Assessment of the possibility of using leucoxene-quartz concentrate as raw material for production of aluminium and magnesium titanates
- 1 — Ph.D. Associate Professor Mendeleev University of Chemical Technology of Russia ▪ Orcid
- 2 — Ph.D. Associate Professor Perm State National Research University ▪ Orcid
- 3 — Ph.D., Dr.Sci. Head of Department Mendeleev University of Chemical Technology of Russia ▪ Orcid ▪ Elibrary ▪ ResearcherID
Abstract
Leucoxene-quartz concentrate is a large-tonnage by-product of development of the Timan oil-titanium field (oil-saturated sandstones) which is not commercially used at present. High content of titanium compounds (to 50 % by weight) and lack of industrial, cost-effective, and safe technologies for its processing determine a high relevance of the work. Conventional processing technologies allow increasing the concentration of TiO2, but they are only a preparation for complex and hazardous selective chlorination. The process of pyrometallurgical conversion of leucoxene-quartz concentrate into aluminium and magnesium titanates was investigated. It was ascertained that the temperature of solid-phase reaction in Al2O3-TiO2-SiO2 system necessary for the synthesis of aluminium titanate (Al2TiO5) is 1,558 °С, and for MgO-TiO2-SiO2 system – 1,372 °С. Scaling up the process made it possible to synthesize a significant number of samples of titanate-containing products, the phase composition of which was studied by X-ray phase analysis. Two main phases were identified in the products: 30 % aluminium/magnesium titanate and 40 % silicon dioxide. In products of pyrometallurgical processing in the presence of aluminium, phases of pseudobrookite (3.5 %) and titanite (0.5 %) were also found. It was ascertained that in magnesium-containing system the formation of three magnesium titanates is possible: MgTiO3 – 25, Mg2TiO4 – 35, MgTi2O5 – 40 %. Experiments on sulphuric acid leaching of samples demonstrated a higher degree of titanium compounds extraction during sulphuric acid processing. An integrated conceptual scheme for processing leucoxene-quartz concentrate to produce a wide range of potential products (coagulants, catalysts, materials for ceramic industry) was proposed.
Introduction
Currently, there is a growing attention to comprehensive processing of large-tonnage mineral raw materials. Most of mining and processing technologies implemented in the Russian Federation do not meet the requirements of the concept of sustainable development and circular economy (recycling of waste and unconventional resources), and, thus, require significant upgrading. The most striking example is the innovative, strategically important, and extremely promising trend in development of oil sands of Timan field. During oil extraction, thousands of tons of valuable mineral raw material components (in particular, oil-saturated sandstones) are simultaneously extracted to the Earth’s surface. After oil separation, the mineral part is directed for permanent storage to the slag dumps of the facility, which not only has a significant negative environmental impact, but also increases the cost of oil produced (processes of purification and separation, environmental payments, maintenance of the slag dump, etc., are included).
Leucoxene is a mineral aggregate, an alteration product of titanium minerals represented by titanium oxide, quartz, ilmenite, iron, and manganese hydroxides [1, 2]. Flotation concentrate obtained in the process of extraction and beneficiation contains up to 50 % by weight of titanium dioxide in the form of rutile [3, 4]. Further beneficiation of the concentrate is possible due to a high degree of intergrowth of titanium and silicon dioxides. According to various sources [1, 5], up to 60 % of explored and 80 % [1] of undiscovered reserves of titanium minerals (over seven billion tons) in the Russian Federation occur in leucoxene sandstones of Timan fields (Yaregskoye – South Timan, Pizhemskoye – Middle Timan).
Taking into account a high demand for titanium compounds from different sectors, metal [6, 7], pigment, sorbent [8], biomaterial [9] and water treatment agent [10, 11] in industry, the development of new technologies for production of titanium compounds from such raw materials is an extremely urgent task.
Unfortunately, the morphological feature of leucoxene (mutual intergrowth of TiO2 and SiO2) imparts to the aggregate an extremely high chemical resistance to most mineral acids, which significantly reduces the choice of potential processing technologies [12, 13].
At present, this waste is not used commercially (except for experiments on using it as raw material for coagulants or welding electrodes), and its processing with conversion into titanium dioxide, due to its low chemical activity, is possible only by selective chlorination at high temperature.
Technological problems (excessive consumption of highly hazardous gaseous chlorine for chlorination of a relatively useless silicon component, accumulation of unreacted silicon dioxide phase in the chlorinator – clogging of chamber with cake) and a high level of industrial and environmental hazard have a negative impact on the economy of the process and make this method unacceptable for processing large volumes of quartz-leucoxene concentrate.
Over the past 30 years, leading research teams developed the technologies that allow an additional beneficiation of leucoxene-quartz concentrate through desiliconization processes. The most significant developments include: reducing or magnetizing firing [14, 15]; autoclave treatment with alkalis [3, 16, 17]; fluoride leaching [18, 19]; plasma-arc melting [20, 21]; silicon-thermal reduction [22]. All these technologies allow increasing the content of titanium compounds to 85-90 % (synthetic rutile), however, in future, the product is also sent to a technologically unsafe and energy-intensive operation of selective chlorination. In addition, the proposed technologies also significantly affect the cost of the recycling process and have several environmental impacts related to the carbon footprint of the product (gas emissions) and the need to dispose of significant volumes of liquid alkaline waste.
A team of authors at Mendeleev University of Chemical Technology of Russia was the first to propose a comprehensive pyro- and hydrometallurgical technology for processing the concentrate with conversion into pseudo-brookite (reactive) which can be processed according to the traditional sulphuric acid technology [23], which will further expand the range of available technologies and manufactured products.
Methods
The main goal of this work is to evaluate the possibility of producing magnesium and aluminium titanates (first proposed for this type of raw material) by pyrometallurgical processing of leucoxene-quartz concentrate (LQC). To achieve this goal, it is necessary to solve the following tasks: to determine the minimum temperature for the start of phase transformations; to investigate phase composition of the obtained products; to evaluate the efficiency of extracting titanium compounds. The proposed process is innovative and allows expanding the potential trends of processing large-tonnage mineral raw materials, which confirms the relevance of the research.
Individual aluminium and magnesium titanates (fusion of titanium and aluminium/magnesium oxides) are already widely used as catalysts [24, 25], ceramic components [26, 27], and for the needs of other industries [28, 29]. Such major consumer of titanates as ceramic industry suggests that LQC processing products will be in demand on the market due to their low cost.
The product of flotation beneficiation of oil-saturated sandstones of the Yaregskoye field was mixed in equimolar ratios with aluminium oxide (chemically pure) or magnesium oxide (chemically pure) and heated in an oxygen-containing atmosphere to the specified temperatures:
Rejection of inert atmosphere during heat treatment is due to economic and technological reasons.
The study of phase transformations during pyrometallurgical processing of LQC in the presence of various additives was carried out by thermogravimetric analysis (TGA) and high-temperature differential scanning calorimetry (DSC) using Netzsch STA 449 F1 Jupiter device of simultaneous thermal analysis combined with a QMS 443 Aeolos mass spectrometer. Samples were heated at a constant rate of 20 K/min in a dynamic atmosphere of a mixture of argon (20 ml/min) and preliminarily prepared (drying, purification, decarbonization) air (60 ml/min) in the temperature range 40-1,580 °С (heating) and 1,580-1,000 °С (cooling); crucible material is platinum. Calibration was performed by reference substances; baseline correction was accomplished following the procedure supplied together with the device. Temperatures of the presumed phase transformations were compared with data of scientific publications [30, 31].
Phase composition of solid samples was identified by X-ray phase analysis on DRON-3 M diffractometer. Data were deciphered using the PCPDFWIN diffraction database. Quantitative composition was calculated based on comparison with pure substances (comparison of intensities) as well as in accordance with data of X-ray fluorescence (JEOL 1610 LV scanning electron microscope with SSD X-Max Inca Energy energy-dispersive spectrometer) and atomic emission analyses (atomic emission spectrometer with magnetic plasma “SpectroSky”) in accordance with the methods specified by the software.
Products of pyrometallurgical treatment were subjected to sulphatization (sulphuric acid leaching); leaching time was four hours, ratio of solid product to sulphuric acid was 1:20 (wt.), concentration of sulphuric acid varied from 60 to 80 % by weight at boiling point of solution:
Content of metals in sulphuric acid solutions was determined in accordance with the previously developed method of atomic emission spectral analysis with magnetic (microwave) plasma using “SpectroSky” device [32, 33].
Efficiency of extraction of the main components was calculated from the formula:
where Сinit is Ti content in processed subsample; Сsol – amount of Ti passing into solution and calculated from the atomic emission analysis data and corrected based on analysis of untapped sediment.
Results and discussion
Chemical composition of initial sample of leucoxene-quartz concentrate (flotation concentrate), %: TiO2 42.1; SiO2 49.3; FexOy 2.8; Al2O3 2.0; (K, Na)2O 1.5; REE oxides, CaO/MgO 2.3.
