Влияние термической обработки на микроструктуру стальных змеевиков нагревательной трубчатой печи
- 1 — д-р техн. наук доцент Санкт-Петербургский горный университет ▪ Orcid ▪ Elibrary ▪ Scopus
- 2 — аспирант Санкт-Петербургский горный университет ▪ Orcid
Аннотация
При транспортировке и переработке тяжелой металлоносной нефти возникают проблемы с локальными разрушениями металлических конструкций и элементов из-за процессов коррозии. Во время эксплуатации оборудования выявлено, что преждевременный выход из строя стальных змеевиков нагревательных трубчатых печей на нефтеперерабатывающих и нефтехимических заводах связан с недостаточной прочностью и коррозионной стойкостью стальных конструкций. Изучение влияния структуры и фазового состава стальных элементов из сплава 15Х5М нагревательных печей нефтеперерабатывающего производства на коррозионные свойства, связанные с потерей массы и локальными разрушениями во время термообработки, позволяет разработать условия защиты и определить режимы нагрева с лимитирующей стадией скорости окисления. Скорость различных типов коррозии стали марки 15Х5М используется в качестве показателя для оценки эффективности примененных режимов термических обработок змеевиков с целью повышения коррозионной стойкости и улучшения их эксплуатационных характеристик. Проведенные эксперименты по термообработке некоторых участков стальных змеевиков позволили определить рациональные режимы нагрева исследуемых змеевиков, что позволяет снизить потерю их массы и повысить коррозионную стойкость рабочих поверхностей во время эксплуатации. Предлагаемый вариант термообработки стальных змеевиков в заданные промежутки времени их работы в трубчатых печах создает условия для устойчивой эксплуатации и влияет на степень промышленной и экологической безопасности при снижении материальных затрат, связанных с ремонтом и заменой отдельных узлов и деталей трубчатых печей.
Введение
Углеводородное сырье, несмотря на поиск новых альтернативных источников энергии и безуглеродных технологий, остается основным компонентном минерально-сырьевого комплекса [25]. Добыча, транспортировка, обработка, экспорт и эффективное использование углеводородных материалов – одна из основных опор в развитии страны [24, 26]. Устойчивое повышение спроса на качественные нефтепродукты зависит от условий эксплуатации некоторых узлов и стальных деталей нагревательных печей и агрегатов нефтеперерабатывающих заводов (НПЗ). Помимо разработки новых типов сплавов для повышения эксплуатационных свойств змеевиков и других стальных деталей, необходимо обеспечить эффективную защиту от коррозии и разработать режимы для стабильной и безаварийной работы при высоких температурах в химически агрессивных средах. На НПЗ это происходит только в очень ограниченном масштабе. Использование стальных змеевиков различного типа зависит в первую очередь от цен на высоколегированные сплавы. Это объясняется тем, что во время термической обработки нефти в трубчатых печах при разрушении стальной поверхности змеевика преобладают в основном процессы, связанные с электрохимической коррозией, поэтому в состав стали нужно вводить модифицирующие и легирующие элементы, снижающие общий уровень коррозии [20]. Существуют тенденция и статистика аварийных остановок НПЗ из-за процессов коррозии, которые преждевременно выводят из строя стальные змеевики, что приводит к экологическим нарушениям, прямым экономическим потерям и производственным травмам [7, 17].
Предварительная термическая обработка стальных змеевиков перед их эксплуатацией может рассматриваться как перспективный метод ограничения преждевременного разрушения поверхности в результате коррозии. Во время термической обработки создаются условия для трансформации структуры, при которой замедляется скорость коррозии, поскольку во время интервального нагрева происходят фазовые превращения, способствующие однородности микроструктуры. Таким образом, стальные змеевики можно эксплуатировать в течение более длительного периода из-за действия лимитирующей стадии механизма коррозии [31].
Предварительную термическую обработку можно отнести к группе стандартных технологических решений, но возможно применение и ряда инновационных подходов в данной области [6, 8, 11]. Значимым также является поиск альтернативных способов сохранения тепла и его рециклинга при нагреве [5, 29]. При этом методологически востребовано как математическое моделирование, так и экспериментальное исследование по определению параметров нефтегазотранспортных систем [14, 15, 22].
Это исследование направлено на определение наилучшей термообработки для конкретного типа сплава, наиболее часто используемого в змеевиках трубчатых печей, для того, чтобы применить термообработку перед использованием змеевиков как меру предосторожности. Возможно использование термообработки в качестве защитной процедуры при износе стальных змеевиков. Влияние получаемых микроструктур на коррозионную способность определяли на термообработанных образцах змеевиков (15Х5М), погруженных в застойную агрессивную (коррозионную) среду, состоящую из 50 % раствора NaCl (3,5 %), подкисленного HCl (pH = 5), и 50 % всесезонного электролита при 25 °С. Работа посвящена улучшению эксплуатационных свойств змеевиков трубчатых печей и повышению их устойчивости к коррозии за счет применения предварительной термической обработки.
Методология
План экспериментальных исследований включает изучение влияния температуры термообработки в диапазоне 200-700 °С, ее продолжительности и количества стадий на потерю массы стальных образцов в стандартном коррозионном испытании. Основным методом структурного исследования образцов являлся металлографический анализ, который проводили на оптическом микроскопе марки ZEISS Axio Lab.A1 (Германия) при увеличениях 20 и 100 раз. Микроструктуры были получены с помощью цифровой камеры ZEISS Axiocam ERc 5s, установленной на микроскопе, и компьютерной обработки изображения с помощью специализированного программного пакета. Cкорость коррозии оценивалась по величине потери массы образцов змеевика из стали марки 15Х5М.
