Методика управления процессом бурения и экспериментальные исследования сил сопротивления при бурении долотами с резцами PDC
- 1 — д-р техн. наук профессор Институт горного дела, геологии и геотехнологий Сибирского федерального университета
- 2 — канд. техн. наук старший преподаватель Институт горного дела, геологии и геотехнологий Сибирского федерального университета
- 3 — ассистент Институт горного дела, геологии и геотехнологий Сибирского федерального университета
- 4 — канд. техн. наук доцент Институт горного дела, геологии и геотехнологий Сибирского федерального университета
- 5 — Университет Цзилинь
Аннотация
Рациональная, теоретически обоснованная и эмпирически верифицированная система управления является условием оптимального управления процессом бурения с соблюдением критериев минимизации затрат временных и материальных ресурсов. Новое поколение породоразрушающего инструмента с применением резцов PDC ( polycrystalline diamante cutters ), крайне эффективных при бурении скважин различного целевого назначения в горных породах средней твердости, диктует необходимость разработки методики и критериев оптимального управления процессом бурения с использованием данного инструмента. В работе представлен аналитический анализ силового взаимодействия породоразрушающих элементов, горной породы, вмещающей забой, и бурового раствора, насыщенного шламом, выделены влияющие факторы, приведены зависимости для определения параметров разрушения горных пород. Эмпирическая верификация теоретических положений проведена на основе анализа данных экспериментального бурения мрамора коронкой с резцами PDC диаметром 76,2 мм, обработанных с применением метода полного факторного эксперимента с получением математических моделей факторов и их графической интерпретации. Рассмотрена методика управления процессом бурения, основанная на оптимальном соотношении частоты вращения инструмента, осевой нагрузки и углубления за один оборот, позволяющая определить по косвенным признакам режим разрушения горной породы на забое скважины и выбрать оптимальные значения параметров режима бурения, которые соответствуют наиболее оптимальным условиям с точки зрения достижения максимальной механической скорости бурения в совокупности с рациональным режимом работы породоразрушающего инструмента. Представлена схема, содержащая возможные варианты режима отработки долота и способы их распознавания по соотношению углубления за один оборот и частоты вращения породоразрушающего инструмента.
Введение. Применение резцов PDC в качестве породоразрушающих элементов для изготов-ления коронок и долот – один из прогрессивнейших трендов при изготовлении породоразру-шающего инструмента для разрушения горных пород [2, 8 - 14]. Инструмент такого типа способен обеспечить высокие скорости бурения скважин различного целевого назначения в горных поро-дах широкого спектра твердости в совокупности с большим ресурсом. Однако вопрос силового анализа взаимодействия породоразрушающих элементов, горной породы, вмещающей забой, и бурового раствора, насыщенного шламом, нельзя назвать досконально изученным.
Силы сопротивления при бурении долотами с резцами типа PDC существенно влияют на процесс разрушения, его эффективность и, в частности, стойкость самих резцов [7]. Исследования, представленные в работе [5], а также аналитические данные компании Smith Bits [15] показывают, что наиболее интенсивный износ резцов возможен в точке на расстоянии 0,8 радиуса долота r, что указывает на основное влияние на изнашивание резцов сил сопротивления работе резцов, величина которых определяется значением линейной скорости перемещения резцов, которая увеличивается от центра торца к его периферии в соответствии с зависимостью 2πωr, где ω – частота вращения долота. Вопросу влияния скорости перемещения резца в процессе резанияскалывания породы на процесс разрушения горной породы посвящены исследования К.И.Борисова [1].
Известна зависимость из работы [1], показывающая связь коэффициента сопротивления разрушению горной породы от величины осевого усилия на резец, полученная в ходе экспериментальных исследований на стенде. Из зависимости следует, что коэффициент сопротивления активно возрастает на этапе упругого деформирования горной породы, снижаясь в момент, когда напряжения в горной породе вызывают активное объемное разрушение и необратимое пластическое деформирование (образование трещин, активное разрушение), чему свидетельствуют значения угла α, полученные в интервале малых (зона упругого деформирования) и более значительных (зона пластического деформирования) значений осевого усилия. При этом следует отметить, что кривая, представленная в данной работе, не учитывает сопротивления среды, а именно бурового раствора, насыщенного шламом, и сопротивления уже разрушенной перед резцом горной породы, но еще не удаленной с забоя скважины.
