Use of clay-containing waste as pozzolanic additives
- 1 — Ph.D. Associate Professor Saint Petersburg Mining University ▪ Orcid
- 2 — Ph.D., Dr.Sci. Chief Researcher NPK “Mekhanobr-tekhnika” (AO) ▪ Orcid
- 3 — Ph.D. Associate Professor Saint Petersburg Mining University ▪ Orcid
Abstract
Growing productivity of mining and processing enterprises entails an increase in the volumes of liquid tailings impoundments and upstream impoundments of ore processing waste. Enterprises face the challenge of minimizing the environmental impact of waste and guaranteeing the sanitary and epidemiological safety of population. The article presents a possibility of recycling one type of such waste (clay-containing concentration tailings of apatite-nepheline and sylvinite ores, coal beneficiation tailings) by using them after preliminary thermochemical treatment as pozzolanic additives to cements and concretes, including concrete mixtures used for soil stabilization, development of territories, reclamation of mine workings, as a component of the insulating layer of landfills for the disposal of municipal solid waste. An analysis of the phase changes of kaolinite, one of the main minerals that make up clay-containing waste, in the temperature range of 200-1,000 °С showed that a change in its mineral form during heat treatment is the main factor in changing its pozzolanic activity. The effect of heat treatment of clay minerals at temperature of 700-800 °C on their pozzolanic activity, estimated by the ability to absorb calcium hydroxide (0.7 g Ca(OH) 2 per 1 g of modified kaolinite), is considered. It is shown that the addition of heat-treated samples (20 % by weight) improves the quality of cement increasing its activity by 15 %, in comparison with the use of unmodified clay minerals. It was proved experimentally that partial replacement of Portland cement with thermally modified kaolinite increases the strength of consolidating stowing mixture by up to 15 %. This approach to processing of ores containing layered silicates, which provides for thermochemical modification of run-of-mine ore, intensifies the processes of tailings thickening and filtering.
Introduction
A significant part of all minerals extracted from the Earth (coal, oil, salts, iron, manganese and aluminium ores, gold and platinum placers, phosphorites, non-metallic building materials, etc.) is enclosed in sedimentary rocks. Clay minerals (clays, mudstones, etc.) predominate among sedimentary rocks, the content of which is up to 50 %.
Many mineral deposits are associated with the presence (as waste rock in them) of clays, mudstones, clay shales composed of layered silicates, highly hydrophilic mineral varieties, which can swell in water. This ability to self-disperse causes great difficulties both in the extraction and processing of such ores. Concentration tailings of ores and coals containing clay minerals create serious problems during storage and disposal, which are exacerbated by process water rotation, since swelling layered silicates (clay minerals) significantly complicate the compaction and dehydration of tailings suspensions.
Water became the scarcest resource at beneficiation plants, and a ubiquitous implementation of intra-factory process water rotation became a necessity. To organize it, it is necessary to achieve the maximum separation of the liquid phase from the solid phase of tailings, for which thickening and filtration operations are used. After these process operations, the mineral part is obtained with a minimum amount of water. Further, from the dehydrated mineral part, valuable products can be obtained that are used in different industries: construction, production of sorbents and refractory materials.
Presence of clay minerals that can retain water reduces the efficiency of these operations, which leads to a decrease in the volume of process water entering the water rotation system. Ways to reduce water content are considered in [1, 2]. In this article, the use of dried ore tailings containing clay minerals is considered.
Among the trends of recycling tailings containing clay minerals, their use as pozzolanic additives to cements (a mineral additive with the ability to bind Ca(OH)2 into stable hydrated forms) [3-5], and as a raw material to produce geopolymers is obvious [6-9]. Production of zeolites is one of the trends for recycling the concentration tailings [10].
Given the large formation volume of the ore concentration tailings containing layered silicates, their recycling is possible only in industries that also have a significant volume [11, 12]. In this regard, the cement industry and production of cement concretes are of greatest interest [13-15].
In the production of cement clinker a lot of fuel is consumed and a significant amount of carbon dioxide is released. Reduction of the share of clinker component and as a consequence minimization of these negative factors is possible due to the use of active mineral additives of natural and artificial origin [16-18].
Thermally activated clays are artificial pozzolans and are regulated by the European standard EN 197-1-2000 and the interstate standard GOST 24211-2008. From ancient times to the present, both natural and technogenic clay minerals were used as additives to cement materials. Pozzolanic activity of thermally activated clays in cement-lime composites depends on the degree of dehydration and chemical transformation of individual minerals during heat treatment [19-21].
