Impact of dry and wet magnetic separator process parameters on iron oxide removal from Egyptian feldspar ore
Abstract
The demand for feldspar as a raw material in the ceramic industry is continuously increasing. Feldspar is abundant in the Earth's crust and typically found alongside other silicate minerals, as well as titanium and iron oxides. This study aims to reduce the iron oxide content in feldspar ore from the Wadi Zirib region and achieve an optimal grade of feldspar concentrate for various industrial uses. The research involved dry and wet magnetic separation techniques followed by leaching with oxalic and citric acids to minimize iron impurities and enhance optical properties. The factors affecting the dry magnetic separation, for feldspar size of –250+45 µm, were optimized using the Box – Behnken factorial design and a non-magnetic concentrate with 0.29 % Fe2O3 and an 92.19 % feldspar yield was obtained. The wet magnetic separation for feldspar fines of size –45µm was optimized and a concentrate with 0.27 % Fe2O3 was achieved. The acid leaching was conducted on the non-magnetic feldspar concentrates using oxalic and citric acid. Oxalic acid was more successful in reducing iron oxide of dry (to 0.19 %) and wet (to 0.12 %) non-magnetic feldspar concentrates. The optical properties of the leached concentrates were improved compared to the original sample, as the whiteness improved up to 90 %.
Funding
The research was conducted with support of the Science, Technology and Innovation Funding Authority, Ministry of Higher Education and Scientific Research, Egypt, grant N 45915.
Introduction
Feldspar, a common rock-forming mineral, holds significant industrial importance due to its widespread use in ceramics, glass manufacturing, and other high-tech applications [1, 2]. The required specifications for feldspar: SiO2 <70 %, Al2O3 >17 %, Fe2O3 <0.1 %, and K2O and Na2O >5 % [3]. Common associated minerals in feldspar ore include clays, mica, rutile, and silicates [4-6]. Feldspar, an abundant mineral in Egypt, often contains iron oxide impurities that degrade its quality and limit its utility. The presence of iron oxide impurities within feldspar deposits poses a considerable challenge to its utilization, as these impurities can adversely affect product quality and processing efficiency.
Numerous studies including chemical, physical and physicochemical methods have been conducted globally to enhance feldspar products for their utilization in ceramic industries [1, 7, 8] . Desliming, magnetic separation and flotation separation is the most important beneficiation technique for upgrading feldspar [9-11] . Magnetic separation, as a prominent beneficiation technique, has garnered substantial interest for its potential to selectively remove iron oxides from feldspar ores [2, 12, 13].
Studies have demonstrated the efficiency of high-intensity magnetic separation (HIMS) for separating paramagnetic minerals such as rutile, ilmenite, wolframite, monazite, siderite, chromite, manganese, and hematite from their native ores. While wet high-intensity magnetic separation (WHIMS) appears to be a straightforward operation, its effectiveness is influenced by various parameters including magnetic field intensity, composition and form of the matrix, feed rate and the rotational speed of the separator.
S.Saisinchai et al. utilized WHIMS as an alternative to reverse flotation for the separation of magnetite and rutile, resulting in a feldspar product with the following composition: SiO2 68.29 %, Al2O3 18.69 %, Fe2O3 0.07 %, K2O 5.83 % and Na2O 6.33 %. This method enabled the effective and environmentally friendly separation of iron-bearing minerals on a commercial scale [14] .
Due to the low processing cost, acid leaching is a viable alternative for removing Fe from feldspar ores following magnetic separation. Organic acids containing –COOH groups, which are less corrosive than inorganic acids, can be used to dissolve iron impurities. These acids are biodegradable and achieve higher metal extraction efficiency at mildly acidic pH levels compared to other agents [15]. Consequently, feldspar is often leached using organic acids and biological methods, which serve as alternatives to mineral acids [16].
Y.Sánchez-Palencia et al. studied the bleaching of kaolin after magnetic separation and found that oxalic and citric acids were significantly more effective than other organic acids like acetic, lactic, and ascorbic acids [17].
Processing iron-containing raw materials, such as feldspar, poses significant challenges due to the fine dissemination and strong associations of iron oxides like hematite and magnetite within the ore. These impurities reduce feldspar quality, limiting its use in industries requiring high purity. Conventional methods are limited to achieve the required specifications, necessitating the integration of advanced physical and chemical separation processes. Environmental concerns highlight the need for sustainable, efficient beneficiation strategies.
This study aligns with current trends by focusing on optimizing separation processes, reducing energy consumption, and minimizing environmental impact to produce feldspar that meets industrial standards for ceramics and glass applications [18-22].
The present study examines the ability of removing iron-bearing contaminants from low-grade Egyptian feldspar ore using physical and chemical separation methods to produce a feldspar product meeting specifications suitable for various industrial applications. The feldspar sample will be ground using a ball mill to prepare a feed of –250+45 µm for dry high-intensity magnetic separation (Magna roll). A statistical experimental design methodology will be applied to optimize the separation of iron-bearing contaminants. The fines (–45 μm) will be separated using wet high-intensity magnetic separation (Box-mag rapid LHW). Additionally, a study on the acid leaching of the non-magnetic feldspar concentrates will be conducted to enhance feldspar purity and whiteness.
Materials and methods
The feldspar sample was obtained from Wadi Zirib, Eastern desert, Egypt. The sample was first crushed using a 5"× 6" Denver Jaw crusher, followed by secondary crushing with a Wedag roller, producing a product with diameters less than 2 mm. Subsequently, the crushed material was milled using a cylindrical ball mill of 20 cm length and an internal diameter of 15 cm, driven by two rollers.
The operational parameters influencing the batch wet grinding process: the grinding media consisted of spherical steel balls with a diameter of 3.66 cm; assuming a bed porosity of 40 %; the ball filling ratio was set at 25 %; solid in slurry was 65 wt.%; mill operating speed 76 rpm, equivalent to 70 % of its critical speed; milling was carried out at different grinding times.
Previous investigations into Egyptian feldspar from the Wadi Zirib locality established that the liberation size is below 250 µm [23-25]. The objective of grinding was to ascertain the optimal grinding time that maximizes the production of coarse sizes (–250+45 µm) while avoiding over-grinding and minimizing the presence of slimes (–45 µm). The presence of slimes is particularly undesirable as they can adversely impact subsequent separation processes, such as magnetic separation and flotation. After each batch grinding test, the ground material was screened using 250 and 45 µm sieves to determine the proportions of +250 µm, –250+45 µm, and –45 µm size fractions. The –250+45 µm was dried and utilized as a feed for the Magna roll (dry high-intensity magnetic separator), while the –45 µm was used as a feed for the Box-mag rapid (wet high gradient magnetic separator).
