Possibilities for creating Russian high-tech bottomhole assembly
- 1 — Ph.D. Deputy General Director Russian Energy Agency of the Russian Ministry of Energy ▪ Orcid ▪ Elibrary ▪ Scopus ▪ ResearcherID
- 2 — Project Director Russian Energy Agency of the Russian Ministry of Energy ▪ Orcid
- 3 — General Director “Axel Telemetria” Ltd. ▪ Orcid
Abstract
Development of high-tech well electronic measuring systems is aimed at creating modern equipment: telemetry, well geophysical measurement equipment, the architecture of which is divided into basic (with measurement channels for gamma logging and inductive resistance) and advanced (with radioactive, acoustic, magnetic resonance and thermobarometric measurement channels, including azimuthal methods of investigation). Over-the-bit measurement modules, rotary steerable systems are being developed and channels for transmitting data to the surface are being improved. Vice versa, specialized surface equipment with highly integrated software is being created. Different measurement modules are manufactured by different companies, which creates uncertainties in the possibility of interfacing the manufacturers' measurement modules into a single well measurement system. The article presents an analysis of the readiness of Russian oil service companies to produce well and surface equipment for drilling Russian directional oil and gas wells, meeting modern requirements for accuracy, lifetime and operating conditions. The possibility of creating a fully Russian well high-tech equipment and the required resources, risks and measures to mitigate them when creating a modern well measurement system are considered.
Introduction
Fulfillment of tasks on providing the level of oil production at the level of 550 million tons per year, defined by the Energy Strategy of the Russian Federation till 2035 [13], is possible through the introduction of new understudied fields, including the Arctic shelf and fields with hard-to-recover reserves (HRR). One of the directions for achieving high field development rates is the construction of horizontal and directional wells. They both increase the volume of produced hydrocarbons, exploit hard-to-reach areas of the fields and provide an opportunity to develop areas with low productivity cost-effectively due to extended horizontal sections, especially with a dense well grid. In less thick formations or in regions with complex geology, quick and accurate adjustment of the wellbore trajectory while drilling is required. This problem is solved by improving the drilling system and well tools. Such fields are developed with foreign well equipment due to the lack of a modern Russian well measuring system. At Russian fields with HRR and at the Arctic shelf the work of foreign enterprises is limited by the legislation of foreign states, that is why it will be necessary to create modern Russian oil and gas equipment for development of new understudied fields. This equipment must meet the modern requirements of reliability (operation under conditions of vibrations up to 30 g, impact loads up to 1000 g with pulse duration up to 5 ms, operating temperature over 150 °С) and durability with preservation of accuracy characteristics in the well (more than 5000 h, inter-service period more than 1500 h) and surface conditions of operation and storage of equipment [22, 23].
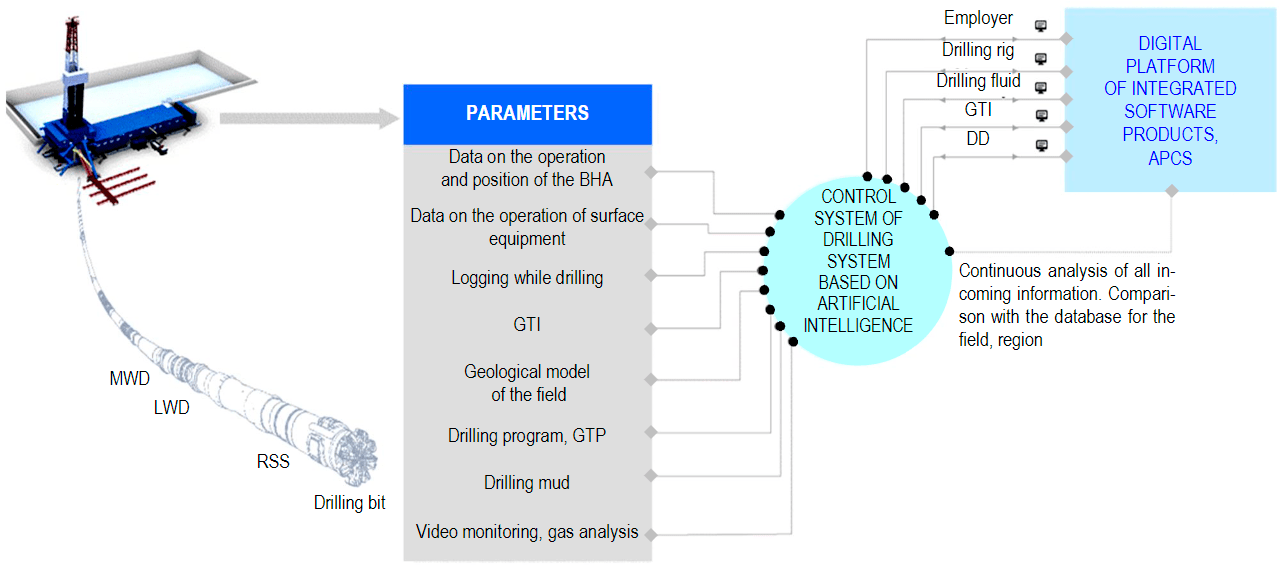
Fig.1. Integrated process control on a drilling rig 2.0 at the field
Improvement of drilling system is a new direction of well construction development, which is reduced to the creation of a digital drilling system (drilling rig 2.0) [3]. It allows drilling wells for various purposes and under all possible climatic conditions autonomously, with minimal human participation (Fig.1).
The defining basis for DR 2.0 is a decision-making system using artificial intelligence based on a digital integration platform, including an automated control system of the drilling rig with functions of management, control, storage and output of information on current processes and equipment status and with an integrated drilling parameter monitoring system.
Digital drilling system 2.0 consists of three global systems:
- surface equipment, including drilling rig, cementing unit, power equipment, controlled by a common automated control system;
- software products that provide, optimize and link the operation of all surface and well systems;
- well equipment and systems, including controlled assemblies for drilling and exploration of wells, drilling pipes, drilling fluids.
