Повышение эффективности технологической подготовки производства комплектующих для изготовления оборудования минерально-сырьевого комплекса
- 1 — канд. техн. наук старший преподаватель Санкт-Петербургский политехнический университет Петра Великого ▪ Orcid
- 2 — канд. техн. наук директор Высшей школы машиностроения Санкт-Петербургский политехнический университет Петра Великого ▪ Orcid
- 3 — ассистент Санкт-Петербургский политехнический университет Петра Великого ▪ Orcid ▪ Elibrary
- 4 — ассистент Санкт-Петербургский политехнический университет Петра Великого ▪ Orcid
Аннотация
Увеличение объемов выпуска комплектующих для производства оборудования, предназначенного для добычи нефти и газа, является ключевым фактором для анализа существующих технологических процессов и поиска новых технологических решений для повышения эффективности производственного процесса и качества комплектующих. В статье представлена имитационная модель, предназначенная для определения рациональных технологических параметров обработки для производства детали «Корпус центратора». Основой оптимизации рабочего цикла поточной линии является синхронизация, основанная на принципе пропорциональности, которая предполагает уравнивание продолжительности всех технологических операций с ритмом поточной линии. Синхронизация технологических операций на поточной линии производится за счет выбора рациональных параметров резания для каждого технологического перехода (скорости резания, подачи, количества рабочих переходов). Деталь «Корпус центратора» изготавливается из титанового сплава ВТ16, обладающего высокой прочностью, коррозийной стойкостью и пластичностью. Для рассматриваемой детали были определены допустимые значения параметров резания на основе расчета суммарной погрешности обработки, а также периодичность замены изношенного режущего инструмента. Описанная в статье имитационная модель позволила повысить эффективность производственного процесса за счет синхронизации технологических операций и поиска рациональных технологических параметров, а также повысить качество изготовления детали «Корпус центратора» за счет анализа погрешности обработки при различных параметрах технологического процесса.
Введение
В современных экономических условиях минерально-сырьевой комплекс является одним из факторов устойчивого развития страны. В России проблемы нефтегазодобычи имеют исключительно важное значение, поскольку отрасль в значительной мере наполняет государственный бюджет и создает большое количество рабочих мест [6, 9-11].
В настоящее время основными энергоносителями являются нефть и газ, продукты переработки которых применяются практически во всех отраслях промышленности. Энергетика является фундаментом экономики России и основным драйвером ее развития, в связи с чем вопросы обеспечения всеобщего доступа к дешевым, надежным, безопасным и экологически чистым источникам энергии являются приоритетными в контексте глобального устойчивого развития [1, 14, 15].
В условиях введения санкций и запрета импорта нефтегазового оборудования остро встает вопрос реализации программы импортозамещения. Многие нефтегазовые компании стремятся вступить в гонку цифровой трансформации, когда цифровые технологии используются для создания новых или преобразования традиционных процессов [16, 27, 35].
Потенциал добычи нефти и газа из плотных пород быстро увеличился за последние два десятилетия. Были усовершенствованы технологии бурения и интенсификации притока, вследствие чего расширились возможности добычи нефти и газа из непроницаемых пород посредством точного направленного бурения, массивного многоступенчатого гидроразрыва пласта и микросейсмического мониторинга [20, 34].
Для предприятий, занимающихся производством оборудования для нефтегазовой отрасли, увеличение объемов выпуска комплектующих неизбежно приводит к необходимости пересмотра существующих технологических процессов с целью их оптимизации для повышения эффективности производственного процесса и поддержания своей конкурентоспособности на рынке нефтегазового оборудования в условиях повышенного спроса.
Рост глобального потребления энергии, растущий спрос на ископаемое топливо и повышение конкуренции приводит к необходимости внедрения передовых технологий в производственный процесс [17, 18, 29]. В этих условиях повышение эффективности производственных процессов напрямую зависит от качества технологической подготовки производства, одной из основных задач которой является определение рациональных параметров технологического процесса.
Наиболее эффективным методом повышения качества технологической подготовки производства является метод имитационного моделирования [8, 13]. Управление технологическими процессами на основе имитационного моделирования в машиностроении входит в число наиболее перспективных направлений его развития [3, 26].
Постановка проблемы
Одной из актуальных проблем при добычи нефти и газа является спуск обсадных колонн в скважины, качество которого зависит от подготовленности ствола и интенсивности изменения зенитного угла, наличия комплекса технических средств для обеспечения качественного спуска, а также цементирования обсадной колонны, которое осуществляется с помощью центратора [7].
В настоящее время наиболее широкое распространение получили жесткие центраторы из-за возможности их использования в скважинах с наклонными и горизонтальными участками [5].
В связи с увеличением объема выпуска данного типа изделий необходима разработка имитационной модели, позволяющей на этапе технологической подготовки производства определять рациональные параметры технологического процесса, которые сокращают трудоемкость изготовления изделия и повышают его качество.
