Justification of the technological scheme parameters for the development of flooded deposits of construction sand
- 1 — Ph.D. Associate Professor Saint Petersburg Mining University
- 2 — Postgraduate Student Saint Petersburg Mining University ▪ Orcid
Abstract
The article describes the main types of technological schemes for working out the flooded strata of sand deposits using hydraulic shovel excavators. The analysis of scientific and technical literature describing the experience of using hydraulic shovel excavators in the open-pit mining, including pits for the extraction of construction sand, has been carried out. The proposed technological scheme is that the development of reserves of the flooded strata without preliminary water reduction is carried out by a hydraulic shovel excavator from under water by a downward digging with the storage of the extracted rock mass in bulk (for dewatering), placed in such a way that when working out the next mining bench width, it is located within the working area of the excavator for simultaneous processing of the next bench width and loading of dewatered sand from the pile. Calculations of the parameters of the operating platform and the excavator block of the proposed technological scheme for conducting open-pit mining were carried out. The dependence for determining the minimum length of the mining operations front of an excavator for drawing up a technological scheme of operation of a backhoe hydraulic excavator on working out the flooded strata with the pile formation for dewatering sand and its subsequent uploading from the pile by the same excavator is presented.
Introduction
The development of the mineral resource base of the country is due to the introduction of advanced technologies and technological production schemes that allow efficient and rational use of available resources and reserves. Advanced mining enterprises are guided by modern technologies and technological schemes, which are characterized by high knowledge intensity [1]. The development of mining technologies and technological schemes of mining production is based on the introduction of advanced information technologies in the design and production of mining operations, the results of interdisciplinary research in the field of mining and consumption of mineral raw materials, production automation, environmental protection [2].
Mining industry is one of the key sectors of the economies of many countries of the world, it determines the efficiency of functioning of other industries, and the enterprises of the mineral resource complex of Russia provide about half of the gross domestic product [3-5].
High rates of civil and road construction lead to increased demand for such common minerals as sand and gravel, therefore, deposits located near settlements and transport communications are increasingly involved in development. These circumstances lead to the need for mining operations in cramped conditions, when the land allotment of a mining enterprise is limited by various infrastructure facilities. Complicating circumstances are also that deposits involved in mineral reserves development are located below the groundwater level.
The open-pit mining method of mineral deposits is prevalent in the sand extraction, which is mainly used in the construction industry (especially as a fine filler in concrete), road construction, for the formation of new territories (alluvial artificial islands) and other fields of activity [6, 7]. The choice of means of mechanization and technological schemes in sand extraction pits is determined by the mining and geological conditions of the deposits, in particular, the degree of flooding of the mineral reserves being developed, the presence and composition of rubbles.
Currently, about 60 % of the sand and sand-gravel deposits being developed and planned for development are characterized by the presence of a flooded strata in mineral deposits. The degree of flooding of a mineral deposit plays an important role in determining the development schemes and choosing the means of mechanization. Pumping groundwater out of the face leads to an increase in the cost of purchasing fixed assets and energy resources. The slightest change in the water level requires consideration of a number of problems, such as changes in the physical and chemical properties, gas and bacterial composition of groundwater, complete disappearance of groundwater sources, drainage of rivers and lakes, changes in the state and properties of the rock mass, the occurrence of karst and other processes.
The technology of conducting open-pit mining operations on flooded deposits of construction sands usually includes the separation of the developed deposit into dry and flooded parts. The development of the flooded part of the sand deposits is carried out mainly by means of hydro-mechanization, in some cases hydraulic or mechanical excavators with equipment such as backhoe or dragline are used for the downward digging of rock from the flooded face [8, 9].
The development of flooded reserves of sand deposits and sand-gravel mixture is associated with the need to bring the mineral to the required degree of humidity. For this purpose, a pile is formed at the pit (in the case of using an excavator method of mining minerals) or an alluvial map (if mining is carried out using a dredger).
