Обоснование и выбор расчетных параметров гидрофицированного комплекса оборудования для получения закладочных смесей из текущих хвостов обогащения
- 1 — д-р техн. наук Санкт-Петербургский горный университет ▪ Orcid
- 2 — канд. техн. наук инженер-конструктор ООО «Сигнал» ▪ Orcid ▪ Elibrary ▪ Scopus
- 3 — канд. техн. наук доцент Санкт-Петербургский горный университет ▪ Orcid
Аннотация
Рассмотрен вопрос о влиянии концентрации твердой фазы на снижение энергетических затрат и удельной энергоемкости при транспортировании пульпы. Показан порядок подготовки гидросмеси из теку щих хвостов обогащения. Приведена схема и описана работа гидрофицированного агрегата для сгущения и гидротранспорта закладочных смесей. Показана схема движения твердых частиц в одном из узлов комплекса – пластинчатом сгустителе. В сводной таблице указаны основные конструктивные параметры и характеристики пластинчатого сгустителя. Приведен общий вид лабораторной установки, используемой для экспериментальных исследований с гидросмесью при различных концентрациях. Представлен пример расчета производительности, плотности и удельной нагрузки. Определена зависимость напряжения сдвига от градиента скорости для различных концентраций пульпы. Проведены экспериментальные исследования процесса сгущения получения гидросмеси из текущих хвостов обогащения. Выявлено, что геометрические размеры сгустителя зависят от концентрации твердой фазы в транспортируемой смеси. Сделан вывод, что расход гидросмеси и потери напора являются функциями реологических характеристик вязкопластической гидросмеси и могут быть рассчитаны по выведенным расчетным зависимостям.
Введение
Главными задачами горного производства и технологий, связанных с гидравлическим транспортом продуктов переработки минерального сырья, являются дальнейшее снижение затрат энергии, уменьшение удельной энергоемкости технологических процессов и освоение безотходных технологий процессов [1-3]. Определяющим и эффективным направлением решения задач безотходных технологий является применение систем добычи полезных ископаемых подземным способом с закладкой выработанного пространства [4-6]. Данный процесс должен включать использование отходов производства (хвостов обогащения) [7-9]. Это повлияет на более интенсивное освоение месторождений, позволит решать вопросы охраны недр и окружающей среды [10, 11].
Добыча руды системами с закладкой горных выработок в настоящее время в России составляет не более 24 % от общей добычи подземным способом. Большинство горно-добывающих предприятий цветной металлургии имеют обогатительные фабрики. Возрастающие объемы закладочных работ определяют необходимость создания и применения новых закладочных смесей, обеспечивающих высокие физико-механические свойства закладочного массива при минимальном расходе вяжущего материала (цемента) [12-14]. При увеличении тонкости помола твердой фазы из-за обеднения руды значительно возрастает выход тонких классов крупности – текущих хвостов обогащения [15-17]. Именно текущие хвосты могут быть основным материалом для закладочных смесей [18-20].
Подготовка смеси на основе текущих хвостов обогащения предусматривает несколько технологических операций [21-23]: сгущение хвостовой пульпы в сгустительных устройствах до высокой концентрации твердой фазы; гидравлическое транспортирование сгущенной смеси с помощью насосного оборудования на закладочные комплексы шахты в расходные емкости [24-26]; дозирование сгущенной гидросмеси в специальных устройствах-активаторах и смешивание смеси с вяжущим материалом; доставка и укладка подготовленной закладочной смеси в горную выработку [27-29].
Первоначальной и основной технологической операцией подготовки закладочной смеси является сгущение гидросмеси, поступающей после технологического процесса обогащения руды [30-32]. В практике горного дела применяются различные сгустители, отличающиеся по конструкции и способу действия, – радиальные, гидроциклоны, центрифуги и др. [33, 34]. В последние годы применяются пластинчатые сгустители [35-37]. Отличительной особенностью сгустителей пластинчатого типа от традиционных радиальных являются меньшие габаритные размеры при равной удельной нагрузке на единицу площади осаждения.
Несмотря на значительные и подтвержденные практически преимущества пластинчатых сгустителей, аппараты этого типа к настоящему времени еще не нашли широкого применения в технологиях гидротранспорта в схемах сгущения хвостовых пульп для получения гидросмесей высоких концентраций. Проблема заключается в недостаточном теоретическом и экспериментальном обосновании процесса осаждения твердых частиц в межпластинных каналах и механизма формирования структуры сгущенного осадка. Это не позволяет создать эффективную конструкцию пластинчатого сгустителя для получения высококонцентрированных гидросмесей для приготовления закладочных смесей [38-40].
Целью работы является выявление параметров, при которых оборудование будет функционировать с меньшими энергетическими и эксплуатационными затратами. В работе рассматриваются в совокупности процессы сгущения (обезвоживания) тонкодисперсных хвостов обогащения, гидравлического транспортирования высококонцентрированных гидросмесей как инертного наполнителя закладочной смеси и зависимости энергетических характеристик грунтовых насосов от реологических свойств перекачиваемых закладочных смесей.
Методы
Гидрофицированный агрегат (рис.1) для подготовки и транспортирования закладочных смесей состоит из последовательно смонтированных блоков: I – расхода (приема) поступающей гидросмеси; II – обезвоживания; III – подачи сгущенной смеси в грунтовый насос; IV – гидротранспорта; V – удаления слива.
