Methodological substantiation of the choice for optimal modes of equipment operation during the stage-wise concentrate removal in iron ores beneficiation
Abstract
The urgent task of improving the quality of iron ore concentrates was studied. We propose to use the stage-wise removal of the concentrate by combining fine screening, regrinding, and magnetic-gravity separation. Exemplified by magnetite ore from the Stoilensky GOK, a scientific and methodological approach to the search for optimal separation parameters and modes was substantiated. It includes several stages: studying the particle size distribution and release of useful components in the feed product to select classification parameters; a series of experiments on grinding oversize products to diverse sizes; beneficiation of the obtained products by MG separation. To select the optimal parameters of ore preparation, an analysis of the beneficiation efficiency was used, which is calculated according to the Hancock – Luyken criterion. The results of the research are experimental dependences that connect the process parameters of beneficiation with those of fine vibratory screening. For the studied ferruginous quartzite ore processed at the Stoilensky GOK, the obtained dependences can be described by a second-order polynomial with a high accuracy of approximation. The best performance is achieved with a particle size of 0.1 mm: Fe tot content in the concentrate is 69.7 %, recovery is 85 %, classification efficiency is 80.4 %. The top size of the product in this case is 0.076 mm, which corresponds to 70-73 % grinding size of –0.045 class.
Introduction
Extraction and processing of iron ore is one of the leading sectors of mining in Russia, in part because this resource is one of the most important export items of our country. Demand for iron ore both in Russia and in the world will increase. This is due to the global population growth, development of new territories, and replacement of worn-out fixed assets. In terms of ore reserves, Russia ranks second in the world, yielding only to Brazil. The quality of domestic iron ore raw materials is noticeably lower than in other countries: the main part of the ores is lean and medium (run-of-mine) with a metal content of 16-40 % [1-4].
As a rule, beneficiation technologies for such ores are based on staged removal of tailings from the process, followed by grinding of the material in a closed cycle with classification and magnetic separation. At the present stage of iron ore processing, the use of multi-stage grinding and magnetic separation is associated with the need for fine grinding of ore at increased energy consumption. Traditional drum magnetic separators do not provide selective separation of fine fractions of magnetite and rock minerals, which leads both to a decrease in the concentrate quality and an increase in the loss of fine magnetite with final tailings.
Modern world requirements for the quality of iron ore products are constantly growing, while iron ore processing enterprises and companies around the world are actively looking for ways to improve the quality of their products. In recent years, due to the development of new industries, the demand for high-quality iron ore concentrates has significantly increased: for powder metallurgy 71.4-72 % Fetot, production of iron-nickel batteries 69-71 %, electrometallurgy processes 68-69.5 % and higher. There is practically no demand for low-grade concentrates and ores that cannot be beneficiated, which led to the cessation of the work of some enterprises (Kamysh-Burunsky plant, Bakalsky mine administration, etc.) [5-7].
Along with this, in the current economic conditions, reducing energy resources for manufactured products, increasing the integrated use of ores, and minimising the technogenic load on the environment are acute. The growth and improvement of production capacities is associated with the transition to deep beneficiation in order to improve the quality of concentrates (agglomerate, pellets) to 70 % and above, while additional costs should pay off at subsequent stages of processing (saving heat, coke, fluxes, increasing metal quality, etc.).
The main increase in the mass fraction of iron in concentrates is obtained by introducing finishing operations of fine grinding and fine screening [8-12], reverse cationic flotation [13-16], the use of more advanced magnetic separators [17-19], in a number of cases, gravity methods are used [20-24].
The identified set of problems suggests the need for scientific research on the development of new process solutions and the use of modern highly efficient equipment for the processing of ferruginous quartzites, providing high performance indicators in accordance with modern environmental safety requirements.
A promising direction for solving these issues is the staged production of high-quality magnetite concentrate by combining fine screening, regrinding, and magnetic-gravity (MG) separation. The operating principle of MG separation is based on the control of magnetic aggregation when a ferromagnetic suspension is exposed to a low-strength magnetic field and a centrifugally ascending water flow. Fine screening is widely used at many mining and beneficiating enterprises for diverse types of mineral raw materials and makes it possible to achieve an increase in the productivity of beneficiating plants, improve the quality of products, and reduce operating costs [25-31].
Such a technology for the staged production of high-quality concentrate was introduced at the crushing and beneficiation plant of “Olkon” JSC and made it possible to increase the concentrate quality to 69-70 % Fetot while maintaining the current level of magnetic iron extraction. In addition, it was possible to reduce the operating costs for the production of commercial iron ore concentrate within 10-15 % by eliminating the equipment used in the additional beneficiation sections [32]. Industrial tests of this technology at “Karelsky Okatysh” JSC made it possible to ensure the production of concentrate with a quality of 70 % Fetot while improving the performance indicators of production due to the timely removal of concentrate and tailings from the beneficiation circuit [33].
Industrial tests of the MG separator MGS-2.0 were carried out at the operating beneficiation plant “Sokolovsko-Sarbayskoye Mining and Beneficiation Production Association” JSC (Kazakhstan) in order to improve the quality of iron ore concentrate [34]. The proposed process for the staged removal of the finished concentrate will not only ensure an increase in product quality to 67-68 %, but also reduce current operating costs, which will have a positive effect on the profitability of products.
The MG separation technology was tested under industrial conditions for KMA ferruginous quartzites (JSC “Stoilensky GOK”) [35, 36]. The possibility to beneficiate magnetite concentrate by this method was established; an increase in the iron content in the concentrate was obtained on average 1.2 % (from 66.5 to 67.7 %). Unclassified material was separated, which led to the impoverishment of magnetite concentrates by a large class. Based on the test results, it is recommended to introduce fine screening to the circuit.
