Influence of heat treatment on the microstructure of steel coils of a heating tube furnace
- 1 — Ph.D., Dr.Sci. Associate Professor Saint Petersburg Mining University ▪ Orcid ▪ Elibrary ▪ Scopus
- 2 — Postgraduate Student Saint Petersburg Mining University ▪ Orcid
Abstract
Transportation and refining of heavy metal-bearing oil are associated with the problems of localized destruction of metal structures and elements due to corrosion. In the process of equipment operation, it was revealed that premature failure of steel coils of heating tube furnaces at oil refineries and petrochemical plants was associated with insufficient strength and corrosion resistance of the steelwork. The study of the effect that structure and phase composition of 15KH5M-alloy steel elements of heating furnaces at oil refineries have on the corrosion properties, associated with mass loss and localized destructions in the process of heat treatment, allows to develop protective measures and determine heating modes with a rate-limiting step of oxidation. The rate of various corrosion types of 15KH5M steel is used as an indicator to assess the effectiveness of the applied modes of coil heat treatment in order to increase their corrosion resistance and improve their operational characteristics. Conducted experiments on heat treatment of certain steel coil sections allowed to determine rational heating modes for the studied coils, which made it possible to reduce their mass loss and increase corrosion resistance of working surfaces in the process of operation. Proposed heat treatment of steel coils at specified intervals of their operation in the tube furnaces creates conditions for their stable performance and affects the degree of industrial and environmental safety, as well as reduces material costs associated with the repair and replacement of individual assemblies and parts of tube furnaces.
Introduction
Despite the search for new alternative energy sources and carbon-free technologies, raw hydrocarbons remain the key component of the mineral resources sector [25]. Extraction, transportation, refining, export and efficient use of hydrocarbon materials constitute one of the main pillars in the development of the country [24, 26]. A steadily increasing demand for high-quality oil products depends on the operating conditions of certain assemblies and steel parts of heating furnaces and oil refinery units. In addition to the development of new types of alloys for improving performance characteristics of coils and other steel parts, it is necessary to provide effective protection against corrosion and to develop modes for stable and trouble-free operation at high temperatures in chemically aggressive media. In oil refineries, it occurs on a very limited scale. The use of steel coils of various types depends primarily on the prices of high-alloy steel. This is explained by the fact that during oil heat treatment in tube furnaces, destruction of the steel coil surface is predominantly caused by the processes of electrochemical corrosion; therefore, modifying and alloying elements need to be added to the steel to reduce the overall level of corrosion [20]. There is a tendency and statistics of emergency shutdowns of oil refineries due to corrosion processes, which prematurely damage steel coils and consequently lead to environmental non-compliance, direct economic losses and industrial accidents [7, 17].
Preliminary heat treatment of steel coils before their use can be considered as a promising method of limiting premature surface damage, caused by corrosion. The process of heat treatment creates conditions for structure transformation, which is associated with reduction of the corrosion rate, since interval heating is accompanied by phase transitions that add to homogeneity of the microstructure. Thus, the operating life of steel coils can be extended due to the rate-limiting step of the corrosion mechanism [31].
Preliminary heat treatment can be classified as a standard technological solution, but it is also possible to use a number of innovative approaches in this area [6, 8, 11]. Another significant option is the search for alternative methods of heat conservation and its recycling during heating [5, 29]. In these circumstances, there is methodological relevance both in mathematical modeling and in experimental studies that determine the parameters of oil and gas transportation systems [14, 15, 22].
The aim of this research is to determine the best mode of heat treatment for a particular type of steel alloy, which is most commonly used in tube furnace coils, in order to apply preliminary heat treatment to the coils as a precautionary measure. The use of heat treatment can serve as a protective procedure against the wear of steel coils. The effect of obtained microstructures on the corrosion resistance was determined using heat-treated coil samples (15KH5M), immersed in a stagnant aggressive (corrosive) medium, composed of 50 % NaCl solution (3.5 %) acidified with HCl (pH = 5) and 50 % of all-season electrolyte at 25 °C. The study is dedicated to improving performance characteristics of steel coils of tube furnaces and increasing their corrosion resistance by means of preliminary heat treatment.
Methodology
Methodology. The program of experimental research involved studying the effect of heat treatment temperature (in the interval of 200-700 °C), duration of heat treatment and the number of stages for the mass loss of steel samples in a standard corrosion test. The main method for structural study of the samples was metallographic analysis, performed on a ZEISS Axio Lab.A1 optical microscope (Germany) at 20x and 100x magnification. Microstructures were obtained using a ZEISS Axiocam ERc 5s digital camera, mounted on a microscope, and computer image processing by means of specialized software. Corrosion rate was estimated by the mass loss of coil samples made of 15KH5M steel.
Results
It is well known that preliminary thermomechanical treatment of certain steel types leads to a 10-fold increase in wear resistance without changing mechanical properties of the workpiece [1, 12]. As a rule, various methods of workpiece heat treatment (tempering, quenching, annealing, homogenization) extend the operating life of tube thermal furnaces and their elements due to short-range structural changes, associated with phase transitions and distribution of the carbon phase, material hardening and reducing the effect of localized corrosion [27, 30].
The parts of tube furnaces are made of heat-resistant low-alloy 15KH5M steel (martensitic class) able to withstand 600-650 °С. Chemical composition of 15KH5M steel is presented in Table 1, with mass percent of the elements (in wt.%) according to the technical standards GOST 550-75, TU 14-3R-62-2002 and GOST R 53932-2010. Critical temperatures of 15KH5M steel are the following: Ас1 – 815, Ас3 – 848, Ar3 – 775, Ar1 – 818 °С.
