Empirical regularities investigation of rock mass discharge by explosion on the free surface of a pit bench
- 1 — Ph.D. Leading Engineer Polyus Project LLC ▪ Orcid ▪ Elibrary ▪ Scopus ▪ ResearcherID
- 2 — Ph.D. Researcher Research Institute of Comprehensive Exploration of Mineral Resources, Russian Academy of Sciences ▪ Orcid
Abstract
Minimizing the discharge of blasted rock mass into the developed space of the pit is a very relevant area for study, as it allows to increase the processability of work and reduce the cost of mining. The article presents the results of experimental industrial explosions, during which the study of this issue was conducted. The main purpose of the work was to establish the key factors affecting the volume of rock mass discharge to the pit haulage berm. During the analysis of the world experience of research on this topic, the key factors affecting the formation of collapse and discharge – natural and technological – are identified. The method of conducting experiments and collecting data for analyzing the influence of technological parameters of location, charging and initiation of wells on the volume of rock mass discharge is described. It is established that the main discharge to the pit haulage berm is formed by the volume of rock mass limited by the prism of the slope angle. With a sufficient rock mass displacement from the edge of the bench crest towards the center of the block, only the wells of the 1st and 2nd rows participate in the discharge formation. Empirical dependences of the total volume of rock mass discharge on the length of the block along the bench crest, the specific consumption of explosives, the size of a rock piece P 50 and the rate of rock breaking are obtained. The obtained results can be used to design the parameters of the drilling and blasting operations (DBO), as well as to predict and evaluate the possible consequences of a mass explosion in similar mining and geological conditions.
Introduction
The key result of drilling and blasting operations (DBO) at pits is the formation of the exploded rock mass collapse of the required quality of fragmentation. Depending on the mining and geological conditions and mining technology, certain requirements are imposed on the collapse according to geometric parameters (height, width, length). The geometric parameters of the collapse have a significant impact on the subsequent technological operations and the safety of mining operations [5, 9].
With a large length and width of the collapse, the exploded rock mass lies in a relatively thin layer on a significant area of the bench. At the same time, if the exploded block is represented by a rock mass, including ore and rock areas (Fig.1, a), then there are displacements in the contours of the ore bodies, which affects the quality indicators of the mined mineral [4, 11]. On wide collapses, the productivity of excavators and dump trucks decreases when loading rock mass [3, 5, 8]. It requires the relocation of equipment to clean up the work site. In such production conditions, the restrictions on the positioning of equipment arise and the technical and economic indicators of the company work deteriorate. When the blocks are breaking above the pit haulage or trapping berm, the volume of the discharged rock mass partially, and sometimes completely, overlaps them (Fig.1, b). In this regard, the downtime of mining and transport equipment associated with clearing driveways increases. In addition, extra equipment is required to clear the discharge. Backfilling of catching berms in some cases, when there is no access to the berms for objective reasons, affects the level of safety of mining operations at the lower horizons of the pit. The described consequences from the rock mass discharge deteriorate the extraction technology and require additional costs for mining operations.
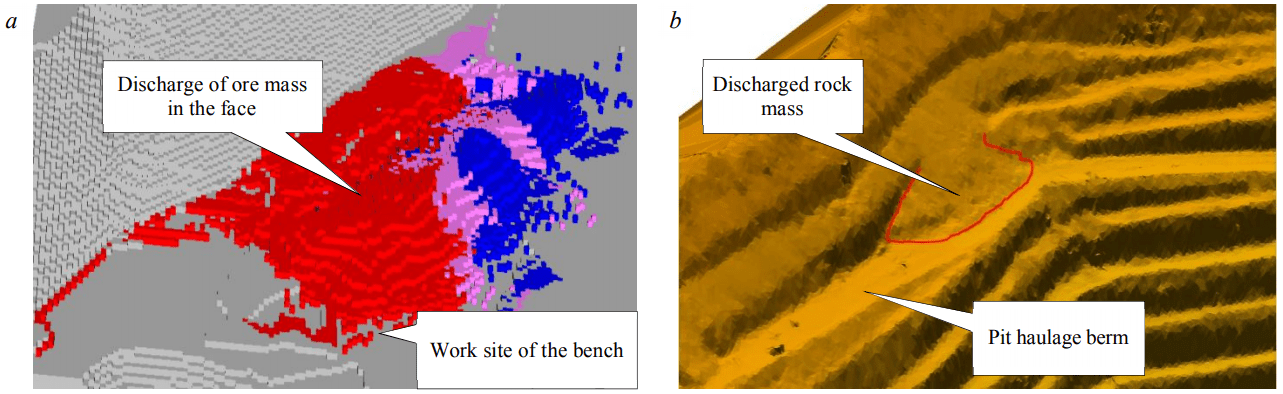
Fig.1. The consequences of discharge of rock mass by blast in a pit. DBO-block on the work site of the bench (a)and above the transport berm (b)
The issues of reducing the width of the collapse and minimizing the volume of discharge to the transport and catching berm of the pit are very relevant for study. Understanding the reasons for the occurrence of the discharge, experimental determination and identification of the main factors affecting the width of the collapse and the volume of rock mass discharge will help the DBO engineer to further manage the parameters of the DBO and will minimize the downtime of mining and transport equipment, increase the productivity of excavation equipment and improve the safety of mining
operations.
