Study on hydrometallurgical recovery of copper and rhenium in processing of substandard copper concentrates
- 1 — Ph.D. associate professor Saint Petersburg Mining University ▪ Orcid ▪ Elibrary ▪ Scopus
- 2 — Postgraduate Student Saint Petersburg Mining University ▪ Orcid
Abstract
Over the past decade, there has been a steady growth in demand for rare metals, with rhenium being one of the most highly demanded, but also one of the most expensive and difficult to obtain. The high demand for rhenium is due to its use as a key component of metallurgical alloys or as a component of catalysts used in the oil refining industry. The aggregate of facts causes profitability of processing of the rhenium-containing mineral resources, which also are the copper substandard concentrates obtained at processing of the Zhezkazgan sandstones. The study focuses on the processes of extraction of copper and sorption recovery of rhenium from solutions of ammonia leaching of copper substandard concentrates. Model solutions similar in the elemental composition to solutions of ammonia leaching solutions of copper substandard concentrates obtained during the processing of Zhezkazgan sandstones were used as an object of the study. The paper estimates extraction characteristics of copper recovery using LIX 84-I solution in kerosene, as well as sorption characteristics of the rhenium recovery process using the Purolite PPA100 anion exchanger. Based on the obtained characteristics the possibility of hydrometallurgical processing of ammonia leaching solutions of substandard copper-sulfide concentrates, and recovery of the obtained commercial products is shown.
Introduction
From the viewpoint of mining and production, rhenium can be considered the most scarce rare metal [12], its average concentration in the Earth crust is 7∙10–8 % [30]. Total world reserves of rhenium are estimated at 13000 t [1]. In the Russian Federation, rhenium is regarded as a metal associated with uranium, copper-pyrite and copper-molybdenum ores [21].
On the territory of the Russian Federation, state balance reserves of rhenium include three copper-molybdenum, two copper-porphyry, one tungsten-molybdenum and one rhenium deposit – Briketno-Zheltukhinskoe [4].
Rhenium fumarole mineralizations of the Kuril Islands volcanoes are considered off-balance but quite promising [28]. According to geological estimates, rhenium concentration in the emissions of the most famous volcano – Kudryavy – can reach 5 g/t.
In the USSR, rhenium production reached 10 t/year, and the main raw materials were molybdenum concentrates from Kazakhstan. Nowadays, supplies of these concentrates have been discontinued, and the metal is being recovered from secondary raw materials and technogenic rhenium-containing wastes of copper production, the amount of which is comparable to the resources of previously mentioned balance deposits [16, 18].
From the technological viewpoint, the interest in rhenium is primarily explained by its properties. The metal is characterized by a high melting point, thermal resistance and a combination of ductility in a free state and hardness after cold working. Due to these properties, rhenium is used in special-purpose high-melting and heat-resistant alloys [9, 28]. Moreover, its chemical affinity with platinum enables the use of rhenium at petrochemical plants as a component of oil cracking catalysts, which reduces platinum consumption [26]. Due to high rhenium prices, its limited production and availability, there is a constant search for its alternatives. For example, in order to avoid using rhenium throughout the entire volume of the alloy, during production the edges and end tips of the blades are only coated with a layer of rhenium alloys. Rhenium is also used as a composite or structural material. The dynamics of its average annual prices and production volumes is presented in Fig.1 [10].
