Sorption purification of acid storage facility water from iron and titanium on organic polymeric materials
- 1 — Ph.D., Dr.Sci. Head of the Department Saint Petersburg Mining University ▪ Orcid ▪ Scopus
- 2 — Ph.D. Assistant Lecturer Saint Petersburg Mining University ▪ Orcid ▪ Scopus
- 3 — Laboratory Assistant Saint Petersburg Mining University ▪ Orcid
- 4 — Laboratory Assistant Saint Petersburg Mining University ▪ Orcid
- 5 — Postgraduate Student Saint Petersburg Mining University ▪ Orcid
Abstract
Obtaining and production of metals from natural raw materials causes a large amount of liquid, solid, and gaseous wastes of various hazard classes that have a negative impact on the environment. In the production of titanium dioxide from ilmenite concentrate, hydrolytic sulphuric acid is formed, which includes various metal cations, their main part is iron (III) and titanium (IV) cations. Hydrolytic acid waste is sent to acid storage facilities, which have a high environmental load. The article describes the technology of ion exchange wastewater treatment of acid storage facility from iron (III) and titanium (IV) cations, which form compounds with sulphate ions and components of organic waste in acidic environments. These compounds are subjected to dispersion and dust loss during the evaporation of a water technogenic facility, especially in summer season. Sorption of complex iron (III) cations [FeSO4]+ and titanyl cations TiO2+ from sulphuric acid solutions on cation exchange resins KU-2-8, Puromet MTS9580, and Puromet MTS9560 was studied. Sorption isotherms were obtained both for individual [FeSO4]+ and TiO2+ cations and in the joint presence. The values of the equilibrium constants at a temperature of 298 K and the changes in the Gibbs energy are estimated. The capacitive characteristics of the sorbent were determined for individual cations and in the joint presence.
Introduction
Titanium production is a source of a large amount of liquid, solid, and gaseous wastes [1-3]. Within the framework of industrial environmental control, enterprises monitor the atmosphere, soils, and water bodies to assess the negative impact of production on the environment (EIA) [4, 5]. Currently, special attention is paid to the environmental safety of production and waste disposal [6, 7]. The global trend is the use of industrial waste as an alternative secondary source for obtaining valuable components [8-10].
Production waste is disposed of in an acid storage facility, the composition of which and the volume of technogenic wastewater with low pH values have a significant impact on the state of the environment [11, 12].
The most well-known large-scale waste of the titanium industry is hydrolytic sulphuric acid, which contains a large amount of iron and titanium cations, which belongs to hazard class II and is an extremely toxic substance, irritates the skin and causes pulmonary edema.
In a sulphuric acid solution, iron and titanium cations form chemical compounds characterized by a high degree of toxicity. As the operating time of the acid storage facility increases and the amount of fresh water that contributes to the dilution of hydrolytic sulphuric acid decreases, there is a tendency for the water level in the storage facility to drop below the critical level, which leads to the drying of the technogenic facility, and, as a result, to evaporation of sulphuric and sulphurous anhydrides, as well as dust formation of iron and titanium compounds. Chemical compounds of these metals, characterized by a high degree of dispersity, belong to hazard class II and cause damage to the upper respiratory tract [13]. An increase in ambient temperature in summer provokes intensive evaporation of other toxic compounds that are not products of ilmenite processing. Compounds also containing chlorine and fluorine of organic origin enter the atmosphere in the gaseous state [14].
In 2018, an environmental accident was recorded in one of the Russian towns associated with the spread of sulphur dioxide, titanium chloride, and iron from a titanium acid storage facility, which led to the evacuation of the town’s residents. The cause of the environmental catastrophe was explained by the presence of more than 20 million m3 of sulphuric acid wastewater containing at least 864,000 tons of commercial sulphuric acid [15].
The sulphuric acid aerosol formed in the atmosphere with the exhaust gases of titanium production at the stages of raw materials decomposition falls out in the form of acid rain during drying and calcination even at low atmospheric pressures. Suspended particles of iron and titanium compounds contained in sulphuric acid vapour act as a seed phase, the degree of curvature of which, according to the principle of isothermal distillation, determines the growth of droplets and the maturation of acid precipitation.
Considering the concentration characteristics of acid storage facilities, wastewater with a pH value much less than unity is a potential source of large-scale environmental problems at the regional and federal levels.
The impact of acid storage facility water on the hydrosphere is assessed by monitoring surface water bodies in the area of the waste disposal facility. When analysing the data on the composition of pollutants presented for 2018, a significant excesses of the MPC for sulphate anions, chloride anions, manganese, iron, and titanium was found in the vast majority of measurements. In some cases, there are excesses of MPC for arsenic and lead.
It should be noted the inevitable processes associated with the neutralization of acid storage facility water with alkaline process water, which leads to the precipitation of iron and titanium hydroxides or their compounds in the form of basic salts. Getting into such conditions, metals accumulate at the bottom of reservoirs.
