Justification and selection of design parameters of the eccentric gear mechanism of the piston lubrication and filling unit for the mining machines maintenance
Abstract
Piston pumps are widely used in the lubrication systems of mining machines. When carrying out technical maintenance (MOT), including lubrication and filling works, at the site of operation of mining machines due to the remoteness from repair shops and warehouses of fuels and lubricants (FAL), mobile repair shops ( MRS), maintenance units (MU) and mechanized filling units (MFU) are used. The specificity of carrying out maintenance is to create conditions for the supply of oils, working fluids and lubricants to the corresponding systems of mining machines for their refueling. Existing piston pumps and pumping units, as a rule, are single-flow, and the piston is driven by a crank mechanism driven from the engine through a worm gear. The emergence of unique, hydraulic, low-mobility mining machines in open pit mining required a significant increase in the power of the MU and MFU oil pumping units, primarily for greases. However, the traditional design of the drive design of a crank-type piston pump unit at a power of over 80 kW does not allow achieving the specified operating time, it is accompanied by intensive wear of the drive elements and increased dynamics during operation. In addition, it is necessary to apply various designs of pumping units for the supply of liquid and grease lubricants. Thus, it is necessary to develop new circuit solutions for pumping units of the crank type, to improve mobile refueling facilities with a modernized design of the pump unit drive of the mobile lubrication and filling station MRS.
Introduction
Sustainable development of enterprises of the mineral resource complex is of great importance, since it largely determines the socio-economic situation of the country [28, 41]. The priority for the development of the global mining industry remains a steady focus on open pit mining, which ensures high economic performance [4]. The global trend in the development of mining is mainly determined by the extraction of raw materials by the open method, due to the best economic indicators [32].
Comprehensive improvement of opencast mining has become the main direction of scientific and technological progress in mining: new technologies are being developed and introduced, with the help of which “smart” deposits are created; in the extraction and transportation of minerals, a huge number of powerful and super-powerful mining machines and quarry equipment are used, which are operated in extreme and difficult climatic conditions; the main processes in production are automated, etc. [16, 17, 38]. An automatic centralized lubrication system (ACLS), which provides accurate metering of the required amount of lubricant into friction units and friction joints, has become a complete set of new open-cut machines everywhere [14, 37, 20]. It has been experimentally proven that the friction of the main units of modern mining equipment operating under high loads can only decrease with continuous lubrication [27, 42]. Regular manual lubrication of a large number of points leads to downtime of mining machinery and equipment. The lubricant is supplied in excess or in insufficient amount, as a result of which the efficiency of the lubrication process of the units does not reach the specified level [39, 42]. For example, 80 % of bearing failures are due to inadequate lubrication and contamination of the lubricant. [13]. ACLS allows you to minimize wear, reduce the cost of fuels and lubricants, increase operational readiness and reduce the risk of failure of mining machines, has a number of advantages over manual lubrication [1, 10, 11].
However, with an increase in productivity, as well as working pressure during the transportation of oils and lubricants through oil pipelines when refueling lubrication systems of mining machines, the issues of innovative circuit solutions of pumping lubrication units, scientifically substantiated technical solutions for the implementation, in particular, of the gear-eccentric drive of the unit, have not been resolved. The ecological and rational use of lubricants requires improving the system of maintenance and repair of mining machines with the possibility of saving these types of resources, which requires additional theoretical and experimental research in the field of substantiation and selection of design and circuit solutions for the gear-eccentric drive of a mobile lubricating and filling unit maintenance of mining machines in open pits [3, 19, 34].
Formulation of problem
Reciprocating pumps or pumping units are widely used in the mining industry and provide process reliability in the industry [2, 5, 21]. Adjustment of these types of pumps on experimental stands at manufacturing plants or in the field is a rather complex and costly research work affecting the design and implementation stages. Piston-type pumping equipment is distinguished by a variety of design features [9, 12, 29]. In the course of the design and selection of piston pumps for various fields of application, the role of mathematical models and applied techniques significantly increases, which would make it possible to predict structural changes in the parameters of pumps. From the point of view of practice, of greater interest are models that allow an in-depth study of the working processes occurring in the pumps.