The tests performed showed that the implementation of the staged concentrate removal requires joint optimization of grinding, fine screening, and beneficiation. We propose an algorithm for comparative studies and the subsequent selection of optimal modes for classification and regrinding according to the beneficiation efficiency.
Materials and research methods
The studies were conducted exemplified by magnetite ore of the Stoilensky GOK with a particle size of –5 mm. The main ore mineral in the sample is magnetite, non-metallic minerals are represented by quartz, amphiboles, including alkaline ones, micas, and carbonate. There is an insignificant admixture of hematite, sulphides, apatite (2-3 % in total).
Waste tailings were separated from the sample by preliminary wet magnetic separation (the yield of tailings was 17.9 %, the content of Fetot and Femagn was 10.57 and 1.32 %, recovery was 5.23 and 0.77 %, respectively). The feed product for the study was magnetic fraction of the ore wet magnetic separation with Fetot content of about 41.8 %, Femagn 37.2 % (Table 1).
Table 1
Characteristics of the feed product for studies
Particle size classes, mm |
Yield, |
Content, % |
Distribution, % |
|||
Fetot |
Femagn |
Fetot |
Femagn |
|||
–5.0+3.15 |
0.15 |
34.02 |
27.30 |
0.12 |
0.11 |
|
–3.15+2.0 |
12.46 |
34.02 |
27.30 |
10.14 |
9.15 |
|
–2.0+1.6 |
9.42 |
35.74 |
30.84 |
8.06 |
7.82 |
|
–1.6+1.0 |
17.94 |
36.19 |
32.35 |
15.54 |
15.61 |
|
–1.0+0.63 |
12.60 |
36.02 |
30.02 |
10.85 |
10.17 |
|
–0.63+0.40 |
8.47 |
35.86 |
30.65 |
7.27 |
6.98 |
|
–0.40+0.2 |
7.26 |
38.39 |
33.60 |
6.67 |
6.56 |
|
–0.2+0.16 |
2.04 |
45.60 |
39.12 |
2.23 |
2.15 |
|
–0.16+0.125 |
2.08 |
50.11 |
44.42 |
2.50 |
2.49 |
|
–0.125+0.10 |
3.39 |
54.14 |
47.30 |
4.40 |
4.32 |
|
–0.10+0.071 |
4.59 |
57.39 |
54.84 |
6.30 |
6.77 |
|
–0.071+0.045 |
6.68 |
57.39 |
54.48 |
9.18 |
9.79 |
|
–0.045+0 |
12.91 |
54.2 |
52.03 |
16.74 |
18.08 |
|
Total |
100.00 |
41.79 |
37.17 |
100.00 |
100.00 |
The top size of the feed product d95 was 2.6 mm (this is the size corresponding to that of the sieve opening through which 95 % of the material passes). More than 68 % of the sample material is in classes larger than 0.315 mm, the amount of –0.045 mm fraction was 12.9 %.
An analysis of the product characteristics revealed a gradual increase in the iron content with a decrease in the particle size class, and the most noticeable increase in values is observed starting from the particle size of –0.16+0.125 mm, Fetot and Femagn contents exceed the average values for the sample by 7-8 %, and in classes less than 0.1 mm, this difference reaches 16-17 %.
The concentration of iron in these classes indicates the presence of a considerable proportion of the released mineral, which enables to send it directly to beneficiation, especially since about 40 % of magnetite is concentrated in the –0.16+0 mm fraction. This is confirmed by the mineralogical study of magnetite release in a sample: the first released grains of magnetite begin to appear in –0.63+0.4 mm classes (about 10 % of free grains), in –0.16+0.125 class their number increases to 70 %, and in classes less than 0.1 mm it reaches 90-97 % of free grains.
Based on the above data, classification (fine screening) is advisable starting from particle size of 0.16 mm and up to 0.071 mm. Screening with a particle size of 0.045 mm was not considered, since the amount of this class does not exceed 13 % and classification on such a fine mesh will require a significant screening range.

Fig.1. Scheme of comparative experiments
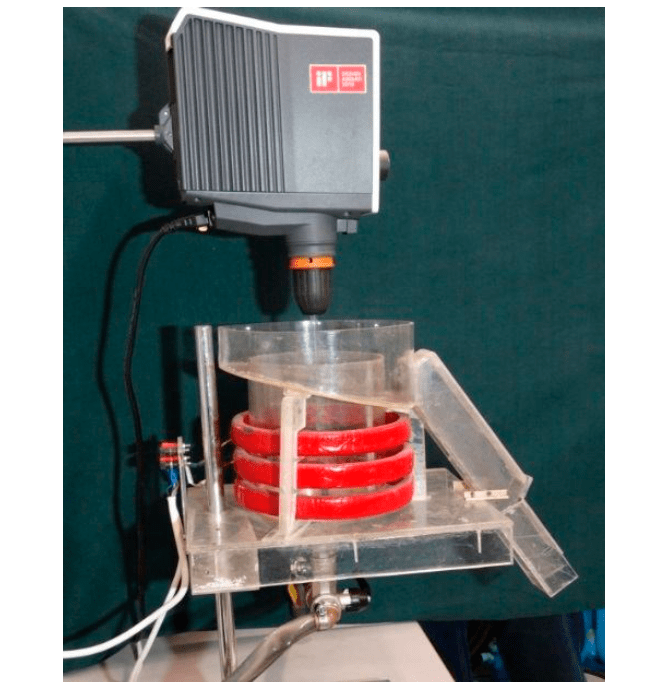
Fig.2. General view of the laboratory setup of the intermittent MG separator
The essence of the research is a series of experiments when supplying ore for beneficiation, regrinded to varied sizes (in this case, from 50 to 85 % of the –0.045 mm class) using classification by grains of diverse sizes. The choice of grinding size as an analysed factor is due to the fact that the staged concentrate removal requires solving an important problem, which is to choose such a particle size of beneficiation, at which it is possible to obtain not only a concentrate with maximum quality, but also tailings. For the purposeful formation and timely output for beneficiation of an efficiently beneficiated size class, a fine screening operation is used. Therefore, choosing the optimal size of classification is a crucial factor that allows not only to increase the efficiency of separating minerals in gravity-magnetic beneficiation, but also to reduce the overgrinding of ore minerals, leading to a decrease in their magnetic properties.
