Justification of the use of a vegetal additive to diesel fuel as a method of protecting underground personnel of coal mines from the impact of harmful emissions of diesel-hydraulic locomotives
- 1 — Ph.D., Dr.Sci. Professor Saint Petersburg mining university ▪ Orcid ▪ Elibrary ▪ Scopus ▪ ResearcherID
- 2 — Postgraduate Student Saint Petersburg mining university ▪ Orcid
- 3 — Ph.D., Dr.Sci. Director Institute of Mining and Civil Engineering TU "Freiberg Mining Academy" ▪ Orcid ▪ Scopus
Abstract
Equipment with diesel engines is used in all mining enterprises. Monorail diesel transport is of great importance in coal mines, as it facilitates the heavy labor of workers when transporting materials and people, fixing mining workings, refueling and repairing equipment, which leads to an increase in the speed of tunneling operations. Reducing the concentration of harmful gases from diesel-hydraulic locomotives at the workplaces of coal mine locomotive drivers can be ensured by the use of additives to diesel fuel that reduce the volume of harmful gas emissions during the operation of diesel-hydraulic locomotives. Additive ester-based on vegetal oil in the amount of 5 mass % in a mixture with hydrotreated diesel fuel reduces the concentration of carbon monoxide by 19-60 %, nitrogen oxides by 17-98 %, depending on the operating mode of the engine, the smoke content of the exhaust gases is reduced to 71 %. There is an improvement in working conditions at the workplace of the driver of a diesel-hydraulic locomotive by the chemical factor due to the reduction of the class of working conditions from 3.1. to 2.
Introduction. Diesel-hydraulic locomotives (DHL) are increasingly used every year in the mining industry, in particular, in coal mines, significantly increasing labor productivity in the transportation of technical and fuel and lubricants, carrying out repair and rigging works, construction and repair of underground roads [22, 24], transportation of people [6, 29, 31] and other activities. In mining companies that use DHL, the air of the working areas is polluted by exhaust gas components. The increase in the concentration of nitrogen oxides and carbon monoxide in the air of the working zones leads to occupational diseases of coal mine personnel, about 3 % of which are associated with the toxic effects of these gases (Fig.1). The benefits of using DHL in coal mines can be achieved only by minimizing harmful emissions, which can lead to occupational diseases of the respiratory system [43, 44].
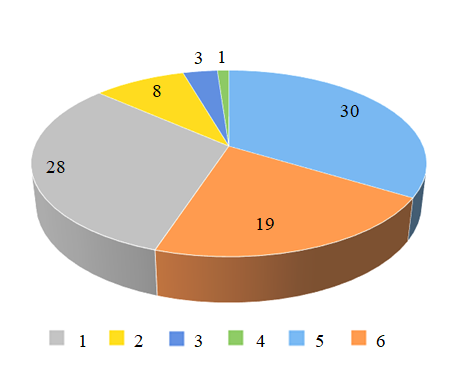
Due to the variability of the gas composition of the air in the working areas, it is of particular importance to determine the nature of the combined effect of the main components of the exhaust gases and to normalize the working conditions of workers by the chemical factor in coal mines [32].
Scientists have been working for many decades to reduce the health effects of DHL exhaust gases. The influence of harmful substances of exhaust gases on the health of workers at different concentrations is most detailed in the works of A.G.Chebotarev [11, 12]. The need to normalize harmful emissions in the air of working areas in coal mines in connection with a significant excess of the maximum permissible concentrations is described in the works of foreign scientists [38 - 40]. Many scientists have studied the chemical composition of the air in the working areas and the physical characteristics of DHL engines before and after the use of filters [13, 18], alternative fuels [21, 37] and various engine modifications [17, 42]. Electronically controlled engines were considered as an effective method of reducing emissions [26, 27, 30], but in this method, the emission concentration is reduced only to values exceeding the maximum permissible concentrations (MPC) allowed by the current norms in the Russian Federation. It is obvious that the development of a method to protect the underground personnel of coal mines from the harmful emissions of diesel-hydraulic locomotives is an urgent task.
