A probabilistic study on hole cleaning optimization
- Ph.D. Associate Professor Sahand University of Technology ▪ Orcid
Abstract
Hole cleaning is considered as one of the most important drilling fluid functions. An efficient hole cleaning ensures a reliable well drilling practice with minimum troublesome problems. In this study, two main steps of hole cleaning, i.e., cuttings removal from under the bit and cuttings transport to the surface are discussed based on the drilling data of a shale formation. The traditional models for optimization of each step are presented. As the models require variety of input data, which are usually subjected to some extent of errors and uncertainties, the output of the model is also an uncertain parameter. Using Monte Carlo simulation, a simple probabilistic study was conducted to quantify the certainty level of the obtained results. Based on the result of this study, it is shown that for the proposed well, a good hole cleaning is expected. However, a more reliable decision for further hole cleaning optimization should be made considering the results of uncertainty analysis.
Introduction
Drilling fluids serve various important functions including hole cleaning, control of formation pore pressure, bit cooling, drill string lubrication, collection of formation data and providing borehole stability [1-4]. The success in drilling operation is significantly dependent on the degree, at which the hole is cleaned from rock cuttings. An efficient hole cleaning leads to improved rate of penetration (ROP) and can mitigate such drilling problems as stuck pipes, loss circulation, poor primary cementing operation, drilling bit misfunctioning, excessive torque and drag, etc. [5-7].
The expression “hole cleaning” is sometimes misinterpreted as cuttings transport, while, hole cleaning is a two-step process: removal of rock cuttings from under the bit and transportation of removed cuttings to the surface.
The efficiency of hole cleaning process is dependent on drilling operational parameters (flow rate of drilling fluid into the well), well geometry (inclination angle, eccentricity of drill string, hole size, drill string outer diameter, casing inner diameter etc.), drilling fluid properties (density and rheological characteristics) and rock cuttings properties (density, average diameter, cuttings volume etc.) [6-8].
Several researchers developed experimental, numerical and analytical models for prediction and optimization of hole cleaning process. In these works, the effects of drilling fluid composition and properties [9-11], type of drilling fluid [12, 13], drilling operational parameters [14-16], well geometry [8, 17, 18], cuttings content and their properties [19-21] and flow properties [22, 23] on the hole cleaning process are investigated. In some reseachers, different factors are considered using computational fluid dynamics (CFD) [6, 24].
Generally, a diverse range of input data is required for hole cleaning models. The amount and accuracy of these input data determines the effectiveness of developed models. The fact that majority of input data are subjected to some extent of errors, leads to some level of uncertainty in the model output. Human errors, mis-interpretation and simplifying procedures are the main sources of error in input data [25].
In this work, drilling data of a specific shale formation are used in traditional models for evaluation of hole cleaning efficiency. In addition, a probabilistic study is conducted to measure the extent of uncertainty in the outputs of hole cleaning models.
Methodology
Firstly, in this section, the traditional methods of hole cleaning optimization are presented and discussed. Then, a set of drilling data in a specific shale formation is presented. These data are used to evaluate the efficiency of hole cleaning, i.e., the effectiveness of cuttings removal from under the bit and cuttings transport to the surface. Finally, a probabilistic study, using Monte Carlo simulation is conducted to quantify the extent of uncertainty in the hole cleaning optimization process.
As it was mentioned earlier, hole cleaning is a two-step process: removal of rock cuttings from under the bit and transportation of removed cuttings to the surface. Therefore, the equations and traditional optimization techniques are presented separately for each part.
Cuttings removal from under the bit
For optimization of cuttings removal from under the bit, usually bit-related hydraulic parameters are investigated and maximized to achieve an efficient cuttings removal. However, the operational limitations, like mud pump rate, should be considered in the optimization procedure. The main bit-related hydraulic parameters are nozzle velocity, bit hydraulic power and jet impact force, which can be calculated as follows [26, 27]:
- nozzle velocity
where Q is the drilling fluid flow rate into the wellbore, m3/s; TFA is the total flow area of bit nozzles, m2;
- bit hydraulic power
where ∆Pb – is the pressure drop of drilling fluid cross the bit; MW is the mud weigh or drilling fluid density, kg/m3; Cd is the bit discharge coefficient (usually set at 0.95);
- jet impact force
Cuttings transport
During cuttings transport, rock cuttings tend to settle down in the hole, while drilling fluid is moving up in the annulus to the surface. Due to the complex nature of cuttings transport process, it is difficult to come up with accurate analytical solutions to analyze the carrying efficiency of drilling fluids. To overcome this challenge, two approaches are usually followed.