В условиях увеличения производственной программы для изготовления детали «Корпуса центратора» представляется рациональным применение поточной линии, к преимуществам которой относятся:
- повышение производительности труда за счет высокого уровня автоматизации, применения специализированных средств технологического оснащения и постоянства транспортных потоков;
- сокращение длительности производственного цикла за счет высокой специализации рабочих мест и постоянного ритма их работы;
- уменьшение заделов незавершенного производства за счет значительного сокращения длительности производственного цикла;
- повышение качества выпускаемой продукции за счет детальной проработки технологического процесса, стандартизации и контроля за качеством выпускаемой продукции;
- снижение себестоимости выпускаемой продукции за счет внедрения комплексных решений по оптимизации производственного процесса.
Одной из основных задач при проектировании поточной линии является сокращение времени перерывов на рабочих местах путем синхронизации технологических операций. Методом синхронизации технологических операций является выбор оптимального сочетания рабочих ходов (схем обработки) и параметров резания на основе предварительного анализа точности и производительности обработки [12, 19].
В настоящее время проблема оптимизации работы поточных линий является актуальной задачей в рамках технологической подготовки производства [22, 28]. В научной литературе представлено большое количество имитационных моделей, направленных на поиск оптимальных параметров поточной линии, таких как длительность производственного цикла, параметры резания, величина межоперационных перерывов и т.д. [21, 23, 31].
Широко освещены вопросы имитационного моделирования и поиска оптимальных параметров поточных линий сборки [25, 33, 36, 37]. Ряд имитационных моделей, представленных в научной литературе [24, 30, 32], базируются на логистических принципах при моделировании производственного процесса.
Задачей исследования является разработка имитационной модели для поточной линии по изготовлению корпуса центратора, которая позволяет синхронизировать работу отдельных ее элементов за счет определения рациональных параметров резания на основе расчета и анализа суммарной погрешности обработки.
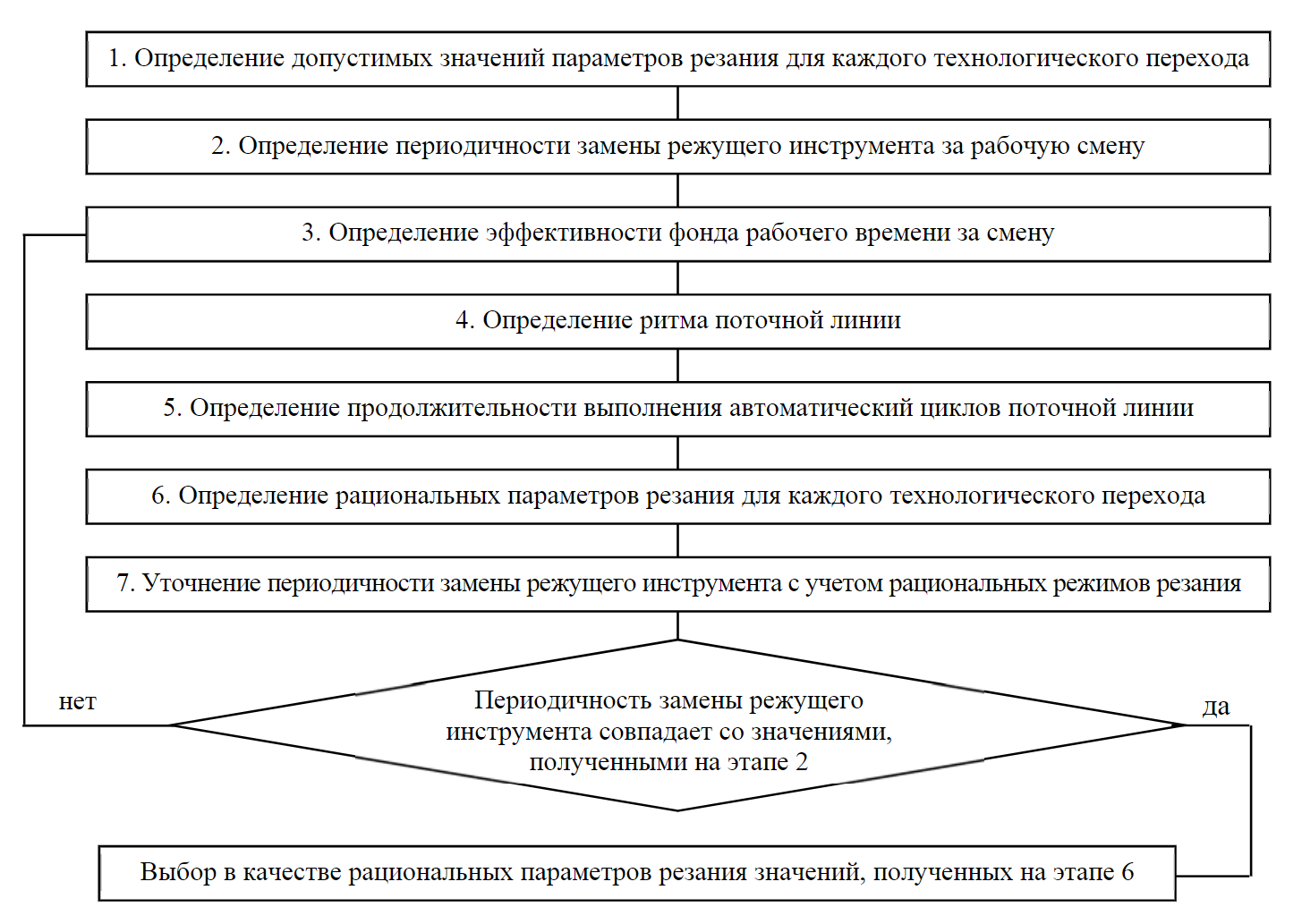
Рис.1. Схема имитационной модели
Описание имитационной модели
Корпус центратора изготавливается из титанового сплава ВТ16. Обработка деталей из титановых сплавов отличается высокой трудоемкостью, поэтому точность их изготовления во многом зависит от выбора оптимальных технологических параметров [2].
