Strategy of mine ventilation control in optimal mode using fuzzy logic controllers
- 1 — Junior Researcher Mining Institute of the Ural Branch of the RAS ▪ Orcid
- 2 — Ph.D., Dr.Sci. Head of the Design and Innovation Center Mining Institute of the Ural Branch of the RAS ▪ Orcid
Abstract
The issues related to improving the efficiency of automatic ventilation control systems of mines that regulate the air supply to the mine in accordance with the need are considered. During the tests of such a system in the 3RU mine of OAO Belaruskali, the shortcomings of its existing, implementation, associated with the incorrect choice of the most difficult-to-ventilate direction, were revealed. The possibilities of implementing a control strategy, in which the system automatically determines the optimal configuration of the operating modes of fans and regulators, are demonstrated. As an alternative to the implemented algorithms, it is proposed to use a fuzzy control device to account for the nonlinearity of the dependence of the input and output parameters of ventilation equipment and to set the conditions for the optimal operating mode of the system in a declarative form. To assess the effectiveness of the proposed approach, the data of simulation modeling of the current ventilation mode and the transition from one ventilation mode to another are analyzed with comparison with the actual data of the system operation. The simulation results show that the use of an upgraded control scheme for the main ventilation fan based on fuzzy logic in the implementation of automatic ventilation control systems makes it possible to eliminate the possibility of a shortage of fresh air in the regulated directions of its movement, as well as excessive power consumption of the main ventilation fan.
Introduction
The approach to ventilation of underground mines (ventilation-on-demand) [1-3] involves the construction of automatic ventilation control systems (AVCS). The systems make it possible to regulate the volume of air supplied to the mine depending on current needs and, as a result, reduce the energy consumption of fans [4, 5]. The following requirements apply to AVCS [6]:
- to provide the required air consumption at the specified points of the distributed ventilation network in accordance with the technological regulations for the ventilation of underground mine workings of the mining enterprise;
- to ensure the minimum possible energy consumption of the main fan unit (MFU) to ensure the specified ventilation conditions;
- do not allow fluctuations in the parameters of the equipment during transients;
- the duration of the change of ventilation modes should not exceed the interval of change in the need for ventilation.
The model of the mine ventilation network is an oriented graph, each branch of which is characterized by aerodynamic drag. If a ventilation regulator is installed in the branch (for example, an automatic ventilation door – AVD), additional resistance is created. In the branches, there may be sources of air draft – ventilation installations – creating a pressure fall.
The criterion for the optimality of ventilation can be formulated as follows:
where
The first condition in (1) means that the actual air flow in the regulated sections of the ventilation network meets the regulatory requirements that ensure safe and comfortable working conditions. The second condition indicates the dependence of the fan's energy consumption not only on its own operating parameters (rotation speed), but also on the position of the ventilation regulators. The same air consumption in the ventilated areas of the mine can be provided by many combinations of their opening angles, each of which leads to different energy consumption by the fan.
The task of finding the optimal ventilation mode is to find such AVD opening angles and MFU rotation speed at which the required air consumption on the ventilation regulators will be provided, and the fan power consumption will be minimum. Ventilation regulators (AVD) must create the minimum possible additional aerodynamic drag in the workings in which they are installed, while ensuring the required air distribution in the mine.
The approach, which is based on the mine ventilation network model represented by a directed graph, is the most general approach to solving the optimization problem. Data from the current air flow sensors at the control points of the ventilation network are transmitted to a computer model of the mine ventilation network. If a deviation is detected between the required and actual air flow values, the air distribution is calculated using the ventilation network model to determine the new parameters of the control means. The parameters determined as a result of solving the air distribution problem are transmitted to the control system, which sets the calculated values of the MFU rotation speed and AVD positions. The process is repeated each time when the required and actual air consumptions at the control points mismatch.
In the real conditions of mine operation, this approach has a number of disadvantages. Firstly, it requires the installation of a large number of air flow sensors sufficient to calibrate the model, which for an underground network of workings requires significant costs for the arrangement of communication lines and subsequent maintenance. Secondly, due to the constant development of mining operations, the model of the ventilation network requires constant updating in manual mode (the length of existing mine workings is changing, worked out sites are being removed of service, new ones are being introduced) [7]. Such updating requires regular measurements by mine specialists and reflection of all changes in the model, which increases the influence of the human factor on the quality of management.
Existing implementations of ventilation equipment control systems within the framework of ventilation-on-demand projects (Garpenberg, Boliden, Sweden [8]; mines of South Africa [9]; El Teniente, Chile [10]; Totten Mine, Vale Inco Ltd, Canada [11], etc.) are characterized by relative compactness of mines working out polymetallic and iron ore deposits. However, mines on the territory of the EEU (in particular, potash deposits) are characterized by larger areas of mine fields (more than 100 km2), volumes of air supplied to the mine (more than 50,000 m3/min) and a significant number of simultaneously operating working zones (mining sites) that are very remote from each other. At the same time, the high intensity of mining operations, coupled with high mine productivity (up to 20 million tons of ore per year), leads to a constant change in the configuration of the mine workings and, accordingly, the ventilation network. These features complicate the task of operational redistribution of air while minimizing the energy consumption of the main ventilation fan.
In the approach to the construction of optimal ventilation control systems [12-14], developed at the Mining Institute of the Ural Branch of the Russian Academy of Sciences, the interpretation of operational data on the actual air distribution into the ventilation network model is excluded. At the same time, the control algorithm of the system corrects the tasks of the control means based on data on the current air flow directly to the AVD and MFU without the need to recalculate the total air distribution in the mine on the topology model of the ventilation network [15]. It is established that the necessary condition for the optimal ventilation mode is the presence of at least one fully open ventilation regulator (i.e., a position in which the additional resistance in the corresponding mining is zero). Current implementations of the systems are based on the control of ventilation equipment (AVD and MFU) using PID-control [16]. The use of fuzzy controllers has become widespread in various fields of industry [17].
The traditional use of fuzzy logic controllers in the implementation of automatic control systems is reduced to solving the problem of nonlinear conversion of input signals into output under the following conditions: the dependence of output parameters on input is unknown or difficult to calculate; there are significant dynamic disturbances and measurement noise; constant variability of the system itself, which requires constant correction of control parameters.
