Increasing the efficiency of phosphate ore processing using flotation method
Abstract
The paper presents flotation of two phosphate ore samples of different origin. Statistical analysis was used to study the effect of operating parameters on flotation efficiency. The paper proposes to increase the efficiency of flotation processing of magmatic phosphate ore with a low grade of the valuable component (P 2 O 5 = 10.88 %), containing nepheline and feldspars, by means of direct anionic flotation. Authors present an optimization of anionic flotation using tall oil fatty acids mixed with anionic phospholane as an anionic collector. The effect of adding soda ash to compensate for the influence of calcium cations on technological parameters of P 2 O 5 flotation was examined. The results of studying the flotation of nepheline ore (flotation tailings of magmatic phosphate ore) showed that replacement of phospholane with oxyethylated isotridecanol allowed to obtain a high-quality concentrate. It was estimated that with the addition of Na 2 CO 3 in the amount of 2,000 g/t, a concentrate was obtained with the grade and recovery of phosphorus pentoxide equal to 39.15 and 94.19 %, respectively. The paper proposes to increase the efficiency of flotation processing of sedimentary phosphate ore with a low grade of the valuable component (P 2 O 5 = 22.5 %), containing gypsum and quartz, by means of desliming followed by anionic or cationic reverse flotation. Tall oil fatty acid with anionic phospholane was used as a collector in anionic reverse flotation, and amine was used in cationic reverse flotation. Sodium tripolyphosphate was used as a P 2 O 5 depressant. It was found to be an effective depressant in both anionic and cationic flotation. When analyzing the statistical plan, it was estimated that the maximum grade of the valuable component in the concentrate (P 2 O 5 = 31.23 %) and the recovery to concentrate of 95.22 % were obtained in the chamber product at amine consumption of 950.88 g/t and sodium tripolyphosphate consumption of 500 g/t.
Introduction
Most of the world's phosphate ores are used in the production of fertilizers and phosphoric acid [20]. Froth flotation is the most widespread method of phosphate ore processing [1, 4, 15]. For the concentration of apatite minerals by means of froth flotation, the industry implements two main processes – direct and reverse flotation.
Direct flotation is used to upgrade magmatic phosphate ores with a low P2O5 grade, rich in silicate minerals, to a commercial product (P2O5 > 30 %) [16, 18]. In direct flotation, apatite becomes hydrophobic, floats and gets separated in a froth layer, while silicate gangue minerals are depressed by means of depressants.
Direct flotation uses anion-active collectors based on fatty acids. It is established that for sedimentary phosphate ores containing calcium bearing mineral as gangue, these collectors are ineffective. Moreover, direct anionic flotation requires the use of warm water and implies difficulties with reusing the recycled water.
For the separation of silicate and phosphate minerals it is more effective to use reverse flotation with cationic collectors. The advantage of cationic collectors over anionic ones is that the former are effective at low temperatures and low consumption. Cationic collectors are suitable for flotation of coarse-grained materials but demonstrate low efficiency in flotation of the fines [14, 31].
The P2O5 grade of the apatite concentrate can be increased to ~ 30-34 % at the recovery of more than 80 % [7, 16]. In order to improve the quality of the apatite concentrate, the initial (rougher) concentrate is subjected to further processing at the second stage of flotation.
Anionic surfactants are commonly used in the flotation process to expand the differences of physical and chemical properties between the apatite surface and associated silicate gangue minerals in the alkaline medium. Most fatty acids (collectors) are usually obtained as waste materials of various industries, for example, tall oil is generated as a by-product of the kraft process in paper industry [11]. Significant components of tall oil fatty acids (TOFA) are oleic and linoleic acids [27]. It is proven that the use of depressants in the flotation process improves the selectivity of fatty acids and reduces their consumption [8]. It is assumed that the depressant is adsorbed on the surface of gangue minerals, which prevents their recovery under the influence of collectors. Papers [29, 31] feature the majority of depressants used in phosphate ore flotation. Sodium silicate was found to be a selective depressant in silicate flotation over a wide pH range. The most effective method is the use of sodium silicate in combination with sodium carbonate [12, 23].
In phosphate ore flotation, alkaline phosphate salts, such as sodium tripolyphosphate (STPP) and tartaric acid, were used as phosphate depressants. After testing five different phosphate depressants using a cationic amine collector, researchers concluded that STPP was the most effective depressing reagent for reverse flotation of coarse silica (+500 µm) from phosphate ore [37]. In addition, results of studies showed that using combinations of anionic and non-ionic reagents could have many synergistic advantages over a single surfactant. It was identified that the use of fatty acids in the presence of non-ionic surfactants improved recovery of the valuable component, reduced consumption of the collector and increased its adsorption selectivity on the surface of the mineral [30, 35, 36].
A.A.Lavrinenko and others researchers studied the efficiency of apatite recovery from brazilite-apatite-magnetite ores using various reagents and came to the conclusion that phospholane was more effective in apatite flotation than tall oil fatty acids. Phospholan was chemisorbed on apatite and changed the structure of its surface due to formation of intermolecular bonds with Ca2+ [10].
The main goal of this study is to optimize the flotation process for two types of phosphate ores of different origin, the samples of which have different physical properties and mineralogical composition.
Statistical methods are widely used to study various processes of ore concentration [5, 21, 24]. Response surface methodology was developed and tested to simulate parameters that affected the processes of grinding and classification [24], gravity concentration [21] and flotation processing of apatite [6, 15].
Materials and methods
Authors examined two samples of phosphate ore with a low grade of the valuable component, different physical properties and mineralogical composition: a sample of sedimentary phosphate ore, taken in Egypt in the Abu-Tartur area of the Western Desert, and a sample of magmatic phosphate ore, taken at the Khibiny deposit of the Kola Peninsula in Russia.
Preparation of samples for flotation. To conduct the tests, the samples were crushed to a particle size of –2 mm, then subjected to wet grinding in a laboratory ball mill (diameter 125 mm, length 170 mm) using 3.3 kg of steel balls of various diameter and 275 ml of water (with a liquid-to-solid ratio of 2:1 by mass). Grinding was carried out until all the material reached the size of –250 µm. The grinded sample of sedimentary phosphate ore was deslimed and washed on a 53 μm sieve. Flotation tests on the sample of sedimentary phosphate ore were performed on a fraction of –250 +53 µm.
