Innovative ways to control dust and explosion safety of mine workings
- 1 — Ph.D., Dr.Sci. Leading Researcher FGBU VNIIPO EMERCOM of Russia ▪ Orcid ▪ Elibrary ▪ Scopus
- 2 — Ph.D. Leading Researcher FGBU VNIIPO EMERCOM of Russia ▪ Orcid ▪ Elibrary ▪ Scopus ▪ ResearcherID
- 3 — Ph.D. Head of Laboratory Saint Petersburg Mining University ▪ Orcid ▪ Elibrary ▪ Scopus ▪ ResearcherID
Abstract
Ensuring dust and explosion safety during underground coal mining is one of the most important tasks of industrial safety and labor protection departments. The main method of preventing explosions of coal dust settled in mine workings is to process them with stone dust (rock dusting). The traditional methods of quality control of rock dusting include radioisotope, optical and chemical methods. To implement them, the devices are equipped with environmentally harmful radioactive elements, expensive optical sensors, desiccants and replaceable flasks with chemical reagents, which increases the cost of analysis and its duration. The measurement error of these devices is 10 % or more. The main purpose of the study is to develop and substantiate a new method for monitoring the dust and explosion safety of mine workings, which will be devoid of the disadvantages of the methods mentioned above. It is proposed to evaluate the quality of rock-dust distribution by a fundamentally new way – thermogravimetric. The method was tested on the dust of coal mines in Kuzbass and the Vorkuta basin, including dust samples taken in mines with actual explosions. The article presents the results of experimental studies of the processes of thermal destruction of coal and stone dust mixtures. The non-overlapping intervals of the thermogravimetric reaction are identified: moisture yield (35-132 °С); volatile matter yield from coal (380-580 °С); thermal degradation of limestone with carbon dioxide yield (650-850 °С). Methods and mathematical dependencies for processing significant and qualitative identification characteristics of thermogravimetric curves in determining the content of non-combustible components in a sample of mine dust are considered.
Introduction
The development of coal deposits is accompanied by intensive formation and release of dust particles into the atmosphere. Dust entering the air is transported over considerable distances and deposited both within the excavation sites and outside them, leading not only to deterioration of working conditions, but also forming dust deposition exceeding the limit values – the lower concentration limits of flame propagation (LCLFP) [8, 11].
In coal mines, an additional factor is created – the limited space that makes possible the occurrence and spread of an explosion of coal dust. The conditional pentagon of dust explosibility (dust deposition above the LCLFP – soaring – oxygen – ignition – close space) receives a logical conclusion [27, 32]. So, if no dust explosions have been recorded at open-pit mining operations, despite the high volumes of dust emission, then explosions at coal mines involving coal dust occur in most coal-producing countries, including Russia [13-15]. The issue of dust control in underground [23, 25] and open-pit coal mining [3], as well as the assessment and reduction of the risks of explosions of dust-methane-air mixtures and the associated risks of injury to workers [1, 22, 31] is given quite a lot of attention.
In the process of coal mining, a mandatory regulatory requirement is to ensure the dust and explosion-proof condition of mine workings, which is achieved by neutralizing the explosive properties of coal dust [26, 28]. In most coal-mining countries, the main way to ensure dust and explosion safety is stone protection or rock dusting, based on the use of non-combustible stone dust [20, 24, 33].
Stone dust is manufactured in accordance with the requirements of GOST R 51569-2000 “Inert dust. Technical specifications” based on limestone (dolomite) – substances with the basic chemical formula СаСО3. In coal mines, a kind of stone dust with hydrophobic additives is used – stone hydrophobic dust (SHD).
In mines with intensive coal mining, several stages of applying stone dust are carried out. Primary rock dusting is carried out in a dead-end face immediately after tunneling 10-20 m of mine workings, then “secondary” and “fine-jet” rock dusting of drifts is carried out in the process of working out the extraction pillar. Fine-jet rock dusting is used, in particular, in the coal mines of Australia. Rock dusting is performed using a wide range of pneumatic and mechanical devices [19, 29].
Practical experience shows that the use of stone dust does not have a significant negative impact on occupational health issues. The main components of stone dust (СаСО3 and hydrophobic additives of natural origin) are environmentally safe. At the same time, the high density of stone dust and sufficiently high humidity in the workings provide an insignificant effect of “re-dusting” due to the movement of personnel or vehicles along the rock dusting of mine workings. The bulk density of stone dust γst.d = 1.156 g/sm3, and a similar indicator for coal dust of various dispersion degrees γcoal.d ranges from 0.238 g/sm3 for size particles of ≤ 20 microns and increases to 0.754 g/sm3 for size particles of 220 microns and more.
Engineering and technical workers of work sites and ventilation services, after carrying out the rock dusting of mine workings, carry out equipment quality control of the work performed every shift. The percentage of non-combustible substances in the formed mixture of coal and stone dust (such a mixture is called “coal-limestone”) is determined and compared with the norm of rock dusting N necessary to ensure dust and explosion safety.
Radioisotope, optical and chemical methods are among the traditional methods of monitoring the state of dust and explosion safety of mine workings [6, 7, 16].
Devices with a radioisotope principle of operation include environmentally harmful radioactive elements and are used in limited quantities, mainly in laboratory design (as an example, the device “Pylox” of the company “EMAG”, Poland).
Optical quality control devices for mine workings have found wide application in foreign coal industry (in the mines of the USA, Australia, Poland). For example, devices “Fotopylox” by “EMAG”, “CDEM-1000” produced by “Sensidyne LP” (USA) and a number of others. The optical principle of determining the content of stone additives in mine dust is based on the difference in the color of dust mixtures. An increase in the concentration of white limestone dust in the “coal-limestone” mixture increases its reflective light ability. One of the most successful optical devices in practice is the CDEM-1000 (Fig.1). The device contains hardware and software components, with the help of which measurements and “intelligent” analysis of the results are carried out. Mine workers receive a final conclusion on the state of explosion hazard: “dangerous” – “RED” or “explosion-proof” – “GREEN”. In terms of overall weight indicators, CDEM-1000 is comparable to a mobile phone – the weight of the device is 230 g, dimensions are 14 × 62 × 32 mm [16]. CDEM-1000 makes it possible to determine the rock dusting of mine workings and assess their dust and explosion safety, taking into account the requirements of industrial safety in US coal mines [29, 34]. According to these requirements, the content of non-combustible substances in dust samples on a fresh air jet should be at least 65 %, and on an outgoing jet – at least 80 %. Every 0.1 % of the methane content in the mine atmosphere increases the rate of rock dusting by 1 % on the fresh jet and by 0.4 % on the outgoing air jet [34].