Результаты
Известно, что предварительная термомеханическая обработка некоторых видов сталей приводит к увеличению износостойкости в 10 раз без изменения механических свойств изделия [1, 12]. Как правило, различные способы термообработки изделий (отпуск, закалка, отжиг, гомогенизация) повышают срок службы трубчатых термических печей и их элементов за счет структурных изменений ближнего порядка, связанных с фазовыми переходами и распределением углеродной фазы, упрочнения материала и снижения влияния местной коррозии [27, 30].
В трубчатых печах используют детали из жаропрочной низколегированной стали марки 15Х5М (мартенситного класса), которые работают при 600-650 °С. Химический состав стали 15Х5М приведен в табл.1, где указана массовая доля элементов в мас.% по ГОСТ 550-75, ТУ 14-3Р-62-2002 и ГОСТ Р 53932-2010. Температуры критических точек стали 15Х5М следующие: Ас1 – 815, Ас3 – 848, Ar3 – 775, Ar1 – 818 °С.
Taблица 1
Химический состав стали 15Х5М, мас.%
Год выпуска |
C |
Si |
Mn |
Ni |
S |
P |
Cr |
Mo |
W |
V |
Ti |
Cu |
Fe |
1975 |
≤ 0,15 |
≤ 0,5 |
≤ 0,5 |
≤ 0,6 |
≤ 0,025 |
≤ 0,03 |
4,5-6 |
0,45-0,6 |
≤ 0,3 |
≤ 0,05 |
≤ 0,03 |
≤ 0,2 |
100- |
2002 |
≤ 0,15 |
≤ 0,5 |
≤ 0,5 |
≤ 0,6 |
≤ 0,025 |
≤ 0,03 |
4,5-6 |
0,45-0,6 |
– |
≤ 0,03 |
– |
≤ 0,2 |
100- |
2010 |
0,11-0,19 |
0,17-0,37 |
0,4-0,7 |
≤ 0,3 |
0,15-0,035 |
≤ 0,035 |
0,8-1,1 |
0,4-0,6 |
– |
0,02-0,07 |
– |
≤ 0,3 |
100- |
Стальные змеевики не имеют склонности к охрупчиванию при закалке, а для удаления образовавшейся окалины (органических и неорганических отложений) с их внутренней поверхности применяют механическую обработку при помощи продувки или пескоструйных аппаратов во время кратковременных остановок оборудования. Однако стальные детали такого типа должны выдерживать высокие рабочие температуры без изменения своих эксплуатационных свойств. Несмотря на это, избежать внутреннего растрескивания змеевиков при критических температурах, давлении и движении агрессивной среды из-за высокой скорости коррозии на поверхности металла – не удается, что приводит к агрессивной местной коррозии. Из-за дальнейшего перегрева и прогара стенок стальных змеевиков с общей или локальной коррозией происходит аварийная остановка оборудования, вплоть до его разрушения при взрыве нефтепродуктов. Подобные случаи типичны для НПЗ, поэтому с заданной периодичностью проводится замена змеевиков [4, 33].
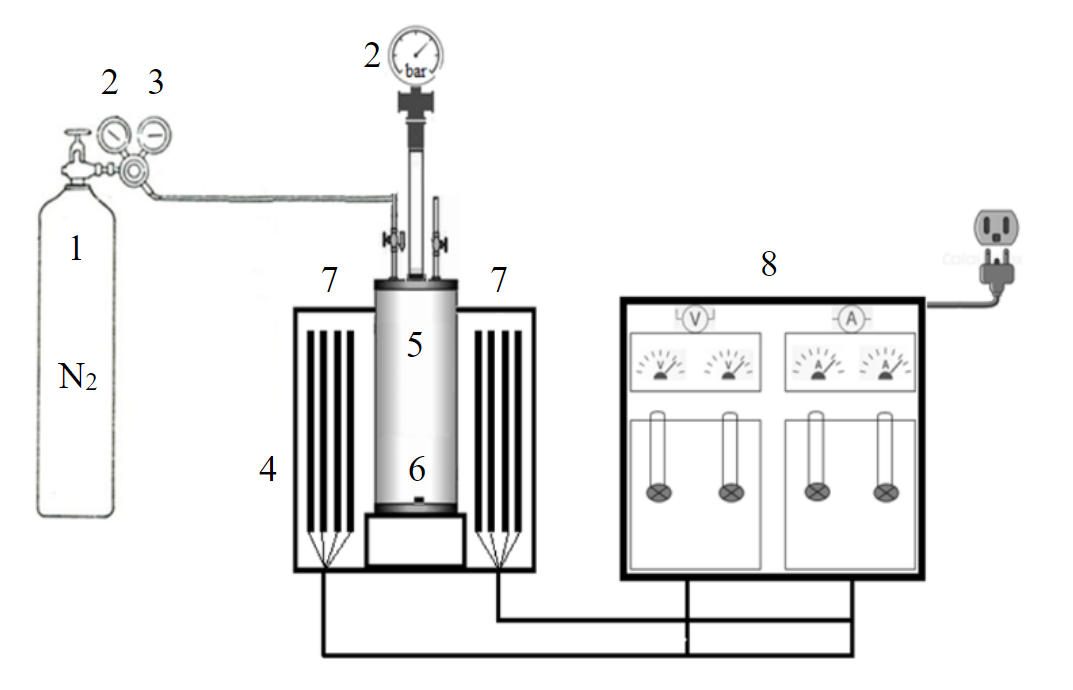
Рис.1. Установка для предварительной термообработки змеевиков трубчатых печей 1 – азотный баллон; 2 – манометры; 3 – расходомер; 4 – печь с силитовым нагревателем; 5 – герметичная термокамера; 6 – образцы змеевиков; 7 – стержни (нагревательные элементы); 8 – трансформатор
Для проведения термообработки образцов стального змеевика была собрана укрупнено-лабораторная установка, схема которой приведена на рис.1. Измерение и поддержание температуры в печи выполнялось с помощью хромель-алюмелевой термопары, включенной в цепь терморегулятора. Для защиты от окисления поверхности стальных темплетов, отобранных от змеевика, их термообработку проводили в атмосфере технического азота.