The simplest way to reduce the acid load on the environment is to neutralize the acid storage facility water with alkaline agents, which is economically feasible. The use of a more economical neutralization component – calcium carbonate, or quicklime, can increase the pH of wastewater. However, as a result, an amount of calcium sulphate that is practically insoluble in any media is formed, equivalent to the spent acid. Thousands of tons of insoluble gypsum formed during neutralization of hydrolytic sulphuric acid will provoke the alienation of adjacent populated areas, so the neutralization technology is not progressive, meeting the principles of “green chemistry”. That is why the task of utilizing acidic water for ilmenite ore processing enterprises is extremely relevant, and the solution of this problem will allow the enterprise to create a closed water cycle.
First of all, it is necessary to purify wastewater from iron and titanium, the compounds of which form volatile components in the conditions of elevated ambient temperatures and discharges of organic waste into the acid storage facility. It is rational to use sulphuric acid purified from admixture compounds in the main technology for mineral concentrate recovery, which, in turn, will significantly increase the level of resource saving in production.
The main methods of purification of process waters of various composition from metals used on an industrial scale are extraction [16, 17], sorption [18-21] (in particular, ion exchange [22, 23]), and flotation [24, 25]. Membrane methods of wastewater treatment [26] and coagulation [27] are also widely used.
In [28, 29], titanium and iron extraction from acidic solutions of titanium production and ilmenite processing was studied. Organophosphorus acids were used as extractants. The maximum degree of extraction of titanium (IV) was 100 % when using D2EHPA and EHEHPA extractants; for iron, the degree of extraction was 95.6 and 98.9 %, respectively. The extraction method of cleaning any production facilities is the most effective; however, the use of organic extractants and solvents requires special safety measures for the operations with flammable and explosive substances [30].
More comfortable and less aggressive in relation to the environment conditions for the processing of technogenic facilities are provided by the use of sorption methods. The use of solid regenerable sorption materials [31] eliminates the use of volatile solvents and ensures the selective extraction of components, including from complex salt systems with high or low pH [32]. As sorption materials, both natural economically available materials [33] and synthesized organic polymer resins are used, which are capable of exhibiting greater selectivity with respect to individual components [34, 35].
Determination of the thermodynamic parameters of the sorption of titanium (IV) and iron (III) ions will make it possible to predict their extraction and purification of acid solutions, which is the scientific basis for the development of a process for the recovery of aggressive components of an acid storage facility and a condition for determining the parameters of sorption plants for wastewater treatment from aggressive components with the associated extraction of valuable metals [36, 37].
Methods
Investigation of the composition of acid storage facility water as a source of pollution
To study the composition of the acid storage facility water, sampling was carried out at a temperature of 30-32 °C. The preparation of liquid samples before analysis consisted in the removal of suspended particles by filtration using a vacuum filter, if necessary, additional filtration operations were performed.
Analysis of the chemical composition, qualitative and quantitative determination of the substances contained were carried out using an inductively coupled plasma emission spectrometer ICPE-9000 Shimadzu (Japan), providing for the necessary dilution of samples 100 and 1000 times.
The content of anions in water samples of the acid storage facility was analysed by chromatography using an LC-20 Shimadzu liquid chromatograph (Japan). During the measurement, the studied samples were diluted 1000 times with distilled water, after which they were subjected to compression filtration to remove organic compounds on special filters (Strata C18-E). Determination of the concentrations of sulphate anions was carried out at a dilution of 20,000 times.
To determine nitrate ions and ammonium cations, an ATP-02 potentiometric automatic titrator manufactured by NPK Akvilon (Russia) with ion-selective electrodes was used.
Preparation of sorption organic polymeric materials
The choice of cation exchange resin is due, first of all, to the availability of ion exchange material in the domestic resin market, low cost, and satisfactory efficiency of use. These criteria are met by the domestic cation exchange resin KU-2-8, which is a strongly acidic gel-type resin obtained by sulphonation of a copolymer of styrene with divinylbenzene, as well as cation exchange resins manufactured by Purolite Ltd: Puromet MTS9580 and Puromet MTS9560, the matrix of which is a macroporous polystyrene framework cross-linked with divinylbenzene. The functional group of the MTS9560 cation exchange resin is represented by phosphonic acid, while the MTS9580 cation exchange resin contains cation-selective chelate groups.
Before the studies, the cation exchange resins were converted into the H+ form by immersion in a sodium sulphate solution with a concentration of 2 mol/l for 24 h, decantation, and placement in a solution of 2 N sulphuric acid for 2-3 h. After appropriate procedures, the ion exchange resin was separated from the sulphuric acid solution and washed with distilled water until pH = 5.
Sorption in static conditions
The sorption was carried out from acidic solutions, simulating the composition of the process waters of the acid storage facility in the production of titanium dioxide.