Based on the data on chemical composition of the sample, stoichiometric (equimolar) amounts of aluminium and magnesium oxides required for the formation of titanates by reactions (1) and (2) were calculated. Data of synchronous thermal analysis of the process of pyrometallurgical treatment of the LQC + Al2O3 sample are presented in Fig.1.
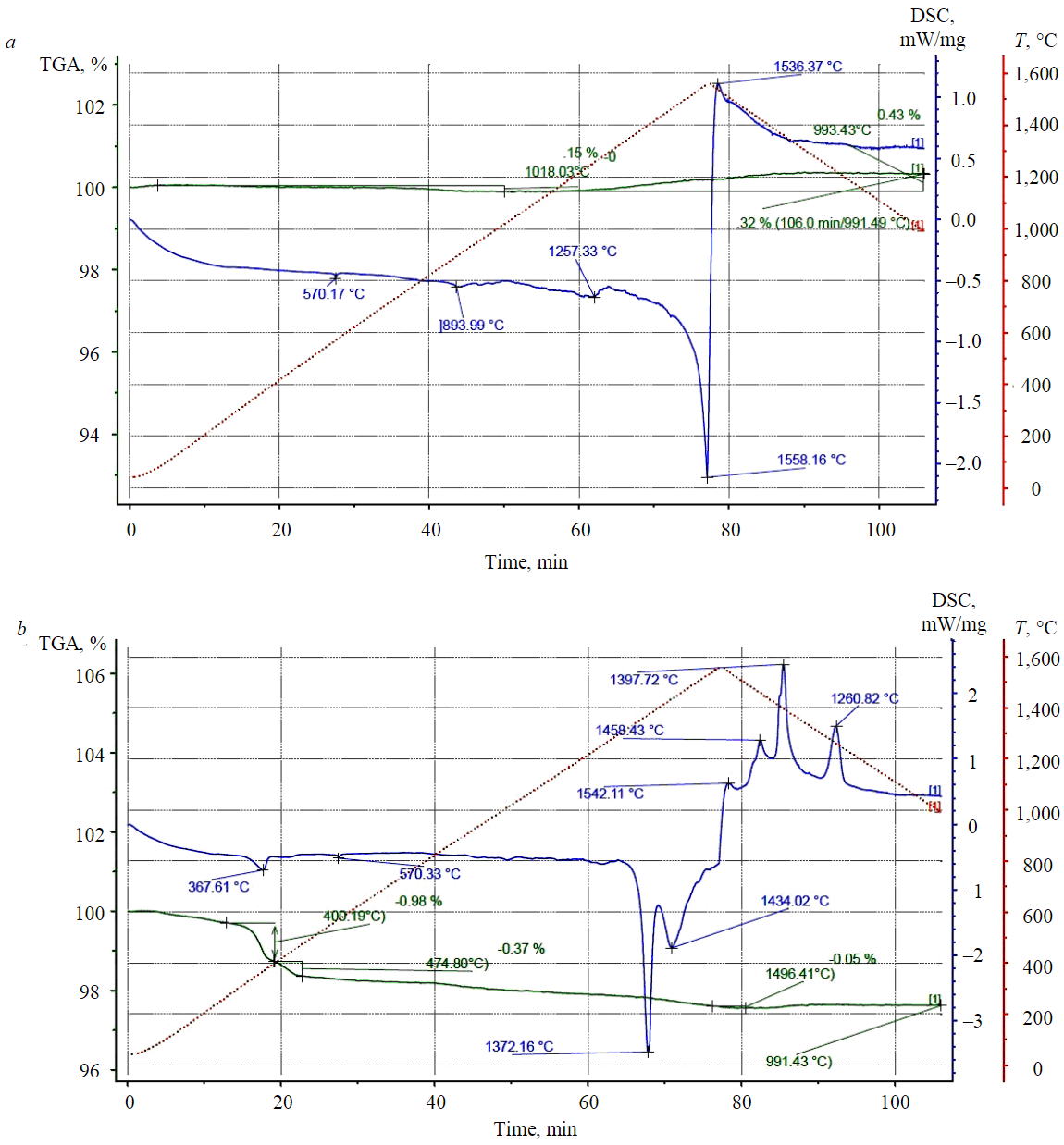
Fig.1. Phase transformations in LQC-Al2O3 (a) and LQC-MgO (b) systems
Figure 1, a shows that the process of phase transformations begins at temperature of about 1,500 °С and is accompanied by a significant endothermic effect – the reaction mixture passes the point of melting and synthesis of titanate. When the reaction mixture is cooled, the melt begins to crystallize, which is confirmed by the corresponding exothermic effect with a peak at 1,536 °C. The data obtained in the experiment are in good agreement with reference information for pure oxide systems [30].
Insignificant endothermic effects recorded in the range of 500-1,400 °С demonstrate decomposition of impurities and phase transformations of components in the reaction mixture. In the process of melting and crystallization of the system, free components capable of oxidation reactions are released from internal cavities of leucoxene grains, and the weight of the sample slightly increases.
Data of simultaneous thermal analysis of pyrometallurgical processing of LQC + MgO sample are presented in Fig.1, b.
Phase transformations in LQC-MgO mixture are much more diverse. Taking into account the ability of magnesium oxide to accumulate and bind CO2 and H2O vapours (hydration) from the environment, two endothermic effects were recorded at temperatures 367 and 570 °С, which corresponds to the processes of crystalline moisture removal and decomposition of impurities. At a temperature of 1,372 °С, an endothermic effect was identified which is characteristic of the process of magnesium titanates formation.
A minor endothermic effect during crystallization can be explained by formation of several compounds: magnesium orthotitanate, titanate, and dititanate. This assumption is confirmed, among other things, by crystallization processes in the sample under study – the DSC curve clearly shows exothermic effects characteristic of crystallization of several phases. Phase transformation temperatures in Fig.1, b are also comparable with temperatures for pure oxide systems presented in [31].
Increased weight of the sample was thermally treated (for LQC-Al2O3 system – 1,550 °С; for LQC-MgO – 1,400 °С) for two hours, and phase composition was analysed. The research results are presented in diffraction patterns (Fig.2).

Fig.2. Phase compositions of LQC-Al2O3 (a) and LQC-MgO (b) samples AT – aluminium titanate; Qw – quartz; Pbs – pseudobrookite; MT – magnesium titanate (MgTiO3); Sph – titanite; M2T – magnesium 2 titanate (MgTi2O5); MOT – magnesium orthotitanate (Mg2TiO4)
Data of X-ray phase analysis presented in the diffraction pattern (Fig.2, a) confirm the presence of aluminium titanate phase in the composition of pyrometallurgical processing products as well as significant amounts of free cristobalite – a high-temperature modification of quartz. The degree of LQC → Al2TiO5 conversion is on average 95-97 %.
Diffraction pattern data (Fig.2, b) confirm the formation of titanium magnesium phases. In the process of high-temperature interaction, the temperature of MgTiO3 formation is exceeded with formation of a eutectic mixture, and, in addition to reaction (2), side reactions (endothermic effects, Fig.1, b) and their inherent processes of crystallization of subcompounds from the binary MgO-TiO2 system become possible (degree of LQC → MgxTiyOz conversion averages 96-98 %):
Based on presented data, phase composition of the products of pyrometallurgical processing was calculated (Table 1).
Table 1
Phase composition of the products of pyrometallurgical LQC processing, %
Sample |
Al2TiO5 |
MgxTiyOz* |
SiO2 |
CaSiTiO5 |
Fe2TiO5 |
TiO2 |
Other impurities |
|
LQC + Al2O3 |
61.7 |
0.2 |
31.7 |
0.50 |
3.60 |
0.1 |
2.2 |
|
LQC + MgO |
– |
52.1 |
40.5 |
0.45 |
0.15 |
0.5 |
6.3 |
* The sum of all forming phases.
Table 1 shows that titanates are the predominant phases in pyrometallurgical processing products. Ranking second in weight is a high-temperature modification of quartz (cristabolite). The product also contains impurities of iron and calcium titanates.
Magnesium titanates are represented by a mixture of three minerals MgTiO3/Mg2TiO4/MgTi2O5 with ratio 25/35/40 %.
Elevated content of impurities (~ 6.5 %) in the system with participation of magnesium compounds can be explained by insufficient temperature (1,400 °С) for the formation of such products as pseudobrookite and aluminium titanate.
Mixtures of titanates and silicon dioxide described in Table 1 can, probably, be separated by flotation by analogy with beneficiation processes of feed ore; however, this process requires significant volumes of samples and was not investigated in this study.
Products of pyrometallurgical processing of LQC were treated with sulphuric acid solutions of various concentrations, and the efficiency of extracting titanium compounds was evaluated (Table 2). The initial leucoxene-quartz concentrate was used as a reference sample.
