Энергоэффективность линейного реечного привода штанговых глубинных насосов
Аннотация
В настоящее время для повышения объемов нефтедобычи и снижения экономических издержек при разработке низкодебитных месторождений актуальна разработка кустовым способом с использованием компактных мобильных приводов штанговых глубинных насосов (ШГН). Целью работы является анализ путей повышения энергоэффективности ШГН за счет снижения потерь механической и электрической энергии, выбор наиболее энергоэффективного компактного привода для разработки низкодебитных месторождений кустовым способом, кинематические и прочностные расчеты привода выбранного типоразмера, разработка адаптивной системы управления группой приводов при кустовой разработке скважин. По результатам выполненных расчетов наибольшим КПД механизма привода обладает линейный реечный привод. Приведены кинематические и прочностные расчеты линейного реечного привода с длиной хода 1120 мм и нагрузкой до 8 т. Показано, что применение систем прямого управления моментом и накопления кинетической энергии элементов привода ШГН и колонны штоков является эффективным средством снижения энергозатрат при добыче нефти из низкодебитных месторождений. Применение разработанной системы запаса и перераспределения потенциальной энергии штоков между ШГН, осуществляющими подъем нефти, позволило устранить колебания потребляемой мощности, снизить ее пиковое значение в три раза, пиковое значение потребляемого из сети тока в два раза, уменьшить потери во входном преобразователе и кабелях в три раза.
Введение
На протяжении долгого времени нефтегазовая отрасль оставалась одним из приоритетнейших направлений в экономическом и промышленном секторе России [1-3]. Для поддержания стабильного роста добычи углеводородных ресурсов необходимо как освоение новых месторождений, так и создание новых и совершенствование уже существующих технологий извлечения нефти. Однако с каждым годом поддерживать такой рост труднее, старые месторождения истощаются и требуют все более сложное и дорогостоящее оборудование для поддержания процесса добычи, а открытие новых месторождений с легкоизвлекаемыми запасами сокращается [4-6]. Поэтому большое внимание привлекают месторождения с трудноизвлекаемыми запасами (ТРИЗ). Согласно актуальным данным доля ТРИЗ в общем запасе нефти на май 2022 г. превысила 66 % [7], что говорит об их высокой значимости в энергетическом балансе страны. ТРИЗ можно разделить на следующие группы: высоковязкие нефти [8-10]; малопроницаемые и низкопористые коллектора [4, 11, 12]; истощенные месторождения [5, 13, 14]; отдаленно расположенные месторождения [3, 15, 16]; низкопродуктивные пласты [17-19]. Последние пользуются большой популярностью в России в связи с наличием больших запасов нефти и более удобным географическим расположением [20].
Для повышения объемов нефтедобычи и снижения экономических издержек разработка месторождений осуществляется кустовым способом [21-23]. Кустовая разработка не является решением проблемы вследствие применения штанговых глубинных насосов (ШГН), в которых в качестве приводов используют балансирные и безбалансирные станки-качалки (С-К), малопригодные в разработке низкодебитных месторождений [24]. Рассмотрим и проанализируем методы повышения энергоэффективности разработок низкодебитных месторождений.
Применяемые в настоящее время в нефтедобыче механические приводы ШГН подразделяются на балансирные и безбалансирные. В балансирных приводах (С-К) возвратно-поступательное перемещение точки подвеса штанг осуществляется качающегося рычага – балансира, соединенного кривошипно-шатунным механизмом (КШМ) с валом трансмиссии [25]. В безбалансирных приводах возвратно-поступательное перемещение точки подвеса штанг осуществляется механизмами с использованием гибких элементов (цепей или канатов) [26]. Также известны гидравлические и линейные безредукторные приводы ШГН, приводы на основе линейных двигателей, линейные приводы на основе систем зубчатое колесо – рейка и ходовой винт – гайка [27, 28]. Очевидно, что КПД механизма зависит от уровня потерь в элементах конструкции привода и его кинематической схемы [26, 29, 30].
Штанговый глубинный насос получает механическую энергию от колонны штанг, совершающей возвратно-поступательное движение, которое сообщает ей привод насосной установки. Он преобразует электрическую энергию, подводимую к электродвигателю привода, в механическую. Таким образом, энергоэффективность работы ШГН напрямую зависит от величины потерь электрической и механической энергии в различных элементах конструкции привода. К основным следует отнести потери в механизме привода ШГН и электрические потери в двигателе привода и пуско-регулирующем оборудовании.
Потребляемая приводом электроэнергия существенно зависит от колебаний мощности в цикле работы электродвигателя привода. Так, при работе С-К возникают существенные колебания потребляемой мощности, меняющейся в семь раз за один цикл работы насоса. Для используемых в качестве приводного двигателя асинхронных двигателей с короткозамкнутым ротором скачки мощности приводят не только к значительным перепадам напряжения в энергосистеме, но и к температурным и механическим перегрузкам двигателя.
Применение реверсивных реечного линейного и цепного приводов приводит к дополнительным потерям в двигателе и в пускорегулирующем оборудовании при его пуске. Для снижения этих потерь в системе управления электродвигателем привода необходимо использовать преобразователи частоты и энергоэффективные алгоритмы управления. Кроме частотного управления двигателем, при совместной работе нескольких приводов насосов при кустовой разработке скважин можно использовать кинетическую энергию движущегося вниз штока при подъеме нефти [27]. Таким образом, энергоэффективность привода ШГН определяется потерями механической и электрической энергии в процессе эксплуатации.
Целью работы является анализ путей повышения энергоэффективности штанговых глубинных насосов за счет снижения потерь механической и электрической энергии, выбор наиболее энергоэффективного компактного привода для разработки низкодебитных месторождений кустовым способом, кинематические и прочностные расчеты привода выбранного типоразмера, разработка адаптивной системы управления группой приводов при кустовой разработке скважин.