According to the scheme in Fig.1, four series of experiments were carried out with a grain classification of 0.16; 0.125; 0.1, and 0.071 mm. Within each series, the oversize product was ground to a size of 50-85 % of the –0.045 mm class at a grinding time of 20, 25, 35, and 45 min. The mineralogical analysis of the ore minerals release was not carried out due to the laboriousness of the research, the grinding efficiency was estimated by the yield and quality of the beneficiation tailings (drainage of the MG separator) [37].
In each series of experiments, a mode was chosen that allowed obtaining the maximum indicators, and among them the optimal beneficiation mode was established, answering two main questions: according to what grain size to classify and to what size to grind the oversize product.
For grinding, a ball mill ML-7 was used, operating in the following mode: ball load mass 9 kg (balls Ø40 mm – 32 %, Ø10 mm – 68 %), sample weight 1200 g, pulp density 62.5 % solid. Magnetic-gravity separation was carried out on a batch laboratory installation, which includes (Fig.2):
- MG separator, the cylinder-conical body of which is made of a non-magnetic transparent material, and on the outside, at the level of the cylindrical part, there is an electromagnetic system in the form of a solenoid coil. The upper part of the separator body is equipped with a circular drain chute with a drainpipe, and in the lower part, at the top of the conical part of the body, there is an unloading pipe with a two-way cock for supplying wash water or discharging the concentrate (magnetic product);
- DC power supply for regulation of magnetic field intensity;
- paddle agitator with adjustable speed to create a centrifugal component of the upward flow.
Discussion of the results
Beneficiation according to the circuit under study was carried out to obtain three products. The oversize screening product (N 1) was not fed to the separation, in real process conditions it will be a circulating product. Magnetite concentrate (N 2) is the magnetic fraction of the MG separator, and, accordingly, product N 3 is beneficiation tailings, which are released into the MG separator overflow.
Table 2
Beneficiation indicators of a sample of ferruginous quartzites obtained in a series of comparative experiments
Beneficiation |
Grinding time, min |
||||||||||||
20 |
25 |
35 |
45 |
||||||||||
Product N in the beneficiation circuit |
|||||||||||||
N 1 |
N 2 |
N 3 |
N 1 |
N 2 |
N 3 |
N 1 |
N 2 |
N 3 |
N 1 |
N 2 |
N 3 |
||
Classification by 0.16 mm grain |
|||||||||||||
γ, % |
3.87 |
52.61 |
43.53 |
1.89 |
50,68 |
47,44 |
0,53 |
48,75 |
50,72 |
0,44 |
48,61 |
50,95 |
|
βFetot, % |
31.20 |
67.77 |
11.32 |
32.66 |
68,31 |
13.93 |
35.06 |
68.18 |
16.82 |
33.54 |
68.30 |
16.86 |
|
βFemagn, % |
N/d |
N/d |
3.47 |
N/d |
N/d |
5.69 |
N/d |
N/d |
9.09 |
N/d |
N/d |
9.46 |
|
εFetot, % |
2.89 |
85.32 |
11.79 |
1.47 |
82.74 |
15.79 |
0.44 |
79.23 |
20.33 |
0.35 |
79.16 |
20.49 |
|
Е, % |
–2.3 |
77.4 |
–75.1 |
–1.0 |
76.0 |
–75.0 |
–0.2 |
72.5 |
–72.3 |
–0.2 |
–72.4 |
–72.4 |
|
d95, mm |
0.110 |
0.08 |
0.065 |
0.055 |
|||||||||
β–0.045, % |
53.0 |
60.2 |
67.0 |
75.3 |
|||||||||
Classification by 0.125 mm grain |
|||||||||||||
γ, % |
4.26 |
51.52 |
44.22 |
2.37 |
51.80 |
45.83 |
0.69 |
50.04 |
49.27 |
0.52 |
48.74 |
50.74 |
|
βFetot, % |
30.72 |
68.64 |
11.09 |
33.77 |
68.88 |
