Обоснование рациональной конструкции исполнительного органа тоннелепроходческого щита для условий шахт Метростроя Санкт-Петербурга
Аннотация
В статье рассмотрены особенности проходки перегонных тоннелей в сложных горно-геологических условиях Метростроя Санкт-Петербурга с использованием современных тоннелепроходческих щитов компании Herrenknecht с гибридными исполнительными органами, оснащенными резцовым и шарошечным породоразрушающими инструментами. Проанализирована работа гибридного исполнительного органа при проходке по неоднородному забойному массиву, состоящему из кембрийской глины с прослойками известняка. Выполнены теоретические и экспериментальные исследования виброактивных шарошек, графическое представление зависимости глубины их внедрения от осевого усилия и осевого усилия совместно с прикладываемой ударной нагрузкой (зависимости глубины внедрения интерпретируются линейной зависимостью). Теоретически и экспериментально подтверждено повышение интенсивности разрушения неоднородного забойного массива, состоящего из кембрийской глины и прослоек известняка при использовании виброактивных породоразрушающих инструментов (шарошек), при этом рост скорости проходки определяется в зависимости от числа их параметров. Рассмотрена конструкция, описаны принцип работы и методика силового расчета роторного исполнительного органа, оснащенного виброактивными шарошками, на основании которой построена номограмма зависимости крутящего момента и производительности тоннелепроходческого щита от скорости подачи исполнительного органа на забой.
Введение
Для удобного и быстрого перемещения в городских условиях используется подземный железнодорожный транспорт – метрополитен. В крупных и современных городах насчитывается больше сотни станций метрополитена. Однако в быстроразвивающемся и застраивающемся Санкт-Петербурге их меньше – 72, что в первую очередь связано со сложными инженерно-геологическими условиями строительства.
Проходка выработок метро Санкт-Петербурга производится в осложненных инженерно-геологических условиях на глубинах от 15 до 70 м [2, 8, 9]. Забойный массив на таких глубинах отличается разнообразием пород. По мере увеличения глубины строительства меняется состав забойного массива от суглинков с включением гранитных гальки и валунов до кембрийской глины с прослойками известняков и песчаников (рис.1) [4].