The peculiarities of the pumping equipment operation with a metered supply of lubricants
to the lubrication system of a mining machine or quarry equipment are studied mainly through complex physical experiments. At the same time, part of the possible operating conditions of piston pumps is extremely difficult or almost impossible to simulate at the stand. For example, the relationship between the pump's working processes and the geometric parameters of the mechanisms for converting the movement of the piston stroke from rotary to reciprocating remains poorly understood. Possible modernization of existing piston pumps used in an automatic centralized lubrication system, namely when filling the system with grease lubricants, requires large expenditures for carrying out work to create new improved designs with increased requirements for the reliability of pumping units [7, 8, 31].
It is necessary to note the existing mobile repair shops, which are used when carrying out lubrication and refueling operations on mining machines without interrupting production due to the remoteness of mining deposits from repair and oil depots. They do not meet the technical parameters and technological equipment when performing refueling operations, do not take into account the specifics of maintenance and repair in the field: they have obsolete technological equipment, low productivity and the impossibility of creating working heads for pushing out greases, recycling of the used oils and implementation of the degree of purification of fuel and lubricants (FAL) issued to the consumer, etc. [6, 15, 33]. Based on this, it is necessary to improve the requirements for mobile refueling facilities and propose ways to solve them, one of which may be the modernization of the main installation of the mobile unit – a piston pump [35, 38].
Methodology
Ensuring the normal operation of the lubrication systems of mining machines is not the only problem of the reliable operation of equipment [40]. Centralized lubrication systems reguire refuelling, change cutting fluids, transmission lubricants, replenish with oil and fuels and lubricants (FAL) excavator, drilling, loading and haul-off equipment, characterized by low mobility, refuel, refuel and change working liquid hydraulic systems of mining machines [26, 42].
It is necessary to note the specifics of the operation of mining machines, namely, a significant distance from oil depots and repair and maintenance bases. It is much faster to carry out the necessary lubrication, filling and repair work on site – without spending time on transportation of equipment, while equipment failures, with rare exceptions, are eliminated at the place of machine operation by mobile repair teams in mobile repair shops (MRS) [9, 10].
Thus, the need for the use of mobile units for carrying out maintenance and repair measures directly at the site of operation of the mining machine increases [6, 22]. Such mobile units allow, without prejudice to mining operations, to reduce the workload of workshops, the period of preventive maintenance and repair measures, and to reduce the ineffective idle run of mining equipment to the places of centralized maintenance. They are used, among other things, for the transportation and use of special equipment at the scene of an accident or for carrying out preventive restoration work, they are distinguished by their high capacity, practicality, and the possibility of using even in difficult road and climatic conditions [15]. Mobile units are a set of equipment that provides comprehensive mechanization of work on lubrication and refueling of mining equipment with liquid oils, grease lubricators, fuel, water and air [5].
The installation kit includes pumps for supplying liquid oils and greases, drums with self-winding hoses, dispensing guns, an air-dispensing tip with a pressure gauge, as well as fittings for connecting pumps to drums and mounting pumps on containers with lubricants [15]. The central element of the installation is a pump that dispenses the required amount of lubricant in a metered manner in accordance with the lubrication or filling charts. Hydraulic pumps are designed for centralized lubrication systems, in particular for the distribution of metered doses of lubricant supplied to rubbing vapors, and can be used for lubrication systems of mining machines in quarries, as well as for other machines and mechanisms that require regular lubrication [25, 36].
An important feature of such reciprocating pumps – plunger and piston – is the ability to regulate the supply of lubricants without stopping working processes [29]. The improvement of pumps is currently continuing in the following directions:
- increasing requirements for tightness (protecting humans and the environment when dosing toxic liquids, ensuring safety when dosing explosive mixtures, saving when dosing expensive liquids or dosing liquids that must be protected from contact with air);
- reducing the dosing error (at the request of the technological process or for economic reasons);
- increasing the uniformity of the supply (the disadvantage, based on the principle of operation of the reciprocating pump, is the fluctuation of the supply within each cycle “suction – discharge”);
- increasing the efficiency of the pump and the pumping unit as a whole (often the pump operates in a constant mode and cost savings can be significant);
- increasing the reliability of the pump (increasing the service life of the components of the pumping unit, thereby increasing the operating time between failures) [35].
