Оценка деформационных характеристик хрупких горных пород за пределом прочности в режиме одноосного сервогидравлического нагружения
Аннотация
Одним из самых надежных методов оценки физико-механических свойств горных пород в результате их разрушения являются лабораторные испытания с применением жестких или сервоприводных испытательных прессов. Они позволяют получить достоверную информацию об изменении этих свойств за пределом прочности на сжатие. Представлены результаты проведенных лабораторных испытаний образцов богатой сульфидной руды, позволившие получить графики их запредельного деформирования. Испытаны как монолитные образцы, так и образцы с концентраторами напряжений в виде отверстий круглого сечения диаметром 3, 5 и 10 мм. Выявлено, что в процессе разрушения образцов модули упругости и деформации уменьшаются в 1,5-2 раза, а в зоне остаточной прочности – в 5-7 раз.
Введение
С увеличением производительности отработки месторождений, разрабатываемых подземным способом, для поддержания темпов добычи необходимо вскрывать новые горизонты, которые часто находятся глубже существующих. С увеличением глубины разработки повышаются риски в осложнении геотехнической обстановки [1-3], которые могут проявляться в виде повышенного горного давления, в том числе и в динамической форме [4-6]. Так, например, глубина разработки рудников Талнаха на некоторых участках достигает более 1000 м при критической глубине удароопасности в 700 м [7-9]. Соответственно, при таких больших глубинах и высоких значениях напряжений для массива горных пород характерно разрушение краевой части. Оно проявляется потенциально в хрупкой форме с высвобождением упругой энергии в виде горного удара. Особенно опасными становятся целики, поскольку они принимают на себя повышенную нагрузку от вышележащей толщи пород. В этом случае применяются противоударные мероприятия, цель которых сформировать локальную зону податливости наведением трещиноватости взрывным способом [10-12] или постепенным разрушением пород, вызванным бурением строчки разгрузочных скважин [13, 14]. Однако оценить изменение физико-механических свойств горных пород в образующихся зонах податливости достаточно трудно. Стандартные лабораторные испытания в рамках ГОСТов направлены на исследование свойств только монолитных горных пород, а оценка нарушенности массива рейтинговыми системами делает в большей степени акцент на природную трещиноватость [15-17]. Один из способов оценки изменения модуля упругости – определение скорости распространения продольных волн до/после разрушения массива [18, 19]. Но решение такой задачи может быть осложнено невозможностью распространения упругой волны сквозь разрушенные участки массива.
При широком развитии компьютерных технологий распространено применение математического моделирования на основе эффективных численных методов конечных или дискретных элементов [20-22]. Реализованные в них упруго-пластические модели позволяют получить информацию (с некоторыми допущениями) о состоянии массива (целиков) и перераспределении в нем напряжений в результате разрушения последнего. Однако для построения адекватных геомеханических моделей необходимы достоверные данные о свойствах материала. Так, для идеально упруго-пластических моделей необходимо знать следующие параметры: сцепление и угол внутреннего трения (или пределы прочности при растяжении и сжатии), модуль упругости, коэффициент Пуассона. Для геомеханических моделей с остаточной прочностью необходимо иметь представление об остаточной прочности горных пород. Так, например, при использовании программы RS2 (Rocscience) при разработке упруго-пластической модели с учетом критерия Кулона – Мора с остаточной прочностью необходимы данные паспорта остаточной прочности горных пород [23, 24]. Часто используемый критерий прочности Хука – Брауна дополнительно требует данные картирования выработок для оценки нарушенности массива [25-27]. Следовательно, необходимые исходные данные можно получить только в результате проведения лабораторных испытаний и полевых исследований.
Оценить процесс разрушения горных пород возможно только при моделировании нагружения, приближенного к реальным условиям. С этой целью можно провести пробоподготовку образцов кубической или цилиндрической формы, испытать в условиях одноосного сжатия в соответствии с ГОСТ 21153.2 «Породы горные. Методы определения предела прочности при одноосном сжатии». Но в таком случае накопленная прессом упругая энергия высвобождается, что приводит к разрушению образца с разлетом его кусков. Чтобы избежать этого, необходимо проводить испытания на жестких или сервоприводных прессах. В таком случае появляется возможность получить полное представление о разрушении образцов с определением значений деформаций за пределом прочности горной породы. Методические основы подобных испытаний представлены в работах [28-30]. Представленные методики нашли свое применение для оценки удароопасности горных пород [31-33]. Такие типы испытаний являются очень сложными в реализации, требуют современного технологичного оборудования.
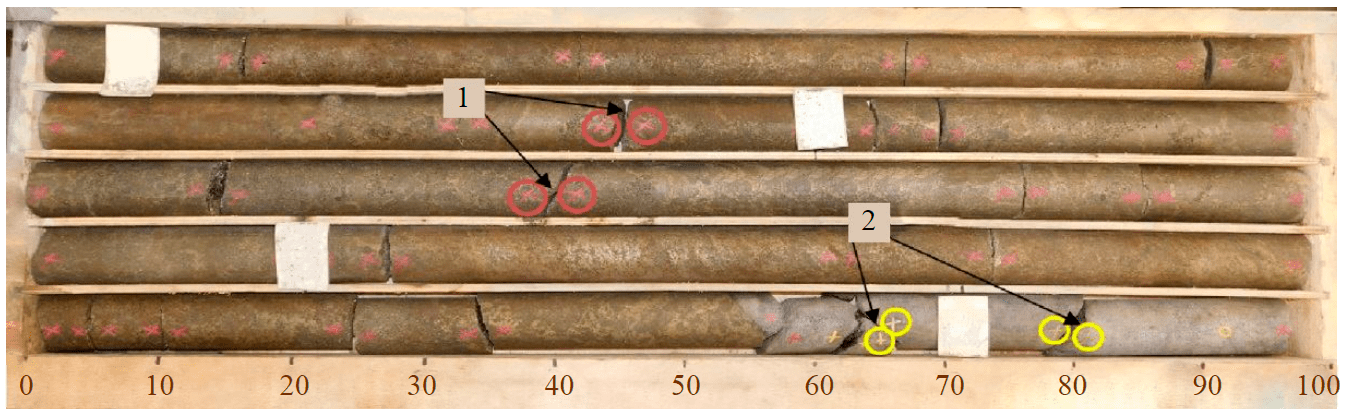
Рис.1. Керн богатой сульфидной руды на контакте с габбро-долеритами 1 – механическое повреждение керна; 2 – естественные трещины
Особенностью проведения испытаний на сервоприводных прессах также является контроль скорости роста значений поперечных деформаций, а, следовательно, получение «петель» спада и нагружения при выравнивании скорости деформирования образца. Однако данный вид испытаний является трудоемким и затратным по времени. Так, в работе [30] указано, что при достижении 70 % от предела прочности необходим контроль нагружения по значениям поперечных деформаций, а скорость нагружения прессом должна обеспечивать их скорость роста не более, чем 0,0001 мм/мм/с. Относительно простой в реализации подход к оценке остаточной прочности представлен в работе [34], подходящий больше для оценки массива бортов карьеров, чем для условий подземной разработки. В данной работе приведены результаты испытаний на запредельное деформирование богатых сульфидных руд Норильского промышленного района для определения изменения деформационных характеристик в процессе разрушения. Отсутствие значительной трещиноватости в рудном массиве (рис.1) в совокупности с высокой жесткостью и высоким показателем коэффициента хрупкости (отношение предела прочности на сжатие к пределу прочности на растяжение), колеблющимся в пределах 9-12 при невысоких значениях предела прочности на сжатие в образе делают данный тип руды удароопасной.
