A reliability study of the traction drive system in haul trucks based on failure analysis of their functional parts
Abstract
The efficiency of a mining and processing plant depends on the level of complex mechanization of the production process. In mineral extraction, haulage is a major cost category, with haul trucks being the key component of the mining transportation system. To improve production performance, mining operations can increase their haulage turnover and reduce transportation costs, which necessitates making haul trucks more reliable. This can be done by improving their mean time to first failure (MTFF) indicators. This article analyzes the reliability status of the traction drive system inhaul trucks operating in the mineral resources sector. It provides a quantitative assessment of traction drive system failures resulting from part defects and discusses the associated repair costs. By examining failure data from 2018 to 2022 and the results of vibration tests performed on a diesel generator, the study reveals that the most expensive failures are associated with defects in the synchronous generator, which are primarily caused by elevated external vibrations. Based on basic vibration tests and vibration spectra tests at different operating modes, recommendations have been formulated concerning the generator’s robustness to external mechanical forces and the ways to increase the generator’s protection grade to prevent dust intrusion. The study also identifies the frequency range that poses the greatest risk of damage to the windings.
Introduction
Currently, haul trucks are extensively utilized in open-pit mining to transport broken ore and rocks [1-3]. In the mining sector, transportation often accounts for 70 % of the total production costs [4, 5], with a major share attributed to traction drive system (TDS) repairs [6]. Haul truck downtime is caused by both scheduled maintenance and repair and emergency repairs resulting from TDS failures [7-9].
The traction drive system consists of a synchronous generator (SG), a control cabinet (CC), and an asynchronous traction motor (ATM) installed on each rear wheel of a haul truck.
To improve the reliability, safety, and efficiency of operating open-pit haul trucks while ensuring optimal maintenance costs, it is necessary to conduct studies to assess and ensure TDS reliability [10-12]. Considering that haul trucks operate in diverse climatic conditions across more than 80 countries worldwide, often under extreme conditions [13-15], there are stringent requirements as to the ability of the TDS to withstand environmental factors.
To date, various studies have been conducted to enhance the reliability of electric motors and their components. These studies include:
- Remote vehicle health monitoring (the engine, the electric drive, and the hydraulic system) to prevent accidents and carry out maintenance and repairs based on the actual condition of the dump truck, rather than using the traditional preventive maintenance approach [16].
- Predicting wear of theelectric motor bearings. Studies in this area [17, 18] explore methods for predicting the remaining lifespan of electric motor bearings using mathematical models.
- Fault finding in asynchronous motors through a multilevel combination of information [19, 20]. The referenced studies present models, one of which gives a conditional probability for different engine performance states based on data obtained from laboratory tests, while the other one identifies the operating modes of an electric motor based on subharmonic parameters.
- Assessing the probability of failure in an asynchronous motor within an electric drive through testing vibration and electrical parameters [21-23].
- Monitoring the state of synchronous generators using electrical signals. This work [24] contributes practical results in fault detection for operating synchronous generators connected to power systems.
- Assessing the life cycle of electric drives to improve power system efficiency. The referenced study [25] proposes a technique for evaluating the health status of electric drives based on normalized amplitudes of frequency components.
- Evaluating the reliability of the traction motor by the calculation method and the fault tree analysis [26-28].
Despite the diverse range of the studies mentioned, there is a notable lack of research specifically dedicated to the reliability of traction motors in mining trucks. While some studies [29, 30], address the reliability of mining trucks, they primarily focus on failures in components such as the internal combustion engine, undercarriage, or wheel motor gearbox, etc. The issue of traction drive system reliability is only considered superficially in such works.
This is an applied study. Based on analyzing operational data, we determined the causes of TDS failures and identified the parts that demand the utmost attention. The major advantage of the study lies in conducting field tests on a synchronous generator after repairs instead of usinga software package withidealized conditions. Checking its health status after operation in a quarry allows to understand the impact of operating conditions and external mechanical vibration loads on the electric drive’s reliability. We emphasize that it is important to bridge the gap between scientific research and industrial applications.
Methods
We conducted reliability tests of haul trucks, analyzing 326 cases of TDS part failures over a 5-year period from 2018 to 2022. To ensure that the sample was representative, haul trucks operating in various regions and climatic conditions were included in the study, encompassing Vietnam, Iran, Uzbekistan, Kazakhstan, Kuzbass, Novosibirsk region, and the Republic of Khakassia. Figure 1 shows the number of TDS part failures during the period under study. Figure 2 presents the cost ratio for restoring the individual TDS parts.
The charts show that the number of TDS failures due to SG failures is much lower compared to CC failures, while SG restoration costs account for three-fourths of the total sum. The reason for this is that it is impossible to perform SG repairs on site, which necessitates additional costs for transporting the damaged part to the manufacturer or a specialized repair company. Moreover, it is usually costly components such as the winding, rotor, and bearing assembly that require repairs. Consequently, these factors result in prolonged downtime for mining trucks.
