Physical and mathematical model of rock destruction by a milling machine cutter
- 1 — Ph.D., Dr.Sci. professor Pacific National University ▪ Orcid ▪ Elibrary ▪ Scopus
- 2 — Ph.D. associate professor Pacific National University ▪ Orcid ▪ Elibrary ▪ Scopus
Abstract
As a result of the analysis of the work on rock destruction by cutters of milling of machines, it was found that the existing developments do not allow us to proceed to the derivation of calculation d dependencies for determining fracture resistance, or can be used only in preliminary calculations of the known by design parameters of milling machines. To eliminate these disadvantages, a combined physical and mathematical model of the process of interaction of a single milling cutter with a spherical tip with the rock has been developed. Consideration of the physical picture of the action of forces and stresses acting from the cutter with spherical tips on the separating rock element in the limiting condition allowed to describe analytically the components of total resistance, which are the mathematical part of the physical and mathematical model of rock destruction by cutters. Analytical dependences for determining the tangential and normal components of fracture resistance of rocks of medium hardness have been obtained. The adequacy of the physical and mathematical model to the physical process of destruction of rocks of different hardness by cutters on a universal stand was tested both in the field and in the laboratory conditions. Technical evaluation of the results of experimental studies confirms the reliability of the developed physical and mathematical model.
Introduction
A great achievement in the development of non-blasting technologies of open-pit and underground mining is the creation of milling machines and combines capable of developing sufficiently hard rocks with a compressive strength of 50-80 MPa and more [11, 13]. In the case of rock development with Protodyakonov scale of hardness up to ƒ = 2, the cutters are equipped with wedge-shaped teeth (Fig.1, a), since with greater hardness their cutting edges break off and the tool begins to work inefficiently [9]. When breaking rocks with a hardness coefficient greater than ƒ = 2, the cutters used (Fig.1, b) with a spherical tip are used [8, 10]. Currently, manufacturers of milling machines and combines equip the working bodies of machines with cutters of this type [23]. This is due to a number of advantages of spherical cutters in comparison with wedge-shaped ones, including increased cutting depth, symmetrical wear, high reliability [24, 27, 41].
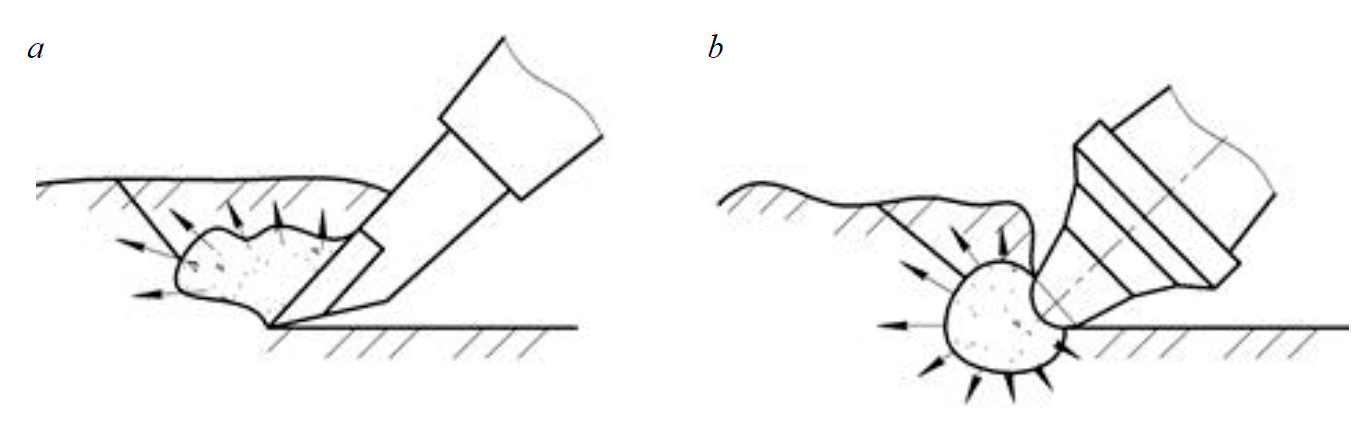
Fig.1. Scheme of interaction of a wedge-shaped cutter with a rock (a) and a spherical tip with a hard rock (b)
A large number of scientific works have been devoted to the process of destruction by a wedge-shaped tooth of frozen and thawed fine-grained rocks, including those with large-block inclusions [2-4]. There are physical and mathematical models [16, 19, 40] and reliable calculation dependences for determining the fracture resistance [17, 18, 39].