Fuzzy sets of the first order [18] allow to take into account the nonlinearity of the relationship of parameters, and fuzzy sets of the second order [19, 20] – to overcome the problems associated with the uncertainty of measurements of input parameters, as well as model parameters. The use of fuzzy controllers is designed to reduce the duration of the system output to the required stable state. Independent of the specific task, algorithms for configuring fuzzy controllers [21-23] allow to adjust the parameters of fuzzy control following changes in the controlled system. The rule base for a fuzzy controller can be either trivial (for example, a small control error corresponds to a small reaction of the system), or contain more complex control logic set by an expert. There are methods of automatic correction of the rule base, allowing achieving the desired characteristics of the equipment [24]. One of the applications of fuzzy control is the determination of coefficients for the PID-controller [25, 26]. Fuzzy controllers are used in a wide range of areas, including when implementing control in hydraulic systems [27, 28] and ventilation control systems (maintaining the required air parameters in stovehouses [29] and intensive care units [30], ventilation of industrial premises [31]).
The purpose of the article is to implement the AVCS management strategy, which assumes ensuring the required air consumption on ventilation regulators while minimizing the energy consumption of the main fan unit based on setting optimality conditions directly in the fuzzy controller rule base.
Methodology
To analyze the work of the existing implementation of the automatic ventilation control system, a number of tests were carried out in the conditions of the 3RU mine of OAO Belaruskali [32, 33]. This makes it possible to assess the speed of the system transition from one ventilation mode to another, its response to disturbances, the stability of the equipment and the efficiency of its functioning.
The mine AVCS consists of one surface MFU, including the main and backup fans, and six automatic louver-type regulators (AVD) installed in each of the main directions (“Sever”, “Vostok”, “Yug”) of the horizons being worked out (–420 and –620 m) [34] (Fig.1).
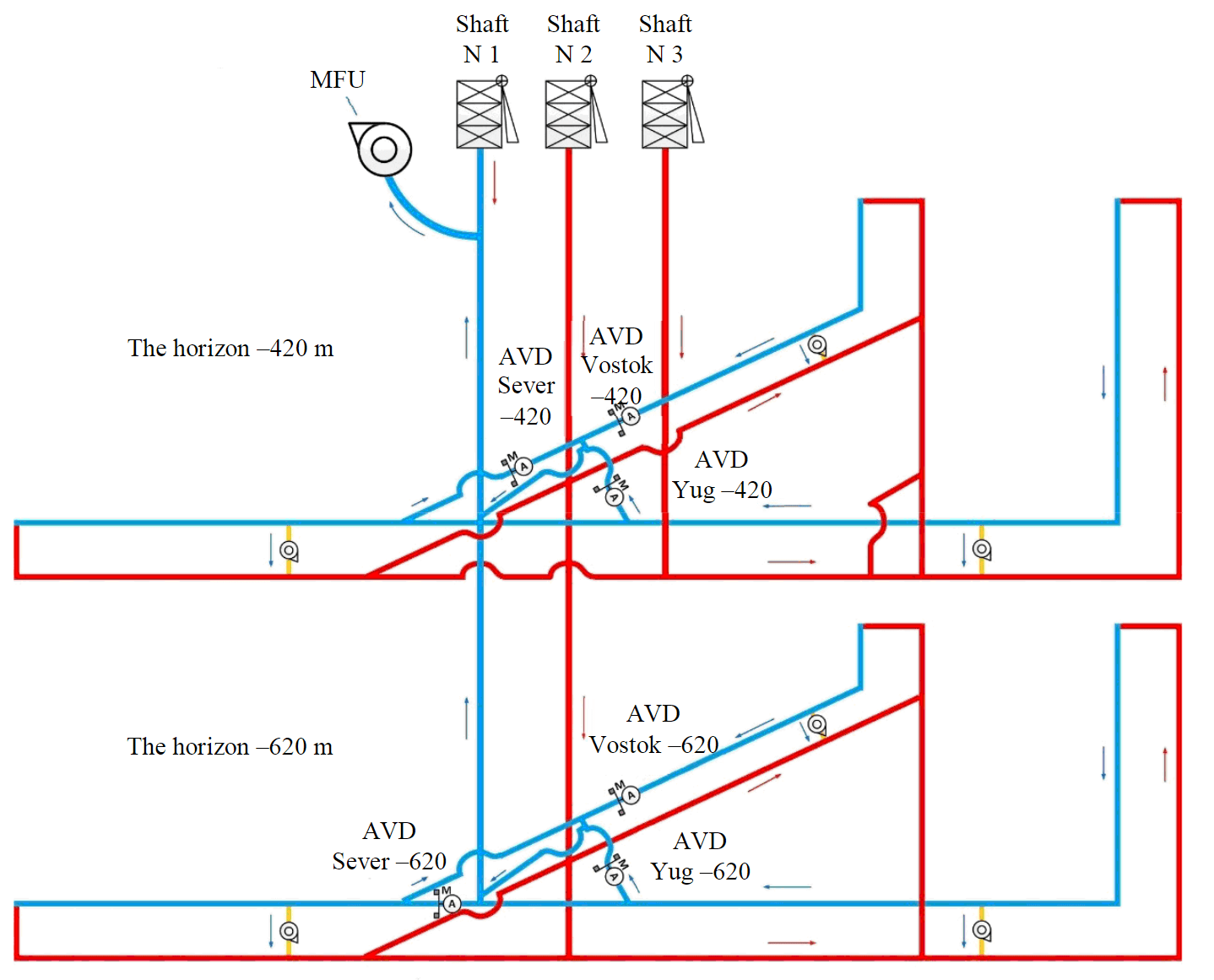
Fig.1. Schematic diagram of the ventilation of the 3RU mine of OAO Belaruskali, indicating the location of the MFU and AVD
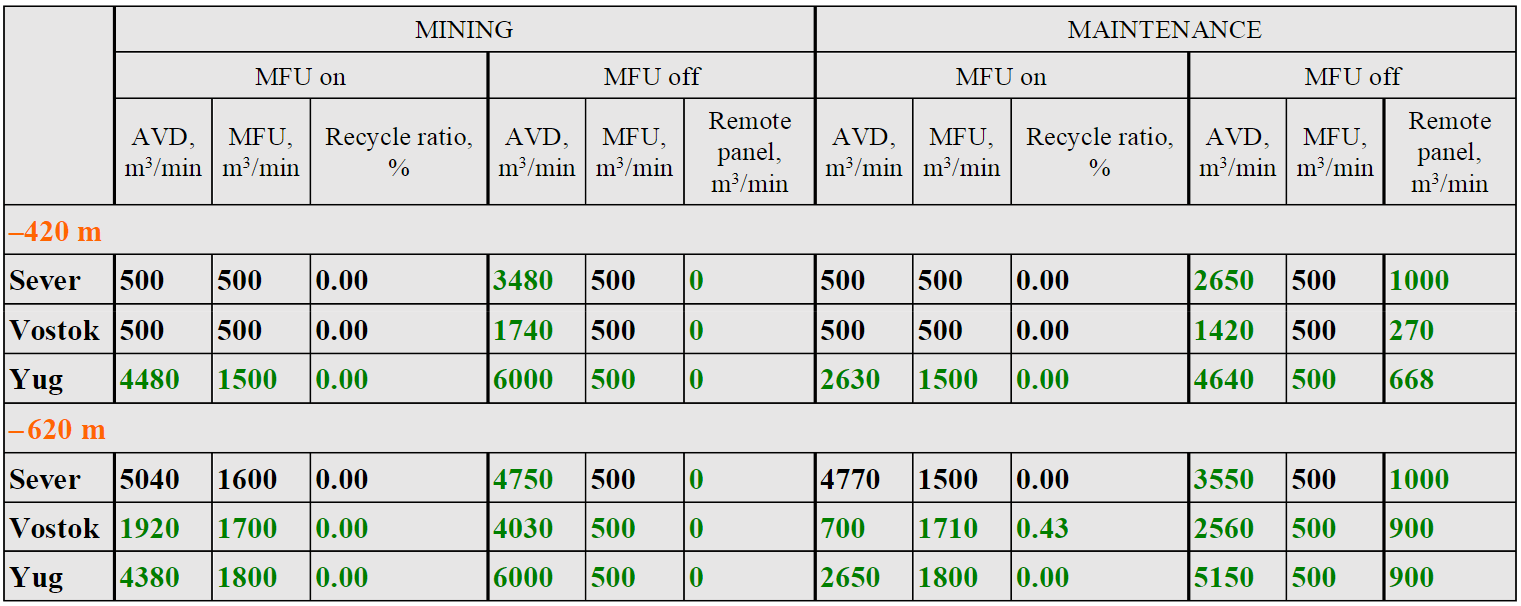
Fig.2. A fragment of the videogram of the controller interface for managing AVCS operation modes
Mine ventilation control consists in changing the rotation angles of the louver regulators depending on the deviation of the specified air flow from the actual one (if the air flow is greater than the required one, then the regulator is covered, increasing the aerodynamic drag of the mine in which it is installed, and vice versa), as well as changing the performance of the MFU (by changing the speed of the impeller). For different operating modes of the mine, the required air flow is set for each regulator (Fig.2). At the beginning of each shift, the dispatcher selects the necessary mode for each AVD, depending on whether mining operations (high air consumption) or repair work are being carried out in the direction.
The required supply of the main ventilation fan, adjustable rotation speed w, is defined as the sum of the specified costs for all regulators and the set value of external leaks (the leakage coefficient is calculated by regular measurements by the ventilation service). The calculated fan supply is adjusted for the amount of lack/excess of air in the “main” direction, at which the value of the opening angle is fixed in accordance with the preset value (Fig.3).