Mineralogical and chemical analysis. An X-ray diffractometer Bruker AXS D8 was used to characterize and identify the minerals. A complete chemical analysis of the sample was carried out using an energy-dispersive X-ray fluorescence spectrometer Shimadzu EDX-7000.
Flotation tests and simulation methods. Flotation tests were performed on a 237 FL-A flotation machine with a cell capacity of 0.35 l at an impeller speed of 1,800 rpm. 100 g of the ore sample were mixed with water in the flotation cell; the repulping process lasted for two minutes before adding the reagent. The processing of sedimentary phosphate ore was performed by means of reverse anionic/cationic flotation, the processing of magmatic phosphate ore – by means of direct anionic flotation. As described in paper [15], in direct anionic flotation of igneous and reverse anionic flotation of sedimentary phosphate ore, a mixture of tall oil with phospholane was used as a collector, and alkylbenzene sulfonic acid was used as an activator.
In reverse cationic flotation of sedimentary phosphate ore, amine was used as a collector. Sodium silicate and STPP were used as depressants for silicate and phosphate in direct and reverse flotation, respectively. (NaOH, H2SO4) and (CaCl2, Na2CO3) were used as pH modifiers in the flotation of sedimentary and magmatic phosphate ores, respectively. The duration of reagent agitation was two and three minutes for the depressant and the collector, respectively; the pulp was aerated and the froth product was collected for three minutes. Froth and chamber products were washed off with water, dried, weighed and chemically analyzed.
Discussions
Mineralogical and chemical analysis
Figure 1 demonstrates an X-ray pattern of sedimentary and magmatic phosphate ores. Francolite is the main mineral component; the main gangue minerals in the sample of sedimentary phosphate ore are gypsum and quartz, whereas in the sample of magmatic phosphate ore those are nepheline and pyroxenes. Microscopic analysis of the sample of sedimentary phosphate ore shows that it mainly consists of phosphate grains in the range of 70-80 % by volume. Their size ranges from 50 to 120 μm. Clastic quartz grains have a diameter of 60-80 μm. Gypsum exists in the form of aggregates ranging from crystalline to microcrystalline. It varies from colorless to translucent pale yellow and takes up 20-30 % by volume. Iron oxide occurs either in the form of red to brown cryptocrystalline aggregates of 20-100 μm that fill the pore space or in the form of partial coating and thin films of phosphate grains (Fig.2). The main components of phosphate ore are presented in Fig.2, a; Fig.2, b shows a large grain of fluorapatite, cemented with gypsum and partially replaced by brown iron oxide. A more detailed mineralogical analysis of sedimentary phosphate ore from Abu-Tartur is presented in papers [13, 25].
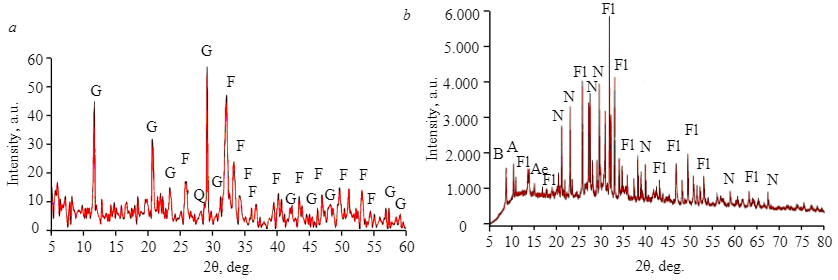
Fig.1. X-ray pattern of the examined samples of sedimentary (a) and magmatic (b) phosphate ores F – francolite; G – gypsum; Q – quartz; Fl – fluorapatite; N – nepheline; A – amphibole; B – biotite; Ae – aegirine
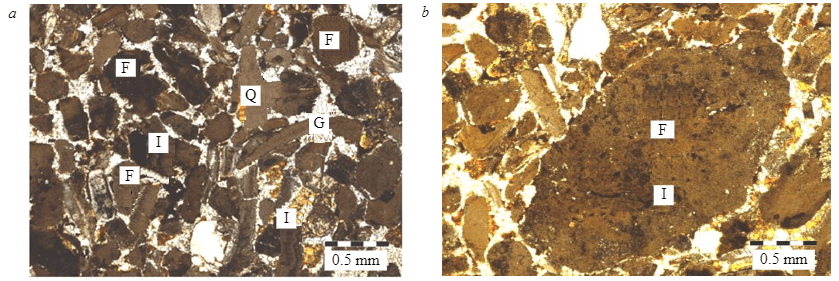
Fig.2. Sedimentary phosphate ores: main components of phosphate ore (a); a large grain of fluorapatite, cemented with gypsum and partially replaced by brown iron oxide (b) F – fluorapatite grains; G – gypsum; I – iron oxides; Q – detrital quartz
Mineralogical characteristics of magmatic phosphate ore were studied earlier [15]. Apatite grains have an average size of 50-100 μm. Most apatite grains are homogeneous, but some of them exhibit a zonal structure. The results of analysis of mineral aggregate liberation in the finely-ground flotation feed are described in detail by the authors of paper [32]. Based on the results obtained, the phosphorus-bearing mineral is present in the form of apatite, the average fluorine grade of the mineral is 4.09 %. The main vein minerals are nepheline – 30.88 %, feldspars – 5.98 %, pyroxenes – 9.22 %, aegirine and aegirine-augite. The ore is characterized by a low content of mica, natrolite, kaolinite, sphene and magnetite. The main phosphorus-bearing mineral is apatite, which contains 99.92 % of the component. It was estimated that in all coarse fractions the majority of apatite particles (70-85 %) are liberated. Moreover, the largest shares (81.12 and 85.73 %) are in the sizes –0.2 +0.16 and –0.045 +0 mm, respectively. The highest percentage of binary aggregate, 24.72 and 26.54 %, is in the size fractions –0.16 +0.071 and –0.071 +0.045 mm, respectively. The binary aggregate is mainly associated with nepheline, apatite aggregates associated with pyroxenes and feldspar are encountered in much smaller quantities. An image of the sample of magmatic phosphate ore was obtained with a scanning (raster) electron microscope using backscattered electron (BSE) detector (Fig.3).
