Study of the kinetics of the process of producing pellets from red mud in a hydrogen flow
- 1 — Postgraduate Student Saint Petersburg Mining University ▪ Orcid
- 2 — Ph.D., Dr.Sci. Associate Professor Saint Petersburg Mining University ▪ Orcid
- 3 — Ph.D. Associate Professor Saint Petersburg Mining University ▪ Orcid
- 4 — Ph.D., Dr.Sci. Professor Central Metallurgical Research and Development Institute
Abstract
The reduction kinetics of serial phase transitions of iron oxides during reduction to a metallized state with different modes of technical hydrogen supply has been studied and substantiated. The results of the pellets formation when 3-5 % molasses is added to the red mud as a binding reagent are presented. The dependences of the reduction rate of iron oxides on the hydrogen flow rate are obtained. Based on the results of the experiments, a kinetic model was constructed, and with the help of X-ray phase and spectral analysis, it was proved that the agglomerates formed after heat treatment received high strength due to the adhesion of reduced iron particles with red mud particles. The use of a new type of charge materials in melting units will reduce the amount of emissions and dust fractions, as well as increase the metal yield.
Introduction
The production of cast iron and steel is one of the largest industries in the world in terms of output [1, 2]. In recent years, due to a decrease in the resource base and a decrease in the total iron content in the ore, many researchers have focused their efforts on involving in the metallurgical process of production waste [3, 4], semi-products in the form of slags, dust from gas treatment plants and mud [5, 6]. The greatest interest for ferrous metallurgy is the involvement in the melting process of red mud (RM), which is formed as a semi-product in the alumina production by the Bayer method from bauxite [7, 8]. The main indicator of this is the iron content (up to 50-60 %) mainly in the form of Fe2O3 [9]. According to global reporting data, the total amount of RM in storage and landfills in the world is estimated at approximately 1.5 billion tons [10]. In Russia, the annual increase in alumina production waste is 7-8 million tons with a total volume of 600 million tons, which are concentrated in sludge storage mainly in the Sverdlovsk region (Ural region). Thus, red muds in the form of a significant amount of off-balance materials of alumina production can be considered as a source of the main charge material for producing cast iron and steel, while reducing the volume of mud storage areas can solve a major environmental problem in the production areas of aluminum enterprises [8, 11, 12].
Since iron in red muds is present in both oxide and hydroxide forms, it is of scientific and technical interest to carry out processing taking into account phase transitions in a reducing medium. Many studies on waste recycling are aimed at developing disposal methods taking into account the multicomponent composition for obtaining various functional materials [12], such as building materials [13-15], paints and pigments [16], catalysts [17], sorbents [18] or selectively isolated oxides of titanium, aluminum, silicon and iron [19-21]. The most promising and effective, as well as reasonable from the point of view of solving environmental problems, is the direct reduction of some metals from oxides [22-24].
Thus, if red mud is considered a semi-product that has undergone preliminary preparation for the production of alumina, then it is most promising to organize the process of obtaining pellets [25] together with gas treatment to obtain reduced products that can perform the function of a strengthening material [26-28]. When processing the prepared pellets in a gas flow, in a given temperature regime, a serial transition of oxide forms to hydroxide forms occurs with the formation of a porous agglomerate, which has a rigid frame of reduced iron, after which the pellets quickly dissolve in the melt during blast furnace melting at a rate exceeding the melting rate of some iron-containing ores [29].
Conducting experiments on the processing of red mud
In [30-32], the parameters of direct reduction of compounds from iron ore pellets at various temperatures under controlled atmospheric conditions were studied. The use of technical hydrogen H2 as a reagent in several variants increases the rate of interaction, especially in a CO2 atmosphere at a temperature of 900-1100 °C.
The results of an experimental study of the direct reduction of pellets of various compositions after the magnetic separation operation confirm the effectiveness of the process. Studies have shown that the reduction of iron under specified conditions is 61.85 % with a total iron content of 65.93 % in the concentrate. On the other hand, under certain conditions, it is possible to obtain a richer concentrate with 90.3 % by weight of Fe – with a degree of metallized state of 94.8 %. However, the use of this method on an industrial scale is economically impractical due to significant energy costs. When briquetting red mud, there are methods of direct injection of iron turnings and dust [33], which serve as a strengthening material and increase the total iron content in briquettes, but these methods are also very expensive for industrial use.
In any case, the study of the process of direct selective separation of iron-containing phases in the hydrogen flow by means of electromagnetic separation may become the subject of the development of a more efficient method of briquetting or agglomeration of red mud. The possibility of direct reduction of iron during the processing of raw pellets from RM with a flow of technical hydrogen H2 is presented in the [20].
The purpose of this work is to develop a technology for producing pellets from samples of red mud from the Uralsky Aluminum Plant in mine-type heating furnaces, combined with hydrogen treatment for subsequent production of reduced products in the form of agglomerates with a high content of reduced iron for blast furnace melting.
Materials and their characteristics
Red mud samples were taken from the mud storage areas of the Uralsky Aluminum Plant (Kamensk-Uralsky, Sverdlovsk region). In the process of alumina production, this plant uses bauxite from various deposits (Severo-Uralskoye, Timanskoye, Yamayskoye, Gvineiskoye), so the content of some components that pass into red sludge (in particular, iron) can vary significantly. Sampling was carried out with a special sampler directly from the hot mud of alumina workshop N 1 (conversion 1 according to the Bayer method) before it was shipped to the mud storage area from the tank. The sampling periodicity was 24 days for 3 samples in 0.5 l containers, taking into account the stable silicon module during the technological cycle in workshop N 1. Sample preparation was carried out according to the RUSAL-UAZ standard in TSLAIT.
At the first stage, RM samples to remove external moisture (MOI) were dried for 2 h at a temperature of 110 °C, then subjected to abrasion in a Nietzsche mill. The chemical composition and microstructure features of red mud particles were determined using X-ray diffractometry SEM analysis and energy dispersive X-ray spectroscopy. Molasses 2-5 % was added as a binder to improve pelletizing.
