Научно-техническое обоснование возможности организации производства игольчатого кокса в России
- 1 — канд. техн. наук исполнительный директор Санкт-Петербургский горный университет ▪ Orcid ▪ Elibrary ▪ Scopus ▪ ResearcherID
- 2 — канд. техн. наук научный сотрудник Санкт-Петербургский горный университет ▪ Orcid ▪ Elibrary ▪ Scopus
- 3 — д-р техн. наук директор Санкт-Петербургский горный университет ▪ Orcid ▪ Elibrary ▪ Scopus ▪ ResearcherID
Аннотация
Россия является одним из мировых лидеров по производству стали, при этом около 33 % производства приходится на переплавку лома в дуговых сталеплавильных печах. Для работы при высоких токовых нагрузках и температуре в печах применяются графитированные электроды марок SHP и UHP, которые в основном состоят из игольчатого кокса. Производство игольчатого кокса сосредоточено в США, Японии, Корее и Китае, где в качестве сырья используют побочные продукты металлургических и нефтеперерабатывающих предприятий – угольное (смолу и пек) и нефтяное (декантойль). В России ежегодная потребность в игольчатом коксе составляет около 100 тыс. т, однако вся она удовлетворяется посредством импорта. Сырьевой потенциал России, установленный авторами статьи, составляет более 5 млн т в год и включает декантойль, каменноугольные смолу и пек, а также тяжелую смолу пиролиза. Описаны результаты получения игольчатого кокса из декантойля и тяжелой смолы пиролиза. Наработка опытных образцов игольчатого кокса проводилась на специально разработанных лабораторных установках замедленного коксования (загрузкой до 0,25 и 80 кг). Сырье было модифицировано по оригинальной технологии Санкт-Петербургского горного университета, сходимость целевых свойств которой подтверждается результатами анализа качества полученных игольчатых коксов, в том числе и после 100-кратного масштабирования. Из полученного кокса были сформованы электроды. После стандартизированных стадий обжига, механической обработки и графитации при 2800-3000 °С коэффициент линейного термического расширения составил менее 1 × 10–6 К–1, а значение удельного электрического сопротивления 7,1-7,4 мкОм, что доказывает, что полученный углеродный материал соответствует по качеству японским аналогам и игольчатому коксу марки Super Premium.
Введение
Игольчатый кокс – это целенаправленно структурированный углеродный материал с высокой долей графитовой фазы, применяемый для изготовления графитированных электродов марок SHP (super-high power) и UHP (ultra-high power) дуговых сталеплавильных печей (ДСП) высокой и сверхвысокой мощностей [1-3]. Графитированные электроды являются основным материалом при производстве стали в ДСП (расход составляет около 5 кг на 1 т стали), которые примерно на 85 % состоят из игольчатого кокса [4, 5]. Благодаря своей ориентированной структуре только такой углеродный материал способен выдерживать высокие токовые нагрузки (плотность тока до 35 А/см2) и температуры до 2800 °С, возникающие в концевой части электрода в процессе переплавки стального лома [6-8]. В последние два десятилетия с развитием транспорта, работающего на альтернативном топливе, растет применение игольчатого кокса в качестве сырьевого материала для литий-ионных аккумуляторов электромобилей [9]. Однако определяющая потребность в игольчатом коксе на протяжении семи десятилетий была обусловлена в первую очередь производством высокосортных марок стали. По данным World Steel Association, в 2021 г. около 560 млн т (28,9 %) стали в мире производится в ДСП (в России и странах СНГ – около 33 %).
Игольчатый кокс в промышленности производят из двух видов сырья – нефтяного и угольного. Нефтяное сырье – это декантированный тяжелый газойль каталитического крекинга (декантойль), который получают на нефтеперерабатывающих заводах в качестве побочного продукта производства высокооктанового компонента автомобильного бензина на установках каталитического крекинга, (например, FCC) [10]. Впервые из нефтяного сырья игольчатый кокс был промышленно получен в 1950-х гг. в США (Great Lakes Carbon Corporation). Угольное сырье – это очищенный от хинолин-нерастворимых примесей каменноугольный пек, который получают на коксохимических заводах металлургических комбинатов в качестве побочного продукта [11, 12]. Впервые из угольного сырья игольчатый кокс был получен в 1970-х гг. в Японии (Mitsubishi Chemical) (рис.1).
Мировой рынок игольчатого кокса непрерывно растет (с 3,54 млрд дол. в 2017 г. до 4,15 млрд дол. в 2021 г.). В 2022 г. производственные мощности представлены 23 компаниями, семь из которых располагаются в трех странах – три в США, три в Японии и одна в Корее, остальные находятся в Китае (табл.1). Такой рынок производителей игольчатого кокса был сформирован к 1980-м годам, и после этого новые мощности не вводились (за исключением Китая). Однако наличие сырьевой базы и перманентный рост потребности в игольчатом коксе, обусловленный лидерством по выпуску стали (1,03 млрд т в 2021 г.), позволили Китаю за последние 10 лет нарастить его фактическое производство до 44 % от всего мирового объема (около 1,8 млн т в год). При этом дефицит электроэнергии является сдерживающим фактором [13, 14], который не позволяет ввести в эксплуатацию готовые мощности китайских предприятий для производства в 2,8 раза большего количества игольчатого кокса.
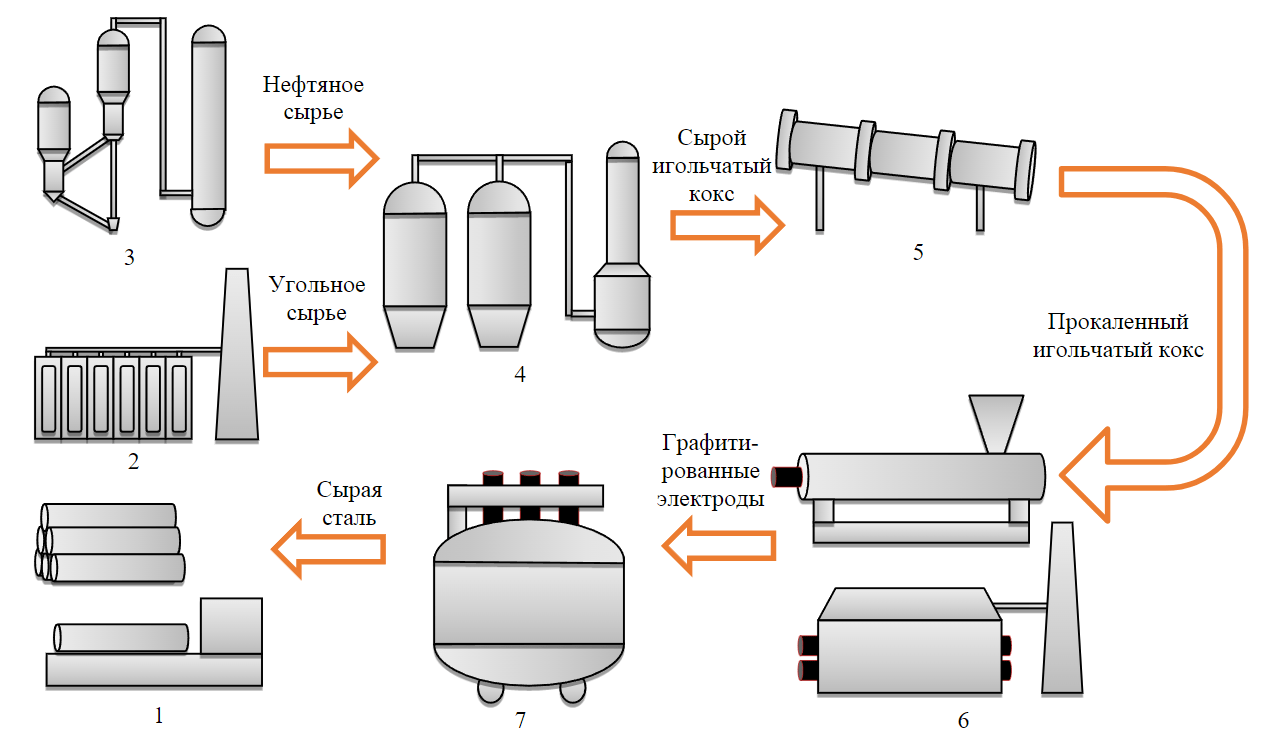
Рис.1. Блок-схема полного цикла производства и применения игольчатого кокса
Таблица 1
Мировое производство игольчатого кокса, тыс. т
Страна |
Компания |
Вид сырья |
2019 |
2021 |
США |
Asbury Carbons |
Нефтяное |
Нет информации |
Нет информации |
GrafTech International |
Нефтяное |
140 |
140 |
|
Phillips 66 Company |
Нефтяное |
370 |
450 |
|
Япония |
Mitsubishi Chemical Holdings Corporation |
Угольное |
80 |
80 |
Nippon Steel Chemical & Material Co. Ltd. (включая C-Chem) |
Нефтяное |
90 |
95 |
|
Угольное |
110 |
110 |
||
Sumitomo Corporation |
Нефтяное |
70 |
70 |
|
Корея |
Posco Chemical |
Угольное |
50 |
63 |
Итого |
910 |
1008 |
||
Китай* |
16 компаний в 2021 г. 15 компаний в 2019 г. |
Нефтяное |
195 (360) |
501 (1180) |
Угольное |
250 (610) |
261 (1000) |
||
Итого по миру |
1355 |
1770 |
* Для Китая в скобках указана мощность производства.
