Combined method for processing spent acid etching solution obtained during manufacturing of titanium products
- 1 — Ph.D. Associate Professor Institute of Chemical Technologies and Engineering – Branch of the Ufa State Petroleum Technological University ▪ Orcid
- 2 — Ph.D., Dr.Sci. Professor Ufa State Petroleum Technological University ▪ Orcid
- 3 — Ph.D., Dr.Sci. Professor Institute of Chemical Technologies and Engineering – Branch of the Ufa State Petroleum Technological University ▪ Orcid
- 4 — Assistant Ufa State Petroleum Technological University ▪ Orcid
Abstract
Possessing high strength, low density and significant chemical resistance, titanium has found wide application in various fields of the national economy – the chemical industry, aviation and rocket technology, mechanical engineering, medicine, etc. The production of titanium products is hampered by a fairly strong oxide film covering its surface. Removal of the oxide film from the surface of titanium workpieces is carried out by etching in solutions of mineral acids of various compositions. A spent acid etching solution (SAES) is formed, containing titanium salt and the remainder of unreacted acids. Almost all etching solutions contain HF and one of the strong acids. This is H2SO4, HCl or HNO3. Thus, the SAES includes ions of titanium, fluorine or chlorine, orsulfate, or nitrate. SAES is quite toxic and must be diluted or cleaned several times before being discharged into a reservoir. Most of the methods used to extract impurities contained in SAES lead to a decrease in their content. As a result of such purification, there is a loss of substances contained in SAES in significant quantities and of interest for further use. The work presents experimental results obtained from the combined processing of SAES containing titanium fluoride, hydrofluoric and hydrochloric acids. At the first stage, SAES is treated with sodium hydroxide. The resulting titanium hydroxide precipitate is filtered off. At the second stage, the filtrate containing sodium fluoride and chloride is processed in a membrane electrolyzer. In this case, not only the extraction of sodium salts from the filtrate occurs, but also the production of sodium hydroxide and a mixture of hydrofluoric and hydrochloric acids. Sodium hydroxide can be used for processing SAES, and a mixture of acids for etching titanium workpieces.
Introduction
Titanium and its alloys are widely used in the manufacture of a wide variety of equipment, which is in high demand due to its anti-corrosion resistance, a good combination of strength properties, temperature resistance, low density and relatively high metal consumption. The main consumers of titanium and its compounds are aircraft and rocket manufacturing [1], chemical industry [2-4], metallurgy [5], medicine [6, 7], catalyst production [8], paint and varnish industry [9]. As a rule, the manufacture of titanium products is accompanied by heating, as a result of which its surface is covered with a fairly strong oxide film. To ensure the manufacturability of titanium workpieces, especially when applying modifying coatings to its surface, it is necessary to remove the oxide film from the surface. Toper form this operation, various methods are used [10-12].
In addition to mechanical, thermal and other methods, thermochemical methods are also widely used [13-15]. Such methods consist in treating the surface of products with mineral acids at certain temperatures [16, 17]. Hydrochloric, sulfuric, nitric, phosphoric and other acids are used as acids to dissolve oxide films on the surface of titanium and its alloys in various concentrations and at different temperatures [16, 17]. In contrast to these acids, hydrofluoric acid dissolves titanium at room temperature. In order to regulate the rate of dissolution of titanium, acids such as HCl, H2SO4, and HNO3 are introduced into the solution of hydrofluoric acid [18]. If the presence of sulfuric acid slightly increases the rate of the titanium dissolution process, then with the introduction of hydrochloric acid into the solution, it almost doubles, and the use of nitric acid leads to a decrease in the rate of dissolution.
In AO Bashkir Soda Company for etching the surface of titanium in the production of oxide-ruthenium-titanium anodes (ORTA), hydrochloric acid is used. The etching process is carried out in 25-27 % HCl at a temperature of about 85 °C. The resulting spent acid etching solution (SAES) in this case contains up to 180 g/l of titanium chloride and up to 110 g/l of hydrochloric acid.