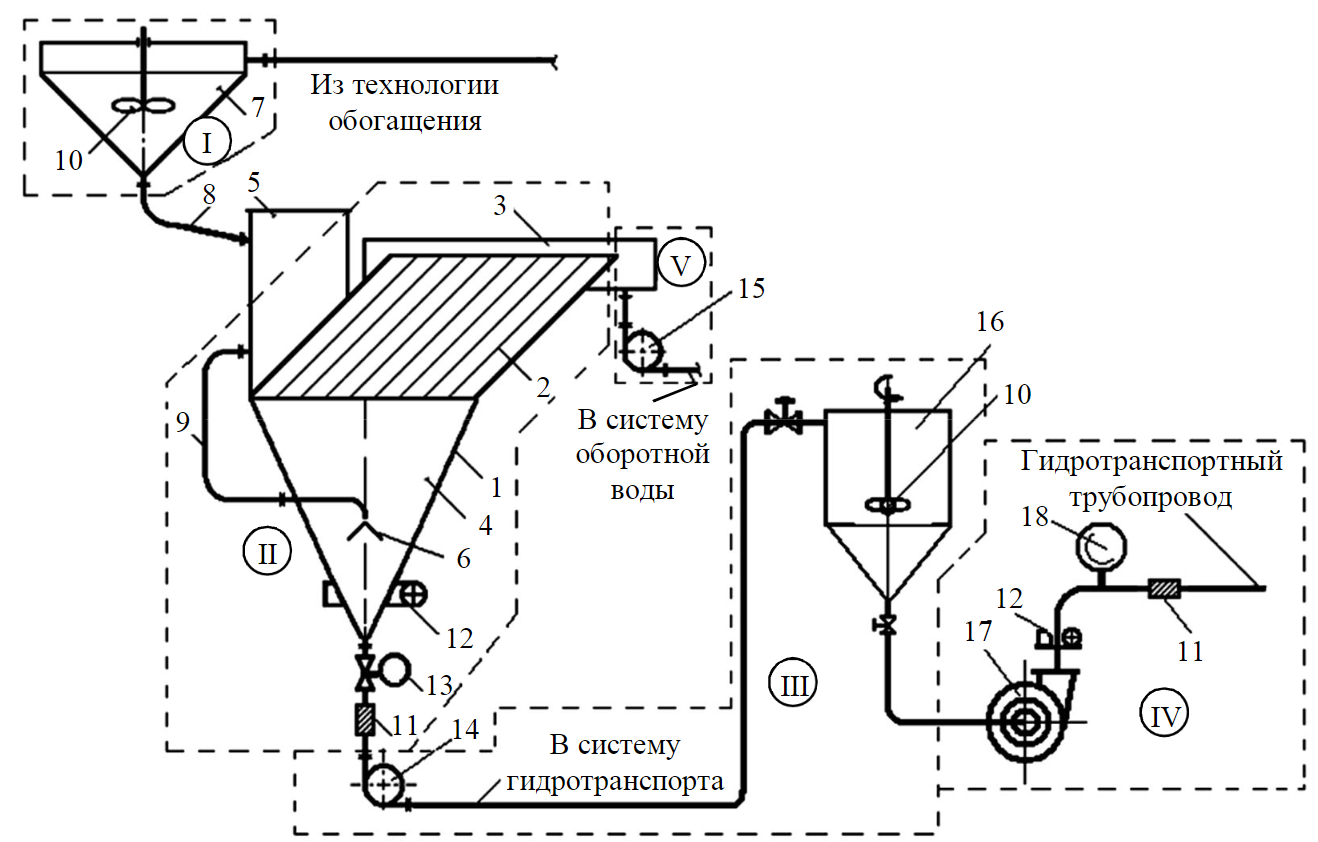
Рис.1. Схема гидрофицированного агрегата для сгущения и гидротранспорта закладочных смесей
Сгущаемая гидросмесь (текущие хвосты обогащения руды), поступает из технологии обогащения в бункер исходной пульпы 7 с импеллером 10 (для предотвращения осаждения твердых частиц). Далее гидросмесь по подводящему трубопроводу 8 заполняет уравнительную емкость 5 и по трубопроводу 9 загружается объем сгустителя (бункер-накопитель 4, блок наклонных пластин 2 и сливной лоток 3). Гидросмесь протекает между пластинами сгустителя 1 с отбойным козырьком 6, где происходит выпадение (седиментация) твердых частиц на всей длине канала. Осадок твердых частиц, формирующийся на нижних пластинах, под действием собственного веса перемещается сверху вниз и осаждается в нижней части бункера-накопителя 4, где формируется сгущенная гидросмесь. Оборотная вода переливается через верхние кромки пластин в сливной лоток 3, установленный по всему периметру блока пластин, и удаляется с помощью насоса 15 в хвостохранилище.
Сгущенная до необходимой концентрации гидросмесь при помощи пульпонасоса 14 подается по трубопроводу с задвижкой 13 в бункер 16 сгущенной гидросмеси, далее при помощи грунтового насоса 17 поступает в гидротранспортный трубопровод и транспортируется на закладочный комплекс, где производится подготовка твердеющей закладочной смеси. Объем смеси и давление данной системы замеряется расходомерами 11 и 12 и манометром 18.