Наряду с Китаем начать производство игольчатого кокса, в основном для удовлетворения своих внутренних потребностей, стремятся лидирующие страны – производители стали – Индия (118,2 млн т), Россия (75,6 млн т) и Иран (28,5 млн т), которые занимают (в 2021 г.) в мире второе, пятое и десятое место соответственно. Потребность России в игольчатом коксе для удовлетворения нужд собственных предприятий по производству стали составляет около 100 тыс. т в год. Российская компания ООО «Эл 6» (ранее – «Энергопром») является монополистом в производстве графитированных электродов марок SHP и UHP, которая ежегодно потребляет до 40 тыс. т импортируемого прокаленного игольчатого кокса.
Постоянно растущая потребность и высокая рыночная цена игольчатого кокса, которая варьируется от 1500 до 3500 дол. за тонну (2019-2022) при энергопотреблении на переработку одной тонны сырья в процессе замедленного коксования 27-40 кВт/ч, делает организацию промышленного производства игольчатого кокса не только стратегически важной, но и экономически оправданной. Объемы инвестиций, направляемых на реализацию проектов по организации производства нефтяного игольчатого кокса Индией (Indian Oil Corporation Ltd., Paradip Refinery), Россией (ПАО «Газпром нефть», Омский НПЗ) и Ираном (Shazand Petrochemical Company, Imam Khomeini Shazand Oil Refinery), составляют 150, 74-100 и 312 млн дол. соответственно. При этом планируемые по результатам реализации проектов объемы производства кокса составляют 56, 38 и 90 тыс. т в год для Индии, России и Ирана соответственно.
Перспектива организации производства игольчатого кокса в России, кроме экономических и стратегических факторов, как и для других объектов минерально-сырьевого и топливно-энергетического комплекса, определяется наличием сырьевой ресурсной базы [15-17]. Оценка сырьевого потенциала России показала, что он представлен как традиционными видами сырья – декантойлем [18] и каменноугольным пеком (вместе с каменноугольной смолой) [19, 20], так и перспективным, не типичным для мирового рынка, – тяжелой смолой пиролиза природного газа(рис.2).
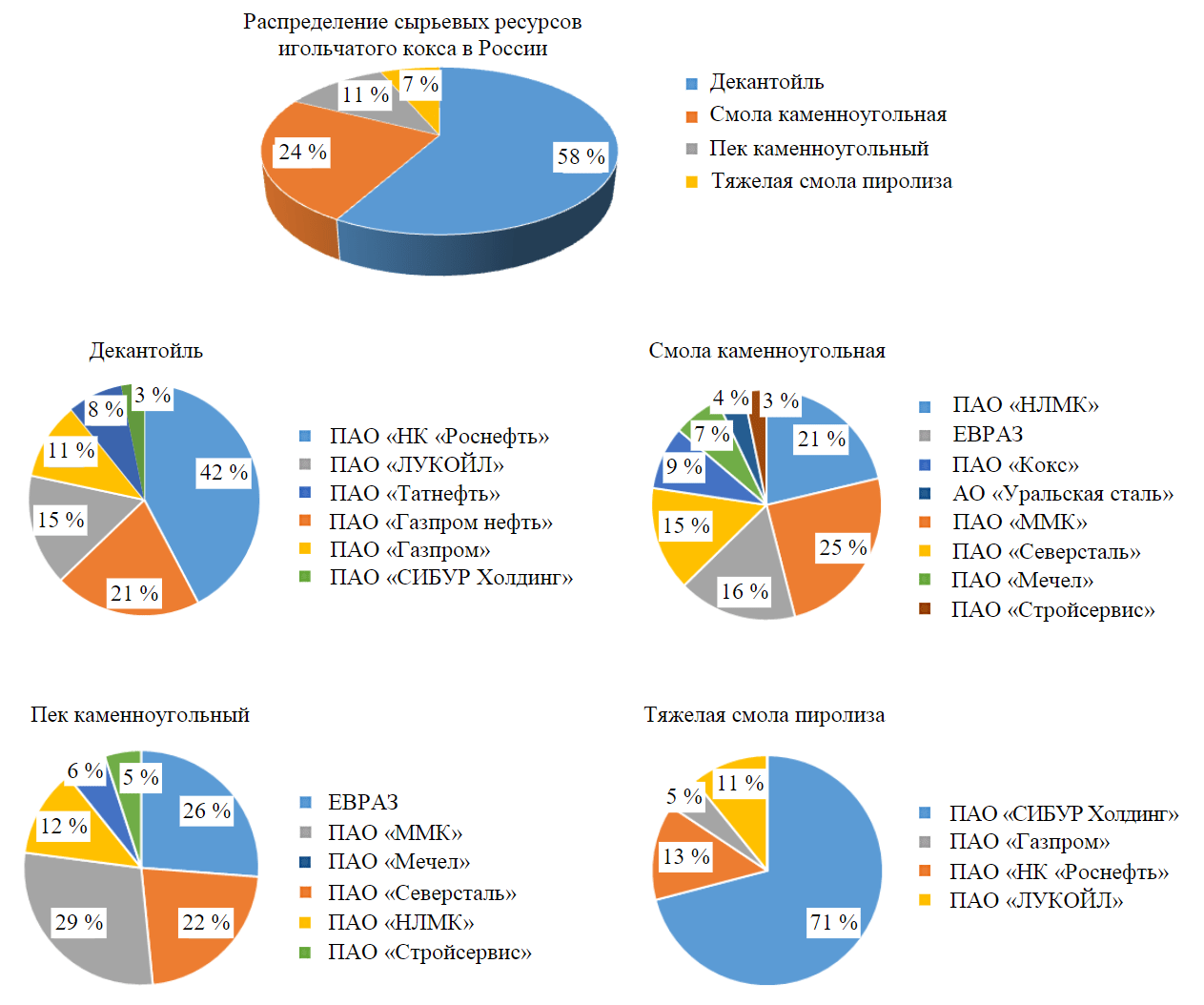
Рис.2. Оценка сырьевого потенциала для производства игольчатого кокса в России
Сырьевой потенциал России представлен 48 техногенными источниками и составляет более 5 млн т в год. Теоретически данного количества достаточно для производства до 800 тыс. т в год игольчатого кокса, причем лидирующие позиции по объему вырабатываемого сырья занимают ПАО «НК «Роснефть», ПАО «Газпром нефть», ПАО «ЛУКОЙЛ», ПАО «Татнефть», ПАО «Газпром», ПАО «НЛМК», ПАО «СИБУР Холдинг», ПАО «ММК» и ЕВРАЗ. Однако большая часть данного сырья не может быть напрямую использована для получения игольчатого кокса в процессе замедленного коксования. Дифференциация по углеводородному составу, содержанию серы и хинолин-нерастворимых веществ требует специальной подготовки или модификации сырья. Мировой опыт внедрения технологий показывает, что для каждого сырьевого источника необходимо разрабатывать индивидуальное научно-техническое решение для получения высококачественного продукта [21-23], при этом должно осуществляться государственное регулирование применительно к объектам минерально-сырьевого комплекса [24, 25].
Целью данной работы является разработка экспериментально обоснованных научно-технических решений для создания промышленного производства игольчатого кокса в России.
Методы
Оптимизация процесса коксования и анализ качества продукта
Методология исследования игольчатого кокса и полученных на его основе электродов разрабатывается в Санкт-Петербургском горном университете и базируется на знаниях международных [26, 27] и отечественных научных школ [28, 29].