Разработанная имитационная модель позволяет синхронизировать работу отдельных элементов поточной линии за счет согласования длительности межоперационных перерывов. Схема имитационной модели состоит из следующих этапов (рис.1):
-
Определение допустимых значений параметров резания (скорости, глубины резания, подачи) для каждого технологического перехода производится на основе расчета суммарной погрешности обработки, которая не должна превышать величины поля допуска на размер
. В случае обработки в структуре одного инструментального перехода нескольких поверхностей с разными полями допусков определение допустимых параметров резания производится на основе расчета суммарной погрешности обработки для размера, величина поля допуска которого имеет минимальное значение.Расчет суммарной погрешности обработки производится на основе следующих составляющих: погрешности позиционирования станка, величины износа режущего инструмента, тепловых деформаций режущего инструмента и детали, упругих деформаций технологической системы, случайных составляющих погрешности обработки. Для титановых сплавов суммарная погрешность обработки определяется по формуле [4]:
где Δ(i) – суммарная погрешность позиционирования, мкм; u(i,τ) – износ режущего инструмента, мкм; ξр(i,τ,u,t) – тепловые деформации режущего инструмента, мкм; ξД(ξР) – тепловые деформации детали, мкм; Δy(t,u) – упругие деформации технологической системы, мкм; ηi – случайные составляющие погрешности обработки, мкм.
Расчет отдельных составляющих суммарной погрешности обработки производится по следующим формулам [7]:
где i – номер детали в партии; τ – время обработки i-й детали; τ – глубина резания; τохл – время охлаждения режущего инструмента перед обработкой i-й детали; K1, ..., K2 – коэффициенты, зависящие от параметров обработки (материалов детали и режущей части инструмента, характеристики технологического оборудования и т.д.).
Выходными данными первого этапа моделирования являются допустимые значения для каждого параметра резания:
, , , где , – минимальное и максимальное допустимые значения скорости резания; , – минимальное и максимальное допустимые значения подачи; , – минимальное и максимальное допустимые значения глубины резания. -
Периодичность замены режущего инструмента за рабочую сменуопределяется исходя из периода стойкости режущего инструмента, который зависит от режимов резания. Задачей данного этапа моделирования является предварительная оценка периодичности замены каждого типа режущего инструмента, применяемого в рабочем цикле поточной линии.
Для оценки периода стойкости используются средние значения параметров резания из допустимых интервалов
где
– среднее значение скорости резания, – подачи, – глубины резания из допустимого интервала; – период стойкости режущего инструмента при средних допустимых значениях параметров резания.Периодичность замены изношенного режущего инструмента определяется по формуле:
где Tр.ри – время работы режущего инструмента за смену, мин; tдет – время работы режущего инструмента для обработки одной детали при средних допустимых режимах резания, мин; Nсм – количество обрабатываемых деталей в смену, шт.
-
Эффективный фонд рабочего времени за смену для поточной линии может быть определен по формуле:
где Дсм – продолжительность рабочей смены, час;
– количество единиц режущего инструмента, которое необходимо заменить за смену, шт.; При – периодичность замены i-го режущего инструмента; m – количество типов режущего инструмента, необходимого для обработки детали; Тз.ри – время, необходимое для замены одной единицы режущего инструмента, мин. -
Определение ритма поточной линии производится на основе эффективного фонда рабочего времени за смену и заданного объема выпуска деталей в смену
-
Определение продолжительности выполнения автоматических циклов поточной линии. Цикл поточной линии может быть представлен в виде сочетания двух типов действий: вспомогательных переходов и рабочих циклов. В качестве рабочих циклов рассматриваются автоматические циклы обработки деталей на станке. К вспомогательным действиям можно отнести доставку заготовок от накопителя к станкам и обратно, перемещение заготовок между станками, автоматический контроль, установку и снятие заготовки, переустановку заготовки в процессе выполнения технологической операции и т.д.
Длительность рабочего цикла поточной линии равна ритму выпуска и может быть описана следующей формулой:
где ACi – длительность i-го автоматического цикла поточной линии; (Tвп)j – длительность j-го вспомогательного перехода поточной линии; i – количество автоматических циклов; j – количество вспомогательных переходов в рабочем цикле поточной линии.