В проведенных ранее исследованиях определено [10, 16], что термическая и/или механическая обработка повышает уровень коррозионной стойкости стальных изделий. При этом отмечается, что пониженная скорость коррозии связана с формированием благоприятной микроструктуры образцов стали [9]. Также исследования указывают на повышенную скорость коррозии внутренней поверхности стальных деталей трубчатой печи, связанную в первую очередь с наличием металлов в углеводородной среде (нефть) [19, 32]. Принимая во внимание высокое значение вязкости металлоносной нефти, ее транспортировка и переработка естественно связана с развитием электрохимической коррозии поверхности змеевиков [18, 28, 34], скорость которой существенно возрастает при нагреве в трубчатой печи и участии отложений различной природы на теплопередающей поверхности [2, 23]. При этом повышенная скорость коррозии является результатом локального повышения температуры из-за низкой теплопроводности отложений, что в конечном итоге приводит к преждевременному выходу из строя змеевиков и остановке всей технологической цепочки.
Влияние температуры термообработки стальных образцов выполнялось в диапазоне 200-700 °С с шагом 100 °С (табл.2). Перед исследованием на электронном микроскопе все образцы стальных змеевиков трубчатой печи были подготовлены в виде темплетов, после чего обработаны и протравлены 5 % раствором азотной кислоты в этаноле (нитала) по стандартной методике [13]. Согласно принятой стандартной методике, для определения скорости коррозии образцов использовали электролит, состоящий из 50 % раствора NaCl (3,5 %) в смеси с HCl (pH = 5) и 50 % раствора на основе серной кислоты, с термостатированием образцов продолжительностью 5 суток при 25 °С. Полученные результаты приведены в табл.2 и на рис.2.
Taблица 2
Влияние температуры термообработки на потерю массы после выдержки в течение 1 ч и при охлаждении воздухом
Образец |
Т,°С |
М0, г |
∆М1, г |
∆М2, г |
∆М3, г |
∆М4, г |
∆М5, г |
∆ |
(∆ |
I0 |
– |
22,5207 |
0,1464 |
0,1466 |
0,1445 |
0,1461 |
0,1444 |
0,1456 |
0,65 |
I1 |
200 |
15,4811 |
0,2275 |
0,227 |
0,2277 |
0,2271 |
0,2272 |
0,2273 |
1,47 |
I2 |
300 |
13,3417 |
0,2581 |
0,2571 |
0,258 |
0,2573 |
0,2549 |
0,2571 |
1,93 |
I3 |
400 |
20,5718 |
0,1189 |
0,1165 |
0,1181 |
0,1179 |
0,1185 |
0,118 |
0,57 |
I4 |
500 |
21,5801 |
0,0166 |
0,0154 |
0,0161 |
0,0159 |
0,0163 |
0,0161 |
0,07 |
I5 |
600 |
19,4914 |
0,1078 |
0,1107 |
0,1072 |
0,1074 |
0,1079 |
0,1082 |
0,55 |
I6 |
700 |
14,5018 |
0,2177 |
0,2005 |
0,2101 |
0,2111 |
0,2113 |
0,2101 |
1,45 |
В табл.2 образец без термической обработки обозначен как I0 и показан как коричневая точка на графике (рис.2). Образцы после термообработки при 200, 300, 400, 500, 600 и 700 °C соответственно обозначаются как I1, I2, I3, I4, I5 и I6 последовательно; М0 – масса образца перед коррозионным испытанием; ∆М – величина потери массы образца в конце обработки при заданной температуре нагрева; ∆
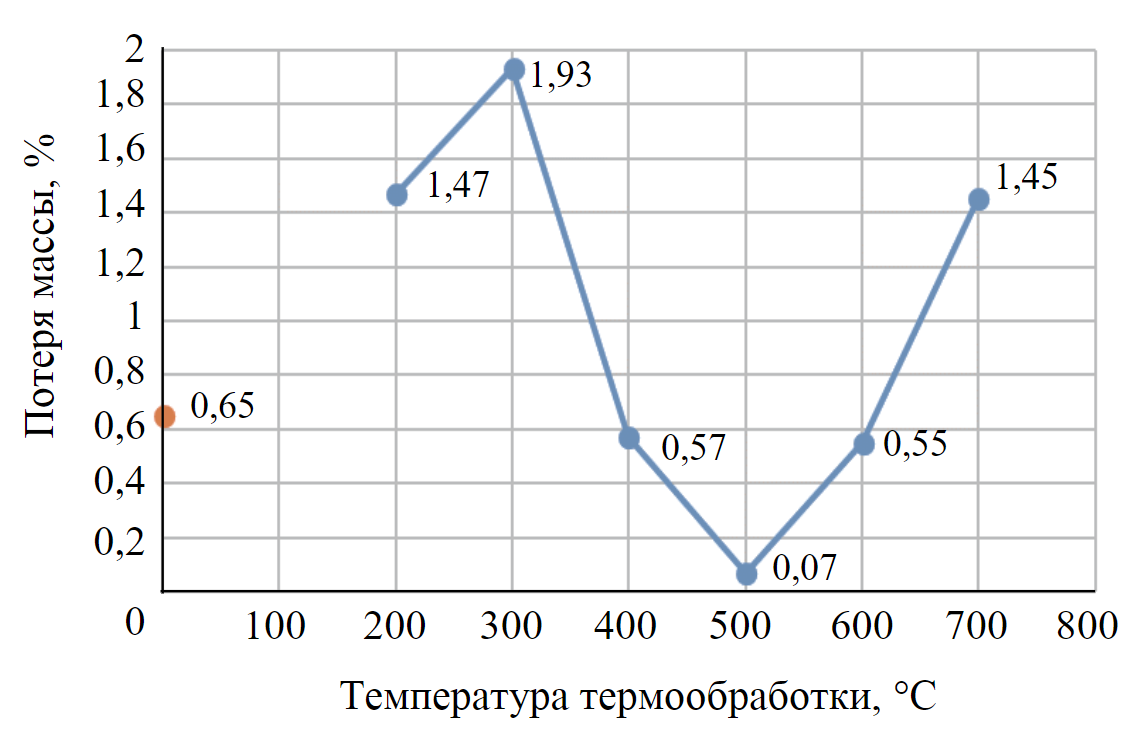
Рис.2. Влияние различных температур термообработки после выдержки в течение 1 ч и охлаждения воздухом на потерю массы
По данным рис.2 видно, что потеря массы снижается на 0,65/0,07 = 9,3 раза после 1 ч выдержки при 500 °C во время термообработки по сравнению с образцами без термической обработки. Допустим, эти условия соответствуют лимитирующей стадии процесса, когда скорость коррозии стремится к 0, не происходят фазовые переходы и не образуется перлит при температуре ниже 500 °C, которая значительно ниже критической (Ac1 = 815 °C) для образца змеевика из сплава 15Х5М.
