Assessment of the efficiency of occupational safety culture management in fuel and energy companies
Abstract
The results of development, testing and implementation of the process of occupational safety culture management in a fuel and energy company including the assessment of current state, assessment of deviation, formation of control action and its implementation are presented. Using the methods of mathematical analysis, the components of occupational safety culture and criteria for their evaluation were developed. As a control action, a procedure for conducting behavioural safety audit was elaborated and implemented. Proceeding from the results of analysing average ratings of safety culture components among the employees prior to and after the introduction of behavioural safety audit, it was concluded that there was a statistically significant increase in the average values of 12 out of 16 ratings of safety culture components. Analysis of the results of 1,011 audits showed the absence of an “alarm area” at the enterprise. Introduction of the developed process management model promotes an increase in the efficiency of attaining a high level of occupational safety culture in fuel and energy companies.
Introduction
Rosstat notes a high level of production injuries at fuel and energy enterprises: in 2021, 1,743 injured persons (8.1 % of total number) were recorded at mining facilities only, 179 (14.9 % of total number) of them were fatal cases. That is why, under regular changes in national and international requirements of the regulatory framework on labour protection, fuel and energy companies consistently take measures aimed at preserving the life and health of workers as the greatest values [1, 2]. The fact that Russia joined the international movement of zero accident reasonably confirms the readiness of the state to transform the available management mechanisms taking into account global practice and is a necessary condition for the progressive and safe development of the country [3-5].
Modern trends in development of occupational safety are concentrated under the framework of a single conceptual risk-oriented approach, which is based on the methodology for analysing and managing risks of different nature, which is accessible, practically applicable and easily integrated into the existing management systems, and the implementation of which leads to creation of a high culture of occupational safety [6].
With introduction of GOST R ISO 45001-2020 “Occupational safety and health management systems. Requirements and application guidelines” identical to the international standard ISO 45001:2018, the management model underwent progressive changes based on integration of the best practices and processes of occupational health and safety management into the business processes of the organization necessary to achieve its strategic goals. The ideology of the standard rightly puts an equal sign between the assessment of the efficiency of organization on labour protection and the assessment of economic efficiency [7].
Among the key innovations of the standard is introduction of a process approach, which allows the organization managers to carry out rational planning of the processes, coordinate their interaction and control the quality and priority of their implementation. The standard points to the dynamism of the methodology and management practices through evaluation of performance indicators, search for opportunities and continuous improvement of business processes efficiency [7].
At the same time, it should be noted that at present, in the Russian regulatory and legal environment there is no single comprehensive methodology for the quantitative assessment and management of the occupational safety culture taking into account the industry context, and realization of initiatives for its development and implementation is of local nature and is, to a greater extent, within the company's area of responsibility. Therefore, the development of a new quantitative approach to assessing the efficiency of occupational safety culture management is of great scientific and practical importance for the fuel and energy sector.
The purpose of this study is to develop a model for improving the process of managing occupational safety culture at a fuel and energy enterprise as a necessary element in creating a preventive policy to reduce industrial injuries.
The purpose determines the statement and solving of the following main tasks:
- analysis of available methods for assessing the level of occupational safety culture;
- development of the process of occupational safety culture management based on the proprietary methodology of its assessment and person-centred involvement of employees of all professional categories in decision-making process;
- development and implementation as a local regulatory act of the procedure for conducting behavioural safety audit (BSA) as a control action based on monitoring of qualitative and quantitative indicators with a possibility of graphical interpretation of the obtained data;
- assessment of the results of implementation of the developed methodology for conducting the BSA and its impact on safety culture level at the enterprise based on statistical data analysis;
- drawing up a corrective action plan to eliminate the “alarm area”, a plan of activities to improve the level of occupational safety culture and a thematic advanced training program for company managers.
Stagewise implementation of the developed model into management system of the company makes it possible to increase the efficiency of managerial decisions and form the necessary behavioural mechanisms of employees in occupational safety culture.
Methods
Currently, there are a number of methodological approaches [8-12] and private practices to assess the maturity of occupational safety culture in companies [13-16]. The most popular internationally recognized industry models are the Bradley curve, M.Fleming's maturity model and P. Hudson's model. Each of these models is based on the experience of many leading companies and demonstrates the evolution stages of occupational safety management system. Thus, for example, DuPont contains over two million questionnaires in its database covering a wide range of industries in 45 countries and over 10.000 enterprises, which allow visualizing the results of assessing the company's key safety culture indicators in the form of a Bradley curve and comparing with other companies of the industry. The questionnaire contains 24 questions in three blocks: leadership, process and actions, and structure.
P.Hudson's model is based on research conducted over 20 years by psychologists and sociologists in more than 120 large companies around the world in various industries with the support of Shell. The questionnaire contains 18 questions in eight main blocks: leadership and managers commitment to labour protection; involvement of personnel in labour protection; organization, sharing responsibility on labour protection, allocation of resources and standards; risk management and workplace safety; operating procedures and instructions; incident reporting, investigation and analysis; information and communication on labour protection; audit and analysis [17].
