Analysis of the screw press mouthpiece parameters for 3D extrusion of peat pieces of tubular type
- 1 — Ph.D., Dr.Sci. Professor Saint Petersburg Mining University ▪ Orcid ▪ Elibrary ▪ Scopus ▪ ResearcherID
- 2 — Postgraduate Student Saint Petersburg Mining University ▪ Orcid
Abstract
The results of theoretical and experimental studies on the creation of a screw press composite mouthpiece screw press for 3D-forming of peat pieces of a tubular type in the field for intensifying the process of field drying of material in a complex mechanized pit are presented. The main purpose of the study was to substantiate the geometric and design parameters of the screw press composite mouthpiece of the spread machine for the production of peat-agglomerated products of the tubular type. The parameters of the mouthpiece are selected based on the geometric characteristics of the peat pieces. An increase in moisture loss during drying of peat-agglomerated products is provided by forming a peat piece in the form of a thick-walled pipe made of a peat raw materials composed of low and high decomposition degrees in a ratio of 1:3. Additive production of polymer-fiber peat composites by extrusion allows to produce products with improved mechanical properties in comparison with non-reinforced raw materials. The vertical arrangement of the peat tubular piece on the drying field allows to increase the loading of the field area by 10 %, increase the convective heat supply to the piece and reduce the contact coefficient of the piece with the field by three times in comparison with the peat spreading of the pieces in the form of a horizontal tape. Based on the analysis of the shape and size of the agglomerated products, the design of a screw press composite mouthpiece consisting of two conditional molding zones of various configurations has been developed. The article presents a parametric analysis of the volumetric productivity of a screw press with a composite mouthpiece of a tubular type, the energy intensity of mechanical processing is determined, the degree of mechanical processing of peat raw materials is estimated with the optimization of the screw parameters for the production of agglomerated products of a tubular type.
Introduction
Widely used technologies and corresponding mining machines for the extraction and processing of organogenic raw materials in modern economic conditions have become ineffective, and their operation is extremely expensive, which poses the task of creating highly efficient and multipurpose machines for the production and high-quality extraction and processing of peat raw materials to the mining industry.
The period of formation of the sustainable peat industry development in Russia is coming to an end, in which peat-producing companies become part of vertically integrated holdings focused on the production of the final product based on peat raw materials: energy, composite materials, food, etc. [8, 9, 11]. The main idea of the industry development is to create the prospective technological processes for the field production of agglomerated peat products with a reasonable choice of a rational complex of technological equipment, the main design and operational parameters of the equipment, with the provision of a given product quality in the conditions of pit mining [2, 24].
In order to develop the peat industry in Russia, the evolution of extraction methods [7, 10] of peat agglomerated products and the modernization of technological equipment is of particular interest [23, 43]. Thus, a prospective technological process for obtaining agglomerated peat products can be performed using a hydraulic excavator, a spread machine in an aggregate with a tractor [38] and a machine for collecting dried agglomerated products. The main feature of the technological process is the mechanical processing of peat mass and its forming into volumetric figures for drying.
The technology of Additive manufacturing (AM) was introduced in the late 1980s. Since that time, many review articles have been published on the methods and materials of AM [46]. The most common and studied materials are plastics, metal, ceramic masses [28], polymers and various composites [41]. Additive production of polymer-fiber composites by extrusion allows to release the products with significantly improved mechanical properties compared to non-reinforced polymers [41].
Methods including extrusion based on plastic pastes (clay, peat raw materials) [3, 37] are most common in industry due to their low cost [42]. The technology of sequential layering of paste on the formed beam, used in the production of agglomerated peat products, is characterized by low capital investment and high speed. The thickness of the compacted material attached to the infinite beam in the extruder is fixed for each piece by separating it from the beam along the z axis, and a solid 3D body formed by the translational movement of the cross-section of the beam is created as a result of breaking it off from the beam and falling with a 90° rotation along the z axis, due to the interpolation of the x axis.
The length of the piece depends on the ratio of the extrusion speeds and the translational movement of the machine along the x axis. The kinematic variables of the process are set by the parameters during the translational movement of the machine and can be accurately performed. The extrusion flow varies depending on the rheological properties of peat raw materials and its behavior in the extrusion device (screw press with a mouthpiece).
It should be noted that the uniformity of the extruded piece is determined by the adhesion of the layers of the new material with the previous one due to adhesion during deformation. Plasticity in the processing of materials based on peat raw materials is a fundamental property, since it determines the technical parameters for converting the peat mass into a 3D shape of a given form by applying pressure. The method based on a screw extruder has high reliability, dimensional stability in a continuous process, and parts printed using the method based on a screw extruder have a higher density [29]. The 3D printing process is only a forming procedure, which includes many stages on the way to preparing for the final parts, with an emphasis on improving the forming mechanism [45].
The shape and size of the extruded piece should be determined in order to maximize the use of the weather conditions of the mining season with the specified physical and mechanical properties of the agglomerated products. The dimensional accuracy and surface quality of additive manufacturing technologies are not key characteristics in this case [44].
The intensity and duration of drying of peat pieces is determined by soil and natural factors (the degree of decomposition, the structure of peat raw materials), meteorological conditions (temperature, humidity, wind speed, precipitation), as well as technological factors, the shape and size of the agglomerated peat products, the location of the piece on the drying field, the intensity of the impact of the forming mechanisms of the press on the peat mass.
The agglomeration of peat raw materials into volumetric large-sized hollow 3D figures by extrusion in the screw press of a spread machine for the intensification of subsequent drying allows to reduce the production time of peat agglomerated products, expand the production season due to the effective use of radiation-convective heat supply during the drying process, and also, while reducing the cost of production, increase the production reliability. The use of mobile screw machines makes it possible to make the process of 3D-forming of the agglomerated products continuous and controlled.
The advantages of press extruders are ease of use, the absence of reciprocating (inertial) forces and the associated reduction in metal consumption, the absence of idling, a wide range of changes in the physical and mechanical properties of the processed materials and the degree of impact on them [13]. However, the functional features of an extruder with a composite mouthpiece in combination with a void-forming device have not been sufficiently studied, the rational design parameters of the mouthpiece sections have not been determined.
The purpose of the work is to carry out a parametric analysis of the compaction of a mechanical mixture of elastic-visco-plastic peat raw materials in a single-screw extruder and to substantiate the design and geometric parameters of the screw press mouthpiece of a spread machine for the production of 3D-agglomerated tubular products with increased moisture loss when drying pieces in an upright position directly in a complex mechanized pit, which is essential for the peat industry development of the country.