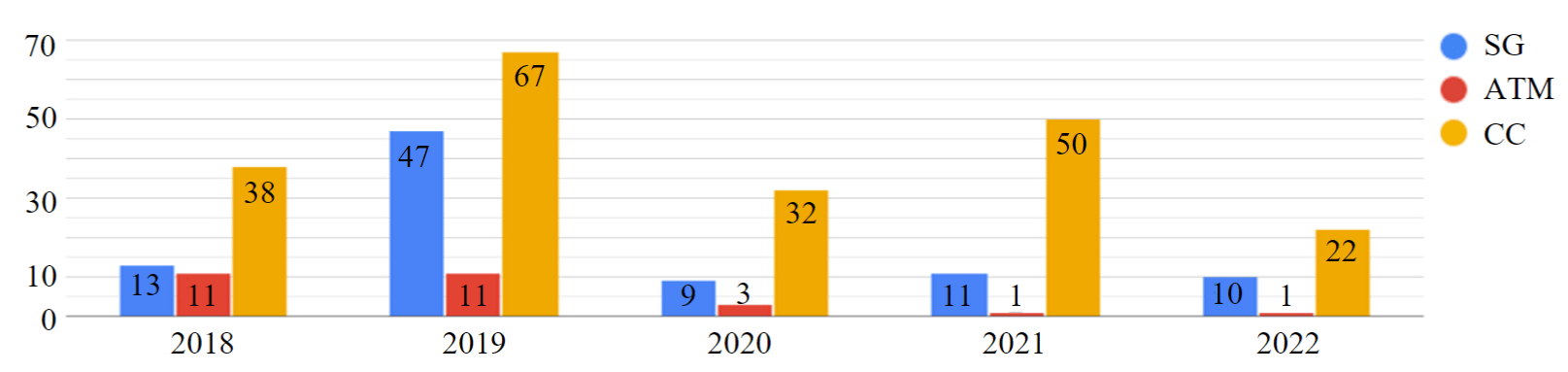
Fig.1. TDS part failures in haul trucks from 2018 to 2022
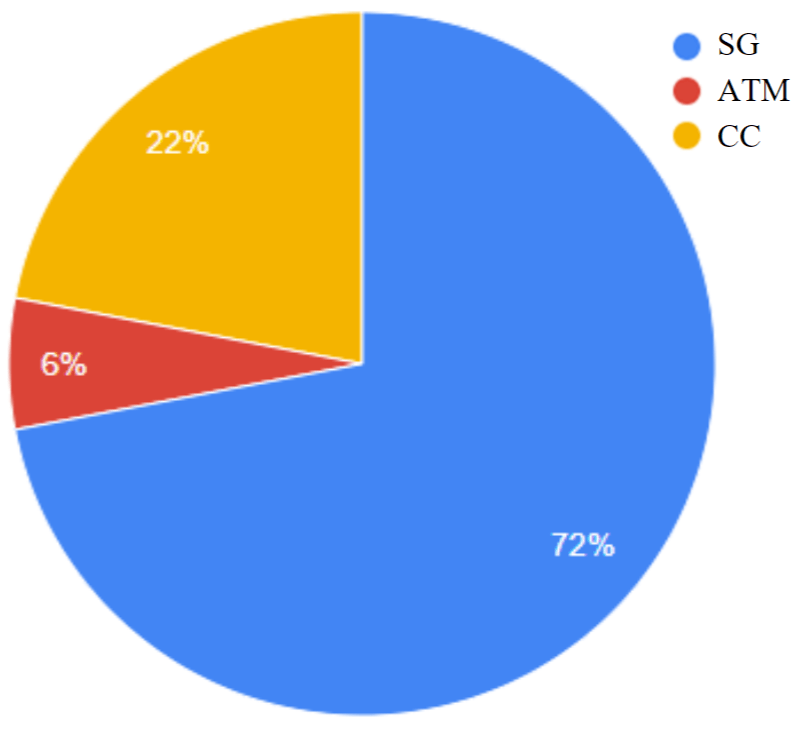
Fig.2. TDS repair costs breakdown from 2018 to 2022
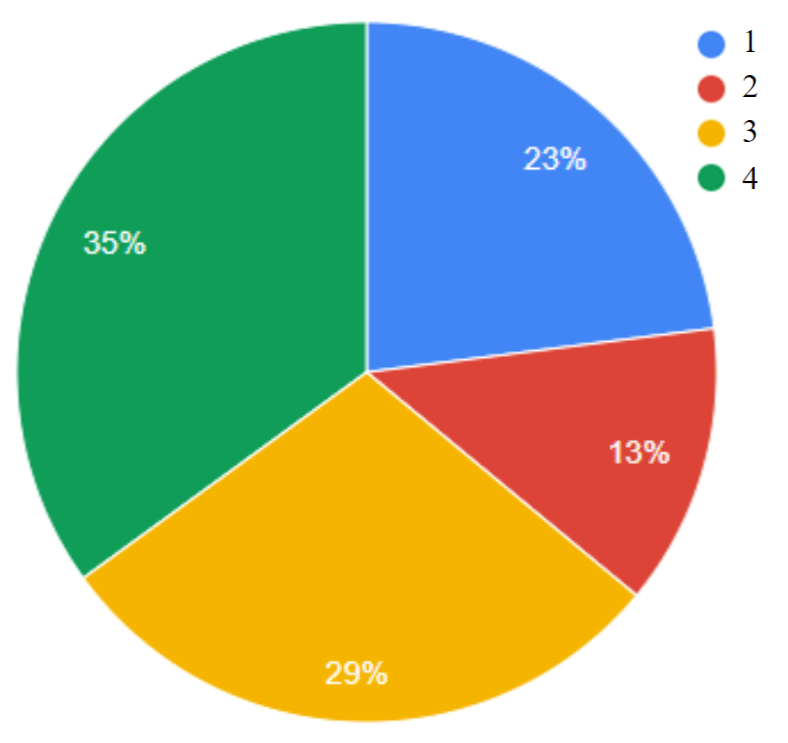
Fig.3. SG failure causes 1 – bearing assembly; 2 – other; 3 – manufacturing defect; 4 – stator winding lead burn-off
Taking into consideration the frequency of SG malfunctions and the largest share of SG costs in TDS restoration, the article will now focus on analyzing TDS failures resulting from SG failures.
Figure 3 illustrates the distribution of SG failuresby individual part failures, which is based on a dataset of 90 failures in haul trucks. SG failures happen due to the challenging and adverse operating conditions and modes experienced by haultrucks, which differ from those of stationary electric drives. These conditions include fluctuating climatic conditions, high levels of dust and humidity, frequent starts and stops, and high thermal and vibration loads [31-33].
Considering the demanding conditions ranging from temperate climates to northern latitudes in which haul trucks operate [34-36], the SG mustwithstand the impact of particular environmental factors and needs to meet several requirements:
- ambient temperature ranging from –50 to +50 °C;
- permissible upper value of the relative humidity of 100 % at a temperature of 25 °С;
- operation at an altitude up to 1,200 m above sea level;
- the IP21 rating of the generator in accordance with the GOST 14254-96 titled “Degrees of protection provided by enclosures (IP code)”;
- operating conditions corresponding to the M28 design category according to GOST 17516.1-90 titled “Electrical articles. General requirement for environment mechanical stability”;
- differential pressure at the inlet duct and filters not exceeding 1 kPa at an air flow rate of 1 m3/s;
- maximum bearing temperature not exceeding 125 °C;
- vibration velocities not exceeding 10 mm/s at idle and 15 mm/s under load;
- the electric drive must ensure the reliable operation of a haul truck at various mines with dust concentrations of up to 10 mg/m3.
Let us consider all types of SG faults in more detail from the most to least common as shown in Fig.3. The “other” category includes the following failure causes: coil deformations caused by transportation; winding displacement in the direction of rotation; short circuit at the stator winding lead.
The study revealed that during operation, a conductive path formed between the generator leadsdue to dust and moisture accumulationon the surfaces of the terminal blocks. As a result, an interphase short circuit occurred, leading to an SG failure. Considering the SG’s operating conditions, it is recommended to improve the insulation of the stator winding lead in order to increase insulation.
Nearly one-third of SG failures occurred due to bearing assembly issues, including the following: bearing roller failure (defective bearing); bearing separator failure (manufacturing defect); lack of or an insufficient amount of lubrication.
Often, one cause of failure triggers another. For instance, insufficient lubrication in the bearing assembly leads to a separator failure. Moreover, it results in overheating within the bearing assembly as the heat generated during operation cannot be uniformly dissipated [37, 38]. To minimize such failures, it is necessary to improve incoming quality control procedures and perform ongoing health checks during operation.
One of the reasons for SG failures is the low quality of components caused by the negligence of electrical machine assemblers.