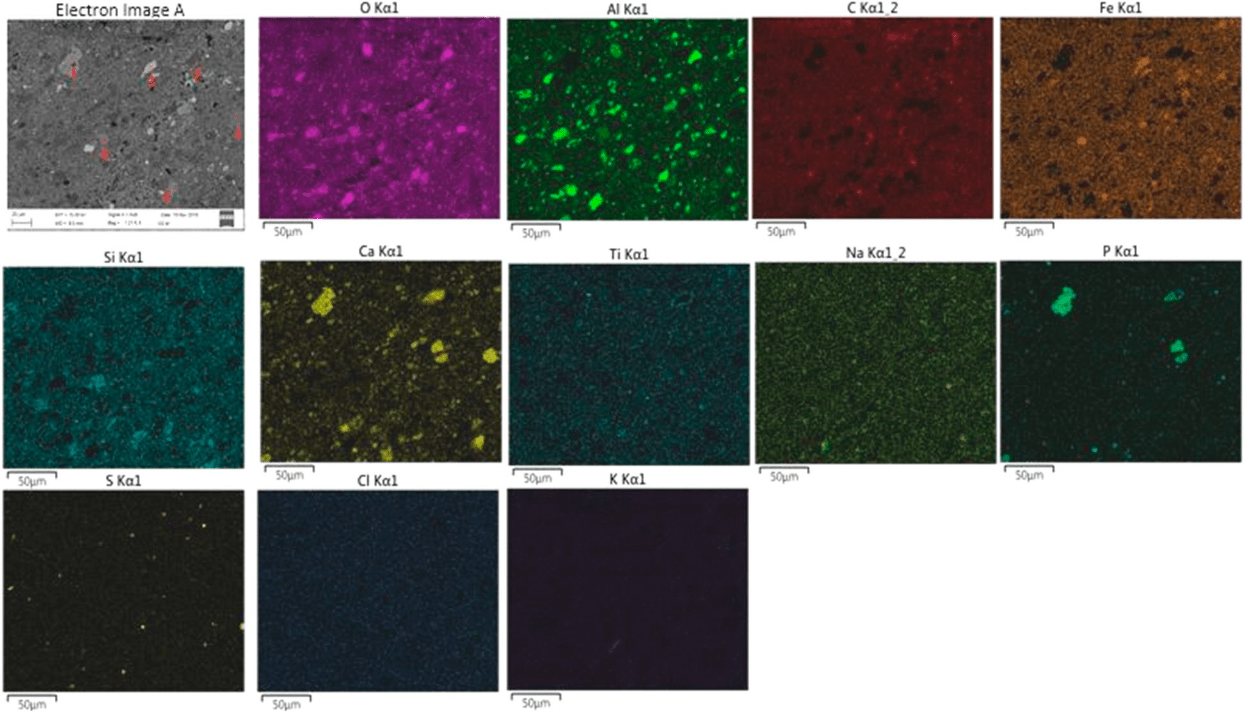
Fig.1. Distribution of elements in the UAZ red mud
The initial mineralogical composition of the red mud mixture was studied using a Siemens D5000 XRD powder diffractometer. X-ray fluorescence analysis was carried out in the laboratories of the Mining University and the University of Oulu (Finland). A chemical analysis of red mud samples was carried out on the Bruker AXS S4 Pioneer analyzer. To reduce the impact of impurities, the main elements were identified on a rotating glass disk.
Thermogravimetric analysis of RM samples weighing 30 g was carried out in platinum crucibles at the ISO:2000 certified Nietzsche STA409 PC Luxx installation in an argon atmosphere (99.999 % purity) at a temperature of 50-1400 °C with a heating rate of 20 °C/min.
Features and main characteristics of the red mud of the Ural region
The chemical composition of the RM samples of the Uralsky Aluminum Plant was obtained using X-ray fluorescence analysis: Fe – 35.01, Fe2O3 – 50.02, SiO2 – 7.14, Al2O3 – 12.73, CaO – 15.00, MgO – 1.01, P2O5 – 0.93, MnO – 0.21, K2O – 0.11, TiO2 – 5.70, S – 0.90, mass loss ignition (internal moisture) – 5,40 % by weight. Initial distribution of red mud particles: 2.4 % (size +2 mm); 11.6 % (+1 mm); 35.70 % (+0.59 mm); 29.6 % (+0.25 mm); 11.4 % (+0.17 mm); 8.1 % (+0.105 mm); 1.2 % (-0.105 mm). The analyzed RM samples using Mastersizer 3000 are distributed in size 0.1-2 mm. The mineralogical composition was determined by X-ray diffraction (XRD) on a BrukerAxs D8 Advance analyzer (Germany) with a Cu-cathode.
Fig.1 shows the distribution scheme of the main elements in the red mud, which consists of the following components: hematite (Fe2O3), kaolin (Al2O3·2SiO2·2H2O), calcium anhydrite (CaSO4), gibbsite (Al(OH)3, anatase (TiO2), quartz (SiO2) and calcium carbonate (CaCO3).
The experimental part
The red mud pellets were prepared in a special disc mixer by adjusting the rotation speed and holding time. Technical characteristics of the mill: disc diameter 400 mm, tank depth 100 mm, tilt angle 52°, rotation speed 17 m/s, rotation time 10 min.
After removing the raw pellets from the mixer shell, they were dried for 56 hours and subjected to a strength test when compressed and dropped from a height of 46 cm. Drying of the material was carried out first in crucibles in a drying cabinet at a temperature of 70-90 °C to a moisture content of 5-10 %, then the mixture was loaded into a rotating shell to produce pellets with the addition of a binder. The crushed RM fraction was fed into the disk pelletizer to a size of less than 500 microns weighing 200 g. Water with molasses in a ratio of 5:1 was supplied to the surface of the disk pelletizer. Pellets were formed within 10 minutes. At the end of the experiment, granules were selected, sieved to a fraction of 3-7 mm in size, which was taken as a measure of the productivity of the disk pelletizer. Then part of the pellets went to the dehydration site, and the second part was subjected (without dehydration) to a strength test. The granules were sieved for air drying for 3 days.