The process of interaction of a cutter with a spherical tip with a rock is complex and underexplored. There are scientific developments on modeling the process of rocks destruction by cutters with a spherical tip based on finite element methods [14, 22, 28, 30], discrete elements [34, 35, 37], finite differences [36]. These developments allow to represent the stresses distribution inside the rock from the pressure of the cutter, but do not make it possible to proceed to the conclusion of calculated dependencies for determining fracture resistances and to calculate the required torque on the milling working body and the required power on the cutter drive, as well as the entire machine in general.
The particular interest presents the concept of determining the parameters of a milling machine based on correlations between the hardness of the rock for uniaxial compression and fracture resistance [33, 38], as well as the required power and fuel consumption [14, 26]. Such a method can be used in preliminary calculations of parameters of the known by the design milling machines, but when creating new types of machines, refined dependencies are required to determine the fracture resistances of a single cutter, and, consequently, the required torque on the milling cutter, the required power, etc.
There are attempts to model the process of milling working bodies from a mathematical point of view [12, 32] without considering the physical nature of rock destruction by a cutter with a spherical tip. However, the obtained equations for determining the torques on the milling cutter [6, 7] without specifying the strength characteristics of the rock being developed by the cutters have no practical application.
Experimental studies of the destruction process with spherical-tipped cutters conducted in Australia [29, 31], as well as at the Institute of Coal SB RAS and Kuzbass State Technical University have a certain practical importance [1].
The regression equations obtained as a result of the experiments make it possible to determine the fracture resistance for a limited number of rocks on which the experiments were conducted.
It is necessary to highlight the mathematical model of rock destruction, which has a modified version that takes into account the wear of the cutter [21]. The model allows to determine the value of the cutting force on the radial cutter during the destruction of various types of rocks. The good convergence of the results of experimental studies with the results of theoretical modeling allows to conclude that the model is adequate. However, the proposed model has a number of assumptions: the rock mass is considered a homogeneous isotropic medium, the mutual influence of neighboring cutters on the process of the rock mass destruction (i.e., the cutting step) is not taken into account.
There is a known model of interaction of a cutter equipped with a spherical tip with a rock, which allows determining the value of the maximum resistance of the rock to destruction [20]. Despite the good convergence of the modeling results [25], the proposed model does not take into account the friction that inevitably occurs between the cutter and the rock. In addition, when developing the model, a simplification was made about the uniformity of the pressure distribution over the contact area of the cutting tool and the rock, which does not allow taking into account the elastic component of the destruction process.
A significant contribution to the study of the process of rock destruction was made by V.V.Neskromnykh and K.N.Borisov [5], who developed a scheme of destruction-chipping of rock with a drill bit cutter, and also revealed the role of the crumpling core on the tangent component of fracture resistance and proposed a simplified dependence for its determination through the chipping stress. With all the importance of the performed work, it should be noted that in the mechanics of a deformable solid, the concepts of chipping stress are not used. Compression, tensile, shear, and crumpling stresses are known. How and by what means to determine the chipping stress in practice is unknown. In addition, these researchers do not take into account the resistances associated with the advancement of the crumpling core in the rock mass, as well as friction along the dulling site [5]. It is difficult to fully apply the scheme (physical and mathematical model) of destruction-chipping to cutters with a spherical tip, since these cutters differ significantly from each other in terms of design features.
The analysis of scientific sources indicates the relevance of the development of a combined physical and mathematical model of the process of interaction with the rock of a single cutter with a spherical tip.
Methodology
Observations during numerous and long-term experimental studies at Pacific National University of the destruction process of frozen fine-grained, shale rocks, as well as concrete with cutters with wedge-shaped and spherical tips show that the cut bottom left by the cutter always has a smooth surface, and the separated pieces (elements) of the rock are uneven (torn). The surface unevenness of the separated rock elements indicates that, in the end, separation is due to breaking stresses. In front of the cutter, a crumpling core is formed in the lower part of the cut, which exerts pressure on the overlying rock layer and causes the separation of rock elements when the limiting state occurs. In the limiting state, the pressure from the crumpling core on the overlying rock layer is equal to the resistance of the upper layer separation. Figure 2 shows a schematic of the limiting state of interaction with the rock of a cutter with a spherical tip at the moment of the upper layer separation. This picture is actually a physical model of the process of rock destruction.