Now we will discuss several individual SG issues that led to haul truck failures and downtime:
- Rotor excitation coil burn-off at the junction with the lead. Such a failure is caused by the lack or low quality of solderingat the junction between the generator pole and the lead to the slip rings at the connection with the terminal strip.
- Damage to the SG’s stator winding caused by a broken piece of the pole core. The probable reason for the failure of this component, which operates under impact loads, is the low strength and plastic characteristics, imperfections in the cast structure, and the absence of heat treatment that should have enhanced the mechanical properties and material structure.
- Fracture of the stator winding lead due to insufficient bolt tightening.
- Damage to the SG’s winding as a result of a short circuit to frame. The reason for the damage is the failure to comply with the requirements of the design documentation for the isolation of the outlet busbars or process flow errors.
One of the major types of faults is the stator winding lead burn-off. This category of faults includes the stator winding lead burn-off from the conducting ring of the stator winding and coil-to-coil connection faults in the winding [39]. The most probable cause is high vibration levels [40-42] exceeding permissible ones. The prolonged exposure to vibrations is a recognized risk factor for various diseases among truck drivers [43-45]. Furthermore, it should be considered that during the operation of a haul truck, clayey sediment could accumulate on the SG’s housing cavity. This accumulation causes a deterioration in heat dissipation from the windings [46-48], as well as an imbalance and increased vibration.
To investigate potential causes for faults in windings, we conducted vibration tests that were aimed at determining general vibration levels and their spectra in various operating modes of a diesel generator set (DGS). In our tests, we used a reconditioned generator operating at an open-pit mine in the Kemerovo region. The following operating modes were tested: idling at speeds of 900 rpm and 1,900 rpm; with loads applied to the braking resistor at 800 rpm and 1,800 rpm.
During the tests, it was observed that the maximum vibration level occurs at rpm values ranging from 1,800 to 1,900. Therefore, for further analysis, we will focus solely on these rotational frequencies.
Figure 4 shows the 14 vibration measurement locations used in our tests:
- points 1, 2, and 3: the vertical, horizontal, and axial vibrations of the bearing assembly of the generator from the slip ringside;
- points 4, 5, and 6: the vertical, horizontal, and axial vibrations of the generator frame from the diesel engine side;
- points 7, 8, and 9: the vertical, horizontal, and axial vibrations of the generator’s left support from the diesel engine side;
- points 10 and 11: the vertical and axial vibrations of the diesel engine cylinder block from the generator side;
- points 12 and 13: the vertical and horizontal vibrations of the diesel engine cylinder block from the radiator side;
- point 14: the horizontal vibration of the DGS frame under the diesel engine.
Discussion of the results
Table 1 presents the results of measuring the root mean square (RMS) values of the DGS’s vibration velocity within the frequency range of 10 to 5,000 Hz. The data shows that both at idle and under load, the vibration of the generator frame remains below the limit of 10 and 15 mm/s, respectively. The exception is some non-standardized points near the generator’s bearing shield. It is worth noting that the overall vibration levels in the engine area at individual pointsare considerably higher than in the generator area. The results are presented as relative units compared to the permissible values for the generator’s vibration velocity, with values exceeding the permissible limits highlighted in bold.
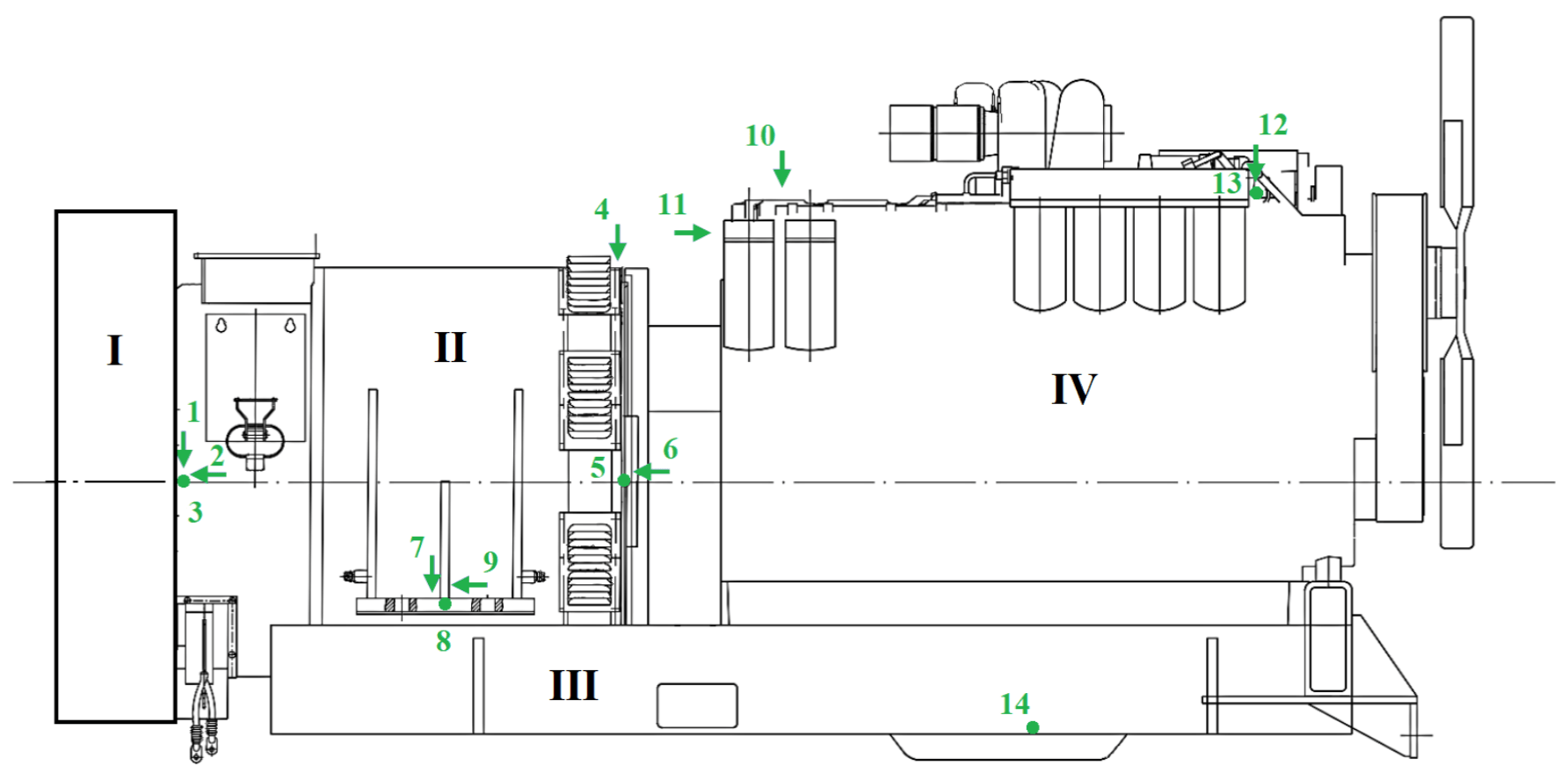
Fig.4. Measurement locations for vibration tests conducted on a diesel generator set I – fan casing; II – synchronous generator; III – diesel generator set frame; IV – diesel engine
Table 1
Relative RMS values of the generator’s vibration velocity, r.u.