Materials and methods
Often peat massifs of natural occurrence have a powerful upper layer of poorly decomposed peat. The process of enriching peat raw materials directly during its excavation with an excavator shovel is of practical interest [6]. In this case, the extraction of peat raw materials occurs from the entire depth of the deposit by cutting the blade of the shovel the chips from the slope of the pit. The stratigraphy of the peat deposit in the shovel revealed a mixture of peat raw materials of both low and high degrees of decomposition – a polymer-fiber composite. The processes of enrichment, mixing and dispersion cause significant changes in the structure of excavated peat raw materials, which is associated with a change in the content of the highly dispersed component in the enriched raw materials, as well as with the peculiarities of the distribution of elements of such compositions in the excavated mixture. The physical nature of the process of peat raw materials dispersion under the influence of angular shear deformations is estimated by the degree of processing effect of mechanical devices on the material λ [5].
To carry out the research, raw materials were selected from the Rohali peat deposit (cadastral number 491). The subsurface area is located 3 km south-west from the Firovo village, 0.6 km south-east of the Korolevo village, Firovskiy district of the Tver region. During the measurement of the peat raw materials humidity on the AND MF-50 analyzer, it was determined that the initial humidity was w = 85.8 % (moisture content of 6.04 kg/kg). At a humidity of 84-86 %, the processed peat raw material comes to a state close to two-phase [34].
The study of the rocks microstructure features is closely related to the assessment of the representativeness of the considered small areas of the medium in relation to the volume of the medium of interest as a whole. The mixture consists of compositions of peat raw materials of low (filler) and high (matrix) degrees of decomposition. During the mixing process, peat fibers of a low degree of decomposition (magellanicum) are bound in a matrix of peat of a high degree of decomposition (cotton grass-sphagnum). With this composition of the polymer-fiber peat mixture, the agglomerated products are obtained in the required specified shape, and the loads exerted on the matrix are redistributed to the filler [33].
Under shear loads, the strength characteristics of the matrix material are decisive. The matrix material must be plastic and have a high contact strength (adhesive strength) with the filler surface. Hardening, crack resistance, and shape preservation of the agglomerated 3D products are obtained at a ratio of binder and filler ~75:25 % [19].
The study of the statistical geometric properties of the pore space surface plays an important role among the tasks of microstructural analysis of porous materials. Assuming the complex and irregular nature of the pore geometry of rock materials, it is necessary to use fractal geometry [23].
The fractal dimension analysis by processing photo images of the surface confirmed the data of the study of the structure of two peat raw materials types mixtures: the strength of the resulting agglomerated peat products will be maximum for surfaces with a multifractal dimension D = 2.6 at a ratio of the components of the mixture of 1:3 [34, 35]. For such a mixture, the spatial framework is fragmented, and the particles of poorly decomposed peat are tightly compressed by the medium of highly decomposed peat (Fig.1).
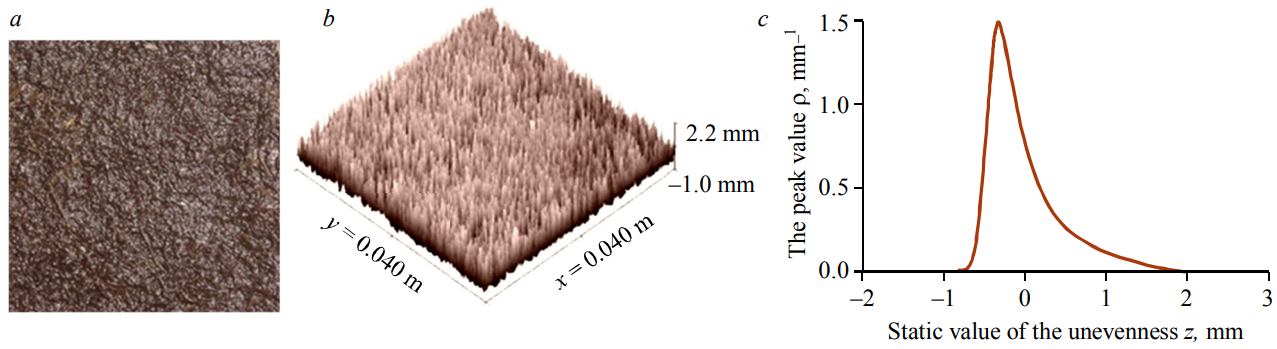
Fig.1. The results of the analysis of the fractal dimension of the sample surface (resolution 1200 ´ 1200 px) (а), three-dimensional view of the surface unevenness (b), the distribution of the height of the surface unevenness of the material (c)
Based on the analysis of the porosity determination and the fractal dimension analysis, it was determined that with the ratio of the components of the mixture of peat raw materials of a low to a high degree of decomposition within 25:75 %, the structure of the piece is formed that meets the high physical and mechanical characteristics of the agglomerated products. Subsequent laboratory studies were carried out at this ratio of the components of the peat raw materials mixture.
Analysis of the shape and size of agglomerated peat products
According to studies [32], in the surface layer on the drying field in the pit conditions, the wind speed is 0.2-0.5 m/s, and no more than 1 % of wind energy is used when drying peat-agglomerated products. Accordingly, for a more complete use of meteorological conditions in the process of drying peat agglomerated products, it is necessary to use not only radiation heat supply, but also the energy of convective heat supply.
It is known that drying of agglomerated products in the field is effective with a maximum reduction in moisture content and internal stresses in the body of the piece at a rational depth of the evaporation zone (hez). The optimal condition is considered when the outer diameter (wall thickness of the piece) does not exceed 30-40 mm [1], moisture evaporation occurs from the entire volume of the piece.
Parametric analysis of the shape and size of the agglomerated products [20] showed that for the drying process intensification of peat agglomerated products, the rational form is a thick-walled pipe with an outer diameter Ds = 0.18 m with a hole ds = 0.10 m with a wall thickness of 0.04 m and a height of Ls = 0.25 m. Figure 2 shows a diagram of a tubular peat piece and a sample obtained under laboratory conditions on an experimental screw press M-2.
The analysis of the wind impact degree showed that when the height of the 3D shape of the piece is more than 0.24 m, the wind speed can increase by 35-40 % [32] to 2 m/s, due to an increase in wind speed, the drying speed can increase due to the use of wind energy.
When drying agglomerated peat products, the decisive indicator is the specific area of the piece Ssa, the value of which is the inverse of the characteristic size of the piece. With the increase in the specific surface area of the piece, the intensity of the drying process increases. Analysis of the location of the piece on the drying field [21] showed that to ensure good ventilation of the pieces by increasing the area of convective heat supply, the preferred location of the tubular piece on the drying field is vertical.
Laboratory studies of natural drying of peat tubular pieces in a vertical position and drying of standard pieces in the form of a lined tape in a horizontal position (Fig.3) showed that the drying rate to a conditional humidity of 62 % (Wp = 1.63 kg/kg) is Tc1 = 41 h for a tubular piece and Tc2 = 54 h for a solid piece, which indicates a drying process intensification of the agglomerated products depending on the shape and location of the piece [21].
