Мониторинг потерь сжатого воздуха в разветвленных воздухопроводных сетях горных предприятий
Аннотация
Сжатый воздух широко используется во многих отраслях промышленности как один из видов безопасного технологичного энергоносителя. Затраты энергии на производство и распределение сжатого воздуха достигают 10 % от общих энергозатрат в экономически развитых странах. Анализ систем производства и распределения сжатого воздуха на предприятиях промышленного сектора показывает, что эффективность систем находится на сравнительно низком уровне. Это обусловлено тем, что данным системам уделяется недостаточно внимания ввиду того, что энергетический мониторинг систем сжатого воздуха имеет определенные трудности – наличие сложных и разветвленных воздухопроводных сетей, обладающих уникальными характеристиками; низкой чувствительностью оборудования, потребляющего сжатый воздух; сложностью проведения аудита пневматического оборудования, которое находится в постоянной работе. В статье проведен анализ вариантов снижения затрат на производство и распределение сжатого воздуха. Одним из перспективных направлений снижения затрат на распределение сжатого воздуха является своевременное обнаружение и ликвидация утечек, возникающих во внешней воздухопроводной сети предприятия. Поставленная задача решается аппаратно-программным мониторингом давления сжатого воздуха в ключевых точках сети. Предлагаемая методика позволяет в режиме реального времени обнаруживать возникающие утечки воздуха в воздухопроводной сети и подавать команды обслуживающему персоналу на их своевременную локализацию. Данная методика была апробирована в промышленных условиях предприятий компании «АЛРОСА» на воздухопроводной сети рудника «Мир» Мирнинского горно-обогатительного комбината и показала удовлетворительную сходимость расчетных значений утечек с фактическими. Практическая значимость полученных результатов состоит в том, что разработанный метод мониторинга утечек воздуха в воздухопроводной сети отличается простотой, несложной программной реализацией и позволяет своевременно локализовать утечки, сокращая тем самым непроизводительные расходы энергоносителя на предприятиях.
Введение
Благодаря своим универсальным свойствам сжатый воздух является одним из основных энергоносителей, используемых во многих процессах разных отраслей промышленности [1, 2]. В промышленном секторе системы производства и распределения сжатого воздуха являются одними из основных потребителей энергии, на которую приходится в среднем 10 % общих затрат энергии, потребляемой в Европейском Союзе и Китае [3]. Однако, несмотря на повсеместное распространение, эффективность использования сжатого воздуха составляет около 19 %, а примерно 75 % составляют затраты на электроэнергию привода компрессорных установок [4]. Таким образом, только 10-30 % электроэнергии, потребляемой компрессорными установками, используется конечным потребителем. Эффективность использования энергии при производстве и распределении сжатого воздуха для горной промышленности России представлена на диаграмме (рис.1). В целом доля затраченной энергии, потребленной компрессорной станцией, которая преобразуется в полезную работу, составляет около 3 %. Это обусловлено тем, что горнорудные предприятия имеют систему разветвленных горных выработок и, соответственно, обладают разветвленными воздухопроводными сетями, в которых сосредоточено порядка 37 % потерь энергии сжатого воздуха [5, 6].
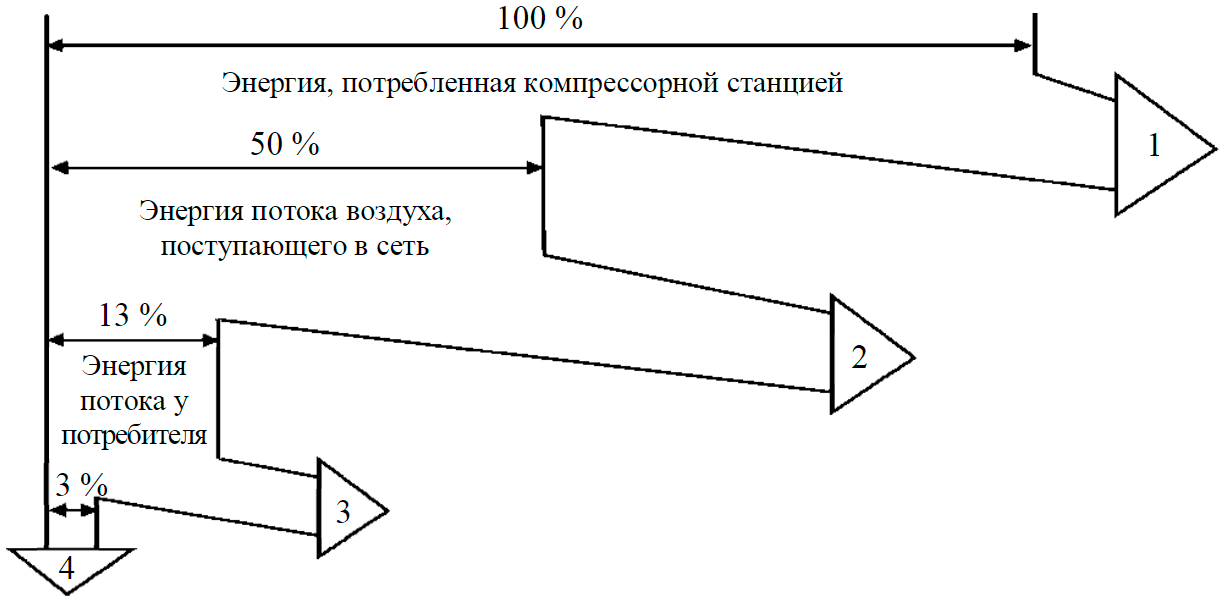
Рис.1. Энергетическая диаграмма производства, распределения и потребления сжатого воздуха на горных предприятиях России 1 – потери энергии на компрессорной станции; 2 – потери энергии в воздухопроводной сети; 3 – потери энергии в пневмопотребителях; 4 – полезная работа
Такой уровень потерь энергии в системах сжатого воздуха в настоящее время следует считать недопустимым вследствие значительного влияния на производство конкурентноспособного продукта. Повышение показателей энергетической эффективности технологического процесса производства и распределения сжатого воздуха основано на модернизации, технологическом развитии и переходе к рациональному использованию энергетических ресурсов [7-10].