In the course of heat treatment of clay minerals, new characteristics are acquired. After thermal activation of kaolinite its pozzolanic activity is much higher in comparison with other clay minerals, which is determined by the structure of kaolinite, in which the elementary package consists of two layers: silicon-oxygen tetrahedral and aluminium-oxygen octahedral having oxygen atoms [22-24].
Kaolinite is not a pozzolanic active additive; its activation (thermal) is required. It can be used as microfiller in Portland cement (in small quantities) due to its high dispersion. Kaolinite can accelerate the hydration of cement, increase compressive and flexural strength, reduce permeability, increase frost resistance, and reduce porosity.
During heat treatment of kaolinite in the range of 400-600 °С, dehydroxylation of the structure, amorphization, and the appearance of aluminium ions in coordination 5 after oxygen occur; this is what causes a high pozzolanic activity of the forming product, metakaolin [25].
In the process of dehydration of clay minerals in the range of 300-900 °С, crystallization water is removed from clay minerals (depending on the mineral variety) until the crystals are completely destroyed and the first eutectics and crystalline neoformations begin to form from the mixture of their oxides. At a temperature of 200 °C, clay activation can start before sintering begins. Different clay minerals have different temperature ranges characteristic of endothermic peaks. Polymineral clays, due to this, have much wider ranges than the monomineral form [26-28].
Methodology
In the previous studies, the authors [29] investigated the effect of different types of heating on silicate minerals: montmorillonite, illite, kaolinite, talc, as well as framework silicate – quartz, as an essential mineral of sedimentary clay rocks characterized by the minimal effect of water on its structural changes.
In this article, kaolinite obtained by beneficiation of kaolin ore from the Troshkovsky deposit is considered, which at heat treatment (convective; hydrothermal; in high-frequency currents; and combined) can change the mineral composition. To compare the thermal effect on clay minerals, montmorillonite was chosen, in which only dehydration occurs during heat treatment. Chemical composition of the materials used is given in Table 1.
Table 1
Chemical composition of silicate minerals, %
Material |
SiO2 |
Al2O3 |
Fe2O3 |
TiO2 |
CaO |
Na2O |
K2O |
MgO |
H2O |
LOI |
Kaolinite |
56.9 |
27.4 |
2.1 |
0.5 |
0.5 |
0.3 |
0.2 |
0.4 |
– |
11.7 |
Montmorillonite |
48.7 |
14.1 |
3.2 |
0.2 |
4.2 |
0.9 |
0.4 |
4.3 |
16.2 |
7.8 |
Kaolin tailings |
78.9 |
13.3 |
0.5 |
0.2 |
0.4 |
0.3 |
0.2 |
0.6 |
– |
5.6 |
In the study of samples conventional methods of analysis were applied. To determine the mass fraction of elements in the samples, an X-ray fluorescence spectrometer with a built-in diffractometer Thermo Fisher Scientific ARL 9900 WorkStation (SC Ecosystema) was used. Pozzolanic activity was determined by the Chapel method [30] from the absorption of Ca(OH)2. Changes in specific surface area of the materials were monitored using a “PSKh-10a” device. Analysis of the structural phase transformations of the studied materials was accomplished by X-ray diffraction (XRD) using a Bruker D8 focus X-ray diffractometer with a Siemens 7000 diffractometer (USA) with Cu-Kα radiation (40 kV, 30 mA, λ = 1.5406 Å). Strength was determined according to GOST 22690-2015. As a secondary tool for determining changes in the structure of minerals, a “Thermoscan-2” device was used, which makes it possible to carry out thermal gravimetric analysis (TGA) and differential thermal analysis (DTA). The material was exposed to temperatures in the range of 25-1,000 °С at atmospheric air pressure. Heating rate was 10 °C/min.
There are several ways to determine pozzolanic activity of minerals. The article [30] considers two methods: determination of the activity index based on strength and measurement of the amount of calcium hydroxide absorbed by the pozzolanic additive (French standard NF P18-513: 2010). These two methods are compared on a sample of metakaolin, and the methods for determining pozzolanic activity give comparable results [31-34].
