Carbon capture and storage: net zero contribution and cost estimation approaches
Abstract
Carbon capture, utilization, and storage (CCUS) are a combination of necessary and promising technologies that can help reduce CO2 emissions, which are not used on a large scale due to the high cost of solutions. This article aims to review and analyze carbon capture and storage (CCS) projects in terms of their net zero contribution and cost estimates. The study identified a wide range of cost estimation methods that can be applied to CCS projects and revealed such issues as a lack of standardization, limited data, and cost data variability. Still, several common trends were found, including the classification of CCS adopters into low-cost and high-cost industries, cost estimation by CCS step (capture, transportation, storage) and industry (power generation, other sectors), and calculation of relative indices to make comparisons with other decarbonization options. The results of the study can serve as a foundation for developing approaches to estimating the costs of CCS in Russia, which are necessary for planning government support measures and involving businesses in the implementation of these initiatives.
Introduction
Fossil fuels are a cornerstone of the global energy sector, and experts claim the situation is unlikely to change greatly in the coming decades [1]. The extraction and use of fossil fuels are responsible for approximately three-quarters of all greenhouse gas emissions globally. The remaining emissions come from agriculture, forestry, land use management, industrial processes, and waste. In order to increase resource efficiency, reduce the carbon intensity of the global economy, and achieve the Paris Agreement goals, greenhouse gas emissions need to decrease by about 45 % by 2030 (compared to 2010) and then reach net zero by 2050.
The journey toward global carbon neutrality is challenging and unpredictable. The Intergovernmental Panel on Climate Change (IPCC) and the International Energy Agency (IEA) both consider carbon capture, utilization, and storage (CCUS) as necessary measures for decarbonization. The Global CCS Institute reports that in 2022, there were twenty-nine commercial CCUS projects globally, with their number growing. The oil and gas and electric power industries are the leaders in CCUS adoption.
The Strategy for Socio-Economic Development of the Russian Federation with Low Greenhouse Gas Emissions until 2050 includes CCUS technologies in its wide range of measures aimed wat reducing carbon emissions. Russia’s climate regulation is still in its infancy [2] but businesses such as Tatneft, Gazprom Neft, and Novatek are starting to show interest in CCUS projects. That being said, there were no active CCUS projects in Russia in 2022.
Cost estimation is crucial to the widespread adoption of CCUS projects. As some of the sector’s technologies are yet to become economically viable, popular, and mature, so there is a wide range of opinions regarding approaches to estimating the cost of the CC(U)S cycle. The developed approaches are not unified, they are applied pointwise for specific purposes and industries. In order to design better models for the implementation of CCUS projects, it is necessary to review and analyze the existing approaches, methods, and cost estimates suitable for CCUS cost planning. This will boost the adoption of government support measures and promote business interest.
The article aims to answer the following research questions: What is the expected contribution of carbon sequestration technologies to achieving carbon neutrality? What are the general approaches to estimating CCS project costs, including methods and techniques for various industries and steps in the CCS process chain? What factors influence the costs of CCS projects?
Methods
This research presents an analysis of the approaches discussed in analytical materials and scientific articles on cost estimation in the global CCUS sector. The research sources include data from organizations such as IPCC, IEA, the Global CCS Institute, the International Renewable Energy Agency IRENA, the Kearney consulting firm, BP, etc. Around the world, CCUS technologies are still in their early stages of development, which limits the supply of data (especially on feasibility studies) from open sources.
The study is based on open-source data, a content analysis of materials from organizations involved in carbon sequestration projects, and scientific articles. The main research methods include systems, comparative, critical, and cause-and-effect analysis. To address specific problems, methods such as consensus forecasting, systematization, typology, and decomposition were used. Particular attention was paid to expert opinions on the issues discussed, with their analysis and comparison.
Discussion
CCUS: the essence and contribution to achieving carbon neutrality.
Carbon capture, utilization, and storage are part of green technologies, but they are considered as supplements. Experts call CCUS a proven and safe technology [3] for reducing CO2 emissions and a critical component for decarbonizing sectors where other decarbonization options are limited, such as the cement, steel, and chemical industries.
The essence of the technology lies in capturing anthropogenic CO2 emissions from large energy or industrial sources where emissions cannot be prevented or reduced through other means. The CCUS process chain involves capturing CO2 from exhaust gases produced by manufacturers (e.g., steel, chemical, or cement factories), coal-fired power plants, or oil and gas processing facilities, followed by its compression, transportation, utilization (in some cases), and permanent storage in geological formations. The most common use of CO2 is in enhanced oil recovery (CO2-EOR) projects, where it is stored in depleted oil and gas reservoirs.
Depending on the number of steps involved, projects in the CCUS sector are classified into several groups:
- Carbon Capture and Storage (CCS) – a combination of technologies that involve the capture and subsequent permanent disposal of CO2 in deep geological formations;
- Carbon Capture and Utilization (CCU) – a combination of technologies that involve the capture and subsequent use of captured CO2 to produce economically valuable products;
- Carbon Capture, Utilization, and Storage (CCUS) – a combination of the first two groups, which involves the capture, use, and disposal of CO2.
The structure of the CCUS process chain depends on the source of emissions, the method of capture, the mode of transportation, and the intended use of the captured CO2.
Of the twenty-nine active CCUS projects worldwide, only eight do not use the captured carbon dioxide for enhanced oil recovery. Most (fourteen) of the projects are implemented in the United States, followed by China and Canada, each with four projects. Among the ongoing projects, CO2 is captured at fourteen natural gas processing facilities. The first large-scale Direct Air Capture (DAC) facility began operating in Iceland in 2021, capturing CO2 directly from the atmosphere [4]. In all other active projects, anthropogenic CO2 is captured from industrial sources.