Since open-pit mining causes significant damage to water, biological and soil resources [10], mining enterprises should take urgent measures for the ecological recovery of disturbed lands and their return to economic use even at the initial stage of operation [11], and besides, the main direction of recultivation of flooded sand deposits is water management. Due to the fact that the flooded pits for the extraction of construction sand are located in close vicinity to settlements, in order to ensure the safe use of these territories by the population, it is necessary to pay attention to the formation of the developed space of the deposit in the form of a flooded pit, the parameters of which depend on the depth of the deposit development, the type of extracted minerals, the technological scheme and technology used [12].
The development of partially flooded and flooded deposits by the excavator method is carried out using mainly draglines and less often backhoe hydraulic excavators. With a high content of rubble, the effectiveness of the draglines use decreases [13].
Shovel excavators with hydraulic drive in combination with road transport are increasingly used in mining industry in the development of mineral deposits of various types [14]. Shovel excavators with hydraulic drive are widely used in excavation and loading operations, especially when the supply of electricity to mining areas is difficult, as well as in pits of small and medium production capacity [15]. Insignificant linear parameters of operation of hydraulic shovel excavators are not restrictions to their use in flooded deposits, since the appearance of elongated working equipment for these machines allows to consider them as alternative options for draglines and even for dredgers.
One of the main advantages of hydraulic shovel excavators with working equipment is the presence of a backhoe, in comparison with other types of excavators, makes it possible to set any trajectory of the shovel movement [16], which allows to clean and form the necessary contours of the excavators operating platform, the lower bench platform and the face without the use of additional equipment.
The main technological scheme, according to which the open-pit mining of mineral deposits
is carried out using backhoe hydraulic excavators in combination with road transport, is the location of the excavator on the bench roof with the working out by the downward digging and loading of
vehicles on the horizon of the hydraulic shovel excavator installation [17, 18]. The preparation of the operating platform is an important factor, especially when loading vehicles, because road conditions at loading and unloading sites predetermine up to 70 % of the wear of truck tires.
The main suppliers of hydraulic shovel excavators to mining enterprises are manufacturing companies: Caterpillar Inc. [19-21], Hitachi [19, 20, 22], Komatsu Ltd. [22-24], Liebherr [19, 20], Volvo, etc. [19].
Backhoe hydraulic excavators with a bucket capacity of up to 10 m3 and maximum parameters of working equipment (shovel booms and dipper handles) are mainly used in pits developing flooded sand deposits. The relative characteristics and efficiency of the excavator are determined, first of all, by a combination of the main parameters of the excavator working equipment. Therefore, a complex study of their interrelations is one of the most important tasks in the theory of general calculations of hydraulic shovel excavators [15, 25].
The shape and size of the working area of the excavator have the greatest impact on the technological capabilities of the equipment and, as a result, the possibility of its use in specific mining and geological conditions. Such geometric parameters as the maximum height and depth of digging, the height of loading and unloading, the radius of digging at the level of the excavator parking, etc. can be determined by the axial profile of the working area [26]. These characteristics are given by manufacturers in numerical format or in the form of graphic kinematic schemes in specialized passport literature.
The design of hydraulic shovel excavators is based on the use of articulated working equipment, in this regard, the radius of action of the excavator does not depend on the height of digging and unloading. The radii of digging and unloading are determined based on the conditions of safe mining operations and efficient loading of the tipper [27].
The use of hydraulic shovel excavators determines the cyclic mode of equipment operation [28, 29], in this regard, downtime and break-ups may occur at any stage of work. This allows changing the type of activity of the equipment after the completion of the excavator cycle, the duration of which is about 25-60 s, depending on the dimensions of the machine.
Methodology
The analysis of technological passports of hydraulic shovel excavators operation showed that the main parameters of the operating platform are the widths: the excavator bench width along the pillar, the additional safety strip (safety bench), the roadway (depends on the linear parameters of vehicles), the shoulder of the pit road, the auxiliary strip and the base of the prism of a possible fall, including the safety shaft.
The minimum width of the operating platform of a hydraulic shovel excavator in road transport depends mainly on the size of the excavation and loading machine, the overall dimensions of tippers and traffic patterns within the working area, as well as on the height of the benches being developed and the physical and mechanical properties of the rocks composing it [30].