Methodology. The characteristics of the obtained fuel with additives were studied for compliance with the requirements of GOST R 52368 [36]. The determination of the group hydrocarbon composition of representative samples of diesel fuel (DF) and diesel fuel with an additive was carried out on a gas chromatography-mass spectrometer GCMS-QP2010 SE Shimadzu.
The determination of the harmful substances amount in the exhaust gases when using DF is performed using the following methods:
• GOST R 56163-2019 “Emissions of pollutants into the atmosphere. A method for calculating the emissions of pollutants into the atmosphere by stationary diesel installations (new and after major repairs) of various capacities and purposes during their operation” [14].
• Calculation of the maximum one-time emissions of the i-th substance during the operation of the ZETOR 1404 turbo engine.
Studies of the amount of harmful gases and smoke content in the exhaust gases were carried out using the INFRAKAR VEKM.413311.002 PS smoke meter and the INFRAKAR D VEKM.415311.007 PS smoke meter.
Discussion. From the analysis of the air composition of the working areas of the SUEK-Kuzbass JSC coal mines, performed by the authors, it follows that the greatest excess of the MPC falls on carbon monoxide and nitrogen oxides [12]. These gases have a negative impact on the health of personnel, causing occupational diseases of the respiratory system [16]. Emissions of nitrogen oxides and carbon monoxide are formed in the air of working areas during fires, coal oxidation, and fuel combustion. To determine the presence of carbon monoxide and nitrogen oxides in the air of the working areas, gas measurements were carried out on the outgoing jet in the workings of the excavation site, in which DHL is used (Table 1).
Table 1
The concentration of emissions in the air of the working areas during the operation of the DHL
Number of DHL routes | Gas content in the air | |||
СО2, % | О2, % | СО, ppm | Nitrogen oxides, ppm | |
4 | 3,13 | 16,07 | 15 | 2 |
2 | 2,36 | 20,93 | 9 | 0,8 |
1 | 2,01 | 22,48 | 6 | 0,2 |
As can be seen from Table 1, the more simultaneously moving DHL is located in the mine, the more the concentration of carbon monoxide and nitrogen oxides in the mine atmosphere increases. It can be concluded that DHL is the main source of these gases in the mine air.
The mines of SUEK-Kuzbass JSC currently use mainly outboard diesel-hydraulic locomotives DLZ110F, DLZ110F-180-4, DLZ110F-180-6 from Ferri, DZ 1800 from SCHARF and KPCS-96 from Becker, as well as ground-mounted DHL KSZS-148. The largest number of working DHL falls on the mines “Named after V.D.Yalevskiy” and “Named after S.M.Kirov”. The working time of the DHL is 3 shifts of 7 hours, the number of covered routes is from 1 to 4 [12].
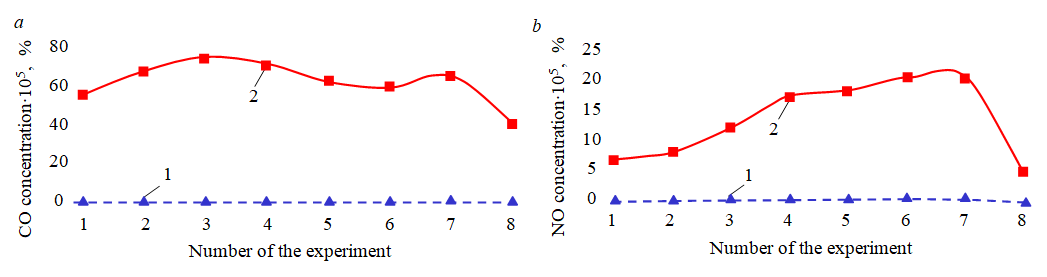
On the example of “Named after V.D.Yalevskiy” mine layout, mining workings are considered, in which the reduction of exhaust gas emissions of DHL can lead to a significant positive effect not only as a normalization of the air parameters of the working areas, but also in terms of reducing the amount of air supplied to the workings for ventilation. Such workings include dead-end parts of the preparatory workings, dismantling chambers, supported workings that are ventilated at the minimum air speed, workings with two or more routes of diesel-hydraulic locomotives, etc.
