Simulation of the electric drive of the shearer to assess the energy efficiency indicators of the power supply system
- 1 — Senior lecturer T.F. Gorbachev Kuzbass State Technical University ▪ Orcid ▪ Elibrary ▪ Scopus ▪ ResearcherID
- 2 — Ph.D. Senior researcher T.F.Gorbachev Kuzbass State Technical University ▪ Orcid ▪ Elibrary
Abstract
This paper considers the problem of electric drive of shearers simulation to assess the indicators of power supply system (PSS) energy efficiency in the context of the introduction of modern devices for controlling the flow of electricity and power. The block diagram of the shearer electric drive simulation model is presented. To take into account fluctuations in the level of consumption of active and reactive power, a model of the executive body of the shearer was used in the work, including a model of the moment of resistance on the auger when cutting. As a result, in the MATLAB Simulink environment, a simulation model of the electric drive of the UKD300 shearer was developed, suitable for assessing the energy efficiency of the electrical complex of mining areas and the feasibility of using modern devices for controlling the flow of electricity and power. As a result of the simulation, it was found that a significant irregularity in the graph of reactive power consumption, caused by repeated short-term operation, makes the use of capacitor units ineffective to compensate for reactive power.
Introduction. Despite the global trend of abandoning hydrocarbon fuels in favor of more environmentally friendly fuel and energy resources, the demand for coal and the development of the coal industry are likely to persist in the coming decades. Thus, the forecast [10] predicts 17 % increase in coal demand under a favorable scenario by 2040 (compared to the level of 2018). The program for the development of the Russian coal industry for the period up to 2035 (hereinafter referred to as the Program) [6] assumes a change in demand for coal by 2035 from –1.16 % (conservative scenario) to +13.95 % (optimistic scenario).
The program [6] envisages increasing the competitiveness of Russian coal companies, including through the technological development of the coal industry: modernization and technical re-equipment; introduction by coal companies of highly efficient coal mining technologies; implementation of digital technologies in the processes of coal mining and processing with elements of the industrial strategy "Industry 4.0".
Professor Yu.A. Plakitkin (ERI RAS) notes [5], that by 2035 the coal production cost should be reduced to 68% compared to 2016. For this, it is necessary to reduce the specific consumption of electricity, which can reach 25 % of the coal production cost. For this purpose, FACTS devices can be used. Prospects for their implementation in PSS of mining enterprises, in particular, high-speed devices for reactive power compensation (RPC) and filtering of higher harmonics D-STATCOM, were considered in works [1, 11].
Due to the fact that FACTS devices have a high speed of response to assess the efficiency of their operation in a coal mine PSS, it is required to take into account the dynamics of mining equipment and the uneven nature of the electrical load. For this, it is necessary to develop a computer simulation model of the PSS of the excavation section of a coal mine and individual electrical consumers. In particular, simulation modeling of the electric drive of the shearer loader is of particular interest, the load graph of which is the most dynamic and has a significant impact on the choice of the location and configuration of FACTS devices, as well as traditional RPC devices.
Formulation of the problem. Simulation modeling of coal mines PSS was carried out earlier by a number of authors. The work [4] presents a simulation model of a coal mine cut-out area, performed in the MATLAB Simulink environment. In this model, the load of mining machines is represented by the Three-Phase Series RLC Load block, which is designed to simulate a static load and does not allow taking into account the dynamic nature of the load of mining electrical equipment. The work [4] shows a simulation model of a multi-motor electric drive system of a mining shearer, also performed in the MATLAB Simulink environment. The electric motors in the model are represented by Asynchronous Machine blocks from the Sim Power Systems library, which allows you to simulate dynamic modes of operation. However, the torque of resistance of the electric drive is set using the Step block, which allows you to simulate a jump-like transition between two torque values. In other words, the moment of resistance of the executive body of the harvester in the steady-state operating mode is assumed to be unchanged, which does not allow to fully assess the nature and dynamics of the power consumption of the harvester. In this regard, these models cannot be used to assess the efficiency of PSS in the context of the introduction of FACTS devices.
