Development of resource-saving technology for excavation of flat-lying coal seams with tight roof rocks (on the example of the Quang Ninh coal basin mines)
- 1 — Ph.D., Dr.Sci. Head of the Department Saint Petersburg Mining University ▪ Orcid
- 2 — Postgraduate Student Saint Petersburg Mining University ▪ Orcid
Abstract
It is shown that the creation of the variants of resource-saving systems for the development of long-column mining is one of the main directions for improving the technological schemes for mining operations in the mines of the Kuang Nin coal basin. They provide a reduction in coal losses in the inter-column pillars and the cost of maintaining preliminary workings fixed with anchorage. The implementation of these directions is difficult (and in some cases practically impossible) when tight rocks are lying over the coal seam, prone to significant hovering in the developed space. In the Quang Ninh basin, 9-10 % of the workings are anchored, the operational losses of coal reach 30 % or more; up to 50 % of the workings are re-anchored annually. It is concluded that the real conditions for reducing coal losses and the effective use of anchor support as the main support of reusable preliminary workings are created when implementing the idea put forward at the St. Petersburg Mining University: leaving the coal pillar of increased width between the reused mine working and the developed space and its subsequent development on the same line with the stoping face simultaneously with the reclamation of the reused mine working.
Introduction
The Quang Ninh coal basin is the main coal mining area of Vietnam, providing about 95 % of the underground extraction of high-quality coal grades Zh and K. The development of the most liquid flat-lying coal seams of medium capacity is carried out using a long-column mining system, which includes the preparation of columns by double preliminary workings. Coal pillars are left between the excavation sites to ensure a technologically satisfactory condition of the reused preliminary workings [1].
This development system in various variants is widely used in promising mines in Russia, China, Australia and other coal-mining countries [2-5] when excavating flat-lying and inclined coal seams using high-performance stoping equipment in longwalls. The main factors determining the need for this development system in modern market conditions of mine operation are the possibility of achieving high labor productivity and low cost of stoping operations [6-8]. The significant disadvantages of the long-column mining system are: significant operational losses of coal in the inter-column pillars, exceeding 15-20 % of the balance reserves [3, 9, 10]; the formation of areas of increased rock pressure under and above the pillars, which negatively affects the development of the converged layers; an increase in the danger of mining operations by the factors of “rock bursts” and “sudden bumps”; increasing the probability of spontaneous combustion of coal in the developed space [11, 12]. The negative impact of disadvantages on coal losses, the economic performance of mines and the safety of mining operations increase as mining operations move to deeper horizons [3, 13-15].
Prospective coal mines of the Quang Ninh coal basin work out flat-lying or inclined coal seams with a capacity of 1.5-2.5 m at depths of 300-400 m in one layer. The maximum depths of the productive layers reach 650 m or more. Data on the physical and mechanical properties of the host rocks in the mines of the Quang Ninh coal basin are given in the Table.
Physical and mechanical properties of host rocks (according to the Vietnamese coal company Vinacomin) [16-18]
Lithological variety of rocks |
Maximum values |
||||
Uniaxial compression strength, MPa |
Tensile strength, MPa |
Bulk density, |
Adhesion force, |
The angle |
|
Sandstone (tight roof rocks) |
177 |
22 |
2,9 |
112 |
34 |
Siltstone |
108 |
17 |
2,8 |
103 |
33 |
Mudstone |
20 |
16 |
2,6 |
33 |
31 |
The mines are characterized by relatively low values of the absolute and relative gas content of the excavation sites, which do not require special measures for the degassing of the formation and the developed space. The length of the excavation columns is 300-800 m, the rate of movement of the longwalls is 15-25 m/month. Stoping works in longwalls are carried out using drilling and blasting operations (95 %) and combines (5 %). Barring of the bottom-hole space of the longwalls is carried out with complete fasteners of the XDY, ZH, GK type. Frame (at least 90 %) and anchor supports are used as the main support in preliminary workings.
The width of the coal pillars left between adjacent excavation columns in the mines of the Quang Ninh coal basin is 20-30 m or more. The actual operational losses of coal in the pillars reach 20-30 % of the balance reserves of the excavation sites [1, 16, 18]. During the transition of mining operations to deeper horizons, the width of the pillar increases. At the same time, the sharpest increase in this parameter is observed at depths exceeding 200-250 m. A similar change in the width of the pillar is observed in many mines around the world [9, 20, 21]. Thus, in the Kuznetsk Basin, the actual width of the inter-column pillars increased from 20-25 to 40-45 m with an increase in the depth of mining operations from 170-200 to 400 m [3, 12, 22].
Attempts to reduce the operational losses of coal by reducing the width of the pillars lead to an increase in the costs of maintaining preliminary workings and production losses during downtime of longwalls associated with the repair of workings.
When using known variants of the long-column mining system [23], the presence of a layer of tight rocks in the roof is among the factors that negatively affect the amount of operational losses of coal in the pillars, as well as the cost of drifting and maintaining (Fig.1) reusable site preliminary workings.
The tight roof rocks of the Quang Ninh coal basin, according to their cavability, belong to the II and III classes according to the classification of the VUGI (former All-Union Coal Institute).