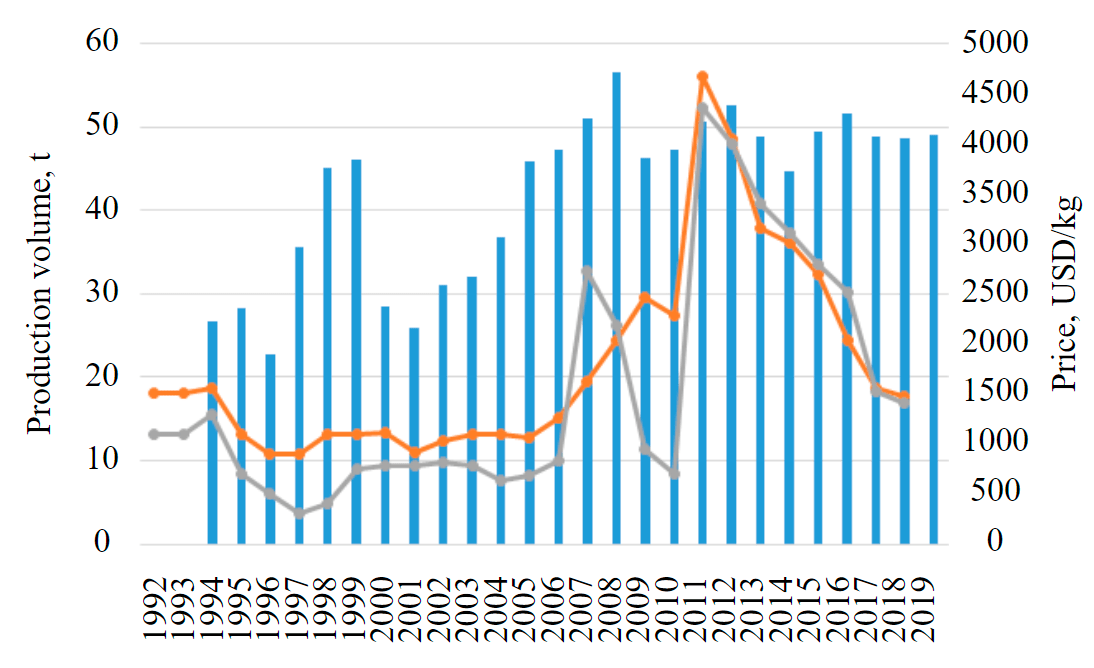
Fig.1. Dynamics of global rhenium production and prices of metallic rhenium and ammonium perrhenate [10] 1 – global production; 2 – ammonium perrhenate, USD/kg; 3 – metallic rhenium (content of 99.99 %), USD/kg
Metallurgical industry annually produces about 100 million tons of rhenium-containing slag, suitable for further processing [3, 4]. The share of copper-smelting production accounts for more than 10 million tons of slag [14]. Under the circumstances, large copper smelters develop technologies to integrate their own waste in the process chains [35]. With regard to substandard copper concentrates, one of the most promising technologies of processing is the hydrometallurgical method, which includes the stages of leaching, copper extraction recovery and subsequent sorption recovery of valuable trace elements, such as rhenium [15].
According to this method, process solution obtained after ammonia leaching of substandard copper concentrates is sent to the stage of copper extraction recovery, after which sorption methods are used to recover perrhenate from the depleted solution [2, 8, 11]. To develop an effective industrial technology, it is necessary to specify operational parameters of the described processes [6, 31].
The processes of copper extraction and rhenium sorption from model solutions of processing substandard copper concentrates have been examined [32]. Estimations have been performed for extraction characteristics of copper recovery using LIX 84-I extractant [25] and sorption characteristics of rhenium recovery using Purolite PPA100 sorbent [23]. The efficiency of these processes in copper and rhenium recovery from ammonia solutions of complex salt composition has been demonstrated [11, 17, 29].
Methodology
Extraction and sorption recovery was performed from ammonia solutions, the composition of which modeled solutions obtained during ammonia leaching of substandard copper concentrates. The model leaching solution contained 20 g/dm3 of Cu, 60 g/dm3 of
In the study of extraction processes, we used the solution of chelating extractant LIX 84-I in kerosene [13], which had proved effective at several plants and was approved for processing copper sulfide concentrates and ores [19, 24]. Extractant solutions of the required concentration were prepared by diluting the calculated aliquot of LIX 84-I in chemically pure kerosene.
In the course of the study, we obtained dependencies of copper recovery rate from model solutions, associated with the ratio of aqueous and organic phase volumes and concentration of LIX 84-I extractant in kerosene.
In the course of the study, we obtained dependencies of copper recovery rate from model solutions, associated with the ratio of aqueous and organic phase volumes and concentration of LIX 84-I extractant in kerosene.
To study the processes of rhenium sorption, Purolite PPA100 anion exchanger in the hydroxyl form was used as a sorbent [20]. The model solution was similar. The process was studied under static conditions as follows: an aliquot of the model solution was sampled into a 100 ml conical flask and a required volume of anion exchanger was added. The flask was closed with a rubber cork and stirred for a defined period in a thermostated system at a stirring rate of 400 rpm. After the sorption, the solution was separated from anion exchanger by means of a glass filter with a porosity of 160 μm. The anion exchanger was sent to regeneration, while the equilibrium solution was analyzed for the content of anions.
To determine the sorption characteristics, adsorption isotherms of perrhenate ions on this ion exchanger were obtained [23] and described by the linear form of the Langmuir isotherm equation, from which the capacity of adsorption monomolecular layer (G∞) and the adsorption equilibrium constant (K) were derived. To determine the kinetic characteristics of ion-exchange sorption, a kinetic dependence of anion exchanger saturation rate during the sorption of perrhenate ions from the model product solution was obtained, which was used to estimate the constant of ion-exchange adsorption rate (k), half-time of the exchange (τ1/2) and diffusion coefficient of perrhenate ions in the ion exchanger phase .