Влияние количества повторных термообработок при 500 °C и последующей закалки исследовалось на примере четырех образцов. При этом первый образец представляет собой контрольный опыт, в котором стальной темплет после термообработки в течение установленного времени не подвергался закалке, а охлаждался на воздухе до комнатной температуры. Остальные образцы подвергались одно-, двух- или трехкратной закалке с последующим отпуском при температуре 500 °C в течение 1 ч и соответствующим охлаждением на воздухе до комнатной температуры. Для равномерного охлаждения образцов их закалка выполнялась в низкотемпературной водносолевой смеси на основе хлористого натрия при ее непрерывном перемешивании. Результаты коррозионного испытания образцов приведены в табл.3 и на рис.3. Согласно этим данным, скорость коррозии по величине потери массы образца представляет собой практически линейную функцию количества термообработок, что можно объяснить интенсивной фазовой перекристаллизацией и ростом количества межкристаллитных дислокаций, выступающих в качестве коррозионноактивных центров и интенсифицирующих коррозионное разрушение примерно 2,2 раза.
Результаты исследования длительности термообработки на коррозионное разрушение закаленных стальных змеевиков приведены в табл.4 и на рис.4. Относительная потеря массы образца снижается с 0,13 до 0,06 % по мере увеличения времени термообработки соответственно с 0,5 до 3 ч, что можно объяснить стабилизацией и выравниванием состава образцов.
Taблица 3
Влияние количества повторных нагревов до 500 °C на потерю массы
Образец |
М0, г |
∆М, г |
(∆М/М0) ∙100, % |
|
I0 |
14,8717 |
0,0168 |
0,11 |
|
I1 |
22,1734 |
0,031 |
0,14 |
|
I2 |
17,8911 |
0,0324 |
0,18 |
|
I3 |
13,1754 |
0,0316 |
0,24 |
Примечания: I0 – образец без закалки; I1 – после первой закалки; I2 –после второй закалки; I3 – после третьей закалки.
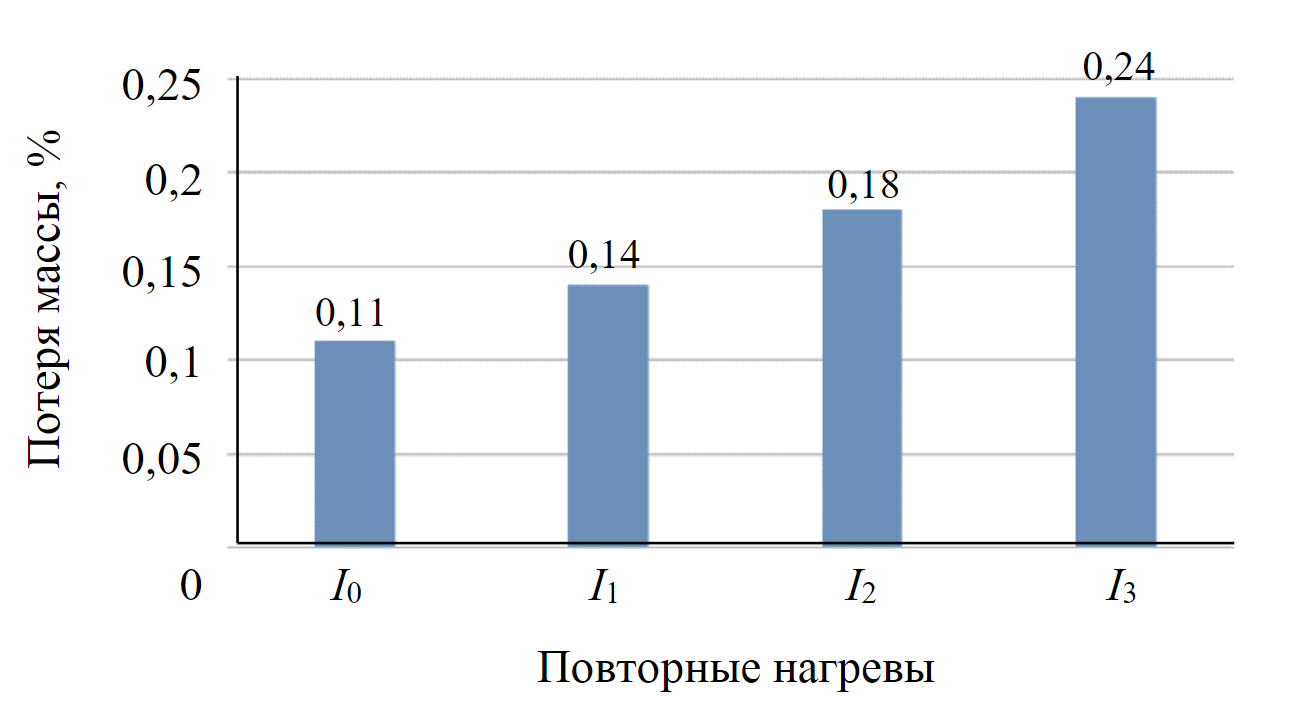
Рис.3. Влияние повторных нагревов при 500 °C на потерю массы
Taблица 4
Влияние времени закалки образцов при 500 °C на потерю массы
Образец |
t, ч |
М0, г |
∆М, г |
(∆М/М0) ∙ 100, % |
||
I0 |
0,5 |
16,8714 |
0,0219 |
0,13 |
||
I1 |
1 |
21,7501 |
0,0196 |
0,09 |
||
I2 |
2 |
19,2174 |
0,0154 |
0,08 |
||
I3 |
3 |
14,2214 |
0,0085 |
0,06 |
Примечание. I0, I1, I2, I3 – образцы, термообработанные при 500 °C в течение 30 мин, 1, 2 и 3 ч последовательно при отпуске, после охлаждения воздухом при комнатной температуре.