Measurementlocations |
Idling at n = 900 rpm |
Idling at n =1,900 rpm |
Load on the braking resistor at n = 800 rpm, I = 250 A |
Load on the braking resistor at n =1,800 rpm, I = 330A |
1 |
0.46 |
1.05 |
0.31 |
0.89 |
2 |
0.58 |
1.62 |
0.44 |
1.08 |
3 |
0.31 |
1.57 |
0.27 |
1.30 |
4 |
0.36 |
0.55 |
0.31 |
0.48 |
5 |
0.22 |
0.63 |
0.13 |
0.42 |
6 |
0.27 |
0.80 |
0.23 |
0.57 |
7 |
0.41 |
0.56 |
0.28 |
0.69 |
8 |
0.26 |
0.95 |
0.21 |
0.68 |
9 |
0.27 |
0.67 |
0.20 |
0.49 |
10 |
0.39 |
1.08 |
0.29 |
0.55 |
11 |
0.22 |
1.34 |
0.16 |
0.38 |
12 |
0.45 |
3.71 |
0.34 |
1.44 |
13 |
0.27 |
0.53 |
0.15 |
0.43 |
14 |
0.47 |
1.07 |
0.30 |
1.77 |
During the tests, the DGS’s vibration acceleration values were measured for two frequency ranges: up to 55 Hz and up to 200 Hz, as specified in the GOST 17516.1-90 titled “Electrical articles. General requirement for environment mechanical stability” for the M28 design category. The results are presented in Table 2, with indicators exceeding the operating limit highlighted in bold. Based on the results, it can be concluded that the external impact on the generator within the frequency range of 0 to 55 Hz complies with the M28 design category requirements, as stated in GOST 17516.1-90. However, the primary contribution to the overall level of generator vibration comes from harmonics with frequencies ranging from 60 to 300 and 400 Hz, which exhibit significantly higher magnitudes compared to vibrations within the 0-55 Hz range. These harmonics pose the greatest risk to the generator’s winding as its resonant frequencies lie within this range. Therefore, the M28 requirements are not applicable to this particular generator. Instead, the M37 design category requirements regarding units installed on piston engines should be used (frequencies ranging from 0.5 to 500 Hz; vibration acceleration up to 100 m/s2).
Table 2
Maximum generator vibration accelerations relativeto the boundary value, frequency ranges 0-55/0-200 Hz, r.u.
Measurementlocations |
Idling at n = 900 rpm |
Idling at n =1,900 rpm |
Load on the braking resistor at n = 800 rpm, I = 250 A |
Load on the braking resistor at n =1,800 rpm, I =330A |
1 |
0.043/0.135 |
0.106/0.444 |
0.024/0.199 |
0.101/0.457 |
2 |
0.092/0.171 |
0.158/0.605 |
0.037/0.265 |
0.158/0.485 |
3 |
0.011/0.123 |
0.047/1.630 |
0.014/0.146 |
0.038/1.930 |
4 |
0.033/0.111 |
0.068/0.167 |
0.017/0.218 |
0.060/0.321 |
5 |
0.019/0.058 |
0.085/0.187 |
0.024/0.033 |
0.093/0.166 |
6 |
0.028/0.087 |
0.065/0.359 |
0.014/0.147 |
0.084/0.340 |
7 |
0.028/0.164 |
0.045/0.516 |