Методология исследования. Рассмотрим теоретические положения, позволяющие учесть сопротивление как уже разрушенной перед резцом горной породы, так и сопротивление среды (бурового раствора) при бурении долотами с резцами PDC. Для уточнения действующих сил и реакций обратимся к схеме (рис.1).

Сила, выталкивающая резец с отрицательным передним углом в процессе резания – скалывания горной породы, может определяться по формуле
где σск – предел прочности на скалывание горной породы, Па; Sск – площадь скалываемой резцом породы на передней грани, м2 ; K – коэффициент, учитывающий превышение усилие сопротивления горной породы резанию-скалыванию при повышении линейной скорости резца.
Размер площадки скалывания породы Sск определен в работе [3]:
где d – диаметр резца, м; h – глубина внедрения резца в породу, м; γск – угол скалывания породы на передней грани резца, град.
В завершенном виде формула (1) будет выглядеть следующим образом:
Сопротивление среды можно рассчитать по формуле, в которой учитывается, прежде всего, скорость перемещения резца и плотность среды:
где ρс – весовая плотность среды с учетом плотности бурового раствора, насыщенного шламом из зоны разрушения и разрушаемой горной породы, H/м3 ; S – площадь резца или его проекции на линию резания, если угол резания φp не равен нулю, а составляет угол более 0 градусов (обычно не более 5-10°); Cс – коэффициент сопротивления со стороны резца, определяемый формой его плоскости (ориентировочно для плоского 1, для круглого выпуклого 0,5, для вогнутого по дуге окружности 1,5).
Таким образом, суммарная сила сопротивления движущемуся по забою резцу равна сумме RB и Rс.
Из представленной схемы (рис.1) следует, что реакция еще не разрушенной горной породы RB воздействует на ядро сжатия (уплотнения) 1, так как в ядре сжатия она разрушена до состояния мелкого дробления. Реакция RB в случае установившегося режима резания – скалывания породы направлена навстречу результирующему вектору осевого усилия и усилия резания – скалывания R и под прямым углом к поверхности резца.
Сила, которая направлена навстречу осевому усилию, компенсируя силу сопротивления RB, будет равна
где γп – передний угол резца, град.
Сопротивление среды обуславливает появление реакции Fн, направленной навстречу осевому усилию и производящей эффект выталкивания резца из горной породы при вращении долота и разрушении горных пород. Эту реакцию можно определить из зависимости
Для определения коэффициента K в формулах (1) и (3) следует использовать результаты экспериментальных исследований по определению возрастающей силы сопротивления резанию – скалыванию породы при росте линейной скорости резца, представленные в работе [3], где приведены зависимости, отражающие влияние скорости резания – скалывания породы vp на величину усилия RB для песчаника.
Из формулы (3) следует, что усилие RB при установившемся режиме резания – скалывания породы, когда все основные параметры, входящие в формулу, остаются неизменными, изменение скорости перемещения резца будет зависеть от значения напряжения породы на скалывание σск. Параметр прочности горной породы σск при повышении скорости резания – скалывания vр будет также возрастать. В этом случае коэффициент K, представленный в формуле (3), будет равен
где RBT – усилие сопротивления, соответствующее значению линейной скорости резца; RBH – усилие сопротивления, соответствующее линейной скорости, близкой к нулевому значению.
Усилие RBT возможно определить из зависимости
где θ – угол наклона опытной кривой, которую можно получить при испытании предела прочности на скалывание определенной горной породы; x – текущее относительное значение расстояния от центра торца долота до точки, в которой происходит определение RB; r – радиус долота.
Таким образом, для успешной оценки параметра K достаточно иметь экспериментально определенную зависимость сопротивления резания – скалывания, а именно угол β, полученный с линии роста параметра RB.
Обсуждение. Для эмпирической оценки полученных значений расчета сопротивлений рассмотрим данные экспериментального бурения мрамора коронкой с резцами PDC диаметром 76,2 мм.
В результате бурения по плану полного факторного эксперимента с двумя влияющими факторами (осевая нагрузка и частота вращения) [4] получены следующие модели, отражающие процесс бурения с различных позиций, учитывающих как темп проходки и ресурс инструмента, так и величину углубления за один оборот – важнейший параметр управления бурением,



На рис.2 показана графическая интерпретация моделей механической скорости бурения (9) в пределах использованных при проведении эксперимента осевой нагрузки Р и частоты вращения ω.