Необходимо отметить существенный вклад ученых Уфимского государственного нефтяного технического университета и Института нефтехимпереработки Республики Башкортостан, представители которых еще в 1980-е гг. проводили опытно-промышленные испытания по получению игольчатого кокса на Красноводском НПЗ (Туркмения) и Ново-Уфимском НПЗ, а в настоящее время осуществляют научно-техническую поддержку проекта ПАО «Газпром нефть» на Омском НПЗ [30]. В Санкт-Петербургском горном университете научные работы, связанные с игольчатым коксом, в середине 2010-х гг. начали проводиться под руководством В.Ю.Бажина и Н.К.Кондрашевой [31, 32], хотя формирование научной школы углеграфитовых соединений было начато еще в середине XX в. М.Б.Рапопортом.
Для выполнения экспериментальных исследований по физическому моделированию процесса получения игольчатого кокса в Научном центре «Проблем переработки минеральных и техногенных ресурсов» Санкт-Петербургского горного университета были специально разработаны две лабораторные установки замедленного коксования с различными объемами загрузки сырья (рис.3).
Основная задача установок – подбор термобарических условий протекания технологического процесса и наработка лабораторных (опытных) образцов продуктов для оценки их показателей качества. Принципиальная технологическая схема работы для обеих спроектированных установок является однотипной. Установка УЗК-1 с загрузкой 0,25 кг используется для кинетических исследований и установления оптимального режима процесса коксования, а установка ЛУЗК с загрузкой до 80 кг – для масштабирования процесса и наработки опытной партии игольчатого кокса высокого качества.
В реакционный аппарат помещается жидкофазное сырье (базовое или модифицированное) в объеме, не превышающем 2/3 реактора для минимизации возможности его переброса во время процесса. Далее система герметизируется, проводится опрессовка инертным газом (азотом), после чего в течение 12 ч сырье нагревается до температуры коксующейся массы (490-500 °С) и выдерживается при заданной температуре для завершения процесса получения сырого игольчатого кокса. Давление в системе является автогенным и контролируется отводом образующихся газожидкостных продуктов в процессе замедленного коксования до значения 0,35 МПа (изб.). Расход отходящих углеводородных газов контролируется по газовому расходомеру, а масса образовавшихся жидких дистиллятов фиксируется в конце эксперимента. После отключения нагрева и полного остывания реакционного аппарата производится механическая разгрузка сырого игольчатого кокса. Далее фиксируется масса полученного углеродного материала и сводится материальный баланс процесса.
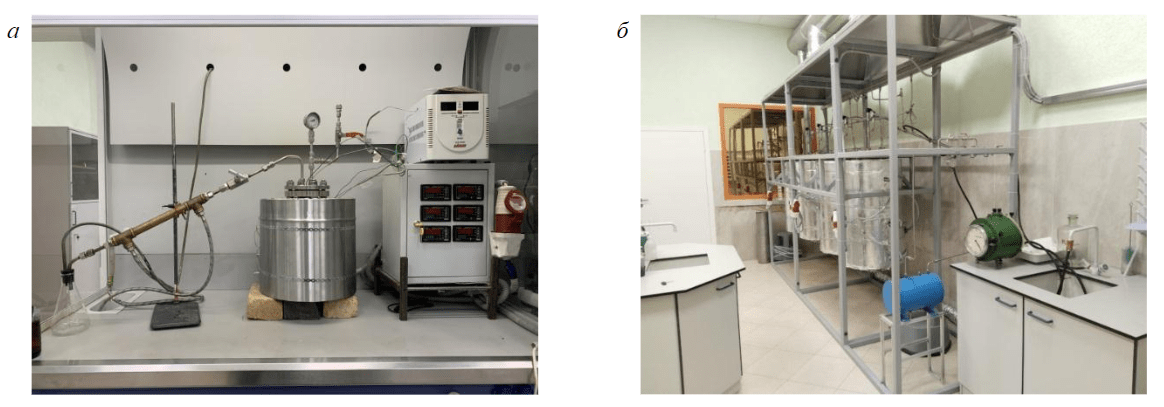
Рис.3. Лабораторные установки замедленного коксования: а – УЗК-1 (до 0,25 кг); б – ЛУЗК (до 80 кг)
Обязательной стадией получения товарного игольчатого кокса является его прокалка при температуре от 1100 до 1500 °С, при которой происходят удаление оставшихся летучих веществ и частичная десульфуризация, повышается степень графитации [33]. Прокалка осуществляется в течение одного часа в высокотемпературной муфельной печи Nabertherm LTH 08/17.
Изучение морфологии поверхности игольчатого кокса осуществляли методом сканирующей электронной микроскопии (СЭМ) на Tescan Vega 3 LMH. Изображения получали во вторичных электронах (SE) в режиме сканирования Resolution, поле обзора 16, 66 мкм и 1 мм. Ускоряющее напряжение составляло 20 кВ, ток эмиссии – 120 мкA. Идентификация и описание образцов кокса было выполнено в соответствии с номенклатурой.
Оценку микроструктуры игольчатого кокса методом оптической микроскопии проводили согласно ГОСТ 26132-84 «Коксы нефтяные и пековые. Метод оценки микроструктуры» на приборе m-Vizio-MET-222 [34, 35].
Кристаллическую структуру игольчатого кокса исследовали на рентгеновском порошковом дифрактометре XRD-7000 Shimadzu (CuKα-излучение 2,7 кВт) при комнатной температуре. Рентгенограммы снимали при большом времени накопления (2 с) и шаге сканирования 0,02°. По полученным пикам с максимумом на удвоенных углах дифракции Брэгга 2θ определяли межплоскостные расстояния по величине дифракционных максимумов (002) и (100), а также среднюю высоту кристаллитов Lc и средний диаметр гексагональных слоев La [28, 36].
Рамановскую спектроскопию образцов игольчатых коксов проводили на Renishaw inVia Raman Microscope с длиной волны возбуждающего света 780 нм и применением 50-кратного объектива; время накопления спектра составляло 10 с, каждый образец снимали пять раз. Полученные спектры комбинированного рассеяния (КР-спектры) нормализовали (на 100 ед.) и раскладывали на пять характерных пиков (D1, D2, D3, D4, G) преобразованием Лоренца.
Определение содержания серы было выполнено на последовательном волнодисперсионном рентгенофлуоресцентном спектрометре XRF-1800 Shimadzu. Аппарат оснащен рентгеновской трубкой с анодом из Rh мощностью 3,6 кВт; ток катода 90 мА; напряжение на трубке 40 кВ. Анализ проводили без предварительного озоления образцов с применением метода добавок (добавляли Ca в форме CaCl2) [37].
Коэффициент термического линейного расширения (КТЛР) образцов прокаленных игольчатых коксов определяли на дилатометре Netzsch DIL 402 C при температуре от 40 до 500 °С со скоростью нагрева 5 °С/мин и продувкой потоком воздуха (расход 50 мл/мин).
Влияние сырья и условий коксования на показатели качества игольчатого кокса и свойства графитированных электродов, которые определяют необходимую последовательность выполнения исследований и применяемые методы, представлено на рис.4.
В качестве материала для исследования были взяты два вида базового сырья – нефтяное и газовое – декантойль и тяжелая смола пиролиза (ТСП) соответственно. В качестве модификатора базового сырья был использован термопластичный полимер ароматического ряда.
Изготовление электродов в глухой матрице
После анализа качества полученного игольчатого кокса на установке УЗК-1 осуществлялась первичная оценка возможности формирования из него углекоксового электрода путем прессования в глухой матрице. Приготовление электродов осуществлялось путем смешения исходного прокаленного игольчатого кокса с различной долей среднетемпературного пека. Количество пека варьировалось от 12 до 14 % по массе.
Смешение игольчатого кокса со среднетемпературным пеком (соответствующим по ГОСТ 10200-2017 марке B1) осуществлялось при повышенной температуре и постоянном перемешивании (рис.5), необходимом для обеспечения эффективного распределения связующего по всему объему коксовой шихты и заполнения пор [38], и включало следующие стадии:
- смешение игольчатого кокса со среднетемпературным пеком; использовались две фракции игольчатого кокса – менее 0,5 мм (50 %) и фракция 0,5-1,0 мм – 50 %;
- нагрев полученной смеси до температуры 125 °С при постоянном перемешивании;
- перемешивание игольчатого кокса с пеком в течение 40 мин при температуре 125 °С (рис.5, а, б);
- прессование полученной композитной смеси при температуре 125 °С в течение 10 мин под давлением 300 кг/см2;
- выпрессовка заготовок – таблеток с диаметром 3,2 и высотой 6,2 см.