Методология
Для испытаний были подготовлены образцы из керна богатой сульфидной руды, диаметр которых составил 45±1 мм, соотношение высоты образца к диаметру 2:1. Образцы взвешивались, и на них проводились неразрушающие испытания (определение скоростей распространения продольных и поперечных волн и деформационных характеристик). Деформационные характеристики определялись с помощью ГОСТ 28985 «Породы горные. Метод определения деформационных характеристик при одноосном сжатии» на прессе H100KU, с применением LVDT-датчиков точностью 0,5 мкм для оценки изменения базы измерений при нагружении/разгрузке образца.
В некоторых образцах создавались концентраторы напряжений в виде отверстий в центре продольного сечения образца. Рассматривались образцы: стандартные цилиндрические (без отверстий); с отверстием Ø3; 5; 10 мм; с двумя отверстиями Ø5 мм. Дополнительно были изготовлены образцы с двумя отверстиями Ø5 мм и поперечной трещиной, имитирующей зону разгрузки, проходящей через данные отверстия. Расстояние между отверстиями было принято в размере трех их диаметров. После рассверловки образцы с отверстиями повторно испытывались на определение деформационных характеристик (модули Юнга и деформации).
Для образцов с одиночным отверстием Ø3 и 5 мм результаты повторных испытаний не имели значительных расхождений с первоначальными испытаниями, что объясняется различной базой измерения и установкой датчиков в разных точках. Были приняты первоначальные данные. Результаты неразрушающего контроля образцов представлены в табл.1.
Таблица 1
Физико-механические свойства горных пород до испытаний
Диаметр, мм |
Высота, мм |
Модуль |
Модуль упругости, МПа |
Модуль |
Модуль |
Коэффициент |
Коэффициент |
Отверстие |
44,62 |
90,65 |
48400 |
56700 |
48400 |
56700 |
0,148 |
0,143 |
Без отверстий |
44,54 |
87,67 |
65300 |
68600 |
65300 |
68600 |
0,218 |
0,187 |
|
44,63 |
87,99 |
60500 |
64000 |
60500 |
64000 |
0,249 |
0,246 |
|
44,58 |
91,92 |
40300 |
45300 |
40300 |
45300 |
0,198 |
0,158 |
|
44,80 |
89,26 |
38500 |
44400 |
38500 |
44400 |
0,127 |
0,117 |
|
44,96 |
89,53 |
34100 |
37700 |
34100 |
37700 |
0,186 |
0,140 |
|
44,94 |
89,80 |
52200 |
52300 |
52200 |
52300 |
0,201 |
0,201 |
|
44,47 |
89,12 |
59200 |
61300 |
59200 |
61300 |
0,202 |
0,202 |
Одно отверстие Ø3 мм |
44,63 |
86,48 |
31900 |
36700 |
31900 |
36700 |
0,151 |
0,151 |
|
44,62 |
89,12 |
66100 |
72100 |
66100 |
72100 |
0,203 |
0,194 |
|
44,34 |
90,68 |
64100 |
64800 |
64100 |
64800 |
0,229 |
0,221 |
|
44,25 |
88,79 |
30300 |
36000 |
30300 |
36000 |
0,154 |
0,166 |
|
44,74 |
89,55 |
66700 |
71200 |
66700 |
71200 |
0,224 |
0,219 |
|
44,61 |
87,53 |
58400 |
62700 |
58400 |
62700 |
0,205 |
0,201 |
Одно отверстие Ø5 мм |
44,67 |
89,72 |
79000 |
80800 |
79000 |
80800 |
0,155 |
0,140 |
|
44,58 |
87,45 |
65000 |
66600 |
61000 |
62500 |
0,206 |
0,192 |
Одно отверстие Ø10 мм |
44,74 |
88,58 |
81900 |
82200 |
78000 |
78300 |
0,201 |
0,198 |
|
44,66 |
88,88 |
50800 |
54100 |
42700 |
45500 |
0,122 |
0,119 |
|
44,95 |
90,5 |
43600 |
49300 |
36600 |
41400 |
0,149 |
0,172 |
|
44,75 |
89,17 |
50100 |
58000 |
42200 |
47500 |
0,173 |
0,170 |
|
44,64 |
88,27 |
63400 |
74800 |
59400 |
69500 |
0,185 |
0,177 |
|
44,61 |
87,71 |
48600 |
52200 |
44200 |
47500 |
0,172 |
0,172 |
Два отверстия Ø5 мм |
44,69 |
87,99 |
76300 |
76900 |
63100 |
63600 |
0,203 |
0,194 |
|
44,65 |
88,71 |
40900 |
44100 |
24900 |
32800 |
0,141 |
0,148 |
|
44,94 |
91,24 |
53900 |
59200 |
49700 |
54300 |
0,200 |
0,206 |
|
44,54 |
89,70 |
72900 |
76000 |
61100 |
67400 |
0,151 |
0,138 |
|
44,62 |
88,76 |
57300 |
65000 |
45900 |
52700 |
0,171 |
0,136 |
|
44,65 |
89,35 |
56200 |
64300 |
32200 |
43600 |
0,118 |
0,102 |
Два отверстия Ø5 мм + поперечная трещина |
45,00 |
89,18 |
38100 |
45000 |
32100 |
38300 |
0,14 |
0,136 |
|
44,92 |
89,81 |
37300 |
40800 |
31800 |
31400 |
0,172 |
0,172 |
|
44,93 |
90,2 |
39400 |
46600 |
32900 |
40100 |
0,176 |
0,178 |
|
44,77 |
89,55 |
44600 |
56900 |
35800 |
43100 |
0,171 |
0,181 |
|
44,71 |
86,65 |
31000* |
37400* |
10200 |
– |
– |
– |
* Первоначальные деформационные характеристики образца определены с учетом поперечной трещины, полученной в результате пробоподготовки.