На рис.3 показана графическая интерпретация модели углубления за один оборот (10). Рациональная область управления режимами бурения, выявленная с помощью анализа энергоемкости (модель (12), показывает, что эффективным будет углубление на уровне 1,3-1,4 мм/об, что обеспечит практически самую высокую, в условиях опыта, механическую скорость бурения.
Обработка полученных данных, в частности графиков механической скорости бурения, позволяет получить графические зависимости углубления за один оборот от величины осевого усилия (рис.3) и частоты вращения (рис.4).
Зависимости на рис.4 получены по графикам механической скорости бурения (см. рис.2) при минимальной, средней и максимальной частоте вращения по зависимости hоб = vм/ω в соответствии с методикой из работы [4]. Представленные на рис.4 графические зависимости свидетельствуют о повышении осевой нагрузки при повышении величины углубления за один оборот, при этом линии углубления за один оборот имеют перекрещивание при Рос = 455 даН. Осевое усилие данной величины разделяет процесс разрушения на усталостно-поверхностный режим (до величины 455 даН) и объемное разрушение (после величины 455 даН).
Режим разрушения меняет и зависимость углубления за один оборот от частоты вращения:
– при усталостно-поверхностном разрушении, когда величины осевого усилия (напряжений в горной породе) недостаточно для объемного разрушения, максимальное углубление h1 наблюдается при максимальном значении частоты вращения (200 мин-1), а минимальное углубление h3 при минимальной частоте вращения (50 мин-1);
– при объемном разрушении ситуация меняется на противоположную, т.е. максимальная величина углубления h1 соответствует наименьшему значению частоты вращения (50 мин-1), а минимальное углубление h3 максимальной частоте вращения (200 мин-1).
На рис.5 представлены графики, показывающие зависимость величины углубления за один оборот от частоты вращения при значениях осевой нагрузки 330 даН в режиме усталостно-поврехностного разрушения и 600, 750 и 800 даН в режиме объемного разрушения горной породы. Представленные данные показывают повышение углубления за один оборот при усталостно-поверхностном разрушении (линия 1 на рис.5) по мере роста частоты вращения бурового инструмента. В то же время при объемном разрушении, напротив, наблюдается снижение углубления за один оборот по мере повышения частоты вращения (линии 2, 3, 4 на рис.5), что указывает на рост сопротивлений со стороны горной породы и среды по мере роста линейной скорости резания – скалывания. При этом темп снижения глубины резания – скалывания горной породы повышается при повышении осевого усилия и соответственно глубины внедрения резцов в горную породу.