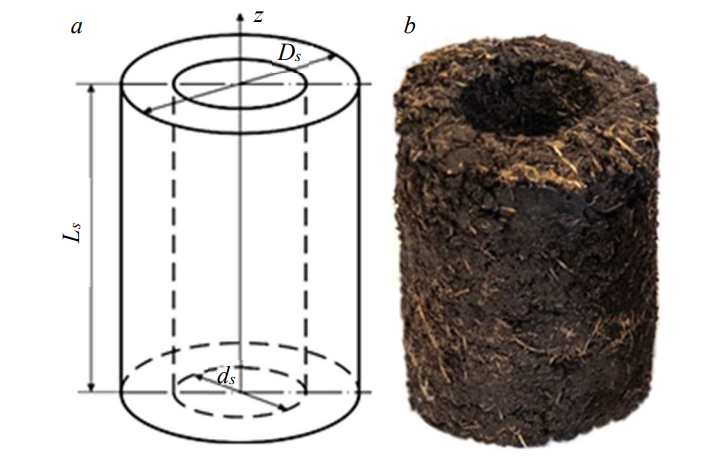
Fig.2. Diagram of a tubular peat piece (a), a laboratory sample obtained from a mixture with a component ratio of 1:3 (b)
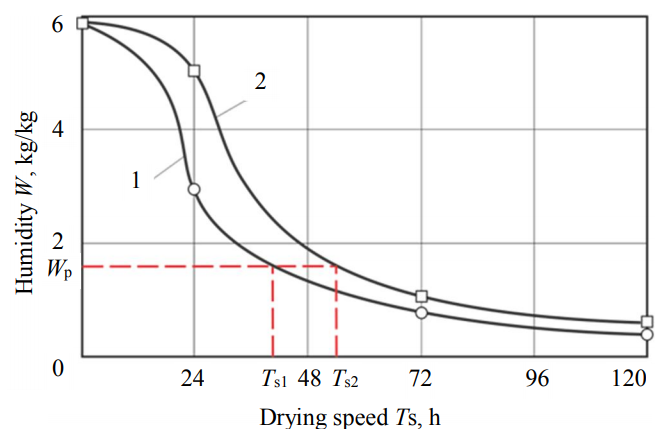
Fig.3. Change in the moisture content of peat pieces during drying 1 – tubular; 2 – solid
The drying time [9] of vertically arranged tubular pieces is reduced by 24 % compared to the drying time of solid pieces in a horizontal position on the drying field, other things being equal.
Based on the selected geometric dimensions of the piece, it was determined that the vertical laying of peat tubular pieces allows increasing the loading of the field area with products by 10 %. During the drying process in the field, when precipitation falls, the drying field is moistened, as a result of which additional time is required for drying the agglomerated products to remove the water absorbed by the peat. As part of a comparative analysis of the contact areas of a piece with a wet base, it was determined that the contact area of a tubular piece with a wet base will decrease by three times in comparison with a horizontal spreading of pieces in the form of a tape. Reducing the contact area with a wet base reduces the moisture exchange with the underlying deposit and reduces the drying time of the agglomerated peat products [1].
The pit production cycle of agglomerated peat products consists in the sequential execution of a number of basic operations: excavation of peat raw materials with a shovel from the pit slope to the full depth of the deposit with loading into the hopper of a spread machine; transportation of excavated peat raw materials [16, 17]; forming of peat raw materials into tubular pieces and laying them on the surface of the field; drying of agglomerated peat products, as a result of which excess moisture [36] from the agglomerated products evaporates into the atmosphere; cleaning, the task of which is to release the drying field from the dried peat products for the next cycle, and stacking the agglomerated peat products.
The analysis of the drying process shows that the maximum decrease in moisture during the production of agglomerated peat products falls on the drying process in the field. One of the factors affecting the drying process and the quality of the agglomerated peat products is the mechanical processing of peat raw materials in a pressure screw press with a forming mouthpiece. The analysis of forming mechanisms for the agglomerating of peat raw materials in the field [33] showed that single-screw mechanisms with continuous forming of a peat piece have become the most widespread. The shapes and sizes of the forming mechanisms are determined by a set of requirements for the final agglomerated peat products: the drying conditions of the piece, the cross-section, density, strength.
To determine the optimal characteristics of the former of agglomerated peat products, it is necessary to study its design, volume capacity and the degree of mechanical processing directly in the mouthpiece of the former.
Based on the analysis of the shape and size of the agglomerated peat products, drying conditions, the location of the piece on the field and laboratory studies of the natural drying of agglomerated peat products in order to intensify the drying process and forming of peat tubular pieces, the design of the composite screw press mouthpiece of the spread machine was developed [12].
Results and discussion
Analysis of the design of a screw press with a composite mouthpiece
As part of the single-screw press analysis, the following were determined: the design and kinematic parameters of the screw; the highest pressure developed by the screw; the maximum and useful power for the operation of the screw press; the degree of mechanical processing of peat raw materials during forming; the efficiency of the screw for the selected length and diameter of the screw at a constant step of turns. The design analysis of the screw press was carried out taking into account the accepted assumptions that the angular screw velocity and the productivity of the screw press are constant. The model of the screw press mouthpiece was analyzed based on the assumption of a piston flow of material through the mouthpiece. Other assumptions are that Coulomb friction exists at the interface between the compacted peat raw material and the mouthpiece, and slipping occurs at the interface of the material with the body [40].
At a given productivity of the screw press, it is possible to determine the screw diameter D or the angular rotation speed of the screw ω. The formed peat raw material is viscoplastic and has adhesion to the screw metal surface. In this case, the coefficient of internal friction is taken as the coefficient of friction, determined from the condition of the particles connection with each other when the layers of peat raw materials are shifted.
The initial data for selecting the parameters of the screw press are: the degree of mechanical processing of the product λ0 = 300; the reserve coefficient of the mechanical processing degree s = 1.1; the coefficient taking into account the rotation of peat with the auger screw φ = 0.2; the ratio of the radius of the auger screws k = r/R = 0.33; the coefficient of material slippage ε = 0.2; the productivity of the press Q = 0.005 m3/s; the tangential tension in the material τ = 6000 Pa; the efficiency of the screw drive ηм = 0.8; the length of the screw l = 1.6 m.
The choice of design parameters of the peat screw press was carried out taking into account the specified restriction on the degree of mechanical processing of peat raw materials [22]
Initial data for determining the volumetric productivity of a screw press with a composite tubular mouthpiece: the outer diameter of the screw D = 0.3 m; the pitch of the screw turns H = 0.2 m; the lifting angle of the helical line of the screw turns along the outer diameter φ = 22°; the height of the screw blade h = 0.1 m; the number of screw runs z = 1; the width of the blade ridge е = 0.01 m; the gap between the inner surface of the cylinder and the outer surface of the screw turn δ = 0.004 m; the screw rotation speed n = 1.966 s–1; the length of the forming zone lf = 0.98 m.