When analyzing the volumes of carbon monoxide and nitrogen oxides in the outgoing jet of the “Named after V.D.Yalevskiy” mine of the SUEK-Kuzbass JSC during the operation of diesel-hydraulic transport and in its absence, a significant discrepancy in the values was revealed. Figure 2 shows the concentration of carbon monoxide and nitrogen oxides, respectively, during the operation of diesel-hydraulic locomotives and during the DHL downtime.
From Fig.2, it can be concluded that the concentration of carbon monoxide and nitrogen oxides on the main outgoing jet when using DHL increases by more than 90 % in comparison with the amount of gases in the air in the absence of DHL.
The composition of the air on the DHL exhaust on the basis of the protocols provided by SUEK-Kuzbass JSC for the mines “Named after V.D.Yalevskiy”, “Komsomolets” and “Named af-ter S.M.Kirov” showed that the concentration of carbon oxides (0.0028, 0.0072 and 0.01688 vol.%) exceeds the permissible norm (0.0017 vol.%) on the DHL exhaust. The concentration of nitrogen oxides (0.0017; 0.0021 and 0.0084 vol.%) also exceeds the maximum permissible concentration (0.00035 vol.%).
The average quantitative and qualitative characteristics of pollutants in the air of the working areas at the “Named after S.M.Kirov” mine of SUEK-Kuzbass JSC are shown in Table 2.
Table 2
Composition of harmful air impurity in working areas and MPC values [9]
Measurement point | Gasconcentration, vol. % | |||
Nitrogen oxides | Carbon dioxide | Carbon monoxide | Oxygen | |
Workplace of the DHL driver | 0,000641 | 0,042 | 0,00182 | 20,921 |
On the outgoing jet | 0,000021 | 0,033 | 0,00061 | 20,921 |
On the exhaust (minimum load) | 0,000802 | 2,021 | 0,00421 | 16,064 |
On the exhaust (maximum load) | 0,001403 | 2,042 | 0,00762 | 16,052 |
20 m from the DHL | 0,000011 | 0,122 | 0,00014 | 20,622 |
MPC | 0,000252 | – | 0,00173 | – |
Thus, it can be seen that the applied methods of protection against harmful emissions at the studied mines of JSC SUEK-Kuzbass do not allow reducing the concentration of harmful substances in the exhaust gases to the requirements of the hygienic standards of GN 2.2.5.1313-03 and recommendations for the use of diesel-powered transport vehicles in coal mines.
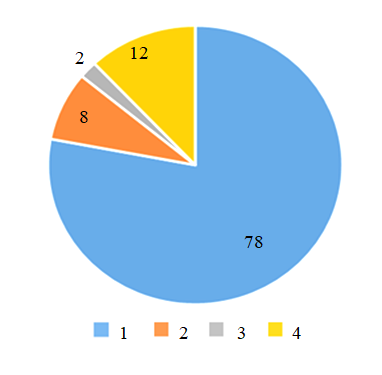
The main methods of collective protection measures (CPM) against the influence of harmful gases, such as the use of filters and catalysts, as well as intensive ventilation, are not always effective [15, 19, 20]. As an additional measure to reduce harmful emissions from DHL, it is proposed to use additives in diesel fuel based on esters [2, 11, 41]. To make additives to diesel fuel, two methods were used: transesterification of vegetal oil and esterification of fatty acids [8, 34, 35]. Laboratory studies have shown that the best characteristics of the compounds obtained in the process of transesterification of vegetal oil in comparison with the substances obtained by the process of esterification of fatty acids. Rational parameters of the transesterification process: temperature 195 0С, reaction time 4 h, mixing speed 250 rpm, raw material ratio oil:alcohol 2:1.Common raw materials for the production of additives are vegetal oils (Table 3).