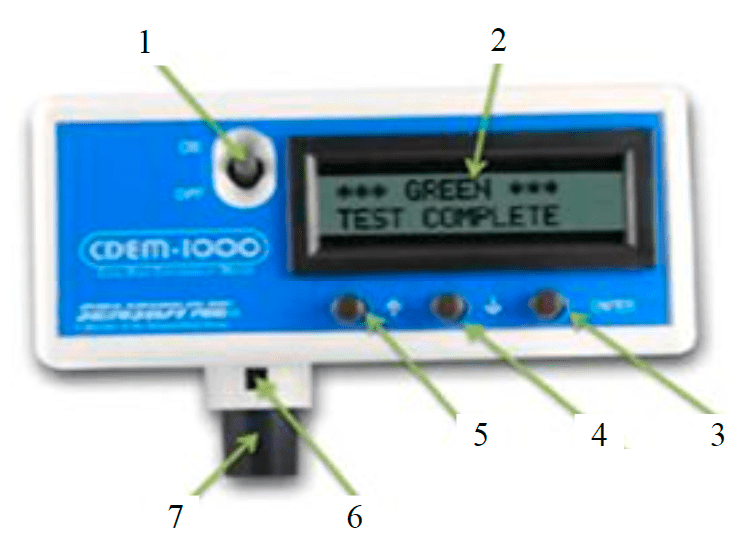
Fig.1. The front panel of the coal dust explosibility device “CDEM-1000” [16] 1 – power button; 2 – display; 3 – “enter” button; 4 and 5 – cursor up and down buttons; 6 – dust container; 7 – optical element
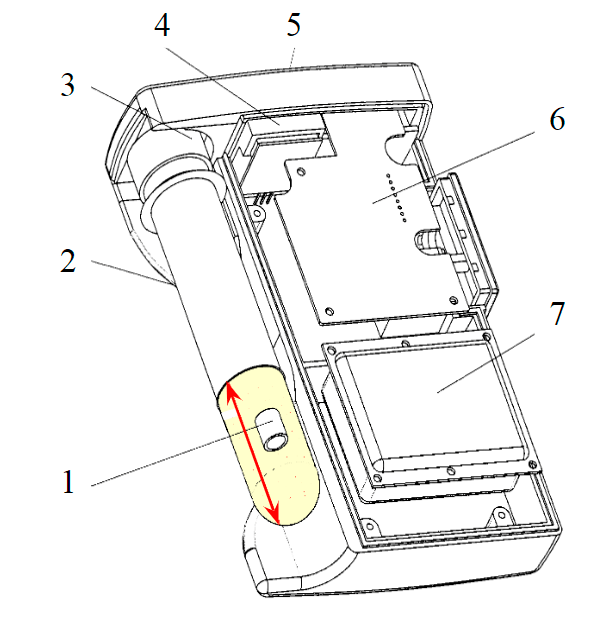
Fig.2. The “PKP”device [6] 1 – dust sample container; 2 – battery; 3 – gas flow sensor; 4 – sealer; 5 – a flask with a chemical reagent; 6 – computing unit; 7 – control panel
In devices with a chemical principle of action, the decomposition reaction of natural substances (dolomite, limestone) is realized when they interact with one of the acids (citric С6H8O7, hydrochloric HCl, etc.) [6, 7].
The decomposition of limestone by citric acid is accompanied by the release of CO2:
According to the reaction (1), about 22.5 liters of CO2 is released from 100 g (or 1 mol) of calcium carbonate at a temperature of 15-20 °С. In the coal industry of Russia, a device for monitoring the dust and explosion safety of mine workings “PKP” is used, based on the chemical principle of action, produced by the company “Gorniy-TSOT” (Fig.2).
For these devices, when the volume of the dust sample container is about 1 cm3, the volume of carbon dioxide released is different (depends on the CaCO3 content) and can reach 0.5 liters, which is enough to implement the process of its control. The PKP device has a calibration dependence “CO2 consumption – СаСО3 percentage”, on the basis of which the microprocessor determines the content of stone dust in the selected sample. The PKP device is compact (170 × 120 × 50 mm), weight 0.6 kg. The duration of one measurement is 10 min, however, an “idle measurement” and duplication of measurements are required, while a reliable result is obtained for at least 20-30 min.
Therefore, in the devices used in Russia and abroad to assess the state of dust and explosion safety of mine workings at coal mines, despite their advantages, as well as small overall dimensions and weight, a number of disadvantages can be identified: periodic replacement of expensive optical sensors; the use of consumables (desiccant, reagents) that require timely replacement and disposal; duplicate “idle” measurements; high measurement error (at least 10 %); calibration of equipment after a relatively small number of measurements.
Taking into account the above, as well as on the basis of high levels of risk of dust-methane-air mixtures explosions in coal mines (the severity of the explosion consequences multiplied by the probability of an event) [8, 13, 14], the development of a new method for assessing the quality of dust and explosion safety of mine workings is of interest from both practical and scientific points of view.
Methodology
The thermogravimetric method for determining the percentage of stone dust is a new control method [5], obtained on the basis of studies of thermal decomposition of energy [17, 21, 30] and coking coals of grades “G”, “D”, “Zh”, “K” without admixtures of stone dust [2, 4, 9], the study of thermal degradation of “pure” limestone and “coal-limestone” mixtures in various proportions [12, 18]. In accordance with the requirements of GOST R 53293-2009 “Fire hazard of substances and materials. Materials, substances, and means of fire protection. Identification by thermal analysis methods” the following methods are used as an instrumental method for identifying “coal-limestone” mixtures: thermogravimetric (TG); thermogravimetric by derivative (DTG).