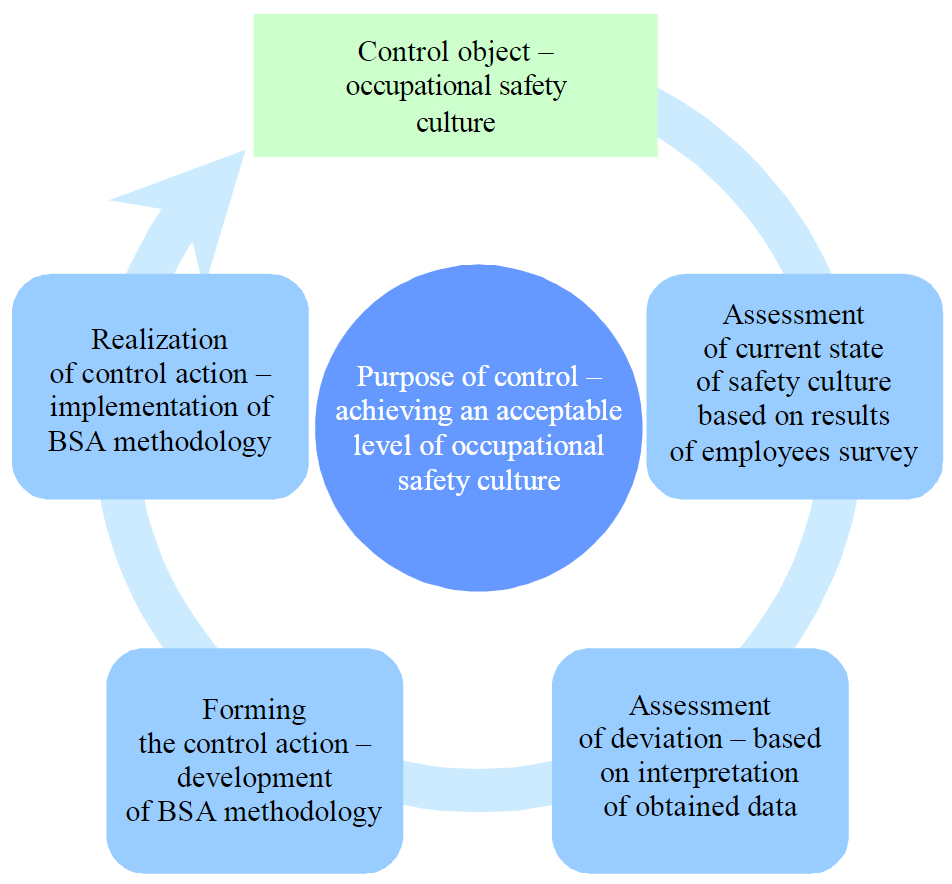
Fig.1. Scheme of the process model of occupational safety culture management system
In the course of the II All-Russian study of the practices of safety culture, labour protection and occupational safety conducted in 2019 with participation of over 600 employees and managers of different industrial enterprises in the country, an adapted model of P. Hudson was used. As a result, it was concluded that 57 % of companies are at a reactive level of occupational safety culture (characterized by a relatively formal attitude of employees to occupational safety issues and response to incidents that had already occurred), 35 % are at an engaging level (having low injury rates due to awareness of employees of responsibility for their own safety in the absence of a significant progress due to a lower efficiency of the available procedures compared to companies with a higher level of occupational safety culture).
In this study, an assessment of the level of occupational safety culture of a fuel and energy company of Russia was carried out using the method of a two-stage survey of employees, for the implementation of which two questionnaires were specially drawn up. The first questionnaire included 10 questions allowing to assess certain sociobiographic characteristics of employees (age, length of service, position held, etc.). The second questionnaire contained questions to assess 16 identified safety culture components [18].
To manage the occupational safety culture in terms of the management system, a process model was developed based on the principles of GOST R ISO 45001-2020 (Fig.1).
According to the developed model, the control object is occupational safety culture, and the goal of control is to achieve its acceptable level. The developed control model was tested and implemented in one of pipeline companies.
Assessment of the current state of occupational safety culture was accomplished in the study [18] based on the methods of statistical data analysis using the results of a two-stage survey of 614 employees of a pipeline company. The values of average assessments of safety culture components were identified with further cluster and variance analyses.
The next element of the developed model is the assessment of deviation, which is the interpretation of data obtained from the assessment of the current state of data and taking decisions on the acceptability of risks as well as the development of necessary measures on occupational safety in accordance with the concept of the risk-oriented approach. Thus, 152 (24.8 %) of the 614 surveyed employees rated safety culture in their organization at a low level (the remaining 75.2 % – at medium and high). Among them are mainly employees who do not believe that it is possible to fulfil all safety requirements and are not ready to interrupt the technological process when violations of safety requirements are detected.
As a response to the identified deviations, another element of the process model is formation of control action. In this study, the control action is interpreted as the BSA procedure which became widespread in the international practice and involves the observation and discussion by the manager of the employee’s actions and conditions at his workplace, the assessment of the identified hazardous actions/conditions and the use, if necessary, of preventive measures. Psychological aspects of the BSA procedure with good reason distinguish it from other types of control and allow changing the attitude of employees to safety involving them in co-management of occupational safety culture regardless of experience and position.