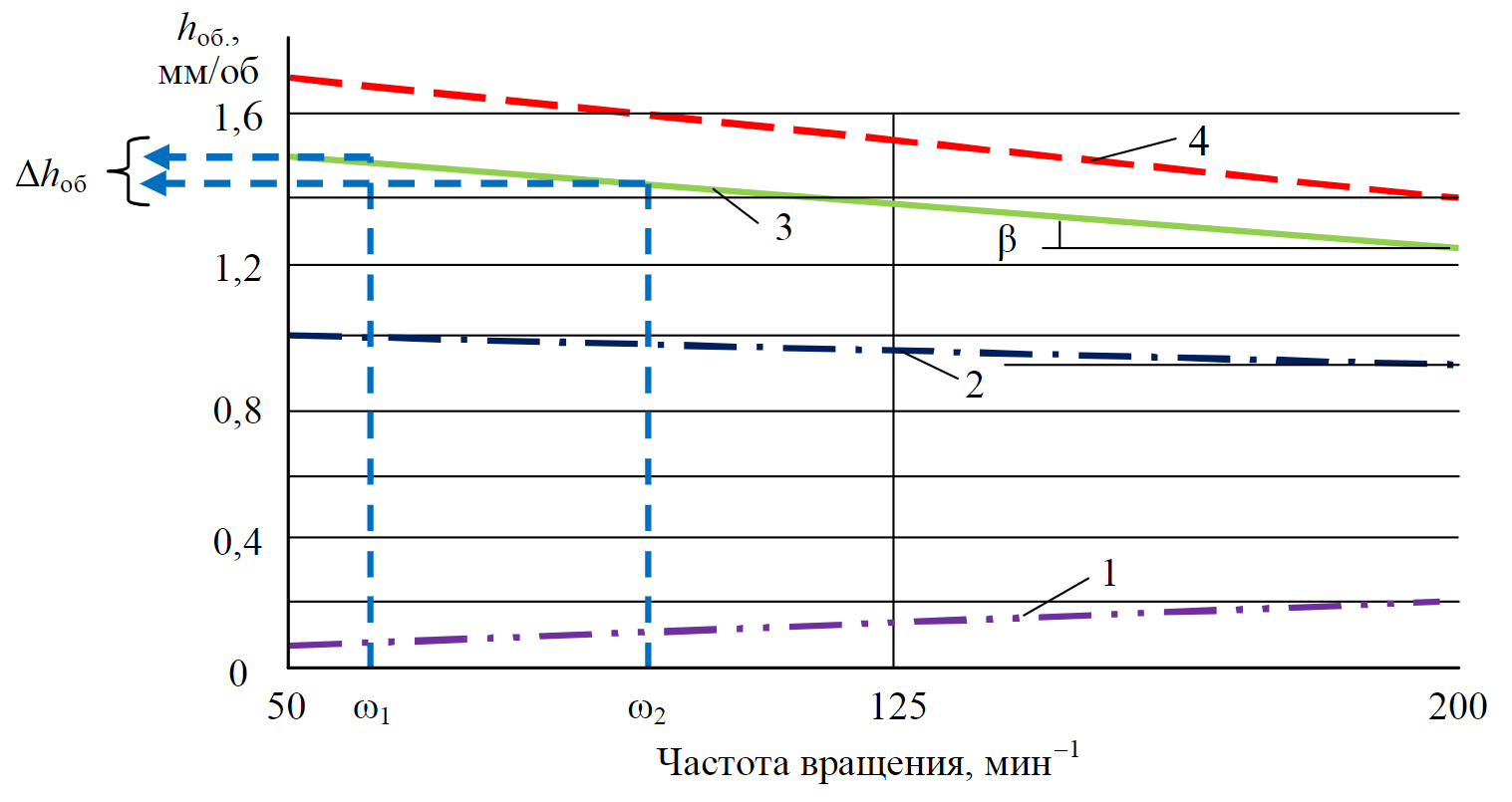
Темп снижения углубления за один оборот, выраженный через угол β, позволяет определить коэффициент сопротивления как тангенс этого угла:
где Δh – величина снижения углубления за один оборот на интервале повышения частоты вра-щения Δω, например, от ω1 до ω2 (рис.5).
Представленные результаты обработки данных экспериментального бурения показывают, что полученные теоретические зависимости получили подтверждение, поскольку свидетельст-вуют, что по мере роста глубины внедрения резцов в породу h сопротивление в режиме объемного разрушения нарастает, а в режиме усталостно-поверхностного разрушения, наоборот снижается. Это связано с тем, что в режиме усталостно-поверхностного разрушения максимальное углубление за один оборот достигается при максимальной частоте вращения, что подтверждено многими экспериментальными данными [4,6].
Результаты. Практическое применение полученных закономерностей может быть реализовано при диагностике режима разрушения горной породы при управлении процессом бурения с применением интерактивных систем, например, забойных телеметрических систем или управления процессом бурения с применением сиcтем компьютерного сопровождения APS [4].
На рис.6 показана программа управления параметрами режима бурения. Например, на эта-пе I произошел рост частоты вращения от величины ω1 до ω2 при неизменной величине осевого усилия (500 даН). В этом случае происходит снижение величины углубления за один оборот вследствие роста сил сопротивлений со стороны разрушаемой породы и среды (формулы (3) и (4), что генерирует появление сил, снижающий величину осевого усилия (формулы (5) и (6).

В данном случае механическая скорость будет определяться произведением vм = h1ω2. Поскольку произошло снижение величины углубления от h0 до h1, рост vм будет незначительным или будет отсутствовать.
Для устранения данной проблемы можно перейти к реализации этапа II, который состоит в повышении осевой нагрузки до 600 даН и снижении частоты вращения до величины ω12, что обеспечит более высокое значение механической скорости бурения в сравнении с этапом I при меньшем значении частоты вращения бурового инструмента.
Отработку бурового инструмента рационально производить по заданной величине углубле-ния за один оборот, например, hоб (рис.6). В этом случае корректировки частоты вращения, на-пример, от ω2 до ω3 и ω4, потребуют изменения и осевого усилия, а именно, от величины осевой нагрузки 600 перейти к 700, а затем и 800 даН, что позволит планомерно повысить механиче-скую скорость бурения по мере повышения частоты вращения.