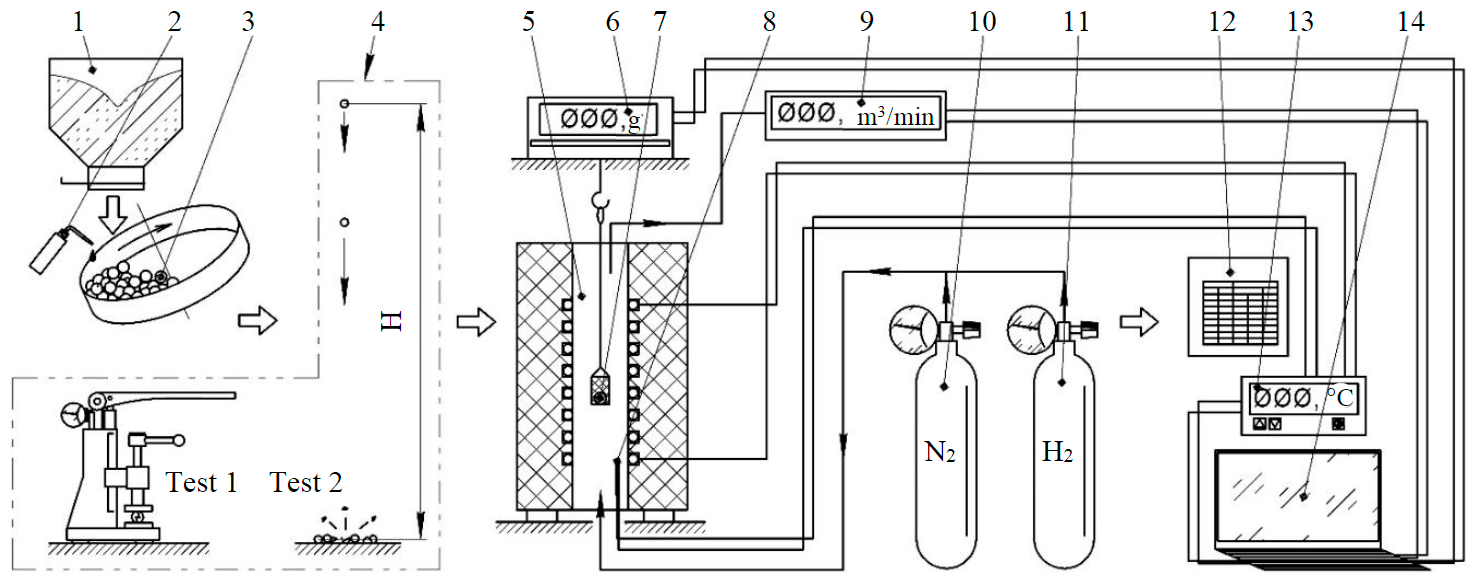
Fig.2. Technological scheme of the RM complex processing experiment 1 – hopper with red mud; 2 – water dispenser with molasses; 3 – disc pelletizer; 4 – strength tests; 5 – shaft furnace; 6 – electronic scales; 7 – Ni-Cr basket with pellets; 8 – heating element and thermocouple; 9 – flow meter; 10 – nitrogen cylinder; 11 – hydrogen tank; 12 – digital converter with PID controller; 13 – term controller; 14 – computer
For each pellet, the mass loss was estimated and the arithmetic mean value of the strength test was calculated. The test according to the standard procedure was repeated three times under the same conditions for pellets of 3-7 mm in size.
To determine the destructibility of pellets, a free fall test was performed on a steel or concrete slab from a height of 46 cm. Resistance to fall damage shows how often green and dry pellets can fall before they show noticeable cracks or crumble. To determine the coefficient of resistance to the dynamic destruction of pellets, a free fall test is performed. Resistance to damage during a fall shows the ratio of whole pellets to destroyed ones. The test was carried out three times with wet pellets (the first day – 24 hours), after which they were dried and tested for destructibility after 56 hours dry (after three days) three more times. The number of destroyed parts was recorded for each experiment and determined based on the arithmetic mean.
Fig.2 shows the scheme of complex processing of red mud to obtain agglomerate with a high content of metallized phase.
At the first stage, 200 g of red mud with a 12 % moisture content was loaded into the receiving tank with a change in the amount of molasses 2-5 %, then it was sprayed onto the surface of the rotating disk ram of the mixer 3. Average composition of molasses mixture: water 20; sugar 62 (sucrose 32; fructose 16; glucose 14); nitrates 10; ash 8 % by weight. The productivity of the mixer for obtaining raw pellets of 3-7 mm in size was calculated by the formula
where WP – the mass of pellets with a given size, g; WF – the mass of red mud loaded into the disc mixer, g.
Results and discussion
Influence of molasses concentration
The effect of adding different amounts of molasses binder (1-4 %) on the mechanical properties of the obtained green and dried granules when mixed in a disk pelletizer at a moisture content of 8 % was studied. It was found that with an increase in the amount of molasses binder, productivity increases. The productivity of the pelletizer with the addition of 1.0 % molasses was 20.0 %, at 1.5 – 31.3, at 2.0 – 42.0, at 3.0 – 43.2, at 4.0 – 38.4 for pellets 3-7 mm. This is due to the fact that with an increase in the amount of molasses binder (Fig.3) dissolved in water, the liquid viscosity increases. This leads to the fact that the capillary pressure of the liquid between the finer particles is higher than that of the coarser particles. This causes their sticking and is due to the fact that interparticle forces decrease with increasing particle size [34].