With optimal ventilation mode, the “main” direction corresponds to the most difficult-to-ventilate direction in which the regulator should be in the fully open position. However, due to the fact that each regulator independently determines the degree of its opening depending on the specified air flow setting, as well as the technical complexity of determining the aerodynamic drag of the corresponding output at the current time, the “main” direction is determined from the maximum value of the required air flow or is set manually by the operator. An incorrectly selected “main” direction leads to one of the situations: the main ventilation fan consumes excessive electricity, since the general configuration of the position of the regulators creates excessive resistance in the ventilation network; in one of the directions (not the “main” one), there is a lack of air when the corresponding regulator is in the fully open position.
In order to determine the possibilities for improving the AVCS control scheme, tests were carried out to assess the possibility of automatically determining the most difficult-to-control direction in the AVCS control cycle. Figure 4 shows the characteristics of the MFU and AVD installed in the mine under study.
As part of the tests, the performance of the main ventilation fan was controlled manually by means of a stepwise change in the speed of the MFU impeller, which leads to the redistribution of air in the shaft and the automatic opening of the regulator in the most difficult-to-ventilate direction. At the beginning of the tests, “–620 Yug” was chosen as the “main” direction (which corresponded to the most difficult-to-ventilate direction for the current ventilation mode according to the simulation results), for which the specified air flow was changed from 4620 to 2770 m3/min.
A sequential decrease in the MFU rotation speed (Fig.5) led to a reconfiguration of the door position, which increased the actual supply of MFU at each segment of a fixed rotation speed (by reducing the aerodynamic drag of the network).
The dynamics of the AVD position first demonstrates their cover (when the actual air consumption on the fan was excessive), then in the process of reducing the fan speed, leading to a lack of air in some directions, a gradual opening to a level corresponding to the optimal position. The fluctuations of the “AVD –620 Yug” controller are caused by the delayed effect of changing the fan operating mode on remote points of the ventilation network (i.e. the controller manages to work out the setpoint change independently before the fan has an effect). As a result, the most difficult-to-ventilate direction was “–420 Yug”, the automatic regulator on which moved to a fully open (technically possible) position.
According to the test results, it can be concluded that the automatic ventilation control system can independently determine the most difficult-to-ventilate direction, i.e. the direction with the greatest aerodynamic drag, at which the regulator will be in the most open state. In case the lack of air in the ventilation network, an increase in the air consumption supplied to the mine can be achieved just by changing the position of the regulators without increasing the fan speed, if none of the regulators is in the fully open position.