In the first approach, correlations, which are available for vertical, directional and horizontal wells, are used. One of the correlations, which is used commonly for evaluation of drilling fluid carrying capacity in vertical or near vertical wells, was defined by Robinson and Morgan, the equation has the following form [28]:
where CCI is carrying capacity index (cuttings carrying index); AV is annular velocity (m/s) of drilling fluid and k is the power law model constant, Pa·s.
CCI values of 1 or greater than 1 indicate good hole cleaning condition [28, 29].
In the second approach, drilling fluid velocity in the annulus upward (annular velocity) and cuttings slippage velocity downward (slip velocity) are compared and the cuttings transport velocity is determined as the difference between annular velocity and slip velocity:
where Va is annular velocity of drilling fluid and Vs is the cuttings slip velocity.
Also, a parameter called transport ratio can be defined based on annular and slip velocities
Higher values of transport ratio indicate more efficient cuttings transport. The main problem in this approach lies in the difficulties of slip velocity calculation. In the case of Newtonian fluids and for regularly shaped particles, the slip velocity (sometimes called as settling velocity) can be calculated by balancing the drag force and net gravitational force. However, for drilling fluids with complex rheological behavior and irregular shaped rock cuttings, slip velocity calculation will be much more difficult [30, 31].
In this study, simplified Chien correlation is used for slip velocity calculation. The correlation, based on calculation of drilling fluid apparent viscosity and particles Reynold number, has the following form for intermediate to turbulent flow regimes [32, 33]:
where ρc is cuttings density, kg/m3; dc is cuttings average diameter, m.
Based on the presented formulas it can be seen that any optimization in hole cleaning process requires careful adjustment of operational and technological parameters like drilling fluid flow rate, rheological properties and density.
Input drilling data
The required data for probabilistic study of hole cleaning, including drilling operational parameters (mud flow rate), drilling fluid properties (density and rheological characteristics) and rock cuttings properties (density and average diameter), were collected based on the drilling experience in a shale formation. The used drilling fluids show Bingham-Plastic rheological behavior. The formation has been drilled in several wells with different fluid and operational parameters based on the well available geological and technical conditions. The range of each parameter obtained from real drilling data:
- Drilling fluid properties: MW 1025.7-1090.4 kg/m3; PV 0.005-0.007 Pa·s; YP 7.18-9.58 Pa; Q 0.028-0.054 m3/s.
- Bit properties: TFA 6.41×10–4 m2; Cd 0.95.
- Well geometry: hole diameter 0.4445 m; drill string outer diameter 0.127 m.
- Cuttings properties: average diameter 1.996×10–3 m; density 2498.4 kg/m3.
Monte Carlo simulation
Monte Carlo simulation is a numerical technique, in which, random samples of input data are generated based on their distribution function. The model output (slip velocity, transport velocity, transport ratio, nozzle velocity, bit hydraulic power, jet impact force) is then calculated for each random number of input data. Therefore, instead of a single output value, there will be a distribution of model output, based on which, the occurrence probability of each output will be calculated [25, 34, 35]. In this study, Oracle Crystal Ball software is used for the probabilistic study of hole cleaning efficiency.
The distribution function of uncertain input parameters are presented in Table. As it can be seen from the table, triangle distribution is selected for input data, as the minimum, maximum and likeliest value of each parameter were known. The choice of triangular distribution is based on the fact that the exact distribution function could not be determined due to the lack of enough input data. However, there were ideas about minimum, maximum and the likeliest values, which justifies the use of triangular distribution function.