The issues of computer modeling of the shearers operating modes were considered in the following works:
• in [13, 14, 16, 19] the modeling of the mechanical part of the shearer and the process of coal destruction is considered; however, these works do not pay attention to the electric part of the electric drive;
• in [12, 17, 18,] the modeling of the electric drive of the shearer is considered, the main attention is paid to the control systems of the electric drive. Reactive power consumption by shearers is not considered in these works.
It should be noted that the literature contains detailed models of the electric drive of mining machines, taking into account dynamic processes, for example [7, 9], but these models are considered in isolation from the PSS and the rest of the mechanized complex of the mining area.
In this article, a simulation model of the most common type of shearers with an unregulated asynchronous electric cutting drive and a frequency-controlled feed drive is considered.
Methodology. The load of the electric drive of the shearer cutting device depends on the extraction of coal (destruction, removal from the cutting zone, conveyor load) and is determined by the mining and geological conditions of the seam being developed and the technological parameters of the shearer's executive body. The uneven arrangement of the augers causes periodic fluctuations in the moment of resistance on the auger, and the random nature of the change in the resistance of the destroyed coal mass – random fluctuations in the moment of resistance [7].
The moment of resistance of the shearer feed electric drive is determined by external forces acting on the shearer: the gravity of the shearer, the force of resistance to the supply of the shearer from the coal mass, the friction force of the supporting mechanisms against the attachments of the conveyor [12]. The force of resistance to the shearer feed has a sharply variable character, since it is determined by the sum of forces on the augers of the executive body of the shearer, therefore, the nature of the electrical consumption of the feed drive is also uneven.
The model of the electric drive of the shearer must include a mechanical part, in which, taking into account mining and geological conditions and random factors, the moment of resistance of the electric motors is formed. The block diagram of the simulation model of the shearer is shown in Fig.1.
Block "Executive body" is designed to simulate the moment of resistance of the shearer auger. Different approaches can be taken to execute this block. In [12] the moment of resistance on the executive body is modeled by the joint operation of two mathematical models – on the auger during cutting and during transportation and loading of coal. These mathematical models take into account the technical parameters of the cutter-loader executive body and describe its operation in detail; however, they are quite laborious for implementation. A simpler, but less accurate version is used in [12] – the executive body is presented as a transfer function that takes into account the average cutting resistance of coal. But this model does not allow to take into account the fluctuations in the moment of resistance due to the uneven distribution of the cutters over the surface of the auger.
For a more complete account of the electric load nature of the shearer in the present work in the "Executive body" block, the component of the resistance moment of the shearer auger during cutting is calculated, as well as the resistance force to the feed of the shearer from the coal mass according to the method [9]:
where Yff – feed force of the i-th cutter; np– number of simultaneously work cutters; D – auger diameter; ZEB(φaug) – function of the cutting element force from the the auger rotation angle.
The "Transmission" block is represented by a two-mass model described by a system of equations [8]:
where J1 – electric motor rotor moment of inertia; J2 – reduced moments of inertia of the transmission and the executive body; Mm – motor torque; φ1, φ2, φ'1, φ'2, φ''1, φ''2 – relative angular displacements of the electric motor and the executive body shafts and their first and second time derivatives, respectively; c – reduced coefficient of stiffness of transmission sections; b – reduced coefficient of inelastic resistance of transmission sections
The "Shearer" block models the moment of resistance for the electric drive of the shearer feed based on the equation [9]:
where rst – drive star radius of the feed subsystem mover; ms – shearer mass; Vfeed – feedrate; g – acceleration of gravity on planet Earth;
In this work, a simulation of a UKD 300 shearer is carried out. The electric cutting drive includes two AMs of 180 kW each with the following parameters: active resistances and inductance of the stator and rotor windings Rs = 0,164 Ohm, Rr = 0,252 Ohm, Ls = 1,821 mH, Lr = 1,821 mH, inductance of the magnetizing branch Lm = 93,832 mH, number of pole pairs p = 2, moment of inertia J = 4,33 kg ∙ m2. The supply electric drive includes two 30 kW AMs with parameters: active resistances and inductance of the stator and rotor windings Rs = 0,789 Ohm, Rr = 1,486 Ohm, Ls = 11,902 mH, Lr = 11,902 mH, inductance of the magnetizing branch Lm = 538,651 mH, number of pole pairs p = 3, moment of inertia J = 1,12 kg ∙ m2.