Методы и материалы
Методология работы включает следующие этапы:
- выбор компактного привода для низкодебитных месторождений с наибольшим КПД механизма привода;
- кинематические расчеты привода выбранного типоразмера, позволяющие определить параметры зубчатой передачи и предельно допустимые нагрузки и ограничения в скорости перемещения рейки (числе двойных ходов) для выбранного мотор-редуктора;
- прочностные расчеты на изгиб зубьев вал-шестерни, позволяющие выбрать материал и способ термической обработки вал-шестерни и зубчатой рейки и поверхностного упрочнения зубьев, вылерживающие нагрузку на шток до 80 кН;
- определение последовательности изготовления деталей и сборки привода, позволяющей изготовить разработанный привод с нагрузкой на шток до 80 кН;
- разработка адаптивной системы управления (САУ) группой приводов на кусте скважин с системой рекуперации энергии движущегося вниз штока, позволяющей снизить энергопотребление приводов регулированием числа двойных ходов и хода штока.
Оценка потерь механической энергии в приводах различной конструкции выполняется при помощи расчета их КПД.
Расчет КПД механизма приводов ШГН
Выполнено сравнение приводов ШГН: на основе балансирного станка-качалки, цепного вертикального привода конструкции РНТЦ ВНИИнефть [25], разработанного в рамках настоящей работы линейного привода на основе системы рейка – зубчатое колесо, привода на основе системы винт – гайка, а также гидравлического привода.
Для сопоставительного анализа КПД механической части приводов используем известные данные. Для расчета КПД механизма привода в качестве входной мощности будем рассматривать механическую мощность приводного двигателя, а в качестве выходной – механическую мощность, передаваемую полированному штоку. КПД привода равен произведению КПД его составляющих.
Кинематическая схема станка-качалки приведена на рис.1, а [30]. В его состав входят: головка балансира (1); балансир, расположенный на паре подшипников скольжения (2); шатун-кривошип (3); опора шатуна-кривошипа (4); клиноременная передача (5, 6); трехступенчатый редуктор (7), состоящий из трех пар цилиндрических зубчатых колес на подшипниках качения (8, 10, 11); кривошипно-шатунный механизм (9), состоящий из пар скольжения шатун-балансир.
КПД станка-качалки оценим по формуле
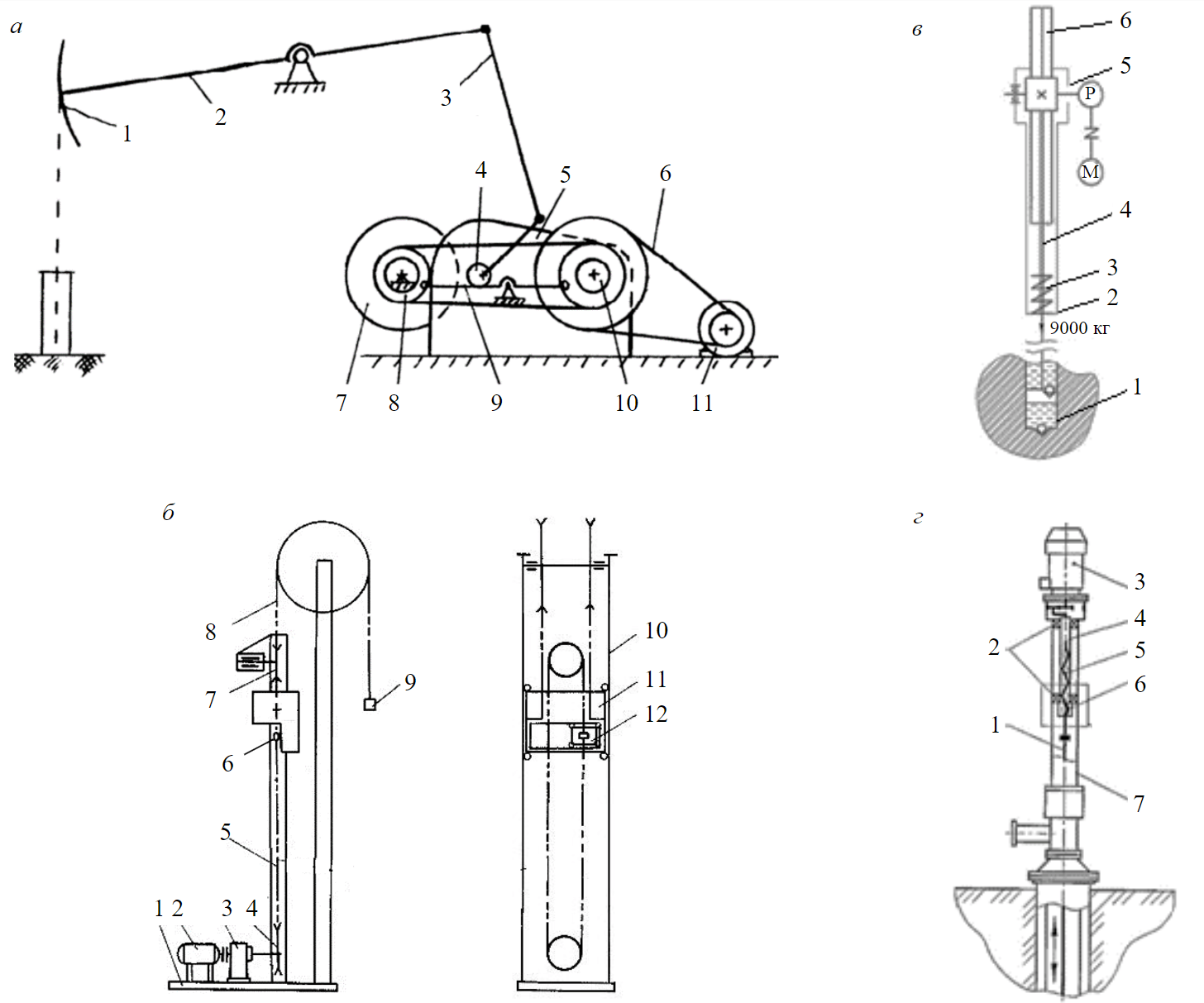
Рис.1. Кинематическая схема балансирного станка-качалки (а), привода с подвижной кареткой (б), разработанного линейного реечного привода ШГН (в), привода с ходовым винтом без реверсирования приводного двигателя (г)
где ηММ – КПД механической муфты, ηММ = 0,98; ηКРП – КПД клиноременной передачи, ηКРП = 0,96; ηПК – КПД подшипников качения, ηПК = 0,992; ηЦЗП – КПД цилиндрической зубчатой передачи, ηЦЗП = 0,97; k – число ступеней редуктора, k = 3; ηКШМ – КПД кривошипно-шатунного механизма, ηКШМ = 0,98; ηПС – КПД подшипников скольжения, ηПС = 0,985*. После подстановки приведенных средних значений получим:
что хорошо согласуется с данными 0,80-0,85.