Exact concentration of the extractant was specified by means of infrared spectroscopy; copper concentrations in the aqueous and organic phases before and after extraction were determined by X-ray fluorescence analysis on an Epsilon 3 spectrometer [34] and confirmed by titration; the concentration of perrhenate ions in the aqueous phase during sorption was estimated by X-ray fluorescence analysis and confirmed photometrically on a Unico photometer [27, 33].
Obtained results and discussion
In the course of the experiment, measurement data were obtained on the extraction of copper from model ammonia leaching solutions of substandard copper concentrates using LIX 84-I extractant and the sorption of perrhenate ions on the Purolite PPA100 ion exchanger. Extraction was carried out under thermostated conditions at a constant temperature of 25 °C.
The effect that the ratio of phase volumes had on copper recovery rate was studied – the results of the experiment are presented in Table 1.
Table 1
The influence of the volume ratio of aqueous and organic phases on copper extraction ratewhen using undiluted LIX 84-I extractant
Ratio of phase volumes, Vorg:Vaq |
Molar concentration of copper in the aqueous phase after extraction Caq |
Molar concentration of copper in the extractant after extraction Сe |
Rate of copper recovery into the extractant E, % |
2:1 |
0,000 |
0,223 |
100,00 |
1:1 |
0,000 |
0,446 |
100,00 |
1:2 |
0,145 |
0,602 |
67,54 |
1:4 |
0,280 |
0,661 |
37,11 |
1:8 |
0,339 |
0,849 |
23,81 |
It can be seen from Table 1 that the rate of copper recovery from the ammonia solution into the extractant sharply decreases with an increase in the volume of the aqueous phase above the ratio Vorg:Vaq = 1:1. Increasing the volume of the organic phase above this value will not have any positive effect on the extraction process.
Experiment results demonstrating the influence of extractant dilution with kerosene on copper recovery rate during extraction are presented in Table 2.
Table 2
Rate of copper recovery into the extractant depending on its concentration
Mass fraction of LIX extractant diluted with kerosene, % |
Molar concentration of copper in the aqueous phase after extraction Caq |
Molar concentration of copper in the extractant after extraction Сe |
Rate of copper recovery into the extractant E, % |
100 |
0,000 |
0,446 |
100,00 |
70 |
0,015 |
0,430 |
96,59 |
40 |
0,207 |
0,239 |
53,61 |
10 |
0,374 |
0,071 |
16,02 |
It can be seen from Table 2 that the use of a 70 % solution of LIX 84-I in kerosene slightly reduces the rate of copper recovery into the extract, whereas the use of a 40 % solution of LIX 84-I in kerosene almost halves the recovery rate to 53.61 %.
The sorption process was studied under thermostated conditions at a constant temperature of 25 °C. Table 3 shows dependencies between rhenium Gibbs adsorption and its concentration in the aqueous phase during sorption on the Purolite PPA100 anion exchanger, as well as values of parameters inverse to the Gibbs adsorption (1/G) and rhenium concentration in the initial solution (1/C) for plotting respective diagrams.
Table 3
Experimental data, obtained in the study of dependencies between equilibrium rhenium content in the phase of Purolite PPA100 anion exchanger and rhenium concentration in the equilibrium solution
Sample N |
Rhenium concentration in the initial solution, mol/l |
Rhenium concentration in the solution after sorption, mol/l |
Change in rhenium concentration as a result of sorption, mol/l |
G, mol/kg |
1/С, l/mol |
1/G, kg/mol |
1 |
0,08785 |
0,05345 |
0,03441 |
0,817 |
11,38 |
1,22 |
2 |
0,04101 |
0,02448 |
0,01652 |
0,393 |
24,38 |
2,55 |
3 |
0,00279 |
0,00070 |
0,00209 |
0,050 |
358,07 |
20,11 |
4 |
0,00132 |
0,00031 |
0,00101 |
0,024 |
756,65 |
41,70 |
5 |
0,00049 |
0,00019 |
0,00030 |
0,007 |
2023,52 |
138,75 |
Figure 2, a demonstrates an isotherm of rhenium sorption on the Purolite PPA100 anion exchanger from the productive leaching solution. Figure 2, b shows a dependency between the inverse values of adsorption and initial rhenium concentration in the aqueous phase. Obtained linear dependency between 1/С and 1/G also confirms that the Langmuir equation adequately describes the isotherm of rhenium sorption on the Purolite PPA100 anion exchanger.