Figure 2 shows a simulation model of a shearer, made in MATLAB Simulink, corresponding to the block diagram in Figure 1.
Block 1 – coal mine PSS, represented by an equivalent resistance and an EMF source of 1140 V. Equivalent resistance corresponds to a short-circuit current of 3.54 kA at the shearer connection point.
Block 2 – frequency converter with a DC link and an autonomous voltage inverter. The capacity of the DC link is selected according to the data of [15].
Block 3 – simulates the moment of resistance for electric motors of the feed drive according to equation (2).
Blocks 4, 6 – asynchronous motors for cutting and feed drives modeled using the Asynchronous Machine block from the Sim Power Systems MATLAB Simulink library.
Block 5 – model of the cutting drive transmission, built on the basis of the system of equations (1).
Block 7 – is made in the form of a program code (MATLAB function) that provides the formation of the moment of resistance of the shearer executive body MEB и силы сопротивления подаче комбайна со стороны угольного массива Yff.
Discussion. Shearers operate in intermittent mode. The duration of inclusion on average ranges from 39.5 to 43.3 %. The average number of shearer starts per hour is 80 [8]. Simulation of the shearer operation in intermittent mode with duty cycle (DC) = 66.67 % (tc = 60 s, tp = 40 s) has been performed. The simulation results are shown in Fig.3-5.
Figure 3 shows a graph of the change in the moment of resistance of the shearer-loader executive body over time, reduced to the rotor of the electric motor. Periodic fluctuations of the moment are associated with uneven distribution of cutters, non-periodic random fluctuations are determined by the value of the coal resistance to cutting, which is set by a random number generator according to the normal distribution law.
Figure 4 shows the graph of the consumption of active and reactive power by the electric drive of cutting and supply of the shearer during one working cycle of intermittent cycle (IC). Basically, the power consumption of the shearer is determined by the operation of the cutting electric drive. During one IC with a duration of 60 s, the simulated shearer consumes (2827.9 + j1914,1) VA ∙ h of electricity, at that, the period of starting the electric drive of the cutting machine accounts for about 7.9 % of the consumption of active and 27.3 % of reactive energy, which indicates a significant increase in the consumption of reactive power by the electric drive during start-up, which follows from Fig.4. Starting processes make the load graph uneven, the consumption of reactive power at its peak is 1432.1 kVAr, and on average over the IC is 172.27 kVAr (standard deviation σ = 200.59 kVAr). For active power, similar values are 565.14 kW at the peak and 254.51 kW (standard deviation σ = 46.6 kW). Thus, the power consumption graph of the reactive power of the shearer cutting electric drive is significantly more uneven than the active power. After the end of the starting processes in the steady-state operating mode of the electric drive, the fluctuations in the consumption of active and reactive power are less significant, the standard deviation is 4.9 kVAr and 46.6 kW, respectively, and the average cosφ = 0.88.