Distribution function of uncertain input data
Parameter |
Distribution type |
Distribution parameters |
||
Minimum |
Maximum |
Likeliest |
||
MW, kg/m3 |
Triangular |
1025.7 |
1090.4 |
1054.5 |
PV, Pa·s |
Triangular |
0.005 |
0.007 |
0.006 |
YP, Pa |
Triangular |
7.18 |
9.58 |
8.38 |
Q, m3/s |
Triangular |
0.028 |
0.054 |
0.044 |
Research results
For investigation of cuttings removal from under the bit, nozzle velocity, bit hydraulic power and jet impact force are analyzed. Fig.1 shows the occurrence probability of these parameters based on the Monte Carlo simulation. Presented results in the Figs. confirm that in the case of uncertain input data, output will not be a single value, but a distribution of possible values, which can be used to quantify the uncertainty.
To quantify the certainty bands, associated with the calculated nozzle velocity, bit hydraulic power and jet impact force, trend charts with specified certainty bands are presented as Fig.2.
Presented data can be used to state the output value with certainty level. For example, in Fig.2, c, it is evident that in the case of uncertain input data, the value of jet impact force lies in the range of 1732-4199 N with a probability of 90 %. Increasing the level of certainty of input data, will narrow down the certainty band of 90 %. Considering the conducted uncertainty analysis, it should be noted that for any further optimization of bit-related hydraulic parameters, certainty level of the outputs should be considered.
For investigation of cuttings transport, the CCI, transport velocity and transport ratio are analyzed. Fig.3 shows the occurrence probability of these parameters based on the Monte Carlo simulation. These figures confirm that in the case of uncertain input data, output will not be a single value, but a distribution of possible values, which can be used to quantify the uncertainty.
To quantify the certainty bands, associated with the calculated CCI and transport ratio, trend charts with specified certainty bands are presented as Fig.4.