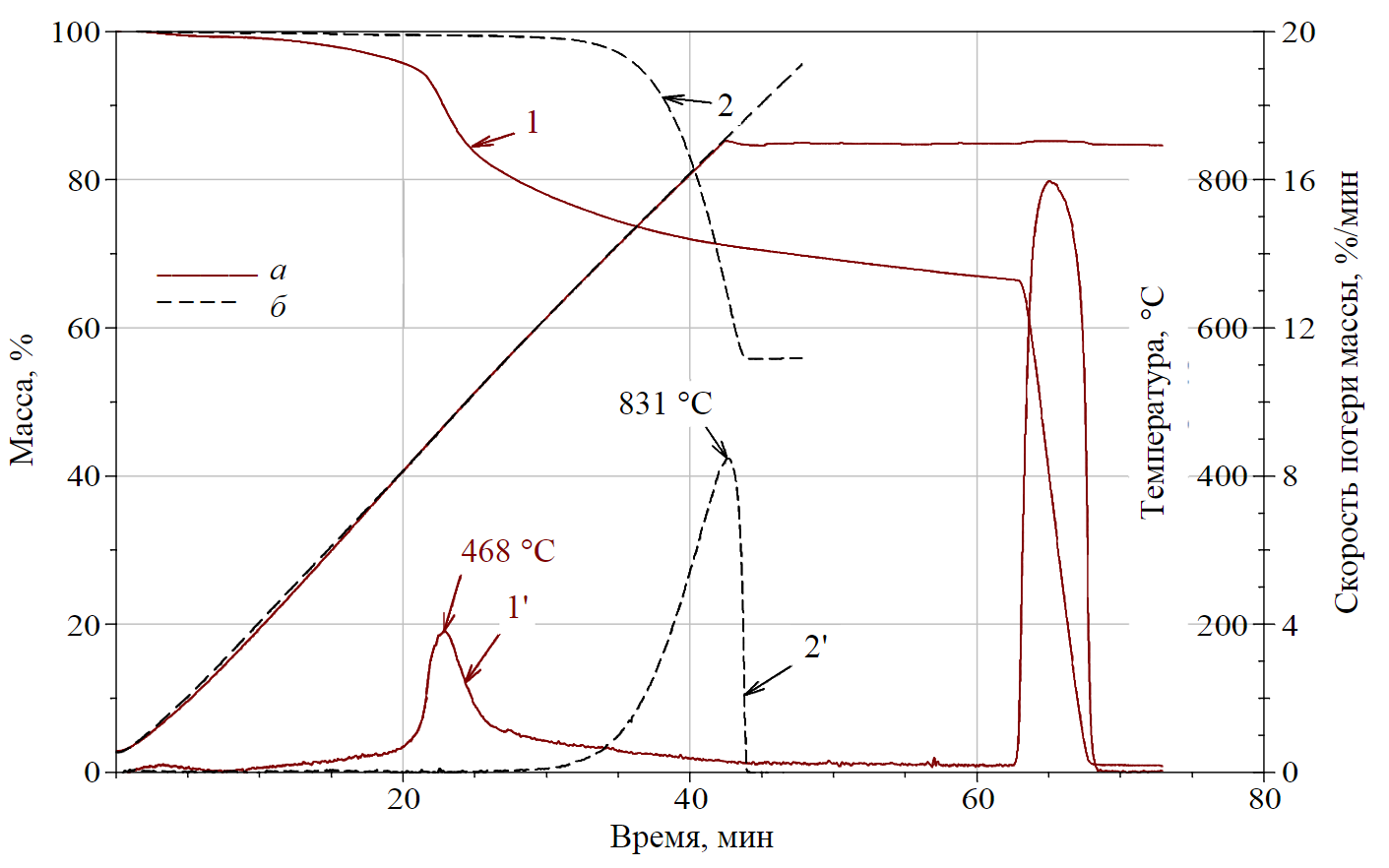
Fig.3. Thermogravimetric curves of samples of coal grade “Zh” fraction 125 microns (a) and limestone (chalk) (b) 1 – TG curve for coal; 2 – TG curve of limestone; 1' – DTG curve of coal; 2' – DTG curve of limestone
The essence of the thermogravimetric method consists in obtaining thermogravimetric TG and DTG curves for “coal-limestone” mixtures in known proportions (for example: 50/50 %; 25/75 %, etc.), as well as for pure stone dust, taken as a conditional mixture of “0 % coal and 100 % limestone”. Based on the analysis of characteristic points of thermogravimetric curves, calibration curves
are constructed that allow identification of a mine dust sample with an unknown percentage of
“coal-limestone” [12, 35].
The method was tested on metrologically certified laboratory equipment – thermoscales
“TGA-951”, included in the thermal analytical complex “DuPont-9900”. To study thermogravimetric processes, a compositional analysis was applied, based on the recommendations of the ASTM E 1131-2014 standard “Standard Test Method for Compositional Analysis by Thermogravimetry”.
The samples were heated in an inert atmosphere with a linear temperature increase from 20-30 to 850 °C at a speed of 20 °C/min. The duration of this mode was 45 min. Isothermal heating at a constant temperature of 850 °C was carried out for 20 min. The secondary combustion mode of carbon or coke residue in order to determine the percentage of ash in the sample took 20 min and provided for the change of an inert atmosphere to an oxidizing one (air). During the heating of the sample, its weighing was carried out and the loss of mass by the sample was recorded with a measurement frequency of 30 points/min. The dynamics of mass loss is represented by thermogravimetric curves (TC), the rate of mass loss or thermogravimetry by derivative is represented by DTG curves.
Discussion
The deposited coal dust in the mine, in relation to which the regulatory requirements for neutralizing its explosive properties (i.e., stone coal dust) are met, contains two main components – coal (with natural mineral additives – ash, moisture) and limestone (with insignificant hydrophobic additives). The comparison of thermogravimetric curves of these components carried out by the authors (Fig.3) shows that their thermal decomposition proceeds in practically non-overlapping temperature intervals. This provides significant opportunities for their identification.
