Изучение особенностей кинетики процесса получения окатышей из красного шлама в потоке водорода
- 1 — аспирант Санкт-Петербургский горный университет ▪ Orcid
- 2 — д-р техн. наук доцент Санкт-Петербургский горный университет ▪ Orcid
- 3 — канд. техн. наук доцент Санкт-Петербургский горный университет ▪ Orcid
- 4 — д-р техн. наук профессор Центральный научно-исследовательский металлургический институт
Аннотация
Изучена и обоснована кинетика восстановления последовательных фазовых переходов оксидов железа при восстановлении до металлизированного состояния с различными режимами подачи технического водорода. Представлены результаты образования окатышей при добавлении к красному шламу в качестве связующего реагента 3-5 % мелассы. Получены зависимости скорости восстановления оксидов железа от скорости водородного потока. По результатам экспериментов построена кинетическая модель, а при помощи рентгенофазового и спектрального анализа доказано, что образующиеся после термической обработки агломераты получили высокую прочность за счет сцепления частиц восстановленного железа с частицами красного шлама. Использование шихтовых материалов нового типа в плавильных агрегатах позволит снизить количество выбросов и пылевидных фракций, а также увеличит выход годного металла.
Введение
Производство чугуна и стали является одним из самых крупных по объему выпуска отраслей в мире [1, 2]. В последние годы в связи с уменьшением ресурсной базы и снижением общего содержания железа в руде многие исследователи сфокусировали свои усилия на вовлечении в металлургический процесс отходов производства [3, 4], полупродуктов в виде шлаков, пыли газоочистных сооружений и шламов [5, 6]. Наибольший интерес для черной металлургии представляет собой вовлечение в процесс плавки красного шлама (КШ), который образуется как полупродукт при производстве глинозема байеровским способом из бокситов [7, 8]. Главным показателем этого является содержание железа (до 50-60 %) в основном в виде Fe2O3 [9]. В соответствии с глобальными отчетными данными, общее количество КШ в накопителях и полигонах в мире оценивается приблизительно в 1,5 млрд т [10]. В России ежегодный прирост отходов глиноземного производства составляет 7-8 млн т при общем их объеме 600 млн т, которые сосредоточивают в шламохранилищах (шламовых полях) в основном в Свердловской области (Уральский регион). Таким образом, красные шламы в виде значительного количества забалансовых материалов глиноземного производства могут рассматриваться как источник основного шихтового материала для получения чугуна и стали, при этом за счет снижения объемов шламовых полей можно решить крупную экологическую проблему на производственных территориях алюминиевых предприятий [8, 11, 12].
Поскольку железо в красных шламах присутствует как в оксидной, так и гидроксидной форме, научно-технический интерес состоит в том, чтобы проводить переработку с учетом фазовых переходов в восстановительной среде. Многие исследования по переработке отходов направлены на разработку способов утилизации с учетом многокомпонентного состава для получения различных функциональных материалов [12], таких как строительные материалы [13-15], краски и пигменты [16], катализаторы [17], сорбенты [18] или избирательно выделенные оксиды титана, алюминия, кремния и железа [19-21]. Наиболее перспективным и эффективным, а также целесообразным с точки зрения решения экологических задач становится прямое восстановление некоторых металлов из оксидов [22-24].
Таким образом, если красный шлам считать полупродуктом, прошедшим предварительную подготовку при получении глинозема, то наиболее перспективно организовать процесс получения окатышей [25] совместно с обработкой газами для получения восстановленных продуктов, которые могут выполнять функцию упрочняющего материала [26-28]. При обработке предварительно подготовленных окатышей в газовом потоке, в заданном температурном режиме, происходит последовательный переход оксидных форм к гидроксидным с образованием пористого агломерата, который имеет жесткий каркас из восстановленного железа, после чего окатыши быстро растворяются в расплаве во время доменной плавки со скоростью, превышающей скорость плавления некоторых железосодержащих руд [29].
Проведение экспериментов по переработке красных шламов
В работах [30-32] были изучены параметры прямого восстановления соединений из окатышей железосодержащей руды при различных температурах в условиях регулируемой атмосферы. Применение в качестве реагента технического водорода H2 в нескольких вариантах увеличивает скорость взаимодействия, особенно в атмосфере CO2 при температуре 900-1100 °C.
Результаты экспериментального исследования прямого восстановления окатышей различного состава после операции магнитной сепарации подтверждают эффективность процесса. Исследования показали, что восстановление железа в заданных условиях составляет 61,85 % при общем содержании железа в концентрате 65,93 %. С другой стороны, при определенных условиях можно получить более богатый по содержанию концентрат с 90,3 % по массе Fe – со степенью металлизированного состояния 94,8 %. Однако применение данного метода в промышленных масштабах экономически нецелесообразно из-за значительных энергозатрат. При брикетировании красного шлама существуют способы прямого ввода железной стружки и пыли [33], которые выполняют функцию упрочняющего материала и повышают общее содержание железа в брикетах, но и эти способы весьма затратны для промышленного использования.
В любом случае изучение процесса прямого избирательного разделения железосодержащих фаз в потоке водорода посредством электромагнитной сепарации может стать предметом разработки более эффективного способа брикетирования или окускования красного шлама. Возможность прямого восстановления железа при обработке сырых окатышей из КШ потоком технического водорода H2 представлена в источнике [20].
Целью данной работы является разработка технологии получения окатышей из образцов красного шлама Уральского алюминиевого завода в нагревательных печах шахтного типа, совмещенное с обработкой водородом для последующего получения восстановленных продуктов в виде агломератов с высоким содержанием восстановленного железа для доменной плавки.
Материалы и их характеристики
Образцы красного шлама были отобраны со шламовых полей Уральского алюминиевого завода (Каменск-Уральский Свердловской обл.). В процессе производства глинозема на этом заводе используют бокситы различных месторождений (Северо-Уральского, Тиманского, Ямайского, Гвинейского), поэтому содержание некоторых компонентов, переходящих в красный шлам (в частности, железа), может существенно изменяться. Отбор проб производили специальным пробоотборником непосредственно из горячего шлама глиноземного цеха № 1 (передел 1 по способу Байера) перед его отгрузкой на шламовое поле из цистерны. Периодичность отбора составляла 24 дня по три пробы в тару по 0,5 л с учетом стабильного кремниевого модуля во время технологического цикла в цехе № 1. Пробоподготовка производилась по стандарту РУСАЛ-УАЗ в ЦЛАИТ.