Длительность каждого вспомогательного перехода является постоянной величиной и определяется техническими параметрами отдельных элементов поточной линии, общая продолжительность автоматических циклов определяется по формуле:
-
Определение рациональных параметров резания для каждого технологического перехода. Согласно принципу пропорциональности продолжительность автоматических циклов должна быть равномерной, это способствует уменьшению простоев отдельных элементов поточной линии. Выбор рациональных параметров резания из допустимых интервалов производится на основе условия
, где Pпл – общая величина простоев на поточной линии; Pi – величина простоя элементами поточной линии.Величина простоя между отдельными элементами поточной линии определяется по формуле:
где Rn-1 – продолжительность рабочего цикла (n – 1)-го элемента поточной линии, с; Rn – продолжительность рабочего цикла n-го элемента поточной линии; – время транспортировки заготовки между (n – 1)-м и n-м элементами поточной линии, с.
Рабочий цикл n-го станка включает в себя автоматический цикл станка (цикл обработки заготовки) Rn и вспомогательное время (Tвп)n:
где ACn – время автоматического цикла на n-м станке; Tуст.заг – время необходимое на установку заготовки в станок; Tсн.заг – время, необходимое на снятие заготовки со станка; Tдоп – время, необходимое для выполнения дополнительных вспомогательных переходов, предусмотренных рабочим циклом поточной линии.
Время автоматического цикла станка зависит от количества технологических переходов, выбранной стратегии обработки и параметров резания,
где Tсм.ри – время смены режущего инструмента, с; b – количество инструментальных переходов в структуре технологической операции; Tрп – время на выполнения рабочих переходов, входящих в структуру технологического перехода, с; Tвп – время выполнения вспомогательных переходов, предусмотренных в структуре технологического перехода, с; m – количество инструментальных переходов;
– дополнительное время, необходимое для реализации процесса обработки, с.Расчет рациональных параметров резания будет производится на основе решения системы уравнений и неравенств:
-
Уточнение периодичности замены изношенного режущего инструмента производится с учетом рациональных режимов резания, принятых по результатам имитационного моделирования, проведенного на этапе 6. Для каждого типа режущего инструмента на основе принятых значений режимов резания уточняется период их стойкости и рассчитывается периодичность замены. Далее определяется общее количество единиц режущего инструмента, которое необходимо заменить за смену с учетом принятых значений параметров резания (рациональных значений):
где
– периодичность замены i-го режущего инструмента с учетом принятых режимов резания, мин.На данном этапе рассматриваются два случая. Если k' = k, то в качестве рациональных параметров резания принимаются значения, полученные на этапе 6: Vрац=Vрасч; sрац=sрасч; tрац=tрасч. Если же k' < k или k' > k, то происходит возврат к этапу 3, и с учетом значения параметра k' производятся повторные моделирование работы поточной линии и расчет параметров Vрац, sрац, tрац.
Определение рациональных параметров резания для корпуса центратора
Описанная имитационная модель была применена на этапе технологической подготовки производства при проектировании поточной линии для изготовления корпуса центратора (рис.2).
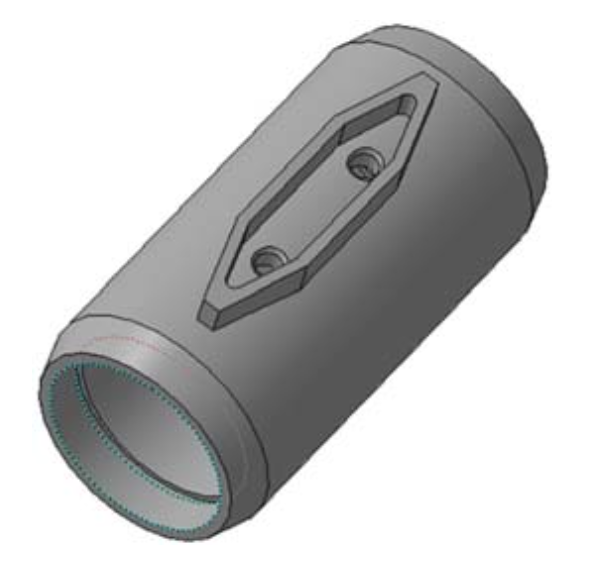
Рис.2. Корпус центратора
Разработанный технологический процесс для детали центратора содержит две механические операции, выполняемые на станках с ЧПУ.
Для реализации разработанного технологического процесса была выбрана производственная линия, состоящая из двух обрабатывающих центров, накопителя для заготовок и готовой продукции, а также системы автоматизации, которая предназначена для транспортировки заготовок между станками и накопителем.
На первом этапе моделирования были рассчитаны допустимые интервалы параметров резания. Для обработки детали корпуса центратора был использован режущий инструмент фирмы Sandvik Coromant. На основе расчета суммарной погрешности обработки были определены допустимые значения для скорости резания и подачи. Глубина резания для каждого технологического перехода была определена на этапе проектирования технологических операций, поэтому при расчете суммарной погрешности обработки данный параметр рассматривался в качестве постоянной величины . Для скорости резания и подачи были получены следующие допустимые значения параметров резания: наружное предварительное точение: V ∈ [50;69,2] м/мин, s ∈ [0,1;0,27] мм/об; внутреннее предварительное точение: V ∈ [50;68,2] м/мин, s ∈ [0,1;0,26] мм/об; внутреннее предварительное точение: V ∈ [50;78,9], s ∈ [0,08;0,29] мм/об; сверление: V ∈ [32;45,2] м/мин, s ∈ [0,112;0,158] мм/об; фрезерование: V ∈ [45;52,9] м/мин, s ∈ [115;136,4] мм/об.