Строительство метро начинается с ручной или механизированной проходки вертикальных шахтных стволов с последующим строительством околоствольных дворов с присущими им дополнительными выработками. Далее осуществляется строительство перегонных тоннелей, наклонных ходов и станций [12]. Для этих целей Метрострой применяет комплекс машин: стволопроходческий комбайн СПК-6; тоннелепроходческие механизированные комплексы КТ1-5,6, КТПМ-5,6 [21, 22], Herrenknecht S-782 и S-441 (для строительства наклонных ходов) [7, 19] (рис.2); тюбингоукладчики для проходки коротких специальных выработок [15, 26, 27]. Herrenknecht S-782 и S-441 являются наиболее современными машинами [16, 24].
Herrenknecht S-782 – тоннелепроходческий механизированный комплекс с активным грунтопригрузом забоя, предназначен для проходки двухпутных тоннелей диаметром 10,5 м в сложных горно-геологических условиях [3]. Учитывая сложность инженерно-геологических условий строительства Санкт-Петербургского метро, конструкторы компании Herrenknecht отдали предпочтение гибридному роторному исполнительному органу, оснащенному не только резцами, но и дисковыми шарошками [11, 13, 23].
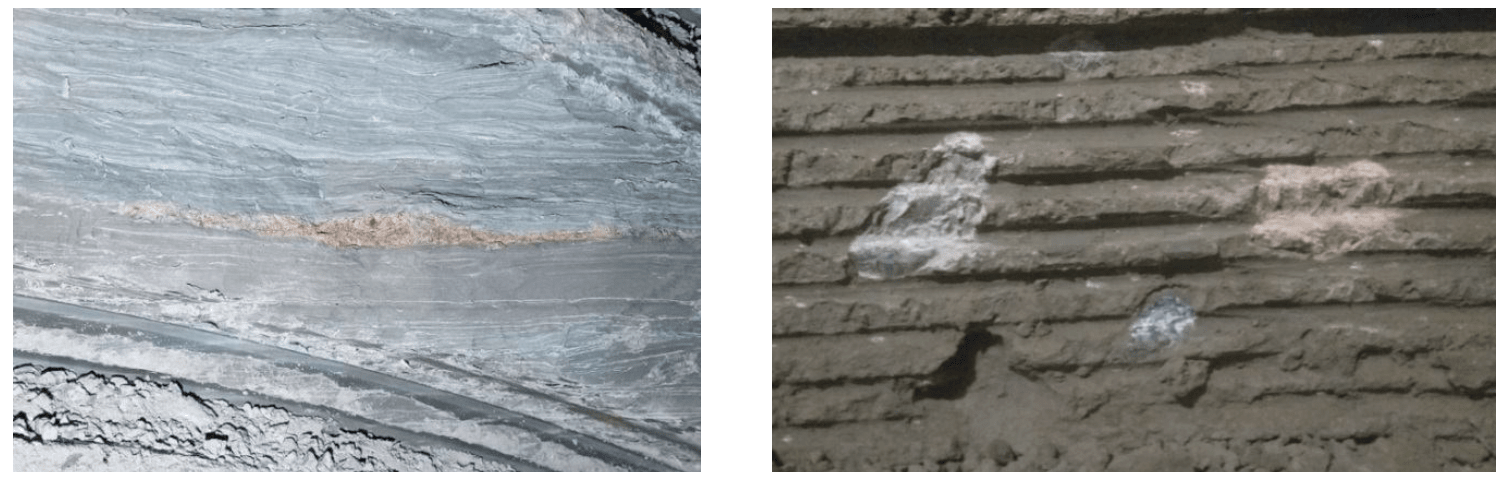
Рис.1. Прослойки известняка в глине, включения гранитных гальки и валунов
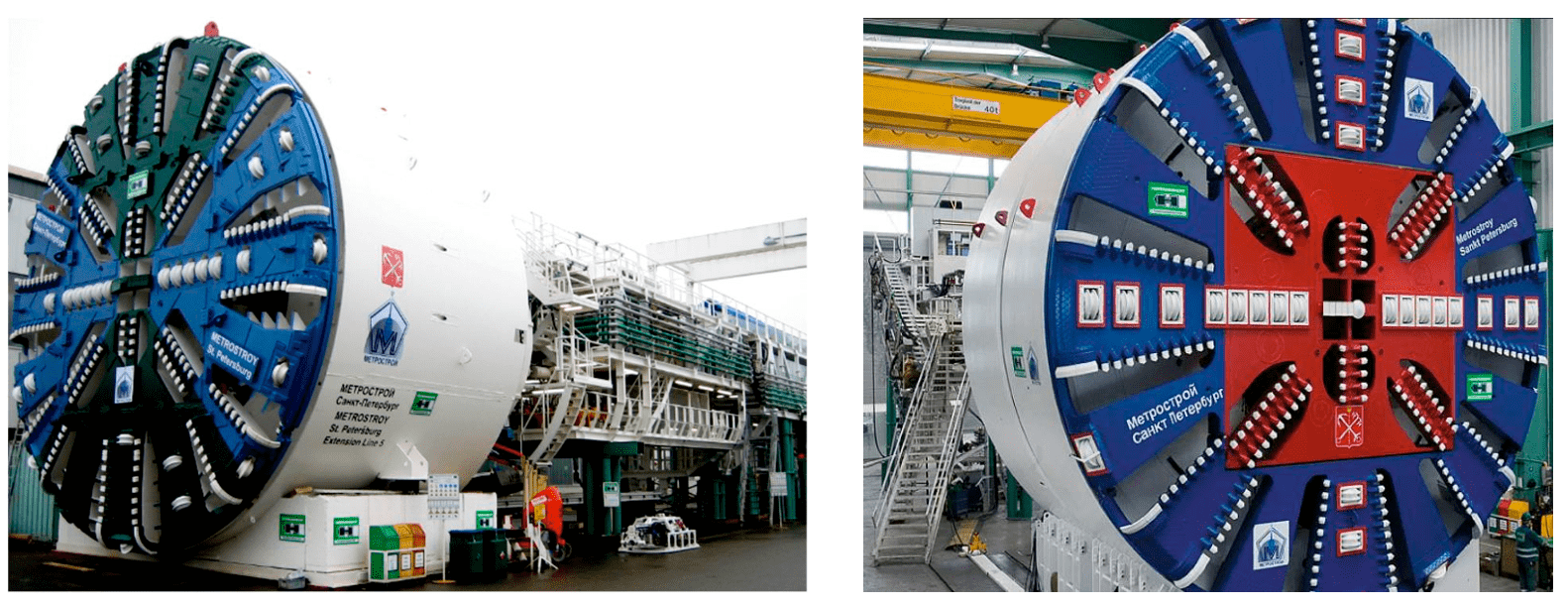
Рис.2. Тоннелепроходческие щиты Herrenknecht S-782 и Herrenknecht S-441
Во время проходки тоннеля по забою, состоящему из кембрийской глины с твердыми включениями, обладающими разными физико-механическими свойствами [14], была выявлена недостаточная эффективность работы роторного исполнительного органа тоннелепроходческого щита Herrenknecht S-782, которая заключалась в низкой эффективности разрушения неоднородного забоя, увеличении крутящего момента на исполнительном органе [5], быстром выходе из строя породоразрушающих инструментов и низкой скорости проходки. Поэтому задача создания исполнительного органа, способного с пониженной энергоемкостью осуществлять разрушение как однородного, так и неоднородного забойного массива без снижения скорости подачи, является особенно актуальной. Для этого нужно оснастить исполнительный орган тоннелепроходческого щита виброударными шарошками. В дальнейшем необходимо выполнить экспериментальные и теоретические расчеты нововведений.
Методология
Для повышения интенсификации разрушения забойного массива дисковыми шарошками [19, 20, 25] предлагается наложить на них ударную нагрузку, что увеличит глубину внедрения диска шарошки. Зная формулу для определения толщины срезаемой стружки роторным исполнительным органом (3), можно сделать вывод, что увеличение толщины срезаемой стружки увеличит скорость подачи исполнительного органа.