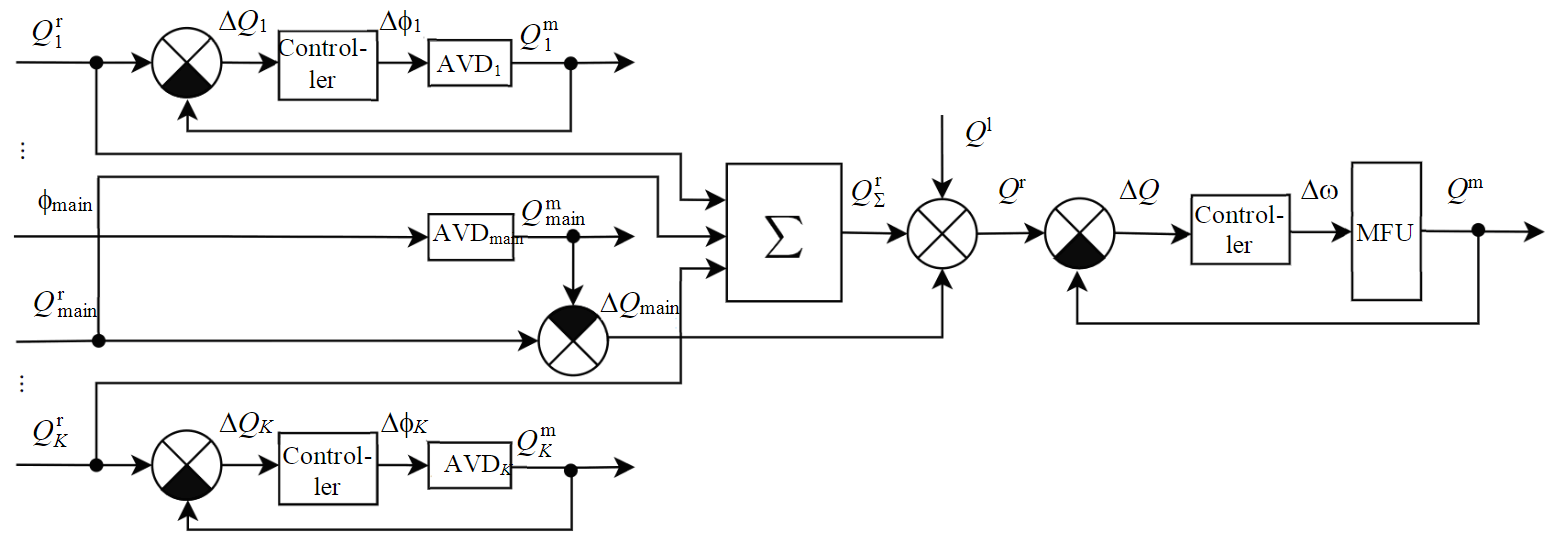
Fig.3. Information structure of the existing AVCS
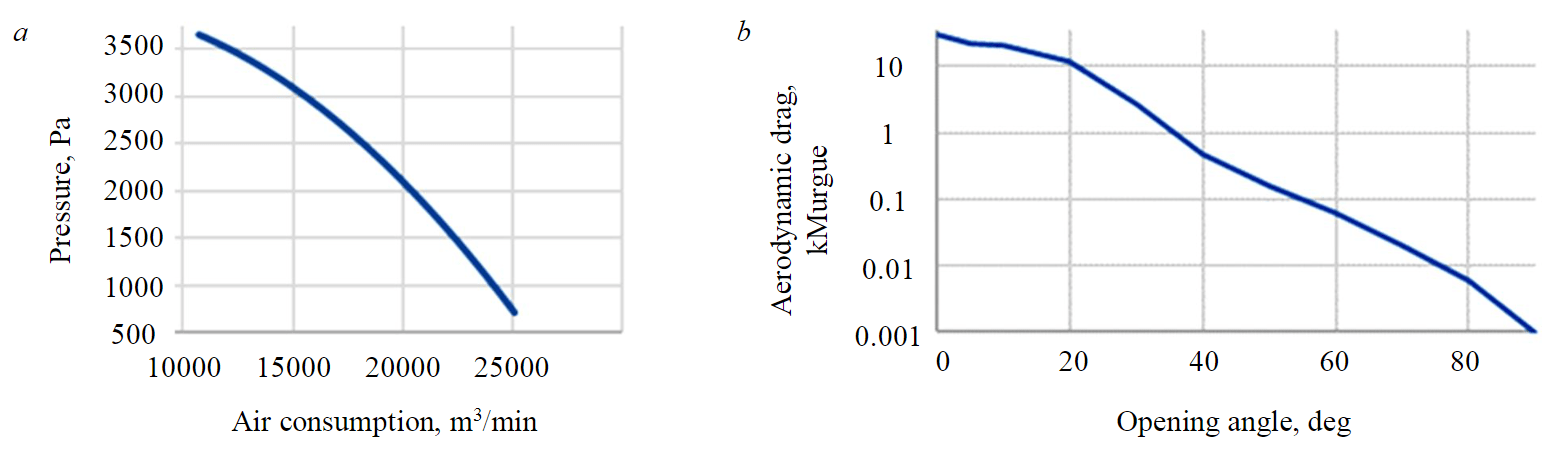
Fig.4. The dependence of the pressure on the air flow MFU (a) and the aerodynamic drag of the regulator on the opening angle (b)
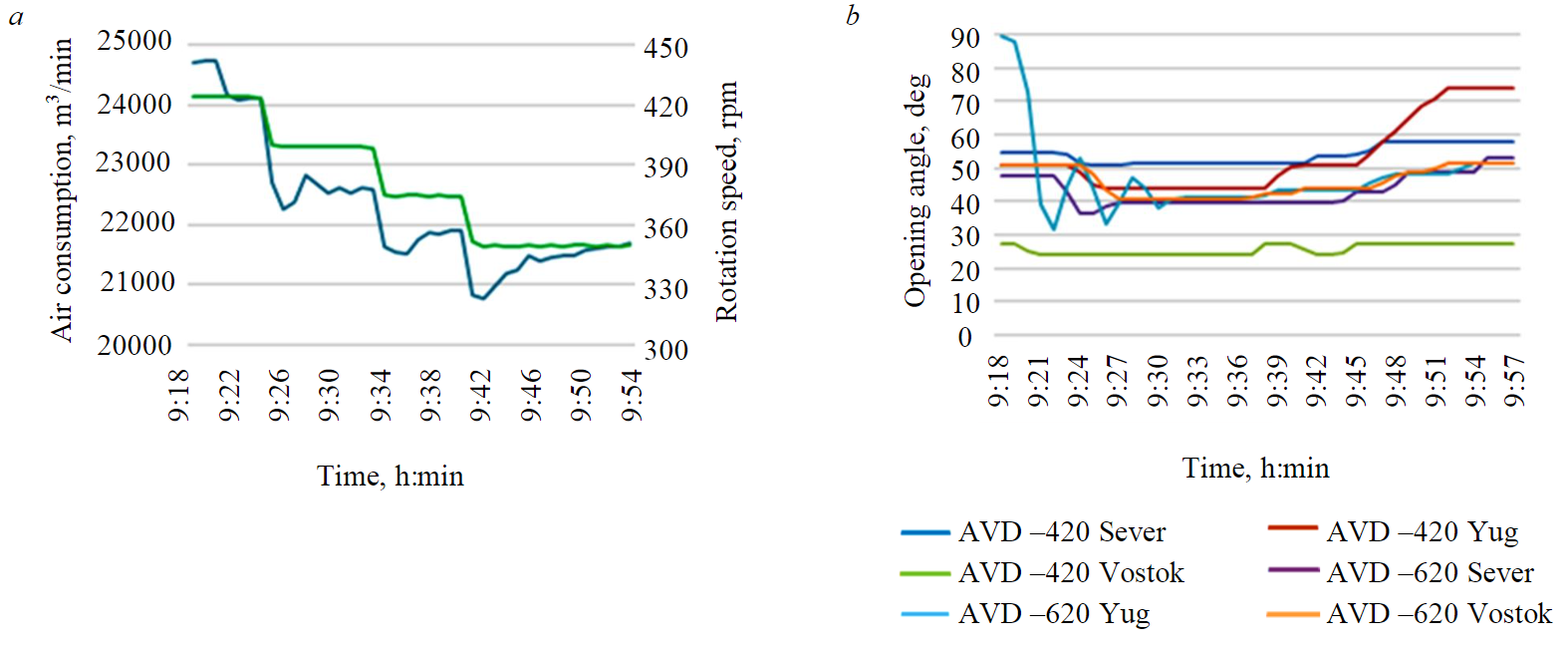
Fig.5. Air consumption per MFU (a) while changing the opening angles of the AVD (b)
To implement a management strategy that makes it possible to compensate for the side effects of excluding the predetermination of the most difficult direction, it is advisable to use a fuzzy control device due to the following circumstances:
- changing the position of the regulator in the most difficult-to-ventilate direction leads to a change in the aerodynamic drag of the ventilation network, which non-linearly affects the air flow provided by the fan;
- the use of linguistic variables and the base of production rules, defined in terms of the subject area, allows to reflect the criteria for choosing the most difficult direction.