The installation of hydraulic shovel excavators in the face during mining is determined by the width of the safety bench, which is determined by the natural slope angle of the rocks being developed, as well as the height of the rock thickness being worked out [31, 32].
The limited space at the loading site affects the maneuverability of the tipper truck during its loading due to the fact that when the tipper truck approaches the excavator for loading, it needs to make turns to position the body in a safe and correct place directly under the shovel of the excavator [33].
The volume of rock extracted from the face for one excavator working parking spot (the volume of the face block) is determined by the excavator movement step (the distance between adjacent parking spots of a backhoe hydraulic excavator), the width of the rock strata being worked out (the height of the bench or sub-bench) and the maximum radius of the excavator digging at the level of the lower platform of the bench. The maximum distance between the adjacent working parking spots of the excavator is determined by the difference between the maximum radius of the excavator digging at the level of the lower platform of the bench and the product of the width of the rock strata being worked out by the cotangent of the slope angle of the bench according to the condition of safe excavator installation.
The bench width of a backhoe hydraulic excavator, working with a downward digging, including when working out a flooded face, is determined by a directly proportional relationship between the radius of the excavator digging, set based on the linear dimensions of the excavator working equipment and determined by the kinematic scheme of work, and the sine of the rotation angles of the excavator from the axis of its stroke when digging, not exceeding 30-45°.
Development of flooded deposits without preliminary water reduction with sand excavation by hydraulic shovel excavator under the water is produced by downward digging with storage of the extracted rock mass in bulk for dewatering. Flooded sands are worked out taking into account the abandonment of a protective layer of dry sands. Sand is shipped from the drained bulk by an excavator or loader to the means of transportation.
When unloading a mixture of water and sand from an excavator shovel into a dewatering pile located on the horizon under development, the minimum width of the operating platform increases by the width of the base of the dewatering shaft and the safe distance between it and technological equipment. The operating platform during the development of flooded deposits of construction sand should be installed at least 0.5 m above the groundwater level in order to create a safety cushion above the aquifer. The distance between the bench crest and bench toe of the dewatering pile includes the placement of trench or side ditch that provides the discharge of water coming from the dewatering pile and safety shaft, limiting the prism of possible bench fall.
The width of a pit road includes the width of the roadway and the shoulder, determined by the number of traffic strips and the overall width of the tipper, as well as, if necessary, other elements, such as dewatering structures (trays or side ditches), a side ditch shelf, etc.