VSMPO-AVISMA Corporation uses a mixture of aqueous solutions of HF and HCl at room temperature to etch the surface of titanium. The resulting SAES contains about 22 g/l of titanium fluoride, about 1.7 g/l of hydrofluoric acid and about 6.2 g/l of hydrochloric acid. This solution is even more toxic than a solution containing only titanium chloride and hydrochloric acid, due to the presence of anion fluoride. The maximum permissible concentrations of SAES components in water bodies of domestic and domestic water use are for ions, mg/l: fluorine 1.5, chlorine 350, sulfate 500, titanium 0.1 (GN 2.1.5.1315-03.Hygienic standards. Maximum permissible concentrations (MPC) of chemicals in the water of water bodies for domestic and domestic water use). Thus, when SAES is discharged into a water body, significant water costs are required to dilute it. In addition, in this case, there is a loss of valuable components that can serve as raw materials for obtaining marketable products. There are known methods for the utilization and neutralization of SAES using ion exchange [19-21], coagulation and sedimentation [22-24], and neutralization [25, 26].The process of neutralization of SAES leads to the consumption of alkaline reagents, the formation of toxic solid wastes such as CaF2 and Na2TiF6 of the 2nd hazard class, as well as to the loss of mi-neral acids [27-30].
In the authors' previous works, the possibility of processing wastewater containing various substances to obtain products that can be used in the production process was considered [31-33].This article presents the results of research on the processing of SAES containing titanium fluoride, hydrofluoric and hydrochloric acids. The SAES was processed in two stages. At the first stage, the SAES was treated with sodium hydroxide titanium. The resulting titanium hydroxide precipitate was filtered off and dried. At the second stage, the filtrate containing fluorine, chlorine and sodium ions was processed in a membrane electrolyzer. As a result of electrochemical treatment of the filtrate in the electrolyzer, sodium hydroxide and a mixture of hydrofluoric and hydrochloric acids were generated.
Methodology
Experimental studies were carried out in two stages. At the first stage, SAES was treated with crystalline sodium hydroxide. For this purpose, crystalline NaOH was added to 100 ml of SAES. The resulting precipitate of titanium hydroxide was filtered and dried at a temperature of 200 °C to a constant weight. The sediment mass was used to determine the degree of titanium recovery from the SAES. The second stage consisted of electrochemical treatment of the filtrate obtained after the separation of titanium hydroxide in electrolyzers with ion-exchange membranes. Two types of electrolyzers were used for the research – without a flow and with the flow of solutions through the chambers.
The study of the distribution of components in the electrolyser chambers, the determination of the current yield and the specific energy consumption for the leachate processing process was carried out in a four-chamber membrane electrolyzer without the flow of solutions through the chambers (Fig.1).
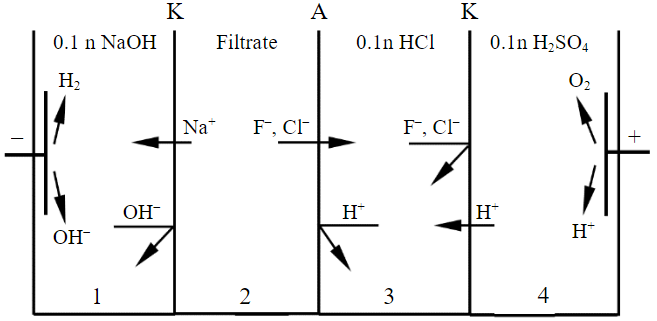
Fig.1. Diagram of a non-flowing electrolyzer for processing leachate obtained after removing titanium from the SAES
A – anion exchange; K – cation exchange membrane
The electrolyzer chambers with a diameter of 6 cm were made of plexiglass plates with a thickness of 2.5 cm. Membranes manufactured by Shchekinoazot OOO were used to separate the chambers: cation exchange membranes of the MK-40 brand, anion exchange membranes of the MA-40 brand. The working surface of each membrane separating the chambers was 14.1 cm2. The cathode material is a stainless steel plate, the anode material is a titanium plate coated with ruthenium oxide (ORTA). A 0.1 n sodium hydroxide solution was loaded into the cathode chamber of the 1st electrolyzer. The filtrate obtained after the extraction of titanium from the SAES was loaded into chamber 2. In chamber 3 – 0.1 n solution of hydrochloric acid. A 0.1 n solution of sulfuric acid was placed in the anode chamber 4. The volume of solutions loaded into all chambers of the electrolyzer was 60 ml.
In the process of treating the filtrate in an electrolysis cell (Fig.1), water decomposes on the cathode to form hydrogen gas and generate hydroxyl ions. At the anode, water decomposes with the release of gaseous oxygen and the generation of hydrogen ions. Sodium and hydrogen ions migrate to the cathode, and hydroxyl, fluorine, and chlorine ions migrate to the anode. The migration of hydrogen ions is hindered by the anion exchange membrane, and the migration of hydroxyl, fluorine, and chlorine ions is hindered by the cation exchange membrane. As a result, sodium hydroxide accumulates in the cathodic chamber 1 of the electrolyzer, and a mixture of hydrofluoric and hydrochloric acids accumulates in chamber 3 of the electrolyzer.