Chemical analysis
Quantitative chemical analysis of the oxides content in feldspar samples was carried out using X-ray fluorescence analysis (XRF), Phillips PW 2404, Netherlands. 10 g of the dried sample is mixed and pressed with 2g of wax as a binder in an aluminum cup, and then exposed to X-ray as a disk. Iron oxide of different separated feldspar samples was followed by using a Perkin Elmer Analyst 400 atomic absorption unit.
Magna roll dry magnetic separation
The coarse-sized feldspar (–250+45 µm) obtained from grinding was subjected to dry magnetic separation using Magna roll dry rare earth magnetic separator (DREMS). This rolling-type separator operates on dry basis with fixed magnets that have high field intensity and gradient (1.5 Ta ~ 15000 G). The roll type magnets (permanent magnetic roll) are made of alloys of rare earth magnetic elements and are utilized in the roller magnetic separators. These rolls are more powerful than ordinary electric magnetic magnets. Due to their magnetic characteristics and unique magnetic series, they produce strong magnetic attraction forces on the magnetic roller. This strong magnetic force can separate minerals with weak magnetic properties. In the end of the experiments the magnetic and non-magnetic fraction are weighted and chemically analyzed.
Wet high-intensity high-gradient magnetic separation
The sample of fraction less than 45 μm which produced from grinding process was pumped as slurry to the laboratory “Box-mag rapid” separator at different feeding flow rates using Masterflex 7518-00 peristaltic pump. The separation was operated at different magnetic field intensities up to 14000 G. When the slurry sample completely passed through the canister box, the fine steel wool was washed with fixed amount of water at constant rate throughout all the tests. After washing, the nonmagnetic clean product was collected. Then the separator was off and the magnetic fraction was then collected by flushing water until the effluent was clear. The magnetic fraction was then collected, dewatered and dried. All products were weighed and chemically analyzed for total iron oxide.
Leaching using different doses of oxalic and citric acids
In these experiments, oxalic or citric acids can be used as a leaching agent for 1 h and 90 °C to dissolve iron oxide impurities. This process will be applied to the produced non-magnetic concentrates (at optimum conditions of the magnetic separation) and the effect of different dosage of the oxalic acid are studied. In each experiment, 10 g of the sample are placed in a beaker on the hot plate with strong stirring. The acids were supplied from El-Nasr Co. for Chemical Industries (Egypt). All solutions were freshly prepared using bi-distilled water.
Optical properties measurement
The whiteness degree was measured for the non-magnetic fraction after magnetic separation and bleaching process was determined using UV whiteness and color-meter model JY 98. The sample was put in the dryer for 2 h at 100 °C to be completely dry. About 10 g of dried sample was compressed by a powder mold. The smooth surface of compressed sample exposed to UV lamp in the measuring port. The equipment is connected to the computer and printer for out putting the results.
Results and discussion
Mineralogy and chemical composition of the sample
The mineralogical and chemical analysis of Wadi Zirib feldspar ore has been previously examined in detail by the authors [24, 25]. XRD analysis of the sample revealed that albite and microcline are the primary feldspar minerals, with quartz as the main gangue and minor hematite impurities. Chemical analysis of the sample by XRF showed that the sample contains: SiO2 75.85 %, Al2O3 12.48 %, Fe2O3 1.40 %, Na2O 3.22 %, K2O 5.36 %, CaO 0.93 %.
The effect of grinding time on crushed feldspar
The size distribution of the feed material as defined from dry sieving, wt.%: 2000 μm – 100; 1160 μm – 81; 850 μm – 55; 590 μm – 35; 417 μm – 15; 250 μm – 0. Before grinding, the fraction less than 250 µm was first separated from the feed. Figure 1 presents the results of grinding kinetics at 65 % solid content in slurry, 5 % powder filling, and 25 % ball filling of size 36.6 mm and different times. Figure 1, a showed that the desired size for Magna roll (–250+45µm) is significantly increased as the grinding time extended to 15 min. However, further grinding beyond this point led to a decrease in the target feed size (–250+45 µm) for the magnetic separation process and an increase in fine slimes (–45 µm). Therefore, a grinding time of 15 min was selected as optimal. The fraction less than 45 μm is suggested to be upgraded using wet high gradient magnetic separation (Box-mag rapid separator).
The variation in the proportion of unground coarse fraction (+250 μm) is described by a basic kinetic equation
where t – grinding time; R0 – percentage of coarse fraction before grinding; k – grinding rate, i.e., the relative decrease in the percentage of coarse fraction per unit time; m – denotes the time dependency of the relative grinding rate [26-28].
Figure 1, b shows relation between ln(t) and ln(R0/Ri). As can be seen from the results obtained, the kinetics of grinding obeys a first-order equation – linear relationship between relative content unground fractions ln(R0/Ri) and ln(t). Based on the results of a study of the kinetics of grinding of feldspar ore, equations were obtained that describes the percent of the production of fractions –250 µm, –250+45 µm and –45 µm at different time, respectively:
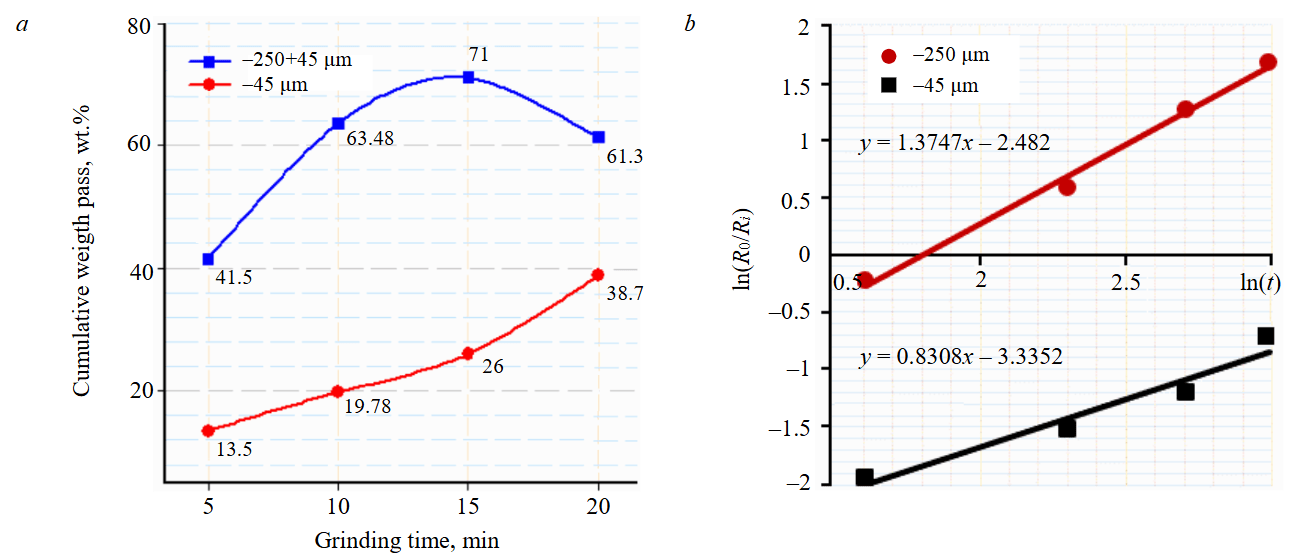
Fig.1. Grinding kinetics of feldspar ore: a – change in percent weight of fraction –250+45, –45 μm at different grinding times; b – relation between ln(t) and ln(R0/Ri)
Magna roll dry magnetic separation
The efficiency of the separation process for coarse-sized feldspar (–250+45 µm) produced after grinding, as well as the percentage of iron oxide removal, were studied using a Box – Behnken factorial design. This design provides insights into the interactions of various factors and the overall functioning of the system. The variables investigated in this research are belt speed (20 to 60 rpm), and feed (20 to 280 g/min). The optimum conditions were evaluated with a second order polynomial function to conduct a correlation between studied variables and responses percent yield of concentrate (non-magnetic fraction) and percent Fe2O3 assay and removal.