This article focuses on CCS projects as they are the most widely used, which makes them easier to analyze. The term “sequestration” means a set of CCS technologies.
Estimates of the total capacity of the currently active CCS projects worldwide range 40-50 Mt CO2 per year. When the projects under development as of 2021 are taken into account, the estimated capacity reaches 149.3 Mt CO2 per year, which is still not enough to achieve climate goals. Although predictions for the future development of carbon capture capacities and their possible contribution to achieving carbon neutrality in the long term vary, they all acknowledge the potential of these technologies.
Based on the IPCC assessment of CO2 capture requirements to keep temperature rise within the climate targets, the Global CCS Institute concluded that global anthropogenic CO2 sequestration should exceed 5 Gt/year by 2050 to offset residual emissions that are difficult to reduce and to balance the global carbon budget. To achieve this goal, the scale of CO2 sequestration will need to demonstrate a more than hundredfold growth over the next three decades. Experts predict the construction of 70 to 100 CCS facilities per year, 100,000 new construction jobs, and 30,000-40,000 permanent jobs for operators and maintenance personnel, with the CCS industry rivalling the size of the global gas sector in the upcoming decades.
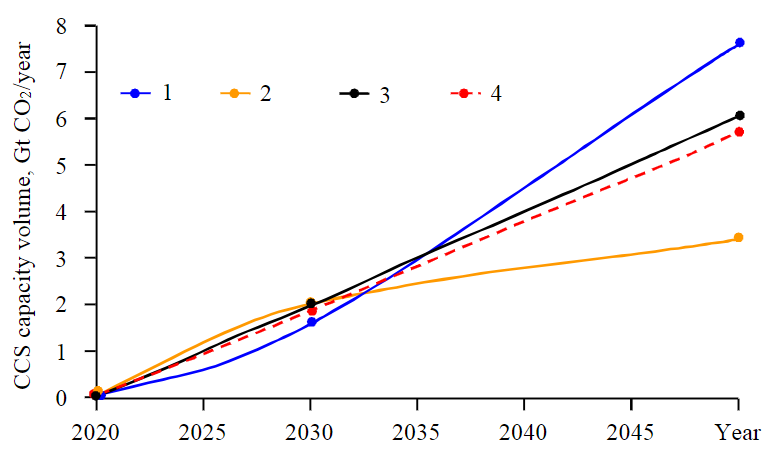
Fig.1. Consensus forecast for CCS capacities if zero emissions are achieved by 2050 1 – IEA; 2 – IRENA; 3 – ВР; 4 – consensus forecast
According to the IEA’s Net Zero scenario aimed at reaching the 1.5 °C target, CCS technologies are not expected to proliferate in the next five years, after which their capacities are projected to grow sharply, reaching 1.6 Gt by 2030 and 7.6 Gt by 2050. BP company, seeing the growing interest in decarbonization worldwide and assuming that the goals set will be achieved, in its Net Zero scenario predicts growth in the total CCS capacity to 6 Gt of CO2 per year by 2050.
The IRENA agency predicts that the amount of CO2 captured will reach 3.4 Gt per year by 2050. It notes that to meet the 1.5 °C target, the scale of CO2 capture needs to grow from 1 to 2 Gt per year by 2030 [5]. The relatively low value of the forecast data is due to the assumption that low-cost renewable energy sources (RES) for many sectors will challenge the CO2 sequestration scenario in combination with the continued use of fossil fuels.
While the growth of global CCS capacities is non-linear and there are no standardized forecasts, possible scenarios for growth in CO2 capture, utilization, and storage capacities over the next 30 years can be presented in the form of a graph based on data available from open sources (Fig.1).
We base our consensus forecast on the idea that growth in total CCS capacities is necessary to achieve the goals of the Paris Agreement.
The gap between the current CCS capacity (40-50 Mt CO2 per year) and the capacity required to achieve these goals (5.8 Gt CO2 per year as per the consensus forecast) is substantial, with a difference of two orders of magnitude. With projected carbon capture rates per year and current annual emissions of 36.3 Gt (2021), it can be estimated that CCS may account for about 16 % of all decarbonization measures. This is consistent with the IEA forecast, which states that CCS might make up approximately 18 % of total decarbonization efforts. All this will require an increase in support measures to enhance the speed and scale of adopting CCS initiatives [6]. The pace of growth in the CCS sector will determine how much investment will be made in such initiatives.
CCS initiatives: general approaches to estimating the costs of their implementation
The cost estimates for CO2 sequestration technologies presented in open sources vary due to the use of different methods and techniques, including expert evaluations, modeling outputs, engineering studies, and the adaptation of previous data [7]. These variations are explained by the fact that cost estimation methods and approaches have evolved along with the evolution of sequestration theory and practice. This makes it crucial to examine and compare the cost parameters of CCS technologies presented in different sources by considering the cost estimation methods used and understanding the main difference between these methods. Table 1 provides an overview of the major approaches used for evaluating CCS technologies in global practice.