Кинематическая схема цепного привода ШГН конструкции [25] представлена на рис.1, б: 1 – рама; 2 – электродвигатель; 3 – редуктор; 4 – ведущий шкив; 5 – непрерывное гибкое звено (цепь); 6 – узел крепления; 7 – направляющий элемент; 8 – разомкнутое гибкое звено (цепь или тросы); 9 – колонна штанг; 10 – стойка; 11 – противовес; 12 – каретка. Привод включает в себя механическую муфту, одноступенчатый редуктор, цепную передачу, пару трения направляющий элемент – каретка, два подшипника качения, являющихся опорой ведущего шкива.
Формула для расчета КПД цепного привода имеет вид [25]:
где ηММ – КПД механической муфты, ηММ = 0,98; ηПК – КПД подшипников качения, ηПК = 0,992; ηЦЗП – КПД цилиндрической зубчатой передачи, ηЦЗП = 0,97; ηЦП – КПД цепной передачи открытого исполнения, ηЦП = 0,92; ηПС – КПД подшипников скольжения, ηПС = 0,985.
После подстановки значений получим:
Кинематическая схема разработанного линейного реечного привода представлена на рис.1, в[31]. Привод содержит конический редуктор KAZ-97 фирмы SEW EURODRIVE, систему рейка – зубчатое колесо, опирающуюся на подшипник качения, подшипник редуктора (1 – основа-ние-опора; 2 – демпфер; 3 – корпус; 4 – рейка; 5 – механизм с редуктором и электродвигателем; 6 – крышка-направляющая).
Формула для расчета КПД линейного реечного привода имеет вид [30]:
где ηКР – КПД конического редуктора, ηКР = 0,965; ηПК – КПД подшипников качения, ηПК = 0,992; ηЦЗП – КПД цилиндрической зубчатой передачи, ηЦЗП = 0,97 [25].
После подстановки значений получим:
Конструкция привода на основе системы ходовой винт – гайка без реверсирования приводного двигателя представлена на рис.1, г [27]: 1 – штанга; 2 – подшипник; 3 – мотор-редуктор; 4 – ведомый вал; 5 – ходовой винт; 6 – гайка; 7 – опора.
Формула для расчета КПД передачи ходовой винт – гайка имеет вид [32]:
где ηПР – КПД планетарного редуктора, ηПР = 0,96; ηПК – КПД подшипников качения, ηПК = 0,992; ηВГ – КПД ролико-винтовой передачи, ηВГ = 0,89 [33].
После подстановки значений получим:
КПД гидравлического привода ШГН зависит от применяемой гидравлической схемы и от уровня утечек. Ввиду сложности применяемых методик для сравнительной оценки используем известные значения ηГП = 0,91-0,75 в зависимости от уровня утечек [34].
На основе проведенных расчетов выбираем линейный реечный привод, имеющий наибольший КПД среди аналогов.
Далее для выбранного типоразмера линейного реечного привода с длиной хода 1120 мм и нагрузкой до 80 кН выполнен кинематический расчет, позволяющий определить параметры зубчатой передачи и предельно допустимые нагрузки и ограничения в скорости перемещения рейки (числе двойных ходов) для выбранного мотор-редуктора.
Кинематический расчет привода
Для расчетов используются максимальная длина хода рейки (L0 = 1120 мм), максимальная скорость движения рейки и нагрузки, действующие на шток (F = 60 и 80 кН). Кинематический расчет позволяет определить линейную скорость перемещения рейки, число двойных ходов в минуту, выбрать диаметр ведущей шестерни, передаточное отношение передачи зубчатое колесо – рейка, произвести подбор мотор-редуктора.
Окружная скорость вращения шестерни равна линейной скорости перемещения рейки [33]:
где D – диаметр шестерни, мм; n – частота вращения шестерни, мин–1.
Выбираем модуль зуба зубчатого колеса шестерни m = 8 мм. С целью уменьшения крутящего момента число зубьев берется минимально возможным Z = 14.
Диаметр шестерни рассчитывается по формуле [33]
Частота вращения шестерни определяется из формулы (1):
Согласно имеющимся для ШГН экспериментальным данным, скорость перемещения штока составляет от 0,25 до 0,5 м/с или от 15 до 30 м/мин.
Линейная скорость перемещения штока (рейки) определяется по формуле [33]
где L0 – длина хода рейки; nдх – число двойных ходов в минуту,
Для скоростей перемещения рейки в диапазоне 0,25-0,5 м/с определим число двойных ходов в минуту (табл.1).
Таблица 1
Расчетные параметры привода с длиной хода L0 = 1120 мм
V0 |
n, мин–1 |
nдх, мин |
F,кH |
P1,кВт |
|
м/с |
м/мин |
||||
0,25 |
15 |
42,7 |
6,7 |
60 |
15 |
80 |
20 |
||||
0,3 |
18 |
51,2 |
8 |
60 |
18 |
80 |
24 |
||||
0,5 |
30 |
85,4 |
13,4 |
60 |
30 |
80 |
40 |
Определяем мощность двигателя привода по формуле [33]
где F – действующая на шток сила, Н; V0 – скорость перемещения штока (рейки), м/с.
Для скоростей перемещения рейки издиапазона 0,25-0,5 м/с и нагрузки на шток F = 60-80 кН необходимая мощность двигателя привода представлена в табл.1. Значения мощности двигателя при V0 = 0,3 м/с и нагрузке F = 60 и 80 кН составляют 18 и 24 кВт соответственно.
Определяем крутящий момент мотор-редуктора по формуле [33]
При нагрузке 60 кН определяем крутящий момент М = 3360 Н/м.
Частота вращения шестерни n, равная частоте вращения выходного вала n2, рассчитывается по формуле [33]
где n1 – частота вращения электродвигателя; i – передаточное число редуктора.
Тогда для V0 = 0,3 м/с и F = 60-80 кН при частоте вращения электродвигателя n1 = 1480 мин–1 передаточное число редуктора i = 28,9, что должно быть учтено при выборе мотор-редуктора.