As part of the study, a methodological approach to assessing and monitoring the BSA results was developed which provides for the auditor to fill out a report form during conversation in which all the identified violations are noted and proposals for preventing their recurrence as well as corrective actions [19]. The analysis of the observed actions/conditions is carried out in seven categories (response of the employee/employees, actions of the employee/employees, workwear and PPE, tools and equipment, rules and regulations, workplace, transport). For each category of observation, from 3 to 12 (40 in total) audit criteria were developed. Description of the employee's actions or conditions at his workplace for the observed categories is evaluated in terms of compliance with one of two qualitative indicators: “hazardous” and “not applicable”. The BSA results are analysed to determine a number of quantitative indicators including No (average value of hazard indicators of one performed audit based on results of all audits conducted over a selected period of time) and Nionl (average value of hazard indicators of the observed category of one performed audit based on results of all audits conducted for a selected period of time). When developing hazard indicators, the approach of computation ease, practical value with the required degree of detail and the possibility of visualizing the results was applied. It should be noted that based on the outcomes of testing the developed recommendations for organizing and evaluating the BSA results, a local regulatory act of the fuel and energy company was approved and put into effect.
Final element of the control model is presented as realization of control action – dynamic implementation of the developed methodology for conducting BSA at the pipeline enterprise under study, analysis of the results obtained and taking corrective actions and proactive measures [19].
To assess the efficiency of control action on the control object, it is necessary to re-survey the employees for determining the current level of occupational safety culture comparing the data obtained with the data of initial assessment. 1,173 employees of the pipeline company participated in the repeated survey. Taking into account different number of employees who took part in the initial and repeated surveys (614 and 1,173 persons, respectively), for comparing the results, it is necessary to comply with the representative sample condition. One of determining factors contributing to resolving the problem of a reasonable choice of the population size is the knowledge of characteristics of the universe (composition and structure of objects, composition of features and a possibility of their measurement, number, temporal and spatial determination). The analysis of these characteristics (both at the stage of sampling, and at the stage of logical statistical processing of dataset obtained) allows drawing conclusions about representativeness of the sampling population. At the same time, when constructing a representative sample model, it is possible to ensure validity of the results [20]. Thus, all employees were divided into groups depending on their belonging to one of three professional categories: workers, specialists and managers. A histogram of the distribution of average ratings of safety culture components based on the results of initial and repeated assessments for various categories of employees was constructed (Fig.2).
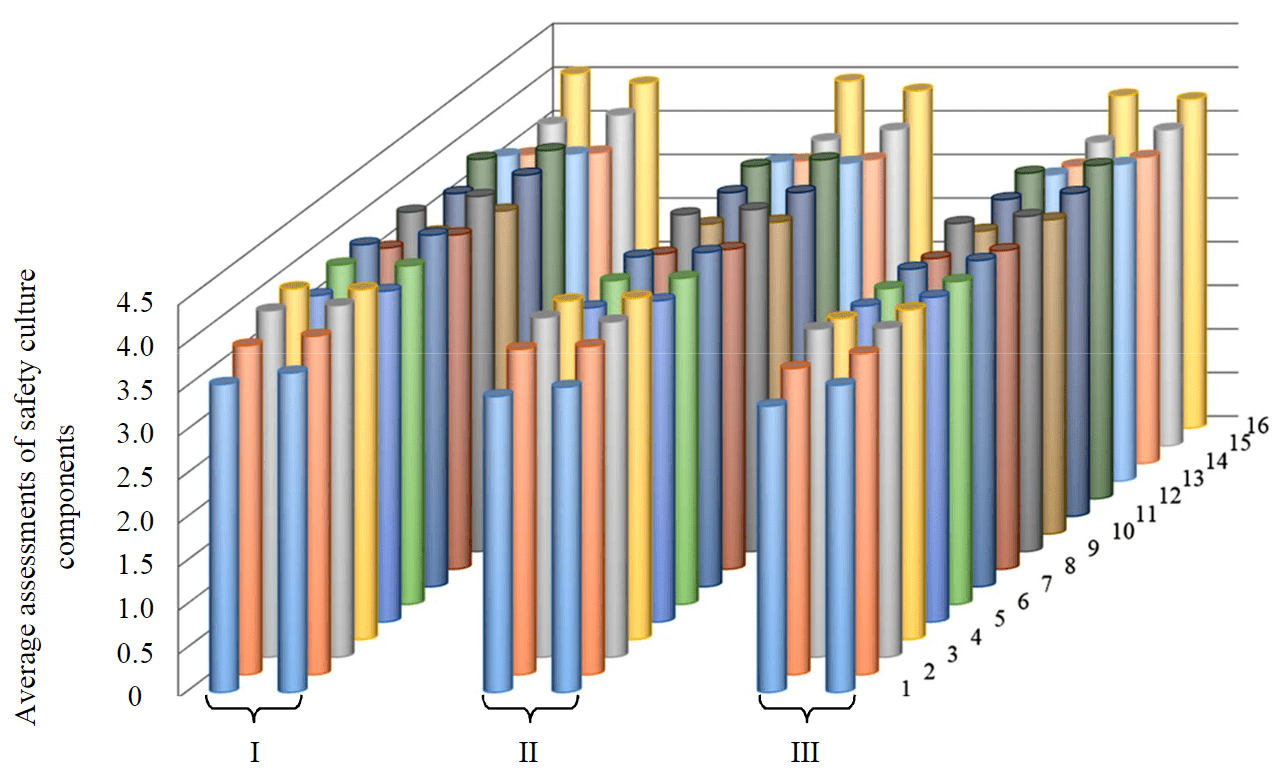
Fig.2. Distribution of average assessments of safety culture components by professional categories of employees prior to and after implementation of control action. Professional categories: I – managers; II – specialists; III – workers (initial assessment and re-assessment). Safety culture components: 1 – motivation; 2 – risk management; 3 – evaluation of occupational safety and labour protection service (HSE) performance; 4 – transparency, information availability; 5 – competencies and training of employees in HSE; 6 – trust; 7 – reporting violations; 8 – assistance from other employees; 9 – evaluation of performance of managers to ensure safety; 10 – assessment of resources to ensure safety; 11 – learning from past mistakes; 12 – personal responsibility for safety; 13 – personal discipline and commitment; 14 – assessment of communications within organization regarding safety issues; 15 – involvement of employees in ensuring safety; 16 – personal interest in safety
Results of re-assessment of the level of occupational safety culture by employees of the professional category “workers” indicate an increase in average values of absolute majority (15 of 16) of components – with the exception of the component “personal interest of employees in safety”. Employees of this professional category rated the component “assessment of managers performance on ensuring safety” most highly.