Experimental methods
The analysis of the world experience in the study and management of the parameters of the exploded rock mass collapse allowed to identify the key factors affecting the formation of the collapse and discharge. Conditionally, they can be divided into two classes [1, 2, 6, 7, 10, 12-17]: natural – the initial parameters of the exploding rock mass; the technological ones determine the method and means of influence on the rock mass.
Natural factors include the characteristics of the rock mass (physical and mechanical properties of rocks, the direction of fracturing, the size of the jointing in the rock mass, tectonic disturbances, etc.). Technological factors are determined depending on natural factors and can be represented by several subsections. The first one includes the parameters of the charge placement in the rock mass (the diameter and height of the charge, the drilling grid, the type of explosive), which determine the specific consumption of explosives. The second one includes the sequence and direction of initiation of borehole explosive charges. They depend on the type of used initiation methods and the geometry of the exploded block.
In this paper, using the example of the mining and geological conditions of the Vostochniy pit of the Olympiadinsky GOK, the influence of the technological DBO parameters on the volume of rock mass discharge to the free surface of the exploded block from the side of the developed pit space is estimated (Fig.2). For the experiment, a site in the pit was selected that excludes the influence of the retaining wall on the collapse parameters. In all the blasts, the 15-meter upper sub-bench of the 30-meter slope of the bench with a slope angle of 60° was studied. The exploded blocks were composed of carbonate-quartz-mica rocks with a hardness of 7-15 on the Protodyakonov scale and the II-III category of rocks according to fracturing.
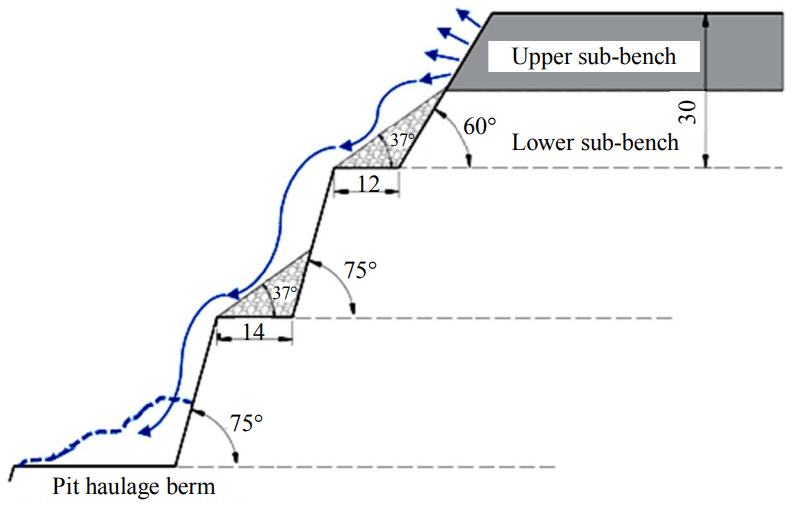
Fig.2. The scheme of experimental blasts
The following parameters were estimated: the specific consumption of explosives, the boreholes diameter, the design of the charge, the installation scheme of the explosive network, the number of free surfaces. To determine the effects of each of them on the volumes of rock mass discharge, a test program was developed, which included conducting a number of experimental blasts of blocks over the pit haulage berm and establishing the relationship between the discharge volumes and various technological parameters of blasting.
