Determination of rational steam consumption in steam-air mixture flotation of apatite-nepheline ores
Abstract
Relevance of the study is determined by the decisions taken to increase the production volume of certain commercial products from mineral raw materials. The scale, impact and consequences of the projects on developing the resource-saving technologies for beneficiation of mineral raw materials are socially significant, and the economic growth of mining production complies with the sustainable development goals. The aim of the study is to develop the flotation circuit and mode that improve the technological performance of beneficiation of apatite-nepheline ores of the Khibiny Massif in the Kola Peninsula. The scientific idea of the work is to develop the flotation circuit, the movement of beneficiation products in which ensures a major increase in the content of the recovered component in the rougher flotation procedure with a simultaneous increase in dressability of the material. The above condition is met when mixing the feedstock with rough concentrate. Recovery of the valuable component from the resulting mixture is accomplished in a mode differing from the known ones in that the heat of steam condensation is used to increase water temperature in the interphase film between the particle and the bubble. For pulp aeration during flotation, a mixture of air and hot steam is used as the gas phase. A high recovery of the valuable component in ore flotation according to the developed circuit and mode is facilitated by increasing water temperature in wetting films due to the steam condensation heat. A high selectivity of flotation with a steam-air mixture can be explained using the concepts of a phonon component of disjoining pressure, the value and sign of which are associated with a difference in the dynamic structure of liquid in the wetting film and bulk liquid.
Introduction
Mineral resources of the RF estimated at 32 trillion US dollars allow the country's mining industry to hold the leading position in manufacture of most mineral products, constitute about 10 % of its gross domestic product (GDP) and provide the employment for over 400.000 persons [1].
According to the forecasts of the leading international consulting companies in Russia, PwC and SRK, offering specialized solutions and recommendations for the customers in mining business, subsequent to the growth of the world GDP at 4 % per year, the demand for mining industry products should be also maintained [2]. These assessments and the need to develop the national economy became the reason for taking decisions on increasing the production volume of certain types of commercial products from mineral raw materials at the state level.
Extracting the maximum profit from production activities is one of the main goals underlying the performance of an enterprise. Reducing the production cost is one of the main directions in the development and rational use of mineral raw materials [3], which can be achieved by attaining the maximum completeness of valuable components recovery and selectivity of the flotation process. An increase in the efficiency of mineral separation by flotation can be achieved by constructing the optimal technological flotation circuits [4, 5] and applying energy effects on wetting films [6, 7].
The aim of the work is to substantiate by the example of apatite-nepheline ores a possibility of improving the technological performance using the flotation circuit with rough concentrate recycling and the flotation mode with water heating in boundary layers of air bubbles. The set goal is achieved by resolving the problems related to the study of the flotation circuit, in which an increase in the content of the extractable component in rougher flotation procedure is attained by mixing the feedstock with rough concentrate separated from 1/2 of ore, as well as the flotation mode by a mixture of air flow supplied for pulp aeration with hot steam.
Methodology
The object of experimental studies is the apatite-nepheline ore of the Khibiny Massif in the Kola Peninsula [8-10]. In the ore sample under study, apatite (> 30 %) and nepheline (~40 %) are most common as well as (in descending order) aegirine (~10 %), feldspars, sphene, titanomagnetite, pyroxenes; hydromicas (~1 %), lepidomelane, rhincolite, kionite, natrolite, rincolite, cancrinite, etc., are less frequent. The content of elements in samples of the feed ore and flotation products was determined by the chemical analysis and X-ray fluorescence (spectrometer S8 TIGER Bruker wave-dispersed type, Germany). The chemical composition of the studied ore sample, %: P2O5 – 11.7; Al2O3 – 13.8; SiO2 – 26.1; Fe2O3 – 4.9; FeO – 0.7; TiO2 – 1.6; MnO – 0.2; CaO – 20.3; MgO – 1.4; SrO – 1.2; Fe – 0.9; Na2O – 9.3; K2O – 3.0; Fe – 1.0; V2O5 – 0.08; others – 3.82.