Для данного типоразмера привода L0 = 1120 мм, F = 60-80 кН подобран мотор-редуктор SEWEURODRIVE KAZ-97 с n1 = 1480 мин–1, P1 = 22 кВт, i = 18,96, n2 = 78 мин–1. Для этого редуктора допускаемая радиальная нагрузка составляет 19,4 кН. Эксплуатационный коэффициент (сервис-фактор) Sf = 1,35. Номинальный крутящий момент на выходе Mn2 = 3210 Н/м. Максимальный крутящий момент на выходе Mn2max = 4300 Н/м. Размерные характеристики редуктора – полый вал с d= 70 мм со шпонкой.
Таким образом, использование двигателя мощностью 22 кВт возможно при ограничениях скорости рейки в пределах 0,25-0,3 м/мин и максимальной допустимой нагрузке 73,3 кН. Скорость 0,5 м/с при заданных нагрузках 60-80 кН возможна при использовании мотор-редуктора мощностью от 30 кВт. При скорости 0,3 м/с и нагрузке 80 кН минимальная мощность составляет 24 кВт, момент равен 4480 Н/м. Указанные параметры мотор-редуктора не позволяют работать при такой нагрузке.
Затем выполняются расчеты на прочность при изгибе зубьев вал-шестерни, по результатам которых выбираются материал и способ термической обработки и поверхностного упрочнения зубьев.
Расчет элементов привода на прочность
Расчет зубьев шестерни на прочность при изгибе производится по формуле
где P – окружное усилие, Н; kF – коэффициент распределения нагрузки; yF – коэффициент формы зуба, зависящий от числа зубьев, при Z = 14 yF ≈ 3,9; bw – ширина зубчатого венца, bw = 139,5 мм; m – модуль зуба зубчатого колеса, m = 8 мм.
Коэффициент распределения нагрузки рассчитывается по формуле [33]
где kFb – коэффициент неравномерности распределения нагрузки по длине зуба, при практически симметричном расположении опор и отношении ширины bw к диаметру D (ψbd = 140/112 = 1,2) kFb = 1,14 (табл.2); kFv – коэффициент динамической нагрузки, при 7-й степени точности и окружной скорости до 3 м/с kFv = 1,15 (табл.3);
Таблица 2
Значение коэффициента концентрации нагрузки Fb
|
Расположение колес относительно опор |
|||
Симметричное |
Несимметричное |
Консольное |
||
Вал весьма жесткий |
Менее жесткий |
|||
0,2 |
1,00 |
1,00 |
1,05 |
1,15 |
0,4 |
1,00 |
1,04 |
1,10 |
1,22 |
0,6 |
1,03 |
1,08 |
1,16 |
1,32 |
0,8 |
1,06 |
1,13 |
1,22 |
1,45 |
1,0 |
1,10 |
1,18 |
1,29 |
– |
1,2 |
1,14 |
1,23 |
1,36 |
– |
Таблица 3
Значение коэффициента kFv для прямозубых колес
Степень точности |
Твердость поверхности зубьев НВ |
Окружная скорость v, м/с |
||
До 3 |
3-8 |
8-12 |
||
6 |
< 350 |
1,00 |
1,20 |
1,30 |
|
> 350 |
1,00 |
1,20 |
1,30 |
7 |
< 350 |
1,15 |
1,35 |
1,45 |
|
> 350 |
1,15 |
1,25 |
1,36 |
8 |
< 350 |
1,25 |
1,45 |
– |
|
> 350 |
1,20 |
1,35 |
– |
9 |
< 350 |
1,35 |
– |
– |
|
> 350 |
1,30 |
– |
– |
При базовом числе циклов допускаемые значения прочности на изгиб определяются по формуле [33]
где σF0limb – напряжения, определяемые режимом термообработки, МПа; коэффициент [n]Fʹ = 1,75 для сталей после нормализации, улучшения и поверхностной закалки, 1,8 – после объемной закалки и 1,55 – после цементации и закалки; коэффициент [n]Fʹʹ = 1 для штампованных, 1,15 для кованых и 1,3 для литых деталей.
Значения σF0limb в зависимости от режима обработки: 1,8 НВ – нормализованные улучшенные колеса; 500-550 МПа – объемная закалка, НRCэ = 45-55; 700 МПа – поверхностная закалка, НRCэ = 48-58; 900 МПа – цементация и закалка, НRCэ = 57-60.
Для штампованного колеса из улучшенной стали 40Х с поверхностной закалкой σF0limb = 700 МПа, для штампованного колеса из стали 20Х после цементации σF0limb = 900 МПа. Коэффициент запаса [n]F = 1,75 для стали после поверхностной закалки и [n]F = 1,55 для стали после цементации.
Рассчитываем допускаемое напряжение по формуле (11):
для стали 40Х с поверхностной закалкой [σ]F = 700/1,75 = 400 МПа,
для стали 20Х после цементации [σ]F = 900/1,55 = 580 МПа.
Напряжение в зубьях по формуле (9):
Таким образом, выбранный модуль из улучшенной стали 40Х с поверхностной закалкой выдерживает нагрузку до 80 кН.
Процесс изготовления деталей линейного реечного привода с длиной хода 1120 мм
Сведения, необходимые для изготовления составных частей элементов линейного реечного привода ШГН, представлены в табл.4.
