Modern approaches to barium ore benefication
- 1 — Ph.D. Head of Laboratory Trofimuk Institute of Petroleum Geology and Geophysics SB RAS; Scientific-Research Center “Ecology” SB RAS ▪ Orcid ▪ Elibrary ▪ Scopus ▪ ResearcherID
- 2 — Ph.D. Head of Department Tyumen Branch of SurgutNIPIneft, Surgutneftegas PJSC ▪ Orcid ▪ Elibrary ▪ Scopus
- 3 — Ph.D. Senior Researcher Trofimuk Institute of Petroleum Geology and Geophysics SB RAS ▪ Orcid
- 4 — Ph.D. Head of Center Trofimuk Institute of Petroleum Geology and Geophysics SB RAS ▪ Orcid ▪ Elibrary ▪ Scopus ▪ ResearcherID
- 5 — Ph.D. Leading Researcher Trofimuk Institute of Petroleum Geology and Geophysics SB RAS ▪ Orcid ▪ Elibrary ▪ Scopus ▪ ResearcherID
Abstract
Barite is one of the critically important minerals in several industries, including the fuel and energy, nuclear, and medical sectors. For decades, its extraction did not require any complex techniques; however, with the depletion of rich barite-bearing veins around the world, the circumstances have changed. While the demand for barite is growing widely, it is necessary to optimize and improve the existing methods for benefication of barite and barite-containing ores, and create new approaches to extracting this mineral, as well as develop technogenic barite deposits accumulated in large quantities during the previous ore production. Dumps and tailings often demonstrate high barite content, while new mining technologies make its extraction cost-efficient. Russian and foreign papers of the last 14 years provide data on the current state of primary and technogenic deposits, areas of barite use and the approaches employed for its benefication. Considering the expansion of the range of barite applications, the growing need for the mineral in the oil and gas industry and the difficulties in developing new barite deposits in Russia, the importance of new approaches to the enrichment of ore tailings in polymetallic deposits is revealed.
Funding The study was performed under IPGG SB RAS projects (N FWZZ-2022-0029, FWZZ-2022-0028).
Introduction
Barite ores include natural mineral formations containing barite in concentrations that would be sufficient for its cost-efficient and technically feasible extraction. This mineral is found in nature in various conditions: carbonatite massifs, sea bottom sediments, stratiform and vein deposits, residual weathering crusts or sedimentary deposits [1, 2]. Barium feldspars, micas and aluminosilicates are usually developed in metamorphosed rocks, barite-polymetallic and barite-pyrite ores. The chemical composition of barite has more than two thousand variations. Barite can be found predominantly in the form of granular, lamellar, radiate and columnar fibrous aggregates. The mineral matrix often contains Sr, Ca, Mn, Mg, Fe, Pb, Zn, Cu, Ag, Au and Hg [3].
In China and the USA, barite is entered in the list of critical raw products with high significance for economic development, which is explained by its multi-purpose usage and unique properties: high specific gravity and density (4.3-4.7 g/cm3), low hardness, weak chemical reactivity, whiteness, and ability to absorb ionizing radiation. Barite is actively used in the fuel and energy, nuclear, and medical industries.
When extracting barite, the final product is presented in lump (coarsely crushed), finely ground (powdered) and micronized forms or as a concentrate. Ground barite is used as a filler and weighting agent, lump barite is used as a raw material for the production of barium compounds. Barium concentrate is the most significant and expensive. Barite can be divided into two classes based on its granulometric composition. Class A, non-drilling barite has six subclasses (KB-1 through KB-6) and is used as a filler, barium-containing compound, or radioprotective material. Class B, drilling barite for drilling fluids is divided into KB-3, KB-5 and KB-6 and is used as a weighting agent. The highest consumption (60-80 %) accrues to class B barite.
World barite reserves currently amount to 1.5-2 billion tons, among which explored, pre-estimated and forecast reserves are distinguished. Explored sources account for 740 million tons, of which approximately half are proven. Based on an assessment of the length of the exploited wells, the construction of which is required for the vast majority of barite, the production and consumption of barite is significantly increasing throughout the world1, although declines are sometimes observed in certain regions [4]. By the early 2020s, global barite consumption was 8.2 million tons per year.
Barite has been explored in 60 countries all over the world, with up to 60 % of the most significant deposits located in Asia. China, India and Morocco are currently the leaders in production; barite is mainly exported by China, India, Morocco, Turkey, and Kazakhstan, and imported by the USA, Saudi Arabia, Canada, Kuwait, Norway, Germany, and Italy [5]. Although Russia is among the top ten countries in both production and consumption of barite, its global share is rather small covering less than 2 % of barite production in 2022.
In Russia, only class B barite is extracted with the average annual production in the last decade of 150-210 thousand tons, tending to increase. General requirements, however, exceed production and reach more than 300-500 thousand tons [6, 7], despite the fact that domestic production, at best, allows one to talk about the threshold of import dependence [5]. Class A barite is currently entirely imported [8], with almost half of all imports coming from Kazakhstan, followed by China and Turkey [5]. Russian barite is exported mainly to Belarus, and import to Russia is ten times higher than export [4]. By 2030, barite requirements in Russia may increase significantly by 2-4 times [4, 9]. The reserves of all known deposits may be exhausted: at the beginning of the 2020s they were estimated, according to various sources, at 12-22 million tons (of which more than 1.1 million tons are suitable for the extraction of class A barite [10]), then by 2030, with growing consumption, only a little over 2 million tons will remain [9]. By different estimates, the time for depletion of reserves varies from one year to 14 years. Therefore, it is reasonable to point out an acute shortage of this raw material, which makes important not only and not so much the exploration and discovery of new deposits as development of new promising methods for its extraction.
In recent decades, the general depletion of barite resources that do not require expensive and complex extraction [11], as well as a large number of dumps and tailings formed during the mining and processing of minerals, have led to the need to create new and improve previous approaches to barite extraction, including repeated processing of technogenic deposits. An analysis of the scientific literature shows a growing interest in modifying mineral extraction technologies by researchers and experts involved in the extraction and processing of barite. Consideration of tailings and dumps of mining and processing plants as promising sources of barite in the coming decades is consistent with the global trends in the extraction of minerals necessary for humans from technogenic deposits.
At the same time, the lack of papers summarizing Russian and international experience of recent years in the production of barite should be noted. Therefore, such a review becomes of particular importance, especially due to the constant expansion of barite applications and the high demand for this mineral in the fuel and energy industry. The purpose of the paper is to analyze modern approaches to barite extraction, including those from dumps and ore processing tailings, in Russia and abroad. We also present the results of scientometric analysis of various technologies; outline trends in technological development in the coming years; consider modern areas of barite use, and describe the current state of Russian deposits. The review material can be useful both to young experts in the metallurgical and processing industries, as well as to researchers developing barite extraction techniques.
Range of barite application
Class A barite is actively used in various industries where its different properties are exploited.
Barite as a filler is useful in the following industries due to its chemical inertness and low reactivity:
- paper, where paste-like barite white pigments based on blanc fix (chemically precipitated barium sulfate – high-grade barite, of 96-98 % whiteness) is used for bleaching glossy and matte paper, including photographic paper;
- rubber and plastic, where barite serves as a white mineral filler, for example, to manufacture linoleum or rubber;
- paint and varnish, where barite is in use for production of fire- and acid-resistant paints. To produce enamels, lithopone is also used – a pigment based on a mixture of barium sulfate and zinc sulfide, which is cheap and environmentally friendly;
- ceramic, where lithopone is used in enamel production;
- construction, where barite is part of barite-concrete mixtures and special cements, completely or partially replacing quartz sand. Such mixtures are used both in the construction of load-bearing/protective structures and as finishing materials. Barite reduces the impact of aggressive environments, for example, in the foundations of heavy structures such as pipelines (including subwater), road surfaces with high requirements for their quality (for example, at airports where durable and flexible top layer is required). Despite the susceptibility to shrinkage deformations and poor resistance to the cyclic influence of temperatures, a careful selection of mixtures containing barite allows to achieve the strength properties of standard concrete compositions [12];
- automobile, where barite is added to the materials for brake pads, sparking plugs or soundin-sulating composites of engines [13].