Iron (III) salt solutions were prepared from chemically pure iron (III) sulphate; titanium (IV) salt solutions were prepared from a 15 % solution of titanium sulphate (III). Titanium (III) sulphate solution was left in contact with air for a day, as a result of which the solution became colourless with the formation of titanyl cations TiO2+.
Quantitative content of individual components in model solutions: iron (III) 0.6-107.6 mmol/l, titanium (IV) in the form of titanyl – 0.4-215.7 mmol/l. When studying the sorption of iron (III) and titanium (IV) in the joint presence, the ratio of metal concentrations was set equal to 5:1 (iron (III) 5.8-591.1 mmol/l and titanium (IV) 1.3-118.5 mmol/l) in accordance with their quantitative ratio in a real solution. The pH value of the initial solutions was 0.3-0.5. The initial solutions were equilibrated with cation exchange resins for 2-3 h until equilibrium was reached, which was proved by the results of kinetic studies with constant stirring of 120 pumps/min at a temperature of 298 K.
To determine the optimal ratio of solid and liquid phases, experiments were carried out at s:l equal to 1:1, 1:5, 1:10, and 1:25 for all selected cation exchange resins. According to experimental data, the highest degree of extraction of iron (III) 43.5 % and titanium (IV) 94.9 % on the KU-2-8 cation exchange resin was achieved only at a phase ratio of 1:1, while the use of the cation exchange resin MTS9580 provides a high degree of extraction (Fe 84.9 %; Ti 96.8 %) with an increase in the phase ratio to 1:5, and the MTS9560 cation exchange resin (Fe 91.5 %; Ti 98.7 %) with a tenfold increase in the liquid phase (s:l = 1:10).
The sorption value was determined by the method of variable concentrations at a constant ratio of s:l
where C0, C∞ are the concentrations of iron (III) or titanium (IV) in the initial and equilibrium solution, respectively, mol/l; V is the solution volume, l; mkat is the mass of the cation exchange resin, kg.
Regeneration of cation exchange resins was carried out with a sulphuric acid solution with a concentration of 2 N. The concentration of iron (III) and titanium (IV) in sulphuric acid solutions was determined by titrimetric, photometric, and X-ray fluorescence methods on a PANalytical Epsilon 3 device (Netherlands).
Discussion of the results
Investigation of the composition of acid storage facility water as a source of pollution
According to the results of semi-quantitative analysis, the presence of the following elements in the composition of hydrolytic sulphuric acid was revealed: Al, B, Ba, Ca, Cr, Cu, Fe, K, Mg, Mn, Na, Ni, P, S, Sc, Sr, Ti, V, Z.
Quantitative content of elements in the acid storage facility water sample, mg/dm3: Al 4440; Ca 1410; Fe 44400; K 1270; Mg 15700; Na 22500; S91100; Ti 3250. The content of all elements exceeds the MPC established for them.
The content of sulphate ions in the acid storage facility water sample, g/l: SO42– 299.0; (converted from ICPE) 273.3.
The content of nitrates and ammonium ions is not so significant compared to macrocomponents and amounts to 23.7 and 10.1 mg/dm3, respectively.
Forms of existence of the iron ion (3+) in sulphuric acid solutions
To assess the forms of occurrence of iron cations (3+) and to establish the nature of sorption of ions by a certain type of cation exchange resin, a thermodynamic estimation of the iron (3+) sulphate complexes content in a solution of sulphuric acid was carried out. The formation of a complex iron ion of the first stage of coordination with the instability constant value KN = 6.6∙10–5 is expressed by the following equation [38]:
The total content of iron (III) in solution is the sum of iron (3+) cations and complex cations
In accordance with the reaction equation (1), the value of the instability constant is expressed:
where Πγ is the ratio of the activity coefficients of the corresponding ions; in square brackets are the equilibrium concentrations of ions.
After a series of mathematical transformations, the ratio of the content of complex cations to the total content of iron (III) in solution is obtained:
in which the values of the activity coefficients are calculated according to the Debye equation with the ionic strength of the solution from 0.8 to 1 mol/kg, corresponding to the ionic strength of a real sulphuric acid solution.
Based on the estimation performed, it was found that the Fe3+ ion is almost absent in the sulphuric acid solution, while the proportion of [FeSO4]+ complex cations is 99.9 %.
Ion exchange extraction of complex cations [FeSO4]+ in static conditions
Sorption isotherms of [FeSO4]+ complex cations on KU-2-8, MTS9580 and MT9560 cation exchange resins at the phase ratio corresponding to the maximum degree of extraction of the component are shown in Fig.1, a.