Таблица 4
Технология изготовления и материал деталей линейного реечного привода
Наименование |
Тип изготовления |
Заготовка/Материал |
Рейка – вал-шестерня (сборка) |
||
Вал-шестерня |
Фрезерная обработка |
Сталь 40ХН |
Рейка |
Фрезерная обработка |
Сталь 40Х |
Замок малый |
Фрезерная обработка |
Лист 20/Сталь 3 |
Замок |
Фрезерная обработка |
Сталь 45 |
Втулка |
Токарная обработка |
Сталь 45 |
Шайба |
Токарная обработка |
Сталь 20 |
Вкладыш |
Лазерная резка |
Лист 2/Сталь 10 |
Корпус (сборка) |
||
Стенка нижняя |
Фрезерная обработка |
АМг3 |
Направляющая верхняя |
Фрезерная обработка |
Сталь45 |
Направляющая боковая |
Фрезерная обработка |
Сталь45 |
Рейка направляющая |
Слесарная обработка |
ЛС59-1 |
Пластина направляющая |
Слесарная обработка |
ЛС59-1 |
Стенка левая |
Фрезерная обработка |
АМг3 |
Стенка правая |
Фрезерная обработка |
АМг3 |
Стенка верхняя |
Фрезерная обработка |
АМг3 |
Кольцо |
Слесарная обработка |
Сталь45 |
Переходник (сварка) |
||
Стенка передняя |
Лазерная резка |
Лист 20/Сталь10 |
Кронштейн |
Слесарная обработка |
Лист 40/Сталь10 |
Кронштейн |
Слесарная обработка |
Труба 80×50×3/Сталь10 |
Ролик |
Токарная обработка |
Круг 35/Сталь45 |
Уголок |
Слесарная обработка |
Лист 6/Сталь10 |
Стенка |
Лазерная резка и гибка |
Лист 6/Сталь10 |
Ухо |
Слесарная обработка |
Лист 20/Сталь3 |
Колонна (сварка) |
||
Стенка |
Лазерная и фрезерная обработка |
Лист 25/Сталь10 |
Пружина сжатия наружная |
Готовое изделие |
|
Пружина сжатия внутренняя |
Готовое изделие |
|
Труба |
Сварка |
Труба 219×5 |
Плита (диск) |
Лазерная резка |
Лист 25/Сталь 3 |
Штанга |
Токарная обработка |
Труба 41×3,5 |
Клапан |
Токарная обработка |
Круг 45/Сталь 3 |
Полукрышка левая |
Токарная обработка |
ЛС59-1 |
Полукрышка правая |
Токарная обработка |
ЛС59-1 |
Стакан (сварка) |
||
Диск стакана |
Токарная обработка |
Лист 25/Сталь3 |
Труба стакана |
Токарная обработка |
Труба 54×3 |
Корпус кожуха (сварка) |
||
Стенка |
Лазерная резка и гибка |
Лист 2/Сталь3 |
Ручка |
Слесарная обработка |
Круг 14/Сталь20 |
Стенка задняя |
Лазерная резка |
Лист 2/Сталь3 |
Фланец (сварка) |
||
Пластина |
Лазерная резка |
Лист 4/ Сталь10 |
Пластина |
Лазерная резка |
Лист 4/ Сталь10 |
Пластина |
Лазерная резка |
Лист 4/ Сталь10 |
Процесс сборки привода
(рис.2). На мотор-редуктор устанавливали нижнюю стенку корпуса (рис.2, а). На вал-шестерню напрессовывался подшипник (рис.2, б), затем она устанавливалась в редуктор, привинчивалась боковая стенка (рис.2, в). Затем в корпус устанавливались направляющие с вкладышами (рис.2, г).

Рис.2. Этапы сборки линейного реечного привода ШГН
После этого осуществлялась сборка колонны (рис.2, д). В нее устанавливались пружины и стакан. Затем редуктор с двигателем в сборе устанавливался на монтажную площадку, после чего совмещались отверстия во фланце колонны и корпусе редуктора, на корпус редуктора устанавливался переходник, после чего устанавливалась зубчатая рейка, которую переворачивали зубьями вниз и передвигали по направляющим до упора, проворачивая вал. Кожух устанавливается на переходник в вертикальном положении и используется в комплектации привода для испытаний на скважине при защите механизма от влаги и пыли. При проведении исследовательских испытаний кожух не устанавливался для визуального контроля перемещений рейки.
Для собранного привода была разработана адаптивная система управления группой приводов на кусте скважин с системой рекуперации энергии движущегося вниз штока, позволяющей снизить энергопотребление приводов регулированием числа двойных ходов и хода штока.
Оптимизация алгоритмов нефтедобычи с точки зрения эффективности и энергопотребления выполнена на основе методов математического моделирования в системе имитационного моделирования Simulink Power System Blockset. Для создания модели системы были использованы математические модели гидравлической и механической (система насос – штанговая колонна и привод ШГН), электрической (преобразователь частоты, накопитель энергии и электродвигатель); электронной (регулятор) составных частей [35], штанговой колонны [36]. Методика разработки математической модели колонны представлена в [36].
Разработанная в настоящей работе адаптивная САУ группы приводов формирует команды для преобразователя частоты. Преобразователь частоты формирует напряжение требуемой частоты и амплитуды для питания асинхронного электродвигателя. Асинхронный электродвигатель, соединенный с редуктором через муфту, передает крутящий момент механизму шестерня-рейка, рейка соединена с полированным штоком и сообщает ему возвратно-поступательное движение. Кинетическая энергия движущих вниз штоков запасается в конденсаторной батарее. САУ выполняет распределение накопленной энергии между приводами при подъеме пластовой жидкости, обеспечивает оптимальное управление в соответствии с дебитом скважины, осуществляет управление с оптимальным наполнением насоса, обеспечивает программным способом предотвращение гидроудара, что позволяет повысить срок службы и надежность работы привода. Приводы соединены между собой и конденсаторной батареей с помощью звена постоянного тока.
Схема разработанной адаптивной САУ, управляющей группой приводов с рекуперацией энергии, и ее реализация для двух приводов ШГН представлены на рис.3, а. Экспериментальный образец САУ имеет два канала для подключения двух приводов ШГН и представляет собой один общий шкаф управления и питания, в котором размещаются преобразователи частоты (ПЧ), управляющий контроллер и конденсатор звена постоянного тока (рис.3, б). Эта система также имеет силовой и информационный каналы. Приводы насоса рассматриваются в составе группы как объекты управления со своими СУ, а их информационные каналы связаны с системой управления высокого уровня через информационный преобразователь. Ввиду того, что для повышения энергоэффективности нефтедобычи используется кинетическая энергия движущегося вниз штока, накапливаемая в конденсаторной батарее, силовые каналы приводов ШГН соединены между собой и накопителем энергии через звено постоянного тока, а одной из задач САУ является распределение накапливаемой энергии между двумя приводами.

Рис.3. Функциональная электрическая схема экспериментального образца САУ (а) и шкаф питания и управления для группы из двух приводов ШГН (б)
Обсуждение результатов. Анализ расчета КПД приводов показал, что разработанный линейный реечный привод имеет наибольший КПД среди аналогов. Компактность привода и возможность установки его непосредственно на устье скважины позволяют снизить эксплуатационные затраты и срок ввода в эксплуатацию, что также способствует повышению экономической эффективности добычи нефти.
