Influence of hydraulic compression on porosity and permeability properties of reservoirs
- 1 — Ph.D., Dr.Sci. Director “Carbon-Oil” LLC ▪ Orcid ▪ Elibrary
- 2 — Ph.D., Dr.Sci. professor Ufa State Oil Technical University ▪ Orcid ▪ Elibrary ▪ Scopus
- 3 — Ph.D., Dr.Sci. professor Ufa State Oil Technical University ▪ Orcid ▪ Elibrary ▪ Scopus ▪ ResearcherID
- 4 — Ph.D. Associate Professor Branch of Ufa State Oil Technical University in Oktyabrskiy ▪ Orcid ▪ Elibrary ▪ Scopus ▪ ResearcherID
- 5 — Ph.D. associate professor Ufa State Oil Technical University ▪ Orcid ▪ Elibrary ▪ Scopus
- 6 — Research Officer Branch of Ufa State Oil Technical University in Oktyabrskiy ▪ Orcid ▪ Elibrary ▪ Scopus ▪ ResearcherID
Abstract
Active development of hard-to-recover oil reserves causes the need for an innovative approach to methods of oil recovery and intensification of its production, based on taking into account the specifics of filtration processes in low-productive reservoirs and complex geological and physical conditions. Pilot works for studying the mechanism of changes in porosity and permeability properties of reservoirs during swabbing of wells are presented. Based on the hydrodynamic investigations performed, the results of the work are analyzed. The method of oil production intensification using hydraulic compression of formation has been developed. It has been shown that when using hydraulic compression technology in the pore space of the formation, the effect of capillary and gravitational forces is strongly reduced. The influence of these forces decreases when significant pressure gradients with changing direction are formed during well swabbing for depression impact on the bottomhole zone of the formation. Hydraulic compression induced an increase in well productivity and flow rate; insights into how how permeability and porosity properties change during well swabbing were clarified. The range of compressive durability (minimum and maximum values) was determined for the Verean deposits of the Melekeskaya Depression and the South Tatar arch. The impact of formation hydraulic compression caused changes in permeability and porosity properties of the reservoir in the bottomhole zone on a qualitative level. Piezo- and hydraulic conductivity increased by 20 %. Experimental work in well 1545 of Keremetyevskoe field showed an increase of piezo- and hydraulic conductivity coefficients, effective formation thickness, change of filtration flows character.
Introduction
Hydrocarbon fields awaiting development are most often located in areas of environmental constraints and hard-to-reach areas. In terms of reserves category, they can be classified as medium and small fields with low productive characteristics. Modern situation in the oil industry requires a focus on small fields. For remote fields that lack roads, power lines and non-compressed gas lift capability, jet units have been used successfully. In this case, the power surface pumps are driven by gas engines running on associated gas from production wells. Based on research and analysis on efficiency of oil production technologies, as early as 1996, hydrodriven pumps were massively introduced at small West Siberian fields.
Scientists and specialists in Russia and the USA have created various jet pump configurations: submerged power-driven and surface-mounted (where the power pump is installed on the surface). A significant disadvantage of such technologies is the need for costly and time-consuming installations. Creating large depressions to deliver flow in low-producing formations requires significant energy inputs, increasing operating costs, which is also a significant disadvantage.
Active commissioning of hard-to-recover reserves (HRR) requires a special approach to designing, monitoring and managing oil production processes due to the special features of filtration [2, 10, 27]. The approach is formed based on studying peculiarities of oil recovery by creating a scientific and methodological basis for decision-making by analogy method [11, 13, 31], and also by using innovative technologies after their testing under specific field conditions and defining the areas of their effective application [12, 32, 38].
Within the investigated structures (Melekesskaya Depression (MD) and South Tatar arch (STA), most of the hydrocarbon HRR are confined to separately located and isolated structural uplifts, which are close to the large-scale fields [9, 29]. Traditional approaches and technologies of developing such oil and gas reserves (development, waterflooding, etc.) do not allow achieving acceptable economic results [1, 28, 36].
The production stock of wells, producing deposits and fields are used with low efficiency, as it is not uncommon for some wells to be idle and/or forced to be abandoned due to insufficient provision (financial and material) for developing or maintaining surface communications and equipment in serviceable condition. In this situation, swabbing of low-producing wells can be used for their operation and serve as an alternative technological method of oil recovery, and there is no need for significant investment in the development [19, 21].
Results of transferring wells from conventional mechanized production to swabbing production show that all such cases resulted in an increase in well flow rates of 100 % or more. For example, at the Maximkinskoye field, formation fluid was extracted from wells N 643 and 644 using screw pumps, with fluid flow rates of 6.5 and 4.1 m3/day, respectively. With the beginning of oil extraction from wells by swabbing, their flow rate increased significantly: well N 643 – 8.6 m3/day (increase 32.3 %), well N 644 – 10.2 m3/day (increase 143.9 %). After inflow stimulation, during further development of the well by means of swabbing, its flow rate decreases in approximately the same proportions during further operation with mechanized oil production. A significant portion of the increase in well flow rate results from the formation of significant alternating pressure gradients in the near-bottomhole zone (NBHZ) during swabbing of the well. Occurrence of alternating pressure gradients of high magnitude levels the effect of capillary and gravitational forces in pore channels and fractures, which contributes to the growth of formation and well productivity [15, 30].
In a fractured porous carbonate reservoir, the pressure is not redistributed at a high rate, which may be due to the movement of formation fluids to the borehole bottoms only through fractures, into which the fluid is filtered from the porous blocks of the reservoir by capillary impregnation [17, 22, 25].
Worth mentioning that operating costs decreased when wells were transferred from traditional mechanical methods of operation to production using periodic swabbing.
Research pilot works to clarify ideas about changes in permeability and porosity properties (PPP) during swabbing were carried out at the well N 21 on the Sverdlovskoye elevation located within the Keremetyevsky subsoil area, developed by the small company “Blagodarov-Oil” LLC. Well 21 is producing oil from a 2.1×0.8 km reservoir in the Verey reservoir with a flow rate of 1.4 m3/day of water-free oil (before operation); the formation pressure in the deposit is 5.7 MPa.
The relationship between formation pressure decrease to and below the permissible limits with deformation of rocks comprising the productive formation, which leads to irreversible PPP deterioration of the carbonate reservoir in deposits containing HRR oil, has not been sufficiently studied [14, 20].
Thus, HRR development by alternative and energy-efficient methods for oil confined to low-producing and complex formations is an important task.
Methodology
In order to increase the efficiency of the impact on low-producing formations, the effect of lowering the bottomhole pressure to the maximum allowable value and below on the processes in the porous medium of productive sediments, causing irreversible changes in reservoir PPP in deposits containing oil HRR, has been studied.