На втором этапе для каждого типа режущего инструмента была определена периодичность его замены с учетом периода стойкости. Величина периода стойкости была вычислена исходя из средних значений параметров резания, принадлежащих допустимому интервалу. В зависимости от метода обработки были получены следующие значения периодичности замены изношенного режущего инструмента в течение смены: черновое наружное точение – 4, черновое растачивание – 3, чистовое растачивание – 2, сверление – 2, фрезерование – 2. Время, необходимое для замены одной единицы изношенного режущего инструмента, составило 2 мин (120 с).
На этапе имитационного моделирования была рассчитана величина эффективного фонда рабочего времени для рабочей смены. С учетом периодичности замены изношенного режущего инструмента и принятого времени переналадки эффективный фонд рабочего времени за смену Фсм будет равен 454 мин.
Определение ритма поточной линии производилось с учетом размера эффективного фонда рабочего времени и объема выпуска деталей за смену. Согласно производственному плану количество изготавливаемых деталей за восьмичасовую смену составляет 75 шт. Таким образом, ритм поточной линии rпл будет равен 6,05 мин (363,2 с).
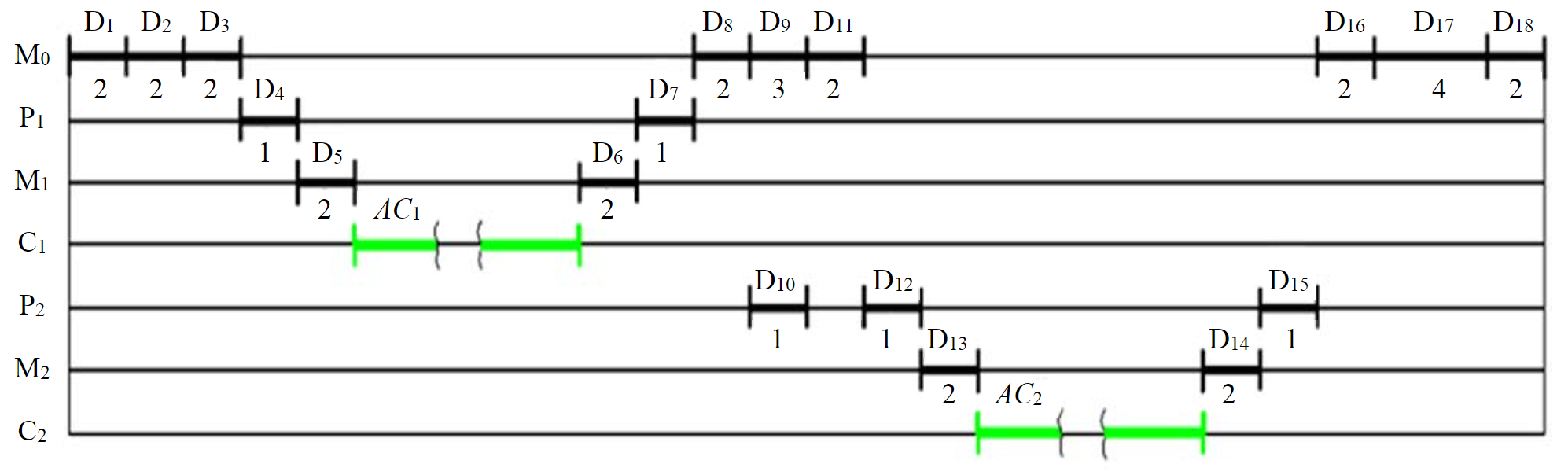
Рис.3. Циклограмма рабочего цикла поточной линии М0 – манипулятор, осуществляющий перемещение заготовок между накопителем и станками; С1 – станок 1; Р1 – паллета, с помощью которой производится перемещение заготовок от манипулятора М0 в рабочую зону станка С1; М1 – манипулятор, осуществляющий установку и снятие заготовок в рабочей зоне станка С1; С2 – станок 2; Р2 – паллета, с помощью которой производится перемещение заготовок от манипулятора М0 в рабочую зону станка С2; М2 – манипулятор, осуществляющий установку и снятие заготовок в рабочей зоне станка С2; З0 – заготовка, которая не проходила механической обработки; З1 – заготовка после первой технологической операции на станке С1; З2 – заготовка после второй технологической операции на станке С2; D1 – взятие заготовки З0 с накопителя; D2 – перемещение манипулятора М0 от накопителя к станку С1; D3 – установка заготовки З0 на паллету Р1; D4 – перемещение паллеты P1 от манипулятора М0 к станку С1; D5 – установка заготовки З0 на станок С1; D6 – снятие заготовки З1 со станка С1 и установка ее на паллету Р1; D7 – перемещение паллеты Р1 от станка С1 к манипулятору М0; D8 – взятие заготовки З1 манипулятором М0; D9 – перемещение манипулятора М0 от станка С1 к станку С2; D10 – перемещение паллеты Р2 от станка С2 к манипулятору М0; D11 – установка заготовки З1 на паллету Р2; D12 – перемещение паллеты Р2 от манипулятора М0 к станку С2; D13 – установка заготовки З1 на станок С2; D14 – снятие заготовки З2 со станка С2; D15 – перемещение паллеты Р2 от станка С2 к манипулятору М0; D16 – взятие заготовки З2 с паллеты Р2; D17 – перемещение манипулятора М0 от станка С2 к накопителю; D18 – установка заготовки З2 в накопитель; AC1 – автоматический цикл на первом станке; AC2 – автоматический цикл на втором станке
Согласно циклограмме (рис.3), величина вспомогательного времени рабочего цикла поточной линии составит
Автоматический цикл 1 (AC1) имеет следующие параметры: количество инструментальных переходов b = 4; дополнительное время, необходимое для реализации маршрута обработки,
Автоматический цикл 2 (AC2) имеет следующие параметры: количество инструментальных переходов b = 5; дополнительное время, необходимое для реализации маршрута обработки,
Для обоих автоматических циклов время на смену режущего инструмента составляет 2 с. Таким образом, уравнения для описания длительности автоматических циклов будут иметь следующий вид:
где V1,...,V9 – скорости резания для инструментальных переходов 1, …, 9; s1,...,s9 – подачи для инструментальных переходов 1, …, 9.