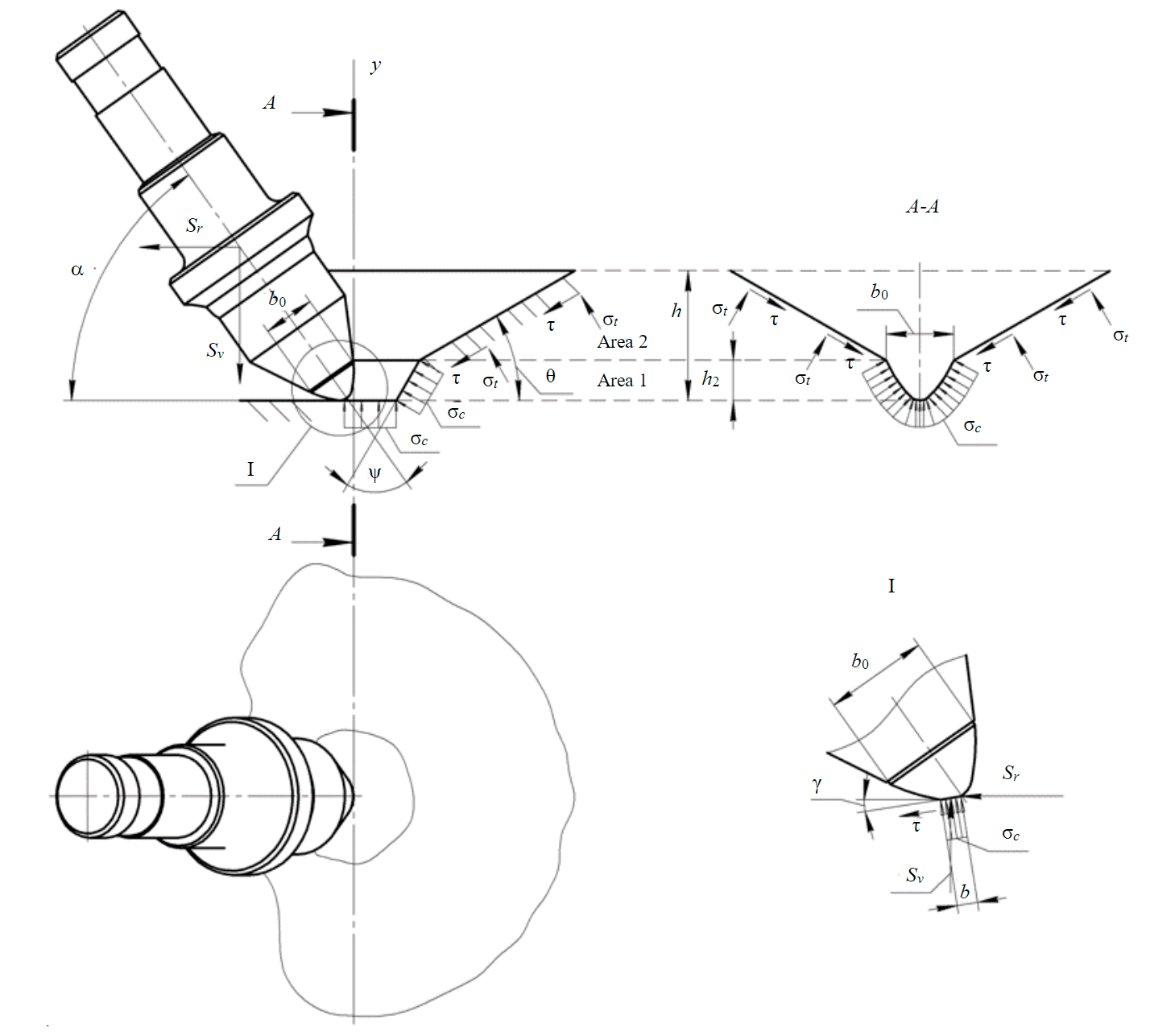
Fig.2. Physical picture of the action of forces and stresses from the cutter on the separated rock element in the limiting state
It is advisable to divide this scheme into two areas. The first area is the surface bounded by the crumpling core. The height of this area is h2, the width is limited by the lateral surfaces of the spherical tip, and at the bottom by the base of the crumpling core. The first area is shown in Fig.3, a, the second – the separation area – in Fig.3, b.