11.33 |
36.00 |
69.37 |
13.70 |
33.77 |
69.56 |
15.06 |
|
βFemagn, % |
N/d |
N/d |
2.92 |
N/d |
N/d |
2.83 |
N/d |
N/d |
5.51 |
N/d |
N/d |
6.76 |
|
εFetot, % |
3.14 |
85.06 |
11.80 |
1.92 |
85.62 |
12.46 |
0.59 |
83.22 |
16.19 |
0.42 |
81.26 |
18.32 |
|
Е, % |
–2.6 |
78.8 |
–76.2 |
–1.1 |
–79.7 |
–78.6 |
–0.2 |
78.3 |
–78.1 |
–0.2 |
76.7 |
–76.5 |
|
d95, mm |
0.104 |
0.093 |
0.081 |
0.071 |
|||||||||
β–0.045, % |
56.1 |
61.0 |
70.7 |
76.7 |
|||||||||
Classification by 0.10 mm grain |
|||||||||||||
γ, % |
7.31 |
49.91 |
42.78 |
4.14 |
50.69 |
45.17 |
1.37 |
51.17 |
47.44 |
0.66 |
49.12 |
50.22 |
|
βFetot, % |
33.44 |
69.14 |
11.17 |
28.55 |
69.30 |
11.94 |
38.15 |
69.74 |
12.32 |
36.99 |
70.20 |
14.56 |
|
βFemagn, % |
N/d |
N/d |
3.01 |
N/d |
N/d |
3.00 |
N/d |
N/d |
4.53 |
N/d |
N/d |
6.02 |
|
εFetot, % |
5.86 |
82.69 |
11.46 |
2.83 |
84.23 |
12.94 |
1.24 |
84.86 |
13.90 |
0.58 |
82.02 |
17.40 |
|
Е, % |
–3.4 |
77.4 |
–74.0 |
–3.1 |
79.1 |
–76.0 |
–0.3 |
80.4 |
–80.1 |
–0.2 |
78.5 |
–78.3 |
|
d95, mm |
0.094 |
0.082 |
0.074 |
0.064 |
|||||||||
β–0.045, % |
60.2 |
65.07 |
73.1 |
79.9 |
|||||||||
Classification by 0.071 mm grain |
|||||||||||||
γ, % |
12.74 |
46.75 |
40.51 |
7.42 |
48.96 |
43.62 |
2.84 |
50.03 |
47.13 |
1.12 |
49.17 |
49.71 |
|
βFetot, % |
37.20 |
69.15 |
10.72 |
37.58 |
69.23 |
11.19 |
36.90 |
69.85 |
11.74 |
36.64 |
69.99 |
13.53 |
|
βFemagn, % |
N/d |
N/d |
2.29 |
N/d |
N/d |
2.44 |
N/d |
N/d |
3.43 |
N/d |
N/d |
4.81 |
|
εFetot, % |
11.45 |
78.06 |
10.49 |
6.71 |
81.55 |
11.74 |
2.53 |
84.15 |
13.32 |
0.99 |
82.82 |
16.19 |
|
Е, % |
–3.0 |
73.1 |
–70.1 |
–1.7 |
76.5 |
–74.8 |
–0.7 |
80.0 |
–79.3 |
–0.3 |
79.0 |
–78.7 |
|
d95, mm |
0.065 |
0.064 |
0.062 |
0.058 |
|||||||||
β–0.045, % |
73.2 |
73.6 |
75.4 |
83.2 |
Notes: γ – product yield; βFetot and βFemagn – content of total and magnetic iron, respectively; εFetot– extraction of total iron; E is the beneficiation efficiency; d95 is the top size of the product; β–0.045 – the content of –0.045 mm class in the product.
Table 2 shows the main indicators of the separation of the feed sample using grinding, magnetic-gravity separation, and classification by grains of diverse sizes. To characterize the product particle size, the top size of the product d95 was determined and the content of the –0.045 mm class (β–0.045) was controlled. In beneficiation products, the content of Fetot was determined by the chemical method in all products, Femagn only in tailings to assess the loss of a useful component.
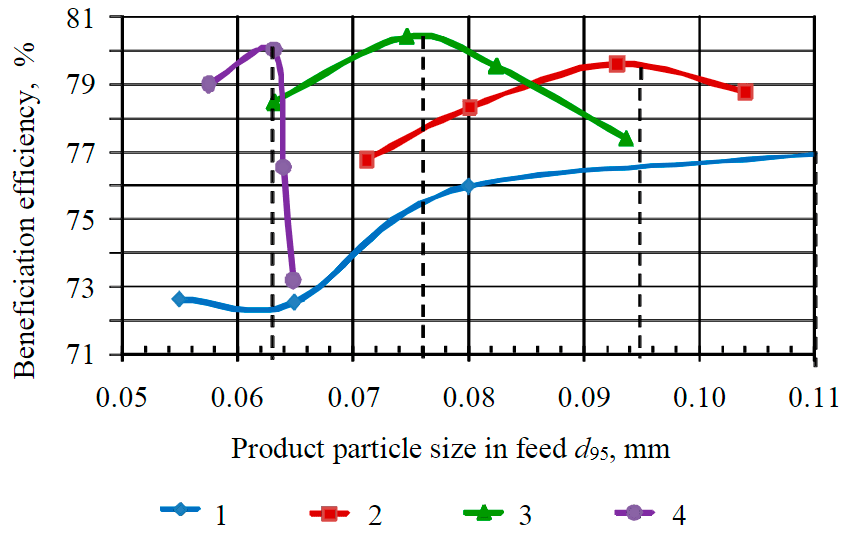
Fig.3. Dependence of the efficiency of magnetic-gravity enrichment on the size of the feed and the use of fine screening 1 – classification 0.16 mm; 2 – 0.125 mm; 3 – 0.1 mm; 4 – 0.071 mm
The obtained data array was analysed in terms of separation efficiency according to the most common Hancock – Luyken process criterion in beneficiation:
where ε is the extraction of a useful component, %; γ – product yield, %; α – useful component content, %; βt is the maximum possible theoretical iron content in magnetite, βt = 72.4 %.
For all series of experiments, rather high values of separation efficiency in the range from 72 to 80 % were obtained. This positively characterizes the MG separation. Graphs of the dependence of the beneficiation efficiency on the size of the feed and the size of the screening cell are shown in Fig.3.