To determine the maximum concentrations of alkali and acid mixtures generated in the cathode and chamber 3 of the electrolyzer, a membrane electrolyzer with a flow of solutions in the chambers of the apparatus was used, schematically shown in Fig.2. The electrolyzer consisted of four cells separated by electrode plates. Each cell is divided into four chambers, which are separated from each other by cation exchange and anion exchange membranes. The working surface of each membrane was 30 cm2. Framed chambers were made of a polyvinyl chloride plate 2 mm thick. To prevent the membranes from sticking together, a mesh stretched from calendered vinyl was placed in each chamber. The entire structure was pulled into a single package by plexiglass plates.
The concentrations of solutions used in an electrolyser with flow chambers (Fig.2) are similar to the concentrations of solutions used in an electrolyser without their flow through the chambers of the apparatus (see Fig.1).
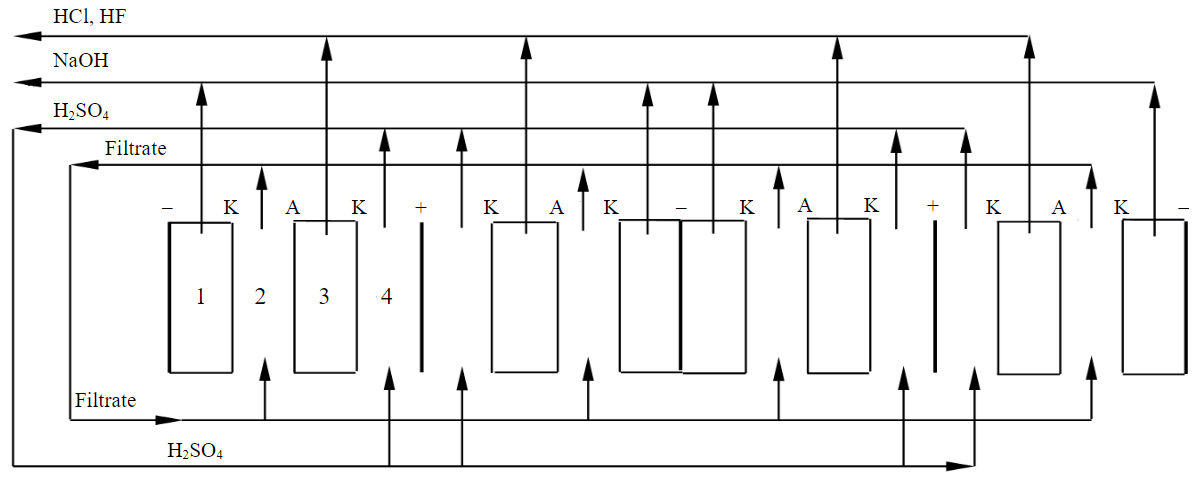
Fig.2. Diagram of a flow-through electrolyzer for processing leachate obtained after removing titanium from the SAES
In chamber 2 of the electrolyzer, filtrate circulated, in the anode chamber – a solution of sulfuric acid. The cathode chamber and chamber 3 are made without the flow of solutions and were pre-filled with 0.1 n solutions of sodium hydroxide and hydrochloric acid, respectively. Solutions of sodium hydroxide and mixtures of hydrofluoric and hydrochloric acids left their respective chambers as they accumulated.
The studies were carried out with a model solution containing titanium fluoride, hydrofluoric acid and hydrochloric acid. The studied solution was obtained by dissolving metallic titanium in a mixture of hydrofluoric and hydrochloric acids. For this purpose, 10 g of VT1-0 titanium was dissolved in 1 l of a mixture of hydrofluoric and hydrochloric acids containing 14.7 g/l of HF and 6.2 g/l of HCl. The composition of the resulting model SAES designed for titanium fluoride is 22 g/l, 0.21 mol/l; hydrofluoric acid – 1.7 g/l, 0.085 mol/l; hydrochloric acid – 6.2 g/l, 0.17 mol/l.
Results and discussion
The results of experiments on the extraction of titanium from the SAES by its treatment with sodium hydroxide are presented in Table 1.Treatment of SAES with sodium hydroxide leads to complete recovery of titanium when the pH of the filtrate reaches 7.6. The filtrate obtained after sedimentation and washing contained 0.92 mol/l of sodium fluoride and 0.17 mol/l of sodium chloride.