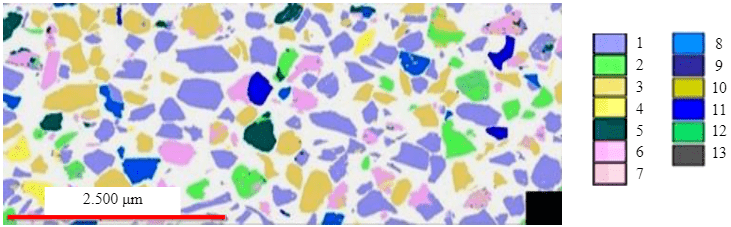
Fig.3. A sample of magmatic phosphate ore 1 – nepheline, calcite; 2 – feldspar; 3 – apatite; 4 – mica; 5 – sodium silicates; 6 – pyroxenes; 7 – zeolites; 8 – titaniferous minerals; 9 – REE minerals; 10 – sulfides; 11 – magnetite, titanomagnetite; 12 – iron oxides and hydroxides; 13 – other minerals
The results of complete chemical analysis of the samples shows that sedimentary phosphate ore has a low grade of P2O5 (~ 22.5 %) and a high grade of SO3 (9.5 %) and SiO2 (10.4 %). Magmatic phosphate ore has a low grade of P2O5 (~ 10.88 %) and a high grade of SiO2 (32.7 %) and Al2O3 (19.1 %).
Flotation of magmatic phosphate ores
Influence of operating parameters on P2O5 grade and recovery. Table 1 presents flotation results of magmatic phosphate ore at various operating parameters. It was identified that the most significant influence on P2O5 grade was exerted by the pH value, P2O5 grade rose steeply with its increase. The pH parameter of the solution determines the degree of ionization and hydrolysis of the collector, which either promotes or prevents adsorption of the collector at various ionized solid/liquid interfaces, contributing to a higher or lower flotation selectivity [22]. It can be seen that the average depressant consumption (300 g/t) is associated with a low collector level (60 g/t) at pH = 11; such conditions lead to an increase in the recovery of the valuable component to the concentrate, where the P2O5 grade is 28.75 %. This is explained by a more effective action of the depressant, as well as by the fact that a small amount of the collector is adsorbed mainly on the apatite surface. At the lowest value of depressant and the highest collector dosage, the low content of P2O5 (22 %) was obtained, due to the fact that the amount of depressant is insufficient to promote a more selective collection of the apatite. In addition, a large amount of collector renders it for adsorption at the surfaces of other mineral particles hence increasing the flotation of impurities [19].
It was estimated that recovery of the valuable component rose steeply with an increase in collector consumption and pH value, especially in the range of 60-100 g/t. At low values of collector consumption in the alkaline medium, recovery increased. The minimum values of recovery and P2O5 grade were obtained at a lower consumption of the collector and a higher consumption of the depressant. This may be explained by the fact that there is not enough collector to cover all mineral surfaces and to make them hydrophobic, hence most valuable minerals do not pass into the froth product and remain in the tailing instead [14].
The optimal values of recovery (73.2 %) and grade (26.8 %) were obtained at centered parameters – collector and depressant consumption, pH value – when recovery and grade were considered simultaneously.
Table 1
Flotation of magmatic phosphate ore at various operating parameters
Collector consumption, g/t |
Depressant consumption, g/t |
pH |
P2O5 grade, % |
P2O5 recovery, % |
140 |
200 |
10.25 |
25.20 |
73.82 |
100 |
300 |
11.00 |
26.60 |
71.40 |
100 |
500 |
9.50 |
18.49 |
15.23 |
100 |
300 |
10.25 |
26.80 |
73.20 |
60 |
300 |
11.00 |
28.75 |
69.5 |
100 |
500 |
11.00 |
26.57 |
71.39 |
140 |
300 |
11.00 |
26.00 |
67.40 |
60 |
500 |
10.25 |
22.13 |
25.94 |
140 |
500 |
10.25 |
27.70 |
65.91 |
140 |
300 |
9.50 |
23.95 |
71.78 |
60 |
100 |
10.25 |
25.78 |
66.00 |
60 |
300 |
9.50 |
17.90 |
13.45 |
140 |
100 |
10.25 |
22.05 |
65.33 |
100 |
100 |
11.00 |
23.32 |
67.17 |
100 |
100 |
9.50 |
19.95 |
51.99 |
100 |
500 |
10.25 |
25.39 |
52.12 |
140 |
500 |
11.00 |
26.00 |
71.18 |
100 |
100 |
10.25 |
24.18 |
69.40 |
140 |
300 |
10.25 |
26.30 |
70.60 |
Influence of grinding duration on P2O5 recovery
Further experiments were carried out on a coarser material (–250 µm), with different grinding duration for different weighed portions. The results demonstrated (Fig. 4) that during the flotation of magmatic phosphate ore, a decrease in grinding fineness as a result of grinding for a long grind time was accompanied by a decrease in both recovery and grade of P2O5. The reason for this was the excessive presence of slime, which negatively affected the selectivity and quality of flotation concentrates [34].
Influence of non-ionic surfactants on the flotation
Research shows that the addition of non-ionic surfactants improves the flotation process due to interaction with fatty acids. Some examples of surfactant mixtures used in the flotation of sparingly soluble ores were arranged in a table in paper [33].
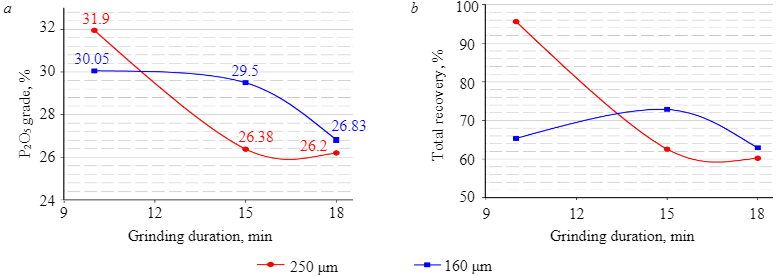
Fig.4. Influence of grinding duration on P2O5 grade (a) and recovery (b)
To better understand the effect of mixing various non-ionic surfactants with tall oil during phosphate ore flotation, the ore was initially subjected to the main (rougher) flotation, with the consumption of the collector (TOFAPh or TOFAOEID), sodium silicate and pH at the level of 100, 300 g/t and 10.25, respectively. The tailings from the rougher flotation were fed to the cleaner flotation with addition of 50 g/t of the collector. The froth product after the rougher flotation was cleaned in two stages with addition of 100 g/t of sodium silicate in the first stage. The results show (Table 2) that P2O5 grade and recovery to the concentrate increased due to the use of non-ionic surfactant in the collector mixture. Replacing phospholane (Ph) with a non-ionic reagent (OEID) allowed to obtain the product with a P2O5 grade of 33.09 % at the recovery of 96.82 %. Thus, a conclusion can be made that the use of TOFAOEID collector allowed to improve technological parameters.
