Методическое обоснование выбора оптимальных режимов работы оборудования схемы стадиального вывода концентрата при обогащении железных руд
Аннотация
Исследована актуальная задача повышения качества железорудных концентратов. Предложено использование технологии стадиального вывода концентрата путем совмещения операций тонкого грохочения, доизмельчения и магнитно-гравитационного обогащения. На примере магнетитовой руды Стойленского ГОКа обоснован научно-методический подход к поиску оптимальных параметров и режимов разделения, включающий несколько этапов: изучение гранулометрического состава и раскрытие полезных компонентов в исходном продукте для выбора параметров классификации; проведение серии опытов по измельчению надрешетных продуктов до различной крупности; обогащение полученных продуктов МГ-сепарацией. Для выбора оптимальных параметров рудоподготовки используется анализ эффективности операции обогащения, которая рассчитывается по критерию Ханкока – Луйкена. Результатом исследований являются экспериментальные зависимости, связывающие технологические показатели обогащения с параметрами процесса тонкого вибрационного грохочения. Для исследуемой руды железистых кварцитов, перерабатываемой на Стойленском ГОКе, полученные зависимости могут быть описаны полиномом второго порядка с высокой достоверностью аппроксимации. Наилучшие показатели достигаются при крупности классификации 0,1 мм: содержание Fe общ в концентрате 69,7 %, извлечение 85 %, эффективность классификации 80,4 %. Номинальная крупность продукта при этом составляет 0,076 мм, что соответствует крупности измельчения 70-73 % класса –0,045 мм.
Введение
Добыча и переработка железной руды является одной из ведущих отраслей горнорудного сектора России, в том числе и потому, что этот ресурс – одна из важнейших статей экспорта нашей страны. Спрос на железную руду как в России, так и в мире будет расти. Это связано с мировым ростом населения, освоением новых территорий, с заменой изношенных основных фондов. По запасам руды Россия занимает второе место в мире, уступая только Бразилии. При этом качество отечественного железорудного сырья заметно ниже, чем в других странах: основная часть руд относится к бедным и средним (рядовым) с содержанием металла 16-40 % [1-4].
Как правило, технологии обогащения таких руд базируются на стадиальном выводе из процесса хвостов с последующим измельчением материала в замкнутом цикле с классификацией и магнитной сепарацией. На современном этапе переработки железных руд использование методов многостадиального измельчения и магнитной сепарации сопряжено с необходимостью тонкого измельчения руды при повышенных расходах энергоресурсов. Традиционные барабанные магнитные сепараторы не обеспечивают при этом селективного разделения тонких фракций магнетита и минералов породы, что приводит как к снижению качества концентрата, так и увеличению потерь тонкого магнетита с отвальными хвостами.
Современные мировые требования к качеству производимой железорудной продукции постоянно растут, при этом во всем мире предприятия и компании по переработке железорудного сырья активно ищут пути повышения качества своей продукции. В последние годы в связи с развитием новых отраслей промышленности значительно вырос спрос на высококачественные железорудные концентраты: для порошковой металлургии 71,4-72 % Feобщ, производства железоникелевых аккумуляторов 69-71 %, процессов электрометаллургии 68-69,5 % и выше. Практически отсутствует спрос на низкосортные концентраты и руды, не поддающиеся обогащению, что привело к прекращению работы некоторых предприятий (Камыш-Бурунский комбинат, Бакальское рудоуправление и др.) [5-7].
Наряду с этим, в нынешних экономических условиях остро стоят вопросы снижения энергоресурсов на производимую продукцию, повышения комплексности использования руд, снижения техногенной нагрузки на окружающую среду. Рост и совершенствование производственных мощностей связывается с переходом на глубокое обогащение с целью повышения качества концентратов (агломерата, окатышей) до 70 % и выше, при этом дополнительные затраты должны окупаться на последующих стадиях передела (экономия тепла, кокса, флюсов, повышение качества металла и т.д.).
Основной прирост массовой доли железа в концентратах получают за счет введения доводочных операций тонкого измельчения и тонкого грохочения [8-12], обратной катионной флотации [13-16], применения более совершенных магнитных сепараторов [17-19], в ряде случаев используются гравитационные методы [20-24].
Обозначенный комплекс проблем предполагает необходимость проведения научных исследований по разработке новых технологических решений и применению современного высокоэффективного оборудования для переработки железистых кварцитов, обеспечивающих высокие технико-экономические показатели в соответствии с современными требованиями экологической безопасности.
Перспективным направлением решения этих вопросов является внедрение технологии стадиального получения высококачественного магнетитового концентрата за счет совмещения процессов тонкого грохочения, доизмельчения и магнитно-гравитационной (МГ) сепарации. Принцип работы МГ-сепарации основан на управлении магнитным агрегированием при воздействии на ферромагнитную суспензию магнитным полем низкой напряженности и центробежно-восходящим водным потоком. Операция тонкого грохочения широко используется на многих горно-обогатительных предприятиях для различных видов минерального сырья и позволяет добиться роста производительности обогатительных фабрик, повышения качества выпускаемой продукции, снижения эксплуатационных расходов [25-31].