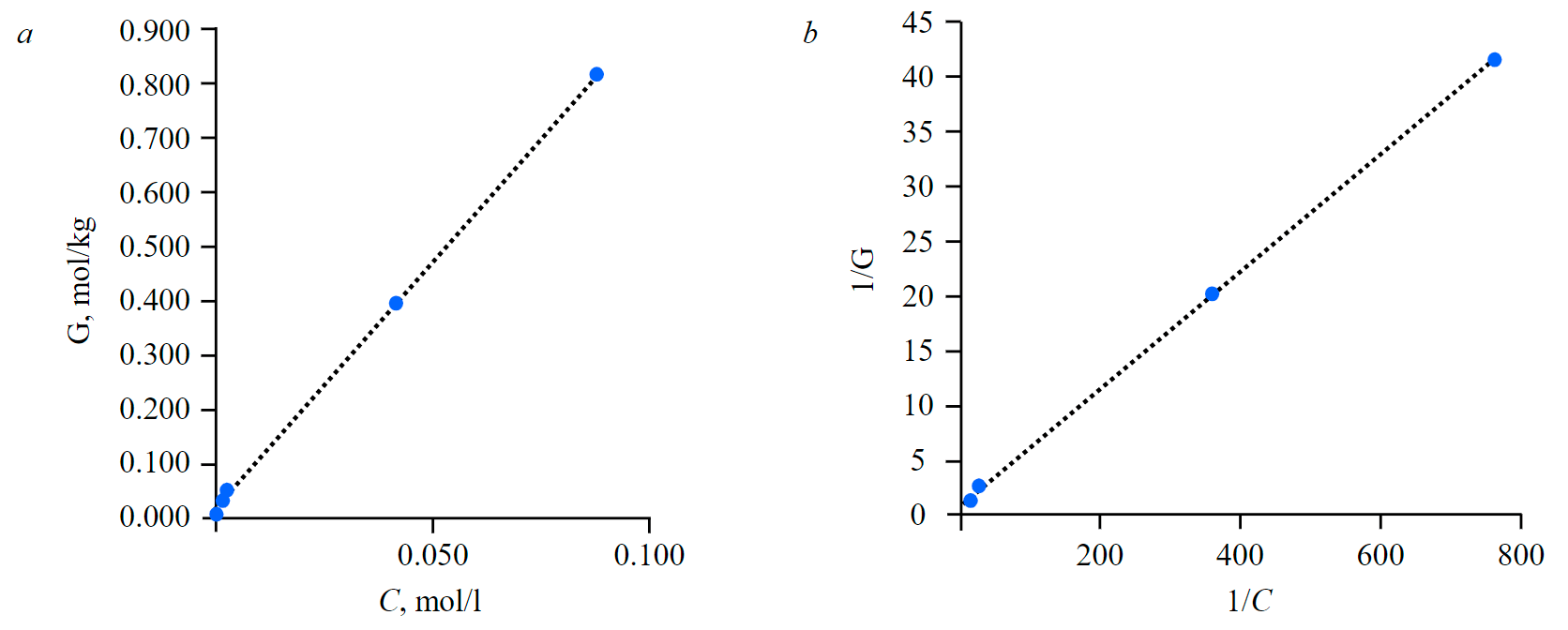
Fig.2. An isotherm of rhenium sorption from a model productive solution for leaching substandard copper concentrates from the Zhezkazgan processing plant on Purolite PPA100 anion exchanger (a) and dependency between inverse values of Gibbs adsorption (1/G) and rhenium concentration (1/С) in the aqueous phase of the initial solution (b)
Linear form equation of the Langmuir isotherm (Fig.2, b) can be expressed as follows:
The capacity of adsorption monomolecular layer (G∞) equals 1.114 mol/kg, adsorption equilibrium constant (K) equals 16.67.
Thus, it was experimentally proven that the isotherm of rhenium sorption from a model process solution, which was a productive solution for ammonia leaching of substandard copper concentrates from the Zhezkazgan processing plant, using Purolite PPA100 anion exchanger, is described by the Langmuir equation in the entire range of rhenium concentration. Experiments on rhenium-containing model solutions confirm that perrhenate ions are absorbed by means of ion exchange with counterions, which neutralize the charge of protonated functional groups of the sorbent.