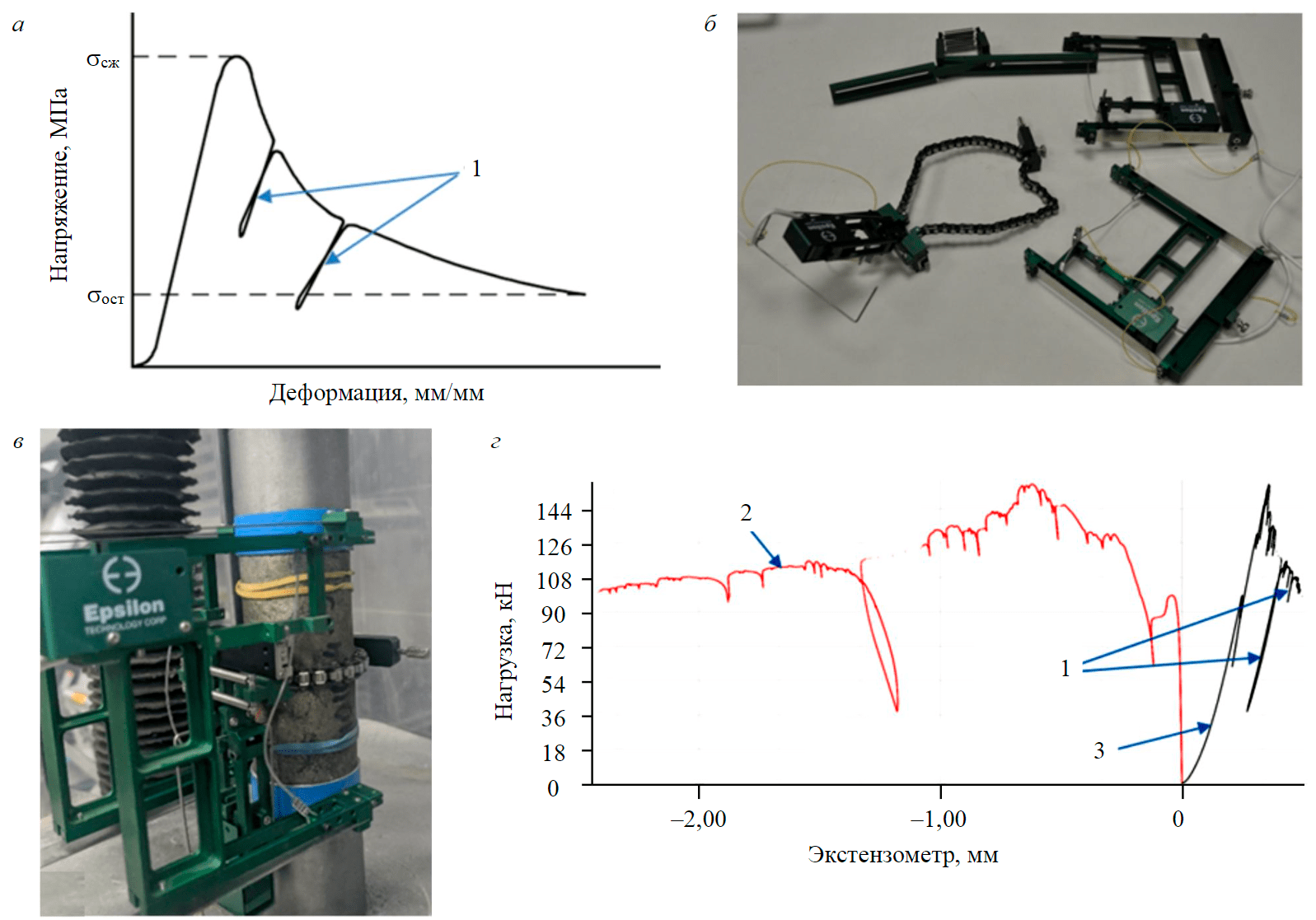
Рис.2. Проведение испытаний: а – график «напряжение – деформация» с «петлями» разгрузки и нагружения; б – экстензометры продольных и поперечных деформаций Epsilon; в – установка для испытаний; г – график нагружения с «петлями», сформированный ПО «Horizont» 1 – «петли»; 2 – перемещения радиального экстензометра; 3 – перемещения продольного экстензометра
Методической основой для определения модуля упругости разупрочненного образца послужил раздел VI «Оценка удароопасности по хрупкости пород с помощью запредельного деформирования» Методических рекомендаций по оценке склонности рудных и нерудных месторождений к горным ударам. Для испытаний использовался испытательный сервоуправляемый пресс TO Super L60 с максимальной нагрузкой 300 кН. Сервопривод позволяет испытательной машине выравнивать нагрузку в соответствии с постоянной скоростью деформирования, что является аналогом режима нагружения на жестких испытательных прессах. Особенностью нагружения с помощью сервопривода является построение характерных «петель» резкого спада и нагружения для выравнивания скорости деформирования при плавном разрушении образца (рис.2, а).
Для получения четкой кривой спада (запредельное деформирование) контроль поддержания заданной скорости деформирования велся по поперечным деформациям, позволяющим на ранней стадии зафиксировать рост трещин и увеличение поперечного сечения вследствие дилатансии и предотвратить разрушение образца упругой энергией. Деформации измерялись специализированными для испытания горных пород экстензометрами тензометрического типа: поперечных – Epsilon 3544-100M-060M-HT2, продольных – Epsilon 3542RA2-100M-600M-HT2 (рис.2, б).