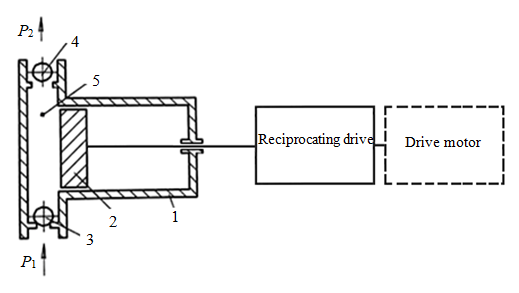
Fig.1. The structure of the piston lubrication and filling unit
In reciprocating pumps, the movement of the lubricator or fuel occurs due to the full stroke in the form of reciprocating movement of the piston (plunger) sealed in the cylinder. The structure of the pumping unit is shown in Fig.1. When the piston 2 moves in the cylinder of pump 1 to the right, the volume of the working chamber 5 increases, the pressure in it decreases and becomes less than the pressure in the inlet P1 and outlet P2 channels. The suction valve 3 opens, the discharge valve 4 closes, the fluid flows from the suction pipeline into the cylinder and fills its working space. When the piston moves to the left, the pressure in the working chamber increases, becomes greater than the values of P1 and P2, the suction valve closes, and the discharge valve opens. The entire volume of liquid contained in the cylinder is displaced into the pressure pipe. The working cycle ends.
The number of cycles (double strokes of the piston) per unit of time is selected based on the dynamics of fluid flow in the working part of the pump, is determined by its properties, the operation of the suction and discharge valves [33].
The described principle of operation of reciprocating pumps is implemented by constructions of various types, by the construction of the pump heads themselves and their drive mechanisms. Different drive types provide different dynamic characteristics of piston movement [1, 8].
The pump drive determines the dynamics of the dosing process in the pump heads and the liquid supply in the suction and discharge pipelines, the amount of dead volume in the dosing head when adjusting the length of the plunger stroke, the efficiency of the unit and its reliability.
Currently, pump drives with crank and eccentric mechanisms are used to convert the rotary motion of the drive motor into reciprocating movements of the slider [9, 30].
There are many methods of constructing mechanisms that provide regulation of the stroke length of the slider both when the pump is stopped and when it is running [30]. The task is to turn the drive eccentric at a given angle without stopping its rotational movement [21].
During the operation of worm gearboxes, high absolute values and an unfavorable direction of the sliding speed led to significant heating of the contact zone of the worm and the worm wheel, as a result of which the oil viscosity in this zone decreases and the friction coefficient increases, problems arise associated with low generated pressures and low productivity. An increase in pressure and productivity leads to intensive wear of the drive of the worm-crank assembly with the formation of a free stroke, the dynamics of wear increases and the durability of the pump decreases, the pump goes out of operation, which can cause the stoppage of objects for preparation and collection of lubricants, which in turn will lead to mining machines failures [1, 12].
A gear-eccentric drive with a deterministic complex movement of the drive and driven gears, responsible for the reciprocating movement of the piston, which provides the supply of oil under high pressure to the lubrication system during lubrication and filling operations for the maintenance of mining machines in open-pit mines is proposed [23].
Discussion
To convert the rotational motion of the crankshaft into a reciprocating linear movement of the piston in the proposed device, only two gears are used, which allows to simplify the design of the piston device, to ensure its compactness with the possibility of transferring significant forces to the piston and to increase the durability and reliability of the device [12, 24]. Installation of the first and second gearwheels with eccentricity relative to their centers of symmetry, namely, the axis of rotation of the crankshaft with the first gearwheel and the longitudinal axis of the crank element with the second gearwheel provides a complex rotational-translational movement of the centers of the gearwheels in the plane of their engagement.