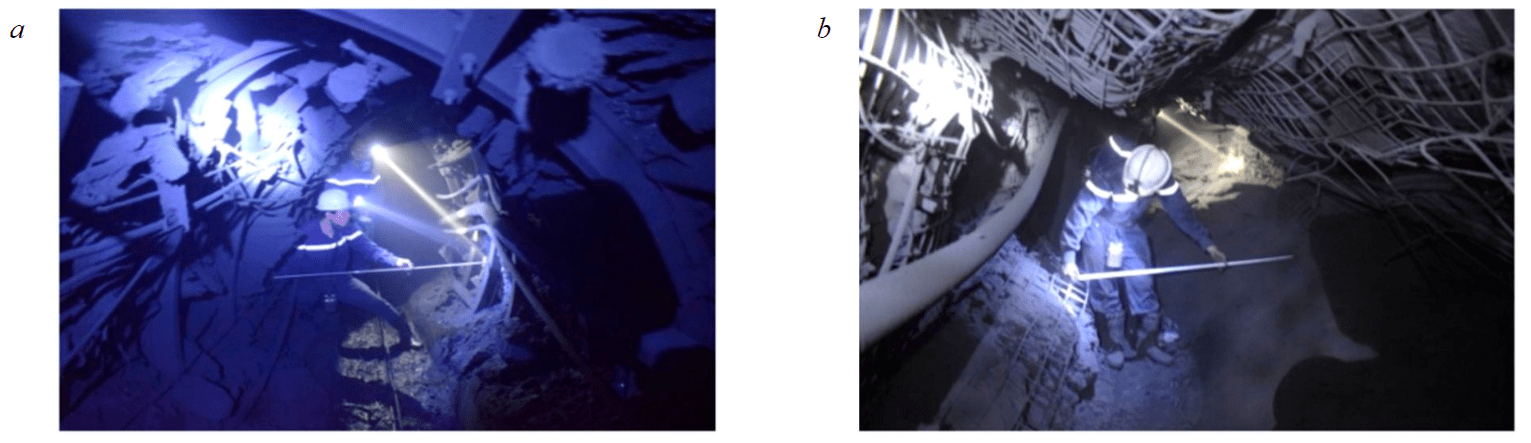
Fig.1. The state of reused preliminary workings, fixed with arch (a) and anchor (b) fasteners, during the development of formation 11 (Hecham mine) with tight rocks of the main roof
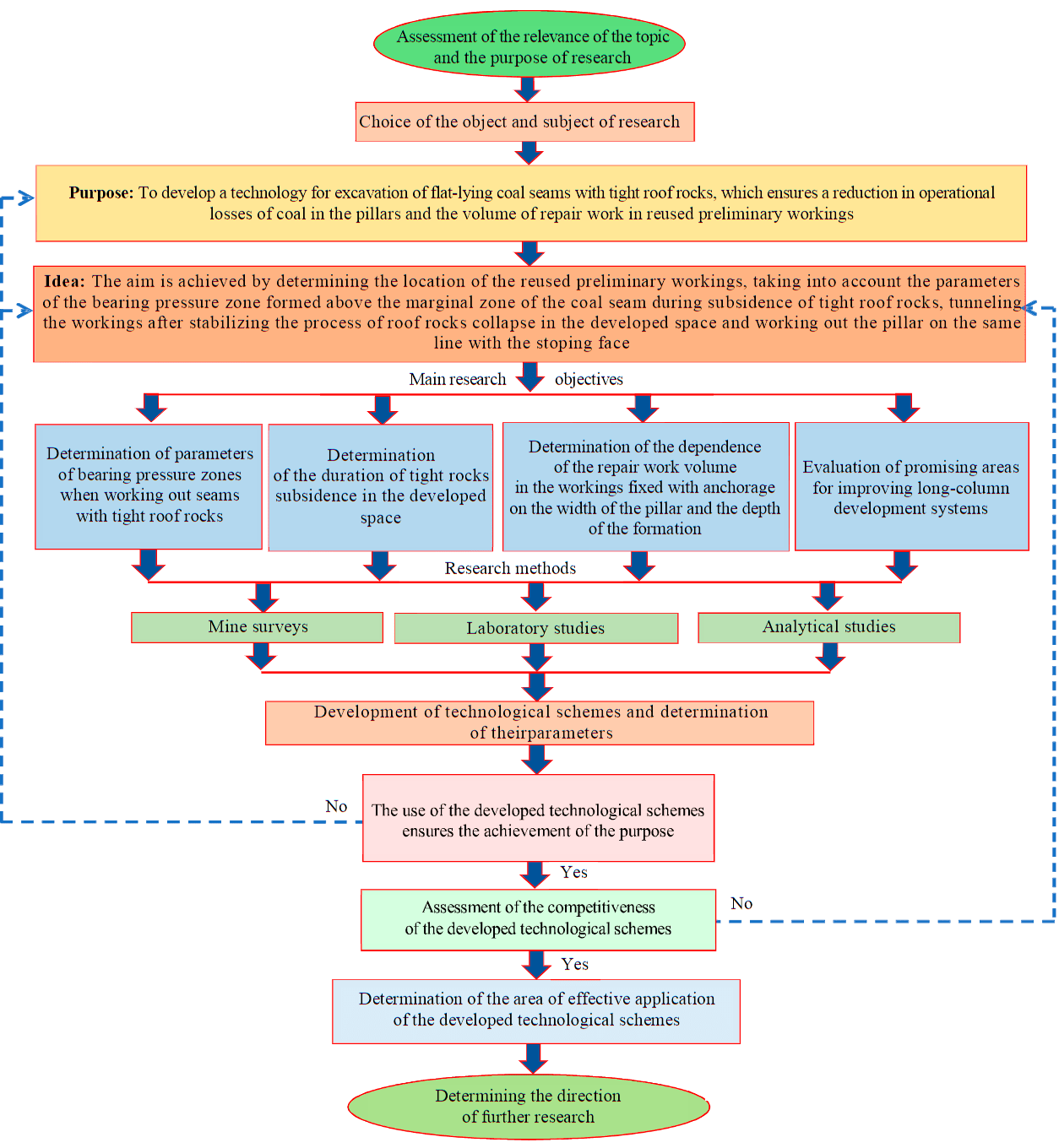
Fig.2. Research algorithm
Class II – in the immediate roof there is a thickness of free caving rocks with a capacity of less than 6-8 times the capacity of the seam being developed. Above there are tight rocks, the collapse of which occurs after a certain time after their exposure on a significant area. Class III – a thick seam of tight rocks lies directly above the formation, the collapse of which occurs when they are exposed over a significant area (VNIMI, 1954).
In the conditions of the Quang Ninh coal basin mines, the mining of coal seams with tight roof rocks prone to significant hovering in the developed space is characterized by the greatest operational losses of coal, the almost complete absence of workings fixed with anchorage, and significant production losses associated with downtime of longwalls during repair work in reused workings [24-26].
The purpose of the research is to develop a resource–saving technology for excavating flat-lying coal seams with tight roof rocks, which ensures a reduction in operational losses of coal in the pillars and the volume of repair work in reused site preliminary workings (Fig.2).
Of particular importance is the solution of this problem when using anchor supports as the main supports of reused workings. Anchor supports in comparison with frame ones have a number of advantages that significantly reduce production costs and increase labor productivity [11, 27-29].
The use of anchor supports allows 5-9 times to reduce the consumption of rolled metal, timber, concrete; 3-5 times to increase the productivity of work when fixing workings; 2-3 times to increase the rate of tunneling of workings; 1.5-2.2 times or more to reduce the cost of ensuring a technologically satisfactory condition of the workings during its lifetime [30-32].
The relevance of the problem solution under consideration for the conditions of the Quang Ninh coal basin mines of Vietnam is evidenced by the following facts:
- the percentage of seams in the roof of which tight rocks are deposited is at least 30 % of the total number of seams being developed [17, 18];
- despite the great attention paid by the Vietnamese coal company Vinacomin to the implementation of anchorage, the actual length of site preliminary workings fixed with anchorage does not exceed 10 %;
- losses of highly liquid coal in the pillars left between the excavation columns amount to 20-30 % or more, which reduces the service life of the mine (by about 25 %).
Methodology
To solve the tasks set, a comprehensive research method was applied (Fig.2): analysis of practical experience in mining flat-lying coal seams of medium capacity; physical and numerical modeling to study the stress-strain state of rocks above the marginal part of the coal rock mass [33-35]; mine studies of the influence of mining factors on the state of site preliminary workings [2, 36-38].
Results discussion
As the main criteria for assessing the reliability of the results obtained with physical (on models made of equivalent materials) and numerical simulations, data from production studies at the mines Quang Ninh coal basin mines, as well as data obtained in similar mining and geological conditions at the mines of the Eastern region of Donbass and the Kuznetsk basin were used.