In turn, employees of the professional categories “specialists” and “managers” changed their assessment upwards in 13 of 16 components.
The presence of components, the assessment of which from re-survey results appeared to be lower, confirms that the process of forming a high culture of occupational safety does not occur at once and depends on many factors, the main of which is natural resistance of employees to changes in occupational safety, especially with innovations [1, 21]. Practice shows that over time, the implementation of behavioural safety processes has a positive impact [22-25] and reduces the number of accidents and injuries in companies [26-29].
For the statistical evaluation of the confidence of changes that occurred as a result of BSA introduction in the assessment of employees, Student's t-test was used, the calculation of which was carried out in the STATISTICA software package using Pearson and Levene tests to check the samples for normality and homogeneity of variances.
Null hypothesis of Student's t-test assumes that mean values of two universes from which the compared independent samples were drawn are the same. STATISTICA software provides for a possibility of evaluating the criterion using p-significance level: if p < 0.05, null hypothesis about the equality of the means is rejected in favour of the alternative one. Therefore, in this case, the difference in the assessment of the occupational safety culture component prior to and after BSA introduction is recognized as statistically significant.
Based on results of analysing average ratings of safety culture components by employees of the professional category “workers” prior to and after BSA introduction, it was concluded that there was a statistically significant increase in average values of ratings of safety culture components (motivation; risk management; transparency, information accessibility; competencies and training of employees in HSE; trust; incident reporting; assistance from other workers; assessment of resources for ensuring safety; personal responsibility for safety; personal discipline and commitment; assessment of communications in the company regarding safety and involvement of employees in ensuring safety), p-significance level of Student's test which is less than 0.05 while observing the conditions of distribution normality and equality of sample variances. At the same time, workers do not demonstrate changes in the following components: assessment of HSE efficiency; assessment of managers performance to ensure safety; learning from past mistakes; personal interest of employees in safety [30].
It should be noted that similar studies were carried out for one of coal companies with total number of surveyed employees over 200. There is a correlation between the results obtained and the results of this study.
Discussion of results
In the presented study, it was found that control action in the form of regular BSA statistically significantly increased the level of occupational safety culture among employees in the professional category “workers” in 12 of 16 components.
To validate the findings and prove that a high level of safety culture leads to a reduction in the number of safety violations by employees when accomplishing the production tasks, data from 1,011 behavioural safety audits conducted during the third and fourth quarters of 2019 at the investigated enterprise were analysed. For a visual assessment of the dynamics of BSA results, a petal diagram of changes in hazard indicator Nionl of the enterprise under study was constructed (Fig.3).
This graphical interpretation makes it possible to identify improvements as well as problem areas in observation categories (called alarm areas) the values of hazard indicators of which increased relative to those obtained from previous observations, to take targeted measures in relation to them. Presence and/or systematic repetition of “alarm area” detection is an important signal to managers about the prerequisites for an incident. The data obtained point to a significant decrease in the indicator in most observation categories. Thus, according to the results of BSA procedure implementation, there is no “alarm area” at the level of the enterprise under study.
Taking into account the zero accident model adopted by the company's managers, it is assumed that in its activities in various business processes, the organization strives to achieve a “zero alarm area”. As part of the implementation of this strategy, an approximate corrective action plan was developed to eliminate the “alarm area” at the enterprise, a fragment of which is presented in Table 1 using the “tools and equipment” category as an example.