Table 2
Flotation of magmatic phosphate ore with TOFAPh collector replaced by TOFAOEID
Collector |
Product |
Ratio of |
Grade, % |
Recovery, % |
||||
P2O5 |
Al2O3 |
SiO2 |
P2O5 |
Al2O3 |
SiO2 |
|||
TOFAPh |
Concentrate 2 |
27.05 |
36.6 |
2.85 |
5.69 |
91 |
3.88 |
4.71 |
Concentrate 1 |
4.25 |
7.88 |
15.18 |
31.70 |
3.08 |
3.24 |
4.12 |
|
Total concentrate |
31.3 |
32.7 |
4.53 |
9.22 |
94.08 |
7.12 |
8.83 |
|
Tailings |
68.7 |
0.94 |
26.93 |
43.39 |
5.92 |
92.88 |
91.17 |
|
Feed sample |
100 |
10.88 |
19.92 |
32.70 |
100 |
100 |
100 |
|
TOFAOEID |
Concentrate 2 |
27.43 |
36.9 |
2.10 |
3.63 |
93.03 |
3.05 |
3.72 |
Concentrate 1 |
4.4 |
9.37 |
8.19 |
15.6 |
3.79 |
2.1 |
2.08 |
|
Total concentrate |
31.83 |
33.09 |
2.94 |
5.29 |
96.82 |
5.15 |
5.8 |
|
Tailings |
68.17 |
0.6 |
27.85 |
45.5 |
3.18 |
94.85 |
94.2 |
|
Feed sample |
100 |
10.88 |
19.92 |
32.70 |
100 |
100 |
100 |
Influence of soda ash on technological parameters of the flotation of magmatic phosphate ore. It is understood that the greatest influence on the flotation process is exerted by calcium and carbonate ions. Figure 5 presents a dependence of P2O5 grade and recovery to the cleaner concentrate on the consumption of soda ash.
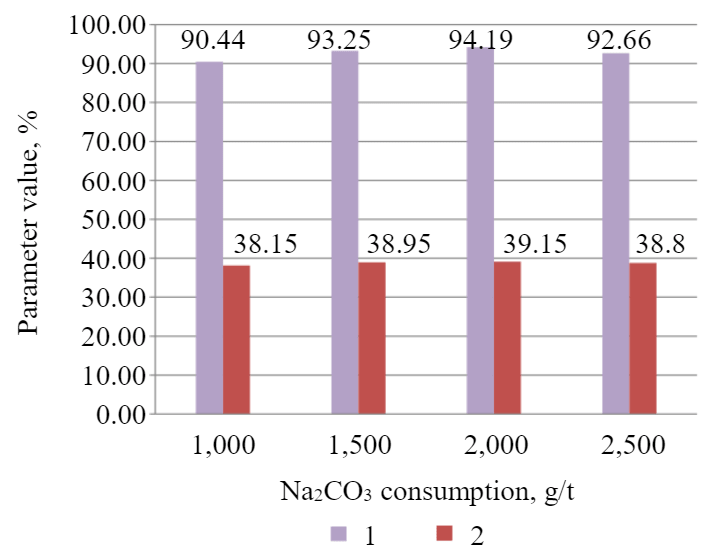
Fig.5. Dependence of P2O5 grade (1) and recovery (2) to the concentrate of cleaner flotation on soda ash consumption
It was identified that the addition of soda to compensate for the influence of calcium cations demonstrated a positive effect. With the addition of 2,000 g/t of Na2CO3, a concentrate was obtained with the grade and recovery of phosphorus pentoxide equal to 39.15 and 94.19 %, respectively.
Flotation of nepheline ore
Experiments to obtain nepheline concentrate were carried out on the flotation tailings of magmatic phosphate ore under the following initial conditions: pH value = 4.8, cationic collector used as a collecting agent (labeled as IP-1), and sodium fluorosilicate used as a nepheline activator.
Influence of activator consumption on the process of nepheline flotation. One of the factors affecting nepheline recovery to the froth product is activator consumption. In the experiments performed, activator consumption varied from 4 to 7 kg/t under constant conditions. The results of the flotation experiments are presented in Table 3. The highest technological parameters
for Al2O3 grade (28.94 %) and recovery to the froth product (86.65 %) were obtained at activator consumption of 6 kg/t.
Table 3
Influence of activator consumption of the flotation process
Activator consumption, kg/t |
Concentration ratio, % |
Al2O3 grade, % |
Al2O3 recovery, % |
4 |
75.89 |
28.24 |
76.93 |
5 |
77.01 |
28.30 |
78.22 |
6 |
83.42 |
28.94 |
86.65 |
7 |
81.19 |
28.32 |
73.07 |
Feed ore |
100 |
27.86 |
100 |
Influence of increase in collector consumption on the process of nepheline flotation. Within the scope of this study, consumption of the collector IP-1 for the main and preliminary flotation was increased from 150 to 200 g/t. In the first experiment, the consumption was increased in preliminary flotation, in the second – in the main one. The activator consumption was 6 kg/t.
The results of the flotation experiment are presented in Table 4. With an increase of the consumption in the main flotation up to 150 g/t, Al2O3 grade in the froth product is observed to rise to 29.55 %. As for the concentration rate and recovery, their values are slightly lower than those obtained at collector consumption of 100 g/t in the main and preliminary flotation. However, it should be taken into account that K2O and Na2O grades are higher in the first scenario of collector consumption and amount to 9.12 and 12.21 %, respectively. Obtained indicators of flotation processing comply with the technical standard TU 2111-28-00203938-93 “Nepheline concentrate”.
