Technological mineralogy: development of a comprehensive assessment of titanium ores (exemplified by the Pizhemskoye deposit)
- 1 — Ph.D., Dr.Sci. Chief Researcher Institute of Geology, Komi Scientific Center, Ural Branch of the Russian Academy of Sciences ▪ Orcid
- 2 — Ph.D., Dr.Sci. Head of the Mineralogical Department All-Russian Scientific Research Institute of Mineral Resources named after N.M.Fedorovsky ▪ Orcid
- 3 — Junior Researcher Institute of Geology, Komi Scientific Center, Ural Branch of the Russian Academy of Sciences ▪ Orcid
Abstract
Technological mineralogy of titanium ores is the basis for assessing their complexity. It enables, from a unified standpoint, to trace the entire course of changes in mineral matter through operating procedures, including beneficiation, processing, and obtaining target industrial products. The study targets are Pizhemskoye ilmenite-leucoxene sandstones, which are distinguished by a complex polymineral composition. Along with the main ore components, there are other metals with different speciation (isomorphic admixture, independent mineral phases). The optimal set of mineralogical analysis methods for the predictive assessment of their further use is substantiated exemplified by titanium ores of the Pizhemskoye deposit, which are complex, noted for a variable content of iron oxides and contain rare earth metals. Examinations by X-ray phase analysis and scanning electron microscopy confirm that the main titanium phases of sandstones are pseudorutile and a polymineral aggregate, “leucoxene”. Considering the granulometric peculiarities of the magnetic and non-magnetic fractions of the gravity concentrate, the prospects of technologies for processing titanium raw materials are discussed. Along with the problems of obtaining high-quality raw materials, the transformations of mineral phases as a result of extreme impacts and their physicochemical properties as a consequence of isomorphic substitution of a part of Ti atoms with natural modifier agents (Fe and V) in the synthesis of titanium oxide nanostructures for industrial applications are considered (photocatalytic nanoreactor).
Introduction
Titanium and its compounds are in demand in various industries (aviation, medicine, etc.) due to their unique properties that persist at high temperatures and aggressive environments, determining the economic and military positions of the state. Raw materials for industrial production are mineral titanium concentrates (ilmenite, rutile, leucoxene) and products of their processing. Various beneficiation circuits [1-3] and processing technologies [4, 5] are used to improve their quality. The domestic raw material base of titanium accounts for 15 % of world reserves. As of January 1, 2021, the balance reserves amounted to 606.9 tons of TiO2. The largest titanium reserves in Russia are concentrated in the Komi Republic (48 %) and are enclosed in two deposits: Yaregskoye oil-titanium, whose ores are rich in TiO2 content (10.44 %), and Pizhemskoye with less rich refractory zircon-ilmenite-leucoxene ores (4.27 % TiO2). The raw material base of titanium is sufficient to meet the domestic needs of the country, however, almost all Russian enterprises using titanium raw materials import it [6, 7]. The development of placer deposits is subject to the complexity of ores, which complicates their processing by the impossibility of extracting all useful minerals (and components), while not all of the extracted products find their consumers. Efficient integrated technologies for the processing of titanium (or titanium-containing) raw materials are needed, based on reliable mineralogical information. Consequently, the role of research in the field of technological mineralogy of titanium ores, including their comprehensive predictive assessment, is sharply increasing.
It is supposed to develop the mineral resource base of titanium raw materials due to its shortage in Russia involving in mining of refractory ores, non-traditional mineral raw materials, including technogenic formations [8-10], effective technologies for their processing, based on reliable data about their typomorphic features and physicochemical (technological) properties [11, 12]. Technological mineralogy of titanium ores combines mineralogical and technological investigations related to the study of their material composition, textural and structural features, technological properties of minerals in the evolution of a single mineralogical technogenic system at the macro-, micro-, nanolevels, aimed at a comprehensive assessment of all mineral raw materials in the elaboration of alternative approaches to the development of refractory ores [13, 14].
Titanium ores of the Middle Timan [15-17] are typical representatives of metamorphosed titanium deposits in Russia: buried leucoxene sandstones of the Yaregskoye deposit and ilmenite-leucoxene sandstones of the Pizhemskoye deposit. Analysing publications on the problems of the Pizhemskoye deposit development [15-18], one should note the lack of knowledge, which is one of the deterrents to its exploitation. The strategic direction of the “RUSTITAN” company in the Pizhemskoye deposit is the integrated use of titanium raw materials with the involvement of high technologies [19, 20]. Particular importance is attached to research in which ilmenite-leucoxene sandstones are considered as promising sources of a number of minerals (Fe, Au, rare, including rare earths, high-purity quartz, etc.) [12, 21, 22], as well as expanding the list of industrial products based on natural titanium raw materials [23-25], new ideas in the field of their evaluation, considering granulometry, presence of mineral admixtures, and phase transformations under conditions of extreme impacts [26, 27].
The methods for directed changes in the physicochemical properties of mineral raw materials at the nanolevel at all stages of its development, including operational circuits for beneficiation [28] and high-tech industrial products (nanocomposites, nanoreactors) as a result of extreme impacts are relevant [29]. The main component of published works on the synthesis of nanostructured titanium dioxide refers to synthetic raw materials [30-32]. Therefore, works involving natural raw materials [33, 34] are relevant for modelling the physicochemical properties of target prototypes for various industrial applications [35].
The purpose of the article is to improve the methodological approaches to the mineralogical support of a comprehensive assessment of titanium ores, considering the transformation of mineral phases as a result of extreme impacts and their physicochemical properties for industrial applications. To achieve the goal, the following tasks were solved: identifying the optimal set of methods for mineralogical analysis for predictive assessment of the further use of titanium sandstones; consideration of the transformation of mineral phases as a result of extreme impacts (exemplified by the non-magnetic fraction of ilmenite-leucoxene sandstones) to improve the methodological approaches to a comprehensive assessment.