Для определения наиболее оптимального соотношения между выбранной частотой враще-ния и осевой нагрузкой в режиме интерактивного управления процессом бурения могут быть применены эмпирические модели типа (10) и соответствующая графическая интерпретация мо-дели (см. рис.3). Например, если заданной величиной при отработке долота является углубление за один оборот hоб, равное 1,3 мм (см. рис.3), то изменение частоты вращения от 100 до 170 мин-1 потребует повышения осевой нагрузки от 710 до 755 даН, что позволит сохранить величину углубления 1,3 мм и повысить механическую скорость с 7,8 до 13,3 м/ч.
Подобные эмпирические модели, полученные в интерактивном режиме, и их интерпретация позволяют оперативно управлять режимами бурения в области, которая обеспечивает рацио-нальную отработку долот.
При отработке бурового инструмента наиболее оптимальным является режим объемного разрушения горной породы. Тем не менее, в процессе проходки на длительном интервале, когда происходит смена горных пород разной степени буримости, наступает износ вооружения долот, меняется объем образующегося шлама и условия очистки забоя от выбуренной породы, количество подаваемого к забою очистного агента, режим бурения может меняться, отклоняясь от благоприятного объемного режима разрушения горных пород в область менее эффективного усталостно-поверхностного режима разрушения.

Например, в ходе износа долота или при смене мягкой горной породы более твердой, режим разрушения может стать усталостно-поверхностным. Возможен вариант зашламования забоя при недостаточной промывке или напротив, может наступить момент, когда чрезмерная подача бурового раствора приведет в гидроподпору торцевой части долота, или случай перегрева вооружения долота и, как следствие, его активное термомеханическое разрушение.
Интерактивная поддержка отработки долота в каждом из перечисленных случаев, учитывая установленные зависимости между углублением за один оборот долота на забое и параметрами режима бурения, позволяет проводить своевременную и оптимальную корректировку условий отработки долота.
На рис.7 представлена схема, содержащая возможные варианты режима отработки долота и способы их распознавания по соотношению углубления за один оборот и частоты вращения долота.
При отработке долота могут наступать с некоторым чередованием следующие режимы работы инструмента:
• I – усталостно-поверхностное разрушение;
• III – возврат к усталостно-поверхностному разрушению, может быть вызвано повышением твердости горой породы, зашламованием забоя, изнашиванием вооружения долота, гидроподпором долота потоком бурового раствора;
• IV – усталостно-поверхностное разрушение, может быть вызвано повышением твердости горой породы, зашламованием забоя, изнашиванием вооружения долота, гидроподпором долота потоком бурового раствора;
• V – возврат к объемному разрушению;
• VI – объемное разрушение на новом уровне осевой нагрузки;
• VII, VIII – повторение режимов III, IV;
IX, X – возврат к объемному разрушению и объемное разрушение на новом уровне осевой нагрузки;
• XII, XIII – переход и режим термомеханического разрушения бурового инструмента при чрезмерной осевой нагрузке (во многом аналогичен режимам III, IV).
Заключение. Таким образом, принимая во внимание изложенные в работе теоретические положения и примеры практической апробации методики управления процессом бурения долотами с резцами PDC, с учетом сил сопротивления при бурении, возможно произвести автоматизацию процесса с применением предложенной методики по представленному алгоритму поиска оптимальных условий протекания процесса по трем основным критериям (частота вращения, осевая нагрузка и величина углубления за один оборот бурового инструмента) с учетом поступающей в режиме реального времени информации о протекании процесса.
Помимо управления процессом в оптимальном диапазоне значений характеристик процесса, используя методику отработки долот с применением эмпирических моделей интерактивного управления процессом бурения, можно распознавать забойные ситуации и управлять параметрами режима, как для выхода из неблагоприятных условий бурения, так и для выбора оптимальных параметров режима при отработке долот по заданной величине углубления за один оборот инструмента на забое скважины.
Представленная в статье методика управления процессом бурения может найти применение при бурении скважин как на твердые полезные ископаемые, так и на нефть и газ относительно небольшой протяженности (до 1000-1500 м), ввиду того, что при более значительных величинах глубины буримых скважин нарастает влияние на процесс управления деструктивных факторов, таких как повышающееся горное давление, оказывающее влияние на физико-механические свойства буримых горных пород. Большая протяженность бурильной колонны в совокупности с возможной сложностью профиля скважины приводит к увеличению потерь мощности на трение колонны и возникновению колебательных процессов, что негативно влияет на передачу осевой нагрузки и частоты вращения долоту от устья скважины.
Литература