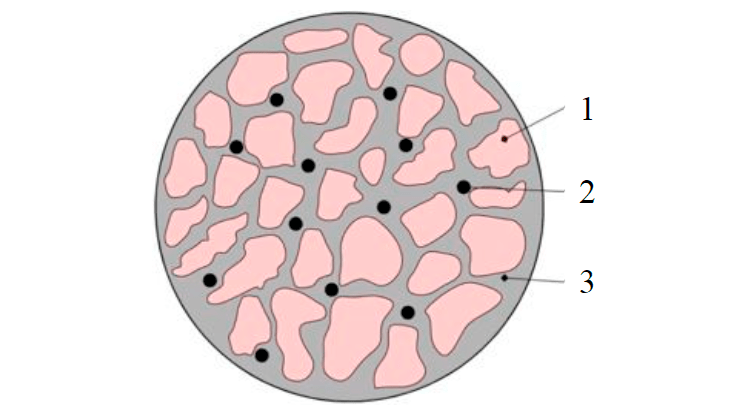
Fig.3. The structure of the pellet 1 – RM; 2 – molasses as a binder; 3 – water
Then the dried pellets were fired in a muffle furnace at a temperature of 900-1200 °C and the behavior of pellets and the effect of heating in neutral and reducing atmospheres were studied. The paper [35] describes the operation of red mud recovering in a vertical furnace in the temperature range of 800-1000 °C. Nitrogen with a feed rate of 1 l/min was used as the controlled atmosphere of the furnace. The pellets were moved to a special Ni-Cr mesh basket and placed in the central zone of the furnace in a hanging state for 30 minutes. To control the change in the weight of pellets, the basket pendant was connected and attached to an electronic scale.
After the completion of the first stage of processing pellets in the furnace, the supply mode was changed and the gas was replaced from nitrogen to hydrogen. The hydrogen pressure was increased at room temperature. The hydrogen source was an electrochemical cell with a passive non-consumable cathode [36], from which hydrogen H2 was released at a load of 100 A during water electrolysis.
Some of the oxides (SiO2, TiO2, Al2O3, MgO, CaO) that are passive to the reduction processes must be converted into a slag component. On the other hand, the amount of reacted oxygen during the supply of hydrogen for the reduction processes of some oxides can be correlated with the indicators of mass loss. Then the yield coefficient of the products, taking into account the mass loss, can be calculated using the following equation:
where M1 – the initial mass of the pellet before the reduction stage, g; M2 – the weight of the sample extracted at various time intervals, g; Mo – the mass of the recovered pellet (agglomerate), g.
According to [26], the state diagram for standard conditions during the phase transition of some oxides to the elementary state (in particular sodium, zinc, lead) at a certain heating temperature in the furnace, sublimate into vapors. In our case, when the RM pellets are heated and processed to a temperature of 900 °C, a whole complex of elementary reduction reactions takes place.
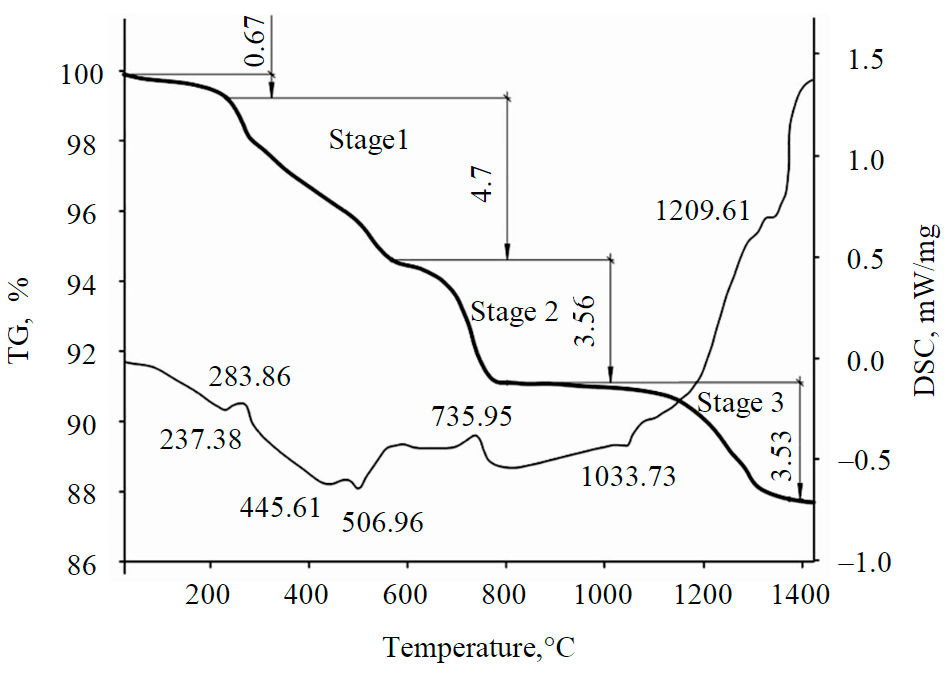
Fig.4. Thermogravimetric curve during heating of a sample of a red mud pellet (UAZ)
Thermal analysis of red mud samples
The results of differential scanning calorimetry (DSC) during heat treatment of red mud samples are shown in Fig.4. The weight of the studied samples was 16.04 g with a weight loss of 12.44 %. Temperature changes have a special effect on mass loss, while there are obvious leaps that can be used to determine possible phase transitions associated with reactions taking place during this time interval with the heat release during the sequential reduction of iron oxides.
At the initial stage of heat treatment in the temperature range of 40.0-244.8 °C, the mass loss of samples is insignificant and amounts to 0.67 %. The change in the mass of RM samples during this period is associated with the loss of external moisture primarily during evaporation. Then there are three main stages of the process:
- The temperature range is 244.8-575.7 °C, when the moisture loss is 4.70 %. This is mainly due to the processes of chemical adsorption of water and decomposition of gibbsite Al2O3 [37].
- In the temperature range of 575.7-897.0 °C, mass losses are associated with the processes of degradation of internal moisture in kaolin and the transition to the form of calcium carbonate. The mass loss during this period is 3.56 %, and the limiting stage takes place at a temperature of 735.9 °C and ends with the decomposition of carbonate (calcite). As noted in [38], calcium carbonate can form in local volumes in the range of 560-720 °C, just as kaolin decomposes at a temperature of 600 °C [39]. At heat treatment temperatures of 800-1100 °C, the mass of samples practically does not decrease.