На первом этапе образцы КШ для удаления внешней влаги (MOI) сушили в течение двух часов при температуре 110 °C, далее подвергли истиранию в мельнице Nietzsche. Химический состав и особенности микроструктуры частиц красного шлама определяли при помощи рентгеновской дифрактометриии SEM-анализа и методом энергодисперсионной рентгеновской спектроскопии. В качестве связующего вещества для улучшения окомкования добавляли мелассу (патоку) 2-5 %.
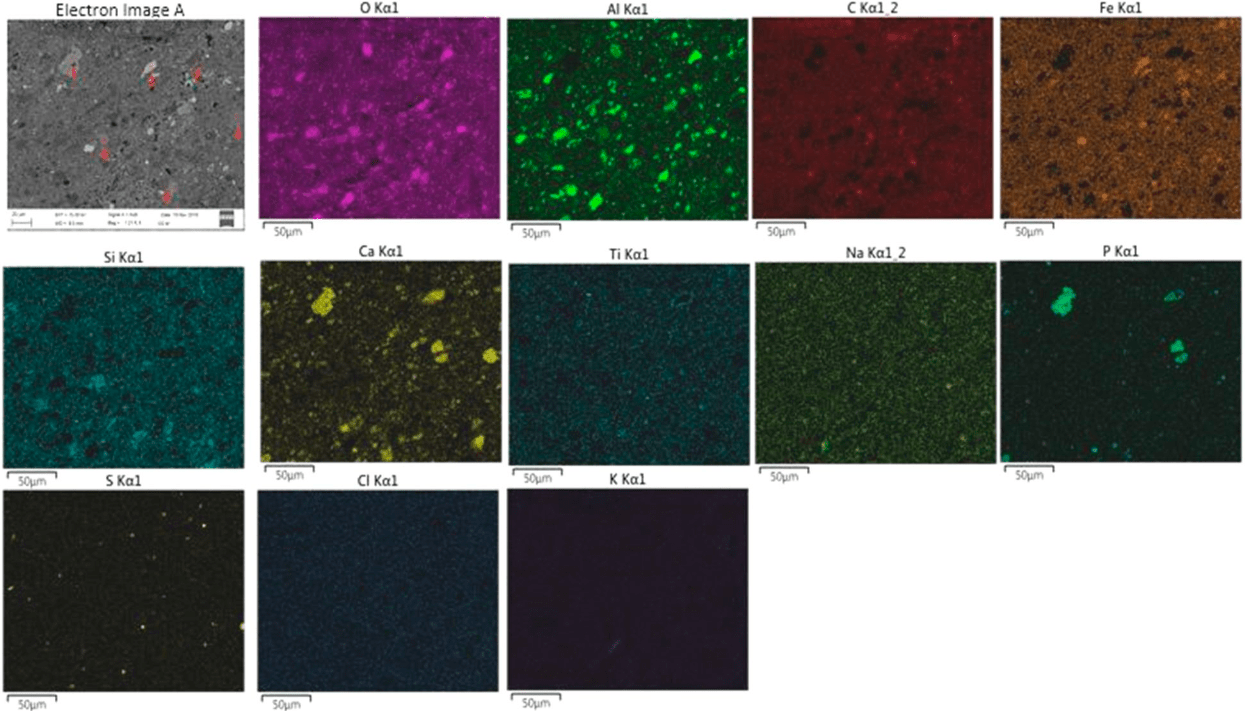
Рис.1. Распределение элементов в красном шламе УАЗа
На порошковом дифрактометре Siemens D5000 XRD изучали первоначальный минералогический состав смеси красного шлама. Рентгено-флюоресцентный анализ проводили в лабораториях Горного университета и Университета Оулу (Финляндия). На анализаторе Bruker AXS S4 Pioneer был проведен химический анализ образцов красного шлама. Для уменьшения воздействия примесей основные элементы были идентифицированы на вращающемся стеклянном диске.
Термогравиметрический анализ образцов КШ массой 30 г проводили в платиновых тиглях на сертифицированной по ISO:2000 установке Nietzsche STA409 PC Luxx в атмосфере аргона (чистотой 99,999 %) при температуре 50-1400 °C со скоростью нагрева 20 °C/мин.
Особенности и основные характеристики красных шламов уральского региона. Химический состав образцов КШ Уральского алюминиевого завода был получен с использованием рентгено-флюоресцентного анализа: Fe – 35,01, Fe2O3 – 50,02, SiO2 – 7,14, Al2O3 – 12,73, CaO – 15,00, MgO – 1,01, P2O5 – 0,93, MnO – 0,21, K2O – 0,11, TiO2 – 5,70, S – 0,90, ППП (внутренней влаги) – 5,40 % по массе. Исходное распределение частиц красного шлама: 2,4 % (размер +2 мм); 11,6 % (+1 мм); 35,70 % (+0,59 мм); 29,6 % (+0,25 мм); 11,4 % (+0,17 мм); 8,1 % (+0,105 мм); 1,2 % (–0,105 мм). Анализируемые образцы КШ при помощи Mastersizer 3000 распределяются по размеру 0,1-2 мм. Минералогический состав определен методом X-ray-дифракции (XRD) на анализаторе BrukerAxs D8 Advance (Germany) с Cu-катодом.
На рис.1 представлена схема распределения основных элементов в красном шламе, который состоит из следующих компонентов: гематит (Fe2O3), каолин (Al2O3·2SiO2·2H2O), ангидрит кальция (CaSO4), гиббсит (Al(OH)3, анатаз (TiO2), кварц (SiO2) и карбонат кальция (CaCO3).
Экспериментальная часть
Окатыши красного шлама были подготовлены в специальном дисковом смесителе при регулировании скорости вращения и времени выдержки. Технические характеристики мельницы: диаметр диска 400 мм, глубина емкости 100 мм, угол наклона 52°, скорость вращения 17 м/с, время вращения 10 мин.
После извлечения сырых окатышей из барабана смесителя их просушивали 56 ч и подвергали испытанию на прочность при сдавливании и сбрасывании с высоты 46 см. Сушка материала осуществлялась сначала в тиглях в сушильном шкафу при температуре 70-90 °C до содержания влаги 5-10 %, далее смесь перегружалась во вращающийся барабан для получения окатышей с добавкой связующего. В дисковый окомкователь подавалась измельченная фракция КШ до размера менее 500 мкм массой 200 г. Вода с мелассой в соотношении 5:1 подавалась на поверхность дискового окомкователя. Окатыши формировались в течение 10 мин. По завершении эксперимента отбирались гранулы, просеянные до фракции размером 3-7 мм, которая принималась за меру производительности дискового окомкователя. Далее часть гранул шла на участок обезвоживания, а вторая часть подвергалась (без обезвоживания) испытанию на прочность. Гранулы просеивали для просушки на воздухе в течение трех суток.