Отличительной особенностью рассматриваемого гидрофицированного комплекса является то, что все технологические операции приготовления закладочной смеси и гидравлического транспортирования объединены в одном агрегате. В такой комплектации упрощаются процессы регулирования и управления технологическим процессом сгущения и гидравлического транспорта сгущенной закладочной смеси. Исследования гидрофицированного комплекса по представленной на рис.1 схеме проводились в лаборатории Горного университета на опытном образце пластинчатого сгустителя. В качестве опытных гидросмесей использовались хвосты обогащения медной руды Джезказганского ГМК.
Основными элементами агрегата для сгущения и гидравлического транспортирования являются пластинчатый сгуститель и грунтовый насос. Особенностью рабочего процесса пластинчатых (тонкослойных) сгустителей является то, что благодаря особой конструкции сгустительного блока 2 улавливаются и отправляются в сгущенный продукт твердые частицы хвостов обогащения мелких классов, до 0,038 мм. Принцип работы пластинчатых сгустителей – противоточный. Сгущаемый поток, содержащий частицы заданного гранулометрического состава движется снизу вверх, а обезвоженный осадок твердых частиц – по нижним пластинам в противоположном направлении – сверху вниз и накапливается в бункере-накопителе 4. Режим работы гидротранспортного агрегата контролируется набором приборов: плотномеры ВИП-2МР; индукционные расходомеры ЭМИС-МАГ 270 на выходе из бункера-накопителя и на нагнетательном патрубке грунтового насоса.
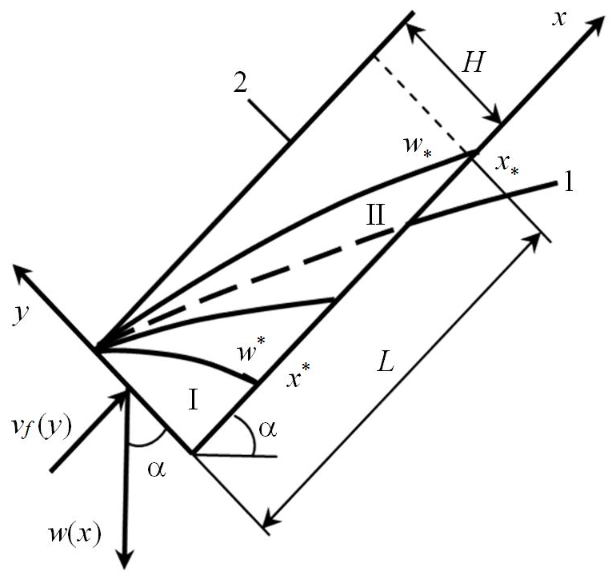
Рис.2. Схема движения твердых частиц в межпластинном канале пластинчатого сгустителя
Основным расчетным параметром пластинчатых сгустителей является длина зоны осаждения твердых частиц – пластин и канала, образованного нижней и верхней пластиной. На рис.2 показана схема осаждения твердых частиц в пространстве между нижней (1) и верхней (2) пластинами. На рис.2: L – общая длина пластин; Н – расстояние между нижней и верхней пластинами; α – угол наклона пластин, град; w*, w* – максимальная и минимальная скорость осаждения твердых частиц, м/с; x*, x* – расстояние формирования осадка твердого материала на нижних пластинах; νf(y) – средняя по площади сечения канала скорость входного потока гидросмеси, м/с; I и II – области полного замутнения (присутствуют все частицы гранулометрического состава гидросмеси) и постепенного осветления входного потока гидросмеси.
Стационарный поток гидросмеси в канале между пластинами обеспечивается при ограниченном значении чисел Рейнольдса и Фруда. Для стационарного режима течения справедливо предположение о гравитационном сносе твердых частиц гранулометрического состава с линий тока гидросмеси. Предварительные эксперименты показали, что критическое число Рейнольдса для обеспечения ламинарного и стационарного режима не превышает 400, т.е.
где Hp – высота канала, м; νc – средняя скорость гидросмеси, м/с; ν – кинематическая вязкость гидросмеси, м2/с.
Для стационарного режима течения гидросмеси были получены значения основных конструктивных и геометрических параметров пластинчатого сгустителя (табл.1), совокупность которых составляет математическую модель рабочего процесса пластинчатого сгустителя.