Table 1
Chemical composition of 15KH5M steel, wt.%
Year of manufacture |
C |
Si |
Mn |
Ni |
S |
P |
Cr |
Mo |
W |
V |
Ti |
Cu |
Fe |
1975 |
≤ 0,15 |
≤ 0,5 |
≤ 0,5 |
≤ 0,6 |
≤ 0,025 |
≤ 0,03 |
4,5-6 |
0,45-0,6 |
≤ 0,3 |
≤ 0,05 |
≤ 0,03 |
≤ 0,2 |
100- |
2002 |
≤ 0,15 |
≤ 0,5 |
≤ 0,5 |
≤ 0,6 |
≤ 0,025 |
≤ 0,03 |
4,5-6 |
0,45-0,6 |
– |
≤ 0,03 |
– |
≤ 0,2 |
100- |
2010 |
0,11-0,19 |
0,17-0,37 |
0,4-0,7 |
≤ 0,3 |
0,15-0,035 |
≤ 0,035 |
0,8-1,1 |
0,4-0,6 |
– |
0,02-0,07 |
– |
≤ 0,3 |
100- |
Steel coils are not prone to embrittlement when quenched. Removal of the formed scale (organic and inorganic deposits) from the inner surface of the coil is carried out by means of mechanical treatment using blowing or sandblasting devices during short-term equipment shutdowns. However, steel parts of this type have to withstand high operating temperatures and maintain their performance characteristics. Due to high corrosion rate on the surface of the metal, it is impossible to avoid internal cracking of the coils at critical temperatures, pressure and motion of the aggressive medium, which leads to aggressive localized corrosion. Further overheating and burning through the walls of steel coils, caused by overall or localized corrosion, lead to emergency shutdown of the equipment, to the extent of its destruction by the explosion of oil products. Such cases are typical for oil refineries, and therefore on a scheduled periodic basis the coils are replaced [4, 33].
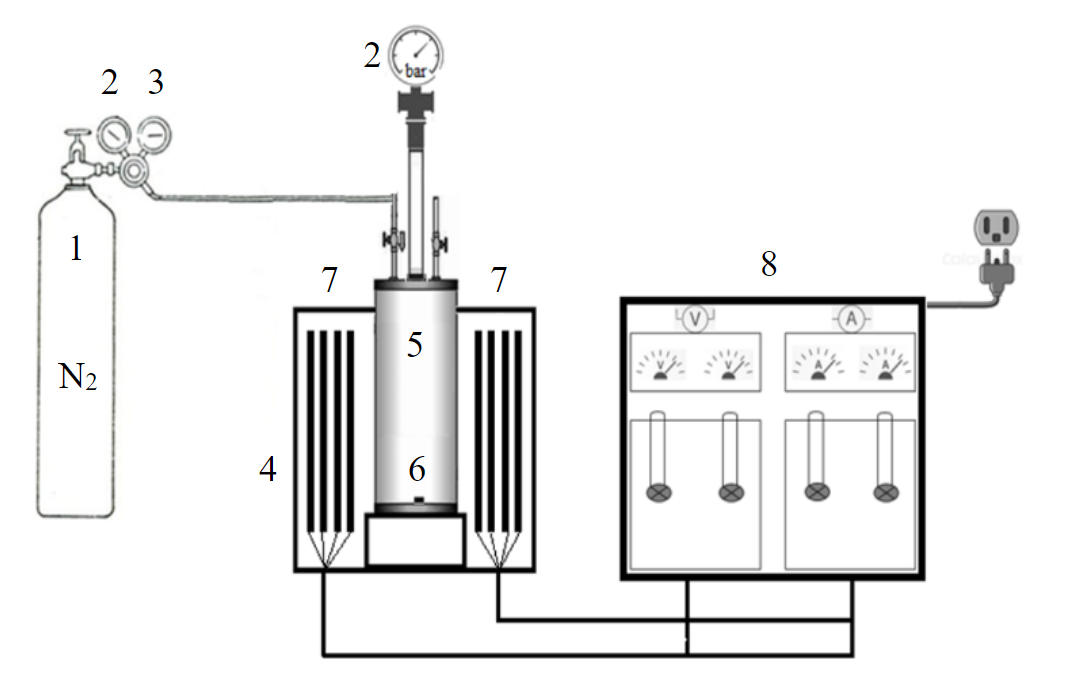
Fig.1. Installation for preliminary heat treatment of tube furnace coils 1 – nitrogen gas cylinder; 2 – manometers; 3 – flow meter; 4 – furnace with a silicon carbide heating element; 5 – sealed thermal chamber; 6 – coil samples; 7 – rods (heating elements); 8 – transformer
In order to perform heat treatment of steel coil samples, we assembled an integrated laboratory installation, the diagram of which is presented in Fig.1. The temperature in the furnace was measured and maintained with the help of a Cr/Al thermocouple connected to the controller. To protect the surface of steel templates obtained from the coil from oxidation, their heat treatment was performed in the atmosphere of technical nitrogen.
