г)
При построении расчетной модели требуется выполнить условие приблизительного равенства площадей расчетных частей на выходе из соплового аппарата и на входе в рабочее колесо. Итоговая расчетная область представляет собой три области соплового аппарата с двумя областями рабочего колеса. Количество ячеек на расчетную область соплового канала и рабочего колеса составило примерно 1250000. Как видно по распределениям на рис.6, полученное рабочее колесо подчиняется известным физическим моделям с учетом нестандартной газовой смеси. При этом турбинная ступень подчиняется общеизвестным законам термодинамики, падают давление и температура, увеличивается скорость в конфузорном канале.
По графику выбирается α1 = 19°, что соответствует n = 89790 об/мин; КПД = 0,807. Полученные параметры ступени рабочего колеса: D1 = 80 мм; α1 = 19°; β2 = 26°; N = 198,7 кВт; КПД = 0,807; Твых = 134,14 °C; u1 = 376 м/c; n = 89790 об/мин; число лопаток рабочего колеса – 15; степень реактивности/радиальности – 0,5/0,5.
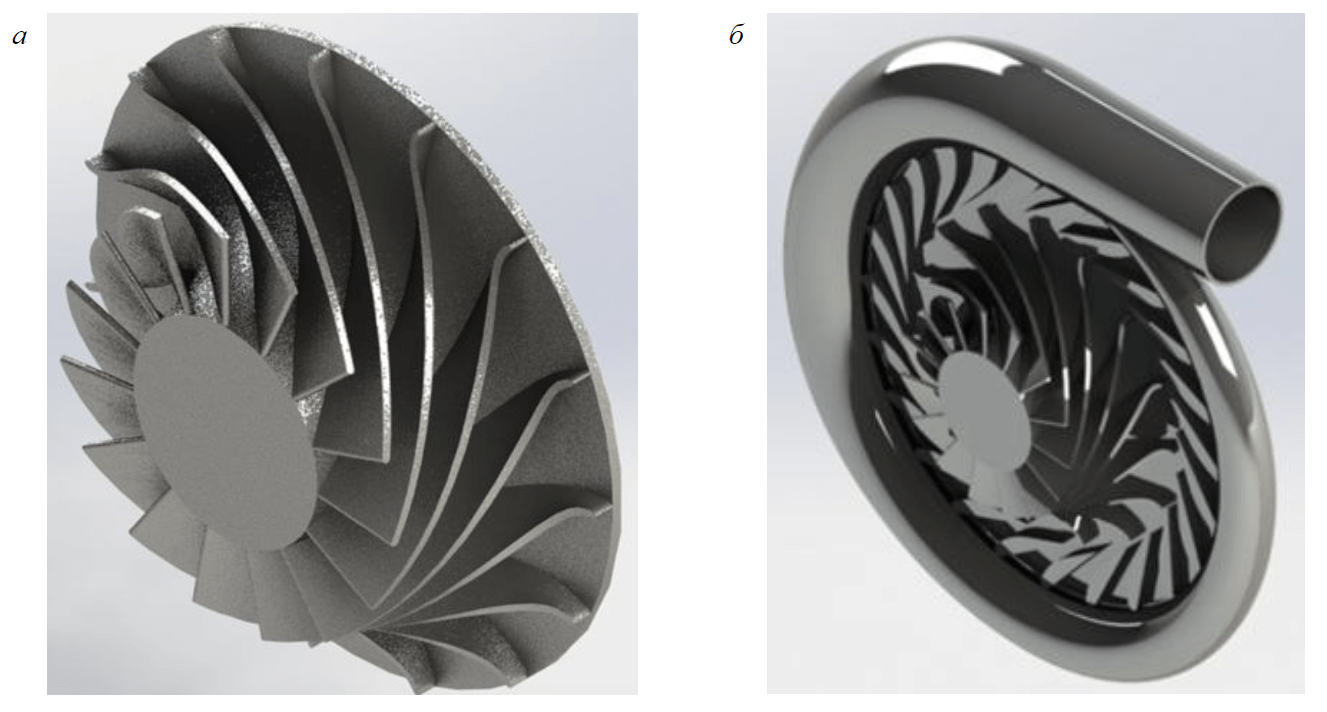
Рис.7. 3D-модель рабочего колеса (а) и улитки с рабочим колесом (б)
При помощи функционального калькулятора рассчитываются осредненные параметры полного давления на входе в сопловый аппарат, статической температуры на выходе из рабочего колеса и др. Полученные результаты численного моделирования: давление на входе P0* = 4,65 МПа; статическая температура на выходе T2 = 399 K; абсолютная скорость на выходе из рабочего колеса c2 = 98,07 м/с; момент на валу турбины по оси z на одну лопатку M = 1,5 Н·м; угол выхода потока из рабочего колеса – 64°.