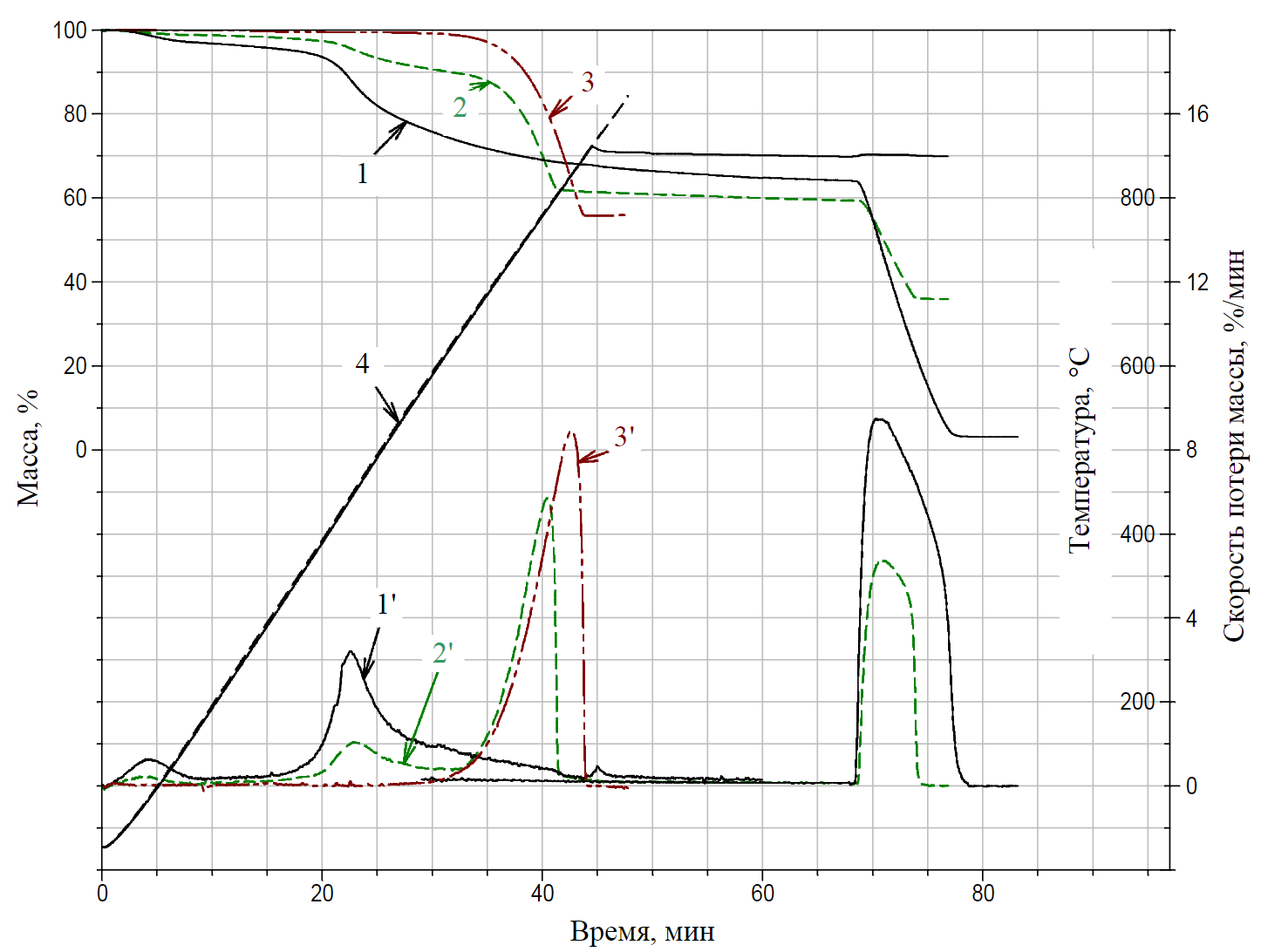
Fig.4. Thermogravimetric curves of samples N 1, 2, 5 1 – TG curve of sample N 1 (f0); 2 – TG curve of sample N 2 (f67); 3 – TG curve of sample N 5 (f100); 4 – temperature (Т,°С); 1' – DTG curve of sample N 1 (φ0); 2' – DTG curve of sample N 2 (φ67); 3' – DTG curve of sample N 5 (φ100)
Thus, the volatile matter yield from coal of grade “Zh” with a maximum particle size of 125 microns is represented as a one-stage reaction with a maximum rate of mass loss (volatile matter yield of organic components) at the temperature of 468 °C (Fig.3, curve 1'). The extrapolated temperatures of the beginning and end of the volatile yield process [10, 12] are equal to 400 and 575 °C, respectively. The volatile yield Vdaf for the considered grade of coal “Zh” with the specified dispersion was Vdaf = 28.8 %. Ash residue after final combustion in atmospheric air (67 min of heating in Fig.3) was A = 0.78 %. When industrial stone dust (without coal impurities) is heated, it is thermally stable to a temperature of ≈ 650 °С or up to 33 min of heating (Fig.3, curve 2'). In the process of further heating of stone dust (or its mixtures with coal) at temperatures above 650 °C, thermal decomposition of CaCO3 occurs, which has features at different concentrations of limestone.
If we denote the TG curve as a function of the change in mass over time М = f (t), then the proposed De Keyser W.L. thermogravimetry by derivative (dM/dt) expresses the rate of mass loss at the current time (DTG curve or φ (t):
In the study of coal-limestone mixtures, to distinguish the experimentally obtained TG and DTG curves, a lower index was introduced in the function f (t) and j (t), which indicates the percentage of limestone in the mixture, for example, f67 (t) and j67 (t) for a mixture with 67 % limestone. In general, the functions of mass loss (TG) and mass loss rate (DTG) are denoted as fх (t) and jх (t), respectively.
With a linear increase in temperature in thermoscales, the temperature value is determined at the current time by the dependence
where Т is temperature, °С; А is the rate of temperature increase, °С /min; t is time, min.
If the heating mode corresponds to condition (3), then temperature T and time t are related linearly and the functions fх and jх are represented in the coordinates “time – mass loss” (abscissa axis – time t, min) or “temperature – mass loss” (abscissa axis – Т, °С).