Barite as a barium-containing compound is the most expensive and demanding material in terms of quality, used primarily in the chemical industry for the following applications:
- medical, where chemical compounds of barium are used in the production of drugs, vitamins, hormones or blood coagulants;
- agricultural, where the toxic properties of barium salts (barium sulfate, barium carbonate, barium chloride, barium peroxide) from lump barite and barium concentrate are actively employed to prepare insecticides and exercise rodent control;
- glass, where barite is used for glass etching, in the production of electric vacuum and light bulb glass. Transparent variations of barite (optical barite) are used in the production of optical instruments including lenses and prisms;
- textile and leather, where barite is used as part of special impregnations – finishing agents;
- electrical engineering, where barite is used to prepare fire- and acid-resistant putties, as well as batteries;
- metallurgy;
- pyrotechnics.
Barite as a radio-, X-ray protective and environmentally friendly material is used in the following industries:
- nuclear, in the construction of nuclear reactors and waste storage facilities (final repositories), where mixtures and solutions that protect against γ- and neutron radiation are required [12, 14, 15]. In connection with the intensive advancement of the nuclear industry, the use of barite in the development of promising radio-protective construction materials is of increasing interest. Of note, barite is superior to many of those materials in terms of efficiency and low cost of production;
- medical, in the construction of special premises (tomography rooms, X-ray rooms), where special dry magnesium-barite mixtures are used, ensuring radiation safety with low-thickness fini-shing concrete or cement layer [16]. In addition to barite-based plaster, elastic self-adhesive materials are also used for radiation protection, successfully replacing lead sheets, known for their toxicity, and barite plaster [17]. Furthermore, barite is used as a radiopaque medium when examining the gastrointestinal tract for tumors.
Class B barite is produced by flotation (the most common in Russia) and gravity separation methods. It is used as a water-insoluble weighting agent for drilling and grouting fluids when drilling wells due to such properties as inertness, high density and low hardness (low abrasiveness and noneffect on the readings of electrical methods in comparison with ferrous weighting agents). Barite for drilling fluids accounts for 60 to 80 % of the total consumption of the mineral. This type of barite has been in active use since the late 1950s and is considered the most profitable [9]. In Russia, it is used extensively by such high-profile companies as Gazpromneft and Surgutneftegaz, and is represented in two industries, fuel and energy (oil and gas production) and geological exploration. In deep and ultra-deep drilling of oil and gas wells with abnormally high formation pressures, drilling fluids weighted with barite prevent solution aeration, collapses of the well walls and the influx of formation waters into the well by maintaining sufficient hydrostatic pressure of the liquid column [18-20]. The disadvantages of barite drilling fluids are associated primarily with the clogging ability of the barite filler when opening reservoirs with low filtration characteristics [21], as well as their sedimentation instability, which increases the likelihood of sticking of drilling tools [22].
It is important to note both the expanding scope of application of class A barite in various sectors of the national economy, and the increasing use of class B barite.
Geological types of barite deposits
Barite deposits can be divided into monomineral (9 %), where barite is the main and only useful element, and complex (91 %), where it is mined as a by-product. Based on mineral associations, barite and barite-containing types are distinguished. Barite type, where barite is the main ore-forming mineral, includes essentially barite, quartz-barite, calcite-barite and sand-clay-barite associations. The barite-containing type consists of barite-sulfide, barite-fluorite and barite-iron associations. By texture, barite ores can be divided into soft (coarse-grained and easily milled), and dense (fine-crystalline and difficult-to-mill).
The genesis of deposits has a strong influence on optimal geological exploration in terms of cost-reduction and the class of barite to be mined: with a content of over 80 %, class A barite is produced, with 80 % – class B barite. According to genesis, barite deposits are most often divided into the following types:
- Hydrothermal, the most abundant, when ore bodies are formed under the conditions of a hydrothermal process from medium- and low-temperature solutions. Additionally, they may contain other minerals and noble metals. Hydrothermal deposits may also include hydrothermal-metasomatic ones, formed either by the replacement of chemically active host rocks, or by recrystallization of ore, when the barite content in the ore increases [3].
- Sedimentary, stratiform sedimentary, stratiform volcanic-sedimentary, hydrothermal-sedimentary, are second most-widespread; but have the greatest industrial importance. Some researchers consider stratiform sedimentary and stratiform volcanogenic-sedimentary types as independent [5]. Historically, they are formed through sedimentation of ocean water components mixed with metal-bearing thermal waters of volcanic areas [3].
- Weathering, formed due to the destruction of barite-containing rocks and ores. Occurs mechanically or under the influence of chemical processes in weathering crusts, when the mechanical and mineralogical composition changes, the mass of rocks with barite is carried away by near-surface waters, and barite aggregates and grains are released from the minerals of the host rocks. As a result, up to 70 % of barite grade to a free state, i.e., the barite concentration increases significantly in comparison with the original rock [10, 23]. At the same time, the properties of barite are preserved during weathering processes. Such deposits are usually discovered incidentally, all Russian barite deposits of this type were discovered simultaneously during other geological explorations [10].
Geological and technological types of ores
According to geological and technological types, deposits are divided into the following:
- vein type, hydrothermal in genesis, they serve as the only raw material for the production of class A barite, since they demonstrate higher barium sulfate contents compared to other types. The width of ore veins, as a rule, is several meters; length is from tens to hundreds of meters; thickness is tens of centimeters. The downside of high quality vein barite is the difficulty of obtaining it due to the variable morphology of ore bodies. A significant part of deposits of this type is small. Barite from vein-type deposits is the only source for industries with high quality requirements;
- stratiform type, or strata, in siliceous-shale complexes, sedimentary in genesis, used for the production of class B barite. They extend up to two kilometers, with 3 to 15 m thickness. These deposits are the most widespread in the world and are cost-effective with relatively easy mining due to simple morphology of ore bodies;
- residual and alluvial (eluvial, deluvial and karst) type, formed akin to weathering; are considered as an alternative to vein-type deposits and can be used to extract class A barite. Despite the lower barite content in comparison with vein-type deposits, residual and alluvial deposits are cost-effective and easily extracted due to the simple morphology of ore bodies, surface bedding and the material composition of ores [7, 23]. These properties enable open mining and simple enrichment methods at relatively low costs.
In Russia, deposit development began in the 18th century [24]. Currently, more than 90 % of significant barite deposits are located in the south of Western Siberia (Khakassia, Tuva, Buryatia, the Altai Territory, the Kemerovo region) and in the Urals (the Chelyabinsk region, the Orenburg region, Komi, Bashkiria and the Yamal-Nenets Autonomous Okrug). In most of them it is possible to extract barite for drilling fluids. Class A barite is not mined, although deposits suitable for its extraction have been discovered in the Altai Mountains [8, 19] and Bashkiria [7, 23].
At the beginning of the 2020s, there were up to 20 deposits in Russia containing about 22 million tons of the mineral: 5 million tons of them were barite deposits (47 % of reserves) and 15 million tons were complex deposits (53 %). In most complex deposits, the quality of the ore is assessed as low or the size of the deposit is considered insignificant [4]. Seven deposits are of industrial importance: two barite-sulfide (1-2) and five barite-only deposits (3-7). Production is carried out at only two of them (6-7) in the Republic of Khakassia (where there are also other barite deposits of all three geological and industrial types [19]):
- Quartzite Sopka (Salair, the Kemerovo region), mining had been carried out since the 1930s, in recent years by Salair Chemical Plant, and was discontinued in 2014. The length of ore bodies is 650-700 m, thickness is 35-130 m. This deposit is suitable for further development, and reserves are estimated at 5.3 million tons [5, 25].
- Pervomaiskoe (Salair, the Kemerovo region), at the stage of preparation for opening. The length of the ore bodies is 16-180 m, thickness is 7-25 m, reserves – 300 thousand tons.
- Khoilinskoe (Komi), production was carried out in 1998-2009 by Khoilinskii Mining and Processing Plant. The length of ore bodies is from 400 m to 1.5 km, thickness is 3.5-6.4 m. Reserves are estimated at 6.8 million tons, of which 2.1 million tons are ready for industrial development, while resources – 9.2 million tons [4, 26, 27].
- Voishorskoe (the Yamal-Nenets Autonomous Okrug), at the stage of preparation for opening (AO Korporatsiya razvitiya). The length of the ore bodies is 50-320 m, thickness is 0.2-6.8 m. Reserves are estimated at 144-382 thousand tons, resources – 800 thousand tons [28, 29].
- Medvedevskoe (the Chelyabinsk region) was discovered in the 19th century, but no mining was carried out. It is the largest Russian deposit of the weathering type. The length is 3.2 km; thickness is 0.2-16 m. Reserves are estimated at 6.6 million tons.