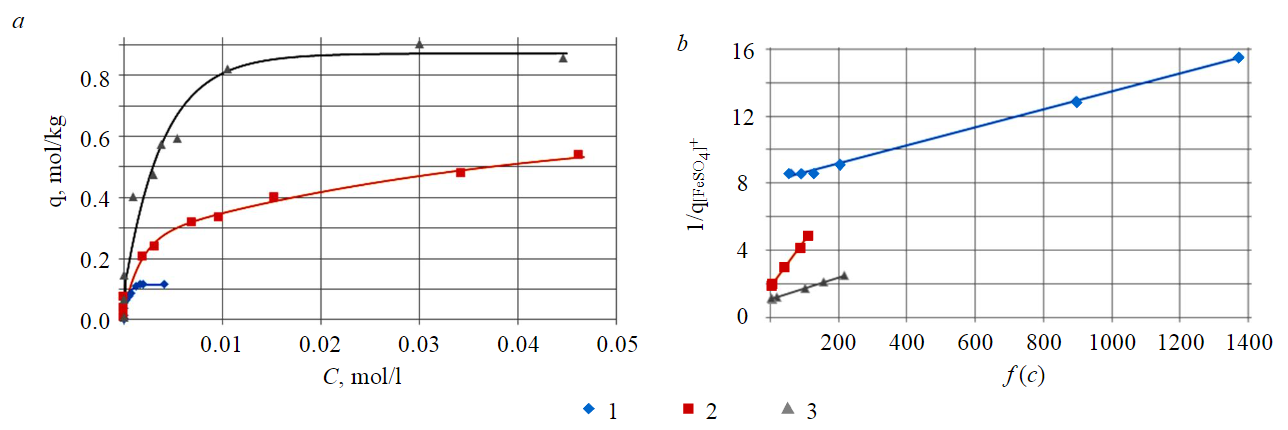
Fig.1. [FeSO4]+ sorption isotherms (a) and their linear forms (b) on cation exchange resins 1 – KU-2-8 (s:l = 1:1); 2 – MTS9580 (s:l = 1:5); 3 – MTS9560 (s:l = 1:10)
The thermodynamic description of sorption isotherms was made based on a linearized mass action law adapted to the ion exchange equation, with the assumption that the solid phase is ideal, and also considering the significant dependence of the activity coefficients on the ion charge, and insignificant dependence on its individual nature [39]. The ion exchange equation has the following form:
mass action law:
where K is the equilibrium constant; q∞ is the total capacity of the sorbent, mol/kg; aH+ , a[FeSO4] is the activity of the corresponding cation, mol/kg; γH+, γ[FeSO4]+ are the activity coefficients of the corresponding cations.
The linear form of the mass action law is obtained after a series of mathematical transformations. The activity coefficients of individual ions are expressed through the average ionic activity coefficients and are estimated on the basis of reference data at an ionic strength value of 0.75 to 0.97 mol/kg:
Expression (2) has the form of a linear equation y = tgaf(c) + b, where
Linear forms of sorption isotherms of the iron (III) complex ion, which are the dependence of the concentration argument
The graphical solution of this equation determines the thermodynamic characteristics of sorption, namely, the ion exchange equilibrium constant and the value of the change in the Gibbs energy, as well as the value of the total capacity of organic polymeric materials presented in Table 1.
Table 1
Thermodynamic and capacitive characteristics of [FeSO4]+ sorption on cation exchange resins
Cation exchange resin |
Approximation equation |
R2 |
qlim, mol/kg |
K |
–∆G298, kJ/mol |
KU-2-8 |
1/q = 0.0054f(c) + 8.0918 |
0.99 |
0.12±0.01 |
(1.25±0.06)∙108 |
46.16±2.31 |
MTS9580 |
1/q = 0.0277f(c) + 1.8284 |
–"– |
0.54±0.03 |
66.01±3.30 |
10.38±0.52 |
MTS9560 |
1/q = 0.0064f(c) + 1.098 |
–"– |
0.86±0.04 |
171.56±8.58 |
12.74±0.64 |
Based on the data from the table, it can be concluded that the MTS9560 cation exchange resin has the highest capacity for complex iron (III) ions. The values of total capacity and limiting sorption within a satisfactory error are consistent with each other for cation exchange resins MTS9560 and MTS9580. However, less significant capacitance characteristics correspond to the KU-2-8 cation exchange resin.
Ion exchange extraction of TiO2+ cations in static conditions
Sorption isotherms of titanyl ion on cation exchange resins are shown in Fig.2, a. The sorption isotherms were described using the linearized mass action law, modified to the ion exchange equation:
The expression for the ion exchange equilibrium constant is as follows:
the linear form of the expression is represented by the following equation:
According to the linear graphical dependence of the concentration argument
Table 2
Thermodynamic and capacitive characteristics of TiO2+ sorption on cation exchange resins
Cation exchange resin |
Approximation equation |
R2 |
qlim, mol/kg |
K |
–∆G298, kJ/mol |
KU-2-8 |
1/q = 0.0372f(c) + 2.8772 |
0.99 |
0.23±0.01 |
1495.53±74.78 |
18.10±0.91 |
MTS9580 |
1/q = 0.0626f(c) + 0.935 |
–"– |
0.81±0.04 |
55.77±2.79 |
9.96±0.50 |
MTS9560 |
1/q = 0.0017f(c) + 1.0242 |
–"– |
0.89±0.04 |
(9.07±0.45)∙104 |
28.27±1.41 |
It follows from Table 2 that the most effective cation exchange resin for titanium extraction in the form of a titanyl ion is MTS9560.