Methodology
The Pizhemskoye deposit is a buried, poorly lithified placer at the northwestern end of the Volsk-Vym ridge in the Middle Timan (Russia) (Fig.1, a). The titanium-bearing bed stretches for more than 10 km from south to north and up to ten km from west to east, occupying an area of about 90 km2 in the middle reaches of the Pechorskaya Pizhma River. Geological structure of the Pizhemskoye deposit area includes the Upper Proterozoic and Devonian deposits on the watersheds, almost everywhere overlain by the Quaternary sediments of various thickness. At the bottom of the Devonian section, a titanium-bearing productive horizon, the Malorucheiskaya Fm., was discovered [6, 15]. The study target was Pizhemskoye ilmenite-leucoxene sandstones (Fig.1, b), taken from the near-contact zone of the second and third units of the Malorucheiskaya Fm. (D2mrc) in an outcrop on the left bank of the Umba River. (64°44ʹ29.15ʺN and 51°31ʹ17.96ʺE). Six samples with a total weight of 12 kg were studied. The nanostructures of titanium oxides obtained from the nonmagnetic fraction of the gravity concentrate according to the developed procedure [36] were also analysed.
Sandstones are distinguished by a complex polymineral composition and textural and structural features; a battery of physical methods of mineralogical analysis was used to obtain reliable information about their composition and structure. Traditional methods of optical microscopy made it possible to obtain only general ideas about the textural and structural features and, to a lesser extent, about the composition (semi-quantitative) of sandstones and their constituent mineral aggregates. Therefore, X-ray and electron microscopic analyses can be considered optimal methods for predictive evaluation of titanium sandstones, but optical microscopy methods (optical-mineralogical and optical-petrographic) must be used without fail. It is they that make it possible to correctly determine the types and sequence of mineralogical studies, and at the final stage contribute to the competent interpretation of the results obtained.
The feed material for the synthesis of titanium dioxide nanotube is a mixture of two phases of high crystallinity of quartz and rutile, in which clay minerals, ilmenite, and anatase are sometimes present in small amounts, which are reliably identified by X-ray phase analysis (XPA).
The sand sample was separated, classified, and fractionated by density (ρ = 2.9 g/cm3). The bulk of mineralogical and analytical work was conducted at the Institute of Geology of the Komi Scientific Centre, the Ural Branch of the Russian Academy of Sciences. Optical-mineralogical analysis of the feed ore and control analyses by the X-ray method were performed on calibrated equipment in the mineralogical department of the All-Russian Scientific Research Institute of Mineral Resources named after N.M.Fedorovsky. The chemical composition was determined by X-ray fluorescence analysis (Shimadzu XRF-1800).
Reliable diagnostics of minerals and determination of the quantitative mineral composition was conducted by XPA (X-ray diffractometer Shimadzu XRD-6000).
Identified features of ore-forming minerals: morphology of minerals and mineral aggregates, their size, heterogeneity (the presence of fractures, mechanical inclusions of quartz in pseudorutile, the distribution of minerals in “leucoxene”, etc.), the presence of secondary alterations (impurities) – leucoxenization of ilmenite and the real composition of minerals was determined using scanning electron microscopy (SEM). The elemental composition was determined by electron probe microanalysis (EPMA) (scanning electron microscope Tescan VEGA-3, equipped with an energy-dispersive spectrometer X-MAX 50 mm2).
Discussion of the results
Granulometric, chemical, and phase compositions of titanium-bea-ring sandstones
Ilmenite-leucoxene (polymineral) sandstones are uneven-grained, clastic material is poorly sorted and weakly rounded, cement is of basal-porous type. The content of material with particle size of –0.25+0.1 mm is 54 %.
TiO2 content in sandstones ranges from 3 to 10 %, while the granulometric examination showed that a decrease in the material particle size can increase TiO2 content to 14.91 %. The maximum content of titanium dioxide falls on the size class –0.071+0.05 mm (see Table). Similar trends can be traced for aluminium, iron, and manganese.