0.025/0.139 |
0.075/0.808 |
8 |
0.035/0.084 |
0.095/0.456 |
0.027/0.119 |
0.139/0.404 |
9 |
0.025/0.088 |
0.061/0.264 |
0.016/0.124 |
0.076/0.297 |
10 |
0.020/0.096 |
0.098/0.156 |
0.009/0.169 |
0.107/0.201 |
11 |
0.013/0.036 |
0.210/0.184 |
0.019/0.047 |
0.073/0.218 |
12 |
0.012/0.053 |
0.614/0.659 |
0.019/0.148 |
0.212/0.440 |
13 |
0.034/0.075 |
0.033/0.259 |
0.017/0.077 |
0.065/0.240 |
14 |
0.024/0.328 |
0.084/0.729 |
0.026/0.235 |
0.133/3.150 |
Figure 5 presents the vibration spectrum of the diesel engine cylinder block for the most active zone (frequency ranges of 1.5 to 2.5 and 3 to 3.5 kHz). The extent to which these high-frequency components affect the generator remains unknown.
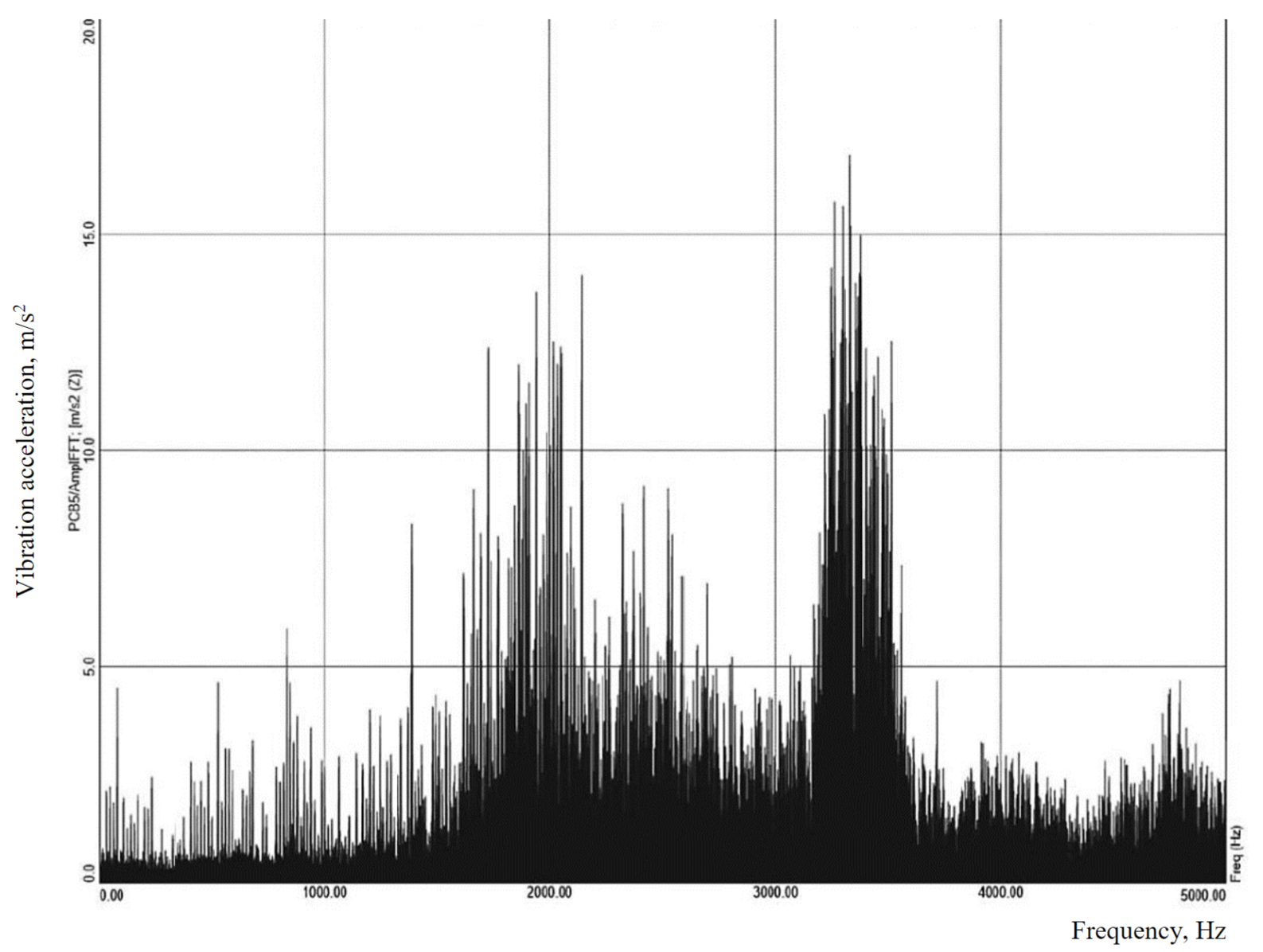
Fig.5. Vibration acceleration spectrum of the diesel engine cylinder block from the radiator side in the vertical direction (point 12)
Table 3 provides the vibration acceleration values for two measurement locations: the generator’s left support from the diesel engine side (point 8) and the DGS frame under the diesel engine (point 14). These values are based on the harmonics of the rotation frequency at 1,846 rpm, 330 A for the braking resistor being loaded. Table 3 demonstrates that the diesel engine is a distinct source of vibration at harmonics 3.5 and 5. Figure 6 illustrates the vibration acceleration spectrum for the aforementioned measurement locations. Importantly, the spectrum type remains consistent regardless of the generator’s load, indicating that the vibration is of a mechanical nature.
Table 3
Vibration accelerations of the generator support and the DGS frame under the diesel engine in the horizontal direction
Frequency, Hz |
Harmonic number |
Vibration acceleration, r.u. |
|
Generator support |
Diesel engine frame |
||
31.01 |
1 |
0.13 |
0.09 |
61.59 |
2 |
0.22 |
0.05 |
77.09 |
2.5 |
0.44 |
0.06 |
108.44 |
3.5 |
0.15 |
0.47 |
152.16 |
5 |
0.08 |
3.13 |
1093.57 |
36.5 |
0.07 |
0.7 |
1131.31 |
37 |
0.15 |
1.1 |
1167.99 |
38 |
0.05 |
0.96 |
The high values observed in the axial vibration of the generator’s bearing assembly (point 3) are associated with the harmonics within the frequency range from 150 Hz to 200 Hz, as indicated in Table 4. This occurrence can be attributed to the resonant characteristics of the part. When testing a similar generator at a plant site, it was found that the natural frequency of the generator’s bearing shield was 180 Hz, as depicted in Fig.7.
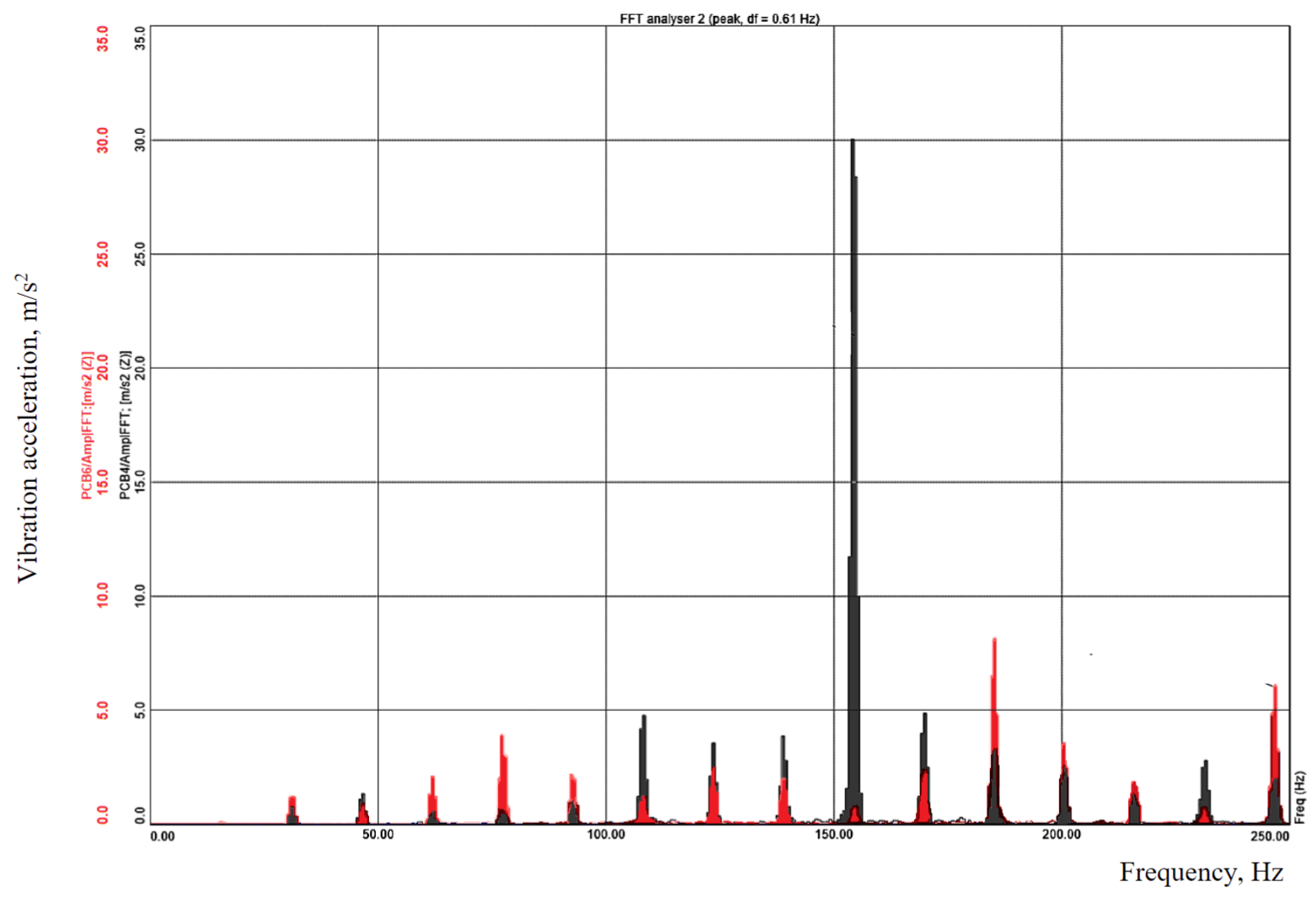