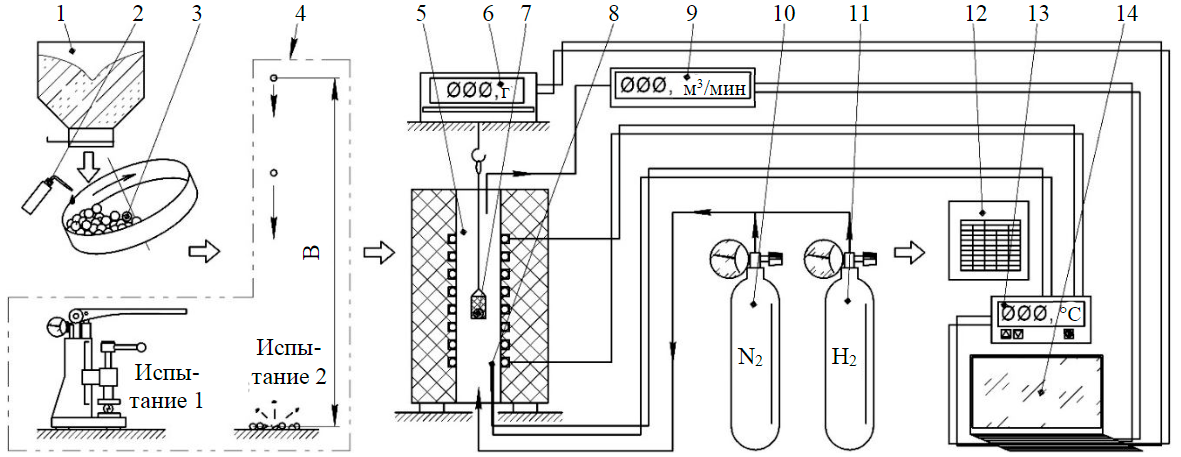
Рис.2. Технологическая схема эксперимента комплексной переработки КШ 1 – бункер с красным шламом; 2 – дозатор воды с мелассой; 3 – дисковый окомкователь; 4 – испытания на прочность; 5 – шахтная печь; 6 – электронные весы; 7 – корзина Ni-Cr с окатышами; 8 – нагревательный элемент и термопара; 9 – расходомер; 10 – баллон с азотом; 11 – емкость с водородом; 12 – цифровой преобразователь с ПИД- регулятором; 13 – терм контроллер; 14 – ЭВМ
Для каждого окатыша производили расчет потери массы и вычисляли среднеарифметическое значение испытания на прочность. Тест по стандартной методике повторяли три раза при одних и тех же условиях для окатышей размером 3-7 мм.
Для определения разрушаемости окатышей проводили тест свободного падения на стальную или бетонную плиту с высоты 46 см. Устойчивость к повреждениям при падении показывает, как часто зеленые и сухие окатыши могут падать, прежде чем покажут заметные трещины или раскрошатся. Для определения коэффициента сопротивления к динамическому разрушению окатышей проводят тест свободного падения. Устойчивость к повреждениям при падении показывает отношение целых окатышей к разрушенным. Тест проводился три раза с влажными окатышами (первые сутки – 24 ч), после чего их просушивали и проверяли на разрушаемость уже через 56 ч сухими (после трех суток) еще три раза. Количество разрушенных частей регистрировалось для каждого эксперимента и определялось на основании среднеарифметического значения.
На рис.2 показана схема комплексной переработки красного шлама для получения агломерата с высоким содержанием металлизированной фазы.
На первом этапе, в приемную емкость загружали 200 г красного шлама с 12 %-ным содержанием влаги при изменении количества мелассы 2-5 %, далее ее распыляли на поверхность вращающегося дискового барабана смесителя 3. Средний состав композиции из мелассы: вода 20; сахар 62 (сахароза 32; фруктоза 16; глюкоза 14); нитраты 10; зола 8 % по массе. Производительность смесителя для получения сырых окатышей размером 3-7 мм рассчитывали по формуле
где WP – масса окатышей с заданным размером, г; WF – масса красного шлама, загруженного в дисковый смеситель, г.
Результаты и их обсуждение
Влияние концентрации мелассы
Изучено влияние добавления различного количества мелассового связующего (1-4 %) на механические свойства полученных зеленых и высушенных гранул при перемешивании в дисковом окомкователе при влажности 8 %. Установлено, что с увеличением количества связующего мелассы производительность увеличивается. Производительность окомкователя при добавлении 1,0 % мелассы составила 20,0 %, при 1,5 – 31,3, при 2,0 – 42,0, при 3,0 – 43,2, при 4,0 – 38,4 для окатышей 3-7 мм. Это связано с тем, что с увеличением количества мелассового связующего (рис.3), растворенного в воде, вязкость жидкости увеличивается. Это приводит к тому, что капиллярное давление жидкости между более мелкими частицами выше, чем у более грубых частиц. Это вызывает их слипание и связано с тем, что межчастичные силы уменьшаются с увеличением размера частиц [34].
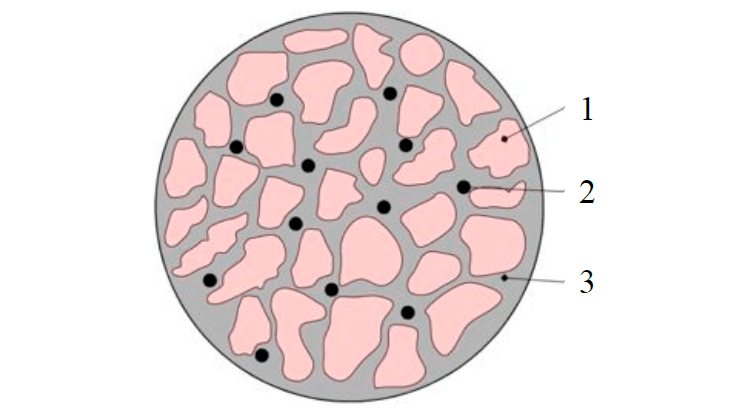
Рис.3. Структура окатыша 1 – КШ; 2 – меласса в качестве связующего; 3 – вода
Далее просушенные окатыши обжигали в муфельной печи при температуре 900-1200 °C и изучали поведение окатышей и влияние нагрева в нейтральной и восстановительной атмосферах. В работе [35] описана операция восстановления красного шлама в вертикальной печи в интервале температур 800-1000 °C. В качестве регулируемой атмосферы печи использовался азот со скоростью подачи 1 л/мин. Окатыши перемещали в специальную сетчатую Ni-Cr корзину и устанавливали ее в центральную зону печи в подвешенном состоянии на 30 мин. Для контроля изменения массы окатышей подвеска корзины была соединена и подключена к электронным весам.