Table 1
Dependence of the degree of titanium recovery from the SAES on the mass of NaOH and pH of the filtrate
NaOH mass added to 100 ml of SAES, g |
2.4 |
2.6 |
2.8 |
3.0 |
3.2 |
3.4 |
36. |
3.8 |
4.0 |
4.2 |
рН |
3.75 |
5.5 |
6.45 |
7.2 |
7.6 |
7.8 |
9.4 |
9.85 |
10.6 |
12.8 |
Recovery rate, % |
85.4 |
89.8 |
96.5 |
98.1 |
99.6 |
100 |
99.8 |
100 |
100 |
100 |
To study the distribution of sodium, fluorine and chlorine ions in the electrolyser chambers, to determine the current yield and specific energy consumption for the process, an apparatus without the flow of solutions through the chambers was used (see Fig.1). The weight of the components in the electrolyser before the experiments, determined by a calculation based on the volume of solutions used and their concentration, was: sodium ions 0.138 g in chamber 1 and 1.504 g in chamber 2; fluorine ions 1.048 g in chamber 2; chlorine ions 0.362 g in chamber 2 and 0.213 g in chamber 3. The current density in the process of filtrate processing varied from 20 to 80 mA/cm2. The amount of electricity passed in all experiments remained constant and amounted to 1.2 A‧h. The distribution of sodium, fluorine and chlorine ions is shown in Table 2.
Table 2
Distribution of sodium, fluorine and chlorine ions in the electrolyser chambers
Current density, mA/cm2 |
Weight, g |
Violation of the material balance calculated |
|||||
Sodium |
Fluorine |
Chlorine |
|||||
Chamber 1 |
Chamber 2 |
Chamber 2 |
Chamber 3 |
Chamber 2 |
Chamber 3 |
||
20 |
0.955 |
0.687 |
0.606 |
0.422 |
0.233 |
0.312 |
5.2 |
40 |
0.929 |
0.713 |
0.593 |
0.455 |
0.228 |
0.311 |
6.3 |
60 |
0.987 |
0.655 |
0.590 |
0.458 |
0.237 |
0.324 |
3.8 |
80 |
0.967 |
0.675 |
0.602 |
0.446 |
0.235 |
0.329 |
5.7 |
Averages |
|||||||
|
0.964 |
0.683 |
0.598 |
0.450 |
0.233 |
0.319 |
|
In the process of electrolysis, sodium ions migrate to chamber 1 of the electrolyzer. In this chamber, sodium ions are concentrated to form hydroxide. In chambers 3 and 4, the presence of sodium ions was not detected. There is no dependence of the degree of extraction of sodium, fluorine and chlorine ions from chamber 2 on the membrane density of the current. This made it possible to determine the average values of the mass of ions in the electrolyser chambers and calculate the error in the results obtained. The calculation of the relative error according to the Student's distribution for a 95 % confidence level for all components varies from 2 % for fluorine ions in electrolyser chamber 2 to 5.6 % for sodium ions in the same chamber. The average recovery rate of sodium ions from chamber 2 was 79.8 %. Fluorine and chlorine ions migrate to the electrolyser chamber 3 and accumulate in it, forming hydrofluoric and hydrochloric acids. The presence of fluorine and chlorine ions in chambers 1 and 4 was not detected. The average recovery rate was 36.4 % fluorine ions and 35.6 % chlorine ions. Since the extraction of sodium ions from the filtrate was calculated by increasing the concentration of sodium hydroxide in chamber 1 of the electrolyzer, and the extraction of fluorine was calculated by increasing the concentration of hydrofluoric acid in chamber 3, it is not possible to calculate the violation of the material balance for these elements. In contrast, the content of chloride ions was determined in all chambers of the apparatus, which made it possible to calculate a violation of the material balance, which amounted to 3.8 to 6.3 %.
Table 3 shows the specific consumption of electrical energy for the leachate processing process and current yield. The data presented are calculated from the results obtained for the extraction of sodium from the filtrate.