The discharge volumes were recorded by surveying measurements before and after the blast. In total, nine large-scale blasts were performed during the experimental work (Table 1). Then the empirical dependences of the volume of discharge per unit length on the technological parameters of the blasting were constructed and analyzed. The emulsion explosive “Emulit” of the brand VET-700 was used. The specific consumption of explosives was taken based on the proven experience of DBO conducting, and changed in the areas of the contour zone.
Table 1
Summary table of experimental blasts
Blast |
Lblock, m |
Vdis, м3 |
Vi, m3/m |
q, kg/m3 |
Br, ms/m |
Average piece, mm |
IS type |
|||
Site 1 |
Site 2 |
1st and 2nd rows |
2nd and 3rd rows |
3rd and 4th rows |
P50 |
|||||
1 |
80 |
6617 |
83 |
1.776 |
1.569 |
32 |
32 |
25 |
253 |
NIS |
2 |
130 |
13945 |
107 |
1.671 |
1.573 |
23 |
29 |
17 |
141 |
NIS |
3 |
107 |
9165 |
86 |
1.598 |
1.516 |
32 |
22 |
21 |
181 |
NIS |
4 |
130 |
9394 |
72 |
1.468 |
1.229 |
44 |
23 |
21 |
196 |
EIS |
5 |
60 |
6863 |
114 |
1.830 |
1.580 |
21 |
21 |
21 |
– |
NIS |
6 |
95 |
5370 |
57 |
1.282 |
1.290 |
31 |
37 |
28 |
240 |
EIS |
7 |
90 |
8387 |
93 |
1.476 |
1.398 |
25 |
17 |
19 |
129 |
NIS |
8 |
60 |
4922 |
82 |
1.664 |
1.418 |
34 |
25 |
18 |
202 |
NIS |
9 |
100 |
9438 |
94 |
1.177 |
1.329 |
43 |
34 |
29 |
198 |
EIS |
To reduce the discharge volumes, small-diameter boreholes were placed in the 1st and 2nd rows (Fig.3), the main boreholes in the 1st row were distributed by an air gap. As an experiment, to determine the effect of a large borehole diameter on the discharge volume, boreholes with a diameter of 311.1 mm were located on two blasts along the 2nd row. Inclined boreholes were drilled along the line of the 1st row, which were charged at 50 % of the main charge. For all the explosions, a cut-in scheme for initiating boreholes was used with the location of the control row in the area of the block center. The diagonals were located in the form of a spike or trapezium with decelerations tested at the company to achieve optimal quality of fragmentation, the rate of rock breaking varied at the level of 15-20 ms/m. The rate of rock breaking for the last three rows changed variably, based on the used initiation systems (IS) – non-electric (NIS Rionel) or electronic (EIS DaveyTronic) (Table 1). The use of two types of IS allowed to work out different deceleration intervals. At the same time, the NIS was used with traditionally approved blasting schemes, and the EIS was used in areas where the rate of rock breaking between rows was increased in order to exclude the likely breakdown of borehole charges.
The following data were tracked and analyzed for each mass blast:
- The length of the block along the bench crest Lblock – the area where there was a rock mass discharge.
- The volume of rock mass discharge Vdis was determined by the mine surveying service of the pit.
- The discharge volume per unit length Vi is a quantitative characteristic for assessing the influence of various parameters, equal to the ratio of the total discharge volume to the length of the block along the edge.
- The specific consumption of explosives q was calculated for two sites on the block (Fig.3): site 1 – the volume of the rock mass, bounded at the top by the prism of the repose angle for hard rocks; site 2 – the volume of the rock mass, including both small-diameter boreholes (215.9 mm) and large-diameter boreholes (311.1 mm). The division by sites was made in order to understand whether the average specific consumption of explosive in the whole block affects the volume of discharge, or whether the 1st and part of the 2nd row still participate in the formation of the discharge.
- The rate of rock breaking between the rows Br – the time of distribution of the explosive rock breaking front in 1 m of the rock mass, was calculated as the ratio of the difference in the values of adjacent time isolines of the explosion mounting scheme to the shortest distance between them (Fig.4). The experiments considered the rate of rock breaking for the first three rows, namely between rows 1-2, 2-3 and 3-4.
- Distribution of the average piece. At all explosions, the particle size composition was measured by the PortaMetrics device. Next, a cumulative graph of the distribution of rock pieces on the block under study was constructed and the characteristic average size of the piece corresponding to 50 % of the total volume of rock pieces (P50) was estimated.