Таблица 1
Конструктивные, геометрические параметры и характеристики пластинчатого сгустителя
Параметр |
Полученные значения |
Средняя скорость гидросмеси, м/с |
|
Высота канала, м |
|
Участок пластин с ламинарным потоком, м |
Для ρs = 2,4 т/м3 (плотность твердого вещества) Lлам = 0,369 |
Общая длина пластин, м |
|
Угол наклона пластин, град |
|
Площадь каналов, м2 |
|
Площадь слива, м2 |
|
Высота наклонной части, м |
|
Вместимость нижней части, м3 |
|
Производительность по твердому материалу, т/ч |
|
Конструктивные и геометрические параметры сгустителя: 1 – разгрузочный канал; 2 – бункер-накопитель; 3 – загрузочный трубопровод; 4 – блок пластин; 5 – уравнительная емкость; 6 – седиментационный канал; 7 – сливной лоток; 8 – сливной канал; 9 – наклонные пластины |
![]() |
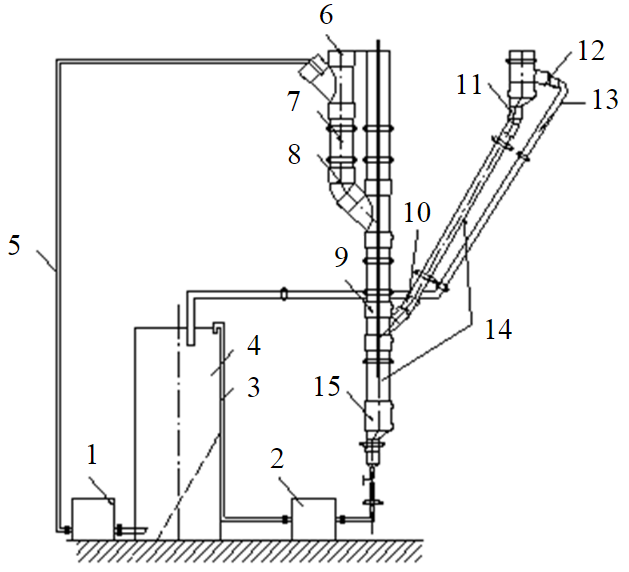
Рис.3. Схема лабораторного пластинчатого сгустителя 1, 2 – насосные агрегаты; 3 – отвод сгущенной гидросмеси; 4 – расходный бак; 5 – загрузочная труба; 6 – входная емкость; 7 – успокоительная емкость; 8 – переход; 9, 15 – бункер-накопитель; 10 – наклонный модуль; 11 – переход на сливной трубопровод; 12, 13 – сливная труба; 14 – стеклянная вставка ∅ 50 мм
Из приведенных расчетов видно, что геометрические и конструктивные характеристики рабочего процесса пластинчатого сгустителя определяются режимом течения гидросмеси в межпластинных каналах Re, гидравлической крупностью твердых частиц гранулометрического состава P(di), производительностью на входе в сгуститель Qi.
Обсуждение результатов
Для проверки адекватности полученной математической модели были проведены эксперименты. Исследования процессов сгущения производились на специально разработанном лабораторном образце тонкослойного пластинчатого сгустителя (рис.3).
Исследуемая гидросмесь с заданными концентрацией и гранулометрическим составом твердых частиц загружадась в расходный бак и перекачивалась по экспериментальному контуру. При достижении установившегося режима работы стенда (через 5-10 мин) отбирались пробы на сливе сгустителя (из трубы 13) и в его разгрузке (3). Пробы анализировались на плотность, определялась концентрация твердых частиц. В процессе экспериментов измерялась высота сгущенного слоя в нижней части сгустителя через прозрачную вставку. По характеру изменения высоты сгущенного слоя определялась стабильность режима работы сгустителя. Данные по содержанию твердых частиц в сливе и разгрузке использовались для определения эффективной площади сгущения по исходному, сгущенному и сливному продуктам. По результатам работы на нескольких концентрациях твердой фазы с учетом удельных параметров сгустителя выбирался наиболее эффективный режим по величине максимальной концентрации в сгущенном продукте и меньшему содержанию твердого в сливе пульпы. Экспериментальные результаты по удельным параметрам пересчитывались на работу промышленных образцов гравитационных сгустителей.
При выполнении экспериментальных исследований на лабораторном пластинчатом сгустителе, производились замеры исходного потока пульпы, приготовленной из хвостов обогащения медной руды. Содержание твердой фазы на входе в сгуститель составляло около 5 % по объему смеси cисх. Производительность загрузочного насоса (2 на рис.3) составляла около 5 л/мин. Производительность системы по твердому материалу составляла около 0,25·10–3 м3/мин (0,675 кг/мин). В процессе экспериментов замерялось время осаждения твердой фазы в нижней части сгустителя до заданной высоты бункера-накопителя, по которому определялась скорость стесненного осаждения твердых частиц. Высота слоя осевших частиц наблюдалась через стеклянную вставку. Изменение расхода сгущенной гидросмеси на выходе из сгустителя с помощью пробкового крана на отводящей трубе меняло концентрацию твердых частиц в сгущенной гидросмеси. Измерялся расход осветленной воды и содержание в ней твердых частиц. Для измерения распределения концентрации твердых частиц по высоте сгустителя (по высоте вертикальной части) в корпусе были просверлены отверстия диаметром 10 мм, через которые отбирались пробы пульпы в специальные тарированные емкости [30]. После отбора пробы отверстия заглушались пластмассовыми заглушками. По времени наполнения мерной емкости определялся расход. Концентрация твердых частиц в пробах определялась взвешиванием на рычажных весах с разновесами. Основные измеряемые величины: время отбора пробы t, с; измерение объема отобранной пробы Wпр, м3; взвешивание пробы Gпр, г; высота слоя уплотненного осадка h, мм; площадь сечения прохождения пульпы Sэф, мм2; количество твердой фазы в гидросмеси qтв, т; концентрация твердой фазы ств, %.
По значениям этих параметров рассчитывались:
- производительность сгустителя в разгрузке аппарата
- плотность сгущенной гидросмеси
- удельная нагрузка на эффективную площадь сгущения
где D – диаметр бункера-накопителя лабораторного сгустителя, D = 50 мм; ρтв – плотность хвостов обогащения медной руды, ρтв = 2700 кг/м3.
Опытные данные по сгущению гидросмеси хвостов обогащения медной руды в лабораторном пластинчатом сгустителе приведены в табл.2.