There is a common notion that productivity of a well decreases several times after its bottomhole pressure decreases from the permissible value, which irreversibly changes pore and fracture space (fracture closure) [6-8] and deteriorates PPP of terrigenous and carbonate reservoirs in the NBHZ [4, 33, 41]. Such phenomena have been noted in field practice, but not all cases show sharp deterioration, which is explained by different mechanical and reservoir properties of rocks and formation fluids [23].
When the bottomhole pressure compares with the critical pressure and falls below it, the reservoir is compressed, blocking pore-fracture channels so that fluids cannot move to the well. However, by overcoming this barrier, the formation of microfractures can increase the PPP of NBHZ [26, 40]. Investigations have also revealed that 10-15 % decrease of formation pressure from the initial one causes sharp irreversible changes of rock permeability due to deformation processes. This may increase the permeability above the initial value [18]. The specific response of rock to stresses that occur during loading and unloading also depends on the rate and mechanism of the force impact. With increasing deformation rate, rock ductility decreases, and in most typical oil field sections, microfracturing along grain boundaries develops during short-term exposure, causing rock structure decompaction [18]. Loosening of rock structure during disjunctive disturbance (deformation) leads to the formation of micropores and microfractures in the deformed rock, and the loosening can amount to several tens of percent (especially in sedimentary rocks) [18].
Other investigations have established that the permeability of reservoir rocks increases as a result of the formation of a new system of micro- and macrofractures, when certain stresses and their magnitude are reached in these rocks. This phenomenon is called geobursting. This technology was tested on some fields near Ural and in Western Siberia and gave good results [5].
Based on previous investigations and conclusions, the paper hypothesises tha the formation of new filtration channels is caused by repeated depressions, which occur during well swabbing.
Methods of deterministic analysis and modeling were used to process the results of reservoir impact and research. Based on simulation of processes in NBHZ, a comprehensive and systematic study for interaction of various factors in ongoing processes and measurement of reservoir parameters affecting the value of well productivity was carried out. The factors affecting the results of hydraulic compression were identified. The most significant ones are compression durability and related porosity of reservoir rock.
Compression durability limit of a reservoir (σc) is a characteristic that determines the possibility of improving the PPP and is at the same time a criterion. Rock durability determined on the rock sample is higher than that of the same rock in the reservoir (in the rock mass) due to the presence of dislocations and their heterogeneity. Rock samples used in the experiments were taken from the wells of the Sverdlovsky uplift. Deposits of the Verey horizon are represented by organogenic-clastic limestone; the reservoir is porous. Based on the laboratory investigations for the compression of rock samples, the compression limits of the rocks composing the verey formation in MV and UTS were calculated using the expression
where σс0 - compression durability limit of the rock; а - empirical coefficient describing the shape of the pores,а = 1.4-4.0; m – porosity of the reservoir.
Using the graph (fig. 1), value range of the compression durability limit for the rocks composing the NBHZ around the analyzed well N 21 was determined to be 4.8-19.0 MPa.
The pressure at the depth of the top of the productive formation, upon reaching which irreversible changes in the pore space of the reservoir and its PPP can begin, is determined by the following expression:
where Рf.c – current formation pressure, MPa.
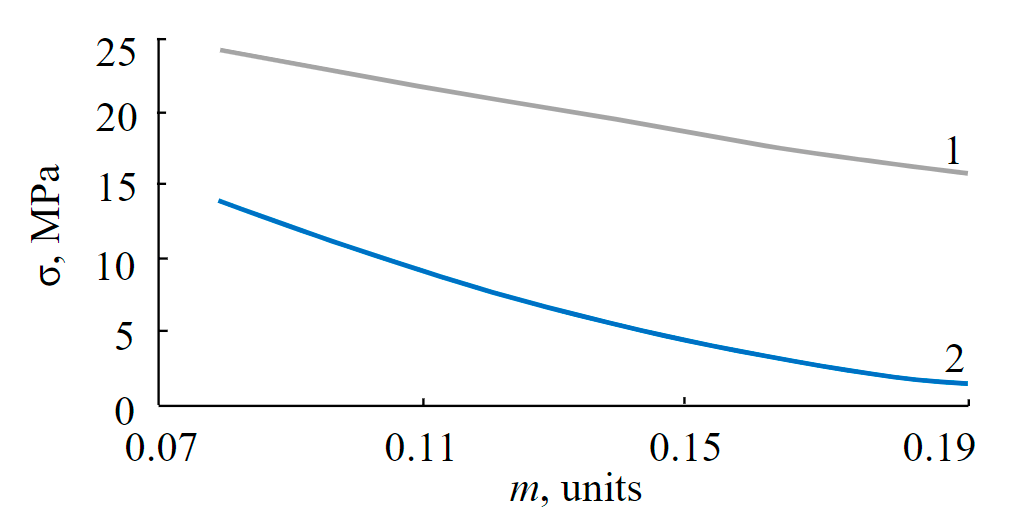
Fig.1. Range of compression limits for rocks comprising the Verey horizon in MV and UTS, depending on porosi-ty 1 – maximum durability limit; 2 – minimum durability limit
In the process of swabbing, when certain conditions were reached, the initiation moment of gradual compression in mineral skeleton of reservoir formation and reduction of filtration channels cross-section occurred, which resulted in decrease of well inflow (and its flow rate). The change in bottomhole pressure during swabbing has been instrumentally recorded and is shown in Fig.2.
When the declining pressure in the well at the depthe of the top of the productive formation fell into the 0.84-0.57 MPa range, the fluids from the formation stopped entering the well. Swabbing was continued for 75h (three operations were performed) to maintain the pressure at that level. The swabbing was then stopped and the pressure recovery curve (PRC) was recorded at the bottomhole of the well. Analysis of the PRC allows to obtain formation characterization and identify the reservoir alterations.
Determination of working thicknesses of productive sediments before and after hydraulic formation compression (HFC) in the production well was carried out using the standard inflow profile method, while in the injection well, the absorption profile was determined.
During the investigation and impact on the NBHZ, a technology was used, in which the processes at the bottomhole of the well during HFC can be monitored. UEGIS-2 jet pump was used for this purpose. The technology with the use of jet pumps allows determining necessary formation parameters during the work and correcting actions of the workover team in the real-time mode. This method of impact on the NBHZ and research allows conducting hydrodynamic investigations of wells (HDIW), determining formation parameters in the near- and far-bottomhole zones, and identifying the boundaries of formation properties changes and the presence of screens inside the reservoir in the interwell space.