- At a temperature of 897.0-1400.0 °C, the mass loss is 3.53 %, and, according to previous studies [40], some silicates decompose during this period, which is confirmed by the endothermic peak on the curve at 1209 °C.
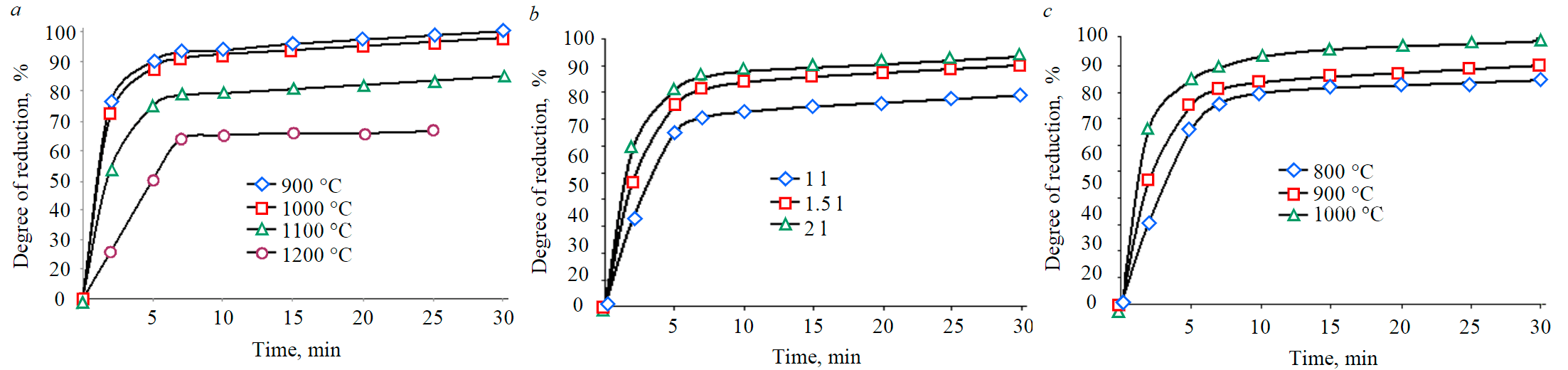
Fig.5. Dependence of the degree of reduction (%) of RM pellets on the sintering temperature (at a hydrogen flow rate of 1 l/min) (a), on different hydrogen consumption (b), with temperature changes (at a hydrogen flow rate of 1.5 l/min) (c)
Sintering RM at different temperatures
The cold compressive strength of the treated pellet at a moisture content of 8 % and molasses of 3 % after sintering at a temperature of 900-1200 °C increases, the sintering temperature also increases.
The effect of the firing temperature on the degree of reduction
The dependence of the degree of RM pellets reduction at a temperature of 900 °C in an atmosphere of hydrogen with a flow rate of 1 l/min, sintered at different temperatures, is shown in Fig.5. The percentage of reduction decreased as the sintering temperature increased.
The heat treatment process takes place in three stages, when the reduction begins at a temperature of more than 800 °C, and the main phase transitions occur in two stages to a temperature of < 900 °C:
For temperature range > 1100 °C:
Thermodynamic analysis shows that optimal results (with a reduced iron yield of up to 87 %) are obtained by direct conversion of hematite into the magnetite phase [20].
Based on the results shown in Fig.5, a, the sintering mode of pellets RM 900 °C, three different H2 flow rates (1, 1.5 and 2 l/min) at a constant reduction temperature (900 °C) for 30 min was chosen to study the recovery rate at different hydrogen consumption. The reduction of RM pellets had a rapid increase with an increase in hydrogen consumption (Fig.5, b). This is due to an increase in hydrogen consumption, which contributes to an increase in hydrogen adsorption, and subsequently the reaction rate increases. The consumption of hydrogen increases, which increases the diffusion of gas through the boundary layer and thereby increases the reduction of ions, which, in turn, leads to an increase in the speed of the stages of the chemical reaction.
The graph of recovery of RM pellets with hydrogen (H2) at a constant flow rate of 1.5 l/min in the temperature range of 800-1000 °C is shown in Fig.5, c. In the initial stages, the reduction rate is the highest for any given reduction temperature, and only then it gradually decreases until the end of the reduction reaction. An increase in temperature leads to an increase in the rate of mass transfer during diffusion, and the rate of desorption increases with the removal of oxygen.
The degree of reduction increases with increasing temperature. A high degree of reduction of RM pellets in the early stages includes the reduction of hematite and magnetite to wustite and part of wustite to iron. The relative slowdown in the recovery rate at the final stage was associated with the recovery of FeO to Fe.
Kinetics of reduction processes of red mud samples
Knowledge of kinetic behavior is necessary to understand and predict reduction processes. There are many methods for estimating isothermal kinetic parameters [41]. In this study, the diffusion process control equation is used to determine the kinetic parameters [42]:
where R – the fractional reduction; t – the reduction time; k – the rate constant.
To study the kinetic features of the reduction process, thermal reduction of RM pellet samples was carried out in a hydrogen medium at 800, 900 and 1000 °C for 0-30 min to obtain the activation energy value.
The graph of the dependence of 1 – 2/3R – (1 – R)2/3 on time is presented for different reduction temperatures in Fig.6. As a result of applying several kinetic models to the reduction process, the following was obtained. The activation energy of the reduction reaction and the pre-exponential coefficient can be calculated using the Arrhenius equation. The reaction rate constant is calculated as follows:
where k0 – the pre–exponential coefficient; Eа – the activation energy; R – the universal gas constant; T – the temperature (°С).