Consideration of the physical model of the destruction process shown in Fig.3 allows to proceed to the analytical determination of the components of the total resistance, namely, to the mathematical part of the overall combined model.
The horizontal component of the fracture resistance is the sum of the horizontal components in the first and second areas of the cut:
The normal component is
In turn,
where Sx1 is the horizontal component of the pressure on the frontal surface of the crumpling core.
If we select a semicircular strip with a width dt, on the frontal surface of the crumpling core, then the force acting perpendicular to the elementary site dF1 will be equal to
Horizontal projection
Full pressure on the frontal surface of the crumpling core
considering that h2/l = cosα2, l = h2/cosα2, after integration
The friction force of the crumpling core on the lower surface
where ƒ – rock-to-rock friction coefficient; r1 – the radius of the crumple core along its lower surface.
Tangential component of the friction force of the cutter at the dulling site (Fig.3, a)
where μ is the angle of friction of the rock on the steel; b is the diameter of the dulling site.
The normal component in area 2
where Sy1 – the force of pressure of crushing stresses on the frontal surface of the crumpling core; St – the pressure force of crushing stresses on the end surface of the crumpling core;
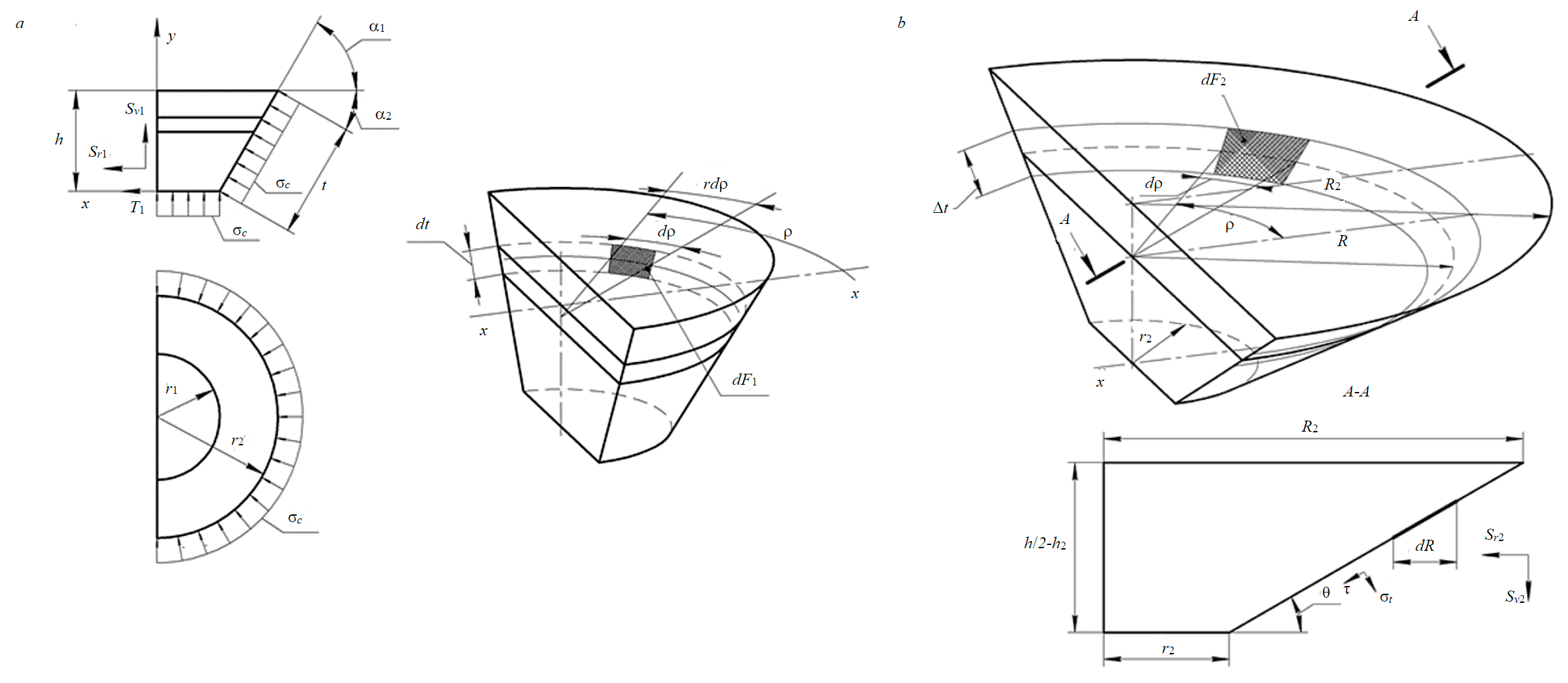
Fig.3. Diagrams of the action of forces and stresses in the limiting state on the separated rock element: a – the area of the crumpling core; b – the area of separation