UEGIS-2 (Fig.3) operates in a well under the action of working technological fluid flowing through it (the simplest variant is water; surface-active agent solutions and oil can also be used), which comes in through the tubing and is pumped from the surface by a mobile pump unit. The working fluid enters the injection channel 6, located in the frame 7, then through nozzle 5 into the chamber 4. At the nozzle inlet in chamber 4 there is a sharp rarefaction, which is transferred to the space under the packer by the passage channel 1, communicating with the uncovered (perforated) formation. Thus, it creates a depression on the formation, regulated by decreasing the pressure in the subpacker space that depends on the work intensity of UEGIS-2, which is regulated by the velocity of the working fluid flowing through the nozzle. The velocity of the working fluid flow through the UEGIS-2 is determined by the developed pressure and productivity of the pumping unit.
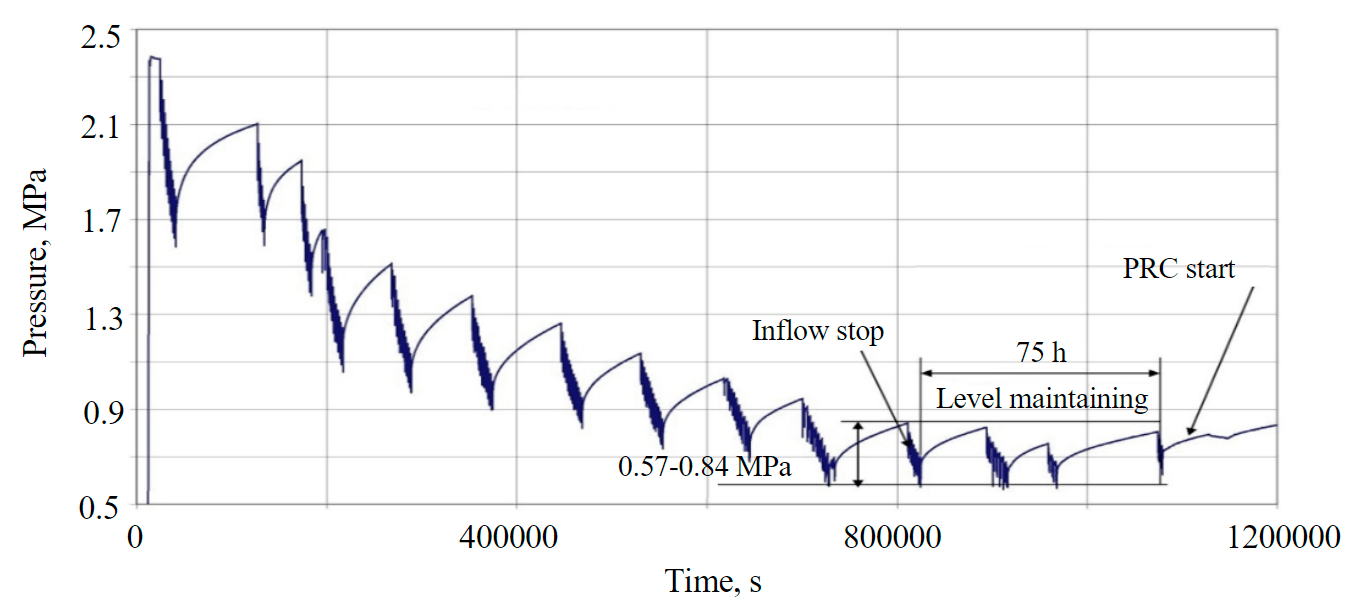
Fig.2. Bottomhole pressure dynamics in the process of swabbing the well N 21
Depression on the formation causes formation fluids to flow into the well (into the subpacker zone), then they rise to the rarefaction zone in chamber 4, where they are “sucked” (lifted) by the working fluid flow into chamber 3 and are carried to the surface through the diffuser 2.
In order to direct the fluid from the tubing to the nozzle, various inserts are used. If the insert is not removed for some time after the unit has stopped, the hydrostatic level is restored.
In order to increase injectivity and reach of the formation by impact, pilot hydro-compression of the formation was carried out in injection well N 1545 of the Maltsevskoye field. Productive formations of Verey horizon and Bashkirian stage of this field lie relatively not deep and have low reservoir pressure. Under these conditions reservoir durability limits are achievable for UEGIS-2.
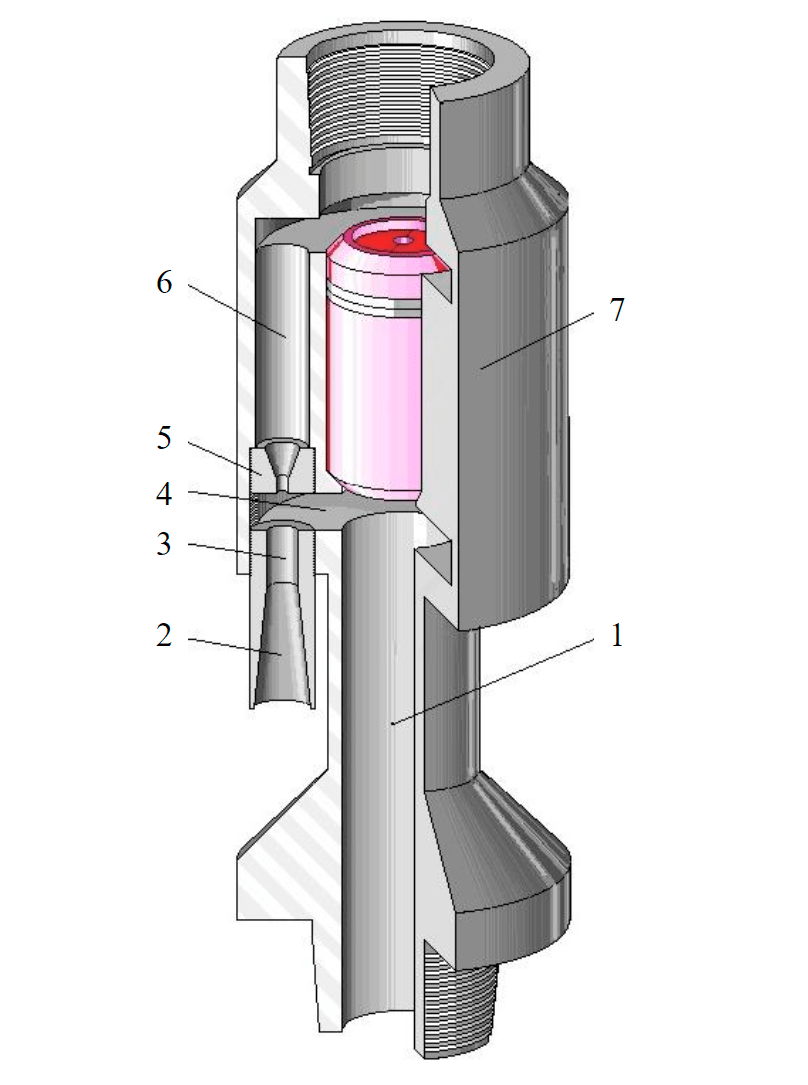
Fig.3. UEGIS-2 pump
The pressure at which irreversible fractures in the formation can occur was calculated during the preparation phase of the work. The maximum possible depression is approximately equal to the average wellhead pressure when injecting fluid into the formation. Theoretically, it is not possible to create a depression below this value.