The experiment according to the Chapel method was as follows [30]: 1 g of metakaolin/kaolinite and 2 g of freshly calcined CaO are placed in a 500 ml clean dry Erlenmeyer flask, and 200 ml of distilled water are added. The flask is hermetically sealed, a Liebig refrigerator is inserted and placed on a laboratory electrically heated magnetic stirrer. The experiment runs for 16 hours at a temperature of 85 °С with constant stirring of the flask contents with a magnetic stirrer. After stirring, the flask is cooled to room temperature. Next, 250 ml of freshly prepared sucrose solution (60 g of sucrose is dissolved in 250 ml of water) is added and stirred with a magnetic stirrer for 15 min. The content of the flask is then filtered through an ashless filter. A similar (blank) experiment is carried out without metakaolin/kaolinite. An aliquot (25 ml) is taken from the stock solution with a calibrated pipette and titrated with a 0.1N HCl burette using phenolphthalein (2-3 drops) as an indicator. The volume of 0.1N HCl used for titration of 25 ml solution of an empty (blank) sample V1 and the volume of 0.1N HCl used for titration of 25 ml of a solution obtained by reaction with metakaolin V2 are determined. Next, the amount of Ca(OH)2 absorbed by 1 g of metakaolin additive is calculated,
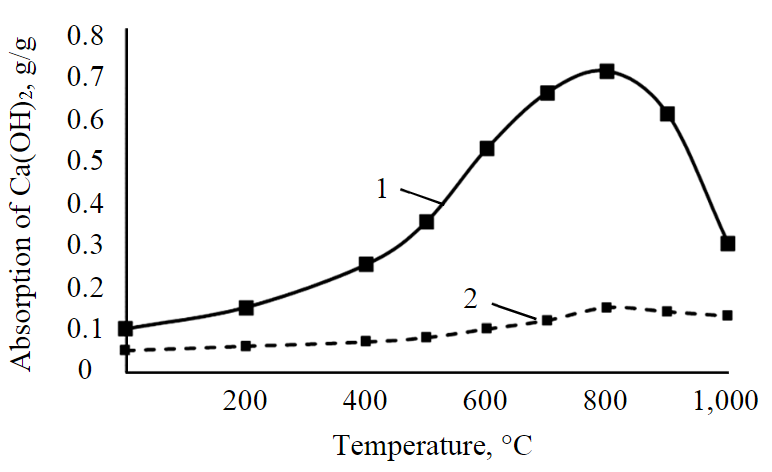
Fig.1. Effect of heat treatment on pozzolanic activity of kaolinite and montmorillonite 1 – kaolinite; 2 – montmorillonite
Discussion of results
A change in mineral form of kaolinite under thermal exposure affects its pozzolanic activity, which is estimated by the ability to absorb calcium hydroxide [35].
According to Fig.1, the growth of pozzolanic activity begins already at a material processing temperature of above 200 °С and reaches a maximum at a temperature of 800 °С; further, with increasing temperature, the pozzolanic activity of kaolinite decreases, which is associated with transition of metakaolin to mullite [36]. The process of calcium hydroxide absorption by heat-treated kaolinite requires a much longer time (from two hours). A comparative assessment of the effect of heat treatment of two minerals on the change in their activity showed that in the temperature range of 400-800 °С, an increase in pozzolanic activity is recorded only in kaolinite, while thermal effect on montmorillonite does not lead to any changes.
The results show that the change in the mineral form of kaolinite is the main factor of the change in its pozzolanic activity, and not the dehydration of clay, as reported in [37, 38].
During heat treatment of clays, the specific surface area (on the “PSKh-10a” device) of montmorillonite decreases due to its dehydration, while no changes are observed in kaolinite (Fig.2, а).
Analysis of weight loss of these minerals (Fig.2, b) suggests that phase composition of kaolinite changes in the temperature range of 400-600 °C, which correlates well with the data on differential thermal analysis (Fig.3).