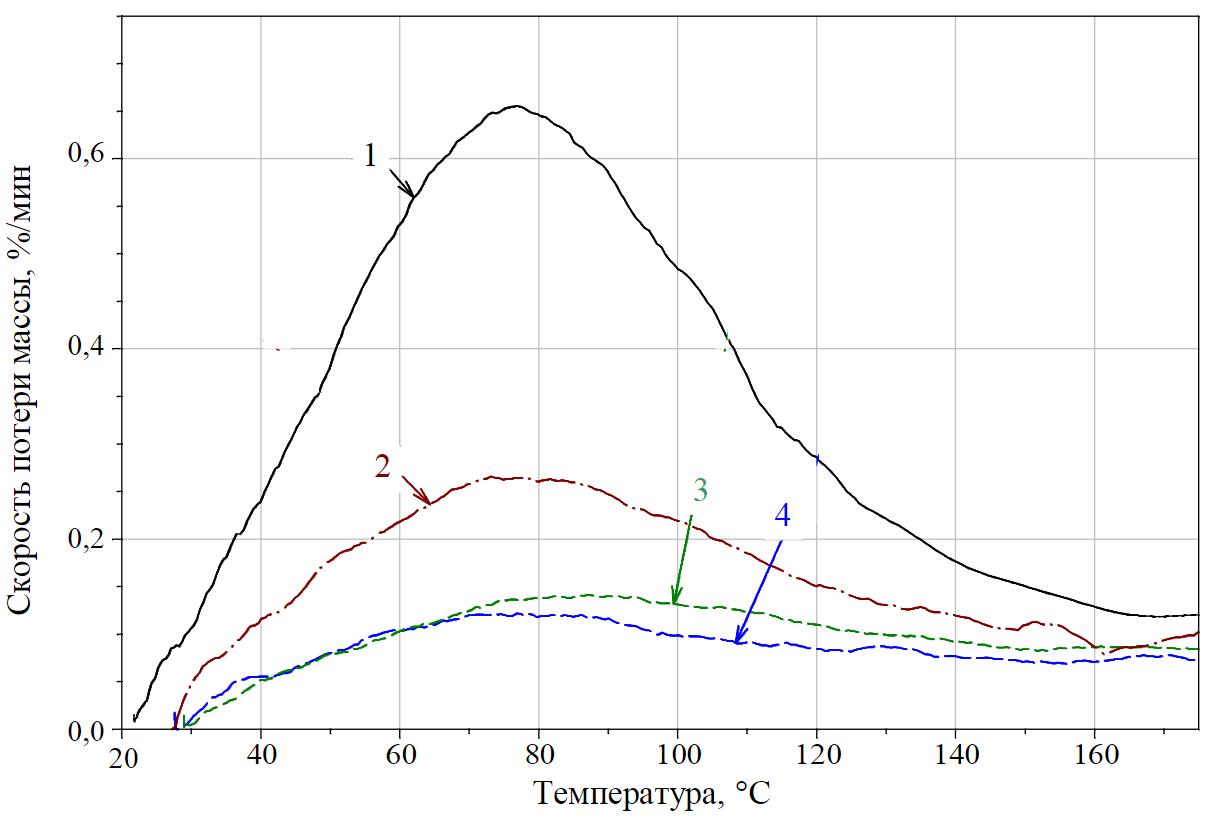
Fig.5. DTG curves of samples N 1-4 (moisture yield)
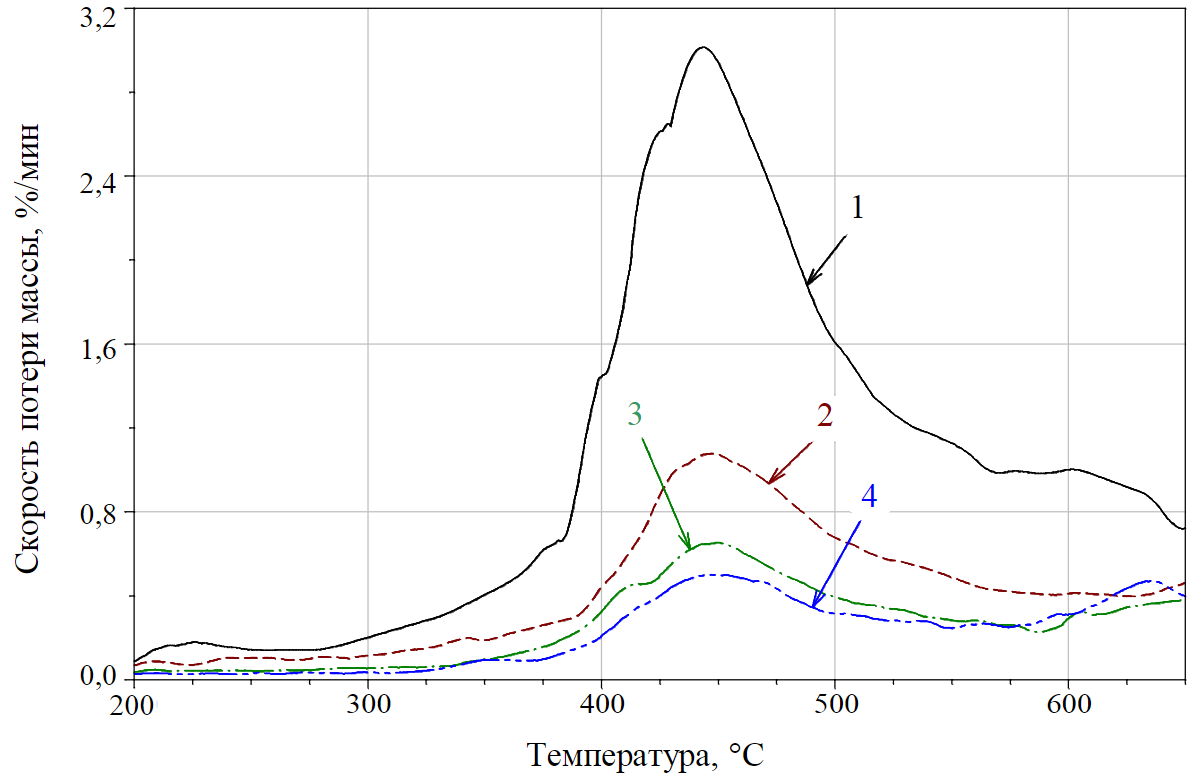
Fig.6. DTG curves of samples N 1-4 (volatile matter yield from coal)
The thermogravimetric method for determining the percentage of stone dust has been worked out on dust mixtures of coal and stone dust (Fig.4-7):
- sample N 1 (a mixture of the type “coal 100 % + limestone 0 %”) included coal grade “D” (curves f0and j0 were obtained from this sample);
- group of samples N 2, 3, 4 – mixtures of coal and stone dust in the following proportions: 33/67, 20/80, 15/85 %, respectively (curves f67and φ67; f80and φ80; f85and φ85);
- sample N 5 – stone dust or a conditional mixture of “0/100 %” (curves f100and φ100).
On the curves of the mass loss rate φ0, φ67, φ100 (Fig.4), three temperature stages of destruction can be distinguished (three local maxima at the 4th, 23rd and 40th minutes of heating):
- moisture yield W in the temperature range from 35 to 132 °C;
- the primary volatile matter yield from coal (without destruction of the core of macromolecules), the values of extrapolated temperatures of this reaction range [10, 12] are from 380 to 580 °C (for the function φ0) and from 400 to 575 °C (for the function φ67);
- the primary volatile matter yield from coal (without destruction of the core of macromolecules), the values of extrapolated temperatures of this reaction range [10, 12] are from 380 to 580 °C (for the function φ0) and from 400 to 575 °C (for the function φ67);
The details of these DTG curves for the three selected stages are shown in Fig.5-7.
As can be seen from Fig. 5, the extrapolated temperatures of the beginning and end of the moisture yield are 35-132°С, the extended range of moisture yield can be assumed within 25-150°С. At a temperature of 77-80 °C, the maximum rate of moisture yield from the samples is achieved. At the same time, the increase in the concentration of limestone (stone dust) in the coal-limestone mixture from 0 % limestone (curve 1) to 100 % (curve 4) is uniquely identified by dynamic thermogravimetry. The presence of hydrophobic additives reduces the moisture content, the value of the functions jх is inversely proportional to the increase in the concentration of stone dust (value x). Also, when moving from curve 1 to curve 4, the maximum rate of moisture output decreases from 0.73 (for the sample – coal 100 %) to 0.11 %/min (for the sample – SHD 100 %) and the total volume of moisture output Wx (areas of curves in the temperature range
25-170 °C) decreases proportionally.