Discussion
The HFC analysis caused a qualitative change of the reservoir PPP in the near-bottomhole zone. Before and after the HFC, PRC investigations were conducted and the results showed a 19 and 18 % increase in piezo- and hydraulic conductivity, respectively. This effect usually occurs when the permeability of the porous medium increases due to porosity growth. When the reservoir is compressed, more microfractures form between separated pore associations, which increases the open porosity of the reservoir.
Based on the interpretation of the research data obtained using deterministic analysis and modeling, it can be stated that the fluid level in the well decreased due to fluid filtration from the wellbore into the pore-fracture space of two zone layers (lag times are 12 and 69 min), located at a distance of about 109-114 m from the well. The fractures that closed during swabbing opened after the depression was reduced, causing the formation to absorb fluid from the well.
Field investigations (HDIW and PRC) using productive formation compression with periodic sustained hard depressions showed that three conditionally circular zones were formed around the well in the formation:
- zone 1 of radius 0.4-3.0 m with new microfracturing;
- zone 2 with a radius of 80-83 m, where the fractures are compressed and the fluid is squeezed out of the matrix;
- zone 3 with a radius of 109-114 m, where sharp fracture opening and fluid absorption occurred.
The zones were identified based on a well investigation by the PRC method, which clearly highlighted two areas with differently directed changes in following values:
- reduced piezoelectricity and increased hydraulic conductivity at 0.4-3 m from the well;
- reduced hydraulic conductivity and increased piezoconductivity at 80-83 m from the well.
Since the mentioned formation parameters differ only in effective thickness and compressibility coefficient, it can be concluded that if the effective thickness is constant, the compressibility coefficient of the formation system changes.
As the porosity of a rock rises, its compressibility coefficient increases, and if the porosity is small, the compressibility coefficient will also be smaller. Consequently, in an area with a radius of 0.4-3 m radius the porosity of the formation has increased. Under such conditions, this can only occur as a result of microfracturing.
At 80-83 m from the borehole, the porosity of the reservoir decreased slightly. This may be a result of depression compressing the reservoir but not causing microfracturing.
Formation with complex geological structure was perforated in the well, causing fluid to “escape” into the interlayer above the interval with re-formed microfractures.
When the reservoir is compressed and additional forces are generated, formation fluids destroy blocking partitions between separated pore spaces, additional microfractures are formed and the open porosity of the formation increases. This mechanism of impact on the formation of the HFC technology improves PPP of the reservoir in the NBHZ, and as a result, the productivity of the treated well increased. Comparing the results of PRC investigations before and after the HFC, it was determined that the productivity coefficient of the well increased from 0.015 to 0.054 m3/(day∙MPa).
Compression of a formation to irreversible deformations of its structure by depression requires more effort than technogenic disjunctive disturbance of the reservoir by significant repression (as in hydraulic fracturing) [35, 37, 39]. The value of the current formation pressure is not always known, especially in the conditions of a multilayer deposit.
In order to clarify formation pressure value and interaction of “unit – pump – well – formation” system, testing through UEGIS-2 depression insert (Fig.4) was carried out. After removal of the insert and interpretation of the measurement recorded by the downhole instrument, the value of formation pressure (10.8-11.0 MPa) was clarified, as well as the pressure dependence at the level of the instrument installation on the unit pressure and the productivity coefficient was determined. Further work was carried out through the PRC insert.
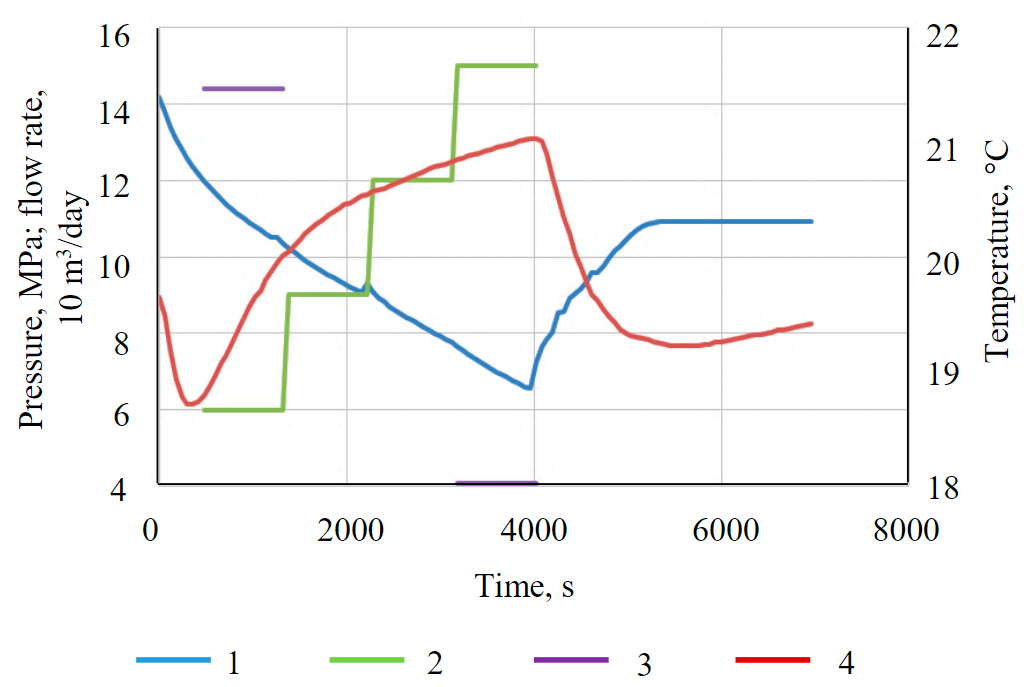
Fig.4. Test results through the depression insert 1 – pressure, MPa; 2 – pressure at the unit, MPa; 3 – flow rate, m3/day; 4 – temperature, °С
When the wellhead pressure was increased in steps from 15 to 18 MPa using the CA-320 unit, the fluid outflow from the well increased linearly. Upon reaching 18 MPa, there was a sharp drop in flow rate, followed by a sharp increase - the first stage of reservoir destruction. Further step-by-step (in 2 MPa increments) increase of the wellhead pressure up to 25 MPa also resulted in the sudden drop of the flow rate, followed by its sharp growth. When wellhead pressure was maintained at 25 MPa for 30 min, the flow did not increase. For technical reasons, operations were stopped at Pw = 25 MPa (Fig.5).