Продолжительность рабочего цикла на первом станке при (Tвп)1=14 с можно описать следующим уравнением:
Продолжительность рабочего цикла на втором станке при (Tвп)2 = 10 с можно описать следующим уравнением:
Время транспортировки заготовки между станками Tтр = 3 с.
Согласно формуле (14), величина простоев для рассматриваемой поточной линии определяется по формуле:
Для эффективной работы поточной линии необходимо, чтобы величина простоев была минимальной
Определение рациональных параметров резания для рассматриваемой поточной линии будет производиться на основе следующей системы уравнений и неравенств:
В результате моделирования работы поточной линии на основе описанной системы уравнений были получены значения параметров резания, которые могут быть приняты в качестве рациональных.
Для первого автоматического цикла были получены следующие значения четырех технологических переходов: V1 = 58,2, s1 = 0,19; V2 = 61,4, s2 = 0,21; V3 = 37,4, s3 = 0,64; V4 = 52,9 м/мин, s4 = 0,213 мм/об.
Для второго автоматического цикла были получены следующие значения пяти технологических переходов: V5 = 61,9, s5 = 0,18; V6 = 47,3, s6 = 123,4; V7 = 49,4, s7 = 125,3; V8 = 37,1, s8 = 0,142; V9 = 48,1 м/мин, s9 = 1 мм/об.
По результатам расчетов периодичность замены инструмента на основе полученных значений параметров резания осталась баз изменения (k = k'), вследствие чего представленные значения можно принять в качестве рациональных параметров резания для обработки корпуса центратора.
Заключение
Применение разработанной имитационной модели на этапе технологической подготовки производства для изготовления корпуса центратора позволило повысить эффективность производственного процесса за счет сокращения длительности межоперационных перерывов, повысить качество выпускаемой продукции за счет расчета и анализа суммарной погрешности обработки, определить рациональные параметры резания.
Литература
- Барьеры реализации водородных инициатив в контексте устойчивого развития глобальной энергетики / В.С.Литвиненко, П.С.Цветков, М.В.Двойников, Г.В.Буслаев // Записки Горного института. 2020. Т. 244. С. 428-438. DOI: 10.31897/PMI.2020.4.5
- Максаров В.В. Технологическое обеспечение качества прецизионных поверхностей детали типа «тел вращения» из титановых сплавов / В.В.Максаров, Е.В.Кошелева, А.Ю.Важенин // Металлообработка. 2018. № 4 (106). С. 52-59.
- Максаров В.В. Технологическое обеспечение параметров точности и шероховатости станин на основе совершенствования торцевого фрезерования на станках с ЧПУ / В.В.Максаров, Р.Р.Рахманкулов // Вестник Рыбинской государственной авиационной технической академии им. П.А.Соловьева. 2017. № 1 (40). С. 268-276.
- Математическая модель погрешности при точении труднообрабатываемых сплавов / И.И.Козарь, Д.Ю.Колодяжный, М.М.Радкевич, Т.А.Цимко // Научно-технические ведомости Санкт-Петербургского государственного университета. 2014. № 2 (195). С. 194-201.
- Опорно-центрирующая оснастка обсадных колонн для крепления боковых стволов / Е.В.Кожевников, Н.И.Николаев, А.В.Розенцвет, А.А.Лырчиков // Вестник Пермского национального исследовательского политехнического университета. Геология. Нефтегазовое и горное дело. 2015. № 16. С. 54-60. DOI: 10.15593/2224-9923/2015.16.6
- Поддубный Ю.А. Методы увеличения нефтеотдачи в мире: сегодня и возможное завтра / Ю.А.Поддубный, А.Ю.Поддубный // Бурение и нефть. 2020. № 12. С. 43-49.