Considering the same modes of grinding, we note that a decrease in the size of the screen cell leads to an increase in the mass fraction of the oversize product, a decrease in the concentrate yield and beneficiation efficiency. When comparing these indicators with other grinding modes, situations may arise when, with the same product particle size in the separation feed, different beneficiation efficiency is achieved, for example: with a feed particle size of 0.65 mm, the separation efficiency can be 73 % with a grain classification of 0.071 mm and be higher (about 79 %) with a coarser classification of 0.1 mm.
Therefore, in each series of experiments on the beneficiation efficiency curves, the maximum values are highlighted, which correspond to certain values of the product particle size when classifying by grain: 0.16 mm, d95 = 0.11 mm; 0.125 mm, d95 = 0.095 mm; 0.10 mm, d95 = 0.076 mm; 0.071 mm, d95 = 0.063 mm.
Using the obtained values of the optimal product particle size that promote the maximum efficiency of MG separation, the values corresponding to this particle size are determined according to the main beneficiation indicators of each series of experiments presented in Fig.4. All of them are shown in Fig.5, where at the zero point (screen cell size 0 mm) the maximum values obtained in experiments without classification, which were carried out additionally, are presented. The nature of the experimental dependences of the parameters under consideration shows that in the studied ranges of classification size, they can be described by
a second-order polynomial with a high accuracy of approximation R2:
- Fetot extraction into concentrate y = –58.04x2 + 27.0x + 82.73, R2 = 0.949;
- beneficiation efficiency y = –623.2x2 + 118.8x + 74.37, R2 = 0.983;
- concentrate yield y = 178.2x2 – 16.32x + 50.78, R2 = 0.852;
- Fetot content in concentrate y = –355.7x2 + 59.02x + 67.34, R2 = 0.978.
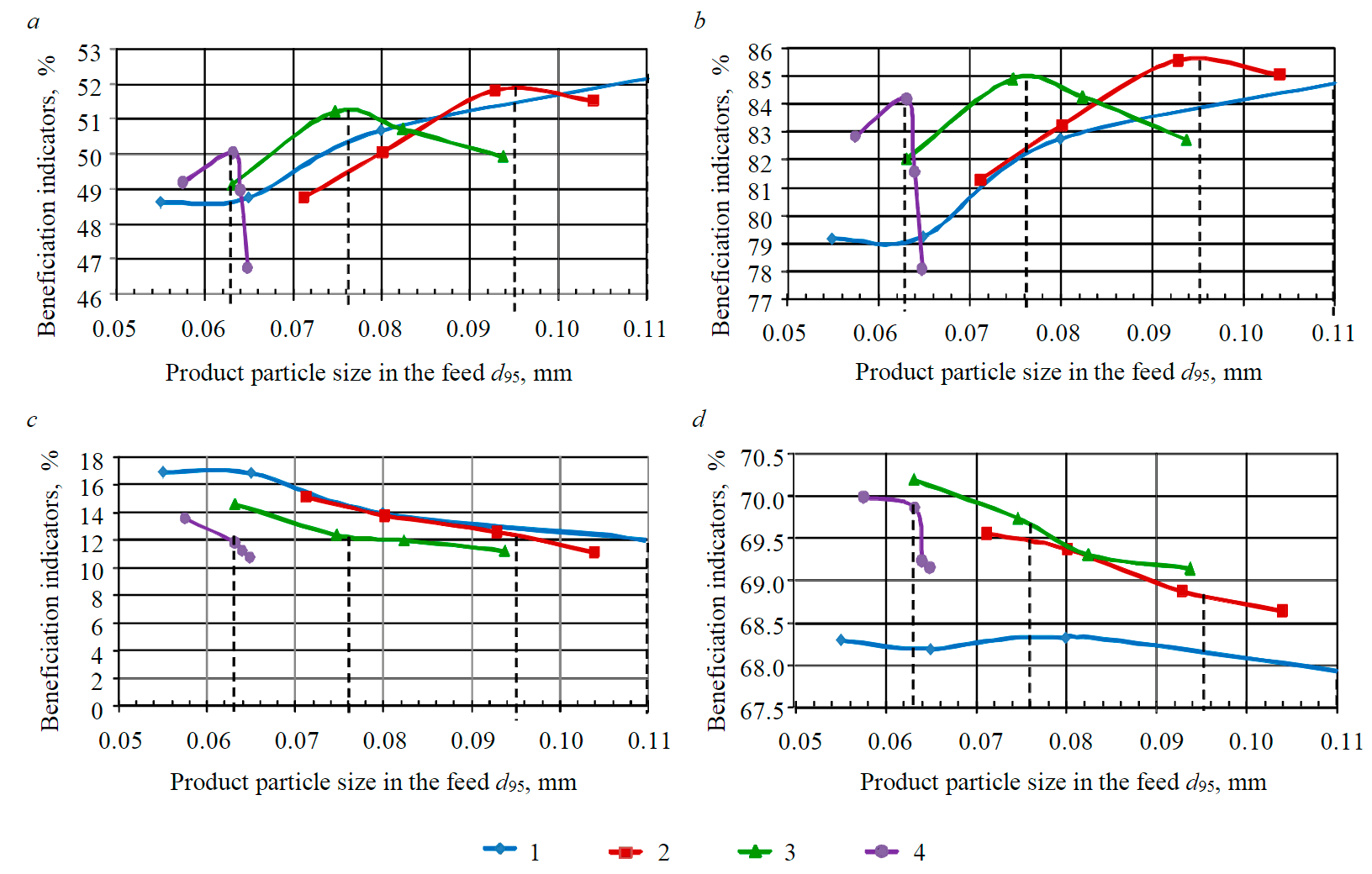
Fig.4. Indicators of magnetic-gravity beneficiation when using classification by grains of various sizes: a – concentrate yield; b – Fetot extraction into the concentrate; c – Fetot content in the overflow; d – Fetot content in the concentrate 1-4 – see legend in Fig.3
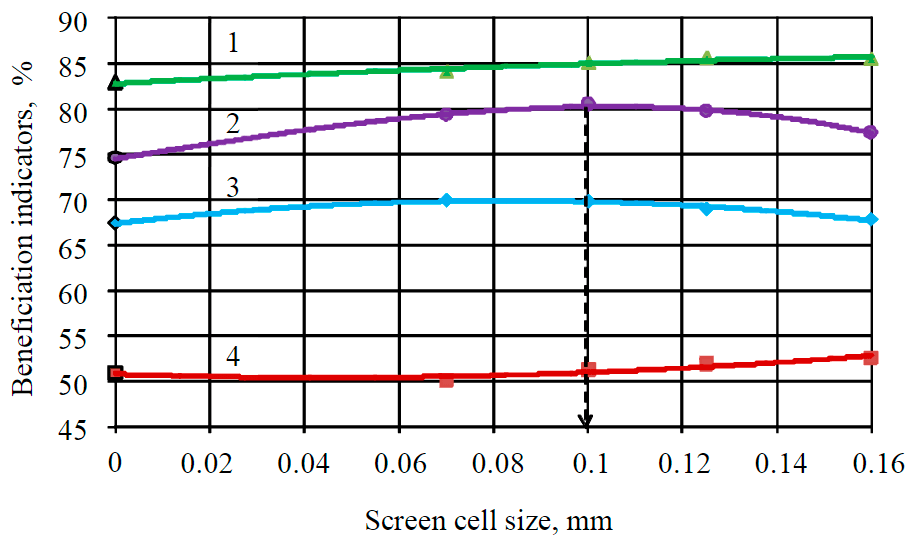