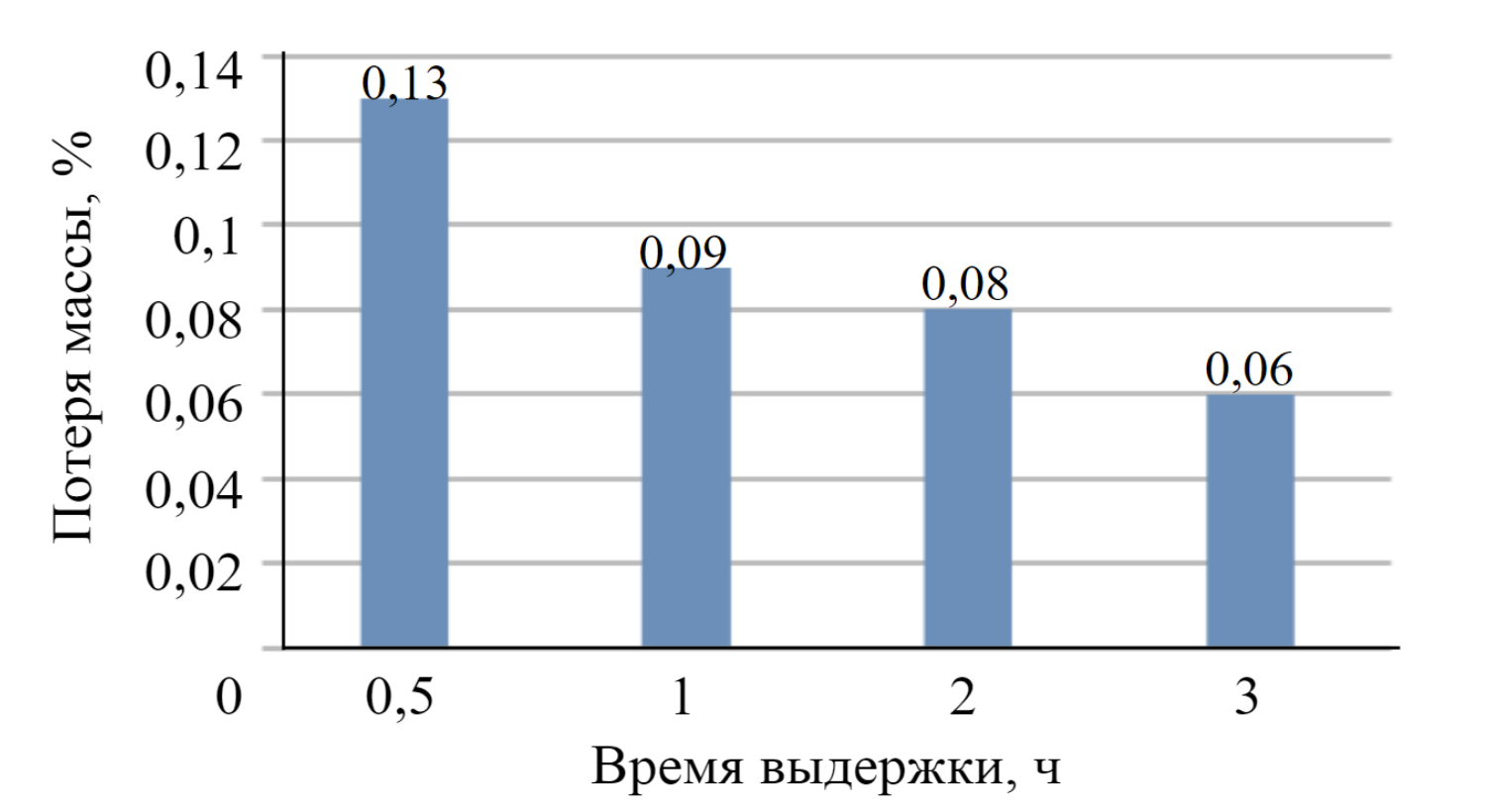
Рис.4. Влияние времени выдержки при 500 °C посредством отпуска на потерю массы
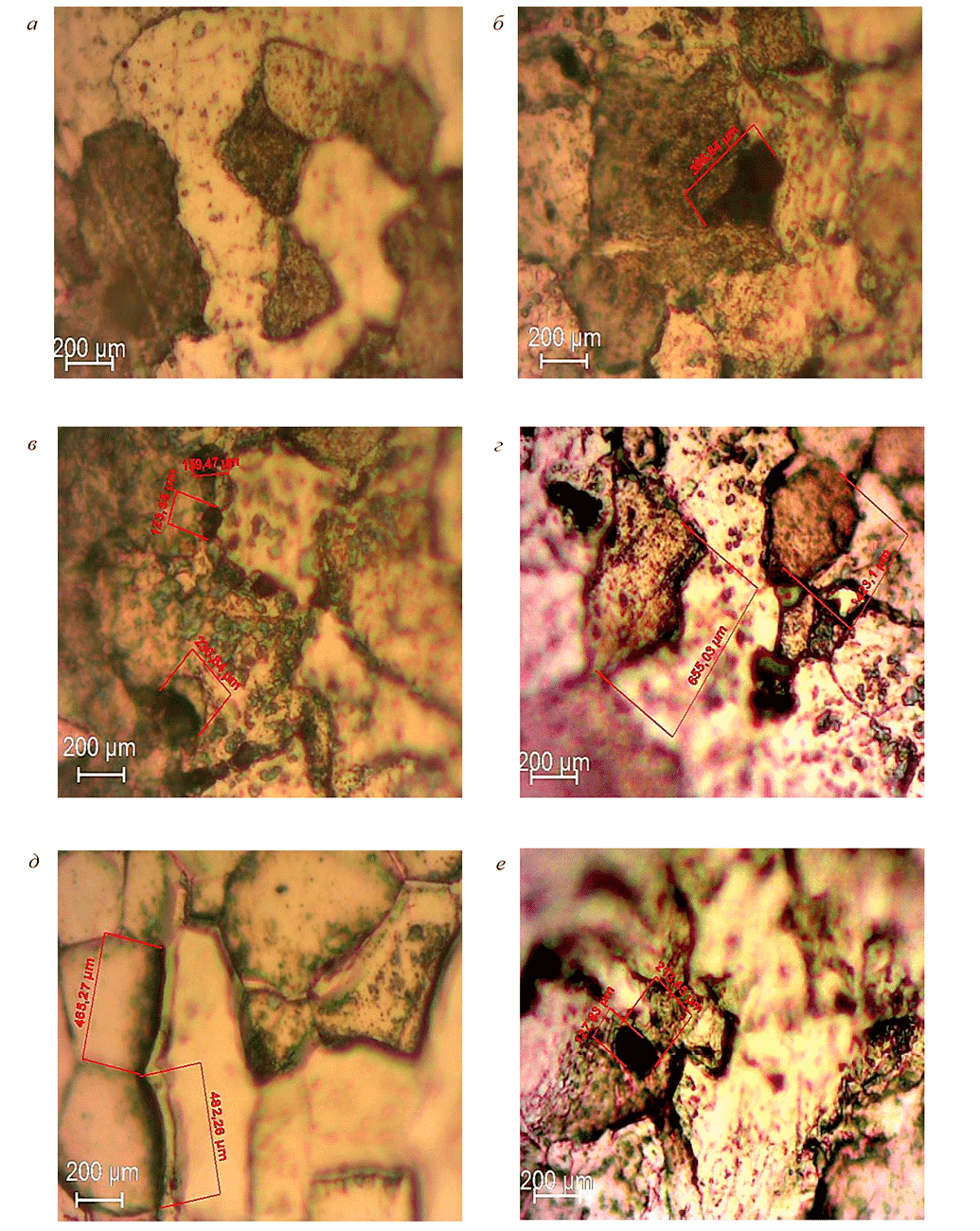
Рис.5 Микроструктуры змеевиков после термообработки при 200 (а), 300 (б), 400 (в), 500 (г), 600 (д) и 700 °С (е) (увеличение х100), выдержки в течение 1 ч и охлаждения воздухом
Исследование микроструктурных характеристик образцов выполнялось в зависимости от температуры термообработки для диапазона 200-700 °С и ее продолжительности (рис.5). При этом можно ориентироваться на известные закономерности термообработки мартенситных сталей, при которой избыточный углерод в составе мартенситной фазы высвобождается за счет выделения цементита Fe3C [3], что в нашем случае позволяет рассчитывать на образование низкоуглеродистых фаз со структурой сорбита и/или троостита [21]. Металлографический анализ показал, что с повышением температуры обработки наблюдается укрупнение кристаллитов феррита, а также распределение карбидистых частиц вдоль зеренных границ (рис.5, в-д) по сравнению с исходной структурой (рис.5, а). Структура при 300 °C состоит из мартенсита с колониями троостита и небольшого количества зерен бейнита (рис.5, б). При 400 °С выделяется цементит из мартенситной фазы, в результате чего она обедняется углеродом; начинается фазовый переход, который приводит к образованию ферритной фазы. Структура при 500 °C (рис.5, г) указывает на формирование зерен, состоящих из сорбита и бейнита, между колоний троостита и отложений карбида, которая характеризуется повышенной коррозионной устойчивостью благодаря образованию мелких сферических зерен цементита на ферритной матрице (рис.5, е). При повышении температуры обработки заметно укрупнение зерен цементита за счет уменьшения концентрации углерода в структуре феррита, что способствует понижению коррозионной устойчивости материала змеевика.
Заключение
Выполненный комплекс исследований позволяет сделать следующие основные выводы:
- Широкое использование низколегированных сталей в качестве конструкционного материала для изготовления змеевиков трубчатых нагревательных печей требует тщательного контроля их предварительной термообработки, которая имеет определяющее значение для повышения коррозионной устойчивости и срока службы змеевиков.