Table 3
Current yield and specific energy consumption of the leachate processing process
Voltage, V |
Current density, mA/cm2 |
Current yield, % |
Electricity consumption |
|
W‧h/g |
W‧h/mol |
|||
1.97 |
20 |
79.3 |
2.36 |
65.67 |
4.12 |
40 |
76.8 |
4.94 |
145.41 |
7.06 |
60 |
82.4 |
8.47 |
228.97 |
12.14 |
80 |
80.5 |
14.89 |
413.67 |
The current yield (average value 79.8 %) is independent of current density. The consumption of electrical energy for the extraction of sodium fluoride and sodium chloride ions from the filtrate is determined by a membrane current density. An increase in the membrane current density is accompanied by a quite sharp increase in the electricity specific consumption for the process. For example, a change in the current density by 20 mA/cm2 in the range of 20-40 mA/cm2 is accompanied by an increase in energy consumption by 79 W·h/mol, and in the range of 60-80 mA/cm2 – by an increase in energy consumption of 185 W·h/mol, i.e. 2.3 times.
Studies on the processing of filtrate in a non-flowing four-chamber electrolyzer with cation exchange and anion exchange membranes indicate the possibility of obtaining solutions containing sodium hydroxide and a mixture of hydrofluoric and hydrochloric acids. To determine the maximum concentration of sodium hydroxide solutions and a mixture of hydrofluoric and hydrochloric acids, a series of experiments was carried out in an electrolyzer with flow-through chambers 2 and 4 (Fig.2). The filtrate treatment process was carried out until the concentration values of sodium hydro-xide and a mixture of hydrofluoric and hydrochloric acids generated in the electrolyzer ceased to change. The volume of solutions circulating in chambers 2 and 4 of the electrolyzer was 2 l each.
Figure 3 shows changes in the concentration of sodium hydroxide, hydrofluoric acid and hydrochloric acid over time at different current densities. The intensity of concentration of alkali and acids is determined by the current density and is maximum at the initial moment of time. Over the course of leachate processing time, the concentration rate decreases and then stops changing. The maximum concentration of substances generated in chambers 1 and 3 of the electrolyzer, achieved in the experiments, is determined by the amount of water transported with the corresponding ions through the ion-exchange membranes, and increases with an increase in current density. The values of the maximum concentrations of sodium hydroxide, hydrofluoric and hydrochloric acids are given in Table 4.
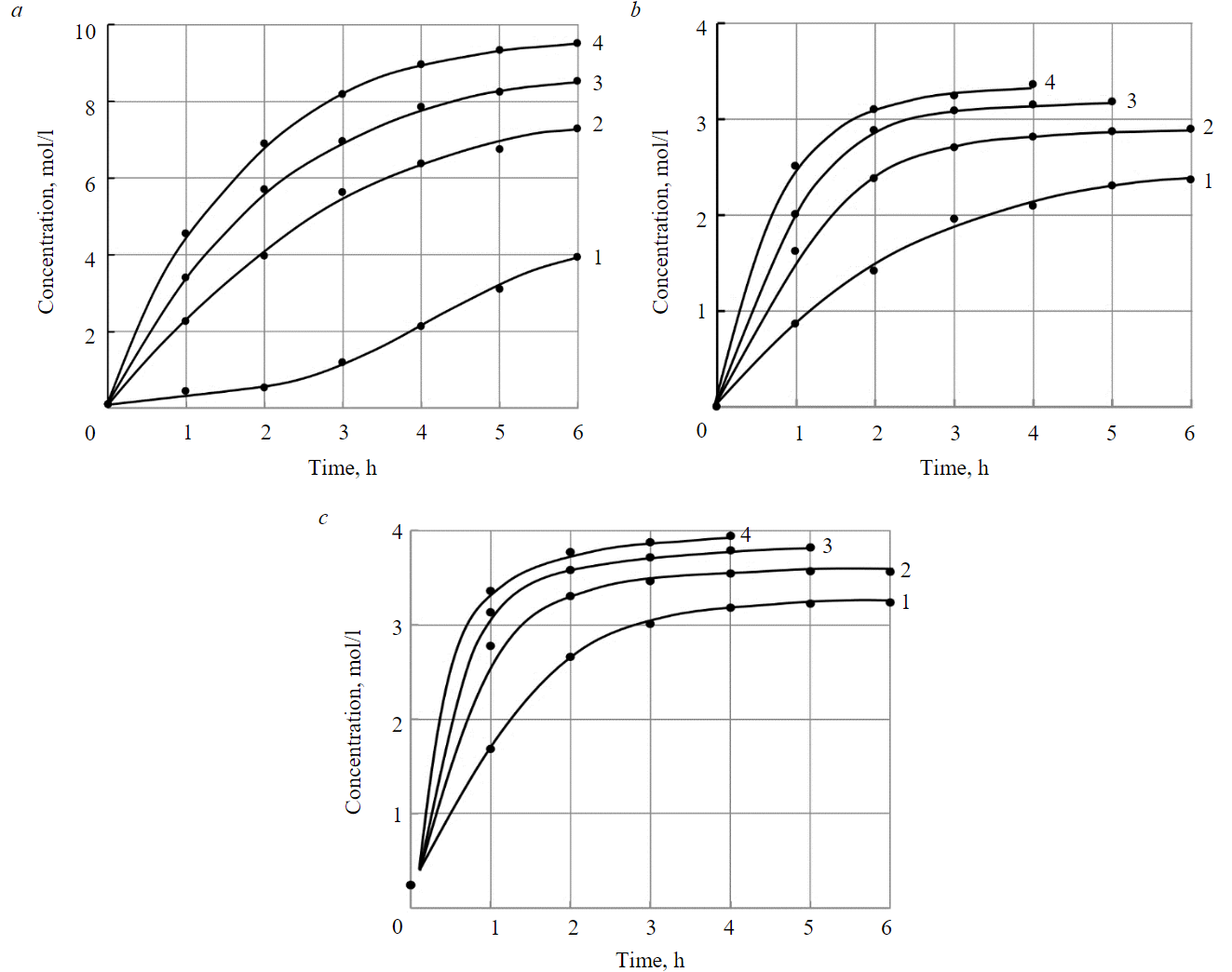
Fig.3. Changes in the concentration of sodium hydroxide (a), hydrofluoric acid (b), hydrochloric acid (c) over time at different current densities
1 – 20; 2 – 40; 3 – 60; 4 – 80 mA/cm2
Table 4
Maximum NaOH, HF and HCl concentrations achieved
Current density, mA/cm2 |
Sodium hydroxide |
Hydrofluoric acid |
Hydrochloric acid |
|||
g/l |
mol/l |
g/l |
mol/l |
g/l |
mol/l |
|
20 |
15.7 |
3.94 |
47.3 |
2.36 |
47.4 |
1.31 |