Таблица 2
Опытные данные по исследованию сгущения гидросмеси хвостов обогащения медной руды
Время, c |
Объем |
Вес |
Плотность смеси, кг/м3 |
Концентрация, |
Удельная нагрузка |
Удельная нагрузка |
Высота осадка, м |
15 |
312,5 |
413,43 |
1323 |
20,0 |
38,21 |
18,34 |
0,318 |
20 |
277 |
413,40 |
1492 |
29,0 |
25,40 |
20,57 |
0,212 |
25 |
260 |
429,50 |
1652 |
38,4 |
19,10 |
20,68 |
0,159 |
30 |
250 |
453,06 |
1812 |
47,8 |
16,30 |
22,00 |
0,127 |
Результаты экспериментов и опытные данные свидетельствуют о зависимости геометрических параметров сгустителя от значения концентрации в разгрузке аппарата. При изменении концентрации изменялись высота слоя осадка в разгрузочной части сгустителя и удельная нагрузка на эффективную площадь сгущения. При изменении концентрации в разгрузке сгустителя от 0,2 до 0,5 % высота уплотненного слоя изменялась от 318 до 127 мм. Удельная нагрузка при этом изменялась от 38,21 м3/(ч∙м2) по пульпе и 18,34 т/(ч∙м2) по твердому материалу до 16,29 м3/(ч∙м2) и 22 т/(ч∙м2). Причем удельная нагрузка по пульпе уменьшалась с увеличением концентрации сгущенной гидросмеси, а нагрузка по твердой фазе потока – увеличивалась.
В процессе экспериментов производились отборы проб из наклонного модуля в трех его сечениях: на входе, в середине и на выходе (слив сгустителя). Гранулометрический состав твердых частиц в отобранных пробах определялся ситовым анализом. Для этого пробы отфильтровывались, сушились и рассеивались через набор сит. Определение количества материала по классам крупности производилось путем взвешивания отдельных классов. Точность ситового анализа составляла около 5 %. На основании ситового анализа производился расчет средневзвешенного диаметра твердых частиц.
В качестве предварительного вывода по результатам экспериментов на лабораторном сгустителе с тонкослойным модулем отметим, что основная часть мелких частиц осаждается в наклонном канале, а геометрические размеры сгустителя определяют величину концентрации твердой фазы в сгущенном продукте. При изменении расхода в разгрузке сгустителя и постоянном расходе на его входе изменяется высота уплотненного осадка и концентрация твердого в сгущенной гидросмеси. Производительность сгустителя по твердому материалу и расход на входе во всех экспериментах оставались постоянными.
Гидравлический транспорт сгущенной гидросмеси на закладочный комплекс
Анализ экспериментальных результатов показывает, что гидросмесь в разгрузке сгустителя формируется высококонцентрированной вязкопластической гидросмесью, течение которой описывается формулой Шведова – Бингама [41]:
где τ – касательное напряжение; τ0 – статическое напряжение; μ – коэффициент динамической вязкости;
Данный предварительный вывод о характере сгущенной гидросмеси подтверждается экспериментальными данными, полученными с помощью ротационного вискозиметра. В формуле Шведова – Бингама определяющим параметром является вязкость, которая изменяется в зависимости от концентрации твердых частиц от минимальных (вязкость оборотной воды) до максимальных значений, характерных для пастовых гидросмесей. Эксперименты проводились на автоматическом универсальном ротационном вискозиметре Rheotest RN 4.1.
В процессе экспериментов определялась зависимость напряжения сдвига от градиента скорости сдвига для различных концентраций твердых частиц сν в объеме исследуемой гидросмеси (табл.3).
Таблица 3
Значения измеренных параметров по модели Шведова – Бингама
Скорость сдвига, с–1 |
Напряжения сдвига (Па) при различных объемных концентрациях твердого материала |
||||
сν = 0,233 |
сν = 0,4 |
сν = 0,498 |
сν = 0,525 |
сν = 0,562 |
|
32,52 |
3,18 |
6,88 |
17,06 |
33,58 |
82,93 |
33,25 |
3,20 |
7,00 |
17,20 |
33,92 |
83,33 |
34,67 |
3,48 |
7,23 |
17,48 |
34,31 |
84,11 |
35,71 |
3,55 |
7,42 |
17,68 |
34,60 |
84,68 |
35,89 |
3,65 |
7,44 |
17,71 |
34,65 |
84,80 |
37,06 |
3,78 |
7,63 |
17,94 |
34,98 |
85,37 |
41,11 |
4,02 |
8,29 |
18,74 |
35,98 |
87,37 |
41,33 |
4,08 |
8,32 |
18,78 |
36,04 |
87,47 |
41,78 |
4,12 |
8,40 |
18,87 |
36,14 |
87,70 |
41,70 |
4,11 |
8,38 |
18,85 |
36,10 |
87,65 |
42,15 |
4,15 |
8,48 |
18,94 |
36,26 |
87,87 |
42,66 |
4,18 |
8,57 |
19,08 |
36,44 |
88,12 |
44,33 |
4,20 |
8,86 |
19,45 |
37,10 |
88,94 |
44,87 |
4,24 |
8,95 |
19,56 |
37,29 |
89,20 |
46,22 |
4,41 |
9,19 |
19,84 |
37,77 |
89,39 |
46,61 |
4,46 |
9,25 |
19,92 |
37,91 |
90,10 |
48,11 |
4,65 |
9,54 |
20,23 |
38,45 |
90,80 |
48,21 |
4,67 |
9,55 |
20,25 |
38,48 |
90,84 |
50,24 |
4,92 |
9,87 |
20,68 |
39,22 |
91,78 |
52,58 |
5,22 |
10,24 |
21,20 |
39,83 |
92,87 |
53,00 |
5,27 |
10,30 |
21,26 |
39,94 |
93,06 |
54,53 |
5,30 |
10,50 |
21,50 |
40,34 |
93,77 |
54,80 |
5,32 |
10,60 |
21,54 |
40,41 |
93,89 |
54,89 |
5,33 |
10,61 |
21,55 |
40,43 |
93,93 |
Экспериментальные данные позволяют рассчитать динамическую вязкость гидросмесей как отношение напряжения сдвига к градиенту скорости сдвига при соответствующих значениях начального напряжения.