Такая технология стадиального получения высококачественного концентрата была внедрена на дробильно-обогатительной фабрике АО «Олкон» и позволила повысить качество концентрата до 69-70 % Feобщ при сохранении текущего уровня извлечения магнитного железа. Кроме того, удалось снизить эксплуатационные затраты на производство товарного железорудного концентрата в пределах 10-15 % за счет исключения оборудования, использовавшегося на секциях дообогащения [32]. Промышленные испытания этой технологии на АО «Карельский окатыш» позволили обеспечить выпуск концентрата качеством 70 % Feобщ при одновременном повышении технико-экономических показателей производства за счет своевременного вывода из цикла обогащения концентрата и отвальных хвостов [33].
Проведены промышленные испытания МГ-сепаратора МГС-2.0 на действующем обогатительном производстве АО «Соколовско-Сарбайское горно-обогатительное производственное объединение» (Казахстан) с целью повышения качества железорудного концентрата [34]. Предлагаемая технология стадиального вывода готового концентрата позволит не только обеспечить прирост качества продукции 67-68 %, но снизить текущие эксплуатационные расходы, что благоприятно скажется на рентабельности продукции.
Для железистых кварцитов КМА (АО «Стойленский ГОК») испытана в промышленных условиях технология МГ-сепарации [35, 36]. Установлена возможность обогащения магнетитового концентрата данным методом, получен прирост содержания железа в концентрате в среднем 1,2 % (с 66,5 до 67,7 %). Сепарация проводилась на неклассифицированном материале, что привело к разубоживанию магнетитовых концентратов крупным классом. По результатам испытаний рекомендовано дополнить исследования введением в схему операции тонкого грохочения.
Проведенные испытания показали, что при реализации технологии стадиального вывода концентрата необходима совместная оптимизация операций измельчения, тонкого грохочения и обогащения. Предложен алгоритм проведения сравнительных исследований и последующего выбора оптимальных режимов классификации и доизмельчения по эффективности работы операции обогащения.
Материалы и методы исследования
Исследования проводились на примере магнетитовой руды Стойленского ГОКа крупностью –5 мм. Основным рудным минералом пробы является магнетит, нерудные минералы представлены кварцем, амфиболами, в том числе щелочными, слюдами, карбонатом. Наблюдается незначительная примесь гематита, сульфидов, апатита (в сумме 2-3 %).
Предварительно мокрой магнитной сепарацией из пробы были выделены отвальные хвосты (выход хвостов составил 17,9 %, содержание Feобщ и Feмагн 10,57 и 1,32 %, извлечение 5,23 и 0,77 % соответственно). Исходным продуктом для изучения являлась магнитная фракция мокрой магнитной сепарации руды с содержанием Feобщ около 41,8 %, Feмагн 37,2 % (табл.1).
Таблица 1
Характеристика исходного продукта для исследований
Классы крупности, мм |
Выход, |
Содержание, % |
Распределение, % |
|||
Feобщ |
Feмагн |
Feобщ |
Feмагн |
|||
–5,0+3,15 |
0,15 |
34,02 |
27,30 |
0,12 |
0,11 |
|
–3,15+2,0 |
12,46 |
34,02 |
27,30 |
10,14 |
9,15 |
|
–2,0+1,6 |
9,42 |
35,74 |
30,84 |
8,06 |
7,82 |
|
–1,6+1,0 |
17,94 |
36,19 |
32,35 |
15,54 |
15,61 |
|
–1,0+0,63 |
12,60 |
36,02 |
30,02 |
10,85 |
10,17 |
|
–0,63+0,40 |
8,47 |
35,86 |
30,65 |
7,27 |
6,98 |
|
–0,40+0,2 |
7,26 |
38,39 |
33,60 |
6,67 |
6,56 |
|
–0,2+0,16 |
2,04 |
45,60 |
39,12 |
2,23 |
2,15 |
|
–0,16+0,125 |
2,08 |
50,11 |
44,42 |
2,50 |
2,49 |
|
–0,125+0,10 |
3,39 |
54,14 |
47,30 |
4,40 |
4,32 |
|
–0,10+0,071 |
4,59 |
57,39 |
54,84 |
6,30 |
6,77 |
|
–0,071+0,045 |
6,68 |
57,39 |
54,48 |
9,18 |
9,79 |
|
–0,045+0 |
12,91 |
54,2 |
52,03 |
16,74 |
18,08 |
|
Итого |
100,00 |
41,79 |
37,17 |
100,00 |
100,00 |
Номинальная крупность исходного продукта d95 составила 2,6 мм (это крупность, соответствующая размеру отверстия сита, через которое проходит 95 % материала). Более 68 % материала пробы находится в классах крупнее 0,315 мм, количество фракции –0,045 мм составило 12,9 %.
Анализ характеристики продукта выявил постепенное увеличение содержания железа с уменьшением класса крупности, причем наиболее заметное повышение значений наблюдается начиная с крупности –0,16+0,125 мм, где содержания Feобщ и Feмагн превышают средние значения по пробе на 7-8 %, а в классах менее 0,1 мм эта разница достигает 16-17 %.