Substituting the values of the screw press parameters, we get the calculated value of the degree of mechanical processing of peat raw materials λ = 330. It is known [22] that the helical line pitch of the screw of a peat press is selected within the limits of H = (0.5-0.6). The ratio of the length l of the screw to its diameter D can be determined as follows:
Substituting the values of the initial data to determine the volumetric capacity of a screw press with a composite tubular mouthpiece, we get the calculated value l/D = 5.85. According to this value, the number of screw turns i = 3l/2D is determined, which is 8.27. Taking i = 8, we get that the calculated ratio l/D = 5.0. For a given design length of the screw l = 1.6 m, the radius of the screw, according to the model R = 3l/4i, will be R = 0.15 m, the diameter of the screw D = 2R = 0.3 m at the step of the turns H = 4R/3 = 0.2 m.
With a given productivity of the screw press and the assumption of conditions that take into account the rotation of peat raw materials together with the auger screw and partial slippage of the material, as well as using the parameters of the screw press, it is possible to determine the productivity:
equal to 0.042 m3/s, the angular velocity of the screw ω = 12,44 s–1 or the rotation speed
The main technological parameters of the extrusion machine are the rotation speed of the extruder screw and the pressure developed by the extruder [4]. The parametric analysis of the volumetric productivity of a screw press with a composite tubular mouthpiece was carried out with the conditional division of the mouthpiece into zones differing in configuration. The section of deformation of peat raw materials in the mouthpiece of the press is schematically shown in Fig.4. The process of forming the profile of a tubular piece in the mouthpiece of the press is carried out when the cylindrical void-forming device rotates relative to the mouthpiece. The axial movement of plasticized peat raw materials in the mouthpiece is the result of the pressure difference in it. Because of the axial displacement of peat raw materials, axial stresses σx are formed, and when the cylindrical void-forming device rotates, circumferential stresses σy arise in the mass. Due to the circumferential stresses, the structure of the material is distributed, and the mechanical strength of the agglomerated material increases [26]. The material is squeezed out by a pressure screw (from left to right) into the gap formed by the inner surface of the mouthpiece body and the outer surface of the void-forming device with the distribution of the material flow in the conical annular 1 and cylindrical annular (coaxial) 2 channels of the composite mouthpiece. This division is due to the fact that different transformations in the processed material occur at different parts of the mouthpiece. These zones themselves are not delimited elements, since they represent a single path for the moving material from the loading device to the exit from the forming hole [18]. For each zone, a particular coefficient of resistance to the flow of peat raw materials should be determined [14].
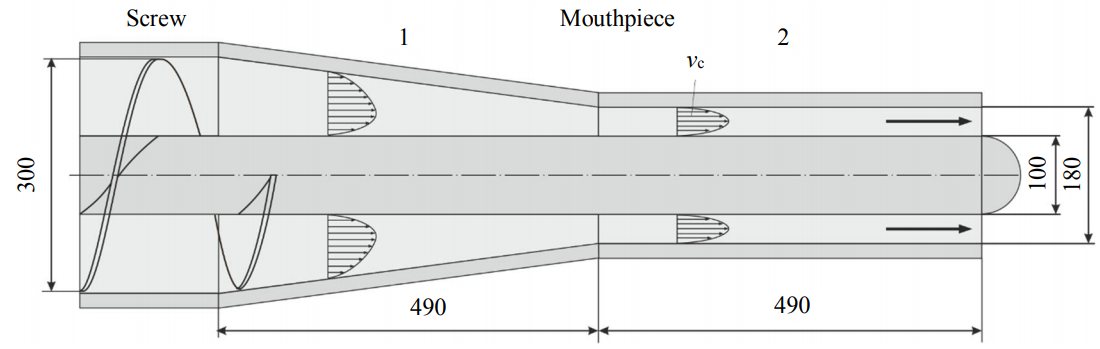
Fig.4. Scheme for the analysis of the degree of mechanical processing of peat raw materials in a screw press with the distribution of the material flow in the conical annular 1 and cylindrical annular (coaxial) 2 channels of the composite mouthpiece
The screw press productivity depends not only on the geometric parameters of the screw and the rotation speed, but also to a large extent on the design of the forming mouthpiece of the press. Based on the hydrodynamic approach to the analysis of the interaction of working bodies with the processed material in the forming zone of the screw press, it is customary to consider three components of the material flow: the movement of the material along the inter-turn space from the loading zone to the forming zone along the screw axis; the movement of the material in the opposite direction, which is caused by a pressure drop P along the length of the screw; the leakage flow moving in the gap between the outer surface of the screw turns and the inner surface of the cylinder in the direction from the forming zone.
Depending on the design of the forming zone and the resistance of the material in the composite mouthpiece during the processing of peat raw materials, the volume capacity of a single-screw press is expressed by the ratio with the conditional flow separation in the screw channel [15]:
where K is the coefficient of the geometric shape of the mouthpiece, m3; n is the screw rotation speed, s-1; А is the direct flow constant, m3; B is the reverse flow constant, m3; is the leakage flow constant for screws with constant geometric dimensions, m3.
The constants of the reverse flow, direct flow and leakage flow in the screw discharge zone with constant geometric dimensions are determined by the formulas, respectively [15]:
where D is the outer diameter of the screw, m; H is the pitch of the screw turns, m; h is the height of the screw blade, m; е is the width of the blade ridge, m; z is the number of screw runs; δ is the gap between the inner surface of the cylinder and the outer surface of the screw turn, m; φ is the lifting angle of the helical line of the screw turns along the outer diameter;
The data for calculating the screw parameters are selected in such a way that it is possible to provide a given volume capacity of the screw press of 0.004 m3/s.
The main geometric characteristic of a composite tubular mouthpiece is its total resistance coefficient, defined as the sum of the resistance coefficients of individual zones of the composite mouthpiece k1 and k2 [31]
where k1, k2 are the partial resistance coefficients of the channel zones with a simple geometric shape, determined by the formulas given in Table 1.
Table 1
Data for calculating the resistance coefficients and shear rate in the elementary channels [30]

Note. Ro, Ri are outer and inner radiuses; R1, R2 are the average radiuses of the cone at the input and output; δ1, δ2 are the thickness of the gap at the input and output
According to the initial data of the designed screw, Table 1 shows the calculated values of the flow constants, resistance coefficients and volumetric productivity of a screw press with a composite tubular mouthpiece.
As a result of the performed analysis, the total resistance coefficient of the composite screw press mouthpiece K = 2.93∙10–6 m3 is determined, which defines the pressure in the mouthpiece required for pushing the compacted mass through the mouthpiece [39]. Thus, as a result of the analysis of the screw press parameters, it was found that its performance is determined by the geometric parameters of the screw, depends on the design of the forming mouthpiece of the press, is proportional to the rotation speed of the screw.