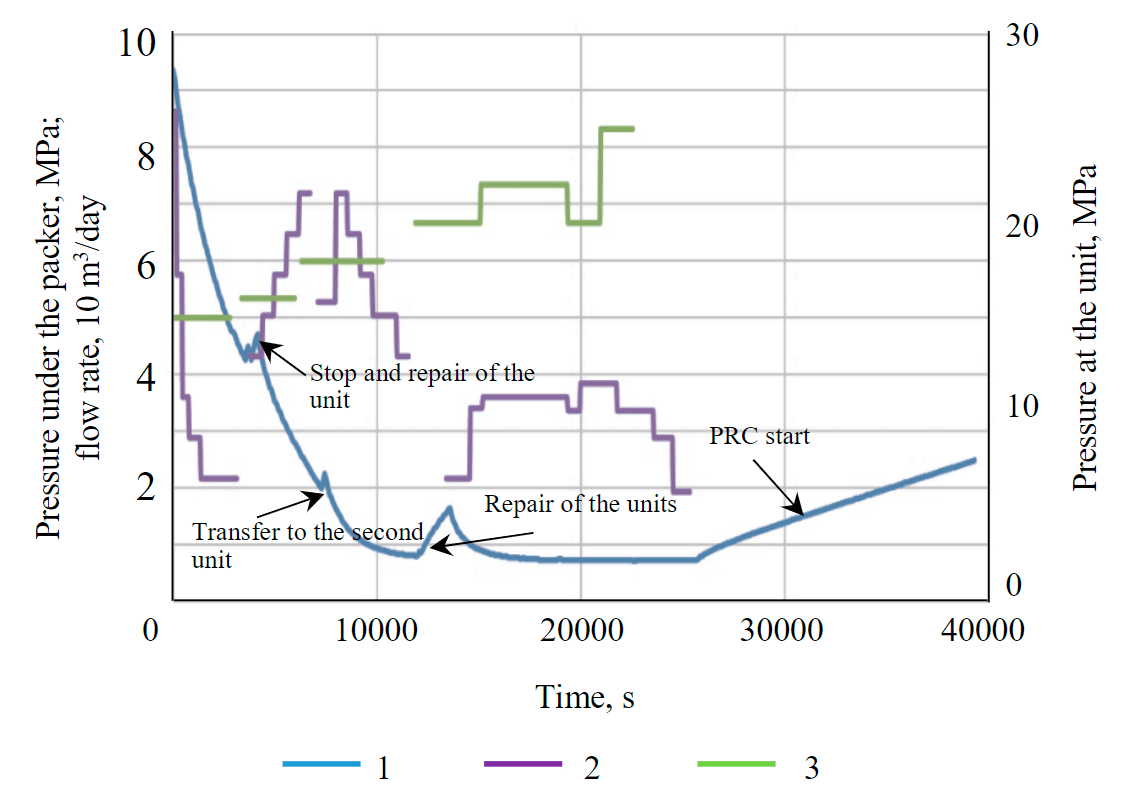
Fig.5. Dynamics of technological parameters at HFC 1 – pressure under the packer, MPa; 2 – flow rate, m3/day; 3 – pressure at the unit, MPa
The outflow and composition of the liquid were monitored during the operation. At the fourth hour of operation with jet pump, oil began to appear in the measuring tank of the CA-320. After the second stage of reservoir destruction at Pw = 20 MPa, mainly oil flowed out of the well.
Changes in the formation matrix occurred when the top of the perforation interval was depressed to 10 MPa (Pw = 18-20 MPa). These values correspond to the first four interlayers that have maximum porosity and permeability coefficients. Clay content of interlayers (variation in the range of 0.7-5.8 %) had no obvious effect on the impact success. The remaining interlayers were not affected. It is possible that if more powerful units had been applied and greater depression had been created, irreversible processes would have occurred in the remaining productive formations as well. However, in this case, increasing the pressure on the unit above 18 MPa did not result in a noticeable reduction in bottomhole pressure.
Nevertheless, the evaluation of parameters by HDIW showed that the formation PPP and the type of fluid movement to the well have changed significantly (Fig.6, table).
The formation was interpreted as screened on three sides before the geological and technical measures (GTM) were carried out; after hydrocompression, the filtration in the formation became radial. The composition of the fluid also changed – the injection well, which had been in operation for a long time, gave an oil inflow during the process. The effective thickness of the formation has increased. All indications are that new channels have formed in the formation that are hydrodynamically connected to the well.
When a depression is created, water is the least compressible and the reservoir skeleton has the highest compression ratio. Therefore, water, with its mobility, breaks through to the well, being an additional factor in destroying blocking partitions in the fracture-pore space and participating in the formation of filtration channels.
The actual operation mode of the injection well (Fig.7) after the GTM indicates the success of the operation. Thus, at equal injection pressures before and after the GTM the injectivity increased by 2-2.1 times, which significantly reduced energy consumption and allowed increasing the pressure gradient.