Концентрация железа в данных классах свидетельствует о наличии значительной доли раскрытого минерала, что позволяет рассматривать возможность направления его непосредственно на обогащение, тем более что во фракции –0,16+0 мм сосредоточено около 40 % магнетита. Это подтверждается данными минералогического изучения раскрытия магнетита в пробе: первые раскрытые зерна магнетита начинают появляться в классах –0,63+0,4 мм (около 10 % свободных зерен), в классе –0,16+0,125 их количество увеличивается до 70 %, а в классах менее 0,1 мм достигает значений 90-97 % свободных зерен.
Исходя из приведенных данных, классификацию (тонкое грохочение) целесообразно проводить, начиная с крупности 0,16 мм и до 0,071 мм. Грохочение по крупности 0,045 мм не рассматривалось, поскольку количество данного класса не превышает 13 % и классификация на такой тонкой сетке потребует значительного фронта грохочения.

Рис.1. Схема проведения сравнительных опытов

Рис.2. Общий вид лабораторной установки МГ-сепаратора периодического действия
Сущность исследований состоит в проведении серий опытов при подаче на обогащение руды, доизмельченной до различной крупности (в данном случае от 50 до 85 % класса –0,045 мм) с использованием классификации по зерну различной крупности. Выбор крупности измельчения, как анализируемого фактора, обусловлен тем, что при использовании стадиального вывода концентрата возникает необходимость решения важной задачи, заключающейся в выборе такой крупности обогащения, при которой возможно получение не только концентрата с максимальным качеством, но и отвальных хвостов. Для целенаправленного формирования и своевременного вывода на обогащение эффективно обогащаемого класса крупности используется операция тонкого грохочения, поэтому выбор оптимальной крупности классификации является важным фактором, позволяющим не только повысить эффективность разделения минералов на гравитационно-магнитном обогащении, но и уменьшить переизмельчение рудных минералов, приводящее к снижению их магнитных свойств.
По схеме, представленной на рис.1, проведено четыре серии опытов с классификацией по зерну 0,16; 0,125; 0,1 и 0,071 мм. Внутри каждой серии надрешетный продукт доизмельчен до крупности 50-85 % класса –0,045 мм при времени измельчения 20, 25, 35 и 45 мин. Минералогический анализ раскрытия рудных минералов не проводился из-за трудоемкости исследований, эффективность измельчения оценивалась по выходу и качеству хвостов обогащения (слив МГ-сепаратора) [37].
В каждой серии опытов выбирался режим, позволяющий получать максимальные показатели, и уже среди них устанавливался оптимальный режим обогащения, отвечающий на два главных вопроса – по зерну какой крупности проводить классификацию и до какой крупности доизмельчать надрешетный продукт.
Для измельчения использовалась шаровая мельница МЛ-7, работающая в следующем режиме: масса шаровой загрузки 9 кг (шары Ø40 мм – 32 %, Ø10 мм – 68 %), масса навески 1200 г, плотность пульпы 62,5 % твердого. Магнитно-гравитационная сепарация проводилась на лабораторной установке периодического действия, в состав которой входят (рис.2):
- МГ-сепаратор, цилиндроконический корпус которого изготовлен из немагнитного прозрачного материала, а снаружи на уровне цилиндрической части расположена электромагнитная система в виде соленоидной катушки. В верхней части корпус сепаратора снабжен круговым сливным желобом со сливным патрубком, а в нижней – в вершине конической части корпуса установлен разгрузочный патрубок с двухходовым краном для подачи промывной воды или выпуска концентрата (магнитного продукта);
- блок питания постоянного напряжения для регулирования напряженности магнитного поля;
- лопастная мешалка с регулируемым числом оборотов для создания центробежной составляющей восходящего потока.
Обсуждение результатов
Обогащение по исследуемой схеме проводилось с получением трех продуктов. Надрешетный продукт грохочения (№ 1) на сепарацию не подавался, в реальных технологических условиях он будет являться циркулирующим продуктом. Магнетитовый концентрат (№ 2) представляет собой магнитную фракцию МГ-сепаратора, а соответственно продукт № 3 – хвосты обогащения, которые выделяются в слив МГ-сепаратора.