Based on Fig.5, the moisture content in the sample is
where Мх (132°) and Мх (35°) – the mass of the sample at a heating temperature of 132 and 35 °C, respectively, mg; Мх (20°) – the mass of the sample before heating, mg.
The process of the volatile matter yield from coal is shown in Fig.6 (curves 1-4 correspond to mixtures with 100; 33; 20; 15 % coal dust grade “G”). In this range, the DTG curves reflect a proportional decrease in the maximum values of the mass loss rate of the samples (at Т ≈ 445 °С) with a decrease in the content of coal dust in the test sample. At the same time, the value of Т ≈ 445 °С, corresponding to the maximum volatile matter yield from coal, remains practically unchanged or weakly depends on changes in the concentration of coal in the mixture. The areas of the curves (or the integral in the temperature range of 380-540 °C) determine the value of the volatile matter yield Vd from dry dust (taking into account the moisture yield in the previous temperature range). Based on the regulatory requirements of GOST R 55660-2013 “Solid mineral fuel. Determination of the volatile matter yield”, determination of the volatile yield Vd makes practical sense only for a sample of coal dust without stone additives (or of the functions j0 and f0) [11]:
where М0 (20°), М0 (380°) and М0 (540°) – the mass of the coal dust sample without stone additives at a heating temperature of 20, 380 and 540 °C, respectively, mg.
Figure 7 demonstrates the main process for identifying coal and stone dust mixtures, namely the decomposition of the most heat–resistant component of the mixture – calcium carbonate СаСО3. With an increase in the content of inert dust from 67 to 100 %, a proportional change in the temperature of the most intense decomposition occurs from Тmax(67 %) = 780 °С to Тmax(100 %) = 835 °С. This makes it possible, for a certain brand of coal and a fixed brand of stone dust, to construct an unambiguous function of the concentration of stone dust in the mixture C from the Тmax parameter determined experimentally. At the same time, the integration of the DTG curves (mass loss rate) in the temperature range from 650 to 850 °C allows to obtain the value of the mass of carbon dioxide released from a mixture of coal and stone dust
where М (650º) and М (850º) – the mass of the sample at a heating temperature of 650 and 850 °C, respectively, mg.
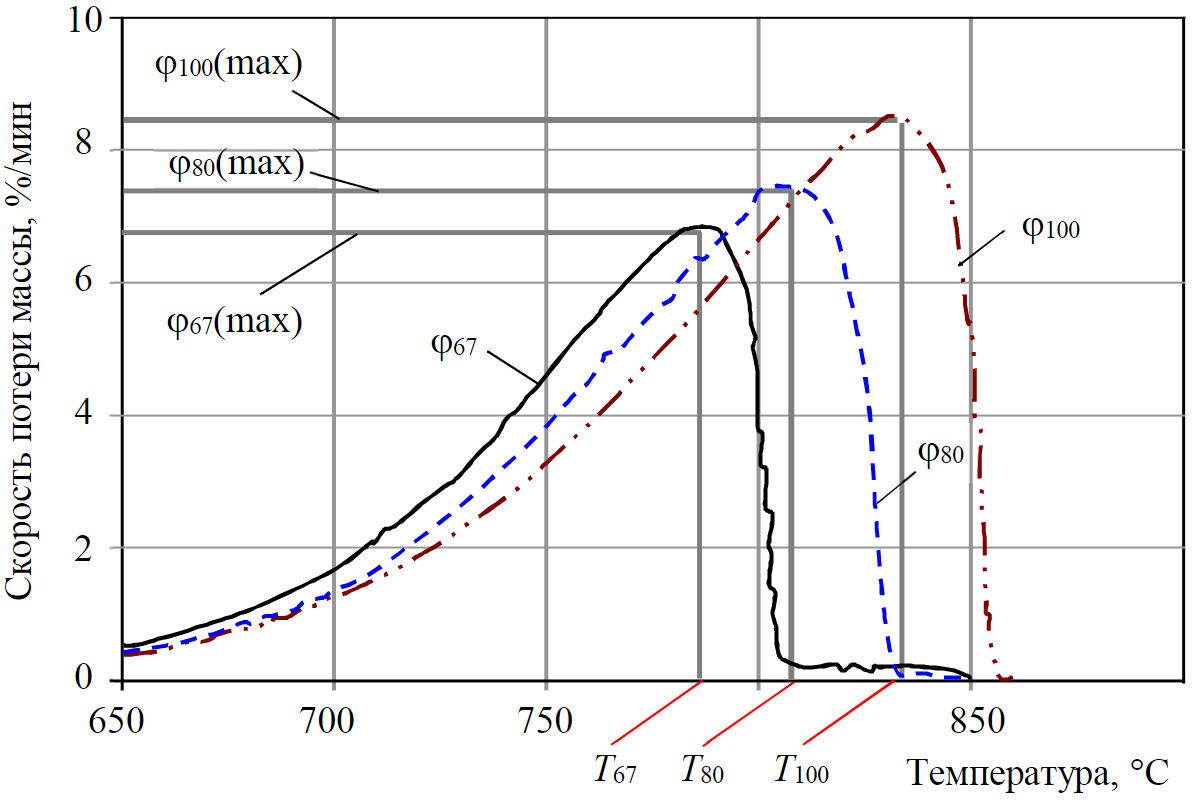
Fig.7. DTG of samples N 2, 3, 5 (destruction of CaCO3 with CO2 yield)
If the mass of carbon dioxide released from the mine dust sample is known, then based on the ratio of the molecular weights of CaO and CO2, the mass of CaCO3 in the sample of the analyzed mine dust will be
Based on the ratio of the initial mass of the sample М0 (before heating) and the mass of calcium carbonate Mls, determined by the formula (7), the content of stone dust in the sample can be determined:
In addition to the calculation method for determining the content of stone dust in a sample based on its thermal decomposition according to formula (8), the characteristic points of the TG and DTG curves provide extensive information for obtaining calibration curves (for example, “moisture content W – content of stone dust C”, “maximum rate of decomposition of limestone in the sample jх-max – content of stone dust C”, etc.). Based on the obtained calibration curves, it is possible to obtain the required parameter C [5].