The ability to rotate the eccentric and fix it in different angular positions relative to the crankshaft journal allows you to form the desired total eccentricity of the first gear wheel relative to the crankshaft rotation axis and thereby set the required piston stroke [24].
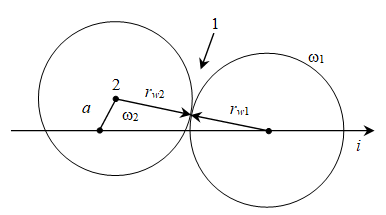
Fig.2. Scheme of a toothed-eccentric pumping drive unit rw1 = rw2, а = е
For a theoretical assessment of the motion laws of the piston of the toothed-eccentric pumping unit of the drive, let us determine how the piston stroke S depends on the angle of rotation of the driving gear φ. To do this, it is necessary to derive the motion law of the output shaft of a flat mechanism with a kinematic pair of the 4th class, to consider the plane-parallel motion of a rigid body (Fig.2).
The gearing provides rolling without sliding of a circle with a radius of rw1 and a circle with a radius of rw2. The speed at point 1, taking into account the absence of slippage, in the vector expression will be equal to:
where i, j, k – unit vectors of three-dimensional space.
Since point 2 moves along a straight line, we get:
Let us compose a system of equations for ω2 и v3:
The motion is flat, so the speeds, taking into account the projection, will be equal
By projecting (3) onto i, j, k, we will get:
Therefore, we have:
Thus, for a given position of the mechanism, the solution is obtained by substituting formulas (7)-(9) in (10).
The complex rotary-rocking motion includes the actual rotation of the wheels around their axes without slipping and the initial movement of the eccentrically located wheel along an arc within ± γ, the value of which is determined by the eccentricity of the driven wheel.
During operation, the driven eccentrically set wheel rotates with acceleration and deceleration, overcoming sections I-II and III-IV in the same time (Fig.3).
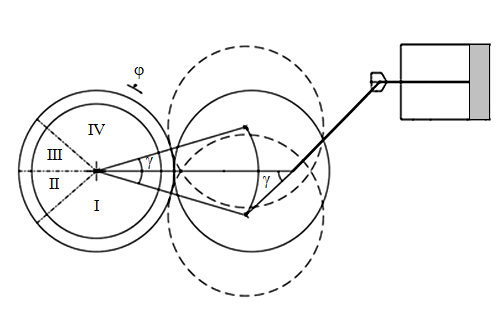
Fig.3. Trajectory of movement of characteristic points of the pumping mechanism of the pump with an eccentric toothed drive I – IV – modeling zones; φ – angle of rotation of the leader gear wheel; γ – swing angle of the driven wheel
After evaluating the trajectory of movement and deriving mathematical formulas describing the movement of two disks, the complete equation of movement of the piston movement for the diagram in Fig.3 is written in the form of the final formula:
where rw1and rw2 – the initial radius of the first and second gears; e2 – eccentricity of the driven gear; S – piston stroke.
To determine the local speed of the piston, we take the derivative with respect to φ:
We obtain the acceleration of the piston as a derivative of the speed:
Based on the law of motion of the piston, the stroke of the piston at a given value of the center distance depends on the eccentricity, as well as the swing angle γ of the driven gear
To prove the obtained conclusion, the graphs of the dependences of the piston stroke and the swing angle on the eccentricity, expressing the value of the eccentricity in the form of a dimensionless quantity as the numerical ratio of the eccentricity to the center distance can be plotted (Fig. 4, 5).
It is clearly seen from the graphs in Fig. 4, 5 that the piston stroke depends on the eccentricity, as well as on the angle of rotation of the driven gear. In the design of the proposed drive, to ensure the compactness of the designed pump, one should take into account the final maximum length of the crank, at which the maximum value of the geometric feed slightly increases and shifts the angle of rotation φ, at which the maximum feed is achieved.