После завершения первой стадии обработки окатышей в печи изменяли режим подачи и заменяли газ с азота на водород. Давление водорода увеличивали при комнатной температуре. Источником водорода являлась электрохимическая ячейка с пассивным нерасходуемым катодом [36], из которой при нагрузке 100 A во время электролиза воды происходило выделение водорода Н2.
Часть оксидов (SiO2, TiO2, Al2O3, MgO, CaO) которые являются пассивными к восстановительным процессам, необходимо переводить в шлаковую составляющую. С другой стороны количество прореагировавшего кислорода при подаче водорода для восстановительных процессов некоторых оксидов, можно соотнести с показателями потери массы. Тогда коэффициент выхода продуктов с учетом потери массы можно рассчитать по следующему уравнению:
где M1 – первоначальная масса окатыша до этапа восстановления, г; M2 – масса навески, извлеченная в различные промежутки времени, г; Mo – масса восстановленного окатыша (агломерата), г.
Согласно работе [26], диаграмма состояния для стандартных условий при фазовом переходе некоторых оксидов в элементарное состояние (в частности натрий, цинк, свинец) при определенной температуре нагрева в печи, возгоняются в пары. В нашем случае при нагреве окатышей КШ и обработке до температуры 900 °С проходит целый комплекс элементарных реакций восстановления.
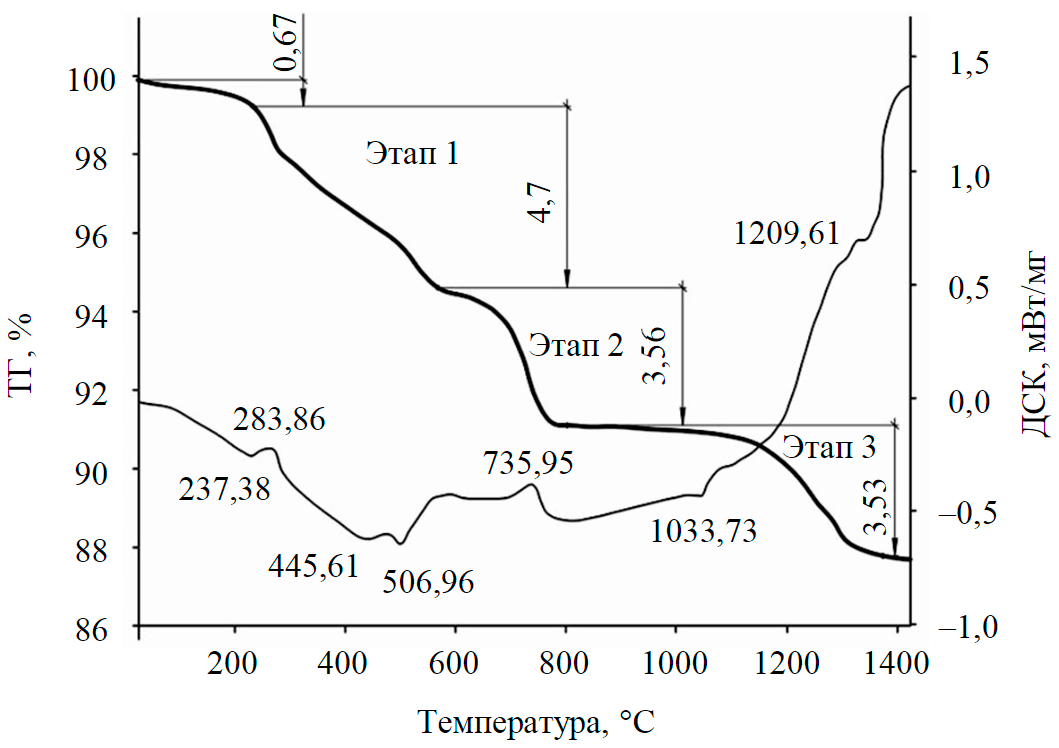
Рис.4. Термогравиметрическая кривая во время нагрева образца окатыша красного шлама (УАЗ)
Термический анализ образцов красного шлама
Результаты избирательной сканирующей калориметрии (DSC) при термической обработке образцов красного шлама представлены на рис.4. Вес исследуемых образцов составлял 16,04 г при потере массы 12,44 %. Особое влияние на потерю массы оказывает изменение температуры, при этом наблюдаются явные скачки, по которым можно определить возможные фазовые переходы, связанные проходящими в этот интервал времени реакциями с выделением тепла при последовательном восстановлении оксидов железа.