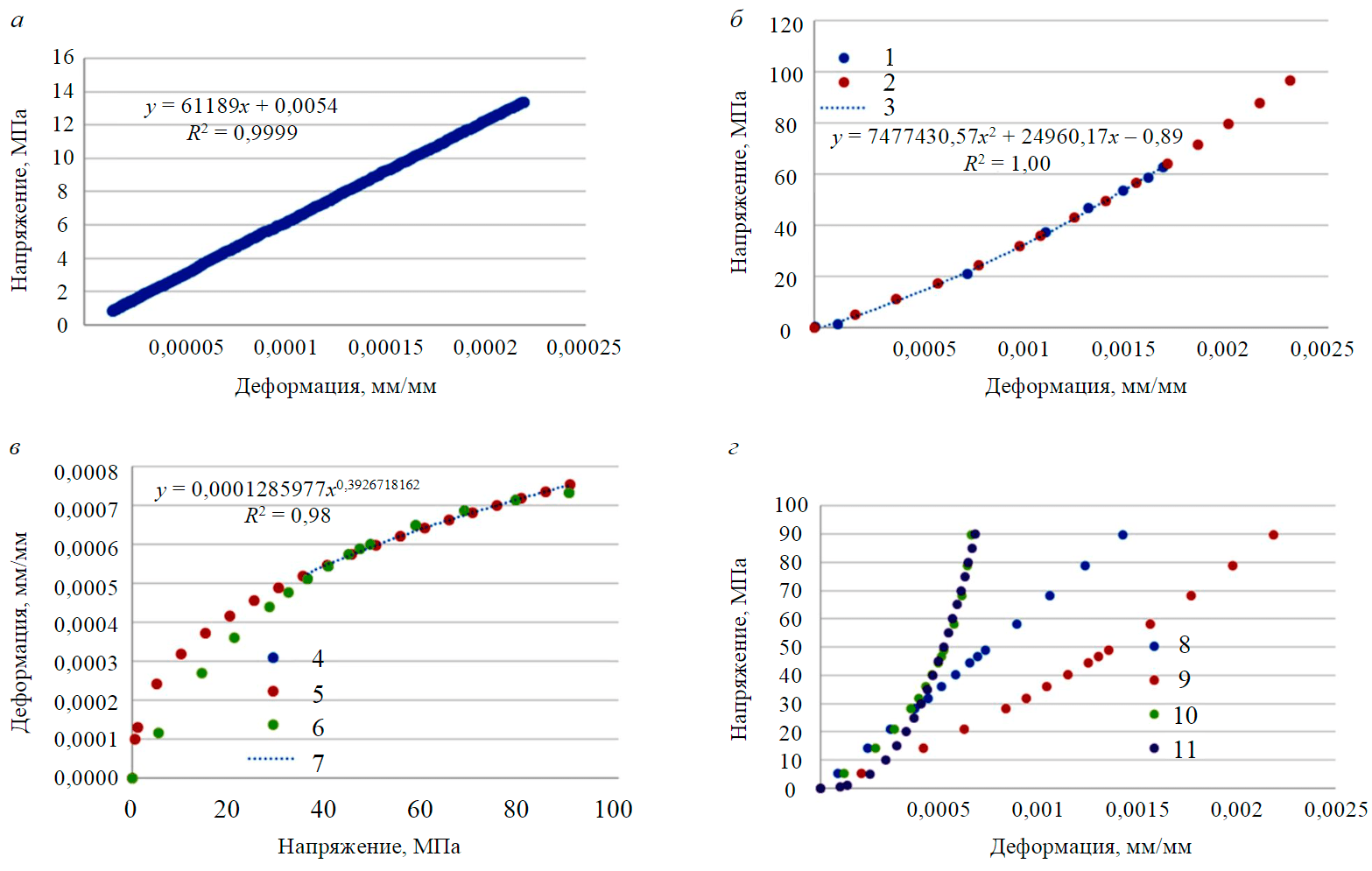
Рис.3. Определение калибровочной функции: а – первоначальное испытание (LVDT) по кривой нагружения; б – испытание на запредельное деформирование (упругий участок); в – нахождение аппроксимационной зависимости; г – сопоставление приведенных экспериментальных данных и полученной аппроксимации 1 – кривая нагружения (Epsilon); 2 – кривая нагружения (аппроксимация); 3 – полиномиальная кривая нагружения (Epsilon); 4 – экспериментальная кривая (30-90 МПа); 5 – аппроксимация; 6 – экспериментальная кривая (0-90 МПа); 7 – степенная экспериментальная кривая (30-90 МПа); 8 – деформации (LVDT); 9 – деформации (Epsilon); 10 – разница деформаций (экспериментальная кривая); 11 – разница деформаций (аппроксимация)
База измерения продольных датчиков постоянна и равнялась 100 мм. Продольная деформация контролировалась по стальным пуансонам, между которыми был установлен образец (рис.2, в). При разрушении образца отдельные части, сформированные при образовании новых поверхностей, испытывают перемещения в непрогнозируемых направлениях и могут перемещаться относительно друг друга, не отражая при этом общего направления деформирования. Результирующим видом разрушения является сжимающая деформация. Для ее надежной регистрации необходимо устанавливать продольный экстензометр на нагрузочные плиты (пуансоны). Такой подход уменьшает искажение результатов измерения при разрушении образца, так как исключает потерю контакта экстензометра с поверхностью. При этом регистрируются дополнительные деформации, возникающие на контакте торцевой поверхности образца и пуансона. При интерпретации результатов измерений этот эффект необходимо учитывать, особенно на участке упругих деформаций, где перемещения относительно малы.
Создание испытательной методики и управление процессом происходило через оболочку специализированного ПО «Horizon» (рис.2, г), поставляемого вместе с прессами TO Super L60. Первый этап испытаний: сжатие образца при постоянной скорости изменения поперечных деформаций (изменения длины окружности образца) 0,02-0,04 мм/мин. Расчет скорости изменения значений поперечных деформаций проводился пересчетом со скорости нагружения образца в 0,1 мм/мин. Данная скорость нагружения характерна при испытаниях удароопасных горных пород [35, 36].
После значительного разрушения образца и недостижения остаточной прочности проводился второй (третий при необходимости) этап испытаний с увеличенной в 2-3 раза скоростью нагружения, так как в данном случае хрупкое разрушение уже невозможно, и увеличение скорости нагружения только сокращает время проведения испытаний.