Consideration of the stage of calcium carbonate decomposition in the coordinates “mass M – time t” (see Fig.4) allows to conclude that there is a functional relationship between the total time of thermal decomposition of the sample and the content of stone dust additives in it. The decomposition time for sample N 5 (100 % inert dust) is maximum – td.f(100) = 44 min (see Fig.4, curve 3'), a decrease in the concentration of СаСО3 to 67 % (see Fig.3, curve 2') leads to a decrease in the value of td.f(67) to 41 min, and the extrapolated value of td.f(0) is 27 min. The thermogravimetric method, based on the dependence of the total decomposition time of the sample on the concentration of the CaCO3 additive in it, has been patented and practically worked out for two main groups of explosion-hazardous coals: coking (Vorkutinskaya and Severnaya mines of Vorkutaugol JSC) and energy (S.M.Kirov,
A.D.Ruban mines and Mine Management Taldinskoye of SUEK-Kuzbass JSC) [5].
Conclusion
The processes of thermogravimetric decomposition of samples of coal and stone dust mixtures make it possible to obtain a significant amount of information about the composition of the sample, represented in the form of thermogravimetric curves (TG and DTG). The characteristic points of the TG and DTG curves make it possible to determine the content of stone dust C in several mutually clarifying ways. The content of C can be defined as a function:
- mass or volume of released СО2;
- the maximum CO2 flow rate or the maximum CO2 yield temperature (dynamic heating methods – three ways of processing data on characteristic points of the process);
- total humidity of a mixture of coal and inert hydrophobic dust;
- the total time of thermal decomposition of the sample under dynamic or quasi-static heating.
The process of thermal decomposition of coal-limestone mixtures is characterized by three main non-overlapping reaction intervals: 35-132 °С – moisture yield from the sample; 380-580 °С – volatile matter yiled from coal while maintaining the thermal stability of calcium carbonate (the upper limit of the interval can increase to 650 °С with a two-stage nature of the destruction of fine coal dust); 650-850 °С – thermal degradation of СаСО3 with СО2 yield. In these intervals, a local maximum of the mass loss rate of the sample (or the maximum rate of thermal degradation) is achieved, corresponding to temperatures of 77-80 °С (maximum moisture yield intensity); 415-425 °С (maximum volatile matter yield from coal of various stages of metamorphism); 770-832 °С (maximum CO2 yield rate during limestone decomposition, coal dust additives have a significant effect on this value, reducing the value from 832 °С at 100 % СаСО3 to 770 °С for a mixture of 60 % СаСО3 and 40 % coal dust).
Additives of stone dust lead to significant changes in the process of thermal decomposition of coal-limestone mixtures. Due to hydrophobic additives in stone dust, there is a significant decrease in moisture in the mixture and at the initial stage of heating (up to 130-132 °C), its yield decreases from 2.7-4.0 % (100 % coal dust) to 0.35 % (85 % SHD and 15 % coal).
The total volatile matter yield from coal in stone dust decreases significantly with the increase in the amount of CaCO3 additives. At the same time, the functional dependence of the maximum volatile yield rate (at a temperature of 415-425 °C) on the content of stone dust is close to linear.
The process of thermal decomposition of an inert additive (CaCO3) takes place in the temperature range above 650°С. Since the main yield of combustible gases from coal dust is completed by 95-98 % at a lower temperature (up to 580°С), only carbon dioxide from thermally decomposing limestone is released in the heating region > 650 °С. Monitoring the CO2 release makes it possible to reliably determine the mass of limestone in the analyzed sample and, accordingly, its percentage in the mine dust sample under study.
The thermogravimetric method for assessing the rock dusting of mine workings, worked out on standard laboratory equipment for energy and coking coal grades, is an operational method, the processing time of one sample is 5-7 min (for conditions of thermoscales of the TGA-951 type). The relative error in determining parameter C does not exceed 2.5 %. The main advantages of the thermogravimetric method include: the absence of expensive optical sensors with a system for recognizing the intensity of reflected light or environmentally harmful radioactive elements, the complete absence of consumable or replaceable materials for each measurement (special drying mixtures for optical control devices or chemical reagents with replaceable containers for chemical reactions – in relation to devices using the PKP type chemical method)).
References
- Gryzunov V.V., Pekarchuk D.S. Qualitative analysis of traumatism structure in coal mines. Gornyi Zhurnal. 2017. N 10, p. 61-64. DOI: 10.17580/gzh.2017.10.13
- Zhiharev S.Y., Pikhkonen P.V., Rodionov V.A. Research of Fire and Explosion Hazardous Properties for Hard Coal at the Prokopyevsk Coal Field of the Kuznetsk Coal Basin. News of the Tula state university. Sciences of Earth. 2017. N 3. p. 84-93 (in Russian).
- Katsubin A.V., Kovshov S.V., Ilyashenko I.S., Marinina V.M. Study of Organic Compounds for Reduction of the Aerotech-nogenic Load From the Coal Mines Highways. Occupational Safety in Industry. 2020. N 1, p. 63-67. DOI: 10.24000/0409-2961-2020-1-63-67 (in Russian).
- Maryandyshev P.A., Chernov A.A., Lyubov V.K. Thermogravimetric and Kinetic Investigations of Peat and Hydrolytic Lignine. Mezhdunarodnyi zhurnal eksperimentalnogo obrazovaniya. 2014. N 12, p. 20-27 (in Russian).
- Romanchenko S.B., Naganovskii Yu.K., Gubina E.A., Vdovina V.V. Patent N 2747022 RF. Thermogravimetric method for assessing the roadstone dusting quality of mine workings. Publ. 23.04.2021. Bul. N 12.
- Voroshilov S.P., Voroshilov Ya.S., Sedelnikov V.E. et al. Patent N 138693 RF. A device for assessing the roadstone dusting quality of mine workings. Publ. 20.03.2014. Bul. N 8.
- Trubitsyn A.A., Voroshilov S.P., Trubitsyna N.V., Voroshilov Ya.S. Patent N 2249816 RF. A method for assessing the preventive treatment quality of coal dust deposits. Publ. 10.04.2005. Bul. N 10.
- Peich L.M., Torrent K.G., An’ez N.F., Eskobar K.-M.M. Prevention and protection against propagation of explosionsin underground coal mines. Journal of Mining Institute. 2017. Vol. 225, p. 307-312. DOI: 10.18454/PMI.2017.3.307
- Rodionov V.A., Pikhkonen L.V., Zhikharev S.Ya. Dispersion of the G-type coal dust of the Vorgashorskoe field and its influ-ence on the thermal destruction process. Perm Journal of Petroleum and Mining Engineering. 2017. Vol. 16. N 4, р. 350-356. DOI: 10.15593/2224-9923/2017.4.6 (in Russian).
- Romanchenko S.B., Devlikanov M.O. Volatile Substances Emission from Coal Dust Dynamics Study by Methods of Thermogravimetric Analysis. Industrial Safety. Scientific-technical magazine. 2019. N 4, p. 23-30 (in Russian).