Let us consider a mathematical description of a fan control model based on fuzzy logic. It is necessary to set fuzzy variables
where
The choice of the maximum shortage and minimum excess consumption for all regulators in expression (2) is due to the need to ensure the actual consumption is not less than the specified one, since compliance with regulatory requirements is a priority task of management;
where
For fuzzy variables, we define the following term sets:
where
Fuzzy sets that make up term sets for fuzzy variables are defined by membership functions:
where
If there is one main ventilation fan, the rules for choosing the optimal ventilation mode for a given air consumption can be formulated as follows: a given air consumption should be provided on each regulator; at least one of the regulators should be fully open (i.e. not to create additional aerodynamic drag).
The rules for fan control can be formulated as follows:
- if there is an excess of air on the controllers in the total, it is necessary to reduce the rotation speed;
- if there is a lack of air, while at least one of the controllers is fully open, it is necessary to increase the rotation speed;
- if there is a lack of air and at the same time no controller is fully open, the rotation speed remains unchanged.
If there is a lack of air in the system, but none of the regulators is fully open, the regulators change their position at a constant fan speed. During the tests, it was demonstrated that in this case the total air consumption supplied to the mine increases. Such a transfer of control from the fan to the controllers can be reflected in the logic of the rule base.
Let us consider the bases of fuzzy inference rules for determining the required increment of the fan impeller speed (Table 1) [35]. The row and column headers correspond to the sets of input variables (DQ and fmax), included in the antecedents of the rules, the values at the intersection of rows and columns correspond to the sets of the output variable from the sequence of rules.
Table 1
|
NL |
NS |
Z |
PS |
PL |
L |
NL |
NS |
Z |
PS |
PL |
M |
NS |
NS |
NS |
Z |
Z |
S |
NL |
NL |
NL |
Z |
Z |
The rule corresponding to the first row and column are as follows: if DQ – negative large, Φmax – large, then Dw – negative large.
The cells highlighted in red correspond to a situation when none of the controllers is fully open, while there is a cumulative lack of air in the system. In this case, the control signals are transmitted to the regulators: the fan frequency remains unchanged, and the controllers must be rebuilt in such a way as to reduce the overall resistance of the network to increase the total air consumption supplied to the shaft at the same fan speed.
The degree of truth of the kth rule is calculated by the formula
where
To calculate the resulting value of the output variable, the formula is used
where
Formulas (5) and (6) represent one of the options for implementing fuzzy logical inference, independent of the solution of a specific problem, in which the product operation is used to calculate the membership functions of each rule. The resulting value of the output variable is defined as the weighted average of the degrees of membership of all rules.
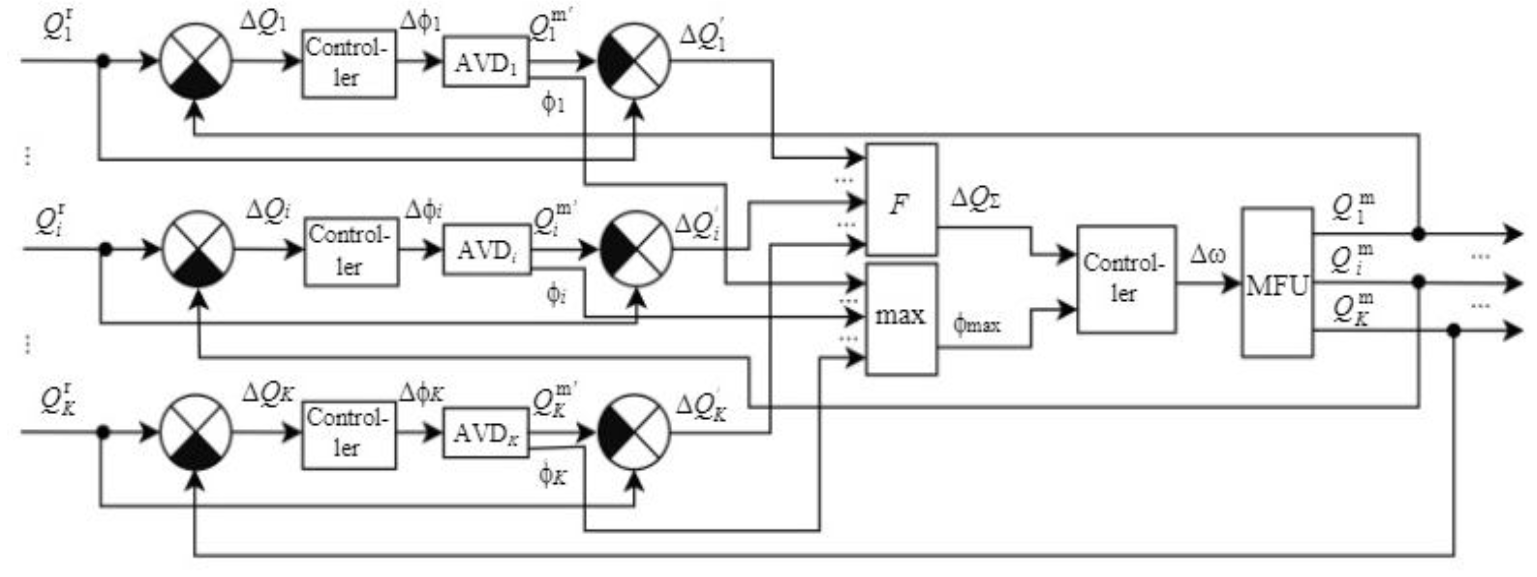
Fig.6. AVCS control scheme with automatic output to the optimal ventilation mode
Figure 6 shows an upgraded AVCS control scheme: first, the AVD changes the opening angle in accordance with the current air flow mismatch
Discussion. To evaluate the effectiveness of the proposed algorithms, the AVCS operation was modeled in the developed module for the analytical complex “AeroSet” on the ventilation network of the mine, built according to the results of air-depression survey, and the simulation results were compared with the actual data of the equipment in the following situations: the current ventilation mode with the specified air consumptions; transition from one ventilation mode to another, accompanied by a change in the set air consumptions on the ventilation regulators.