Для теоретического определения зависимости глубины внедрения шарошки в породу от осевого усилия используется формула
где R – радиус шарошки, мм; ƒ – крепость породы; α – угол заострения, град.; Рос – осевое усилие, кН; m – коэффициент трения металла шарошки о породу; kз – коэффициент затупления диска шарошки.
Для определения зависимости глубины внедрения шарошки в породу от прикладываемой ударной нагрузки применяется формула
где z – число лезвий; d – диаметр шарошки, м; σсж – предел прочности породы на сжатие, Па; Руд – ударная мощность, Вт; nуд – частота ударов, с–1.
Для определения зависимости глубины внедрения от осевого усилия с накладываемой ударной нагрузкой обратимся к правилу аддитивности.
В ходе проведенных расчетов было выявлено, что при наложении ударной нагрузки на дисковые шарошки прирост значения величины глубины внедрения диска шарошки в кембрийскую глину составил 27 %, а в известняк 40 %. Далее это необходимо проверить экспериментально: для исследований был спроектирован и изготовлен стенд (рис.3).
Экспериментальный стенд состоит из рамы 1 и подвижной рамы 6, на которую с помощью зажима 7 закреплен перфоратор 8 со штангой 5, шарошечной моделью 4 и центрирующей направляющей 3. Далее подвижная рама устанавливается в раму 1 над образцом породы 2. Сверху на подвижную раму, с целью изменения осевого усилия Рос, устанавливались сменные тарированные грузы.
Исследования проводились на образцах кембрийской глины и известняка, обладающих естественной влажностью 10 %. Для достижения достоверных результатов исследования проводились при 10-15 °С – естественной температуре разрушаемого забойного массива. Проведение исследований на образцах породы с меньшей влажностью (высушенных) повлияло бы на достоверность результатов из-за повышения трещиноватости и хрупкости породы.
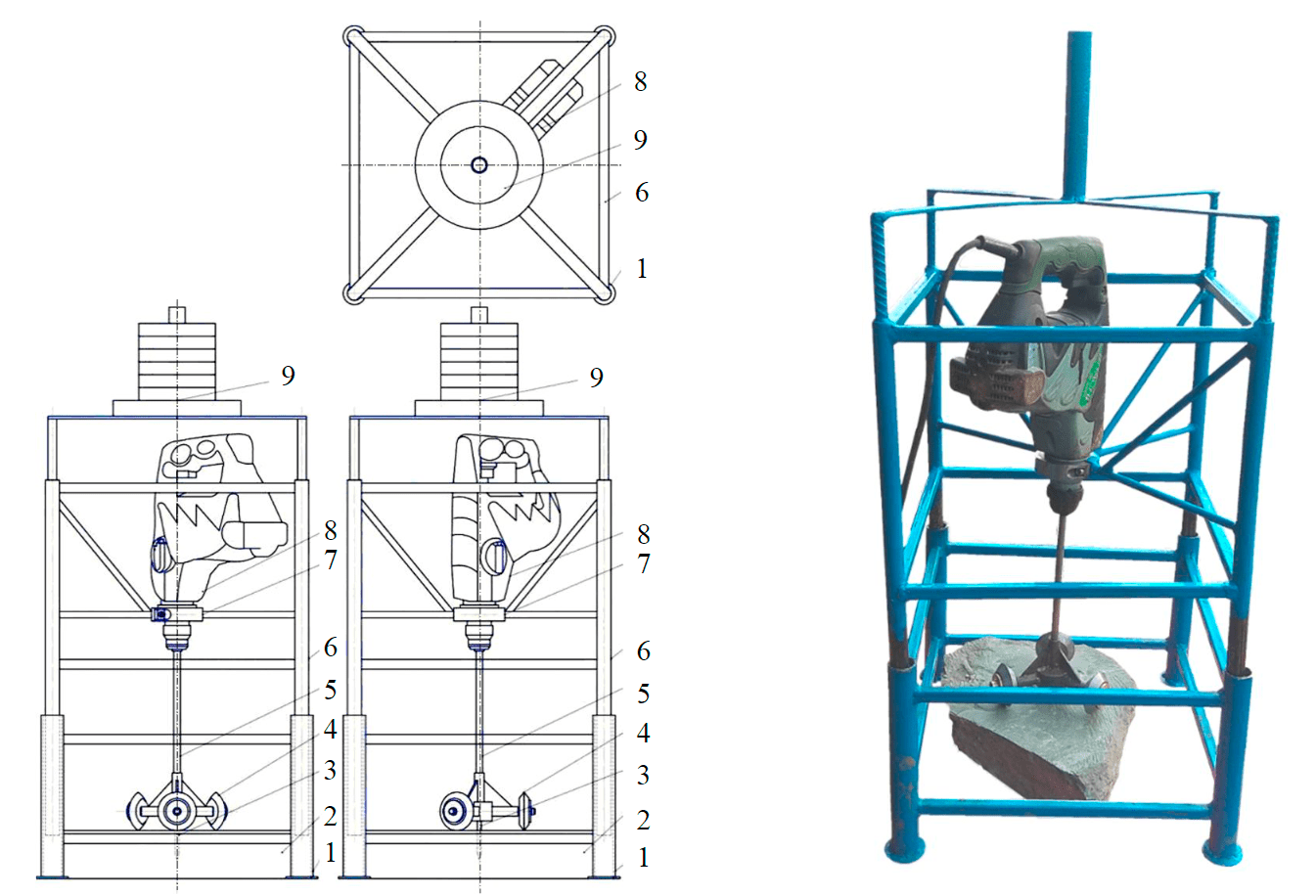
Рис.3. Эспериментальный стенд
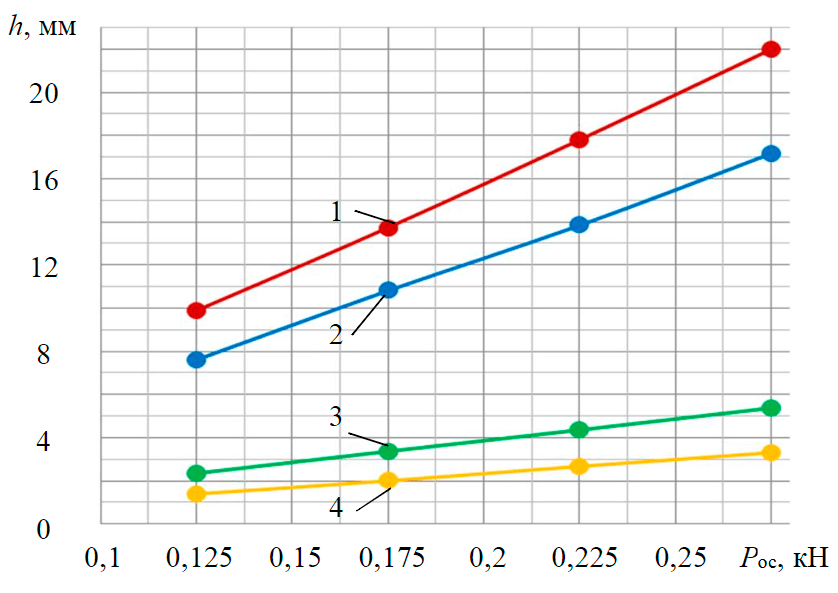
Рис.4. Зависимости глубины внедрения диска шарошек в образцы кембрийской глины и известняка от осевого усилия и осевого усилия совместно с наложением ударной нагрузки 1 – кембрийская глина (Рос + Ауд); 2 – кембрийская глина (Рос); 3 – известняк (Рос + Ауд); 4 – известняк (Рос)
Экспериментальные исследования проводились за отведенный временной интервал в двух режимах работы перфоратора: вращательном и вращательно-ударном. Замер глубины внедрения диска шарошек производился после каждого проведенного опыта в серии. По результатам экспериментальных исследований были построены зависимости (рис.4).