40 |
291.4 |
7.29 |
57.7 |
2.89 |
52.0 |
1.42 |
60 |
341.1 |
8.53 |
63.6 |
3.18 |
55.8 |
1.53 |
80 |
380.4 |
9.51 |
67.0 |
3.35 |
57.6 |
1.58 |
The change in the concentration of sodium hydroxide, hydrofluoric acid and hydrochloric acid in the concentration chambers of the electrolyser is determined by the mobility of sodium, fluorine and chlorine ions that create an electric current, the design parameters of the unit and is described by the equation
where Cnas is the limit concentration of these compounds; j – current density; S is the area of the ion-exchange membrane; q is a parameter depending on the mobility of ions and technological modes, determined experimentally for each of these compounds.
The solution of equation (1) has the form:
It follows from the ratio (2) that the change in the concentration of sodium hydroxide, hydrofluoric acid and hydrochloric acid in the concentration chambers of the electrolysis cell occurs according to an exponential law, depending on the parameter q, which coincides with the experimental curves (Fig.3). As follows from the above experimental studies, for sodium hydroxide Cnas = 380.4 g/l, q ≈ 4.06·103 C; hydrochloric acid Cnas = 57.6 g/l, q ≈ 2.84·103 C; hydrofluoric acid Cnas = 67.0 g/l, q ≈2.44·103 C.
The above ratios can be used in process design. The results obtained during the study of the process of processing of spent acid etching solution of titanium production, containing titanium, fluorine and chlorine ions, made it possible to propose an approximate technological scheme of processing (Fig.4).

Fig.4. Technological scheme for processing spent acid etching solution
Conclusion
The presented results obtained during the study of the process of SAES processing containing 22 g/l of titanium fluoride, 1.7 g/l of hydrofluoric acid and 6.2 g/l of hydrochloric acid without taking into account impurities in metallic titanium of the VT1-0 grade, allow us to draw the following conclusions.
SAES contains significant amounts of titanium fluoride, hydrofluoric acid and hydrochloric acid. Such a solution has increased toxicity and must be cleaned of impurities before being discharged into a water body. It is possible to process SAES to obtain substances used in production.
Treatment of SAES with sodium hydroxide to the pH of a solution of 7.6 makes it possible to completely recover titanium. After drying and calcining the sludge, titanium oxide can be used in the paint and varnish industry (titanium white). The filtrate after the separation of titanium hydroxide consists of a solution of fluoride and sodium chloride. Processing of this filtrate in a four-chamber electrolyzer with cation exchange and anion exchange membranes makes it possible to obtain solutions of sodium hydroxide and mixtures of hydrofluoric and hydrochloric acids. Sodium hydroxide can be used to treat SAES to extract titanium. A mixture of hydrofluoric and hydrochloric acids, after adjustment, can be used for etching the surface of titanium billets.