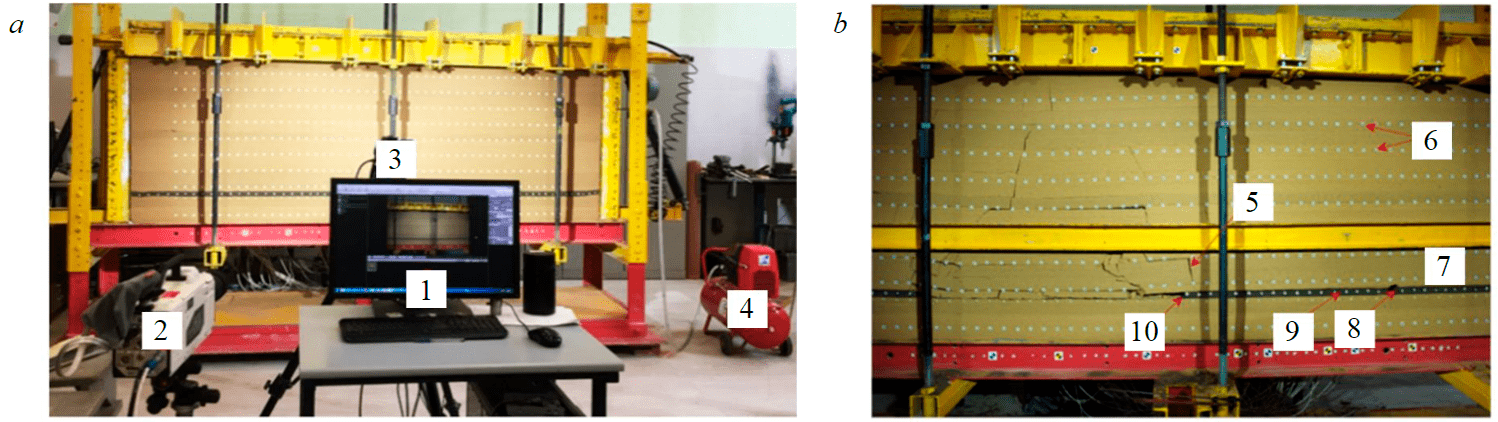
Fig.3. General view of the model made of equivalent materials (a) during its testing (b) 1 – computer and software for recording images; 2 – observation camera; 3 – digital camera; 4 – loading control system; 5 – fracture crack; 6 – marks; 7 – tight roof rocks; 8 – reused working; 9 – worked out coal seam; 10 – the boundary of the developed space
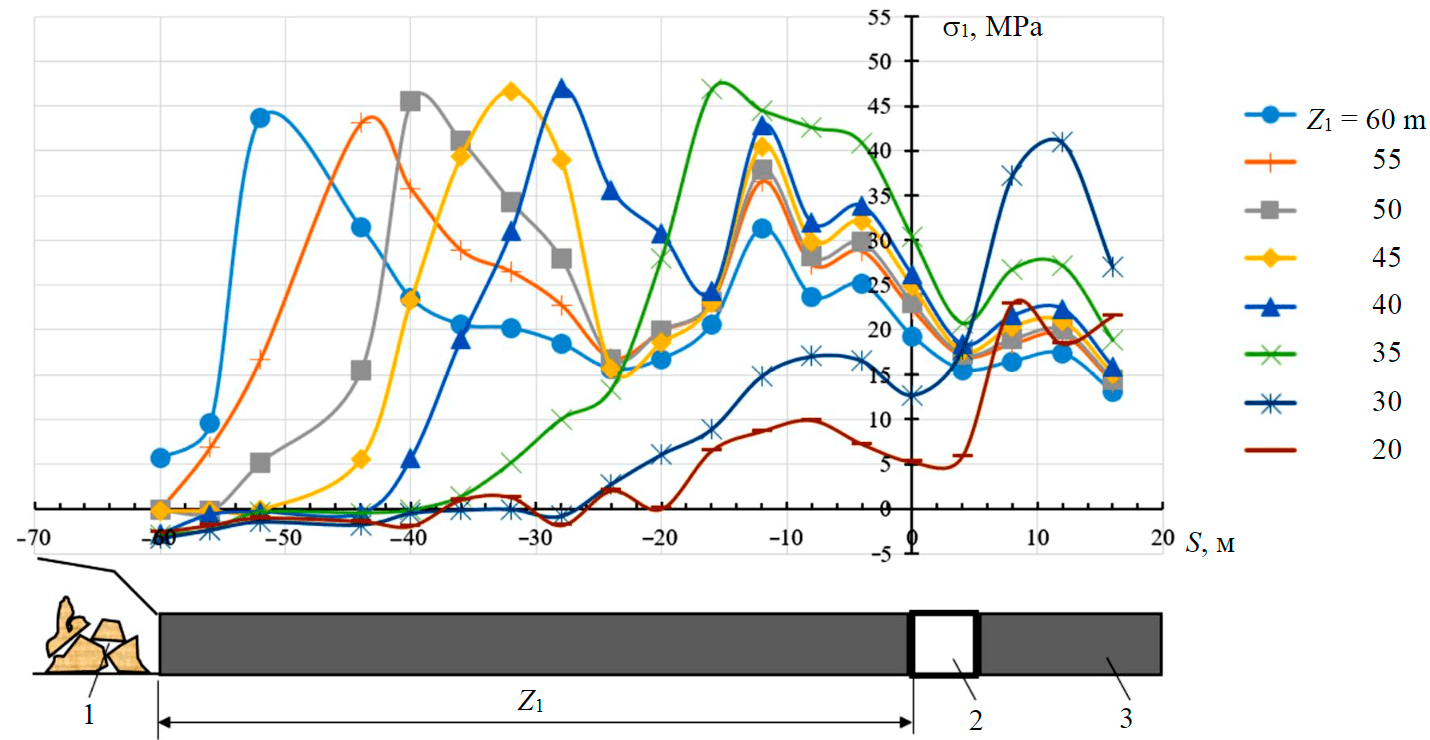
Fig.4. The influence of the width of the pillar located between the reused working and the developed space on the stress distribution in the marginal zone of the formation (seam 11, Hecham mine) 1 – developed space; 2 – reused working; 3 – coal seam; Z1 – the width of the pillar
The main aims of the research on models made of equivalent materials were to assess the parameters of the bearing pressure zone formed above the marginal part of the coal rock mass and in the coal pillars, and to establish the places of formation of the main fracture cracks in the tight roof rocks. Laboratory studies on models made of equivalent materials (Fig.3) were carried out in accordance with the methods adopted at the Saint Petersburg Mining University.