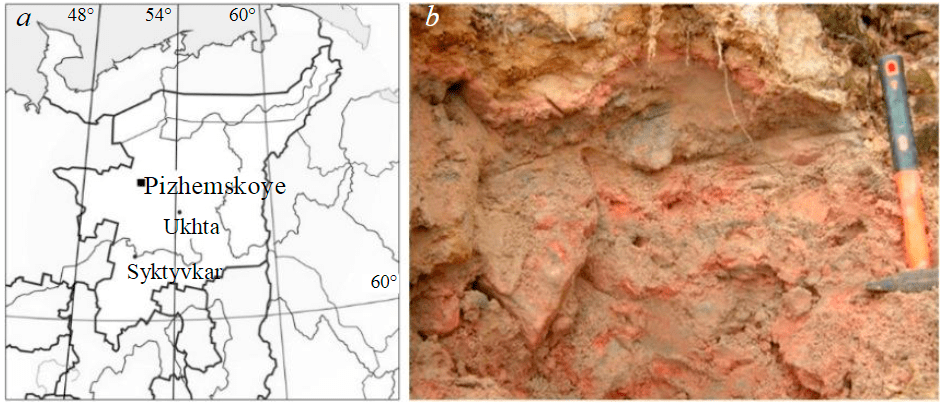
Fig.1. Pizhemskoe deposit (a), outcrop on the left bank of the Umba River (b)
Granulometric* and chemical** compositions of titanium-bearing sandstones (wt.%)
Size class, mm |
SiO2 |
TiO2 |
Al2O3 |
Fe2O3 |
MnO |
ZrO2 |
Other |
||
–1.0+0.5 (11) |
89.55 (2.02) |
3.26 (0.65) |
5.95 (1.66) |
0.48 (0.1) |
0.01 (0.01) |
0 (0.01) |
0.75 (0.2) |
||
–0.5+0.25 (25) |
–0.5+0.4 |
87.99 (3.54) |
4.56 (1.99) |
6.26 (1.71) |
0.48 (0.15) |
0.02 (0.01) |
0 (0.01) |
0.69 (0.56) |
|
–0.4+0.315 |
88.3 (4.07) |
5.2 (1.7) |
5.36 (1.57) |
0.5 (0.16) |
0.02 (0.01) |
0 (0.01) |
0.62 (0.86) |
||
–0.315+0.25 |
86.73 (4.04) |
6.28 (1.71) |
5.68 (1.99) |
0.62 (0.19) |
0.03 (0.02) |
0 (0.01) |
0.66 (0.58) |
||
–0.25+0.1 (54) |
–0.25+0.2 |
81.48 (3.69) |
8.16 (1.05) |
8.57 (2.25) |
0.84 (0.22) |
0.04 (0.02) |
0 (0.01) |
0.91 (0.82) |
|
–0.2+0.16 |
79.78 (2.75) |
9.61 (0.82) |
8.41 (2.39) |
1.27 (0.07) |
0.08 (0) |
0 (0.01) |
0.85 (0.61) |
||
–0.16+0.125 |
75.23 (2.15) |
12.55 (2.75) |
8.85 (2.28) |
2.1 (0.39) |
0.14 (0.04) |
0.03 (0.01) |
1.1 (1.06) |
||
–0.125+0.1 |
75.45 (3.14) |
12.02 (2.76) |
8.64 (4.14) |
2.56 (0.44) |
0.17 (0.04) |
0.03 (0) |
1.13 (1.66) |
||
–0.1+0.05 (9) |
–0.1+0.071 |
77.69 (6.05) |
10.22 (1.73) |
8.48 (6.33) |
2.16 (0.05) |
0.11 (0.02) |
0.17 (0.05) |
1.17 (1.36) |
|
–0.071+0.05 |
65.89 (1.2) |
14.91 (4.61) |
14.15 (4.76) |
2.99 (0.42) |
0.17 (0.04) |
0.28 (0.07) |
1.61 (1.56) |
||
–0.05 (1) |
62.44 (2.27) |
12.87 (3.23) |
18.17 (2.62) |
2.85 (0.24) |
0.16 (0.04) |
0.15 (0.03) |
3.36 (2.36) |
*In parentheses is the average yield of the size class. **Mean values are given, standard deviation is in parentheses.
The main titanium phases are Fe2O3·3TiO2 pseudorutile and a polymineral aggregate, leucoxene, which were formed as a result of FeO·TiO2 ilmenite weathering. Minor minerals include siderite, goethite, and hematite. The content of each can vary from 3 to 7 %. These minerals are predominantly of secondary origin. Sandstones contain muscovite and kaolinite, a small amount of zircon, as well as minerals containing niobium and rare earth metals [15, 22]. Siderite, with which iron is associated, forms a cementing agent in sandstones. In general, titanium phases remain a problem in ore beneficiation processes, in particular, magnetic separation methods. A significant amount of quartz in the form of inclusions (up to 40 %) in pseudorutile and “leucoxene” grains complicates the use of physical beneficiation methods and the production of high-quality titanium concentrates.
Optical-mineralogical analysis
The main rock-forming mineral is quartz. The sandstones are formed by ilmenite, rutile, anatase, zircon, epidote, magnetite, chrome spinelides, tourmaline, pyrite, and monazite. “Leucoxene” is represented by aggregates of varying degrees of preservation, has a black colour, metallic lustre, shell-like fracture. The following varieties are distinguished: ilmenite without visual traces of alteration (metallic lustre is present on most of the grains surface); ilmenite of varying degrees of preservation (fracturing), on the surface of which there are light-coloured impurities, areas of leucoxenization from insignificant in area to occupying most of the grain. The main share of ilmenite and “leucoxene” grains is concentrated in the size classes –0.5+0.25 and –0.25+0.1 mm. The content of titanium minerals increases with a decrease in fineness, which is associated with the release of their intergrowths.
XPA. An X-ray phase analysis of the gravity concentrate of titanium-bearing sandstones was conducted, considering granulometry (Fig.2). The study established that the main minerals are quartz, rutile, anatase, and ilmenite. In association with them, clay minerals are present in insignificant amounts, which are reliably identified by XPA.
EPMA. It made it possible to reveal the features of ilmenite and “leucoxene” grains morphology, to establish the mineral phases on their surface and in the volume, to determine the morphostructural characteristics of microsized quartz grains and aluminosilicate phases in “leucoxene” and ilmenite. Ti/(Ti + Fe) ratio was used to assign the products of ilmenite alteration to one phase or another: < 0.5 – unaltered ilmenite; 0.5-0.6 – hydrated (altered) ilmenite; 0.6-0.7 – pseudorutile; 0.7-1.0 – “leucoxene”.