The studies performed earlier [10, 16] estimate that thermal and/or mechanical treatment increase corrosion resistance of steel workpieces. At the same time, it is noted that reduced corrosion rate is associated with a more favorable microstructure of the studied steel samples [9]. The studies also indicate elevated rates of corrosion on the inner surface of steel parts of the tube furnace, which is primarily attributed to the presence of metals in the hydrocarbon medium (oil) [19, 32]. Taking into account high viscosity of metal-bearing oil, its transportation and refining are naturally associated with the development of electrochemical corrosion of the coil surface [18, 28, 34], the rate of which significantly increases with the heating in the tube furnace and in the presence of sediments of various origin on the heat-transmitting surface [2, 23]. Notably, elevated corrosion rates result from localized temperature increase due to low thermal conductivity of the sediments, which ultimately leads to premature failure of steel coils and shutdown of the entire technological chain.
The influence of the temperature of steel coil heat treatment was studied in the interval of 200-700 °C with a step of 100 °C (Table 2). Before examination with an electron microscope, all the samples of the tube furnace steel coils were prepared as templates and then processed and etched with a 5 % solution of nitric acid in ethanol (nital), according to the conventional method [13]. To estimate sample corrosion rate according to the accepted conventional method, we used an electrolyte composed of 50 % NaCl solution (3.5 %) mixed with HCl (pH = 5) and 50 % sulfuric acid based solution with thermostatic control of the samples for 5 days at 25 °C. The results obtained are presented in Table 2 and Fig.2.
Table 2
Influence of heat treatment temperature on mass loss after 1 h of hold time and air cooling
Sample |
Т,°С |
М0, g |
∆М1, g |
∆М2, g |
∆М3, g |
∆М4, g |
∆М5, g |
∆ |
(∆ |
I0 |
– |
22,5207 |
0,1464 |
0,1466 |
0,1445 |
0,1461 |
0,1444 |
0,1456 |
0,65 |
I1 |
200 |
15,4811 |
0,2275 |
0,227 |
0,2277 |
0,2271 |
0,2272 |
0,2273 |
1,47 |
I2 |
300 |
13,3417 |
0,2581 |
0,2571 |
0,258 |
0,2573 |
0,2549 |
0,2571 |
1,93 |
I3 |
400 |
20,5718 |
0,1189 |
0,1165 |
0,1181 |
0,1179 |
0,1185 |
0,118 |
0,57 |
I4 |
500 |
21,5801 |
0,0166 |
0,0154 |
0,0161 |
0,0159 |
0,0163 |
0,0161 |
0,07 |
I5 |
600 |
19,4914 |
0,1078 |
0,1107 |
0,1072 |
0,1074 |
0,1079 |
0,1082 |
0,55 |
I6 |
700 |
14,5018 |
0,2177 |
0,2005 |
0,2101 |
0,2111 |
0,2113 |
0,2101 |
1,45 |
In Table 2, the sample without heat treatment is designated as I0 in the graph it is shown as a brown dot (Fig.2). Samples subjected to heat treatment under 200, 300, 400, 500, 600 and 700 °C are designated as I1, I2, I3, I4, I5 and I6, respectively; М0 is the mass loss of the sample at the end of treatment at a given temperature of heating; ∆
In Table 2, the sample without heat treatment is designated as I0 in the graph it is shown as a brown dot (Fig.2). Samples subjected to heat treatment under 200, 300, 400, 500, 600 and 700 °C are designated as I1, I2, I3, I4, I5 and I6, respectively; М0 is the mass loss of the sample at the end of treatment at a given temperature of heating; ∆
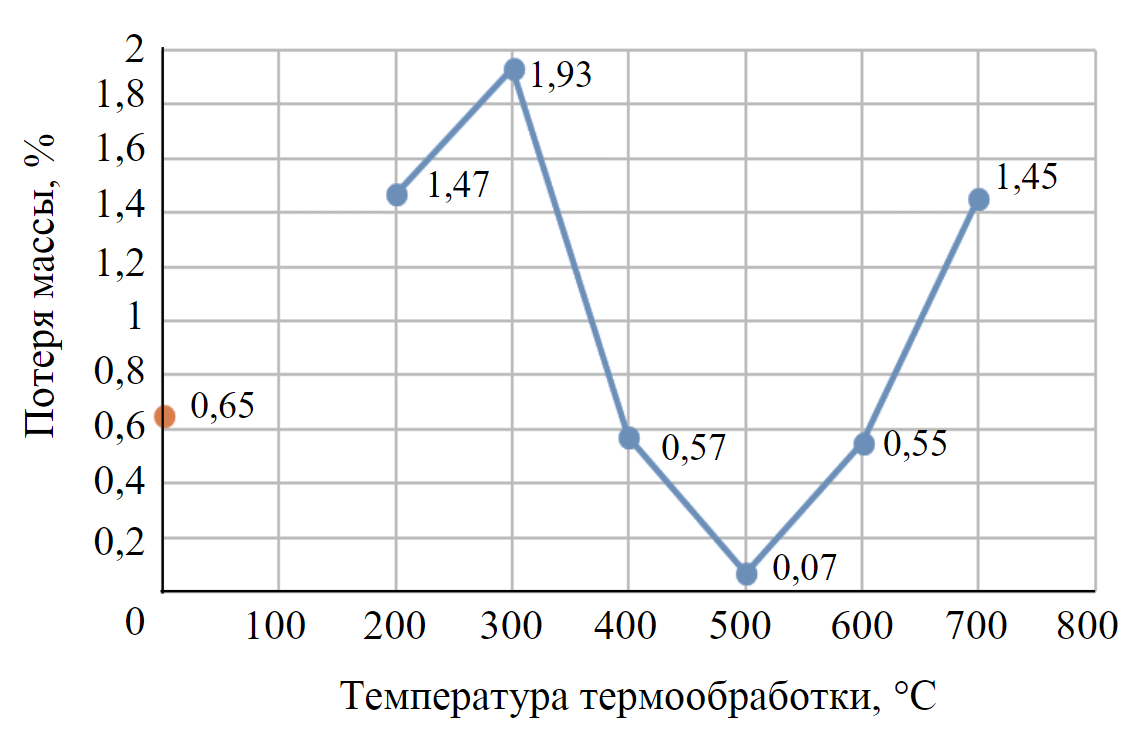
Fig.2. Influence of different temperatures of heat treatment on mass loss after 1 h of hold time and air cooling
According to Fig.2, it can be seen that in case of thermal heating the mass loss decreases by factor of 0.65/0.07 = 9.3 after 1 h of hold time at 500 °C compared to the samples without heat treatment. It was assumed that these conditions corresponded to the rate-limiting step of the process, when the corrosion rate tends to zero, there are no phase transitions and pearlite does not form under temperatures below 500 °C, which is significantly lower than the critical point (Ac1 = 815 °C) for the coil sample made of 15KH5M steel.