Trends charts can help to identify the certainty associated with the outputs. As it is evident from the Fig.4, а, the CCI is greater than 1.42 with a certainty of 90 %. This shows the efficient cuttings transport in the proposed well. Analysis of the transport velocity and transport ratio also confirms the effective cuttings transport. For further optimization of CCI or any other cuttings transport indicator, certainty of the results should be considered, especially when input data are uncertain, as in the case of this study.
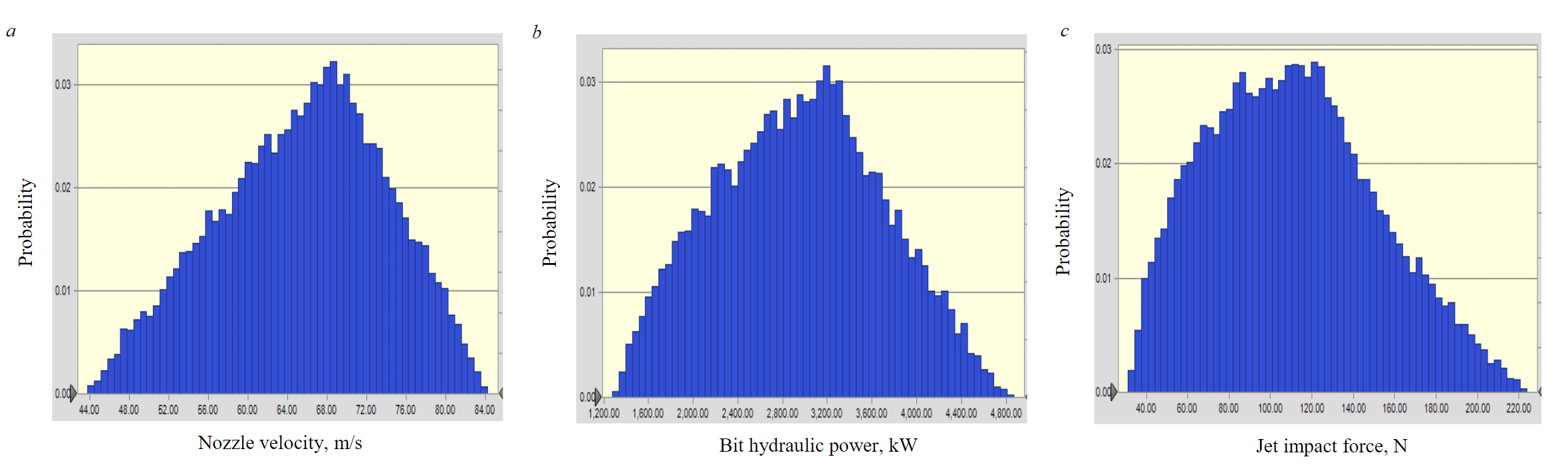
Fig.1. Occurrence probabilities of nozzle velocity (a), bit hydraulic power (b) and jet impact force (c)
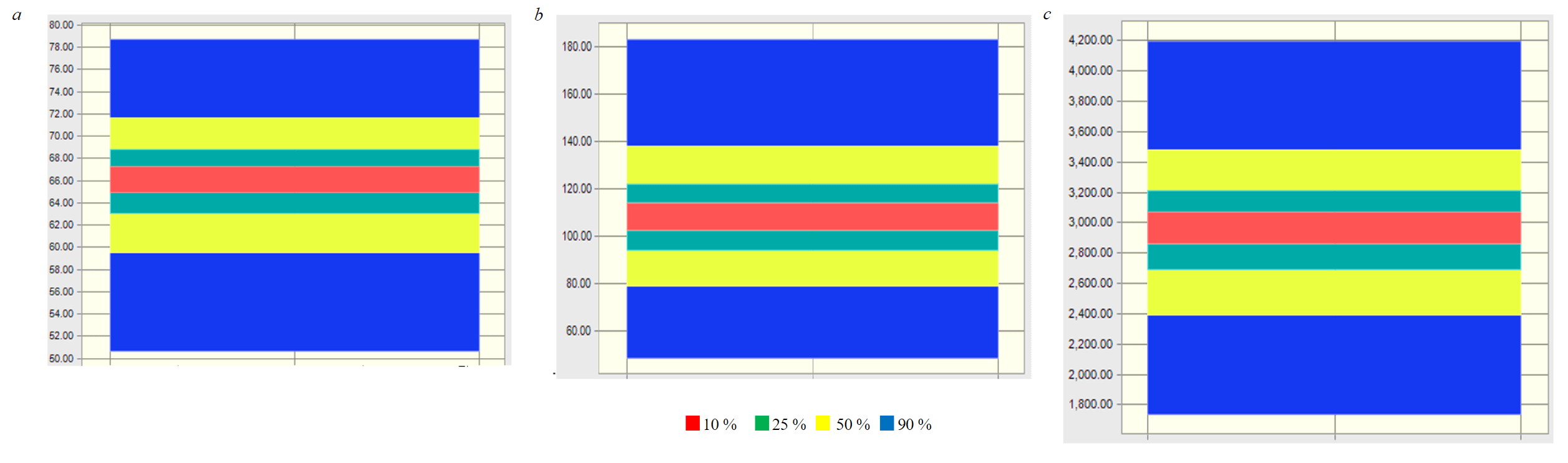
Fig.2. Certainty bands associated with nozzle velocity (a), hydraulic power (b) and jet impact force (c)
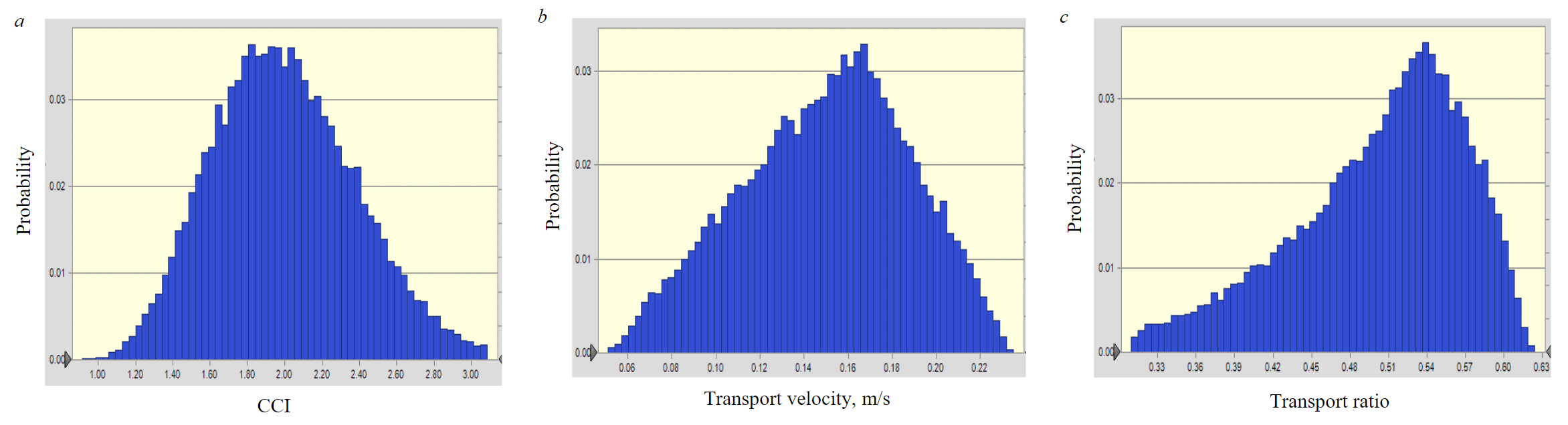
Fig.3. Occurrence probabilities of CCI (a), transport velocity (b) and transport ratio (c)
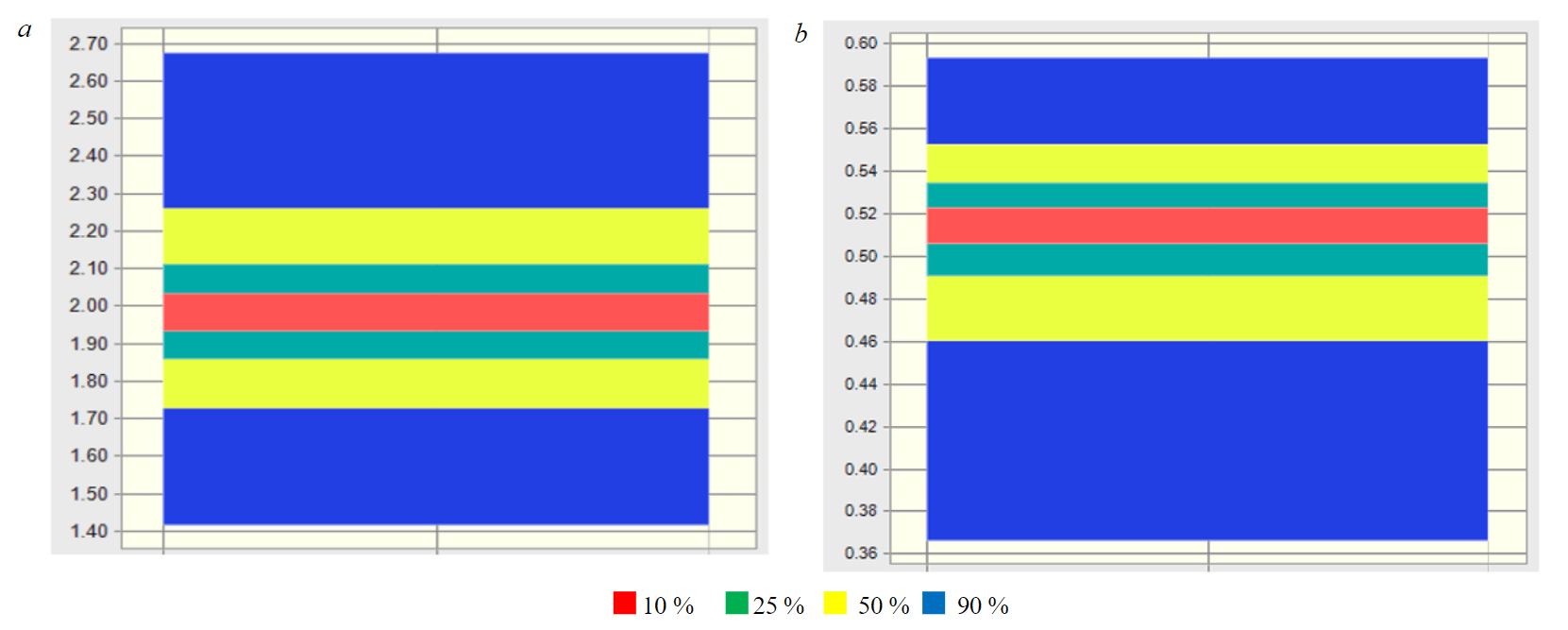
Fig.4. Certainty bands associated with CCI (a) and transport ratio (b)
Conclusion
One of the most important drilling fluid functions is efficient hole cleaning, which is necessary for an effective drilling practice with minimum operational difficulties. As all hole cleaning optimization models require variety of uncertain input data, the output also will be an uncertain value. In this work, using Monte Carlo simulation, a simple probabilistic study was conducted on traditional hole cleaning models to quantify the level of certainty/uncertainty in the calculation procedure. This approach may ensure a more reliable decision about optimization. Following conclusions can be made based on the obtained results:
- Results confirm that in the case of uncertain input data, there will be some extent of uncertainty in the parameters of hole cleaning optimization, i.e., nozzle velocity, bit hydraulic power, jet impact force, CCI, transport velocity and transport ratio.
- With known certainty level of each parameter, a more reliable decision can be made for further hole cleaning optimization.
- CCI had a value of greater than 1.42 with a certainty of 90 %, which indicates the efficient cuttings transport in the proposed well.
- Obtained occurrence probabilities of transport velocity and transport ratio also confirm the efficient cuttings transport in the proposed well.