Table 1
CCS Cost Estimation Approaches [8, 9]
Approach |
Essence |
Finding the total cost of sequestration per ton of CO2 |
This approach can serve as a standard for various industries and process chains, enabling comparisons with other decarbonization options, such as using renewable energy sources and energy conservation |
Cost estimation: |
|
by process steps |
A standard approach that can be applied to all industries. It estimates costs for each step in the process chain (carbon capture, transportation, and storage) separately to sum them up in different combinations depending on the conditions |
by industry |
This approach focuses on costs for each specific industry and is usually applied when analyzing capture costs for a specific industrial facility |
by BASE and OPTI scenarios |
This approach analyzes base costs (for high-cost capacities) and optimized costs (for improved and low-cost capacities). It can track cost reductions caused by progress in solutions and predict the subsequent improvement in the economic parameters of sequestration |
Splitting CCS adopters into the electric power industry and other industrial sectors |
This approach divides industries into two groups: the electric power industry and other industrial sectors. Different methods are used to estimate costs in each group |
The cost of sequestration per ton of CO2 is the key metric used to evaluate the effectiveness of CCS solutions. It allows for making comparisons between different CCS technology options and with other decarbonization options, including renewable energy sources. CCS technologies have a high cost per ton of CO2, with process costs reaching 199 and 194 dol./t CO2 in industries such as steel and cement production, which is an obstacle to their widespread adoption. In the past eight years, fourteen large-scale CCS projects have been canceled, and it happened due to economic reasons in eleven of the cases. To accurately evaluate CCS costs per ton of CO2, it is crucial to determine whether the captured or avoided CO2 will be used in the calculations. The difference between these two parameters is presented in [8] and reflected in Fig.2.
As the commissioning of CCS facilities increases the total amount of CO2 emissions at the site, the amount of CO2 avoided is always lower than that of CO2 captured. The cost per ton of CO2 is inversely proportional. This makes methods that take into account emissions avoided more accurate. However, CO2 captured is also often used in cost calculations. The cost per ton of CO2 captured becomes particularly relevant when considering capture costs only, as it makes it possible to compare the cost with the market price in the event of CO2 sales and assess the project economic feasibility [9].
There are three methods common for all industries that are used to estimate the costs per ton of emissions avoided [10]. These methods are based on the concept of Levelized Energy Cost (LEC; also Levelized Cost of Energy – LCOE), which is the break-even production price [11]:
where Ei is the amount of electricity generated and sold, MW; P is the electricity price (LCOE), conditional units; Ii is the annual investment in CCS (the amount of investment for the lifecycle of the project divided by the number of years), conditional units; Ci is annual operating CCS costs, conditional units; Fi is fuel costs (as the largest item of operating costs), conditional units; i is the number of years of project operation; r is the discount rate.
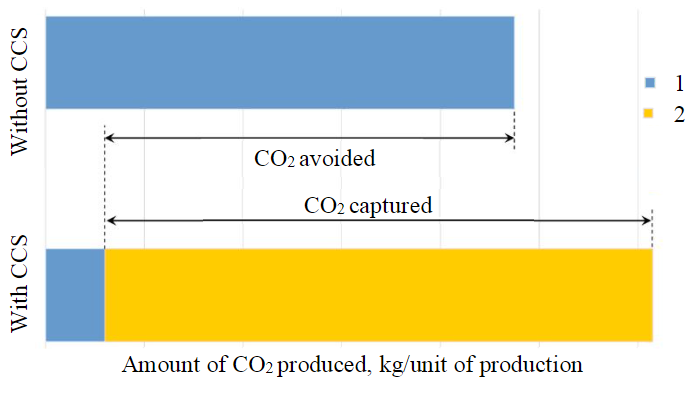
Fig.2. The difference between the mass of CO2 captured and CO2 avoided [8] 1 – emitted; 2 – captured
Formula (1) can be transformed to derive the formula for LCOE, which is defined as the average estimated cost of electricity generation throughout the entire life cycle of a power plant. This indicator was initially used to determine the cost of preventing CO2 emissions in the energy sector [8] but later adapted for industry (Levelized Cost of Key Material – LCOKM):
The first method for estimating the cost per ton emissions avoided is exhaustive and is directly related to the levelized cost of electricity. The essence of the method is to compare the cost of production at a facility with CCS and the same facility without CCS and find the cost of sequestration per ton of CO2:
where are normalized unit costs with CCS and without CCS; , are CO2 emissions per unit of production without CCS and with CCS, t.
Even though this method is quite accurate, its significant drawback is the need to collect a substantial amount of technical and economic data on the object under consideration [10]. If the implementation of a CCS project does not affect the primary production, two methods can be used. The second method factors in the discounted cash flows of the CCS project. The sequestration cost per ton of CO2 can be found as follows
where NPV is the net present value of the CCS project, conditional units; is emissions avoided per year, t.
A third cost estimation method can be used to simplify the calculations. The application of this method requires the assumption that the annual operating costs and the amount of CO2 emissions avoided remain constant throughout the life of the project [10]:
The calculation methods listed above can also be used to estimate costs by industry or process step. The division of the CCS chain into steps is crucial in evaluating the cost of a set of technologies. The total CCS costs consist of the following components [3]: capturing CO2 at the source of emissions, its isolation and purification (for future use), dehydration and compression or liquefaction depending on the transportation method, transportation via pipeline, ship or other means of transport, injection of CO2 underground, and subsequent storage monitoring. Capture typically accounts for about 75 % of the total process chain costs, while transportation and storage account for about 25 %. The cost of capture is also a key factor in estimating the cost of CCS across technology adopters, with industries such as natural gas processing, ethanol production, and ammonia production being relatively cheaper.
The literature on the topic also describes an approach in which both base and optimized costs are evaluated. Base costs (BASE) are a conservative estimate that represents the cost of the first CCS facility/unit constructed immediately after the demonstration phase. Optimized costs (OPTI) are the costs of improved facilities/units that include technological advancements and final solutions. Usually, OPTI costs are lower than BASE costs. Both estimates take into account the improvement and development of technologies after a successful demonstration, but they represent insufficiently mature technologies that will only be available in the long term.