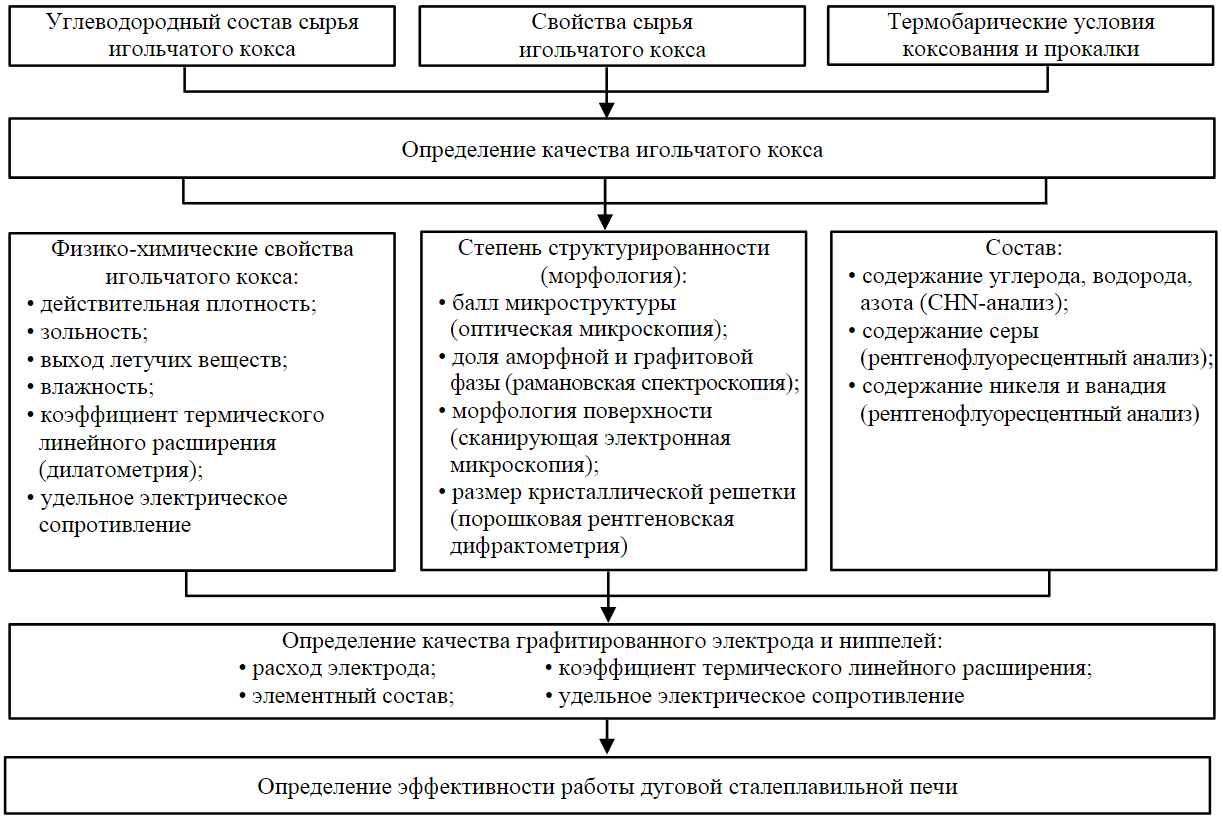
Рис.4. Влияние сырья и условий процесса коксования на показатели качества игольчатого кокса и свойства графитированных электродов
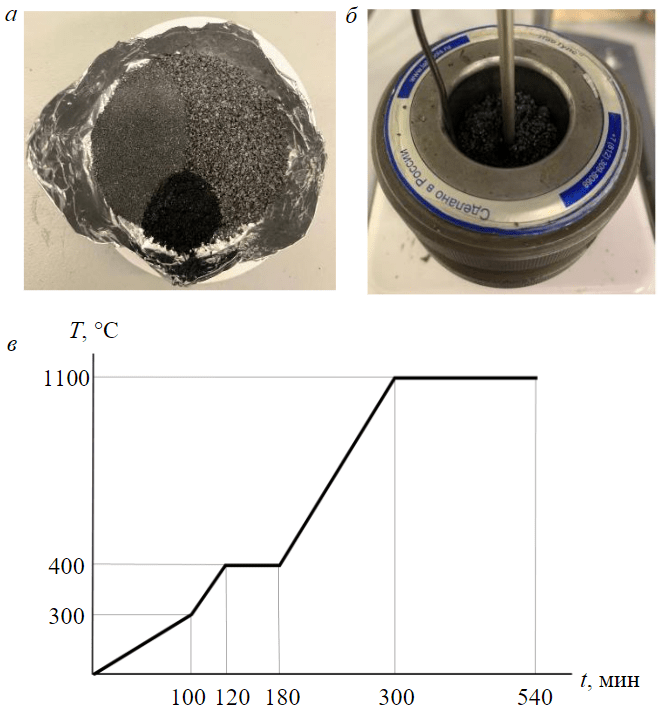
Рис.5. Приготовление обожженного углекоксового электрода: а – шихта для композита; б – горячее смешение для формовки; в – температурный режим обжига композита
Полученные заготовки в дальнейшем подвергались высокотемпературному обжигу в слое кокса для создания восстановительной среды и снижения доли выгорания обжигаемого электрода. Максимальная температура обжига составила 1100 °С при общем времени обжига 540 мин, изотермическую выдержку проводили при температуре 1100 °С в течение 240 мин (рис.5, в).
Изготовление электродов экструзионным прессованием
Экструзионное прессование применялось для оценки возможности формирования электродов из прокаленных образцов игольчатого кокса, полученных на установке ЛУЗК с загрузкой 80 кг. Предварительно технологический режим, тип сырья и способ модификации были установлены на УЗК-1. Приготовление электрода экструзионным прессованием включало следующие стадии:
- дозировка шихты согласно требованиям к ниппелям в ООО «Эл 6»;
- смешение фракций кокса с прогревом, добавление к прогретой углеродной массе электродного среднетемпературного пека и повторное смешение;
- горячее прессование полученной массы в экструдере-прессе;
- нарезка экструдатов для последующих обжига и механической обработки;
- обжиг полученных экструдатов при температуре 850 °С, изотермическая выдержка при 850 °С составляла 1 ч;
- механическая обработка полученных обожженных электродов;
- графитация обожженных электродов при температуре 2800-3000 °С.
Обсуждение результатов
Предварительная оценка возможности применения базового сырья для получения игольчатого кокса определялась экспериментальными результатами углеводородного состава (SARA-анализ) [39] и основных физико-химических свойств (табл.2).
Таблица 2
Физико-химические свойства и состав базового сырья коксования
Показатель |
Декантойль |
ТСП |
Требования Горного университета |
Парафино-нафтеновые, % по массе |
8,00 |
8,00 |
8,0-28,0 |
Ароматические, % по массе |
88,00 |
53,46 |
Не менее 61,4 |
Смолы, % по массе |
4,00 |
24,14 |
1,0-14,0 |
Асфальтены, % по массе |
0,10 |
14,54 |
Не более 2,8 |
Плотность при 15 °С, кг/м3 |
1046,1 |
1073,3 |
– |
Содержание серы, % по массе |
0,142 |
0,086 |
Не более 0,7 |
Зольность, % по массе |
0,012 |
0,010 |
0,0013-0,018 |
Динамическая вязкость (при 50 °C и различной концентрации полимера), мПа·с при 0 % по массе |
130,8 |
61,2 |
– |
при 5 % по массе |
1000,0 |
301,6 |
– |
при 10 % по массе |
7350,0 |
2533,0 |
– |
при 15 % по массе |
98200,0 |
10107,0 |
– |
Сравнительный анализ физико-химических свойств показал, что состав исследуемого декантойля полностью соответствует требованиям к сырью игольчатого кокса.
Для выбора оптимальных термобарических условий и модификатора для базового сырья опытные испытания по коксованию первоначально проводили на лабораторной установке УЗК-1 с загрузкой по сырью 0,25 кг. Режим коксования был подобран, исходя из возможностей существующих промышленных установок замедленного коксования, – по термической нагрузке на трубчатую печь и реактор, а также на основе максимально допустимого давления в адиабатических реакторах (табл.3).
Полученные образцы углеродных материалов (сырой кокс) прокаливались при температуре 1250-1300 °С в токе азота в течение одного часа для оценки морфологии полученного кокса. Физико-химические свойства прокаленных игольчатых коксов, параметры их кристаллической решетки и коэффициент термического линейного расширения представлены в табл.4.