- Tolcheinskoe (Khakassia), mining has been carried out since 1995 by AO Barit, barite concentrate is produced at OOO Bogradskii Mining and Processing Plant. The deposit consists of the Main ore body of a lens-shaped shape and a northern deposit, 1 km length, 4.6-10 m thickness. Over the years of operation, 2975 thousand tons of ore containing 1243 thousand tons of barite have been mined, and the remaining reserves of 1.2 million tons should be enough for another 3-8 years [5, 19].
- Kuten-Bulukskoe (Khakassia) has been developed since 2020 by OOO Khimtekh – Geologya. It produces 85 thousand tons of ore per year, containing 49 thousand tons of barite. The deposit consists of 11 accumulations with a length of 2 km and a thickness of 3.6 m. Forecast resources are estimated at 3.6 million tons, which should be enough for 11 years [5].
There are other promising deposits in Russia. Large forecast barite resources are located in the Far Eastern Federal District (the Magadan region, the Primorsk and Khabarovsk territories), the deposits of which can become an important raw material base for providing weighting material to drilling enterprises, taking into account the prospects for the development of the oil and gas industry in the Far East [9, 26]. Barite ores of the Murmansk region are considered an important source of barite for the development of Arctic hydrocarbon deposits (Sallanlatva) with ore reserves of 13 million tons of barite and resources of 160 million tons [20, 28]. Among the submarine hydrotherms, economically significant massive barite mineralization (Barite Hills) was discovered in the 1980s in the Deryugina depression of the Sea of Okhotsk near the northern tip of Sakhalin Island [30, 31]. Since the 1970s, barite concentrations have been known in the Sea of Japan [32]. Barite was also found in the deposits of the Middle and Southern Urals at the Safyanovskoe deposit [33]; in the Perm region, where barite is of minor significance and is included in celestine intergrowths [34]; in Tuva at the Karasug ore field [1]; and in Buryatia at the Khalyutinskoe and Gunduiskoe fields [1, 4].
Despite the abundance of barite deposits in Russia, its production is difficult for many regions, for example, due to harsh mining and geological conditions (in the North Caucasus), lack of production infrastructure (in Yakutia or the Krasnoyarsk Territory), insufficient geological descriptions of mineral deposits (in the Arctic zone of Russia), etc. [5, 28]. Thus, with the general depletion of highly profitable barite deposits both in Russia and abroad, accompanied with growing production needs for barite of both classes, it becomes increasingly more difficult and expensive to obtain high-quality barite concentrates. Therefore, processing technogenic deposits becomes important for the following reasons:
- many technogenic deposits are rich with barite content (15-30 %), which significantly expands the resource base of this mineral;
- barite-containing wastes do not require extraction from the subsoil and grinding, which significantly reduces the cost of obtaining a barite product;
- the important task of eliminating or reducing the area of tailings dumps, which negatively affect the environment and create risks for public health, is being solved, since barite-containing technogenic wastes are a source of soil, air and water pollution with heavy metals and barite dust [35 , 36];
- in Russia, secondary development of tailings dumps in the short term appears to be extremely important in terms of import substitution and increasing the volume of domestic barite concentrate.
Extracting barite from tailings is becoming essential for increasing the ore mining efficiency and reducing the anthropogenic load on the environment. In Russia, promising objects of interest are, for example, dumps in Ursk, the Kemerovo region. The waste storage facility was formed in the 1930s after extracting gold by cyanidation from the oxidation zone of the Novo-Urskoe pyrite deposit, discovered in 1932 as part of the Urskoe ore field and comprised of the Novo-Urskoe, Beloklyuchevskoe, Samoilovskoe deposits, and several ore occurrences. Polymetallic deposits of the Ur group are confined to a complex of metamorphic formations, the primary composition of which is difficult to determine precisely [37]. Within the deposit, 11 ore bodies containing industrial ores were identified and explored [38]. Numerous researchers studied and described their structure, morphology, material composition, sequence of mineral formation, and mining history [39, 40]. In accordance with the soil survey report of the state geological map, the mining dumps of the Novo-Urskoye deposit are technogenic deposits of barite [41], the total reserves of technogenic raw materials are 700 thousand tons with a barite content of 15-30 wt.%. The predicted production volume of barite concentrate for the entire period of development of the tailing is about 180 thousand tons, the annual production level of barite concentrate is 20 thousand tons [42, 43].
The stored wastes from the enrichment of barite-polymetallic ores from the Salair ore field are also promising for the development [44]. Particularly, the barite content in the stored wastes of the Talmovskie sands tailings is estimated at 9 %, its horizons are represented by medium and small grains of 100-300 μm, as well as fine grains forming interlayers and cemented aggregates [45]. Technogenic barite deposits of interest also include the Zarechenskoe deposit in the Altai Territory [24]; the processing plants of the Kyzyl-Tashtyg deposit in the Republic of Tyva; the dumps of substandard barite ores from the Khoylinskii Mining and Processing Plant in the Komi Republic; technogenic wastes from the enrichment of the Uchalinskii mining and processing plant in the Chelyabinsk region [46], etc.
Much attention is paid to ore processing storage facilities in other countries that also observe depletion of natural deposits as well as high energy costs for barite extraction and the negative impact of tailings on the environment [47, 48].
Materials and methods
Current approaches to obtaining barite are described, including those often used in the development of tailings ponds.
The review used the publications of Russian and foreign experts for 2010-2024, indexed in the following databases:
- VINITI abstract services: databases “Geography”, “Geology”, “Geophysics”, “Mining”, “Chemistry” and “Environmental Protection” (viniti.ru/products/abstract-journal);
- Scientific Electronic Library bibliographic database (elibrary.ru);
- American Chemical Society SciFinder-n database (scifinder-n.cas.org);
- Scopus bibliographic database by Elsevier (scopus.com);
- Derwent Innovations Index patent database by Clarivate (clarivate.libguides.com/webofscienceplatform/dii).
Additionally, the reference lists of the papers selected for the review were analyzed. In total, more than 180 scientific articles and reviews were studied. The papers most relevant to the analyzed topic were included in this review.
Technologies for benefication of barite and barite-containing ores
Barite recovery methods depend on the type of deposit and, accordingly, its initial share in the ore. The processing of barite ores is the least costly, but such ores are steadily decreasing in the world. On the contrary, barite-polymetallic and technogenic deposits require more complex methods due to the low share of barite extraction into concentrate. The high cleavage of barite with other components has led to an abundance of various methods for the extraction, concentration and purification of barite and their permanent improvement based of the latest knowledge and technologies. The choice of one or other approach largely depends on the mineralogical composition and structure of the ore of polymetallic and technogenic deposits, the size of barite inclusions, the established requirements for the quality of the final product, etc.
When extracting barite and obtaining the most valuable barite concentrate the experts are mainly guided by GOST 4682-84 “Barite concentrate. Specifications”. In relation to barite for drilling liquids, many countries follow the regulatory requirements of the American Petroleum Institute (API), ISO 13500:2008 “Petroleum and natural gas industries – Drilling fluid materials – Specifications and tests”. In Russia, GOST R 56946-2016 “Oil and Gas Industry. Drilling Mud Materials” applies. Due to the exhaustion of global reserves of easily mined barite, the criteria for its quality are periodically revised. In particular, lower-density barite-poor raw materials are involved in processing, and preservation of the previous quality of the concentrate is compensated by increased requirements to its other characteristics, for example, to narrower fractionation of grain size composition [11], and extraction methods are complicated, improved and optimized.
Any barite production method begins with a washing step. Since barite is often mixed with clay and sand rocks, the properties of mechanical heterogeneity of components and water permeability of clays are exploited to disintegrate it. At the washing stages of disintegration (grinding to 25-100 mm), screening and classification, barite raw materials are separated from thin classes with working units of various machines (ball mills, etc.) that grind the rock under the influence of water and air. In rare cases, washing is sufficient to obtain barite of the desired quality.
Washing is used for coarse-grained ores, and when extracting barite from polymetallic and technogenic deposits, mechanical, chemical, and thermal benefication is used. Benefication is based on various barite properties, i.e., its flotation activity, high specific gravity, chemical inertness, weak magnetic ability, or reaction to heating. The two most common mechanical methods are flotation and gravity enrichment. More specific approaches include electromagnetic and radiometric separation, chemical bleaching, decripitation, and recovery in hydrocyclones.
Mechanical (physical) methods
Flotation
Flotation has been known since the 1930s, a detailed overview, stages of development of this approach and the equipment used are described in [49]. Often, barite flotation is only one of the stages of flotation benefication of polymetallic ores when extracting lead, copper, zinc, silver, etc. Therefore, it is used only in barite-polymetallic deposits, which account for up to a quarter of world barite production. It is mainly employed in the treatment of fine barite ores that cannot be separated by other methods. As a result of flotation, it is possible to obtain a high-quality barite concentrate suitable for the chemical industry.