Ion exchange extraction of a mixture of titanium (IV) and iron (III) compounds
The characteristics of the joint sorption of iron (III) and titanium (IV) on cation exchange resins were estimated, obtained by linearization of sorption isotherms using a modification of the mass action law for complex iron (III) cations (2) and oxotitanium (IV) cation (3) (Table 3).
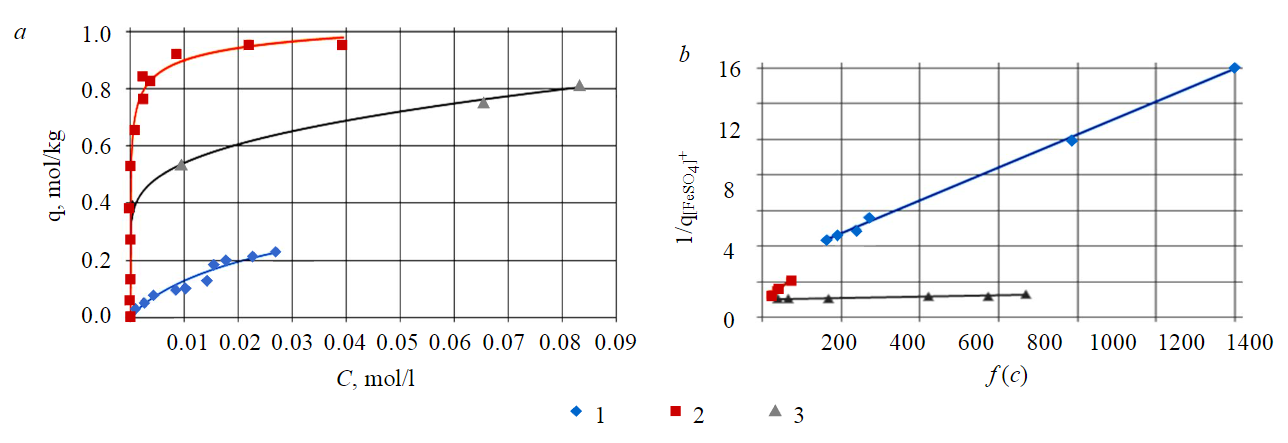
Fig.2. TiO2+ sorption isotherms on cation exchange resins (a) and their linear forms (b) on cation exchange resins 1 – KU-2-8 (s:l = 1:1); 2 – MTS9580 (s:l = 1:5); 3 – MTS9560 (s:l = 1:10)
Table 3
Thermodynamic and capacitance characteristics of joint sorption of [FeSO4]+ and TiO2+ on cation exchange resins
Cation exchange resin |
Cation |
Approximation equation |
R2 |
qlim, mol/kg |
KU-2-8 |
[FeSO4]+ |
1/q = 0.1233f(c) + 0.3401 |
0.99 |
0.55±0.03 |
TiO2+ |
1/q = 0.0432f(c) + 10.783 |
–"– |
0.10±0.01 |
|
MTS9580 |
[FeSO4]+ |
1/q = 0.2449f(c) + 1.322 |
–"– |
1.29±0.06 |
TiO2+ |
1/q = 0.0082f(c) + 3.848 |
–"– |
0.29±0.01 |
|
MTS9560 |
[FeSO4]+ |
1/q = 0.066f(c) + 0.4209 |
–"– |
1.42±0.07 |
TiO2+ |
1/q = 0.0024f(c) + 1.579 |
–"– |
0.77±0.04 |
With the joint sorption of titanyl and the iron (III) complex ion, an increase in the limiting capacity for iron (III) and a decrease in titanyl are observed on all cation exchange resins. This is obviously due to the individual characteristics of specific ions in solution and their activity coefficients. The oxotitanium cation in aqueous solutions tends to hydrolysis: TiO2+ + H2O = TiOOH+ + H+. Partially hydrolysed TiOOH+ ions, which have a lower charge compared to iron sulphate (III) cation, are less competitive in the ion exchange process.
The cation exchange resin KU-2-8 has a lower sorption capacity, which is explained by the peculiarity of its structure. Despite the common matrix of all tested polymer resins, which are the basis of the styrene-divinylbenzene copolymer, Puromet MTS9580 and Puromet MTS9560 cation exchange resins are macroporous ion exchangers with pore sizes exceeding the sizes of sorbed ions. The Puromet MTS9560 ion exchange resin contains a bispicolylamine functional group –H2N–CH2–C5H4N–, the nitrogen atoms, of which create an additional inductive effect on the sorbed cations, while the Puromet MTS9580 ion exchange material contains functional groups that form the stronger chelates with extractable cations, the greater the mass they have.