The length of the excavator block, or the length of the mining front per excavator, is one of the key parameters of the field development system, which affects the productivity of the complex of excavation, loading and transport equipment. The considerable length of the excavator mining front allows to reduce the loss of time for the transition of the excavator to a new bench width and the re-laying of transport communications. The operation of the excavator with minimal excavator blocks in length allows reducing the transport mileage on in-pit roads and increases the intensity of mining. In this regard, the choice of the optimal length of the excavator block is an important research task for the geological and mining conditions of each specific mineral deposit.
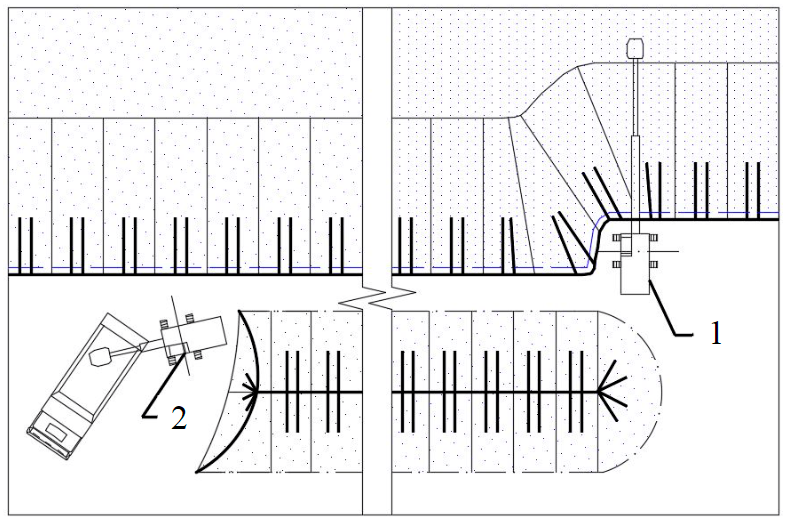
Fig.1. The scheme of mining operations using a backhoe hydraulic excavator on the excavation of the flooded strata with the formation of a pile for dewatering sand 1 and subsequent loading of the dewatered mineral from the pile into vehicles by a second excavator 2
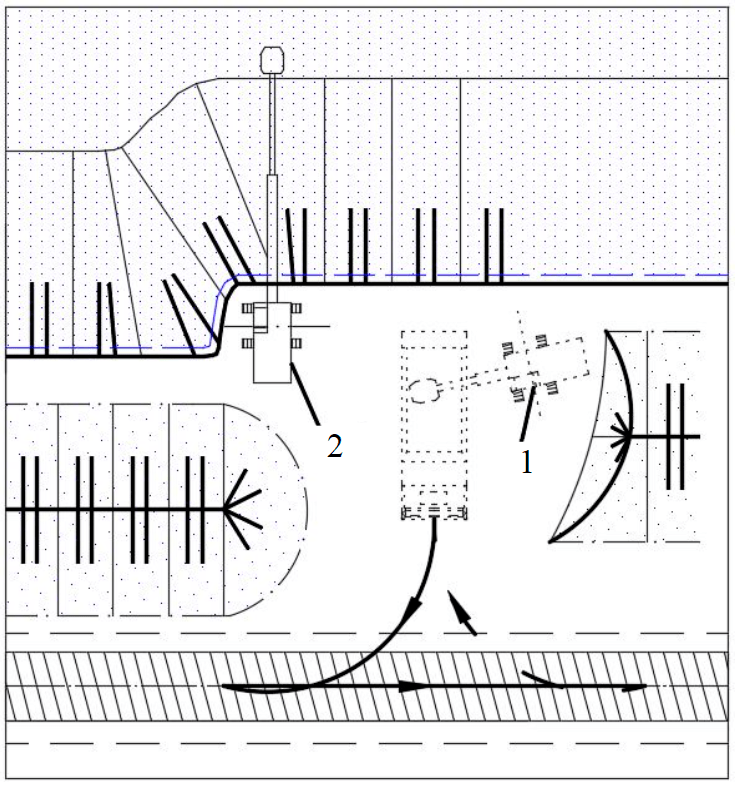
Fig.2. The scheme of mining operations using a backhoe hydraulic excavator on the loading of sand from the pile 1 and its subsequent working off the flooded strata with the formation of a pile for dewatering sand 2
The development of small flooded pits for the production of construction sand, such as line road pits, causes cramped conditions for mining operations, therefore, there is a need for the dewatering of minerals in the contours of the mining bench width. Dewatering in the bench width contours leads to the need to leave the pile for a long time so that the water coming from digging sand or sand-gravel mixture from the flooded face drains from the entire body of the pile.
To transport the dewatered mineral from the pile to the vehicles, a second excavator and a shovel loader can be used, which moves after the mining excavator at a distance sufficient for dewatering the pile (Fig.1). This technological scheme requires the presence of two excavation and loading units of equipment in one bench width.
In order to ensure the development of the flooded face and the loading of the dehydrated mineral from the pile by one excavator, a technological scheme can be used in which the development of the reserves of the flooded strata without preliminary water reduction is carried out from under the water by a downward digging with the storage of the extracted rock mass into a bulk for dewatering, located in such a way that during the development of the next mining bench width, this bulk is located within the working area of the excavator. After the completion of the first mining bench width, the excavator moves
to the beginning of the second bench width and, with an advancing stroke, ships the dehydrated mineral from the pile to the vehicles, then, with a retreating stroke by a downward digging, it works out the flooded reserves with the storage of the extracted rock mass in the dewatering bulk, located in the next mining bench width (Fig.2).
The minimum length of the mining front of the excavator in the considered technological scheme should ensure the necessary productivity of the excavator during the dewatering of the mineral in the pile to the required values. In the case of pits with limited parameters, when drawing up calendar plans for the development of mining operations, it is necessary to take into account the time interval between the formation of the pile and its loading, required for the dewatering of the mineral in the pile to the desired values.