Table 1
A fragment of corrective action plan to eliminate the “alarm area” at a fuel and energy enterprise. in “tools and equipment” category
Corrective actions |
Deadline |
Responsible person |
1. Raising the priority and monitoring on an ongoing basis under personal control 2. Receiving feedback from employees on the practice of using tools and equipment 3. Drawing-up of checklists for checking the availability, serviceability and compliance 4. Replacement of homemade tools and equipment. 5. Expression of gratitude to employees of departments in which the minimum values 6. Dissemination of the results of corrective actions among all employees of the company. 7. Verify that the listed corrective actions were taken |
Within |
Company together with department heads |
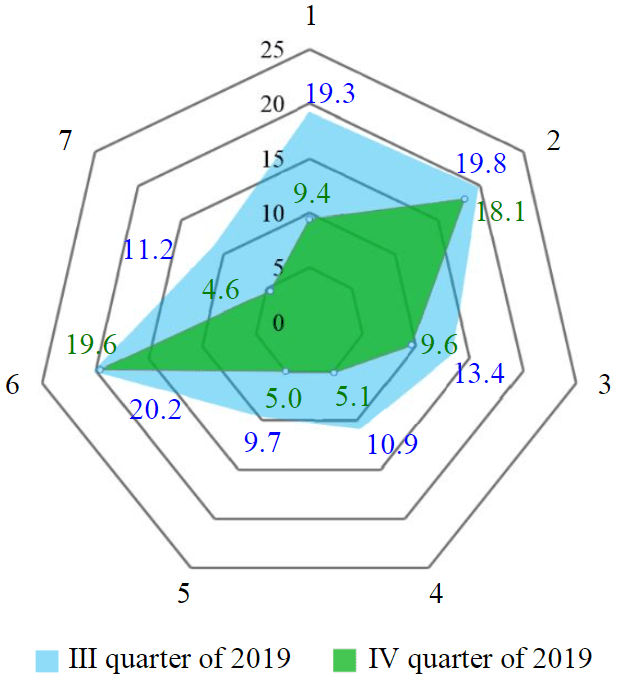
Fig.3. Dynamics of changes in hazard indicator of the company based on results of 1,011 BSA 1 – response of employee/employees; 2 – actions of employee/employees; 3 – workwear and PPE; 4 – tools and equipment; 5 – rules and regulations;
6 – workplace; 7 – transport
Thus, the conducted study shows that during formation and implementation of control action at the next stage of improving the indicators of occupational safety culture, it is necessary to pay special attention to employees of the professional category “managers”. It is important for managers to show leadership qualities and create conditions for a trust-based dialogue [21, 31-33], when employees are not afraid to report violations [34-36]. The methods of forming the necessary psychological climate in a conversation with an employee were also the basis of recommendations on conducting BSA drawn up for the auditors.
International practice shows that a significant effect in increasing the motivation of managers can be achieved through the development of training sessions using modern educational technologies and methods that take into account sociopsychological aspects of conducting classes (case method, group discussion, brainstorming, debriefing, etc.) [37]. Based on the analysis of approaches to training using interactive technologies, a programme of advanced training for managers and specialists of different levels “Behavioural safety audit. Rules for conducting” was successfully developed and tested which contributes both to acquisition by auditors of skills in conducting BSA, and the formation and development of a high level of occupational safety culture [37-39]. There are face-to-face (at Gubkin Russian State University of Oil and Gas), online (remote) and field (with a visit to the company) training formats. In 2020-2022, over 300 managers of fuel and energy companies passed training with subsequent certification.
In order to continuously proactively upgrade the process of managing the occupational safety culture, an action plan was also developed to improve the level of occupational safety culture at a pipeline enterprise [40-42]. Main directions:
- development and updating of regulatory framework in occupational safety culture (concepts for development of occupational safety culture, local regulations for quantitative assessment of occupational safety culture, etc.);
- development of leadership competencies [43-45];
- ensuring transparency of communications on occupational safety;
- formation of a positive attitude to changes in occupational safety [46, 47];
- building an effective system of motivation for safe labour [3, 48, 49];
- automation of processes in occupational safety culture.
Table 2 presents a fragment of the drawn-up plan for the direction “Development of leadership competencies”.
Table 2
A fragment of an action plan to improve the level of occupational safety culture at the fuel and energy enterprise for the direction “Development of leadership competencies”
Measures for stagewise improvement of the level of occupational safety culture |
Deadline |
Results |
Organization of training for managers of all levels according to advanced training programme: • behavioural safety audit. Rules for conducting; • leadership in occupational safety; • identification of hazards and risk management in occupational safety; • analysis of root causes of incidents. Procedure for determining them and When organizing training, it is recommended to provide for: • training of internal trainers; • conducting field seminars/trainings |
Constantly – in |
Certificate |
Organization of employees training in first aid skills with involvement of health care workers |
Constantly – in |
Certificate |
Development and implementation of personnel assessment system that allows determining the development level of critically important personal and leadership qualities of employees |
Within three years |
Assessment system of critically important personal and |
Acquisition of innovative AR/VR (augmented/virtual reality) simulators in occupational safety, innovative elements of personal protective equipment (with smart sensors for remote monitoring of health and location indicators), simulation dummies/simulators with maximum functionality and a high degree of likelihood, popularization of organization of training at test sites |
Within two years |
Innovative on training |
Organization of probation periods for specialists of HSE department to exchange experience on improving the level of occupational safety culture |
Constantly – in |
Report and |
Participation of employees (including young professionals) in thematic conferences (international, all-Russian, and corporate) on the development of occupational safety culture |
Constantly – in |
Protocols |
Holding periodical meetings with teams – “Hour of Safety” |
In accordance with |
Reports |
Development of the institution of mentoring (teaching employees the principles of safe work under the guidance of a mentor assigned to them) |
Constantly |
Updating |
Conclusion
As a result of a comprehensive study, a model for improving the process of managing occupational safety culture in fuel and energy companies was developed and implemented including an assessment of the current state (based on results of surveying 614 employees of a pipeline company using methods of statistical data analysis), deviation assessment (interpretation of the obtained data and decision-making on the acceptability of risks ), forming a control action (development of BSA methodology) and its implementation (dynamic implementation of the developed procedure, analysis of the results obtained and implementation of corrective actions and proactive measures).