Fig.6. Vibration acceleration spectrum of the generator’s support (point 8 – red) and the DGS frame under the diesel engine (point 14 – black) in the horizontal direction at 1,846 rpm
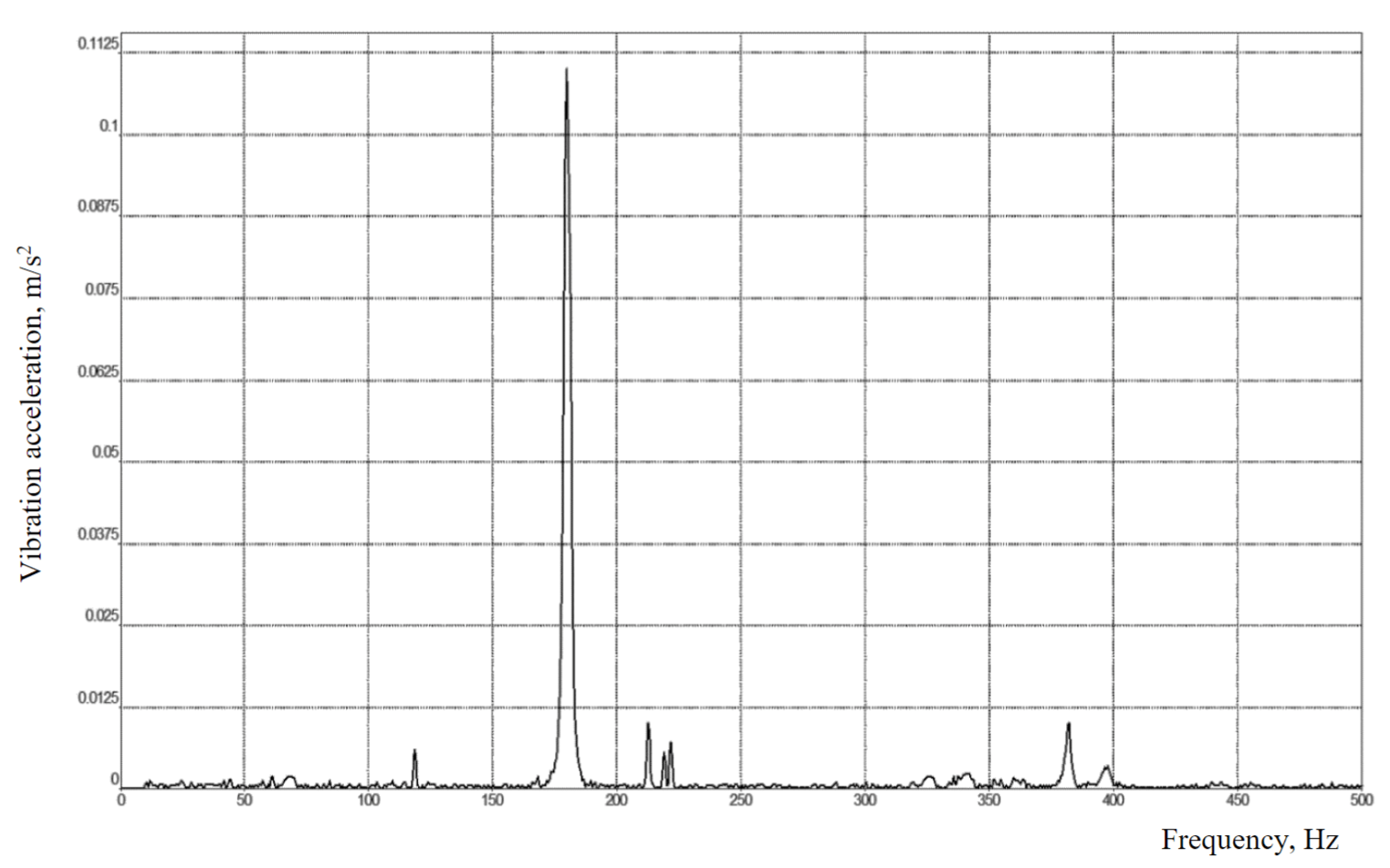
Fig.7. Vibration acceleration spectrum of the generator’s end shield in the axial direction
Table 4
Vibration acceleration of the bearing assembly in the axial direction by frequency harmonics at 1,914 rpm, 325 A
Frequency, Hz |
31.7 |
63.6 |
95.2 |
127.1 |
143.3 |
159.2 |
175.3 |
190.9 |
205.2 |
Harmonic number |
1 |
2 |
3 |
4 |
4.5 |
5 |
5.5 |
6 |
6.5 |
Vibration acceleration, r.u. |
0.01 |
0.07 |
0.21 |
0.31 |
0.35 |
0.47 |
1.26 |
1.92 |
1.62 |
Conclusion
Based on the results of vibration tests, this article examined traction drive system (TDS) failures in haultrucks, analyzed the causes of synchronous generator (SG) failures, and conducted bench tests of a diesel generators set (DGS) to identify the causes of stator winding failures. The following conclusions can be drawn:
- Our analysis of SG failures revealed that the stator winding (35 %) and the bearing assembly (29 %) are the functional units with the highest failure degrees. Failures in the stator winding encompass issues such as stator winding lead burn-off and coil-to-coil connection faults in the winding.
- The primary cause of stator winding failures is the excessive external vibration impact on the generator, surpassing the levels given in relevant technicalspecifications.
- The general level ofthe vibration velocity of the generator frame at speeds ranging from 1,800 to 1,900 rpm does not exceed the permissible values outlined in the regulatory documents.
- The external mechanical impact on the generator does not align with the M28 design category requirements as defined in GOST 17516.1-90 titled “Electrical articles. General requirement for environment mechanical stability”. It has been determined that the M37 design category requirements should be used (frequencies ranging from 0.5 Hz to 500 Hz with vibration acceleration of up to 100 m/s2).
- The test results indicate that generator vibration is practically unaffected by its load and is primarily attributed to mechanical causes.
- The most hazardous vibrations to the generator windings lie within the frequency range of 60 Hz to 200 Hz. The engine has been identified as the source of vibrations within this frequency range, at least for certainharmonics.
- The issue of stator winding damage is complex, and its root cause lies not only in the vibrations of the diesel engine or generator but also in the natural frequencies of the winding or its fixtures.