Возможности снижения затрат энергии на производство сжатого воздуха связаны со снижением энергозатрат на привод компрессоров, на транспортировку воздуха по трубопроводным системам, на управление пневматическими системами [11]. В исследованиях [12, 13] отмечено, что внедрение необходимых мероприятий по энергосбережению в системах производства и транспортирования сжатого воздуха имеет потенциал снижения энергопотребления от 56 до 66 %.
Решение поставленной задачи осуществляется комплексными методами. Основные направления повышения эффективности систем сжатого воздуха направлены на использование электропривода с высоким КПД [14], внедрение частотно-регулируемых приводов [15, 16], модернизацию систем автоматического управления [17, 18], использование современных конструкций осушителей и воздушных фильтров [3, 19]. Следует учитывать внешнюю часть систем сжатого воздуха, к которой относятся распределительная воздухопроводная сеть с запорной и контрольной аппаратурой, и само используемое технологическое оборудование, оказывающие значительное влияние на эффективность использования энергии. Следует отметить, что некоторые методы повышения эффективности компрессорных станций могут приводить к ухудшению других технических показателей предприятия, например, внедрение частотно-регулируемого привода негативно влияет на уровень качества электроэнергии в части несиносуидальности напряжения и тока [20].
Энергоаудит предприятий позволяет выявить технические проблемы систем сжатого воздуха и его распределения [21-23]. В исследованиях отмечается, что несмотря на дороговизну данного энергоносителя, на предприятиях не учитывается эффективность системы до того момента, когда потери давления в системе достигнут критического уровня и начнут влиять на нормальное течение технологического процесса и нормальную работу оборудования [14]. Указанная особенность систем приводит ко временной задержке осуществления необходимых управляющих воздействий, направленных на повышение энергоэффективности производства [24].
В последнее время продвигаемая концепция развития систем мониторинга и управления интеллектуальных технических комплексов [7, 25] требует разработки автоматизированных систем на предприятиях горнодобывающей промышленности, которые бы учитывали необходимые факторы жизненного цикла рассматриваемых технологических схем.
Методология
Перспективное направление повышения энергоэффективности на промышленных предприятиях – внедрение качественного энергетического менеджмента, который будет играть значительную роль для поддержания на необходимом уровне минимальных затрат электроэнергии. Это достигается в процессе энергоаудита и позволяет сохранять сниженное энергопотребление в производстве с экономией до 20 % [26]. Несмотря на высокую эффективность, реализация энергоменеджмента сдерживается поддержкой предприятиями других приоритетных направлений: повышения технических навыков управляющего персонала и низкой мотивации сотрудников, принимающих необходимые решения [27, 28].
Существующие технологии позволяют осуществлять мониторинг параметров различных систем промышленных объектов и визуализировать их на мнемонической схеме, отображаемой на экране оператора. Все больше предприятий добывающей промышленности начинают внедрять современные телекоммуникационные решения и технологии, что позволяет в значительной степени снизить вероятность производственных ошибок и оптимизировать течение производственных процессов. Вместе с тем, не существует доступных подходов для мониторинга в реальном времени энергетических характеристик систем производства и распределения сжатого воздуха. Во многих случаях единственным индикатором технических или эксплуатационных проблем, характеризующих системы сжатого воздуха, является повышенное потребление электроэнергии компрессорной станцией. На увеличение энергопотребления влияют не только повышение производительности компрессорных установок и технические проблемы, но и неконтролируемые утечки воздуха [2, 29]. Таким образом, необходимо использование системы, включающей в себя мониторинг основных технических параметров в реальном времени, процедуры выявления непроизводительных потерь сжатого воздуха и системы быстрого оповещения для управления устранением причины непроизводительного расхода воздуха.
Рассмотрим техническую сторону повышения энергоэффективности систем производства и распределения сжатого воздуха. Принято разделять системы сжатого воздуха на две части: производство и распределение сжатого воздуха. В первую часть входят сами компрессорные агрегаты, воздушные фильтры, воздухосборники, влагоотделители и т.п. Во вторую часть входят регулирующие клапаны, распределительные воздухопроводы с фасонными частями и технологическое оборудование, работающее на сжатом воздухе. Вторая часть в целом представляет собой внешнюю сеть компрессорной установки.