References
- Abbas A.K., Alsaba M.T., Al Dushaishi M.F. Improving hole cleaning in horizontal wells by using nanocomposite water-based mud. Journal of Petroleum Science and Engineering. 2021. Vol. 203. N 108619. DOI: 10.1016/j.petrol.2021.108619
- Andrade G.M.P., Oechsler B.F., Coelho J.S.C. et al.Evaluation of characteristic diameter on barite settling in drilling fluids by Monte Carlo method. Journal of Petroleum Science and Engineering. 2021. Vol. 206. N 109072. DOI: 10.1016/j.petrol.2021.109072
- Ashena R., Hekmatinia A.-A., Ghalambor A. et al. Improving drilling hydraulics estimations – a case study. Journal of Petroleum Exploration and Production Technology. 2021. Vol. 11, p. 2763-2776. DOI: 10.1007/s13202-021-01203-4
- Assi A.H. Enhancing the Lifting Capacity of Drilling Fluids in Vertical Oil Wells. Iraqi Journal of Chemical and Petroleum Engineering. 2017. Vol. 18, p. 13-29.
- Awad A.M., Hussein I.A., Nasser M.S. et al.A CFD-RSM study of cuttings transport in non-Newtonian drilling fluids: Impact of operational parameters. Journal of Petroleum Science and Engineering. 2022. Vol. 208. Part C. N 109613. DOI: 10.1016/j.petrol.2021.109613
- 6.Badrouchi F., Rasouli V., Badrouchi N.Impact of hole cleaning and drilling performance on the equivalent circulating density. Journal of Petroleum Science and Engineering. 2022. Vol. 211. N 110150. DOI: 10.1016/j.petrol.2022.110150
- Barooah A., Khan M.S., Khaled M.S. et al. Investigation of cutting transport in horizontal/deviated annulus using visualization and pressure drop techniques for two-phase slurry flow. Journal of Natural Gas Science and Engineering. 2022. Vol. 100. N 104460. DOI: 10.1016/j.jngse.2022.104460
- Boyou N.V., Ismail I., Wan Sulaiman W.R. et al. Experimental investigation of hole cleaning in directional drilling by using nano-enhanced water-based drilling fluids. Journal of Petroleum Science and Engineering. 2019. Vol. 176, p. 220-231. DOI: 10.1016/j.petrol.2019.01.063
- Choupani M.A., Tabatabaee Moradi S.Sh., Tabatabaei Nejad S.A. Study on Attapulgite as Drilling Fluid Clay Additive in Persian Gulf Seawater. International Journal of Engineering. Transactions C: Aspects. 2022. Vol. 35. N 3, p. 587-595. DOI: 10.5829/ije.2022.35.03C.12