The flotation method is based on the difference in the surface properties of the components present in the ore or its processing tailings. Barite belongs to well-floated minerals and is easily separated from rocks or tailings. For the purpose, flotation reagents (collectors) can be added to it, which affect the surface of the barite particles. As a result, barite is trapped by air bubbles and rises to the surface as foam, while other components remain at the bottom.
An inverse scheme can also be used, when reagents (depressors) suppress the flotation properties of barite, as a result it precipitates, and other components of the material float [50]. Both procedures can be applied to increase the efficiency of flotation while collectors are added to some components of the initial material, and depressors to others.
Generalized process of barite flotation from tailings includes the following stages:
- Crushing of tailings obtained after extraction of barite from ore or after other stages of benefication, as a result of which a fraction suitable for flotation is created. For example, cone or jaw crushers are used in the crushing process. At this stage, an important task is to select the optimal size of crushing, since under some conditions a decrease in the size of the material leads to an increase in the concentration of barite [20], while after reaching a certain threshold, the content of barite in the crushed material, on the contrary, may decrease.
- Classification, when the resulting fine ore passes through screens that divide the material into different fractions depending on particle size. Barite is concentrated on the lower screen with small cells, and after sieving it enters the tray, from where it comes for grinding. The empty rock at the top of the screen is sent to the dump.
- Additional grinding in various types of mills including rod, ball, jet, drum or centrifugal. The initial material is ground into a fine fraction to facilitate subsequent processing. Dry and wet grinding are used.
- Preparation of barite ore pulp when ground tailings are mixed with water. At this stage, the mode of water treatment and pulp softening, and the establishment of the desired acidity (pH) of the pulp are important [51].
- Addition of modifiers, foaming agents and barite collectors to the pulp. Modifiers include sodium sulfide or cyanide, zinc and copper sulfate, liquid glass (with the addition of sodium polyaluminosilicate to reduce the consumption of liquid glass). Collectors preferably represented by flotation reagents, which include the most commonly used oleic acid, citric acid, industrial (sulfate) soap, liquid glass, tall (mixed with kerosene) or pine oil, asidol, alkyl sulfates, alkyl sulfonates, soda ash, lime, baritol, ditalan, lauryl phosphate, VS-2 collectors, VS-4, DNS-VN, S-3, etc.
Dextrin, starch, chromic peak, permanganate, iodates, chloride, barium, sodium hexametaphosphate, gellan gum, etc. are used in reverse flotation with suppression of the flotation properties of barite leading to its precipitation.
In recent years, conceptually new approaches from biotechnology have been introduced. Microorganisms and their metabolic products are used to enrich ores that are poor in mineral content. Similar to traditional reagents, different properties of microorganisms (acidity, hydrophobicity, surface charge) are used to enhance foam formation, as collectors or agents for suppressing flotation properties, as well as modifiers [52, 53]. By microbial adsorption and redox reactions, microorganisms change the physicochemical properties of mineral surfaces, separating valuable minerals from waste rock.
In the past few years, microorganisms have been increasingly used in the flotation of various minerals and it often turns out to be a cheaper alternative to traditional reagents. The environmental friendliness of microorganism enrichment is higher due to a lower level of production waste and increased efficiency, and with microorganisms resistant to salt, acids and alkalis, prospects are outlined for the use of seawater and wastewater in the flotation process, which also makes production more environmentally friendly [54].
In barite flotation, microbial cells and their metabolites (proteins and polysaccharides) are used, which impact the mineral changing its surface properties like reagents, as a result of which the necessary characteristics for bioflotation or barite biodepression are achieved [55]. All these reagents, including biological reagents, are used both separately and in different combinations. Particular attention is paid to the optimal ratio of density of the collector/depressor sorption forms depending on the composition of the initial material and the specified parameters of the final product.
- Flotation which includes the mixing of material in various flotation chambers (for example, in a flotation column), when air or other gas is continuously supplied to the pulp, creating foam. Hydrophobic barite particles due to physically sorbed collector molecules adhere to foam bubbles and rise to the surface. Thus, barite is separated from the rest of the rocks and tailings. Often sulfide materials (for example, sphalerite or galena) undergo flotation, after which barite is simultaneously extracted from the tailings of sulfide flotation. Therefore, this step may involve several additional stripping steps after the main flotation and is completed by the control flotation.
The material can be preheated by microwave radiation, which increases the specific surface area of barite [56], to improve flotation properties. Ultrasound can also be used at this stage, which showed the following results in experiments:
- improved foaming, which enhances the selectivity effect (although the efficiency of flotation production of barite with and without ultrasound was significantly less pronounced in comparison with the other types of ores) [57];
- increased oil agglomeration of barite with an increased wetting angle, thus improved hydrophobicity of barite surface [58].
It is important to select the optimal ultrasound power.
- Cleaning, i.e., separation of concentrate from flotation reagents, for example, on a vibrating screen, its washing with appropriate solutions.
- Drying and calcination of barite is the final stage of flotation to improve the quality of barite concentrate and achieve the necessary characteristics.
The technologies, the set of flotation reagents and the number of flotation steps may vary depending on the characteristics of the starting material, technical requirements and other conditions.
The disadvantages of flotation are primarily due to the use of the flotation reagents, which often are expensive, toxic (since many of them do not decompose [55]), and are also difficult to remove from the barite product obtained during flotation. The level of water-soluble salts and other fine fractions in the final product often exceeds acceptable values [20]. Although the removal of foreign impurities and reagent residues is inherent in the flotation scheme, in practice it turns out to be difficult and costly [59]. Residual flotation agents impair the wetting of barite in the mud and cause its foaming. In turn, increased air saturation (aeration) of the solution reduces the weighting capacity, increases viscosity and worsens washing of wells. Flotation benefication of barite is not always effective in the presence of components with similar flotation properties in the initial material: calcite, dolomite, quartz, and limestone.
Despite these disadvantages, the flotation method has a long history and a significant technological groundwork, the design of its technological scheme is being improved, first in the laboratory and then in the industry [48, 58]. New collectors and depressors are constantly being sought to improve flotation efficiency [60-62]. Much attention is paid to the search for affordable, highly efficient and selective reagents with low toxicity achieved by minimizing their use [48, 51, 63]. Therefore, in barite-polymetallic deposits, flotation remains one of the most common methods for extracting barite.
The flotation method continues to be actively employed in various countries in the development of both primary and technogenic deposits. In the last decade, the flotation mining method at technogenic deposits has been used, for example, at tailings dams in India for separation from quartz [59], at barite-polymetallic mines in Kazakhstan [64]; based on the results of laboratory studies its use at tailing dumps in Algeria are considered [65].
Gravity separation
The method of gravity separation, or gravitational benefication, for separating mineral complexes relies on the differences in contrast properties, in particular, the difference in density between barite and other minerals. The method is used for medium-grained ores, allowing to concentrate small fractions at a relatively low cost. As barite has high density, 1.5 times higher than the density of associated minerals, it can be separated by gravity when heavy barite particles move to the lower part of the device, while light minerals remain on the surface.
The main stages of gravity separation of barite include as follows:
- Crushing.
- Classification.
- Gravity separation based on differences in material densities. On gravitational equipment, the ore is subjected to gravitational forces separating barite from less dense components. The lifting power of water jet force large and heavy barite grains to accumulate in the tail of a table.
- Cleaning, which is an important step in washing the resulting concentrate, for example, from clay particles that impair rheological properties. The purpose of this step is to achieve the specified purity and quality of the concentrate.
- Drying, during which excess moisture is removed from the enriched barite.
Similar to the flotation method, it is important to optimally select the crushing time during gravity separation, as well as tune the gravity equipment adjusting vibration intensity (pulsation frequency) and amplitude, set the rate of stratification and transportation of particles, determine the required water flow rate, compressed air pressure, drum angle, etc. [20]. The concentration of barite content in the resulting product, as well as the scope of losses that escape to the tailings, largely depends on these criteria.
The disadvantages of gravity separation of barite include the difficulty of tuning the equipment and especially periodic reconfiguration for material with different initial content of barite, which often requires a complete shutdown. In addition, the final product may contain minerals with similar density, particularly, siderite, magnetite and sulfides, which prove difficult to separate by this method.