Table4
Influence of increase in collector consumption on the process of nepheline flotation
IP-1 consumption |
Product |
Concentration ratio, % |
Grade, % |
Recovery, % |
|||||||
preliminary |
main |
AL2O3 |
К2O |
Na2O |
SiO2 |
AL2O3 |
К2O |
Na2O |
SiO2 |
||
50 |
100 |
Froth product |
|
|
|
|
|
|
|
|
|
|
|
Preliminary flotation |
2.33 |
24.99 |
8.15 |
10.60 |
42.77 |
2.09 |
2.44 |
2.13 |
2.19 |
Main flotation |
83.42 |
28.94 |
8.4 |
11.85 |
42.6 |
86.65 |
87.16 |
85.22 |
78.09 |
||
Chamber product |
14.25 |
21.99 |
5.87 |
10.30 |
62.98 |
11.25 |
10.41 |
12.65 |
19.72 |
||
Feed ore |
100 |
27.86 |
8.04 |
11.60 |
45.51 |
100 |
100 |
100 |
100 |
||
100 |
100 |
Froth product |
|
|
|
|
|
|
|
|
|
|
|
Preliminary flotation |
5.69 |
23.23 |
6.20 |
9.10 |
44.50 |
4.74 |
4.39 |
4.46 |
5.56 |
Main flotation |
83.46 |
29.48 |
9.08 |
12.10 |
42.60 |
88.31 |
94.26 |
87.06 |
78.12 |
||
Chamber product |
10.85 |
17.83 |
1.01 |
9.06 |
68.42 |
6.95 |
1.36 |
8.48 |
16.32 |
||
Feed ore |
100 |
27.86 |
8.04 |
11.60 |
45.51 |
100 |
100 |
100 |
100 |
||
50 |
150 |
Froth product |
|
|
|
|
|
|
|
|
|
|
|
Preliminary flotation |
1.97 |
24.80 |
8.61 |
8.70 |
43.75 |
1.75 |
2.11 |
1.48 |
1.89 |
Main flotation |
80.73 |
29.55 |
9.12 |
12.21 |
42.50 |
85.62 |
91.57 |
84.97 |
75.39 |
||
Chamber product |
17.31 |
20.32 |
2.94 |
9.08 |
59.75 |
12.63 |
6.32 |
13.55 |
22.72 |
||
Feed ore |
100 |
27.86 |
8.04 |
11.60 |
45.51 |
100 |
100 |
100 |
100 |
Flotation of sedimentary phosphate ore
Results of anionic flotation without preliminary desliming. With an increase in collector consumption, the P2O5 grade of the concentrate increases with a decrease in its recovery. A concentrate with the maximum P2O5 grade (25.7 %) and a recovery of 61.7 % was obtained at collector consumption of 1500 g/t and depressant consumption
of 500 g/t (Table 5).
It was identified that the flotation concentrate without preliminary desliming had low quality (insufficient for fertilizer production); therefore it was proposed to deslime the ore before flotation.
Table 5
Flotation without desliming
TOFAPh, g/t |
Sodium silicate, g/t |
P2O5 |
|
Grade, % |
Recovery, % |
||
500 |
500 |
22.7 |
83 |
1,000 |
500 |
23.4 |
58 |
1,500 |
500 |
25.7 |
61.7 |
1,500 |
1,000 |
23.1 |
59 |
1,500 |
1,500 |
24.6 |
79 |
Attrition and desliming of the ore. As a rule, collectors are sensitive to the presence of slime in the ore [2, 3, 9]. Clay minerals of ultrafine size can cover ore particles and prevent the attachment of bubbles to valuable mineral particles, which reduces flotation efficiency [26, 28]. Clay consumes large amounts of flotation reagent and significantly decreases the efficiency of separation. Hence, the sample was subjected to washing and attrition/desliming to remove fine clay minerals. The results of attrition followed by desliming in the class of –53 μm are presented in Table 6. Due to removal of such impurities as SO3, Fe2O3 and SiO2 in the coarse fraction (–250 +53), a high grade of P2O5 (27.97 %) is observed at the recovery of 72.1 %. The majority of silicates (SiO2) pass into the fine fraction (–53 μm), and therefore, ore desliming is a necessary operation before the flotation.
Table 6
Desliming on the screen ( –53 μm)
Fraction, μm |
Concentration ratio, % |
P2O5 |
SiO2 |
SO3 |
CaO |
Fe2O3 |
||||||
% |
R |
% |
*R |
% |
R |
% |
R |
% |
R |
|||
–250 +53 |
58 |
27.97 |
72.1 |
3.28 |
18.29 |
6.86 |
41.88 |
54.1 |
67.62 |
3.6 |
49.71 |
|
–53 |
42 |
14.94 |
27.9 |
20.23 |
81.71 |
13.14 |
58.12 |
35.76 |
32.37 |
5.02 |
50.29 |
|
Feed ore |
100 |
22.5 |
100 |
10.4 |
100 |
9.5 |
100 |
46.4 |
100 |
4.2 |
100 |
Note. *R stands for recovery.
Reverse flotation using anionic collector. In order to improve flotation of the carbonate, anionic reverse flotation in acidic media was proposed. The depression action of phosphate mineral in acidic media is probably due to the adsorption (or formation) of aqueous CaHPO4 on its surface. This phenomenon prevents the adsorption of surfactant ions on the surface of phosphate particles [15, 17].
A coarse-grained fraction –250 +53 µm of sedimentary phosphate ore was used as feed sample for the flotation. STPP was used as a P2O5 depressant at constant pH= 6.
The results showed that the P2O5 grade gradually went up with an increase in depressant consumption (STPP). The P2O5 recovery decreased slightly due to an increase in its grade. The maximum P2O5 grade (30.1 %), at the recovery of 90.6 %, was obtained in the chamber product at collector consumption of 2,000 g/t (TOFAPh) and depressant consumption of 1,500 g/t (STPP) (Table 7).