Developments in CCS technology initially focused on energy facilities, but in the last decade, they have been expanding to carbon-intensive industries, including the raw materials sector [12]. The division of industries into power generation and other sectors is based on differences in costing methods. As the primary product of the electric power industry is electricity, which can be used to operate CO2 capture facilities, such indicators can be used as the levelized cost of electricity, considered and based on the increase in the cost of production per unit of electricity produced, as well as taking into account energy losses or reduction in efficiency when comparing the performance of a plant not using CCS to that of the same plant using CCS and others [7].
The partial pressure of CO2 in waste gases from the power industry is significantly lower than in many industrial sources [3]. This is the reason for high capture costs and, subsequently, the high total sequestration costs at power plants. It is important to note that as of the beginning of 2022, only one power plant – the Boundary Dam in Canada – was running a commercial CO2 capture project.
CCS costs at different process chain steps (capture, transportation, and storage): ranges and approaches to estimation.
The CCS process chain can vary depending on the source of emissions, carbon capture method, and options for CO2 transportation and disposal. When evaluating complex CCS solutions, it is necessary to consider different possible combinations. The basic approach to cost estimation involves dividing the process chain into steps (capture, transportation, and storage), after which CCS costs are calculated for each individual step.
Capturing carbon dioxide is usually the most expensive step in the entire CCS process chain, which is one of the reasons why progress in CCS technology has been slow [3]. There are three main CO2 capture methods [13]:
- Post-combustion capture is the most mature, popular (outside the oil and gas sector), and cost-effective technology [14]. It involves removing CO2 from flue gases produced by the combustion of fossil fuels or other carbon-containing materials, such as biomass, and is mainly used in thermal power plants [15, 16]. A notable example is the Boundary Dam project in Canada, which is the world’s first coal-fired power plant to successfully use CCS technology.
- Pre-combustion capture is more energy-efficient than post-combustion, but it requires higher initial capital costs for the integrated gasification combined cycle [13]. It is used to capture CO2 in electricity production and in industries such as chemicals and steel mills. Examples include the Great Plains plant in the United States, where emissions come from synthetic natural gas production, and Coffeyville, where emissions come from a fertilizer plant [17, 18].
- Oxy-fuel combustion is a process in which combustion occurs in an oxygen-enriched environment, resulting in the formation of exhaust gases that consist mainly of CO2 (~ 89 % by volume) and water vapor [16]. This approach is less mature than the other two, but it is actively used in new projects under development [19].
Carbon capture costs are usually calculated as the sum of the capital and operating costs of the plant in U.S. dollars per ton of CO2 captured or avoided. They are called levelized capture costs and usually serve as a basis for comparing CO2 capture facilities ranging in their capacities and applications.
Table 2 presents the cost of capturing one ton of CO2 as reported by different sources (the International Energy Agency – IEA, the U.S. National Petroleum Council – NPC), and Harvard University Belfer Center) at 2019 prices.
Table 2
Carbon capture costs for various emission sources in the U.S. at 2019 prices
Source |
International Energy Agency (IEA) |
National Petroleum Council (NPC) |
Belfer Center |
Coal-fired power plants |
50-100 |
83-268 |
19-128 |
Gas-fired power plants |
n/a |
93-290 |
48-146 |
Cement production |
60-120 |
64-95 |
18-199 |
Steel production |
40-100 |
75-113 |
8-129 |
Hydrogen production |
50-80 |
61-88 |
63-132 |
Ethanol production |
n/a |
24-34 |
25-35 |
Ammonia production |
25-35 |
21-30 |
21-31 |
Natural gas processing |
15-25 |
23-35 |
n/a |
Table 2 shows that the cost of capturing a ton of CO2 varies greatly across industries. This variation is due to a range of factors, including differences in emission sources, facility capacities, electricity costs, equipment, and others. Although the sources demonstrate differences in the values reported, low-cost and high-cost industries can be distinguished, with the former having a narrower range of cost estimates (for example, 21-35 dol. in ammonia production compared to 18-199 dol. in the cement industry).
Figure 3 shows direct air capture costs (according to the IEA) and the ranges of costs at different industrial facilities with the division of CCS adopters into low-cost and high-cost industries.
Carbon capture costs can account for up to three-fourths of the total CCS project costs, particularly in industries such as electricity, cement, and steel, which are considered to be high-cost. One of the factors complicating capture in these industries is the low concentration of CO2 in the off-gas stream. On the contrary, in industries where the off-gas stream contains a high concentration of CO2, such as natural gas processing, ethanol production, and ammonia production, the costs of carbon capture and the entire CCS process chain are much lower [3].
In the production of hydrogen through coal reforming and gasification, the costs will be low if CO2 is captured from a concentrated stream, and the degree of carbon capture will be around 60 % of total emissions [20]. It can be increased to 90 % with additional capture from a low-concentration stream, but this increases the costs. Hence, the hydrogen production industry can either be a high-cost or low-cost CCS adopter.