Using statistical data analysis, the efficiency of introducing a control action to increase the level of safety culture at the enterprise under study was experimentally proved, confirmed by positive changes in the assessment of most safety culture components by employees (after introduction of BSA procedure, 1,173 persons surveyed).
Taking into account global practice and development strategy of the company, the following products were compiled:
- plan of corrective actions to eliminate the “alarm area” for its seven categories;
- action plan to improve the level of occupational safety culture including six main trends;
- thematic certification programme for advanced training in “Behavioural safety audit. Rules for conducting” in which in 2020-2022 over 300 managers of all levels at fuel and energy companies took part.
In future studies, it is planned to analyse the dynamics of model implementation as part of the audit of the company's occupational safety culture including analytical monitoring of the system of qualitative and quantitative indicators of BSA and the results of a quantitative assessment of the level of occupational safety culture as well as an assessment of implementation of corrective action plan to eliminate the “alarm area” and an action plan to improve the level of occupational safety culture for the reporting period.
Adaptive implementation of the developed model promotes achievement of an acceptable corporate level of occupational safety culture, improvement of leadership competencies, improvement of working conditions and, as a consequence, reduction of the level of occupational injuries and
occupational morbidity in fuel and energy companies in the concept of a risk-oriented approach to occupational safety management system which has a significant economic effect in the current situation and strategic perspective.
References
- Rudakov M.L. “Zero accident” corporate programmes as an element of strategic planning in the field of occupational safety and health at coal mining enterprises. Journal of Mining Institute. Vol. 219, p. 465-471. DOI: 10.18454/PMI.2016.3.465
- Zwetsloot G., Leka S., Kines P., Jain A. Vision zero: Developing proactive leading indicators for safety, health and wellbeing at work. Safety Science. 2020. Vol. 130. N 104890, p. 1-10. DOI: 10.1016/j.ssci.2020.104890
- Smirniakova V.V., Smirniakov V.V., Almosova Y.V., Kargopolova A.P. “Vision Zero” Concept as a Tool for the Effective Occupational Safety Management System Formation in JSC “SUEK-Kuzbass”. Sustainability. 2021. Vol. 13 (11). N 6335, p. 1-19. DOI: 10.3390/su13116335
- Nævestad T.-O., Hesjevoll I.S., Ranestad K., Antonsen S. Strategies regulatory authorities can use to influence safety culture in organizations: Lessons based on experiences from three sectors. Safety Science. 2019. Vol. 118, p. 409-423. DOI: 10.1016/j.ssci.2019.05.020
- Zwetsloot G., Kines P., Ruotsala R. et al. The importance of commitment, communication, culture and learning for the implementation of the Zero Accident Vision in 27 companies in Europe. Safety Science. 2017. Vol. 96, p. 22-32. DOI: 10.1016/j.ssci.2017.03.001
- Nikulin A.N., Dolzhikov I.S., Klimova I.V., Smirnov Yu.G. Assessment of the effectiveness and efficiency of the occupational health and safety management system at a mining enterprise. Industrial Safety. 2021. N 1, p. 66-72 (in Russian). DOI: 10.24000/0409-2961-2021-1-66-72
- Doronina O.D., Safonov A.L. New International Standard ISO 45001:2016 “Occupational health and safety management systems – Requirements”. Meditsina truda i promyshlennaya ekologiya. N 10, p. 40-44 (in Russian).
