Prediction of the geomechanical state of the rock mass when mining salt deposits with stowing
- 1 — Ph.D., Dr.Sci. Professor Wroclaw University of Science and Technology ▪ Orcid ▪ Scopus ▪ ResearcherID
- 2 — Ph.D. Associate Professor National University of Science and Technology “MISiS” ▪ Orcid ▪ Scopus
- 3 — Ph.D. Associate Professor National University of Science and Technology “MISiS” ▪ Orcid ▪ Scopus
- 4 — Master’s Degree Student Technische Hochschule Georg Agricola ▪ Orcid ▪ Scopus
- 5 — Ph.D. Assistant Lecturer Saint Petersburg Mining University ▪ Orcid ▪ Elibrary ▪ Scopus ▪ ResearcherID
Abstract
The technogenic impact of mining on the environment is analyzed and the transition to geotechnology with stowing to reduce the impact of mining operations is proposed. The results of the research work devoted to the justification of parameters of the development of salt deposits with stowing and the definition of the influence of stowing on the dynamics of deformation of the underworked rock massif are presented. The relevance of research aimed at creating a safe and efficient technology for the transition from systems with natural maintenance of stoping space to systems with stowing has been substantiated. The results of studies on qualitative and quantitative assessment of the state of the rock massif (by the finite element method using FLAC3D software), worked out by combines, are given and the dynamics of the impact of mining operations on the rock mass and the change in the maximum stresses during the hardening of the stowing in the chambers are revealed. The numerical modeling method is used to analyze the conditions of change in the state of the underworked rock mass, to establish the mechanisms of its deformation at various stages of development. It is recommended to use this approach for geotechnical assessment of the rock mass state in conditions of using development systems of different classes.
Introduction
The consumption of mineral resources is increasing, which, together with the exponentially growing population of the Earth, is becoming close to exponential. Russia is among the world leaders in the extraction and processing of minerals (extraction and processing of potash salts is no exception). With the increased demand of mankind for agricultural products, the demand for potash fertilizers is increasing. Russia is the second largest producer of potash fertilizers on the world stage. The industry demonstrates a significant increase in production volumes (the country accounts for about 19 %). High demand leads to the intensification of production, the need to enter new capacities and the construction of new mines.
The main production is concentrated in the Perm Region at the Verkhnekamskoye deposit of potassium and magnesium salts and is carried out at a depth of 400 m by technology with natural maintenance of the stoping space. For more than 50 years of development, many voids have formed in the subsurface, which seriously affect the rock mass behavior.
The Verkhnekamskoye deposit is not the only one in Russia – two mines are under construction at the Gremyachinskiy and Nivenskoye deposits. Their distinctive feature is the occurrence depth, which is 1150 and 1200 m, respectively. Taking into account the fact that the losses during the development of the Verkhnekamskoye deposit amount to about 65 % [1], it can be assumed that with an increase in the depth of development at the Gremyachinskiy and Nivenskoye deposits, they will approach 85 %. It is also very complicated to predict the persistence of the pillars stability over time [2]. The work experience at the Verkhnekamskoye deposit has shown that due to the plasticity of salt, elastic-plastic deformations occur in the pillars, which causes their destruction [3]. All this leads not only to an increase in the costs of providing technological extraction of minerals, enrichment and primary processing, but also to an increase in the risk of rock pressure in unpredictable forms. This means that rational geotechnology already at this stage is obliged to create a fundamental foundation and initiate the advanced development of science with the integration of mining experience and scientific and technological knowledge.
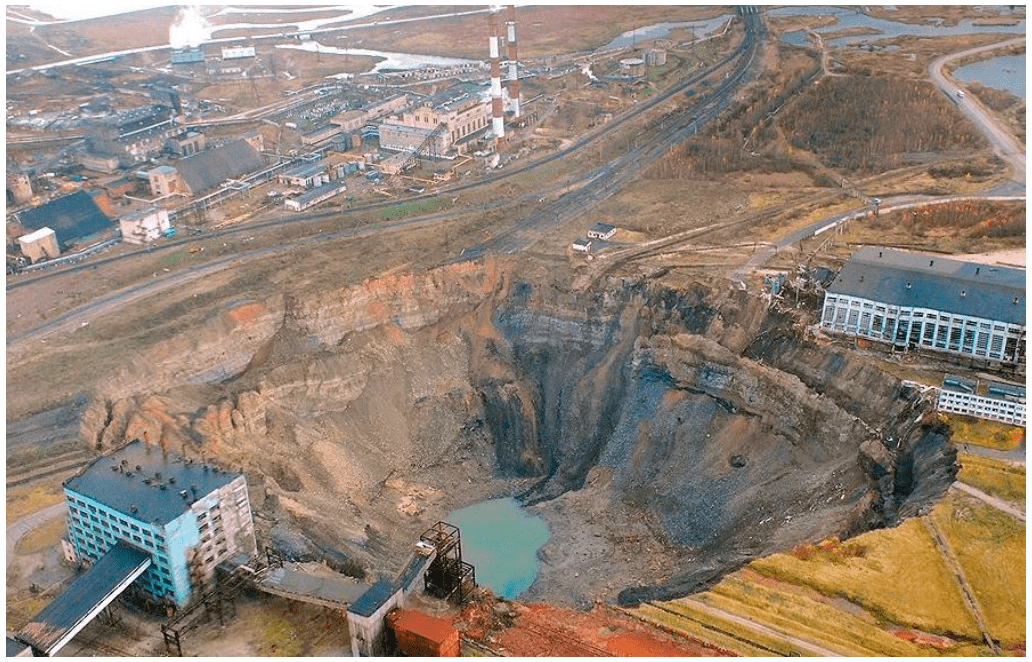
Fig.1. Sinkhole at the Uralkali mine (Perm Krai, Russia)
Due to the growing demand for mineral resources and the limited capacity of the biosphere, the earth surface is experiencing a huge technogenic load [4]. Due to the limited capacity of the biosphere to self-regulation and self-reproduction, it is necessary to create gentle technologies that ensure the sustainable mining development [5]. Mining waste and secondary concrete from dismantling works in civil construction may be suitable for use in large-scale earthworks, provided their neutral impact on the environment with respect to the spread of chemical or other sources of pollution [6]. Studies on the safe use of coal tailings after landscape reclamation were presented at the Technical University of Ostrava (Czech Republic) [7].