At the same time, gravity separation is devoid of the disadvantages of flotation. The barite weighting agent obtained through gravity separation does not have residual flotation reagents, water-soluble salts, and demonstrate an optimal particle size distribution; it is less consumed in the composition of drilling muds and provides higher density. It is also cheaper. The method is widely known in Russia [20] and abroad.
Hydrocyclones are technological cylindrical devices with a conical base, in which, under the influence of a rotating flow of liquids and centrifugal force, materials with different sizes and densities are separated. With regard to barite, the method undergoes experimental testing both at the level of microbarite [66] and separating barite from other components of tailings [67], as well as at extracting barite from spent drilling muds [68]. The barite recovery process with hydrocyclones typically involves the following steps:
- crushing;
- classification, where materials pass through hydrocyclones driven by piston pumps and are deposited centrifugally on the walls of the device;
- washing, where larger particles sent for repeated crushing and processing are removed, while small particles containing barite are collected in separate compartments;
- separating barite from water or other materials, for example, by filtration or centrifugation.
As with other barite processes, tuning is important in hydrocyclones. Thus, elevating the pressure in a hydrocyclone, optimizing the temperature regime, etc. can increase the efficiency of the procedure. Hydrocyclone advantages are easy operation and classification efficiency, including pellet size. Centrifuge enrichment is effective primarily for fine fractions of high-gravity minerals. With regard to relatively light and cheap barite, hydrocyclones can only slightly increase its yield. In addition, experts note extremely high-energy costs, which significantly reduces the economic feasibility of using hydrocyclones in the barite benefication.
Electromagnetic separation
Electromagnetic separation (magnetic separation, magnetic benefication) is widely used to enrich barite in the separation of minerals with magnetic susceptibility in tailings. Since barite does not possess magnetic properties, this method can be effective for its separation from other minerals from mixed ores, especially with a similar density, when gravity separation is useless. It is suitable for barite rocks containing quartz, iron impurities, and is effective for separating barite from hematite and magnetite.
The barite magnetic separation process includes the following steps:
- Crushing.
- Heating to 200-700 °C for ore pretreatment, creating the necessary differences in the conductivity of the components of the initial material. In some cases, various chemical reagents and powdered substances with a given conductivity are used that are adsorbed by the components of the material. In particular, oleic acid and graphite dust adsorbed by barite particles increase the conductivity of barite and facilitate its separation from quartz.
- Electromagnetic separation, when mixed material, passing through magnetic separators at a temperature of 93-240 °C, is exposed to magnetic fields. In this case, magnetic minerals are attracted and separated from non-magnetic particles containing barite. Separation of magnetic and non-magnetic fractions can take place in several stages.
- Classification, for example, on a sieve, pneumatic or magnetic separator, which may be required to further separate barite from the remaining minerals.
As with other barite recovery methods, the efficiency of magnetic separation depends on the type of ore and its composition, the settings of the magnetic separators, for example, magnetic field strength, and other parameters.
The disadvantages of the method include high electricity consumption, especially at the stage of preliminary ore processing, which can entail significant economic costs. In addition, some other minerals, such as hematite or magnetite, can be separated along with barite. In such a case, it may be necessary to use additional technologies to further separate and obtain pure barite. The method is used in technogenic fields of Slovakia [69].
Chemical bleaching
This chemical method (also known as flocculation) is based on special chemical reagents used instead of mechanical opening of raw materials to agglomerate small barite particles into large globules, which simplifies their separation from the rest of the tailings. As a result, ground bleached barite is obtained. The technology should be considered as qualitative modification of the barite product rather than benefication. The method includes the following steps:
- In the crushing step, the barite ore is crushed to produce particles of the necessary size. This is required to increase the contact surface between the reagents and the ore.
- The ground ore is placed in large containers of water with added chemicals such as sulfuric, hydrochloric or nitric acids (15-20 % by weight of barite powder). Upon that, large aggregates of barite particles are formed, connected to each other as clumps larger and heavier than empty rock. Under the influence of gravity, they settle to the bottom of containers and can be separated from other minerals.
- Stages of multiple (up to 10 times) washing, dehydration and drying of the leached product, and subsequently the barite concentrate is separated from the remaining moisture and reagents, the presence of which is not allowed in the final product.
- From the obtained ground bleached barite, it is also possible to obtain an even higher quality product microbarite. It requires additional grinding in jet mills and acid treatment.
Thermal decripitation
Decripitation is a method of thermal benefication based on the heterogeneous thermal properties of the mineral and various consequences of thermal exposure to barite and empty rock. During decripitation, certain minerals are selectively destroyed under the influence of heating or the “heating – rapid cooling” cycle: the water contained in the minerals, when heated to 400-450 °C, leads to their cracking due to pressure. Minerals are destroyed along cleavage planes, or the links between minerals are significantly weakened. During decripitation, barite cracks and turns into a powder, while the accompanying minerals remain in their original state. The scheme is implemented in three stages:
- heating ore in a tube furnace;
- classification on a sieve, where the empty upper rock goes to the dump, and the lower goes to further processing;
- final sorting of barite on thin sieves.
Thermal decripitation has been known since the 1930s, it is used mainly for fine ores. Large process losses are frequent due to incomplete separation of thin material. Decripitation is effective in thermal dehydration of barite raw materials when it is processed into bleached microbarite, which should be considered modification rather than benefication. In Russia, it is not used in the industry.
Radiometric separation
The method implies large-scale separation for preliminary benefication and is based on the ability of minerals to emit, absorb or reflect various radiation [70], mainly X-ray radiometric separation is used. The stages include crushing, screening, and washing of the class and the radiometric separation.
When considering the technological parameters of radiometric separation, the task of separating barite from silicate rocks is successfully solved. The ore varies in color from white to yellow and green to brown with a material size of –16 + 9 mm. Two-stage benefication is carried out with Sortex 621 M (a photometric belt-type separator with a vibrating feeder manufactured by Gunson’s Sortex Ltd.). The intensity of reflected light is measured under free fall of mineral pieces. The sorting mechanism includes a pneumatic valve. For material with a size of 20 mm, the response frequency reaches 200-250 Hz, and for smaller material – 400-600 Hz. First, white barite concentrate (BaSO4 content is 95.2 %) is released, then brown barite concentrate (BaSO4 content is 91.1 %).
X-ray radiometric separation (based on measuring the energy of characteristic radiation from irradiating a substance with X-ray or γ-radiation) was used on barite ores of the Sobskoe deposit; the released BaO concentrate contained 93.1 % of the useful component.
It is possible to use the near-infrared method (determine the difference in the interaction of electromagnetic radiation in the near infrared range with molecules of the material surface) to separate barite and fluorite from calcite and dolomite [71].
In order to identify the demand for and prevalence of barite extraction approaches, a scientometric analysis was carried out on a full sample of reviewed papers, as well as patents from the Derwent Innovations Index database (see Figure). Flotation demonstrates the greatest interest at the global level. At the same time, it is important to note that flotation is applied mainly to polymetallic ores, where barit extraction is secondary and gives less than a quarter of the world mineral production. Gravity, electromagnetic separation and chemical bleaching are leading in barite and technogenic deposits; and patenting of the obtained results is noticeably prevailing in electromagnetic separation and chemical bleaching compared to research articles. This indicates the maturity of these technologies, when the volume of scientific research, reflected in journal articles, is declining and is replaced by registrable technological know-how published in patent documents. To a certain extent, the interest in the hydrocyclone method for barite production is increasing, although experts note its applicability mainly to fine fractions of the mineral, as well as high energy costs. The least interest in the last decade is observed in thermal decripitation and radiometric methods, for which there are no patents, and the number of research papers is low.
Most of the described methods are complementary and can be used jointly. Combined methods include magnetic flotation, roasting ore followed by magnetic separation, magnetic separation together with chemical bleaching, chemical bleaching with decripitation, etc. Also, some methods can be part of a technological chain of other approaches; it is especially characteristic of chemical methods that constitute an integral part of many other methods. In addition, in recent years, complex mathematical models have been increasingly used in each approach, including those based on neural networks that have become popular. They help determine the content of barite in the initial material, the degree of possible extraction of the mineral, calculate the optimal conditions in tuning the equipment [48], calculate the necessary benefication parameters for both barite and the products obtained with its participation, for example, concrete solutions [72].
The described methods of barite extraction are used to varying degrees in the regions of the world by companies for the extraction and production of class A and B barite (see Table).