Table 3
Physical and chemical parameters of vegetal oil additives [21]
Characteristic | Corn oil | Flax oil | Cameline oil |
Ester content, % | 94 | 95 | 96,5 |
Density at 20 0C, kg/m3 | 0,8759 | 0,872 | 0,87658 |
Viscosity at 40 0C, mm2/s | 4,493 | 5,1 | 4,5717 |
Flash point, °C | 122 | 135 | 152 |
Sulfur, mg/kg | 8,52 | 6,9 | 5,6 |
Cetane number | 51 | 53 | 56 |
Solidification temperature, °C | –7 | –9 | –11 |
Refractive index | 1,4506 | 1,4506 | 1,4507 |
Fractional composition, °C | 299-351 | 280-309 | 275-302 |
The conducted studies have established that cameline oil and diatomic alcohol – ethylene glycol can be used as raw materials for the production of additives [11] (Fig.3).
Since additives can affect the properties of fuel in different ways when they are compounded with diesel fuel, it is necessary to study the characteristics of diesel fuel with each of the obtained additives [1, 14] (Table 4). Additives 1-3 are obtained on the basis of various raw materials (flax and corn are the most common food crops in Russia, camelina is a non-food raw material suitable for growing in most climatic zones of Russia); 4-6 are additives obtained from cameline oil and various alcohols (monatomic and diatomic).
Analysis of operational and environmental characteristics of fuel with additives (Table 4), showed that fuel with an additive 5 obtained from cameline oil has better properties in comparison with additives from other vegetal oils [3, 28].
For the research, a sample of diesel fuel with an additive 5 in the amount of an additive of 5 mass % was selected, since this sample belongs to the EURO 5 environmental class in terms of sulfur content and has the best lubricity (the main indicator of the service life of engine parts), equal to 113 microns.
Table 4
Physical and chemical parameters of DF with additives [21]
Sample number | Ester content, % | Density at 20 °C, g/sm3 | Viscosity at 40 °C, mm2/s | Sulfur, mg/kg | Freezing point, °С | Lubricity, microns |
DF + additive 1 | ||||||
1 | 1 | 0,855 | 4,57 | 7 | –13 | 378 |
2 | 5 | 0,856 | 5,00 | 7 | –13 | 335 |
3 | 10 | 0,857 | 4,49 | 7 | –12 | 253 |
DF + additive2 | ||||||
4 | 1 | 0,855 | 4,00 | 7 | –13 | 332 |
5 | 5 | 0,855 | 4,09 | 7 | –13 | 327 |
6 | 10 | 0,856 | 4,22 | 7 | –13 | 308 |
DF + additive3 | ||||||
7 | 1 | 0,855 | 4,95 | 7 | –13 | 412 |
8 | 5 | 0,856 | 4,99 | 7 | –13 | 329 |
9 | 10 | 0,857 | 4,89 | 7 | –12 | 283 |
DF + additive4 | ||||||
10 | 1 | 0,855 | 2,83 | 1 | –12 | 194 |
11 | 5 | 0,837 | 3,01 | 3 | –12 | 151 |
12 | 10 | 0,841 | 3,26 | 8 | –13 | 213 |
DF + additive5 | ||||||
13 | 1 | 0,855 | 2,83 | 33 | –12 | 195 |
14 | 5 | 0,837 | 3,02 | 10 | –13 | 113 |
15 | 10 | 0,840 | 3,29 | 10 | –13 | 133 |
DF + additive6 | ||||||
16 | 1 | 0,855 | 2,85 | 27 | –12 | 305 |
17 | 5 | 0,839 | 3,12 | 19 | –12 | 265 |
18 | 10 | 0,843 | 3,52 | 14 | –13 | 207 |
Laboratory and stand tests have shown that with the inclusion of an additive in DF, compared with the use of hydrotreated diesel fuel without an additive, the concentration of carbon monoxide in the exhaust gases decreases by 16-70 % at maximum engine load and by 30-50 % at partial load (75 %) (Fig.4, a). Additionally, the concentration of hydrocarbons in the exhaust gases was measured, which decreased by 6-26 % at maximum load and by 25-43 % at partial load (75 %) (Fig.4, b).