Для типоразмера привода для нагрузок на шток 60-80 кН подобран мотор-редуктор SEWEURODRIVE KAZ-97 с n1 = 1480 мин–1, P1 = 22 кВт, i = 19, n2 = 78 мин–1, Sf = 1,35, Mn2 = 3210 Н/м. Использование мотор-редуктора мощностью 22 кВт ограничивает скорости перемещения рейки в пределах 0,25-0,3 м/мин и допустимую нагрузку 73,3 кН. При расчетных нагрузках 60-80 кН скорость перемещения рейки, равная 0,5 м/с, допустима для двигателей мощностью более 30 кВт. На скорости 0,3 м/с и нагрузке 80 кН минимальная мощность равна 24 кВт, а на скорости 0,5 м/с и нагрузке 60 кН – 30 кВт.
Для выбранного мотор-редуктора мощностью 22 кВт при неизменности длины хода рейки ограничения по скорости перемещения штока или нагрузок на шток возможны за счет снижения частоты вращения шестерни и количества двойных ходов, а также скорости перемещения рейки. Это можно обеспечить при уменьшении частоты тока, который подается на электродвигатель, что достигается за счет использования преобразователя частоты в системе управления привода. Применение ПЧ позволяет также осуществлять торможение при остановке и смене направления перемещения и уменьшить инерционные нагрузки при реверсировании направления движения.
При скорости 0,3 м/с, нагрузке 80 кН и скорости 0,5 м/с, нагрузке 60 кН требуется использовать размерные параметры редуктора с большими габаритами, чем SEWEURODRIVE KAZ-97. Подходящим вариантом для этих условий является мотор-редуктор Bonfiglioli А803 24,5 Р200 BN200L4 с характеристиками P1 = 30 кВт, n1 = 1470 мин–1, n2 = 60 мин–1, Mn2 = 4377 Н·м, Sf = 1,5, радиальная нагрузка на выходном валу Rn2 = 4330 Н.

Рис.4. Сборочные единицы линейного реечного привода ШГН
По результатам расчета на прочность при изгибе зубьев была выбрана вал-шестерня из улучшенной стали 40ХН с поверхностной закалкой зубьев, которая выдерживает нагрузку до 80 кН. Также с учетом проведенных расчетов были выбраны материалы и технологии изготовления остальных составных частей и деталей привода, подобраны технологические режимы термообработки. Фотографии некоторых деталей представлены на рис.4: вал-шестерня (сталь 40ХН, улучшение + закалка токами высокой частоты (ТВЧ) для поверхности зубьев (рис.4, а), зубчатая рейка (сталь 40Х, улучшение, рис.4, б), детали корпуса c вкладышами из латуни ЛС59-1 и стенками из алюминиевого сплава АМг3 (рис.4, в, г). Колонна, кожух, преходник и стакан представляют собой сварные конструкции из углеродистых сталей.
Также произведены механическая (токарная и фрезерная) и термическая обработки (нормализация) деталей для сборки рейки с вал-шестерней (малый замок, замок, втулка, шайба, в соответствии с табл.4) и лазерная резка деталей для деталей вкладыша (рис.4, в). Чистовая механическая обработка деталей корпуса (рис.4, г) осуществлялась в соответствии с табл.4. Для изготовления переходника (табл.4) была выполнена чистовая механическая обработка, лазерная резка и сварка деталей (рис.4, д).
Изготовленные и термообработанные пружины показаны на рис.4, е. Для изготовления колонны и стакана была выполнена лазерная резка, токарная и фрезерная обработка, а затем сварка деталей (табл.4). Колонна в сборе с установленными внутрь стаканом и пружинами показана на рис.4, ж. Для изготовления кожуха выполнены лазерная резка, гибка и сварка деталей (табл.4), готовые кожухи представлены на рис.4, з.
На рис.5 представлен линейный реечный привод в сборе с длиной хода 1200 мм и нагрузкой на шток до 80 кН, закрепленный на испытательном стенде для испытаний на холостом ходу. Асинхронный электродвигатель, передающий реечному механизму крутящий момент, через упругую муфту соединен с редуктором, который передает возвратно-поступательное движение насосной штанге. Зубчатая реечная передача состоит из закрепленной на стойке зубчатой рейки и вала-шестерни, перемещающейся в вертикальном направлении для обеспечения возвратно-поступательного движения насосных штанг. Зубчатый венец вала-шестерни при вращении электродвигателя, находясь в зацеплении с зубчатой рейкой, на прямом ходу перемещает ее вертикально вверх, а при реверсивном вращении двигателя на обратном ходу – вертикально вниз. Стойка зубчатой рейки в верхнем конце жестко соединена со штоком штанговой колонны при помощи зажима, обеспечивающего передачу усилия от привода к колонне штанг. В U-образной стойке зубчатой рейки вдоль оси рабочего хода насоса имеется продольный открытый канал для перемещения в нем штока внутри стойки.

Рис.5. Конструкция (а) и изготовленный реечный привод в сборе (б) 1 – подставка; 2 – асинхронный электродвигатель; 3 – полированный шток; 4 – масляная ванна; 5 – редуктор; 6 – шестерня и ось; 7 – корпус механизма; 8 – зубчатая рейка; 9 – штангодержатель
Под нижним краем стойки привода расположен масляный поддон (ванна) для смазки, в который погружается нижняя часть стойки, в результате чего обеспечивается смазка во время каждого рабочего хода. Поддон для смазки представляет собой кольцевую полость, образованную двумя трубами, герметично соединенными внизу, заполненную смазкой, которая закачивается в верхнюю часть полости. Внутренняя трубчатая стенка поддона расположена вокруг устьевого штока и свободно помещается внутри отверстия рейки для обеспечения хода, а внешняя стенка трубчатого поддона расположена вокруг рейки. Привод также содержит пружину, расположенную внутри полости в поддоне под нижним краем стойки для торможения рейки при движении насоса вниз и разгона рейки во время прямого хода насоса вверх.
При движении стойки вверх микропроцессорная система управления линейным реечным приводом обеспечивает работу электродвигателя в двигательном режиме, а при движении вниз – в режиме торможения (генераторном режиме). Приводы насосов, работающие на кусте скважин, соединяются звеном постоянного тока, к которому подключается конденсаторная батарея большой емкости для накопления и хранения энергии, вырабатываемой в генераторном режиме при обратном ходе штока вниз. Накопленная энергия потребляется электродвигателем на прямом ходу штока вверх во время работы в двигательном (нагруженном) режиме. Микропроцессорная система управления, подбирающая интенсивность откачки для каждого насоса, регулирует расход запасенной энергии на подъем нефти, что позволяет экономичнее расходовать электроэнергию.