When unloading rock from the shovel of an excavator for dewatering into a pile located on the horizon under development, the parameters of loading by a hydraulic excavator of the vehicle become irrelevant. The main parameters in the technological scheme under consideration that affect the hydraulic excavator bench width are the width of the bench and the area of the dewatering pile, the dimensions of which can be determined depending on the volume of rock extracted from the face during one working parking of the excavator.
When excavating sand from under water, the mineral is placed on the work site in a pile for dewatering, therefore, when determining the width of the work site, it is necessary to take into account the parameters of the pile, the size of the base of which depends on the height and slope angle of the pile [34].
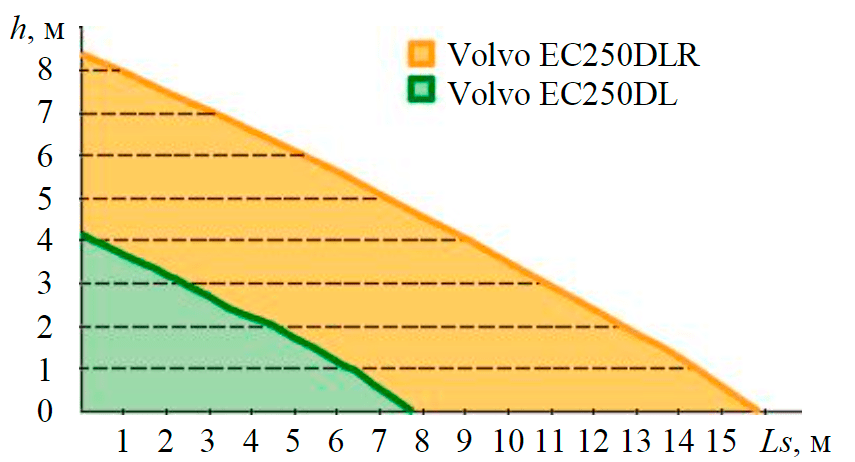
Fig.3. Diagram of the dependence of the distances between adjacent work parking spots on the capacity of the sand strata being worked for the Volvo EC250 hydraulic excavator with various working equipment
Discussion
Pit sand and sand-gravel mass in the Leningrad region are mined at more than 50 developed sites, sea sand – in the Gulf of Finland [35]. The total extraction volume of these minerals is about 70 % of the extraction volume of minerals at all objects operated in the region [36].
In order to test the results of theoretical research, the conditions for the development of the Agalatovo construction sands deposit in the Leningrad region were considered, which is carried out according to the technological scheme with the excavation of the flooded strata by a dredger and loading sand from the alluvial map by a hydraulic shovel excavator. The sand is drained in three alluvial maps, the area of which is more than four hectares, which determines the increase in the cost of using the land allotment for the enterprise.
With the aid of computer modeling, the values for the maximum distances between adjacent working parking spots of a backhoe hydraulic excavator Ls for different capacities of the strata being worked out h are established. The development takes place by downward digging with a slope angle of the bench equal to 33°, using the example of a hydraulic shovel excavator Volvo EC250 (with a boom length equal to 6 m with a handle length of 2.97 m), similar in technical characteristics to the excavator Volvo EC 249 BLC, which is used at the Agalatovo pit, but is not currently available, and models on a similar base with extended DLR equipment with a boom length equal to 10.2 m with a handle length of 7.85 m (Fig.3).
Based on the obtained values of the distance between adjacent excavator parking lots, it is possible to determine the volume of rock extracted from the face in one parking lot, which determines the parameters of the dewatering pile during excavator operation according to the scheme shown in Fig.2.
As a result of the calculations carried out using a program to determine the parameters of the excavator bench width into the flooded face (registration number 2020614350, registration date: 01.04.2020), the values of the optimal bench width and the width of the operating platform of backhoe hydraulic excavators were revealed when unloading the shovel into pile for dewatering with subsequent loading into motor vehicles. For the Volvo EC250 excavator with extended DLR equipment with a boom length of 10.2 m, a handle length of 7.85 m, when it is worked out with a downward digging of a flooded strata with a capacity of 3 m and a slope angle of 33°, the optimal excavator bench width will be 6.4 m, the excavator movement step is 6.5 m, the height of the pile for dewatering is 3.4 m, and the width of the operating platform is about 20-25 m.