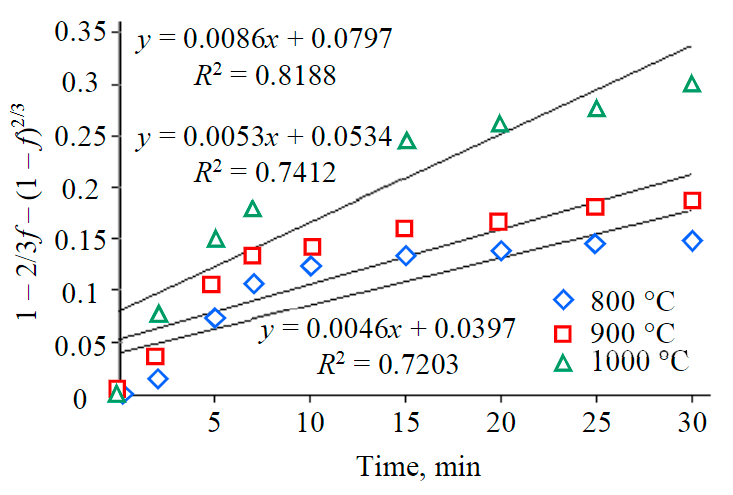
Fig.6. Dependence of the controlled diffusion rate (1 – 2/3f – (1 – f)2/3) on the reduction time RM in the hydrogen atmosphere
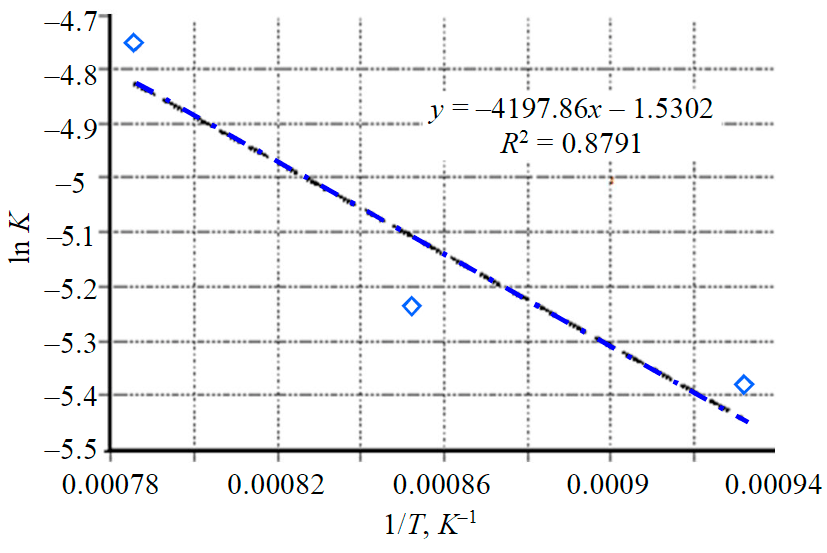
Fig.7. Dependence of the reaction rate ln K on 1/T for diffusion control models
The lnK dependences on 1/T (Fig.7) form a straight line; the tilt of the section is expressed in relation to E/R. Thus, the activation energy can be obtained by multiplying the tilt by the universal gas constant, it is 35 kJ/mol.
As a result of the conducted research, it is possible to obtain iron-containing products that can become alternative raw materials [43-47]. This corresponds to the Action Plan for the development of the mineral resource base of Russia [48-50].
Conclusions
The complex of studies carried out on the processing of red mud from the Uralsky Aluminum Plant showed the possibility of obtaining high-strength agglomerates with elements of reduced iron when creating technological conditions for heating pellets in a reducing medium of technical hydrogen:
- The addition of red mud powder mixed with molasses at the first stage ensures the preservation of the size of raw pellets 3-7 mm and a sufficient level of strength for the subsequent classification and agglomeration operation.
- With an increase in the firing temperature of pellets, their strength increases, which is associated with the formation of phases of reduced iron with a decrease in the overall porosity level.
- At a given rate of hydrogen flow in the furnace volume, iron oxides are reduced to 87 %, with a sequential increase in temperature at a rate of 20 ° C/min in the range of 800-1000 ° C.
The use of hydrogen as a reducing atmosphere when heating pellets of red mud makes it possible to obtain agglomerates with a high degree of strength at an iron content of 70-80 % without admixtures of sodium, phosphorus, zinc. This approach gives grounds to use agglomerates from red mud as an alternative raw material for blast furnace melting. This technology is more efficient in terms of performance (high-strength agglomerate with a high iron content of up to 87 %) and in terms the kinetics of the process (thermodynamic conditions in the hydrogen flow occur with higher rates of transition from one oxide form to another).
References
- Kaushik P., Fruehan R.J. Behavior of direct reduced iron and hot briquetted iron in the upper blast furnace shaft: Part I. Fundamentals of kinetics and mechanism of oxidation. Metallurgical and Materials Transactions B. 2006. Vol. 37, p. 715-725. DOI: 10.1007/s11663-006-0055-2
- 2. Wiley D.E., Ho M.T., Bustamante A. Assessment of Opportunities for CO2 Capture at Iron and Steel Mills: An Australian Perspective. Energy Procedia. 2011. Vol. 4, p. 2654-2661. DOI: 1016/j.egypro.2011.02.165
- Khalifa A.A., Utkov V.A., Brichkin V.N. Red mud effect on dicalcium silicate polymorphism and sinter self-destruction prevention. iPolytech Journal. 2020. Vol. 24. N 1, p. 231-240 (in Russian). DOI: 10.21285/1814-3520-2020-1-231-240
- Besedin A.A., Utkov V.A., Brichkin V.N., Sizyakov V.M. Agglomeration sintering of red mud. Obogashchenie rud. 2014. Vol. 2, p. 28-31.
- Trushko V.L., Kuskov V.B., Kuskova Ya.V. Complex processing of high-grade iron ores. Obogashchenie rud. 2014. Vol. 1, p. 39-43.