Радиусы xгр окружности в сечениях и соответствующие им углы Δν: 23 мм/0°; 20,5/45; 18,8/90; 17,2/135; 15,2/180; 13,2/225; 10,6/270; 7,5/315; 0/360.
Модель рабочего колеса и вид сборки представлены на рис.7. Для оценки габаритов установки по полученным результатам в первом приближении построена геометрия улитки и сборка.
Разработанный турбодетандер предполагается применять для привода вала электрогенератора. Однако главной проблемой такого решения является высокая скорость вращения турбины и вала электрогенератора. Для обеспечения качественных параметров генерируемой электроэнергии в структуру комплекса включаются неуправляемый и активный выпрямители напряжения, а также пассивные и активные силовые фильтры высших гармоник. Полученная электроэнергия может быть направлена на питание собственных нужд комплекса или на другие цели в области расположения комплекса.
Предлагаемый подход основан на автоматизации расчета и конструировании микротурбинных детандеров, разрабатываемых специально под параметры потока и свойства рабочей среды. Полученные 3D-модели элементов детандера могут быть напечатаны на 3D-принтере, и после чистовой обработки использованы в составе детандер-генераторов (для снятия давления отходящих и дымовых газов) традиционного и органических циклов Ренкина с водой и низкокипящей средой.
Заключение
Рассмотрена схема малотоннажной установки переработки углеводородных газов, которая может применяться для широкого круга задач: утилизации низконапорного газа и ПНГ; обеспечения метанолом или синтетическими жидкими углеводородами удаленных от инфраструктуры объектов. Схема усовершенствована за счет добавления четырех микротурбинных детандерных генераторов, что позволит повысить эффективность процесса.
Выявлены основные геометрические размеры колеса турбодетандера, определено оптимальное значение угла α1, исходя из заданных характеристик входного диаметра и оборотов. Следующим этапом разработки станет исследование и улучшение аэродинамических характеристик полученного соплового аппарата и рабочего колеса, подробный расчет подводящей улитки.
Предложенная методика облегчает расчет конструктивных параметров микротурбин с учетом особенностей рабочей среды, температуры, давления и производительности подаваемого на них потока газа.
Создание микротурбогенераторов, способных работать в среде отходящих газов, паров воды и низкокипящих жидкостей, позволит повысить энергоэффективность процесса и снизить углеродный след получаемых продуктов.
Литература
- Litvinenko V. The role of hydrocarbons in the global energy agenda: The focus on liquefied natural gas // Resources. 2020. Vol. 9. Iss. 5. № 59. DOI: 10.3390/resources9050059
- Ilinova A., Chanysheva A. Algorithm for assessing the prospects of offshore oil and gas projects in the Arctic // Energy Reports. 2020. Vol. 6. Supplement 2. P. 1349-1355. DOI: 10.1016/j.egyr.2019.11.110
- Litvinenko V.S., Dvoynikov M.V., Trushko V.L. Elaboration of a conceptual solution for the development of the arctic shelf from seasonally flooded coastal areas // International Journal of Mining Science and Technology. 2021. Vol. 6. Supplement 2. P. 504-509. DOI: 10.1016/j.ijmst.2021.09.010
- Щипачев А.М., Дмитриева А.С. Применение эффекта резонансного энергоразделения в пунктах редуцирования природного газа с целью повышения энергоэффективности системы газораспределения // Записки Горного института. 2021. Т. 248. С. 253-259. DOI: 10.31897/PMI.2021.2.9
- Фейгин В.И., Брагинский О.Б., Заболотский С.А. и др. Исследование состояния и перспектив направлений переработки нефти и газа, нефте- и газохимии в РФ. М.: Экон-информ, 2011. 806 с.