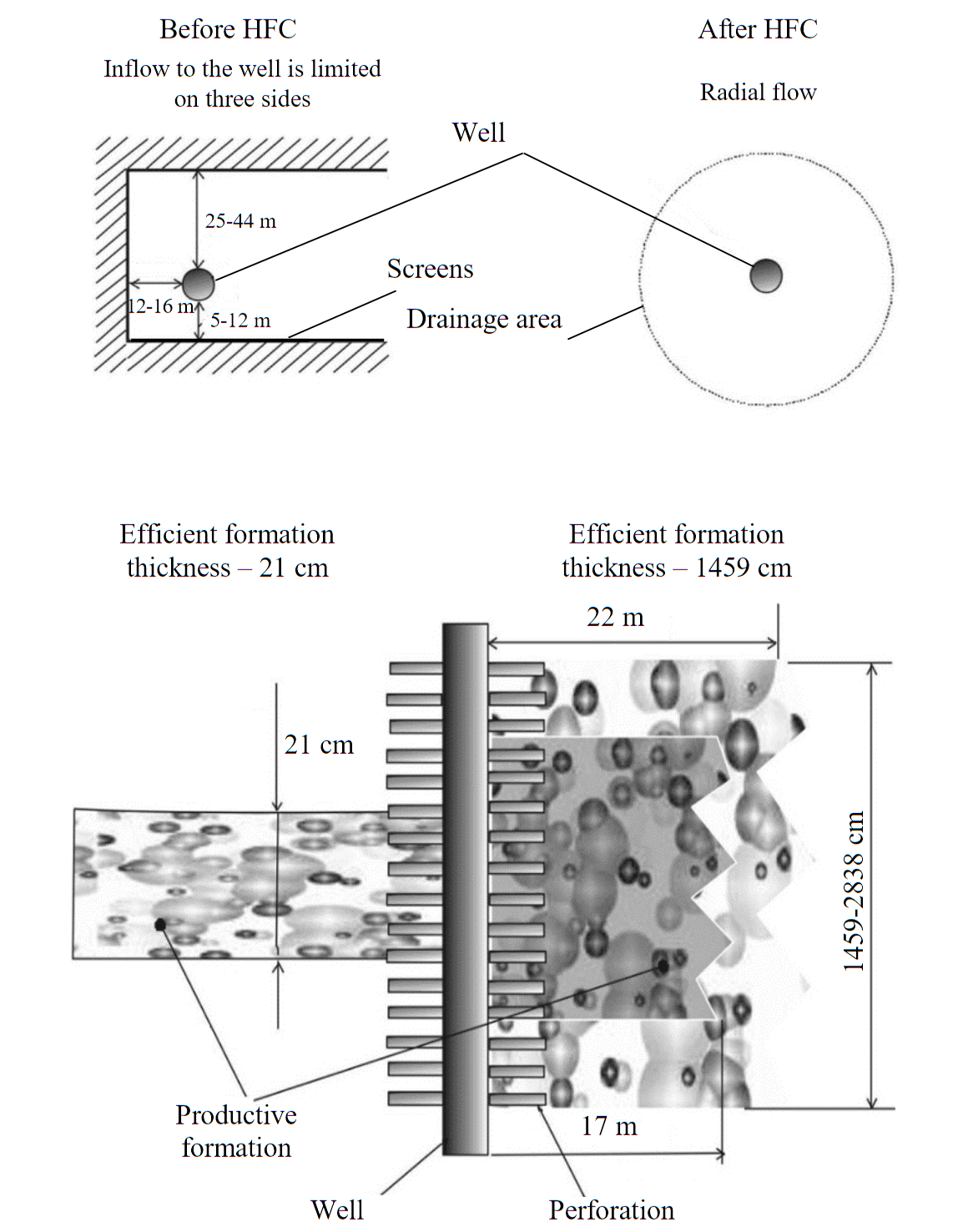
Fig.6. Geometric parameters of the formation before and after the HFC
Thus, it is shown that irreversible changes in the reservoir can be achieved not only by repressions, as in hydraulic fracturing, but also by long term depressions (HFC), which under specific geological and physical conditions of small remote fields can be positioned as a production enhancement method. Theoretical conclusions have been confirmed by works at specific wells of Keremetyevsky subsoil area.
Parameters of the productive formation in well N 1545, determined by processing the results of the PRC investigation
Formation parameters |
Values |
|
Before HFC |
After HFC |
|
Formation model |
Rectangular strip, screened on three sides |
Circular formation with a well in the center |
Hydroconductivity, (µm2∙m)/(mPa∙s) |
0.0032 |
0.0046 |
Piezoconductivity, m2/s |
9∙10–4 |
13∙10–4 |
Formation pressure, MPа |
13.5 |
13.5 |
Effective thickness, m |
0.2 |
14.59 |
Bottomhole pressure, MPа |
17.1 |
16.9 |
Injection coefficient, m3/(day∙MPa) |
3.33 |
7.0 |
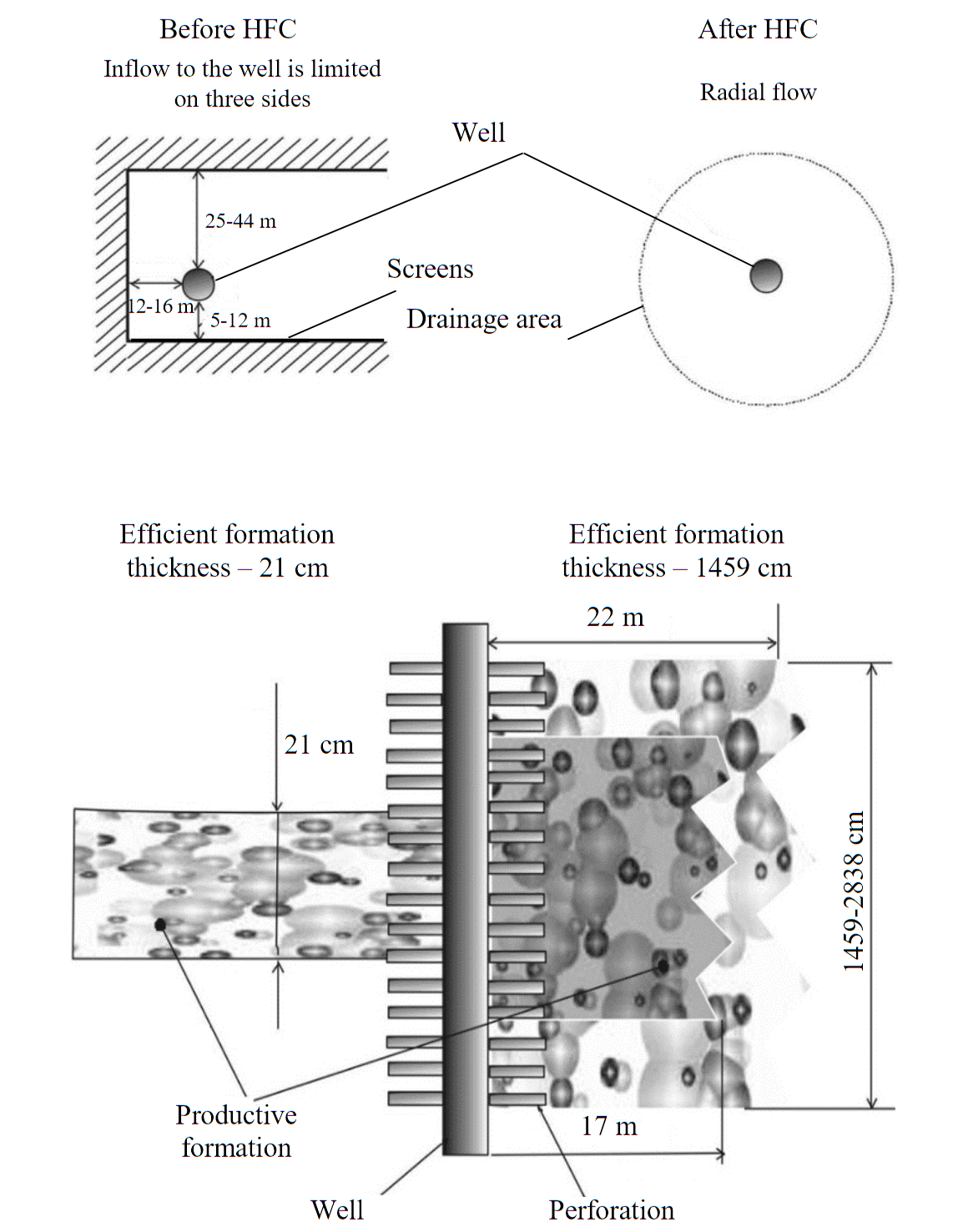
Fig.7. Injection dynamics in well N 1545 1 – Qliq before HFC; 2 – Qliq after HFC; 3 – Рw before HFC; 4 – Рw after HFC
It can be assumed that the impact on productive formation by hydraulic compression causes lowering of rock mass and can cause phenomena dangerous for the environment. In [3, 24] it is shown that geodynamic processes, caused by disturbance in equilibrium of rock and formation pressure in productive formations, have a negative impact on geological environment (subsidence and sinking of earth surface, flooding, earthquakes, etc.). The degree of impact depends on the size of the field, scale and implementation level of technological processes. Development of large oil and gas fields can have a significant, and in some cases irreversible, regional impact on the environmental situation. At the same time, it is necessary to take into account that small oil fields are distant from each other by dozens of kilometers. That is why the impact of their development processes on the environment is local and can be easily overcome by the nature [16, 34].