During the extraction of minerals, the natural state of the rock mass changes, which leads to a redistribution of stresses in it and the development of cracks [8, 9]. In some cases, cracks reach the day surface, which leads to its collapse or violation of the water-proof thickness and the breakthrough of water into the mine [10] (Fig.1).
Improving the organization of stoping operations will increase the completeness of excavation, reduce the cost of mining and the negative impact of geotechnology on the environment. Inaccurate and erroneous calculations lead to incorrect decision-making, which is the reason for the wrong choice of mining technology. All this leads to a violation of the integrity and tightness of large aquifers, which causes flooding of underground structures, a significant deterioration of general mine safety and changes in the hydrogeological situation of the deposit [11].
Similar problems are observed during the construction of various objects. Some examples were given in works where the causes of rocky landslides [12] and sinkholes of karst formations [13] were considered, which cause vibration fluctuations affecting the environment and objects [14]. Methods of reducing vibration fluctuations were considered in [15].
The use of mining and construction waste is an important issue worldwide [16]. But the use of man-made and industrial waste has a very local size and significance. The possibility of using large volumes of man-made waste (crushed waste rock from dumps) for large infrastructure projects – roads, railways, dams – are considered in [17]. In this regard, it is possible to identify the factors to be taken into account when using man-made waste: the suitability of waste in terms of their strength and environmental friendliness; financial costs for preparing for sale (crushing, sorting, creating a mixture, forming a rock mass, etc.); availability (availability in the right place, the optimal time and the required volume); environmental costs (transportation, storage, cleaning, etc.).
The development of a deposit using a hardening stowing of the developed space allows solving the issues of mining deep horizons, deposits in a combined method, effective management of rock pressure, preservation of the water-proof thickness and exclusion of the formation of dips on the day surface [18], which increases the safety of mining operations [19]. Geotechnology with a stowing gives the following economic effects: an increase in the life of the mine and the completeness of the excavation. The use of man-made waste in the stowing mixture allows to obtain a number of environmental effects: preservation of the day surface; utilization of man-made waste; reduction of the harmful effects of waste on the environment [20], and in total with the following economic results: no costs for the construction of waste rock dumps and tailings; exclusion of environmental deductions, etc. will lead to a multiplier effect [21].
It can be concluded that the creation of technologies for the extraction of potassium-magnesium salts using systems with a stowing based on enrichment waste and predicting the behavior of the underworked rock mass before the start of mining operations is an urgent task.
When applying the technology with the stowing of the developed space, it is necessary to solve several main tasks: to determine the optimal strength characteristics of the stowing rock mass after solidification; to identify the composition of the stowing material; to solve the issue of the completeness of filling the developed space with the stowing material.
The development of a methodology for calculating the strength characteristics of the stowing rock mass, the creation of a model for extracting minerals and modeling the processes that occur during the extraction of minerals are among the main tasks of modern geotechnology.
The main indicator of the stowing rock mass is its strength after solidification, when calculating which modern techniques rely on numerical modeling.
The most acute issue is the development of salt deposits [2], for which a chamber development system is used with the abandonment of chain pillars. But this system has a number of disadvantages:
- mineral losses up to 65 %;
- environmental pollution due to the large volume of man-made waste;
- constant redistribution of rock pressure due to the presence of voids and plasticity of the pillars;
- violation of the day surface due to the destruction of the pillars and caving formation;
- violation of the water-proof thickness and flooding of the mine.
During the development of potash deposits and the subsequent enrichment of the extracted ores, a large amount of man-made waste is formed, which is stored in dumps and tailings on the surface. The use of geotechnology with a hardening stowing during the development of potash deposits will eliminate a number of disadvantages that arose earlier. The issues of using potash ore enrichment waste as an inert filler were disclosed in [1, 22]. Cement [23] and slags [24] were used as a binder when creating a stowing rock mass based on waste from the enrichment of potash ores. To improve the components properties of the filling mixture and increase the normative characteristics of the rock mass, the use of activation processing of components is proposed [25, 26] with preliminary reprocessing [27].
Modeling is increasingly used to predict various situations [28]. Modeling or comparative analysis of various processes in all fields of science and production is becoming widespread [29].
For research, a chamber development system with the chain pillars leaving with a three-stage excavation and subsequent stowing was selected as an object of modeling (Fig.2), in which the most complete extraction of minerals with the least losses is achieved at average ore body capacities.
The subject of the study is the justification of the parameters of the technology of mining salt deposits and the determination of the strength characteristics of the stowing rock mass, as well as the establishment of the influence of stoping operations on the dynamics of deformation changes in the underworked salt rock mass. Geotechnology with a stowing will minimize the development of cracks in the underworked salt rock mass and ensure the safety of the water-proof thickness, as a result of which it will protect the mine from emergency flooding. Special focus is given to the completeness of the excavation and the use of enrichment waste in the stowing, which will lead to an improvement in the qualitative and quantitative indicators of extraction and a reduction of man-made waste on the surface. The initial stage for modeling processes is a virgin rock mass [30].