Mine tests of diesel fuel with the developed additive in the Zetor 1404 turbo engine showed that its use in the amount of 5 wt.% in the fuel composition allows to reduce CO emissions during its combustion in comparison with the use of standard diesel fuel by 19-60 % (from 0.0329 to 0.0129 % when operating at idle DHL, from 0.0107 to 0.0087 % when working at maximum load). Also, the concentration of nitrogen oxides decreases by 17-98 % (from 0.01445 to 0.00025 % when idle, from 0.02254 to 0.01869 % when working at medium speed).
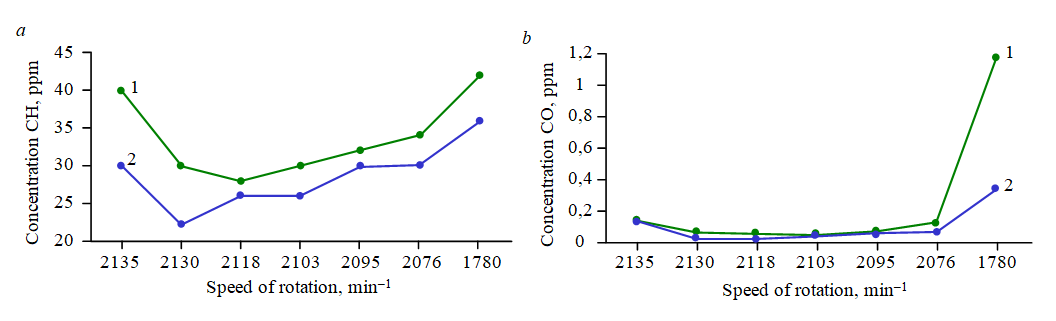
Thus, the above research results show the effectiveness of using the developed additive in DHL fuel [23, 26]. Its use makes it possible to significantly reduce the concentration of harmful emissions in mine workings, which, in turn, leads to an improvement in the working conditions of underground personnel by the chemical factor [5, 10].
The task of the industrial experiment was a comparative assessment of the content of carbon monoxide and nitrogen oxides in the exhaust gases in the working area of the DHL driver without the use of an additive in the fuel and with an additive (Table 5).
Table 5
Comparative analysis of the content of carbon monoxide and nitrogen oxides in the working area of the DHL driver when using the additive and without it
Parameter | СО | Nitrogen oxides | СО | Nitrogen oxides |
Before using CPM | After using CPM | |||
Mine “Named after S.M.Kirov” | ||||
At idle speed | ||||
MPC, % | 0,0017 | 0,00025 | 0,0017 | 0,00025 |
Excess, times | 2,7 | 3,0 | 0,8 | 0,7 |
Class of working conditions | 3,1 | 3,1 | 2 | 2 |
At 1520 rpm | ||||
Excess, times | 2,1 | 2,7 | 0,7 | 0,5 |
Class of working conditions | 3,1 | 3,1 | 2 | 2 |
At maximum speed | ||||
Excess, times | 2,0 | 1,7 | - | - |
Class of working conditions | 3,1 | 3,1 | 2 | 2 |
Mine “Komsomolets" | ||||
At idle speed | ||||
Excess, times | 1,4 | 1,8 | 0,5 | 0,6 |
Class of working conditions | 3,1 | 3,1 | 2 | 2 |
At 1520 rpm | ||||
Excess, times | 1,8 | 1,7 | 0,4 | 0,5 |
Class of working conditions | 3,1 | 3,1 | 2 | 2 |
At maximum speed | ||||
Excess, times | 2,0 | 1,9 | 0,4 | – |
Class of working conditions | 3,1 | 3,1 | 2 | 2 |
Mine “Named after V.D.Yalevskiy” | ||||
Atidlespeed | ||||
Excess, times | 2,2 | 2,0 | 0,5 | 0,4 |
Class of working conditions | 3,1 | 3,1 | 2 | 2 |
At 1520 rpm | ||||
Excess, times | 2,4 | 2,8 | 0,5 | 0,4 |
Class of working conditions | 3,1 | 3,1 | 2 | 2 |
At maximum speed | ||||
Excess, times | 2,5 | 3,0 | 0,4 | 0,3 |
Class of working conditions | 3,1 | 3,1 | 2 | 2 |
In the air of the working areas of coal mines, there are increased concentrations of harmful gases, which is reflected in the protocols of the special assessment of working conditions (SAWC) by the chemical factor. As the analysis of the SAWC results showed, the effectiveness of measures taken at the mines to reduce exhaust gas emissions in some cases is insufficient. For individual workplaces, the class of working conditions by the chemical factor is equal to 3.1 or 3.2.