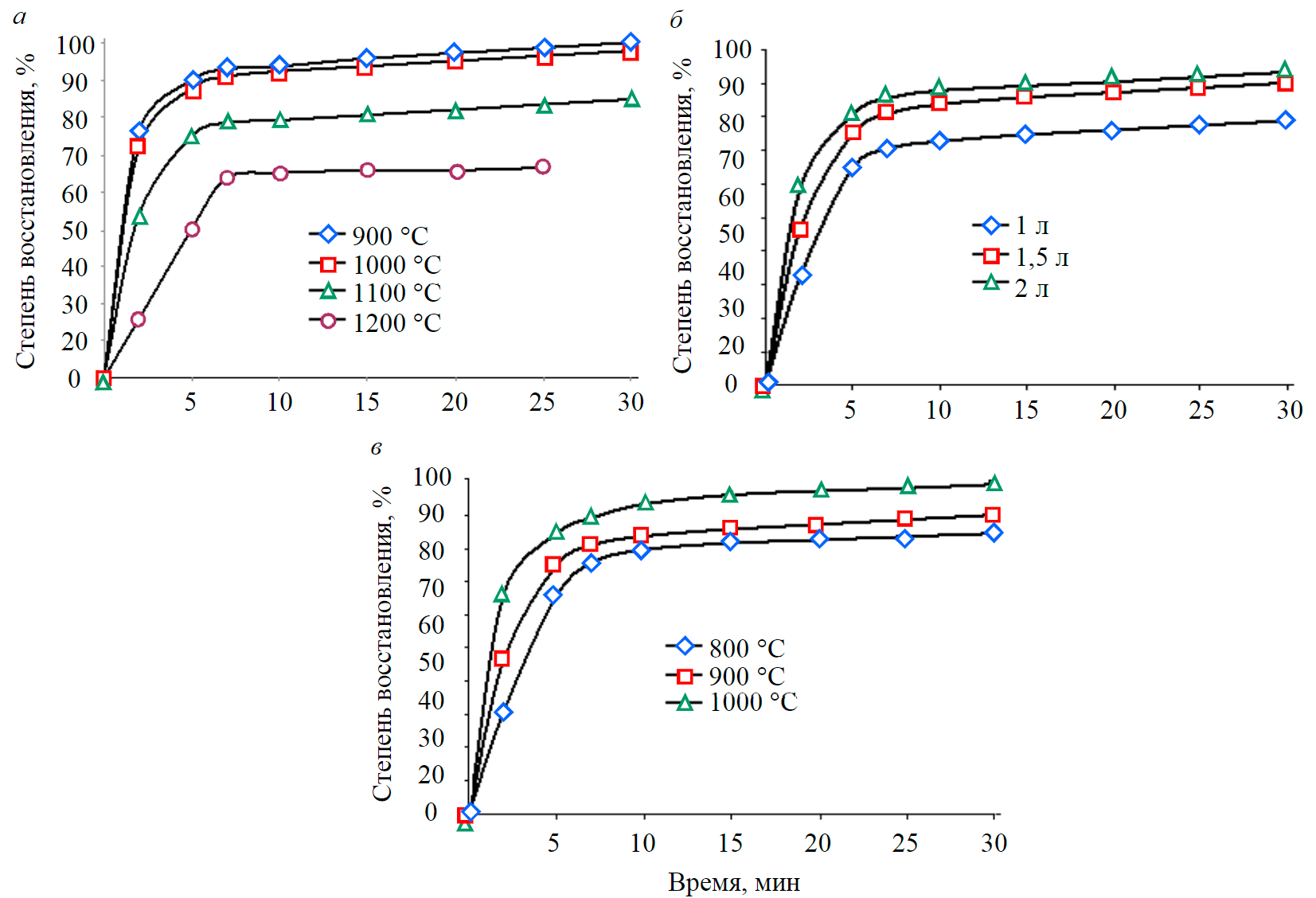
Рис.5. Зависимость степени восстановления (%) КШ окатышей от температуры спекания (при скорости водородного потока 1 л/мин) (а), от различного расхода водорода (б), при изменении температуры (при скорости водородного потока 1,5 л/мин) (в)
На первоначальном этапе термической обработки в интервале температур 40,0-244,8 °C потеря массы образцов незначительна и составляет 0,67 %. Изменение массы образцов КШ в этот период связано с потерей внешней влаги в первую очередь при испарении. Далее проходят три главные стадии процесса:
- Интервал температур 244,8-575,7 °C, когда потери влаги составляют 4,70 %. Это связано главным образом с процессами химической адсорбции воды и декомпозицией гиббсита Al2O3 [37].
- В интервале температур 575,7-897,0 °C потери массы связаны с процессами деградатации внутренней влаги в каолине и переходом в форму карбоната кальция. Потери массы в этот период составляют 3,56 %, а лимитирующая стадия проходит при температуре 735,9 °C и заканчивается разложением карбоната (кальцита). Как отмечено в работе [38], карбонат кальция может формироваться в локальных объемах в интервале 560-720 °C подобно тому, как каолин разлагается при температуре 600 °C [39]. При температурах термообработки 800-1100 °C масса образцов практически не снижается.
- При температуре 897,0-1400,0 °C потери массы составляют 3,53 %, и, согласно предыдущим исследованиям [40], в этот промежуток происходит разложение некоторых силикатов, что подтверждается эндотермическим пиком на кривой при 1209 °C.
Спекание КШ при различных температурах
Прочность на холодное сжатие обработанного окатыша при влажности 8 % и мелассе 3 % после спекания при температуре 900-1200 °С увеличивается, температура спекания также растет.
Влияние температуры обжига на степень восстановления
Зависимость степени восстановления КШ окатышей при температуре 900 °С в атмосфере водорода с расходом 1 л/мин, спеченного при различных температурах, показана на рис.5. Процент восстановления уменьшался по мере повышения температуры спекания.
Процесс термической обработки проходит в три этапа, когда восстановление начинается при нагреве более 800 °С, а основные фазовые переходы происходят в две стадии до температуры < 900 °C:
Для интервала температур > 1100 °C:
Термодинамический анализ показывает, что оптимальные результаты (с выходом восстановленного железа до 87 %) получаются при прямой конверсии гематита в фазу магнетита [20].
На основании результатов, приведенных на рис.5, а, для исследования скорости восстановления при различном расходе водорода был выбран режим спекания окатышей КШ 900 °С, три различных расхода Н2 (1, 1,5 и 2 л/мин) при постоянной температуре восстановления (900 °С) в течение 30 мин. Восстановление окатышей КШ имело быстрый рост с увеличением расхода водорода (рис.5, б). Это связано с повышением расхода водорода, что способствует повышению адсорбции водорода, а в последующем скорость реакции увеличивается. Повышается расход водорода, что увеличивает диффузию газа через пограничный слой и тем самым увеличивает восстановление ионов, что, в свою очередь, приводит к повышению скорости стадий химической реакции.
График восстановления окатышей КШ водородом (Н2) при постоянном расходе 1,5 л/мин в температурном диапазоне 800-1000 °С представлен на рис.5, в. На начальных стадиях скорость восстановления является самой высокой для любой заданной температуры восстановления, и только потом она постепенно снижается до конца реакции восстановления. Повышение температуры приводит к увеличению скорости массопереноса при диффузии, а скорость десорбции при этом увеличивается при удалении кислорода.
Степень восстановления увеличивается с повышением температуры. Высокая степень восстановления окатышей КШ на ранних стадиях включает восстановление гематита и магнетита до вустита и части вустита до железа. Относительное замедление темпа восстановления на заключительном этапе было связано с восстановлением FeO до Fe.
Кинетика восстановительных процессов образцов красного шлама
Знание кинетического поведения необходимо для понимания и прогнозирования процессов восстановления. Существует множество методов оценки изотермических кинетических параметров [41]. В данном исследовании для определения кинетических
где R – дробное сокращение; t – время сокращения; k – постоянная скорости.