- Filho A.P.G., Waterson P. Maturity models and safety culture: A critical review. Safety Science. 2018. Vol. 105, 192-211. DOI: 10.1016/j.ssci.2018.02.017
- Behari N. Assessing process safety culture maturity for specialty gas operations: A case study. Process Safety and Environmental Protection. 2019. Vol. 123, p. 1-10. DOI: 10.1016/j.psep.2018.12.012
- Iqbal H., Waheed B., Haider H. et al. Mapping safety culture attributes with integrity management program to achieve assessment goals: A framework for oil and gas pipelines industry. Journal of Safety Research. 2019. Vol. 68, p. 59-69. DOI: 10.1016/j.jsr.2018.12.010
- Kalteh H.O., Salesi M., Cousins R., Mokarami H. Assessing safety culture in a gas refinery complex: Development of a tool using a sociotechnical work systems and macroergonomics approach. Safety Science. 2020. Vol. 132. N 104969, p. 1-9. DOI: 10.1016/j.ssci.2020.104969
- Jiang W., Fu G., Liang C., Han W. Study on quantitative measurement result of safety culture. Safety Science. 2020. Vol. 128. N 104751, p. 1-13. DOI: 10.1016/j.ssci.2020.104751
- Makarov P.V., Kramar V.S., Khasanov O.S., Smerdin I.V. Analysis of safety culture at the enterprise. Neftegazovoye delo. N 3, p. 147-169 (in Russian). DOI: 10.17122/ogbus-2018-3-147-169
- Bobrov A.F., Kiselev S.M., Shcheblanov V.U. Assessment of the safety culture at the radioactive waste and spent nuclear fuel disposal facilities. Hygiene and Sanitation, Russian journal. Vol. 96 (9), p. 888-892 (in Russian). DOI: 10.18821/0016-9900-2017-96-9-888-892
- Stemn E., Bofinger C., Cliff D., Hassall M.E. Examining the relationship between safety culture maturity and safety performance of the mining industry. Safety Science. 2019. Vol. 113, p. 345-355. DOI: 10.1016/j.ssci.2018.12.008
- Zwetsloot G.,Van Kampen J., Steijn W., Post S. Ranking of process safety cultures for risk-based inspections using indicative safety culture assessments. Journal of Loss Prevention in the Process Industries. 2020. Vol. 64. N 104065, p. 1-9. DOI: 10.1016/j.jlp.2020.104065
- Hudson P. Implementing a safety culture in a major multi-national. Safety Science. 2007. Vol. 45. Iss. 6, p. 697-722. DOI: 10.1016/j.ssci.2007.04.005
- Glebova E.V., Volokhina A.T., Vikhrov A.E. Estimate of the Level of Industrial Safety Culture based on the Application of the Methods of Statistical Data Analysis. Occupational Safety in Industry. 2019. N 12, p. 66-74 (in Russian). DOI: 10.24000/0409-2961-2019-12-66-74
- Glebova E.V., Volokhina A.T., Vikhrov A.E.Development and Implementation of Methods for Behavioral Safety Audit Conducting in the Fuel and Energy Complex. IOP Conference Series: Earth and Environmental Science. 2020. Vol. 459. Chapter 2, p. 1-7. DOI: 10.1088/1755-1315/459/3/032015
- Tulebaeva A.A. The problem of building the representative model of a social object. PNRPU Sociology and Economics Bulletin. N 3, p. 72-81 (in Russian). DOI: 10.15593/2224-9354/2018.3.5
- Boulagouas W., García-Herrero S., Chaib R. et al. On the contribution to the alignment during an organizational change: Measurement of job satisfaction with working conditions. Journal of Safety Research. 2021. Vol. 76, p. 289-300. DOI: 10.1016/j.jsr.2020.12.006
- Cooper M.D. Behavioral Safety Interventions A Review of Process Design Factors. Professional Safety. 2009. Vol. 54, p. 36-45.
- Ismail F., Hashim A.E.Steps for the Behavioural Based Safety: A Case Study Approach. International Journal of Engineering and Technology. 2012. Vol. 4. N 5, p. 594-496. DOI: 10.7763/IJET.2012.V4.440
- Geller E.S. Behavior-Based Safety and Occupational Risk Management. Behavior Modification. 2005. Vol. 29. Iss. 3, p. 539-561. DOI: 10.1177/0145445504273287
- Mansur A., Nasution M.I. Identification of Behavior Based Safety by Using Traffic Light Analysis to Reduce Accidents. IOP Conference Series: Materials Science and Engineering. 2016. N 105, p. 1-9. DOI: 10.1088/1757-899X/105/1/012033
- Chen D., Tian H. Behavior Based Safety for Accidents Prevention and Positive Study in China Construction Project. Procedia Engineering. 2012. N 43, p. 528-534. DOI: 10.1016/j.proeng.2012.08.092
- Jasiulewicz-Kaczmarek M., Szwedzka K., Szczuka M. Behaviour Based Intervention for Occupational Safety – Case Study. Procedia Manufacturing. 2015. Vol. 3, p. 4876-4883. DOI: 10.1016/j.promfg.2015.07.615
- Blanc F., Ottimofiore G., Myers K. From OSH regulation to safety results: Using behavioral insights and a “supply chain” approach to improve outcomes – The experience of the health and safety Executive. Safety Science. 2022. Vol. 145. N 105491, p. 1- DOI: 10.1016/j.ssci.2021.105491
- Gendler S.G., Kochetkova E.A., Dal N.N. Experience improvement by management of labor protection in the coal industry of Russia on the example of joint stock company “Vorkutaugol”. Journal of Mining Institute. 2013. Vol. 206, p. 173-176 (in Russian).
- Vikhrov A.E. Development of a method for conducting behavioural safety audit at fuel and energy facilities. Avtoref. dis. … kand. tekhn. nauk. Мoscow: Moskovskii energeticheskii institut, 2022, p. 20 (in Russian).