Global drilling systems 2.0 are needed to provide modern approaches to oil and gas wells drilling, which are closely linked to the information measurement channels of the drilling process. The information channels include:
- well measurements – telemetry, geophysical measurements while drilling, pipe and annular pressure measurements in the vicinity of the borehole bottom, cavernometry, etc.;
- surface drilling rig sensor system – drilling string weight, torque applied to the drilling string at the wellhead of the drilling well, gas analysis data, continuous automated control of the drilling fluid level at all key units of the drilling rig and the wellhead, pressure and flow rate of the drilling fluid at the wellhead, etc.;
- control system of drilling unit operation parameters in combination with automated process system and application of frequency-controlled drives.
According to geological data and data received from information channels of drilling system 2.0, artificial intelligence based on predictive analytics of drilling processes will ensure accident-free drilling with a reduction of non-productive time while drilling and cost reduction when drilling directional wells by 17 % or more, when drilling a well with horizontal ending by at least 19 %, which will eventually reduce field development costs.
Creation of the DR 2.0 pool and partial modernization of existing rigs will allow:
- reducing capital investment in the development of new fields by 15-20 %;
- lowering the average main drilling period for new fields from 8 to 4-5 years;
- reducing the number of wells by drilling multilateral and horizontal wells;
- lowering operating costs for drilling operations by up to 40 %.
Well construction using digital drilling system 2.0 technologies requires the use of high-tech well equipment, which can be divided into three groups – MWD (measurement while drilling) bottomhole telemetry systems, LWD (logging while drilling) logging systems and rotary steerable systems. Well high-tech systems allow:
- controlling the spatial deviation of the borehole in relation to geological objects in the process of drilling in order to improve the efficiency of the drilled well [19, 24];
- logging in horizontal and deviated wells [18];
- prompt obtaining the data on quantitative assessment of formation parameters and reservoir properties and making informed decisions on changing the well trajectory depending on the changing geological conditions of the well during drilling [21];
- obtaining logging data directly during and after drilling to build complex hydrodynamic models;
- eliminating additional intermediate wireline or pipe logging to assess and clarify geological conditions along the wellbore.
Thus, it is possible both to achieve the reduction of non-productive well construction time spent on geophysical measurements and to increase well flow rate [16].
This equipment is operated under the simultaneous impact load up to 1000 g with pulse duration up to 5 ms, vibration ± 30 g and temperature up to +150 °С. Such systems have high efficiency and reliability, as the quality, time and costs of well construction depend on it.
Today, the situation on the Russian oil services market is as follows: the share of foreign RSS used for drilling wells with complex wellbore profile and low thickness productive formations of 0.5 m or less, as well as in the fields with HRR and the Arctic shelf is 100 %. In the Russian Federation RSS have been successfully pilot-tested by NPP “BURINTEKH” Ltd. (the results are used to improve the designs). Two more enterprises (“RUS” Ltd., “GERS Technology” Ltd.) are at the stage of pilot-tests. The appearance of Russian serial samples of RSS will allow satisfying internal demand of oil and gas producing enterprises (not less than 22 units/year) and developing Russian market which will exceed 184.2 billion rubles by 2030 [10].
Production and serial release of MWD equipment is fully mastered in the Russian Federation, but the localization degree of components and electronic component base (ECB) does not exceed 50 %.
LWD equipment is also produced by Russian enterprises, with approximately the same degree of components and ECB localization, equal to 50 %. The import-dependent element of well equipment is the electronic component base (Table 1).
Table 1
Ratio of Russian and foreign components in MWD and LWD
Component |
Share of foreign components, % |
Radio electronic components |
|
PLIS (USA, Korea) |
100 |
Microcontrollers (USA) |
100 |
Passive elements (China) |
90 |
Integral circuits (USA, Japan) |
100 |
Energy-independent memory Flash (European Union, Korea) |
100 |
Lithium batteries (Canada) |
50 |
Sensors |
|
Accelerometers (European Union, Japan, USA) |
100 |
Pressure sensor (USA, Russia) |
50 |
Magnetometers (European Union, USA) |
100 |
MEMS sensors (USA, European Union) |
100 |
Photoelectronic multipliers (Japan) |
100 |
Rare-earth magnetic alloys (China) |
100 |
Crystals (USA, Russia) |
50 |
Neutron counters (USA, Russia) |
50 |
Discussion
In the process of directional drilling of oil and gas wells, telesystems with a hydraulic communication channel are currently used. Until recently, along with hydraulic communication channel, telesystems with electromagnetic and cable communication channels were widely used [9], in some cases – with acoustic method of information transfer. In Russia and abroad there is a gradual reduction of electromagnetic (applied only at low depths up to 2000 m and during conductor drilling, etc., in this segment there is a growth of operations), acoustic and cable communication channels. This is due to the fact that the hydraulic channel has the ability to transmit data from the well at a distance of more than 12 thousand meters compared with the electromagnetic channel (up to 4 thousand meters maximum), allows reducing non-productive time up to 500 % in comparison with the cable channel and does not depend on the geological features of the field, which can seriously reduce the effective depth of the electromagnetic channel (in some cases up to 600 m). Electromagnetic, acoustic and cable channels will keep their niche during drilling of top sections, mainly due to economic reasons, such as low cost of works, as well as during depression drilling , when the use of hydraulic channel is limited or impossible. That is why today the hydraulic communication channel is being improved as the most demanded in the oil services market for telemetry in the process of directional drilling of oil and gas wells.
In Russia, telemetry for the drilling process is produced in sufficient quantity and has an extensive range of systems, both by the method of information transfer and by technical characteristics. The weak point of all Russian MWD systems with hydraulic communication channel is data transmission speed, the guaranteed speed up to 3 bps is reached, in foreign companies – 70 bps [6] (by means of data compression). Research is being conducted in this direction, and today there is already a positive trend, according to the results of pilot well drilling the data transfer rate up to 4.8 bps was achieved [7].