CO2 transportation is a crucial component of the CCS process chain, linking CO2 capture sources to storage locations. In the current state of the art, pipelines and ships are the two main modes of transportation, with road freight vehicles and rail transport used much less frequently [21]. CO2 transportation through any of these methods is a mature technology [3] that has been tested
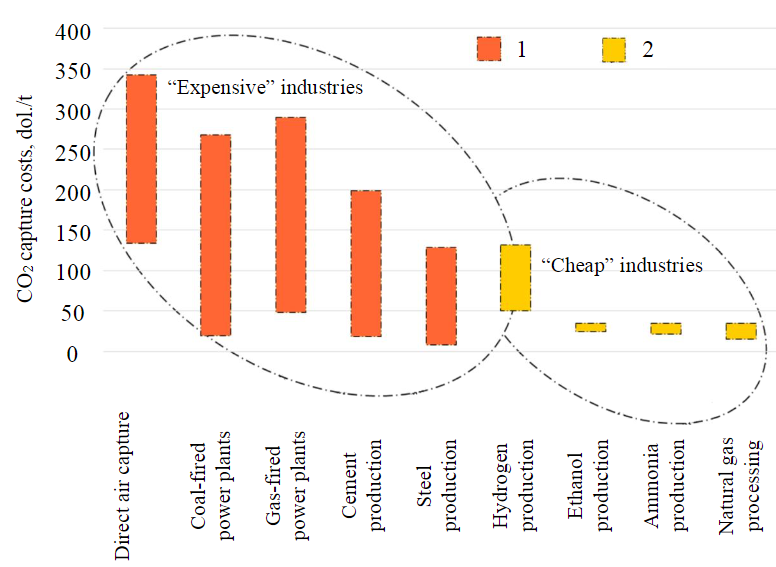
Fig.3. Direct air capture costs and carbon capture costs by industry CO2 concentration: 1 – low; 2 – high
by the gas industry over the last 80 years, although not yet implemented on a large scale. The major share of CO2 is transported through pipelines, with the United States accounting for approximately 85 % of all CO2 pipelines [3]. Other countries with CO2 transportation pipelines include Canada, Brazil, China, the Netherlands, Norway, Saudi Arabia, and the UAE. Maritime transportation of CO2 is technologically similar to the transportation of liquefied natural gas, and it can be assumed that there are no technological obstacles to the use and scaling of this CO2 transportation method. Transportation costs primarily depend on the location of the facility and the existing transport infrastructure. For instance, the cost of transporting two million tons of CO2 per year through pipelines is estimated to range 4-31 dol./t, while maritime transportation is estimated to cost 21-27 dol./t, depending on the distance.
According to a theoretical study by the Zero Emissions Platform, transportation costs depend on the CO2 mass and the transportation distance. If large amounts of CO2 need to be transported over short to medium distances, pipelines are the preferred method, and the cost per ton increases in proportion to the distance. On the other hand, maritime transport requires the preliminary liquefaction of gas, which significantly increases costs and is economically more viable for medium volumes over long distances [22]. The study also found that economies of scale are prominent when transporting gas by pipeline.
Geological storage of carbon dioxideis the final step in the CCS process chain. The technology and other solutions for CO2 injection, storage, and monitoring have long been around and are well-known. CO2 storage requires compression, and in order to maintain high pressure, the storage reservoir should be situated at a depth of at least 800 m [23]. CO2 is usually stored in geological formations comparable to natural water, oil, or gas reservoirs, and the technologies used are similar to those applied in enhanced oil recovery [3].
There are three well-established CO2 storage methods [3]: the injection of CO2 into oil reservoirs for enhanced oil recovery and subsequent storage (CO2-EOR), storage in saline formations, and storage in depleted oil and gas reservoirs [3].
CO2 is injected into the reservoir through a well, where it remains trapped. The process is accompanied by constant monitoring before, during, and after the injection and well shut-in. The first technology (CO2-EOR) together with storage represents a beneficial use of gas for enhanced oil recovery. The other two options are passive storage methods. The majority of CCS projects worldwide are implemented using the CO2-EOR technology. Each of these storage options can be used either onshore or offshore. Most commercial projects currently utilize deep onshore saline formations as storage facilities, while depleted oil and gas reservoirs are mainly used for pilot and demonstration projects due to their lower costs [3].
As CO2 injection and storage monitoring technologies are widely used in the oil and gas industry, they can be adapted for CCS purposes. Estimates of CO2 storage costs in this industry are approximate. They are characterized by a fairly large variation. According to the International Energy Agency (IEA), CO2 storage costs in this industry range 5-55 dol./t. For over 60 % of onshore facilities, they do not exceed 10 dol./t. Offshore, they are less than 40 dol./t in half of the cases. Meanwhile, the National Petroleum Council estimates the cost of onshore CO2 storage in the United States to range 1-18 dol./t, depending on the region and the scale of injection. The main factor influencing CO2 storage costs is the nature of the specific storage facility. It can be concluded that the cost of storage in the early stages of CCS scale-up in each region will be lower, as the cheapest available storage solutions will be used first, while more expensive options will be pursued when more storage capacity is needed.
Some projects reveal their data on the total costs per ton of CO2 transportation and storage.For example, the Northern Lights project, which is the world’s first CO2 transportation and storage infrastructure where CO2 storage is provided as a service, estimates storage costs to range 30-45 dol./t CO2 [3]. The project implementation plan involves transporting CO2 by ships from various ports for disposal in the North Sea.
According to data available in open sources, Russia has enormous potential for CO2 storage facilities. Given the vital role of the oil and gas industry in the Russian economy and the decline in exploration conditions, experts predict the emergence and growth of CO2-EOR technologies in the country in the near future. The IEA and several other organizations estimate that Russia’s storage capacity can become several times greater than in other countries. The total potential for CO2 storage in sedimentary basins, including oil and gas reservoirs and aquifers, is estimated to be 1,213 Gtaccording to sources such as the IEA and the Massachusetts Institute of Technology. The State Balance of Mineral Reserves of the Russian Federation estimates that oil and gas reservoirs suitable for CO2 storage have a capacity of 305 Gt. According to the United Nations Economic Commission for Europe (UNECE), the potential for CO2 storage in Russia’s oil reservoirs is 56 Gt. These estimates lead to the conclusion that the availability of adequate carbon dioxide storage capacities in Russia will facilitate the development of such initiatives.