ANOVA data for the separation system implies the well convenience of the experimental results to the polynomial model equation and thus the accuracy of this model (Table 1). The Model F-values suggest that the model is statistically significant, with only a 0.01 % chance that such a large F-value could occur due to random noise. The critical value (F-critical) of the F-value is 230.16 %; model < 0.0001 %; feed rate < 0.0001 %; delt speed < 0.0001 %. P-values less than 0.0500 indicate that the corresponding model terms are significant.
Table 1
ANOVA data for response surface quadratic model of RER magnetic separator
The statistical parameters |
Yield, % |
Fe2O3, % |
||
Assay |
Removal |
|||
Standard deviation |
0. 154 3 |
0.0006 |
0.0690 |
|
R-squared |
0.99 9 6 |
0.9999 |
0.9996 |
|
Adequate precision |
142.58 |
293.67 |
104.789 |
|
F-value |
|
|
|
|
|
Model |
2277.3 |
8950.06 |
2216.22 |
Feed rate |
5111.52 |
8580.5 |
20.74 |
|
Belt speed |
4066.43 |
7200 |
28.33 |
Figure 2 depicts the response surface of different operating variables of Magna roll using Box – Behnken factorial design. Figure 2, a represents the effects of belt speed and feed rate on the percent yield of non-magnetic fraction. It has been shown that the yield percent of concentrate (non-magnetic fraction) increased with increasing the feeding rate and decreasing the belt speed. The maximum yield percent of the concentrate (94 %) was observed at maximum feed rate (280 g/min) and minimum belt speed (20 rpm), while minimum yield (77.05 %) was observed at lowest feed rate (20 g/min) and highest belt speed (60 rpm). According to S.K.Tripathy et al. [29], a high roll rotation will increase the centrifugal force component, resulting in the material more readily being projected to the non-magnetic fraction. However, this could be influenced by the initial feed size of the sample, the percentage of fines, the material's susceptibility to a magnetic field, and the type of associated gangue (whether the gangue mineral shows positive or negative susceptibility), as well as the degree of liberation. Based on our observations, there is a decrease in the yield of non-magnetic product and more contamination with iron-bearing minerals as the belt speed increases, accompanied by a rise in the percentage of fines (–125+45 µm) in the magnetic product (Table 2). The impact of belt speed on the percentage of fines is notably more significant than that of feeding rate. The percentage of fines in the magnetic product increases with the belt speed, rising from 56 % at low speed and high feed rate to 79 % at high speed and low feed rate. These fines tend to adhere to the roll due to the increasing centrifugal force and may due to the retention time not enough to separate more fine feldspar into non-magnetic fraction, which negatively affects the grade of Fe2O3 and its percentage removal.
Figure 2, b illustrates the impact of feed rate and belt speed on the percentage of iron oxide in the non-magnetic fraction. By raising the feed rate from 20 to 150 g/min, the percentage of iron oxide in the concentrate decreased. Elevating the feed rate beyond 150 g/min adversely impacted separation efficiency and resulted in an increase in the percentage of iron oxide in the concentrate (non-magnetic fraction). High feed rates may have an adverse impact on separation since a greater number of particles will need to share the field intensity, thereby reducing usable area between the magnets [30].
This finding aligns with prior research [31], which determined that, Increasing the feed rate of Magna roll over 200 g/min led to overcrowding in the separation zone and, hence a corresponding deterioration in the quality of the concentrate took place. The best quality concentrate with the lowest iron oxide content (0.3 %) was obtained with a medium feed rate of 150 g/min and a low belt speed of 20 rpm. The highest Fe2O3 percentage (0.43 %) is observed at the minimum feed rate coupled with the maximum belt speed.
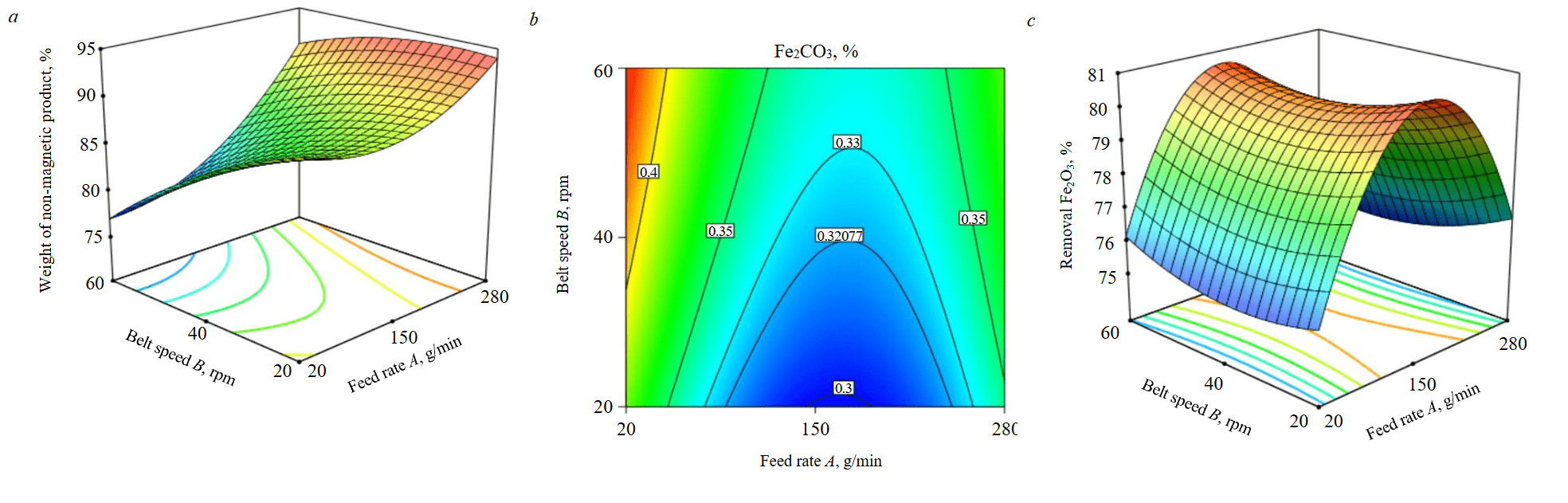
Fig.2. 3D relationship between belt speed, feed rate with percent yield of the concentrate (a); the percent Fe2O3 in the concentrate (b); the percent removal Fe2O3 (c)
As a general rule, pick-up separators like belts or rolls are optimally operated with a single particle layer (a minimum feed rate, 20 g/min) to minimize the “shielding effect” caused by additional layers of feed. While this approach maximizes the separation of iron-bearing minerals, it commonly leads to reduced productivity. Conversely, increasing the number of feed layers on the belt enhances productivity but tends to minimize the grade of separation [32].