The effect of the number of reheats at 500 °C and subsequent quenching was studied on four samples. The first sample was used in the control test, where the steel template after heat treatment for a specified time was not subjected to quenching but was cooled in the air to room temperature. The remaining samples were subjected to one, two or three stages of quenching with subsequent tempering at 500 °C for one hour and cooling in the air to room temperature. For uniform cooling of the samples, their quenching was carried out in a low-temperature salt-water mixture based on sodium chloride, which was continuously stirred. The results of the corrosion test are presented in Table 3 and Fig.3. According to the data, corrosion rate estimated by the mass loss of the sample was practically a linear function of the number of reheats, which can be explained by the intensive phase of recrystallization and associated increase in the number of intercrystalline dislocations, which act as corrosive centers and intensify corrosion damage by factor of around 2.2.
Results of the study on the effect of heat treatment duration on the corrosion damage of quenched steel coils are presented in Table 4 and Fig.4. Relative mass loss of the sample decreases from 0.13 to 0.06 %, as heat treatment duration increases from 0.5 to 3 h, which can be explained by stabilization and levelling of sample composition.
Taблица 3
Influence of the number of reheats to 500 °C on the mass loss
Sample |
М0, g |
∆М, g |
(∆М/М0) ∙100, % |
|
I0 |
14,8717 |
0,0168 |
0,11 |
|
I1 |
22,1734 |
0,031 |
0,14 |
|
I2 |
17,8911 |
0,0324 |
0,18 |
|
I3 |
13,1754 |
0,0316 |
0,24 |
Notes. I0 – sample without quenching; I1 – sample after the first quenching; I2 –sample after second quenching; I3 – sample after third quenching.
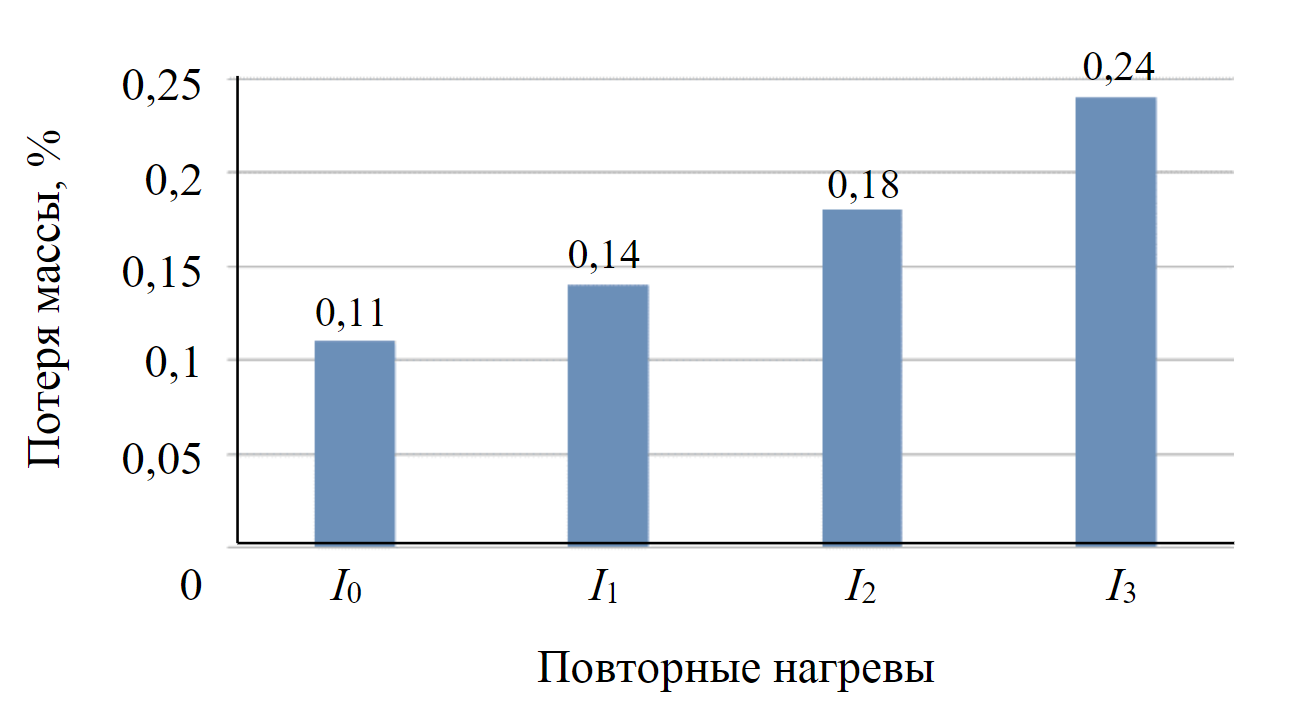
Fig.3. Influence of reheats to 500 °C on the mass loss
Taблица 4
Influence of tempering time at 500 °C on the mass loss
Sample |
t, ч |
М0, g |
∆М, g |
(∆М/М0) ∙ 100, % |
||
I0 |
0,5 |
16,8714 |
0,0219 |
0,13 |
||
I1 |
1 |
21,7501 |
0,0196 |
0,09 |
||
I2 |
2 |
19,2174 |
0,0154 |
0,08 |
||
I3 |
3 |
14,2214 |
0,0085 |
0,06 |
Note. I0, I1, I2, I3 – samples subjected to heat treatment by tempering at 500 °C for 30 min, 1, 2 and 3 h, respectively, after cooling in the air at room temperature.