Экспериментальная кривая вязкости описывается зависимостью вида
где μ0 – коэффициент динамической вязкости чистой воды, Па∙с.
Формула устанавливает связь вязкости сгущенной гидросмеси и концентрации твердых частиц и определяет удельные потери напора при гидротранспорте сгущенных гидросмесей.
Для установления функциональной зависимости потерь напора при течении гидросмеси по трубопроводу запишем формулу Шведова – Бингама в виде
где σ=τ0/τ – относительное напряжение.
Для статического напряжения можно записать:
а общее напряжение будет равно
Выражение для потерь давления при течении гидросмеси по трубопроводу:
Потери давления будут равны
где iсм – потери напора гидросмеси, м/м; ρ – плотность смеси, кг/м3;
Если скорость сдвига для ламинарного режима течения равна
В итоге формула потерь напора для вязкопластической гидросмеси запишется в следующем виде:
В отличие от известной зависимости удельных потерь напора Дарси – Весбаха для обычных гидросмесей, полученная формула учитывает относительные значения касательных напряжений, возникающих при течении вязкопластической гидросмеси. Относительное напряжение сдвига изменяется от 0 до 1. Если относительное напряжение равно 0, гидросмесь не проявляет вязкопластических свойств и представляет собой обычную ньютоновскую жидкость. Если относительное напряжение равно 1, то гидросмесь представляет собой твердое тело. Главным параметром, определяющим тип гидросмеси (ньютоновская или вязкопластическая) является объемная концентрация твердой фазы.
Заключение
В результате проведенного комплексного теоретического и экспериментального исследования гидрофицированного агрегата для сгущения и гидротранспорта высококонцентрированных гидросмесей продуктов обогащения полиметаллической руды на закладочные комплексы горного предприятии решена важная задача создания ресурсосберегающей техники и технологии с разработкой научно обоснованной методики расчета процессов сгущения и гидравлического транспорта. В ходе исследований установлено:
- Эффективным для подготовки закладочной смеси является гидрфицированный агрегат, включающий устройство для сгущения хвостовой пульпы до высоких концентраций твердой фазы и грунтовый насос для перекачки сгущенной закладочной смеси на закладочные комплексы горного предприятия.
- Движение хвостовой пульпы в канале между пластинами сгустителя сопровождается осаждением твердых частиц по всей длине нижних пластин. Характер осаждения твердого материала зависит от скорости стесненного падения твердых частиц (гидравлической крупности), являющейся функцией вязкости пульпы. Физической моделью процесса сгущения (обезвоживания) гидросмесей хвостов обогащения является гипотеза гравитационного сноса твердых частиц с линий тока, взятая за основу при разработке алгоритма расчета конструктивных, технологических и геометрических параметров сгустителей пластинчатого типа.
- Закон распределения твердых частиц по длине зоны осаждения, наличие в сгущенном осадке преимущественно частиц мелких классов крупности и высокая степень концентрации твердых частиц свидетельствуют о том, что сгущенный продукт характеризуется неньютоновскими реологическими свойствами.
- Для механизма течения исследуемых гидросмесей наиболее приемлема теория деформации неньютоновских жидкостей Шведова – Бингама и академика П.И.Ребиндера, в соответствии с которой при течении структурированных гидросмесей характерны три режима: с неразрушенной структурой потока при τ< τ0 (ламинарный режим течения); с непрерывно разрушающейся структурой, когда τ ≥ τ0 (переходной режим течения от ламинарного к турбулентному течению); с разрушенной структурой при τ >> τ0 (развитый турбулентный режим течения).
- Расход гидросмеси и потери напора являются функциями реологических характеристик вязкопластической гидросмеси и могут быть рассчитаны по выведенным расчетным зависимостям, которые в совокупности определяют математическую модель течения вязкопластических гидросмесей хвостов обогащения руд по гидротранспортным трубопроводам.
- Результаты теоретических исследований процессов сгущения и гидротранспорта сгущенных гидросмесей подтверждаются опытными данными, полученными при выполнении экспериментальных исследований на опытном образце пластинчатого сгустителя и лабораторной гидротранспортной установки.
Литература
- Бабокин Г.И. Исследование влияния технологической схемы работы и длины лавы на удельный расход электрической энергии очистного комбайна // Горный информационно-аналитический бюллетень. 2021. № 2. С. 139-149. DOI: 10.25018/0236-1493-2021-2-0-139-149
- Пичуев А.В., Мартышкин В.В. Комплексная оценка энергоэффективности тоннелепроходческих механизированных комплексов // Технический оппонент. 2019. № 2. С. 26-28.