- Dvoynikov M.V., Nutskova M.V., Blinov P.A. Developments Made in the Field of Drilling Fluids by Saint Petersburg Mining University. International Journal of Engineering Transactions A: Basics. 2020. Vol. 33. Iss. 4, p. 702-711. DOI: 10.5829/ije.2020.33.04a.22
- Epelle E.I., Obande W., Okolie J.A., Wilberforce T. CFD modelling and simulation of drill cuttings transport efficiency in annular bends: Effect of particle size polydispersity. Journal of Petroleum Science and Engineering. 2022. Vol. 208. Part E. N 109795. DOI: 10.1016/j.petrol.2021.109795
- Ferroudji H., Rahman M.A., Hadjadj A., Ntow Ofei T. 3D numerical and experimental modelling of multiphase flow through an annular geometry applied for cuttings transport. International Journal of Multiphase Flow. 2022. Vol. 151. N 104044. DOI: 10.1016/j.ijmultiphaseflow.2022.104044
- Gbadamosi A.O., Junin R., Abdalla Y., Agi A. Experimental investigation of the effects of silica nanoparticle on hole cleaning efficiency of water-based drilling mud. Journal of Petroleum Science and Engineering. 2019. Vol. 172, p. 1226-1234. DOI: 10.1016/j.petrol.2018.09.097
- Gorji M., Kazemi A., Ganji D.D. Uncertainties due to fuelheating value and burner efficiency on performance functionsof turbofan engines using Monte Carlo simulation. International Journal of Engineering. Transactions A: Basics. 2014. Vol. 27. N 7, p. 1139-1148. DOI: 10.5829/idosi.ije.2014.27.07a.16
- Gulraiz S., Gray K.E. Study on the combined effect of thixotropy, particle shape, and particle size on cuttings transport in horizontal annuli. Powder Technology. 2021. Vol. 392, p. 703-716. DOI: 10.1016/j.powtec.2021.07.041
- Heshamudin N.S., Katende A., Rashid H.A., Ismail I. Experimental investigation of the effect of drill pipe rotation on improving hole cleaning using water-based mud enriched with polypropylene beads in vertical and horizontal wellbores. Journal of Petroleum Science and Engineering. 2019. Vol. 179, p. 1173-1185. DOI: 10.1016/j.petrol.2019.04.086
- Huque M.M., Rahman M.A., Zendehboudi S., Butt S. Experimental and numerical study of cuttings transport in inclined drilling operations. Journal of Petroleum Science and Engineering. 2022. Vol. 208. Part B. N 109394. DOI: 10.1016/j.petrol.2021.109394