A full range of LWD equipment in demand on the oilfield services market has been put into mass production, except for nuclear magnetic logging, because this method of well testing is not widespread in Russian fields.
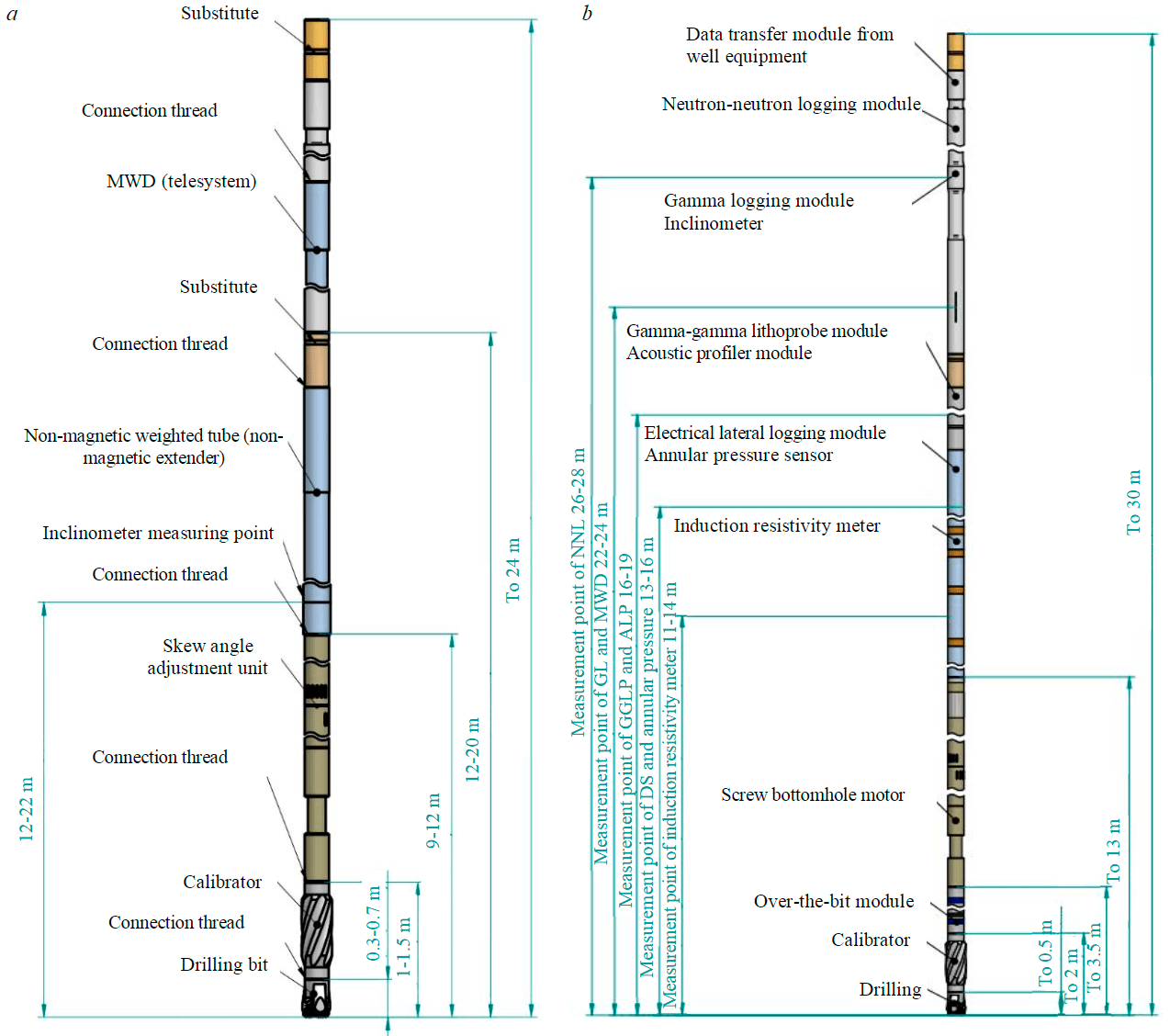
Fig.2. Bottomhole assembly architecture: а – basic; b – extended
In the world practice of using geophysical methods of well logging and their combinations used during drilling, there is a quite large number of types and subtypes, so it is reasonable to highlight only those that are successfully used at Russian fields [11]: gamma-ray logging; induction resistivity meter; lateral micro-logging; measurement of annular pressure; acoustic caliper; gamma-gamma logging; neutron-neutron logging; other, including azimuthal research methods.
There are several types of bottomhole assembly (BHA) (Fig.2) in terms of well measurement methods available:
- using MWD systems only;
- a basic system that utilizes the MWD and LWD systems using induction and gamma ray logging methods, as well as with an over-the-bit module;
- extended system using MWD and basic, which is supplemented by density, neutron logging, as well as acoustic lateral and other methods, including azimuthal methods [1]. It includes: gamma-ray logging; high-frequency resistivity meter (induction); azimuthal gamma-ray logging; gamma spectroscopy (azimuthal); photoelectric absorption index (azimuthal); gamma-gamma logging
(azimuthal); neutron-neutron logging (azimuthal); pulse neuron logging (azimuthal); azimuthal high-frequency resistivity meter (induction); electrical lateral micro-logging (azimuthal); acoustic logging; DD; - with the use of rotary steerable systems.
The demand of the Russian market for high-tech well equipment in the fuel and energy sector in 2019 was 513 units, while Russian companies produced 371 units, the rest of the equipment was purchased abroad. Table 2 shows the need of the Russian market for assemblies.
Table 2
Production of high-tech well equipment in the Russian Federation
Assembly |
Need |
Produced |
Margin |
MWD |
315 |
226 |
89 |
LWD basic |
260 |
63 |
197 |
LWD extended |
153 |
82 |
71 |
An important role in the well measuring system is played by a high-tech hardware-software surface system using highly specialized software. This class of equipment is deeply integrated with the MWD system and represents a single high-tech system for use in the drilling process.