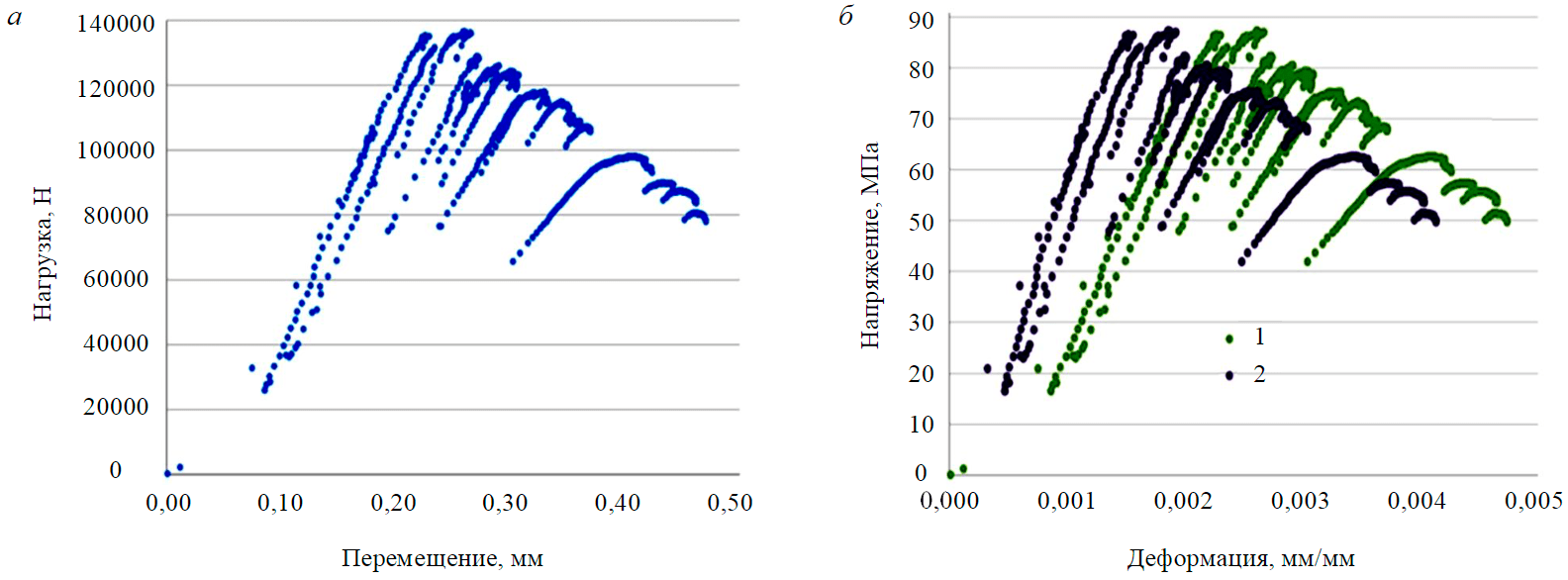
Рис.4. Графики испытаний: а – исходный (нагрузка – перемещения); б – напряжения – деформации до/после калибровки 1 – исходный график; 2 – калибровка
Для анализа полученных результатов использовались значения продольных перемещений. Модули упругости и деформации определялись на участках деформирования за пределом прочности в моменты, когда сервопривод пресса выравнивал скорость деформирования образца и образовывал на графике «петли» резкого спада и нагружения.
Калибровка графиков испытаний
Поскольку с помощью продольных экстензометров измерялись перемещения между нагружающими пуансонами, то могли исказиться результаты ввиду фиксации дополнительных деформаций на торцах образцов, что привело к занижению значений модулей упругости и деформации. Причем разница в значениях логично возрастала с увеличением жесткости образца.
Для отсечения лишних деформаций проведена калибровка графиков по зоне упругости (рис.3). В калибровку заложено допущение, что отклонение Δε является функцией f(P), где P – нагрузка на образец, МПа.
Для выявления этой зависимости определены аппроксимирующие функции ветвей нагрузки при первоначальном определении деформационных характеристик (в случае образцов с отверстиями определение деформационных характеристик после рассверловки) с помощью LVDT-датчиков (деформации (LVDT) и в зоне упругости при испытании на запредельное деформирование (деформации (Epsilon). Выявлены значения деформаций по аппроксимированным кривым при одинаковых значениях напряжений, вычислены значения Δε, что является разницей между деформациями Epsilon и LVDT, построены графики «напряжение – деформация». Наибольшая сходимость достигалась при аппроксимации степенной функцией.
Калибровка графика полного деформирования проведена индивидуально для каждого образца в необходимом интервале напряжений, поэтому степенная аппроксимация графика «напряжение – деформация» (рис.3, в) в каждом случае уникальна. Пересчет деформаций проведен по формуле
где εEps – деформации (Epsilon), мм/мм; Δε(P) – степенная функция типа Δε = APB, мм/мм; P – напряжение в образце, вызванное нагрузкой пресса, МПа; A и B – эмпирические коэффициенты. Пример обработки графика испытаний одного из образцов представлен на рис.4.
После калибровки графиков оценивались модули упругости и деформации. В случаях, когда образец испытывался в несколько этапов, при наличии «петель» разгрузки и нагрузки на полке остаточной прочности, модули упругости и деформации определялись именно на этих участках.
Обсуждение результатов
Результаты определения значений модулей упругости и деформации после калибровки представлены в табл.2. Однако по некоторым образцам не удалось выявить «петли» разгрузки и нагрузки.
Таблица 2
Физико-механические свойства образцов после испытаний
Отверстия |
Модуль деформации |
Модуль упругости |
Модуль деформации |
Модуль деформации |
Модуль деформации |
Модуль упругости |
Eд1/Eд4 |
Eу1/Eу4 |
Предел прочности на |
Остаточная прочность, |
Нет |
48400 |
56700 |
25200 |
46000 |
7109 |
11219 |
6,81 |
5,05 |
42,83 |
3,2 |
Нет |
65300 |
68600 |
33800 |
65100 |
17264 |
27047 |
3,78 |
2,54 |
63,24 |
– |
Нет |
60500 |
64000 |
45800 |
65300 |
30397 |
46038 |
1,99 |
1,39 |
87,27 |
– |
Нет |
40300 |
45300 |
31700 |
37200 |
– |
– |
– |
– |
70,88 |
– |
Нет |
38500 |
44400 |
33700 |
38600 |
33598 |
38393 |
1,15 |
1,16 |
71,96 |
3,4 |
Нет |
34100 |
37700 |
32000 |
35900 |
25136 |
25760 |
1,36 |
1,46 |
66,08 |
1,96 |
Нет |
52200 |
52300 |
47400 |
54800 |
8388 |
12402 |
6,22 |
4,22 |
95,54 |
5,4 |
Одно (3 мм) |
59200 |
61300 |
33400 |
47200 |
10349 |
11569 |
5,72 |
5,3 |
49,81 |
2,5 |
Одно (3 мм) |
31900 |
36700 |
22300 |
33100 |
9173 |
8220 |
3,48 |
4,46 |
53,96 |
3,2 |
Одно (3 мм) |
66100 |
72100 |
26400 |
63900 |
36444 |
21045 |
1,81 |
3,43 |
49,88 |
3,89 |
Одно (3 мм) |
64100 |
64800 |
37500 |
62900 |
48613 |
53710 |
1,32 |
1,21 |
47,83 |
2,3 |
Одно (3 мм) |
30300 |
36000 |
28200 |
30200 |
7984 |
7965 |
3,8 |
4,52 |
53,21 |
3,7 |
Одно (3 мм) |
66700 |
71200 |
42833 |
58800 |
– |
– |
– |
– |
87,23 |
– |
Одно (5 мм) |
58400 |
62700 |
31800 |
52900 |
– |
– |
– |
– |
63,26 |
1,0 |
Одно (5 мм) |
79000 |
80800 |
46100 |
76500 |
– |
– |
– |
– |
100,08 |
– |
Одно (10 мм) |
42200 |
47500 |
34600 |
37100 |
– |
– |
– |
– |
64,32 |
1,5 |
Одно (10 мм) |
59400 |
69500 |
30100 |
52000 |
– |
– |
– |
– |
71,20 |
1,0 |
Одно (10 мм) |
61000 |
62500 |
25100 |
58600 |
– |