Линейные размеры и межплоскостные расстояния соответствуют значениям получаемых в мире образцов игольчатого кокса. Наблюдается незначительное увеличение межплоскостного расстояния d002 (3,4822-3,5161 Å) при увеличении доли модификатора в исходном сырье с максимумом при 10 % по массе. На полученной дифрактограмме наблюдается симметричная форма пика (002), что свидетельствует о формировании структуры, приближающейся к графитовой. По результатам рентгенофазового анализа о характере микроструктуры нефтяных коксов можно судить по соотношению средней высоты Lc и среднего диаметра La кристаллитов. Так, чем дальше значение этого соотношения от единицы, тем более вытянутый характер элементарной ячейки. При увеличении концентрации модификатора от 0 до 10 % по массе соотношение Lc к La снижается, отдаляясь от единицы, а при 15 % значительно увеличивается (табл.4).
Таблица 3
Материальные балансы коксования на установке УЗК-1 с загрузкой 0,25 кг
Номер опыта |
Взято, % по массе |
Получено, % по массе |
|||||||
Базовое сырье |
Модификатор |
Итого сырья |
Кокс |
Дистилляты коксования |
Газ и потери |
Итого продуктов |
|||
Декантойль |
|
||||||||
1 |
100,0 |
0,0 |
100,0 |
44,8 |
36,2 |
19,0 |
100,0 |
|
|
2 |
97,5 |
2,5 |
100,0 |
46,0 |
36,6 |
17,4 |
100,0 |
|
|
3 |
95,0 |
5,0 |
100,0 |
45,6 |
37,2 |
17,2 |
100,0 |
|
|
4 |
90,0 |
10,0 |
100,0 |
44,4 |
39,2 |
16,4 |
100,0 |
|
|
5 |
85,0 |
15,0 |
100,0 |
45,2 |
42,2 |
12,6 |
100,0 |
|
|
Тяжелая смола пиролиза |
|
||||||||
6 |
100,0 |
0,0 |
100,0 |
28,4 |
56,4 |
15,2 |
100,0 |
|
|
7 |
90,0 |
10,0 |
100,0 |
29,6 |
63,6 |
6,8 |
100,0 |
|
|
8 |
85,0 |
15,0 |
100,0 |
30,0 |
66,0 |
4,0 |
100,0 |
|
Таблица 4
Результаты определения физико-химических свойств и расчетов структурных характеристик синтезированных прокаленных игольчатых коксов
Показатель |
Номер опыта |
|||||||
1 |
2 |
3 |
4 |
5 |
6 |
7 |
8 |
|
Балл микроструктуры |
5,40 |
5,70 |
6,10 |
6,15 |
5,70 |
4,80 |
5,30 |
5,40 |
Действительная плотность, г/см3 |
2,09 |
2,12 |
2,13 |
2,14 |
2,14 |
2,06 |
2,10 |
2,12 |
Выход летучих, % по массе |
5,27 |
4,33 |
4,86 |
5,14 |
4,33 |
5,11 |
5,12 |
5,09 |
Зольность, % |
0,05 |
0,05 |
0,05 |
0,04 |
0,04 |
0,06 |
0,07 |
0,07 |
Влажность, % |
0,05 |
0,05 |
0,06 |
0,06 |
0,05 |
0,12 |
0,13 |
0,20 |
Содержание серы, % по массе |
0,18 |
0,15 |
0,15 |
0,14 |
0,32 |
0,11 |
0,11 |
0,11 |
Рентгеноструктурный анализ |
|
|
|
|
|
|
|
|
Оценка по рефлексу (002): |
|
|
|
|
|
|
|
|
2θ, град |
25,56 |
25,54 |
25,45 |
25,31 |
25,49 |
– |
– |
– |
β, град |
2,24 |
2,23 |
2,42 |
2,37 |
2,20 |
– |
– |
– |
d002, Å |
3,48 |
3,48 |
3,49 |
3,51 |
3,49 |
– |
– |
– |
Lc, Å |
36,03 |
36,19 |
33,33 |
34,03 |
36,68 |
– |
– |
– |
Оценка по рефлексу (100): |
|
|
|
|
|
|
|
|
2θ, град |
43,04 |
42,88 |
42,69 |
42,76 |
42,94 |
– |
– |
– |
β, град |
2,23 |
2,21 |
2,11 |
1,97 |
2,24 |
– |
– |
– |
d100, Å |
2,09 |
2,10 |
2,12 |
2,11 |
2,10 |
– |
– |
– |
La, Å |
78,44 |
77,35 |
82,82 |
88,76 |
78,06 |
– |
– |
– |
La/Lc |
0,45 |
0,45 |
0,40 |
0,38 |
0,46 |
– |
– |
– |
Показатель КТЛР (ASTM D 6745) при различных значениях температур, 1 × 10–6 К–1: |
|
|
|
|
|
|
|
|
при 40 °С |
25,09 |
– |
24,45 |
7,33 |
–10,43 |
– |
– |
– |
при 200 °С |
4,81 |
– |
14,00 |
14,14 |
11,87 |
– |
– |
– |
при 300 °С |
–19,20 |
– |
8,92 |
5,73 |
6,95 |
– |
– |
– |
при 400 °С |
10,51 |
– |
12,51 |
8,15 |
11,32 |
– |
– |
– |
при 500 °С |
4,35 |
– |
5,31 |
5,14 |
9,58 |
– |
– |
– |
Основным показателем, определяющим качество игольчатого кокса, является коэффициент термического линейного расширения, в результате проведенных испытаний наблюдается тенденция снижения степени деформации углеродного материала при термическом воздействии с увеличением доли модификатора в исходном сырье (см. табл.4). При этом минимальный КТЛР 5,73 × 10–6 К–1 (при 300 °С) соответствует концентрации модификатора 10 % по массе.
Поскольку для формирования игольчатой структуры необходимы длительное существование пластического состояния жидкой фазы и ее низкая вязкость, то экстремальная зависимость может быть объяснена значительным увеличением вязкости системы за счет добавления большой концентрации модификатора – 15 % по массе (см. табл.2). Лимитирующей стадией для жидкофазного термолиза является диффузия, которая затрудняется при значительном увеличении вязкости системы, при этом наблюдаются ухудшение роста и развития мезофазы за счет терминации коалесценции мезофазных сфер и торможение деформации данных сфер конвективными потоками. Таким образом, высоковязкая среда неблагоприятна для образования струйчатой структуры. Для подтверждения определена динамическая вязкость смеси при 50 °С декантойля с различными концентрациями модификатора (см. табл.2).
Совокупное исследование физико-химических свойств и морфологии прокаленных коксов методами сканирующей электронной микроскопии и спектроскопии в плоскополяризованном свете (балл микроструктуры) позволило выявить наиболее качественные образцы из обоих видов базового сырья при его полимерной модификации, для декантойля это опыт 4 с добавлением 10 % по массе модификатора, а для тяжелой смолы пиролиза опыт 8 с добавлением 15 % по массе модификатора. Наиболее характерная морфология для синтезированных прокаленных игольчатых коксов с наибольшим баллом микроструктуры для двух типов сырья представлена в табл.5. Однако образцы, полученные из ТСП, обладают более низким баллом микроструктуры и плотностью, по морфологии представляют собой переходную структуру с относительно высокой долей изотропной фазы. Поэтому дальнейшие исследования по получению игольчатого кокса проводились с использованием только декантойля в качестве базового сырья.
Для количественной оценки доли графитовой фазы и труднографитируемой аморфной фазы проведена спектроскопия комбинационного рассеяния образца игольчатого кокса, полученного в опыте 4 (рис.6). На основании результатов интегрирования полученных пиков рассчитаны их площади (D1 = 1312,53; D2 = 1609,00; D3 = 1498,00; D4 = 1154,77; G = 1584,31) и выполнена полуколичественная оценка доли каждой фазы в образце исследуемого прокаленного игольчатого кокса из опыта 4. Образец состоит в основном из разориентированной графитовой фазы – 69,33 % по массе, что является характерным для турбостратной структуры игольчатого кокса, при этом доля идеальной графитовой фазы составляет 6,10 % по массе, а аморфной фазы – 24,59 % по массе.