As part of the industrial experiment, it was found that at the workplace of the DHL driver, as well as in the adjacent working area (for example, in the twenty-meter zone from the DHL), there are points with an excess of carbon dioxide, carbon monoxide and nitrogen oxides in the air. The maximum excess for carbon monoxide is 6.7 times, for nitrogen oxides-10 times.
Using the Ansys CFX software, a computer simulation of the carbon monoxide distribution in the working area of the DHL driver was performed when the engine was running using fuel without additives at maximum speed. The simulation result is shown in Fig.5, which shows that in the vertical section of the DHL cab at the level of the driver's respiratory organs, there are excess concentrations of carbon monoxide.
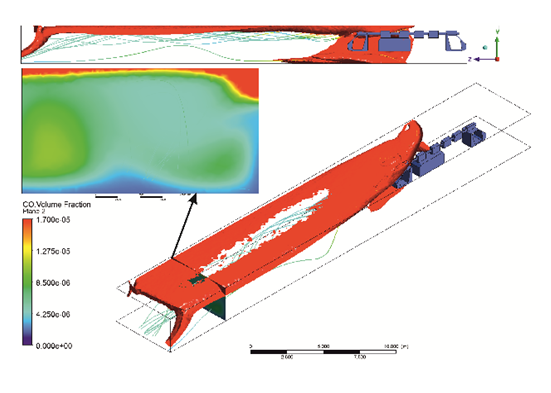
As can be seen from Table 5, the use of the additive in the amount of 5 mass % allows to achieve an improvement in working conditions in the working area of the DHL driver by the chemical factor and reduce the class of working conditions from 3.1. to 2.
Conclusion. It should be noted that in the air of the working areas of coal mines, up to 90 % of carbon monoxide and nitrogen oxides emissions are formed during the operation of diesel-hydraulic locomotives. In the working area of the diesel-hydraulic locomotives driver in coal mines, the concentration of carbon monoxide and nitrogen oxides exceeds the norm by more than two times.
The most rational way to reduce the concentration of harmful gases in the air of working areas is to use a vegetal additive to DHL fuel, which allows to increase the completeness of fuel combustion and thereby reduce the concentration of carbon monoxide in the engine exhaust. The additive obtained from cameline oil has better environmental and operational characteristics compared to other types of raw materials. It is experimentally established that the content of this additive in a mixture with hydrotreated diesel fuel should be 5 %.
Stand tests of additives on a diesel engine showed that the concentration of carbon oxides in the exhaust gases is reduced by 16-70 % at maximum load and by 30-50 % at partial load (75 %), depending on the number of revolutions, the additionally changed concentration of hydrocarbons in the exhaust gases is reduced by 6-26 % at maximum load and by 25-43 % at partial load (75 %). The smoke content of the exhaust gases is reduced to 71 %. The use of the additive in the Zetor 1404 turbo engine reduces CO emissions from the combustion of DF with the additive in comparison with the use of usual diesel fuel by 19-60 % and reduces the concentration of nitrogen oxides by 17-98 %.
The impact of harmful emissions on the health and working conditions of coal mine workers is of the greatest importance. The use of the developed additive to diesel fuel reduces the class of working conditions by the chemical factor in the workplaces of the DHL driver from 3.1 to 2.