- Установлено, что предпочтительным режимом предварительной термообработки мартенситных сталей для повышения их коррозионной устойчивости является температура на уровне 500 °C и продолжительность процесса 2-3 ч. Такой режим обработки стальных образцов формирует однородную структуру стали с включением цементита в виде сферических частиц на ферритной основе (матрице), обеспечивающую повышение коррозионной устойчивости материала более чем в 9 раз по сравнению с образцами, не прошедшими предварительную термообработку.
Работа выполнена при поддержке правительства Республики Сирия в рамках диссертационной работы с целью повышения эксплуатационных характеристик металлических конструкций и оборудования нефтегазовых производств.
Литература
- Курганова Ю.А. Анализ возможности повышения свойств материала ВК15 для бурового инструмента / Ю.А.Курганова, К.С.Панина, П.С.Бешенков // Записки Горного института. 2018. Т. 233. С. 518-524. DOI: 10.31897/PMI.2018.5.518
- Причина быстрого износа тангенциальных резцов / В.И.Болобов, В.Л.Болобов, М.П.Талеров, В.С.Бочков // Записки Горного института. 2012. Т. 195. С. 238-240.
- Щипачев А.М. Влияние послесварочной обработки на скорость сплошной коррозии и микроструктуру сварных соединений сталей 20 и 30ХГСА / А.М.Щипачев, С.В.Горбачев // Записки Горного института. 2018. Т. 231. С. 307-311. DOI: 10.25515/PMI.2018.3.307
- Alexandrova T. Beneficiation of a low-grade phosphate ore using a reverse flotation technique / T.Aleksandrova, A.Elbendari, N.Nikolaeva // Mineral Processing and Extractive Metallurgy Review. 2020. Vol. 1. P. 1-6. DOI: 10.1080/08827508.2020.1806834
- Amer A.E. Numerical investigations on latent heat storage unit using phase change material / A.E.Amer, V.A.Lebedev // All-Russian scientific conference with international participation «Thermophysics and Power Engineering in Academic Centers» (TPEAC-2019), 21-23 October, 2019, St. Petersburg, Russian Federation. Journal of Physics: Conference Series, 2020. Vol. 1565. P. 1-9. DOI: 10.1088/1742-6596/1565/1/012099
- Assessment of possibility of obtaining alloying components in the process of desalting of heavy hydrocarbon raw materials. Part 1 / B.Issa, V.Yu.Bazhin, T.A.Alexandrova, V.G.Povarov // CIS Iron and Steel Review. 2020. Vol. 19. P. 8-12. DOI: 10.17580/cisisr.2020.01.02
- Characterizing foulants on slotted liner and probing the surface interaction mechanisms in organic media with implication for an antifouling strategy in oil production / L.Gong, J.Wang, L.Xiang et al. // Fuel. 2021. Vol. 290. P. 346-350. DOI: 10.1016/j.fuel.2020.120008
- Choi J. High-frequency heat treatment of AISI 1045 specimens and current calculations of the induction heating coil using metal phase transformation simulations / J.Choi, S.Lee // Metals. 2020. Vol. 10. Iss. 11. P. 1-11. DOI: 10.3390/met10111484
- Corrosion monitoring of complex heat recovery steam generation boilers / M.Ghafri, N.Behlani, S.Omairy, A.Muatasam, M.Nasif // XV International Conference Problems of Corrosion and Corrosion Protection of Materials «CORROSION-2020», 15-16 October, 2020, Lviv, Ukraine. OnePetro, 2020. Vol. 2020. P. 1-10.
- Design and analysis of parallel flow heat exchanger with baffles / R.Sharavanan, G.Boopathy, P.Periyasamy, R.Ramanan // International Journal of Mechanical and Production Engineering Research and Development. 2019. Vol. 9. Iss. 4. P. 1173-1182. DOI: 10.24247/ijmperdaug2019122
- Development of environmentally friendly diesel fuel / N.K.Kondrasheva, A.M.Eremeeva, K.S.Nelkenbaum et al. // Petroleum Science and Technology. 2019. Vol. 37. Iss. 12. P. 1478-1484. DOI: 10.1080/10916466.2019.1594285
- Enhancement of properties of micro-alloyed Low-carbon Ni-added Steel by thermomechanical treatment / D.Roy, A.K.Gupta, Md.S.Alam, S.Srikanth, B.K.Jha // Journal of Materials Engineering and Performance. 2020. Vol. 29. Iss. 12. P. 7952-7963. DOI: 10.1007/s11665-020-05311-w
- Failure analysis of an air-cooled heat exchanger in natural gas dehydration unit / M.Javidi, M.A.Sadeghi, R.Jafari, A.A.Hoodib // Engineering Failure Analysis. 2020. Vol. 115. P. 689-701. DOI: 10.1016/j.engfailanal.2020.104678
- Fetisov V.G. Aggregative simulation method for implementing mathematical models for gas transmission systems / V.G.Fetisov, A.K.Nikolaev, Yu.V.Lykov // IOP Conferences Series: Materials Science and Engineering. 2018. Vol. 327. Iss. 2. P. 1-9. DOI: 10.1088/1757-899X/327/2/022033
- Fetisov V.G. Experimental studies for determining gas flow rate accidental release on linear part of pipeline / V.G.Fetisov, A.K.Nikolaev, Yu.V.Lykov // IOP Conferences Series: Materials Science and Engineering. 2017. Vol. 87. Iss. 6. P. 1-7. DOI: 10.1088/1755-1315/87/6/062003
- Gorovei M.C. The effect of some key changes in the chemistry of water in relation to copper and brass corrosion control / M.C.Gorovei, L.Benéa // Euroinvent ICIR 2018, 17-18 May, 2018, Iasi, Romania. IOP Conference Series: Materials Science and Engineering, 2018. Vol. 374. P. 236-248. DOI: 10.1088/1757-899X/374/1/012057
- Hasan B.O. Study on oil fouling in a double pipe heat exchanger with mitigation by a surfactant / B.O.Hasan, H.Sh.Majdi, M.Hathal // Heat Transfer. 2020. Vol. 49. Iss 5. P. 2645-2658. DOI: 10.1002/htj.21738
- Ifezue D. Investigation of failed coils from a steam boiler // Journal of Failure Analysis and Prevention. 2017. Vol. 17. Iss. 5. P. 825-830. DOI: 10.1007/s11668-017-0330-3
- Increasing the corrosion resistance of tubular furnace elements at temperature range 400-700 °C in accelerated testing for real operational conditions / B.Issa, V.Yu.Bazhin, T.A.Aleksandrova // Materials of the 12th Russian-German raw materials conference, 27-29 November, 2019, St. Petersburg, Russian Federation. CRC Press, 2020. Vol. 1. P. 174-185.