Энергетические потери во внешней сети происходят, в основном, из-за утечек воздуха, на которые приходится до 20-50 % потерь [3, 11]. Эти потери обусловлены негерметичностью разъемных соединений, неисправностью муфт, фитингов, разрушением воздухопроводов, разрывом шлангов и т.п. [11].
Проведенный обзор опыта эксплуатации систем сжатого воздуха и доступных возможностей снижения затрат энергии в данных системах позволяет сделать вывод, что большинство технологических процессов имеют возможность для значительного снижения эксплуатационных расходов за счет снижения объемных утечек воздуха во внешних воздухопроводных сетях. Ремонт данных систем требует минимальных капиталовложений и позволяет быстро окупить затраты.
Основным показателем при оценке потенциальной экономии энергии и затрат является количественная оценка расхода воздуха, происходящего из-за утечек. Существующие методы количественной оценки объема утечек оценивают либо общий расход системы, либо расход воздуха от отдельных утечек [30]. Для оценки общих потерь в системе снабжения сжатым воздухом используются четыре основных метода, которые включают испытание на снижение давления, измерение мощности компрессора, использование портативного ультразвукового расходомера и установку встроенного расходомера. Все эти методы требуют прерывания производственных процессов, так как технология определения утечек предполагает измерение количеств воздуха, обусловленных только утечками в системе. Измерение отдельных утечек может быть выполнено во время производства. Каждый из перечисленных методов имеет недостатки, которые создают значительную погрешность при измерении расхода воздуха [31].
Другим вариантом измерения утечек является применение ультразвуковых накладных расходомеров, которые используют ультразвуковые волны для оценки скорости воздуха, протекающего внутри трубопровода сжатого воздуха. Они непосредственно измеряют скорость в трубе и им необходимо известное значение давления в системе. Этот метод требует множество настроек, калибровку, а также определение значения некоторых трудно определимых параметров [32]. Кроме того, предъявляются жесткие требования к расположению расходомера и правильному его креплению к трубе. Таким образом, наличие большого числа настраиваемых параметров предопределяет значительные погрешности при измерении расхода утечек.
Еще один метод косвенного определения утечек основан на измерении электрических параметров (величины напряжения и силы тока), подводимых к зажимам электродвигателя компрессора, что позволяет вычислить мощность, потребляемую для сжатия воздуха [3]. Разность показаний измеренной и расчетной мощности компрессора дает возможность рассчитать расход воздуха, обусловленный утечками в системе. Этот метод широко применяется в энергоаудите предприятий, но требует сертификации, калибровки электрооборудования и значительных затрат времени на поиск и изоляцию требуемых электрических линий. Кроме того, метод предназначен для оценки только общего расхода воздуха в системе и не позволяет дифференцировать потери на отдельных участках трубопровода.
При выявлении отдельных утечек наиболее распространенным методом является ультразвуковое обнаружение утечек [33]. Данный метод позволяет определять утечки, которые происходят при точечной разгерметизации трубопроводов, имеет высокую погрешность и сложность определения суммарного расхода воздуха, обусловленного наличием множества точек.
Одним из новых методов следует считать термодинамический с использованием нагревательных элементов и термопар [31]. Измерение утечек осуществляется при остановленном технологическом процессе, так что в трубопроводе сжатого воздуха только циркулирует поток, обусловленный утечками. Компрессор продолжает работать для поддержания давления в системе. Наружная часть трубы нагревается с помощью тепловых нагревателей, и результирующий температурный профиль измеряется с помощью термопар или других аналогичных измерителей температуры. При подаче тепла на трубу результирующий температурный профиль будет меняться в зависимости от потока воздуха в трубе. Изменение расхода воздуха приводит к изменению коэффициента теплоотдачи внутри трубы, что влияет на изменение температуры по отношению к исходному значению. Метод обладает достаточной точностью, но требует специального оборудования и его соответствующей калибровки. Сложность и дороговизна данного метода ограничивает его широкое применение.
Обсуждение
Разветвленность воздухопроводной сети и наличие большого числа потребителей сжатого воздуха требует строгого учета потерь, возникающих при транспортировке энергоносителя. Существующие технические средства позволяют контролировать основные параметры энергоносителя на всех этапах его перемещения. Однако их широкое распространение сдерживается дороговизной и необходимостью затрат на дополнительное техническое обслуживание. В некоторых случаях требуется специализированное программное обеспечение, применяемое в рамках необходимых функциональных задач [34, 35]. На наш взгляд, в данных условиях более целесообразными становятся методы, основанные на мониторинге основных параметров энергоносителя с дифференцированным учетом факторов, позволяющих в реальном режиме времени отслеживать утечки. Своевременная локализация выявленных утечек позволяет значительно сократить вредные потери и непроизводительные затраты в системах сжатого воздуха.