– |
– |
– |
39,07 |
1,65 |
Одно (10 мм) |
78000 |
78300 |
39100 |
74200 |
29259 |
24976 |
2,67 |
3,14 |
74,05 |
2,0 |
Одно (10 мм) |
42700 |
45500 |
18600 |
43800 |
– |
– |
– |
– |
33,62 |
2,5 |
Одно (10 мм) |
36600 |
41400 |
26400 |
34200 |
18617 |
32614 |
1,97 |
1,27 |
58,60 |
2,2 |
Два (5 мм) |
44200 |
47500 |
24200 |
43700 |
15414 |
– |
2,87 |
– |
42,33 |
4,1 |
Два (5 мм) |
63100 |
63600 |
43000 |
61800 |
25453 |
17735 |
2,48 |
3,59 |
65,17 |
5,4 |
Два (5 мм) |
24900 |
32800 |
17800 |
21200 |
14547 |
12621 |
1,71 |
2,6 |
32,03 |
11,2 |
Два (5 мм) |
49700 |
54300 |
36400 |
45200 |
42257 |
41618 |
1,18 |
1,3 |
98,95 |
2,2 |
Два (5 мм) |
61100 |
67400 |
52500 |
61900 |
39301 |
39167 |
1,55 |
1,72 |
104,28 |
1,34 |
Два (5 мм) |
45900 |
52700 |
34900 |
45500 |
25176 |
24965 |
1,82 |
2,11 |
77,03 |
– |
Два (5 мм) + трещина |
32200 |
43600 |
27200 |
32200 |
20250 |
– |
1,59 |
– |
52,65 |
4,4 |
Два (5 мм) + трещина |
32100 |
38300 |
28400 |
32600 |
15908 |
15182 |
2,02 |
2,52 |
56,86 |
3,1 |
Два (5 мм) + трещина |
31800 |
31400 |
31200 |
32000 |
– |
– |
– |
– |
54,27 |
– |
Два (5 мм) + трещина |
32900 |
40100 |
30700 |
33000 |
2572 |
5324 |
12,8 |
7,53 |
47,01 |
5,0 |
Два (5 мм) + трещина |
35800 |
43100 |
30000 |
37400 |
5875 |
– |
6,09 |
– |
38,72 |
6,9 |
Два (5 мм) + трещина |
10200 |
– |
– |
– |
– |
– |
– |
– |
25,10 |
– |
Из табл.2 следует, что у образцов модули упругости и деформации, определенные до предела остаточной прочности, уменьшаются в 1,2-2 раза по сравнению с исходными характеристиками, а при оценке «петель» на «полках» остаточной прочности наблюдается уменьшение модулей в 5-7 раз. Образцы с двумя отверстиями и поперечной трещиной часто при испытаниях доводились до полки остаточной прочности. Однако количество «петель» меньше из-за равномерного развития пластических деформаций ввиду наличия трещины, что не позволило в полной мере оценить их деформационные характеристики в процессе разрушения.
Независимо от влияния отверстия на характер спада нагружений, наличие отверстий позволило сохранить разрушенный образец в более устойчивом состоянии, чем образцы без отверстий. Так, из семи монолитных образцов форму после разрушения держали только три образца, тогда как все образцы с отверстиями сохранили форму. Возможно, это связано с тем, что в монолитных образцах разрушение равномерно распределялось по всему образцу, тогда как в образцах с отверстиями именно отверстия концентрировали на себе большую часть разрушения (рис.5).
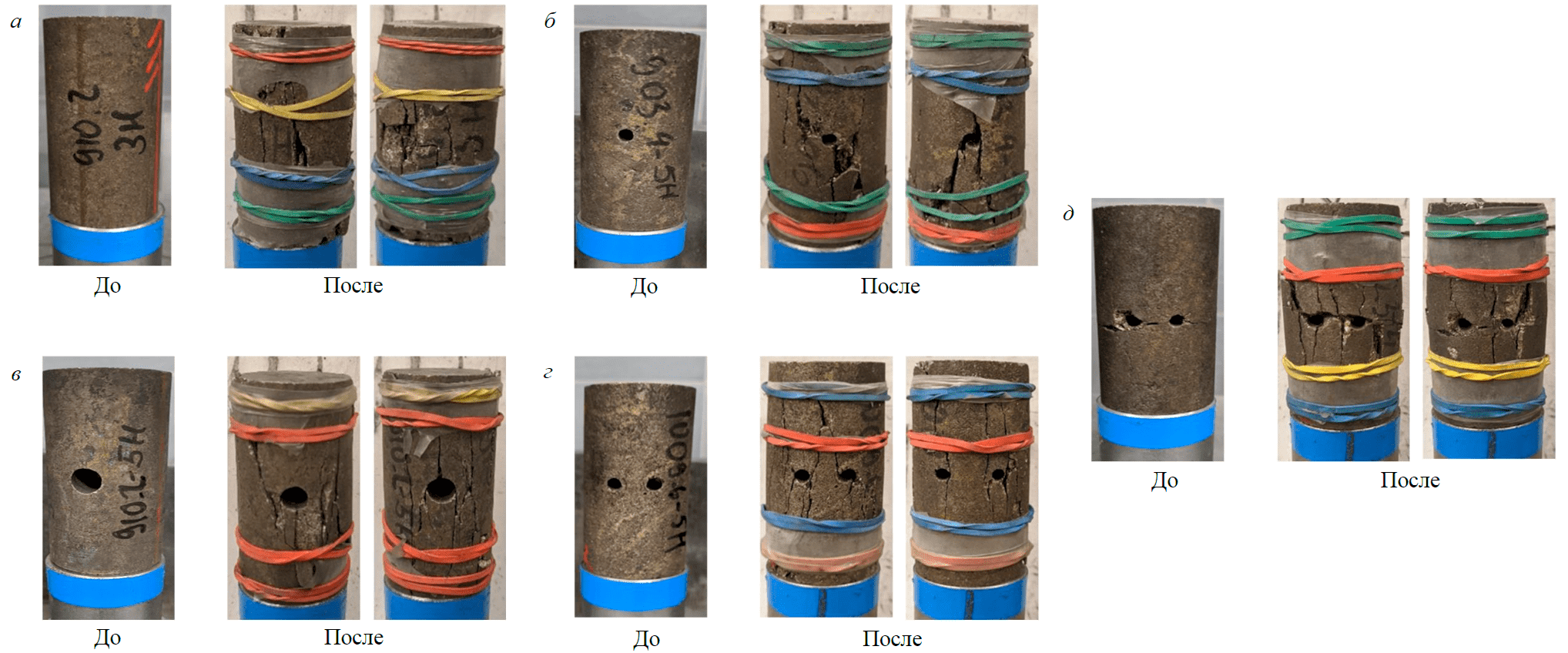
Рис.5. Характер разрушения образцов после испытаний при концентраторах напряжений различной конфигурации: а – стандартный (без отверстий): развитие вертикальной трещиноватости по поверхности образца; б – отверстие Ø3 мм: концентрация трещин вокруг отверстия круглого сечения, развитие вертикальных трещин вверх и вниз; в – отверстие Ø10 мм: концентрация трещин вокруг отверстия круглого сечения, рост вертикальных трещин от оси отверстия; г – два отверстия Ø5 мм: концентрация трещин вокруг отверстия круглого сечения, наблюдается сращивание трещин, образованных вдоль соседних отверстий; д – два отверстия Ø5 мм + трещина: концентрация трещин вокруг отверстия круглого сечения, развитие вертикального трещинообразвания в «целике» между отверстиями
Заключение
Несмотря на широкий спектр возможностей, для оценки разрушения горной породы под нагрузкой лучшим способом является проведение лабораторных испытаний с последующим построением графиков запредельных деформаций. Запредельные испытания на сервогидравлических испытательных прессах с контролем скорости роста значений поперечных деформаций, благодаря построению «петель» разгрузки и нагружения, позволяют оценить модули упругости и деформации за пределом прочности образца. Проведенные испытания на примере образцов богатой сульфидной руды показали, что в процессе разрушения модули упругости и деформации уменьшаются примерно в 1,5-2 раза, а в зоне остаточной прочности в 5-7 раз.
Концентраторы напряжений (отверстия Ø3 и 5 мм) незначительно повлияли на изменение прочностных свойств и почти не сказались на изменении изначального значения модуля упругости и деформации. Однако отверстий таких размеров было достаточно, чтобы изменить характер разрушения образцов – трещины развивались вблизи отверстий. В случае испытаний образцов без отверстий трещинообразование происходило по поверхности практически равномерно. Наличие таких концентраторов напряжений, как два отверстия Ø5 мм совместно с поперечной трещиной, имитирующей участок разгрузки, позволяют ввиду заметного снижения прочности провести испытания с большей вероятностью достижения полки остаточной прочности образца. Однако они значительно уменьшают количество «петель» разгрузки и нагружения, позволяющих достаточно точно оценить модули упругости и деформации.