Thus, for ion exchange purification of acidic aqueous media containing iron and titanium ions, it is preferable to use macroporous cation exchange resins with a spongy structure.
Conclusion
Chemical industry enterprises and, in particular, manufacturers of titanium products, as a rule, are city-forming for any region, and it should be borne in mind that the receipt of income in city budgets is ensured by the vigorous activity of enterprises, which is inextricably linked with a significant amount of waste. Recovery of the process tank with hydrolytic sulphuric acid is possible due to the phased extraction of accompanying macrocomponents, which will ensure consistent purification of the acid to the production standards established by the industry regulations of the enterprise and will also allow the reuse of spent highly concentrated solutions of sulphuric acid in the main process of titanium production.
Thus, there is a need to prevent a negative impact on the environment by applying measures for the treatment of acid storage wastewater using modern organic polymeric materials.
The analysis of the acid storage facility waters as a source of environmental pollution was carried out, and their chemical composition was determined. The main components contained in process waters are identified: Al, Ca, Fe, K, Mg, Na, S, and Ti.
The sorption of iron (III) and titanium (IV) ions from sulphuric acid solutions with a pH value of 0.3-0.5, corresponding to the process waters of the acid storage facility, was studied. The ion exchange resins KU-2-8, Puromet MTS9580, and Puromet MTS9560, which have a similar styrene-divinylbenzene matrix, were used as the sorption material.
The results of thermodynamic estimation substantiate the existence of ionic forms of extractable components from the sulphuric acid solution, which have [FeSO4]+ and TiO2+ composition. The results of ion exchange extraction of both individual ions and their sum from solutions containing 0.10-10.55 mg/l of iron (III), 0.03-2.47 mg/l of titanium (IV), and 0.3-0.5 mol/l of sulphuric acid were obtained.
The values of ion exchange equilibrium constants and Gibbs energy changes, which determine the effective extraction of titanium and iron from process solutions, are estimated. Capacitive characteristics of polymeric sorbents are determined. The Puromet MTS9560 cation exchange resin has the highest capacity with respect to iron and titanium: for titanium, the sorption capacity was 0.89±0.04 mol/kg, for iron 0.86±0.04 mol/kg. With the joint presence of components, an increase in the sorption of iron to 1.42±0.07 mol/kg and a slight decrease for titanium to 0.77±0.04 mol/kg are observed.
References
- Chukaeva M.A., Matveeva V.A., Sverchkov I.P. Complex processing of high-carbon ash and slag waste. Journal of Mining Institute. Vol. 253, p. 97-104. DOI: 10.31897/PMI.2022.5
- Kudinova A.A., Poltoratckaya M.E., Gabdulkhakov R.R. et al. Parameters influence establishment of the petroleum coke genesis on the structure and properties of a highly porous carbon material obtained by activation of KOH. Journal of Porous Materials. 2022. Vol. 25. Iss. 5, p. 1599-1616. DOI: 10.1007/s10934-022-01287-1
- Ivanik S.A., Ilyukhin D.A. Flotation extraction of elemental sulfur from gold-bearing cakes. Journal of Mining Institute. Vol. 242, p. 202-208. DOI: 10.31897/PMI.2020.2.202
- Ahmed S.F., Mofijur M., Ahmed B. et al. Nanomaterials as a sustainable choice for treating wastewater. Environmental Research. 2022. Vol. 214. Part 1. N 113807. DOI: 10.1016/j.envres.2022.113807
- Tengfei Ma, Hanjin Luo, Kaibo Huang et al. Integrated ecological risk assessment of heavy metals in an oil shale mining area after restoration. Journal of Environmental Management. 2021. Vol. 300. N 113797. DOI: 10.1016/j.jenvman.2021.113797
- Litvinova T.E., Suchkov D.V. Comprehensive approach to the utilisation of technogenic waste from the mineral resource complex. Mining Informational and Analytical Bulletin. N 6-1, p. 331-348 (in Russian). DOI: 10.25018/0236_1493_2022_61_0_331
- Pashkevich M.A., Korotaeva A.E. Analysis of biological methods for quarry wastewater treatment from nitrogen compounds. Geology and Geophysics of Russian South. Vol. 11. N 4, p. 170-182 (in Russian). DOI: 10.46698/VNC.2021.87.18.014
- Pyagay I.N., Shaidulina A.A., Konoplin R.R. et al. Production of Amorphous Silicon Dioxide Derived from Aluminum Fluoride Industrial Waste and Consideration of the Possibility of Its Use as Al2O3-SiO2 Catalyst Supports. Catalysts. 2022. Vol. 12. N 2. N DOI: 10.3390/catal12020162
- Lutskiy D.S., Ignatovich A.S. Study on hydrometallurgical recovery of copper and rhenium in processing of substandard copper concentrates. Journal of Mining Institute. Vol. 251, p. 723-729. DOI: 10.31897/PMI.2021.5.11
- Yiqian Ma, Stopic S., Xakalashe B. et al. A cleaner approach for recovering Al and Ti from coal fly ash via microwave-assisted baking, leaching, and precipitation. Hydrometallurgy. 2021. Vol. 206. N DOI: 10.1016/j.hydromet.2021.105754
- Pfaff G. Titanium dioxide pigments. Physical Sciences Reviews. 2021. Vol. 6. Iss. 11, p. 679-696. DOI: 10.1515/psr-2020-0199
- Congxue Tian, Shuanghua Huang, Ying Yang. Anatase TiO2 white pigment production from unenriched industrial titanyl sulfate solution via short sulfate process. Dyes and Pigments. 2013. Vol. 96. Iss. 2, p. 609-613. DOI: 10.1016/j.dyepig.2012.09.016
- Medvedeva M.S., Ivanov S.V. Analysis of the negative impact of air pollution in the Republic of Crimea on the increase in diseases of bronchopulmonary pathology in this region. Modern Science. 2020. N 5-3, p. 454-459 (in Russian).