MDG-3 pressure sensors were used to study the stress state of the model rock mass. Calibration of sensors and processing of their readings were carried out using software such as ACTest Pro, which allows monitoring the progress of the experiment in real time. During the model test, vertical and horizontal displacements of marks 6 were photofixed (Fig.3) with an accuracy of 1/5 pixel (< 0.0001 m), which made it possible to track the appearance and dynamics of the cracks development in the mined rock thickness [14, 39]. When modeling, the following similarity conditions are accepted:
where Ls, μs, ρs, σs – geometric size, Poisson's ratio, density and uniaxial compressive strength of rock layers in the study area, respectively; Lm, μm, ρm, σm – geometric size, Poisson's ratio, density and uniaxial compressive strength of rock layers in the model, respectively.
Fig.3, b shows a model illustrating the development of a flat-lying coal seam 11 with a capacity of 3 m in the conditions of the Hecham mine, when testing this model, the width of the pillar between the preliminary working and the developed space varied from 60 to 20 m (Fig.4). The performed studies have shown that when the width of the pillar is more than 50 m, there are no increased deformations in the workings; at 40-45 m, individual cracks appear in the roof of the workings; at 35 m, the roof of the workings is characterized by an increased frequency of cracks. Intensive lowering of the roof rocks and displacement of the sides of the workings were recorded with the width of the pillar equal to 25 m. The complete destruction of the secured workings occurred with a width of the pillar about 20 m. The maximum vertical stresses on the pillar after its destruction were less than 25 % of the maximum stresses in the bearing pressure zone recorded with a width of pillar of more than 60 m.
The results of laboratory studies on models made of equivalent materials are in satisfactory agreement with the results of studies of the stress-strain state of a rock mass using the finite element method with the FLAC3D (ITASCA) program [40, 41].
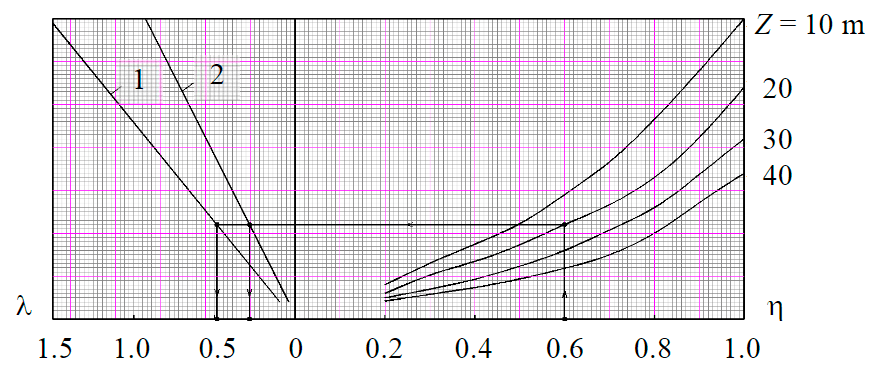
Fig.5. The influence of mining factors on the volume of repair work in reused site preliminary workings during the development of coal seams with tight roof rocks 1 – when fixing workings with anchor fasteners; 2 – when fixing workings with frame fasteners
The main task of mine research was to establish the nature and degree of influence of geological and mining factors on the volume of repair work in preliminary workings during the development of coal seams, in the roof of which tight rocks lay. The results of the studies for reused site preliminary workings, secured from the side of the developed space by coal pillar, are presented in Fig.5:
where ∑li – the total length of the sites of reused workings, within which repair work was carried out; lcol – length of the excavation column; η – coefficient characterizing geomechanical conditions for maintaining working; σrm – stresses in the rock mass; σcom – weighted average uniaxial compression strength of the host rocks; Z – the width of the pillar.
When constructing the nomogram, data on repair work related to the complete re-anchoring of workings, the installation of additional “reinforcement” support and the replacement of individual elements of the support were used. At the same time, repair work related to the footwalling of soil rocks was not taken into account due to the lack of actual data sufficient for their reliable statistical processing.
The performed studies have shown that an increase in the width of the pillar from 10 to 40-50 m leads to a decrease in the total length of the sites of reused workings within which repairs were carried out: by 2.0-2.2 times when using frame supports, by 2.3-2.4 times – anchor supports.
An increase in the depth of mining operations leads to a constant increase in the volume of repair work in the workings. At the same time, the most significant changes are observed during the transition to depths characterized by the values of the coefficient of conditions η ≥ 0.45-0.6.
The most “sensitive” to an increase in the depth of mining operations and a change in the width of the pillar are the workings fixed with anchorage. In the conditions of the Quang Ninh coal basin mines at depths of 300-400 m (η = 0.3-0.4) with the width of the inter-column coal pillars equal to 20-30 m, up to 50 % of the total length of workings with frame supports of the SIP type (special interchangeable profiles), and 40-50 % or more of the total length of workings with anchor supports of the CDCT type (steel polymer anchors) are reinforced. This leads not only to an increase in production costs directly for repair work, but also to an increase in irreparable production losses associated with downtime of longwalls during repair work.
As follows from Fig.5 and the results of laboratory studies (see Fig.4), a significant reduction in the volume of repair work in the preliminary workings fixed with anchorage can be achieved in the conditions of the Quang Ninh coal basin mines with an increase in the width of the pillar Z to 40 m. With an increase in the width of the pillar from 20 to 40 m during mining operations at depths characterized by the values of the coefficient of conditions η = 0.6, the volume of repair work decreases by 50-70 %. But an increase in the width of the inter-column pillar leads to a proportional increase in the operational losses of coal. This is one of the reasons why the introduction of anchor supports in the mines of Vietnam is being held back. Their use, as evidenced by the world experience of underground mining of coal deposits [42, 43], creates objective prerequisites for a significant reduction in production costs.
The intensification of mining observed at the mines increases the “price” of unplanned downtime of longwalls with production losses, which implies higher requirements for the reliability of the technological scheme of the mine [44-46].
An analysis of the practical experience of working out flat-lying and inclined formations in the Quang Ninh coal basin mines using the long-column mining system showed that the main causes of unplanned downtime of longwalls include repair work in reused preliminary workings during periods when they are in the zones of influence of stoping operations. The total downtime of longwalls increases with an increase in the length of excavation columns and longwalls, as well as with the transition of mining operations to deeper horizons.
The main function of the pillars left between the excavation sites is to ensure a technologically satisfactory condition of the preliminary workings intended for reuse by the time the adjacent column is completed, as well as to reduce the displacement of rocks in the reused workings during the period of column excavation. Failure to comply with these conditions leads to production losses or spatial deconcentration of mining operations, which results in an increase in production costs associated with additional costs for tunneling and maintaining preliminary workings, transportation, ventilation, etc. [46-49].
The estimation of production losses (P) associated with the technologically unsatisfactory state of the preliminary workings can be carried out using the expression:
where Аl – average daily design load on longwall, t; а – the period of time required for carrying out repair work in the preliminary development before its reuse; Аav – the actual average daily load on longwall during excavation of the excavation column, t; Тcol – duration of working out of the excavation column, day.