Проектирование компрессорных станций и расчет воздухопроводных сетей для стационарных проектных режимов работы потребителей сжатого воздуха не представляет больших трудностей и достаточно подробно описан [36, 37]. Основная задача компрессорной установки – подача воздуха к конечному потребителю с соответствующими технологическими параметрами, к которым относятся давление, расход и качество воздуха. Важными параметрами внешней сети компрессорной установки являются длина, диаметры трубопроводов, шероховатость, наличие местных сопротивлений. Соответствующий расчет и последующий выбор этих параметров позволяет минимизировать потери и использовать компрессорные машины с наименьшим потреблением энергии.
При проектировании воздухопроводных сетей с учетом нормативных документов по отношению к воздухопроводам и качеству подаваемого воздуха, учет утечек принимается декларативно от 0,3 до 0,5 м3/мин на 1 км трубопровода. Величины данных проектных утечек принимаются в зависимости от опыта эксплуатации компрессорных станций по предприятиям определенных отраслей. Такой подход обуславливает усредненный показатель утечек без учета множества внешних факторов, что является достаточно нецелесообразным. Некоторые факторы могут создавать уровень потерь от утечек до 40 % от номинального расхода потребителя [38, 39].
Для обеспечения текущего мониторинга уровня утечек и их локализации в магистральных трубопроводах сжатого воздуха с целью последующего менеджмента для принятия решений по снижению непроизводительных расходов предлагается метод косвенного определения утечек в воздухопроводной сети. Данный метод заключается в том, что используются значения расхода воздуха потребителей, подключенных к определенным участкам в соответствии со схемой воздухопроводной сети. По мониторингу падения давления на этих участках определяется расход воздуха, обусловленный утечками. Метод применим для длинных и разветвленных сетей сжатого воздуха, что характерно для предприятий горной и химической отраслей. В таких системах подачи сжатого воздуха преобладающими являются линейные потери давления по сравнению с местными потерями. Таким образом, используя уравнение Дарси – Вейсбаха [37], записанное для i-го участка воздухопроводной сети, определяется расчетное падения давления Δpi на соответствующем участке, которое обусловлено расходом сжатого воздуха потребителями данного участка и утечками,
где di – диаметр трубы; λ – коэффициент гидравлического трения; li – приведенная длина i-го участка воздухопровода; di – диаметр i-го участка воздухопровода; Qсрi – среднее значение объемного расхода воздуха на i-м участке; ρсрi – среднее значение плотности транспортируемого сжатого воздуха.
Объемный расход сжатого воздуха на участке воздухопровода складывается из расхода потребителя или последующего участка и возникающих утечек, которые обусловлены не герметичностью соединений и нарушением сплошности трубопровода. Среднее значение объемного расхода может быть определено из выражения
где Qпi – полезный объемный расход на i-м участке, обусловленный расходом конечных потребителей; Qутi – объемные потери сжатого воздуха на i-м участке.
Сравнение выражений (1) и (2) позволяет получить зависимость падения давления на рассматриваемом участке от возникающих объемных утечек на этом же участке:
Преобразование выражения (3) позволяет вычислить объемные утечки сжатого воздуха на i-м участке:
В полученное выражение (4) входит ρсрi – среднее значение плотности транспортируемого сжатого воздуха. Данный параметр зависит от термодинамического состояния транспортируемой среды. При движении сжатого воздуха из начальной точки, в которой он имеет параметры давления p1, температуры T1 и плотности ρ1, происходит изменение его термодинамических параметров до значений p2, T2 и ρ2. Примем во внимание, что движение сжатого воздуха по стальным трубопроводам сопровождается как его охлаждением вследствие теплопередачи через стенки трубопровода, так и определенным повышением температуры из-за трения воздуха о стенки трубопровода, имеющим значительную шероховатость. В первом приближении примем, что снижение температуры воздуха на рассматриваемом участке трубопровода происходит по адиабатическому закону. Тогда среднее значение плотности транспортируемого сжатого воздуха вычисляется из выражения
где pнi – абсолютное давление сжатого воздуха в начале i-го участка трубопровода; R – газовая постоянная воздуха; Tнi – абсолютная термодинамическая температура воздуха в начале i-го участка воздухопровода.
Мониторинг параметров сжатого воздуха осуществляется в ключевых точках воздухопроводной сети: на выходе компрессорной станции, в местах разветвлений воздухопроводной сети, около приемников сжатого воздуха. Основным преобладающим параметром сжатого воздуха для заданных условий является избыточное давление в точках трубопровода, которое регистрируется цифровыми манометрами и любое их отклонение отслеживается энергетической службой предприятия. В некоторых ключевых точках воздухопроводной сети дополнительно устанавливаются цифровые термометры, которые регистрируют температуру подаваемого сжатого воздуха. В тех точках сети, где отсутствуют термометры, температура вычисляется методом линейной интерполяции, из данных ближайших точек воздухопроводной сети. Согласно проектной схеме манометры регистрируют давление воздуха в начале p1 и в конце p2 участков наблюдаемого трубопровода, что позволяет учитывать разность их показаний, которое равно общему падению давления на данном участке трубопровода:
Так как объемная производительность промышленных компрессоров Vк и потребителей сжатого воздуха Vп измеряется в [м3/мин], то перейдя от размерности [м3/с] к размерности [м3/мин] и принимая во внимание неучтенные в принятой модели факторы, получим окончательное выражение для мониторинга утечек воздуха на i-м участке трубопровода:
где Vутi – расчетный объемный расход утечек на i-м участке, м3/мин; kc – коэффициент согласования, учитывающий дополнительное падение давления, связанное с конфигурацией участка воздухопроводной сети (наличие вентилей, разветвлений, поворотов и т.п.); Vпi – расчетный объемный расход потребителей на i-м участке, м3/мин, определяемый по паспортным данным оборудования или результатам последнего аудита хозяйства сжатого воздуха предприятия.