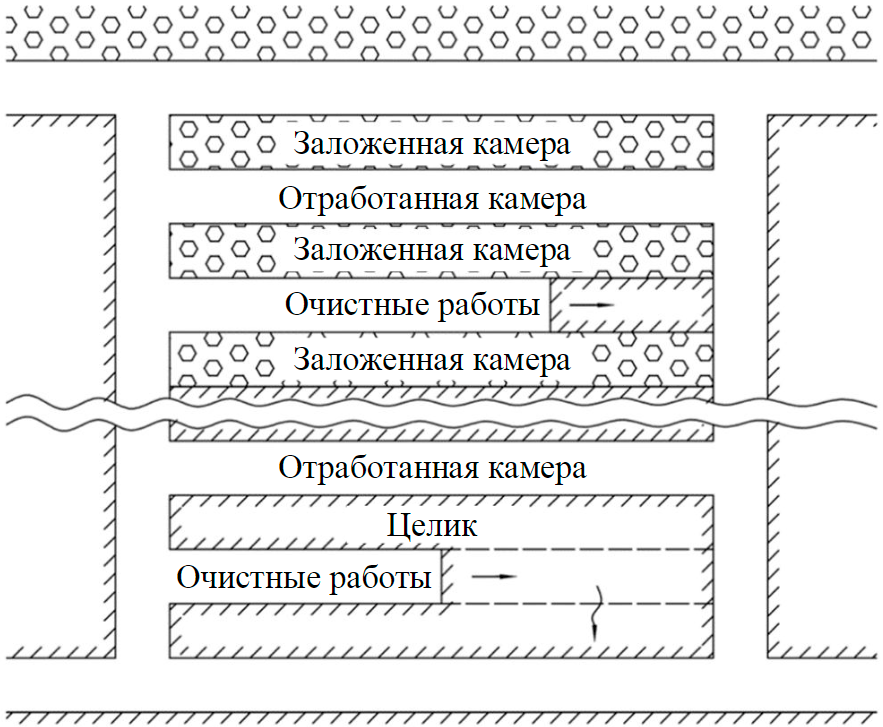
Fig.2. Chamber development system with the chain pillars leaving with subsequent stowing for horizontal deposits of small and medium capacity
Deposits are worked out by a chamber development system with the chain pillars leaving [31]. The stoping unit is worked out with chambers 4 m wide and 200 m long, leaving 8 m long inter-chamber pillars. The worked-out chambers in the proposed model are filled with a hardening stowing.
The inter-chamber pillars are worked out in two stages: first, a part of the pillar, equal to half of its width, is worked out between the worked-out chambers, followed by stowing with hardening mixtures, then the remaining part. After that, the developed space can remain open or be stowed (Table 1).
Table 1
The order of working out the chambers
Number of chambers |
1 |
2 |
3 |
4 |
5 |
6 |
7 |
8 |
9 |
Stage of development |
I |
II |
III |
I |
II |
III |
I |
II |
III |
Width of the chamber, m |
4 |
4 |
4 |
4 |
4 |
4 |
4 |
4 |
4 |
Table 2
Mining plan
Stages/days |
1 |
2 |
3 |
4 |
5 |
6 |
7 |
8 |
9 |
10 |
11 |
12 |
13 |
14 |
69 |
70 |
71 |
72 |
73 |
74 |
75 |
76 |
77 |
78 |
79 |
80 |
I |
1 |
2 |
3 |
4 |
5 |
6 |
7 |
8 |
9 |
10 |
1 |
2 |
3 |
4 |
59 |
60 |
|
|
|
|
|
|
|
|
|
|
II |
|
|
|
|
|
|
|
|
|
|
|
|
|
|
|
|
1 |
2 |
3 |
4 |
5 |
6 |
7 |
8 |
9 |
10 |
III |
|
|
|
|
|
|
|
|
|
|
|
|
|
|
|
|
|
|
|
|
|
|
|
|
|
|
I |
|
1 |
2 |
3 |
4 |
5 |
6 |
7 |
8 |
9 |
10 |
1 |
2 |
3 |
58 |
59 |
60 |
|
|
|
|
|
|
|
|
|
II |
|
|
|
|
|
|
|
|
|
|
|
|
|
|
|
|
|
1 |
2 |
3 |
4 |
5 |
6 |
7 |
8 |
9 |
III |
|
|
|
|
|
|
|
|
|
|
|
|
|
|
|
|
|
|
|
|
|
|
|
|
|
|
I |
|
|
1 |
2 |
3 |
4 |
5 |
6 |
7 |
8 |
9 |
10 |
1 |
2 |
57 |
58 |
59 |
60 |
|
|
|
|
|
|
|
|
II |
|
|
|
|
|
|
|
|
|
|
|
|
|
|
|
|
|
|
1 |
2 |
3 |
4 |
5 |
6 |
7 |
8 |
III |
|
|
|
|
|
|
|
|
|
|
|
|
|
|
|
|
|
|
|
|
|
|
|
|
|
|
Stages/days |
81 |
82 |
83 |
84 |
139 |
140 |
141 |
142 |
143 |
144 |
145 |
146 |
147 |
148 |
149 |
150 |
151 |
152 |
153 |
154 |
209 |
210 |
211 |
212 |
I |
|
|
|
|
|
|
|
|
|
|
|
|
|
|
|
|
|
|
|
|
|
|
|
|
II |
1 |
2 |
3 |
4 |
59 |
60 |
|
|
|
|
|
|
|
|
|
|
|
|
|
|
|
|
|
|
III |
|
|
|
|
|
|
1 |
2 |
3 |
4 |
5 |
6 |
7 |
8 |
9 |
10 |
1 |
2 |
3 |
4 |
59 |
60 |
|
|
I |
|
|
|
|
|
|
|
|
|
|
|
|
|
|
|
|
|
|
|
|
|
|
|
|
II |
10 |
1 |
2 |
3 |
58 |
59 |
60 |
|
|
|
|
|
|
|
|
|
|
|
|
|
|
|
|
|
III |
|
|
|
|
|
|
|
1 |
2 |
3 |
4 |
5 |
6 |
7 |
8 |
9 |
10 |
1 |
2 |
3 |
58 |
59 |
60 |
|
I |
|
|
|
|
|
|
|
|
|
|
|
|
|
|
|
|
|
|
|
|
|
|
|
|
II |
9 |
10 |
1 |
2 |
57 |
58 |
59 |
60 |
|
|
|
|
|
|
|
|
|
|
|
|
|
|
|
|
III |
|
|
|
|
|
|
|
|
1 |
2 |
3 |
4 |
5 |
6 |
7 |
8 |
9 |
10 |
1 |
2 |
57 |
58 |
59 |
60 |
Note 1-10 – working out and filling of chambers (10 days); 1-60 – stowing strength set (60 days)
In addition to safe mining operations, the selected width of the chamber and the pillars should ensure the effective use of mining equipment. When using a stowing for a chamber development system with the chain pillars leaving it is possible to simultaneously work out several chambers along one conveyor line, which increases productivity, and the stowing of the developed space reduces losses. Also, with the help of this technology, it is possible to adjust the hardening time of the stowing rock mass to the calculated strength (the maximum set is reached after 90 days). In the model, the strength set period was 60 days. Taking such a time value, it means that the time gap during the development of neighboring chambers was 70 days, taking into account mining operations and the filling of workings; the depth of development is 1200 m.