To make sure that the theoretical calculations are correct, we will consider the second version of the conversion of the rotational motion of the gears into the reciprocating motion of the plunger with the realized variable gear ratio. For this purpose, a stand was assembled on the basis of the Department of Mechanical Engineering of the Saint Petersburg Mining University (Fig.6), consisting of from ordinary wheels with an involute tooth profile, having different axes of rotation, displaced by equal distances e with respect to the geometric centers. The main condition – constant center distance – is preserved.
In the course of the experiment, it was possible to simulate the initial positions of the gearing of the gear wheels, which make it possible to change the gear ratio with a constant center distance. Due to the change in the position of the initial engagement of the drive and driven wheels by an angle φ, the stroke of the plunger can be adjusted by changing the amount of eccentricity, thereby increasing or decreasing the supply of lubricants. The obtained experimental data were processed using a universal software system for finite element analysis of ANSYS. Figure 7 shows 2 of the 14 modeled possible positions.
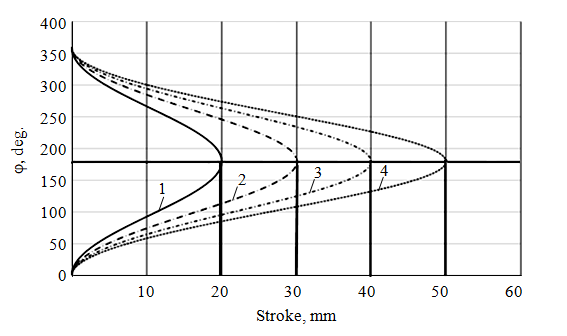
Fig.4. The dependence of the piston stroke on the angle of rotation of the crank 1 – 0.1; 2 – 0.66; 3 – 0.5; 4 – 0.4

Fig. 5. Changing the swing angle from the angle of rotation of the driving gear 1 – 0.1; 2 – 0.66; 3 – 0.5; 4 – 0.4
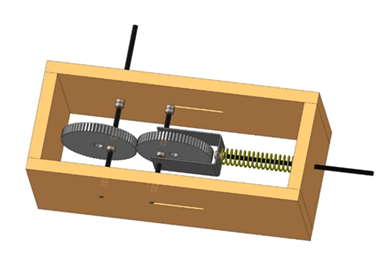
Fig.6. 3D model of the stand
The trajectories of the points on the root and top of the drive gear teeth marked in red in Fig.7 confirm the dependence of the piston stroke on the change in eccentricity. The possibility of turning the eccentric and fixing it in different angular positions allows you to form the desired total eccentricity and thereby set the required piston stroke, providing the necessary movement of the gear wheels. The pump, equipped with the proposed motion conversion mechanism, simplifies the design of the piston pump, its compactness with the possibility of transferring significant forces to the piston and increases the durability and reliability of the device.
Conclusion
In order to reduce the time and resources spent on the development and implementation of piston pumps, it is required to apply modern approaches to design everywhere, with the refinement and improvement of the methods of further bench tests. The development and application of new mathematical models for further changes in the design parameters of the pump can significantly reduce the cost of such types of work as design, experimental and commissioning, as well as reduce the time for the introduction of more advanced designs.
It has been theoretically proven and experimentally confirmed that the angle of rotation of the driving gear of the swinging unit of the toothed-eccentric drive of the pump lubrication and filling unit for maintenance of mining machines in open pits is a function of the angles of rotation and swing of the driven gear with an eccentrically located axis of rotation, which is a reciprocating motion with a deterministic asymmetric in absolute value half-periods of the forward and reverse cycle together with the piston of the pump unit, while the stroke of the latter is determined by the eccentricities of the installation of the driving and driven gears and the phase difference of their installation in the initial position of the pumping unit.
Simulation model of the process of functioning of the pumping unit of the toothed-eccentric drive of the pump lubrication and filling unit for the maintenance of mining machines of open pits, including the functions of deterministic changes in the values of parameters, phase difference and eccentricities of the driving and driven gears, and the geometric dimensions of the elements of the pumping unit , allows you to estimate the magnitude of the piston stroke, the change in its speed and acceleration.