- Садридинов А.Б., Пичуев А.В., Карпенко С.М. Комплексный анализ показателей энергоэффективности промышленных предприятий // Энергобезопасность и энергосбережение. 2018. № 2. С. 15-17. DOI: 10.18635/2071-2219-2018-2-15-17
- Голик В.И., Дмитрак Ю.В., Чжун Чан, Масленников С.А. Использование хвостов обогащения в приготовлении твердеющих закладочных смесей // Известия Уральского государственного горного университета. 2018. №2 (50). С. 95-101. DOI: 10.21440/2307-2091-2018-2-95-101 99
- Куликова А.А. Ковалева А.М. Применение хвостов обогащения в качестве закладки выработанного пространства рудников // Горный информационно-аналитический бюллетень. 2021. № 2-1. С. 144-154. DOI: 10.25018/0236-1493-2021-21-0-144-154
- Смирнов О.Ю. Исследование условий применения систем разработки месторождений с закладкой в различных горно-геологических условиях // Известия вузов. Горный журнал. 2019. № 5. С. 14-20. DOI: 21440/0536-1028-2019-5-14-20
- Alexakhin A., Sala D., Golovin K., Kovalev R. Reducing energy costs for pipeline transportation // Transportation Research Procedia. 2021. Vol. 57. P. 24-32. DOI: 10.1016/j.trpro.2021.09.021
- Aben Kh., Krupnik L.A., Shaposhnik Y.N. Technology of blasting at the contact with backfilled stopes // Горный журнал Казахстана. 2017. № 11. С. 4 -5.
- Lèbre É., Corder G. D., Golev A. Sustainable practices in the management of mining waste: A focus on the mineral resource // Minerals Engineering. Vol. 107. P. 34-36. DOI: 10.1016/j.mineng.2016.12.004
- Крупник Л.А., Абен Х.Х., Мырзахметов С.С. и др. Отбойка руды на контакте с закладкой при разработке подкарьерных запасов // Взрывное дело. 2017. № 117-74. С. 205-213.
- Садридинов А.Б., Пичуев А.В., Петуров В.И. Повышение энергоэффективности горнопроходческих работ // Транспортная инфраструктура Сибирского региона. 2016. Т. 1. С. 641-645.
- Александрова Т.Н., Потемкин В.А. Разработка методики оценки процесса гидроциклонирования c учетом реологических параметров минеральной суспензии // Записки Горного института. 2021. Т. 252. С.908-916. DOI: 10.31897/PMI.2021.6.12
- Власак П. Течение крупнозернистых гидросмесей в трубах // Записки Горного института. 2017. Т. 225. С. 338-341. DOI: 10.18454/2017.3.338
- Гембицкая И.М., Гвоздецкая М.В. Трансформация зерен технологического сырья при получении мелкодисперсных порошков // Записки Горного института. 2022. Т. 249. С.401-407. DOI: 10.31897/PMI.2021.3.9
- Ревель-Муроз П.А., Фридлянд Я.М., Кутуков С.Е. и др. Оценка гидравлической эффективности по данным мониторинга технологических режимов эксплуатации // Наука и технологии трубопроводного транспорта нефти и нефтепродуктов. 2019. № 9. С. 8-19. DOI: 10.28999/2541-9595-2019-9-1-8-19
- Устинова Я.В., Коптев В.Ю., Крук М.Н. Механические свойства калийсодержащей руды как фактор выбора способа обработки материала // Кузнечно-штамповочное производство. Обработка материалов давлением. 2021. № 6. С. 21-30.
- Cheng Q., Zheng A., Yang L. et al. Studies on energy consumption of crude oil pipeline transportation process based on the unavoidable exergy loss rate // Case Studies in Thermal Engineering. 2018. Vol. 12. P. 8-15. DOI: 10.1016/j.csite.2018.02.005
- Авксентьев С.Ю., Сержан С.Л., Труфанова И.С. Определение параметров гидротранспорта хвостов обогащения железной руды качканарского ГОКа // Горный информационно-аналитический бюллетень. 2018. № 11. С. 3-14. DOI: 10.25018/0236-1493-2018-4-11-3-14
- Большунова О.М., Ватлина А.М., Коржев А.А. Влияние концентрации гидросмеси на энергоэффективность работы системы насос-пульпопровод // Инновации и перспективы развития горного машиностроения и электромеханики: IPDME-2021, 22-23 апреля 2021, Санкт-Петербург, Россия. Санкт-Петербургский горный университет, 2021. С. 147-149.
- Александров В.И., Тимухин С.А., Махараткин П.Н. Энергетическая эффективность гидравлического транспорта хвостов обогащения железной руды на Качканарском ГОКе // Записки Горного института. 2017. Т. 225. С. 330-337. DOI: 10.18454/PMI.2017.3.330
- Бауман А.В. Анализ агрегативной и седиментационной устойчивости технологических пульп // Обогащение руд. 2018. № 2. С. 55-60. DOI: 10.17580/or.2018.02.10
- Кибирев В.И., Бауман А.В., Никитин А.Е. О создании современных российских сгустителей // Горная промышленность. 2017. № 5 (135). С. 33-35.