As follows from Table 2, the outcrop time is 10 days, during which the stoping chambers will be worked out (5 days) and prepared, and stowing works will be carried out (5 days).
Before starting the construction of the model, analytical calculations of the elastic properties (Young's modulus, Poisson's ratio and strength characteristics of uniaxial compression) of the stowing were performed with the derivation of the dependence of time, loads and deformations to determine the interaction of the overlying roof rocks on the stowing rock mass (changes in the strength characteristics of the stowing over time were taken into account).
Taking into account the parameters of the strength set of the stowing, along with the dependence on pressure, there is an additional dependence of solidification and strength on time.
The composition of the filling mixture is determined by the results of studies on uniaxial compression and endometrium and depends on the normative strength of the homologated rock mass and the rate of strength gain during solidification. When choosing the composition, it is necessary to take into account the additional heating of the air in the chambers during hydration and the volume of drainage. In this model, the filling coefficient of the chambers with the stowing material was assumed to be 100 %.
Methodology
An assessment of the stress-strain state of the mining system during the development of steep-falling salt deposits was carried out. The studies results obtained by quantitative assessment of the rock mass state (the Barton method) were used [32].
The analysis of the potential possibilities of crack development was considered in [31] in the conditions of a flat deformation state.
When using the Roschlau and Heintze scheme [33], the Finite Element Method (FEM) is widely used to solve problems in the mechanics of solids capable of changing the surface area, shape, volume, and internal structure under the action of external forces [34]. The method of numerical modeling and finite elements is widely used in mining and geomechanics. Based on it, ITASCA Consulting Group has created the FLAC3D 5.01 program, which implements an idea of an existing system that differs from the real model, but is much closer to the algorithmic description. In order to reduce the estimated time and eliminate the influence of depth on the simulation results, a pseudo-volume model is used, since in modeling the depth axis is calculated in small values (up to 1 m). This model takes into account all the parameters of the studied rock mass, which characterize its properties and the dynamics of changes over time. With the help of FEM in the FLAC3D 5.01 program, stresses and deformations of various solids that arise as a result of the influence of internal and external forces are modeled, their calculated values are given and complex structural formations are investigated.
The requirements for the strength characteristics of the stowing rock mass depend on the characteristics of the overlying rocks of the worked-out rock mass and are determined by the maximum rock pressure affecting the stowed chambers [35]. Rock pressure calculations are performed using software based on the finite difference method (FLAC3D 5.01). The program was used to build three-dimensional models of various nonlinear properties of materials, as it is based on certain modeling parameters (fast Lagrange analysis of continuums in three dimensions). FLAC3D has a library or database with equations for describing various properties of materials and their changes. At the same time, it is possible to build models taking into account various factors: solidification time; plastic (material destruction criteria) and/or creeping properties of the rock mass; time of strength gain of the stowing rock mass; elastic properties of the stowing rock mass; elastic or plastic properties of ores and host rocks.

Fig.3. In-situ measurements
According to the modeling methodology developed by ITASCA Consulting Group, the geometric dimensions of the model are 5-8 sizes of the studied object [33]. The simulation section in consideration consists of 9 chambers 4 m wide and 4 m high, where the depth (distance along the y axis) is 1 m, since this model is presented as 2.5D.
Accepted geometric parameters of the model (Fig.3): width – 180 m (x axis), depth – 1 m (y axis). The thickness of the geological layers are: the overlying roof rocks (red) – 40 m; the salt layer being worked out (green) – 4 m; the underlying soil rocks (blue) – 10 m.
The height of the underlying rocks of 10 m was adopted for the research, since they have a significant impact on the dynamics of the redistribution of rock pressure loads in the soil of the mine workings.
Table 3
Physical and mechanical properties of materials in the model (creeping properties)
Description |
Thickness, m |
Density, kg/m3 |
Poisson’s ratio |
E-module, |
Structural |
Stress range |
Rock salt of the roof |
40 |
2150 |
0.24 |
21300 |
1.65E – 15 |
5.3 |
Potash layer |
4 |
2000 |
0.20 |
19200 |
9.27E – 15 |
5.8 |
Rock salt in the soil |
10 |
2150 |
0.25 |
18900 |
9.28E – 14 |
3.7 |
In the conducted research, an ideal elasto-plastic model was used, which is a generalization of an elastic and rigid-plastic medium with internal friction [3].
Table 4
Physical and mechanical properties of the stowing rock mass (elastic properties)
Description |
Density, kg/m3 |
Poisson’s ratio |
Pressure, |
E-module, |
Time, |
E-module, |
Stowing |
2000 |
0.23 |
0.0 |
25 |
0 |
75 |
0.6 |
50 |
30 |
150 |
|||
1.2 |
75 |
90 |
300 |
|||
2.5 |
100 |
3600 |
300 |
|||
5.0 |
125 |
– |
– |
|||
10.0 |
150 |
– |
– |
|||
20.0 |
250 |
– |
– |
|||
40.0 |
600 |
– |
– |
|||
80.0 |
1200 |
– |
– |
In the modeling, power distributions in empirical data (Power Law) were used for various properties of rocks (creeping) and the stowing rock mass (elastic). The simulation load applied in the upper part of the model is 30 MPa, which corresponds to a development depth of 1200 m. Measurement points (in-situ measurements) were installed in the center of the chamber (point 1) at a distance of 12 m from the lower boundary of the model, in the roof of the mine working (point 2) 14 m and at a distance of 30 (point 3) and 50 m (point 4). Measurements of maximum stresses were carried out.