The tangent component of the fracture resistance in area 2 (see Fig.2) can be determined by integrating normal σ and tangential τ stresses. The rock area 2 is half of a truncated cone. The height of the truncated cone is h – h2, and the angle of inclination of the separation surface is θ (Fig.3, b). If we select a strip of width dl on the separation surface with radius R, and denote an infinitesimal strip dF = dldrR on the strip, then the forces on this elementary site will be equal: in the horizontal direction
in the vertical direction
After integrating equations (14) and (15) on dr and dR we obtain
If we assume that r2 = b0/2, where b0 is the diameter of the cutter at the installation site of the solid-alloy tip, then
After substituting in (16) and (17) the integration limits, we obtain
By adding the components of the resistances in areas 1 and 2, as well as the resistances associated with dulling, the calculated dependences of the total resistance to the rock destruction by a cutter with a spherical tip are determined. Thus
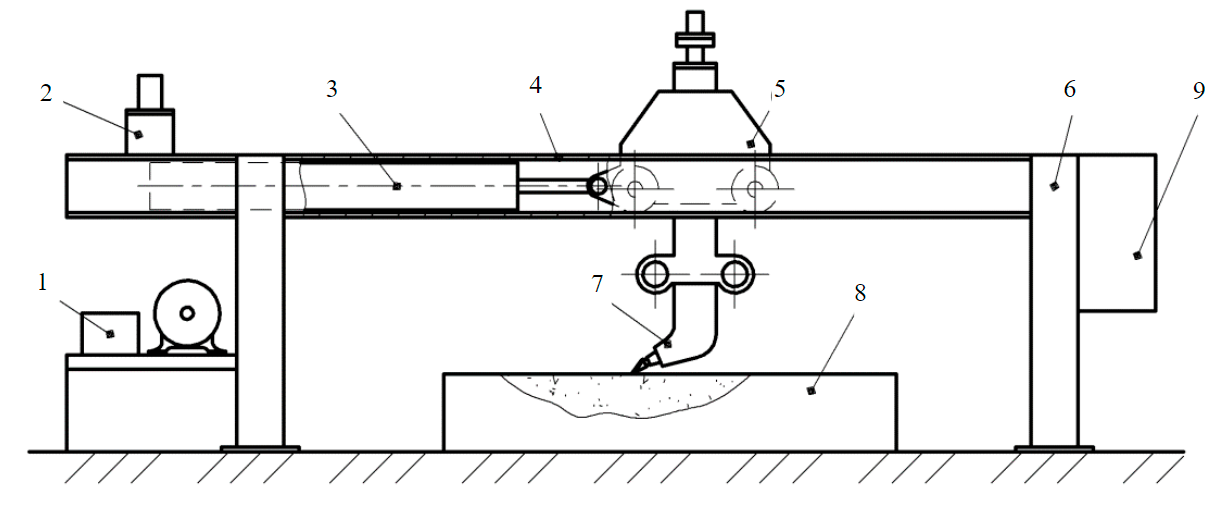
Fig.4. Rock destruction stand 1 – pumping station; 2 – hydraulic distributor; 3 – traction hydraulic cylinder; 4 – guide beams; 5 – support racks; 6 – strain gauge trolley; 7 – cutter; 8 – rock block; 9 – strain gauge equipment block
In order to test the functional dependencies (21), (22), which form the basis of the developed physical and mathematical model, for convergence with experimental values, experiments were conducted on the destruction of certain rocks and materials by the cutters of the Wirtgen 2600SM milling combine – frozen sand belonging to the VI category with a hardness coefficient of 2 on the Protodiakonov scale; medium-hard slate of the V category with a hardness coefficient of 4; concrete with a compressive strength of 60 MPa and a density of 2320 kg/m3. The destruction was carried out on a universal stand (Fig.4) both in the field and in the laboratory. Experiments on the destruction of slate rocks were carried out directly in the open-pit, while the stand was aggregated with a tractor.