References
- Kozyaruk А.Е., Kamyshyan A.M. Improving the Energy Efficiency of the Electromechanical Transmission of an Open-pit Dump Truck. Journal of Mining Institute. Vol. 239, p. 576-582. DOI: 10.31897/PMI.2019.5.576
- Patterson S.R., Kozan E., Hyland P. Energy efficient scheduling of open-pit coal mine trucks. European Journal of Operational Research. 2017. Vol. 262. Iss. 2, p. 759-770. DOI: 1016/j.ejor.2017.03.081
- Dubinkin D., Sadovets V., Syrkin I., Chicherin I. Assessment of the Need to Create Control Sytem of Unmanned Dump Truck. E3S Web of Conferences. 2020. Vol. 177. N 03022. DOI: 10.1051/e3sconf/202017703022
- Kuznetsov D., Kosolapov A. Dynamic of performance of open-pit dump trucks in ore mining in severe climatic environment. Transportation Research Procedia. 2022. Vol. 63, p. 1042-1048. DOI: 10.1016/j.trpro.2022.06.104
- Zhuravlev A.G., Isakov M.V. Experimental testing of open pit dump trucks in operating conditions. Mining Informational and Analytical Bulletin. 2020. N 3-1, p. 530-542 (in Russian). DOI: 10.25018/0236-1493-2020-31-0-530-542
- Kuzin E.G., Рudov E.Yu., Dubinkin D.M. Analysis of failures of mining dump truck components under operating conditions. Mining equipment and electromechanics. N 2, p. 55-61 (in Russian). DOI: 10.26730/1816-4528-2021-2-55-61
- Vlasov Yu.A., Spirin E.N., Lyapin A.N. Analysis of the reasons of low operational reliability of career dump trucks. Scientific review. Technical sciences. N 5, p. 37-44 (in Russian).
- Semykina A., Zagorodnii N., Novikov A. Study of the effectiveness of the organization of the system of maintenance and repair of quarry transport of mining and processing plants. Transportation Research Procedia. 2022. Vol. 63, p. 983-989. DOI: 10.1016/j.trpro.2022.06.097
- Dubinkin D.M., Kartashov A.B., Arutyunyan G.A. et al. Development of a program and methodology for preliminary testing of an autonomous quarry dump truck. Mining equipment and electromechanics. N 6, p. 59-65. DOI: 10.26730/1816-4528-2021-6-59-65
- Zhen Wang, Lihui Zhao, Zhiguo Kong et al. Development of accelerated reliability test cycle for electric drive system based on vehicle operating data. Engineering Failure Analysis. 2022. Vol. 141. N 106696. DOI: 10.1016/j.engfailanal.2022.106696
- Makharatkin P.N., Abdulaev E.K., Vishnyakov G.Yu. et al. Increase of efficiency of dump trucks functioning on the basis of justification of their rational speed by means of simulation modeling. Mining Informational and Analytical Bulletin. N 6-2, p. 237-250 (in Russian). DOI: 10.25018/0236_1493_2022_62_0_237
- Yanbiao Feng, Zuomin Dong. Integrated design and control optimization of fuel cell hybrid mining truck with minimized lifecycle cost. Applied Energy. 2020. Vol. 270. N 115164. DOI: 10.1016/j.apenergy.2020.115164
- Bolshunova O.M., Korzhev A.A., Kamyshyan A.M. Adaptive control system of dump truck traction electric drive. IOP Conference Series: Materials Science and Engineering. 2018. Vol. 327. Iss. 5. N 052007. DOI: 1088/1757-899X/327/5/052007
- Yanbiao Feng, Qiang Liu, Yong Li et al. Energy efficiency and CO2 emission comparison of alternative powertrain solutions for mining haul truck using integrated design and control optimization. Journal of Cleaner Production. 2022. Vol. 370. N 133568. DOI: 10.1016/j.jclepro.2022.133568
- Seifoori S., Parrany A.M., Khodayari M. A high-cycle fatigue failure analysis for the turbocharger shaft of BELAZ 75131 mining dump truck. Engineering Failure Analysis. 2020. Vol. 116. N 104752. DOI: 10.1016/j.engfailanal.2020.104752
- Klebanov A.F., Sizemov D.N., Kadochnikov M.V. Integrated Approach to Remote Monitoring of Technical and Operating Conditions of Mine Dump Trucks. Russian Mining Industry. N 2, p. 75-81 (in Russian). DOI: 10.30686/1609- 9192-2020-2-75-81
- Koteleva N., Korolev N., Zhukovskiy Yu., Baranov G. A Soft Sensor for Measuring the Wear of an Induction Motor Bearing by the Park’s Vector Components of Current and Voltage. Sensors. Vol. 21. Iss. 23. N 7900. DOI: 10.3390/s21237900
- Kundu P., Darpe A.K., Kulkarni M.S. Weibull accelerated failure time regression model for remaining useful life prediction of bearing working under multiple operating conditions. Mechanical Systems and Signal Processing. 2019. Vol. 134. N 106302. DOI: 1016/j.ymssp.2019.106302
- Jinjiang Wang, Peilun Fu, Laibin Zhang et al. Multilevel Information Fusion for Induction Motor Fault Diagnosis. IEEE/ASME Transactions on Mechatronics. 2019. Vol. 24. Iss. 5, p. 2139-2150. DOI: 10.1109/TMECH.2019.2928967
- Minakova T. E., Malarev V. I., Korzhev A. A. Method to identify operating regimes of asynchronous drivers by subharmonic parameters in mining. Mining Informational and Analytical Bulletin. N 11, p. 96-108 (in Russian). DOI: 10.25018/0236_1493_2022_11_0_96
- Zhukovskiy Yu.L., Vasilev B.Y., Korolev N.A., Malkova Y.M. Analysis of the behavior of asynchronous electric drive with a closed scalar control system when changing the inductance of the magnetizing circuit. Indonesian Journal of Science and Technology. 2023. Vol. 8. N 1, p. 65-78. DOI: 10.17509/ijost.v8i1.51983
- Glowacz A., Glowacz W., Kozik J. et al. Detection of Deterioration of Three-phase Induction Motor using Vibration Signals. Measurement Science Review.2019. Vol. 19. N 6, p. 241-249. DOI: 10.2478/msr-2019-0031
- Barański M. New vibration diagnostic method of PM generators and traction motors – detecting of vibrations caused by unbalance. IEEE International Energy Conference (Energycon), 13-16 May 2014, Cavtat, Croatia. IEEE, 2014. P. 28-32. DOI: 10.1109/ENERGYCON.2014.6850401
- Salomon C.P., Ferreira C., Sant’Ana W.C. et al. A Study of Fault Diagnosis Based on Electrical Signature Analysis for Synchronous Generators Predictive Maintenance in Bulk Electric Systems. 2019. Vol. 12. Iss. 8. N 1506. DOI: 10.3390/en12081506