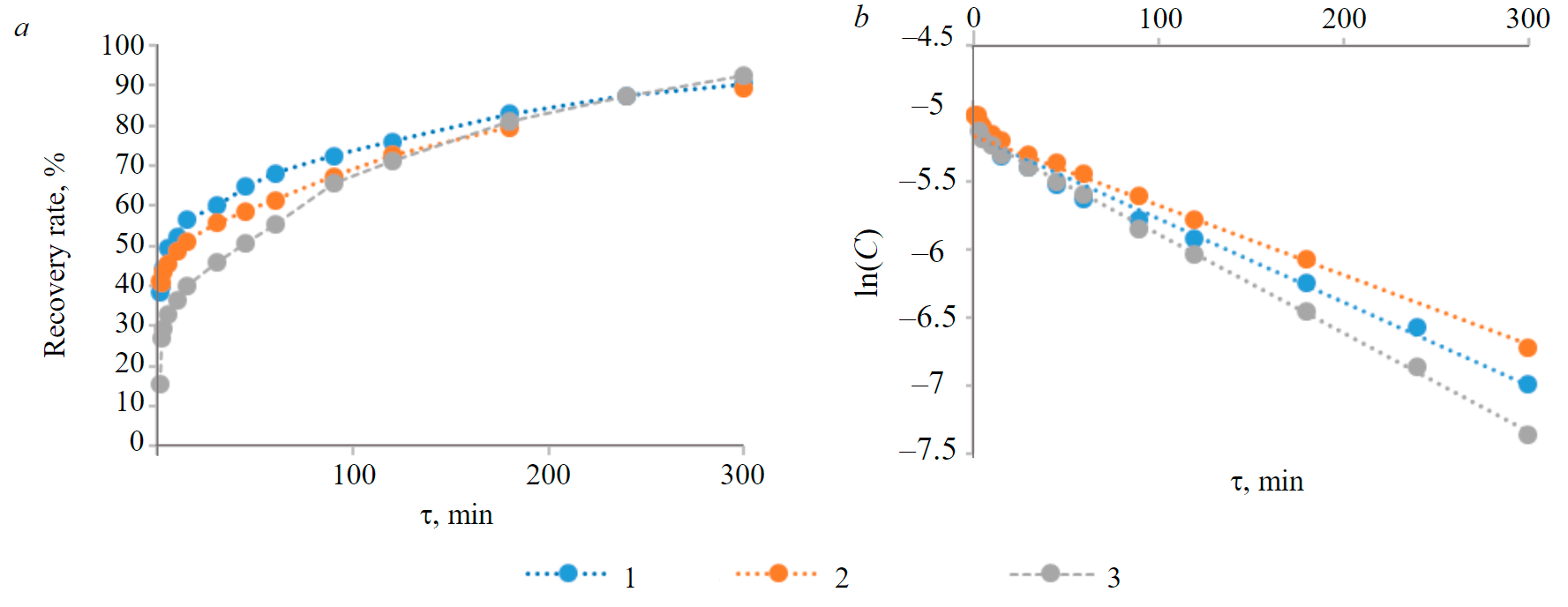
Fig.3. Dependencies between sorption time and saturation rates of anion exchangers during the sorption of perrhenate ions from the model productive solution for leaching substandard copper concentrates from the Zhezkazgan processing plant (a) and their logarithmic forms (b) 1 – AV-17-8; 2 – Purolite A103; 3 – Purolite PPA100
One of the important aspects of the study was aimed to estimate such kinetic characteristics of the ion-exchange process as the constant of ion-exchange adsorption rate (k, min–1), half-time of the exchange (τ1/2, min) and diffusion coefficient in the ion exchanger phase (cm2/s). Obtained numerical values of these characteristics allow to compare kinetic efficiency of Purolite PPA100 anion exchanger with existing analogues, represented by two widely used industrial ion exchangers, AV-17-8 and Purolite A103.
In order to perform kinetic studies, ion exchangers were prepared in accordance with the manufacturer's recommendations by the method described in GOST 10896-78. Measurements for the kinetic curves were taken under static conditions by mixing rhenium-containing solution and a weighed portion of the sorbent; phases were separated by filtration and analyzed.
Kinetic curves of ion-exchange sorption of perrhenate ions on ion exchangers Purolite PPA100, AV-17-8 and Purolite A103, as well as their logarithmic forms are presented in Fig.3, a, b.
From the linear logarithmic forms of kinetic dependencies shown in Fig.3, b, the constants of ion-exchange adsorption rate (k) and half-time of the exchange for the anion exchangers Purolite PPA100, AV-17-8 and Purolite A103 were derived, see Table 4.
There are a number of methods for determining the numerical value of diffusion coefficients. It has been noted that the overwhelming majority of ions, excluding large organic ions, at room temperature in aqueous solutions are characterized by diffusion coefficients in the range of 10–5 cm2/s. On the contrary, in ion exchangers diffusion coefficients fall within the interval of 10–6-10–16 cm2/s [6].