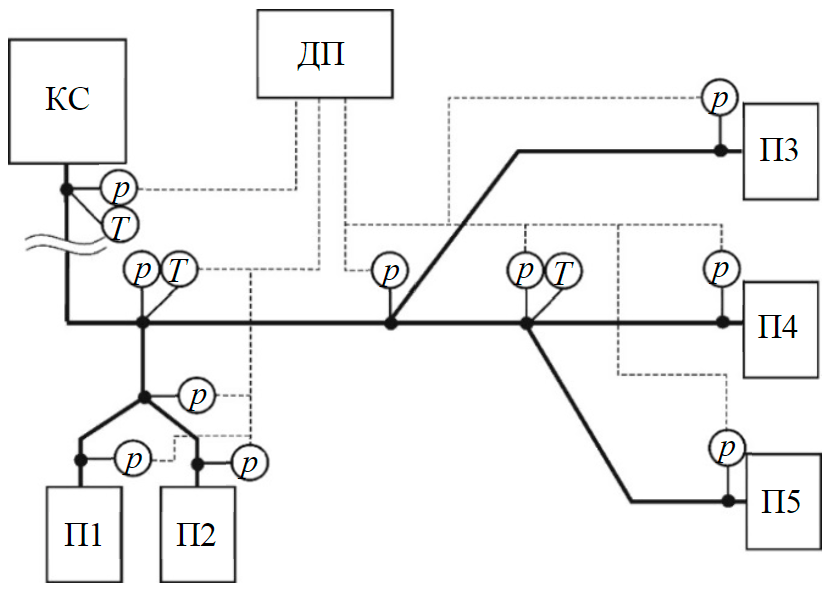
Рис.2. Примерная схема мониторинга воздухопроводной сети подземного рудника «Мир» Мирнинского горно-обогатительного комбината
КС – компрессорная станция; П1 – П5 – пневмоприемники; p – датчики давления; T – датчики температуры; ДП – диспетчерский пульт
Для успешной реализации данной методики необходимо установить значение коэффициента согласования kc. Так как на его величину влияют достаточно много случайных факторов, то установление зависимости значения коэффициента согласования от конфигурации и параметров трубопровода может быть построено на базе эксперимента с помощью эмпирических формул. Экспериментальные исследования были проведены на воздухопроводной сети рудника «Мир» Мирнинского горно-обогатительного комбината компании «АЛРОСА». Существующая система диспетчеризации рудника позволяет в режиме реального времени следить за показаниями давления в контрольных точках трубопровода сжатого воздуха и режимом работы пневмоустановок. Оператор диспетчерского пульта видит на контрольном мониторе план горных работ с расположением оборудования и показаниями приборов в контрольных точках. Функциональная схема мониторинга воздухопроводной сети рудника показана на рис.2. Датчики давления располагаются в узловых точках, связывающих отдельные участки воздухопроводной сети, или в местах расположения пневмоприемников.
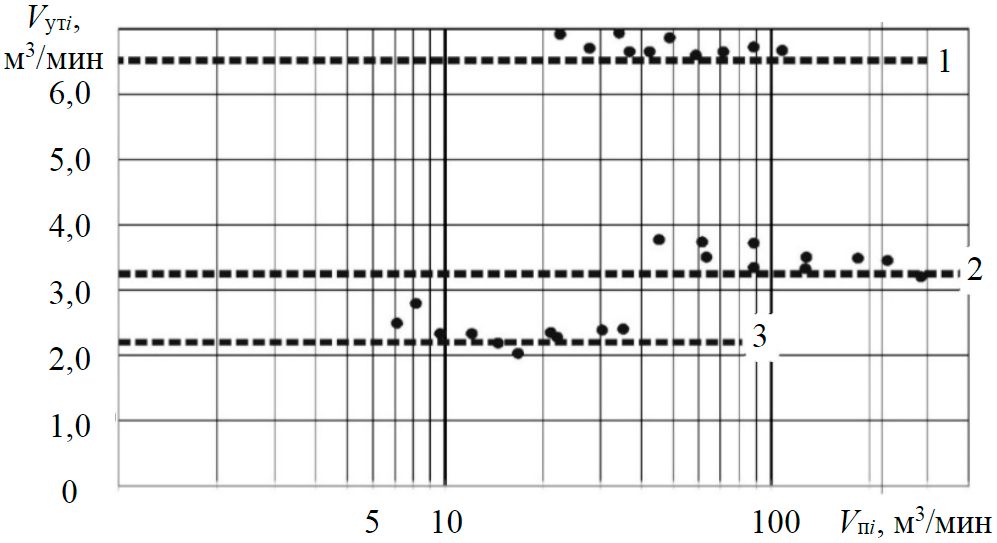
Рис.3. Результаты экспериментальных исследований определения утечек на участках воздухопроводав квершлаге (1), в стволе (2), в штреке (3)
Потребность подземных и наземных комплексов рудника «Мир» в сжатом воздухе обеспечивается от поверхностной компрессорной станции. Компрессорная станция оборудована четырьмя компрессорами ZR-750/7.5-50 (подача 124,4 м3/мин, давление (75 Па) 7,5 кг/см2, мощность электродвигателя 750 кВт). Суммарная проектная производительность рабочих агрегатов составляет 373,5 м3/мин. Работа компрессорной станции предусмотрена в автоматическом режиме, с выводом необходимых параметров диспетчеру рудника.