Fig.7. Simulated operation of a toothed-eccentric mechanism in the AYSYS environment
The piston pump unit with an eccentric toothed drive, included in the MRS nomenclature, will allow refueling of the lubrication systems of mining machines directly at the place of their operation without losing time and resource for moving the machine to the places of maintenance. At the same time, the modernized pump unit can operate with lubricants of different density and fluidity – from greases to working fluids of hydraulic systems. Thus, such units can act as an effective alternative to pumping units with a crank mechanism, especially when it comes to powerful units. Pumps with a crank-connecting rod drive are effective when the installed engine power is up to 3-5 kW, with an increase in the power of existing pumping units, an increase in the load of the drive mechanism leads to intensive wear of the worm-crank assembly with the formation of a free stroke, which increases the dynamic component, leads to shock loading during the reverse course and, ultimately, a sharp intensification of degradation processes, a decrease in the resource. The proposed drive design is devoid of these drawbacks, since the eccentric gear transmission does not allow the teeth to open, is capable of transmitting significant forces, providing a deterministic reciprocating movement of the piston with the possibility of regulating its stroke and thereby supply without stopping the pump unit during lubrication and filling operations-within the framework of maintenance of mining machines in open pits and reducing the labor intensity of these works.
References
- Vlasov Yu.A., Spirin E.N., Lyapin A.N. et al. Analysis of the reasons of low operational reliability of career dump trucks. Scientific review. Technical sciences. 2016. N 5, p. 37-44 (in Russian).
- Borovkova I.I., Zaslavskii A.V., Kuzenkov N.V. Application of dosing pumps and pumping units Grundfos in the project of the Sochinskaya TPP. Energosberezhenie i vodopodgotovka. 2005. N 3, p. 68-70 (in Russian).
- Bules P.A. Ensuring the reliability of hydraulic mining excavators during their operation in open pit mines in Russia: Avtoref. dis. ... kand. tekhn. nauk. Natsionalnyi issledovatelskii tekhnologicheskii universitet “MISiS”. Moscow, 2016, p. 22 (in Russian).
- Velikanov V.S. Mining excavator working equipment load forecasting according to a fuzzy-logistic model. Journal of Mining Institute. 2020. Vol. 241, p. 29-36. DOI: 10.31897/pmi.2020.1.29
- Verzhansky A.P., Ostrovsky M.C., Mnatsakanian V.U. Modern Technology for Maintenance and Repair of Mining Machinery and Equipment. Mining informational and analytical bulletin (scientific and technical journal). 2014. N S1, p. 422-449 (in Russian).
- Gmyrya S.V. The relevance of the use of mobile mechanical repair workshops. News of the Tula state university. Sciences of Earth. 2015. N 6-1, p. 93-97 (in Russian).
- Gosman A.I. The use of a centralized lubrication system on the example of an EKG-10 excavator. Gornaya promyshlennost. 2007. N 3 (73), p. 42-43 (in Russian).
- Gosmann A.I., Eliseev E.V., Konovalov D.B. Lincoln automatic lubrication system for power shovels. Russian mining industry. 2010. N 5, p. 40-41 (in Russian).
- Zuev A.G., Dyachkov A.Yu. Dosing pumps: innovative developments. Neft. Gaz. Novatsii. 2010. N 9, p. 32-35 (in Russian).
- Ivanova P.V., Kuvshinkin S.Yu. The range of permissible values of the parameters of the working equipment of a mining excavator. Sbornik materialov V vserossiiskoi, 58 nauchno-prakticheskoi konferentsii molodykh uchenykh “Rossiya molodaya”, Kemerovo, 16-19 aprelya 2013. Kemerovo: Kuzbasskii gosudarstvennyi tekhnicheskii universitet, 2013. Vol. 1, p. 87-88 (in Russian).