Samples with a height of 100 mm and a diameter of 71.4 mm were used when testing rocks for cut with compression and tension by the indirect method of diametric compression. The crumpling stresses were determined by pressing a steel punch into the rock using a universal testing machine UMM-50 (GOST 7855-61).
The rock destruction stand works as follows. A strain gauge trolley 6, carrying a working body 7, moves along the guides in the beams 4. The destruction of rock 8 occurs in layers. The chip thickness is changed using a screw-type device. The design of the stand provides for its installation on skis and coupling with a traction machine. This makes it possible to conduct experiments in the field.
In the course of experimental studies, the parameters of the cut left by the cutter were determined: the camber angle θ [15], angles α1, α2, height h2, as well as the dimensions r1 and r2, which determine the shape of the crumpling core. It is quite simple to perform such measurements on hard rocks, since the crumpling cores are often separated together with the separation area, and the appearance and color of the crumpling cores differ significantly from the rock in the separation area.
The processing of the fixed maximum values of the components of the fracture resistances according to the Sr and Sb oscillograms is quite consistent with the results of the calculation according to the dependencies (21), (22) of the developed mathematical model of the process of rocks destruction by milling machine cutters. The calculation results obtained from the dependencies (21), (22) differ from the experimental ones by no more than 12-13 %, which indicates the correctness of the initial positions taken when developing a physical and mathematical model.
Conclusion
The developed physical and mathematical model of the process of rocks destruction by a single cutter with a spherical tip and the obtained analytical dependences for determining the tangential and normal components of the fracture resistance give a reasonable opportunity, with a known rock hardness, the number of cutters and their trajectory along the face, to calculate the torques on the working bodies of milling machines, the required power for their drive and, consequently, the actual productivity.
References
- Gerike P.B., Gerike B.L. Tool search for mechanical destruction of strong rock masses. Mining informational and analytical bulletin. 2012. N S2, p. 241-265 (in Russian). URL
- Zaitsev V.I., Karpikov A.V., Che V.V. Application efficiency of PDС bits. Earth Sciences and subsoil use. 2014. N 5 (48), p. 58-66 (in Russian). URL
- Tretyak A.Ya., Popov V.V., Grossu A.N., Borisov K.A. Innovative approaches to designing highly efficient rock-breaking tool. Mining informational and analytical bulletin. 2017. N 8, p. 217-222. DOI: 10.25018/0236-1493-2017-8-0-225-230 (in Russian).
- Katanov B.A., Vnukov V.G. The use of rod cutters as a destructive tool of medium-hard rocks. Vestnik Kuzbasskogo gosudarstvennogo tekhnicheskogo universiteta. 2004. N 6.1, p. 29-33 (in Russian). URL
- Neskromnykh V.V., Borisov K.I. Analytical study of the process of cutting-chipping rock by a bit with PDC cutters. Izvestiya Tomskogo politekhnicheskogo universiteta. 2013. Vol. 323. N 1, p. 191-195. URL
- Ostanovsky A.A., Vasin M.A. Theoretical aspects of adaptive process for rock cutting. Mining informational and analytical bulletin. 2014. N 2, p. 198-203 (in Russian). URL
- Popov S., Andrienko S. Algorithm for calculating the energy of contact interaction of the operating tool of the bar machine in conditions of wear with a fixed abrasive. New Materials and Technologies in Metallurgy and Mechanical Engineering. 2013. N 2, p. 138-146. DOI: 10.15588/.v0i2.99623 (in Ukrainian).
- Prokopenko S.A. Prospective design of cutters for increasing the grade of coal produced by the mines. Ugol. 2017. N 4, p. 29-31. DOI: 10.18796/0041-5790-2017-4-29-31 (in Russian).