Литература
- Рыбак Я., Хайрутдинов М.М., Кузиев Д.А. и др. Прогнозирование геомеханического состояния массива при отработке соляных месторождений с закладкой // Записки Горного института. 2022. Т. 253. С. 61-70. DOI: 10.31897/PMI.2022.2
- HongpuKang, PengfeiJiang, YongzhengWu, FuqiangGao. A combined «ground support-rock modification-destressing» strategy for 1000-m deep roadways in extreme squeezing ground condition // International Journal of Rock Mechanics and Mining Sciences. 2021. Vol. 142. № 104746. DOI: 10.1016/j.ijrmms.2021.104746
- Jian Zhou, Chao Chen, Kun Du et al. A new hybrid model of information entropy and unascertained measurement with different membership functions for evaluating destressability in burst-prone underground mines // Engineering with Computers. 2020. Vol. 38. P. 381-399. DOI:10.1007/s00366-020-01151-3
- Рассказов И.Ю., Саксин Б.Г., Усиков В.И., Потапчук М.И. Геодинамическое состояние массива пород Николаевского полиметаллического месторождения и особенности проявления удароопасности при его освоении // Горный журнал. 2016. № 12. С. 23-25. DOI: 10.17580/gzh.2016.12.03
- Тюпин В.Н. Оценка критической глубины месторождений по условию ударопасности // Записки Горного института. 2019. Т. 236. С. 167-171. DOI: 10.31897/PMI.2019.2.167
- Сидоров Д.В., Потапчук М.И., Сидляр А.В., Курсакин Г.А. Оценка удароопаснсти при освоении глубоких горизонтов Николаевского месторождения // Записки Горного института. 2019. Т. 238. С. 392-398. DOI: 10.31897/PMI.2019.4.392
- Плешко М.С., Давыдов А.А., Сильченко Ю.А., Каледин О.С. Эффективные решения по креплению сверхглубокого ствола СКС-1 рудника «Скалистый» в сложных геомехани-ческих условиях // Горный журнал. 2020. № 6. С. 57-62. DOI: 10.17580/gzh.2020.06.08
- Сергунин М.П., Алборов А.Э., Андреев А.А., Буслова М.А. Оценка напряжений впереди фронта очистных работ при увеличении ширины зоны разгрузки в условиях Октябрьского и Талнахского месторождений // Горный журнал. 2020. № 6. С. 38-41. DOI: 10.17580/gzh.2020.06.06
- Баландин В.В., Леонов В.Л., Куранов А.Д., Багаутдинов И.И. Опыт применения обобщенного критерия Хука – Брауна к определению типов и параметров крепей в условиях Октябрьского месторождения медно-никелевых руд // Горный журнал. 2019. № 11. С. 14-18. DOI: 10.17580/gzh.2019.11.01
- Konicek P., Schreiber. Rockburst prevention via distress blasting of competent roof rocks in hard coal longwall mining // Journal of the Southern African Institute of Mining and Metallurgy. 2018. Vol. 118. P. 235-242. DOI: 10.1759/2411-9717/2018/v118n3a6
- Vennes I., Mitri H., Chinnasane D.R., Yao M. Effect of Stress Anisotropy on the Efficiency of Large-Scale Destress Blasting // Rock Mechanics and Rock Engineering. 2021. Vol. 54. P. 31-46. DOI: 10.1007/s00603-020-02252-7
- Saadatmand Hashemi A., Katsabanis P. Tunnel face preconditioning using destress blast-ingblasting in deep underground excavations // Tunnelling and Underground Space Technology. 2021. Vol. 117. № 104126. DOI: 10.106/j.tust.2021.104126
- Карпов Г.Н., Ковальский Е.Р., Смычник А.Д. Определение параметров разгрузки массива горных пород на концевых участках демонтажной камеры // Горный информационно-аналитический бюллетень. 2019. № 8. С. 95-107. DOI: 10.25018/0236-14932019-08-0-95-107
- Сидляр А.В., Потапчук М.И., Терешкин А.А. Геомеханическое обоснование мер безопасности при разработке Николаевского полиметаллического месторождения, опасного по горным ударам // Горный информационно-аналитический бюллетень. 2017. № 7. С. 184-194. DOI: 10.25018/0236-1493-2017-7-0-184-194
- Hoek E., Brown E.T. The Hoek-Brown failure criterion and GSI – 2018 edition // Journal of Rock Mechanics and Geotechnical Engineering. 2019. Vol. 11. Iss. 3. P. 445-463. DOI: 10.1016/j.jrmge.2018.08.001
- Winn K. Multi-approach Geological Strength Index (GSI) Determination for Stratified Sedimentary Rock Masses in Singapore // Geotechnical and Geological Engineering. 2020. Vol. 38. P. 2351-2358. DOI: 10.1007/s10706-019-01149-9