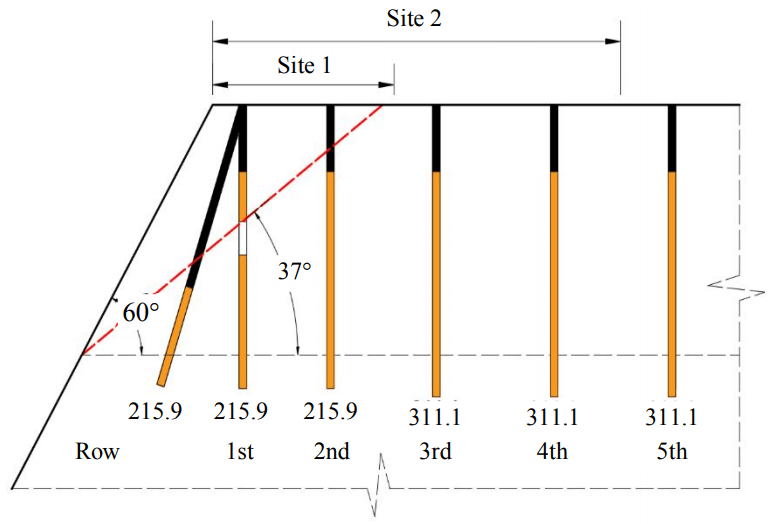
Fig.3. Scheme for calculating the specific consumption of explosives for various sites
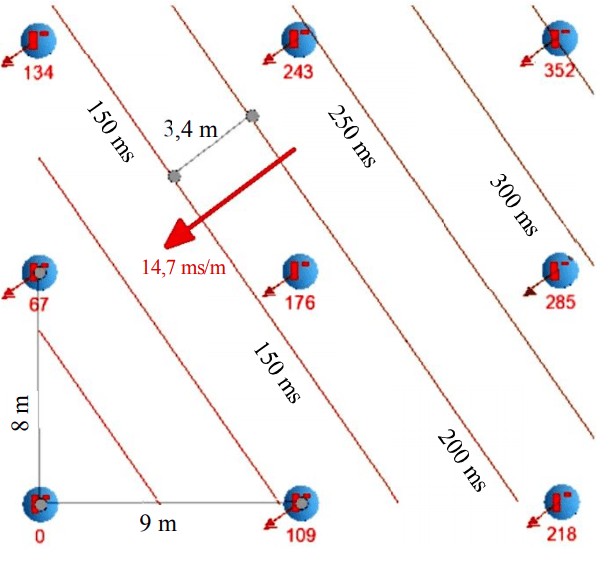
Fig.4. Scheme for calculating the rate of rock breaking
Processing and discussion of the results
The discharge volumes per unit length were 57-114 m3/m (Table 1). If we go back to Fig.3 and estimate the volume of the prism bounded by the repose angle, taking into account the fragmentation coefficient of 1.5 (the empirical average coefficient derived in production), we get an average value of 127 m3/m. Comparing this value with the volume of the actual discharge per unit length, we can conclude that the main discharge of the rock mass in the exploded block is formed precisely by the volume limited by the prism of the repose angle. Thus, with a sufficient displacement of the rock mass towards the center of the block, only the boreholes of the 1st and 2nd rows participate in the formation of the discharge.
Fig.5, a shows the graph of the empirical dependence of the volume of discharge on the specific consumptions of explosives calculated for sites 1 and 2 (see Fig.3). The coefficient of determination for site 1 is higher (0.62 relative to 0.58) than for site 2. This fact confirms the priority of the discharge formation due to the boreholes of the 1st and 2nd rows.
At the blast N 2 and N 5, boreholes with diameters of 311.1 mm were placed along the 2nd row. All other things being equal, this location of the boreholes led to an overestimated discharge volume (107 and 114 m3/m, respectively) relative to the other blasts. On the other blocks, boreholes witha diameter of 311.1 mm were placed starting from the 3rd row. This scheme did not increase the discharge volumes and can be recommended as optimally sufficient to minimize the discharge.
Figure 5, b shows the dependence of the volume of discharge on the size of a rock piece P50. Note that there is a certain dependence of these two parameters – the smaller the size of a rock piece, the greater the volume of discharge. The low correlation indicates that the average particle size composition was taken into account without reference to the volumes of the discharged rock mass (the particle size composition of the discharge was not measured). The obtained correlation in the particle size composition is directly related to the specific consumption of explosives and the rate of rock breaking.