Таблица 2
Показатели обогащения пробы железистых кварцитов, полученные в сериях сравнительных опытов
Показатели |
Время измельчения, мин |
||||||||||||
20 |
25 |
35 |
45 |
||||||||||
Номер продукта на схеме обогащения |
|||||||||||||
№ 1 |
№ 2 |
№ 3 |
№ 1 |
№ 2 |
№ 3 |
№ 1 |
№ 2 |
№ 3 |
№ 1 |
№ 2 |
№ 3 |
||
Классификация по зерну 0,16 мм |
|||||||||||||
γ, % |
3,87 |
52,61 |
43,53 |
1,89 |
50,68 |
47,44 |
0,53 |
48,75 |
50,72 |
0,44 |
48,61 |
50,95 |
|
βFeобщ, % |
31,20 |
67,77 |
11,32 |
32,66 |
68,31 |
13,93 |
35,06 |
68,18 |
16,82 |
33,54 |
68,30 |
16,86 |
|
βFeмагн, % |
Не опр. |
Не опр. |
3,47 |
Не опр. |
Не опр. |
5,69 |
Не опр. |
Не опр. |
9,09 |
Не опр. |
Не опр. |
9,46 |
|
εFeобщ, % |
2,89 |
85,32 |
11,79 |
1,47 |
82,74 |
15,79 |
0,44 |
79,23 |
20,33 |
0,35 |
79,16 |
20,49 |
|
Е, % |
–2,3 |
77,4 |
–75,1 |
–1,0 |
76,0 |
–75,0 |
–0,2 |
72,5 |
–72,3 |
–0,2 |
–72,4 |
–72,4 |
|
d95, мм |
0,110 |
0,08 |
0,065 |
0,055 |
|||||||||
β–0,045, % |
53,0 |
60,2 |
67,0 |
75,3 |
|||||||||
Классификация по зерну 0,125 мм |
|||||||||||||
γ, % |
4,26 |
51,52 |
44,22 |
2,37 |
51,80 |
45,83 |
0,69 |
50,04 |
49,27 |
0,52 |
48,74 |
50,74 |
|
βFeобщ, % |
30,72 |
68,64 |
11,09 |
33,77 |
68,88 |
11,33 |
36,00 |
69,37 |
13,70 |
33,77 |
69,56 |
15,06 |
|
βFeмагн, % |
Не опр. |
Не опр. |
2,92 |
Не опр. |
Не опр. |
2,83 |
Не опр. |
Не опр. |
5,51 |
Не опр. |
Не опр. |
6,76 |
|
εFeобщ, % |
3,14 |
85,06 |
11,80 |
1,92 |
85,62 |
12,46 |
0,59 |
83,22 |
16,19 |
0,42 |
81,26 |
18,32 |
|
Е, % |
–2,6 |
78,8 |
–76,2 |
–1,1 |
–79,7 |
–78,6 |
–0,2 |
78,3 |
–78,1 |
–0,2 |
76,7 |
–76,5 |
|
d95, мм |
0,104 |
0,093 |
0,081 |
0,071 |
|||||||||
β–0,045, % |
56,1 |
61,0 |
70,7 |
76,7 |
|||||||||
Классификация по зерну 0,10 мм |
|||||||||||||
γ, % |
7,31 |
49,91 |
42,78 |
4,14 |
50,69 |
45,17 |
1,37 |
51,17 |
47,44 |
0,66 |
49,12 |
50,22 |
|
βFeобщ, % |
33,44 |
69,14 |
11,17 |
28,55 |
69,30 |
11,94 |
38,15 |
69,74 |
12,32 |
36,99 |
70,20 |
14,56 |
|
βFeмагн, % |
Не опр. |
Не опр. |
3,01 |
Не опр. |
Не опр. |
3,00 |
Не опр. |
Не опр. |
4,53 |
Не опр. |
Не опр. |
6,02 |
|
εFeобщ, % |
5,86 |
82,69 |
11,46 |
2,83 |
84,23 |
12,94 |
1,24 |
84,86 |
13,90 |
0,58 |
82,02 |
17,40 |
|
Е, % |
–3,4 |
77,4 |
–74,0 |
–3,1 |
79,1 |
–76,0 |
–0,3 |
80,4 |
–80,1 |
–0,2 |
78,5 |
–78,3 |
|
d95, мм |
0,094 |
0,082 |
0,074 |
0,064 |
|||||||||
β–0,045, % |
60,2 |
65,07 |
73,1 |
79,9 |
|||||||||
Классификация по зерну 0,071 мм |
|||||||||||||
γ, % |
12,74 |
46,75 |
40,51 |
7,42 |
48,96 |
43,62 |
2,84 |
50,03 |
47,13 |
1,12 |
49,17 |
49,71 |
|
βFeобщ, % |
37,20 |
69,15 |
10,72 |
37,58 |
69,23 |
11,19 |
36,90 |
69,85 |
11,74 |
36,64 |
69,99 |
13,53 |
|
βFeмагн, % |
Не опр. |
Не опр. |
2,29 |
Не опр. |
Не опр. |
2,44 |
Не опр. |
Не опр. |
3,43 |
Не опр. |
Не опр. |
4,81 |
|
εFeобщ, % |
11,45 |
78,06 |
10,49 |
6,71 |
81,55 |
11,74 |
2,53 |
84,15 |
13,32 |
0,99 |
82,82 |
16,19 |
|
Е, % |
–3,0 |
73,1 |
–70,1 |
–1,7 |
76,5 |
–74,8 |
–0,7 |
80,0 |
–79,3 |
–0,3 |
79,0 |
–78,7 |
|
d95, мм |
0,065 |
0,064 |
0,062 |
0,058 |
|||||||||
β–0,045, % |
73,2 |
73,6 |
75,4 |
83,2 |
Примечания: γ – выход продукта; βFeобщ и βFeмагн – содержание общего и магнитного железа соответственно; εFeобщ – извлечение общего железа; Е – эффективность обогащения; d95 – номинальная крупность продукта; β–0,045 – содержание класса –0,045 мм в продукте.