Fig.5. Indicators obtained at the maximum beneficiation efficiency in experiments with classification by grains of various sizes 1 – Fetot extraction; 2 – beneficiation efficiency; 3 – Fetot content in the concentrate; 4 – concentrate yield
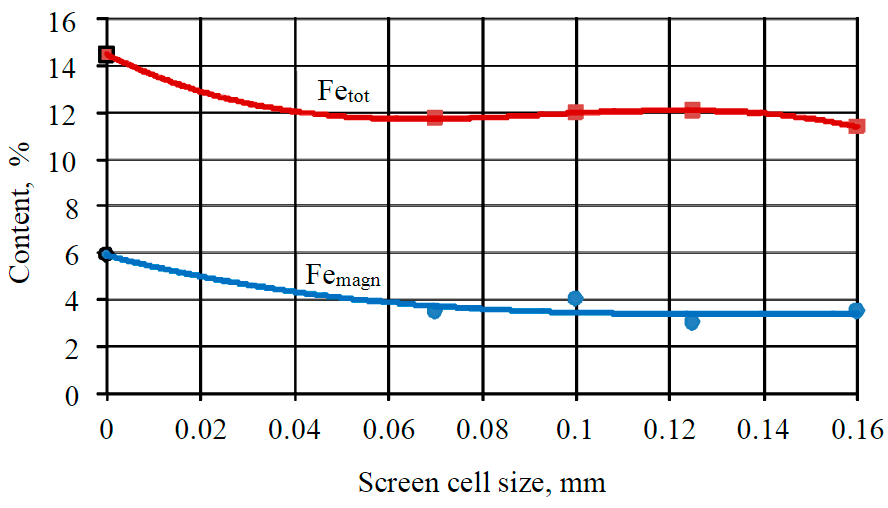
Fig.6. Iron content in tailings
It follows from Fig. 5 that the maximum beneficiation efficiency of 80.4 % is achieved with a classification size of 0.1 mm, while the Fetot content in the concentrate is 69.7 %, recovery is 85.1 %. The beneficiation maximum in this particle size range is consistent with the data on the dissemination of magnetite in the Stoilenskoye deposit ores, which averages about 0.08 mm.
Analysing iron losses with tailings (Fig.6), we note that with the selected separation mode, they are in the zone of minimum values, they are Fetot about 12 % and Femagn 3-4 %.
Thus, in order to achieve optimal performance in the magnetic-gravity separation of magnetite ore at Stoilensky GOK, the necessary conditions are:
- use of fine screening with a mesh size of 0.1 mm;
- regrinding of the oversize product to a particle size 70-73 % of the –0.045 mm class, which corresponds to the top size d95 = 0.076 mm.
The lowest beneficiation efficiency and Fetot content in the concentrate were obtained when ore was enriched without classification, but the highest iron losses with overflow were observed. This proves that the timely removal of the product ready for beneficiation (using fine screening) from the mill feed makes it possible to prevent overgrinding of the useful component and increase the efficiency of its beneficiation.
Conclusion
One of the promising ways to improve the quality of iron ore concentrates is the staged concentrate removal technology based on a combination of fine screening, regrinding, and magnetic-gravity separation.
The article presents the studies aimed at finding optimal parameters and separation modes by joint optimization of ore preparation and beneficiation operations. For this purpose, a scientific and methodological approach to experiments has been developed, which includes several main stages:
- Based on the analysis of granulometric and chemical composition, as well as data on dissemination and release of the useful component, the particle size of the classification is selected, at which fine screening will be carried out. For the studied ore, the range of such particle size was from 0.16 to 0.071 mm.