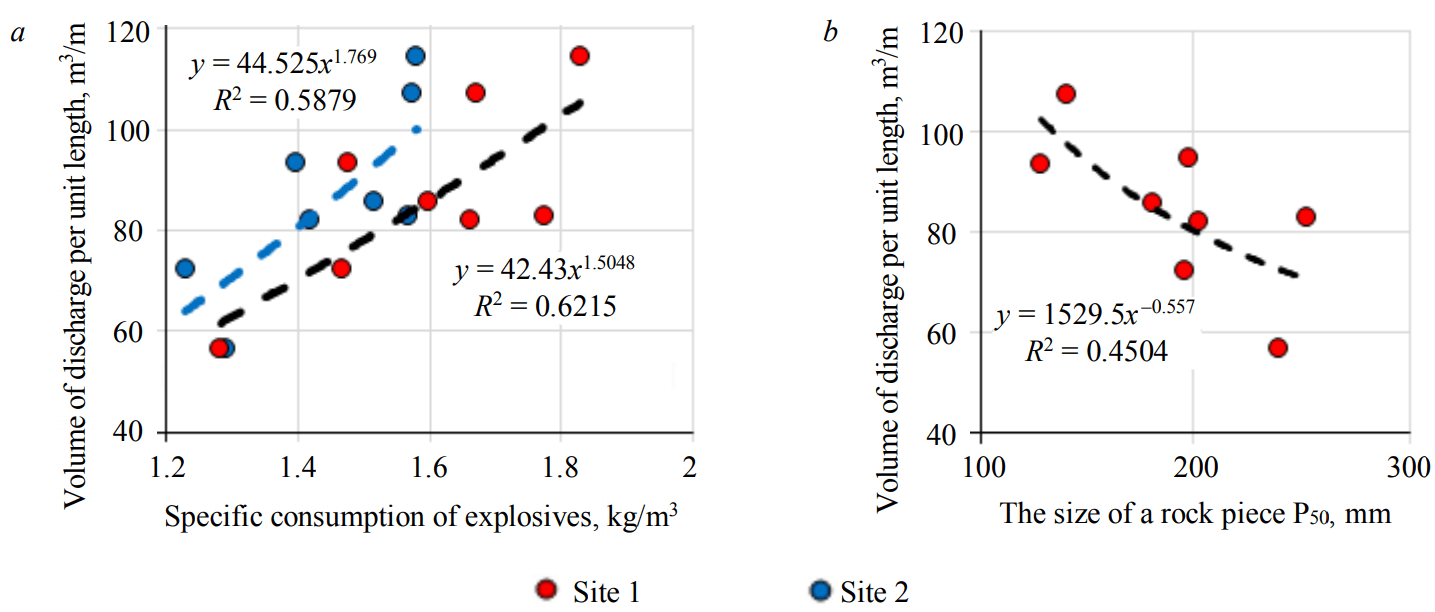
Fig.5. The dependence of the volume of discharge per unit length on the specific consumption of explosives (a) and the average size of a rock piece P50 (b)
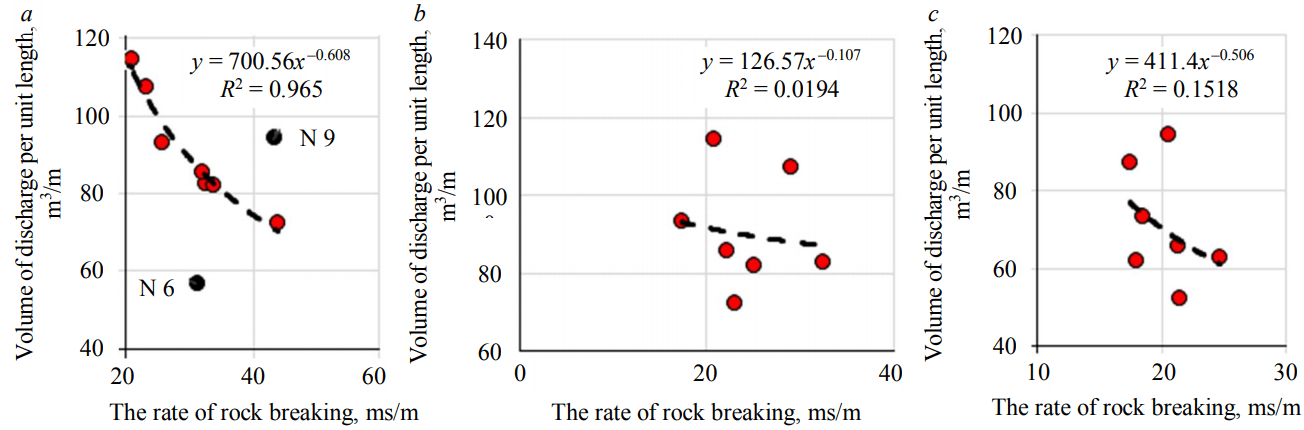
Fig.6. The dependence of the volume of discharge per unit length on the rate of rock breaking between the 1st and 2nd rows (a),
the 2nd and 3rd rows (b), the 3rd and 4th rows (c)
Figure 6 shows the obtained empirical dependences of the discharge volume per unit length on the rate of rock breaking between rows 1-2, 2-3 and 3-4. The high coefficient of determination (0.96) was noted for the rate of rock breaking between the 1st and 2nd rows, which cannot be said about the other sites, where no correlation was found, which means that the volume of discharge directly depends on the deceleration (delay) of the 1st row. This fact confirms the previously proposed provision the priority formation of discharge at the expense of boreholes of the 1st and 2nd rows.