Table 2
Efficiency of titanium extraction
Sample |
Concentration of H2SO4, % |
||
60 |
70 |
80 |
|
LQC |
17 |
19 |
29 |
LQC + Al2O3 |
42 |
56 |
69 |
LQC + MgO |
75 |
88 |
81 |
From the data of Table 2 it can be concluded that the process of pyrometallurgical processing allows obtai-ning the products that are well exposed by sulphuric acid (higher degree of titanium compounds extraction). The most “efficient” concentration of sulphuric acid for leaching the titanium component from magnesium titanates is 60-70 % by weight, while aluminium titanates required a higher concentration of sulphuric acid (~ 80 % by weight) for complete extraction. Based on the data on composition of solutions (a mixture of titanium and aluminium/magnesium sulphates) according to reactions (3) and (4) and the data of preliminary experiments, a possibility of their use as coagulants for treatment of wastewater from pulp industry [34], surface runoff [35] and other wastewater types [36, 37] was determined.
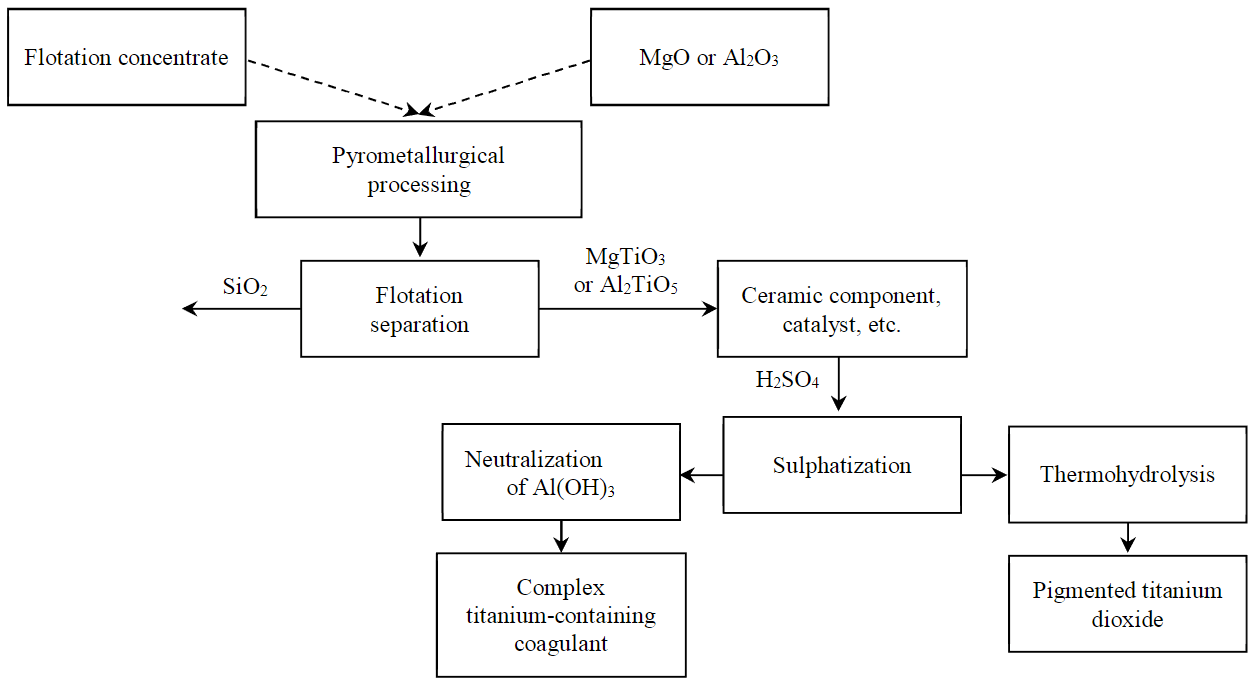
Fig.3. Conceptual diagram of comprehensive LQC processing
Discussion of results
The stage of pyrometallurgical processing proposed in the work with production of titanates can become a part of the concept technology for comprehensive LQC processing (Fig.3).
Quartz-leucoxene enriched to titanium dioxide content ~ 45-50 % is directed to mixing with magnesium/aluminium oxides using drum mills. During mixing, partial grinding of phases occurs which has a positive effect on pyrometallurgical processing. Heat treatment is carried out at temperature not lower than 1,525 °С for LQC-Al2O3 system and 1,400 °С for LQC-MgO system for four hours, while the processing time directly depends on the type of equipment used and can be reduced based on results of pilot industrial tests. The resulting sintered mass is cooled and crushed. Provided there is further hydrometallurgical processing using sulphuric acid, it is possible to obtain solutions of complex titanium-containing coagulants, and in case of thermohydrolysis, titanium dioxide (anatase). When using titanates as a component of ceramics or a catalyst, it is possible to carry out flotation beneficiation (over 90 % for titanates).
Based on preliminary experiments, a possibility of using synthesized titanates as raw material to produce complex titanium-containing coagulants (sulphuric acid processing) or as a precursor for the synthesis of titanium dioxide (magnesium titanate) was established. Beneficiated products can also be used as a ceramic component; however, this hypothesis requires experimental studies by experts.
The proposed technology for processing leucoxene-quartz concentrate can, probably, be applied to similar ores of related fields (Pizhemskoye field of Timan) [1, 38]. Implementation of the proposed scheme as one of alternative directions for processing leucoxene-quartz concentrates will also allow the maximum implementation of the concept of resource saving [39].
Conclusion
As part of the work, a possibility of obtaining aluminium and magnesium titanates by pyrometallurgical processing of large-tonnage waste – leucoxene-quartz concentrate was established for the first time.
It was ascertained that the minimum temperature required for phase transformations in the Al2O3-TiO2-SiO2 system (synthesis of Al2TiO5) is 1,510 °С, and for MgO-TiO2-SiO2 system (synthesis of MgxTiyOz) – 1,375 °С. The conversion degree of initial LQC into titanates averaged 95-98 %.
Phase composition of the products of pyrometallurgical processing of LQC in the presence of aluminium or magnesium oxides was identified. For the aluminium-containing system, the only product is aluminium titanate Al2TiO5), while in magnesium-containing system, the synthesis of intermediate products such as MgTiO3 25 %, Mg2TiO4 35 %, MgTi2O5 40 % was possible.
Phase composition of products for the LQC- Al2O3 system is represented by a mixture of 60 % Al2TiO5 and 30 % SiO2 as well as 10 % impurity compounds, including 3.6 % pseudobrookite (Fe2TiO5) and 0.5 % titanite (CaSiTiO5), and for LQC-MgO system 52 % according to the sum of magnesium titanates, 40 % SiO2 and to 8 % impurities. It should be noted that pseudobrookite and titanite phases were absent in this system (LQC–MgO), which is primarily due to insufficient temperature.
It was proved that the products of pyrometallurgical processing of LQC in the presence of oxide additives in terms of extraction degree of titanium compounds in the process of leaching with sulphuric acid solutions, significantly exceed the initial LQC (on average four to five times), which, subject to the economic feasibility of pyrometallurgical processing, will make it possible to use them as titanium-containing raw material for sulphuric acid technology for titanium oxysulphate/dioxide production or as complex titanium-containing coagulants for water treatment.
According to the preliminary feasibility study, the cost of pyrometallurgical processing of leucoxene-quartz concentrate (reagent and energy costs) with conversion into aluminium or magnesium titanates will be equivalent to the cost of autoclave leaching, but significantly lower than that of selective chlorination processes. The proposed concept technology for the production of titanates does not claim to cover processing of the entire volume of LQC, but is aimed only at a part of raw materials (1-2 % of production volumes) with obtaining products of increased market value (ceramic components, catalysts, coagulants).
The minimum market value (without regard for the demand level) of the products (titanates) obtained in the process proposed by the authors is approximately 30-40 % higher than the cost of titanium concentrate (raw material for the production of titanium dioxide by selective chlorination) obtained by autoclave leaching.
References
- Makeyev A.B., Bryanchaninova N.I., Krasotkina A.O. Unique titanium Deposits of Timan: genesis and age issues. Journal of Mining Institute. 2022. Vol. 255, p. 275-289. DOI: 31897/PMI.2022.32
- Makeev A.B. Typomorphic features of minerals of Ti ores from the Pizhemskoe deposit. 2016. N 1, p. 24-49.
- Zanaveskin K.L. Influence of chemical and granulometric composition of quartz-leucoxene concentrate on its processing with conversion into titanium tetrachloride in fluidized bed reactors. Tsvetnye metally. 2022. N 8, p. 45-55 (in Russian). DOI: 10.17580/tsm.2022.08.06
- Sadykhov G.B., Zablotskaya Y.V., Anisonyan K.G. et al. Extraction of High-Quality Titanium Raw Materials from Leucoxene Concentrates of the Yarega Deposit. Russian Metallurgy (Metally). 2018. Iss. 11, p. 1015-1019. DOI: 10.1134/s0036029518110101
- BykhovskiyZ., Remizova L.I., Chebotareva O.S. The Ore Base of the Titanium in Russia: the Potential of the Development and Evolution. Ferrous Metallurgy. Bulletin of Scientific, Technical and Economic Information. 2017. N 10, p. 16-22 (in Russian).