The minimum length of the mining front of the excavator for the technological scheme with the operation of a backhoe hydraulic excavator on the development of a flooded strata with the formation of a pile for dewatering sand and its subsequent loading from the pile by the same excavator is calculated according to the following dependence:
where Tdt – dewatering time of rock in the pile, min; E – excavator shovel capacity, m3; Kf, Kf.st – the coefficients of loading the excavator shovel with minerals when digging from the face and from the pile, respectively; Kus, Kus.st – the coefficients of the excavator use when digging from the face and from the pile, respectively; tc, tc.st – the duration of the working cycle of the excavator when digging from the face and from the pile, respectively, min; Kl, Kl.st – the rock fragmentation indexes when digging from the face and from the pile, respectively; tsh – time required to move the excavator to an adjacent bench width, min; Rs.max, Rs.saf – maximum and safe excavator digging radii when digging from the face, respectively, m; h – bench height, m; Ast – the excavated bench width of the excavator, m.
Dewatering of sand in the formed pile is carried out by drainage due to the action of gravitational forces. The duration of rock dewatering in the pile depends on the height of the pile, granulometric and mineralogical composition, climatic and other conditions.
For the conditions of the development of the Agalatovo construction sands deposit in the Leningrad region, the minimum length of the excavator mining front for the technological scheme with the operation of a backhoe hydraulic excavator on the development of a flooded strata with the formation of a pile for dewatering sand and its subsequent loading from the pile by the same excavator will be 200-300 m, depending on humidity.
Conclusion
The conducted studies show that the use of the technological scheme of mining operations when working out the flooded strata using hydraulic shovel excavators will reduce the area of the land allotment occupied by the enterprise for the formation of alluvial maps and bulk for dewatering sand. The dependences of the distances between adjacent work parking spots on the capacity of the sand strata being worked out for modern and promising models of backhoe hydraulic excavators from the most well-known manufacturers allow to establish the shape and dimensions of the working area for these excavators.
The introduction of the proposed technological scheme for the extraction of construction sand with dewatering in the bench width contour at the construction sand deposits will lead to a reduction in the required fleet of working equipment of the enterprise and will allow the development of the flooded strata of the deposits, taking into account the optimal operating parameters of the equipment available at the pits.
Prospects for the development of technological schemes with in-hole dewatering are associated with the development of excavator construction, so the appearance of the class of heavy backhoe hydraulic excavators will significantly expand the possibilities of excavator development of the flooded strata of sand deposits.
References
- Litvinenko V.S., Sergeev I.B. Innovative development of the mineral resource sector. Problemy prognozirovaniya. 2019. N 6, p. 60-72 (in Russian).
- Kazanin O.I., Drebenstedt C. Mining Education in the 21st Century: Global Challenges and Prospects. Journal of Mining Institute. 2017. Vol. 225, p. 369-375. DOI: 10.18454/PMI.2017.3.369
- Bykova E.N. Allotment of land for mining enterprises. Journal of Mining Institute. 2012. Vol. 199, р. 314-319 (in Russian).
- Danilov A.S., Matveeva V.A., Pashkevich M.A. The assessment of technogenic massifs as the sources of ecological danger. Mir russkogo slova. 2017. N 2, p. 115-120 (in Russian).
- Litvinenko V., Bowbrick I., Naumov I., Zaitseva Z. Global guidelines and requirements for professional competencies of natural resource extraction engineers: Implications for ESG principles and sustainable development goals. Journal of Cleaner Production. 2022. N 130530 (in press). DOI: 10.1016/j.jclepro.2022.130530
- Lapshin N.S., Fomin S.I. Principles of technological schemes construction for processing sand-gravel mixture at low-productivity roadside pits. Nauka i biznes: puti razvitiya. 2019. N 12(102), p. 97-101 (in Russian).