Table 2
Box – Behnken design results for Magna roll magnetic separator
Test number |
Feed rate, g/min |
Belt speed, rpm |
Non-magnetic product, wt.% |
Fe2O3, % |
Removal Fe2O3, % |
Magnetic product, wt.% |
Fe2O3, % |
–125+45 µm in magnetic product, % |
1 |
150 |
40 |
85.93 |
0.32 |
80.36 |
14.07 |
7.97 |
66.50 |
2 |
280 |
60 |
91.06 |
0.37 |
75.93 |
8.94 |
11.84 |
69.00 |
3 |
280 |
20 |
94.00 |
0.35 |
76.50 |
6.00 |
17.89 |
56.00 |
4 |
20 |
60 |
77.05 |
0.43 |
76.33 |
22.95 |
4.65 |
79.00 |
5 |
150 |
40 |
85.93 |
0.32 |
80.36 |
14.07 |
7.97 |
66.50 |
6 |
20 |
20 |
89.86 |
0.38 |
75.61 |
10.14 |
10.45 |
64.00 |
7 |
150 |
60 |
80.38 |
0.34 |
80.48 |
19.62 |
5.74 |
73.60 |
8 |
280 |
40 |
93.70 |
0.36 |
75.91 |
6.30 |
16.80 |
62.00 |
9 |
150 |
20 |
88.73 |
0.30 |
80.99 |
11.27 |
10.06 |
60.00 |
10 |
20 |
40 |
84.83 |
0.41 |
75.16 |
15.17 |
6.94 |
71.00 |
However, it has been noticed that utilizing multiple layers on the belt resulted in enhanced separation compared to a single layer, particularly at lower belt speed (higher retention time). This improvement can be attributed to the heightened presence of fines passing into the magnetic fraction, which is characterized by a lower percentage of Fe2O3 compared to the coarser particles (>125 μm). At lower feed rates, the non-magnetic fraction comprised roughly 23 %, with the highest percentage of fines reaching 79 %.
Figure 2, c shows the effect of feed rate and belt speed on the percent removal of iron oxide in the non-magnetic fraction. The maximum percent removal of iron oxide (80.9 %) was obtained at moderate feed rate and low belt speed. The impact of feed rate on the percent Fe2O3 removal is more significant than the influence of belt speed:
Yield of non-magnetic fraction = +93.68448 – 0.063561A – 0.079903B + 0.000949AB + 0.000201A2 – 0.003291;
Fe2O3 = +0.362888 – 0.001203A + 0.002146B – 2.30769E – 0.6AB + 3.75740E – 06A2 – 1.00000E – 0.5B2;
Removal Fe2O3 = +75.57419 + 0.090634A – 0.107003B – 0.000148AB – 0.000279A2 + 0.001521B2,
where A – feed rate g/min; B – belt speed, rpm; value of R2 was 0.999 for this model.
The high value of R2 indicates that the quadratic equation is capable of representing the system under the given experimental domain.
Figure 3 shows the optimum parameters of Box – Behnken design of feldspar dry magnetic separation using Magna roll magnetic separator are: 20 rpm belt speed and 150 g/min feed rate. With these optimum parameters, 87.76 % of non-magnetic feldspar concentrate containing a minimum 0.285 % Fe2O3 and a maximum 81.1 % removal. The best operational conditions have been specified by the highest desirability (0.948).
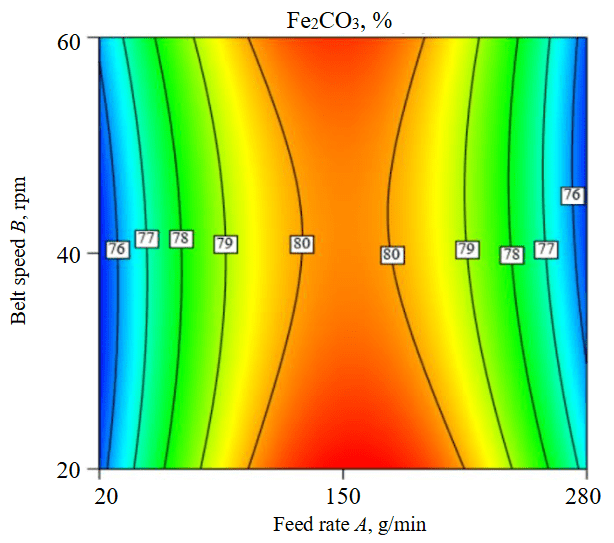
Fig.3. The desirability of operational parameters of feed rate and belt speed for the dry separation of feldspar ore using Magna roll magnetic separator
Table 3 shows the results of fractionating the –250+45 µm feed into two size cuts, –250+125 µm and –125+45 µm. It has been showed that separation of fine size –125+45 µm under a monolayer feed rate 20 g/min, belt speed of 20 rpm resulting in obtaining a high quality of concentrate but the percent yield is very low 61.83 % and this explains the previous results of increasing the fines in magnetic separation by decreasing the belt speed. The separation efficiency in coarse fraction size –250+125 µm is better than the fine one –125+45 µm where the product in case of coarse feed size, the percent Fe2O3 dropped from 1.87 to 0.284 % with a percentage removal of 86 % at low feed rate and low speed, while in case of fine fraction, the concentrate of Fe2O3 0.275 % was obtained from a feed of 0.54 % with only 68.68 % removal. When separating a finer feed (–125+45 µm), however, the yield increase with increasing the feed rate but the percentage removal decreased.