Any point of the kinetic curve can roughly be estimated based on the values of recovery rate and time. In particular, the value of diffusion coefficient in the ion exchanger phase can be estimated from the value of diffusion half-time (τ1/2) [6]:
where F0 is assumed to be 0.03 for a spherical particle, 0.06 for a cylindrical and 0.049 for a plate-like one; R is the average radius of anion exchanger particle, cm.
Based on the values of diffusion coefficients, it is possible to draw conclusions about the gel mechanism of diffusion in the sorbent.
Таблица 4
Sorption characteristics of anion exchangers
Ion exchanger |
Linear form of kinetic dependency |
Constant of ion-exchange adsorption rate k, min– |
Half-time of the exchange τ1/2, min |
Diffusion coefficient in the ion exchanger phase |
Purolite PPA100 |
lnC = –5,1644 – 0,0072t |
0,0072 |
96,25 |
2,92·10–8 |
АВ-17-8 |
lnC = –5,1644 – 0,0057t |
0,0057 |
121,58 |
2,50·10–8 |
Purolite A103 |
lnC = –5,1644 – 0,0056t |
0,0056 |
123,75 |
2,27·10–8 |
Conclusion
Dependencies of copper recovery from model ammonia leaching solutions have been established for various concentrations of the extractant and ratios of aqueous and organic phases. It has been demonstrated that an increase in the extractant concentration and volume led to an increase in copper recovery into the organic phase. The authors calculated the optimal volume ratio of aqueous and organic phases, which was Vorg:Vaq = 1:1, and the optimal concentration of the extractant in the organic phase, which amounted to 70 %. Stoichiometric consumption of the extractant allows to combine the operations of copper recovery and concentration from ammonia leaching solutions, which is relevant for handling solutions formed during the processing of technogenic raw materials. The efficiency of Purolite PPA100 sorbent for rhenium recovery from ammonia leaching solutions has been demonstrated. An isotherm of rhenium sorption from a model leaching solution of substandard copper concentrates from the Zhezkazgan processing plant has been obtained on Purolite PPA100 anion exchanger. The values of end capacity and adsorption equilibrium constants for the Purolite PPA100 anion exchanger have been estimated (G∞ = 1.114 mol/kg; K = 16.67). Kinetic dependencies between sorption time and saturation rate of anion exchangers Purolite PPA100, AV-17-8 and Purolite A103 during the sorption of perrhenate ions from model productive solutions for leaching substandard copper concentrates from the Zhezkazgan processing plant have been established. The constants of ion-exchange adsorption rate, half-time of the exchange and diffusion coefficient have been estimated. At 25 °С, for Purolite PPA100 anion exchanger the results were k = 0.0072 min–1, τ1/2 = 96.25min,
References
- Karas S.A., Kremenetskii A.A., Orlov S.Yu. et al. Briketno-Zheltuhinskoe Rhenium Deposit – a New Geological and Industrial Type of Hydrogenic Deposits: Characteristics of the Geological Structure and Technology of In-Situ Leaching. Razvedka i okhrana nedr. 2016. N 11, p. 26-30 (in Russian). URL
- Voropanova L.A., Pukhova V.P. Extraction of Copper, Cobalt and Nickel Ions from Aqueous Solutions by Extractant Cyanex 272. Journal of Mining Institute. 2018. Vol. 233, p. 498-505. DOI: 10.31897/PMI.2018.5.498 (in Russian).
- Pechen V.A., Vanin I.A., Veselova O.A., Troshkina I.D. Sorption of Rhenium from Sulfuric Acid Solutions with Trialkylamine-Containing Impregnates. Uspekhi v khimii i khimicheskoi tekhnologii. 2016. Vol. 30. N 6 (175), p. 38-40 (in Russian). URL
- Sulimova M.A., Sizyakov V.M., Litvinova T.E., Vasilev V.V. On Possibility of the Use of Metallurgical Production Wastes as a Sorbent in the Industrial Water Cycle. Chernye metally. 2016. N 8 (1016), p. 43-49 (in Russian). URL
- Petrov G.V., Boduen A.Ya., Ivanov B.S., Serebryakov M.A. Investigation of Ammonia Autoclave Leaching of Silver and Rhenium Containing Subconditioned Copper Concentrate. Tsvetnye metally. 2016. Vol. 10, р. 23-28. DOI: 10.17580/tsm.2016.10.03 (in Russian).