Проанализировав график, можно сделать вывод, что прирост глубины внедрения диска шарошки в образец кембрийской глины составил 22 %, а образец известняка – 39 %. При этом для комплексной оценки влияния пластового давления на глубину внедрения диска шарошки в породу возможно дальнейшее проведение экспериментальных исследований в забоях шахт.
Расхождение теоретических и экспериментальных значений величины глубины внедрения шарошек объясняется потерями энергии удара на возможные деформации в шарошечной модели. Можно сделать вывод, что модель разрушения образцов кембрийской глины и известняка виброударными шарошками хорошо описывает изучаемый процесс.
В дальнейшем была разработана конструкция виброактивной шарошки, устанавливаемой на роторный исполнительный орган тоннелепроходческого щита (рис.5).
Во время работы по разрушению кембрийской глины дисковые шарошки вдавлены в забойный массив. При наличии твердых включений или прослоек происходит отжатие шарошки 6 вместе с толкателем 3 в направляющей 10 в сторону, противоположную забою. Пружина 17, сцентрированная в кольцевых пазах 1, сжимаясь, позволяет снизить ударную динамику, возникающую при изменении физико-механических свойств разрушаемого забойного массива. В момент сжатия пружины 17 включается концевой датчик 13 и подает сигнал на включение генератору колебаний 18. Включение генератора 18 происходит только тогда, когда произошло отжатие шарошки от пластины 7. Таким образом, исключена возможность удара оси шарошки по фронтальной части ротора. Виброударные колебания от генератора колебаний 18 передаются на шарошку 6 через толкатель 3 и ось 4. В этот момент шарошка 6 совершает высокочастотные и низкоамплитудные возвратно-поступательные движения, тем самым разрушая твердые прослойки.
Существуют готовые решения генераторов колебаний с различными параметрами. Он представляет собой пневматический поршневой вибратор, выполненный в алюминиевом корпусе. Принцип работы заключается в том, что при подаче воздушного давления во впускное отверстие сжатый воздух толкает поршень, который в свою очередь наносит удар в основание корпуса. Оптимальные параметры генератора колебаний: n = 2500-3000 уд/мин, Ауд = 240-280 Дж.
Силовой расчет роторного исполнительного органа производится в следующей последовательности:
-
Определяется величина толщины срезаемой стружки, значение которой пропорционально скорости подачи исполнительного органа на забой [30, 32]:
где vп – скорость подачи исполнительного органа на забой, м/с; nио – частота вращения исполнительного органа, с–1; m – число резцов в линии резания (общее количество резцов, установленных на роторе, составляет 103 штуки, при этом 56 штук располагаются по четыре резца, 38 – по два резца и 9 – по одному резцу в линии резания).