- Branca T.A., Colla V., Algermissen D. et al. Reuse and Recycling of By-Products in the Steel Sector: Recent Achievements Paving the Way to Circular Economy and Industrial Symbiosis in Europe. Metals. 2020. Vol. 10. Iss. 3, p. 1-18. DOI: 10.3390/met10030345
- Cao J.-L., Yan Z.-L., Deng Q.-F. et al. Mesoporous modified-red-mud supported Ni catalysts for ammonia decomposition to hydrogen. International Journal of Hydrogen Energy. 2014. Vol. 39. Iss. 11, p. 5747-5755. DOI: 10.1016/j.ijhydene.2014.01.169
- Prabu V.A., Manikandan V., Uthayakumar M. Effect of red mud on the mechanical properties of banana/polyester composites using design of experiments. Proceedings of the Institution of Mechanical Engineers, Part L. Journal of Materials: Design and Applications. 2013. Vol. 227. N 2, p. 143-155. DOI: 10.1177/1464420712464709
- Kumar S., Kumar R., Bandopadhyay A. Innovative methodologies for the utilisation of wastes from metallurgical and allied industries. Resources, Conservation and Recycling. 2006. Vol. 48. Iss. 4, p. 301-314. DOI: 10.1016/j.resconrec.2006.03.003
- Ayres R.U., Holmberg J., Andersson B. Materials and the Global Environment: Waste Mining in the 21st Century. MRS Bulletin. 2001. Vol. 26. Iss. 6, p. 477-480. DOI: 10.1557/mrs2001.119
- Utkov V.A., Sizyakov V.M. Modern questions of the metallurgical processing red mud. Journal of Mining Institute. 2013. Vol. 202, p. 39-43 (in Russian).
- Podgorodetskiy G., Gorbunov V., Panov A. et al. Complex additives on the basis of red mud for intensification of iron-ore sintering and pelletizing. Light Metals. 2015, p. 107-111.
- Fu T., Wei, J.H., Bao H., Liang J. Multiscale Study on the Modification Mechanism of Red Mud Modified Asphalt. Advances in Materials Science and Engineering. 2020. N 2150215, p. 1-9. DOI: 10.1155/2020/2150215
- Liu Yanju, Naidu R. Hidden values in bauxite residue (red mud): Recovery of metals. Waste Management. 2014. Vol. 34. N 12, p. 2662-2673. DOI: 10.1016/j.wasman.2014.09.003
- Mukiza E., Ling Ling Zhang, Xiaoming Liu, Na Zhang. Utilization of red mud in road base and subgrade materials: A review. Resources, Conservation and Recycling. 2019. Vol. 141, p. 187-199. DOI: 10.1016/j.resconrec.2018.10.031
- Pera J., Boumaza R., Ambroise J. Development of a pozzolanic pigment from red mud. Cement and Concrete Research. 1997. Vol. 27, Iss. 5, p. 1513-1522. DOI: 10.1016/S0008-8846(97)00162-2
- Qiang Liu, Ruirui Xinab, Chengcheng Li et al. Application of red mud as a basic catalyst for biodiesel production. Journal of Environmental Sciences. 2013. Vol. 25. Iss. 4, p. 823-829. DOI: 10.1016/S1001-0742(12)60067-9
- Shaobin Wang, Ang H.M., Tadé M.O. Novel applications of red mud as coagulant, adsorbent and catalyst for environmentally benign processes. Chemosphere. 2008. Vol. 72, p. 1621-1635. DOI: 10.1016/j.chemosphere.2008.05.013
- Akcil A., Akhmadiyeva N., Abdulvaliyev R. et al. Overview On Extraction and Separation of Rare Earth Elements from Red Mud: Focus on Scandium. Mineral Processing and Extractive Metallurgy Review. 2018. Vol. 39. Iss. 3, p. 145-151. DOI: 10.1080/08827508.2017.1288116
- Alkan G., Xakalashe B., Yagmurlu B. et al. Conditioning of Red Mud for Subsequent Titanium and Scandium Recovery – A Conceptual Design Study. World of Metallurgy – ERZMETALL. 2017. Vol. 70. N 2, p. 5-12.
- Das B., Prakash S., Reddy P.S.R., Misra V.N. An overview of utilization of slag and sludge from steel industries. Resources, Conservation and Recycling. 2007. Vol. 50. Iss. 1, p. 40-57. DOI: 10.1016/j.resconrec.2006.05.008
- Yi Man, Junxia Feng. Effect of gas composition on reduction behavior in red mud and iron ore pellets. Powder Technology. 2016. Vol. 301, p. 674-678. DOI: 10.1016/j.powtec.2016.06.013
- Man Y., Feng J.X., Wang Y.Y. A study of direct reduction characteristics of bayer process red mud-coal composite pellets. Thermal Science. 2019. Vol. 23. N 5, p. 2569-2576.
- Pyagay I.N., Kremcheev E.A., Pasechnik L., Yatsenko, S.P. Carbonization processing of bauxite residue as an alternative rare metal recovery process. Tsvetnye Metally. 2020, p. 56-63. DOI: 10.17580/tsm.2020.10.08
- Yibo He, Biao Tang, Qiang Li, Zongshu Zou. A Comprehensive Static Model of an Iron Bath Smelting Reduction Process with Thick Slag for Alumina-Rich Iron Ore. ISIJ International. 2015. Vol. 55. Iss. 10, p. 2125-2134. DOI: 10.2355/isijinternational.ISIJINT-2015-255
- Mombelli D., Barella S., Gruttadauria A., Mapelli C. Iron Recovery from Bauxite Tailings Red Mud by Thermal Reduction with Blast Furnace Sludge. Applied Sciences. 2019. Vol. 9. N 22, p. 1-23. DOI: 10.3390/app9224902
- Guoshan Ning, Bo Zhang, Chengjun Liu et al. Large-Scale Consumption and Zero-Waste Recycling Method of Red Mud in Steel Making Process. Minerals. 2018. Vol. 8. N 3, p. 1-16. DOI: 10.3390/min8030102
- Rath S.S., Jayasankar K., Satapathy B.K. et al. Kinetics and Statistical Behaviour of Iron Recovery from Red Mud using Plasma Arc Furnace. High Temperature Materials and Processes. 2011. Vol. 30, p. 211-215. DOI: 10.1515/HTMP.2011.031
- Pyagay I.N., Kozhevnikov V.L., Pasechnik L.А., Skachkov V.М. Processing of alumina production red mud with recovery of scandium concentrate. Journal of Mining Institute. 2016. Vol. 218, p. 225-232 (in Russian).