- Zakharyan S.V., Rogozhnikov D.A., Karimova L.M. et al. Study of Hydrometallurgical Processing of Roasted Copper Concentrate Leach Solutions. Vestnik Irkutskogo gosudarstvennogo tekhnicheskogo universiteta. 2018. Vol. 22. N 5 (136), p. 207-213 (in Russian). URL
- Yun A.B., Zakharyan S.V., Karimova L.M. et al. Research on Nitric Acid Leaching of ZPP Rough Copper Concentrate from the Ores of Current Production of Kazakhmys Corporation LLP. Abishevskie chteniya-2016: Materialy Mezhdunarodnoi nauchno-prakticheskoi konferentsii “Innovatsii v kompleksnoi pererabotke mineralnogo syrya”, 21-22 yanvarya2016, Almaty, Respublika Kazakhstan. RGP “NTs KPMS RK”, 2016, p. 581-583 (in Russian).
- Leshukova K.V., Serebryakov M.A., Boduen A.Ya. The Use of Autoclave Leaching for Substandard Ore Concentrates Containing Copper and Zinc. Nedelya nauki SPbPU: Materialy nauchnoi konferentsii s mezhdunarodnym uchastiem. Institut metallurgii, mashinostroeniya i transporta. Part 1, 13-19 noyabrya 2017, Sankt-Peterburg, Rossiiskaya Federatsiya. Izd-vo Politekhnicheskogo un-ta, 2017, p. 95-97 (in Russian).
- Nasteka V.V., Vavilov V.V., Golub V.P. The Role and Opportunities of Import Substitution in the Development of Russian Turbomachinery. Gazovaya promyshlennost. 2017. N 2. Vol. 754, p. 10-16 (in Russian). URL
- Naumov A.V. Rhenium Rhythms (World Market Review). Izvestiya vuzov. Tsvetnaya metallurgiya. 2007. N 6, p. 36-41 (in Russian). URL
- Orlov A.K., Konovalov G.V., Boduen A.Ya. Pyrometallurgical Selection of Copper-Zinc Materials. Journal of Mining Institute. 2011. Vol. 192, р. 65-68 (in Russian). https://pmi.spmi.ru/index.php/pmi/article/view/6319
- Pikalova V.S., Tigunov L.P., Bykhovskii L.Z. Alloying Metals of Russia. Mineral Raw Materials Resources: State, Utilization, Perspective of Development. Chernaya metallurgiya. Byulleten nauchno-tekhnicheskoi i ekonomicheskoi informatsii. 2019. Vol. 75. N 6, p. 675-682. DOI: 10.32339/0135-5910-2019-6-675-682 (in Russian).
- Khudoyarov S.R., Yusupkhodzhaev A.A., Matkarimov S.T. et al. Improving the Efficiency of Processing Sulfide Copper Concentrates in Smelting Furnaces. World science. 2017. Vol. 1. N 1 (17), p. 43-44 (in Russian). URL
- Troshkina I.D., Shilyaev A.V., Adrakhmanova T.G., Maiboroda A.B. Rhenium in Unconventional Raw Materials: Distribution and Recoverability. Razvedka i okhrana nedr. 2011. N 6, p. 87-90 (in Russian). URL
- Rylnikova M.V., Yun A.B., Terenteva I.V. The Second Breath of Zhezkazgan. Gornaya promyshlennost. 2015. N 3 (121), p. 32-34 (in Russian). URL
- Ukraintsev I.V., Trubilov V.S., Klepikov A.S. Poor, Subconditioned and Technogenic Raw Materials as a Prospective Source of Copper Obtaining. Tsvetnye metally. 2016. N 10, p. 36-42. DOI: 10.17580/tsm.2016.10.05 (in Russian).