Unplanned shutdowns of stoping operations during downtime of longwalls associated with the repair of workings lead to irreparable production losses. In absolute terms, the loss of production by high-performance longwalls is estimated at hundreds of thousands of tons per month.
Recommended resource-saving technologies for excavating flat-lying coal seams with tight roof rocks
The set purpose (see Fig.2) is achieved by using the idea, the main statements of which are:
- the width of the inter-column pillar must be taken into account the width of the zone of dangerous bearing pressure formed in the marginal part of the coal seam during the subsidence of tight roof rocks in the developed space;
- simultaneously with the reclamation of the reused site workings, work out the inter-column pillar of coal on the same line with the stoping face;
- service roadways that provide the possibility of ventilation of a dead-end site of longwall when working out the pillar on the same line with the stoping face, it is necessary to pass after stabilization of the subsidence of tight roof rocks in the developed space, taking into account the location of the fracture crack in tight rocks.
The developed variants of the long-column mining system, ensuring the achievement of the set purpose and recommended for use in the Quang Ninh coal basin mines of Vietnam, are shown in Fig.6. When using the variant shown in Fig.6, a, to prepare for the development of the FADE column by longwall N 2, double drifts 6, 7 and a face entry 8 are passed. Face entries 14 run between drifts 6 and 7, separated by coal pillar with a width of Z1. The width of the pillar Z1 is assumed to be greater than the width of the zone of dangerous bearing pressure formed in the marginal zone of the coal seam.
To estimate the width of the dangerous stress zone (L1 or L2, Fig.7), a program has been developed [50], which allows calculating vertical stresses in the bearing pressure zone formed above the marginal part of the coal seam adjacent to the developed space. During the development of the program, the results of mine and laboratory studies of the authors were used, as well as the data given in the guidelines “Calculation and experimental evaluation of stresses in the pillars and marginal parts of the coal seam” (VNIMI, 1973).
The width of the pillar Z1 between the reused site preliminary development and the developed space is recommended to take more than the width of the dangerous stress zone (L1 or L2, Fig.7).
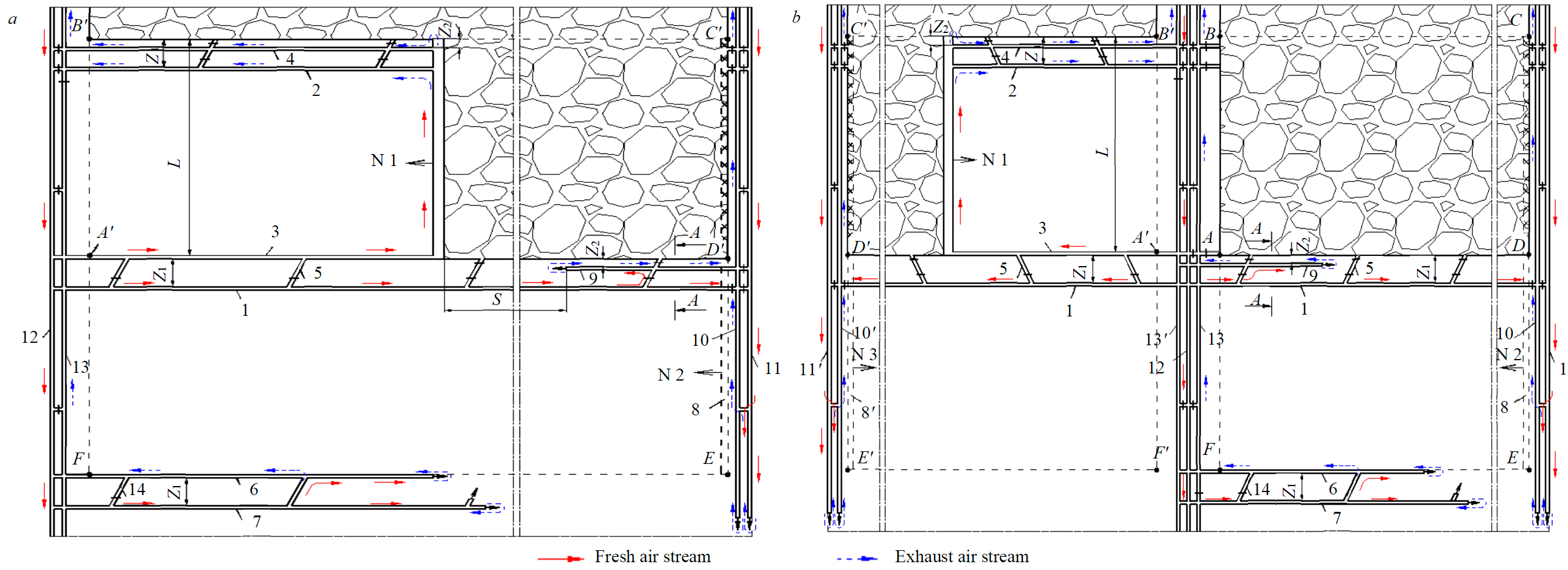
Fig.6. Variants of the long–column mining system recommended for use in the Quang Ninh coal basin mines of Vietnam: а – at Lcol > vt; b – at Lcol ≤ vt (v is the speed of longwall movement; t is the duration of stabilization of subsidence of tight roof rocks in the developed space) 1, 3 – transport drifts of the worked-out column A'B'C'D'; 2 – ventilation shaft of the worked out column A'B'C'D'; 4 – service roadway of the worked-out column A'B'C'D'; 5 – entry (breakthrough); 6, 7 – transport drifts of the prepared column FADE; 8 – face entry; 9 – service roadway of the prepared column ADEF; 10, 11 – flank workings; 12 – panel incline; 13 – manway of the panel incline; 14 – entry (breakthrough); Z1 – the width of the coal pillar left during the tunneling of transport drifts 6 and 7; Z2 – the width of pillar between the service roadway 4 of the worked out column A'B'C'D' and the developed space (the width of the pillar left from the side of the developed space during the tunneling of the service roadway 9 of the prepared column ADEF); S – the distance between the face of the work being carried out 9 and longwall N 1; L – longwall length
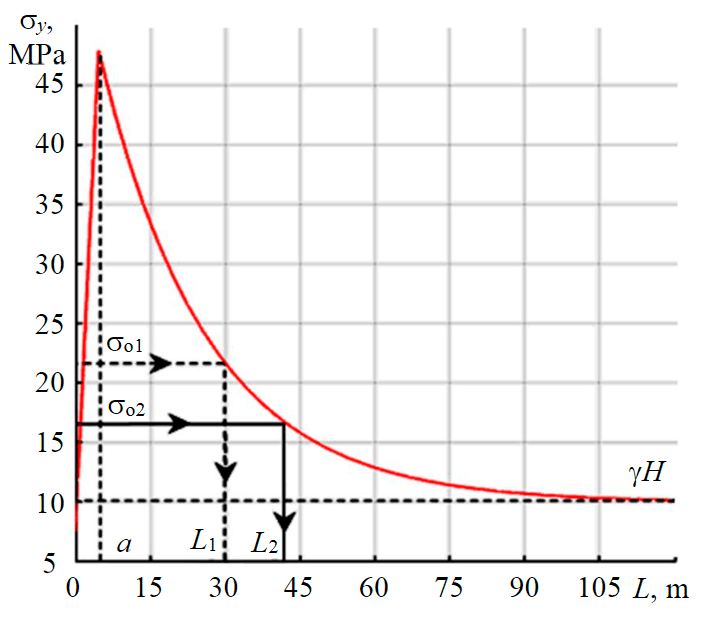
Fig.7. An example of determining the parameters of the reference pressure zone and plotting the stress distribution in the marginal part of the coal seam 11 for the conditions of the Hecham mine: σy – vertical stress; σо1, σо2 – dangerous stresses in the array when using frame and anchor supports, respectively; γH – geostatic stress level; γ – volumetric weight of rocks; H – depth of rocks; L1, L2 – the width of the zone of dangerous stresses when using frame and anchor supports, respectively
In the example considered (Fig.7), when using frame supports (SIP), the width of the pillar should be taken about 30 m, when using anchor supports (CDCT) – more than 40 m.