- Korolev N., Kozyaruk A., Morenov V. Efficiency Increase of Energy Systems in Oil and Gas Industry by Evaluation of Electric Drive Lifecycle. 2021. Vol. 14. Iss. 19. N 6074. DOI: 10.3390/en14196074
- Qi Gong, Bingzhi Chen, Yonghua Li, Pengpeng Zhi. Reliability Assessment Based on GO Method of Metro Traction System.Advances in Materials Science and Engineering. 2020. Vol. 2020. N 2829084, p. 1-13. DOI: 10.1155/2020/2829084
- Jianqiang Liu, Shi Li, Yong Jiang, Krishnamurthy M. Reliability Evaluating for Traction Drive System of High-speed Electrical Multiple Units. IEEE Transportation Electrification Conference and Expo (ITEC), 16-19 June 2013, Detroit, USA. IEEE, 2013, 1-6. DOI: 10.1109/ITEC.2013.6574491
- Shuai Lin, Xiaochun Fang, Fei Lin et al. Reliability of rail transit traction drive system – A review. Microelectronics Reliability. 2018. Vol. 88-90, p. 1281-1285. DOI: 10.1016/j.microrel.2018.07.037
- Каbikеnоv S.J., Buyаlich G.D., Sembayev N.S. Ways to Upgrade the Utilisation Efficiency of Open-Pit Dump Trucks. PalArch's Journal of Archaeology of Egypt/Egyptology. 2020. Vol. 17. N 3, p. 602-614. DOI: 10.48080/jae.v17i3.138
- Andreeva L.I., Ushakov Yu.Yu. Research of operational reliability of quarry dump trucks. News of the Ural State Mining University.3 (43), p. 74-77 (in Russian). DOI: 10.21440/2307-2091-2016-3-74-77
- Vinogradov A.B., Gnezdov N.E., Chistoserdov V.L., Korotkov A.A. Mining Dump Trucks Electrical Traction Equipment Improvement // XI International Conference on Electrical Power Drive Systems (ICEPDS), 04-07 October 2020, St. Petersburg, Russia. IEEE, 2020, p. 1-4. DOI: 10.1109/ICEPDS47235.2020.9249279
- Ziran Guo, Ming Yang, Xu Huang. Bearing fault diagnosis based on speed signal and CNN model. Energy Reports. 2022. Vol. 8. S. 13, p. 904-913. DOI: 10.1016/j.egyr.2022.08.041
- Tsyglianu P.P., Romasheva N.V., Fadeeva M.I., Petrov I.V. Engineering projects in the Russian fuel and energy complex: Actual problems, factors and recommendations for development. 2023. N 3, p. 45-51. DOI: 10.18796/0041-5790-2023-3-45-51
- Borisenko A.N., Oleinikov A.V., Semenov M.N. Improving maintenance and preventive over-haul programs for open pit dump trucks at SUEK-Khakassia. Mining Informational and Analytical Bulletin. N 6, p. 104-119 (in Russian).DOI: 10.25018/0236_1493_2021_6_0_104
- Khalturin A.A., Parfenchik K.D., Shpenst V.A. Features of Oil Spills Monitoring on the Water Surface by the Russian Federation in the Arctic Region. Journal of Marine Science and Engineering. 2023. Vol. 11. Iss. 1. N 111. DOI: 10.3390/jmse11010111
- Petrov D.S., Korotaeva A.E., Pashkevich M.A., Chukaeva M.A. Assessment of heavy metal accumulation potential of aquatic plants for bioindication and bioremediation of aquatic environment. Environmental Monitoring and Assessment. 2023. Vol. 195. N 122. DOI: 10.1007/s10661-022-10750-0
- Jin Woo Oh, Dogun Park, Jongpil Jeong. Fault Detection for Lubricant Bearing with CNN. 2nd International Conference on Intelligent Autonomous Systems (ICoIAS), 28 February – 02 March 2019, Singapore. IEEE, 2019, p. 142-145. DOI: 1109/ICoIAS.2019.00031
- Karpat F., Kalay O.C., Dirik A.E. et al. Convolutional Neural Networks Based Rolling Bearing Fault Classification Under Variable Operating Conditions. International Conference on INnovations in Intelligent SysTems and Applications (INISTA), 25-27 August 2021, Kocaeli, Turkey. IEEE, 2021, p. 1-6. DOI: 10.1109/INISTA52262.2021.9548378
- Ehya H., Lyng Rødal G.L., Nysveen A., Nilssen R. Condition Monitoring of Wound Field Synchronous Generator under Inter-turn Short Circuit Fault utilizing Vibration Signal. 23rd International Conference on Electrical Machines and Systems (ICEMS), 24-27 November 2020, Hamamatsu, Japan. IEEE, 2020. P. 177-182. DOI: 10.23919/ICEMS50442.2020.9291088
- Andreeva L.I. Machinery availability evaluation in mining. Mining Informational and Analytical Bulletin. N 5, p. 136-143 (in Russian). DOI: 10.25018/0236-1493-2018-5-0-136-143
- Rudakov M.L., Duka N.E. Analysis of properties of deafeners to design personal ear protectors. Mining Informational and Analytical Bulletin. N 3, p. 165-180 (in Russian). DOI: 10.25018/0236_1493_2022_3_0_165
- Ustinov D., Nazarychev A., Pelenev D. et al. Investigation of the Effect of Current Protections in Conditions of Single-Phase Ground Fault through Transient Resistance in the Electrical Networks of Mining Enterprises. Energies. 2023. Vol. 16. Iss. 9. N 3690. DOI: 10.3390/en16093690
- Gendler S.G., Prokhorova E.A. Assessment of the cumulative impact of occupational injuries and diseases on the state of labor protection in the coal industry. Mining Informational and Analytical Bulletin. N 10-2, p. 105-116. DOI: 10.25018/0236_1493_2022_102_0_105
- Gendler S.G., Fazylov I.R., Abashin A.N. The results of experimental studies of the thermal regime of oil mines in the thermal method of oil production. Mining Informational and Analytical Bulletin. N 6-1, p. 248-262 (in Russian). DOI: 10.25018/0236_1493_2022_61_0_248
- Babyr K.V., Ustinov D.A., Pelenev D.N. Improving Electrical Safety of the Maintenance Personnel in the Conditions of Incomplete Single-Phase Ground Faults. Occupational Safety in Industry. N8, p.55-61 (in Russian). DOI: 10.24000/0409-2961-2022-8-55-61
- Xihui Liang, Ming J. Zuo, Zhipeng Feng. Dynamic modeling of gearbox faults: A review. Mechanical Systems and Signal Processing. 2018. Vol. 98, p. 852-876. DOI: 10.1016/j.ymssp.2017.05.024
- Haijun Zhang, Mingjie Zhang, Xin Wang. Fracture failure analysis of insulation with initial crack defect for stator end-winding in induction motor by using magnetic-structural coupling model. Engineering Failure Analysis. 2023. Vol. 149. N 107239. DOI: 10.1016/j.engfailanal.2023.107239
- Yetgin A.G. Effects of induction motor end ring faults on motor performance. Experimental results. Engineering Failure Analysis. 2019. Vol. 96, p. 374-383. DOI: 10.1016/j.engfailanal.2018.10.019