A system of factors determining CCS costs
Each step in the CCS value chain has a set of factors that influence costs. There are also a number of opportunities for cost reduction (Fig.4).
According to expert estimates, carbon capture costs are inversely proportional to the partial pressure of CO2 in the gas flow as long as other conditions remain equal [24]. This is due to the fact that the partial pressure determines the parameters of process equipment (such as its size and characteristics), the energy costs (the higher the partial pressure, the lower the energy costs), and the available capture technologies, which all contribute to the total cost of capturing and extracting CO2 from the source gas.

Fig.4. Factors determining CCS costs
Capital expenditures of carbon capture facilities often change non-linearly with growth in scale. The proportion is usually exponential [25]:
are capital costs in projects A and B, conditional units; are carbon capture capacities in projects A and B, conditional units; n ranges from 0.6 (one facility) to 0.8 (several facilities).
For a CO2 capture facility, doubling the capacity is expected to increase capital costs by about 50 % [3]. This means that the capital costs per unit of emissions captured or avoided should decrease by about 25 %. Based on this relationship, we can conclude that the effect will be more pronounced with a significant increase in power. Experts recommend that the capacity of capture installations should be greater than 0.4-0.45 Mt/year in order to minimize capture costs [3].
Special attention is given to modularization as a potential cost-reducing factor in CO2 capture facilities. This involves creating standardized units using mass production technologies and incorporating breakthrough innovations, such as improved sorbents, membranes, or innovative carbon capture technologies like Direct Air Capture (DAC). The cost of capture also depends on the cost of electricity and other resources in the area. Given that energy costs play a significant role in the cost of capturing and compressing CO2, utilizing low-cost power sources, such as waste heat, can reduce capture costs by approximately 10-20 dol./t CO2, according to the CCS Global Institute [3].
CO2 capture in high-cost industries has become cheaper over the past decade, and the costs are expected to decrease by 50 % by 2025 compared to 2010 [3]. This is due to the well-known effects of learning and accumulation of experience that accompany the development of any industrial technology [26, 27]. For example, in 2014, carbon capture costs for the Boundary Dam project reached approximately 105 dol./t CO2 (in 2020 prices), while already in 2017, they stood at 70 dol./t CO2 at the U.S.’s Petra Nova plant, which is also a coal-fired facility [28]. Like most projects around the world, Petra Nova uses CO2 for enhanced oil recovery, but its operation was frozen in 2020 due to a sharp drop in oil prices [29].
The location of the project facilities and the available infrastructure will influence CO2 transportation costs. Pipelines, offshore platforms, on-shore facilities, and wells available on site can facilitate the reuse of capacities, thus significantly reducing both the transportation and storage capital costs. Pipeline transportation costs exhibit economies of scale; for a distance of 1 km, the cost per ton of CO2 transported decreases significantly with an annual transportation volume of up to 0.5 Mt per year. However, as the annual volume increases, the cost reduction becomes less pronounced [3]. Hence, the costs are very high for small volumes of transported gas but rapidly decrease as the volume grows and then level off once the amount of transported CO2 reaches millions of tons.
It is more economical to transport CO2 in its liquid state. Compression costs consist of equipment capital costs and energy costs for operating the compressor [3]. Transporting CO2 as gas by ship produces very small economies of scale, and so do the operating costs for compression. An additional reduction in transportation costs can be achieved by creating a transport infrastructure with the integration of different modes of transport, the division of costs within clusters, and a more pronounced manifestation of economies of scale [30].
Large CO2 emitters are usually able to transport CO2 in such volumes that it is cost-effective, to the extent possible. When clusters develop, they serve as the core assets at the node, allowing smaller CO2 emitters to use the pipelines to transport CO2 economically [31].
CO2 storage costs are largely determined by the type of reservoir and the presence of existing infrastructure. The Zero Emissions Platform study found that CO2 storage in poorly explored offshore saline formations without infrastructure is expensive. In contrast, storing CO2 in a well-understood onshore site, such as depleted oil and gas reservoirs with reusable infrastructure, is the most cost-effective option.
It is expected that the scaling up of CCS technologies will make the assessment of potential CO2 storage facilities more routine and, as a result, cheaper. Experts predict a possible reduction of up to 20 % due to the developments in seismic exploration and well drilling techniques taking into account the aspects of CO2 storage [32]. Digitalization and automation will play a crucial role in reducing costs not only at the storage stage but also throughout the entire CCS process chain.
Conclusions. Studies on the topic show that a wide range of cost estimation approaches can be used in the CCS sector, which are difficult to standardize at this stage. There is a high degree of estimation uncertainty and a significant variation in estimates across industries and data sources. This can be explained by the limited number of ongoing projects, the utilization of different cost estimation methodologies (with some relying on theoretical studies and others on actual data), and the difficulties in applying the analogy method since each case is unique. Nevertheless, the general guidelines and conclusions presented in the study can provide a foundation for planning CCS activities in Russia.
It is anticipated that, following global trends, such Russian industries as oil, gas, and energy will be the first to adopt CCS technologies. The dominance of fossil fuels in the global energy mix that is expected to continue over the next 10-15 years. This circumstance makes the adoption of CO2 sequestration options, particularly CO2-EOR technologies, more relevant in Russia [33]. The results of this study suggest that the future of both Russian and global CCS sectors looks promising.