During the mining of the column A'B'C'D' by longwall N 1 with a certain lag S of the stoping face from the flank workings 10 and 11, the service roadway 9 is carried out. Between the developed space and the service roadway 9 during its tunneling, a coal pillar is left, the width Z2 of which is determined from the condition for ensuring safe ventilation of the dead-end part of longwall N 1 due to diffusion (general depression). In accordance with paragraph 154 of the “Safety Rules in Coal Mines” (2017), it is allowed to ventilate through diffusion dead-end workings up to 6 m long in gas mines and up to 10 m in non-gas mines.
In this case, it is advisable to place the service roadway 9 at a distance of Z2 (see Fig.6) from the developed space exceeding the distance d from the boundary of the developed space to the fracture crack in the main roof. With this layout, the working 9 is under the “protection” of the main roof, which perceives the increased loads formed in the bearing pressure zone. According to laboratory studies, on models made of equivalent materials, the distance d does not exceed 4-5 m.
The parameter Z2 must be determined using the expressions: d < Z2 ≤ 6 m – for gas mines; d < Z2 ≤ 10 m – for non-gas mines.
In Fig.6, the FADE column is worked out with longwall N 2 after the finishing of the stoping work in longwall N 1. Drifts 2, 3 and service roadway 4 are extinguished behind longwall N 1. Reused drifts 1 and 2 are secured by the width of the coal pillars Z1. Drift 1 is used as a transport drift during the operation of longwall N 1; during the operation of longwall N 2, it is reused as a ventilation drift.
The variant shown in Fig.6, a, is recommended for the length of the excavation columns L > tV; the variant in Fig.6, b – for the length of the excavation columns L ≤ tV, where L – the design length of the excavation column; t – the duration of stabilization of subsidence of tight roof rocks in the developed space; V – the speed of longwall movement.
In the conditions of the Quang Ninh coal basin mines, the actual speeds of longwall movement during stoping operations using drilling and blasting operations are 15-25 m/month, the duration of stabilization of subsidence of tight roof rocks in the developed space is up to 6-8 months. Taking into account these facts, the prospects for the implementation of the scheme (Fig.6, a) are associated with the development of sites of mine fields with a seam strike size of more than 200-250 m. The scheme shown in Fig.6, b is advisable to use when working out sites of mine fields with a seam strike size of less than 250 m. The actual length of the excavation pillars at the Khacham and other mines is 300-800 m, the speed of longwalls movement is 15-25 m/month. In the conditions of modern Russian coal mines with the speeds of mechanized longwalls movement reaching 450-500 m/month, the scheme (Fig.6, a) is advisable to apply with the length of the excavation columns more than 3000-3500 m.
The use of the recommended technological schemes makes it possible to provide the most favorable conditions for maintaining production intended for reuse. During the entire period of its existence, this mine is secured according to the scheme “the pillar with a width Z1 – rock mass”. The adoption of the width of the pillar Z1, comparable with the width of the zone of dangerous bearing pressure, which is formed above the marginal part of the coal massif, allows to significantly (by 1.5-2.3 times or more) reduce the cost of maintaining reusable workings with any types of supports and to ensure the possibility of using anchor support as the main support of reusable workings.
The reduction of operational losses of coal is ensured by the complete development of the inter-column pillars. With the mining system used in the mines of Vietnam, losses in one pillar with a column length of 800 m reach 100 thousand tons of coal or more.
Taking into account the nature of the dependencies shown in Fig.5, as well as the inevitable increase in the depth of mining operations and the length of excavation columns in the future, the economic efficiency of using the developed technology will constantly increase. Among the additional positive effects achieved by using this technology are an increase in the efficiency of mining suites of contiguous formations and a decrease in the probability of gas-dynamic phenomena during the development of formations, dangerous for sudden outbursts of coal and gas.
Conclusion
Variants of the long-column mining system with the leaving of coal pillar in the developed space are characterized by significant drawbacks, the negative impact of which is constantly increasing with the improvement of coal stoping excavation technologies and the transition of mining operations to deeper horizons. The drawbacks include: a constant increase in the operational losses of coal and the costs of tunneling, maintenance of site workings; reduction of balance reserves associated with the impossibility of safe mining of contiguous formations in areas of high rock pressure formed under (above) the coal pillars; increased risk of rock bursts and sudden outbursts of coal and gas.
Prerequisites for the almost complete elimination of operational losses of coal in the pillars and the effective use of anchor support as the main support of the reused preliminary workings are created when coal pillar of increased width is left between the reused workings and the developed space, and its subsequent development on the same line with the stoping face simultaneously with the reclamation of the reused workings.
When using well-known variants of the long-column mining system without leaving coal pillars in the developed space, the factors that have the most significant negative impact on the operational losses of coal, the cost of tunneling and maintaining reused site preliminary workings include hovering in the developed space and dynamic subsidence of tight roof rocks, as well as the distance from the reused workings to the developed spaces.
When using the recommended resource-saving technology of mining formations, the costs of tunneling and maintaining reusable preliminary workings are minimized.
It is recommended to carry out the service roadway, which provides the possibility of ventilation of the dead-end part of the longwall when working out the pillar on the same line with the stoping face, at a distance from the developed space exceeding the distance from the fracture crack in the tight roof rocks to the developed space. With this layout, the service roadway is under the “protection” of tight rocks that perceive increased loads formed in the bearing pressure zone, which significantly reduces the cost of fixing.
The introduction of the developed resource-saving technology at mines working out flat-lying coal seams makes it possible to almost completely eliminate the operational losses of coal in the pillars and use cost-effective anchorage as the main support for reused preliminary workings. The expected economic effect of tunneling and maintenance using the developed technology when working out just one 700 m long excavation column at the Hecham mine is at least 10-20 million rubles.
The research results can be used in the educational process for the training of mining engineers at Saint Petersburg Mining University and Hanoi Mining and Geological University of Vietnam.