- Whittaker M.T. Titanium alloys. Metals. 2015. Vol. 5. Iss. 3, p. 1437-1439. DOI: 10.3390/met5031437
- Mathur R., Emproto C., Simon A.C. et al. A Chemical Separation and Measuring Technique for Titanium Isotopes for Titanium Ores and Iron-Rich Minerals. Minerals. 2022. Vol. 12. Iss. 5. N 644. DOI: 10.3390/min12050644
- Neto F.C., Giaretton M.V., Neves G.O. et al. An Overview of Highly Porous Titanium Processed via Metal Injection Molding in Combination with the Space Holder Method. Metals. 2022. Vol. 12. Iss. 5. N 783. DOI: 10.3390/met12050783
- Kaur M., Singh K. Review on titanium and titanium based alloys as biomaterials for orthopaedic applications. Materials Science and Engineering: C. 2019. Vol. 102, p. 844-862. DOI: 1016/j.msec.2019.04.064
- Yonghai Gan, Jingbiao Li, Li Zhang et al.Potential of titanium coagulants for water and wastewater treatment: Current status and future perspectives. Chemical Engineering Journal. 2021. Vol. 406. N 126837. DOI: 1016/j.cej.2020.126837
- Thomas M., Bąk J., Królikowska J.Efficiency of titanium salts as alternative coagulants in water and wastewater treatment: Short review. Desalination and Water Treatment. 2020. Vol. 208, p. 261-272. DOI: 5004/dwt.2020.26689
- Zanaveskin K.L., Maslennikov A.N., Makhin M.N., Zanaveskin L.N. Influence of granulometric composition on leucoxene concentrate processing with titanium tetrachloride obtaining (Yaregskoe deposit). Ore and Metals. N 10, p. 79-85 (in Russian). DOI: 10.17580/tsm.2016.10.11
- Zanaveskin K.L., Meshalkin V.P.Chlorination of Quartz-Leucoxene Concentrate of Yarega Field. Metallurgical and Materials Transactions. 2020. Vol. 51. 3, p. 906-915. DOI: 10.1007/s11663-020-01810-2
- Kopiev D. Yu., Anisonyan K.G., Olyunina T.V., Sadykhov G.B. Effect of the reducing roasting conditions on sulfuric acid recovery of leucoxene concentrate. Ore and Metals. N 11, p. 56-61 (in Russian). DOI: 10.17580/tsm.2018.11.08
- Anisonyan K.G., Sadykhov G.B., Olyunina T.V. et al. Study of the process of magnetizing roasting of leucoxene concentrate. Metally. 2011. N 4, p. 62-66 (in Russian).
- Zablotskaya Yu.V., Sadykhov G.B., Olyunina T.V., Goncharenko T.V. Prospects for development of the Yaregskoye field as a source for obtaining artificial rutile and wollastonite. Chernaya metallurgiya. Byulleten nauchno-tekhnicheskoi i ekonomicheskoi informatsii. 2015. N 9, p. 12-15 (in Russian).
- Rodriguez M.H., Rosales G.D., Pinna E.G. et al.Extraction of titanium from low-grade ore with different leaching agents in autoclave. Metals. 2020. Vol. 10. Iss. 4. DOI: 10.3390/met10040497
- Perovskiy I.А., Burtsev I.N., Ponaryadov A.V., Smorokov A.A.Ammonium fluoride roasting and water leaching of leucoxene concentrates to produce a high grade titanium dioxide resource (of the Yaregskoye deposit, Timan, Russia). Hydrometallurgy. 2022. Vol. 210. N 105858. DOI: 1016/j.hydromet.2022.105858
- Smorokov A.A., Kantaev A.S., Bryankin D.V., Miklashevich A.A. Development of a low-temperature desiliconization method for the leucoxene concentrate of the Yarega deposit with a solution of ammonium hydrogen fluoride. Izvestiya vysshikh uchebnykh zavedenii. khimiya i khimicheskaya tekhnologiya. 2022. Vol. 65. N 2, p. 127-133 (in Russian). DOI: 10.6060/ivkkt.20226502.6551
- Nikolaev A.A., Kirpichev D.E., Nikolaev A.V. Thermophysical Parameters of the Anode Region of Plasma Arc under the Reduction Smelting of Quartz-Leucoxene Concentrate in a Metal-Graphite Reactor. Inorganic Materials: Applied Research. 2020. Vol. 11 (3), p. 563-567. DOI: 10.1134/S207511332003034X
- Nikolaev A.A., Nikolaev A.V., Kirpichev D.E. Separation of Titanium and Silicon Oxides during Plasma-Arc Melting of Quartz-Leucoxene Concentrate. Inorganic Materials: Applied Research. 2022. Vol. 13, p. 716-720. DOI: 10.1134/S2075113322030273
- Istomina E.I., Istomin P.V., Nadutkin A.V., Grass V.E. Desiliconization of leucoxene concentrate through the vacuum silicothermic reduction. Novye ogneupory (New Refractories). N 3, p. 5-9 (in Russian). DOI: 10.17073/1683-4518-2020-3-5-9
- Kuzin E.N., Kruchinina N.E., Fadeev A.B., Nosova T.I. Principles of pyro-hydrometallurgical processing of quartz-leucoxene concentrate with the formation of a pseudobrukite phase. Obogashchenie rud. 2021. N 3, p. 33-38 (in Russian). DOI: 10.17580/or.2021.03.06
- Trung N.Đ., Anh H.C., Tri N., Lộc L.C. Fabrication of TiO2/Al2TiO5 nanocomposite photocatalysts. International Journal of Nanotechnology. 2020. Vol. 17, p. 607-622. DOI: 1504/ijnt.2020.111328
- Maitre S., Mitra R., Nath T.K. Aqueous Mg-Ion Supercapacitor and Bi-Functional Electrocatalyst Based on MgTiO₃ J Nanosci Nanotechnol. 2021. Vol. 21. Iss. 12, p. 6217-6226. DOI: 10.1166/jnn.2021.19321
- Kim I.J., Gauckler L.G. Formation, Decomposition and Thermal Stability of Al2TiO5 Journal of Ceramic Science and Technology. 2012. Vol. 3. Iss. 2, p. 49-60 DOI: 10.4416/JCST2011-00049
- Turdiev D.S. The investigation of heat stability of the ceramic wares for glass melting. Novye ogneupory (New Refractories) Vol. 3, p. 157-159 (in Russian). DOI: 10.17073/1683-4518-2013-3-157-159
- Borkovska L., Khomenkova L., Stara T. et al. Optical and structural properties of Mn-doped magnesium titanates fabricated with excess MgO. Materials Today Communications. 2021. Vol. 27. N 102373. DOI: 10.1016/j.mtcomm.2021.102373
- Goldin B.A., Ryabkov Yu.I., Sitnikov P.A. et al. Synthesis of titanates with ilmenite structure. Izvestiya Komi nauchnogo tsentra Uralskogo otdeleniya Rossiyskoy akademii nauk. Vol. 4 (8), p. 29-34 (in Russian).
- Jianchao Zheng, Xiaojun Hu, Zhongshan Ren et al. Solid-state Reaction Studies in Al2O3–TiO2 System by Diffusion Couple Method. ISIJ International. 2017. Vol. 57. N 10, p. 1762-1766. DOI: 10.2355/isijinternational.isijint-2017-042
- Suzuki Y., Shinoda Y. Magnesium dititanate (MgTi2O5) with pseudobrookite structure: a review. Science and Technology of Advanced Materials. 2011. Vol. 12. Iss. 3. DOI: 10.1088/1468-6996/12/3/034301
- Balaram V., Rahaman W., Roy P. Recent advances in MC-ICP-MS applications in Earth and environmental sciences: Challenges and solutions. Geosystems and Geoenvironment. 2022. Vol. 1. N 100019. DOI: 10.1016/j. geogeo.2021.100019
- Kuchumov V.A., Shoomkin S.S. Analisys of the chemical composition of the bearing alloy used in the production of Sm-Co-based permanent magnets. Global Energy (Materials Science. Power Engineering). Vol. 23. N 1, p. 219-225 (in Russian). DOI: 10.18721/ JEST.230122
- Izmailova N.L., Lorentson A.V., Chernoberezhskii Yu.N. Composite coagulant based on titanyl sulfate and aluminum sulfate. Russian Journal of Applied Chemistry. Vol. 88, p. 458-462 (in Russian). DOI: 10.1134/S1070427215030155
- Krutchinina N., Kuzin E., Azopkov S. et al. Modification of Titanium Coagulant by Sulphate Process. Ecology and Industry of Russia. N 2, p. 24-27 (in Russian). DOI: 10.18412/1816-0395-2017-2-24-27
- Yang Wan, Xin Huang, Baoyou Shi et al. Reduction of organic matter and disinfection byproducts formation potential by titanium, aluminum and ferric salts coagulation for micro-polluted source water treatment. Chemosphere. Vol. 219, p. 28-35. DOI: 10.1016/j.chemosphere.2018.11.117
- Jie Xu, Yanxia Zhao, Baoyu Gao, Qian Zhao. Enhanced algae removal by Ti-based coagulant: comparison with conventional Al- and Fe-based coagulants. Environmental Science and Pollution Research. 2018. Vol. 25. N 13, p. 13147-13158. DOI: 1007/s11356-018-1482-8
- Kotova O.B., Ozhogina E.G., Ponaryadov A.V. Technological mineralogy: development of a comprehensive assessment of titanium ores (exemplified by the Pizhemskoye deposit). Journal of Mining Institute. Vol. 256, p. 632-641. DOI: 10.31897/PMI.2022.78
- Fedoseev S.V., Sanneris Gaida, Tochilo M.V. А analysis and classification of resource saving technologies for reproduction of mineral resources of titanium industry. Journal of Mining Institute. 2016. Vol. 221, р. 756-760 (in Russian). DOI: 10.18454/pmi.2016.5.756
Introduction
Currently, there is a growing attention to comprehensive processing of large-tonnage mineral raw materials. Most of mining and processing technologies implemented in the Russian Federation do not meet the requirements of the concept of sustainable development and circular economy (recycling of waste and unconventional resources), and, thus, require significant upgrading. The most striking example is the innovative, strategically important, and extremely promising trend in development of oil sands of Timan field. During oil extraction, thousands of tons of valuable mineral raw material components (in particular, oil-saturated sandstones) are simultaneously extracted to the Earth’s surface. After oil separation, the mineral part is directed for permanent storage to the slag dumps of the facility, which not only has a significant negative environmental impact, but also increases the cost of oil produced (processes of purification and separation, environmental payments, maintenance of the slag dump, etc., are included).