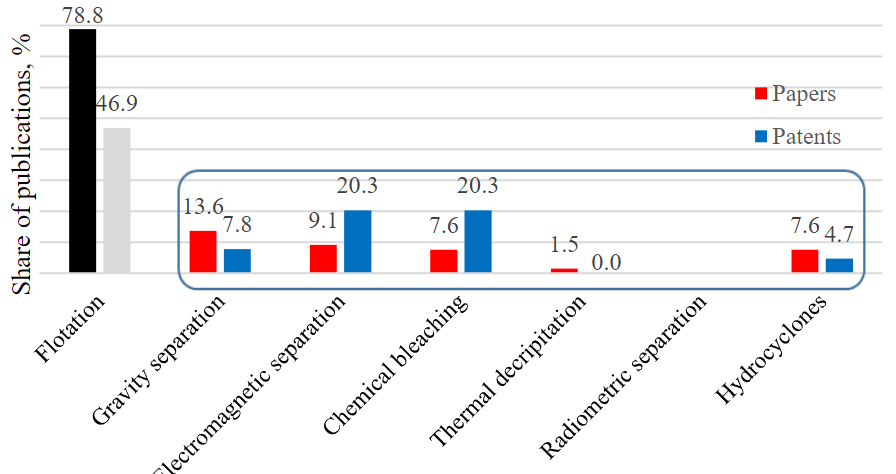
Distribution of the prevalence of barite benefication approaches in scientific papers and patents for 2010-2024. Some publications describe two or more approaches, so they are included simultaneously in several groups
The most productive countries, regions and companies in the barite industry
Country |
Barite extraction regions |
Barite Mining and Production Companies |
India |
Andhra Pradesh (Mangampet village) and Rajasthan |
20 Microns (20microns.com); Chemi Enterprises (chemienterprises.in); Finokoats & Colours (finokoats.com); Gayatri Microns (gayatrimicrons.com); Girikandra Trading Company (girikandra.net); Golden Micro Chemicals (goldenmicrochemicals.in); Satya Laxmi Mud-Chem PVT (slmpl.com) |
Kazakhstan |
Zhambyl, Karaganda, Mangistau, Turkestan Regions |
Dostau Litas (baritkz.kz);Global Chemicals Company (gcc.kz); Global Chemicals Industries / Karazhal Operating (gcind.kz) |
China |
Gansu, Guangzhou,Guizhou, Fujian, Hubei, Hunan, Shaanxi Provinces, Guangxi Zhuang Autonomous Region |
Dalian Huanqiu Minerals (hq-minerals.com); GuiZhou Saboman (www.chinabarite.cc); Handan Tianmu Chemicals (tianmuchem.guidechem.com); Majiang JGL Barite Mine (yuensons.lookchem.com) |
Morocco |
Drâa-Tafilalet, Casablanca-Settat |
Ado Barite Morocco (adomorocco.csglobal.com.tr); Bastion Industries (bastiongroup.net); Mounir Negoce (mounirnegoce.com); Terra Nova Minerals (terra-nova.ma) |
Nigeria |
Adamawa, Benue, Gombe States,Zamfara, Cross River, Nasarawa, Plateau, Taraba, Ebonai |
Breitz Group (breitzgroup.co); Helicon Group (heli-ng.com); PolyGuard Investment Nigeria (polyguardinvestmentng.com) |
Pakistan |
Balochistan (Daddar districts, Las Bela) and Khyber Pakhtunkhwa (Hazara District) |
Pakistan Mineral Development Corporation (pmdc.gov.pk); Pakistan Minerals Company (pakistanmineralscompany.com) |
Turkey |
Konya, Malatya, Sivas, Isparta |
Barit Maden Turk (baritmaden.com); Baser Mining (basermining.com);Deep Drilling Chemicals (ddc-ltd.com); Efe Baryt Mining (efemaden.com.tr); Gulmer Madencilik (gulmercapricorn.com); Meta Global Madencilik (metaglobalchem.com) |
Conclusion
An analysis of the modern literature on barite ore benefication revealed significant and increasing importance of this mineral for a variety of industries. Despite the repeatedly announced transition to a green economy, the fuel and energy complex is still the paramount consumer of barite required for the annual drilling of all new wells. With the depletion of barite-rich deposits, wastes of mining and processing plants are of fundamental importance for barite production, as these technogenic deposits enable extraction of large amounts of barite.
Gravity and electromagnetic separation, as well as chemical bleaching are the most significant extraction approaches for the barite and technogenic deposits. At the same time, electromagnetic separation and chemical bleaching in the last decade are in the phase of active patenting of the relevant technologies, exceeding journal papers in the absolute as well as share numbers, which indicates the maturity of these methods.
In the last decade, both the Russian and international research in the field of barite ore benefication cover the following interrelated areas:
- Making technologies and barite products increasingly environmentally friendly, which is achieved through decreased toxicity of current and emerging reagents used in separation of barite extraction. Conceptually new ways of benefication emerge relying on various microorganisms that do not harm nature. Due to an extensive variety of microorganisms, their rapid reproduction and a wide range of applications in benefication, bioflotation is considered as a solid basis for the industrial use of microorganisms in the coming years, as well as an effective solution for creating safe and environmentally friendly mineral production.
- Increasing the efficiency of methods where mathematical models come to the fore to optimize all technological processes, including neural networks.
- Reducing the total cost of benefication works, particularly decreasing energy and reagent consumption.
References
- Bolonin A.V., Nikiforov A.V. Intermediate Sulfates in Barite-Celestite Isomorphic Series: Composition and Mode of Occurrence. Geology of Ore Deposits. 2014. Vol. 56. N 4, p. 302-314. DOI: 10.1134/S1075701514040023
- Lein A.Y., Kravchishina M.D. Barium Geochemical Cycle in the Ocean. Lithology and Mineral Resources. 2021. Vol. 56. N 4. P. 293-308. DOI: 10.1134/S0024490221040052
- Egorova I.P., Akhmanov G.G., Bulatkina T.A. Typomorphic features of barite. National Geology. 2010. N 2, p. 3-8 (in Russia).
- Kuznetsov D.S., Burtsev I.N., Kuznetsov S.K. Barite raw market and prospects for the development of deposits in the Republic of Komi. The North and the Market: Forming the Economic Order. 2022. Vol. 25. N 3, p. 171-185 (in Russian). DOI: 10.37614/2220-802X.3.2022.77.012
- Boyarko G.Yu., Khatkov V.Yu. Current state of production and consumption of barite raw materials in Russia. Bulletin of the Tomsk Polytechnic University. Geo Assets Engineering. 2021. Vol. 332. N 10, р. 180-191 (in Russian). DOI: 10.18799/24131830/2021/10/3403
- Akhmanov G.G., Egorova I.P., Bulatkina T.A. Method for determining the genesis barite field early exploration work. Prospect and protection of mineral resources. 2017. N 4, p. 11-15 (in Russian).
- Akhmanov G.G., Bulatkina T.A., Egorova I.P. et al. Deposits of the residual type of the Republic of Bashkortostan – basis for the creation of raw material base of “non-drilling” barit. Prospect and protection of mineral resources. 2019. N 6, p. 14-18 (in Russian).
- Senatorov P.P. Problems of the mineral resource base of the main types of non-metals used in the chemical complex of Russia. Mineral Resources of Russia. Economics & Management. 2019. N 1, p. 31-35 (in Russian).
- Akhmanov G.G., Egorova I.P., Bulatkina T.A. Current status and development prospects of the barite mineral resources base. Mineral Resources of Russia. Economics & Management. 2017. N 6, p. 4-14 (in Russian)
- Akhmanov G.G., Egorova I.P., Bulatkina T.A. Barite deposits weathering – a promising source of high-quality raw material. National Geology. 2016. N 2, p. 23-31 (in Russian).
- Ryzhkov A.V., Koreshkov N.G. Current Status with Mineral Resource Base of Barite and New Requirements to Barite Weighting Agents in Drill Mud. Neft. Gas. Novacii. 2020. N 11 (239), p. 33-36 (in Russian).
- Novikov N.V., Samchenko S.V., Okolnikova G.E. Barite-containing radiation protective building materials. RUDN Journal of Engineering Research. 2020. Vol. 21. N 1, p. 94-98 (in Russian). DOI: 10.22363/2312-8143-2020-21-1-94-98
- Bhatti M.A., Kazmi K.R., Mehmood R. et al. Beneficiation Study on Barite Ore of Duddar Area, District Lasbela, Balochistan Province, Pakistan. Pakistan Journal of Scientific and Industrial Research Series A: Physical Sciences. 2017. Vol. 60. N 1, p. 9-21. DOI: 10.52763/PJSIR.PHYS.SCI.60.1.2017.9.22
- Ahmad I., Shahzada K., Ahmad M.I. et al. Densification of Concrete using Barite as Fine Aggregate and its Effect on Concrete Mechanical and Radiation Shielding Properties. Journal of Engineering Research. 2019. Vol. 7. N 4, p. 81-95.