Table 7
Influence of collector and depressant on technological parameters of reverse P2O5 flotation
Collector |
Depressant |
Concentration ratio, % |
Grade, % |
Recovery, % |
||||
P2O5 |
SO3 |
SiO2 |
P2O5 |
SO3 |
SiO2 |
|||
1,000 |
1,500 |
88 |
29.2 |
6.24 |
3.05 |
91.8 |
80.04 |
81.8 |
1,500 |
1,000 |
90.6 |
28.79 |
6.27 |
3.10 |
93.2 |
82.8 |
85.6 |
1,500 |
500 |
88 |
28.45 |
5.95 |
3.25 |
89.5 |
76.3 |
87.1 |
1,500 |
1,500 |
85.4 |
29.73 |
5.64 |
3.21 |
90.7 |
70.21 |
83.5 |
2,000 |
1,500 |
84.2 |
30.1 |
6.07 |
3.24 |
90.6 |
74.5 |
83.1 |
Results of reverse flotation using cationic collector. It is a known fact that amines are effective flotation reagents for silicate separation in all pH ranges.
Figures 6, 7 demonstrate the results of reverse flotation with and without using STPP as a P2O5 depressant at pH = 6.
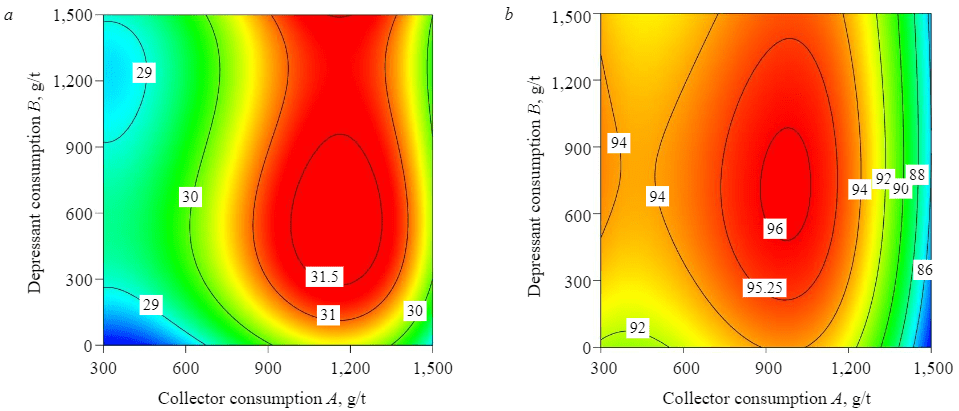
Fig.6. Consumption levels of amine and STPP per P2O5 grade (a) and recovery (b)
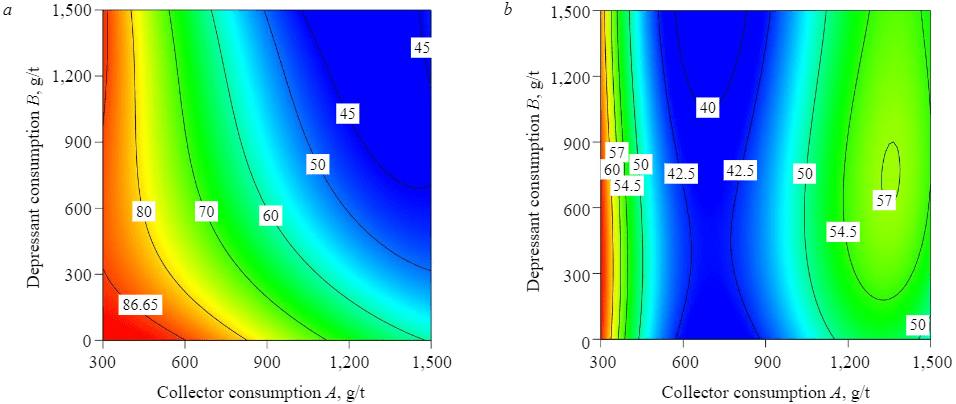
Fig.7. Consumption levels of amine and STPP per recovery of SiO2 (a) and SO3 (b)
It is obvious that the use of amine as a collector without using STPP as a depressant has a positive effect on the separation of quartz and gypsum. The separation of quartz (SiO2) proceeds efficiently with an increase in amine consumption, whereas the separation of gypsum deteriorates with an increase in amine consumption above 900 g/t. The maximum P2O5 recovery (93.91 %) and grade (29.85 %) were obtained at amine consumption of 900 g/t.
With the use of STPP, the grade and recovery of P2O5 gradually go up with an increase in collector consumption up to 900 g/t. An increase in collector consumption above 900 g/t sharply reduces P2O5 recovery and grade. Out of all the different considered levels of collector and depressant consumption, the best result is obtained at the amine consumption of 900 g/t and STPP consumption of 500 g/t – a concentrate with the P2O5 grade of 31.31 % and the recovery of 96 %.
The addition of STPP also affects the recovery of quartz. At amine consumption of 900 g/t, the SiO2 recovery in the chamber product decreased from 80.7 % at the grade of 3.01 % without using STPP to 52.03 % at the grade of 1.99 % (with the addition of 1,500 g/t of STPP). At the collector consumption of 1,500 g/t of amine and depressant consumption of 1,500 g/t of STPP, the grade of quartz in the chamber product reached its minimum (SiO2 recovery of 45.14 % at the grade of 1.86 %).
The quadratic model, obtained for predicting the response variables, can be expressed in the following equations:
P2O5 grade = 27.87 + 8.246∙10–3A ‒ 1.8959∙10–3 B ‒ 4.1029∙10–6A2 + 8.517∙10–7B2.
P2O5 recovery = 88.567 + 2.094∙10–2A ‒ 1.5925∙10–5A2.
SiO2 grade = 4.284 ‒ 3.2369∙10–3A ‒ 4.697∙10–4 B + 1.264∙10–6A2 + 2.0069∙10–7B2.
SiO2 recovery = 117.29 ‒ 9.367∙10–2A ‒ 7.4689∙10–3 B + 3.386∙10–5A2.
SO3 grade = 6.486 ‒ 6.856∙10–3A + 3.174∙10–4 B + 3.648∙10–6A2 ‒ 2.662∙10–7B2 + 1.5000∙10–7AB.
SO3 recovery = 88.14 ‒ 8.434∙10–2A ‒ 2.6846∙10–3 B + 4.1029∙10–5A2,
where А is the consumption of the collector (amine), g/t; В is the consumption of the depressant (STPP), g/t.