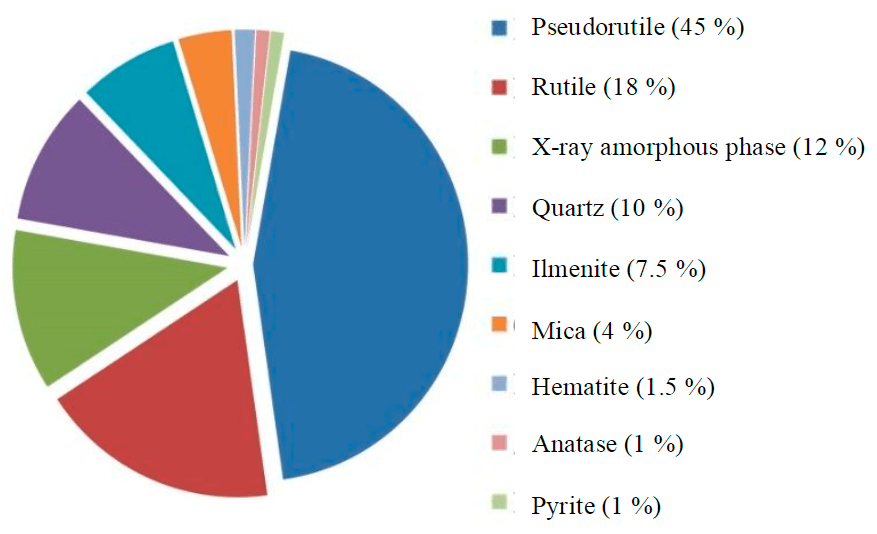
Fig.2. Mineral composition of the heavy fraction (fraction –0.25+0.1 mm; XRF)
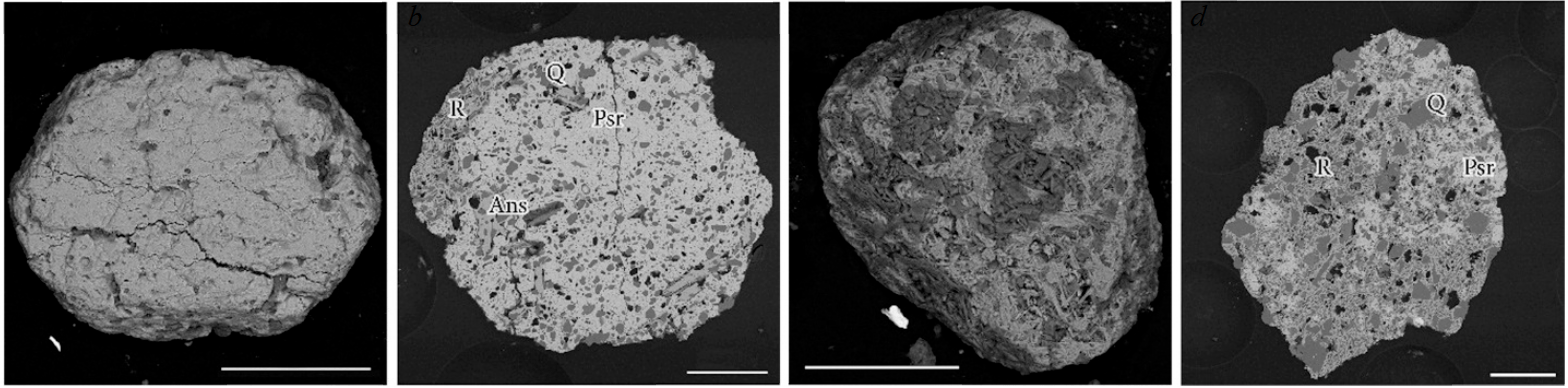
Fig.3. SEM images of grains of ilmenite (a, b) and “leucoxene” (c, d) (elastically reflected electron mode; Q is quartz, R is rutile, Ans is anatase, Psr is pseudorutile)
SEM. Ilmenite is represented by isometric angular, elongated rounded, less often isometric rounded grains with a zonal structure (Fig.3, a). The mineral contains admixtures of vanadium (up to 0.48 wt.%) and manganese (up to 5 wt.%). The distribution of iron over the volume of mineral grains was studied (Fig.4). Variations in the values of Ti/(Ti + Fe) ratio are in the range of 0.58-0.69 (pseudorutile). Smaller values are noted in the central part of the grains, while larger values are characteristic of the peripheral zones. An increase in values indicates a greater degree of iron removal and alteration of ilmenite. In mineral fissures, the values of Ti/(Ti + Fe) ratio are 0.99, which is typical of rutile. It is represented by acicular microcrystals that form a sagenite lattice of rutile twins fused at an angle of 60°. Rutile is located both along fissures with clear boundaries and directly on the surface of ilmenite. Cavities and voids in ilmenite grains are filled with quartz (see Fig.3, b). Fractured quartz grains (up to tens of mm) with clear crystal forms fill voids and cavities in the ilmenite matrix. The proportion of quartz and aluminosilicate phases (clay minerals) in ilmenite reaches 23 %.
EPMA showed that Ti and Fe are uniformly distributed in ilmenite, except for areas where ilmenite is completely replaced by rutile, which develops along fissures towards the centre of grains.
“Leucoxene”, which makes up the main part of the gravity concentrate, accumulates in the non-magnetic fraction and is represented by rounded isometric and oval flattened aggregates of acicular microcrystals of rutile and quartz with pseudorutile relics (Fig.3, c). Most of the grain is occupied by rutile (sagenite lattice of rutile twins, as in ilmenite); there are areas of development of rutile crystallites, which are a homogeneous mass (Fig.3, d).
Iron in “leucoxene” is concentrated inside the aggregates (Fig.5) and is associated with pseudorutile relics with clear boundaries. Along the perimeter of the mineral relics, smaller areas of pseudorutile are observed, the remains of the primary mineral. Quartz grains have clear crystal forms, the surface is porous. The volume fraction of quartz and aluminosilicate phases is somewhat higher than that of ilmenite grains (28 %).
Ilmenite and “leucoxene” grains are polymineral aggregates (the sizes of individual phases are from several micrometres to 100 μm), the main “pollutants” are quartz and aluminosilicate phases, which cannot be reliably separated by physical methods. One of the promising directions for solving these problems is considered to be a directed change in the physicochemical properties of mineral raw materials as a result of various influences [10, 18, 24].