Leucoxene is a mineral aggregate, an alteration product of titanium minerals represented by titanium oxide, quartz, ilmenite, iron, and manganese hydroxides [1, 2]. Flotation concentrate obtained in the process of extraction and beneficiation contains up to 50 % by weight of titanium dioxide in the form of rutile [3, 4]. Further beneficiation of the concentrate is possible due to a high degree of intergrowth of titanium and silicon dioxides. According to various sources [1, 5], up to 60 % of explored and 80 % [1] of undiscovered reserves of titanium minerals (over seven billion tons) in the Russian Federation occur in leucoxene sandstones of Timan fields (Yaregskoye – South Timan, Pizhemskoye – Middle Timan).
Taking into account a high demand for titanium compounds from different sectors, metal [6, 7], pigment, sorbent [8], biomaterial [9] and water treatment agent [10, 11] in industry, the development of new technologies for production of titanium compounds from such raw materials is an extremely urgent task.
Unfortunately, the morphological feature of leucoxene (mutual intergrowth of TiO2 and SiO2) imparts to the aggregate an extremely high chemical resistance to most mineral acids, which significantly reduces the choice of potential processing technologies [12, 13].
At present, this waste is not used commercially (except for experiments on using it as raw material for coagulants or welding electrodes), and its processing with conversion into titanium dioxide, due to its low chemical activity, is possible only by selective chlorination at high temperature.
Technological problems (excessive consumption of highly hazardous gaseous chlorine for chlorination of a relatively useless silicon component, accumulation of unreacted silicon dioxide phase in the chlorinator – clogging of chamber with cake) and a high level of industrial and environmental hazard have a negative impact on the economy of the process and make this method unacceptable for processing large volumes of quartz-leucoxene concentrate.
Over the past 30 years, leading research teams developed the technologies that allow an additional beneficiation of leucoxene-quartz concentrate through desiliconization processes. The most significant developments include: reducing or magnetizing firing [14, 15]; autoclave treatment with alkalis [3, 16, 17]; fluoride leaching [18, 19]; plasma-arc melting [20, 21]; silicon-thermal reduction [22]. All these technologies allow increasing the content of titanium compounds to 85-90 % (synthetic rutile), however, in future, the product is also sent to a technologically unsafe and energy-intensive operation of selective chlorination. In addition, the proposed technologies also significantly affect the cost of the recycling process and have several environmental impacts related to the carbon footprint of the product (gas emissions) and the need to dispose of significant volumes of liquid alkaline waste.
A team of authors at Mendeleev University of Chemical Technology of Russia was the first to propose a comprehensive pyro- and hydrometallurgical technology for processing the concentrate with conversion into pseudo-brookite (reactive) which can be processed according to the traditional sulphuric acid technology [23], which will further expand the range of available technologies and manufactured products.
Methods
The main goal of this work is to evaluate the possibility of producing magnesium and aluminium titanates (first proposed for this type of raw material) by pyrometallurgical processing of leucoxene-quartz concentrate (LQC). To achieve this goal, it is necessary to solve the following tasks: to determine the minimum temperature for the start of phase transformations; to investigate phase composition of the obtained products; to evaluate the efficiency of extracting titanium compounds. The proposed process is innovative and allows expanding the potential trends of processing large-tonnage mineral raw materials, which confirms the relevance of the research.
Individual aluminium and magnesium titanates (fusion of titanium and aluminium/magnesium oxides) are already widely used as catalysts [24, 25], ceramic components [26, 27], and for the needs of other industries [28, 29]. Such major consumer of titanates as ceramic industry suggests that LQC processing products will be in demand on the market due to their low cost.
The product of flotation beneficiation of oil-saturated sandstones of the Yaregskoye field was mixed in equimolar ratios with aluminium oxide (chemically pure) or magnesium oxide (chemically pure) and heated in an oxygen-containing atmosphere to the specified temperatures:
Rejection of inert atmosphere during heat treatment is due to economic and technological reasons.
The study of phase transformations during pyrometallurgical processing of LQC in the presence of various additives was carried out by thermogravimetric analysis (TGA) and high-temperature differential scanning calorimetry (DSC) using Netzsch STA 449 F1 Jupiter device of simultaneous thermal analysis combined with a QMS 443 Aeolos mass spectrometer. Samples were heated at a constant rate of 20 K/min in a dynamic atmosphere of a mixture of argon (20 ml/min) and preliminarily prepared (drying, purification, decarbonization) air (60 ml/min) in the temperature range 40-1,580 °С (heating) and 1,580-1,000 °С (cooling); crucible material is platinum. Calibration was performed by reference substances; baseline correction was accomplished following the procedure supplied together with the device. Temperatures of the presumed phase transformations were compared with data of scientific publications [30, 31].
Phase composition of solid samples was identified by X-ray phase analysis on DRON-3 M diffractometer. Data were deciphered using the PCPDFWIN diffraction database. Quantitative composition was calculated based on comparison with pure substances (comparison of intensities) as well as in accordance with data of X-ray fluorescence (JEOL 1610 LV scanning electron microscope with SSD X-Max Inca Energy energy-dispersive spectrometer) and atomic emission analyses (atomic emission spectrometer with magnetic plasma “SpectroSky”) in accordance with the methods specified by the software.
Products of pyrometallurgical treatment were subjected to sulphatization (sulphuric acid leaching); leaching time was four hours, ratio of solid product to sulphuric acid was 1:20 (wt.), concentration of sulphuric acid varied from 60 to 80 % by weight at boiling point of solution:
Content of metals in sulphuric acid solutions was determined in accordance with the previously developed method of atomic emission spectral analysis with magnetic (microwave) plasma using “SpectroSky” device [32, 33].
Efficiency of extraction of the main components was calculated from the formula:
where Сinit is Ti content in processed subsample; Сsol – amount of Ti passing into solution and calculated from the atomic emission analysis data and corrected based on analysis of untapped sediment.
Results and discussion
Chemical composition of initial sample of leucoxene-quartz concentrate (flotation concentrate), %: TiO2 42.1; SiO2 49.3; FexOy 2.8; Al2O3 2.0; (K, Na)2O 1.5; REE oxides, CaO/MgO 2.3.
Based on the data on chemical composition of the sample, stoichiometric (equimolar) amounts of aluminium and magnesium oxides required for the formation of titanates by reactions (1) and (2) were calculated. Data of synchronous thermal analysis of the process of pyrometallurgical treatment of the LQC + Al2O3 sample are presented in Fig.1.