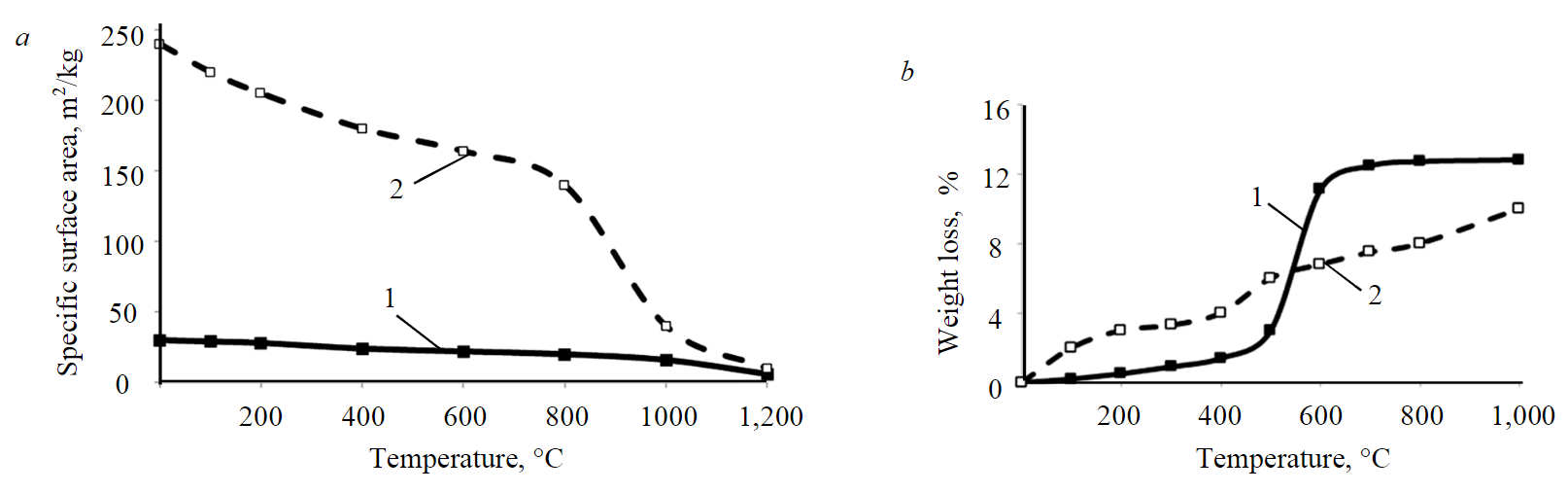
Fig.2. Effect of heat treatment on specific surface area (a) and dehydration (b) of kaolinite and montmorillonite 1 – kaolinite; 2 – montmorillonite
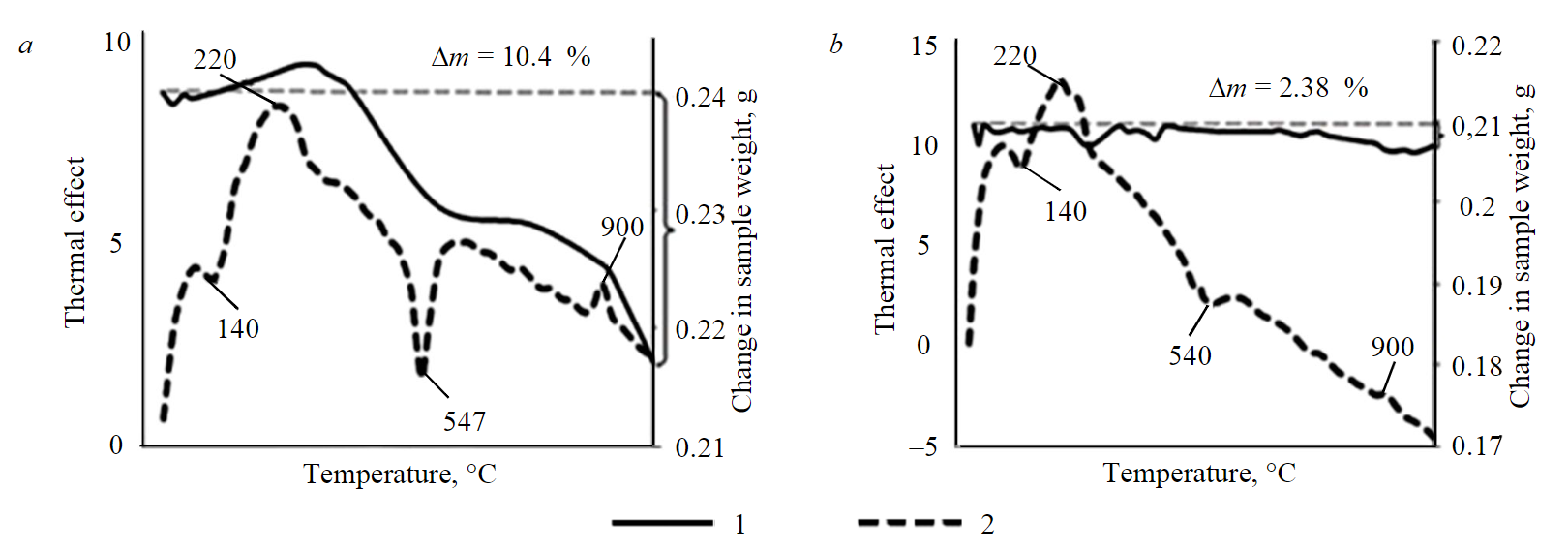
Fig.3. Differential thermal analysis of kaolinite samples: a – original sample; b – sample after heating (550 °С) 1 – weight loss; 2 – thermal impact
For this analysis, two samples of kaolinite were used: initial (without heat treatment) and after convective heating at 550 °C. The choice of temperatures and type of heating are described in detail in the research [29], which states that the types of heating (convective; hydrothermal; in high- frequency currents; and combined) have the same effect on the change in phase composition of the mineral and differ only in the rate at which this effect is achieved. According to this indicator, preference was given to convective heating.