Рис.3. Зависимость эффективности магнитно-гравитационного обогащения от крупности питания и использования тонкого грохочения 1 – классификация 0,16 мм; 2 – 0,125 мм; 3 – 0,1 мм; 4 – 0,071 мм
В табл.2 приведены основные показатели разделения исходной пробы при использовании измельчения, магнитно-гравитационного обогащения и классификации по зерну различной крупности. Для характеристики крупности продукта определялась номинальная крупность продукта d95 и контролировалось содержание класса –0,045 мм (β–0,045). В продуктах обогащения химическим методом определялось содержание Feобщ во всех продуктах, Feмагн только в хвостах для оценки потерь полезного компонента.
Анализ полученного массива данных проводился с точки зрения эффективности разделения по наиболее распространенному в обогащении технологическому критерию Ханкока – Луйкена:
где ε – извлечение полезного компонента, %; γ – выход продукта, %; α – содержание полезного компонента, %; βт – максимально возможное теоретическое содержание железа в магнетите, βт = 72,4 %.
По всем сериям опытов получены достаточно высокие значения эффективности разделения, которые варьируются в интервале от 72 до 80 %, что положительно характеризует процесс МГ-сепарации. Графики зависимости эффективности обогащения от крупности питания и размера ячейки грохочения приведены на рис.3.
Рассматривая одинаковые режимы измельчения, отметим, что уменьшение размера ячейки грохота приводит к увеличению массовой доли надрешетного продукта, снижению выхода концентрата и эффективности обогащения. При сопоставлении этих показателей с другими режимами измельчения могут возникать ситуации, когда при одинаковой крупности продукта в питании сепарации достигается различная эффективность обогащения, например: при крупности в питании 0,65 мм эффективность разделения может составлять 73 % при классификации по зерну 0,071 мм и быть выше (около 79 %) при более грубой классификации 0,1 мм.
Поэтому в каждой серии опытов на кривых эффективности обогащения выделены максимальные значения, которым соответствуют определенные значения крупности продукта при классификации по зерну: 0,16 мм, d95 = 0,11 мм; 0,125 мм, d95 = 0,095 мм; 0,10 мм, d95 = = 0,076 мм; 0,071 мм, d95 = 0,063 мм.
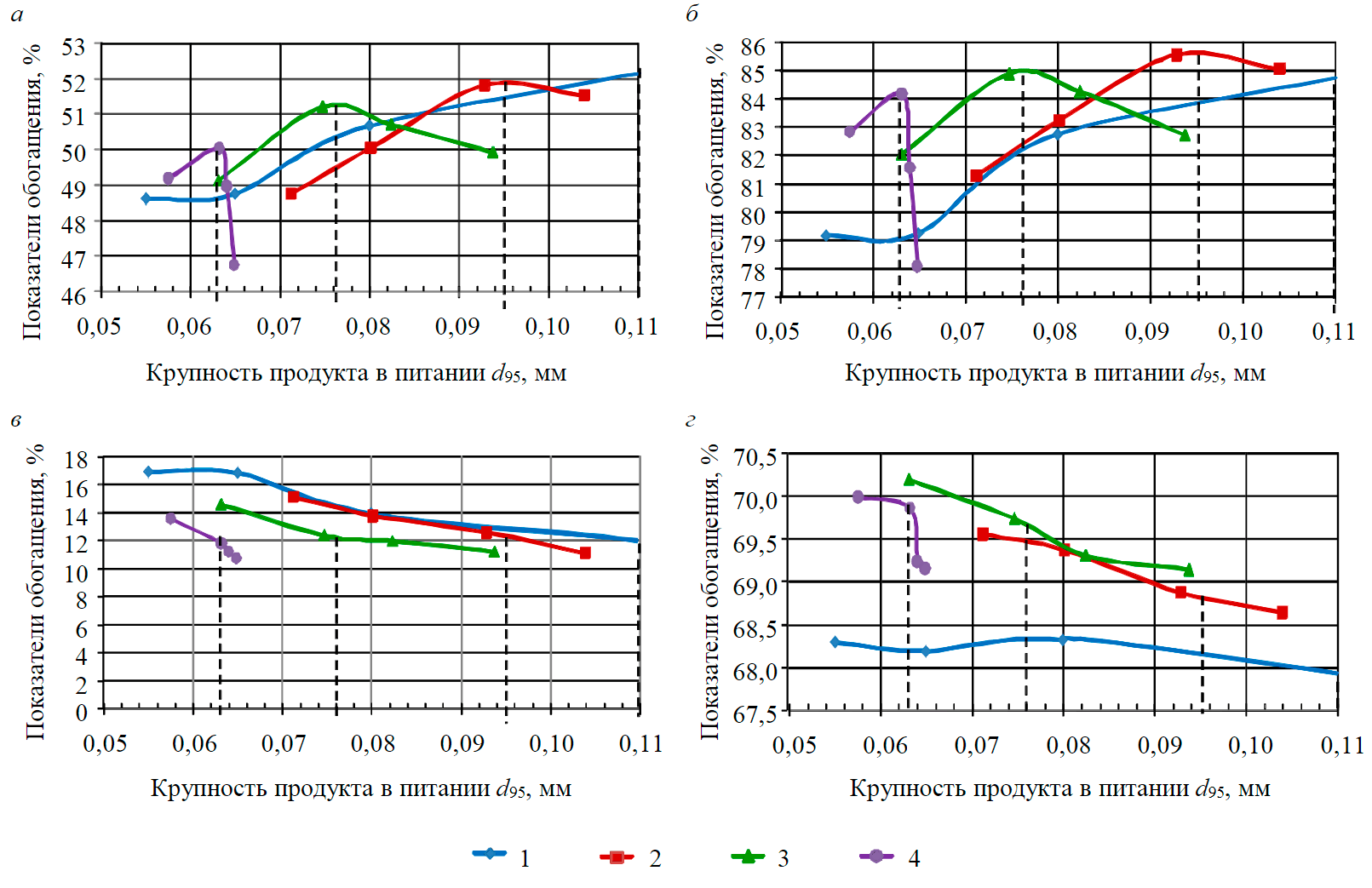
Рис.4. Показатели магнитно-гравитационного обогащения при использовании классификации по зерну различной крупности: а – выход концентрата; б – извлечение Feобщ в концентрат; в – содержание Feобщ в сливе; г – содержание Feобщ в концентрате 1-4 – см. условные обозначения на рис.3

Рис.5. Показатели, полученные при максимальной эффективности обогащения в опытах с классификацией по зерну различной крупности 1 – извлечение Feобщ; 2 – эффективность обогащения; 3 – содержание Feобщ в концентрате; 4 – выход концентрата

Рис.6. Содержание железа в хвостах обогащения
Используя полученные значения оптимальной крупности продукта, в которых достигается максимальная эффективность МГ-сепарации, по характеристикам основных показателей обогащения каждой серии опытов, представленным на рис.4, определены соответствующие этой крупности значения. Все они приведены на рис.5, где в нулевой точке (размер ячейки грохота 0 мм) представлены максимальные значения, полученные в опытах без классификации, которые были проведены дополнительно. Характер экспериментальных зависимостей рассматриваемых параметров показывает, что в исследуемых диапазонах крупности классификации они могут быть описаны полиномом второго порядка с высокой достоверностью аппроксимации R2:
- извлечение Feобщ в концентрат y= –58,04x2 + 27,0x + 82,73, R2 = 0,949;
- эффективность обогащения y= –623,2x2 + 118,8x + 74,37, R2 = 0,983;
- выход концентрата y= 178,2x2 – 16,32x + 50,78, R2 = 0,852;
- содержание Feобщ в концентрате y= –355,7x2 + 59,02x + 67,34, R2 = 0,978.
Из рис.5 следует, что максимум эффективности обогащения 80,4 % достигается при крупности классификации 0,1 мм, при этом содержание Feобщ в концентрате составляет 69,7 %, извлечение 85,1 %. Нахождение максимума обогащения в этом диапазоне крупности согласуется с данными о вкрапленности магнетита в рудах Стойленского месторождения, которая в среднем составляет около 0,08 мм.
Анализируя потери железа с хвостами (рис.6), отметим, что при выбранном режиме разделения они находятся в зоне минимальных значений, их содержание составляет Feобщ около 12 % и Feмагн 3-4 %.
Таким образом, для достижения оптимальных показателей при магнитно-гравитационном обогащении магнетитовой руды Стойленского ГОКа необходимыми условиями являются:
- использование тонкого грохочения с размером ячейки сита 0,1 мм;
- доизмельчение надрешетного продукта до крупности 70-73 % класса –0,045 мм, что соответствует номинальной крупности d95= 0,076 мм.
Самые низкие значения эффективности обогащения и содержания Feобщ в концентрате были получены при обогащении руды без классификации, но при этом наблюдаются самые высокие потери железа со сливом. Это доказывает, что своевременный вывод готового для обогащения продукта (с использованием тонкого грохочения) из питания мельницы позволяет предотвратить переизмельчение полезного компонента и повысить эффективность его обогащения.
Заключение
Одним из перспективных путей решения проблемы повышения качества железорудных концентратов является реализация технологии стадиального вывода концентрата, основанная на сочетании операций тонкого грохочения, доизмельчения и магнитно-гравитационного обогащения.
В работе представлены исследования, направленные на поиск оптимальных параметров и режимов разделения путем совместной оптимизации операций рудоподготовки и обогащения. Для этой цели разработан научно-методический подход к проведению экспериментов, включающий несколько основных этапов:
- Исходя из анализа гранулометрического и химического состава, а также данных по вкрапленности и раскрытию полезного компонента выбирается крупность классификации, при которой будет проводиться операция тонкого грохочения. Для исследуемой руды диапазон такой крупности составил от 0,16 до 0,071 мм.
- После классификации по выбранному классу крупности проводится измельчение надрешетного продукта, где исследуется свой диапазон крупности. Выбор крупности измельчения зависит от вкрапленности полезного компонента в изучаемом сырье, а для корректного построения зависимостей необходимо провести не менее 3-4 измельчений. Для исследуемой руды крупность измельчения составила 50-85 % класса –0,045 мм.
- Выбор оптимальных параметров рудоподготовки проводится по результатам последующего обогащения, в нашем случае магнитно-гравитационной сепарации. В качестве критерия оценки выбран такой технологический параметр, как эффективность обогащения, рассчитанная по формуле Ханкока – Луйкена.