The basis of the study was the determination of the deformation of the overlying roof rocks and the maximum stresses depending on time.
When modeling the salt material, linear elastic deformation and stationary creeping were assumed. To simulate creeping, the Norton function was used in the form of a power dependence, which makes it possible to reproduce the behavior of the dominant creeping. But this function does not take into account its symptoms caused by transients or damage. The geothermal gradient is taken into account by structural parameters in combination with the Arrhenius equation, based on the statement about the uniform temperature of rocks (the material and its characteristics are given in Table 3).
The elastic material model was used when modeling a stowing in FLAC3D. The elasticity modulus for different values of pressure and time is given in Tables 3 and 4.
Modeling taking into account linear elastic deformation, stationary creeping for ores and host rocks and elastic deformation of the stowing allows to adapt the behavior of the solid stowing material in the modeling in accordance with the test results. The effective elasticity modulus is interpolated from Tables 3 and 4. The coefficients given in Table 4 are taken from the results of M.Votyakov's research [22].
Discussion
On the graph (Fig.4) it can be seen that the maximum deformation of the roof was in chamber 3 and was 0.506 m, and the minimum – in chamber 4 (0.450 m). In chambers 1 and 9, the deformation of the roof was the smallest, they were excluded from analytical studies due to the fact that the purity of the experiment was violated in them – the chambers border on a virgin rock mass, which significantly affects the deformation.
The simulation results showed that 95 % of the maximum convergence of the roof occurs up to 213 days, after which the roof “sits down” on the stowing rock mass, which takes on the pressure of the overlying rocks.