- Повышение качества крепления скважин / Л.Б.Хузина, Р.И.Фазлыева, А.Х.Габзалилова // Деловой журнал Neftegaz.ru. 2018. № 1(73). С. 88-91.
- Повышение эффективности технологической подготовки единичного и мелкосерийного производства на основе имитационного моделирования / С.А.Любомудров, И.Н.Хрусталева, А.А.Толстолеc, А.П.Маслаков // Записки Горного института. 2019. Т. 240. С. 669-677. DOI: 10.31897/PMI.2019.6.669
- Разманова С.В. Нефтесервисные компании в рамках цифровизации экономики: оценка перспектив инновационного развития / С.В.Разманова, О.В.Андрухова // Записки Горного и института. 2020. Т. 244. С. 482-492. DOI: 10.31897/PMI.2020.4.11
- Состояние и перспективы повышения нефтеотдачи пластов в России (часть 1) / А.А.Колеватов, С.В.Афанасьев, С.Т.Закенов и др. // Бурение и нефть. 2020. № 12. С. 3-19.
- Состояние и перспективы повышения нефтеотдачи пластов в России (часть 2) / И.В.Шарф, И.В.Афанаскин, С.Г.Вольпин и др. // Бурение и нефть. 2021. № 1. С. 3-22.
- Технологические особенности магнитно-абразивной обработки в условиях цифровых технологий / В.В.Максаров, А.И.Кексин, И.А.Филипенко, И.А.Бригаднов // Металлообработка. 2019. № 4(112). С. 3-10.
- Хрусталева И.Н. Имитационная модель технологической подготовки производства цеха механической обработки / И.Н.Хрусталева, С.А.Любомудров, П.И.Романов // Научно-технические ведомости СПбПУ. Естественные и инженерные науки. 2017. Т. 23. № 2. С. 215-222. DOI: 10.18721/JEST.230219
- Чернышева Е.А. Современные аспекты развития нефтепереработки в России // Бурение и нефть. 2015. № 5. С. 4-8.
- A state-of-the-art review of the application of nanotechnology in the oil and gas industry with a focus on drilling engineering / J.A.Ali, A.M.Kalhury, A.N.Sabir et al. // Journal of Petroleum Science and Engineering. 2020. Vol. 191. № 107118. DOI: 10.1016/j.petrol.2020.107118
- Abdulrahman I. Process intensification in the oil and gas industry: A technological framework / I.Abdulrahman, V.Máša, S.Y.Teng // Chemical Engineering and Processing – Process Intensification. 2021. Vol. 159. № 108208. DOI: 10.1016/j.cep.2020.108208
- Advanced nanomaterials in oil and gas industry: Design, application and challenges / M.Khalil, B.M.Jan, C.W.Tong, M.A.Berawi // Applied Energy. 2017. Vol. 191. P. 287-310. DOI: 10.1016/j.apenergy.2017.01.074
- Asl M.G..Dynamic asymmetric optimal portfolio allocation between energy stocks and energy commodities: Evidence from clean energy and oil and gas companies / M.G.Asl, G.Canarella, S.M.Miller // Resources Policy. 2021. Vol. 71. № 101982. DOI: 10.1016/j.resourpol.2020.101982
- Automating production engineering for custom and small-batch production on the basis of simulation modeling / I.N.Khrustaleva, S.A.Lyubomudrov, L.G.Chernykh et al. // International Conference on Innovations, Physical Studies and Digitalization in Mining Engineering (IPDME) 2020, 23-24 April, 2020, St. Petersburg, Russian Federation. Journal of Physics: Conference Series. 2021. Vol. 1753. № 012047. DOI: 10.1088/1742-6596/1753/1/012047
- Boak J. Shale Gas, Tight Oil, Shale Oil and Hydraulic Fracturing t / J.Boak, R.Kleinberg // Future Energy (Third Edition). Improved, Sustainable and Clean Options for our Plane. Elsevier, 2020. P. 67-95. DOI: 10.1016/B978-0-08-102886-5.00004-9
- Bulenkov Y. Structure of a products flow in multi-nomenclature rotary lines with regard to tool change times // IOP Conference Series: Materials Science and Engineering. 2018. Vol. 400. Iss. 2. № 022014. DOI: 10.1088/1757-899X/400/2/022014
- Ding S. Flow line machining of turbine blades. Proceedings / S.Ding, D.Yang, Z.Han // International Conference on Intelligent Mechatronics and Automation. 2004. P. 140-145. DOI: 10.1109/ICIMA.2004.1384177
- Gwiazda A. Modeling of a production system using the multi-agent approach / A.Gwiazda, A.Sękala, W.Banaś // ModTech International Conference – Modern Technologies in Industrial Engineering V, 14-17 June, 2017, Sibiu, Romania. IOP Conference Series: Materials Science and Engineering. 2017. Vol. 227. № 012052. DOI: 10.1088/1757-899X/227/1/012052
- Humbeck P. Future Scenarios of Value Creation in Mechanical Engineering – Derivation of Recommendations for Action / P.Humbeck, S.Mangold, T.Bauernhansl // 53rd CIRP Conference on Manufacturing Systems, 1-3 July, 2020, Chicago, USA. Procedia CIRP. 2020. Vol. 93. P. 844-849. DOI: 10.1016/j.procir.2020.03.093