В результате исследований получаются экспериментальные зависимости, связывающие технологические показатели обогащения с параметрами процесса грохочения. Для исследуемой руды железистых кварцитов полученные зависимости могут быть описаны полиномом второго порядка с высокой достоверностью аппроксимации. Наилучшие показатели достигаются при крупности классификации 0,1 мм, при этом содержание Feобщ в концентрате составляет 69,7 %, извлечение 85 %, эффективность классификации 80,4 %. Номинальная крупность продукта при этом составляет –0,076 мм, что соответствует крупности измельчения 70-73 % класса –0,045 мм.
Предложенный методический подход по выбору оптимальных режимов работы оборудования для схемы стадиального вывода концентрата может быть использован не только для железистых кварцитов Стойленского ГОКа, но и рядовых и бедных железных руд других месторождений.
Литература
- Артяева М.А., Пономаренко Т.В. Обзор крупнейших компаний на мировом рынке черных металлов // Социально-экономические явления и процессы. 2017. Т. 12. № 6. С. 9-16. DOI: 10.20310/1819-8813-2017-12-6-9-16
- Растянникова Е.В. Железорудная промышленность в странах БРИКС – перспективы четвертой промышленной революции // Экономика: вчера, сегодня, завтра. 2018. Т. 8. № 8А. С. 334-346.
- Эрикссон М., Лёф А., Лёф О. Обзор мирового рынка железной руды за 2019-2020 годы // Горная промышленность. 2021. № 1. С. 74-82. DOI: 10.30686/1609-9192-2021-1-74-82
- Lu Liming. Iron ore: mineralogy, processing and environmental sustainability. Cambridge: Woodhead Publishing, 2015. 641 p.
- Рудыка В.И. Перспективы технологии прямого восстановления железа в металлургическом производстве // Черная металлургия. Бюллетень научно-технической и экономической информации. 2017. № 11. С. 14-22.
- Юшина Т.И., Чантурия Е.Л., Думов А.М., Мясков А.В. Современные тенденции в развитии технологий переработки железных руд // Горный журнал. 2021. № 11. С. 75-83. DOI: 10.17580/gzh.2021.11.10
- Oliazadeh M., Vazirizadeh А.Removing impurities from iron ores: methods and industrial cases // XXVIII International Mineral Processing Congress (IMPC 2016), 11-15 September 2016, Quebec, Canada. Canadian Institute of Mining Metallurgy & Petroleum, 2016. P. 4290-4302.
- БарановВ.Ф., ПатковскаяН.А, ТасинаТ.И. Современные тенденции в технологии переработки магнетитовых железных руд. Основные направления // Обогащение руд. 2013. № 3. С. 10-17.
- Максимов И.И., Сентемова В.А. Особенности технологии обогащения окисленных железистых кварцитов с повышенным содержанием магнетита // Обогащение руд. 2012. № 3. С. 7-10.
- Пелевин А.Е., Корнилков С.В., Дмитриев А.Н., Багазеев В.К. Повышение качества магнетитовых концентратов при раздельном обогащении природных типов и разновидностей железных руд // Горный информационно-аналитический бюллетень. 2021. № 11-1. С. 306-317. DOI: 10.25018/0236_1493_2021_111_0_306
- Олейник Т.А., Мулявко В.И., Ляшенко В.И., Олейник М.О. Развитие технологий и технических средств обогащения гематитовых руд // Черная металлургия. Бюллетень научно-технической и экономической информации. 2016. № 5. С. 5-10.
- Исмагилов Р.И., Козуб А.В., Гридасов И.Н., Шелепов Э.В. Современные направления повышения эффективности переработки железистых кварцитов на примере АО «Михайловский ГОК им. А.В.Варичева» // Горная промышленность. 2020. № 4. С. 98-103. DOI: 10.30686/1609-9192-2020-4-98-103
- AbhyarthanaPattanaik, VenugopalRayasam. Analysis of reverse cationic iron ore fines flotation using RSM-D-optimal design – An approach towards sustainability // Advanced Powder Technology. 2018. Vol. 29. Iss. 12. P. 3404-3414. DOI: 10.1016/j.apt.2018.09.021
- Xiaolong Zhang, Xiaotian Gu, Yuexin Han et al. Flotation of Iron Ores: A Review // Mineral Proceeding and Extractive Metallurgy Review. 2021. Vol. 42. Iss. 3. P. 184-212. DOI: 10.1080/08827508.2019.1689494
- Elves Matiolo, Hudson Jean Bianquini Couto, Neymayer Lima et al. Improving recovery of iron using column flotation of iron ore slimes // Minerals Engineering. 2020. Vol. 158. № 106608. DOI: 10.1016/j.mineng.2020.106608
- Wanzhong Yin., Jizhen Wang, Longhua Xu. N Reagents in the Reverse Flotation of Carbonate-Containing Iron Ores // Proceedings of the 11th International Congress for Applied Mineralogy. Cham: Springer International Publishing, 2015. P.459-470.