- Diakov N.N., Malchenko Yu.A., Lipchenko A.E. et al. “Crimean Titanium” Acid Plant, Ecological Crisis in the Northern Crimea (Armyansk) and Possible Ways of Its Decision. Ekologicheskaya bezopasnost pribrezhnoy i shelfovoy zon moray. N 1, p. 83-95 (in Russian). DOI: 10.22449/2413-5577-2019-1-83-95
- Mishkova D.V., Kalaidov A.N. Substantiation of risks at a chemically hazardous facility of PAO “Crimean Titan”. Materialy III Mezhdunarodnoi nauchno-prakticheskoi konferentsii, posvyashchennoi Vsemirnomu dnyu grazhdanskoi oborony “Grazhdanskaya oborona na strazhe mira i bezopasnosti”, 1 marta 2019, Мoscow, Russia. Мoscow: Izd-vo “Akademiya Gosudarstvennoi protivopozharnoi sluzhby Ministerstva Rossiiskoi Federatsii po delam grazhdanskoi oborony, chrezvychainym situatsiyam i likvidatsii posledstvii stikhiinykh bedstvii”, 2019. Vol. 2, p. 249-256 (in Russian).
- Arman M.K., Srivastava B., Chatterjee M., Mandal B. Solid-phase extraction, separation and preconcentration of titanium(IV) with SSG-V10 from some other toxic cations: a molecular interpretation supported by DFT. RSC Advances. 2014. Vol. 4. Iss. 64, p. 33923-33934. DOI: 10.1039/c4ra04110k
- Petrov G.V., Fokina S.B., Nikitina T. Aspects of iridium extraction from chloride solutions. Non-ferrous Metals. 2021. N 1, p. 10-14. DOI: 10.17580/nfm.2021.01.02
- Blokhin A.A., Murashkin Yu.V., Mikhaylenko M.A. Ion Exchange Treatment of Cobalt Acetate Solutions to Remove Iron(III) Impurity. Russian Journal of Applied Chemistry. 2021. Vol. 94. Iss. 1, p. 116-121. DOI: 10.1134/S1070427221010171
- Petrov G., Zotova I., Nikitina T., Fokina S. Sorption recovery of platinum metals from production solutions of sulfate-chloride leaching of chromite wastes. Metals. 2021. Vol. 11. N 4. N DOI: 10.3390/met11040569
- Nureev R.R., Pashkevich M.A., Kharko P.A. Evaluation of the impact of copper ore enrichment waste on surface and ground waters. Geologiya i geofizika Yuga Rossii. 2022. N 12 (4), p. 169-179 (in Russian). DOI: 10.46698/VNC.2022.37.95.013
- Plokhov A.S., Pashkevich M.A. Investigation of the treatment of drainage waters of the copper processing plant tailings. Obogashchenie rud. 2022. N 3, p. 40-44 (in Russian). DOI: 17580/or.2022.03.07
- Aydin Ö., Özmetin C., Korkmaz M., Fil B.A. A semiempirical kinetic model for removal of iron (Fe3+) from saturated boric acid solution by ion exchange using amberlite IR-120 resin. Particulate Science and Technology. 2017. Vol. 35. Iss. 5, p. 505-511. DOI: 10.1080/02726351.2015.1076916
- Fernandes S., Romão I.S., Abreu C.M.R. et al. Selective separation of Cr(III) and Fe(III) from liquid effluents using a chelating resin. Water Science and Technology. 2012. Vol. 66. N 9, p. 1968-1976. DOI: 10.2166/wst.2012.406
- Lobacheva O.L.Ion Flotation of Ytterbium Water-Salt Systems – An Innovative Aspect of the Modern Industry. Water. 2021. Vol. 13. N 24. N DOI: 10.3390/w13243493
- Dzhevaga N.V., Lobacheva O.L.Reduction in Technogenic Burden on the Environment by Flotation Recovery of Rare Earth Elements from Diluted Industrial Solutions. Applied Sciences. 2021. Vol. 11. N 16. N DOI: 10.3390/app11167452
- Jafarian H., Firouzjaei M.D., Aktij S.A. et al. Synthesis of heterogeneous metal organic Framework-Graphene oxide nanocomposite membranes for water treatment. Chemical Engineering Journal. 2023. Vol. 455. N 140851. DOI: 10.1016/j.cej.2022.140851