От компрессорной станции до клетевого ствола сжатый воздух подается по трубопроводу с номинальными диаметрами DN400 и DN350, далее по клетевому стволу по трубопроводу DN300, по квершлагам рабочих горизонтов по трубопроводам DN200, по остальным выработкам по трубопроводам с диаметрами DN150. Трубопроводы оборудованы влагоотделителями и коммутационной арматурой.
Большинство пневмопотребителей не имеют постоянного местоположения в руднике. Согласно плану горных работ и производственной необходимости пневмопотребители подключаются к трубопроводу сжатого воздуха в ответвлениях, предусмотренных проектом.
Для вычисления потерь сжатого воздуха и коэффициента согласования kc экспериментальные участки были разделены по номинальным диаметрам и расположению в воздухопроводной сети предприятия. Результаты измерений значения давления на исследуемых участках воздухопровода поступали на пульт оператора. Измерения проводились при разном числе подключенных потребителей сжатого воздуха, следовательно, изменялись расход и величины падения давлений воздуха в точках измерения. Расчет условных утечек производился согласно формуле (4), при этом значение коэффициента согласования kc принималось равным 1. Результаты измерений утечек экспериментальными методами на тех же участках обозначены на графике (рис.3) пунктирными линиями.
В результате проведенных экспериментов было установлено, что значение коэффициента согласования находится в диапазоне от 0,93 до 0,97 (см. таблицу). При малых расходах воздуха погрешность определения утечек данным методом снижается, что связано с определенной чувствительностью датчиков-преобразователей давления и их погрешностью, которая составляет 1-2 %. При расходах, соответствующих основным рабочим режимам на предприятии, данная методика дает удовлетворительный результат с погрешностью измерений 6-7 %.
Значение коэффициента kc
Участок |
Номинальный диаметр, мм |
Среднее значение kc |
Погрешность расчетных данных, % |
Ствол |
350 |
0,93 |
5,3 |
Квершлаг |
200 |
0,97 |
2,5 |
Производственные участки, штреки |
150 |
0,95 |
5,8 |
Основное назначение данной методики заключается не в точном определении утечек, а в своевременном их обнаружении и немедленной локализации. Схема работы заключается в следующем. Показания приборов посредством линий связи передаются на пульт диспетчера, где происходит их визуализация. Программное обеспечение автоматизированной системы контроля воздухопроводной сети, построенное с учетом предлагаемой методики, позволяет выдавать сигналы при отклонениях режима работы системы от расчетных параметров. Менеджмент предприятия оценивает эти отклонения и принимает меры для локализации утечек и, в конечном итоге, к снижению энергопотребления компрессорной станцией предприятия. Данная система повышает энергетическую безопасность транспорта сжатого воздуха, исключает влияние человеческого фактора и является одним из шагов развития высокоэффективного цифрового предприятия [36, 40].
Заключение
Результаты проведенных исследований позволяют сделать следующие выводы.
Одним из методов технической реализации эффективного менеджмента сетей сжатого воздуха является программно-техническая реализация мониторинга утечек на участках воздухопроводной сети, осуществляемая в режиме реального времени.
Математическая модель, учитывающая особенности воздухопроводных сетей и наличие показателей значения давления в контрольных точках сети, позволяет расчетным методом определять утечки в сети. Результаты экспериментальных исследований на воздухопроводной сети рудника «Мир» Мирнинского горно-обогатительного комбината показали отклонение расчетных парметров не более 7 % от фактических значений утечек. Внедрение указанной системы с четким менеджментом энергослужбы уменьшает расход электрической энергии приводов компрессорных агрегатов рудника «Мир» на 4720 кВт•ч в год.
Программная реализация указанного метода позволяет в режиме реального времени осуществлять мониторинг состояния воздухопроводной сети и определять участки, имеющие повышенные потери энергоносителя. Метод определения утечек в сетях сжатого воздуха отличается простотой, несложной программной интеграцией в существующую систему диспетчеризации, и может найти применение для мониторинга состояния внешних сетей компрессорных установок на промышленных предприятиях с разветвленными воздухопроводными сетями.