Such marginal fields can be the main targets of the proposed HFC technology for enhanced oil recovery.
Conclusion
As a result of pilot works at wells of Maksimkinskoye and Keremetyevskoye fields, the efficiency of HFC swabbing method for oil production stimulation was proved for the first time. Geobursting was used as an integral part of the HFC technology in order to form a new microfracturing in low-productive formation for the purpose of increasing the permeability. It was found out that the application of HFC increases hydro- and piezoconductivity coefficients by almost 1.2 times, potential productivity coefficient and flow rate at 1 MPa – 3.7 times; the efficiency of the producing formation thickness increases from 0.2 to 14.59 m. When a similar effect is applied to an injection well, hydrodynamic investigations have shown a 2.1-fold increase in injectivity coefficient, which significantly reduces energy costs and increases the pressure gradient in the formation pressure maintenance system.
References
- Andreev A.V., Mukhametshin V.Sh., Kotenev Yu.A. Predicting deposit productivity in hard-to-recover carbonate reservoirs. Nauchnye trudy NIPI NEFTEGAZ GNKAR. 2016. N 3, p. 40-45 (in Russian).
- Belov A.Yu., Belova A.A., Strakhov P.N. Geological aspects of the development of hydrocarbon deposits with hard-to-recover reserves. Oil Industry. 2021. N 3, p. 50-53. DOI: 10.24887/0028-2448-2021-3-50-53
- Bulygin D.V., Nikolaev A.N., Elesin A.V. Hydrodynamic evaluation of the efficiency of flow deflecting technologies in conditions of formation of man-made filtration channels. Georesources. 2018. Vol. 20. N 3. Part 1, p. 172-177. DOI: 10.18599/grs.2018.3.172-177
- Yakupov R.F., Khakimzyanov I.N., Mukhametshin V.V., Kuleshova L.S. Application of a hydrodynamic model in the creation of an oil back cone in water-oil zones. Nauchnye trudy NIPI NEFTEGAZ GNKAR. 2021. N 2, p. 54-61 (in Russian).
- Karev V.I., Kovalenko Yu.F. Geomechanics of oil and gas wells. Vestnik of Lobachevsky University of Nizhni Novgorod. 2011. N 4 (2), p. 448-450 (in Russian). URL
- Kashnikov Yu.A., Yakimov S.Yu. Geomechanical and hydrodynamic estimation of the bottom-hole pressure influence on the well performance. Oil Industry. 2019. N 11, p. 111-115. DOI: 10.24887/0028-2448-2019-11-111-115 (in Russian).
- Martyushev D.A., Galkin S.V., Shelepov V.V. Influence of rock stress state on matrix and fracture permeability in different lithological and facial zones of the Tournai-Famenian oil deposits of the Upper Kama region. Vestnik Moskovskogo universiteta. Seriya 4: Geologiya. 2019. Vol. 5, p. 44-52. DOI: 10.3103/S0145875219060061
- Martyushev D.A. Experimental study of the influence of bottomhole pressure of producing wells on reserve production from complicated carbonate reservoirs. Bulletin of the Tomsk Polytechnic University. Geo Assets Engineering. 2021. Vol. 332. N 5, p. 110-119. DOI: 10.18799/24131830/2021/05/3190 (in Russian).
- Muslimov R.Kh. A new strategy for oil fields development in modern Russia – production optimization and oil recovery maximization. Neft. Gaz. Novatsii. 2016. N 4 (187), p. 8-17 (in Russian). URL
- Muslimov R.Kh. On a new paradigm for the development of the oil and gas complex in Russia. Oil Industry. 2021. N 3, p. 8-13. DOI: 10.24.887/0028-2448-2021-3-8-13 (in Russian).
- Mukhametshin V.V., Kuleshova L.S. On reducing uncertainty in waterflood management of hard-to-recover reserves. Izvestiya Tomskogo politekhnicheskogo universiteta. Inzhiniring georesursov. 2020. Vol. 331. N 5, p. 140-146. DOI: 10.18799/24131830/2020/5/2644 (in Russian).
- Mukhametshin V.V., Andreev V.E. Increasing the efficiency of assessing the performance of techniques aimed at expanding the use of resource potential of oilfields with hard-to-recover reserves. Bulletin of the Tomsk Polytechnic University. Geo Аssets Engineering. 2018. Vol. 329. N 8, p. 30-36 (in Russian). URL
- Mukhametshin V.V. Improving the efficiency of performance evaluation of technologies aimed at expanding the use of the resource base of fields with hard-to-recover reserves. Nauchnye trudy NIPI NEFTEGAZ GNKAR. 2020. N 4, p. 42-50 (in Russian).
- Galkin V.I., Ponomareva I.N., Cherepanov S.S. et al. New approach to the study of the results of hydraulic fracturing (on the example of Bobrikovsky deposits of the Shershnevsky field). Bulletin of the Tomsk Polytechnic University. Geo Аssets Engineering. 2020. Vol. 331. N 4, p. 107-114. DOI: 10.18799/24131830/2020/4/2598
- Khakimzyanov I.N., Mukhametshin V.Sh., Bakhtizin R.N., Sheshdirov R.I. Determination of the volumetric well grid coefficient for estimating the final oil recovery coefficient when developing oil deposits with horizontal wells. Nauchnye trudy NIPI NEFTEGAZ GNKAR. 2021. N 2, p. 47-53 (in Russian).
- Yakupov R.F., Mukhametshin V.Sh., Khakimzyanov I.N., Trofimov V.E. Optimization of reserve production from water oil zones of D3ps horizon of Shkapovsky oil field by means of horizontal wells. Georesources. 2019. Vol. 21. N 3, p. 55-61. DOI: 10.18599/grs.2019.3.55-61
- Davydova A.E., Shchurenko A.A., Dadakin N.M. et al. Optimization of carbonate reservoir well testing. Perm Journal of Petroleum and Mining Engineering. 2018. Vol. 17. N 2, p. 123-135. DOI: 10.15593/2224-9923/2018.2.3 (in Russian).