Таблица 5
Сканирующая электронная микроскопия
Номер опыта |
Поле обзора, мкм |
Балл микроструктуры |
||
1000 |
66 |
16 |
||
4 |
|
|
|
![]() |
8 |
|
|
|
|
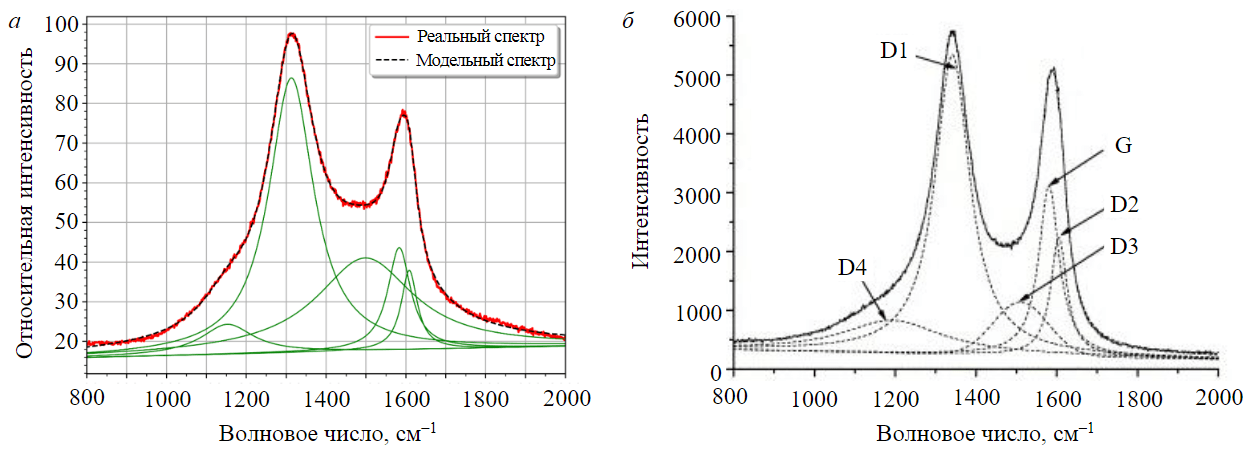
Рис.6. Разложение спектров комбинационного рассеяния: а – для исследуемого образца 4; б – для углеродного материала. D1 – неупорядоченная графитовая решетка (края графенового слоя); D2 – неупорядоченная графитовая решетка (поверхностные слои графена); D3 – аморфный углерод (лоренцевская форма линии); D4 – неупорядоченная графитовая решетка; G – идеальная графитовая решетка
Для уточнения сходимости и достоверности установленных оптимальных параметров процесса коксования и установления возможности реализации этих данных в укрупненном масштабе исследования проводились на установке ЛУЗК с одновременной загрузкой до 80 кг, что соответствовало 100-кратному масштабированию (для каждого реактора). В качестве базового сырья был использован декантойль с модификатором, содержание которого в базовом сырье составляло 10 % по массе. На ЛУЗК проведены два испытания по наработке опытных партий кокса – без применения модификатора (опыт 9) и с его применением (опыт 10). Материальные балансы масштабированных опытных испытаний представлены в табл.6.
Таблица 6
Материальные балансы масштабирования процесса коксования на установке ЛУЗК
Вещество |
Опыт 9 |
Опыт 10 |
|||
Масса, г |
Содержание, % по массе |
Масса, г |
Содержание, % по массе |
||
|
Приход |
|
|||
Декантойль |
20900,00 |
100,00 |
19140,00 |
90,00 |
|
Модификатор |
0,00 |
0,00 |
2126,10 |
10,00 |
|
Итого |
20900,00 |
100,00 |
21266,10 |
100,00 |
|
|
Выход |
|
|||
Сумма дистиллятов |
10880,00 |
52,06 |
11460,00 |
53,89 |
|
Игольчатый кокс |
7060,00 |
33,78 |
7460,00 |
35,08 |
|
Углеводородный газ |
2419,00 |
11,57 |
2126,00 |
10,00 |
|
Потери |
541,00 |
2,59 |
220,10 |
1,03 |
|
Итого |
20900,00 |
100,00 |
21266,10 |
100,00 |
|
Анализ полученных результатов показал, что при масштабном увеличении объема единовременной загрузки основные технологические параметры процесса не выходят за рамки предполагаемого коридора погрешности эксперимента, кроме того, наблюдается заметное сближение качества продукции со значениями аналогов премиального качества. При этом снижался выход углеродного материала и увеличивался выход дистиллятов. Изменение материального баланса обуславливается более высокой глубиной разложения при термолизе малого объема сырья и, как следствие, повышенным выходом кокса.
При сравнительном анализе материальных балансов термолиза модифицированного и немодифицированного сырья наблюдается незначительное увеличение выхода углеродного материала, дистиллятных фракций и снижение доли газообразной фракции за счет увеличения молекулярной массы сырья вследствие внедрения модификатора.
Образцы игольчатых коксов, полученные в ходе опытов 9 и 10, подвергнуты прокалке в токе азота при 1400 °С в течение одного часа c последующей оценкой морфологии модифицированного образца методом сканирующей электронной микроскопии [40, 41]. По результатам оценки полученных СЭМ-изображений можно отметить наличие развитой ламеллярной структуры модифицированного образца (опыт 10), при этом общее поле обзора практически не включает изотропную аморфную фазу, что характерно для качественного игольчатого кокса.
Дальнейшее исследование наработанных в ходе опытных испытаний на установке ЛУЗК образцов игольчатых коксов базового и модифицированного сырья проводилось на базе инженерно-технической лаборатории ООО «Эл 6» (Новочеркасск) для оценки качества партий основным потребителем в России (табл.7).
Таблица 7
Результаты исследования физико-химических свойств игольчатых коксов в ООО «Эл 6»
Показатель |
Метод |
Игольчатый кокс |
Импортный игольчатый кокс (Япония) |
|
Немодифицированный (опыт 9) |
Модифицированный (опыт 10) |
|||
Действительная плотность, г/см3 |
ГОСТ 22898 |
2,14 |
2,14 |
Не менее 2,13 |
Массовая доля золы, % |
ГОСТ 22692 |
0,2 |
0,2 |
Не более 0,3 |
Массовая доля общей серы, % |
ГОСТ 32465 |
0,12 |
0,05 |
Не более 0,40 |
Массовая доля азота, % |
ГОСТ 32979 |
0,24 |
0,22 |
Не более 0,40 |
Балл микроструктуры |
ГОСТ 26132 |
5,3 |
5,8 |
– |
КТЛР 20-520 °С на обожженном электроде, 1 × 10–6 К–1 |
ГОСТ Р 54253 |
2,08 |
1,96 |
– |
По основным физико-химическим свойствам игольчатый кокс на основе модифицированного сырья превосходит образец из базового декантойля, в особенности по показателям «балл микроструктуры» и «КТЛР», что свидетельствует о большей степени структурированности игольчатого кокса из модифицированного сырья, а также подтверждает работу модификатора.
Для получения достоверных результатов на практике оценку КТЛР и удельного электрического сопротивления (УЭС) игольчатого кокса проводят на готовом графитированном электроде. Из наработанных игольчатых коксов были изготовлены образцы электродов, которые затем были направлены на графитацию. Полученные образцы сырых и обожженных механически обработанных электродов представлены на рис.7, а, б, а образцы электродов после графитации при температурах 2800-3000 °С – на рис.7, в.
На основе результатов исследования полученных графитированных электродов основной показатель качества – коэффициент термического линейного расширения – для образца из игольчатого кокса, полученного модификацией сырья термопластичным полимером, принимает более низкие значения и удовлетворяет требования к премиальным маркам (КТЛР < 1 × 10–6 К–1). Требуемая степень графитации двух полученных образцов электродов оценивалась по значению УЭС, которое составляло 7,1-7,4 мкОм × м и соответствовало предъявляемым требованиям к электродам дуговых сталеплавильных печей высокой и сверхвысокой мощности.