Ore sample was crushed in a closed cycle with a vibratory screen to a fineness of 3 mm. Crushed ore weighing 1 kg was ground in a rod mill (rod load 8.7 kg) to a fineness of 52-55 % of the 74 µm class at a S:L ratio = 1:0.75. Flotation was conducted in a mechanical-type laboratory flotation machine with 3 dm3 cell volume designed by the OAO “Geopribor” at liquefaction R = 2.54. Pulp aeration was performed by a (Ø68 mm) impeller in the form of a concave disk with four radial blades and a hub; at an impeller speed of 1.863 rpm, 1.14 m3/min of air per 1 m3 cell volume got into the pulp. Froth product was removed from the flotation cell at a frequency of 23 times per minute through a 119 mm wide overflow weir by a mechanical skimmer.
During flotation, the air entering the flotation machine for pulp aeration was mixed with hot steam (≥ 104°C). The impeller of the flotation machine disperses the cocurrent flows of air and steam into bubbles filled with steam. When the bubbles filled with steam come into contact with minerals, water temperature in the wetting film separating them increases due to the heat of steam condensation. Temperature effect on the result of particle sticking to the bubble leads to a change in the isotherm of structural forces. It is caused by rearrangement of water structure in a thin film and a corresponding change in its stability (equilibrium thickness) with increasing temperature.
To supply steam-air mixture to the flotation cell, a steam pipeline is coaxially inserted into the aeration pipe of its impeller unit according to the “pipe in pipe” type (Fig.1, view 1, 2). Through the aeration (external) (Ø6.7 mm) pipe, atmospheric air entered the low pressure zone in the pulp created by the rotating impeller of the flotation machine, and through the inner pipe (Ø5.3 mm) – aluminum steam pipeline – the cocurrent flow of saturated steam arrived. Pipes with air and steam were inserted into the hole in the above-impeller disk, on leaving which they mixed forming a steam-air mixture with temperature 85.7-94.7 °С (temperature was measured using a chromel-copel thermocouple).
The intensity of water evaporation in the steam generator was controlled by the value of operating voltage U applied to the tubular electric heaters (TEH) (Fig.1). In the steady mode, UI power supplied to the TEH is spent on producing steam Gsr and heat losses Qloss to the environment:
where I is current; Gsx – steam amount and dryness.
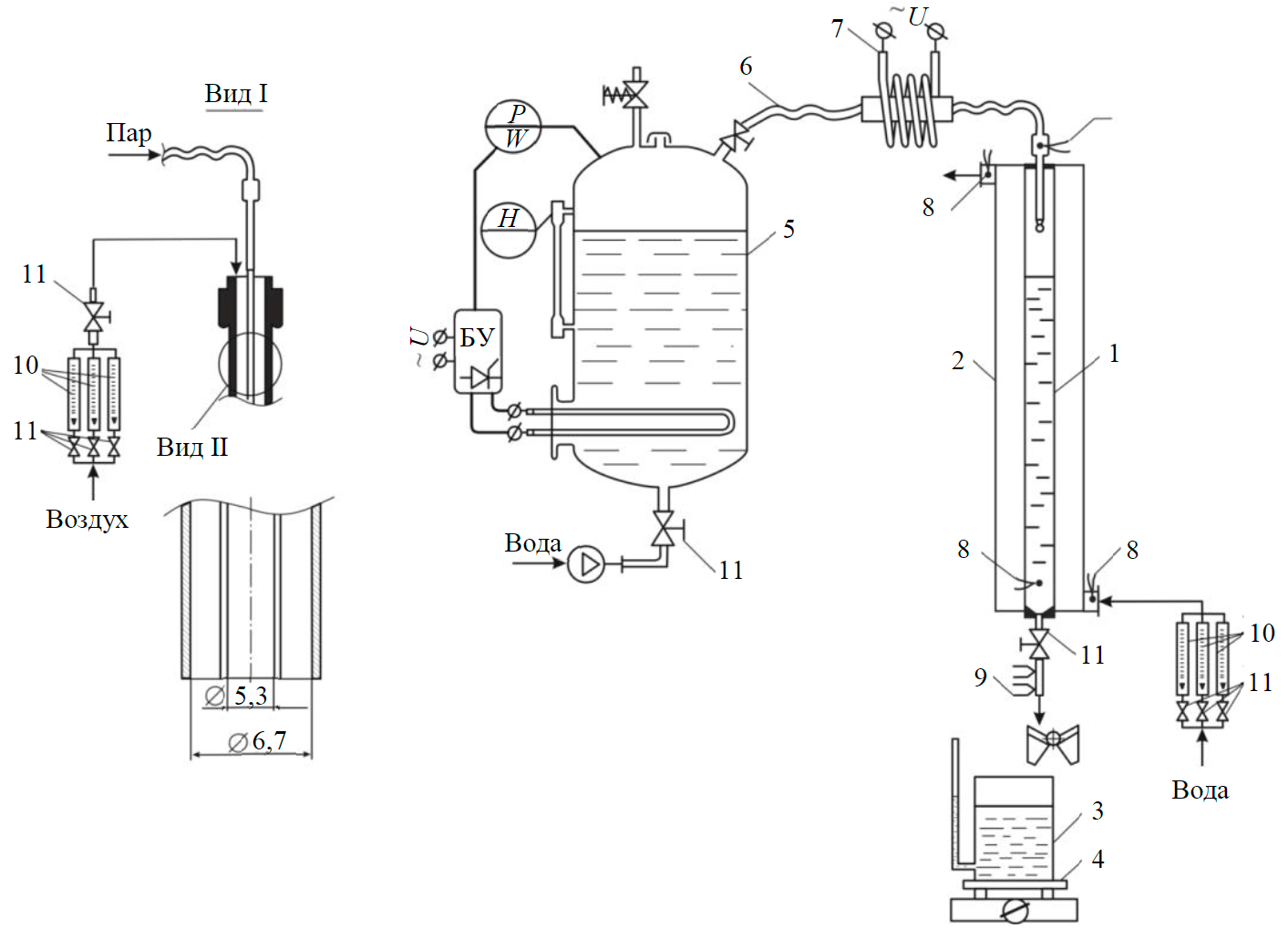
Fig.1. Experimental unit for determining steam dryness 1 – measuring tube with a cooling jacket 2; 3 – measuring container with scales 4; 5 – steam generator boiler with steam line 6 and electric superheater 7; 8 – thermocouple; 9 – resistance thermometer; 10, 11 – rotameters with control valves
Steam dryness was determined experimentally (Fig.1) by a change in the mass ΔM2-M1 and water temperature from Т1 to Т2 when it is bubbled by steam for time τ.