Simulation of the current ventilation mode was based on December 18, 2019 AVCS data.
Table 2
Actual and model air consumption for the current ventilation mode
AVD |
Set consumption, m3/min |
Actual consumption, m3/min |
Deviationfrom the setconsumption, % |
Model consumption, m3/min |
Deviationfrom the setconsumption, % |
|
–420 Vostok |
1420 |
1190 |
–16.2 |
1421 |
0.07 |
|
–420 Sever |
1830 |
1790 |
–2.19 |
1830 |
0.0 |
|
–420 Yug |
4590 |
5439 |
18.5 |
4596 |
0.13 |
|
–620 Vostok |
3300 |
3259 |
–1.24 |
3112 |
–5.7 |
|
–620 Sever |
3200 |
3078 |
–3.81 |
3202 |
0.06 |
|
–620 Yug |
3520 |
4021 |
14.23 |
3401 |
–3.38 |
Note. A significant lack of air is highlighted in red, an excess is highlighted in green.
Comparison of actual and specified consumptions (Table 2) shows that in the main directions the deviations of air consumptions are within 10 %, but in some areas, there is a significant overconsumption or lack of air.
In the steady-state configuration of the parameters of the AVCS elements, according to the simulation results, the air consumption on the fan is 19997 m3/min at 352 rpm, while the actual fan performance is 19292 m3/min at 373 rpm.
Comparison of the position of automatic ventilation doors on the design model and in the control system (Table 3) shows that the configuration of the door position in the AVCS is set in a non-optimal way.
Table 3
Actual and model opening angles of the controllers for the current ventilation mode
AVD |
Actual opening angle, deg |
Model opening angle, deg |
AVD |
Actual opening angle, deg |
Model opening angle, deg |
|||||
–420 Vostok |
24 |
35 |
–620 Vostok |
47 |
90* |
|||||
–420 Sever |
45 |
37 |
–620 Sever |
40 |
62 |
|||||
–420 Yug |
77* |
78 |
–620 Yug |
44 |
90* |
* Controllers with the maximum opening angle.
The “main” direction in AVCS is the “–420 Yug” direction (the largest value of the required air consumption), which leads to suboptimal operation of the fan to ensure the specified air consumptions. Based on the simulation results, the most difficult-to-ventilate direction is “–620 Vostok” or “–620 Yug”.
AVCS operation data for February 26, 2019 were used to simulate changes in the ventilation mode. During the day, the required air consumption was changed on several controllers, which led to a significant redistribution of air throughout the mine (Table 4).
Table 4
Actual and model air consumption when changing the ventilation mode
AVD |
Initial set consumption, m3/min |
Final set consumption, m3/min |
Final actual consumption, m3/min |
Deviation from the specified consumption, % |
Final model consumption, m3/min |
Deviation from the specified consumption, % |
–420 Vostok |
1400 |
1400 |
1420 |
1.4 |
1411 |
0.8 |
–420 Sever |
2510 |
2810 |
2812 |
0.0 |
2817 |
0.2 |
–420 Yug |
4290 |
2880 |
3006 |
4.3 |
2884 |
0.1 |
–620 Vostok |
2890 |
2890 |
2954 |
2.2 |
2955 |
2.2 |
–620 Sever |
2620 |
2620 |
2592 |
–1.1 |
2624 |
0.2 |
–620 Yug |
5310 |
3800 |
3929 |
3.4 |
3609 |
–5.0 |
The use of algorithms based on fuzzy control allows the MFU to reach the specified ventilation mode faster (Fig.7). A significant subsidence of the rotation speed, as well as the opening angle of the controller in the most difficult-to-ventilate direction “–620 Yug”, is due to a significant reduction in the required air consumption on this controller and the working out of this AVD setpoint to reduce the actual air consumption on the MFU, which is justified from the point of view of control stability. The return of the “AVD –620 Yug” controller to the fully open state confirms the ability of the system itself to determine the most difficult direction.
In this situation, the “main” direction in the AVCS is set correctly and corresponds to the condition of the largest air consumption. The set air consumption in the case of actual and model data is within the permissible 5 % range of deviations.