In 2030, the basic architecture segment will account for 42 % of total LWD operations, while LWD 2 and LWD 3 will account for 42 % and 16 %, respectively (Fig.3) [10].
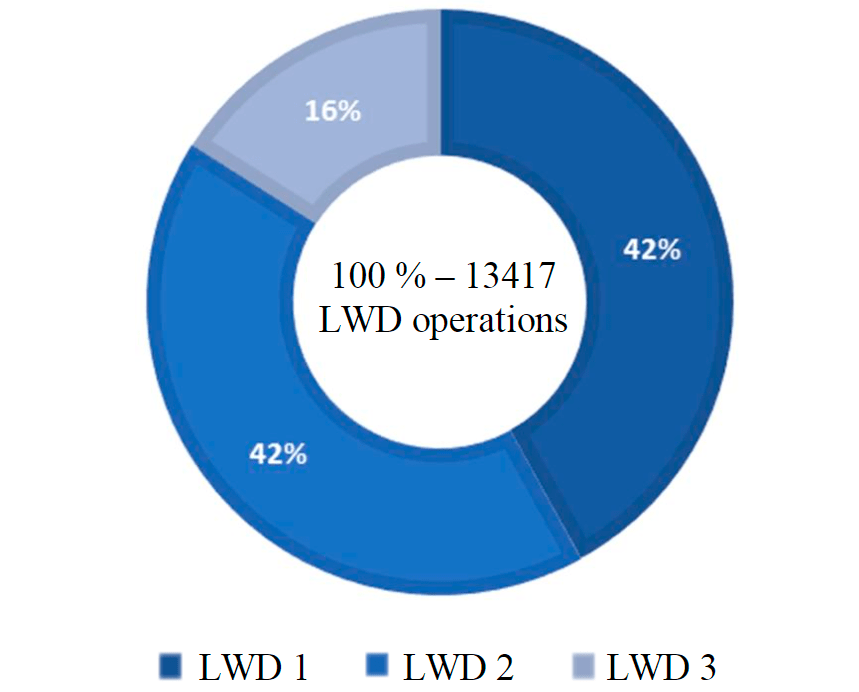
Fig.3. Shares of individual segments in the total number of LWD operations in Russia in 2030 (neutral scenario) LWD 1 – operations using inclinometry probes (angle and azimuth measurements), gamma and resistivity meters; LWD 2 – using inclinometer, gamma-, resistivity meter and NNL (neutron-neutron logging) probes; LWD 3 – using azimuthal logging methods (in addition to the basic system)
Suppose that, ideally, the average time per operation would be 5 to 10 days (not considering efficiency of the application, but assuming the use of methods that accelerate well drilling), we can conclude that the Russian market demand in 2030 will be from 190 to 360 systems per year (minimum). Considering the efficiency of the equipment application, which at the moment is about 30 % in most cases, and the fact that today the period of wells drilling is far from being ideal, these figures should be 3-4 times greater.
Thanks to the modular architecture of well equipment, the functionality and purpose of the BHA can change depending on the tasks to be performed. For example, to drill top unproductive sections of a well, there is no need to use LWD modules, and it is enough to use a basic BHA, as there is no relevance to analyze rock properties. For drilling productive horizons there is such a need, as it is necessary to conduct the wellbore in accordance with the requirements of the plan-program, and to ensure the maximum possible well flow rate by implementing geo-navigation to correct the spatial position of the wellbore based on the geology of the formations. In this case, different BHA architecture, including extended types, are used. The modularity of well systems allows the composition and content of well measurement modules to be changed directly in the field, without the use of production bases.
Despite the fact that the serial production of well and surface equipment was mastered in Russia, oilfield service companies produce a limited number of modules, which are presented either as separate well measurement modules or are designed to work with a particular type of system. That is why there are technical difficulties when configuring Russian BHA modules of different manufacturers. This is due to the use of different types of electrical connectors, interfaces, inter-module connectors, data transfer protocols, etc.
The task of interfacing the equipment of individual manufacturers is not easy, because the system data bus of well measuring system forms its architecture and functionality. The point is that electronic architecture of well modules is formed around the central processor unit (Fig.4), to which all measuring modules of the well system are connected through the data bus. Module of the central processing unit performs the function of system data bus administration and also sets the necessary functionality of system for solution of a specific task. In some cases it controls the pulsator (performs the function of data transmission module). Its functionality also includes interaction with surface equipment to configure or change user settings of the well system, including the format of data transmitted to the surface, synchronization of system time, etc.
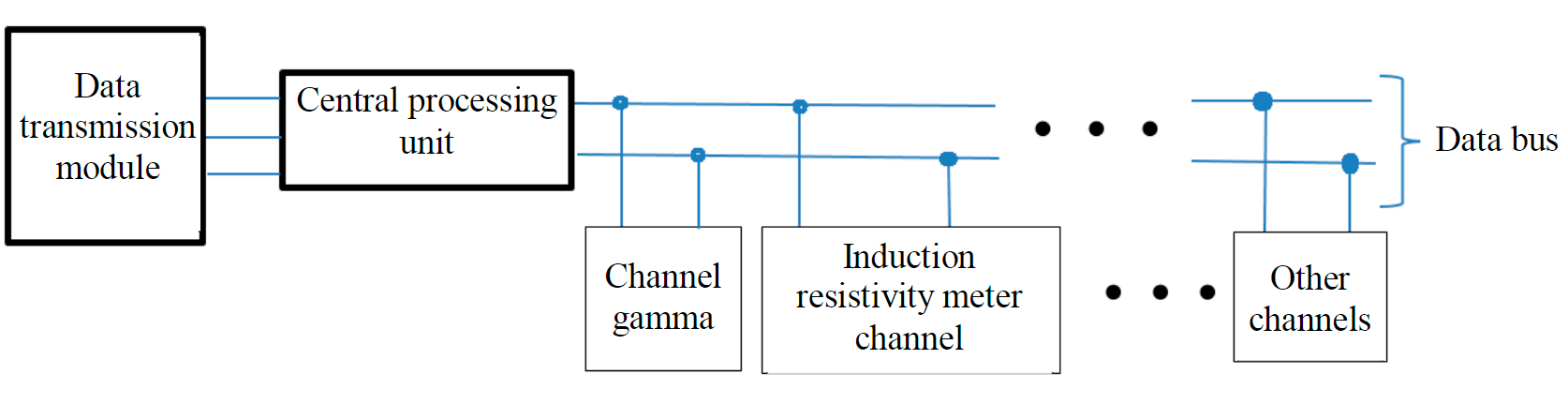
Fig.4. Classic data bus architecture of well equipment
The main inter-module communication protocols are RS-485, CAN, I2C, Q-Bus, etc. Data bus based on the RS-485 interface described in ANSI TIA / EIA-485-A: 1998 standard is a transceiver connected using a twisted pair – two wires twisted with each other. The RS-485 interface is based on the principle of differential transmission, that is, the transmission of the same signal over two conductors.