- After classification by the selected particle size class, the oversize product is grinded, where its particle size range is examined. The choice of grinding size depends on the impregnation of the useful component in the studied raw material, and for the correct construction of dependencies, at least
3-4 grindings are needed. For the studied ore, the grinding size was 50-85 % of the –0.045 mm class. - The choice of optimal parameters for ore preparation is based on the results of subsequent beneficiation, in our case magnetic-gravity separation. As an evaluation criterion, such a process parameter as the beneficiation efficiency calculated by the Hancock-Luyken formula was chosen.
As a result of the research, experimental dependencies are obtained that connect the process indicators of beneficiation with the screening parameters. For the studied ore of ferruginous quartzites, the obtained dependences can be described by a second-order polynomial with a high accuracy of approximation. The best performance is achieved with a classification size of 0.1 mm, while Fetot content in the concentrate is 69.7 %, recovery is 85 %, classification efficiency is 80.4 %. The top size of the product in this case is –0.076 mm, which corresponds to the particle size of grinding 70-73 % of the class –0.045 mm.
The proposed methodological approach for choosing the optimal operating modes of equipment for the stage-wise concentrate removal circuit can be used not only for ferruginous quartzites of the Stoilensky GOK, but also for run-of-mine and lean iron ores from other deposits.
References
- Artyaeva M.A., Ponomarenko T.V. The Review of the Largest Companies at the World Market of Ferrous Metals. Social-Economic Phenomena and Processes. 2017. Vol. 12. N 6, p. 9-16 (in Russian). DOI: 10.20310/1819-8813-2017-12-6-9-16
- Rastyannikova E.V. Iron ore industry in the BRICS countries – prospects for the fourth industrial revolution. Economics: Yesterday, Today and Tomorrow. 2018. Vol. 8 N 8А, p. 334-346 (in Russian).
- Ericsson M., Löf A., Löf O. Iron ore market report 2019-2020. Russian Mining Industry. 2021. N 1, p. 74-82 (in Russian). DOI: 10.30686/1609-9192-2021-1-74-82
- Lu Liming. Iron ore: mineralogy, processing and environmental sustainability. Cambridge: Woodhead Publishing, 2015, p. 641.
- Rudyka V.I. The Prospects for the Technology for the Direct Reduction of the Iron in the Metallurgical Production. Ferrous Metallurgy. Bulletin of Scientific, Technical and Economic Information. 2017. N 11, p. 14-23 (in Russian).
- Yushina T.I., Chanturia E.L., Dumov A.M., Myaskov A.V. Modern trends of technological advancement in iron ore processing. Gornyi zhurnal. 2021. N 11, p. 75-83 (in Russian). DOI: 10.17580/gzh.2021.11.10
- Oliazadeh M., Vazirizadeh А.Removing impurities from iron ores: methods and industrial cases. XXVIII International Mineral Processing Congress (IMPC 2016), 11-15 September 2016, Quebec, Canada. Canadian Institute of Mining Metallurgy & Petroleum, 2016, p. 4290-4302.
- Baranov V.F., Patkovskaya N.А., Tasina Т.I. Current trends in magnetite iron ores processing technology. Basic trends. Obogashchenie rud. 2013. N 3, p. 10-17 (in Russian).
- Maksimov I.I., Sentemova V.A. Special features of high-magnetite oxidized ferruginous quartzites processing technology. Obogashchenie rud. 2012. N 3, p. 7-10 (in Russian).
- 10. Pelevin A.E., Kornilkov S.V., Dmitriev A.N., Bagazeev V.K. Quality improvement of magnetite concentrate in separate processing of different iron ore types and varieties. Mining informational and analytical bulletin. 2021. N 11-1, p. 306-317 (in Russian). DOI: 10.25018/0236_1493_2021_111_0_306
- Oleinik T.A., Mulyavko V.I., Lyashenko V.I., Oleinik M.O. The Development of the Technologies and Technical Facilities for the Concentration of the Hematite Ores. Ferrous Metallurgy. Bulletin of Scientific, Technical and Economic Information. 2016. N 5, p. 5-11 (in Russian).
- Ismagilov R.I., Kozub A.V., Gridasov I.N., Shelepov E.V. Case Study: Advanced Solutions Applied by JSC Andrei Varichev Mikhailovsky GOK to Improve Ferruginous Quartzite Concentration Performance. Russian Mining Industry. 2020. N 4, p. 98-103 (in Russian). DOI: 10.30686/1609-9192-2020-4-98-103
- Abhyarthana Pattanaik, Venugopal Rayasam. Analysis of reverse cationic iron ore fines flotation using RSM-D-optimal design – An approach towards sustainability. Advanced Powder Technology. 2018. Vol. 29. Iss. 12, p. 3404-3414. DOI: 10.1016/j.apt.2018.09.021
- Xiaolong Zhang, Xiaotian Gu, Yuexin Han et al. Flotation of Iron Ores: A Review. Mineral Proceeding and Extractive Metallurgy Review. 2021. Vol. 42. Iss. 3, p. 184-212. DOI: 10.1080/08827508.2019.1689494
- Elves Matiolo, Hudson Jean Bianquini Couto, Neymayer Lima et al. Improving recovery of iron using column flotation of iron ore slimes. Minerals Engineering. 2020. Vol. 158. N 106608. DOI: 10.1016/j.mineng.2020.106608
- Wanzhong Yin., Jizhen Wang, Longhua Xu. N Reagents in the Reverse Flotation of Carbonate-Containing Iron Ores. Proceedings of the 11th International Congress for Applied Mineralogy. Cham: Springer International Publishing, 2015, p. 459-470.