Table 3
Results of feed fractionation prior to separation
Fraction size, μm |
Yeld, % |
Fe2O3, % |
Feed rate, g/min |
Belt speed В, rpm |
Non-magnetic product |
||
Weight, wt.% |
Fe2O3, % |
Removal Fe2O3, % |
|||||
–250+125 |
64.2 |
1.87 |
20 |
20 |
92.51 |
0.28 |
86.16 |
150 |
20 |
93.70 |
0.30 |
84.97 |
|||
280 |
20 |
97.74 |
0.49 |
74.39 |
|||
280 |
60 |
95.49 |
0.33 |
83.15 |
|||
–125+45
|
35.8 |
0.54 |
20 |
20 |
61.83 |
0.27 |
69.09 |
150 |
20 |
89.50 |
0.28 |
53.59 |
|||
280 |
20 |
96.75 |
0.39 |
30.13 |
|||
280 |
60 |
87.75 |
0.35 |
43.13 |
Table 4 summarize the results of separation with and without fractionating the feed into two size cuts. Considering the high concentrate quality, the best separation was at feed rate 20 g/min and belt speed 20 rpm. This confirms the necessitates using very closed size feeds with this kind of separator. Considering the high yield percentage with high productivity. A total yield of the final concentrate 92.19 % with iron content of 0.293 % Fe2O3 and 80.7 % removal was obtained at feed rate 150 g/min and belt speed 20 rpm. From these results it could be concluded that, separating the feed into two closed fraction size is a good choice for obtaining high quality of concentrate with high yield percent. From the economical point of view, the feed rate of 150 g/min with a belt speed of 20 g/min was chosen for preparing the feed for subsequent purification process.
Table 4
Results of separation with and whithout fractionating
Feed rate, g/min |
Belt speed, rpm |
Non-magnetic product |
|||||
With fractionation |
Without fractionation |
||||||
Weight, wt.% |
Fe2O3, % |
Removal Fe2O3, % |
Weight, wt.% |
Fe2O3, % |
Removal Fe2O3, % |
||
20 |
20 |
81.54 |
0.28 |
83.69 |
89.86 |
0.38 |
75.61 |
150 |
20 |
92.19 |
0.29 |
80.90 |
88.73 |
0.30 |
80.99 |
280 |
20 |
97.37 |
0.45 |
68.70 |
94.00 |
0.35 |
76.50 |
280 |
60 |
92.68 |
0.34 |
77.49 |
91.06 |
0.38 |
75.28 |
Box-mag rapid HGMS of fine feldspar (–45 µm)
The major reason affecting the selectivity of HGMS is the retention of non-magnetic gangue as the feed passes through the magnetized matrix stack [33, 34]. The affecting variables (percent solid in the slurry, feed rate, and magnetic field intensity) on the separation of iron oxide from fine feldspar sample (–45µm) are demonstrated in Fig.4.
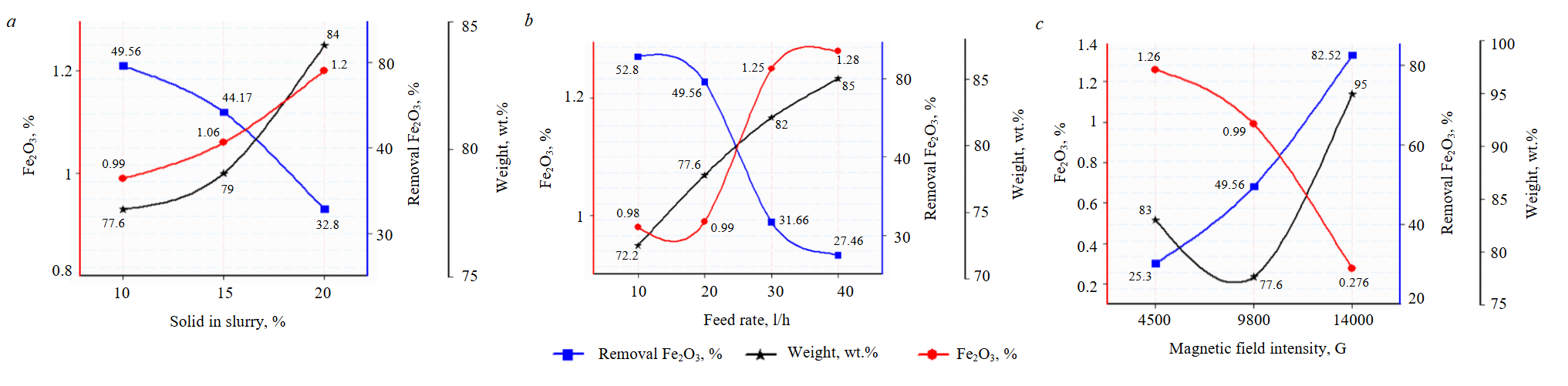
Fig.4. Variable affecting on the separation of iron oxide using Box-mag: solid in the slurry (a); feed rate (b); magnetic field intensity (c)
Effect of percent solid in the slurry
If the percent solid in slurry is high, the reduction of the flow of materials tends to make magnetic particles to be covered by feldspar particles. The iron magnetic impurity separates mixed with feldspar, therefore non-magnetic (concentrate) yield and iron grade are high, too. Therefore, it is difficult to separate iron magnetic impurity from feldspar with higher pulp density.
At a constant field intensity (9800 G), the results of an investigation into the effect of increasing the solid percentage on percent iron oxide and its removal by wet magnetic separation using Box-mag rapid magnetic separator were shown in Fig.4, a. With increasing solid percent in the pulp, the efficiency of the separation decreases and in the same time the removing percentage of iron oxide decreased. This might be explained by the possibility that when the solid percentage rises, magnetic particles could become coated with non-magnetic ones and pass to the non-magnetic fraction, which causes the percent of iron oxide in the non-magnetic fraction to increase [35]. The solid percent in slurry for the following series was taken as 10 %.
Effect of feeding rate
The basic concept of retention time entails controlling the flow rate in a canister to balance the medium's viscous drag on the suspended particles in slurry against the force of magnetic attraction created in the matrix by the background field. The main objective for effective magnetic separation remains concentrated on maximizing retention time, as it directly affects both the quality of the product and the rate of production [36].