Изучение кинетических особенностей процесса восстановления для получения значения энергии активации проводили термическое восстановление образцов окатышей КШ в водородной среде при 800, 900 и 1000 °C в течение 0-30 мин.
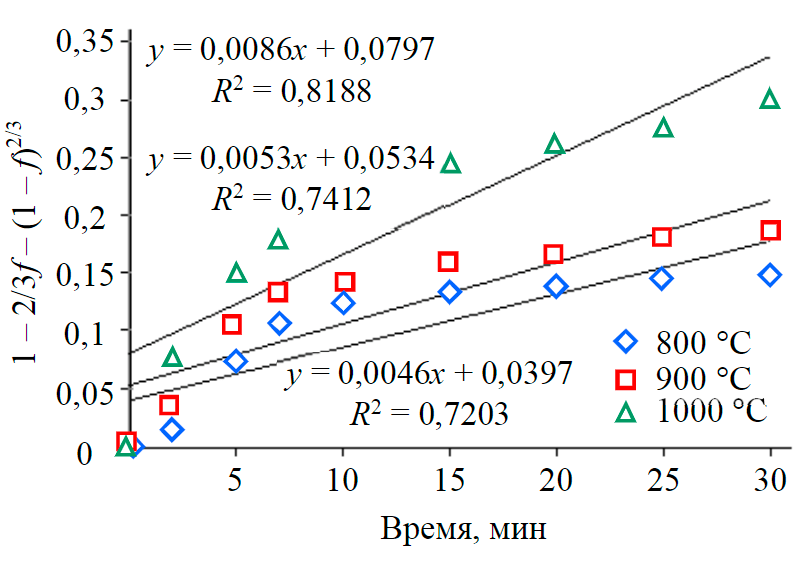
Рис.6. Зависимость скорости контролируемой диффузии (1 – 2/3f – (1 – f)2/3) от времени
восстановления КШ в атмосфере водорода
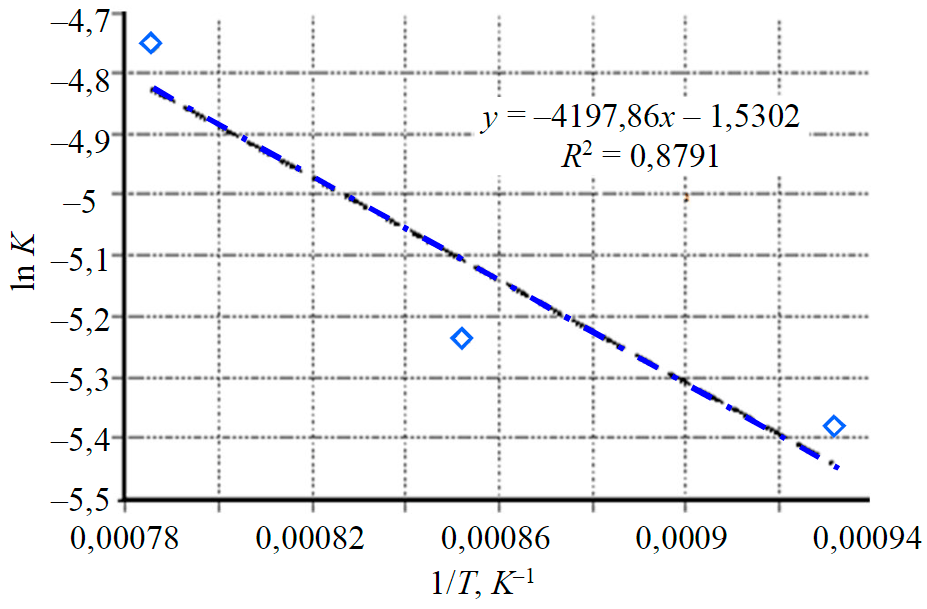
Рис.7. Зависимость скорости реакции ln K от 1/T для моделей диффузионного управления
График зависимости 1 – 2/3R – (1 – R)2/3 от времени представлен для различных температур восстановления на рис.6. В результате применения нескольких кинетических моделей к процессу восстановления было получено следующее. Энергия активации реакции восстановления и предэкспоненциальный коэффициент могут быть рассчитаны с помощью уравнения Аррениуса. Константа скорости реакции вычисляется так:
где k0 – предэкспоненциальный коэффициент; Eа – энергия активации; R – универсальная газовая постоянная; T – температура (°С).
Зависимости lnK от 1/T (рис.7) составляют прямую линию; наклон участка выражается в отношении E/R. Таким образом, энергия активации может быть получена умножением наклона на универсальную газовую постоянную, она составляет 35 кДж/моль.
В результате проведенных исследований можно получить железосодержащие продукты, которые могут стать альтернативным сырьем [43-47]. Это соответствует Плану мероприятий развития минерально-сырьевой базы России [48-50].
Выводы
Комплекс проведенных исследований по переработке красного шлама Уральского алюминиевого завода показал возможность получения высокопрочных агломератов с элементами восстановленного железа при создании технологических условий нагрева окатышей в восстановительной среде технического водорода:
- Добавление на первом этапе порошка красного шлама, смешанного с мелассой обеспечивает сохранение размеров сырых окатышей 3-7 мм и достаточный уровень прочности для проведения последующей операции классификации и агломерации.
- При увеличении температуры обжига окатышей увеличивается их прочность, что связано с образование фаз восстановленного железа при снижении общего уровня пористости.
- При заданной скорости водородного потока в объеме печи обеспечивается восстановление оксидов железа до 87 %, последовательном увеличении температуры со скоростью 20 °C/мин в интервале 800-1000 °C.
Использование в качестве восстановительной атмосферы водорода при нагреве окатышей красного шлама позволяет получить агломераты с высокой степенью прочности при содержании железа 70-80 % без примесей натрия, фосфора, цинка. Такой подход дает основание использовать агломераты из красного шлама в качестве альтернативного сырья для доменной плавки. Данная технология более эффективна по результативности (высокопрочный агломерат с высоким содержанием железа до 87 %) и по кинетике протекания процесса (по термодинамическим условиям в водородном потоке происходит с более высокими скоростями перехода из одной оксидной формы в другой).