- Pelevin A.E. Increasing the efficiency of iron-ore dressing by separation in an alternative magnetic field. Chernye metally. 2021. N 5, p. 4-9 (in Russian). DOI: 10.17580/chm.2021.05.01
- Jiang Wen, Zhang Yimin. Development and application of complex Flashing-field magnetic cleaner. Advanced Materials Research. 2014. Vol. 1073-1076, p. 2177-2188. DOI: 10.4028/www.scientific.net/AMR.1073-1076.2177
- Rosario P.P. Technical and economic assessment of a non-conventional HPGR circuit. Minerals Engineering. 2017. Vol. 103-104, p. 102-111. DOI: 10.1016/j.mineng.2016.10.019
- Prokopyev S.A., Pelevin A.E., Napolskikh S.A., Gelbing R.A. Staged screw separation of magnetite concentrate. Obogashchenie rud. 2018. N 4, p. 28-33 (in Russian). DOI: 10.17580/or.2018.04.06
- Sadeghi M., Bazin C., Hodouin D. et al. Control of spiral concentrators for the concentration of iron ore. XXVIII International Mineral Processing Congress (IMPC 2016), 11-15 September 2016, Quebec, Canada. Canadian Institute of Mining Metallurgy & Petroleum, 2016, p. 4534-4545.
- Kuskov V., Kuskova Y., Udovitsky V.Effective processing of the iron ores. IInd International Innovative Mining Symposium (Devoted to Russian Federation Year of Environment), 20-22 November 2017, Kemerovo, Russia. E3S Web of Conferences, 2017. Vol. 21. N 02010. DOI: 10.1051/e3sconf/20172102010
- Vaisberg, L.A., Kuskova, Y.V. Improvement of circular concentrating tables as development of gravity concentration methods. Obogashchenie rud. 2017. N 4, p. 54-60 (in Russian). DOI: 10.17580/or.2017.04.10
- Fomin A.V., Khokhulya M.S. Improving efficiency of gravity separation of fine iron ore materials using computer modeling. Topical Issues of Rational Use of Natural Resources. London: Taylor & Francis Group CRC Press, 2019. Vol. 2, p. 509-516.
- Gzogyan T.N., Vinnikov V.A. Fractionation and separation processes in beneficiation circuits of ferruginous quartzites of complex composition. Gornyi informatsionno-analiticheskii byulleten. 2012. N 8, p. 172-177 (in Russian).
- Korovnikov A.N., Buzunova T.A. Ore slurry classification on a vibrating screen. Obogashchenie rud. 2018. N 5, p. 17-21 (in Russian). DOI: 10.17580/or.2018.05.03
- Leonov V. The practice of Derrick technologies in mining industry. Maining Report Glyukauf na russkom yazyke. 2014. N 3, p. 66-70 (in Russian). URL (accessed 14.09.2022).
- Pelevin A.E., Sytykh N.A. Fine hydraulic screening for staged separation of titanium-magnetite concentrate. Obogashchenie rud. 2021. N 1, p. 8-14 (in Russian). DOI: 10.17580/or.2021.01.02
- Tsypin E.F., Mamonov S.V., Vlasov I.A. The products of copper-zinc ore sizing and fine screening in closed grinding cycles. Izvestiya. Non-Ferrous Metallurgy. 2016. N 2, p. 4-11 (in Russian). DOI: 10.17073/0021-3438-2016-2-4-11
- Albuquerque L.G., Wheeler J.E., Valine S.B. Application of high frequency screens in closing grinding circuits. Revista Escola de Minas. 2009. Vol. 62. N 1, p. 167-173.
- Jahani M., Farzanegan A., Noaparast M. Investigation of screening performance of banana screens using LIGGGHTS DEM solver. Powder Technology. 2015. Vol. 283, p. 32-47. DOI: 10.1016/j.powtec.2015.05.016
- Opalev A.S., Khokhulya M.S., Fomin A.V., Karpov I.V. Creation of innovative technologies for production of high-quality iron concentrate production in the North West of Russia. Gornyi zhurnal. 2019. N 6, p. 56-61 (in Russian). DOI: 10.17580/gzh.2019.06.07
- Opalev A.S., Karpov I.V., Krivovichev S.V. Enhancing magnetite quartzite processing efficiency at Karelsky Okatysh. Gornyi zhurnal. 2021. N 11, p. 66-74 (in Russian). DOI: 10.17580/gzh.2021.11.09
- Grinenko V.I., Opalev A.S., Maevsky P.V., Karpov I.V. Improvement of iron ore concentrate quality by gravity and magnetic separation at SSGPO JSC. Gornyi zhurnal. 2021. N 10, p. 81-86 (in Russian). DOI: 10.17580/gzh.2021.10.10
- Gzogyan S.R., Scherbakov A.V. Improving the quality of concentrates of Stoilensky GOK JSC with the use of magnetic Agravity separation. Obogashchenie rud. 2020. N 6, p. 3-8 (in Russian). DOI: 10.17580/or.2020.06.01
- Gzogyan T.N., Opalev A.S., Gzogyan S.R., Shcherbakov A.V. The use of magnetic-gravity separation to obtain high-quality concentrates from KMA ferruginous quartzites. Materialy XII Kongressa obogatitelei stran SNG, 25-27 fevralya 2019, Moscow, Russia. Moscow: ITEP, 2019, p. 182-186 (in Russian).
- Pelevin A.E., Sytykh N.A. Titanomagnetite ore two-stage grinding circuit tests. Obogashchenie rud. 2018. N 2, p. 13-18 (in Russian). DOI: 10.17580/or.2018.02.03