Electrical and timing characteristics of RS-485 interface:
- up to 32 transceivers in one network segment are supported;
- maximum length of one network segment 1200 m;
- only one transmitter can be active at a time;
- maximum number of nodes in the network – 256, including trunk amplifiers;
- bit rate/line length ratios: 62.5 kbps 1200 m (one twisted pair); 375 kbps 500 m (one twisted pair); 500 kbps; 1000 kbps; 2400 kbps 100 m (two twisted pairs); 10,000 kbps 10 m.
The bus for the CAN protocol at the physical level is the same twisted pair, as in the RS-485 protocol, through which signals of different levels are distributed. The CAN bus belongs to broadcast buses. This means that all nodes without exception will receive all messages. However, CAN hardware enables local filtering so that each module can only respond to messages of interest. In fact, there is no concept of a message address in the CAN protocol. Instead, the content of the message is defined by the identifier, which is in the message.
The CAN protocol is described in ISO 11898-1 and can be summarized as follows:
- messages are small, usually 8 bytes, protected by a checksum;
- messages have no explicit addresses, instead each message contains a numeric value that controls its order on the bus and can also serve as an identifier for the contents of the message;
- error handling scheme allows messages to be retransmitted if they were not received by the recipient;
- effective means are available for locating faults and removing faulty nodes from the bus;
- maximum data bit rate up to 10 Mbit/s.
The I2C protocol was developed by Philips and is intended for commercial use. The physical organization of the protocol requires two lines, data and time pulses. There is a master and a slave device on the bus, the time pulses are generated by the master, the slave only signals that data were received. Each device is recognized by a unique address and can operate as a transmitter or receiver. Each element is identified by its own unique address, which includes a device group and a specific device number. Any element that initiates a transmission is the master, any addressable element is a slave. In systems with more than one master, the same element can act as master or as slave.
The Q-Bus protocol is based on the M-Bus protocol, which is the industry standard for the wired network of various devices, sensors and measuring instruments. M-Bus is standardized throughout Europe according to DIN 1434 and EN 13757. As a result, QUNDIS Q M-Bus devices can be networked with each other.
Physically, Q-Bus is two conductors, so the data and address lines use the same lines. Technical features: input/output with memory mapping; addressing with byte accuracy; strict master-slave relationship on the bus; asynchronous communication protocol; half-duplex transmission mode; bit rate 300-9600 bps; transmission range in standard configuration up to 1000 m; range of slave devices to signal repeater up to 350 m; number of devices on the line up to 250.
Measuring well modules include microcontrollers, program and data memory, interface microcircuits, time microcircuits with corresponding time frequency generators (quartz resonators). All these components in high-temperature, impact and vibration-resistant design are not produced by Russian industry. Manufacturers of well equipment have the following requirements to external loads – operating temperature not less than 200 °С, sinusoidal mean square vibrations not less than 35 g, impact loads not less than 1500 g with the pulse duration not less than 5 ms [5].
It should be noted that there are systems (e.g. MWD) without modular architecture that have no system data bus, measuring modules are connected directly to the microcontroller ports and to the interfaces available in it, therefore, the microcontroller resources are used up when connecting two or three additional measuring modules to it. Such systems, as a rule, are subject to deep modernization for connection of additional modules, or are used independently without possibility to connect additional measuring modules. This architecture is obsolete, but still exists and is in use.
To control the trajectory of the well it is necessary to transmit measured data from the well to the surface, usually through an electromagnetic or hydraulic communication channel. Usually it has only one data communication line for data transfer, for which specialized formats of transmitted data are developed. Data transfer formats from the bottomhole are built according to the following architecture:
- waiting for pulse transmission to start; adjustable parameter (usually 30-35 s) is necessary to bring the mud pumps to nominal operation to avoid pump start-up noise overlapping with the useful signal;
- data transmission begins with the so-called synchroparcel (Fig.5, Flag), which has an exceptionally unique combination of pulses, necessary to ensure correlation of the received signal zeroing on the signal detector timer and start of counting of the surface software timer in order to synchronize with the surface well equipment. It has parameters strictly regulated by the manufacturer, conditioned by the regulations of the communication channel and strictly defined frequency (width) of pulse transmission. The first synchroparcel after the pumps start can be used to enable the surface digital signal processor to determine the nature of the transmitted data to correct the coefficients of the final pulse characteristics filter and its pre-configuration;
- then “FID” or “Tag” (signal) pre-programmed in the well equipment and stored in the surface software at the stage of configuration of the well equipment before the lowering into the well, the digit of which can be from 4 to 12 bits, this parameter contains information about the structure of transmitted data;
- then the information data is transmitted in the sequence and in the range of bits encoded in the “Tag”.