- Jorge N., Teixeira A.R., Lucas M.S., Peres J.A. Combined organic coagulants and photocatalytic processes for winery wastewater treatment. Journal of Environmental Management. 2023. Vol. 326. Part B. N 116819. DOI: 10.1016/j.jenvman.2022.116819
- Lili Zhang, Ting-an Zhang, Guozhi Lv et al. Extraction Separation of Ti(IV) and Fe(II) Using D2EHPA from the Raffinate Obtained After Extraction of Scandium from Titanium Dioxide Waste Acid. The Journal of the Minerals, Metals & Materials Society. 2022. Vol. 74, p. 1061-1069. DOI: 10.1007/s11837-021-05118-7
- Keyu Zhu, Qifeng Wei, Huaquan Li, Xiulian Ren. Solvent extraction of titanium from ilmenite hydrochloric acid leachate: Optimization and investigation of extraction reactions of all contained metal ions. Minerals Engineering. 2022. Vol. 186. N DOI: 10.1016/j.mineng.2022.107744
- Xue Hua Mao, Dai Jun Liu. Solvent extraction and stripping of tetravalent titanium from acidic chloride solutions by trioctylphosphine Advanced Materials Research. 2012. Vol. 550-553, p. 616-621. DOI: 10.4028/www.scientific.net/AMR.550-553.616
- Asadu C.O., Anthony E.C., Elijah O.C. et al. Development of an adsorbent for the remediation of crude oil polluted water using stearic acid grafted coconut husk (cocos nucifera) composite. Applied Surface Science Advance. 2021. Vol. 6. N DOI: 10.1016/j.apsadv.2021.100179
- Izadi A., Mohebbi A., Amiri M., Izadi N. Removal of iron ions from industrial copper raffinate and electrowinning electrolyte solutions by chemical precipitation and ion exchange. Minerals Engineering. 2017. Vol. 113, p. 23-35. DOI: 10.1016/j.mineng.2017.07.018
- Billah R.E.K., Haddaji Y., Goudali O. et al. Removal and Regeneration of Iron(III) from Water Using New Treated Fluorapatite Extracted from Natural Phosphate as Adsorbent. Biointerface Research in Applied Chemistry. 2021. Vol. 11.5, p. 13130-13140. DOI: 10.33263/BRIAC115.1313013140
- Wołowicz A., Wawrzkiewicz M. Screening of Ion Exchange Resins for Hazardous Ni(II) Removal from Aqueous Solutions: Kinetic and Equilibrium Batch Adsorption Method. Processes. 2021. Vol. 9. Iss. 2. N 285. DOI: 10.3390/pr9020285
- Ulloa L., Martínez-Minchero M., Bringas E. et al. Split regeneration of chelating resins for the selective recovery of nickel and copper. Separation and Purification Technology. 2020. Vol. 253. N DOI: 10.1016/j.seppur.2020.117516
- Víctor-Ortega M.D., Ochando-Pulido J.M., Martínez-Ferez A. Thermodynamic and kinetic studies on iron removal by means of a novel strong-acid cation exchange resin for olive mill effluent reclamation. Ecological Engineering. 2016. Vol. 86, p. 53-59. DOI: 10.1016/j.ecoleng.2015.10.027
- Abdolah R., Goodarzi V., Baghersad M.H.Introducing a new co-polymeric adsorbent with fast sorption rate and high sorption capacity for removing the heavy metal ions: A thermodynamic and kinetic study. Scientia Iranica. 2020. Vol. 28. Iss. 3, p. 1436- DOI: 10.24200/sci.2020.54302.3691
- Cheremisina O.V., Chirkst D.E., Ponomareva M.A. Thermodynamic study of cerium sorption onto anionite from sulfate me Russian Journal of Physical Chemistry A. 2013. Vol. 87. N 2, p. 288-295. DOI: 10.1134/S0036024413020349
- Cheremisina O.V., Schenk J., Cheremisina E.A., Ponomareva M.A. Thermodynamic model of ion-exchange process as exemplified by cerium sorption from multisalt solutions. Journal of Mining Institute. Vol. 237, p. 307-316. DOI: 10.31897/PMI.2019.3.307