The results of resistance parameters calculation in a composite tubular mouthpiece of a screw press: the direct flow constant is 7.697·10–3 m3; the reverse flow constant is 5.612·10–6 m3; the leakage flow constant is 8.692·10–8 m3; the resistance coefficient of the annular conical channel 8.233·10–6 m3; he resistance coefficient of the calibration annular cylindrical channel is 4.814·10–6 m3; he total resistance coefficient of the mouthpiece is 2.93∙10–6 m3.
When using a calibrating annular cylindrical channel, the value of the resistance coefficient of the material is 40 % less than the resistance coefficient of the annular conical channel. Then the pressure screw part of the composite tubular mouthpiece will increase the pressure (head), thereby reducing the energy consumption for forming peat mass into peat tubular pieces.
A decrease in energy consumption during forming using a calibrating annular cylindrical channel is a consequence of a decrease in the resistance coefficients and external friction of peat when it moves in the forming zone of a composite tubular mouthpiece.
The energy consumption of mechanical processing and forming of peat raw materials in a screw press with a composite tubular mouthpiece and a void-forming device
When the processed material enters the screw press mouthpiece (Fig.4), normal stresses and shear stresses occur, which vary depending on the geometric dimensions of the profiling elements of the mouthpiece and relax at the output of the mouthpiece.
The shear stress of the material depends on the normal pressure σ:
where
In a single-screw extruder, the material moves due to friction forces, the effectiveness of which mainly depends on the friction of the material against the cylinder walls. In the conical annular channel 1 (Fig.4) [22], the following condition is met:
where ffr is the friction coefficient of the specified pair of materials (peat raw materials for steel – 0.12), depending on the characteristics of peat raw materials (botanical composition, degree of decomposition, humidity, deformation rate and degree of mechanical processing of peat raw materials in a screw press [22, 25].
The adhesion and the friction coefficient depend on the deformation rate, as well as on the general technical and physical-mechanical properties of peat raw materials. When determining the energy intensity of mechanical processing and forming of peat raw materials in a screw press, the values
The change in the viscosity of peat raw materials indicates changes occurring in its structure. The balanced state in a steady flow is characterized by an increase in the mechanical processing of the material with a decrease in shear strength and effective viscosity. The effective viscosity decreases with an increase in the effective pressure in the system:
Pressure losses on the elementary zones of the mouthpiece can be determined as follows [30]:
where Q is the press productivity, m3/s; ηi is the effective viscosity of the material in the elementary zones of the mouthpiece, Pa·s; Ki is the coefficient of resistance of the elementary zones of the mouthpiece, m3.
As a result of the calculation, the material shear rate γ, the effective viscosity η and the pressure loss in the channel ∆Р for the annular conical channel were 12.24 s–1, 326.90 Pa·s, 198.53 kPa respectively; for the annular cylindrical channel 42.6 s–1, 93.87 Pа·s, 97.47 kPa respectively. The total pressure loss in the composite tubular mouthpiece of the press with a void-forming device was ∆P = 296 kPa.
The analysis of the energy intensity of mechanical processing and forming of peat raw materials in the composite screw press mouthpiece showed that when the annular conical channel of the composite mouthpiece narrows, a decrease in the pressure of the peat mass is observed. The narrowing in the annular conical channel serves to create additional resistance to the movement of the material due to its transverse deformation.
The pressure developed by the screw at the selected geometric parameters is determined as follows:
The pressing power depends on the physical and mechanical properties of peat raw materials, turning, returning and compressing the mass in the screw, the friction of the mass against the auger screw and the body, the roughness of the surface of the screw and the body [20]. The effective power at the highest pressure is calculated as follows:
Based on the results of studies in the forming of plastic clay materials [31] and the results of calculating the shear rate of the material, the effective viscosity and pressure losses in the mouthpiece of the press, it is assumed that energy costs will increase due to the friction of the peat mass on the surface of the annular conical channel, as well as an increase in wear of the channel surface.
Evaluation of the degree of mechanical processing of peat raw materials in the composite screw press mouthpiece and screw parameters optimization
The method of assessing the mechanical processing degree of peat by changing its physical and mechanical properties allows assessing the processing capacity of any mechanism at the stage of developing its design scheme. The method proposed by F.A.Opeyko [8] is based on the use of two invariants of the symmetric strain and stress tensor. The average degree of mechanical processing as the intensity of deformations is taken as an indicator of the processing effect of the mechanism on the material:
where λ11, λ22, λ33 are relative elongations in the directions of the coordinate axes x2, x3; λ12, λ23, λ13 are half of the corresponding shear angles.
The generalized index of deformation of peat raw materials in the mechanism depends only on its design features and is determined without considering the physical-mechanical and dimensional-mass properties of peat, which significantly expands the possibilities of analyzing the operation of specific mechanisms when dispersing peat raw materials with known physical-mechanical characteristics. Also, these models allow to design mechanisms with a given processing capacity.
As a result of modeling, the assessment of energy costs for 3D-forming of peat pieces of a tubular type [21] by a screw press with a composite mouthpiece and the processing capacity of the mechanism are subject to determination. The geometry of the pressing screw (Fig.4) provides a high degree of compaction of the material in the mouthpiece of the press, which allows getting a compact piece of high density and strength. The movement of the material, compression and stress distribution depend primarily on the selected design and the geometry of the pressure screw, in which the peat beam is continuously formed. The screw tube passes into a void-forming device of the same diameter [22].
During the mechanical processing of peat raw materials, there is a shift on the inner walls of the conical annular and cylindrical annular channels, depending on the nature of the distribution of the peat mass movement speed in the channels [8]. So, for the pressure part of the screw, the degree of mechanical processing is determined by:
where Q is the mobile screw press productivity, ε is the coefficient of slippage;
The mass movement in the conical annular channel 1 of the mouthpiece (Fig.4) occurs at a variable speed. The average volume degree of mechanical processing of peat raw materials in it will depend on the nature of the material flow rate distribution, it can be represented as the sum of changes in the degree of mechanical processing on the inner walls of the channel and on the surface of the void-forming device
In the cylindrical annular channel 2 (see Fig.2) the screw press mouthpiece, the mass moves at a constant speed, and the shift occurs in thin layers directly at the inner surface of the mouthpiece and at the outer surface of the void-forming device as a result of mass friction on the surfaces. In this case, the degree of mechanical processing is:
The generalized model of the degree of mechanical processing of peat raw materials in a screw press, taking into account the material flow rates distribution in the conical annular 1 and cylindrical annular (coaxial) channels of the composite screw press mouthpiece 2, is determined as follows:
Based on the estimate of the total degree of mechanical processing λ, the specific stress during the processing of peat raw materials (limit) will be equal to
productivity for processing peat raw materials in a screw press with the selected parameters:
In order to determine the highest pressure when forming peat raw materials in the composite screw press mouthpiece, an analysis of the optimal ratio between the geometric parameters of the screw – its radius R and the pitch of the turns H was carried out. The analysis of the dependence of the screw press productivity Q, the degree of mechanical processing of peat raw materials λ and the screw pressure σ was carried out on its design parameter H/R at a constant angular velocity ω and at different values of the step of the screw turns H [8].