Figure 4, b illustrates the impact of increasing the feeding rate on the removing of iron oxide from fine feldspar ore. It is obvious that raising the feeding rate results in an increase in the weight percentage of the non-magnetic fraction, concurrently reducing separation efficiency, i.e., increasing the presence of iron oxide in the non-magnetic fraction. This phenomenon may be attributed to lower particle speeds, which enhance the likelihood of iron-bearing particles being easily picked up and separated in the magnetic fraction, allowing a greater migration of nonmagnetic particles [35]. From an economic standpoint, the feeding rate of 20 l/h. was selected for subsequent tests because the percent yield of the non-magnetic fraction is higher at this rate compared to 10 l/h, and there is minimal fluctuation in both the percent of Fe2O3 and its removal.
Impact of increasing the magnetic field intensity
The ability to separate one material from another or removal of magnetizable particles from streams relies on how they respond to magnetic force in conjunction with various external forces, such as gravitational, inertial, hydrodynamic, and centrifugal forces [37, 38]. Fluid drag force as the main competing force is responsible for expelling non-magnetic particles out from the matrix box. The main external force influencing a magnetic separator is magnetic force, which is directly correlated with the intensity of the magnetic field. To attain a high magnetic particle recovery, the magnetic separation force must be greater than the sum of competing forces. However, if the magnetic force greatly exceeds the competing forces, the separation's selectivity will be poor. Therefore, selecting an appropriate magnetic field intensity is crucial [39, 40].
The experiment is carried out with the following parameters: a 10 % solid in the slurry, a feed rate of 20 l/h. Magnetic field intensities of 4500, 9800 and 14,000 G are selected (Fig.4, c). The iron oxide drastically decreased with increasing the magnetic field, it decreased from 1.26 % at 4500 G to 0.276 % at 14,000 G. Also, high Fe2O3 removal from feldspar was obtained at high magnetic field. As a result, the percent removal increased from 25.52 % at 4500 to 82.52 % at 14,000 G.
Acid leaching of the non-magnetic feldspar concentrates
Acid leaching of the non-magnetic feldspar concentrates is a pivotal process aiming to enhance the purity and the optical properties of feldspar products. This method involves treating the feldspar concentrates with organic acids to dissolve the iron-bearing compounds. Through optimizing leaching conditions, the Fe-bearing minerals are selectively dissolved, leaving behind a purified feldspar product with improved chemical composition and whiteness.
Citric or oxalic acid act as a chelating agent, forming soluble complexes with iron ions in the presence of water. Using citric acid, a possible chemical equation for the reaction is [41-44]:
the hydronium ions react with hematite (Fe2O3) to release iron (III) ions (Fe3+):
the citrate ions (C6H5O73−) bind to the released Fe3+ forming stable and soluble iron-citrate complexes:
The solubilized iron citrate complex is removed from the feldspar ore.
In case of oxalic acid (C2H2O4) dissociates in water, producing hydronium ions (H3O+) and oxalate ions (C2O42−): The chemical equation can be presented as:
The released iron (III) ions (Fe3+) react with oxalate ions (C2O42−) to form highly stable and soluble iron-oxalate complexes, which can be washed away from the ore,
The citric and oxalic acid concentration should be optimized to effectively chelate iron while minimizing the dissolution of feldspar itself.
The non-magnetic feldspar product of size fraction –250+45 µm obtained using Magna roll dry high intensity magnetic separator underwent leaching process. The acid leaching was conducted using oxalic and citric acids to dissolve iron oxide further, using varying dosages of the acids (Table 5). When treated with oxalic acid, iron oxide reduced from 0.293 to 0.21 % at 3 kg/t dosage, achieving an 82.50 % removal. Conversely, at the same citric acid concentration, it decreased to 0.26 %, suggesting high efficiency of oxalic acid in iron oxide removal. Dosages exceeding 3 kg/t of oxalic acid showed no significant impact on iron oxide removal.
Table 5
Leaching results of the non-magnetic feldspar concentrate using citric and oxalic acids
Concentrate |
Acid |
Amount of reagent, kg/t |
|||||||||
0 |
1 |
2 |
3 |
4 |
|||||||
IO |
IOR |
IO |
IOR |
IO |
IOR |
IO |
IOR |
IO |
IOR |
||
Magna roll, –250+45 μm |
Citric |
0.293 |
80.7 |
0.28 |
81.3 |
0.26 |
81.8 |
0.26 |
81.2 |
0.26 |
81.2 |
Oxalic |
0.293 |
80.7 |
0.24 |
81.58 |
0.22 |
82 |
0.21 |
82.5 |
0.21 |
82.5 |
|
Box-mag rapid, –45 μm |
Citric |
0.276 |
82.52 |
0.25 |
82.19 |
0.23 |
82.35 |
0.2 |
82.4 |
0.2 |
82.4 |
Oxalic |
0.276 |
82.52 |
0.21 |
82.26 |
0.19 |
82.45 |
0.15 |
82.84 |
0.12 |
82.91 |
Note. IO – iron oxide, %; IOR – iron oxide overall percent removal.
Also, the leaching process was applied to the non-magnetic feldspar product of size fraction –45 µm obtained from Box-mag rapid wet high intensity magnetic separator. Reaffirming the efficiency of oxalic acid over citric acid. Oxalic acid reduced iron oxide from 0.21 to 0.12 %, achieving an overall removal 82.91 %, while citric acid reduced it to 0.20 with an 82.4 % removal.
Table 6 displays the optical properties of the leached concentrate, showing an increase in whiteness from 65.19 to 89.80 % compared to the original sample.
Table 6
Optical properties of feldspar products after leaching with oxalic acid, %
Leaching concentrates |
Brightness |
ISO brightness |
Whiteness |
Redness |
Yellowness |
Product Magna roll |
77.44 |
80.45 |
88.12 |
6.63 |
8.23 |
Product Box-mag rapid |
79.25 |
82.76 |
89.80 |
4.85 |
6.88 |
Conclusions
This study aimed at reducing the iron oxide content in Wadi Zirib feldspar ore and achieving an optimal grade of feldspar concentrate for various industrial uses.
The kinetics of feldspar grinding obeyed a first-order equation – linear relationship between relative content unground fractions ln(R0/Ri) and ln(t).
The factors affecting the dry magnetic separation, for feldspar size of –250+45µm, were optimized using the Box – Behnken factorial design. Applying the Magna roll optimum parameters, 20 rpm belt speed and 150 g/min feed rate, a non-magnetic concentrate with 0.29 % Fe2O3 and 92.19 % feldspar yield was obtained.
The wet magnetic separation for feldspar fines (–45µm) was optimized. Applying the Box-mag rapid optimum parameters, 10.0 % solid in slurry, 20 l/h feeding rate with maximum magnetic field intensity of 14,000 G, a concentrate with 0.27 % Fe2O3 was achieved with Fe2O3 removal of 82.52 %.