Для реализации энергоэффективного управления группой приводов на кусте близкорасположенных скважин с рекуперацией энергии предлагается адаптивная САУ, включающая входной преобразователь, управляемый источник тока, обеспечивающий процессы заряда и разряда конденсатора большой емкости (накопитель энергии штока) и выдающая команды на запуск и останов приводов, входящих в группу, работу в двигательном и генераторном режимах. Предлагаемая адаптивная САУ позволяет реализовать алгоритмы энергоэффективного управления группами приводов ШГН, обеспечивающие снижение колебаний потребляемой мощности и тока путем выбора скорости плунжера, числа качаний ШГН и длительности паузы между ними в соответствии с дебитом скважин.
Наиболее эффективным электрическим способом повышения КПД является применение разработанной системы запасения и перераспределения потенциальной энергии штоков между ШГН, осуществляющими подъем нефти. Это позволило устранить колебания потребляемой мощности, снизить ее пиковое значение в три раза, пиковое значение потребляемого из сети тока в два раза, уменьшить потери во входном преобразователе и кабелях в три раза.
Применение системы рекуперации энергии позволяет сократить капитальные затраты за счет снижения поперечного сечения сетевых кабелей, использования входного трансформатора или дизель-генераторной установки меньшей мощности в случае автономного питания группы приводов.
Таким образом, применение системы прямого управления моментом и системы накопления кинетической энергии элементов привода ШГН и колонны штока являются эффективным средством для снижения энергозатрат при добыче нефти из низкодебитных месторождений.
Заключение
Выполнен анализ путей повышения энергоэффективности штанговых глубинных насосов механическими способами. Показано, что наиболее эффективным механическим способом повышения КПД является применение линейного реечного привода разработанной конструкции, позволяющего повысить КПД установки на 10 % по сравнению с аналогами. Необходимо учитывать существующие в цикле работы электродвигателя привода колебания потребляемой мощности, приводящие к снижению КПД электродвигателя. Выполнены кинематический и прочностной расчеты линейного реечного привода с длиной хода 1120 мм и нагрузкой до 80 кН, описаны процессы его изготовления, термообработки деталей и сборки. Осуществлена сборка и проведены испытания привода на холостом ходу.
Разрабатываемые групповые энергоэффективные мобильные приводы ШГН и адаптивные САУ предназначены для оснащения «кустов» скважин на нефтяных месторождениях современным отечественным энергосберегающим оборудованиям для нефтедобычи взамен устаревшего и изношенного оборудования , а также для импортозамещения техники.
При достаточно больших объемах добычи общая энергоэффективность и снижение капитальных и эксплуатационных затрат может принести значительный экономический эффект, а срок окупаемости групповых САУ может составить не более года за счет возможности оснащения групповыми САУ любых типов приводов ШГН. Повысится энергоэффективность нефтедобычи, снизятся затраты на обустройство скважин, экологическая нагрузка на зоны нефтедобычи, повысится общий уровень автоматизации производства и технологическая культура нефтедобычи в целом.
Литература
- Кorolev N., Kozyaruk A., Morenov V. Efficiency Increase of Energy Systems in Oil and Gas Industry by Evaluation of Electric Drive Lifecycle // Energies. 2021. Vol. 14. Iss. 19. № 6074. DOI: 10.3390/en14196074
- Zakaev D., Nikolaichuk L., Filatova I. Problems of Oil Refining Industry Development in Russia // International Journal of Engineering Research and Technology. 2020. Vol. № 2. P. 267-270. DOI: 10.37624/IJERT/13.2.2020.267-270
- Samylovskaya E., Makhovikov A., Lutonin A. et al. Digital Technologies in Arctic Oil and Gas Resources Extraction: Global Trends and Russian Experience // Resources. 2022. Vol. Iss. 3. № 29. DOI: 10.3390/resources11030029
- Tananykhin D., Palyanitsina A., Rahman A. Analysis of Production Logging and Well Testing Data to Improve the Development System for Reservoirs with Complex Geological Structure // Procedia Environmental Science, Engineering and Management. 2020. Vol. № 4. P. 629-648.
- Korolev M., Rogachev M., Tananykhin D. Regulation of filtration characteristics of highly watered terrigenous formations using complex chemical compositions based on surfactants // Journal of Applied Engineering Science. 2020. Vol. 18. 1. P. 147-156. DOI: 10.5937/jaes18-24542
- Mardashov D., Duryagin V., Islamov S. Technology for Improving the Efficiency of Fractured Reservoir Development Using Gel-Forming Compositions // Energies. 2021. Vol. 14. Iss. 24. № DOI: 10.3390/en14248254
- Prischepa O., Nefedov Y., Nikiforova V., Xu Ruiming. Raw material base of Russia’s unconventional oil and gas reserves (hydrocarbons shale strata) // Frontiers in Earth Science. 2022. Vol. 10. № 958315. DOI: 10.3389/feart.2022.958315
- Jie Yu, Hongping Quan, Shihao Chang, Zhiyu Huang. Research on a fluorine-containing asphaltene dispersant and its application in improving the fluidity of heavy oil // Journal of Molecular Liquids. 2023. Vol.375. № DOI: 10.1016/j.molliq.2023.121318
- Lei He, Yong Dai, Jingjie Hou et al. MXene based immobilized microorganism for chemical oxygen demand reduction of oilfield wastewater and heavy oil viscosity reduction to enhance recovery // Journal of Environmental Chemical Engineering. 2023. Vol. 11. 2. № 109376. DOI: 10.1016/j.jece.2023.109376