- Hoek E., Diedrierichs M.S. Empirical estimation of rock mass modulus // International Journal of Rock Mechanics & Mining Sciences. 2006. Vol. 43. Iss. 2. P. 203-215. DOI:10.1016/j.ijrmms.2005.06.005
- Николенко П.В., Шкуратник В.Л., Чепур М.Д. Использование нагрева для повышения чувствительности ультразвукового метода контроля напряжений в породном массиве // Горный информационно-аналитический бюллетень. 2021. № 11. С. 159-168. DOI:10.25018/0236_1493_2021_11_0_159
- Раджаоалисон Х. Злотковский А., Рамболаманана Ж. Определение механических свойств песчаника неразрушающим методом // Записки Горного института. 2020. Т. 241. С. 113-117. DOI: 10.31897/PMI.2020.1.113
- Протосеня А.Г., Иовлев Г.А. Прогноз пространственного напряженно-деформированного состояния физически нелинейного грунтового массива в призабойной зоне тоннеля // Горный информационно-аналитический бюллетень. 2020. № 5. С. 128-139. DOI: 10.25018/0236-1493-2020-5-0-128-139
- Protosenya A.G., Verbilo P.E. Analysis of the jointed rock mass mechanical characteristics anisotropy under conditions of apatite-nepheline mineral deposits // Topical Issues of Rational Use of Natural Resources: Proceedings of the XV International Forum-Contest of Students and Young Researchers under the auspices of UNESCO, 13-17 May 2019, St. Petersburg, Russia. Saint Petersburg Mining University, 2019. P. 187-197.
- АушевЕ.В., ЧереповскийА.А., ЛысенкоМ.В. идр. Геомеханическая оценка горнотехнической ситуации при формировании демонтажной камеры и производстве демонтажных работ // Уголь. 2019. № 11 (1124). С. 20-26. DOI: 10.18796/0041-5790-2019-11-20-26
- Peiqi Xi, Yuming Huo, Defu Zhu et al. Development and application of triangulation joint network based on an FEM program (RS2) // Journal of Geophysics and Engineering. 2022. Vol. 19. Iss. 2. P. 245-254. DOI: 10.1093/jge/gxac013
- Dang V.K., Do N.A., Dinh V.D. Estimating the radial displacement on the tunnel boundary by rock mass classification systems // International Journal of GEOMATE. 2022. Vol. 22. № 9. P. 9-15. DOI: 10.21660/2022.92.19
- Zareifard M.R. A new semi-numerical method for elastoplastic analysis of a circular tunnel excavated in a Hoek – Brown strain-softening rock mass considering the blast-induced damaged zone // Сomputers and Geotechnics. 2020. Vol. 122. № 103476. DOI: 0.1016/j.compgeo.2020.103476
- Jinwang Li, Caihua Shen, Xiufeng He et al. Numerical solution for circular tunnel excavated in strain-softening rock masses considering damaged zone // Scientific Reports. 2022. Vol. 12. № 4465. DOI: 10.1038/s41598-022-08531-3
- Bertuzzi R. Revisiting rock classification to estimate rock mass properties // Journal of Rock Mechanics and Geotechnical Engineering. 2019. Vol. 11. Iss. 3. P. 494-510. DOI:10.1016/j.jrmge.2018.08.011
- Ставрогин А.Н., Тарасов Б.Г. Экспериментальная физика и механика горных пород. СПб: Наука, 2001. 342 с.
- Ставрогин А.Н., Протосеня А.Г. Механика деформирования и разрушения горных пород. М.: Недра, 1992. 224 с.
- Eberhardt E. The complete ISRM suggested methods for rock characterization, testing and monitoring: 1974-2006 // Commission on Testing Methods, International Society for Rock Mechanics. 2009. 628 p.
- Козырев А.А., Кузнецов Н.Н., Федотова Ю.В., Шоков А.Н. Определение степени удароопасности скальных горных пород по результатам испытаний при одноосном сжатии // Известия вузов. Горный журнал. 2019. № 6. С. 41-50. DOI:10.21440/0536-1028-2019-6-41-50
- Айнбиндер И.И., Овчаренко О.В. Исследования потенциальной удароопасности массива горных пород на проектируемых глубинах отработки месторождения «Валунистое» // Горный информационно-аналитический бюллетень. 2022. № 6. С. 35-45. DOI: 10.25018/0236_1493_2022_6_0_35
- Бирючев И.В., Макаров А.Б., Усов А.А. Геомеханическая модель. Часть 2. Использование // Горный журнал. 2020. № 2. С. 35-44. DOI: 10.17580/gzh.2020.02.04
- Павлович А.А., Коршунов В.А., Бажуков А.А., Мельников Н.Я. Оценка прочности массива горных пород при разработке месторождений открытым способом // Записки Горного института. 2019. Т. 239. С. 502-509. DOI: 10.31897/PMI.2019.5.502
- Zavacky M., Stefanak J. Strains of rock during uniaxial compression test // The Civil Engineering Journal. 2019. Vol. 3. № 32. P. 398-403.
- Tao Qin, Hongru Sun, Heng Liu et al. Experimental Study on Mechanical and Acoustic Emission Char-acteristics of Rock Samples under Different Stress Paths // Shock and Vibration. 2018. Vol. 2018. № 4813724. DOI: 10.1155/2018/4813724