Conditions for the analysis: the length of the screw l = 1.6 m; the screw diameter
The pressures developed by the screw at different values of the pitch of the screw turns were determined [22] in this way:
The results of the analysis are presented in Table 2. The productivity of the screw at the given values of the step of the turns [8] is calculated as follows:
For variable values of H, the values of the productivity of the screw press Q are obtained, presented in Table 2. The degree of mechanical processing of peat raw materials in a screw press at the specified values of the step of the screw turns
Table 2
The results of the analysis of the dependence of the screw parameters on the design parameter H/R at a constant
angular velocity (screw length l = 1.6 m; radius R = 0.15 m)
Step of turns Н, m |
Design parameter H/R |
Pressure |
Press productivity Q, m3/s |
The degree of mechanical processing of peat raw materials l |
0.18 |
1.20 |
297.87 |
0.0038 |
421.25 |
0.20 |
1.33 |
301.59 |
0.0042 |
379.12 |
0.22 |
1.47 |
299.10 |
0.0046 |
344.66 |
0.24 |
1.60 |
293.22 |
0.0050 |
315.94 |
0.26 |
1.73 |
285.53 |
0.0055 |
291.63 |
0.28 |
1.87 |
276.97 |
0.0059 |
270.80 |
0.30 |
2.00 |
268.08 |
0.0063 |
252.75 |
Thus, the net volumetric productivity of a single-screw extruder is a combination of resistance and pressure flows, and the working capacity of the extruder is determined by the rotation speed of the screw, the back pressure in the mouthpiece and the rheological properties of peat raw materials. The combination of these variables limits the operating range and flexibility of the screw press [27].
Taking into account the model of the degree of mechanical processing and the analysis carried out (Table 2) the graphical dependences of the volumetric productivity of the screw press Q, the degree of mechanical processing of peat raw materials λ, the pressure in the screw σ on different ratios of the design parameter H/R with a step of H = 0.2 m were built (Fig.5). By changing the ratio of the pitch of the helical blade of the screw to the radius in the loading, transportation and compression zones, it is possible to significantly increase the density of the extruded material.
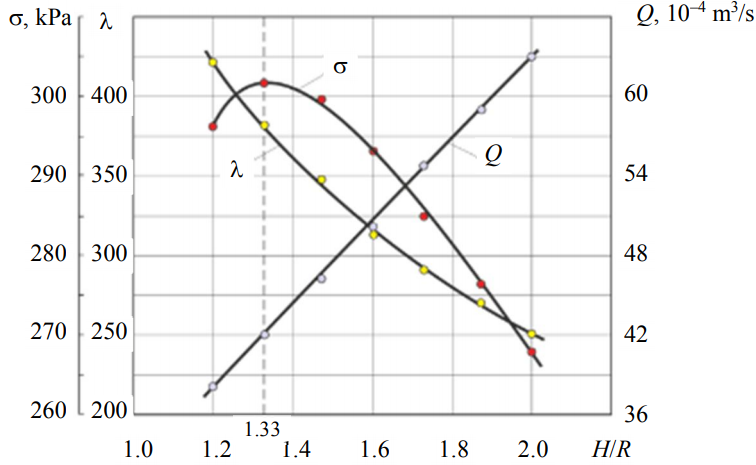
Fig.5. Dependences of the productivity of the screw Q, the degree of mechanical processing of the material l, the pressure in the screw from its design parameter H/R
When optimizing the screw parameters, it was found that the pressure developed by the screw reaches the maximum value at the ratio of the design parameter H/R = 1.33, which is consistent with the recommendations of F.A.Opeyko [8] for determining the optimal design and kinematic parameters of peat screw presses. It is also determined that there is no linear relationship between deformation and force in dispersed systems, due to the fact that the transmitted energy in these systems partially turns into heat and dissipates over time.
It is determined that the productivity of the screw press depends on the ability of the pressure screw to create the necessary pressure to overcome the resistance of the screw mouthpiece and depends on the length of the composite mouthpiece. The optimal screw pressure when forming peat raw materials corresponds to the range of 300-400 kPa. The capacity for processing peat raw materials in a screw press with the selected parameters was 13.44 kW.
Conclusion
Based on the information analysis and the conducted research, the need to improve the existing technological equipment for the production of agglomerated peat products in the field has been identified. The study was carried out in order to intensify the process of field drying of peat agglomerated products through the use of a tubular piece shape. Additive production of polymer-fiber peat composites by extrusion allows to make products with significantly improved mechanical properties compared to non-reinforced raw materials. To give a certain 3D shape to the piece and increase its strength characteristics, during the analysis of porosity and fractal dimension based on photo images of samples, it was determined that the maximum mechanical strength of the piece corresponds to a multifractal dimension D = 2.6 in a polymer-fiber composite with a ratio of components of a peat mixture of low and high decomposition degrees of 1:3.
In order to increase the convective component of the heat balance during drying, it was determined that when forming a piece with a height of more than 0.24 m, when laying it in a vertical position, the wind speed increases by 35-40 %. It was also found that the vertical laying of peat tubular pieces in comparison with the spreading of pieces in the form of a horizontal tape allows to increase the loading of the field for drying by 10 %, and the coefficient of contact of the piece with the wet base will decrease threefold, which contributes to an increase in the intensity of drying. It is theoretically proved that for the intensification of the drying process, the rational form of a peat piece is a thick-walled pipe with an outer diameter of D = 0.18 m, a hole ds = 0.1 m, a wall thickness of 0.04 m and a height Ls = 0.25 m.
Taking into account the requirements for the shape and size of the piece formed during the study, a patented design of a screw press with a composite mouthpiece [12] consisting of sequentially arranged annular conical and annular cylindrical channels with a void-forming device is proposed.
The volumetric productivity of a screw press with a composite tubular mouthpiece depends on the design of the forming mouthpiece of the press. The design of the screw press is conditionally divided into zones in the form of an annular conical channel, the narrowing of which determines the pressure developed in the extruder and the productivity of the machine and an annular cylindrical channel in which a piece of a given shape and size is calibrated. As a result of the performed analysis, the total resistance coefficient of the composite screw press mouthpiece K = 2.93∙10–6 m3 is determined, on which the pressure in the mouthpiece necessary for pushing the mass through the mouthpiece depends.
The influence of geometric and operating parameters on the productivity and design of the screw press was studied using a model of the degree of mechanical processing of peat raw materials. As a result of the theoretical analysis of the working process of pressing peat raw materials, analytical expressions were obtained to determine the degree of mechanical processing of peat raw materials in a screw press with a composite mouthpiece when moving the peat mass in each zone. Taking into account the distribution of the material flow in the conical annular and cylindrical annular channels of the mouthpiece, the total degree of mechanical processing does not exceed λ = 379, and the specific stress during processing of the material .