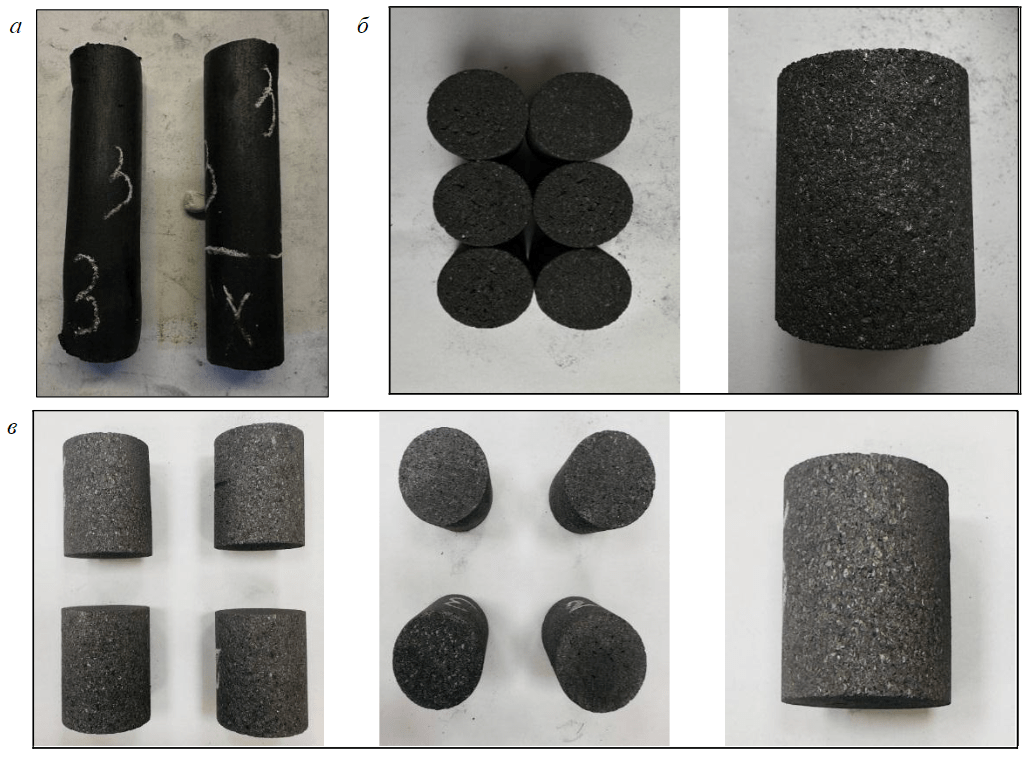
Рис.7. Образцы приготовленных электродов экструзионным прессованием: а – сырые; б – обожженные и механически обработанные; в – графитированные
Заключение
В ходе экспериментальных исследований по получению игольчатого кокса в Санкт-Петербургском горном университете были достигнуты следующие результаты:
- Выполнена аналитическая оценка сырьевых ресурсов, которые необходимы для организации промышленного производства игольчатого кокса в России, – всего 48 техногенных источников: декантойль (58 %), тяжелая смола пиролиза (7 %), каменноугольная смола (24 %) и каменноугольный пек (11 %). В совокупности это составляет более 5 млн т в год, чего теоретически достаточно для производства до 800 тыс. т игольчатого кокса ежегодно. Однако требования к углеводородному составу, содержанию серы и хинолин-нерастворимых веществ обуславливают необходимость специальной подготовки или модификации исходного сырья и непременно сокращают количество практически возможного производства игольчатого кокса.
- На базе Научного центра «Проблем переработки минеральных и техногенных ресурсов» Санкт-Петербургского горного университета был создан уникальный лабораторный комплекс, включающий две установки замедленного коксования – УЗК-1 (загрузка до 0,25 кг) и ЛУЗК (загрузка до 80 кг), которые позволяют устанавливать влияние сырья и технологических параметров процесса на показатели качества игольчатого кокса и свойства графитированных электродов.
- Наиболее качественным для полимерной модификации базовым углеводородным сырьем является декантойль, обладающий низким содержанием серы (до 0,7 %) и асфальтенов (не более 2,8 %), а также высоким содержанием ароматических углеводородов (выше 66 %).
- Тяжелая смола пиролиза является для России потенциально более перспективным базовым сырьем для производства игольчатого кокса, чем декантойль, поскольку практически не содержит серы, при этом включение дополнительных технологических операций для достижения данного показателя в производственную цепочку не требуется. Однако для повышения структурированности игольчатого кокса из тяжелой смолы пиролиза также необходима предварительная полимерная модификация, как и для декантойля.
- Выявлено, что разложение спектров комбинационного рассеяния потенциально является наиболее информативным для оценки степени структурированности игольчатого кокса, поскольку позволяет количественно определять доли идеальной графитовой и аморфной фаз. Данный вид анализа может быть использован в лабораториях наряду с оценкой по баллу микроструктуры или может заменить его, поскольку является менее времязатратным.
- Экспериментально доказана работа модификатора сырья игольчатого кокса – термопластичного полимера ароматического ряда – как для декантойля, так и для тяжелой смолы пиролиза, это подтверждается 100-кратным масштабированием процесса (по результатам оценки КТЛР и балла микроструктуры).
- Выявлено, что наработанные образцы игольчатых коксов после сырьевой модификации в составе шихты хорошо формуются в процессе изготовления электродов экструзионным прессованием и после стандартизированных процедур обжига, механической обработки и графитации при температурах 2800-3000 °С удовлетворяют требованиям к данному виду продукции (КТЛР < 1 ×10–6 К–1 и УЭС 7,1-7,4 мкОм).
- Высокоструктурированный игольчатый кокс, полученный по оригинальной технологии Санкт-Петербургского горного университета при использовании 10 % по массе модификатора, имеет повышенный балл микроструктуры – 5,8, по сравнению с 5,3 без модификации (на укрупненной партии ЛУЗК), ламеллярную структуру с низкой долей аморфной фазы, низкое значение КТЛР электрода 0,897 ×10–6 К–1 (при температуре оценки 20-520 °С), что соответствует по качеству импортным японским аналогам и игольчатому коксу марки SuperPremium.
Литература
- XianXu, LouweiCui, JunheShietal. Effects of co-carbonization of medium and low temperature refined pitch and high temperature refined pitch on the structure and properties of needle coke // Journal of Analytical and Applied Pyrolysis. 2023. Vol. 169. № 105783. DOI: 10.1016/j.jaap.2022.105783
- Yangyang Yu, Feng Wang, Wiafe Biney B. et al. Co-carbonization of ethylene tar and fluid catalytic cracking decant oil: Development of high-quality needle coke feedstock // Fuel. 2022. Vol. 322. № 124170. DOI: 10.1016/j.fuel.2022.124170
- He Liu, Shouhui Jiao, Wenchao Liu et al. Effects of decompressing carbonization on the preparation of needle coke from FCC decant oil // Journal of Analytical and Applied Pyrolysis. 2022. Vol. 162. № 105454. DOI: 10.1016/j.jaap.2022.105454
- Kieush L., Schenk J., Koveria A. et al. Utilization of Renewable Carbon in Electric Arc Furnace-Based Steel Production: Comparative Evaluation of Properties of Conventional and Non-Conventional Carbon-Bearing Sources // Metals. 2023. Vol. 13. Iss.4. № 722. DOI: 10.3390/met13040722
- Бажин В.Ю., Крылов К.А., Шариков Ф.Ю. Обоснование термофизического воздействия на электродную массу для получения равномерной структуры электродов из игольчатого кокса для руднотермических печей // iPolytech Journal. 2023. Т. 27. № 1. С. 161-173. DOI: 10.21285/1814-3520-2023-1-161-173
- Simakov A.S., Trifonova M.E., Gorlenkov D.V. Virtual Analyzer of the Voltage and Current Spectrum of the Electric Arc in Electric Arc Furnaces // Russian Metallurgy (Metally). 2021. Vol. 2021. № 6. P. 713-719. DOI: 10.1134/S0036029521060252
- Polyakov A.A., Gorlanov E.S., Mushihin E.A. Analytical Modeling of Current and Potential Distribution over Carbon and Low-Consumable Anodes during Aluminum Reduction Process // Journal of The Electrochemical Society. 2022. Vol. 169. Iss. 5. № 053502. DOI: 10.1149/1945-7111/ac6a16
- СвергузоваС.В., СапроноваЖ.А., ЗубковаО.С. идр. Пыль электросталеплавильного производства как сырье для получения коагулянта // Записки Горного института. 2023. Т. 260. С. 279-288. DOI: 10.31897/PMI.2023.23
- Xiangye Li, Lei Zhao, Tieshi He et al. Highly conductive, hierarchical porous ultra-fine carbon fibers derived from polyacrylonitrile/polymethylmethacrylate/needle coke as binder-free electrodes for high-performance supercapacitors // Journal of Power Sources. 2022. Vol. 521. № 230943. DOI: 10.1016/j.jpowsour.2021.230943
- Stratiev D., Shishkova I., Yankov V. et al. Impact of H-Oil vacuum residue hydrocracking severity on fluid catalytic cracking unit performance // Petroleum Science and Technology. 2020. Vol. 38. Iss. 6. P. 565-573. DOI: 10.1080/10916466.2020.1772821
- Qi Li, Dongyun Han, Haiyan Qiao et al. Structural evolution of the thermal conversion products of modified coal tar pitch // Carbon Letters. 2023. Vol. 33. Iss. 1. P. 261-271. DOI: 10.1007/s42823-022-00433-8