- Smirnyakov V.V., Smirnyakova V.V. Unhandy factors in statistics of accidental gas and dust explosions in coal mines in Russia. Gornyi Zhurnal. 2016. N 1, p. 30-34. DOI: 10.17580/gzh.2016.01.07 (in Russian).
- Romanchenko S.B., Gubina E.A., Ushakov D.V., Naganowskiy Yu.K. Thermogravimetric Analysis of Coal Dust and Inert Additives in Dust and Explosion Protection Systems. Industrial Safety. Scientific-technical magazine. 2020. N 2, p. 13-21 (in Russian).
- Yuan-Pan Zheng, Chang-Gen Feng, Guo-Xun Jing et al. A statistical analysis of coal mine accidents caused by coal dust ex-plosions in China. Journal of Loss Prevention in the Process Industries. 2009. Vol. 22. Iss. 4, p. 528-532. DOI: 10.1016/j.jlp.2009.02.010
- Smirnyakov V.V., Smirnyakova V.V., Pekarchuk D.S., Orlov F.A. Analysis of methane and dust explosions in modern coal mines in Russia. International Journal of Civil Engineering and Technology. 2019. Vol. 10. Iss. 2, p. 1917-1929
- Breslin J.A. One Hundred Years of Federal Mining Safety and Health Research. U.S. Department of Health and Human Ser-vices, Centers for Disease Control and Prevention, National Institute for Occupational Safety and Health. 2010. Vol. 128, p. 98.
- CDEM1000 Coal Dust Explosibility Meter Coal Dust Explosion URL (date of access 03.06.2021).
- da Silva Filho C.G., Milioli F.Ed. Thermogravimetric Analysis of the Combustion of a Brazilian mineral Coal. Quimica Nova. 2008. Vol. 31. N 1, p. 98-103. DOI: 10.1590/S0100-40422008000100021
- Dunayevska N., Zasiadko Y., Shchudlo T. Thermal destruction kinetics of coal and solid biomass mixtures. Ukrainian Food Journal. 2018. Vol. 7. Iss. 4, p. 738-753. DOI: 10.24263/2304-974X-2018-7-4-17
- Fiscor S. Innovative rock-dusting system to assist with respirable dust compliance. Coal Age. 2015. Vol. 120. N 10, p. 38-39.
- Harris M.L., Sapko M.J. Floor dust erosion during early stages of coal dust explosion development. International Journal of Mining Science and Technology. 2019. Vol. 29. Iss. 6, p. 825-830. DOI: 10.1016/j.ijmst.2019.09.001
- Heydari M., Rahman M., Gupta R. Kinetic Study and Thermal Decomposition Behavior of Lignite Coal. Hindawi Publishing Corporation International Journal of Chemical Engineering. 2015. Vol. 2015. N 481739. DOI: 10.1155/2015/481739
- Kabanov E.I., Korshunov G.I., Magomet R.D. Quantitative risk assessment of miners injury during explosions of methane-dust-air mixtures in underground workings. Journal of Applied Science and Engineering. 2020. Vol. 24. Iss. 1, p. 105-110. DOI: 10.6180/jase.202102_24(1).0014
- Kornev A.V., G Korshunov.I., Kudelas D. Reduction of Dust in the Longwall Faces of Coal Mines: Problems and Perspec-tive Solutions. Acta Montanistica Slovaca. 2021. Vol. 26. Iss. 1, p. 84-97. DOI: 10.46544/AMS.v26i1.07
- Kurnia J.C., Kurnia J.C., Sasmito A.P., Mujumdar A.S. Dust dispersion and management in underground mining faces. International Journal of Mining Science and Technology. 2014. Vol. 24. Iss. 1, p. 39-44. DOI: 10.1016/j.ijmst.2013.12.007
- Magomet R.D., Rodionov V.A., Soloviov V.B. Methodological approach to issue of researching dust-explosion protection of mine workings of coal mines. International Journal of Civil Engineering and Technology. 2019. Vol. 10. Iss. 2, p. 1154-1161.
- Maier P., Hartlieb P., Brune J.F. Laboratory Scaled Coal Dust Explosions and Physical Test Results for CFD Explosion Models. Berg Huettenmaenn Monatsh. 2020. Vol. 165. Iss. 6, p. 265-269. DOI: 10.1007/s00501-020-00985-0
- Yueze L., Saad A., Sasmito A.P., Kurnia J.C. Prediction of air flow, methane, and coal dust dispersion in a room and pillar mining face. International Journal of Mining Science and Technology. 2017. Vol. 27. Iss. 4, p. 657-662. DOI: 10.1016/j.ijmst.2017.05.019
- Cao Weiguoa, Huang Liyuana, Zhang Jianxin. Research on characteristic parameters of coal dust explosion. Procedia Engi-neering. 2012. Vol. 45, p. 442-447. DOI: 10.1016/j.proeng.2012.08.183
- Harteis S.P., Alexander D.W., Harris M.L. et al. Review of Rock Dusting Practices in Underground Coal Mines. U.S. De-partment of Health and Human Services, Centers for Disease Control and Prevention, National Institute for Occupational Safety and Health, 2017. Vol. 101, p. 97.
- Samih S. Thermogravimetric analysis and kinetics of coal. The Canadian Jornal of Chemical Engineering. 2018. Vol. 96. Iss. 10, p. 2144-2154. DOI: 10.1002/cjce.23198
- Shulei Shi, Bingyou Jiang, Xiangrui Meng. Assessment of gas and dust explosion in coal mines by means of fuzzyfault tree analysis. International Journal of Mining Science and Technology. 2018. Vol. 28. Iss. 6, p. 991-998. DOI: 10.1016/j.ijmst.2018.07.007
- Soloviov V.B., Magomet R.D. The ways of safety improvement during the outburst-prone and gas-bearing coal seams development. Journal of Industrial Pollution Control. 2017. Vol. 33 N 1, p. 1042-1047.
- Thakur P. Advanced Mine Ventilation Respirable Coal Dust Combustible Gas and Mine Fire Control. Advanced Mine Ventilation. Woodhead Publishing, 2019, p. 377-398. DOI: 10.1016/B978-0-08-100457-9.00023-7
- Title 30. Mineral Resources. Vol. 1. Parts 1-199. Washington: U.S. Government Printing Office. 2009, p. 767. URL (date of access 03.06.2021).
- Tolvanen H., Kokko L., Raiko R. Fast pyrolysis of coal, peat, and torrefied wood: Mass loss study with a drop tube reactor, particle geometry analysis, and kinetics modeling. Fuel. 2013. Vol. 111, p. 148-156. DOI: 10.1016/j.fuel.2013.04.030