The original sample of mineral raw material (Fig.3, a) has an endothermic effect, the peak of which falls at 140 °C. This effect is associated with removal of physically bound water from the channels and pores of the raw material with preservation of microstructure. The next endothermic effect peaks at 547 °C. This is the key effect, as it indicates a change in microstructure of the material and formation of metakaolin. The second endothermic peak of heat-treated material at 540 °C (Fig.3, b) is less intense than that of the original kaolinite. This indicates that kaolinite almost completely passed into another phase.
Data on the change in phase composition were determined by the X-ray diffraction method. During heat treatment kaolinite first transforms into metakaolin, which usually cannot be detected by the X-ray method [39]. XRD analysis showed that the height of kaolinite peak decreases after heat treatment (from 834 to 262 °С), and a new phase forms – dehydrated halloysite. Kaolinite and halloysite have a similar structure, but the latter has a certain amount of interlayer water (d = 9.5-10.2 Å). In the process of dehydration, the interplanar distance of halloysite decreases and becomes close to the value of kaolinite (d = 7.2 Å).
An increase in pozzolanic activity of kaolinite during heat treatment ensures its effect on the activity of Portland cement. It was shown in [38] that the maximum positive effect of the addition of thermally modified kaolinite is observed when its share in the binder is 20 %. Based on this, determination of the activity of the composite binder was performed on a mixture of kaolinite 20 % and cement of grade TsEM II/A-Sh 32.5N 80 %, with normal solution consistency. Kaolinite processed at different temperatures was added to the mixture. The best indicators of the activity of this binder were recorded after addition of kaolinite modified at 700 °С; the strength increased by 15 %.
In connection with a broader use of concentration tailings for backfilling the worked-out areas in mines and open pits, a possibility of using thermally modified kaolinite to replace part of Portland cement in stowing mixtures was tested. For this, the initial stowing mixture was prepared which contained 80 % of finely dispersed quartz (fineness modulus 1.5) and 20 % of binder – Portland cement. Thermally modified kaolinite was added to Portland cement, thus, the mixture contained 80 % quartz, 16 % Portland cement, 4 % kaolinite.
Studies have shown that partial replacement of Portland cement with thermally modified kaolinite increases the strength of the hardening stowing mixture by 20 % of initial compressive strength of 3.5 MPa. Partial replacement of the stowing mixture with heat-treated kaolinite gives another positive effect – disjoining pressure of the stowing mixture decreases, thus reducing the likelihood of its self-destruction when the mixture solidifies in the worked-out area. These results are confirmed by papers [35, 38] and are given in Table 2.
Table 2
Disjoining actions of stowing mixture of different composition [37]
Time, days |
Disjoining pressure of mixtures, MPa |
Time, days |
Disjoining pressure of mixtures, MPa |
|||
Portland cement 100 % |
Added kaolinite 20 % |
Portland cement100 % |
Added kaolinite 20 % |
|||
25 |
0.00 |
0.00 |
200 |
3.50 |
2.30 |
|
50 |
1.50 |
1.10 |
250 |
3.60 |
2.40 |
|
100 |
2.70 |
1.85 |
350 |
3.60 |
2.50
|
|
150 |
3.25 |
2.10 |
|
|
|
|
Coal tailings containing kaolinite are also of interest for use in stowing mixtures [40, 41]. For further research, beneficiation tailings of high-ash Vorkuta coals were used. The data on the effect of heat treatment of coal tailings containing 20 % kaolinite on the strength of Portland cement concrete after 28 days are presented (Table 3). Similar to other products based on kaolinite the maximum strength of concrete is recorded at a material processing temperature of 700 °С; the strength increases by 10 %.
The influence of heat treatment time of coal tailings on the modification degree was studied. It is shown that with an increase in processing time to 90 min, the strength of the mixture increases by 10-12 MPa.