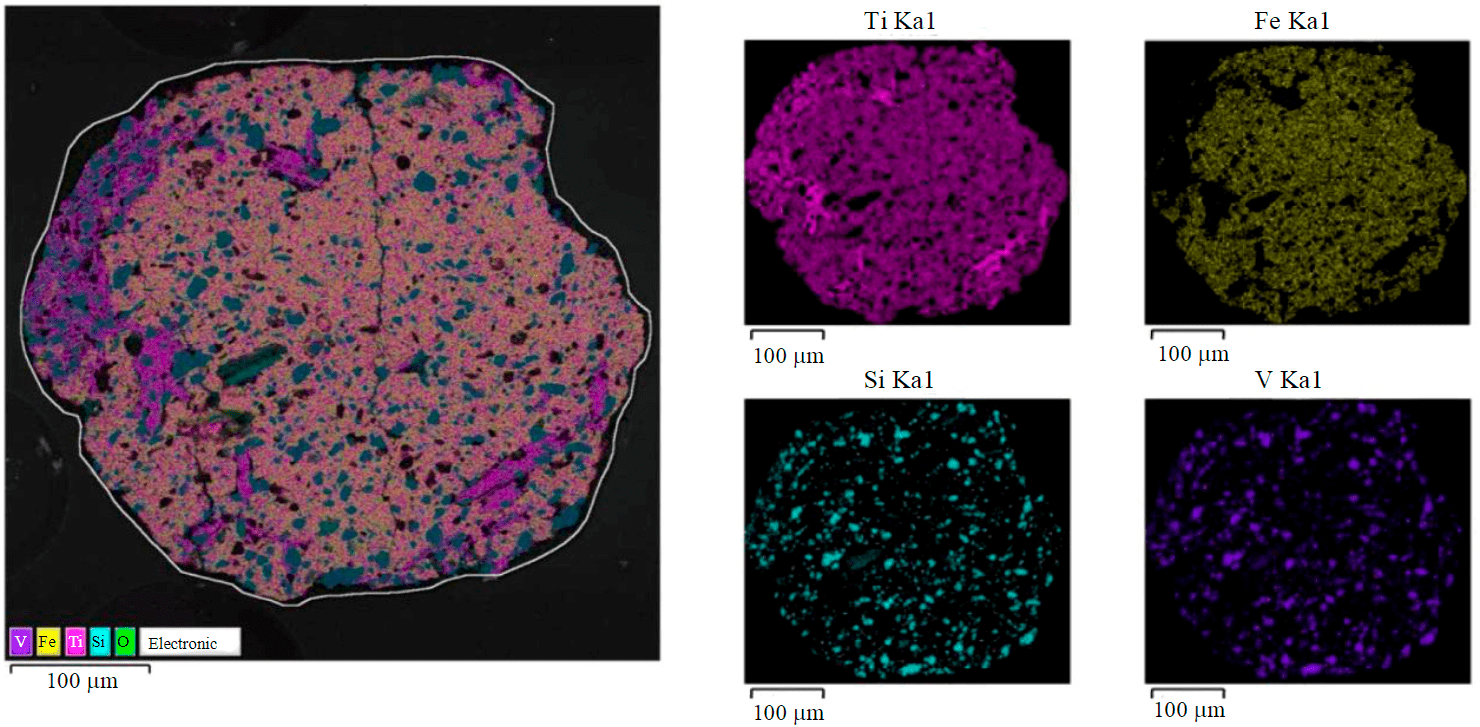
Fig.4. SEM image of an ilmenite grain: element distribution (elastically reflected electron mode, characteristic X-ray emission)
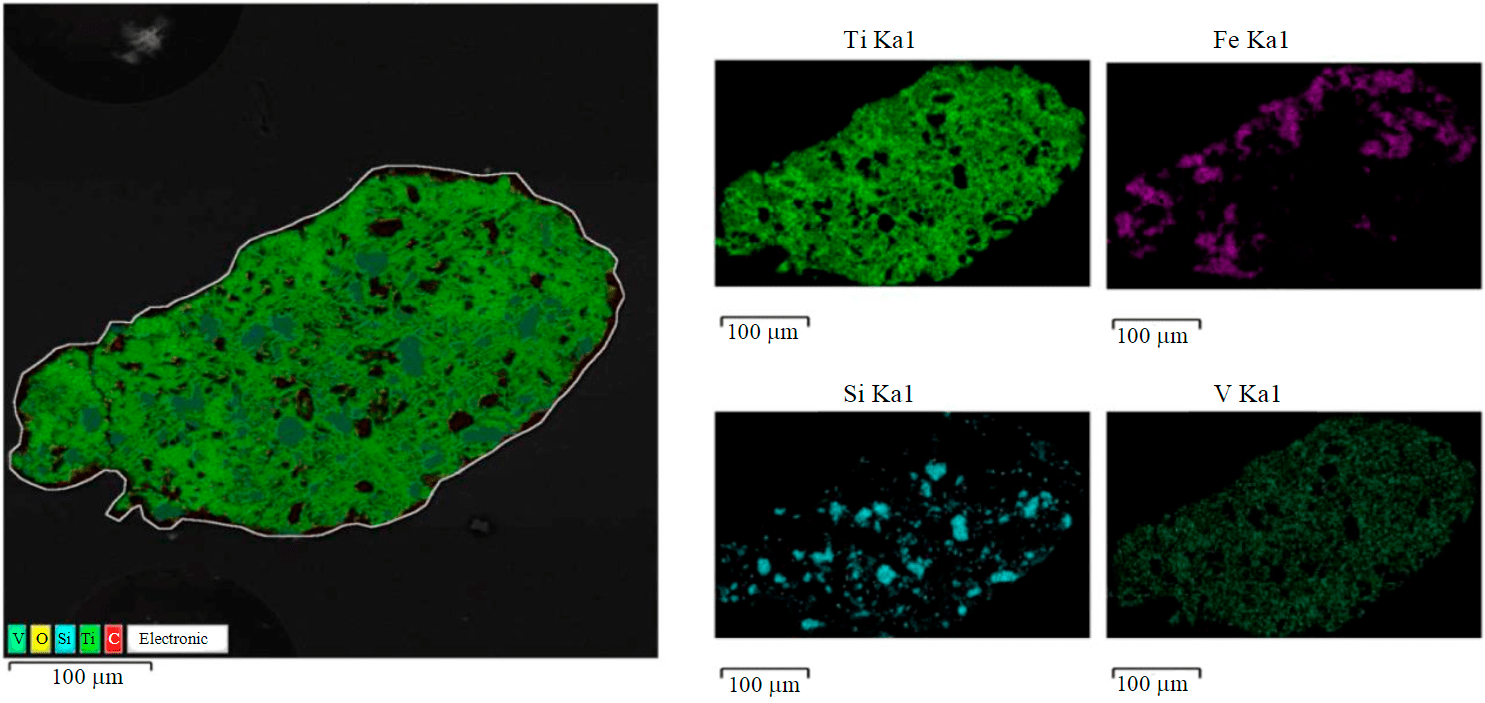
Fig.5. SEM image of “leucoxene”: element distribution (elastically reflected electron mode, characteristic X-ray emission)
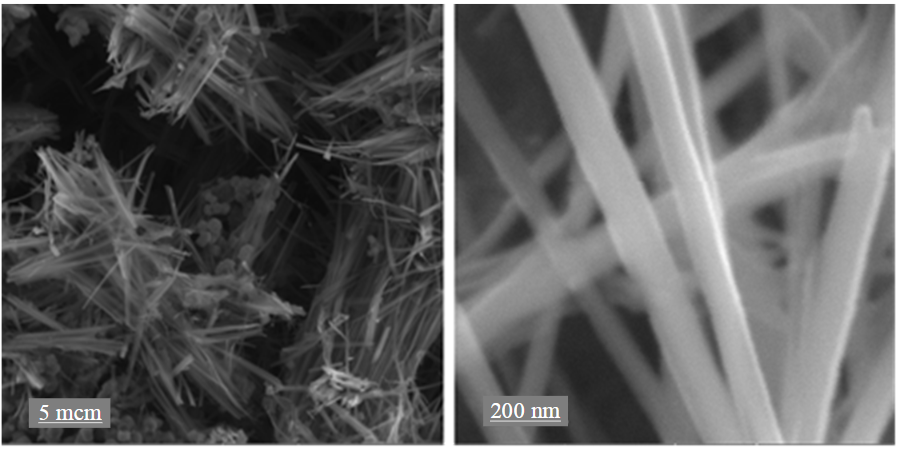
Fig.6. SEM image of titanium oxide nanostructures: outer diameter 50-115 nm, length (5-6)·103 nm (mode of elastically reflected electrons)
Transformation of mineral phases as a result of extreme impacts and their physical and chemical properties
In the development of methods for directed changes in the physicochemical properties of mineral raw materials, phase transformations in the system “non-magnetic fraction of the gravity concentrate of Pizhemskoye ilmenite-leucoxene sandstone – hydrothermal treatment in an alkali solution” were studied [30]. The most significant result is that such extreme impact on the raw material is the cause of breaking the Ti-O bonds. Therefore, the original titanium mineral phases are transformed: “sheet” structures are formed, which are folded into nanotubes (one-dimensional structures) (Fig.6). The phase composition of the synthesized sample is represented by quartz and a low-crystalline phase corresponding to the formed one-dimensional nanostructures of titanium oxides, identified as hydrated sodium titanate (NaxH2 – xTi3O7).
SEM images (Fig.6) enable to estimate the geometric parameters of the obtained one-dimensional nanostructures, which have the following chemical composition, wt.%: 83.92 TiO2; 0.7 SiO2; 0.39 Fe2O3; 2.42 Na2O; 3.95 CaO; 1.02 V2O5 (modifier agents are in bold).
The synthesized “product”, corresponding to the formed one-dimensional nanostructures of titanium oxides, is conditionally designated Fe-V-TNT (it has a high specific surface area of 200-250 m2/g, is a promising sorbent [30]).
SEM images (see Fig.4, 5) show the distribution of Ti, Fe, and V in grains of ilmenite and “leucoxene”. Based on the analysis of the chemical composition in the local volume and SEM images, it can be assumed that Ti atoms can be replaced by Fe and V atoms according to the scheme 3Ti4+ → Fe2+ + 2V5+ or 2Ti4+ → Fe3+ + V5+. Isomorphic substitution of a part of Ti atoms with natural admixtures of vanadium and iron (modifier agents) leads to the appearance of additional allowed levels within the Fe-V-TNT band gap, which prevent the recombination of electrons and holes formed under the action of radiation and serve as additional active surface centres (for example, in reactions of organic molecules decomposition). The band gap of Fe-V-TNT is 2.4 eV, which makes it possible to use the synthesized product as an efficient photocatalytic reactor [30] as an alternative to commercial analogues used [37].