- Malzahn J., Preciado I., Ding Wang et al. Effect of secondary gas-phase reactions (SGR) in pyrolysis of carbon feedstocks for anisotropic carbon materials production – 1: Controlling SGR to modify intermediate coal tar species to improve pitch anisotropy // Journal of Analytical and Applied Pyrolysis. 2022. Vol. 164. № 105541. DOI: 10.1016/j.jaap.2022.105541
- Bo Wang, Limao Wang, Shuai Zhong et al. Low-Carbon Transformation of Electric System against Power Shortage in China: Policy Optimization // Energies. 2022. Vol. 15. Iss. 4. № 1574. DOI: 10.3390/en15041574
- Guilhot L. An analysis of China’s energy policy from 1981 to 2020: Transitioning towards to a diversified and low-carbon energy system // Energy Policy. 2022. Vol. 162. № 112806. DOI: 10.1016/j.enpol.2022.112806
- Kapustin V.M., Glagoleva V.F. Physicochemical Aspects of Petroleum Coke Formation (Review) // Petroleum Chemistry. 2016. Vol.56. №1. P. 1-9. DOI: 10.1134/S0965544116010035
- Литвинова Т.Е., Сучков Д.В. Комплексный подход к утилизации техногенных отходов минерально-сырьевого комплекса // Горный информационно-аналитический бюллетень. 2022. № 6-1. С. 331-348. DOI: 10.25018/0236_1493_2022_61_0_331
- Cherepovitsyn A., Rutenko E. Strategic Planning of Oil and Gas Companies: The Decarbonization Transition // Energies. 2022. Vol. 15. Iss. 17. № 6163. DOI: 10.3390/en15176163
- Lei Li, Xiongchao Lin, Yukun Zhang et al. Characteristics of the mesophase and needle coke derived from the blended coal tar and biomass tar pitch // Journal of Analytical and Applied Pyrolysis. 2020. Vol. 150. № 104889. DOI: 10.1016/j.jaap.2020.104889
- Kozlov A.P., Cherkasova T.G., Frolov S.V. et al. Innovative Coal-Tar Products at PAO Koks // Coke and Chemistry. 2020. Vol. 63. № 7. P. 344-350. DOI: 10.3103/S1068364X20070054
- Zhichen Zhang, Bin Lou, Ning Zhao et al. Co-carbonization behavior of the blended heavy oil and low temperature coal tar for the preparation of needle coke // Fuel. 2021. Vol. 302. № 121139. DOI: 10.1016/j.fuel.2021.121139
- Litvinenko V.S. Digital Economy as a Factor in the Technological Development of the Mineral Sector // Natural Resources Research. 2020. Vol. 29. № 3. P. 1521-1541. DOI: 10.1007/s11053-019-09568-4
- Smol M., Marcinek P., Duda J., Szołdrowska D. Importance of Sustainable Mineral Resource Management in Implementing the Circular Economy (CE) Model and the European Green Deal Strategy // Resources. 2020. Vol. 9. Iss. 5. № 55. DOI: 10.3390/resources9050055
- Ershov M.A., Savelenko V.D., Makhmudova A.E. et al. Technological Potential Analysis and Vacant Technology Forecasting in Properties and Composition of Low-Sulfur Marine Fuel Oil (VLSFO and ULSFO) Bunkered in Key World Ports // Journal of Marine Science and Engineering. 2022. Vol. 10. Iss. 12. № 1828. DOI: 10.3390/jmse10121828
- ЛитвиненкоВ.С., ПетровЕ.И., ВасилевскаяД.В. идр. Оценка роли государства в управлении минеральными ресурсами // Записки Горного института. 2023. Т. 259. С. 95-111. DOI: 10.31897/PMI.2022.100
- Litvinenko V., Bowbriсk I., Naumov I., Zaitseva Z. Global guidelines and requirements for professional competencies of natural resource extraction engineers: Implications for ESG principles and sustainable development goals // Journal of Cleaner Production. 2022. Vol. 338. № 130530. DOI: 10.1016/j.jclepro.2022.130530
- Andreoli S., Brown S.H., Uppili S., Eser S. Laboratory Coking and a New Optical Texture Classification Parameter: Screening of Petroleum Refinery Streams for Premium Needle Coke Production // Energy & Fuels. 2022. Vol. 36. Iss. 18. P. 10910-10919. DOI: 10.1021/acs.energyfuels.2c02077
- Zhichen Zhang, Hui Du, Shuhai Guo et al. Probing the effect of molecular structure and compositions in extracted oil on the characteristics of needle coke // Fuel. 2021. Vol. 301. № 120984. DOI: 10.1016/j.fuel.2021.120984
- Ismagilov Z.R., Sozinov S.A., Popova A.N., Zaporin V.P. Structural Analysis of Needle Coke // Coke and Chemistry. 2019. Vol. 62. № 4. P. 135-142. DOI: 10.3103/S1068364X19040021
- Dolomatov M.Y., Burangulov D.Z., Dolomatova M.M. et al. Low-Sulphur Vacuum Gasoil of Western Siberia Oil: The Impact of Its Structural and Chemical Features on the Properties of the Produced Needle Coke // Journal of Carbon Research. 2022. Vol. 8. Iss. 1. № 19. DOI: 10.3390/c8010019
- Патент № 2717815 РФ. Способ получения нефтяного игольчатого кокса / В.П.Запорин, С.В.Сухов, К.В.Федотов и др. Опубл. 25.03.2020. Бюл. № 9.
- Bazhin V.Yu. Structural Modification of Petroleum Needle Coke by Adding Lithium on Calcining // Coke and Chemistry. 2015. Vol. 58. № 4. P. 138-142. DOI: 10.3103/S1068364X15040043
- Kondrasheva N.K., Vasilev V.V., Boitsova A.A. Study of Feasibility of Producing High-Quality Petroleum Coke from Heavy Yarega Oil // Chemistry and Technology of Fuels and Oils. 2017. Vol. 52. № 6. P. 663-669. DOI: 10.1007/s10553-017-0758-x
- Sharikov Yu.V., Sharikov F.Yu., Krylov K.A. Mathematical Model of Optimum Control for Petroleum Coke Production in a Rotary Tube Kiln // Theoretical Foundations of Chemical Engineering. 2021. Vol.55. №4. P. 711-719. DOI: 10.1134/S0040579521030192
- Назаренко М.Ю., Салтыкова С.Н. Получение полукокса из горючих сланцев Ленинградского месторождения // Черные металлы. 2022. № 10. С. 4-8. DOI: 10.17580/chm.2022.10.01
- Vinogradova A., Gogolinskii K., Umanskii A. et al. Method of the Mechanical Properties Evaluation of Polyethylene Gas Pipelines with Portable Hardness Testers // Inventions. 2022. Vol.7. Iss.4. № 125. DOI: 10.3390/inventions7040125
- Cултанбеков Р.Р., Щипачев А.М. Проявление несовместимости судовых остаточных топлив: способ определения совместимости, исследования состава топлив и осадка // Записки Горного института. 2022. Т. 257. С. 843-852. DOI: 10.31897/PMI.2022.56
- Sverchkov I.P., Gembitskaya I.M., Povarov V.G., Chukaeva M.A. Method of reference samples preparation for X-ray fluorescence analysis // Talanta. 2023. Vol. 252. № 123820. DOI: 10.1016/j.talanta.2022.123820
- Qingwen Wei, Keliang Pang, Cai Liang et al. The fracture characteristics and enhancement mechanism of crushing strength for the coke with hot pressing // Journal of Analytical and Applied Pyrolysis. 2023. Vol. 171. № 105981. DOI: 10.1016/j.jaap.2023.105981
- Поваров В.Г., Ефимов И.И. Применение модели UNIFAC в расчете физико-химических свойств экотоксикантов для технологических и экоаналитических целей // Записки Горного института. 2023. Т. 260. С. 238-247. DOI: 10.31897/PMI.2023.41
- Savchenkov S.A., Bazhin V.Yu., Povarov V.G. Research on the process of gadolinium recovery from the melt of salts on formation of Mg – Zn – Gd master alloys for manufacturing of magnesium and aluminium special-purpose alloys // Non-ferrous Metals. 2020. № 1. P. 35-40. DOI: 10.17580/nfm.2020.01.06
- Savchenkov S.A., Bazhin V.Yu., Brichkin V.N. et al. Production Features of Magnesium-Neodymium Master Alloy Synthesis // Metallurgist. 2019. Vol. 63. №3-4. P. 394-402. DOI: 10.1007/s11015-019-00835-6