Based on experimental studies, the optimal design and operating parameters were determined: the length of the channels of the forming mouthpiece L = 0.49 m; the angular rotation speed ω = 12.44 s–1. The slope angle of the pressing channel of the forming mouthpiece is determined by the angle of internal friction 12°. Optimization of the screw press parameters according to the H/R criterion showed that the maximum pressure of 301.6 kPa developed by the screw is achieved with the ratio of its design parameter H/R = 1.33.
The obtained values of the design and geometric parameters of the screw press with a composite mouthpiece and a void-forming device correspond to the range of recommended values of 300-400 kPa, which provide the maximum pressure in the screw press mouthpiece, taking into account the rate of flow of peat mass in order to ensure sufficient compaction of the material in time. The geometric parameters of the composite screw press mouthpiece determined in the work allow to obtain a 3D peat piece in the form of a thick-walled pipe from peat raw materials of a low and high degree of decomposition, with an increased ability of moisture loss during drying in the field. Laboratory studies on the natural drying of samples of peat tubular pieces in an upright position confirm the ability of the piece to be in a state of intensive drying for a long time, as a result of which the time until the cleaning humidity is reduced.
References
- Afanasev A.E. Structure formation of colloidal and capillary-porous bodies during drying. Tver: Tverskoi gosudarstvennyi tekhnicheskii universitet, 2003, p. 190 (in Russian).
- Vagapova E.A., Khudyakova I.N., Ivanov S.L. The reason for the choice of equipment for primary dehydration of raw peat during its hydraulic mining from undrained peat deposit. Gornyi informatsionno-analiticheskii byulleten. 2019. N S18, p. 3-12. DOI: 10.25018/0236-1493-2019-7-18-3-11 (in Russian).
- Demyanenko O.V., Kopanitsa N.O., Sorokina E.A. Performance characteristics of 3d printing construction mixes depending on thermallymodified peat additive. Vestnik Tomskogo gosudarstvennogo arkhitekturno-stroitelnogo universiteta. 2018. N 4, p. 122-134. DOI: 10.31675/1607-1859-2018-20-4-122-134 (in Russian).
- Dyadichev V., Kolesnikov A., Dyadich A. Improvement of extrusion equipment and technologies for processing secondary combined polymer materials and mixtures. Dinamika sistem, mekhanizmov i mashin. 2018. Vol. 6. N 1, p. 162-167. DOI: 10.25206/2310-9793-2018-6-1-162-167
- Zyuzin B.F., Fomin D.S. On the impact of physical-mechanical properties of the source of peat in the process of mechanical dispersion. Trudy Instorfa. 2013. N 7 (60), p. 49-52 (in Russian).
- Ivanov S.L., Ivanova P.V., Kuvshinkin S.Y. Promising model range career excavators operating time assessment in real operating conditions. Journal of Mining Institute. 2020. Vol. 242, p. 228-233. DOI: 10.31897/PMI.2020.2.228
- Iakupov D.R., Ivanov S.L., Ivanova P.V., Permyakova E.K. Classification of peat extraction methods and means of their implementation. Gornyi informatsionno-analiticheskii byulleten. 2020. N S34, p. 3-12. DOI: 10.25018/0236-1493-2020-10-34-3-12 (in Russian).
- Kislov N.V., Slysh У.М., Lyutko G.I. Calculation of processed peat stress when shifting on steel. Gornaya mekhanika i mashinostroenie. 2012. N 1, p. 16-21 (in Russian).
- Krymskii K.I., Bolshunova O.M. Overview of modern methods and technical tools of measuring peat moisture. Journal of Mining Institute. 2012. Vol. 196, p. 248-251 (in Russian).
- Kuskov V.B., Bazhin V.Y. Use of various types of carbon-containing raw materials to produce thermal energy. Journal of Mining Institute. 2016. Vol. 220, p. 582-586. DOI: 10.18454/PMI.2016.4.582
- Panov V.V., Misnikov O.S., Kuporova A.V. Problems and prospects of development of peat production in Russian Federation. Gornyi informatsionno-analiticheskii byulleten. 2017. N 5, p. 105-117 (in Russian).
- Fedorov A.S., Mikhailov A.V., Garifullin D.R. Patent N 195588 RF. Device for forming peat raw materials into tubular pieces. Publ. 31.01.2020. Bul. N 4 (in Russian).
- Priporov I.Y., Bachu T.N. Optimization of design parameters of the variable screw pitch of the press-extruder KMZ-2 on the basis of the experiment planning. Izvestiya Orenburgskogo gosudarstvennogo agrarnogo universiteta. 2017. N 3 (65), p. 84-87 (in Russian).
- Pyatov V., Holubeu A., Shyrayeu P. Design technique of screw-type machines for extrusion of plastic media. Vestnik
Vitebskogo gosudarstvennogo tekhnologicheskogo universiteta. 2017. N 2 (33), p. 45-52 (in Russian). - Suvorova Yu.A., Tarova A.A., Ryazanov I.V. The Influence of the Composite Chemical Absorbent on Its Sorption and Performance Characteristics. Vestnik Tambovskogo gosudarstvennogo tekhnicheskogo universiteta. 2018. Vol. 24. N 2, p. 307-317. DOI: 10.17277/vestnik.2018.02. pp.307-317 (in Russian).
- Stepuk E.Y. Choice of optimal parameters for transportation of frozen peat screw conveyor. Journal of Mining Institute. 2011. Vol. 189, p. 111-112 (in Russian).
- Stepuk E.Y., Ivanov S.L. Stand for evaluating the efficiency of transport of peat. Journal of Mining Institute. 2011. Vol. 189, p. 113-116 (in Russian).
- Popov V.P., Martynova D.V., Antimonov S.V. et al. Theoretical substantiation of the energy- and resource-saving design of a screw extruder for the production of high-quality feeds. Izvestiya Orenburgskogo gosudarstvennogo agrarnogo universiteta. 2017. N 6 (68), p. 107-109 (in Russian).
- Terentev A.A., Suvorov V.I. Structure and properties of formed peat products: Monograph. Tver: Sozvezdie, 2004, p. 136 (in Russian).
- Terekhin E.P. The technique engineering calculation granulating screw press for bentonite clays activation. Gornyi informatsionno-analiticheskii byulleten. 2013. N 5, p. 215-218. (in Russian).
- Fedorov A.S., Kazakov Y.A., Fadeev D.V. Parameters of the screw press mouthpiece on the basis of requirements to the peat formed products. Gornyi informatsionno-analiticheskii byulleten. 2020. N S9, p. 3-16. DOI: 10.25018/0236-1493-2020-3-9-3-16 (in Russian).
- Fedorov A.S., Mikhailov A.V., Garifullin D.R. Mechanical processing of peat raw materials in a composite srew press mouthpiece. Gornyi informatsionno-analiticheskii byulleten. 2020. N S44, p. 3-13. DOI: 10.25018/0236-1493-2020-12-44-3-13 (in Russian).