-
Определяется сила резания на передней грани резца [17]:
где Рк – показатель контактной прочности породы, МПа; kα – коэффициент, учитывающий влияние угла резания; kb – коэффициент, учитывающий влияние ширины режущей кромки резца; t – шаг расстановки резцов, мм; μд – коэффициент трения движения резца о горную породу; Fср – средняя величина проекции площадки затупления резца по задней грани на плоскость резания, мм2.
-
Определяется крутящий момент, необходимый для разрушения забойного массива резцовым породоразрушающим инструментом:
где Pzрi – усилие на резце в группе расстановки резцов, кНм; ni – количество резцов в группе расстановки резцов (n1 = 9;n2 = 38;n4 = 56); Rсрi – средний радиус расстановки групп резцов (для группы расстановки резцов, в линии резания которых находится по одному резцу – Rср1= 1,1 м; по два резца – Rср2= 2,5 м; по четыре резца – Rср4= 4,15 м).
Для того, чтобы получить общее значение крутящего момента, необходимо просуммировать значения крутящих моментов групп расстановки резцов:
Аналогично рассчитываются значения усилий резания и крутящего момента, необходимые для разрушения забойного массива забурником и ковшами.
-
Определяется усилие перекатывания дисковых шарошек [10, 29]:
где s – шаг резания, мм; σр – предел прочности породы на растяжение, МПа; R – радиус диска шарошки, мм; T – ширина режущей кромки шарошки, мм; γ – угол контакта между инструментом и горной породой, рад.; ψ – коэффициент, описывающий функцию распределенной нагрузки (находится в пределах от –0,2 до 0,2, уменьшаясь по мере увеличения ширины режущей кромки).
Проведенные экспериментальные исследования показали, что наложение ударной нагрузки на породоразрушающий инструмент не приводит к существенному увеличению силы на нем, поэтому значение усилия перекатывания виброактивных шарошек будет соответствовать значению усилия перекатывания дисковых (Pzвибр = Pzдиск).
-
Определяется крутящий момент на шарошечном породоразрушающем инструменте [1, 28, 31]:
где n – количество шарошек; Rср – средний радиус расстановки шарошек, м.
-
Определяется крутящий момент, идущий на разрушение горной породы породоразрушающими инструментами. Для этого необходимо просуммировать крутящие моменты от резцов, ковшей, забурника, шарошек:
-
Определяется производительность тоннелепроходческого щита [6]:
где Rщ – ра (10)диус щита, м.
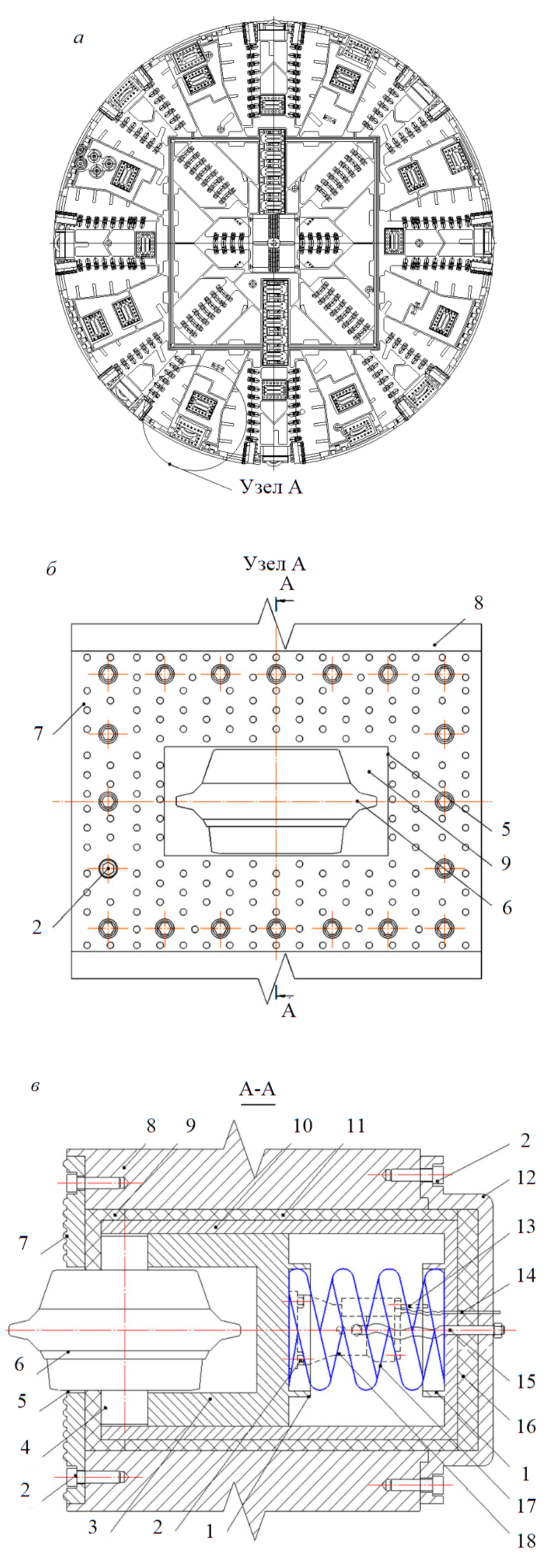
Рис.5. Общий вид исполнительного органа (а), конструкция виброактивной шарошки (б, в)
На основе произведенного расчета основных силовых показателей исполнительного органа была построена номограмма (рис.6).