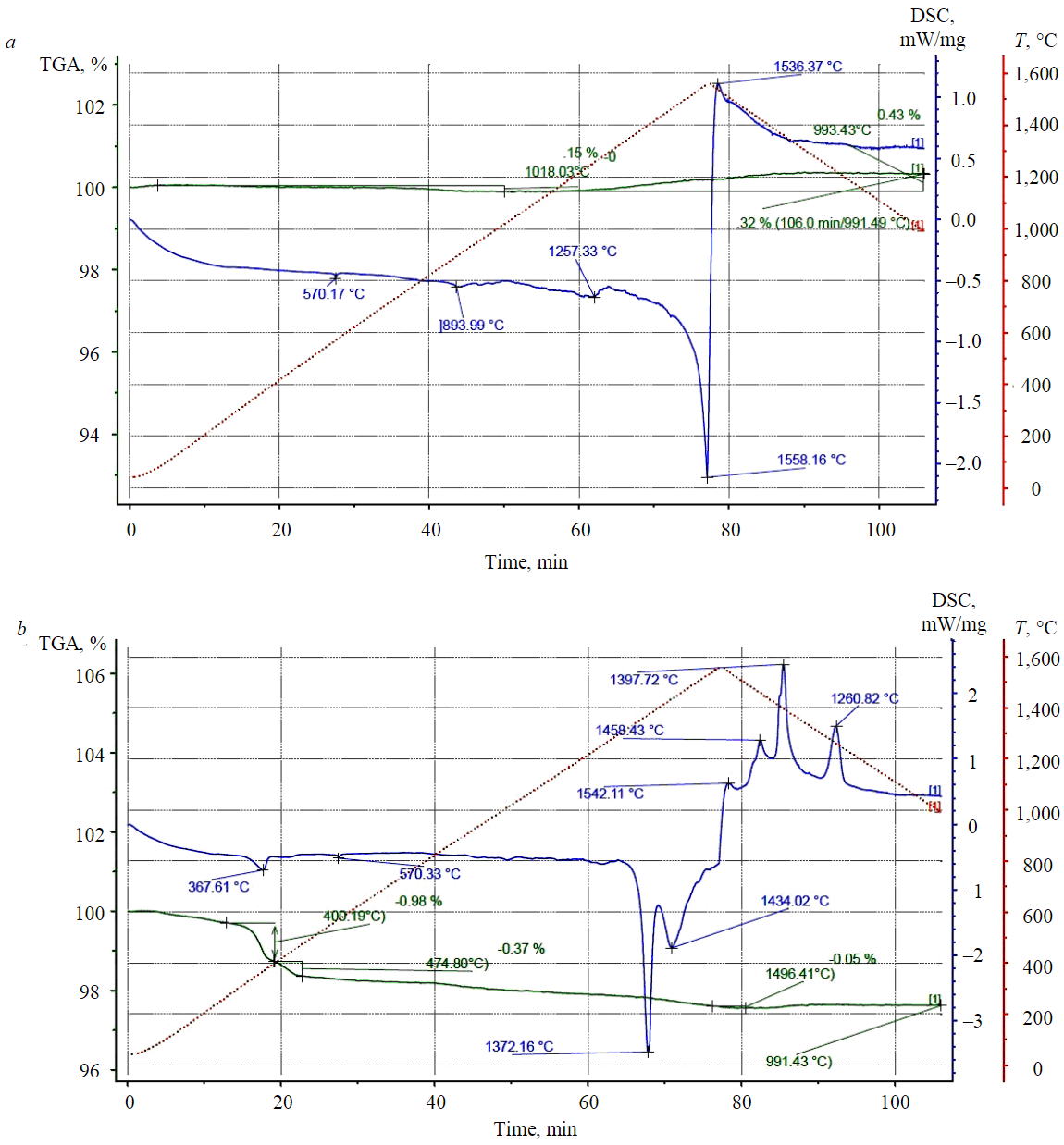
Fig.1. Phase transformations in LQC-Al2O3 (a) and LQC-MgO (b) systems
Figure 1, a shows that the process of phase transformations begins at temperature of about 1,500 °С and is accompanied by a significant endothermic effect – the reaction mixture passes the point of melting and synthesis of titanate. When the reaction mixture is cooled, the melt begins to crystallize, which is confirmed by the corresponding exothermic effect with a peak at 1,536 °C. The data obtained in the experiment are in good agreement with reference information for pure oxide systems [30].
Insignificant endothermic effects recorded in the range of 500-1,400 °С demonstrate decomposition of impurities and phase transformations of components in the reaction mixture. In the process of melting and crystallization of the system, free components capable of oxidation reactions are released from internal cavities of leucoxene grains, and the weight of the sample slightly increases.
Data of simultaneous thermal analysis of pyrometallurgical processing of LQC + MgO sample are presented in Fig.1, b.
Phase transformations in LQC-MgO mixture are much more diverse. Taking into account the ability of magnesium oxide to accumulate and bind CO2 and H2O vapours (hydration) from the environment, two endothermic effects were recorded at temperatures 367 and 570 °С, which corresponds to the processes of crystalline moisture removal and decomposition of impurities. At a temperature of 1,372 °С, an endothermic effect was identified which is characteristic of the process of magnesium titanates formation.
A minor endothermic effect during crystallization can be explained by formation of several compounds: magnesium orthotitanate, titanate, and dititanate. This assumption is confirmed, among other things, by crystallization processes in the sample under study – the DSC curve clearly shows exothermic effects characteristic of crystallization of several phases. Phase transformation temperatures in Fig.1, b are also comparable with temperatures for pure oxide systems presented in [31].
Increased weight of the sample was thermally treated (for LQC-Al2O3 system – 1,550 °С; for LQC-MgO – 1,400 °С) for two hours, and phase composition was analysed. The research results are presented in diffraction patterns (Fig.2).

Fig.2. Phase compositions of LQC-Al2O3 (a) and LQC-MgO (b) samples AT – aluminium titanate; Qw – quartz; Pbs – pseudobrookite; MT – magnesium titanate (MgTiO3); Sph – titanite; M2T – magnesium 2 titanate (MgTi2O5); MOT – magnesium orthotitanate (Mg2TiO4)
Data of X-ray phase analysis presented in the diffraction pattern (Fig.2, a) confirm the presence of aluminium titanate phase in the composition of pyrometallurgical processing products as well as significant amounts of free cristobalite – a high-temperature modification of quartz. The degree of LQC → Al2TiO5 conversion is on average 95-97 %.
Diffraction pattern data (Fig.2, b) confirm the formation of titanium magnesium phases. In the process of high-temperature interaction, the temperature of MgTiO3 formation is exceeded with formation of a eutectic mixture, and, in addition to reaction (2), side reactions (endothermic effects, Fig.1, b) and their inherent processes of crystallization of subcompounds from the binary MgO-TiO2 system become possible (degree of LQC → MgxTiyOz conversion averages 96-98 %):
Based on presented data, phase composition of the products of pyrometallurgical processing was calculated (Table 1).
Table 1
Phase composition of the products of pyrometallurgical LQC processing, %
Sample |
Al2TiO5 |
MgxTiyOz* |
SiO2 |
CaSiTiO5 |
Fe2TiO5 |
TiO2 |
Other impurities |
|
LQC + Al2O3 |
61.7 |
0.2 |
31.7 |
0.50 |
3.60 |
0.1 |
2.2 |
|
LQC + MgO |
– |
52.1 |
40.5 |
0.45 |
0.15 |
0.5 |
6.3 |
* The sum of all forming phases.
Table 1 shows that titanates are the predominant phases in pyrometallurgical processing products. Ranking second in weight is a high-temperature modification of quartz (cristabolite). The product also contains impurities of iron and calcium titanates.
Magnesium titanates are represented by a mixture of three minerals MgTiO3/Mg2TiO4/MgTi2O5 with ratio 25/35/40 %.
Elevated content of impurities (~ 6.5 %) in the system with participation of magnesium compounds can be explained by insufficient temperature (1,400 °С) for the formation of such products as pseudobrookite and aluminium titanate.
Mixtures of titanates and silicon dioxide described in Table 1 can, probably, be separated by flotation by analogy with beneficiation processes of feed ore; however, this process requires significant volumes of samples and was not investigated in this study.
Products of pyrometallurgical processing of LQC were treated with sulphuric acid solutions of various concentrations, and the efficiency of extracting titanium compounds was evaluated (Table 2). The initial leucoxene-quartz concentrate was used as a reference sample.
Table 2
Efficiency of titanium extraction
Sample |
Concentration of H2SO4, % |
||
60 |
70 |
80 |
|
LQC |
17 |
19 |
29 |
LQC + Al2O3 |
42 |
56 |
69 |
LQC + MgO |
75 |
88 |
81 |
From the data of Table 2 it can be concluded that the process of pyrometallurgical processing allows obtai-ning the products that are well exposed by sulphuric acid (higher degree of titanium compounds extraction). The most “efficient” concentration of sulphuric acid for leaching the titanium component from magnesium titanates is 60-70 % by weight, while aluminium titanates required a higher concentration of sulphuric acid (~ 80 % by weight) for complete extraction. Based on the data on composition of solutions (a mixture of titanium and aluminium/magnesium sulphates) according to reactions (3) and (4) and the data of preliminary experiments, a possibility of their use as coagulants for treatment of wastewater from pulp industry [34], surface runoff [35] and other wastewater types [36, 37] was determined.