References
- Abramkin N.I., Pham Duc Thang. Study Areas the Comprehensive Mechanization of Cleaning Works on Coal Winning Technology in Medium-Thick Inclined Seams for Quang Hanh Mine. Mining informational and analytical bulletin. 2017. N 1, p. 202-210 (in Russian).
- Agafonov V.V., Shavrov P.V. Analysis of methods for determining effective forms of development of technological systems of coal mines. Mining informational and analytical bulletin. 2011. N 10, p. 9-12 (in Russian).
- Zubov V.P. Status and directions of improvement of development systems of coal seams on perspective Kuzbass coal mines. Journal of Mining Institute. 2017. Vol. 225, p. 292-297. DOI: 10.18454/PMI.2017.3.292
- Dao Viet Doan, Bai Xia, Van Diep Dinh. Control technology for coal roadway with mudstone interlayer in Nui Beo coal mine. International Journal of GEOMATE. 2019. Vol. 17. Iss. 60, p. 259-266. DOI: 10.21660/2019.60.39560
- Kalinin S.I., Route G.N., Ignatov Yu.М., Cherdantsev A.M. The required for the daily production of coal from lava length of 400 meters in the conditions of the mine named after V.D.Yalevsky. Bulletin of the Kuzbass State Technical University. 2018. N 5, p. 27-34 (in Russian). DOI: 10.26730/1999-4125-2018-5-27-34
- Belodedov A.A. Justification of the workings technology effectiveness with unloading cavities when establishing stable parameters of coal pillars. Mining informational and analytical bulletin. 2010. N 4, p. 197-200 (in Russian).
- Valiev N.G., Potapov V.Ya., Potapov V.V. Technology for the coal deposits development, ensuring environmental and industrial safety of mining operations. Izvestiya vuzov. Gornyi zhurnal. 2011. N 6, p. 101-107 (in Russian).
- Kazanin O.I., Yaroshenko V.V. Decrease in coal losses during mining of contiguous seams in the near-bottom part at Vorkuta deposit. Journal of Mining Institute. 2020. Vol. 244, p. 395-401. DOI: 10.31897/PMI.2020.4.1
- Lishuai Jiang, Atsushi Sainoki, Hani S. Mitri et al. Influence of fracture-induced weakening on coal mine gateroad stability. International Journal of Rock Mechanics & Mining Sciences. 2016. Vol. 88, p. 307-317. DOI: 10.1016/j.ijrmms.2016.04.017
- Hongwei Wang, Yaodong Jiang, Yixin Zhao, Jie Zhu, Shuai Liu. Numerical investigation of the dynamic mechanical state of a coal pillar during longwall mining panel extraction. Rock Mechanics and Rock Engineering. 2013. Vol. 46. N 5, p. 1211-1221. DOI: 10.1007/s00603-012-0337-8
- Aksenov V.V., Kazantsev A.A., Dortman A.A. Review of existing types of mining supports and analysis of their application in geowinchester technology. Mining informational and analytical bulletin. 2012. N 3, p. 130-137 (in Russian).
- Valiev N.G., Berkovich V.Kh., Propp V.D., Kokarev K.V. The problems of developing protection pillars under the exploitation of ore deposits. Izvestiya vuzov. Gornyi zhurnal. 2018. N 2, p. 4-9 (in Russian). DOI: 10.21440/0536-1028-2018-2-4-9
- Demin V.F., Demina T.V., Aliev S.B., Razumnyak N.L. Estimation of deformation processes parameters in preparatory workings when using anchor barring. Mining informational and analytical bulletin. 2012. N 12, p. 28-36 (in Russian).
- Zuev B.Y. Methodology of modeling nonlinear geomechanical processes in blocky and layered rock masses on models made of equivalent materials. Journal of Mining Institute. 2021. Vol. 250, p. 542-552. DOI: 10.31897/PMI.2021.4.7
- Kachurin N.M., Sheinkman L.E., Pushkarev A.E., Kovalev R.A. Ensuring the safety of the technological process of mining coal deposits. Izvestiya Tulskogo gosudarstvennogo universiteta. Estestvennye nauki. 2012. N 1, p. 142-148 (in Russian).
- Ngoc Minh Nguyen, Duc Thang Pham.Tendencies of mining technology development in relation to deep mines. Mining Science and Technology. 2019. Vol. 4. N 1, p. 16-22. DOI: 10.17073/2500-0632-2019-1-16-22
- Le Tien Dung, Nguyen Chi Thanh, Dao Van Chi.Estimation of Coal and Rock Mechanical Properties for Numerical Modelling of Longwall Extraction. Inżynieria Mineralna. 2020. Vol. 1. N 2, p. 41-47. DOI: 10.29227/IM-2020-02-07
- Nguyen V.D., Nguyen P.H., Do M.T.Experimental Study on the Efficacy of Water Infusion for Underground Mining of a Coal Seam. Applied Sciences. 2019. Vol. 9. Iss. 18. N 3820. DOI: 10.3390/app9183820
- Chu Thi Que, Nevskaya M., Marinina O. Coal Mines in Vietnam: Geological Conditions and Their Influence on Production Sustainability Indicators. Sustainability. 2021. Vol. 13. Iss. 21. N 11800. DOI: 10.3390/su132111800
- Esterhuizen E., Mark C., Murphy M.M. Numerical model calibration for simulating coal pillars, gob and overburden response. Proceedings of the Twenty-Ninth International Conference on Ground Control in Mining. Morgantown, USA. 2010, p. 46-57.
- Kovalski E.R., Gromtsev K.V., Petrov D.N. Modeling Deformation of Rib Pillars during Backfill. Mining informational and analytical bulletin. 2020. N 79, p. 87-101 (in Russian). DOI: 10.25018/0236-1493-2020-9-0-87-101
- Osminin D.V. Prospects for the development and implementation of technological schemes for step-by-step anchoring of mine workings at Kuzbass mines. Ugol. 2014. N 10, p. 40-44 (in Russian).
- Golovaty I.I., Petrovsky A.B., Petrovsky Yu.B. Long-Term Manufacturing Schemes of the Development and Mining the Third Potash Seam in the Mine Field of the Krasnoslobodsky Mine. Mining Mechanical Engineering and Machine-Building. 2014. N 3, p. 24-35 (in Russian).
- Melnik V.V., Agafonov V.V. Organizational-Technological and Scientific-Methodical Support of Design of Coal Mines. Mining informational and analytical bulletin. 2016. N 1, p. 286-299 (in Russian).