Литература
- Kaushik P., Fruehan R.J. Behavior of direct reduced iron and hot briquetted iron in the upper blast furnace shaft: Part I. Fundamentals of kinetics and mechanism of oxidation // Metallurgical and Materials Transactions B. 2006. Vol. 37. P. 715-725. DOI: 10.1007/s11663-006-0055-2
- Wiley D.E., Ho M.T., Bustamante A. Assessment of Opportunities for CO2 Capture at Iron and Steel Mills: An Australian Perspective // Energy Procedia. 2011. Vol.4. P. 2654-2661. DOI: 10.1016/j.egypro.2011.02.165
- Халифа А.А., Утков В.А., Бричкин В.Н. Влияние красного шлама на предотвращение полиморфизма двухкальциевого силиката и саморазрушение агломерата // Вестник Иркутского государственного технического университета. 2020. Т. 24. № 1. С. 231-240. DOI: 10.21285/1814-3520-2020-1-231-240
- Беседин А.А., Утков В.А., Бричкин В.Н., Сизяков В.М. Агломерационное спекание красных шламов // Обогащение руд. 2014. Т. 2. С. 28-31.
- Трушко В.Л., Кусков В.Б., Кускова Я.В. Комплексная переработка богатых железных руд // Обогащение руд. 2014. Т. 1. С. 39-43.
- Branca T.A., Colla V., Algermissen D. et al. Reuse and Recycling of By-Products in the Steel Sector: Recent Achievements Paving the Way to Circular Economy and Industrial Symbiosis in Europe // Metals. 2020. Vol. 10. Iss. 3. P. 1-18. DOI: 10.3390/met10030345
- Cao J.-L., Yan Z.-L., Deng Q.-F. et al. Mesoporous modified-red-mud supported Ni catalysts for ammonia decomposition to hydrogen // International Journal of Hydrogen Energy. 2014. Vol. 39. Iss. 11. P. 5747-5755. DOI: 10.1016/j.ijhydene.2014.01.169
- Prabu V.A., Manikandan V., Uthayakumar M. Effect of red mud on the mechanical properties of banana/polyester composites using design of experiments // Proceedings of the Institution of Mechanical Engineers, Part L // Journal of Materials: Design and Applications. 2013. Vol. 227. № 2. P. 143-155. DOI: 10.1177/1464420712464709
- Kumar S., Kumar R., Bandopadhyay A. Innovative methodologies for the utilisation of wastes from metallurgical and allied industries // Resources, Conservation and Recycling. 2006. Vol. 48. Iss. 4. P. 301-314. DOI: 10.1016/j.resconrec.2006.03.003
- Ayres R.U., Holmberg J., Andersson B. Materials and the Global Environment: Waste Mining in the 21st Century // MRS Bulletin. 2001. Vol.26. Iss. 6. P. 477-480. DOI: 10.1557/mrs2001.119
- Утков В.А., Сизяков В.М. Современные вопросы металлургической переработки красных шламов // Записки Горного института. 2013. Т. 202. С. 39-43.
- Podgorodetskiy G., Gorbunov V., Panov A. et al. Complex additives on the basis of red mud for intensification of iron-ore sintering and pelletizing // Light Metals. 2015. P. 107-111.
- Fu T., Wei, J.H., Bao H., Liang J. Multiscale Study on the Modification Mechanism of Red Mud Modified Asphalt // Advances in Materials Science and Engineering. 2020. № 2150215. P. 1-9. DOI: 10.1155/2020/2150215
- Liu Yanju, Naidu R. Hidden values in bauxite residue (red mud): Recovery of metals // Waste Management. 2014. Vol. 34. № 12. P. 2662-2673. DOI: 10.1016/j.wasman.2014.09.003
- Mukiza E., Ling Ling Zhang, Xiaoming Liu, Na Zhang. Utilization of red mud in road base and subgrade materials: A review // Resources, Conservation and Recycling. 2019. Vol. 141. P. 187-199. DOI: 10.1016/j.resconrec.2018.10.031
- Pera J., Boumaza R., Ambroise J. Development of a pozzolanic pigment from red mud // Cement and Concrete Research. 1997. Vol. 27, Iss. 5. P. 1513-1522. DOI: 10.1016/S0008-8846(97)00162-2
- Qiang Liu, Ruirui Xinab, Chengcheng Li et al. Application of red mud as a basic catalyst for biodiesel production // Journal of Environmental Sciences. 2013. Vol. 25. Iss. 4. P. 823-829. DOI: 10.1016/S1001-0742(12)60067-9
- Shaobin Wang, Ang H.M., Tadé M.O. Novel applications of red mud as coagulant, adsorbent and catalyst for environmentally benign processes // Chemosphere. 2008. Vol. 72. P. 1621-1635. DOI: 10.1016/j.chemosphere.2008.05.013
- Akcil A., Akhmadiyeva N., Abdulvaliyev R. et al. Overview On Extraction and Separation of Rare Earth Elements from Red Mud: Focus on Scandium // Mineral Processing and Extractive Metallurgy Review. 2018. Vol. 39. Iss. 3. P. 145-151. DOI: 10.1080/08827508.2017.1288116
- Alkan G., Xakalashe B., Yagmurlu B. et al. Conditioning of Red Mud for Subsequent Titanium and Scandium Recovery – A Conceptual Design Study // World of Metallurgy – ERZMETALL. 2017. Vol. 70. № 2. P. 5-12.
- Das B., Prakash S., Reddy P.S.R., Misra V.N. An overview of utilization of slag and sludge from steel industries // Resources, Conservation and Recycling. 2007. Vol. 50. Iss. 1. P. 40-57. DOI: 10.1016/j.resconrec.2006.05.008
- Yi Man, Junxia Feng. Effect of gas composition on reduction behavior in red mud and iron ore pellets // Powder Technology. 2016. Vol. 301. P. 674-678. DOI: 10.1016/j.powtec.2016.06.013
- Man Y., Feng J.X., Wang Y.Y. A study of direct reduction characteristics of bayer process red mud-coal composite pellets // Thermal Science. 2019. Vol.23. № 5. P. 2569-2576.