- Samchenko S.V., Novikov N.V. Influence of a barite containing additive on the properties of cellular concrete. Technique and Technology of Silicates. 2022. Vol. 29. N 4, p. 335-341 (in Russian).
- Chenhao Zeng, Qing Kang, Zhongshan Duan et al. Development of Polymer Composites in Radiation Shielding Applications: A Review. Journal of Inorganic and Organometallic Polymers and Materials. 2023. Vol. 33. Iss. 8, p. 2191-2239. DOI: 10.1007/s10904-023-02725-6
- Cherkasov V.D., Yurkin Yu.V., Suntsov D.L. Technical and economic comparison of design solutions for radiation protection against X-ray radiation. Engineering Journal of Don. 2021. N 1, p. 230-243 (in Russian).
- Ishbaev G., Dilmiev M., Khristenko A. et al. Development of more heavy thermally stable salt-saturated drilling mud by “BURINTECH” SPE” LLC. Burenie & neft. 2013. N 9, p. 47-48 (in Russian).
- Akhmanov G.G., Egorova I.P., Bulatkina T.A. The state and prospects of development of the mineral resource base of barite of the Republic of Khakassia. Prospect and protection of mineral resources. 2022. N 7, p. 41-49 (in Russian). DOI: 10.53085/0034-026X_2022_07_41
- Gershenkop A.Sh., Khokhulya M.S., Kontorina T.A. Development of the technology of gravity and magnetic separation of barite-siderite ores in Sallanlatva deposit. Mining Informational and Analitical Bulletin. 2007. N 10, p. 358-364.
- Leusheva E.L., Alikhanov N.Т., Brovkina N.N. Study on the rheological properties of barite-free drilling mud with high density. Journal of Mining Institute. 2022. Vol. 258, p. 976-985. DOI: 10.31897/PMI.2022.38
- Pereyma A.A., Dubov N.M., Cherkasova V.E. The mud on the basis of biopolymer for hole making in AHFP. Construction of Oil and Gas Wells on Land and Sea. 2010. N 4, p. 34-38 (in Russian).
- Akhmanov G.G., Egorova I.P., Bulatkina T.A. The problem of providing the industry with high-quality barite raw materials, ways of its solution. Prospect and protection of mineral resources. 2021. N 8, p. 9-14 (in Russian).
- Grinev O.M., Semiryakov A.S., Bestemyanova K.V., Grinev R.O. Morphostructure and stages of the formation of the Zmeinogorsk barite-polymetallic deposit (Rudny Altai). Advances in current natural sciences. 2022. N 8, p. 81-95 (in Russian). DOI: 10.17513/use.37872
- Bortnikova S.B., Yurkevich N.V., Edelev A.V. et al.Hydrochemical and gaseous anomalies on sulfide tailings (Salair, Kemerovo region). Izvestiya Tomskogo politekhnicheskogo universiteta. Inzhiniring georesursov. 2021. Vol. 332. N 2, p. 26-35 (in Russian). DOI: 10.18799/24131830/2021/2/3040
- Kalinin E.P. Barites of the Komi Republic: current state and development potential. Vestnik of the Institute of Geology of the Komi Science Center of the Ural Branch of the Russian Academy of Sciences. 2010. N 3, p. 2-5 (in Russian).
- Kuznetsov S.K., Burtsev I.N., Tarbaev M.B. et al. Mineral resources of the Vorkuta region and the prospects of their development. Proceedings of the Komi Science Centre of the Ural Division of the Russian Academy of Sciences. 2021. N 3 (49), p. 65-74 (in Russian). DOI: 10.19110/1994-5655-2021-3-65-74
- Senatorov P.P., Belyayev Y.V., Kuzmina I.A. Nonmetallic minerals in the Russian Arctic zone: resource potential and its utilization. Mineral Resources of Russia. Economics & Management. 2015. N 2, p. 9-21 (in Russian).
- Vikentev I.V. Metallogenic studies in the Polar Urals and problems of developing its mineral resource potential. Metallogeniya drevnikh i sovremennykh okeanov. 2020. N 1, p. 36-40.
- Akhmanov G.G., Egorova I.P., Michailik P.E. et al. To genesis of travertinopodobnye barites of Derugin basin (Okhotsk Sea). National Geology. 2015. N 1, p. 82-88 (in Russian).
- Astakhov A.S., Ivin V.V., Karnaukh V.N. et al. Barite mineralization in the Deryugin Basin of the Okhotsk Sea: Active processes and formation conditions. Russian Geology and Geophysics. 2017. Vol. 58. N 2, p. 165-176. DOI: 10.1016/j.rgg.2017.01.002
- Astakhova N.V. Barium in ferromanganese crusts from the Sea of Japan: peculiarities of allocation and interrelation with main ore phases. Vestnik of the Institute of Geology of the Komi Science Center of the Ural Branch of the Russian Academy of Sciences. 2019. N 3, p. 31-40 (in Russian). DOI: 10.19110/2221-1381-2019-03-31-40
- Safina N.P., Melekestseva I.Yu., Ankusheva N.N. et al. Barite from ores of the Safyanovsky pyrite deposit (Middle Urals) and hydrothermal fields Semenov-1 and 3 (Mid-Atlantic Ridge): comparative analysis of formation conditions. Metallogeniya drevnikh i sovremennykh okeanov. 2015. N 1, p. 93-97.
- Korotchenkova O.V. Celestine and barite of the Verkhnekamskoe salt deposit (Perm region). Problemy mineralogii, petrografii i metallogenii. Nauchnye chteniya pamyati P.N.Chirvinskogo. 2019. Vol. 22, p. 73-79.
- Afolayan D.O., Eggleston C.M., Onwualu A.P. et al. Physicochemical Studies for Risk Identification, Assessment, and Characterization of Artisanal Barite Mining in Nigeria. Sustainability. 2021. Vol. 13. Iss. 23. N 12982. DOI: 10.3390/su132312982
- Yurkevich N.V., Eltsov I.N., Gureev V.N. et al. Technogenic effect on the environment in the Russian arctic by the example of the Norilsk industrial area. Bulletin of the Tomsk Polytechnic University. Geo Аssets Engineering. 2021. Vol. 332. N 12, р. 230-249 (in Russian). DOI: 10.18799/24131830/2021/12/3207
- Bolgov G.P. Salair sulfides. Ur group of polymetallic deposits. Izvestiya Tomskogo industrialnogo instituta. 1937. Vol. 58. Iss. 1-3, p. 45-96.
- Distanov E.G. Pyrite-polymetallic deposits of Siberia. Novosibirsk: Nauka. Sibirskoe otdelenie, 1977, p. 351.
- Cherepnin V.K. Towadrs the composition and genesis of ores from the Ur deposits of Salair. Izvestiya Tomskogo Ordena Trudovogo Krasnogo Znameni politekhnicheskogo instituta imeni S.M.Kirova. 1958. Vol. 90, p. 56-68.
- Olenchenko V.V., Kucher D.O., Bortnikova S.B. et al. Vertical and lateral spreading of highly mineralized acid drainage solutions (Ur dump, Salair): electrical resistivity tomography and hydrogeochemical data. Russian Geology and Geophysics. 2016. Vol. 57. N 4, p. 617-628. DOI: 10.1016/j.rgg.2015.05.014
- Gosudarstvennaya geologicheskaya karta Rossiiskoi Federatsii masshtaba 1:200000. Izdanie vtoroe. Seriya Kuzbasskaya. List N-45XIV (Gur'evsk). Obyasnitelnaya zapiska. Saint Petersburg: Kartograficheskaya fabrika VSEGEI, 2002, p. 88.
- Mishenin M.V., Yurkevich N.V. Experience in geological and economic assessment of technogenic deposits (using the example of barite). GeoEvraziya-2023. Geologorazvedochnye tekhnologii: nauka i biznes: Trudy VI Mezhdunarodnoi geologo-geofizicheskoi konferentsii, 27-29 March 2023, Moscow, Russia: v 3 tomakh. Tver: PoliPRESS, 2023. Vol. I (III), p. 44-47.
- Khusainova А.Sh., Yurkevich N.V., Bortnikova Sv.B. Secondary barite from the Novo-Ursk dump. Geodynamics and Minerageny of Northern Eurasia: Materials of VI International scientific conference, 13-17 March 2023, Ulan-Ude, Russia. Ulan-Ude: Buryat State University Publishing Department, 2023, p. 567-570 (in Russian).