Литература
- Cabello Eras J.J., Sagastume Gutiérrez A., Sousa Santos V., Cabello Ulloa M.J. Energy management of compressed air systems. Assessing the production and use of compressed air in industry // Energy. 2020. Vol. 213. № 118662. DOI: 10.1016/j.energy.2020.118662
- Nehler T. Linking energy efficiency measures in industrial compressed air systems with non-energy benefits – a review // Renew and Sustain Energy Review. 2018. Vol. 89. P. 72-87. DOI: 10.1016/j.rser.2018.02.018
- Saidur R., Rahim N.A., Hasanuzzaman M. A review on compressed-air energy use and energy savings // Renew Sustain Energy Review. 2010. Vol. 14. Iss. 4. P. 1135-1153. DOI: 10.1016/j.rser.2009.11.013
- Mousavi S., Kara S., Kornfeld B. Energy efficiency of compressed air systems // Procedia CIRP. 2014. Vol.15. P.313-318. DOI: 10.1016/j.procir.2014.06.026
- 5. Миняев Ю.Н., Угольников А.В., Молодцов В.В. Исследование объемных потерь в пневматических сетях рудничных компрессорных установок // Горный информационно-аналитический бюллетень. 2006. № 2. С. 254-257.
- Миняев Ю.Н. Энергетические потери в пневмосистемах рудничных компрессорных установок // Известия Уральского государственного горного университета. 2003. Вып. 16. С. 44-46.
- Жуковский Ю.Л., Лаврик А.Ю., Семенюк А.В., Васильков О.С. Потенциал управления электропотреблением в условиях изолированной энергосистемы удаленного населенного пункта // Устойчивое развитие горных территорий. 2020. Т. 12. № 4 (46). С. 583-591. DOI: 10.21177/1998-4502-2020-12-4-583-591
- Goldberg A., Reinaud J., Taylor R.P. Promotion systems and incentives for adoption of energy management systems in industry // Some international lessons learned relevant for China. 2011. 36 p.
- Harris J., Anderson J., Shafron W. Investment in energy efficiency: a survey of Australian firms // Energy Policy. 2000. Vol. 28. Iss. 12. P. 897-876. DOI: 10.1016/S0301-4215(00)00075-6
- La T. Don't Let Compressed Air Blow Away Your Profits // Energy Engineering. 2013. Vol. 111. Iss. 1. P. 7-15. DOI: 10.1080/01998595.2013.10769725
- Abdelaziz E.A., Saidur R., Mekhilef S. A review on energy saving strategies in industrial sector // Renew Sustain Energy Reviews. 2011. Vol. 15. Iss.1. P. 150-168. DOI: 10.1016/j.rser.2010.09.003
- Marshall R.C. Optimization of single-unit compressed air systems // Energy Engineering. 2012. Vol. 109. Iss. 1. P. 10-35. DOI: 10.1080/01998595.2012.1043657
- McKane A., Hasanbeigi A. Motor systems energy efficiency supply curves: A methodology for assessing the energy efficiency potential of industrial motor systems // Energy Policy. 2011. Vol. 39. Iss. 10. P. 6595-6607. DOI: 10.1016/j.enpol.2011.08.004
- Kaya D., Phelan P., Chau D., Sarac H.I. Energy conservation in compressed-air systems // International journal of Energy Research. 2002. Vol. 26. Iss. 9. P. 837-849. DOI: 10.1002/er.823
- Шклярский Я.Э., Брагин А.А. Снижение потерь энергии в электрических сетях предприятий // Известия высших учебных заведений. Горный журнал. 2013. № 1. С. 99-103.
- Abd Elsadek E.M., Ashour H., Refaat R.A., Mostafa M. Efficiency Improvement and Saving Energy within Electro-Pneumatic System Using VFD: (case study: Production line) // Proceedings of 2019 International Conference on Innovative Trends in Computer Engineering (ITCE 2019), 2-4 February 2019, Aswan, Egypt. IEEE, 2019. P. 248-253. DOI: 10.1109/ITCE.2019.8646536
- Neale J.R., Kamp P.J.J. Compressed air system best practice programmes: What needs to change to secure long-term energy savings for New Zealand? // Energy Policy. 2009. Vol. 37. Iss.9. P.3400-3408. DOI: 10.1016/j.enpol.2009.04.047
- Gordon F., Peters J., Harris J., Scales B. Why is the treasure still buried? Breaching the barriers to compressed air system efficiency // Proceedings ACEEE Summer Study on Energy Efficiency in Industry. 1999. P. 709-718.