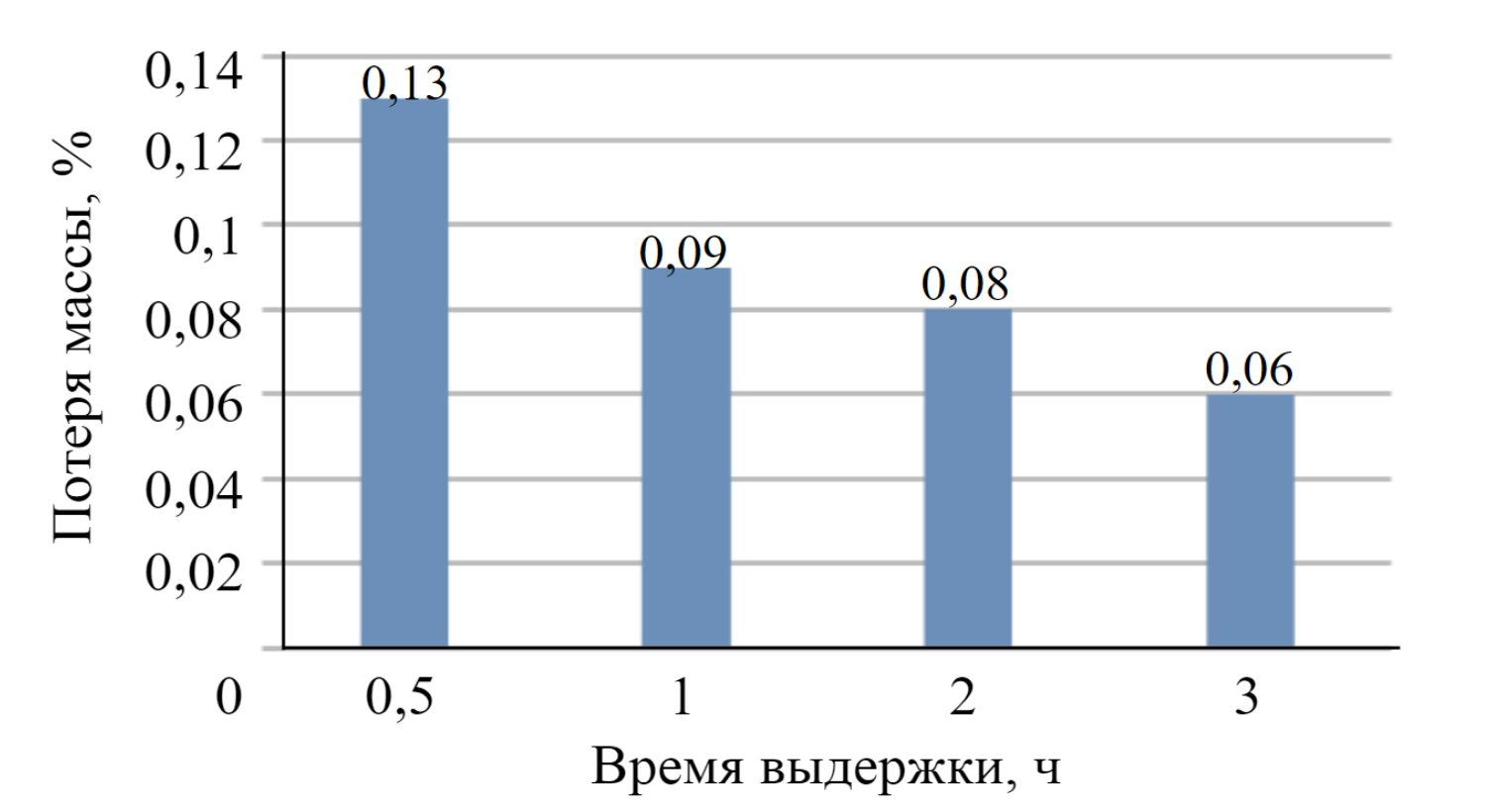
Fig.4. Influence of tempering hold time at 500 °C on the mass loss
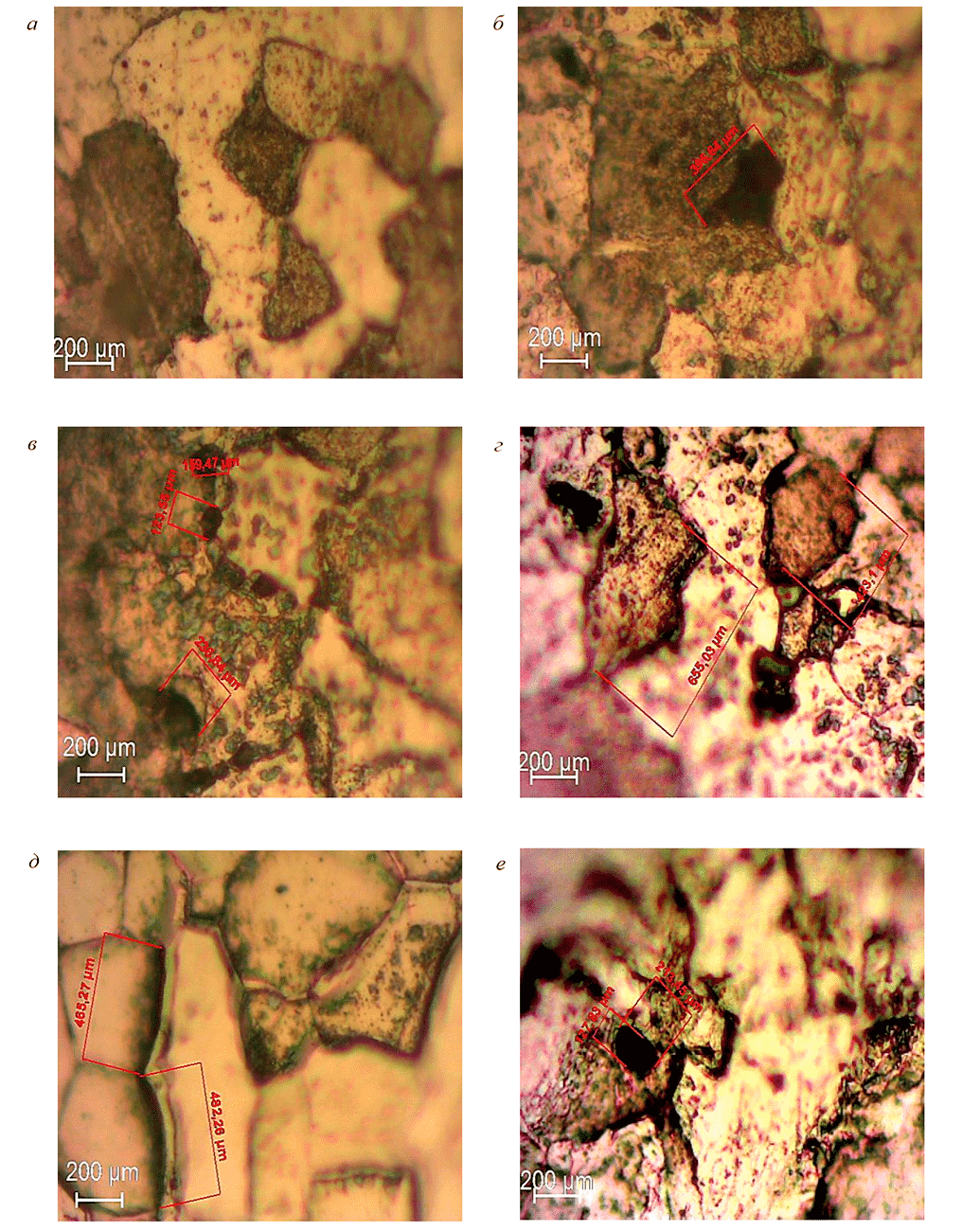
Fig.5. Microstructures of steel coils after heat treatment at 200 (a), 300 (b), 400 (c), 500 (d), 600 (e) and 700 °С (f ) (100x magnification), tempering for 1 h and air cooling
Analysis of microstructural characteristics of the samples was carried out depending on the temperature of heat treatment in the interval 200-700 °C and its duration (Fig.5). For this purpose, one can rely on the known patterns of heat treatment for martensitic steels, where excess carbon in the composition of the martensite phase gets liberated due to the release of cementite Fe3C [3], which in our case holds out the prospect of forming low-carbon phases with the structure of sorbite and/or troostite [21]. Metallographic analysis demonstrated that with an increase in the treatment temperature, one can observe coarsening of the crystalline grains of ferrite, as well as distribution of carbide particles along the grain boundaries (Fig.5, c-e) compared to the initial structure (Fig.5, a). At 300 °C, the structure consists of martensite with troostite colonies and a small fraction of bainite grains (Fig.5, b). At 400 °C, cementite begins to precipitate from the martensite phase. This process results in carbon depletion of the martensite phase and starts a phase transition, which leads to generation of the ferrite phase. At 500 °C, the structure in Fig.5, d indicates the formation of sorbite and bainite grains between the troostite colonies and carbide deposits. According to performed experimental studies, this structure is characterized by increased corrosion resistance due to the formation of small spherical grains of cementite in the ferrite matrix (Fig.5, f ). As the treatment temperature rises, cementite grains grow faster due to lowering carbon concentration in the ferrite structure, which contributes to decreasing corrosion resistance of the coil material.
Conclusions
Performed set of studies allows to draw the following main conclusions:
- The widespread use of low-alloy steel as a construction material for manufacturing coils of heating tube furnaces requires strict control over their preliminary heat treatment, which is particular-ly important for increasing corrosion resistance and extending operating life of the coils..