Oxalic acid was more successful than citric acid in leaching iron oxide of dry and wet non-magnetic feldspar concentrates. The leaching of non-magnetic product of size fraction –250+45 µm reduced iron oxide from 0.29 to 0.21 % at 3 kg/t oxalic dosage, achieving an Fe2O3 removal of 82.50 % while whiteness is improved up to 88.12 %. Also, leaching of the non-magnetic feldspar product of size fraction –45 µm using oxalic acid reduced iron oxide from 0.27 to 0.12 %, achieving an 82.91 % removal with an increase in whiteness up to 89.80 %. To enhance the efficiency of iron oxide removal and improve the overall purity of the final product, integrating a sequential magnetic beneficiation scheme is recommended for future studies.
References
- Zahradník J., Jirásek J., Starý J., Sivek M. Production, Reserves, and Processing of Feldspar and Feldspathoid Rocks in the Czech Republic from 2005 to 2019 – An Overview. Minerals. 2020. Vol. 10. Iss. 8. N 722. DOI: 10.3390/min10080722
- Ye Zhang, Yuehua Hu, Ning Sun et al. Systematic review of feldspar beneficiation and its comprehensive application. Minerals Engineering. 2018. Vol. 128, p. 141-152. DOI: 10.1016/j.mineng.2018.08.043
- Baila F., Labbilta T., Darmane Y. Feldspar Purification from Iron Impurities: A Review of Treatment Methods. Mineral Processing and Extractive Metallurgy Review. 2024. Vol. 45. Iss. 6, p. 564-572. DOI: 10.1080/08827508.2023.2217322
- Castroviejo R. Silicates. A Practical Guide to Ore Microscopy – Volume 1: Mineral Identification. Springer, 2023. 819-844. DOI: 10.1007/978-3-031-12654-3_135
- Vrbický T., Přikryl R. Recovery of Some Critical Raw Materials from Processing Waste of Feldspar Ore Related to Hydrothermally Altered Granite: Laboratory-Scale Beneficiation. Minerals. 2021. Vol. 11. Iss. 5. N 455. DOI: 10.3390/min11050455
- Ruiqi Xie, Yimin Zhu, Jie Liu, Yanjun Li. The flotation behavior and adsorption mechanism of a new cationic collector on the separation of spodumene from feldspar and quartz. Separation and Purification Technology. Vol. 264. N 118445. DOI: 10.1016/j.seppur.2021.118445
- Gulbin Yu.L., Akbarpuran Khaiyati S.A., Sirotkin A.N. Mineral composition and thermobarometry of metamorphic rocks of Western Ny Friesland, Svalbard. Journal of Mining Institute. Vol. 263, p. 657-673.
- Chunfu Liu, Weitao Wang, Han Wang et al. A Review on Removal of Iron Impurities from Quartz Mineral. Minerals. 2023. Vol. 13. Iss. 9. N DOI: 10.3390/min13091128
- Elbendari A., Aleksandrov A., Nikolaeva N., Afanasova A. Selective flotation of phosphorus-bearing ores. E3S Web of Conferences. 2020. Vol. 192. N 02021. DOI: 10.1051/e3sconf/202019202021
- Gougazeh M.H. Beneficiation and Upgrading of Low-Grade Feldspar Ore in Medina, Saudi Arabia. Journal of Ecological Engineering. 2022. Vol. 23. Iss. 6, p. 271-277. DOI: 10.12911/22998993/147834
- Sizyakov V.M. Chemical and technological mechanisms of a alkaline aluminum silicates sintering and a hydrochemical sinter processing. Journal of Mining Institute. Vol. 217, p. 102-112 (in Russian).
- Jiangang Ku, Kunpeng Wang, Qian Wang, Zhongyun Lei. Application of Magnetic Separation Technology in Resource Utilization and Environmental Treatment. Separations. 2024. Vol. 11. Iss. 5. N 130. DOI: 10.3390/separations11050130
- Junxiong Zhan, Jinshan Lu, Di Wang et al. Scalable recycling of feldspar slime into high-quality concentrates by removal of colored minerals using the combined beneficiation processes. Separation and Purification Technology. 2023. Vol. 309. N 123061. DOI: 10.1016/j.seppur.2022.123061
- Saisinchai S., Boonpramote T., Meechumna P. Upgrading Feldspar by WHIMS and Flotation Techniques. Engineering Journal. 2015. Vol. 19. Iss. 4, p. 83-92. DOI: 10.4186/ej.2015.19.4.83
- Hayatullah, Asma Shafiq Shathi, Md Golam Mostafa et al. Iron removal from red clay using oxalic acid leaching for enhanced ceramic industry applications. Heliyon. 2024. Vol. 10. Iss. 19. N e38863. DOI: 10.1016/j.heliyon.2024.e38863
- Samantray J., Anand A., Dash B. et al. Silicate minerals – Potential source of potash – A review. Minerals Engineering. 2022. Vol. 179. N 107463. DOI: 10.1016/j.mineng.2022.107463
- Sánchez-Palencia Y., Bolonio D., Ortega M.F. et al. Iron Removal from Kaolin Waste Dumps by Chemical (Oxalic and Citric Acids) and Biological (Bacillus Strain) Leaching. Clays and Clay Minerals. 2022. Vol. 70. N 3. p. 386-404. DOI: 10.1007/s42860-022-00192-7
- Yassin Kh.E., Mourad S.H., Khalil M.M.H. et al. Upgrading and Surface Coating of Egyptian White Sand with Polymers and Silanes. Rudarsko-geološko-naftni zbornik. 2024. Vol. 39. N 1, p. 101-114. DOI: 10.17794/rgn.2024.1.9
- Aleksandrova T.N., Chanturiya A.V., Kuznetsov V.V. Mineralogical and technological features and patterns of selective disintegration of ferruginous quartzites of the Mikhailovskoye deposit. Journal of Mining Institute. Vol. 256, p. 517-526. DOI: 10.31897/PMI.2022.58
- Nikolaeva N.V., Aleksandrova T.N., Chanturiya E.L., Afanasova A. Mineral and Technological Features of Magnetite-Hematite Ores and Their Influence on the Choice of Processing Technology. ACS Omega. 2021. Vol. 6. Iss. 13, p. 9077-9085. DOI: 10.1021/acsomega.1c00129
- Athira S., Gangaputhiran S. A Critical Review on Potential Use of Iron Ore Tailings as Structural Fill Material. Soil Behavior and Characterization of Geomaterials. Springer, 2022, 69-78. DOI: 10.1007/978-981-19-6513-5_6