Table 3
Effect of heat treatment time of coal tailings containing 20 % kaolinite on the strength of Portland cement concrete (tailings:cement 1:3) after 28 days
Time of heat treatment, min |
Strength at heat treatment, MPa |
Time of heat treatment, min |
Strength at heat treatment, MPa |
||||
500 °С |
600 °С |
700 °С |
500 °С |
600 °С |
700 °С |
||
0 |
30.0 |
30.0 |
30.0 |
40 |
39.8 |
42.5 |
43.9 |
20 |
35.7 |
38.5 |
40.0 |
60 |
41.0 |
43.0 |
44.5 |
30 |
38.2 |
41.5 |
42.8 |
90 |
40.0 |
44.0 |
42.5 |
Thus, it can be concluded that preliminary thermal treatment of concentration tailings of various ores containing clay minerals makes it possible to use this type of raw material, for example, in the construction industry as an additive to cements, and to create conditions for their disposal as part of stowing mixtures.
Conclusion. As a result of studying the effect of thermal modification of clay-containing ores and coals before their beneficiation on the processes of dehydration and disposal of tailings, the following was ascertained:
- during heat treatment of kaolinite, the growth of pozzolanic activity begins already at a temperature above 200 °С and reaches a maximum at a temperature of 800 °С; further, with increasing temperature, pozzolanic activity of kaolinite decreases, which is associated with transition of metakaolin to mullite;
- change in mineral form of kaolinite is the main factor in changing its pozzolanic activity (rather than dehydration of clay, as previously presumed);
- heat treatment does not lead to a change in specific surface area of kaolinite;
- an increase in pozzolanic activity of kaolinite during heat treatment shows up in its effect on the strength of Portland cement concrete – the addition of heat-treated samples (20 % by weight) improves the quality of cement increasing its strength by 15 %;
- partial replacement of Portland cement with thermally modified kaolinite increases the strength of the hardening stowing mixture by 20 %; thermally activated kaolinite contained in tailings has a higher pozzolanic activity than kaolinite without activation, which allows to use the concentration tailings of thermally modified ores and coals (at 700-800 °С) as pozzolanic additives to cements and concretes.
The obtained results indicate that such an approach to the processing of ores containing layered silicates, which provides for thermochemical modification of run-of-mine ore, creates favourable prerequisites for using the concentration tailings of these ores as pozzolanic additives to cements and concretes. For example, they can be added to concrete mixtures used in soil stabilization; territory improvement; mine workings reclamation; and also as a component of insulating layer of municipal solid waste landfills.
References
- EhsaniM., Unesi M., Tamartash R. Clay sedimentation and consolidation behavior in tailing storage facilities over mine lifetime. Journal of Mining and Environment. 2019. Vol. 10. N 1, p. 113-124. DOI: 10.22044/jme.2018.7165.1569
- Islam, Williams D.J., Liano-Serna M., Chenming Zhang. Settling, consolidation and shear strength behavior of coal tailings slurry. International Journal of Mining Science and Technology. 2020. Vol. 30. Iss. 6, p. 849-857. DOI: 10.1016/j.ijmst.2020.03.013
- Javrujan H.S., Gaishun E.S., Mirina V.A. Innovative additives in the production of wall ceramics. Engineering Journal of Don. N 4, p. 2007-2016 (in Russian).
- Kulikova M.A. Justification of the necessity of forming a protective screen for dumping waste dumps in the development fields. Journal of Mining Institute. Vol. 203, p. 185-189 (in Russian).