- Khlyupin A.N., Dinariev O.Yu. Fractal analysis of the three-dimensional microstructure of porous materials. Zhurnal tekhnicheskoi fiziki. 2015. Vol. 85. Iss. 6, p. 17-22 (in Russian).
- Tselovalnikov A.P., Mkrtchyan A.S. Modern directions of modernization of peat machines and equipment. Innovatsii na transporte i v mashinostroenii, 14-15 aprelya, 2015, Sankt-Peterburg, Rossiya. Sankt-Peterburgskii gornyi universitet, 2015, p. 67 (in Russian).
- Chistyi V.I., Stasevich V.I., Chistyi I.N. Machine for Lump Peat Production. Gornaya mekhanika i mashinostroenie. 2012. N 3, p. 38-46 (in Russian).
- Baranowski W., Palutkiewicz P., Werner K. The special design of extrusion head for manufacturing of polymer pipes with increased mechanical strength. Polimery. 2015. Vol. 60. Iss.1, p. 66-71. DOI: 10.14314/polimery.2015.066
- Bouvier J.-M., Campanella O.H. Extrusion Processing Technology: Food and Non‐Food Biomaterials. John Wiley & Sons, 2014, p. 530. DOI: 10.1002/9781118541685
- e Costa E.C., Duarte J.P., Bártolo P. A review of additive manufacturing for ceramic production. Rapid Prototyping Journal. 2017. Vol. 23. Iss. 5, p. 954-963. DOI: 10.1108/RPJ-09-2015-0128
- Li W., Ghazanfari A., Leu M.C., Landers R.G. Extrusion-on-demand methods for high solids loading ceramic paste in freeform extrusion fabrication. Virtual and Physical Prototyping. 2017. Vol. 12. Iss. 3, p. 193-205. DOI: 10.1080/17452759.2017.1312735
- Hopmann C. Michaeli C.W. Extrusion Dies for Plastics and Rubber: Design and Engineering Computations. 4th Edition. Munich: Hanser Publishers, 2016, p. 469. DOI: 10.3139/9781569906248
- Kocserha I., Kristály F. Effects of Extruder Head’s Geometry on the Properties of Extruded Ceramic Products. Materials Science Forum. 2010. Vol. 659, p. 499-504. DOI: 10.4028/www.scientific.net/MSF.659.499
- 32. Mikhailov A. Peat surface mining methods and equipment selection. Mine Planning and Equipment Selection. Proceedings of the 22nd MPES Conference, 14-19 October, 2013, Dresden, Germany. Springer, 2014, p. 1243-1249. DOI: 10.1007/978-3-319-02678-7_120
- Mikhailov A.V., Fedorov A.S., Garmaev O.Z. Preliminary study of tubular peat extrusion. International Conference on Mechanical Engineering, Automation and Control Systems 2018, 12-14 December, 2018, Novosibirsk, Russian Federation. IOP Conference Series: Materials Science and Engineering, 2019. Vol. 560. N 012061. DOI: 10.1088/1757-899X/560/1/012061
- Mikhailov A.V., Garmaev O.Z., Fedorov A.S. The Relationship between Fractal Properties and Active Porosity of Peat Compositions. Key Engineering Materials. 2020. N 836, p. 58-62. DOI: 10.4028/www.scientific.net/KEM.836.58
- Miloš B., Bensa A. Fractal approach in characterization of spatial pattern of soil properties. Eurasian Journal of Soil Science. 2017. Vol. 6. Iss. 1, p. 20-27. DOI: 10.18393/ejss.284260
- Ivanov S.L., Khudyakova I.N., Vagapova E.A., Ivanova P.V. Modeling of the process of mechanical dehydration of raw peat materials in the working tools of mining machines. International Conference on Innovations, Physical Studies and Digitalization in Mining Engineering (IPDME), 23-24 April, 2020, St. Petersburg, Russian Federation. IOP Publishing Journal of Physics: Conference Series, 2021. Vol. 1753. N 012048. DOI: 10.1088/1742-6596/1753/1/012048
- Liiv J., Teppand T., Rikmann E., Tenno T. Novel ecosustainable peat and oil shale ash- based 3D-printable composite material. Sustainable Materials and Technologies. 2018. Vol. 17. N e00067. DOI: 10.1016/j.susmat.2018.e00067
- Yablonev A.L., Gorlov I.V., Kozyreva L., Fomin K. Optimization of Driving Trailers Transmission for Peat Transportation. IIIrd International Innovative Mining Symposium, 3-5 October, 2018, Kemerovo, Russian Federation. E3S Web of Conferences, 2018. Vol. 41. N 03001. DOI: 10.1051/e3sconf/20184103001
- Orisaleye J.I., Ojolo S.J. Mathematical Modelling of Pressure Distribution along the Die of a Biomass Briquetting Machine. International Journal of Design Engineering. 2019. Vol. 9. Iss. 1, p. 36-50. DOI: 10.1504/IJDE.2019.104125
- Orisaleye J.I., Ojolo S.J. Parametric analysis and design of straight screw extruder for solids compaction. Journal of King Saud University – Engineering Sciences. 2019. Vol. 31. Iss. 1, p. 86-96. DOI: 10.1016/j.jksues.2017.03.004
- 41. Parandoush P., Lin D. A review on additive manufacturing of polymer-fiber composites. Composite Structures. 2017. Vol. 182, p. 36-53. DOI: 10.1016/j.compstruct.2017.08.088
- Ruscitti A., Tapia C., Rendtorff N.M. A review on additive manufacturing of ceramic materials based on extrusion processes of clay pastes. Cerâmica. 2020. Vol. 66, p. 354-366. DOI: 10.1590/0366-69132020663802918
- Ivanov S.L., Iakupov D.R., Ivanova P.V., Permiakova E.K. Structure modeling of mining machinery systems for production of raw peat materials. International Conference on Innovations, Physical Studies and Digitalization in Mining Engineering (IPDME), 23-24 April, 2020, St. Petersburg, Russian Federation. IOP Publishing Journal of Physics: Conference Series, 2021. Vol. 1753. N 012057. DOI: 10.1088/1742-6596/1753/1/012057
- Travitzky N., Bonet A., Dermeik B. et al. Additive manufacturing of ceramic-based materials. Additive Manufacturing of Ceramic-Based Materials. 2014. Vol. 16. Iss. 6, p. 729-754. DOI: 10.1002/adem.201400097
- Chen Z., Li Z., Li J. et al. 3D printing of ceramics: A review. Journal of the European Ceramic Society. 2019. Vol. 39, p. 661-687. DOI: 10.1016/j.jeurceramsoc.2018.11.013
- Wang J.C., Dommati H., Hsieh S.J. Review of additive manufacturing methods for high-performance ceramic materials. International Journal of Advanced Manufacturing Technology. 2019. Vol. 103. Iss. 5-8, p. 2627-2647. DOI: 10.1007/s00170-019-03669-3