References
- Lysenko M.P., Tlekhusezh M.A. Titanium and its application in various industries. Scientific Review. Pedagogical science. 2019. N 4. Part 4, p. 64-67 (in Russian).
- Dyachenko A.N., Dyachenko E.N., Kraidenko R.I. Titanium dioxide: market, production, new technologies. Russian Coatings Journal. 2021. N 7-8, p. 41-50 (in Russian).
- Petrova T.A., Epishina A.D. Anti-corrosion protection of pipelines at mining and processing enterprises. Obogashchenie rud. 2023. N 6, p. 52-58 (in Russian). DOI: 10.17580/or.2023.06.09
- Soldatov V.G., Vavilin Ya.A.The use of titanium for the deoxidation of steel. Uralskii nauchnyi vestnik. 2019. Vol. 9. N 2, p. 17-21 (in Russian).
- Zeynalov E.B., Huseynov E.R., Salmanova N.I., Abdurahmanova N.A. Nano-grade titanium dioxide on the nanocarbon carrier as catalyst in aerobic oxidation of alkyl aromatic hydrocarbons. Chemical Problems. 2020. N 3 (18), p. 351-360. DOI: 10.32737/2221-8688-2020-3-351-360
- Trushin P.V. Application of finely granulated titanium nickelide in surgical practice. Medical News of North Caucasus. 2019. Vol. 14. N 3, p. 472-475. DOI: 10.14300/mnnc.2019.14114
- Marin E., Lanzutti A. Biomedical Applications of Titanium Alloys: A Comprehensive Review. Materials. 2024. Vol.17. Iss. 1. N 114. DOI: 10.3390/ma17010114
- Lakshmanan V.I., Roy R., Halim M.A. Innovative Process for the Production of Titanium Dioxide. Innovative Process Development in Metallurgical Industry. Cham: Springer, 2016, p. 359-383. DOI: 10.1007/978-3-319-21599-0_18
- Sadeghi M.H., Esfahany M.N. Development of a Safe and Environmentally Friendly Sulfate Process for the Production of Titanium Oxide. Industrial and Engineering Chemistry Research. 2022. Vol. 61. N 4, p. 1786-1796. DOI: 10.1021/acs.iecr.1c03364
- de Formanoir C., Suard M., Dendievel R. et al. Improving the mechanical efficiency of electron beam melted titanium lattice structures by chemical etching. Additive Manufacturing. 2016. Vol. 11, p. 71-76. DOI: 10.1016/j.addma.2016.05.001
- Liu Z., Tsai I.-L., Thompson G.E. et al. Chemical etching behaviour of titanium in bromine-methanol electrolyte. Materials Chemistry and Physics. 2015. Vol. 160, p. 329-336. DOI: 10.1016/j.matchemphys.2015.04.045
- Marin E., Diamanti M.V., Boffelli M. et al. Effect of etching on the composition and structure of anodic spark deposition films on titanium. Materials & Design. 2016. Vol. 108, p. 77-85. DOI: 10.1016/j.matdes.2016.06.088
- Cheremisina O.V., Sergeev V.V., Fedorov A.T., Alferova D.A. Separation of rare-earth metals and titanium in complex apatite concentrate processing. Obogashchenie rud. 2020. N 5, p. 30-34 (in Russian). DOI: 10.17580/or.2020.05.05
- Denisova O.V., Karapetyan K.G. Carbon materials surface modified with transition metal ions. Tsvetnye metally. 2023. N 8, p. 56-61 (in Russian). DOI: 10.17580/tsm.2023.08.10
- Kovalskaya K.V., Gorlanov E.S. Ligatures Al – Ti – B: Structure Formation in Modified Alloys. Tsvetnye metally. 2022. N 7, p. 57-64. DOI: 10.17580/tsm.2022.07.06
- Tyulagin P.E., Murashova N.M., Morozova Ya., Nasakina E.O. Etching of titanium with reverse microemulsions of sodium dodecylsulfate containing inorganic acids. Uspekhi v khimii i khimicheskoi tekhnologii. 2021. Vol. 35. N 9 (244), p. 53-55 (in Russian).