- Цветков П.С., Федосеев С.В. Анализ специфики организации проектов малотоннажного производства СПГ // Записки Горного института. 2020. Т. 246. С. 678-686. DOI: 10.31897/PMI.2020.6.10
- Арутюнов В.С., Стрекова Л.Н., Савченко В.И. и др. Перспективы конверсии углеводородных газов в жидкие продукты на основе азотсодержащего синтез-газа (обзор) // Нефтехимия. 2019. Т. 59. № 3. С.246-255. DOI: 10.1134/S002824211903002X
- Леушева Е.Л., Моренов В.А. Разработка когенерационного комплекса с бинарным циклом для энергообеспечения нефтегазовых предприятий // Нефтяное хозяйство. 2017. № 7. С. 104-106. DOI: 10.24887/0028-2448-2017-7-104-106
- The World Bank. URL (дата обращения 23.03.2022).
- Statistical Review of World Energy 2022. URL (дата обращения 26.09.2022).
- Tsvetkov P., Cherepovitsyn A., Makhovikov A. Economic assessment of heat and power generation from small-scale liquefied natural gas in Russia // Energy Reports. 2020. Vol. 6. Supplement 2. P. 391-402. DOI: 10.1016/j.egyr.2019.11.093
- Iakovleva E., Belova M., Soares A. Allocation of potentially environmentally hazardous sections on pipelines // Geosciences. 2021. Vol. 11. Iss. 1. P. 1-11. DOI: 10.3390/geosciences1101000
- Цветков П.С., Федосеев С.В. Анализ специфики организации проектов малотоннажного производства СПГ // Записки Горного института. 2020. Т. 246. С. 678-686. DOI: 10.31897/PMI.2020.6.10
- Лищинер И.И., Малова О.В., Тарасов А.Л. и др. Получение метанола из забалластированного азотом синтез-газа // Катализ в промышленности. 2010. № 4. C. 50-55.
- Sultanbekov R. Beloglazov I., Islamov S. et al. Exploring of the incompatibility of marine residual fuel: A case study using machine learning methods // Energies. 2021. Vol. 14. Iss. 24. № 8422. DOI: 10.3390/en14248422
- Loseva E., Lozovsky I., Zhostkov R., Syasko V. Wavelet Analysis for Evaluating the Length of Precast Spliced Piles Using Low Strain Integrity Testing // Applied Sciences. 2022. Vol. 12. Iss. 21. № 10901. DOI: 10.3390/app122110901
- 17. Koteleva N., Loseva E. Development of an Algorithm for Determining Defects in Cast-in-Place Piles Based on the Data Analysis of Low Strain Integrity Testing // Applied Sciences. 2022. Vol. 12. Iss. 20. № DOI: 10.3390/app122010636
- Litvinenko V., Meyer B. Syngas Production: Status and Potential for Implementation in Russian Industry. Cham: Springer, 2018. 161 p. DOI: 10.1007/978-3-319-70963-5
- Ahmadi M., Alizadeh S.M., Tananykhin D. et al. Laboratory evaluation of hybrid chemical enhanced oil recovery methods coupled with carbon dioxide // Energy Reports. 2021. Vol. 7. P. 960-967. DOI: 10.1016/j.egyr.2021.02.005
- Guo Q., Ahmadi M.H., Lahafdoozian M. et al. A laboratory approach on the improvement of oil recovery and carbon dioxide storage capacity improvement by cyclic carbon dioxide injection // Energy Reports. 2021. Vol. 7. P. 1571-1580. DOI: 10.1016/j.egyr.2021.03.012
- Ostadi M., Paso K.G., Rodriguez-Fabia S. et al. Process Integration of Green Hydrogen: Decarbonization of Chemical Industries // Energies. 2020. Vol. 13. Iss. 18. № 4859. DOI: 10.3390/en13184859
- Morenov V., Leusheva E., Buslaev G. et al. System of Comprehensive Energy-Efficient Utilization of Associated Petroleum Gas with Reduced Carbon Footprint in the Field Conditions // Energies. 2020. Vol. 13. Iss. 18. № 4921. DOI: 10.3390/en13184921
- Турбодетандерные агрегаты. URL (дата обращения 23.03.2022).