Mineralogical information about the original ore (rock) and its beneficiation products, in particular pseudorutile and leucoxene concentrates, obtained by a set of mineralogical analysis methods (optical and electron microscopy with energy dispersive analysis, X-ray imaging), makes it possible to predict the cost-effective use of this raw material. The high content of quartz in sandstones requires the desiliconization of titanium products in the beneficiation circuit. It will not be possible to completely get rid of the quartz included in the leucoxene aggregate in the leucoxene concentrate. With the disintegration of sandstones and subsequent magnetic analysis, it may not be possible to achieve the maximum release of titanium minerals, in particular pseudorutile [6, 15]. Process flows include wet disintegration of titanium sandstones (for maximum release with minimal loss of titanium) followed by separation into magnetic and non-magnetic fractions (with “leucoxene” being concentrated in the non-magnetic fraction). The traditional solution is autoclave leaching with the production of high-quality titanium raw materials (92 % titanium dioxide) [17].
Considering the granulometric peculiarities of the magnetic and non-magnetic fractions of the gravity concentrate becomes a principal factor that makes it possible to increase the mass fraction of titanium dioxide in the ilmenite-leucoxene concentrate. However, a finely dispersed mass leads to aggregation processes (constitutes a cementing material), which also introduces problems into the beneficiation.
In order to form the optimal cost-benefit ratio in the development of ilmenite-leucoxene sandstones, modern technologies for complex processing are being developed to obtain high-quality titanium raw materials and extract highly pure quartz, rare, including rare earth elements, with minimizing the loss of useful components [25, 38]. The chemical composition of rocks, including rare earth metals, is described in more detail in [22], including a generalizing work [6]. However, there is still no unambiguous answer about the speciation of rare, including rare earth metals, so it is still difficult to predict the probability of their extraction. At the same time, the use of compounds (which are part of sands and hinder their beneficiation, including cementing material) as natural modifier agents in the synthesis of nanocomposites or nanoreactors will make it possible to reassess the complexity of titanium ores and reduce their cost. To develop this area of research, we propose to develop modern technologies considering the “harmful” admixtures of titanium raw materials and phase transformations under extreme conditions exemplified by the synthesis of titanium oxide nanostructures (nanoreactors, nanocomposites, etc.) based on a non-magnetic fraction of gravity concentrate, “leucoxene”.