- Prokopenko S.A., Cehlar M. Improving efficiency of rock destruction through twinned operation of various bit cutters. Ugol. 2018. N 11, p. 18-21. DOI: 10.18796/0041-5790-2018-11-18-21 (in Russian).
- Prokopenko S.A., Ludzish V.S. Evolution of cutting picks for underground mining machinery. Russian mining industry. 2015. N 2, p. 65 (in Russian). URL
- Zhabin A.B., Polyakov A.V., Averin E.A. et al. Ways of development for the theory of rock and coal destruction by picks. Ugol. 2019. N 9, p. 24-28. DOI: 10.18796/0041-5790-2019-9-24-28 (in Russian).
- Pushmin P.S., Romanov G.R. Features of the mechanism of solid rock breaking by a diamond rock-cutting tool. Earth Sciences and subsoil use. 2014. N 5 (48), p. 67-72 (in Russian). URL
- Zhabin A.B., Polyakov A.V., Averin E.A., Sarychev V.I. State of scientific researches in the field of rock destruction by picks at the turn of the century. News of the Tula state university. Sciences of Earth. 2018. N 1, p. 230-247. DOI: 10.24410/px6n-5y37
- Sysoev N.I. Chu Kim Hung. Applications of finite element method to determine design parameters of drilling cutters. Bulletin of higher educational institutions. North Caucasus region. Technical sciences. 2015. N 4 (185), p. 73-80. DOI: 10.17213/0321-2653-2015-4-73-80
- Cheban A.U. Experimental study of rock disintegration with milling cutters of the working body. Bulletin of PNU. 2012. N 1 (24), p. 125-128 (in Russian). URL
- Shemyakin S.A., Shishkin E.A. Analytical theories for determining the resistance to cutting (loosening) of frozen rocks and their application in the practice of calculating earthmoving equipment: monograph. Khabarovsk: Izd-vo Tikhookeanskogo gosudarstvennogo universiteta, 2014, p. 143 (in Russian).
- Shemyakin S.A., Cheban A.Yu. Determination of resistance to cutting of frozen rocks deeply blocked (slot). Mining equipment and electromechanics. 2015. N 6 (115), p. 39-44.
- Shemyakin S.A., Gamolya Yu.A., Cheban A.Yu. Technical and technological solutions for the development of frozen rocks in mining and construction: Monograph. Khabarovsk: Izd-vo Dalnevostochnogo gosudarstvennogo universiteta putei soobshcheniya, 2017, p. 188 (in Russian).
- Xuefeng Li, Shibo Wang, S.Ge et al. A theoretical model for estimating the peak cutting force of conical picks. Experimental Mechanics. 2018. Vol. 58, p. 709-720. DOI: 10.1007/s11340-017-0372-1
- Bao R.H. Estimating the peak indentation force of the edge chipping of rocks using single point-attack pick. Rock mechanics and rock engineering. 2011. Vol. 44, p. 339-347. DOI: 10.1007/s00603-010-0133-2
- Bilgin N., Copur H., Balci C. Effect of replacing disc cutters with chisel tools on performance of a TBM in difficult ground conditions. Tunnelling and underground space technology. 2012. Vol. 27. Iss. 1, p. 41-51. DOI: 10.1016/j.tust.2011.06.006
- Carbonell J.M., Onate E., Suarez B. Modelling of tunnelling processes and rock cutting tool wear with the particle finite element method (PFEM). Computational mechanics. 2013. Vol. 52, p. 607-629. DOI: 10.1007/s00466-013-0835-x
- Dewangan S.,Chattopadhyaya S., Hloch S. Wear assessment of conical pick used in coal cutting operation. Rock mechanics and rock engineering. 2015. Vol. 48, p. 2129-2139. DOI: 10.1007/s00603-014-0680-z
- Bilgin N., Demircin M.A., Copur H. et al. Dominant rock properties affecting the performance of conical picks and the comparison of some experimental and theoretical results. International journal of rock mechanics and mining sciences. 2006. Vol. 43. Iss. 1, p. 139-156. DOI: 10.1016/j.ijrmms.2005.04.009
- Goktan N., Gunes N. A semi-empirical approach to cutting force prediction for point-attach picks. Journal of the southern African institute of mining and metallurgy. 2005. Vol. 105. Iss. 4, p. 257-263. URL