- Кузьмин Е.В., Святецкий В.С., Марковец В.В. Сгущение отходов переработки урановых руд с получением пасты для подземного размещения // Горный журнал. 2018. № 7. С. 73-77. DOI: 10.17580/gzh.2018.07.14
- Avksentiev S.Y., Avksentieva E.Y. Determining the parameters of the hydraulic transport of tailings for processing iron ore // IOP Conference Series: Earth and Environmental Science. 2018. Vol. 194. № DOI: 10.1088/1755-1315/194/3/032003
- Qinglin Cheng, Anbo Zheng, Lu Yang et al. Studies on energy consumption of crude oil pipeline transportation process based on the unavoidable exergy loss rate // Case Studies in Thermal Engineering. 2018. Vol. 12. P. 8-15. DOI: 10.1016/j.csite.2018.02.005
- Коптев В.Ю. Выбор транспортных машин для проектирования транспортных систем горных предприятий // Инновации и перспективы развития горного машиностроения и электромеханики: IPDME-2017, 23-24 марта 2017, Санкт-Петербург, Россия. Санкт-Петербургский горный университет, 2017. С. 57-61.
- He , Jiang R., Zhang J. Analysis of minimum specific energy consumption and optimal transport concentration of slurry pipeline transport systems // Particuology. 2021. Vol. 66. P. 38-37. DOI: 10.1016/j.partic.2021.08.004
- Zhen Li, Songlin Wu, Shiwen Zhang et al. Optimization of Land Reuse Structure in Coal Mining Subsided Areas Considering Regional Economic Development: A Case Study in Pei County, China // 2020. Vol. 12. Iss. 8. №3335. DOI: 10.3390/su12083335
- Masip-Macía Y., Pedrera J., Castro M.T. et al. Analysis of Energy Sustainability in Ore Slurry Pumping Transport Systems // Sustainability. 2019. Vol. 11. 11. № 3191. DOI: 10.3390/su11113191
- Фролов Д.В. Исследование и обоснование подходов к оптимизации процессов сгущения угольных шламов // Вестник Кузбасского государственного университета. № 2(126). C. 61-69. DOI: 10.26730/1999-4125-2018-2-61-69
- Kaiwei Chu, Jiang Chen, Yu A.B., Williams R.A. Numerical studies of multiphase flow and separation performance of natural medium cyclones for recovering waste coal // Powder Technology. Vol. 314. P. 532-541. DOI: 10.1016/j.powtec.2016.10.047
- Watling H.R., Collinsona D.M., Watling R.J., Shiers D.W. Simulated heap leaching and recovery of multiple elements from a mineralised black shale // Hydrometallurgy. 2017. Vol. 167. Р. 48-57. DOI: 10.1016/j.hydromet.2016.10.015
- Jinyi Tian, Long Ni, Tao Song et al. An overview of operating parameters and conditions in hydrocyclones for enhanced separations // Separation and Purification Technology. Vol. 206. P. 268-285. DOI: 10.1016/j.seppur.2018.06.015
- Akhbarifar S., Shiruani M. Improving cyclone efficiency for small particles // Chemical Engineering Research and Design. 2019. Vol. 147. P. 483-492. DOI: 10.1016/j.cherd.2019.05.026
- Тусупбаев Н.К., Батырбаева А., Амантай Н. и др. Изучение процесса сгущения и фильтрации свинцовоцинковых концентратов присутствии неионогенных полимеров и их смеси с анионными полиэлектролитами // Материалы Международной практической интернет-конференции «Актуальные проблемы науки», 22 ноября 2018, Алматы, Казахстан. Satbauev University, 2018. С. 1-6. DOI: 10.31643/2018.025
- Бусарев А.В., Селюгин А.С., Ягин Я.В.Исследование процессов очистки нефтесодержащих стоков машиностроительных предприятий с применением напорных гидроциклонов // Международный журнал прикладных и фундаментальных исследований. 2017. № 8-2. С. 190-194.
- Vahidifar S., Saffarian R., Hajidavalloo E. Introducing the theory of successful settling in order to evaluate and optimize the sedimentation tanks // Meccanica. 2018. Vol. 53. P. 3477-3493. DOI: 10.1007/s11012-018-0907-2
- Svetlov A., Makarov D., Selivanova E. et al. Heap leaching and perspectives of bioleaching technology for the processing of low-grade copper-nickel sulfide ores in Murmansk region, Russia // Journal of the Polish Mineral Engineering Society (Inzynieria Mineralna). 2017. Vol. 18. № 1 (39). Р. 51-57.
- Bagheri G., Bonadonna C. On the drag of freely falling non-spherical particles // Powder Technology. 2016. Vol. 301. P. 526-544. DOI: 10.1016/j.powtec.2016.06.015
- Wachter S., Jakobs , Kolb T. Effect of Solid Particles on Droplet Size Applying the Time-Shift Method for Spray Investigation // Applied Science. 2020. Vol. 10. Iss. 21. № 7615. DOI: 10.3390/app10217615
- Матвиенко О.В., Базуев В.П., Сабылина Н.Р. и др. Исследование установившегося течения вязкопластического битумного вяжущего, описываемого моделью Шведова – Бингама, в цилиндрической трубе // Вестник Томского государственного архитектурно-строительного университета. 2019. № 3. C. 158-177. DOI: 10.31675/1607-1859-2019-21-3-158-177