- Ma K. Mechanical System Design and Simulation Research of a Demonstration Assembly Line / K.Ma, Y.Chen, Y.Sun // 2019 2nd International Conference on Mechanical Manufacturing and Industrial Engineering, 14-16 December, 2019, Beijing, China. IOP Conference Series: Materials Science and Engineering. 2020. Vol. 784. № 012026. DOI: 10.1088/1757-899X/784/1/012026
- Muthanna J. Simulation of Assembly Line Balancing in Automotive Component Manufacturing / J.Muthanna, N.M.Razali // 2nd International Manufacturing Engineering Conference and 3rd Asia-Pacific Conference on Manufacturing Systems (IMEC-APCOMS 2015), 12-14 November, 2015, Kuala Lumpur, Malaysia. IOP Conference Series: Materials Science and Engineering. 2016. Vol. 114. № 012049. DOI: 10.1088/1757-899X/114/1/012049
- Oil and Gas 4.0 era: A systematic review and outlook / H.Lu, L.Guo, M.Azimi, K.Huang // Computers in Industry. 2019. Vol. 111. P. 68-90. DOI: 10.1016/j.compind.2019.06.007
- Performance evaluation of the support bush manufacturing line by modeling and simulation / F.S.Blaga, I.Stănășel, A.Pop et al. // Annual Session of Scientific Papers. «IMT ORADEA 2019», 30-31 May, 2019, Oradea, Felix SPA, Romania. IOP Conference Series: Materials Science and Engineering. 2019. Vol. 568. № 012030. DOI: 10.1088/1757-899X/568/1/012030
- Progress and development directions of stimulation techniques for ultra-deep oil and gas reservoirs / Q.Lei, Y.Xu, Z.Yang et al. // Petroleum Exploration and Development. 2021. Vol. 48. Iss. 1. P. 221-231. DOI: 10.1016/S1876-3804(21)60018-6
- Pschybilla T. Evaluation of end-to-end process and information flow analyses through digital transformation in mechanical engineering / T.Pschybilla, A.Homann // 53rd CIRP Conference on Manufacturing Systems, 1-3 July, 2020, Chicago, USA. Procedia CIRP. 2020. Vol. 93. P. 298-303. DOI: 10.1016/j.procir.2020.04.070
- Research on Automatic Flow-shop Planning Problem Based on Data Driven Modelling Simulation and Optimization / Weikang Fang, Zailin Guan, Dan Luo et al. // International Conference on Intelligent Manufacturing and Intelligent Materials (2IM 2019), 9-11 May, 2019, Sanya, China. IOP Conference Series: Materials Science and Engineering. 2019. Vol. 565. № 012005. DOI: 10.1088/1757-899X/565/1/012005
- Research on Simulation Decision of Logistics in Flexible Factory / L.Wentao, R.Yan, Z.Jianfu, D.Linjiang // 3rd International Conference on Data Mining, Communications and Information Technology (DMCIT 2019), 24-26 May, 2019, Beijing, China. IOP Conference Series: Journal of Physics: Conference Series. 2019. Vol. 1284. № 012015. DOI: 10.1088/1742-6596/1284/1/012015
- Revina I.V. Simulation modeling of the assembly process / I.V.Revina, E.N.Trifonova // XIII International Scientific and Technical Conference «Applied Mechanics and Systems Dynamics», 5-7 November, 2019, Omsk, Russian Federation. Journal of Physics: Conference Series. 2020. Vol. 1441. № 012110. DOI: 10.1088/1742-6596/1441/1/012110
- Senderov S.M. Approaches to the identification of critical facilities and critical combinations of facilities in the gas industry in terms of its operability / S.M.Senderov, S.V.Vorobev // Reliability Engineering & System Safety. 2020. Vol. 203. № 107046. DOI: 10.1016/j.ress.2020.107046
- Smart reservoir management in the oil and gas industry / D.Castiñeira, H.Darabi, X.Zhai, W.Benhallam // Smart Manufacturing. Elsevier, 2020. P. 107-141. DOI: 10.1016/B978-0-12-820028-5.00004-7
- Yasir A.S.H.M. Assembly Line Efficiency Improvement by Using WITNESS Simulation Software / A.S.H.M.Yasir, N.M.Z.N.Mohamed // The 4th Asia Pacific Conference on Manufacturing Systems and the 3rd International Manufacturing Engineering Conference, 7-8 December, 2017, Yogyakarta, Indonesia. IOP Conference Series: Materials Science and Engineering. 2018. Vol. 319. № 012004. DOI: 10.1088/1757-899X/319/1/012004
- Yasir A.S.H.M. Development of framework for armoured vehicle assembly line efficiency improvement by using simulation analysis: Part 1 /A.S.H.M.Yasir, N.M.Z.N.Mohamed, A.Q.Basri // 1st International Postgraduate Conference on Mechanical Engineering (IPCME2018), 31 October, 2018, UMP Pekan, Pahang, Malaysia. IOP Conference Series: Materials Science and Engineering. 2019. Vol. 469. № 012090. DOI: 10.1088/1757-899X/469/1/012090