It is necessary to pay attention to the specifics identified during the blasts N 6 and N 9 (Fig.6, a). The lowest discharge volume of 57 m3/m was recorded at blast N 6. Analyzing the parameters of the blast, it is necessary to note a cardinal difference in comparison with other blasts. It consisted in the presence of an additional (third) free surface on the opposite side from the slope of the bench, which was formed by an excavator during the loading of previously exploded rock mass. This blast had the look of a narrow strip with a width of 30 and a length of 100 m, in fact, the rock breaking was carried out in the direction of the space developed by the excavator. Due to this, the minimization of the discharge volume is achieved (the point has the lowest level for discharges on the graph).
At block N 9, a high discharge volume was recorded – 94 m3/m, although the specific consumption of explosives was low, and the rate of rock breaking was increased in comparison with the other blocks (Table 1). During the production of this explosion, a scheme with the distribution of the 1st and 2nd rows was tested (only the 1st row was distributed on the other blocks). We believe that since the 2nd row was distributed, its proper displacement to the center of the block was not achieved, most of the volume of the exploded rock mass from the 2nd row shifted to a lesser extent due to the presence of an air gap and a smaller mass of the charge. At the same time, a support was created for the 1st row, which, under the influence of the blast energy in the clamped environment created by the 2nd row, as well as under the influence of gravity, rolled down to the pit haulage berm at a repose angle.
According to the results of the analysis, it can be argued that the main technological parameters of blasting that affect the volume of rock mass discharge are the specific consumption of explosives falling on the first two rows of boreholes from the bench crest, and the rate of rock breaking between the 1st and 2nd rows. Of course, these two parameters have a complex effect (to a greater extent, the discharge is affected by the specific consumption of explosives and the rate of rock breaking), therefore, it makes sense to determine the general dependence for these two parameters and eliminate uncertainty in the assessment of the priority of each of them.
Since the specific consumption of explosives with the discharge volume has a direct relationship, and the rate of rock breaking is inverse, we will construct an empirical dependence of the discharge volume per unit length Vi on the parameter q/Br (Fig.7).
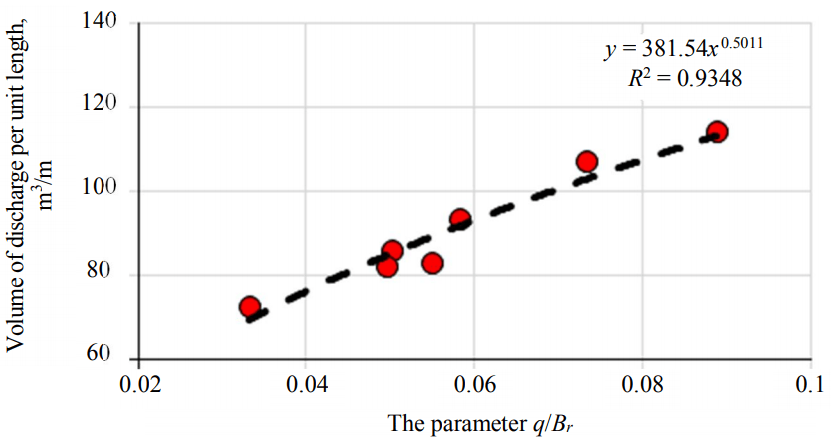
Fig.7. The dependence of the discharge volume on the ratio of the specific consumption of explosives to the rate of rock breaking for the site of the first two rows
The coefficient of determination of the obtained dependence was 0.93. The previously obtained small coefficient of determination for the specific consumption of explosives was completely compensated by the rate of rock breaking, which once again confirms the correctness of the above reasoning. Thus, the parameter of the discharge volume per unit length is a function of the discharge volume and the block length along the bench crest and can be represented by an empirical dependence:
Express the volume of the discharge:
where Lblock is the length of the block along the bench crest, m; q is the specific consumption of explosives for the 1st and 2nd rows, kg/m3; Br is the rate of rock breaking between the 1st and 2nd rows, ms/m (taking into account the retention of the rate of rock breaking between rows 2-3 and 3-4 within 20-30 ms/m).