- It was identified that preferred conditions of preliminary heat treatment of martensitic steels for in-creasing their corrosion resistance include the temperature of the process at the level of 500 °C and duration of the process around 2-3 h. Such conditions of steel sample treatment provide formation of a uniform steel structure with inclusion of cementite in the form of spherical grains in the ferrite base (matrix), which results in a more than 9-fold increase in corrosion resistance of the material compared to the samples without preliminary heat treatment.
The study was supported by the Government of the Republic of Syria as a part of a dissertation research aimed at improving performance characteristics of metal structures and equipment for oil and gas industries.
References
- Kurganova Y.A., Panina K.S., Beshenkov P. S. Analysis of possible enhancement of properties of VK15 material used for drilling tools. Journal of Mining Institute. 2018. Vol. 233, p. 518-524. DOI: 10.31897/PMI.2018.5.518
- Bolobov V.I., Bolobov V.L., Talerov M.P., Bochkov V.S. Cause rapid wear tangential cutters. Journal of Mining Institute. 2012. Vol. 195, p. 238-240 (in Russian).
- Shchipachev A.M., Gorbachev S.V. Influence of post-welding processing on continuous corrosion rate and microstructure of welded joints of steel 20 and 30KHGSA. Journal of Mining Institute. 2018. Vol. 231, p. 307-311. DOI: 10.25515/PMI.2018.3.307
- Alexandrova T., Elbendari A., Nikolaeva N. Beneficiation of a low-grade phosphate ore using a reverse flotation technique. Mineral Processing and Extractive Metallurgy Review. 2020. Vol. 1, p. 1-6. DOI: 10.1080/08827508.2020.1806834
- Amer A.E., Lebedev V.A. Numerical investigations on latent heat storage unit using phase change material. All-Russian scientific conference with international participation “Thermophysics and Power Engineering in Academic Centers” (TPEAC-2019), 21-23 October, 2019, St. Petersburg, Russian Federation. Journal of Physics: Conference Series, 2020. Vol. 1565, p. 1-9. DOI: 10.1088/1742-6596/1565/1/012099
- Issa B., Bazhin V.Yu., Alexandrova T.A., Povarov V.G. Assessment of possibility of obtaining alloying components in the process of desalting of heavy hydrocarbon raw materials. Part 1. CIS Iron and Steel Review. 2020. Vol. 19, p. 8-12. DOI: 10.17580/cisisr.2020.01.02
- Gong L., Wang J., Xiang L. et al. Characterizing foulants on slotted liner and probing the surface interaction mechanisms in organic media with implication for an antifouling strategy in oil production. Fuel. 2021. Vol. 290, p. 346-350. DOI: 10.1016/j.fuel.2020.120008
- Choi J., Lee S. High-frequency heat treatment of AISI 1045 specimens and current calculations of the induction heating coil using metal phase transformation simulations. Metals. 2020. Vol. 10. Iss. 11, p. 1-11. DOI: 10.3390/met10111484
- Ghafri M., Behlani N., Omairy S., Muatasam A., Nasif M. Corrosion monitoring of complex heat recovery steam generation boilers. XV International Conference Problems of Corrosion and Corrosion Protection of Materials “CORROSION-2020”, 15-16 October, 2020, Lviv, Ukraine. OnePetro, 2020. Vol. 2020, p. 1-10.
- Sharavanan R., Boopathy G., Periyasamy P., Ramanan R. Design and analysis of parallel flow heat exchanger with baffles. International Journal of Mechanical and Production Engineering Research and Development. 2019. Vol. 9. Iss. 4, p. 1173-1182. DOI: 10.24247/ijmperdaug2019122
- Kondrasheva N.K., Eremeeva A.M., Nelkenbaum K.S. et al. Development of environmentally friendly diesel fuel. Petroleum Science and Technology. 2019. Vol. 37. Iss. 12, p. 1478-1484. DOI: 10.1080/10916466.2019.1594285
- Roy D., Gupta A.K., Alam Md.S., Srikanth S., Jha B.K. Enhancement of properties of micro-alloyed Low-carbon Ni-added Steel by thermomechanical treatment. Journal of Materials Engineering and Performance. 2020. Vol. 29. Iss. 12, p. 7952-7963. DOI: 10.1007/s11665-020-05311-w
- Javidi M., Sadeghi M.A., Jafari R., Hoodib A.A. Failure analysis of an air-cooled heat exchanger in natural gas dehydration unit. Engineering Failure Analysis. 2020. Vol. 115, p. 689-701. DOI: 10.1016/j.engfailanal.2020.104678
- Fetisov V.G., Nikolaev A.K., Lykov Yu.V. Aggregative simulation method for implementing mathematical models for gas transmission systems. IOP Conferences Series: Materials Science and Engineering. 2018. Vol. 327. Iss. 2, p. 1-9. DOI: 10.1088/1757-899X/327/2/022033
- Fetisov V.G.,Nikolaev A.K., Lykov Yu.V. Experimental studies for determining gas flow rate accidental release on linear part of pipeline. IOP Conferences Series: Materials Science and Engineering. 2017. Vol. 87. Iss. 6, p. 1-7. DOI: 10.1088/1755-1315/87/6/062003
- Gorovei M.C., Benéa L. The effect of some key changes in the chemistry of water in relation to copper and brass corrosion control. Euroinvent ICIR 2018, 17-18 May 2018, Iasi, Romania. IOP Conference Series: Materials Science and Engineering, 2018. Vol. 374, p. 236-248. DOI: 10.1088/1757-899X/374/1/012057
- Hasan B.O.,Majdi H.Sh., Hathal M. Study on oil fouling in a double pipe heat exchanger with mitigation by a surfactant. Heat Transfer. 2020. Vol. 49. Iss. 5, p. 2645-2658. DOI: 10.1002/htj.21738
- Ifezue D. Investigation of failed coils from a steam boiler. Journal of Failure Analysis and Prevention. 2017. Vol. 17. Iss. 5, p. 825-830. DOI: 10.1007/s11668-017-0330-3
- Issa B., Bazhin V.Yu., Aleksandrova T.A. Increasing the corrosion resistance of tubular furnace elements at temperature range 400-700°C in accelerated testing for real operational conditions. Materials of the 12th Russian-German raw materials conference, 27-29 November, 2019, St. Petersburg, Russian Federation. CRC Press, 2020. Vol. 1, p. 174-185.