- Terrell R.E. Improving compressed air system efficiency – know what you really need // Energy Engineering: Journal of the Association of Energy Engineering. 1999. Vol. 96. Iss.1. P.7-15. DOI: 10.1080/01998595.1999.10530444
- Пирог С., Шклярский Я.Э., Скамьин А.Н. Идентификация местоположения нелинейной электрической нагрузки // Записки Горного института. 2019. Т. 237. С. 317-321. DOI: 10.31897/PMI.2019.3.317
- Hasmandova M. Compressed air systems: Auditing and replacing air compressors // Filtration & Separation. 2008. Vol. 45. Iss. 9. P. 41-42. DOI: 10.1016/s0015-1882(08)70373-2
- Thabet M., Sanders D., Haddad M. et al. Management of Compressed Air to Reduce Energy Consumption Using Intelligent Systems // Advances in Intelligent Systems and Computing, 3-4 September 2020, London, United Kingdom. Springer, 2020. Vol. 1252. P. 206-217. DOI: 10.1007/978-3-030-55190-2_16
- Trianni A., Accordini D., Cagno E. Identification and categorization of factors affecting the adoption of energy efficiency measures within compressed air systems // Energies.2020. Vol. 13. Iss. 19. № 5116. DOI: 10.3390/en13195116
- Dindorf R. Estimating potential energy savings in compressed air systems // Procedia Engineering. 2012. Vol.39. P. 204-211. DOI: 10.1016/j.proeng.2012.07.026
- Паляницин П.С., Петров П.А., Бажин В.Ю. К вопросу ресурсо- и энергосбережения в производстве корунда // Вестник Иркутского государственного технического университета. Т. 24. № 6. С. 1347-1356. DOI: 10.21285/1814-3520-2020-6-1347-1356
- May G., Stahl B., Taisch M., Kiritsis D. Energy management in manufacturing: From literature review to a conceptual framework // Journal of Cleaner Production. 2017. Vol. 167. P. 1464-1489. DOI: 10.1016/j.jclepro.2016.10.191
- Brunke J.C., Johansson M., Thollander P. Empirical investigation of barriers and drivers to the adoption of energy conservation measures, energy management practices and energy services in the Swedish iron and steel industry // Journal of cleaner production. 2014. Vol. 84. P. 509-525. DOI: 10.1016/j.jclepro.2014.04.078
- Fernando Y., Wei Lin Hor. Impacts of energy management practices on energy efficiency and carbon emissions reduction: A survey of Malaysian manufacturing firms // Resources, Conservation and Recycling. 2017. Vol. 126. P. 62-73. DOI: 10.1016/j.resconrec.2017.07.023
- Nehler T., Parra R., Thollande P. Implementation of energy efficiency measures in compressed air systems: barriers, drivers and non-energy benefits // Energy Efficiency. 2018. Vol. 11. P.1281-1302. DOI: 10.1007/s12053-018-9647-3
- Perz K., Rewolińska A. Impact of network expansions on energy losses in compressed air // 1st International Conference Functional and Engineering Materials – FEM 2019 16-18 October 2019, Lodz, Poland. IOP Conference Series: Materials Science and Engineering. 2020. Vol. 743. № 012045. DOI: 10.1088/1757-899X/743/1/012045
- Terrill T.J., Kim T., Rasmussen B.P. Feasibility of using thermal response methods for nonintrusive compressed air flow measurement // Flow Measurement and Instrumentation. 2021. Vol. 77. № 101869. DOI: 10.1016/j.flowmeasinst.2020.101869
- Belligoli Z., Dwight R., Kok G., Lucas P. A Bayesian study of uncertainty in ultrasonic flow meters under non-ideal flow conditions // Metrologia. 2017. Vol. 54. Iss. 4. № 584. DOI: 10.1088/1681-7575/aa7b8d
- Guenther T., Krol A. Automated detection of compressed air leaks using a scanning ultrasonic sensor system // 2016 IEEE Sensors Applications Symposium (SAS), 20-22 April 2016, Catania, Italy. IEEE, 2016. №16051876. DOI: 10.1109/SAS.2016.7479830
- Емельянов А.П., Васильев Б.Ю. Алгоритмы и технические средства управления автоматизированным электроприводом турбомеханизмов // Вестник Ивановского государственного энергетического университета. 2013. № 1. С. 92-96.
- Ильюшин Ю.В., Афанасьева О.В. Разработка Scada-модели компрессорной станции магистрального газопровода // Записки Горного института. 2019. Т. 240. С. 686-693. DOI: 10.31897/PMI.2019.6.686
- Котелева Н.И., Жуковский Ю.Л., Козак Р.А. Технология дополненной реальности как средство повышения безопасности промышленных производств // Горный информационно-аналитический бюллетень. 2019. № S7. С. 117-129. DOI: 10.25018/0236-1493-2019-4-7-117-129
- Menon E.S.Piping Calculations Manual. NY: McGraw-Hill Education, 2005. 666 p.
- Кузнецов Ю.В., Кузнецов М.Ю. Сжатый воздух. Екатеринбург: Уральское отделение Российской академии наук, 2007. 511 с.
- Menon E.S.Pipeline Planning and Construction Field Manual. Elsevier Inc, 2011. 576 p.
- Лисовский В.В., Родионов В.А. Основные направления совершенствования единой системы управления промышленной безопасностью и охраной труда в АО «СУЭК» // Горный информационно-аналитический бюллетень. 2019. № S6. С. 21-32. DOI: 10.25018/0236-1493-2019-4-6-21-32