- Пягай И.Н., Кремчеев Э.А., Пасечник Л.А., Яценко С.П. Карбонизационный способ переработки отходов глиноземного производства – альтернативная технология извлечения редких металлов // Цветные металлы. 2020. № 10. C. 56-63. DOI: 10.17580/tsm.2020.10.08
- Yibo He, Biao Tang, Qiang Li, Zongshu Zou. A Comprehensive Static Model of an Iron Bath Smelting Reduction Process with Thick Slag for Alumina-Rich Iron Ore // ISIJ International. 2015. Vol. 55. Iss. 10. P. 2125-2134. DOI: 10.2355/isijinternational.ISIJINT-2015-255
- Mombelli D., Barella S., Gruttadauria A., Mapelli C. Iron Recovery from Bauxite Tailings Red Mud by Thermal Reduction with Blast Furnace Sludge // Applied Sciences. 2019. Vol. 9. № 22. P. 1-23. DOI: 10.3390/app9224902
- Guoshan Ning, Bo Zhang, Chengjun Liu et al. Large-Scale Consumption and Zero-Waste Recycling Method of Red Mud in Steel Making Process // Minerals. 2018. Vol. 8. № 3. P. 1-16. DOI: 10.3390/min8030102
- Rath S.S., Jayasankar K., Satapathy B.K. et al. Kinetics and Statistical Behaviour of Iron Recovery from Red Mud using Plasma Arc Furnace // High Temperature Materials and Processes. 2011. Vol.30. P. 211-215. DOI: 10.1515/HTMP.2011.031
- Пягай И.Н., Кожевников В.Л., Пасечник Л.А., Скачков В.М. Переработка отвального шлама глиноземного производства с извлечением скандиевого концентрата // Записки Горного института. 2016. Т. 218. С. 225-232.
- Trushko V.L., Utkov V.A., Sivushov A.A. Reducing the environmental impact of blast furnaces by means of red mud from alumina production // Steel in Translation. 2017. Vol. 47. Iss. 8. P. 576-578.
- Zhu De-qing,Chun Tie-jun,Pan Jian, He Zhen. Recovery of Iron From High-Iron Red Mud by Reduction Roasting With Adding Sodium Salt // Journal of Iron and Steel Research International. 2020. Vol.19. № 8. P. 1-5. DOI: 10.1016/S1006-706X(12)60131-9
- Трушко В.Л., Дашко Р.Э., Кусков В.Б., Клямко А.С. Технология «холодного» брикетирования богатых руд Яковлевского месторождения // Записки Горного института. 2011. Т. 190. С. 133-137.
- Samouhos M., Taxiarchou M., Pilatos G. et al. Controlled reduction of red mud by H2 followed by magnetic separation // Minerals Engineering. 2017. Vol. 105. P. 36-43. DOI: 10.1016/j.mineng.2017.01.004
- Knight P. Agglomeration processes, phenomena, technologies, equipment. Powder Technology. Verlag GmbH: Wiley-VCH, 2002. P. 29-138. DOI: 10.1002/9783527619801
- El-Hussiny N.A., Shalabi M.E.H. A self-reduced intermediate product from iron and steel plants waste materials using a briquetting process // Powder Technology. 2011. Vol. 205, Iss. 1-3. P. 217-223. DOI: 10.1016/j.powtec.2010.09.017
- Busè R., Mombelli D., Mapelli C. Metals recovery from furnaces dust: Waelz process // La Metallurgia Italiana. 2014. Vol. 106 (5). P. 19-27.
- Antunes M.L.P., Couperthwaite S.J., Conceição da F.T. et al. Red Mud from Brazil: Thermal Behavior and Physical Properties // Industrial and Engineering Chemistry Research. 2012. Vol. 51. P. 775-779. DOI: 10.1021/ie201700k
- Liu Yong, Lin C., Wu Y. Characterization of red mud derived from a combined Bayer Process and bauxite calcination method // Journal of Hazardous Materials. 2007. Vol. 146. № 1. P. 255-261. DOI: 10.1016/j.jhazmat.2006.12.015
- McСann, G., Strezov V., Lucas J.A. et al. Iron Ore Characterisation during High Temperature Thermal Processing // Developments in Chemical Engineering and Mineral Processing. 2004. Vol. 12. № 3/4. P. 1-14.
- Meher S.N. Thermal Analysis of Nalco Red Mud // International Journal of Chemical Studies. 2014. Vol. 1. Iss. 5. P. 1-9.
- Hammam A., Ying Li, Hao Nie et al. Isothermal and Non-Isothermal Reduction Behaviors of Iron Ore Compacts in Pure Hydrogen Atmosphere and Kinetic Analysis // Mining, Metallurgy & Exploration. 2021. Vol. 38. P. 81-93. DOI: 10.1007/s42461-020-00317-3
- Yu-ming Wang, Zhang-fu Yuan. Reductive kinetics of the reaction between a natural ilmenite and carbon // International Journal of Mineral Processing. 2006. Vol. 81. № 3. P. 133-140. DOI: 10.1016/J.MINPRO.2006.07.010
- Litvinenko V. The Role of Hydrocarbons in the Global Energy Agenda: The Focus on Liquefied Natural Gas // Resources. 2020. Vol. 9. Iss. 5. № 59. DOI: 10.3390/resources9050059
- Sizyakov V.M., Kawalla R., Brichkin V.N. Geochemical aspects of the mining and processing of the large-tonne mineral resources of the hibinian alkaline massif // Geochemistry. 2019. Vol. 80. Iss. 3. DOI: 10.1016/j.chemer.2019.04.002
- Litvinenko V.S. Digital Economy as a Factor in the Technological Development of the Mineral Sector // Natural Resources Research. 2020. Vol. 29. P. 1521-1541. DOI: 10.1007/s11053-019-09568-4
- Litvinenko V.S., Sergeev I.B. Innovations as a Factor in the Development of the Natural Resources Sector // Studies on Russian Economic Development. 2019. Vol. 30. Iss. 6. P. 637-645. DOI: 10.1134/S107570071906011X
- Knyazkina V.I., Safronchuk K.A., Ivanov S.L., Pumpur E.V. Assessment of the state of a lubricator by the size of the acoustic signal in a loaded pair of friction of a mining machine transmission // Journal of Physics: Conference Series. 2020. Vol. 1515. P. 1-5. DOI: 10.1088/1742-6596/1515/5/052037
- 48. Quiroz Cabascango V.E., Sharikov Y.V. Mathematical modeling of mass, heat and fluid flow in a reverberatory furnace for melting nickel-containing raw // Journal of Physics: Conference Series. 2021. Vol. 1753 (1). № 012064. DOI: 10.1088/1742-6596/1753/1/012064
- Shklyarskiy Y., Dobush I., Jiménez Carrizosa M. et al. Method for Evaluation of the Utility’s and Consumers’ Contribution to the Current and Voltage Distortions at the PCC // Energies. 2021. Vol. 14 (24). № 8416. DOI: 10.3390/en14248416
- Skamyin A.N., Rastvorova I.V. Consumed power regulation algorithm in the presence of high harmonics // Journal of Physics: Conference Series. 2021. Vol. 1753. № 012042. DOI: 10.1088/1742-6596/1753/1/012042