Analysis of the statistical plan showed that the maximum grade of the valuable component in the concentrate (P2O5 = 31.23 %) at the recovery of 95.22 % was obtained in the chamber product at amine consumption of 950.88 g/t and STPP consumption of 500 g/t.
Conclusions
The paper presents flotation results for two types of phosphate ores of different origin. Statistical analysis was used to study the effect of operating parameters on the efficiency of separating gangue minerals and the valuable components.
It was identified that to obtain commercial concentrate from magmatic phosphate ores, the main (rougher) flotation should be followed by two cleaner and one scavenger flotation stages. At the main flotation stage, high recovery and grade of P2O5 were achieved at average values of collector consumption (100 g/t), depressant consumption (300 g/t) and pH of 10.25. It was proven that addition of non-ionic surfactants (OEID) increased flotation efficiency of magmatic phosphate ores. The maximum P2O5 grade (33.09 %) at total recovery of 96.82 % was achieved from low-quality raw materials, containing 10.88 %
of P2O5, with the use of OEID, which would not be obtained in the flotation using only ionic surfactants.
The paper examines the influence of soda ash on the technological parameters of P2O5 flotation. It was estimated that the optimal value of soda consumption was 2,000 g/t. At the given consumption, the P2O5 grade in the concentrate is at its maximum and reaches 39.15 at the recovery of 94.19 %.
Moreover, the study addressed nepheline flotation from the tailings of magmatic phosphate ore flotation. The best result was achieved at pH = 4.80, activator consumption of 6 kg/t, consumption of the cationic collector IP-1 50 g/t in the preliminary flotation and 100 g/t in the main one. Obtained indicators of flotation processing comply with the technical standard TU 2111-28-00203938-93 “Nepheline concentrate”.
A method of desliming with subsequent anionic or cationic reverse flotation was proposed for processing sedimentary phosphate ores. Desliming allowed to remove clay particles that had a negative effect on the flotation process. A high grade of P2O5 (27.97 %) at the recovery of 72.1 % was obtained in the coarse fraction (+53 μm) by means of scrubbing followed by desliming. As a result, the majority of quartz and gypsum was found in the fine fraction (–53 µm).
Anionic flotation using a mixture of tall oil and STPP demonstrated that STPP selectively depressed phosphate ore. The maximum P2O5 grade (30.1 %) at the recovery of 90.6 % was obtained in the chamber product using 2,000 g/t of the collector and 1,500 g/t of the depressant. Cationic reverse flotation using amine as a collector showed that with an increase in amine consumption, the quartz grade in the chamber product decreased. The maximum P2O5 grade (31.31%) at the recovery of 96 % was obtained in the chamber product using 900 g/t of the collector (amine) and 500 g/t of the depressant (STPP).
Obtained phosphorus-bearing concentrates can be used in the production of fertilizers and phosphoric acid.
References
- Gurev A.A. Sustainable development of crude ore resources and benefication facilities of JSC “Apatit” based on best engineering solutions. Journal of Mining Institute. 2017. Vol. 228, p. 662-673. DOI: 10.25515/PMI.2017.6.662
- Ivanik S.A., Ilyukhin D.A. Flotation extraction of elemental sulfur from gold-bearing cakes. Journal of Mining Institute. 2020. Vol. 242, p. 202-208. DOI: 10.31897/PMI.2020.2.202
- Kuskov V.B., Kuskova Ya.V. The amderminskoye deposit fluorite ores gravity concentration. Obogashchenie Rud. 2017. Vol. 6. N 327, p. 20-25. DOI: 10.17580/or.2017.06.04 (in Russian).
- Cheban A.Y. Engineering of Complex Structure Apatite Deposits and Excavating-Sorting Equipment for Its Implementation. Journal of Mining Institute. 2019. Vol. 238, p. 399-404. DOI: 10.31897/PMI.2019.4.399
- Alattar A.L., Bazhin V.Y. Al–Cu–B4C Composite Materials for the Production of High-Strength Billets. Metallurgist. 2020. Vol. 64. N5, p. 566-573. DOI: 10.1007/s11015-020-01028-2
- Aleksandrova T., Elbendari A., Nikolaeva N. Beneficiation of a low-grade phosphate ore using a reverse flotation technique. Mineral Processing and Extractive Metallurgy Review. 2020, p. 1-6. DOI: 10.1080/08827508.2020.1806834
- Alsafasfeh A., Alagha L. Recovery of phosphate minerals from plant tailings using direct froth flotation. Minerals. 2017. Vol. 7(8), p. 145. DOI: 10.3390/min7080145
- Al-Thyabat S. Evaluation of mechanical flotation of non-slimed Jordanian siliceous phosphate. Arabian Journal for Science and Engineering. 2012. Vol. 37. N 4, p. 877-887. DOI: 10.1007/s13369-012-0235-0
- Amer A.E., Lebedev V.A. Numerical Investigations on Latent Heat Storage Unit using Phase Change Material. Journal of Physics: Conference Series. 2020. Vol. 1565. N 012099. DOI: 10.1088/1742-6596/1565/1/012099
- Lavrinenko A.A., Shrader E.A., Kharchikov A.N., Kunilova I.V. Apatite flotation from brazilite-apatite-magnetite ore. Journal of Mining Science. 2013. Vol. 49. N 5, p. 811-818. DOI: 10.1134/S106273914905016X
- Oliveira de P., Mansur H., Mansur A. et al. Apatite flotation using pataua palm tree oil as collector. Journal of Materials Research and Technology. 2019. Vol. 8. Iss. 5, p. 4612-4619. DOI: 10.1016/j.jmrt.2019.08.005