- Khusainova A.Sh., Bortnikova S.B., Gaskova O.L. et al. Secondary minerals of Fe, Pb, Cu in sulfide-containing tailings: sequence of formation, electrochemical reactions and physicochemical model (Talmovskie Sands, Salaire, Russia). Earth Sciences. 2023. Vol. 23. N 1. N ES1006 (in Russian). DOI: 10.2205/2023ES000810
- Yurkevich N.V., Khusainova A.Sh., Bortnikova S.B. Resources of barite, non-ferrous and precious metals in the Talmovskie peski tailing dump: mineralogical, geochemical and geophysical data. Geology and mineral resources of Siberia. 2023. N 3 (55), p. 105-114 (in Russia). DOI: 10.20403/2078-0575-2023-3-105-114
- Leonteva E.V., Medyanik N.L., Kalugina N.L. Thermochemical chloro-ammonium processing of technogenic dump sulphide tailings. Mining Informational and Analytical Bulletin. 2017. N 1, p. 305-316 (in Russian).
- Edelev A.V., Yurkevich N.V., Gureev V.N., Mazov N.A. Reclamation of Waste Storage Sites of the Mining Industry in the Russian Federation. Journal of Mining Science. 2022. Vol. 58. N 6, p. 1053-1068. DOI: 10.1134/S1062739122060205
- Deniz V., Umucu Y., Deniz O.T. Estimation of grade and recovery in the concentration of barite tailings by the flotation using the MLR and ANN analyses. Physicochemical Problems of Mineral Processing. 2022. Vol. 58. Iss. 5. N 150646. DOI: 10.37190/ppmp/150646
- Fuerstenau D.W., Pradip. A Century of Research Leading to Understanding the Scientific Basis of Selective Mineral Flotation and Design of Flotation Collectors. Mining, Metallurgy & Exploration. 2019. Vol. 36. Iss. 1, p. 3-20. DOI: 10.1007/s42461-018-0042-6
- Long Wang, Weijian Lyu, Lingyun Huang et al. Utilization of gellan gum as a novel eco-friendly depressant in the flotation separation of fluorite from barite. Minerals Engineering. 2022. Vol. 184. N 107640. DOI: 10.1016/j.mineng.2022.107640
- Gudvill M.N., Bogidaev S.A. Study of collecting agent Fomol and mineral surface interaction in water recirculation environment. Proceedings of the Siberian Department of the Section of Earth Sciences, Russian Academy of Natural Sciences. Geology, Prospecting and Exploration of Ore Deposits. 2016. N 4 (57), р. 70-76 (in Russian). DOI: 10.21285/0130-108Х-2016-57-4-70-76
- Zhonghua Xue, Yali Feng, Haoran Li et al. A comprehensive review on progresses of coal and minerals bioflotation in presence of microorganisms. Journal of Environmental Chemical Engineering. 2023. Vol. 11. Iss. 6. N 111182. DOI: 10.1016/j.jece.2023.111182
- Asgari K., Huang Q., Khoshdast H., Hassanzadeh A. A Review on Bioflotation of Coal and Minerals: Classification, Mechanisms, Challenges, and Future Perspectives. Mineral Processing and Extractive Metallurgy Review. 2024. Vol. 45. Iss. 1, p. 46-76. DOI: 10.1080/08827508.2022.2121919
- San Martín F., Kracht W., Vargas T. Biodepression of pyrite using Acidithiobacillus ferrooxidans in seawater. Minerals Engineering. 2018. Vol. 117, p. 127-131. DOI: 10.1016/j.mineng.2017.11.005
- Ashkavandi R.A., Azimi E., Hosseini M.R. Bacillus licheniformis a potential bio-collector for Barite-Quartz selective separation. Minerals Engineering. 2022. Vol. 175. N 107285. DOI: 10.1016/j.mineng.2021.107285
- Jing Guo, Ming Wen, Jingxuan Wu. Mchanistic study on the flotation of barite with C18H33NaO2 under microwave radiation based on UV-visible spectrophotometric analysis. Physicochemical Problems of Mineral Processing. 2022. Vol. 58. Iss. 6. N 156349. DOI: 10.37190/ppmp/156349
- Cilek E.C., Ozgen S. Improvement of the Flotation Selectivity in a Mechanical Flotation Cell by Ultrasound. Separation Science and Technology. 2010. Vol. 45. Iss. 4, p. 572-579. DOI: 10.1080/01496390903484966
- Esmeli K. The Effect of Ultrasound Treatment on Oil Agglomeration of Barite. Mineral Processing and Extractive Metallurgy Review. 2023. Vol. 44. Iss. 3, p. 189-200. DOI: 10.1080/08827508.2022.2155957
- Raju G.B., Ratchambigai S., Rao M.A. et al. Beneficiation of Barite Dumps by Flotation Column; Lab-Scale Studies to Commercial Production. Transactions of the Indian Institute of Metals. 2016. Vol. 69. Iss. 1, p. 75-81. DOI: 10.1007/s12666-015-0700-z
- Cheng Liu, Xinyue Zhang, Yunfei Zheng et al. Utilization of water glass as a dispersant to improve the separation performance of fluorite from barite slimes. Colloids and Surfaces A: Physicochemical and Engineering Aspects. 2022. Vol. 635. N 128036. DOI: 10.1016/j.colsurfa.2021.128036
- Cheng Liu, Shaoxian Song, Hongqiang Li. Selective flotation of fluorite from barite using trisodium phosphate as a depressant. Minerals Engineering. 2019. Vol. 134, p. 390-393. DOI: 10.1016/j.mineng.2019.02.008
- Ying Lu, Weiping Liu, Xuming Wang et al. Lauryl Phosphate Flotation Chemistry in Barite Flotation. Minerals. 2020. Vol. 10. Iss. 3. N 280. DOI: 10.3390/min10030280
- Randin O.I., Gudvill M.N., Bogidaev S.A. Investigation of reagent “Phomol” interaction mechanism under barite ore flotation. Proceedings of Irkutsk State Technical University. 2012. N 6 (65), p. 119-123 (in Russian).
- Turebekova K., Katkeeva G., Sultangaziev R. et al. Choice of Scheme and Reagents for Flotation of Technogenic Barite Raw Materials. University Proceedings. 2022. N 4 (89), p. 85-90 (in Russian). DOI: 10.52209/1609-1825_2022_4_85
- Larachi N., Bali A., Ould Hamou M., Bensaadi S. Recovery of lead and barite from the abandoned Ichmoul mine wastes in Algeria. Environmental Earth Sciences. 2019. Vol. 78. Iss. 20. N 601. DOI: 10.1007/s12665-019-8593-5
- Neesse Th., Dueck J., Schwemmer H., Farghaly M. Using a high pressure hydrocyclone for solids classification in the submicron range. Minerals Engineering. 2015. Vol. 71, p. 85-88. DOI: 10.1016/j.mineng.2014.10.017
- Dueck J., Minkov L.L. On the Conditions of Clogging in a Hydrocyclone. Theoretical Foundations of Chemical Engineering. 2019. Vol. 53. N 4, p. 529-537. DOI: 10.1134/s0040579519040171
- Wenjie Lv, Jinchao Zhao, Mingxun Hao et al. Enhancing classification and recovery of barite from waste drilling fluid by inlet particle arranging of hydrocyclone. Journal of Water Process Engineering. 2023. Vol. 56. N 104341. DOI: 10.1016/j.jwpe.2023.104341
- Hredzák S., Dolinská S., Znamenáčková I. et al. Possibilities of Siderite and Barite Concentrates Preparation from Tailings of Settling Pit Nearby Markušovce Village (Eastern Slovakia). Inżynieria Mineralna. 2019. Vol. 1. N 1, p. 19-24. DOI: 10.29227/IM-2019-01-03
- Boroznovskaya N.N., Zyryanova L.A., Pekov I.V. Luminescent Properties of Natural Barite: Evidence for Its Genesis. Doklady Earth Sciences. 2016. Vol. 471. Part 1, p. 1171-1173. DOI: 10.1134/s1028334x16110118
- Kobzev A.S. Radiometric benefication of mineral raw materials. Moscow: Gornaya kniga, 2015, p. 25.
- Tosee S.V.R., Faridmehr I. Mechanical properties prediction of heavyweight concrete using generalized regression neural network (GRNN). Romanian Journal of Materials. 2022. Vol. 52. N 3, p. 303-310.