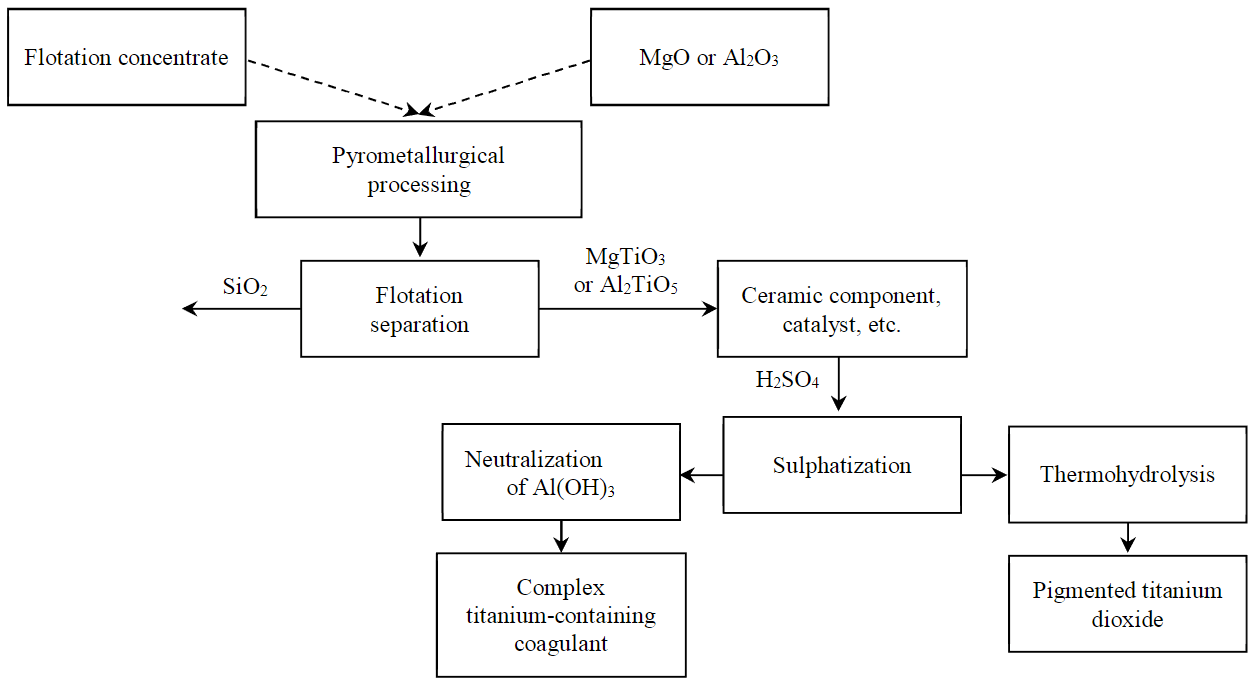
Fig.3. Conceptual diagram of comprehensive LQC processing
Discussion of results
The stage of pyrometallurgical processing proposed in the work with production of titanates can become a part of the concept technology for comprehensive LQC processing (Fig.3).
Quartz-leucoxene enriched to titanium dioxide content ~ 45-50 % is directed to mixing with magnesium/aluminium oxides using drum mills. During mixing, partial grinding of phases occurs which has a positive effect on pyrometallurgical processing. Heat treatment is carried out at temperature not lower than 1,525 °С for LQC-Al2O3 system and 1,400 °С for LQC-MgO system for four hours, while the processing time directly depends on the type of equipment used and can be reduced based on results of pilot industrial tests. The resulting sintered mass is cooled and crushed. Provided there is further hydrometallurgical processing using sulphuric acid, it is possible to obtain solutions of complex titanium-containing coagulants, and in case of thermohydrolysis, titanium dioxide (anatase). When using titanates as a component of ceramics or a catalyst, it is possible to carry out flotation beneficiation (over 90 % for titanates).
Based on preliminary experiments, a possibility of using synthesized titanates as raw material to produce complex titanium-containing coagulants (sulphuric acid processing) or as a precursor for the synthesis of titanium dioxide (magnesium titanate) was established. Beneficiated products can also be used as a ceramic component; however, this hypothesis requires experimental studies by experts.
The proposed technology for processing leucoxene-quartz concentrate can, probably, be applied to similar ores of related fields (Pizhemskoye field of Timan) [1, 38]. Implementation of the proposed scheme as one of alternative directions for processing leucoxene-quartz concentrates will also allow the maximum implementation of the concept of resource saving [39].
Conclusion
As part of the work, a possibility of obtaining aluminium and magnesium titanates by pyrometallurgical processing of large-tonnage waste – leucoxene-quartz concentrate was established for the first time.
It was ascertained that the minimum temperature required for phase transformations in the Al2O3-TiO2-SiO2 system (synthesis of Al2TiO5) is 1,510 °С, and for MgO-TiO2-SiO2 system (synthesis of MgxTiyOz) – 1,375 °С. The conversion degree of initial LQC into titanates averaged 95-98 %.
Phase composition of the products of pyrometallurgical processing of LQC in the presence of aluminium or magnesium oxides was identified. For the aluminium-containing system, the only product is aluminium titanate Al2TiO5), while in magnesium-containing system, the synthesis of intermediate products such as MgTiO3 25 %, Mg2TiO4 35 %, MgTi2O5 40 % was possible.
Phase composition of products for the LQC- Al2O3 system is represented by a mixture of 60 % Al2TiO5 and 30 % SiO2 as well as 10 % impurity compounds, including 3.6 % pseudobrookite (Fe2TiO5) and 0.5 % titanite (CaSiTiO5), and for LQC-MgO system 52 % according to the sum of magnesium titanates, 40 % SiO2 and to 8 % impurities. It should be noted that pseudobrookite and titanite phases were absent in this system (LQC–MgO), which is primarily due to insufficient temperature.
It was proved that the products of pyrometallurgical processing of LQC in the presence of oxide additives in terms of extraction degree of titanium compounds in the process of leaching with sulphuric acid solutions, significantly exceed the initial LQC (on average four to five times), which, subject to the economic feasibility of pyrometallurgical processing, will make it possible to use them as titanium-containing raw material for sulphuric acid technology for titanium oxysulphate/dioxide production or as complex titanium-containing coagulants for water treatment.
According to the preliminary feasibility study, the cost of pyrometallurgical processing of leucoxene-quartz concentrate (reagent and energy costs) with conversion into aluminium or magnesium titanates will be equivalent to the cost of autoclave leaching, but significantly lower than that of selective chlorination processes. The proposed concept technology for the production of titanates does not claim to cover processing of the entire volume of LQC, but is aimed only at a part of raw materials (1-2 % of production volumes) with obtaining products of increased market value (ceramic components, catalysts, coagulants).
The minimum market value (without regard for the demand level) of the products (titanates) obtained in the process proposed by the authors is approximately 30-40 % higher than the cost of titanium concentrate (raw material for the production of titanium dioxide by selective chlorination) obtained by autoclave leaching.
References
- Makeyev A.B., Bryanchaninova N.I., Krasotkina A.O. Unique titanium Deposits of Timan: genesis and age issues. Journal of Mining Institute. 2022. Vol. 255, p. 275-289. DOI: 31897/PMI.2022.32
- Makeev A.B. Typomorphic features of minerals of Ti ores from the Pizhemskoe deposit. 2016. N 1, p. 24-49.
- Zanaveskin K.L. Influence of chemical and granulometric composition of quartz-leucoxene concentrate on its processing with conversion into titanium tetrachloride in fluidized bed reactors. Tsvetnye metally. 2022. N 8, p. 45-55 (in Russian). DOI: 10.17580/tsm.2022.08.06
- Sadykhov G.B., Zablotskaya Y.V., Anisonyan K.G. et al. Extraction of High-Quality Titanium Raw Materials from Leucoxene Concentrates of the Yarega Deposit. Russian Metallurgy (Metally). 2018. Iss. 11, p. 1015-1019. DOI: 10.1134/s0036029518110101
- BykhovskiyZ., Remizova L.I., Chebotareva O.S. The Ore Base of the Titanium in Russia: the Potential of the Development and Evolution. Ferrous Metallurgy. Bulletin of Scientific, Technical and Economic Information. 2017. N 10, p. 16-22 (in Russian).