- Smirnova S.V., Baulin V.E., Torocheshnikova I.I., Pletnev I.V. Extraction of Cadmium, Lead, Cobalt, Copper and Zinc from Aqueous Solutions into Hydrophobic-Hydrophilic Ionic Liquids. Vestnik Moskovskogo universiteta. Seriya 2. Khimiya. 2016. Vol. 57. N 1, p. 11-17 (in Russian). URL
- Cheremisina O.V., Ponomareva M.A., Sagdiev V.N. Sorption recovery of gallium and aluminum from alkaline solutions on an AN-31 anion exchanger. Russian Journal of Non-Ferrous Metals. 2017. Vol. 58, p. 365-372. DOI: 10.3103/S1067821217040046
- Chopabayeva N. Sorption and desorption of rhenium ions by lignin sorbents. Journal of Chemical Technology and Metallurgy. 2019. Vol. 54. Iss. 3, p. 585-594. URL
- Krishnan S., Zulkapli N.S., Kamyab H. et al. Current technologies for recovery of metals from industrial wastes: An overview. Environmental Technology and Innovation. 2021. Vol. 22. N 101525. DOI: 10.1016/j.eti.2021.101525
- Désirée E.P. Rhenium. Reviews in Mineral Commodity Summaries 2018. U.S. Geological Survey, 2018, p. 200. DOI: 10.3133/70194932
- Guang-Ju C., Jian-Ming G., Mei Z., Min G. Efficient and selective recovery of Ni, Cu, and Co from low-nickel matte via a hydrometallurgical process. International Journal of Minerals, Metallurgy and Materials. 2017. Vol. 24. N 3, p. 249-256. DOI: 10.1007/s12613-017-1402-9
- Fathi M.B., B Rezai., Alamdari E.K. Competitive adsorption characteristics of rhenium in single and binary (Re-Mo) systems using Purolite A170. International Journal Mineral Processing. 2018. Vol. 169, p. 1-6. DOI: 10.1016/j.minpro.2017.10.003
- Fleitlikh I.Y., Grigorieva N.A., Logutenko O.A. Extraction of non-ferrous metals and iron with systems based on Bis (2, 4, 4-Trimethylpentyl) dithiophosphinic acid (Cyanex 301), a review. Solvent Extraction and Ion Exchange. 2018. Vol. 36. Iss. 1, p. 1-21. DOI: 10.1080/07366299.2017.1411034
- Mubarok M.Z., Yunita F.E. Solvent extraction of nickel and cobalt from ammonia-ammonium carbonate solution by using LIX 84-ICNS. International Journal of Nonferrous Metallurgy. 2015. Vol. 4. N 3, p.15-27. DOI: 10.4236/ijnm.2015.43003
- Kazakov M.O., Lavrenovb A.V., Arbuzovb A.B. et al. Nickel- and rhenium-containing sulfated zirconia catalyst for simultaneous benzene alkylation and alkanes isomerization. Journal of Siberian Federal University. Chemistry. 2016. Vol. 1, p. 89-99. DOI: 10.17516/1998-2836-2016-9-1-89-99
- Weijun Shan, Danyang Zhang, Xin Wang et al. One-pot synthesis of mesoporous chitosan-silica composite from sodium silicate for application in Rhenium (VII) adsorption. Microporous and Mesoporous Materials. 2019. Vol. 2, p. 44-53. DOI: 10.1016/j.micromeso.2018.10.030
- Peng J.Q., Zhang H.T., Li Y.F. Review of Blade Materials for IGT. Procedia Engineenig. 2015. Vol. 130, p. 668-675. DOI: 10.1016/j.proeng.2015.12.295
- Sagdiev V.N., Cheremisina O.V., Ponomareva M.A., Zatula E.S. Process of extraction of gallium from technological solutions with the use of ion exchange resins. Metallurgist. 2019. Vol. 63. N 2, p. 206-214. DOI: 10.1007/s11015-019-00811-0
- Bo Zhang, Hong-Zhao Liu, Wei Wang et al. Recovery of rhenium from copper leach solutions using ion exchange with weak base resins. Hydrometallurgy. 2017. Vol. 173, p. 50-56. DOI: 10.1016/j.hydromet.2017.08.002
- Siziakova E.V., Ivanov P.V. On the role of hydrated calcium carboaluminate in the improvement of the production technology of alumina from nephelines. Journal of Physics: Conference Series. 2020. Vol. 1515. N 22048. DOI: 10.1088/1742-6596/1515/2/022048
- Smolinski T., Wawszczak D., Deptula A. et al. Solvent extraction of Cu, Mo, V, and U from leach solutions of copper ore and flotation tailings. Journal of Radioanalytical and Nuclear Chemistry. 2017. Vol. 314, p. 69-75. DOI: 10.1007/s10967-017-5383-y
- Sulimova M.A. Possible use of processed ferromanganese concretions for production sewage purification. Journal of Physics: Conference Series. 2019. Vol. 1399. Iss. 5. N 055062. DOI: 10.1088/1742-6596/1399/5/055062
- Sizyakova E.V., Tikhonova E.V., Sizyakova E.V., Cherkasova M.V. Synthesis of hydrocarboaluminates of alkali earth metals from natural magnesium-containing feedstock in conditions of alumina production. Russian Journal of Non-Ferrous Metals. 2017. Vol. 58, p. 36-43. DOI: 10.3103/S1067821217010114
- Yusupkhodjayev A.A., Khojiyev S.T. Methods of decreasing of copper loss with slag in smelting processes. Web of Scholar. 2017. N 2 (11), p. 5-8. URL