The obtained dependence can be used in production for predictive calculations of the total discharge volume depending on various technological parameters. For example, we will make a comparative calculation of the predicted volume of rock mass discharge for three blasting conditions:
- Basic, applied version (Lblock = 100 m, q = 1.2 kg/m3, Br = 20 ms/m).
- The specific consumption of explosives is reduced by 10 %, and the rate of rock breaking is increased by 30 m s/m relative to the basic version (Lblock = 100 m, q = 1.1 kg/m3, Br = 50 ms/m).
- The specific consumption of explosives is reduced by 20 %, and the rate of rock breaking is increased by 50 m s/m relative to the basic version (Lblock = 100 m, q = 1.0 kg/m3, Br = 70 ms/m).
Table 2
Comparative table for calculating the total discharge volume
Version |
Lblock, m |
q, kg/m3 |
Br, ms/m |
Vdis, m3 |
Decrease, % |
1 |
100 |
1.2 |
20 |
9357 |
Basic |
2 |
1.1 |
50 |
5666 |
39 |
|
3 |
1.0 |
70 |
4566 |
51 |
The results of the calculations (Table 2) clearly show that when changing the two main technological parameters, the discharge volume can be reduced almost twice in comparison with the basic version. It should be noted that taking into account the decrease in the specific consumption of explosives and an increase in the rate of rock breaking, it is likely that an insufficient quality of rock fragmentation will be obtained (in the conditions of the conducted experiments, good quality was obtained). With a decrease in the specific consumption of explosives, the charge fragmentation energy decreases, and with an increase in the rate of rock breaking, the probability of damage (breakdown) of near-by explosive charges which are exploded at different times increases. Therefore, the DBO parameters should be selected by experimental-industrial blasts taking into account specific mining and geological conditions and taking into account the requirements for the quality of the blast. The obtained empirical dependence (2) allows to select the DBO boundary parameters without taking into account the requirements for the blast quality criterion. The question of the mutual correlation of the DBO quality and the volume of discharge is planned to be additionally studied by experimental-industrial blasts, including that with the development of more representative statistics (also at other pits) according to the methods and dependencies given in this article.
Conclusion
A complex of experimental-industrial blasts of blocks on a free surface above the pit haulage berm was carried out. The purpose of the work is to establish technological criteria that affect the volume of rock mass discharge in the mining and geological conditions of the active pit. Based on experimental work, an empirical dependence was obtained for determining the discharge volume on the parameters of the specific consumption of explosive, the rate of rock breaking and the length of the block along the bench crest. Important aspects that can be applied by DBO engineers when designing a large-scale blast to minimize the volume of rock mass discharge to the pit haulage berm have been established:
- The optimal number of rows of small diameter boreholes (215.9 mm) along the bench crest, taking into account the minimization of discharge, is two rows. The location of large-diameter boreholes (311.1 mm) on the 2nd row led to an increase in the discharge volume by 32 % compared to the diameter of 215.9 mm.
- The distribution of the 2nd row along with the 1st led to an increase in the discharge volume by 30 % compared to the distribution of only one first row.
- An additional (third) free surface formed by the excavator on the opposite side of the slope of the bench reduced the discharge volume by 32 % compared to the version with two free surfaces (i.e. without preemptive loading of part of the block).