- Пелевин А.Е. Повышение эффективности обогащения железорудного сырья путем применения сепарации в переменном магнитном поле // Черные металлы. 2021. № 5. С. 4-9. DOI: 10.17580/chm.2021.05.01
- Jiang Wen, Zhang Yimin. Development and application of complex Flashing-field magnetic cleaner // Advanced Materials Research. 2014. Vol. 1073-1076. Р. 2177-2188. DOI: 10.4028/www.scientific.net/AMR.1073-1076.2177
- Rosario P.P. Technical and economic assessment of a non-onventional HPGR circuit // Minerals Engineering. 2017. Vol.103-104. P. 102-111. DOI: 10.1016/j.mineng.2016.10.019
- Прокопьев С.А., Пелевин А.Е., Напольских С.А., Гельбинг Р.А. Стадиальное выделение магнетитового концентрата с использованием винтовой сепарации // Обогащение руд. 2018. № 4. С. 28-33. DOI: 10.17580/or.2018.04.06
- Sadeghi M., Bazin C., Hodouin D. et al. Control of spiral concentrators for the concentration of iron ore // XXVIII International Mineral Processing Congress (IMPC 2016), 11-15 September 2016, Quebec, Canada. Canadian Institute of Mining Metallurgy & Petroleum, 2016. P. 4534-4545.
- Kuskov V., Kuskova Y., Udovitsky V. Effective processing of the iron ores // IInd International Innovative Mining Symposium (Devoted to Russian Federation Year of Environment), 20-22 November 2017, Kemerovo, Russia. E3S Web of Conferences, 2017. Vol. 21. № 02010. DOI: 10.1051/e3sconf/20172102010
- Вайсберг Л.А., Кускова Я.В. Совершенствование круглых концентрационных столов как развитие гравитационных методов обогащения // Обогащение руд. 2017. № 4. С. 54-60. DOI: 10.17580/or.2017.04.10
- Fomin A.V., Khokhulya M.S. Improving efficiency of gravity separation of fine iron ore materials using computer modeling // Topical Issues of Rational Use of Natural Resources. London: Taylor & Francis Group CRC Press, 2019. Vol.2. P. 509-516.
- Гзогян Т.Н., Винников В.А. Процессы фракционирования и разделения в схемах обогащения железистых кварцитов сложного состава // Горный информационно-аналитический бюллетень. 2012. № 8. С. 172-177.
- Коровников А.Н., Бузунова Т.А. Исследование процесса классификации рудных пульп на вибрационном грохоте // Обогащение руд. 2018. № 5. С. 17-21. DOI: 10.17580/or.2018.05.03
- Леонов В. Практика технологий Derrick в горнодобывающей промышленности // Майнинг Репорт Глюкауф на русском языке. 2014. № 3. С. 66-70. URL (дата обращения 14.09.2022).
- Пелевин А.Е., Сытых Н.А. Применение тонкого гидравлического грохочения для стадиального выделения титаномагнетитового концентрата // Обогащение руд. 2021. № 1. С. 8-14. DOI: 10.17580/or.2021.01.02
- Цыпин Е.Ф., Мамонов С.В., Власов И.А. Продукты классификации и тонкого грохочения замкнутого цикла измельчения медно-цинковой руды // Известия вузов. Цветная металлургия. 2016. № 2. С. 4-11. DOI: 10.17073/0021-3438-2016-2-4-11
- Albuquerque L.G., Wheeler J.E., Valine S.B. Application of high frequency screens in closing grinding circuits // Revista Escola de Minas. 2009. Vol. 62. № 1. P. 167-173.
- Jahani M., Farzanegan A., Noaparast M. Investigation of screening performance of banana screens using LIGGGHTS DEM solver // Powder Technology. 2015. Vol. 283. P. 32-47. DOI: 10.1016/j.powtec.2015.05.016
- Опалев А.С., Хохуля М.С., Фомин А.В., Карпов И.В. Создание инновационных технологий производства высококачественного железорудного концентрата на предприятиях Северо-Запада России // Горный журнал. 2019. № 6. С. 56-61. DOI: 10.17580/gzh.2019.06.07
- Опалев А.С., Карпов И.В., Кривовичев С.В. Повышение эффективности переработки магнетитовых кварцитов на АО «Карельский окатыш» // Горный журнал. 2021. № 11. С. 66-74. DOI: 10.17580/gzh.2021.11.09
- Гриненко В.И., Опалев А.С., Маевский П.В., Карпов И.В. Повышение качества железорудного концентрата на АО «ССГПО» методом магнитно-гравитационной сепарации // Горный журнал. 2021. № 10. С. 81-86. DOI: 10.17580/gzh.2021.10.10
- Гзогян С.Р., Щербаков А.В. Повышение качества концентратов АО «Стойленский ГОК» с использованием магнито-гравитационной сепарации // Обогащение руд. 2020. № 6. С. 3-8. DOI: 10.17580/or.2020.06.01
- Гзогян Т.Н., Опалев А.С., Гзогян С.Р., Щербаков А.В. Применение магнитно-гравитационной сепарации для получения высококачественных концентратов из железистых кварцитов КМА // Материалы XII Конгресса обогатителей стран СНГ, 25-27 февраля 2019, Москва, Россия. М.: ИТЕП, 2019. С. 182-186.
- Пелевин А.Е., Сытых Н.А. Испытания двухстадиальной схемы измельчения титаномагнетитовой руды // Обогащение руд. 2018. № 2. С. 13-18. DOI: 10.17580/or.2018.02.03