- Abam T.K.S., Oba T. Recent case studies of sand mining, utilization and environmental impacts in the Niger delta. Journal of Environmental Geology. 2018. Vol. 2 (2), p. 64-67.
- Semenov D.A., Vahrushev S.I. Method of selection of the dredger for dredging sand and gravel from the bottom of the River Kama. Izvestiya KGASU. 2016. N 4(38), p. 451-458 (in Russian).
- Cheban A. Hydromechanized mining construction of rocks in the basin of river Amur. Vestnik gosudarstvennogo universiteta morskogo i rechnogo flota imeni admirala S.O.Makarova. 2016. N 2 (36), p. 73-78 (in Russian). DOI: 10.21821/2309-5180-2016-8-2-73-78
- Kruk M., Semenov A., Cherepovitsyn A., Nikulina A. Environmental and Economic Damage from the Development of Oil and Gas Fields in the Arctic Shelf of the Russian Federation. European Research Studies Journal. 2018. Vol. XXI. Special Iss. 2, p. 423-433.
- Patel D.K.A., Patel B.P., Patel M.K.A. A Critical Review on Kinematics of Hydraulic Excavator Backhoe Attachment. International Journal of Mechanical Engineering and Robotics Research. 2015. Vol. 4. N 2, p. 188-203.
- Lamkov I.M., Chermoshentsev A.Yu. Substantiation of the need to use a digital relief model to study the bottom surface of flooded pits located on the territory of Novosibirsk. Interekspo Geo-Sibir. 2016. Vol. 4. N 2, p. 69-73 (in Russian).
- Onika S.G., Gets A.K., Khalyavkin F.G., Rebert B.S. Technical plan of development of water-bearing areneceous, sand-and-gravel deposit. Gornaya mekhanika i mashinostroyeniye. 2016. N 2, p. 5-8 (in Russian).
- Dobrovolskii A.I., Leonov E.I., Kutovoi A.V. et al. Improving the efficiency of coal open-pit mine development by optimizing technological parameters in difficult mining and geological conditions. Ugol. 2019. N 10, p. 72-78 (in Russian). DOI: 10.18796/0041-5790-2019-10-72-78
- Yang Ch., Huang K., Li Yi. et al. Review for Development of Hydraulic Excavator Attachment. Energy Science and Technology. 2012. Vol. 3. N 2, p. 93-97. DOI: 10.3968/j.est.1923847920120302.386
- Marinin M., Marinina O. Improvement of project decisions efficiency and cost optimization at the mine engineering stage of reclamation in the context of open pit ore mining. International Multidisciplinary Scientific GeoConference Surveying Geology and Mining Ecology Management, 29 June – 5 July 2017, Albena, Bulgaria. 2017. Vol. 17. N 13, p. 423-428. DOI: 10.5593/sgem2017/13/S03.054
- Kholodnyakov E.V. Loginov, Vu Duc Tuan. Low-waste open-pit minings using hydraulic excavators Mining informational and analytical bulletin. 2017. N 1, p. 357-363 (in Russian).
- Loginov E.V., Loktiukova O.Iu., Melnitskaya M.E. Calculation of Bench Width for Backhoe Hydraulic Excavators Operated in Sinking Mining Systems. Journal of Engineering and Applied Sciences. 2019. Vol. 14. Iss. 17, p. 6444-6448. DOI: 10.36478/jeasci.2019.6444.6448
- Ivanova P.V., Asonov S.A., Ivanov S.L., Kuvshinkin S.Yu. Analysis of the structure and reliability of a modern fleet of mine excavators. Mining informational and analytical bulletin. 2017. N 7, р. 51-57 (in Russian). DOI: 10.25018/0236-1493-2017-7-0-51-57
- Poderni R.Yu. World market of advanced extraction-and-loading machines for open pit mining. Mining informational and analytical bulletin. 2015. N 2, p. 148-168 (in Russian).
- Shibanov D.A., Ivanov S.L., Fokin A.S., Zvonarev I.E. Improving the strategy of technical service of mine excavators by introducing Total Productivity Maintenance into the system. Journal of Mining Institute. 2014. Vol. 209, p. 109-115 (in Russian).