- Issa B., Bazhin V.Yu., Telyakov N.M., Telyakov A.N. Increasing the corrosion resistance of welded radiant and convection flexible pipes in tubular furnaces of the Kinef refinery. VI Youth Forum of the World Petroleum Council – Future Leaders Forum (WPF 2019), 23-28 June 2019, St. Petersburg, Russian Federation. CRC Press, 2019. Vol. 1, p. 243-249.
- Jakobi D., Karduck P. Behavior of high-temperature tube materials in sulfur-containing steam-cracking conditions. CORROSION 2018, 15-19 April 2018, Phoenix, Arizona, US. OnePetro, 2018. Vol. 2018, p. 6358-6371.
- Jarmai K., Szű R. Investigation of welded protective covers for heat treatment. Pollack Periodica. 2020. Vol. 15. Iss. 1, p. 15-26. DOI: 10.1556/606.2020.15.1.2
- Li F., Ning J., Liang S.Y. Analytical modeling of the temperature using uniform moving heat source in planar induction heating process. Applied Sciences. 2019. Vol. 9. Iss. 7, p. 24-36. DOI: 10.3390/app9071445
- Litvinenko V.S., Sergeev I.B. Innovations as a factor in the development of the natural resources sector. Studies on Russian Economic Development. 2019. Vol. 30. Iss. 6, p. 637-645. DOI: 10.1134/S107570071906011X
- Litvinenko V.The role of hydrocarbons in the global energy agenda: the focus on liquefied natural gas. Resources. 2020. Vol. 9. Iss. 5, p. 1-22. DOI: 10.3390/RESOURCES9050059
- Chen X., Zhou H., Zhang T. et al. Mechanism of interaction between the Cu/Cr interface and its chemical mixing on tensile strength and electrical conductivity of a Cu-Cr-Zr alloy. Materials & Design. 2019. Vol. 180. N 107976. DOI: 10.1016/j.matdes.2019.107976
- Pevzner M.Z., Khayutin S.G. Formation of structure, texture and properties and control of continuous induction heat treatment of brass strips. Metal Science and Heat Treatment. 2020. Vol. 62. Iss. 7-8, p. 534-539. DOI: 10.1007/s11041-020-00598-x
- Shi X., Shi Y. Corrosion fatigue cracking of tube coils in an actifier column catalytic cracker. Engineering Failure Analysis. 2003. Vol. 10. Iss. 3, p. 297-306. DOI: 10.1016/S1350-6307(02)00074-2
- Sedlak K., Bruzzone P., Rummel T., Nagel M. Study of the hot-spot temperature during quench in the non-planar coils of W7-X. IEEE Transactions on Applied Superconductivity. 2018. Vol. 28. Iss. 3, p. 27-36. DOI: 10.1109/TASC.2017.2779147
- Mori H., Kagaya H., Izumi S. et al. Suppression of heat generation in magnetic stimulation coil applied for treating dysphagia. Magnetic Society of Japan. 2019. Vol. 43. Iss. 4, p. 84-90. DOI: 10.3379/msjmag.1907R003
- Scheuerlein C., Lackner F., Savary F. et al. Thermomechanical behavior of the HL-LHC 11 Tesla Nb3SN magnet coil constituents during reaction heat treatment. IEEE Transactions on Applied Superconductivity. 2018. Vol. 28. Iss. 3, p. 45-57. DOI: 10.1109/TASC.2018.2792485
- Issa B., Bazhin V.Yu., Telyakov N.M., Telyakov A.N. The role of chloride, oxygen and aluminum on corrosion resistance of coiled-pipes in tubular furnaces of oil refinery. Quality Management and Reliability of Technical Systems, 20-21 June, 2019, St. Petersburg, Russian Federation. IOP Conference Series: Materials Science and Engineering, 2019. Vol. 666, p. 1-8. DOI: 10.1088/1757-899X/666/1/012027
- Yang Z., Si J. Study on influence of three kinds of stress on crack propagation in butt welds of spiral coil waterwall for ultra supercritical boiler. 2017 3rd International Conference on Applied Materials and Manufacturing Technology (ICAMMT 2017), 23-25 June, 2017, Changsha, China. IOP Conference Series: Materials Science and Engineering, 2017. Vol. 242, p. 1-9. DOI: 10.1088/1757-899X/242/1/012051
- Zyl van G., Al-Salmi A. Fitness-for-service assessment of externally corroded convection coil tube. American Society of Mechanical Engineers (ASME), 14-19 July, 2019, San Antonio, Texas, USA. 2019. Vol. 3, p. 181-192. DOI: 10.1115/PVP2019-93829