При работе проходческого щита основными факторами, ограничивающими скорость подачи исполнительного органа на забой, являются номинальное значение крутящего момента и скорость выдачи отработанной породы из призабойного пространства. Таким образом, исполнительный орган щита, вооруженный резцами и шарошками при проходке по забою, состоящему из глины, будет обладать скоростью подачи 0,0007 м/с (точка А'), которая ограничена представленными ранее факторами. При этом значение теоретической производительности составит 5388 м3/сут (точка А''), что соответствует скорости проходки 21,4 м/сут.
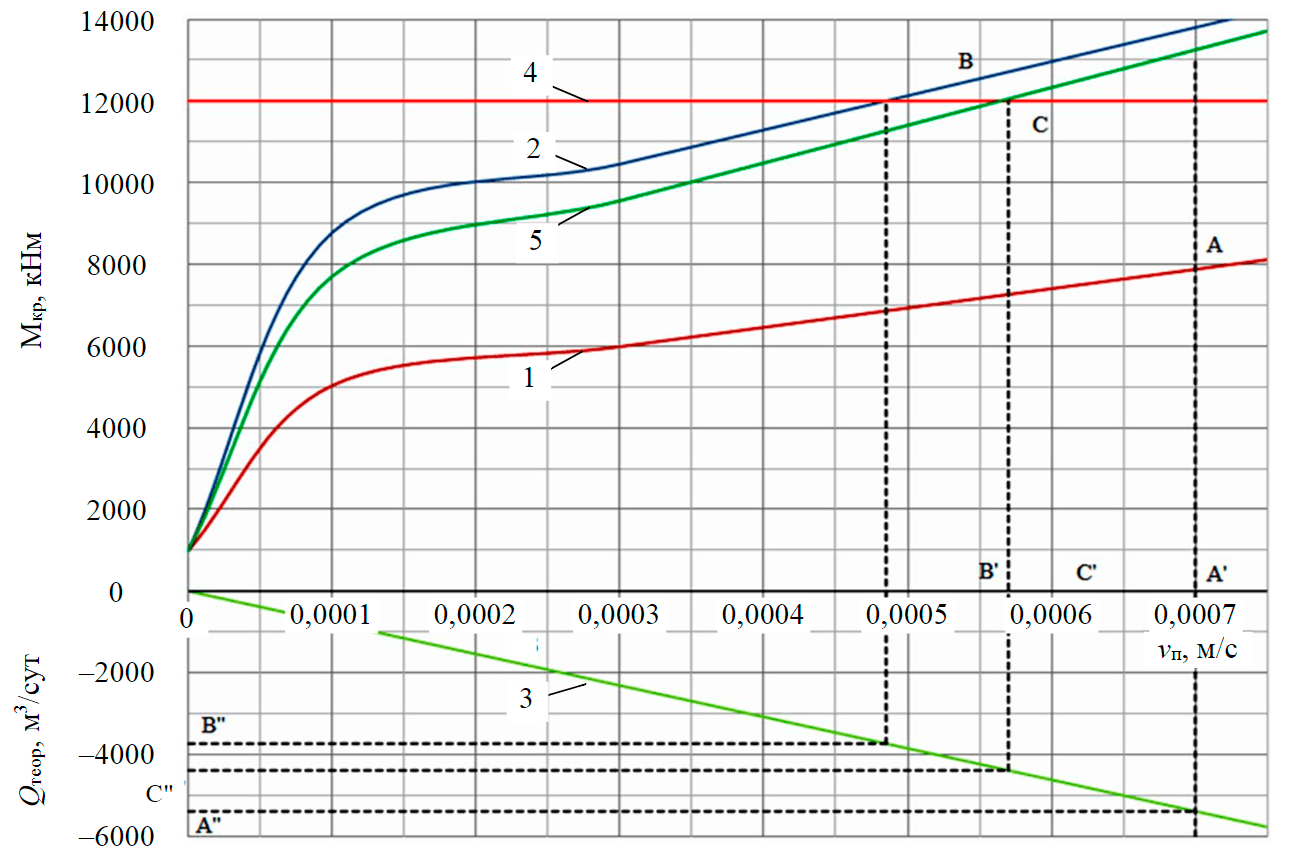
Рис.6. Номограмма зависимости крутящего момента и производительности от скорости подачи исполнительного органа 1 – кембрийская глина; 2 – кембрийская глина с прослойкой известняка; 3 – производительность; 4 – Мном; 5 – кембрийская глина с прослойкой известняка (разрушение виброактиными шарошками и усовершенствованная схема резания)
При работе исполнительного органа проходческого щита по комбинированному забою, состоящему из глины с прослойками известняка толщиной до 1 м, скорость подачи будет равна 0,000485 м/с (точка В') и ограничена номинальным крутящим моментом (точка В), составляющим 12000 кНм. Это связано с возросшими значениями усилий на резцах и, как следствие, ростом крутящего момента, связанных с изменением физико-механических свойств разрушаемого массива. При такой скорости подачи значение теоретической производительности будет составлять 3733 м3/сут (точка В"), или 16,4 м/сут – скорость проходки.