When planning CCS projects, it is crucial to consider factors that significantly impact their costs. For example, small-scale processes should be avoided as they will be very expensive. Also, it is important to pre-plan and model an efficient process chain. A comprehensive understanding of CCS costing aspects in different industries is crucial for informed decision-making, shaping public policy, and designing support measures. As all operating capacities around the world have been developed with the help of regulatory measures or incentives, such as enhanced oil recovery revenues or tax incentives, it can be said that government support is imperative for CCS projects. While CO2-EOR projects may have access to cheap existing transport infrastructure or storage, thereby getting an advantage, they are not cost-effective on their own. The initial stages of the project life cycle and high-cost industries such as electricity, cement, and steel production are where government support measures are especially critical.
In the context of Russia, it is expected that there will be a growing interest in the full range of CCS solutions. In line with this, the Accounts Chamber of the Russian Federation has already begun gathering and analyzing data on the most popular tools for reducing greenhouse gas emissions, including CCS technologies. This proves that the present study is highly relevant.
The development of an efficient system for CO2 transportation is crucial for the widespread adoption of CCS technologies in Russia. Effective planning and strategic investment in large-scale CO2 transport infrastructure are imperative for reducing costs, as well as obtaining accurate data on potential storage reservoirs. In Russia, the exploration of potential CO2 storage sites is still in its early stages, which presents challenges in both the planning and cost estimation of the CCS process chain.
A promising approach for scaling up the CCS market is the formation of clusters consisting of groups of CO2 emitters from various industries that share infrastructure. In this context, Ural, Central, and Northwestern Federal Districts, along with Western Siberia, present promising opportunities for the development of CCS clusters.
Experts consider experience accumulation and personnel training as critical factors for the successful implementation of future CCS projects at a lower cost, as their effects can already be seen in global practice. In addition to experience accumulation, developing related industries, such as new technologies and equipment production, is also necessary to significantly reduce costs. Public perception and the effectiveness of CCS initiatives, as well as their popularization, are other important considerations [34-36].
We plan to continue our research by analyzing the technical and economic aspects of implementing CCS projects in different industries, developing conceptual models, and conducting feasibility studies of CCS pilot projects in Russia.
References
- Global and Russian Energy Outlook. Moscow: Institut energeticheskih issledovanij Rossijskoj akademii nauk – Moskovskaya shkola upravleniya Skolkovo, 2019, p. 210 (in Russian).
- Bashmakov I.A. Russian Low Carbon Development Strategy. Voprosy ekonomiki. 2020. Vol. 7, p. 51-74 (in Russian). DOI: 10.32609/0042-8736-2020-7-51-74
- Kearns D., Liu H., Consoli С. Technology readiness and costs for CCS – March 2021. Global CCS Institute, 2021, p. 50.
- Ozkan M., Nayak S.P., Ruiz A.D., Jiang W.Current status and pillars of direct air capture technologies. iScience. 2022. Vol. 25. Iss. 4. N 103990. DOI: 10.1016/j.isci.2022.103990
- Lyons M., Durrant P., Kochhar K.ReachingZero With Renewnables: Capturing Carbon. Technical Paper. 2021. N 4, p. 108.
- Ilinova A.A., Romasheva N.V., Stroykov G.A. Prospects and social effects of carbon dioxide sequestration and utilization projects. Journal of Mining Institute. Vol. 244, p. 493-502. DOI: 10.31897/PMI.2020.4.12
- Budinis S., Krevor S., Mac Dowell N. et al. An assessment of CCS costs, barriers and potential. Energy strategy reviews. 2018. Vol. 22, p. 61-81. DOI: 10.1016/j.esr.2018.08.003
- Intergovernmental Panel on Climate Change, Working Group III. Special report on carbon dioxide capture and storage. Cambridge: Cambridge University Press, 2005, p. 443.
- Rubin E.S. Understanding the pitfalls of CCS cost estimates. International Journal of Greenhouse Gas Control. 2012. 10, p. 181-190. DOI: 10.1016/j.ijggc.2012.06.004
- Roussanaly S. Calculating CO2 avoidance costs of Carbon Capture and Storage from industry. Carbon Management. 2019. Vol. 10. Iss. 1, p. 105-112. DOI: 10.1080/17583004.2018.1553435
- Rubin E.S., Short C., Booras G. et al.A proposed methodology for CO2 capture and storage cost estimates. International Journal of Greenhouse Gas Control. 2013. Vol. 17. P. 488-503. DOI: 10.1016/j.ijggc.2013.06.004
- Kapetaki Z., Miranda Barbosa E.Carbon capture utilisation and storage: technology market report. Luxembourg: European Commission, Joint Research Centre Publications Office, 2019, p. 55. DOI: 10.2760/89623
- Koytsoumpa E.I., Bergins C., Kakaras E. The CO2 economy: Review of CO2 capture and reuse technologies. The Journal of Supercritical Fluids. 2018. Vol. 132, p. 3-16. DOI: 10.1016/j.supflu.2017.07.029
- Zhiwu L., Wichitpan R., Helei L. et al.Recent progress and new developments in post-combustion carbon-capture technology with amine based solvents. International Journal of Greenhouse Gas Control. 2015. Vol. 40, p. 26-54. DOI: 10.1016/j.ijggc.2015.06.017
- Azarabadi H., Lackner K.S. Postcombustion Capture or Direct Air Capture in Decarbonizing US Natural Gas Power? Environmental Science & Technology. 2020. Vol. 54. Iss. 8, p. 5102-5111. DOI: 10.1021/acs.est.0c00161
- Technology scouting-carbon capture: from today’s to novel technologies. Brussels: Concawe Review, 2021. Vol. 29 (2), p. 11.