- Spitaels L., Rivière-LorphèvreÉ., Díaz M.C. et al.Surface finishing of EBM parts by (electro-) chemical etching. Procedia CIRP. 2022. Vol. 108, p. 112-117. DOI: 10.1016/j.procir.2022.03.023
- Motasim M., Aydoğan S., Agacayak T. et al. The influence of sodium fluoride on the dissolution kinetics of metallic titanium in citric acid solution using the rotating disc method. Hydrometallurgy. 2024. Vol. 226. N 106297. DOI: 10.1016/j.hydromet.2024.106297
- Cheremisina O.V., Ponomareva M.A., Molotilova A.Yu. et al. Sorption purification of acid storage facility water from iron and titanium on organic polymeric materials. Journal of Mining Institute. 2023. Vol. 264, p. 971-980. DOI: 10.31897/PMI.2023.28
- Kolomensky A.B., Shakhov S.V., Kolomensky B.A. Influence of gas-saturated layers and oxide films on the impact toughness of titanium alloys of different strength. Bulletin of Voronezh State Technical University. 2017. Vol. 13. N 2, p. 132-139 (in Russian).
- Shtefan V.V., Smirnova A.Y. Oxidation of titanium in Zr- and Mo-containing solutions. Protection of Metals and Physical Chemistry of Surfaces. 2017. Vol. 53. N 2, p. 322-328. DOI: 10.1134/S2070205117020241
- Lyubushkin T.G., Nosova T.I., Kuzin E.N. Influence of titanium-containing reagent addition on the coagulation process of galvanic wastewater. Uspekhi v khimii i khimicheskoi tekhnologii. 2021. Vol. 35. N 12 (247), p. 108-110 (in Russian).
- Bhattacharya S., Saha I., Mukhopadhyay A. et al. Role of nanotechnology in water treatment and purification: Potential applications and implications. International Journal of Chemical Science and Technology. 2013. Vol. 3. Iss. 3, p. 59-64.
- Kuzin E.N., Averina Yu.M., Kurbatov A.Yu., Cherednichenko A.G. Increasing the efficiency of wastewater treatment from galvanic production using titanium-containing coagulants and membrane treatment. Ecology and Industry of Russia. Vol. 28. N 3, p. 27-31 (in Russian). DOI: 10.18412/1816-0395-2024-3-27-31
- El Khalloufi M., Drevelle O., Soucy G. Titanium: An Overview of Resources and Production Methods. Minerals. 2021. Vol. 11. Iss. 12. N 1425. DOI: 10.3390/min11121425
- Karshyga Z., Ultarakova A., Lokhova N. et al. Processing of Titanium-Magnesium Production Waste. Journal of Ecological Engineering. 2022. Vol. 23. Iss. 7, p 215-225. DOI: 10.12911/22998993/150004
- Osipenko N.G., Kirjanov S.V., Rzjankin S.A., Teterin V.V. Patent N 2538900 RU. Treatment of effluents of titanium-magnesium production. Publ. 10.01.2015. Bul. N 1 (in Russian).
- Ismailov T.A., Shangereeva B.A., Shakhmaeva A.R., Kazalieva E. Patent N 2786369 RU. Method for treatment before spraying of titanium-germanium (Ti-Ge). Publ. 20.12.2022. Bul. N 35 (in Russian).
- Orlov A.P. Patent N 2758704 RU. Method for treatment of thin titanium sheets. Publ. 01.11.2021. Bul. N 31 (in Russian).
- Ivanova L.S., Makshakov V.V., Zadorozhnyj S.V. Patent N 2522061 RU. Method of producing anodes. Publ. 10.07.2014. Bul. N 19 (in Russian).
- Bykovskii N.A., Vinokurov E.G., Shulaev N.S. Experimental analysis of efficiency of electrochemical process of processing waste water for production of sodium bicarbonate with production of sodium hydroxide. ChemChemTech. 2021. V. 64. N 8, p. 139-145 (in Russian). DOI: 10.6060/ivkkt.20216408.6445
- Meshalkin V.P., Aristov V.M., Shulaev N.S., Bykovskii N.A. Physicochemical Foundations of an Energy and Resource Efficient Combined Technology for Processing of Soda Ash Production Wastewater. Doklady Chemistry. 2020. Vol. 494. Part 1, p. 145-148. DOI: 10.1134/S0012500820090025
- Bykovskii N.A., Puchkova L.N., Fanakova N.N. et al. Recycling the Wastewater in the Production of Ethylenediamine. Chemical and Petroleum Engineering. 2019. Vol. 54. Iss. 11-12, p. 787-794. DOI: 10.1007/s10556-019-00551-7