Усовершенствовав ротор установкой виброактивных шарошек, толщина срезаемой стружки, как и скорость подачи исполнительного органа на забой, увеличатся в 1,3 раза. При этом значение скорости подачи будет ограничиваться номинальным крутящим моментом (точка С) и составит 0,00057 м/с (точка С') со значением теоретической производительности 4387 м3/сут (точка С"), или скоростью проходки 19,7 м/сут.
Заключение.
Для оптимизации процесса разрушения смешанного забойного массива в горно-геологических условиях шахт Метростроя Санкт-Петербурга предложена запатентованная конструкция роторного исполнительного органа тоннелепроходческого щита, оснащенного виброактивными шарошками.
В ходе проведенных теоретических и экспериментальных исследований была выявлена линейная зависимость повышения значения глубины внедрения дисковых шарошек в образцы породы при наложении на них ударной нагрузки, причем для кембрийской глины увеличение составило 22 %, для известняка – 39 %.
Силовой расчет роторного исполнительного органа и производительности тоннелепроходческого щита показал повышение скорости проходки тоннеля неоднородным забойным массивом, состоящим из кембрийской глины и прослоек известняка в горно-геологических условиях шахт Метростроя Санкт-Петербурга на 30 % при установке разработанных виброактивных шарошек.
Помимо увеличения скорости проходки установка виброактивных шарошек позволит существенно снизить изнашивание породоразрушающих инструментов. Поэтому в дальнейшем необходимо исследовать и провести производственные испытания надежности и ремонтопригодности разработанной конструкции.
Литература
- Аверин Е.А. Зарубежный опыт использования клиновидных дисковых шарошек при оснащении тоннелепроходческих щитов // Горные науки и технологии. 2018. № 4. С. 41-50. DOI: 10.17073/2500-0632-2018-4-41-50
- Александрова О.Ю. Проблемы освоения подземного пространства Санкт-Петербурга и геологические процессы // Записки Горного института. 2008. Т. 176. С. 209-212.
- Будников В.Б. Математическое описание динамики щита тоннелепроходческого комплекса // Известия Тульского государственного университета. Технические науки. 2012. Вып. 11. Ч. 1. С. 194-198.
- Вербило П.Э. Оценка рисков при разработке проекта тампонирования затопленных тоннелей / П.Э.Вербило, Е.И.Кабанов // Горный информационно-аналитический бюллетень. 2017. № S5-2. С. 25-33.
- Влияние формы корпуса рабочего органа горного комбайна на нагруженность дискового инструмента / А.Ю.Борисов, А.А.Хорешок, Л.Е.Маметьев, А.М.Цехин // Горное оборудование и электромеханика. 2016. № 6 (124). С. 30-37.
- Выбор и расчет рабочего органа тоннельной щитовой машины с активным пригрузом забоя / А.В.Поляков, А.Б.Жабин, П.Н.Чеботарев, В.Г.Хачатурян // Известия Тульского государственного университета. Науки о земле. 2019. Вып. 4. С.139-149.
- Гигиняк И.Е. Сооружение наклонного хода станции метрополитена с помощью ТПМК фирмы «Херренкнехт» в Санкт-Петербурге // Метро и тоннели. 2009. № 5. С. 4-5.
- Дашко Р.Э. Влияние гидрогеологических условий на безопасность освоения подземного пространства при строительстве транспортных тоннелей / Р.Э.Дашко, П.В.Котюков, А.В.Шидловская // Записки Горного института. 2012. Т. 199. С. 9-16.
- Дашко Р.Э. Инженерно-геологическое обеспечение эксплуатационной надежности подземных транспортных сооружений в Санкт-Петербурге / Р.Э.Дашко, П.В.Котюков // Записки Горного института. 2011. Т. 190. С. 71-77.
- Жабин А.Б. Сопоставление отечественных и зарубежных методов расчета усилий на лобовых дисковых шарошках при разрушении горных пород / А.Б.Жабин, А.В.Поляков, Е.А.Аверин // Горный журнал. 2018. № 12. С. 65-68. DOI: 10.17580/gzh.2018.12.13
- Задков Д.А. Особенности формирования элементарных сколов в процессе резания углей и изотропных материалов эталонным резцом горных машин / Д.А.Задков, В.В.Габов, К.Л.Нгуен // Записки Горного института. 2019. Т. 236. С. 153-161. DOI: 10.31897/PMI.2019.2.153
- Карасев Е.А. Особенности работы сборных обделок транспортных тоннелей // Записки Горного института. 2010. Т. 185. С. 180-183.
- Каркашадзе Г.Г. Исследование процесса разрушения пород дисковыми шарошками / Г.Г.Каркашадзе, А.В.Бабич // Горный информационно-аналитический бюллетень. 2017. № 1. С. 109-116.