- Gunes Yilmaz N., Tumac D., Goktan R.M. Rock cuttability assessment using the concept of hybrid dynamic hardness (HDH). Bulletin of engineering geology and the environment. 2015. Vol. 74, p. 1363-1374. DOI: 10.1007/s10064-014-0692-7
- Khair A.W. Research and innovations for continuous miner’s cutting head for efficient cutting process of rock/coal. In Proceedings of the 17th International mining congress and exhibition of Turkey, 19-22 June 2001, Ankara, Turkey. Chamber of Mining Engineers of Turkey, 2001. Vol. 17, p. 45-55. URL
- Li H.S., Liu S.Y., Xu P.P. Numerical simulation on interaction stress analysis of rock with conical picks. Tunnelling and Underground Space Technology. 2019. Vol. 85, p. 231-242. DOI: 10.1016/j.tust.2018.12.014
- Li X., Tiryaki B., Cleary P.W. Hard rock cutting with SMARTCUT technology. Conference: 22nd World mining congress and expo, 11-16 September 2011, Istanbul, Turkey. Chamber of Mining Engineers of Turkey, 2011, p. 725-732. DOI: 10.13140/2.1.4381.0885
- Li X., Lv Y., Zeng Q., Wang J. Research on strength of roadheader conical picks based on finite element analysis. Open mechanical engineering journal. 2015. Vol. 9, p. 521-526. DOI: 10.2174/1874155X01509010521
- Shao W., Sheng Li X., Sun Y., Huang H. Linear rock cutting with SMART*CUT picks. Applied mechanics and materials. 2013. Vol. 477-478, p. 1378-1384. DOI: 10.4028/www.scientific.net/AMM.477-478.1378
- Mezyk A., Klein W., Fice M. et al. Mechatronic model of continuous miner cutting drum driveline. Mechatronics. 2015. Vol. 37, p. 12-20. DOI: 10.1016/j.mechatronics.2015.11.004
- Prakash A., Vemavarapu M., Singh K.B. A new rock cuttability index for predicting key performance indicators of surface miners. International journal of rock mechanics and mining sciences. 2015. Vol. 77, p. 339-347. DOI: 10.1016/j.ijrmms.2015.04.016
- Qianqian Z., Zhennan H., Mengqi Z., Jianguang Z. Prediction of tool forces in rock cutting using discrete element method. Electronic journal of geotechnical engineering. 2015. Vol. 20(5), p 1607-1625. URL
- Rojek J., Oñate E., Labra C., Kargl H. Discrete element modelling of rock cutting. Particle-based methods. 2011, p. 247-267. DOI: 10.1007/978-94-007-0735-1_10
- Su O., Akcin N.A., te Kamp L. Modeling of cutting forces acting on a conical pick. Proceeding of EURO: TUN 2009 II International conference on computational methods in tunneling, 9-11 September 2009, Bochum, Germany. Aedificatio Publishers, 2009, p. 1-8. URL
- Su O., Ali Akcin N. Numerical simulation of rock cutting using the discrete element method. International journal of rock mechanics and mining sciences. 2011. Vol. 48. Iss. 3, p. 434-442. DOI: 10.1016/j.ijrmms.2010.08.012
- Wang S., Huang L., Li X. Analysis of rockburst triggered by hard rock fragmentation using a conical pick under high uniaxial stress. Tunnelling and Underground Space Technology. 2020 Vol. 96. N 103195. DOI: 10.1016/j.tust.2019.103195
- Wang X., Su O. Specific energy analysis of rock cutting based on fracture mechanics: a case study using a conical pick on sandstone. Engineering fracture mechanics. 2019. Vol. 213, p. 197-205. DOI: 10.1016/j.engfracmech.2019.04.010
- Yasar S. Predictive plots for conical pick performance using mechanical and elastoplastic properties of rocks. Journal of rock mechanics and geotechnical engineering. 2020. Vol. 12. Iss. 5, p. 1027-1035. DOI: 10.1016/j.jrmge.2019.12.020
- Yilmaz N.G., Yurdakul M., Goktan R.M. Prediction of radial bit cutting force in high-strength rocks using multiple linear regression analysis. International journal of rock mechanics and mining sciences. 2007. Vol. 44. Iss. 6, p. 962-970. DOI: 10.1016/j.ijrmms.2007.02.0