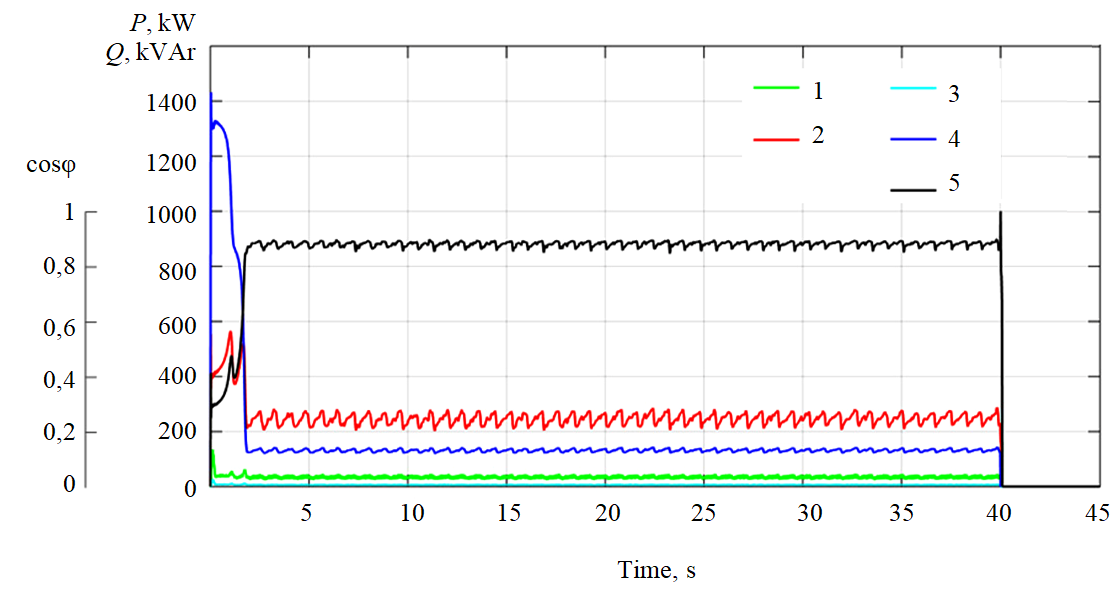
Based on the simulation results (Fig.4), the shearer requires the introduction of reactive power compensation devices for a short time within approximately 1.85 s after energizing the electric drive (during start-up). Due to the fact that the shearer operates in intermittent mode with frequent starts, it is required from the compensating device to increase the generation of reactive power for a short time every minute. Static capacitor banks are not able to cope with this task due to insufficient speed, therefore, the use of high-speed devices for reactive power compensation based on FACTS technologies is required.
Figure 5 shows the waveforms of the instantaneous values of the current of the electric drive of supply and cutting.
Due to the fact that the feed drive has frequency control, the current consumed by it is essentially non-sinusoidal (THD > 100 %). Due to the fact that the power of the feed drive is several times less than that of the cutting drive, the non-sinusoidality of the total current of the shearer is insignificant (THD = 10 %). Insignificant distortions of the sinusoidality of the current curve of the cutting drive are associated with the appearance of higher voltage harmonics caused by the non-sinusoidality of the current curve of the feed drive. When using frequency control to drive cutting, the total current of the shearer may have significant harmonic distortions, which can make the filtering of higher harmonics in the coal mine PSS relevant. Usually, fast-acting RPCs based on FACTS technology shearer the functions of both a compensating device and an active filter of higher harmonics.
Conclusion. The growth in the power-to-weight ratio of mining equipment creates new challenges in the development of measures to increase the energy efficiency of coal mining, requiring the creation of simulation computer models of the coal mine PSS.
As the results of modeling the electric drive of the shearer have shown, a significant uneven consumption of reactive power by the electric drive of the shearer is caused by intermittent operation with frequent starts. It was determined that the reactive power compensation device requires high-speed operation, since the main peak of reactive power consumption by the electric drive of the shearer lasts about 1.85 s, which necessitates consideration of reactive power compensation of FACTS devices.
The development of technology for intelligent control of electricity and power flows, in particular FACTS devices, can contribute to a significant increase in the energy efficiency of PSS in coal mines by means of high-speed compensation of reactive power, voltage stabilization and filtering of higher harmonic components. The developed simulation model is suitable for assessing the energy efficiency indicators of the electrical and technical complex of the coal mine excavation and the efficiency of using modern devices for controlling the flows of electricity and power.