The obtained results can be used in production when designing large-scale blasts over a pit haulage berm to assess possible consequences and make operational adjustments to the DBO project. The directions of further research within the framework of the covered topic will be aimed at obtaining a larger number of measurements, taking into account the study of the dependence of the discharge on natural factors, as well as the presence of a retaining wall when working out the sub-bench.
References
- Aharonyan G.A., Aharonyan A.G. Modeling the process of the displacement and formation of the exploded rock mass desintegration at an explosion in a fractured medium. Metallurgiya, materialovedenie, nedropolzovanie. 2018. N 1 (21), p. 84-95 (in Russian).
- Alenichev I.A. Correction of explosive ratio with allowance for apatite-nepheline ores flooding. Mining informational and analytical bulletin. 2016. N 7, p. 364-373 (in Russian).
- Blinov A.N. Regularities of the formation of the structure of the rock mass collapse during blasting operations at pits: Avtoref. dis. … kand. tekhn. nauk. Ekaterinburg: Institut gornogo dela Uralskogo otdeleniya Rossiiskoi akademii nauk, 2001, p. 24 (in Russian).
- Kabelco S., Dunaev V., Guerasimov A. Verification of computer technology of forecasting the collapse of blasted rock mass in open pits. Mine surveying and subsurface use. 2016. N 3 (83), p. 62-65 (in Russian).
- Kopylov S.V. Method for determining the parameters of the exploded rock mass collapse in pits: Avtoref. dis. … kand. tekhn. nauk. Moscow: Institut problem kompleksnogo osvoeniya nedr Rossiiskoi akademii nauk, 2005, p. 22 (in Russian).
- Laptev Yu.V., Kantemirov V.D., Yakovlev A.M. Computer modeling of rock mass breakup in selective mining. Almanac of Modern Science and Education. 2014. N 5-6 (84), p. 92-96 (in Russian).
- Paramonov G.P., Lisevich V.V. Forecasting of parameters of a rock mass collapse when blasting work. International Research Journal. 2016. N 4 (46), p. 100-103. DOI: 10.18454/IRJ.2016.46.025 (in Russian).
- Rakishev B.R. Models of rock collapse on benches with various technologies of blasting operations. Journal of Mining Institute. 2007. Vol. 171, p. 39-44 (in Russian).
- Rozhdestvenskii V.N. Investigation of methods for controlling the collapse width during rock blasting at pits: Avtoref. dis. … kand. tekhn. nauk. Ekaterinburg: Institut gornogo dela Uralskogo otdeleniya Rossiiskoi akademii nauk, 1997, p. 27 (in Russian).
- Brent G.F., Noy M.J. Throw blasting analysis. Proceedings Eighth International Symposium on Rock Fragmentation by Blasting, 7-11 May, 2006, Santiago, Chile, p. 717-722.
- Fitzgerald M., York S., Cooke D., Thornton D. Blast Monitoring and Blast Translation – Case Study of a Grade Improvement Project at the Fimiston Pit, Kalgoorlie, Western Australia. Eighth International Mining Geology Conference, 22-24 August, 2011, Queenstown, New Zealand. Australasian Institute of Mining and Metallurgy, 2011, p. 285-297.
- Choudhary B.S. Firing patterns and its effect on muck pile shape parameters and fragmentation in quarry blasts. International Journal of Research in Engineering and Technology. 2013. Vol. 2. Iss. 9, p. 32-45.
- Esen S., Nagarajan M. Muck pile shaping for draglines and dozers at surface coalmines. 11th International symposium on rock fragmentation by blasting, 24-26 August, 2015, Sydney, Australia. Australasian Institute of Mining and Metallurgy, 2015, p. 1-8.
- Isheyskiy V., Marinin M., Dolzhikov V. Combination of fracturing areas after blasting column charges during destruction of rocks. International Journal of Engineering Research and Technology. 2019. Vol. 12. N 12. P. 2953-2956.
- Paul S., David C. Factors governing the muck pile characteristics. 43rd annual conference on explosives and blasting techniques, 29 January – 1 Febrary, 2017. Orlando, Florida, USA. URL (date of access 10.04.2020).
- Rai P., Yang H. Blast design for controlled augmentation of muck pile throw and drop. Tunnel and Underground Space. 2010. Vol. 20. Iss. 5, p. 360-368.
- Sastry V., Chander R. Fragmentation and throw due to blasting – Role of initiation systems. Proceedings 36th International conference on explosives and blasting, Los Angeles, USA, 2008, p. 371-376.