The following should be noted as promising areas for processing Pizhemskoye ilmenite-leucoxene sandstones in connection with their mineralogical features in the context of the conducted surveys and previously published works: extraction of titanium minerals, possibly iron and quartz, should be considered first of all; sandstones contain rare metals, which increases the prospective significance of the ore as a complex one; it is necessary to take into account the transformation of mineral phases as a result of extreme impacts exemplified by the non-magnetic fraction of the gravity concentrate of ilmenite-leucoxene sandstones and their target physicochemical properties for industrial applications (nanoreactors, nanocomposites), which will reduce the loss of useful components of titanium sandstones, inevitable during operating procedure because of their morphostructural features.
Conclusion
Mineralogical features of Pizhemskoye ilmenite-leucoxene sandstones (their complex polymineral composition containing along with the main ore components other metals with different speciation (isomorphic admixture, independent mineral phases), and the main titanium phases of titanium-bearing sandstones are pseudorutile Fe2O3·3TiO2 and “leucoxene”) identified by a battery of mineral analytical methods with the dominant role of XPA and SEM, made it possible to evaluate their physicochemical properties for further use.
In order to develop modifier mineral raw materials to improve the efficiency of their utilization, including cementing material, the transformations of titanium mineral phases as a result of extreme impacts and their physicochemical properties for industrial applications (sorbents, nanoreactors, nanocomposites, etc.) are considered.
For the first time, an attempt was made to improve the methodological approaches to the mineralogical study of Pizhemskoye titanium ores as part of the mineralogical support of their comprehensive assessment, considering the transformation of mineral phases as a result of extreme impacts and physical and chemical properties as modifier agents in the synthesis of industrial products.
References
- Bykhovskiy L.Z., Tigunov L.P. Titanium raw materials of Russia. Rossiyskiy khimicheskiy zhurnal. 2010. N 2 (54), p. 73-86.
- König U., Verryn S.M.C. Heavy Mineral Sands Mining and Downstream Processing: Value of Mineralogical Monitoring Using XRD. Minerals. 2021. Vol. 11. Iss. 11. N DOI: 10.3390/min11111253
- Zou X., Pang Z., Ji L., Lu X. TiO2 as a source of titanium. Metal Oxides, Titanium Dioxide (TiO2) and Its Applications. Elsevier, 2021, p. 429-448.
- Sun H., Wang J., Dong X., Xue Q. A literature review of titanium slag metallurgical processes. Metalurgia International. 2012. Vol. 17. Iss. 7, p. 49-56.
- Wensheng Zhang, Zhaowu Zhu, Chu Yong Cheng. A literature review of titanium metallurgical processes. Hydrometallurgy. 2011. Vol. 108. Iss. 3-4, p. 177-188. DOI: 10.1016/j.hydromet.2011.04.005
- Sadykhov G.B.Fundamental problems and prospects for the use of titanium raw materials in Russia. Ferrous Metallurgy. 2020. Vol. 63. N 3-4, p. 178-194 (in Russian). DOI: 10.17073/0368-0797-2020-3-4-178-194
- National report on the state and use of mineral resources of the Russian Federation in 2020. Мoscow: Rosnedra, 2021, p. 568.
- Bykhovskiy L.Z., Arkhipova N.A. Strategic rare metal supply in Russia: Current state and future prospects. Gornyi zhurnal. 2017. Vol. 7, p. 4-10 (in Russian). DOI: 10.17580/gzh.2017.07.01
- Sporykhina L.V., Bykhovsky L.Z., Chebotareva O.S. Non-Traditional Sources of Titanium: Criteria for Identification, Problems of Exploitation. Mineral recourses of Russia. Economics and management. 2019. N 1 (164), p. 24-30 (in Russian).
- Chanturiya V.A., Shadrunova I.V., Gorlova O.E. Innovative processes of deep and environmentally safe processing of technogenic raw materials in the face of new economic challenges. Ustoychivoe razvitie gornykh territoriy. 2021. Vol. 13. N 2 (48), p. 224-237. DOI: 10.21177/1998-4502-2021-13-2-224-237
- Bystrov I.G., Pirogov B.I., Yakushina O.A. Morphostructural and Constitutional Features of Titanomagnetite in Iron Ore of the Pudozhgorsky Deposit. Geology of Ore Deposits. 2015. Vol. 57. N 6, p. 496-521. DOI: 10.1134/S1075701515060070
- Sadykhov G.B., Makeyev B., Kopyev D.Y. et al. Mineralogical and Technological Features of the Titanium-Bearing Sandstones of the Pizhemskoye Deposit. Russian Metallurgy (Metally). 2021. N 9, p. 1143–1154. DOI: 10.1134/S0036029521090147
- Levchenko E.N. Features of the material composition of titanium-zirconium placers in Russia. Litologiya i poleznye iskopaemye. N 2, p. 134-153.
- Ozhogina E.G., Kotova O.B. How Technological Mineralogy Can Solve Problems of Integrated Processing of Mineral Raw. Sustainable Development of Mountain Territories. 2021. Vol. 13. N 2 (48), p. 170-178 (in Russian). DOI: 10.21177/1998-4502-2021-13-2-170-178
- Makeev A.B. Typomorphic Features of Minerals of Ti Ores from the Pizhemskoe Deposit. Mineralogy. 2016. N 1, p. 24-49 (in Russian).
- Plyakin A.M., Ershova O.V. On the Age of Devonian Polymeric Alluvial Deposits in Timan. Vestnik IG Komi SC UB RAS. 2010. Vol. 1. N 1, p. 60-63 (in Russian).