- Arsentev V.A., Gerasimov A.M. Use of Clay-Containing Tailings in Geopolymer Production. Tsvetnye metally. N 11, p. 58-62 (in Russian). DOI: 10.17580/tsm.2021.11.08
- Mifeng Gou, Longfei Zhou, Nathalene Wei Ying Then. Utilization of tailings in cement and concrete: A review. Science and Engineering of Composite Materials. 2019. Vol. 26. Iss. 1, p. 449-464. DOI: 10.1515/secm-2019-0029
- Obenaus-Emler R., Illikainen M., Falah M. Geopolymers from mining tailings for more sustainable raw material supply. MATEC Web of Conferences. 2019. Vol. 274. N 05001. DOI: 10.1051/matecconf/201927405001
- Paiva H., Yliniemi J., Illikainen M. Mine tailings geopolymers as a waste management solution for a more sustainable habitat. Sustainability. 2019. Vol. 11. Iss. 4. N 995. DOI: 10.3390/su11040995
- Feng Rao, Qi Liu. Geopolymerization and its potential application in mine tailings consolidation: A review. Mineral Processing and Extractive Metallurgy Review. 2015. Vol. 36. Iss. 6, p. 399-409. DOI: 10.1080/08827508.2015.1055625
- Hartati, Prasetyoko D., Santoso M. et al. A review on synthesis of kaolin-based zeolite and the effect of impurities. Journal of the Chinese Chemical Society. 2020. Vol. 67. Iss. 6, p. 911-936. DOI: 10.1002/jccs.201900047
- Ermilova E.Yu., Kamalova Z.A., Rakhimov R.Z. The clay of Koschakovsky field of Тatarstan Republic as a component of hybrid additive to blended portland cement. News of the Kazan State University of Architecture and Engineering. 2015. N 4 (34), 259-263 (in Russian).
- Rakhimov R.Z., Rakhimova N.R., Gaifullin A.R., Morozov V.P. Dehydration of clays of different mineral composition during calcination. News of the Kazan State University of Architecture and Engineering. N 4 (38), p. 388-394 (in Russian).
- Shishakina O.A., Palamarchuk A.A. Technology Overview of Technology Waste Disposal in the Manufacture of Construction Materials. International Journal of Applied and Fundamental Research. N 4, p. 198-203 (in Russian).
- Chukaeva M.A., Matveeva V.A., Sverchkov I.P. Complex processing of high-carbon ash and slag waste. Journal of Mining Institute. Vol. 253, p. 97-104. DOI: 10.31897/PMI.2022.5
- Arsentev V.A., Marmandyan V.Z., Samukov A.D., Kabirov A.M. Innovate technologies in waste of extraction and nonmetallic raw materials processing. Journal of Mining Institute. Vol. 198, p. 219-222 (in Russian).
- Lalomov D.A., Glazunov V.V. Collaborative interpretation of the data obtained by resistivity and ground penetrating radar methods for assessing the permeability of sandy clay soils. Journal of Mining Institute. Vol. 229, p. 3-12. DOI: 10.25515/PMI.2018.1.3
- Litvinova T.E., Suchkov D.V. Comprehensive approach to the utilisation of technogenic waste from the mineral resource Mining informational and analytical bulletin. 2022. Iss. 6-1, p. 331-348 (in Russian). DOI: 10.25018/0236_1493_2022_61_0_331
- Danilov A.S., Matveeva V.A., Korelskiy D.S., Horttanainen M. Backfill of a Mined-Out Gold Ore Deposit with the Cemented Rubber-Cord and Waste Rock Paste: Environmental Changes in Aqueous Media. Journal of Ecological Engineering. 2021. Vol. 22. N 7, p. 190-203. DOI: 10.12911/22998993/138870
- Klyuev S., Sevostyanov V., Sevostyanov M. et al. Improvement of technical means for recycling of technogenic waste to construction fiber. Case Studies in Construction Materials. 2022. Vol. 16. N e01071. DOI: 10.1016/j.cscm.2022.e01071
- Zubkova O., Alexeev A., Polyanskiy A. et al. Complex Processing of Saponite Waste from a Diamond-Mining Enterprise. Applied Sciences. Vol. 11. Iss. 14. N 6615. DOI: 10.3390/app11146615
- Kutepov Yu.I., Kutepova N.A., Vasileva A.D., Mukhina A.S. Engineering-geological and eco-logical concerns in operation and reclamation of high slope dumps at open-pit mines in Kuzbass. Mining informational and analytical bulletin. Iss. 8, p. 164-178 (in Russian). DOI: 10.25018/0236_1493_2021_8_0_164
- Dubovikov O.A., Brichkin V.N. Directions and prospects of using low grade process fuel to produce alumina. Journal of Mining Institute. Vol. 220, p. 587-594.