- Anqi He, Junjian Li, Mengchen Jiang et al. Study of cyclic waterflooding for improving oil recovery in Lukeqin heavy oil reservoir // Geoenergy Science and Engineering. 2023. Vol. 223. № DOI: 10.1016/j.geoen.2023.211467
- Wan-Li Kang, Bo-Bo Zhou., Issakhov M., Gabdullin M. Advances in enhanced oil recovery technologies for low permeability reservoirs // Petroleum Science. 2022. Vol. 19. 4. P. 1622-1640. DOI: 10.1016/j.petsci.2022.06.010
- Chunxue Cui, Zhijun Zhou, Ziang He. Enhance oil recovery in low permeability reservoirs: Optimization and evaluation of ultra-high molecular weight HPAM/phenolic weak gel system // Journal of Petroleum Science and Engineering. 2020. Vol.195. № DOI: 10.1016/j.petrol.2020.107908
- Pothula G.K., Vij R.K., Bera A. An overview of chemical enhanced oil recovery and its status in India // Petroleum Science. 2023. DOI: 10.1016/j.petsci.2023.01.001
- Bera A., Vij R. K., Shah S. Impact of newly implemented enhanced oil and gas recovery screening policy on current oil production and future energy supply in India // Journal of Petroleum Science and Engineering. 2021. Vol.207. № DOI: 10.1016/j.petrol.2021.109196
- Zhijuan Zhao, Yan Li, Yougang Tang, Xinjie Ji. Conceptual design and numerical analysis of a novel platform for marginal oilfields development // Ocean Engineering. 2019. Vol. 187. № 106145. DOI: 10.1016/j.oceaneng.2019.106145
- Dmitrieva D., Romasheva N. Sustainable Development of Oil and Gas Potential of the Arctic and Its Shelf Zone: The Role of Innovations // Journal of Marine Science and Engineering. 2020. Vol.8. 12. № 1003. DOI: 10.3390/jmse8121003
- Peng Fei, Luo Dongkun, Yin Chengfang et al. Tight Oil Accumulation Characteristics and Resource Potential Evaluation of the Xiagou Formation in Qingxi Depression, Jiuquan Basin // Energy Procedia. 2019. Vol. 158. P. 5940-5945. DOI: 10.1016/j.egypro.2019.01.528
- Jingwei Cui, Rukai Zhu, Sen Li et al. Development patterns of source rocks in the depression lake basin and its influence on oil accumulation: Case study of the Chang 7 member of the Triassic Yanchang Formation, Ordos Basin, China // Journal of Natural Gas Geoscience. 2019. Vol. 4. Iss. 4. P. 191-204. DOI: 10.1016/j.jnggs.2019.08.002
- Leusheva E., Brovkina N., Morenov V. Investigation of Non-Linear Rheological Characteristics of Barite-Free Drilling Fluids // Fluids. 2021. Vol.6. 9. № 327. DOI: 10.3390/fluids6090327
- Мухаметшин В.Ш., Андреев В.Е., Ахметов Р.Т. Повышение эффективности использования ресурсной базы месторождений с трудноизвлекаемыми запасами нефти // Нефтегазовое дело. 2015. Т. № 4. С. 122-125.
- Wen-Jun Huang, De-Li Gao. Analysis of drilling difficulty of extended-reach wells based on drilling limit theory // Petroleum Science. 2022. Vol. 19. Iss. 3. P. 1099-1109. DOI: 10.1016/j.petsci.2021.12.030
- Abramov A. Agile methodology of well pad development // Journal of Petroleum Exploration and Production Technology. 2020. Vol. 10. Iss. 8. P. 3483-3496. DOI: 10.1007/s13202-020-00993-3
- Abramov A. Optimization of well pad design and drilling – well clustering // Petroleum Exploration and Development. 2019. Vol. 46. Iss. 3. P. 614-620. DOI: 10.1016/S1876-3804(19)60041-8
- Уразаков К.Р., Молчанова В.А., Тугунов П.М. Метод расчета динамических нагрузок и энергопотребления штанговой установки с системой автоматического уравновешивания // Записки Горного института. 2020. Т. C.640-649. DOI: 10.31897/PMI.2020.6.6
- Патент №2150607РФ. Привод скважинного штангового насоса / В.М.Валовский, Р.М.Ахунов, М.И.Манько, Н.В.Федосеенко. Опубл. 10.06.2000. Бюл. №
- Патент №2482332РФ. Безбалансирный станок-качалка / А.В.Дмитриев, В.Г.Фадеев, А.Ф.Садыков, Р.А.Ермаков, Р.Р. Кашапов, Н.В. Новиков. Опубл. 20.05.2013. Бюл. № 14.
- Patent № 8152492 U.S. Linear Rod Pump Apparatus and Method / T.L.Beck, R.G.Anderson, R.G.Peterson, M.A.MacDonald. Publ. 10.04.2012.
- Patent № 20200224651 U.S. Linear rack drive for submersible rod pump for oil production / A.Kurkov. Publ. 16.07.2020.
- Sivenkov A.V., Chirkova O.S., Konchus D., Mikhailov A.V. Development of Flux for Protection of the Surface of Liquid-Metallic Low-Melting-Point Fusible Melt // Key Engineering Materials. 2020. Vol. 854. P. 126-132. DOI: 10.4028/www.scientific.net/KEM.854.126
- Заявка на изобретение №94039340РФ. Станок-качалка / Х.Н. Мухаметшин. Опубл. 20.08.1996.
- Патент №167305РФ. Линейный привод штангового глубинного насоса / П.П.Петков, А.П.Петкова, В.Е.Брунман, А.Н.Волков, О.В.Кочнева, К.В.Балабанов. Опубл. 27.12.2016. Бюл. № 36.
- Мехдиев К.К. Оценка эффективности эксплуатации штанговых глубинных насосов на морских месторождениях в условиях интенсивного песко-водопроявления // Socar Proceedings. № 4. С. 53-60. DOI: 10.5510/OGP20190400411
- Артыкаева Э.М. Энергоресурсосберегающее электрооборудование нефтедобыващих установок с плунжерным погружным насосом: Автореф. дис. … канд. техн. наук. Чебоксары: Чувашский государственный университет им. И.Н.Ульянова, 2012. 21 с.
- Ивановский В.Н. Энергетика добычи нефти: основные направления оптимизации энергопотребления // Инженерная практика. 2011. № 6. С. 18-26.
- Лысенко В.Д., Грайфер В.И. Разработка малопродуктивных нефтяных месторождений. М.: Недра-Бизнесцентр, 2001. 562 с.
- Brunman V.E., Vataev A.S., Volkov N. et al. Optimizing Pump-Drive Operation to Improve the Energy-Efficiency of Oil Extraction // Russian Engineering Research. 2017. Vol.37. № 6. P.479-484. DOI: 10.3103/S1068798X17060089