- Snetkov D.S., Kosolapov A.I. Substantiation of equipment complexes for the development of brown coal deposits in the mode of coal quality management. IOP Conference Series: Earth and Environmental Science. 2019. Vol. 378. N 012102. DOI: 10.1088/1755-1315/378/1/012102
- Merzlyakov V.G., Slesarev B.V., Shteinzaig V.M. Expearance Operation Hydravlick Shovels Komatsu Mining Germany on the Mining of Russia. Mining Equipment and Electromechanics. 2013. N 5, p.15-20 (in Russian).
- Yakubovskiy M.M., Isheiskii V.A. Substantiation the technological schemes for development of hydrolytic lignin’s dumps. International Journal of Civil Engineering and Technology. 2018. Vol. 9. Iss. 11, p. 1640-1646.
- Pobegailo P.А., Smolyanitskii E.A. The review and the analysis of the existing methods of determination of key parameters of hydraulic excavators. Mining informational and analytical bulletin. 2015. N 4, p. 216-219 (in Russian).
- Mitrev R.P. A set of complementary indicators for assessment of the geometrical properties of the hydraulic excavator workspace. Naukovedenie. 2016. Vol. 8. N 4 (35), p. 64-77 (in Russian).
- Ananin V.G., Emilov A.B. On the profitability of the operation of mine excavators. Interstroimekh – 2015: Materialy mezhdunarodnoi nauchno-tekhnicheskoi konferentsii, Kazan, 9-11 sentyabrya 2015. Kazan: Kazanskii gosudarstvennyi arkhitekturno-stroitelnyi universitet, 2015, р. 12-16 (in Russian).
- Fisonga M., Mutambo V. Optimization of the fleet per shovel productivity in surface mining: Case study of Chilanga Cement, Lusaka Zambia. Cogent Engineering. 2017. Vol. 4. Iss. 1. DOI: 10.1080/23311916.2017.1386852
- Lazarevic O.Z., Lazarevic B.M. Determining the dynamic characteristics of hydraulic excavators. Vojnotehnicki glasnik. Military technical courier. 2018. Vol. 66. Iss. 1, p. 41-62.
- Bass K.M., Krivda V.V., Shvets D.V., Levchenko E.S. Dependence of change workflow settings playgrounds in applying the mechanism of changes center of mass in the pit dump trucks. Geo-Technical mechanics. 2014. 114, p. 251-260 (in Russian).
- Senkevich V.I. Justification of the bench height when operating hydraulic excavators with a downward digging. Nauka – obrazovaniyu, proizvodstvu, ekonomike: materialy 13-i Mezhdunarodnoi nauchno-tekhnicheskoi konferentsii. Minsk: BNTU. 2015. Vol. 3, p. 13 (in Russian).
- Kholodnyakov G.A., Argimbaev K.R., Reshetnyak S.P. Determination of the height of the mining face during the development of tailings by a hydraulic backhoe excavator. Journal of Mining Institute. 2012. Vol.195, p. 138-141 (in Russian).
- Manyele S.V. Investigation of Excavator Performance Factors in an Open-Pit Mine Using Loading Cycle Time. Engineering. 2017. Vol. 9. N 7, p. 599-624. DOI: 10.4236/eng.2017.97038
- Semenuk S.D., Berezovsky S.N., Tereshchenko A.N. Rational and effective working out of nonmetallic building materials (sand, gravel) for building and repair of motorways in open-cast mines of the Mogilev area. Bulletin of the Belarusian-Russian University. 2011. N 2, p. 134-140 (in Russian).
- Peshkova G.Yu. Analysis of the development of the non-metallic construction materials market: main trends and development prospects. Vestnik Nauchno-issledovatelskogo tsentra korporativnogo prava, upravleniya i venchurnogo investirovaniya Syktyvkarskogo gosudarstvennogo universiteta. 2014. N 4, p. 53-64 (in Russian).
- Cherepovitsyn A.E., Smirnova N.V. Cadastral valuation of the state subsoil fund objects for sand and sand-gravel deposits of the Leningrad Region. Journal of Mining Institute. Vol. 201, p. 142-145 (in Russian).