- Issoufou M.K., Song X., Zhu Z., Xu Z. Predicting cuttings settling velocity in drilling muds and in rising-bubbles-containing muds. Journal of Petroleum Science and Engineering. 2021. Vol. 204. DOI: 10.1016/j.petrol.2021.108766
- Jafarifar I., Karimi Dehkordi B., Abbasi H., Schaffie M. Evaluation and optimization of water-salt based drilling fluids for slim-hole wells in one of Iranian central oil fields. Upstream Oil and Gas Technology. 2020. Vol. 5. DOI: 10.1016/j.upstre.2020.100010
- Leusheva E, Morenov V., Tabatabaee Moradi S.Sh. Effect of Carbonate Additives on Dynamic Filtration Index of Drilling Mud. International Journal of Engineering. Transactions B: Applications. 2020. Vol. 33. Iss. 5, p. 934-939. DOI: 10.5829/ije.2020.33.05b.26
- Mahmoud H., Alhajabdalla M., Nasser M.S., Hussein I.A.Settling behavior of fine cuttings in fiber-containing polyanionic fluids for drilling and hole cleaning application. Journal of Petroleum Science and Engineering. 2021. Vol. 199. N 108337. DOI: 10.1016/j.petrol.2020.108337
- Mahmoud H., Hamza A., Nasser M.S., Hussein I.A. Hole cleaning and drilling fluid sweeps in horizontal and deviated wells: Comprehensive review. Journal of Petroleum Science and Engineering. 2020. Vol. 186. N 106748. DOI: 10.1016/j.petrol.2019.106748
- Mazen A.Z., Mujtaba I.M., Hassanpour A., Rahmanian N.Mathematical modelling of performance and wear prediction of PDC drill bits: Impact of bit profile, bit hydraulic, and rock strength. Journal of Petroleum Science and Engineering. 2020. Vol. 188. N 106849. DOI: 10.1016/j.petrol.2019.106849
- Mohamed A., Salehi S., Ahmed R. Significance and complications of drilling fluid rheology in geothermal drilling: A review. Geothermics. 2021. Vol. 93. N 102066. DOI: 10.1016/j.geothermics.2021.102066
- Mohammadsalehi M., Malekzadeh N. Application of New Hole Cleaning Optimization Method within All Ranges of Hole Inclinations. International Petroleum Technology Conference, 15-17 November 2011, Bangkok, Thailand. 2012. DOI: 10.2523/IPTC-14154-MS