- Коршунов В.А. Новый способ определения предела прочности при растяжении горных пород / В.А.Коршунов, Ю.М.Карташов // Записки Горного института. 2011. Т. 190. С. 202-206.
- Лавренко С.А. Исследование процесса разрушения кембрийских глин резанием при проходке выработок метро Санкт-Петербурга / С.А.Лавренко, И.А.Королев // Горный журнал. 2018. № 2. C. 53-58. DOI: 10.17580/gzh.2018.02.08
- Механизированная проходка тоннелей в городских условиях. Методология проектирования и управления строительством / В.Гульелметти, П.Грассо, А.Махтаба, Ш.Сю. СПб: Изд-во Политехнического университета, 2013. 602 с.
- Основы проектирования исполнительных органов тоннелепроходческих машин / А.Б.Жабин, А.В.Поляков, Е.А.Аверин, Ю.Н.Линник // Горный информационно-аналитический бюллетень. 2019. № 6. С. 156-164.
DOI: 10.25018/0236-1493-2019-06-0-156-164 - Основные этапы разработки и моделирования параметров дискового инструмента проходческих и очистных горных машин / А.А.Хорешок, Л.Е.Маметьев, А.М.Цехин и др. // Горное оборудование и электромеханика. 2015. № 7 (116). С. 9-16.
- Практика внедрения безосадочных технологий при строительстве Санкт-Петербургского метрополитена / К.П.Безродный, А.И.Салан, В.А.Маслак и др. // Записки Горного института. 2012. Т. 199. С. 190-195.
- Прейс Е.В. Моделирование образования объема крупных элементов при разрушении угля дисковой шарошкой / Е.В.Прейс, В.В.Кузнецов // Горное оборудование и электромеханика. 2015. № 7 (116). С. 37-41.
- Расчет роторного исполнительного органа тоннелепроходческого механизированного комплекса КТПМ-6.0 / А.Б.Жабин, Ан.В.Поляков, Ал.В.Поляков и др. // Горное оборудование и электромеханика. 2012. № 4. С. 26-32.
- Совершенствование работы исполнительного органа проходческого щита КТ1-5,6М / Д.Г.Лукин, Д.А.Юнгмейстер, А.И.Ячейкин, А.И.Исаев // Горный журнал. 2018. №12. С. 73-77. DOI: 10.17580/gzh.2018.12.15
- Состояние научных исследований в области разрушения горных пород резцовым инструментом на рубеже веков / А.Б.Жабин, А.В.Поляков, Е.А.Аверин, В.И.Сарычев // Известия Тульского государственного университета. Науки о Земле. 2018. № 1. С. 230-247.
- Схема расстановки резцов на шнековых исполнительных органах с подрезными, парными и групповыми срезами/ В.В.Габов, В.С.Нгуен, Д.А.Задков и др. // Горный информационно-аналитический бюллетень. 2020. № S4. С. 3-14. DOI: 10.25018/0236-1493-2020-1-4-3-14
- Хорешок А.А. Прогнозирование максимального объема разрушенного материала дисковым инструментом / А.А.Хорешок, В.В.Кузнецов, А.Ю.Борисов // Горный информационно-аналитический бюллетень. 2011. № 9. С. 299-304.
- Шишлянников Д.И. Оценка нагруженности приводов комбайнов «Урал-20Р» при двухстадийной разработке забоя / Д.И.Шишлянников, М.Г.Трифанов, Г.Д.Трифанов // Записки Горного института. 2020. Т. 242. С. 234-241. DOI: 10.31897/PMI.2020.2.234
- Lavrenko S. Test results for hydraulic drives of sucker-rod pumping units / S.A.Lavrenko, I.Klushnik, V.Iarmolenko // ARPN Journal of Engineering and Applied Sciences. 2019. Vol. 14. № 16. P. 2881-2885.
- Li F.H. A Theoretical Model for Estimating the Wear of the Disc Cutter / F.H.Li, Z.X.Cai, Y.A.Kang // Applied Mechanics and Materials. 2011. Vol. 90-93. P. 2232-2236. DOI: 10.4028/www.scientific.net/AMM.90-93.2232
- Rostami J. Study of pressure distribution within the crushed zone in the contact area between rock and disc cutters // International Journal of Rock Mechanics and Mining Sciences. 2013. Vol. 57. P. 172-186. DOI: 10.1016/j.ijrmms.2012.07.031
- Shishlyannikov D.I. Investigation of the destruction process of potash ore with a single cutter using promising cross cutting pattern/ D.I.Shishlyannikov, I.E.Zvonarev // Applied Sciences. 2021. Vol. 11. Iss. 1. P. 1-11. DOI: 10.3390/app11010464
- Tumac D. Investigations into the cutting characteristics of CCS type disc cutters and the comparison between experimental, theoretical and empirical force estimations / D.Tumac, C.Balci // Tunnelling And Underground Underground Space Technology. 2015. Vol. 45. P. 84-98. DOI: 10.1016/j.tust.2014.09.009
- Zhabin А. Scale factors for conversion of forces on disc cutters for the main domestic and foreign methods / А.Zhabin, А.Polyakov, Е.Averin // Mining of Mineral Deposits. 2017. Vol. 11. Iss. 3. P. 50-55. DOI: 10.15407/mining11.03.050