Conclusion
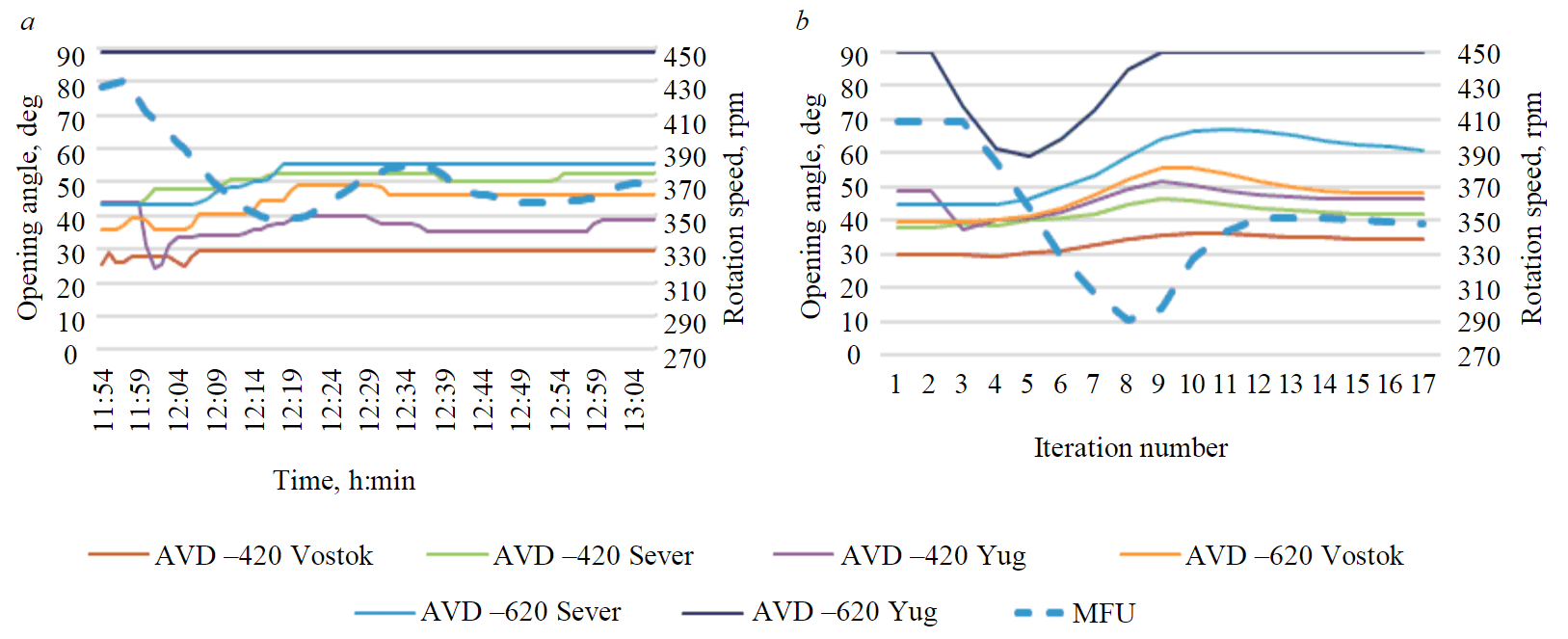
Fig.7. Change in the opening angles of the controllers and the rotation speed of the MFU during the transition from one ventilation mode to another: MFU and AVD AVCS data (a), simulation results (b)
The conducted studies have shown that when implementing AVCS, the preliminary choice of the most difficult-to-ventilate direction based on the largest air consumption (or at the discretion of the operator) can lead to the failure to provide the specified consumptions in the directions and the overconsumption of electricity by the fan.
The proposed approach to the formation of the fuzzy controller rule base makes it possible to realize the possibility of automatically selecting the most difficult-to-ventilate direction, the AVCS output to the optimal ventilation mode is provided, minimizing the energy consumption of the MFU.
The upgraded control scheme was tested on an up-to-date model of the ventilation network of the 3RU mine of OAO Belaruskali, while the results of model calculations were compared with the actual AVCS data for specific time intervals of its operation.
The proposed ventilation management strategy eliminates the lack of air in regulated directions without the need for external control.
References
- Acuña E., Alvarez R., Hurtado J. Updated Ventilation on Demand review: implementation and savings achieved. Proceedings of the 1st International Conference of Underground Mining, 19-21 October 2016, Chile, Santiago. 2016, p. 606-617.
- De Vilhena Costa L., Margarida da Silva J. Cost-saving electrical energy consumption in underground ventilation by the use of ventilation on demand. Mining Technology. 2019. Vol. 129. Iss. 1, p. 1-8. DOI: 10.1080/25726668.2019.1651581
- Chatterjee A., Zhang L., Xia X.Optimization of mine ventilation fan speeds according to ventilation on demand and time of use tariff. Applied Energy. 2015. Vol. 146, p. 65-73. DOI: 10.1016/j.apenergy.2015.01.134
- Hardcastle S., Kocsis C., Lacroix R. Strategic mine ventilation control: a source of potential energy savings. Proceedings of Montreal Energy & Mines, Montreal, Canada. 2007, p. 255-263.
- Moreau K., Laamanen C., Bose R. et al. Environmental impact improvements due to introducing automation into underground copper mines. International Journal of Mining Science and Technology. 2021. Vol. 31. N 6. p. 1159-1167. DOI: 10.1016/j.ijmst.2021.11.009
- Kazakov B.P., Shalimov A.V., Kiryakov A.S. Energy-saving mine ventilation. Journal of Mining Science. 2013. Vol. 49. N 3, p. 475-481. DOI: 10.1134/S1062739149030155
- Semin M.A., Grishin E.L., Levin L.Y., Zaitsev A.V. Automated ventilation control in mines. Challenges, state of the art, areas for improvement. Journal of Mining Institute. 2020. Vol. 246, p. 623-632. DOI: 10.31897/PMI.2020.6.4
- Sjöström S., Klintenäs E., Johansson P., Nyqvist J. Optimized model-based control of main mine ventilation air flows with minimized energy consumption. International Journal of Mining Science and Technology. 2020. Vol. 30. N 4, p. 533-539. DOI: 10.1016/j.ijmst.2020.05.016
- Nel A.J.H., Arndt C., Vosloo J.C., Mathews M.J. Achieving energy efficiency with medium voltage variable speed drives for ventilation-on-demand in South African mines. Journal of Cleaner Production. 2019. Vol. 232, p. 379-390. DOI: 10.1016/j.jclepro.2019.05.376
- Acuña E., Feliú A. Considering ventilation on demand for the developments of the New Level Mine Project, El Teniente. Deep Mining 2014: Proceedings of the Seventh International Conference on Deep and High Stress Mining, Australian Centre for Geomechanics, Perth, Australia. 2014, p. 813-821. DOI: 36487/ACG_rep/1410_59_Acuna
- Acuña E., Allen C. Ventilation control system implementation and energy consumption reduction at Totten Mine with Level 4 Tagging and future plans. Proceedings of the First International Conference on Underground Mining, Technology, Canada, Sudbury. 2017, p. 89-95. DOI: 10.36487/ACG_rep/1710_06_Acuna
- Semin M.A., Kruglov Yu.V. Dynamic boundary conditions of the fan type in non-stationary problems of mine ventilation. Gornyi informatsionno-analiticheskii byulleten. 2012. N 5, p. 259-263 (in Russian).