Figure 5 shows the changes in the maximum stresses for different chambers at the second measurement point (in the roof of the mine workings). The graph shows that a sharp change in the stress state in the roof occurs up to 213 days. It means that at this time there was a final redistribution of rock pressure, which is confirmed by the previous study of deformation (see Fig.3). Figure 6 shows the maximum stresses as a function of time. The end of the stowing works for each chamber is taken as a reference point and the time interval of 7-60 days is considered, when the main strength set of the stowing material occurs.
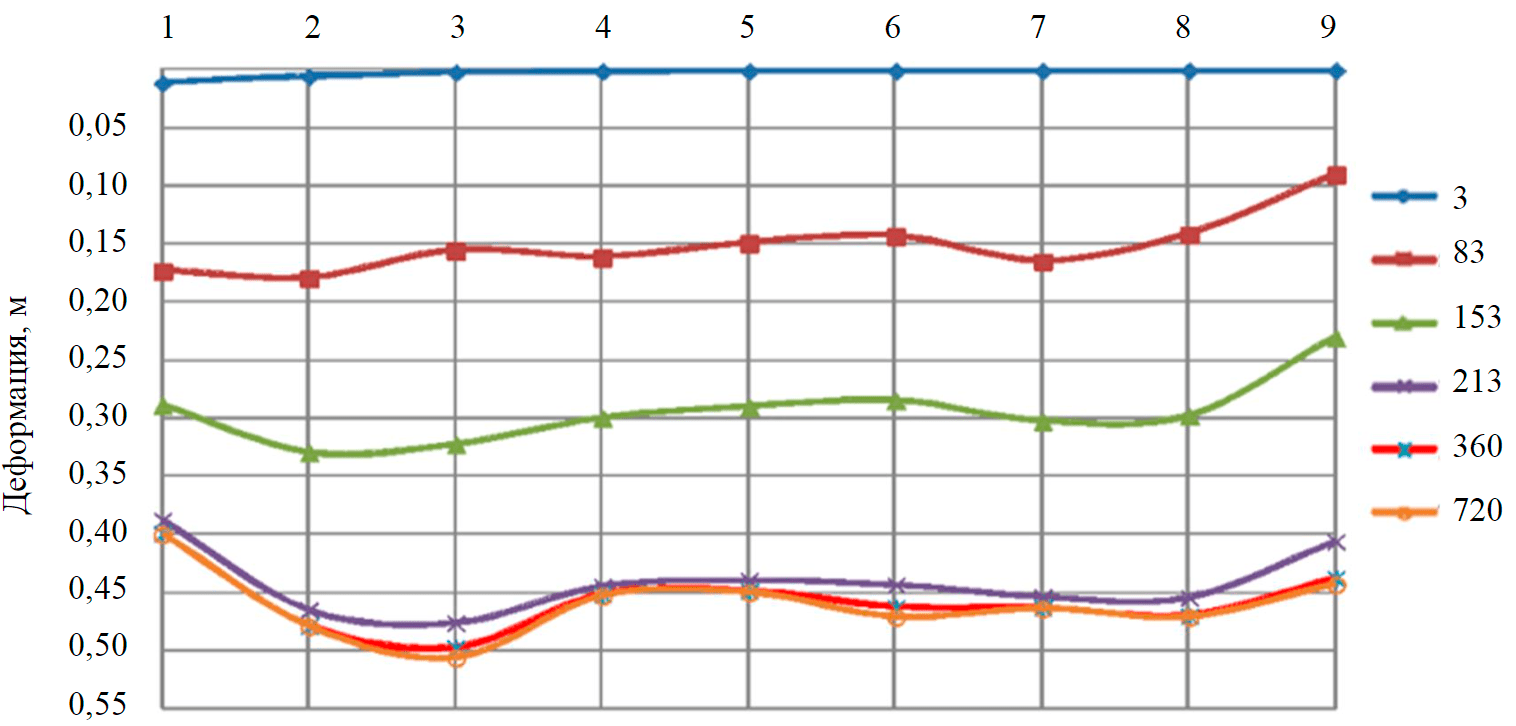
Fig.4. Deformations in the second measurement point (in the roof at 14 m mark) depending on the time
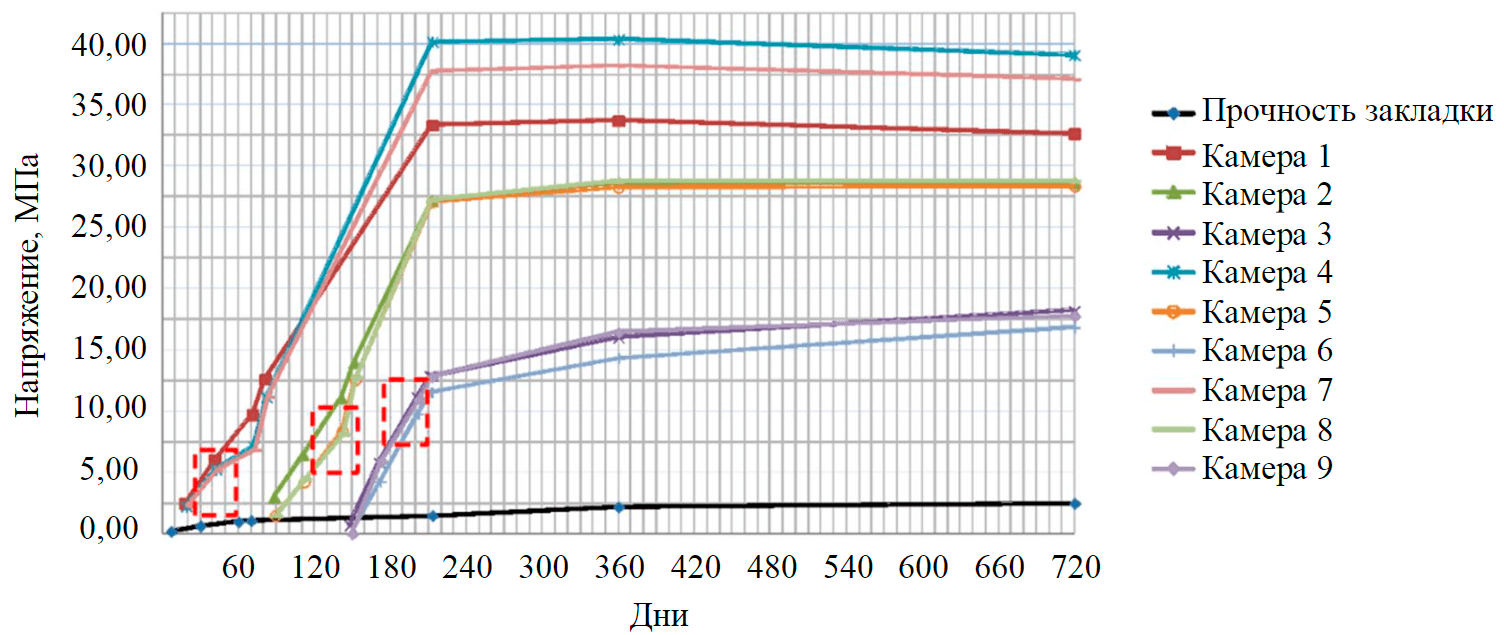
Fig.5. Change of maximum stresses in the second measurement point in time for different chambers
As follows from the graph (Fig.5), the highest expected stress (chamber 2) among the maximum is 11.1 MPa. These data allow to create a stowing rock mass with pre-known and necessary characteristics, taking into account the time of strength gain of the stowing rock mass and changes (redistribution) of rock pressure.
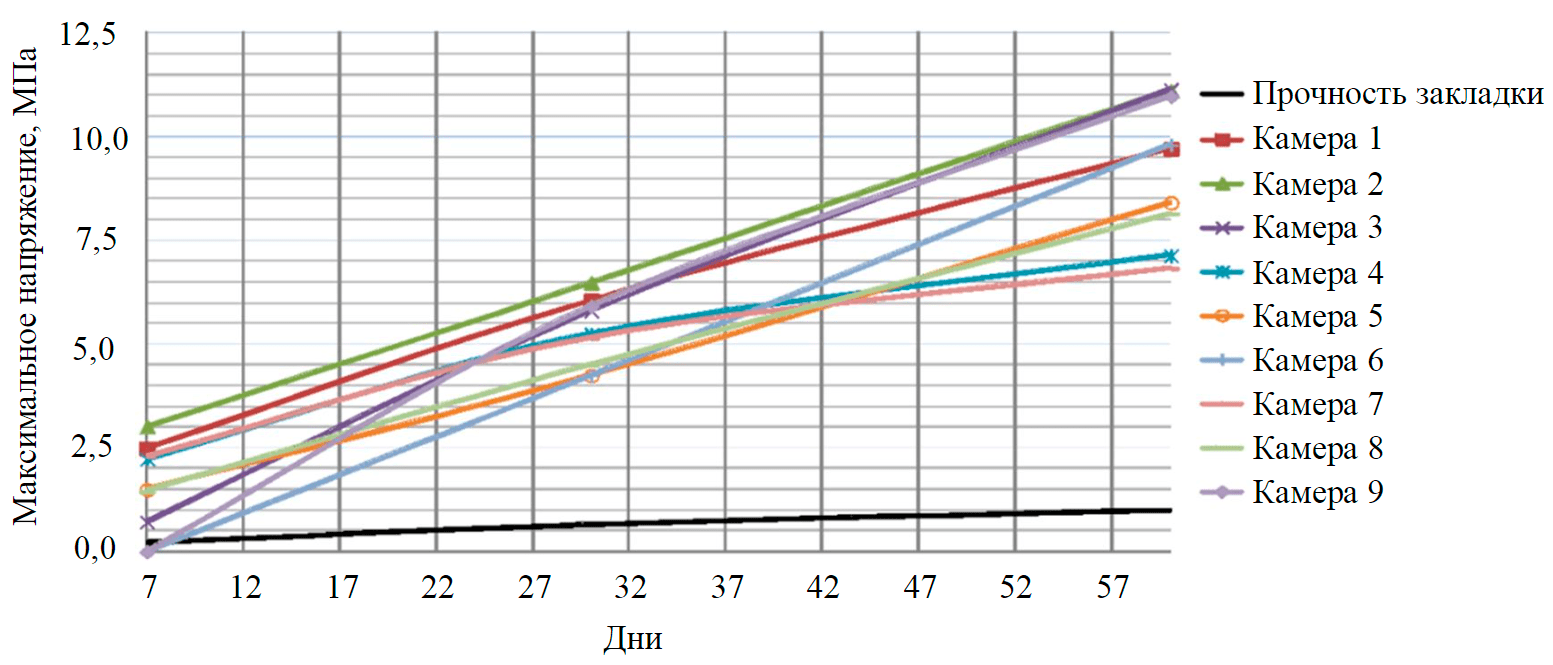
Fig.6. Maximum stresses depending on the time after stowing the developed space
After 213 days, the stowing has practically no noticeable deformations, the kinetics of rock pressure slows down. In this model, using in-situ measurements at various points, the maximum stresses and deformations are determined, which will allow predicting the violation of the rock mass integrity (the formation of man-made fracturing) and the water-proof thickness of aquifers; the impact of mining operations on the earth surface. Also, the method allows to determine the optimal value of the strength characteristics of the stowing rock mass, which will help to create it with pre-known, predetermined characteristics. This makes it possible to choose the optimal composition of the filling mixture during the development of the deposit with the artificial maintenance of the stoping space.