- Lu Y.L., Liu D.W., Jia X.D. et al. A review on flotation process of scheelite. In Advanced Materials Research. 2014. Vol. 962, p. 388-392. DOI: 10.4028/www.scientific.net/AMR.962-965.388
- Baioumy H., Tada R. Origin of Late Cretaceous phosphorites in Egypt. Cretaceous Research. 2005. Vol. 26. Iss. 2, p. 261-275. DOI: 10.1016/j.cretres.2004.12.004
- Ruan Y., Zhang Z., Luo H. et al. Effects of metal ions on the flotation of apatite, dolomite and quartz. Minerals. 2018. Vol. 8(4), p. 141. DOI: 10.3390/min8040141
- Elbendary A., Aleksandrova T., Nikolaeva N. Influence of operating parameters on the flotation of the Khibiny Apatite-Nepheline Deposits. Journal of Materials Research and Technology. 2019. Vol.8. Iss. 6, p. 5080-5090. DOI: 10.1016/j.jmrt.2019.08.027
- El-Midany A.A., Arafat Y. Enhancing phosphate grade using oleic acid–sodium dodecyl sulfate mixtures. Chemical Engineering Communications. 2016. Vol. 203. Iss. 5, p. 660-665. DOI: 10.1080/00986445.2015.1078797
- El-Mofty S.E.D., El-Midany A. Calcite flotation in potassium oleate/potassium dihydrogen phosphate system. Journal of Surfactants and Detergents. 2015. Vol. 18. N5, p. 905-911. DOI: 10.1007/s11743-015-1707-5
- ElDeeb A.B., Brichkin V.N., Kurtenkov R.V., Bormotov I.S. Extraction of alumina from kaolin by a combination of pyro- and hydro-metallurgical processes. Applied Clay Science. 2019. Vol. 172, p. 146-154. DOI: 10.1016/j.clay.2019.03.008
- Santana R.C., Ribeiro J.A., Santos M.A. et al. Flotation of fine apatite ore using microbubbles. Separation and Purification Technology. 2012. Vol. 98, p. 402-409. DOI: 10.1016/j.seppur.2012.06.014
- Ibrahim S.S., Yassin K.E., Boulos T.R. Processing of an East Mediterranean phosphate ore sample by an integrated attrition scrubbing/classification scheme (part one). Separation Science and Technology. 2020. Vol.55. Iss. 5, p. 967-979. DOI: 10.1080/01496395.2019.1575413
- Issa B., Aleksandrova T.A. Processes of Extraction of Non-Ferrous and Precious Metals from Alternative Sources of Raw Materials. IOP Conference Series: Materials Science and Engineering. 2019. Vol. 582. N 012022. DOI: 10.1088/1757-899X/582/1/012022
- Kawatra S.K., Carlson J.T. Beneficiation of phosphate ore. Society for Mining, Metallurgy, and Exploration, 2013, p. 154.
- Liu L., Xue J., Zhu J. Removing fluorite and calcite from scheelite during flotation separation process with calcium-and sodium-containing reagents. EPD Congress. The Minerals, Metals & Materials Society. 2014. Vol. 2014, p. 431-439. DOI: 10.1002/9781118889664.ch52
- Lvov V.V., Chitalov L.S. Comparison of the different ways of the ball Bond work index determining. International Journal of Mechanical Engineering and Technology. 2019. Vol. 10. Iss. 3, p. 1180-1194.
- Abou El-Anwar A.E., Mekky H.S., Abd El Rahim S.H., Aita S.K. Mineralogical, geochemical characteristics and origin of Late Cretaceous phosphorite in Duwi Formation (Geble Duwi Mine), Red Sea region, Egypt. Egyptian Journal of Petroleum. 2017. Vol. 26. Iss. 1, p. 157-169. DOI:10.1016/j.ejpe.2016.01.004
- Rahman A., Khodadadi D.A., Mahmoud A., Maoming F. Nano-microbubble flotation of fine and ultrafine chalcopyrite particles. International Journal of Mining Science and Technology. 2014. Vol. 24. Iss. 4, p. 559-566. DOI: 10.1016/j.ijmst.2014.05.021
- Panda H. Handbook on tall oil rosin production. Processing and Utilization. Asia Pacific Business Press Inc., 2013, p.480.
- Kou J., G Xu., Tao D. et al. Phosphate Flotation Enhancement Using Clay Binder. Beneficiation of Phosphates: New Thought, New Technology, New Development. Society for Mining Metallurgy & Exploration, 2012, p. 335-342.
- Derhy M., Taha Y., Hakkou R., Benzaazoua M. Review of the Main Factors Affecting the Flotation of Phosphate Ores. Minerals. 2020. Vol. 10(12). N 1109. DOI: 10.3390/min10121109
- 30. Romashev A.O. Use of Additive Technologies to Optimize Design of Classifying Devices. IOP Conference Series: Materials Science and Engineering. 2019. Vol. 665. N 012009. DOI: 1088/1757-899X/665/1/012009
- Ruan Y., He D., Chi R. Review on beneficiation techniques and reagents used for phosphate ores. Minerals. 2019. Vol. 9(4), p. 253-271. DOI: 10.3390/min9040253
- Elbendari A., Aleksandrov A., Nikolaeva N., Afanasova A. Selective flotation of phosphorus-bearing ores. E3S Web of Conferences, 2020. Vol. 192, p. 1-8. DOI: 10.1051/e3sconf/202019202021
- Sis H., Chander S. Improving froth characteristics and flotation recovery of phosphate ores with nonionic surfactants. Minerals Engineering. 2003. Vol. 16. Iss. 7, p. 587-595. DOI: 10.1016/S0892-6875(03)00137-7
- Yuexian Y., Liqiang M., Mingli C., Qi L. Slime coatings in froth flotation: A review. Minerals Engineering. 2017. Vol. 114, p. 26-36. DOI: 10.1016/j.mineng.2017.09.002
- Filippova I.V., Filippov L.O., Duverger A., Severov V.V. Synergetic effect of a mixture of anionic and nonionic reagents: Ca mineral contrast separation by flotation at neutral pH. Minerals Engineering. 2014. Vol. 66-68, p. 135-144. DOI: 10.1016/j.mineng.2014.05.009
- Xu L., Hu Y., Tian J. et al. Synergistic effect of mixed cationic/anionic collectors on flotation and adsorption of muscovite. Colloids and Surfaces A: Physicochemical and Engineering Aspects. 2016. Vol. 492, p. 181-189. DOI: 10.1016/j.colsurfa.2015.11.003
- Zhang P., Snow R. Evaluation of phosphate depressants in the phosphate/silica system. Minerals & Metallurgical Processing. 2009. Vol. 26. N 2, p. 101-104. DOI: 10.1007/BF03403425