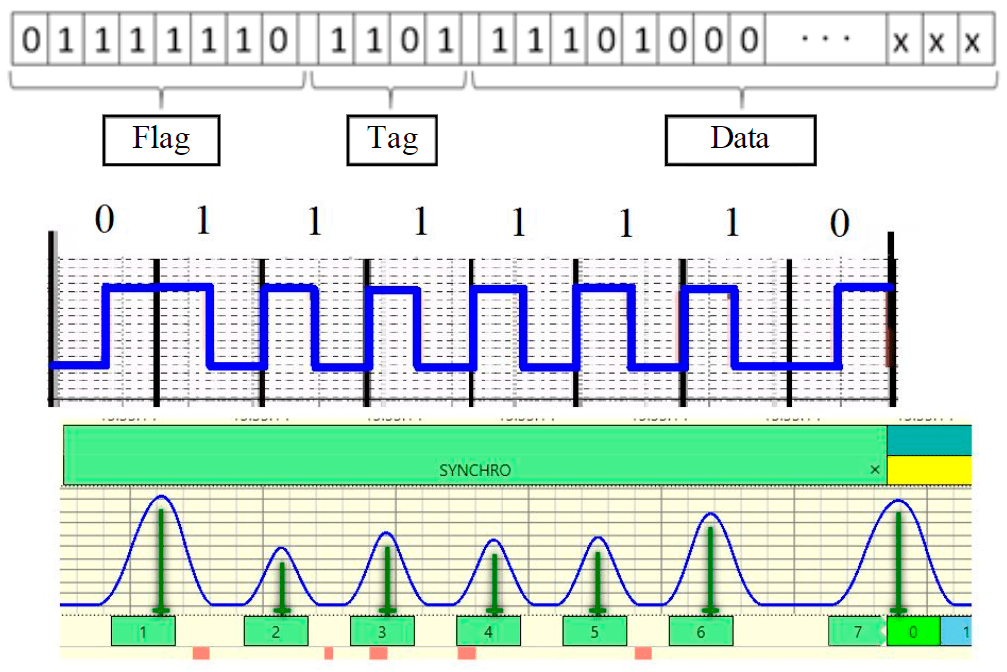
Fig.5. Classic frame format of the transmitted information on the surface by the example of the transmission protocol Manchester
Several different types of devices are used to generate pressure pulses in the drilling fluid, the signal generated by them is subdivided into three types: positive pulse; negative pulse; continuous wave. The data are subdivided into modulation types (Manchester, code-pulse, time-pulse, etc.), but the general principle of the frame format of the transmitted data remains the same.
Surface hardware system is designed to receive data from various sensors located on the rig (pressure, depth, weight, pump strokes, etc.); primary filtering of signals from sensors and transferring them to software; implementation of hardware decoding of signal transmitted by well system (currently considered an obsolete method, but used by a number of Russian and Western manufacturers).
The function of surface software includes: programming of well equipment prior to the lowering into the well – data transmission frequencies; data frame formats, which can be selected in the process of drilling in manual or automatic mode; reading and recording information into well modules; performing filtering and decoding of transmitted information using various mathematical algorithms with the possibility of using artificial intelligence; maintaining a drilling log; generating a database, reporting information in graphical and digital form; exchange information with a remote server via a local network and Internet.
Thus, in order to get the well assembly from different measuring modules of Russian manufacturers into a unified measuring system, i.e. modules of different manufacturers, having different data transfer protocols, it is necessary to develop and produce not only universal telescopic extensions to provide inter-module electrical connections of connectors into unified data bus, but also to bring data buses of modules into unified protocol by means of electronic protocol converters, which can be made in the form of individual electrical boards or inter-module inserts. In addition, it is necessary to develop a high-tech surface hardware-software system, which performs receipt of information from the well, its processing, formation of data base, formation of reporting documentation in graphical and digital form, deeply integrated with functionality of well module of central processing unit.
Threaded connections of individual manufacturers meet the requirements of the standards, but can still differ in types of threads in the same size of the measuring module, so it will be necessary to develop and produce threaded adapters. For example, in 108 mm assembly threaded connections according to GOST 28487-90 3-86, 3-88 and identical foreign threaded connections according to API 7 can be used. For connecting assemblies into one system an adapter with 3-86 threads on one end and 3-88 on the opposite one will be necessary. Russia has equipment for making threaded connections of any global standards for pipe threads. Russian standards for pipe threads are unified with foreign ones, although they are not their direct analogues. It should be taken into account that for cutting pipe threads, calibers for each type of threads (plain and threaded) and cutting plates required by the standard are necessary. Calibers and threading plates can be produced at toolmaking enterprises in Russia.
OJSC “Kogalymneftegeophysika” has a successful experience of integrating measurement modules from different Russian manufacturers into a single measurement well system with the possibility of obtaining different BHA architectures in terms of functionality. This result is achieved at the expense of application of well modules of the master controller, interface well modules, surface hardware and software of enterprise “Axel Telemetria” Ltd. [8].
“Technologicheskaya Compania Schlumberger” Ltd., based at “Geofit” factory, is also localizing the production of the M/LWD system by applying the maximum number of Russian developments in the field of well instrumentation. To date, an interface module for well measurement modules of various protocols was created. Prototype induction resistivity meter, a pulsator and a surface software package were developed and produced. Acoustic cavity meter, over-the-bit module, well pressure sensor and rotary steerable system are being developed. Company is already using the neutron density logging unit of SPE “Energia” Ltd. [11] in integration with foreign high-rate telemetry and LWD devices. A prototype of a well measuring system is planned to be built by the end of 2021.
The main technological market trends for the coming years will be:
- creation of a two-way high-rate communication link between surface and well equipment of 70 bps or more [12].
- development of logging while drilling is aimed at: increasing the accuracy of LWD ±10 to 2 % by creating a network of metrological polygons distributed over the federal districts of Russia, corresponding to the world level, and developing ( actualizing, updating existing) techniques of GWI data interpretation [2]; increasing the depth of rock probing over 12 m, improving automation and environmental safety [14]; development of methodological and software-interpretation metrology support, corresponding to its world level [17]; development and implementation of Russian LWD systems with azimuthal methods.