- Kruglov Y.V., Levin L.Y., Zaitsev A.V. Calculation method for the unsteady air supply in mine ventilation networks. Journal of Mining Science. 2011. Vol. 47. N 5, p. 651-659. DOI: 10.1134/S1062739147050145
- Maltsev S.V., Kazakov B.P., Semin M.A. Development of ways to improve the efficiency of ventilation of mines with complex ventilation systems. Izvestiya Tulskogo gosudarstvennogo universiteta. Nauki o Zemle. 2019. N 4, p. 283-291 (in Russian).
- Kruglov Yu.V., Semin M.A., Zaitsev A.V. Mathematical Simulation of Optimal Automatic Ventilation Control Systems Operation in Underground Mines. Izvestija Tulskogo gosudarstvennogo universiteta. Nauki o zemle. 2011. N 2, p. 116-126 (in Russian).
- Kruglov Iu.V., Semin M.A. Improving the algorithm of effective air management in ventilation systems of complex Perm Journal of Petroleum and Mining Engineering. 2013. Vol. 12. N 9, p. 106-115 (in Russian).
- Precup R.-E., Hellendoorn H. A survey on industrial applications of fuzzy control. Computers in Industry. 2011. Vol. 62. Iss. 3, p. 213-226. DOI: 10.1016/j.compind.2010.10.001
- Pal S.K., Mandal D.P. Fuzzy Logic and Approximate Reasoning: An Overview. IETE Journal of Research. 1991. Vol. 37. Iss. 5-6, p. 548-560.
- Tai K., El-Sayed A.-R., Biglarbegian M. et al. Review of recent type-2 fuzzy controller applications. Algorithms. 2016. Vol. 9. Iss. 2. N 39. DOI: 10.3390/a9020039
- Rojas J.D., Salazar O., Serrano H. Nie-Tan Method and its Improved Version: A Counterexample. Ingeniería. 2016. Vol. 21. N 2, p. 138-153. DOI: 10.14483/udistrital.jour.reving.2016.2.a02
- García P., García C.A., Fernández L.M. et al. ANFIS Based Control of a Grid-Connected Hybrid System Integrating Renewable Energies, Hydrogen and Batteries. IEEE Transactions on Industrial Informatics. 2014. Vol. 10. N 2, p. 1107-1117. DOI: 10.1109/TII.2013.2290069
- Pratihar D.K., Hui N. Evolution of Fuzzy Controllers and Applications. Studies in Computational Intelligence. 2007, 47-69. DOI: 10.1007/978-3-540-72377-6_3
- Duy-Trung Nguyen, Ngoc-Khoat Nguyen, Hung-Lan Le, Van-Tiem Nguyen. Designing PSO-Based PI-type Fuzzy Logic Controllers: A Typical Application to Load-Frequency Control Strategy of an Interconnected Hydropower System. Proceedings of the 2019 3rd International Conference on Automation, Control and Robots, 11-13 October 2019, Prague, Czech Pepublic. China University of Geosciences, 2019, p. 61-66. DOI: 10.1145/3365265.3365278
- Kondratenko Y., Kondratenko G., Sidenko I. Two-stage method of fuzzy rule base correction for variable structure of input vector. Proceedings of 2017 IEEE First Ukraine Conference on Electrical and Computer Engineering (UKRCON), 29 May – 2 June 2017, Kiev, Ukraine. IEEE, 2017, p. 1043-1049. DOI: 10.1109/UKRCON.2017.8100409
- Bejarbaneh E., Bagheri A., Bejarbaneh B. et al. A new adjusting technique for PID type fuzzy logic controller using PSOSCALF optimization algorithm. Applied Soft Computing. 2019. Vol. 85. DOI: 10.1016/j.asoc.2019.105822
- Kirui G., Wang J. Design of a Fuzzy FOPID Controller for Power Level Control of a Pressurized Water Reactor. Proceedings of the 2020 12th International Conference on Machine Learning and Computing (ICMLC 2020), 15-17 February 2020, Shenzhen, China. Association for Computing Machinery, 2020, p. 549-553. DOI: 10.1145/3383972.3384004
- Ksantini M., Ellouze A., Delmotte F. Control of a hydraulic system by means of a fuzzy approach. An International Journal of Optimization and Control: Theories & Applications. 2013. Vol. 3. N 2, p. 121-131. DOI: 10.11121/ijocta.01.2013.00153
- Tamilselvan G.M., Aarthy P. Online tuning of fuzzy logic controller using Kalman algorithm for conical tank system. Journal of Applied Research and Technology. 2017. Vol. 15, p. 492- DOI: 10.1016/j.jart.2017.05.004
- Hameed I.A.Simplified architecture of a type-2 fuzzy controller using four embedded type-1 fuzzy controllers and its application to a greenhouse climate control system. Proceedings of the Institution of Mechanical Engineers. Part I: Journal of Systems and Control Engineering. 2009. Vol. 223. N 5, p. 619-631. DOI: 10.1243/09596518JSCE708
- Saritas I., Etik N., Allahverdi N., Sert I. Fuzzy expert system design for operating room air-condition control systems. Expert Systems with Applications. 2007. Vol. 36. Iss. 6, p. 23-30. DOI: 10.1016/j.eswa.2009.02.028
- Fashchilenko V.N., Varfolomeev S.V. Drive Control System for Suction-And-Exhaust Ventilation of Processing Plants. Mining informational and analytical bulletin. 2015. N 2, p. 182-188 (in Russian).
- Grishin E.L., Nakaryakov E.V., Trushkova N.A., Sannikovich A.N. Experience in implementation of dynamic mine ventilation control. Gornyi zhurnal. N 8, p. 103-108 (in Russian). DOI: 10.17580/gzh.2018.08.15
- Semin M.A., Levin L.Y., Maltsev S.V.Development of automated mine ventilation control systems for belarusian potash mines. Archives of Mining Sciences. 2020. Vol. 65. N 4, p. 803-820. DOI: 10.24425/ams.2020.135178
- Kashnikov A.V., Levin L.Y. Applying machine learning techniques to mine ventilation control systems. Proceedings of 2017 XX IEEE International Conference on Soft Computing and Measurements (SCM), 24-26 May 2017, St. Petersburg, Russia. IEEE, 2017, p. 391-393. DOI: 10.1109/SCM.2017.7970595
- Kashnikov A.V., Levin L.Y. Fan and Regulators Fuzzy Control in Mine Ventilation Systems. Proceedings of 2019 XXII International Conference on Soft Computing and Measurements (SCM), 23-25 May 2019, St. Petersburg, Russia. IEEE, 2019, p. 85-88. DOI: 10.1109/SCM.2019.8903698