- Trushko V.L., Utkov V.A., Sivushov A.A. Reducing the environmental impact of blast furnaces by means of red mud from alumina production. Steel in Translation. 2017. Vol. 47. Iss. 8, p. 576-578.
- Zhu De-qing,Chun Tie-jun,Pan Jian, He Zhen. Recovery of Iron From High-Iron Red Mud by Reduction Roasting With Adding Sodium Salt. Journal of Iron and Steel Research International. 2020. Vol. 19. N 8, p. 1-5. DOI: 10.1016/S1006-706X(12)60131-9
- Trushko V.L., Dashko R.E., Kuskov V.B., Klyamko A.S. Technology of “cold” briquetting of rich ores of the Jakovlevsky deposit. Journal of Mining Institute. 2011. Vol. 190, p. 133-137 (in Russian).
- Samouhos M., Taxiarchou M., Pilatos G. et al. Controlled reduction of red mud by H2 followed by magnetic separation. Minerals Engineering. 2017. Vol. 105, p. 36-43. DOI: 10.1016/j.mineng.2017.01.004
- Knight P. Agglomeration processes, phenomena, technologies, equipment. Powder Technology. Verlag GmbH: Wiley-VCH, 2002, p. 29-138. DOI: 10.1002/9783527619801
- El-Hussiny N.A., Shalabi M.E.H. A self-reduced intermediate product from iron and steel plants waste materials using a briquetting process. Powder Technology. 2011. Vol. 205, Iss. 1-3, p. 217-223. DOI: 10.1016/j.powtec.2010.09.017
- Busè R., Mombelli D., Mapelli C. Metals recovery from furnaces dust: Waelz process. La Metallurgia Italiana. 2014. Vol. 106 (5), p. 19-27.
- Antunes M.L.P., Couperthwaite S.J., Conceição da F.T. et al. Red Mud from Brazil: Thermal Behavior and Physical Properties. Industrial and Engineering Chemistry Research. 2012. Vol. 51, p. 775-779. DOI: 10.1021/ie201700k
- Liu Yong, Lin C., Wu Y. Characterization of red mud derived from a combined Bayer Process and bauxite calcination method. Journal of Hazardous Materials. 2007. Vol. 146. N 1, p. 255-261. DOI: 10.1016/j.jhazmat.2006.12.015
- McСann, G., Strezov V., Lucas J.A. et al. Iron Ore Characterisation during High Temperature Thermal Processing. Developments in Chemical Engineering and Mineral Processing. 2004. Vol. 12. N 3/4, p. 1-14.
- Meher S.N. Thermal Analysis of Nalco Red Mud. International Journal of Chemical Studies. 2014. Vol. 1. Iss. 5, p. 1-9.
- Hammam A., Ying Li, Hao Nie et al. Isothermal and Non-Isothermal Reduction Behaviors of Iron Ore Compacts in Pure Hydrogen Atmosphere and Kinetic Analysis. Mining, Metallurgy & Exploration. 2021. Vol. 38, p. 81-93. DOI: 10.1007/s42461-020-00317-3
- Yu-ming Wang, Zhang-fu Yuan. Reductive kinetics of the reaction between a natural ilmenite and carbon. International Journal of Mineral Processing. 2006. Vol. 81. N 3, p. 133-140. DOI: 10.1016/J.MINPRO.2006.07.010
- Litvinenko V. The Role of Hydrocarbons in the Global Energy Agenda: The Focus on Liquefied Natural Gas. Resources. 2020. Vol. 9. Iss. 5. N 59. DOI: 10.3390/resources9050059
- Sizyakov V.M., Kawalla R., Brichkin V.N. Geochemical aspects of the mining and processing of the large-tonne mineral resources of the hibinian alkaline massif. Geochemistry. 2019. Vol. 80. Iss. 3. DOI: 10.1016/j.chemer.2019.04.002
- Litvinenko V.S. Digital Economy as a Factor in the Technological Development of the Mineral Sector. Natural Resources Research. 2020. Vol. 29, p. 1521-1541. DOI: 10.1007/s11053-019-09568-4
- Litvinenko V.S., Sergeev I.B. Innovations as a Factor in the Development of the Natural Resources Sector. Studies on Russian Economic Development. 2019. Vol. 30. Iss. 6, p. 637-645. DOI: 10.1134/S107570071906011X
- Knyazkina V.I., Safronchuk K.A., Ivanov S.L., Pumpur E.V.Assessment of the state of a lubricator by the size of the acoustic signal in a loaded pair of friction of a mining machine transmission. Journal of Physics: Conference Series. 2020. Vol. 1515, p. 1-5. DOI: 10.1088/1742-6596/1515/5/052037
- Quiroz Cabascango V.E., Sharikov Y.V. Mathematical modeling of mass, heat and fluid flow in a reverberatory furnace for melting nickel-containing raw. Journal of Physics: Conference Series. 2021. Vol. 1753 (1). N 012064. DOI: 10.1088/1742-6596/1753/1/012064
- Shklyarskiy Y., Dobush I., Jiménez Carrizosa M. et al. Method for Evaluation of the Utility’s and Consumers’ Contribution to the Current and Voltage Distortions at the PCC. Energies. 2021. Vol. 14 (24). N 8416. DOI: 10.3390/en14248416
- Skamyin A.N., Rastvorova I.V. Consumed power regulation algorithm in the presence of high harmonics. Journal of Physics: Conference Series. 2021. Vol. 1753. N 012042. DOI: 10.1088/1742-6596/1753/1/012042