- Mearns K., Yule S. The role of national culture in determining safety performance: Challenges for the global oil and gas industry. Safety Science. 2009. Vol. 47. Iss. 6, p. 777-785. DOI: 10.1016/j.ssci.2008.01.009
- Houette B., Mueller-Hirth N. Practices, preferences, and understandings of rewarding to improve safety in high-risk indus Journal of Safety Research. 2022. Vol. 80, p. 302-310. DOI: 10.1016/j.jsr.2021.12.013
- Yorio P.L., Edwards J., Hoeneveld D. Safety culture across cultures. Safety Science. 2019. Vol. 120, p. 402-410. DOI: 10.1016/j.ssci.2019.07.021
- Bhandari S., Hallowell M.R. Influence of safety climate on risk tolerance and risk-taking behavior: A cross-cultural examination. Safety Science. 2022. Vol. 146. N 105559, p. 1-11. DOI: 10.1016/j.ssci.2021.105559
- Fruhen L.S., Andrei D.M., Griffin M.A. Leaders as motivators and meaning makers: How perceived leader behaviors and leader safety commitment attributions shape employees’ safety behaviors. Safety Science. 2022. Vol. 152. N 105775, 1-11. DOI: 10.1016/j.ssci.2022.105775
- Mathisen G.E., Tjora T., Bergh L.I.V. Speaking up about safety concerns in high-risk industries: Correlates of safety voice in the offshore oil rig sector. Safety Science. 2022. Vol. 145. N 105487, p. 1-11. DOI: 10.1016/j.ssci.2021.105487
- Glebova E.V., Zayats B.S., Volokhina A.T., Vikhrov A.E. Application of interactive technologies in organizing training of managers and specialists of the fuel and energy complex in the field of industrial safety. Journal of Physics: Conference Series. 2020. N 1691. N 012209, p. 1-5. DOI: 10.1088/1742-6596/1691/1/012209
- Lilburne C.M., Lant P.A., Hassall M.E. Exploring oil and gas industry workers’ knowledge and information needs. Journal of Loss Prevention in the Process Industries. 2021. Vol. 72. N 104514, p. 1-11. DOI: 10.1016/j.jlp.2021.104514
- Kretschmann J., Plien M., Thi Hoai Nga Nguyen, Rudakov M. Effective capacity building by empowerment teaching in the field of occupational safety and health management in mining. Journal of Mining Institute. 2020. Vol. 242, p. 248-256. DOI: 10.31897/PMI.2020.2.248
- Kvalheim S.A., Dahl Ø. Safety compliance and safety climate: A repeated cross-sectional study in the oil and gas industry. Journal of Safety Research. 2016. Vol. 59, p. 33-41. DOI: 10.1016/j.jsr.2016.10.006
- Claxton G., Hosie P., Sharma P. Toward an effective occupational health and safety culture: A multiple stakeholder perspective. Journal of Safety Research. 2022. DOI: 10.1016/j.jsr.2022.04.006
- Yuan Gao, Yunxiao Fan, Jing Wang et al. The mediating role of safety management practices in process safety culture in the Chinese oil industry. Journal of Loss Prevention in the Process Industries. 2019. Vol. 57, p. 223-230. DOI: 10.1016/j.jlp.2018.11.017
- Dahl Ø., Kongsvik T. Safety climate and mindful safety practices in the oil and gas industry // Journal of Safety Research. 2018. Vol. 64, p. 29-36. DOI: 10.1016/j.jsr.2017.12.009
- Tumanov M.V., Gendler S.G., Kabanov E.I. et al Personal risk index as a promising management tool for human factor in labor protection. Mining Informational and Analytical Bulletin. N 6-1, p. 230-247 (in Russian). DOI: 10.25018/0236_1493_2022_61_0_230
- Nikulin A.N., Ikonnikov D.А., Dolzhikov I.S. Increasing Labour Safety on Coal Mines. International Journal of Emerging Trends in Engineering Research. 2019. Vol. 7. N 12, p. 842-848. DOI: 10.30534/ijeter/2019/197122019
- Fabiano B., Pettinato M., Currò F., Reverberi A.P. A field study on human factor and safety performances in a downstream oil industry. Safety Science. 2022. Vol. 153. N 105795, p. 1-11. DOI: 10.1016/j.ssci.2022.105795
- Kanse L., Parkes K., Hodkiewicz M. et al. Are you sure you want me to follow this? A study of procedure management, user perceptions and compliance behavior. Safety Science. 2018. Vol. 101, p. 19-32. DOI: 10.1016/j.ssci.2017.08.003
- Gridina E., Kovshov S., Borovikov D. Hazard mapping as a fundamental element of OSH management systems currently used in the mining sector. Scientific Bulletin of National Mining University. 2022. N 1, p. 107-115. DOI: 10.33271/nvngu/2022-1/107
- Hussain Md.A., Ahmed A., Rubiee S., Masud A.K.M. Safety Interventions Evaluation in an Oil and Gas Company. Procedia Engineering. 2017. Vol. 194, p. 315-322. DOI: 10.1016/j.proeng.2017.08.151