- introduction of stationary and pulsed neutron technologies for autonomous equipment options, as well as drilling logging equipment.
- substitution of cable (pipe) geophysical well investigation methods with LWD methods.
- automation of the drilling process by means of a software package that works in conjunction with M/LWD systems and drilling rig equipment (“Drilling rig 2.0”).
The development of fields with HRR uses modern and advanced LWD well equipment, where trends are noted in the following areas:
- nuclear magnetic resonance (NMR) method is an alternative method for determining porosity, permeability, water saturation, effective porosity and saturation patterns under different geological conditions [26, 27];
- broadband cross-dipole acoustic methods provide information from the elastic properties of rocks by probing the formation in radial direction with reference to the wellbore sector [28, 29];
- dielectric logging used in conjunction with a cross-dipole acoustic measurement module;
- pulsed neutron gamma spectrometric logging aims at a detailed study of the component composition and the permeability and porosity properties of rocks [20, 25].
Conclusion
More than 60 % of the wells at the Russian oil and gas fields, out of 8 822 production and exploration wells with a total penetration of 28.5 million meters, completed in 2019, were built by foreign and Russian oil service companies using foreign equipment. It should be noted that foreign companies are not allowed to work on the Russian Arctic shelf and fields with hard-to-recover reserves and is regulated by the laws of foreign countries, so it is important to create own technologies and equipment to develop domestic oil and gas fields, which will facilitate the entry of Russian oilfield services companies to foreign markets.
To date, Russian companies manufacturing downhole equipment produce a full range of borehole assemblies (excluding RSS and DD), but Russian equipment is inferior to foreign equipment in a number of parameters: lifetime; accuracy of inclinometer and GWI measurements; data interpretation methodologies; flexibility of configuration, functionality (including specialized software), etc.
Russian companies usually produce no more than two or three BHA modules at the plant, so in order to obtain an extended BHA, a number of technical challenges need to be met in terms of interfacing modules from different manufacturers into a single measurement system:
- develop a module to interface the various data transmission protocols into a single data bus protocol, through which the data can be received by the master controller (central processing unit) of the wells measuring system;
- develop a universal telescopic connectors for the physical interconnection of data buses;
- develop a universal master controller module capable of operating the entire range of well equipment and data transfer modules;
- develop a universal surface hardware and software system;
- to upgrade the existing metrological support of well and GWI equipment in order to improve the accuracy of data interpretation to ±2 % (currently ±10 %) and to develop, update and upgrade modern methods of GWI data interpretation [2];
- create a testing ground for field tests to improve the reliability of well equipment created in Russia and to develop new, modern technologies of oil and gas well drilling [15].
There are risks in creating a Russian well system. To date, the development of Russian fields and fields on the Arctic shelf is restricted not only to foreign companies, but also to the use of foreign components, utilities and software. Risks of restricting the use of foreign components are most evident in the high-temperature electronic component base. The most critical are high-temperature microcontrollers, digital signal processors and memory. For software the most critical are CAD, CAE and COE programs, where it is necessary to maintain the design and develop electric circuits and mechanism parts, and to calculate the dynamics of liquid and gas flows, analyze the effects of vibration and fatigue stresses, etc. Essential limitations are imposed on licensed products Ansys, MATLAB, OrCAD and others that enable modeling fundamental processes, nature of their course and probability of certain events. It is important to note that this category of software products cannot be used even in the initial stages of design.
To minimize risks when implementing Russian projects with Russian equipment and oilfield services it is necessary to develop and establish serial production of components for well equipment, such as sensors (accelerometers, photoelectronic multipliers, neutron detectors, etc.), electronic component base, production of corrosion-resistant and precision steels and alloys, as well as to create test sites and modern metrological support of GWI equipment [9]. The analysis of production capacities of Russian enterprises by Centre of Competence for Technological Development of the fuel and energy industry showed that the reserves for serial production of sensors, steels and alloys, and electronic component base are mainly available at enterprises of military industry [1, 4]. It is necessary to increase the degree of localization for Russian equipment to the level of at least 80 %, and for some positions to 100 %.
Diversification of existing production capacities, including those of the military industry (for the production of heat- and vibration-resistant ECB and detectors), will help to eliminate the technological gap in the area of drilling the precision oil and gas wells, acquire competences in the production of world-class civilian products and develop new markets.
References
- Zhdaneev O.V., Durdyeva A.A., Bravkov P.V. Technical policy issues of the fuel and energy sectors of the Russian Federation. Moscow: Nauka, 2020, p. 304 (in Russian).
- Zhdaneev O.V., Zaitsev A.V., Lobankov V.M. Metrological support for the logging while drilling and wireline equipment. Journal of Mining Institute. 2020. Vol. 246, p. 667-677. DOI: 10.31897/PMI.2020.6.9
- Zhdaneev O.V., Frolov K.N. Drilling Technology Priorities in Russia. Oil Industry. 2020. N 5, p. 42-48. DOI: 10.24887/0028-2448-2020-5-42-48
- Zhdaneev O., Сhuboksarov V. Technical Policy of the Oil and Gas Industry in Russia: Tasks and Priorities. Energy Policy. 2020. N 5 (147), p. 76-91. DOI: 10.46920/2409-5516_2020_5147_76 (in Russian).
- Zhdaneev O.V., Zaitsev A.V., Lobankov V.M., Frolov K.N. The Concept of Testing Downhole Equipment. Subsoil use ХХI century. 2021. N 1-2 (90), p. 4-15 (in Russian).
- Nikiforov G.V., Kochetkova O.P. Digital technology in oil and gas wells drilling control. URL (date of access 08.09.2021) (in Russian).
- “Axel Telemetria” Ltd. URL (date of access 08.09.2021) (in Russian).