- Pavlova N.N. Deformation and reservoir properties of rocks. Moscow: Nedra, 1975, p. 240 (in Russian).
- Zubova L.Yu., Zubova O.D., Knyazev P.Yu., Khuzin R.R. Patent N 2462588 RF. Method of hydraulic reservoir compression. Opubl. 27.09.2012 (in Russian).
- Rogachev M.K., Mukhametshin V.V. Control and regulation of the hydrochloric acid treatment of the bottomhole zone based on field-geological data. Journal of Mining Institute. 2018. Vol. 231, p. 275-280. DOI: 10.25515/pmi.2018.3.275
- Khuzin R.R. Geotechnological bases for the development of hard-to-recover reserves in small, complex oil fields. Samara: Neft. Gaz. Novatsii, 2012, p. 384 (in Russian).
- Yakupov R.F., Mukhametshin V.Sh. Problem of efficiency of low-productivity carbonate reservoir development on example of Turnaisian stage of Tuymazinskoye field. Oil Industry. 2013. N 12, p. 106-110 (in Russian). URL
- Yaremiichuk R.S., Kachmar Yu.D. Drilling-in of productive horizons and development of wells. Lvov: Vishcha shkola, 1982, p. 152.
- Alvarado V., Thyne G., Murrell G.R. Screening Strategy for Chemical Enhanced Oil Recovery in Wyoming Basin. SPE Annual Technical Conference and Exhibition, 21-24 September 2008, Denver, Colorado, USA. OnePetro, 2008. N SPE-115940-MS. DOI: 10.2118/115940-MS
- Xin Du, Zhiwei Lu, Dongmei Li et al. A novel analytical well test model for fractured vuggy carbonate reservoirs considering the coupling between oil flow and wave propagation. Journal of Petroleum Science and Engineering. 2019. Vol. 173, p. 447-461. DOI: 10.1016/j.petrol.2018.09.077
- Cao Dinghong, Ni Yuwei, Yao Fei et al. Application and Realization of Fuzzy Method for Selecting Wells and Formations in Fracturing in Putaohua Oilfield: Production and Operations: Diagnostics and Evaluation. SPE Technical Symposium of Saudi Arabia Section, 21-23 May 2006, Dhahran, Saudi Arabia. OnePetro, 2006. N SPE-106355-MS. DOI: 10.2118/106355-MS
- Cheng Jing, Xiaowei Dong, Wenhao Cuid et al. Artificial neural network-based time-domain interwell tracer testing for ultralow-permeability fractured reservoirs. Journal of Petroleum Science and Engineering. 2020. Vol. 195. N 107558. DOI: 10.1016/j.petrol.2020.107558
- Economides J.M., Nolte K.I. Reservoir stimulation. West Sussex, England: Wiley, 2000, p. 856.
- Tongwen Jiang, Wei Yao, Xiongwei Sun et al. Evolution of anisotropic permeability of fractured sandstones subjected to true-triaxial stresses during reservoir depletion. Journal of Petroleum Science and Engineering. 2020. N 108251. DOI: 10.1016/j.petrol.2020.108251
- Xinlei Shi, Yunjiang Cui, Wankun Xu et al. Formation permeability evaluation and productivity prediction based on mobility from pressure measurement while drilling. Petroleum Exploration and Development. 2020. Vol. 47. Iss. 1, p. 146-153. DOI: 10.1016/S1876-3804(20)60013-1
- Ghareb Hamada, Veronique Joseph. Developed correlations between sound wave velocity and porosity, permeability and mechanical properties of sandstone core samples. Petroleum Research. 2020. Vol. 5. Iss. 4, p. 326-338. DOI: 10.1016/j.ptlrs.2020.07.001
- Jiazheng Qin, Shiqing Cheng, Peng Li et al. Interference well-test model for vertical well with double-segment fracture in a multi-well system. Journal of Petroleum Science and Engineering. 2019. Vol. 183. N 106412. DOI: 10.1016/j.petrol.2019.106412
- Jirjees Ali Y.,Abdulaziz A.M. Influences of uncertainty in well log petrophysics and fluid properties on well test interpretation: An application in West Al Qurna Oil Field, South Iraq. Influences Egyptian Journal of Petroleum. 2019. Vol. 28. Iss. 4, p. 383-392. DOI: 10.1016/j.ejpe.2019.08.005
- Jun He, Kegang Ling. Measuring permeabilities of Middle-Bakken samples using three different methods. Journal of Natural Gas Science and Engineering. 2016. Vol. 31, p. 28-38. DOI: 10.1016/j.jngse.2016.03.007
- Nur Wijaya, Sheng J.J. Comparative study of well soaking timing (pre vs. post flowback) for water blockage removal from matrix-fracture interface. Petroleum. 2020. Vol. 6. Iss. 3, p. 286-292. DOI: 10.1016/j.petlm.2019.11.001
- Economides M.J., Oligney R., Valkó P. Unified fracture design: bridging the gap between theory and practice. Texas: Orsa Press, 2002, p. 200.
- Daolun Li, Wenshu Zha, Shufeng Liu et al.Pressure transient analysis of low permeability reservoir with pseudo threshold pressure gradient. Journal of Petroleum Science and Engineering. 2016. Vol. 147, p. 308-316. DOI: 10.1016/j.petrol.2016.05.036
- Tyncherov K.T., Mukhametshin V.Sh., Khuzina L.B. Method to control and correct telemtry well information in the basis of residue number system. Journal of Fundamental and Applied Sciences. 2017. Vol. 9. N 2S, p. 1370-1374.DOI: 10.4314/jfas.v9i2s.848
- Mardashov D.V., Rogachev M.K., Zeigman Yu.V., Mukhametshin V.V. Well Killing Technology before Workover Operation in Complicated Conditions. Energies. 2021. Vol. 14. Iss. 3. N 654, p. 1-15. DOI: 10.3390/en14030654
- Yakupov R.F., Mukhametshin V.Sh., Tyncherov K.T. Filtration model of oil coning in a bottom water-drive reservoir. Periodico Tche Quimica. 2018. Vol. 15. Iss. 30, p. 725-733.
- Zoveidavianpoor M., Samsuri A., Shadizadeh S.R. Development of a Fuzzy System Model for Candidate-well Selection for Hydraulic Fracturing in a Carbonate Reservoir. SPE Oil and Gas India Conference and Exhibition, 28-30 March 2012, Mumbai, India. OnePetro, 2012. N SPE-153200-MS. DOI: 10.2118/153200-MS