Conclusion
Civil construction and mining industries have the potential of waste-free production, which determines the use of mid-products (man-made industrial waste) in a closed cycle of main and secondary production. For the balanced and harmonious exploitation of natural resources, it is necessary to carry out technological and technical changes in industrial and mining productions, adjust the direction of investments, and change the vector of development of scientific and technical research. It should be taken into account that the use of geotechnology with a stowing during the development of salt deposits, along with the potential of waste-free production, allows improving the qualitative and quantitative indicators of extraction and increasing the safety of mining operations.
Modeling in FLAC3D will help to predict changes in the stress-strain state of the underworked salt rock mass, assess the possibility of cracks and ensure the safety of the water-proof thickness, protect the mine from flooding, which will increase the safety of mining operations. The use of numerical modeling allows to select the parameters of the mining technology.
References
- Savich I.N., Votyakov M.V. Technology of stoping excavation of the Verkhnekamskoe potash deposit. Mining information and analytical bulletin. 2006. N 9, p. 268-271 (in Russian).
- Kashnikov Y.A., Ermashov A.O., Efimov A.A. Geological and Geomechanical Model of the Verkhnekamsk Potash Deposit Site. Journal of Mining Institute. 2019. Vol. 237, p. 259-267. DOI: 10.31897/pmi.2019.3.259
- Baryakh A.A., Telegina E.A. Analysis of the conditions of water-proof layer destruction in various variants of the chamber development system. Mining information and analytical bulletin. 2013. N 1, p. 34-40 (in Russian).
- Hongyu Long, Hongyong Liu, Xingwei Li, Longjun Chen. An Evolutionary Game Theory Study for Construction and Demolition Waste Recycling Considering Green Development Performance under the Chinese Government’s Reward-Penalty Mechanism. Internstional Journal of Environmantal Research and Public Health. 2020. Vol. 17. Iss. 17. N 6303. DOI: 10.3390/ijerph17176303
- Grayson R.L. Addressing the Dual Challenges of Meeting Demand for Minerals and Sustainable Development. Minerals. 2011. Vol. 1, p. 1-2. DOI: 10.3390/min1010001
- Ponomarenko T., Nevskaya M., Jonek-Kowalska I. Mineral Resource Depletion Assessment: Alternatives. Problems. Results. Sustainability. 2021. Vol. 13. Iss. 2. N 862. DOI: 10.3390/su13020862
- Kozubal J.Technical universities for civil engineering career in Republic of Poland. Procedia Engineering. 2015. Vol. 117, p. 521-529. DOI: 10.1016/j.proeng.2015.08.204
- Adigamov A.E., Yudenkov A.V. Stress-Strain Behavior Model of Disturbed Rock Mass with Regard to Anisotropy and Discontinuities. Mining informational and analytical bulletin. 2021. N 8, p. 93-103 (in Russian). DOI: 10.25018/0236_1493_2021_8_0_931
- Gabov V.V., Zadkov D.A., Kuzkin A.Y., Elikhin A.S. Fractured-laminar structure of formations and methods of coal. Key Engineering Materials. 2020. Vol. 836, p. 90-96. DOI: 10.4028/www.scientific.net/KEM.836.90
- Yu L., Ignatov Y., Ivannikov A. et al. Common features in the manifestation of natural and induced geodynamic events in the eastern regions of Russia and China. III National scientific conference with foreign participants “Geodynamical Processes and Natural Hazards”, 27-31 May 2019, Yuzhno-Sakhalinsk, Russian Federation. IOP Conference Series: Earth and Environmental Science, 2019. Vol. 324. N 012004. DOI: 10.1088/1755-1315/324/1/012004
- Klyuev R.V., Golik V. I., Bosikov I.I. Comprehensive Assessment of Hydrogeological Conditions for Formation of Mineral Water Resources of the Nizhne-Karmadon Deposit. Bulletin of the Tomsk Polytechnic University. Geo Assets Engineering. 2021. Vol. 332, N 8, p. 206-218. DOI: 10.18799/24131830/2021/8/3319
- Sanz-Pérez E., Menéndez-Pidal I., Lomoschitz A., Galindo-Aires R. The pico de navas slump (Burgos, Spain): A large rocky landslide caused by underlying clayey sand fluidification. Journal of Iberian Geology. 2016. Vol. 42. Iss. 1, p. 55-68. DOI: 10.5209/rev_JIGE.2016.v42.n1.49727
- Sanz E., Rosas P., Menéndez-Pidal I. Drainage and siphoning of a karstic spring: A case study. Journal of Cave and Karst Studies. 2016. Vol. 78. Iss. 3, p. 183-197. DOI: 10.4311/2015ES0134
- Wyjadłowski M. Methodology of dynamic monitoring of structures in the vicinity of hydrotechnical works – selected case studies. Studia Geotechnica et Mechanica. 2017. Vol. 39. N 4, p. 121-129. DOI: 10.1515/sgem-2017-0042
- Oliveira F., Fernandes I. Influence of geotechnical works on neighboring structures. 17th International Multidisciplinary Scientific GeoConference (SGEM 2017), 27-29 November 2017, Vienna, Austria. SGEM, 2017. Iss. 33, p. 993-1001. DOI: 10.5593/sgem2017/12/S02.126