- Radioactive logging during drilling. URL (date of access 08.09.2021) (in Russian).
- Rogachev O.K., Lyshenko A.A. In Russian – telemetry, in English – MWD. URL (date of access 08.09.2021) (in Russian).
- The Russian directional and horizontal drilling support services market: current status and its development scenarios for 2020-2030. RPI study June 2020. URL (date of access 10.09.2021) (in Russian).
- Rosneft and Schlumberger develop local high-tech drilling equipment market. URL (date of access 08.09.2021) (in Russian).
- DD, telemetry and logging technologies during drilling. URL (date of access 26.09.2021) (in Russian).
- Energy Strategy of the Russian Federation to 2035. URL (date of access 2.08.2021) (in Russian).
- Hsu-Hsiang Wu, Golla C., Parker T. et al. A New Ultra-Deep Azimuthal Electromagnetic LWD Sensor for Reservoir Insight. SPWLA 59th Annual Logging Symposium, 2-6 June 2018, London, UK. OnePetro, 2018. N SPWLA-2018-X.
- Amorim D., Hanley D., Leite D.J. BHA Selection and Parameter Definition Using Vibration Prediction Software Leads to Significant Drilling Performance Improvements. SPE Latin America and Caribbean Petroleum Engineering Conference, 16-18 April 2012, Mexico City, Mexico. OnePetro, 2012. N SPE-152231-PP. DOI: 10.2118/152231-MS
- Carpenter Chris. Thailand Joint-Development Project Delivers MWD/LWD Benefits. Journal of Petroleum Technology. 2019. Vol. 71. Iss. 2, p. 50-52. DOI: 10.2118/0219-0050-JPT
- Chuilon P., Puyou G., Caroli E. et al. From Houston API Calibration Pits… to Artigueloutan Logging Metrological Facility. SPWLA 60th Annual Logging: Symposium Society of Petrophysicists and Well-Log Analysts, 15-19 June 2019, Texas, Houston, USA. OnePetro, 2019. N SPWLA-2019-GGGGG. DOI: 10.30632/T60ALS-2019_GGGGG
- Hansen R.R., White J. Features of Logging-While-Drilling (LWD) in Horizontal Wells. SPE/IADC Drilling Conference, 11-14 March 1991, Amsterdam, The Netherlands. OnePetro, 1991. N SPE-21989-MS. DOI: 10.2118/21989-MS
- Edvardsen I., Nyrnes E., Johnsen M.G.G. et al. Improving the Accuracy and Reliability of MWD/Magnetic-Wellbore-Directional Surveying in the Barents Sea. SPE Drill & Completion. 2014. Vol. 29. Iss. 2, p. 215-225. DOI: 10.2118/166226-PA
- Luycx Mathilde, Torres-Verdín Carlos, Mohnke Oliver et al. Improvements of Fast Modeling of LWD Neutron Logs Acquired in Enlarged Boreholes for a Commercial LWD Too. SPWLA 59th Annual Logging Symposium, 2-6 June 2018, London, UK. OnePetro, 2018. N SPWLA-2018-HHH.
- Jackson C.E., Fredericks P.D. Proactive Use of Logging-While-Drilling (LWD) Measurements Improve Horizontal Well Drilling and Subsequent Evaluation. SPE/IADC Asia Pacific Drilling Technology, 9-11 September 1996, Kuala Lumpur, Malaysia. OnePetro, 1996. N SPE-37157-MS. DOI: 10.2118/37157-MS
- Sugiura J., Jones S. A Drill Bit and Drilling Motor with Embedded High-Frequency 1600 Hz Drilling Dynamics Sensors Provide New Insights into Challenging Downhole Drilling Conditions. SPE/IADC International Drilling Conference and Exhibition, 4-7 March 2019, Hague, Netherlands. OnePetro, 2019. Vol. 4. Iss. 3, p. 223-247. DOI: 10.2118/194138-MS
- Jain J.R., Ledgerwood L.W., Hoffmann O.J. et al. Mitigation of Torsional Stick-Slip Vibrations in Oil Well Drilling through PDC Bit Design: Putting Theories to the Test. SPE Annual Technical Conference and Exhibition. 30 October – 2 November 2011. Denver, Colorado, USA. OnePetro, 2011. DOI: 10.2118/146561-MS
- Monterrosa L.C., Ferreira R.M., Blackburn J.D. MWD Surveying Enhancement Techniques and Survey Management Workflows Applied at a Barents Sea Field for Accurate Wellbore Positioning. SPE/IADC Drilling Conference and Exhibition, 14-16 March 2017, Hague, Netherlands. OnePetro, 2017. N SPE-184678-MS. DOI: 10.2118/184678-MS
- Nikitin A., Korjik M. An Impact of Nanotechnology on the Next Generation of Neutron Porosity LWD Tools. SPE International Oilfield Nanotechnology Conference and Exhibition, 12-14 June 2012, Noordwijk, Netherlands. OnePetro, 2012. N SPE-157024-MS. DOI: 10.2118/157024-MS
- Jachmann R.C., Li L., Reiderman A. Patent N US9784881. Nuclear magnetic resonance apparatus, systems, and methods. 2017.
- Kwak H., Hursan G., Shao W. et al. Predicting Carbonate Rock Properties Using NMR Data and Generalized Interpolation-Based Techniques. Petrophysics. 2016. Vol. 57. Iss. 4, p. 351-368.
- Jianqing Wei, Xiao He, Hao Chen, Xiuming Wang. Wavefield characteristics of unipole sonic LWD with eccentric tools. SEG Technical Program Expanded Abstracts. 2018, p. 734-738. DOI: 10.1190/segam2018-2996720.1
- Xinding Fang, Arthur Cheng. Detection of formation shear wave in a slow formation using monopole-acoustic logging while drilling. 2017 SEG International Exposition and Annual Meeting, September 2017, Houston, Texas, N SEG-2017-17635320.