- Whittaker M.T. Titanium alloys. Metals. 2015. Vol. 5. Iss. 3, p. 1437-1439. DOI: 10.3390/met5031437
- Mathur R., Emproto C., Simon A.C. et al. A Chemical Separation and Measuring Technique for Titanium Isotopes for Titanium Ores and Iron-Rich Minerals. Minerals. 2022. Vol. 12. Iss. 5. N 644. DOI: 10.3390/min12050644
- Neto F.C., Giaretton M.V., Neves G.O. et al. An Overview of Highly Porous Titanium Processed via Metal Injection Molding in Combination with the Space Holder Method. Metals. 2022. Vol. 12. Iss. 5. N 783. DOI: 10.3390/met12050783
- Kaur M., Singh K. Review on titanium and titanium based alloys as biomaterials for orthopaedic applications. Materials Science and Engineering: C. 2019. Vol. 102, p. 844-862. DOI: 1016/j.msec.2019.04.064
- Yonghai Gan, Jingbiao Li, Li Zhang et al.Potential of titanium coagulants for water and wastewater treatment: Current status and future perspectives. Chemical Engineering Journal. 2021. Vol. 406. N 126837. DOI: 1016/j.cej.2020.126837
- Thomas M., Bąk J., Królikowska J.Efficiency of titanium salts as alternative coagulants in water and wastewater treatment: Short review. Desalination and Water Treatment. 2020. Vol. 208, p. 261-272. DOI: 5004/dwt.2020.26689
- Zanaveskin K.L., Maslennikov A.N., Makhin M.N., Zanaveskin L.N. Influence of granulometric composition on leucoxene concentrate processing with titanium tetrachloride obtaining (Yaregskoe deposit). Ore and Metals. N 10, p. 79-85 (in Russian). DOI: 10.17580/tsm.2016.10.11
- Zanaveskin K.L., Meshalkin V.P.Chlorination of Quartz-Leucoxene Concentrate of Yarega Field. Metallurgical and Materials Transactions. 2020. Vol. 51. 3, p. 906-915. DOI: 10.1007/s11663-020-01810-2
- Kopiev D. Yu., Anisonyan K.G., Olyunina T.V., Sadykhov G.B. Effect of the reducing roasting conditions on sulfuric acid recovery of leucoxene concentrate. Ore and Metals. N 11, p. 56-61 (in Russian). DOI: 10.17580/tsm.2018.11.08
- Anisonyan K.G., Sadykhov G.B., Olyunina T.V. et al. Study of the process of magnetizing roasting of leucoxene concentrate. Metally. 2011. N 4, p. 62-66 (in Russian).
- Zablotskaya Yu.V., Sadykhov G.B., Olyunina T.V., Goncharenko T.V. Prospects for development of the Yaregskoye field as a source for obtaining artificial rutile and wollastonite. Chernaya metallurgiya. Byulleten nauchno-tekhnicheskoi i ekonomicheskoi informatsii. 2015. N 9, p. 12-15 (in Russian).
- Rodriguez M.H., Rosales G.D., Pinna E.G. et al.Extraction of titanium from low-grade ore with different leaching agents in autoclave. Metals. 2020. Vol. 10. Iss. 4. DOI: 10.3390/met10040497
- Perovskiy I.А., Burtsev I.N., Ponaryadov A.V., Smorokov A.A.Ammonium fluoride roasting and water leaching of leucoxene concentrates to produce a high grade titanium dioxide resource (of the Yaregskoye deposit, Timan, Russia). Hydrometallurgy. 2022. Vol. 210. N 105858. DOI: 1016/j.hydromet.2022.105858
- Smorokov A.A., Kantaev A.S., Bryankin D.V., Miklashevich A.A. Development of a low-temperature desiliconization method for the leucoxene concentrate of the Yarega deposit with a solution of ammonium hydrogen fluoride. Izvestiya vysshikh uchebnykh zavedenii. khimiya i khimicheskaya tekhnologiya. 2022. Vol. 65. N 2, p. 127-133 (in Russian). DOI: 10.6060/ivkkt.20226502.6551
- Nikolaev A.A., Kirpichev D.E., Nikolaev A.V. Thermophysical Parameters of the Anode Region of Plasma Arc under the Reduction Smelting of Quartz-Leucoxene Concentrate in a Metal-Graphite Reactor. Inorganic Materials: Applied Research. 2020. Vol. 11 (3), p. 563-567. DOI: 10.1134/S207511332003034X
- Nikolaev A.A., Nikolaev A.V., Kirpichev D.E. Separation of Titanium and Silicon Oxides during Plasma-Arc Melting of Quartz-Leucoxene Concentrate. Inorganic Materials: Applied Research. 2022. Vol. 13, p. 716-720. DOI: 10.1134/S2075113322030273
- Istomina E.I., Istomin P.V., Nadutkin A.V., Grass V.E. Desiliconization of leucoxene concentrate through the vacuum silicothermic reduction. Novye ogneupory (New Refractories). N 3, p. 5-9 (in Russian). DOI: 10.17073/1683-4518-2020-3-5-9
- Kuzin E.N., Kruchinina N.E., Fadeev A.B., Nosova T.I. Principles of pyro-hydrometallurgical processing of quartz-leucoxene concentrate with the formation of a pseudobrukite phase. Obogashchenie rud. 2021. N 3, p. 33-38 (in Russian). DOI: 10.17580/or.2021.03.06
- Trung N.Đ., Anh H.C., Tri N., Lộc L.C. Fabrication of TiO2/Al2TiO5 nanocomposite photocatalysts. International Journal of Nanotechnology. 2020. Vol. 17, p. 607-622. DOI: 1504/ijnt.2020.111328
- Maitre S., Mitra R., Nath T.K. Aqueous Mg-Ion Supercapacitor and Bi-Functional Electrocatalyst Based on MgTiO₃ J Nanosci Nanotechnol. 2021. Vol. 21. Iss. 12, p. 6217-6226. DOI: 10.1166/jnn.2021.19321
- Kim I.J., Gauckler L.G. Formation, Decomposition and Thermal Stability of Al2TiO5 Journal of Ceramic Science and Technology. 2012. Vol. 3. Iss. 2, p. 49-60 DOI: 10.4416/JCST2011-00049
- Turdiev D.S. The investigation of heat stability of the ceramic wares for glass melting. Novye ogneupory (New Refractories) Vol. 3, p. 157-159 (in Russian). DOI: 10.17073/1683-4518-2013-3-157-159
- Borkovska L., Khomenkova L., Stara T. et al. Optical and structural properties of Mn-doped magnesium titanates fabricated with excess MgO. Materials Today Communications. 2021. Vol. 27. N 102373. DOI: 10.1016/j.mtcomm.2021.102373
- Goldin B.A., Ryabkov Yu.I., Sitnikov P.A. et al. Synthesis of titanates with ilmenite structure. Izvestiya Komi nauchnogo tsentra Uralskogo otdeleniya Rossiyskoy akademii nauk. Vol. 4 (8), p. 29-34 (in Russian).
- Jianchao Zheng, Xiaojun Hu, Zhongshan Ren et al. Solid-state Reaction Studies in Al2O3–TiO2 System by Diffusion Couple Method. ISIJ International. 2017. Vol. 57. N 10, p. 1762-1766. DOI: 10.2355/isijinternational.isijint-2017-042
- Suzuki Y., Shinoda Y. Magnesium dititanate (MgTi2O5) with pseudobrookite structure: a review. Science and Technology of Advanced Materials. 2011. Vol. 12. Iss. 3. DOI: 10.1088/1468-6996/12/3/034301
- Balaram V., Rahaman W., Roy P. Recent advances in MC-ICP-MS applications in Earth and environmental sciences: Challenges and solutions. Geosystems and Geoenvironment. 2022. Vol. 1. N 100019. DOI: 10.1016/j. geogeo.2021.100019
- Kuchumov V.A., Shoomkin S.S. Analisys of the chemical composition of the bearing alloy used in the production of Sm-Co-based permanent magnets. Global Energy (Materials Science. Power Engineering). Vol. 23. N 1, p. 219-225 (in Russian). DOI: 10.18721/ JEST.230122
- Izmailova N.L., Lorentson A.V., Chernoberezhskii Yu.N. Composite coagulant based on titanyl sulfate and aluminum sulfate. Russian Journal of Applied Chemistry. Vol. 88, p. 458-462 (in Russian). DOI: 10.1134/S1070427215030155
- Krutchinina N., Kuzin E., Azopkov S. et al. Modification of Titanium Coagulant by Sulphate Process. Ecology and Industry of Russia. N 2, p. 24-27 (in Russian). DOI: 10.18412/1816-0395-2017-2-24-27
- Yang Wan, Xin Huang, Baoyou Shi et al. Reduction of organic matter and disinfection byproducts formation potential by titanium, aluminum and ferric salts coagulation for micro-polluted source water treatment. Chemosphere. Vol. 219, p. 28-35. DOI: 10.1016/j.chemosphere.2018.11.117
- Jie Xu, Yanxia Zhao, Baoyu Gao, Qian Zhao. Enhanced algae removal by Ti-based coagulant: comparison with conventional Al- and Fe-based coagulants. Environmental Science and Pollution Research. 2018. Vol. 25. N 13, p. 13147-13158. DOI: 1007/s11356-018-1482-8
- Kotova O.B., Ozhogina E.G., Ponaryadov A.V. Technological mineralogy: development of a comprehensive assessment of titanium ores (exemplified by the Pizhemskoye deposit). Journal of Mining Institute. Vol. 256, p. 632-641. DOI: 10.31897/PMI.2022.78
- Fedoseev S.V., Sanneris Gaida, Tochilo M.V. А analysis and classification of resource saving technologies for reproduction of mineral resources of titanium industry. Journal of Mining Institute. 2016. Vol. 221, р. 756-760 (in Russian). DOI: 10.18454/pmi.2016.5.756