- Kawalec J., Kwiecień S., Pilipenko A., Rybak J. Application of crushed concrete in geotechnical engineering – selected issues. IOP Conference Series: Earth and Environmental Sciences. 2017. Vol. 95. Iss. 2. N 022057. DOI: 10.1088/1755-1315/95/2/022057
- Pizoń J., Gołaszewski J., Alwaeli M., Szwan P. Properties of Concrete with Recycled Concrete Aggregate Containing Metallurgical Sludge Waste. Materials. 2020. Vol. 13. Iss. 6. N 1448. DOI: 10.3390/ma13061448
- Zeqiri K. Investigation of the mining accidents at “Stan Terg” mine. Mining Science. 2020. Vol. 27, p. 39-46. DOI: 10.37190/msc202703
- Golik V.I., Razorenov Yu.I., Dmitrak Yu.V., Gabaraev O.Z. Safety Improvement of the Underground Ore Extraction Considering Mass Geodynamics. Occupational Safety in Industry. 2019. N 8, p. 36-42 (in Russian). DOI: 10.24000/0409-2961-2019-8-36-42
- Golik V.I., Tsidaev B.S., Kachurin N.M., Vernigor V.V. Prospects of Tailings Utilization from Sadonsky Mines. Sustainable Development of Mountain Territories. 2020. Vol. 12. N 1 (43), p. 128-136 (in Russian). DOI: 10.21177/1998-4502-2020-12-1-128-136
- Zglinicki K., Szamałek K., Wołkowicz S. Critical Minerals from Post-Processing Tailing. A Case Study from Bangka Island, Indonesia. Minerals. 2021. Vol. 11. Iss. 4. N 352. DOI: 10.3390/min11040352
- Khairutdinov M.M., Votyakov M.V. Selection of chemical additives for hardening stowings in potash mines. Mining information and analytical bulletin. 2007. N 6, p. 218-220 (in Russian).
- Khayrutdinov M.M., Kongar-Syuryun Ch.B., Tyulyaeva Yu.S., Khayrutdinov A.M. Cementless Backfill Mixtures Based on Water-Soluble Manmade Waste. Bulletin of the Tomsk Polytechnic University. Geo Assets Engineering. 2020. Vol. 331. N 11, p. 30-36 (in Russian). DOI: 10.18799/24131830/2020/11/2883
- Golik V.I., Kongar-Syuryun Ch.B., Tyulyaeva Yu.S., Khairutdinov A.M. The Use of Binders Based on Metallurgical Slags in the Composition of Based Mixtures. News of the Tula state university. Sciences of Earth. 2020. N 4, p. 389-400 (in Russian).
- Ermolovich O.V., Ermolovich E.A. Composite Backfilling Materials with the Addition of Mechanically Activated Beneficiation Tailings. News of the Tula state university. Sciences of Earth. 2016. N 3, p. 24-30 (in Russian).
- Noui A., Bouglada M.S., Belagraa L. et al. Study of the mechanical behavior and durability of mortars based on prepared san. Mining Science. 2020. Vol. 27, p. 47-59. DOI: 10.37190/msc202704
- Golik V.I. Metal Leaching Technologies – The Way of Reanimation of Mining Ossetia. Sustainable Development of Mountain Territories. 2020. Vol. 12. N 2 (44), p. 273-282 (in Russian). DOI: 10.21177/1998-4502-2020-12-2-273-282
- Kosarev O.V., Tcvetkov P.S., Makhovikov A.B. et al. Modeling of Industrial IoT complex for underground space scanning on the base of Arduino platform. Topical Issues of Rational Use of Natural Resources: Proceedings of the International Forum-Contest of Young Researchers. New York: CRC, 2018, p. 407-412.
- Perekutnev V.E., Zotov V.V. Comparative assessment of rubber steel cables for vertical mine hoists. Mining informational and analytical bulletin. 2020. N 7, p. 85-93 (in Russian). DOI: 10.25018/0236-1493-2020-7-0-85-93
- Gospodarikov A.P., Mansurova S.E., Montikov A.V. Geomechanical substantiation of the rock mass model for the analysis of the limit state of the pillars. Journal of Mining Institute. 2004. Vol. 156, p. 130-132 (in Russian).
- Zubkov V.V., Filinkov A.A. Geomechanical substantiation of projects of ore deposits mining. Journal of Mining Institute. 2010. Vol. 188, p. 31-35 (in Russian).
- Eremenko V.A. Stress State Modeling of Coaxial Three-Level Open Stoping in Map3D. Mining informational and analytical bulletin. 2018. N 11, p. 5-17 (in Russian). DOI: 10.25018/0236-1493-2018-11-0-5-17
- Litvinenko V. Advancement of geomechanics and geodynamics at the mineral ore mining and underground space development. ISRM European Rock Mechanics Symposium – EUROCK 2018, 22-26 May 2018, Saint Petersburg, Russia. OnePetro, 2018. N ISRM-EUROCK-2018-001.
- Batugin A., Myaskov A., Ignatov Y. et al. Re-Using of Data on Rockbursts for Up-to-Date Research of the Geodynamic Safety Problem. World Multidisciplinary Earth Sciences Symposium (WMESS 2018), 3-7 September 2018, Prague, Czech Republic. IOP Conference Series: Earth and Environmental Science, 2019. Vol. 221. N 012089. DOI: 10.1088/1755-1315/221/1/012089
- Voronov E.T., Tyupin V.N. Substantiation of strength of the filling mass by taking a blast effect into account for the room-and-pillar methods. Journal of Mining Institute. 2018. Vol. 229, p. 22-26. DOI: 10.25515/pmi.2018.1.22