- Xue Sun, Chenglei Hu, Tianguo Li et al. Research progress on iron-rich industrial waste as environmentally functional material. Sustainable Chemistry and Pharmacy. 2024. Vol. 42. N 101772. DOI: 10.1016/j.scp.2024.101772
- Ahmed M.M., Ibrahim G.A., Rizk A.M.E., Mahmoud N.A. Reduce the Iron Content in Egyptian Feldspar Ore of Wadi Zirib for Industrial Applications. International Journal of Mining Engineering and Mineral Processing. 2016. Vol. 5. N 2. p. 25-34. DOI: 10.5923/j.mining.20160502.01
- Yassin Kh.E., Elbendari A.M., Hassan E.-S.R.E. Optimizing the removal of iron oxide from Egyptian feldspar ore. Physicochemical Problems of Mineral Processing. 2023. Vol. 59 (6). N 176420. DOI: 10.37190/ppmp/176420
- Yassin Kh.E., Hassan E.-S.R.E., Abdel Khalek N.A., Elbendari A.M. Some aspects on grindability of feldspar ore using ball mill. Particulate Science and Technology. 2024. Vol. 42. Iss. 5, p. 837-848. DOI: 10.1080/02726351.2023.2293168
- Petrakis E., Komnitsas K. Effect of Grinding Media Size on Ferronickel Slag Ball Milling Efficiency and Energy Requirements Using Kinetics and Attainable Region Approaches. Minerals. 2022. Vol. 12. Iss. 2. N 184. DOI: 10.3390/min12020184
- Rudakova L.V., Niftaliev S.I., Natarova E.S. Kinetics and the mechanism of chemically-deposited calcium carbonate grinding. Condensed Matter and Interphases. Vol. 20. N 2, p. 248-254 (in Russian). DOI: 10.17308/kcmf.2018.20/516
- Jianwen Yu, Yonghong Qin, Peng Gao et al. An innovative approach for determining the grinding media system of ball mill based on grinding kinetics and linear superposition principle. Powder Technology. 2021. Vol. 378. Part A, p. 172-181. DOI: 10.1016/j.powtec.2020.09.076
- Tripathy S.K., Singh V., Murthy Y.R. et al. Influence of process parameters of dry high intensity magnetic separators on separation of hematite. International Journal of Mineral Processing. 2017. Vol. 160, p. 16-31. DOI: 10.1016/j.minpro.2017.01.007
- Tripathy S.K., Banerjee P.K., Suresh N. et al. Dry High-Intensity Magnetic Separation In Mineral Industry – A Review Of Present Status And Future Prospects. Mineral Processing and Extractive Metallurgy Review. 2017. Vol. 38. Iss. 6, p. 339-365. DOI: 1080/08827508.2017.1323743
- Ibrahim S.S., Mohamed H.A., Boulos T.R. Dry magnetic separation of nepheline syenite ores. Physicochemical Problems of Mineral Processing. 2002. Vol. 36 (1), p. 173-183.
- Ibrahim S.S., Farahat M.M., Boulos T.R. Optimizing the performance of the RER magnetic separator for upgrading silica sands. Particulate Science and Technology. 2015. Vol. 35. Iss. 1, p. 21-28. DOI: 10.1080/02726351.2015.1121179
- Zhicheng Hu, Dongfang Lu, Xiayu Zheng et al. Development of a high-gradient magnetic separator for enhancing selective separation: A review. Powder Technology. 2023. Vol. 421. N 118435. DOI: 10.1016/j.powtec.2023.118435
- Jianwu Zeng, Xiong Tong, Dongxia Feng et al. Highly selective capture characteristics of magnetic wires in CHGMS method. Minerals Engineering. 2020. Vol. 149. N 106243. DOI: 10.1016/j.mineng.2020.106243
- Ibrahim S.S., Selim A.Q., Farahat M.M. et al. On Improving the Separation Efficiency of a Wet High Gradient Magnetic Separator for the Removal of Pyrite from Egyptian Coal. International Journal of Coal Preparation and Utilization. 2017. Vol. 37. Iss. 2, p. 59-74. DOI: 1080/19392699.2015.1125894
- Iranmanesh M., Hulliger J. Magnetic separation: its application in mining, waste purification, medicine, biochemistry and chemistry. Chemical Society Reviews. 2017. Vol. 46. Iss. 19, p. 5925-5934. DOI: 10.1039/C7CS00230K
- Aleksandrova T.N., O’Connor C. Processing of platinum group metal ores in Russia and South Africa: current state and prospects. Journal of Mining Institute. Vol. 244, p. 462-473. DOI: 10.31897/PMI.2020.4.9
- Nunna V., Suthers S.P., Pownceby M.I., Sparrow G.J. Beneficiation Strategies for Removal of Silica and Alumina from Low-Grade Hematite-Goethite Iron Ores. Mineral Processing and Extractive Metallurgy Review. 2022. Vol. 43. Iss. 8, p. 1049-1067. DOI: 10.1080/08827508.2021.2003353
- Kong J.W., Li S.Q., Miao X. et al. Experimental study on removal of iron from potash feldspar. IOP Conference Series: Earth and Environmental Science. 2017. Vol. 68. N 012013. DOI: 10.1088/1755-1315/68/1/012013
- Karagüzel C., Çelik M.S. Revisiting flotation mechanisms of the selective separation of alkali feldspars in the presence of NaCl. Physicochemical Problems of Mineral Processing. 2022. Vol. 58 (5). N 149928. DOI: 10.37190/ppmp/149928
- Olvera Venegas P.N., Hernández Cruz L.E., Lapidus G.T. Dissolution of Iron from Oxides in a Solution of Citric Acid and Sodium Thiosulfate. Advanced Materials Research. 2014. Vol. 976, p. 114-118. DOI: 10.4028/www.scientific.net/AMR.976.114
- Vapur H., Top S., Demirci S. Purification of feldspar from colored impurities using organic acids. Physicochemical Problems of Mineral Processing. 2017. Vol. 53 (1), p. 168-175. DOI: 10.5277/ppmp170112
- Pariyan K., Hosseini M.R., Ahmadi A., Zahiri A. Optimization and kinetics of oxalic acid treatment of feldspar for removing the iron oxide impurities. Separation Science and Technology. 2020. Vol. 55. Iss. 10, p. 1871-1882. DOI: 10.1080/01496395.2019.1612913
- Arslan V. A study on the dissolution kinetics of iron oxide leaching from clays by oxalic acid. Physicochemical Problems of Mineral Processing. 2021. Vol. 57 (3), p. 97-111. DOI: 10.37190/ppmp/135543