- Increasing the corrosion resistance of welded radiant and convection flexible pipes in tubular furnaces of the Kinef refinery / B.Issa, V.Yu.Bazhin, N.M.Telyakov, A.N.Telyakov // VI Youth Forum of the World Petroleum Council – Future Leaders Forum (WPF 2019), 23-28 June, 2019, St. Petersburg, Russian Federation. CRC Press, 2019. Vol. 1. P. 243-249.
- Jakobi D. Behavior of high-temperature tube materials in sulfur-containing steam-cracking conditions / D.Jakobi, P.Karduck // CORROSION 2018, 15-19 April, 2018, Phoenix, Arizona, US. OnePetro, 2018. Vol. 2018. P. 6358-6371.
- Jarmai K. Investigation of welded protective covers for heat treatment / K.Jarmai, R.Szű // Pollack Periodica. 2020. Vol. 15. Iss. 1. P. 15-26. DOI: 10.1556/606.2020.15.1.2
- Li F. Analytical modeling of the temperature using uniform moving heat source in planar induction heating process / F.Li, J.Ning, S.Y.Liang // Applied Sciences. 2019. Vol. 9. Iss. 7. P. 24-36. DOI: 10.3390/app9071445
- Litvinenko V.S. Innovations as a factor in the development of the natural resources sector / V.S.Litvinenko, I.B.Sergeev // Studies on Russian Economic Development. 2019. Vol. 30. Iss. 6. P. 637-645. DOI: 10.1134/S107570071906011X
- Litvinenko V. The role of hydrocarbons in the global energy agenda: the focus on liquefied natural gas // Resources. 2020. Vol. 9. Iss. 5. P. 1-22. DOI: 10.3390/RESOURCES9050059
- Mechanism of interaction between the Cu/Cr interface and its chemical mixing on tensile strength and electrical conductivity of a Cu-Cr-Zr alloy / X.Chen, H.Zhou, T.Zhang et al. // Materials & Design. 2019. Vol. 180. № 107976. DOI: 10.1016/j.matdes.2019.107976
- Pevzner M.Z. Formation of structure, texture and properties and control of continuous induction heat treatment of brass strips / M.Z.Pevzner, S.G.Khayutin // Metal Science and Heat Treatment. 2020. Vol. 62. Iss. 7-8. P. 534-539. DOI: 10.1007/s11041-020-00598-x
- Shi X. Corrosion fatigue cracking of tube coils in an actifier column catalytic cracker / X.Shi, Y.Shi // Engineering Failure Analysis. 2003. Vol. 10. Iss. 3. P. 297-306. DOI: 10.1016/S1350-6307(02)00074-2
- Study of the hot-spot temperature during quench in the non-planar coils of W7-X / K.Sedlak, P.Bruzzone, T.Rummel, M.Nagel // IEEE Transactions on Applied Superconductivity. 2018. Vol. 28. Iss. 3. P. 27-36. DOI: 10.1109/TASC.2017.2779147
- Suppression of heat generation in magnetic stimulation coil applied for treating dysphagia / H.Mori, H.Kagaya, S.Izumi et al. // Magnetic Society of Japan. 2019. Vol. 43. Iss. 4. P. 84-90. DOI: 10.3379/msjmag.1907R003
- Thermomechanical behavior of the HL-LHC 11 Tesla Nb3SN magnet coil constituents during reaction heat treatment / C.Scheuerlein, F.Lackner, F.Savary et al. // IEEE Transactions on Applied Superconductivity. 2018. Vol. 28. Iss. 3. P. 45-57. DOI: 10.1109/TASC.2018.2792485
- The role of chloride, oxygen and aluminum on corrosion resistance of coiled-pipes in tubular furnaces of oil refinery / B.Issa, V.Yu.Bazhin, N.M.Telyakov, A.N.Telyakov // Quality Management and Reliability of Technical Systems, 20-21 June, 2019, St. Petersburg, Russian Federation. IOP Conference Series: Materials Science and Engineering, 2019. Vol. 666. P. 1-8. DOI: 10.1088/1757-899X/666/1/012027
- Yang Z. Study on influence of three kinds of stress on crack propagation in butt welds of spiral coil waterwall for ultra supercritical boiler / Z.Yan, J.Si // 2017 3rd International Conference on Applied Materials and Manufacturing Technology (ICAMMT 2017), 23-25 June, 2017, Changsha, China. IOP Conference Series: Materials Science and Engineering, 2017. Vol. 242. P. 1-9. DOI: 10.1088/1757-899X/242/1/012051
- Zyl van G. Fitness-for-service assessment of externally corroded convection coil tube / G.van Zyl, A.Al-Salmi // American Society of Mechanical Engineers (ASME), 14-19 July, 2019, San Antonio, Texas, USA. 2019. Vol. 3. P. 181-192. DOI: 10.1115/PVP2019-93829