- Ivanova P.V., Kuvshinkin S.Yu., Shibanov D.A. Fault tolerance assessment of modern open-pit excavators manufactured by IZ-KARTEX named after PG Korobkov. Innovatsii na transporte i v mashinostroenii: sbornik trudov IV mezhdunarodnoi nauchno-prakticheskoi konferentsii, 28-29 aprelya 2016. St. Peterburg: Natsionalnyi mineralno-syrevoi universitet “Gornyi”, 2016. Vol. 2, p. 157-159 (in Russian).
- Kazymova E.N.O., Golovanov O.A. Modernization of plunger pump for dispensing of toxic fluids. Computational nanotechnology. 2016. N 1, p. 63-73 (in Russian).
- Katanov B.A. Mining excavator reliability and ways to improve it. Vestnik Kuzbasskogo gosudarstvennogo tekhnicheskogo universiteta. 2003. N 5, p. 47-48 (in Russian).
- Katanov B.A. On the reliability of mining excavators. Gornyi informatsionno-analiticheskii byulleten. 2005. N 3, p. 88-91 (in Russian).
- Kvaginidze V.S., Koretskii V.B., Chupeikina N.N. Mobile repair shops in open pit mining. Gornyi informatsionno-analiticheskii byulleten. 2007. Vol. 17. N 3, p. 360-364 (in Russian).
- Kovalchuk S.N. Effect of operating conditions on wear intensity of mining machinery reducers. Bulletin of the Kuzbass State Technical University. 2012. N 1(89), p. 31-34 (in Russian).
- Kovshov S.V., Pasynkov A.V. Evaluation of dust emissions during transportation of rock mass at deposits developed open pit mine. News of the Tula state university. Sciences of Earth. 2020. N 2, p. 78-87 (in Russian).
- Shibanov D.A., Shishlyannikov D.I., Ivanova P.V., Ivanov S.L. Complex assessment of the factors defining an operating time of excavators EKG a new product line of “IZ-KARTEX”. Mining equipment and electromechanics. 2015. N 9(118), p. 3-9 (in Russian).
- Korneev S.V. Methodology for improving the system of maintenance of road, construction and hoisting-and-transport machines: Avtoref. dis. ... d-r tekhn. nauk. Omsk: Sibirskaya gosudarstvennaya avtomobilno-dorozhnaya akademiya, 2003, p. 34 (in Russian).
- Zagaynov M.A., Kostenkov E.A., Kuznetsov D.S. Lubrication of bearings as a way to prevent machine failure. International Journal of Humanities and Natural Sciences. 2019. Vol. 9-1, p. 72-75 (in Russian).
- Kuzenkov N.V. Drive designs for low capacity dozing pumps. Industrial Automatic Control Systems and Controllers. 2006. N 1, p. 35-37 (in Russian).
- Kurganov V.M., Gryaznov M.V., Kolobanov S.V. Assessment of operational reliability of quarry excavator-dump truck complexes. Journal of Mining Institute. 2020. Vol. 241, p. 10-21. DOI: 10.31897/pmi.2020
- Prozorov L.K., Garmash V.B., Lazovskii L.I., Gaevskaya O.I. Patent N 2333463 RF. A method for controlling and monitoring the performance of a plunger dosing pump and a device for its implementation. Publ. 10.09.2008. Bul. N 25 (in Russian).
- Sevastyanov A.V., Tretyakov R.S., Safronchuk K.A., Knyazkina V.I., Ivanov S.L. Patent N 2716521 RF. Pump piston device. Publ. 12.03.2020. Byul. N 8 (in Russian).
- Dolgushin A.A., Denisov A.A. Patent N 68646 U1 RF. Lubricant dispenser for centralized lubrication system. Publ. 27.11.2007 (in Russian).
- Pozhidaev Yu.A., Maltseva D.A., Balandyuk I.P. Method of lubrication of friction units of mechanical systems and control device of the lubrication system. Sbornik nauchnykh trudov 5-i Mezhdunarodnoi nauchno-prakticheskoi konferentsii “Tekhnika i tekhnologii: puti innovatsionnogo razvitiya”, 29-30 iyunya 2015, Kursk, Rossiya. Moscow: Universitetskaya kniga, 2015, p. 178-179 (in Russian).