- Dubovikov O.A., Brichkin V.N., Ris A.D., Sundurov A.V. Thermochemical activation of hydrated aluminosilicates and its importance for alumina production. Non-ferrous Metals. 2018. N 2, p. 10-15. DOI: 10.17580/nfm.2018.02.02
- Kotova O.B., Ustyugov V.A., Shiyong Sun, Ponaryadov A.V. Mullite production: phase trans-formations of kaolinite, thermodynamics of the process. Journal of Mining Institute. Vol. 254, p. 129-135. DOI: 10.31897/PMI.2022.43
- Erasmus E. The influence of thermal treatment on properties of kaolin. Hemijska industrija. 2016. Vol. 70. Iss. 5, 595-601. DOI: 10.2298/HEMIND150720066E
- Pashkevich М.А., Petrova Т.А.Recyclability of Ore Beneficiation Wastes at the Lomonosov Deposit. Journal of Ecological Engineering. 2019. Vol. 20. Iss. 2, p. 27-33. DOI: 10.12911/22998993/94919
- Kuznetsov V.S., Suprun I.K. Reduction of an Adverse Impact During Well Drilling by Means of Drilling Waste Usage. Journal of Ecological Engineering. 2017. Vol. 18. Iss. 2, p. 12-15. DOI: 10.12911/22998993/68211
- Dashko R.E., Lokhmatikov G.A. The Upper Kotlin clays of the Saint Petersburg region as a foundation and medium for unique facilities: an engineering-geological and geotechnical analysis. Journal of Mining Institute. Vol. 254, p. 180-190. DOI: 10.31897/PMI.2022.13
- Gerasimov A.M., Eremina O.V. Application Microwave Radiation for Directional Changes of Layered Silicates Properties. Eurasian Mining. 2021. N 1, p. 55-60. DOI: 10.17580/em.2021.01.11
- Zyryanov M.S., Ahmetzhanov A.M., Manushina A.S., Potapova E.N. Determination of puzzolanic activity of metakaolins abstract. Advances in Chemistry and Chemical Technology. Vol. 30. N 7, p. 44-46 (in Russian).
- Rakhimov R.Z., Rakhimova N.R., Stoyanov O.V. Clay pozzolans. Part 1. Review. Bulletin of the Technological University. Vol. 19. N 1, p. 5-13 (in Russian).
- Salau M.A., Osemeke O.J. Effects of Temperature on the Pozzolanic Characteristics of Metakaolin-Concrete. Physical Science International Journal. 2015. Vol. 6. N 3, p. 131-143. DOI: 10.9734/psij/2015/13146
- Juanrong Zheng, Lijie Guo, Zhenbo Zhao. Effect of calcined hard kaolin dosage on strength development of CPB of fine tailings with sulphide. Advances in Materials Science and Engineering. Vol. 2017. N 8631074. DOI: 10.1155/2017/8631074
- Ferraz E., Slávka A., Walid H. et al. Pozzolanic activity of metakaolins by the French Standard of the modified Chapelle Test: A direct methodology. Acta Geodynamica et Geomaterialia. 2015. Vol. 12. N 3, p. 289-298. DOI: 10.13168/AGG.2015.0026
- Zhao Cao, Yongdan Cao, Hongjuan Dong et al. Effect of calcination condition on the microstructure and pozzolanic activity of calcined coal gangue. International Journal of Mineral Processing. 2016. Vol. 146, p. 23-28. DOI: 10.1016/j.minpro.2015.11.008
- Sivkov S.P., Potapova E.N., Zakharov S.A., Nazarov D.V. Hydration and Hardening of Cement in the Presence of Metakaolin. ALITinform: Cement. Concrete. Dry Mixtures. N 1, p. 80-89 (in Russian).
- Amran M., Fediuk R., Klyuev S., Qader D.N. Sustainable development of basalt fiber-reinforced high-strength eco-friendly concrete with a modified composite binder. Case Studies in Construction Materials. 2022. Vol. 17. N e01550. DOI: 10.1016/j.cscm.2022.e01550
- QiaoC., Si P., Yu J.G. A Systematic Investigation into the Extraction of Aluminum from Coal Spoil through Kaolinite. Environmental Science & Technology. 2008. Vol. 42. Iss. 22, p. 8541-8546. DOI: 10.1021/es801798u
- Pashkevich M.A., Alekseenko A.V. Reutilization Prospects of Diamond Clay Tailings at the Lomonosov Mine, Northwestern Russia. 2020. N 10. N 517. DOI: 10.3390/min10060517
- Nazarenko M.Yu., Kondrasheva N.K., Saltykova S.N. The characteristic of waste of oil shale processing for use as filtering materials. Water and Ecology. Vol. 23. Iss. 1, p. 9-16 (in Russian). DOI: 10.23968/2305-3488.2018.23.1.9-16
- Ivkin A.S., Vasiliev V.V., Salamatova E.V. et al. Adhesion of Bitumen to Minerals. Coke and Chemistry. 2022. Vol. 65, p. 24-32. DOI: 10.3103/S1068364X22010033