- Zanaveskin K.L., Maslennikov A.N., Zanaveskina S.M., Dmitriev G.S. The Yaregskoye deposit leucoxene processing by means of autoclave leaching. Obogashchenie rud. 2016. N 6, p. 14-20 (in Russian). DOI: 10.17580/or.2016.06.03
- Perovskiy I.А., Burtsev I.N., Ponaryadov A.V., Smorokov A.A. Ammonium fluoride roasting and water leaching of leucoxene concentrates to produce a high grade titanium dioxide resource (of the Yaregskoye deposit, Timan, Russia). Hydrometallurgy. 2022. Vol. 210. N 105858. DOI: 10.1016/j.hydromet.2022.105858
- Makeev A.B. Pizhemskoye titanium deposit: aspects of the geological structure, mineral composition of ores, genesis, technology, and commercial development. Geologiya i mineral'nye resursy Evropeyskogo Severo-Vostoka Rossii: Materialy XVII Geologicheskogo s"ezda Respubliki Komi, Syktyvkar, 16-18 aprelya 2019, Syktyvkar, Rossiya. Institut geologii Komi nauchnogo tsentra Ural'skogo otdeleniya Rossiyskoy akademii nauk, 2019, p. 324-326.
- Tkachuk A.N., Trofimov E.N., Novikov A.A. Project of construction of mining and metallurgical complex on the basis of Pizhemskoe titanium deposit. Gornyi zhurnal. 2013. N 9, p. 67-70 (in Russian).
- Skublov S.G., Krasotkina A.O., Makeev A.B. et al. The First Data on the U-Pb Age (Tims and La-Icp-Ms) of Rutile from the Ichetju Polymineral Occurrence, the Middle Timan. Journal of Mining Institute. 2018. Vol. 232, p. 357-363.
DOI: 10.31897/PMI.2018.4.357 - Ponaryadov A.V. Minerals and Processing Features of Ilmenite-Leucoxene Ores of Pizhemskoe Deposit, Middle Timan. Vestnik IG Komi SC UB RAS. 2017. N 1 (265), p. 29-36. DOI: 10.19110/2221-1381-2017-1-29-36
- Anisimova A.B. Deep and integrated processing of mineral raw materials: definition and economic sense. The Eurasian Scientific Journal. 2019. Vol. 6 (11). URL (accessed 12.06.2022) (in Russian).
- Jihua Zhai, Pan Chen, Wei Sun et al. A review of mineral processing of ilmenite by flotation. Minerals Engineering. 2020. Vol. 157. N DOI: 10.1016/j.mineng.2020.106558
- Makeev A.B., Lyutoev V.P. Spectroscopy in process mineralogy. The Pizhemskoye deposit titanium ores concentrates mineral composition. Obogashchenie rud. 2015. N 5, p. 33-41 (in Russian). DOI: 10.17580/or.2015.05.06
- Jung E.J., Kim J., Lee Y.R. A comparative study on the chloride effectiveness of synthetic rutile and natural rutile manufactured from ilmenite ore. Scientific Reports. 2021. Vol. 11. N DOI: 10.1038/s41598-021-83485-6
- Kordzadeh-Kermani V., Schaffie M., Rafsanjani H.H., Ranjbar M. Amodified process for leaching of ilmenite and production of TiO2 Hydrometallurgy. 2020. Vol. 198. N105507. DOI: 10.1016/j.hydromet.2020.105507
- Aleksandrova T.N., Afanasova A.V., Nikolaeva N.V. Low- Grade Structures of Noble and Non- Ferrous Metals and Methods of Their Selective Separation. Sustainable Development of Mountain Territories. 2021. Vol. 13. N 2 (48), p. 161-169 (in Russian). DOI: 10.21177/1998-4502-2021-13-2-161-169
- Aphairaja D., Wirunmongkol T., Pavasupree S., Limsuwan P.Synthesis of Titanate Nanotubes from Thai Leucoxene Mineral. Procedia Engineering. 2012. Vol. 32, p. 1068-1072. DOI: 10.1016/j.proeng.2012.02.056
- Bhadra C.M., Truong V.Kh., Pham V.T.H. et al. Antibacterial titanium nano-patterned arrays inspired by dragonfly wings. Scientific Reports. 2015. Vol. 5. N DOI: 10.1038/srep16817
- Souza W., Piperni S.G., Laviola P. et al. The two faces of titanium dioxide nanoparticles bio-camouflage in 3D bone spheroids. Scientific Reports. 2019. Vol. 27. Iss. 9. N DOI: 10.1038/s41598-019-45797-6
- Diasanayake M.A.K.L., Senadeera G.K.R., Sarangika H.N.M. et al. TiO2 as a Low Cost, Multi Functional Material. Materials Today: Proceedings. 2016. Vol. 3. Supplement 1, p. 40-47. DOI: 10.1016/j.matpr.2016.01.006
- Ponaryadov A.V., Kotova O.B., Sun S. et al. Natural titanium dioxide nanotubes. Építőanyag – JSBCM. 2020. Vol. 72. Iss. 5, p. 152-155. DOI: 10.14382/epitoanyag-jsbcm.2020.25
- Fauzi A., Lalasari L.H., Sofyan N. et al. Synthesis of titanium dioxide nanotube derived from ilmenite mineral through post-hydrothermal treatment and its photocatalytic performance. Eastern-European Journal of Enterprise Technologies. 2022. Vol. 2, p. 15-29. DOI: 15587/1729-4061.2022.255145
- Doong R., Kao I. Fabrication and Characterization of nanostructured tittanate materials by the hydrothermal treatment method. Recent Patents on Nanotechnology. 2008. Vol. 2, p. 84-102. DOI: 10.2174/187221008784534497
- Kotova O.B., Ponaryadov A.V., Gömze L.A. Hydrothermal Synthesis of TiO2 Nanotubes from Concentrate of Titanium Ore of Pizhemskoe Deposit (Russia). Vestnik IG Komi SC UB RAS. 2016. N 1 (253), p. 34-36 (in Russian). DOI: 10.19110/2221-1381-2016-1-34-36
- Ponaryadov A.V., Kotova O.B., Shiyong Sun. Photocatalytic nanoreactor based on low-dimensional titanium oxide structures. Vestnik of Geosciences. 2022. N 1 (325), p. 54-56 (in Russian). DOI: 10.19110/geov.2022.1.5
- Nikolaev A.A., Kirpichev D.E., Samokhin A.V., Nikolaev A.V. Thermochemical plasma-Arc treatment of leucoxene concentrate. Inorganic Mater. 2017. Vol. 8, p. 406-411. DOI: 10.1134/S2075113317030182