- ROTOFLOW Turboexpanders. URL (дата обращения 23.03.2022).
- Микротурбины CAPSTONE. URL (дата обращения 23.03.2022).
- Загашвили Ю.В., Ефремов В.Н., Кузьмин А.М. и др. Комплекс получения синтез-газа для малотоннажного производства метанола // Нефтегазохимия. 2017. № 1. С. 19-26.
- Карташев А.Л., Мартынов А.А. Математическое моделирование и оптимизация структуры течения в ступени радиально-осевой турбины микрогазотурбинной установки // Вестник Южно-Уральского государственного университета. Серия: Машиностроение. 2015. № 3. С. 28-36.
- Пассар А.В. Влияние формы меридионального контура рабочего колеса на параметры потока газа в радиально-осевой турбине газотурбинной установки // Известия Томского политехнического университета. 2017. Т. 328. № 9. С. 33-48.
- Karimi Noughabi A., Sammak S. Detailed Design and Aerodynamic Performance Analysis of a Radial-Inflow Turbine // Applied Sciences.2018. Vol. 8. Iss. 11. № 2207. DOI: 10.3390/app8112207
- Huebner J., Kata D., Kusiński J. et al. Microstructure of laser cladded carbide reinforced Inconel 625 alloy for turbine blade application // Ceramics International. 2017. Vol. 43. Iss. 12. P. 8677-8684. DOI: 10.1016/j.ceramint.2017.03.194
- Rahbar K., Mahmoud S., Al-Dadah R.K. Development and experimental study of a small-scale compressed air radial inflow turbine for distributed power // Applied Thermal Engineering. 2017. Vol. 116. P. 549-583. DOI: 10.1016/j.applthermaleng.2017.01.100
- Батурин О.В. Профилирование рабочих колес радиально-осевых турбин с помощью кривых Безье // Вестник Самарского государственного аэрокосмического университета им. академика С.П.Королёва (национального исследовательского университета). 2011. № 3-3 (27). С. 125-130.
- Григорьев В.А., Калабухов Д.С., Радько В.М. Численное газодинамическое моделирование одноступенчатых центростремительных турбин сверхмалой мощности // Вісник двигунобудування. 2013. № 2. С. 118-124.
- Разработка технических решений в обеспечение создания отечественных высокоэффективных масштабируемых безмасляных турбогенераторов авиационного и энергетического назначения в классе мощности 100 кВт. URL (дата обращения 23.03.2022).
- Belousov A.E, Ovchinnikov E.S. Mathematical Modeling of the Operation of an Expander-Generator Pressure Regulator in Non-Stationary Conditions of Small Gas Pressure Reduction Stations // Mathematics. 2022. Vol. 10. Iss. 3. № 393. DOI: 10.3390/math10030393
- Лищинер И.И., Малова О.В., Толчинский Л.С. Модульные энерготехнологические установки «Энергосинтоп» // Газохимия: состояние и пути развития в ХХI веке. Труды Московского семинара по газохимии 2012-2013 гг. М.: Изд. центр РГУ нефти и газа имени И.М. Губкина, 2014. 140 с.
- Piven V., Zagashvili I., Kuzmin A. Natural gas emissions capture on site by small-sized noncatalytic converter of Methane to Syngas – Methanol that emulates liquid rocket engine // 2nd International Conference on Petrochemical Engineering, 23-25 July 2018, Kuala Lumpur, Malaysia. Arch Pet Environ Biotechnol. 2018. Vol. 3. Iss. 3. P. 32. DOI: 10.29011/2574-7614-C1-005