- Mazurov B.T., Mustafin M.G., Panzhin A.A. Estimation Method for Vector Field Divergence of Earth Crust Deformations in the Process of Mineral Deposits Development. Journal of Mining Institute. 2019. Vol. 238, p. 376-382. DOI: 10.31897/PMI.2019.4.376
- Jian-biao Bai, Wen-long Shen, Guan-long Guo et al.Roof deformation, failure characteristics, and preventive techniques of gob-side entry driving heading adjacent to the advancing working face. Rock Mechanics and Rock Engineering. 2015. Vol. 48, p. 2447-2458. DOI: 10.1007/s00603-015-0713-2
- Eremenko V.A., Lushnikov V.N., Sendi M.P. et al. Justification and choice of technology, methods of barring and maintenance of mine workings in unstable rocks of the deep horizons of the Kholbinsky mine. Gornyi zhurnal. 2013. N 7, p. 59-66 (in Russian).
- Ignatov V.N., Titov A.N., Borisova E.I. On the issue of mining schedules transformation. Mining informational and analytical bulletin. 2010. N 8, p. 375-378 (in Russian).
- Prushak V.Ya., Karaban' D.T., Gubanov V.A. et al. Determination of the length and pliability of the anchor support in the conditions of roof rocks stratification. Gornyi zhurnal. 2009. N 5, p. 72-74 (in Russian).
- Meshkov A.A., Popov A.L., Popova Yu.V. et al. Prediction of Hazardous Phenomena within Operating Coal Seam for the Yalevsky Mine Field. Mining informational and analytical bulletin. 2020. N 2, p. 22-33 (in Russian). DOI: 10.25018/0236-1493-2020-2-0-22-33
- Sementsov V.V., Osminin D.V., Nifanov E.V. Stability of Excavating Mine Workings during Development of Formations with Hard-To-Break Roofs. Bulletin of the VostNII Scientific Center for Industrial and Environmental Safety. 2021. N 3, p. 14-25 (in Russian). DOI: 10.25558/VOSTNII.2021.47.12.002
- Yang Yu, Jianbiao Bai, Xiangyu Wang, Lianying Zhang. Control of the Surrounding Rock of a Goaf-Side Entry Driving Heading Mining Face. Sustainability. 2020. Vol. 12. Iss. 7. N 2623. DOI: 10.3390/su12072623
- 33. Karpov G.N., Kovalski E.R., Smychnik A.D. Determination of rock destressing parameters at the ends of disassembling room. Mining informational and analytical bulletin. 2019. N 8, p. 95-107. DOI: 10.25018/0236-1493-2019-08-0-95-107
- Sidorov D.V., Potapchuk M.I., Sidlyar A.V., Kursakin G.A. Assessment of Rock-Burst Hazard in Deep Layer Mining at Nikolayevskoye Field. Journal of Mining Institute. 2019. Vol. 238, p. 392-398. DOI: 10.31897/PMI.2019.4.392
- Rylnikova M.V., Eremenko V.A., Esina E.N. Destressing of Rockburst-Hazardous and Damaged Zones. Mining informational and analytical bulletin. 2014. N 12, p. 32-29 (in Russian).
- Gospodarikov A.P., Morozov K.V., Revin I.E. A Method of Data Interpretation in Seismicity and Deformation Monitoring in Underground Mining in Terms of the Kukisvumchorr Deposit of Apatit Company. Mining informational and analytical bulletin. 2019. N 8, p. 157-168 (in Russian). DOI: 10.25018/0236-1493-2019-08-0-157-168
- Kaplunov D.R., Radchenko D.N. Design philosophy and choice of technologies for sustainable development of underground mines. Gornyi zhurnal. 2017. N 11, p. 52-59 (in Russian). DOI: 10.17580/gzh.2017.11.10
- Trubetskoy K.N., Myaskov A.V., Galchenko Yu.P., Eremenko V.A. Creation and justification of convergent technologies for underground mining of thick solid mineral deposits. Gornyi zhurnal. 2019. N 5, p. 6-13 (in Russian). DOI: 10.17580/gzh.2019.05.01
- Protosenya A.G., Iovlev G.A. Prediction of Spatial Stress-Strain Behavior of Physically Nonlinear Soil Mass in Tunnel Face Area. Mining informational and analytical bulletin. 2020. N 5, p. 128-139 (in Russian). DOI: 10.25018/0236-1493-2020-5-0-128-139
- Nikiforov A.V., Vinogradov E.A., Kochneva A.A. Analysis of multiple seam stability. International journal of civil engineering and technology. 2019. Vol. 10 (2), p. 1132-1139.
- Shabanimashcool M., Li C.C. A numerical study of stress changes in barrier pillars and a border area in a longwall coal mine. International Journal of Coal Geology. 2013. Vol. 106. P. 39-47. DOI: 10.1016/j.coal.2012.12.008
- Chen A.Width Design of Small Coal Pillar of Gob-Side Entry Driving in Soft Rock Working Face and Its Application of Zaoquan Coal Mine. Advances in Civil Engineering. 2021. Vol. 2021. N 9999957. DOI: 10.1155/2021/9999957
- Mohammadi H., Farsangi M.A.E., Jalalifar H., Ahmadi A.R. A geometric computational model for calculation of longwall face effect on gate roadways. Rock Mechanics and Rock Engineering. 2016. Vol. 49, p. 303-314. DOI: 10.1007/s00603-015-0739-5
- Shen W.L., Bai J.B., Li W.F., Wang X.Y. Prediction of relative displacement for entry roof with weak plane under the effect of mining abutment stress. Tunnelling and Underground Space Technology. 2018. Vol. 71. P. 309-317. DOI: 10.1016/j.tust.2017.08.023
- Lishuai Jiang, Peipeng Zhang, Lianjun Chen et al.Numerical approach for goaf-side entry layout and yield pillar design in fractured ground conditions. Rock Mechanics and Rock Engineering. 2017. Vol. 50, p. 3049-3071. DOI: 10.1007/s00603-017-1277-0
- Jiránková E., Petros V., Sancer J. The assessment of stress in an exploited rock mass based on the disturbance of the rigid overlying strata. International Journal of Rock Mechanics and Mining Sciences. 2012. Vol. 50, p. 77-82. DOI: 10.1016/j.ijrmms.2012.01.004
- Wenlong Shen, Tongqiang Xiao, Meng Wang et al.Numerical modeling of entry position design: a field case. International Journal of Mining Science and Technology. 2018. Vol. 28. Iss. 6, p. 985-990. DOI: 10.1016/j.ijmst.2018.02.006
- Zvezdkin V.A., Zuev B.Yu., Klimkina V.M. et al. The study of the stress-strain state of the soil during the development of separating rock masses of deep mines of Talnakh. Journal of Mining Institute. 2009. Vol. 185, p. 81-84 (in Russian).
- Tcvetkov P., Cherepovitsyn A., Fedoseev S. The Changing Role of CO2 in the Transition to a Circular Economy: Review of Carbon Sequestration Projects. Sustainability. 2019. Vol. 11. Iss. 20. N 5834. DOI: 10.3390/su11205834
- Zubov V.P., Le Quan Phuc. Patent N 2021613663 RF. A program for calculating the parameters of the bearing pressure zone and the stress distribution diagram in the marginal part of the coal mass. Publ. 05.03.2021. Bul. N 3.