- Muherei M.A., Basaleh S.S. True Power Law Drilling Fluid Model: Effect of Its Rheological Parameters on Static Particle Settling Velocity. International Research Journal of Engineering and Technology (IRJET). 2016. Vol. 3. Iss.1, p. 77-88.
- Robinson L., Morgan M. Effect of Hole Cleaning on Drilling Rate and Performance. AADE 2004 Drilling Fluids Conference, 6-7 April 2004, Houston, Texas, 2004, p. 1-7.
- Salubi V., Mahon R., Oluyemi G., Oyeneyin B. Effect of two-phase gas-liquid flow patterns on cuttings transport efficiency. Journal of Petroleum Science and Engineering. 2022. Vol. 208. Part A. N 109281. DOI: 10.1016/j.petrol.2021.109281
- Sayindla S., Lund B., Ytrehus J.D., Saasen A. Hole-cleaning performance comparison of oil-based and water-based drilling fluids. Journal of Petroleum Science and Engineering. 2017. Vol. 159, p. 49-57. DOI: 10.1016/j.petrol.2017.08.069
- Khaled M.Sh., Khan M.S., Ferroudji H. et al.Dimensionless data-driven model for optimizing hole cleaning efficiency in daily drilling operations. Journal of Natural Gas Science and Engineering. 2021. Vol. 96. № 104315. DOI: 10.1016/j.jngse.2021.104315
- Sun X., Zhang K., Chen Y., Li W.Study on the settling velocity of drilling cuttings in the power law. Powder Technology. 2020. Vol. 362, p. 278-287. DOI: 10.1016/j.powtec.2019.11.025
- Tabatabaee Moradi S.Sh., Nikolaev N.I. Uncertainty assessment of wellbore stability analysis in horizontal sections. SN Applied Sciences. 2020. Vol. 2. N 437. DOI: 10.1007/s42452-020-2237-y
- Yan T., Qu J., Sun X., Chen Y. Numerical investigation on horizontal wellbore hole cleaning with a four-lobed drill pipe using CFD-DEM method. Powder Technology. 2020. Vol. 375, p. 249-261. DOI: 10.1016/j.powtec.2020.07.103005
- Yan T., Qu J., Sun X., Li W. A novel predictive model of drag coefficient and settling velocity of drill cuttings in non-Newtonian drilling fluids. Petroleum Science. 2021. Vol. 18. Iss. 6, p. 1729-1738. DOI: 10.1016/j.petsci.2021.09.003
- Yeo L., Feng Y., Seibi A., Temani A. Optimization of hole cleaning in horizontal and inclined wellbores: A study with computational fluid dynamics. Journal of Petroleum Science and Engineering. 2021. Vol. 205. N 108993. DOI: 10.1016/j.petrol.2021.108993