- Shakhanov N.I., Varfolomeev I.A., Ershov E.V., Yudina O.V. Predicting equipment failures in conditions of a small number of breakdowns. Vestnik Cherepovetskogo gosudarstvennogo universiteta. 2016. N 6 (75), p. 36-41 (in Russian).
- Pronin E.M., Vasilev V.E., Tsvetkov V.Y. The factors defining the stability and sustainable development of mineral and raw materials enterprises and the factors’ influence оn the activity results evaluation. Journal of Mining Institute. 2011. Vol. 191, p. 176-182 (in Russian).
- Svechnikov A.N. Installation for lubrication of units and assemblies of machines. Molodezh i nauka. 2016. N 7, p. 140-140 (in Russian).
- Sevastyanov A.V. Improvement and modernization of dosing equipment. Ekspozitsiya Neft Gaz. 2015. N 1 (40), p. 23 (in Russian).
- Eliseev E.V., Pashentseva O.A., Gosman A.I., Konovalov D.B. Lubrication systems: effective wear reduction. Put i putevoe khozyaistvo. 2012. N 1, p. 5-9 (in Russian).
- Smirnov V.P., Lel Yu.I. The theory of open-pit heavy vehicles. Ekaterinburg: UrO RAN, 2002, p. 355 (in Russian).
- Khabardin V.N., Chubareva М.V., Khabardina А.V., Bazaron S.I. Modern systems of machines technical maintenance and their analysis. Vestnik IrGSHA. 2014. Vol. 65, p. 101-110 (in Russian).
- Ushakov Yu.Yu. Justification of the parameters of the system of maintenance and repair of mining dump trucks: Avtoref. dis. ... kand. tekhn. nauk. Yuzhno-Uralskii gosudarstvennyi universitet (natsionalnyi issledovatelskii universitet). Ekaterinburg, 2016, p. 24 (in Russian).
- Farnin E.P. The equipment for lubricating, cleaning and fueling operations in the system of corporate services. Molodezh' i nauka. 2017. N 6, p. 121-121 (in Russian).
- Khabardina A.V., Chubareva M.V. Lubrica-refueling service operations of machines and technical means of their execution in the field. Vestnik IrGSHA. 2017. N 78, p. 148-157 (in Russian).
- Charomsky A.A. Modern lubricant as a guarantee of effective operation of mining equipment. Ugol. 2016. N 11(1088), p. 19-21 (in Russian).
- Shibanov D.A. Prospects for improving the system of maintenance and repair of mining excavator produced by LLC “IZ-Karteks imeni P.G.Korobkova”. Perm Journal of Petroleum and Mining Engineering. 2013. N 8, p. 128-135. DOI: 10.15593/2224-9923/2013.8.14 (in Russian).
- Alekseeva L.B., Maksarov V.V. Evaluation of effect of oil film of rotor bearing. IOP Conference Series: Materials Science and Engineering. 2018. Vol. 327. Iss. 2. N 022003. DOI: 10.1088/1757-899X/327/2/022003
- Burge P. Overcoming industrial automation lubricant challenges using the right lubrication in the right application is critical and so is looking at technological advancements designed to reduce bearing wear and corrosion. URL (date of access 22.02.2021).
- Litvinenko V.S., Sergeev I.B. Innovations as a Factor in the Development of the Natural Resources Sector. Studies on Russian Economic Development. 2019. Vol. 30, p. 637-645. DOI: 10.1134 / S107570071906011X
- 42. Safronchuk K.A., Knyazkina V.I. Ivanov S.L. Mobile lubrication and filling units to reduce mining machines and equipment downtime when providing maintenance. International Conference on Mechanical Engineering, Automation and Control Systems, 12-14 December 2018, Novosibirsk, Russian Federation. IOP Conference Series: Materials Science and Engineering, 2019. Vol. 560. N 012088. DOI: 10.1088/1757-899X/560/1/012088