- Jansen D., Gazzani M., Manzolini G. et al.Pre-combustion CO2 International Journal of Greenhouse Gas Control. 2015. Vol. 40, p. 167-187. DOI: 10.1016/j.ijggc.2015.05.028
- Madejski P., Chmiel K., Subramanian N., Kús T. Methods and Techniques for CO2 Capture: Review of Potential Solutions and Applications in Modern Energy Technologies. Energies. 2022. Vol. 15. N 887. DOI: 10.3390/en15030887
- Mosleh M.H., Sedighi M., Babaei M., Turner M. 16 – Geological sequestration of carbon dioxide. Managing Global Warming. 2019, p. 487-500. DOI: 10.1016/B978-0-12-814104-5.00016-8
- Soltani R., Rosen M.A., Dincer I. Assessment of CO2 capture options from various points in steam methane reforming for hydrogen production. International Journal of Hydrogen Energy. 2014. Vol. 39. Iss. 35, p. 20266-20275. DOI: 10.1016/j.ijhydene.2014.09.161
- Baroudi H.A., Awoyomi A., Patchigolla K. et al. A review of large-scale CO2 shipping and marine emissions management for carbon capture, utilisation and storage. Applied Energy. 2021. Vol. 287. N 116743. DOI: 10.1016/j.apenergy.2021.116510
- Knoope M.M.J., Ramirez A., Faaij A.P.C. Investing in CO2 transport infrastructure under uncertainty: A comparison between ships and pipelines. International Journal of Greenhouse Gas Control. 2015. Vol. 41, p. 174-193. DOI: 10.1016/j.ijggc.2015.07.013
- Aminu M.D., Nabavi S.A., Rochelle C.A., Manovic V. A review of developments in carbon dioxide storage. Applied Energy. 2017. Vol. 208, p. 1389-1419. DOI: 10.1016/j.apenergy.2017.09.015
- Bains P., Psarras P., Wilcox J.CO2 capture from the industry sector. Science. 2017. Vol. 63, p. 146-172. DOI: 10.1016/j.pecs.2017.07.001
- Tribe M.A., Alpine R.L.W. Scale economies and the “0.6 rule”. Engineering Costs and Production Economics. 1986. Vol. 10. Iss. 4, p. 271-278. DOI: 10.1016/0167-188X(86)90053-4
- Leeson D., Mac Dowell N., Shah N. et al. A Techno-Economic Analysis and Systematic Review of Carbon Capture and Storage (CCS) Applied to the Iron and Steel, Cement, Oil Refining and Pulp and Paper Industries, As Well As Other High Purity PSources. International Journal of Greenhouse Gas Control. 2017. Vol. 61, p. 71-84. DOI: 10.1016/j.ijggc.2017.03.020
- Tcvetkov P. Climate Policy Imbalance in the Energy Sector: Time to Focus on the Value of CO2 Energies. 2021. Vol. 14. Iss. 2. N 411. DOI: 10.3390/en14020411
- Kennedy G.A.Parish Post-Combustion CO2 Capture and Sequestration Demonstration Project. US Department of Energy, 2020. DOI: 10.2172/1608572
- Nessi E., Papadopoulos A.I., Seferlis P. A review of research facilities, pilot and commercial plants for solvent-based post-combustion CO2 capture: Packed bed, phase-change and rotating processes. International Journal of Greenhouse Gas Control. 2021. Vol. 111. N 103474. DOI: 10.1016/j.ijggc.2021.103474
- Sun X., Alcalde J., Bakhtbidar M. et al. Hubs and clusters approach to unlock the development of carbon capture and storage – Case study in Spain. Applied Energy. 2021. Vol. 300. N 117418. DOI: 10.1016/j.apenergy.2021.117418
- Brownsort P.A., Scott V., Haszeldine R.S. Reducing costs of carbon capture and storage by shared reuse of existing pipeline – Case study of a CO2 capture cluster for industry and power in Scotland. International Journal of Greenhouse Gas Control. 2016. Vol. 52, p. 130-138. DOI: 10.1016/j.ijggc.2016.06.004
- Neades S. IEAGHG 2020: Value of Emerging and Enabling Technologies in Reducing Costs, Risks and Timescales for CCS. URL (accessed 28.05.2022).
- Cherepovitsyn A., Fedoseev S., Tcvetkov P. et al. Potential of Russian Regions to Implement CO2-Enhanced Oil Recovery. Energies. 2018. Vol. 11. N 1528. DOI: 10.3390/en11061528
- Fedoseev S.V., Tcvetkov P.S. Key Factors of Public Perception of Carbon Dioxide Capture and Storage Projects. Journal of Mining Institute. Vol. 237, p. 361-368. DOI: 10.31897/PMI.2019.3.361
- Cherepovitsyn A., Chvileva T., Fedoseev S.Popularization of Carbon Capture and Storage Technology in Society: Principles and Methods. International Journal of Environmental Research and Public Health. 2020. Vol. 17. Iss. 14. N 8368. DOI: 10.3390/ijerph17228368
- Vasilev Y., Vasileva P., Tsvetkova A. International review of public perception of CCS technologies. 19th International Multidisciplinary Scientific Geo Conference SGEM, 30 June – 6 July 2019, Albena, Bulgaria. STEF92 Technology, 2019. Vol. 19 (5.1), p. 415-422. DOI: 10.5593/sgem2019/5.1/S20.052