Thus, if the heat given off by the steam during condensation is equal,
(where ΔМ is the mass of condensate obtained during the experiment; r, vaporization heat; ср, heat capacity of water; Тs, Т2, saturation temperature of steam and mixture at the end of experiment) and heat obtained by water in a measuring container,
(Н1, Н2, enthalpy of water at the beginning and end of the experiment; М1, Т1, mass and temperature of water at the beginning of the experiment), steam dryness х is determined from the expression:
During the time, heat losses at surface area of heat and mass transfer F and temperature difference Δt will be:
where k is heat transfer coefficient. Or at water temperature in thermostat Тm
Taking into account (1) and (2) we shall obtain:
Steam consumption Gsteam in the presence of air was determined by the weight method (weighing with an accuracy to 0.01 g) at complete condensation of steam (Fig.2). Heat transfer coefficient was determined on the unit and following the procedure described in [6].
Discussion
The need to increase the content of useful components in rougher flotation is determined by a relationship between the content of the recovered component in the feedstock, its extraction and quality of the concentrate. In practice, this is resolved by the structure of the separation cascade [11-13] which is commonly arranged in such a way [14-16], that the necessary pulp beneficiation is achieved by rerecycling the middlings. In the canonical circuit [17-19], tailings of primary cleaning and recleaner flotation concentrate [20-22] are recycled to rougher flotation, which leads to an increasing content of recoverable mineral [23, 24] at the expense of its difficult-to-float (persistent) forms. When mixing products of similar composition, but different separability, the flotation feed is diluted by persistent forms of the recovered mineral – the recovered minerals are distributed according to floatability, which reduces the dressability of the raw material. The flotation rate constant of the hard-to-recover forms of a valuable mineral equalizes (or becomes smaller) with the flotation rate constant of easily floatable depressed minerals, and the separability of the mineral mixture decreases. With increasing flow rate of the depressant, the flotation rate of difficult-to-float forms of the recovered mineral decreases faster than the rate of easily floatable forms of the depressed mineral. Difficult-to-float forms of the recovered mineral accumulate in middlings circulating in the circuit, the yield of which can be hundreds of percent of the original feed. When mixing products in the circuit, account should be taken of the entropy of the mixture and the entropy associated with inhomogeneity of the separation properties [25]. Open-cycle-circuits in rougher flotation can be closer to the ideal separation cascade than to directing the middlings to earlier stages [26].
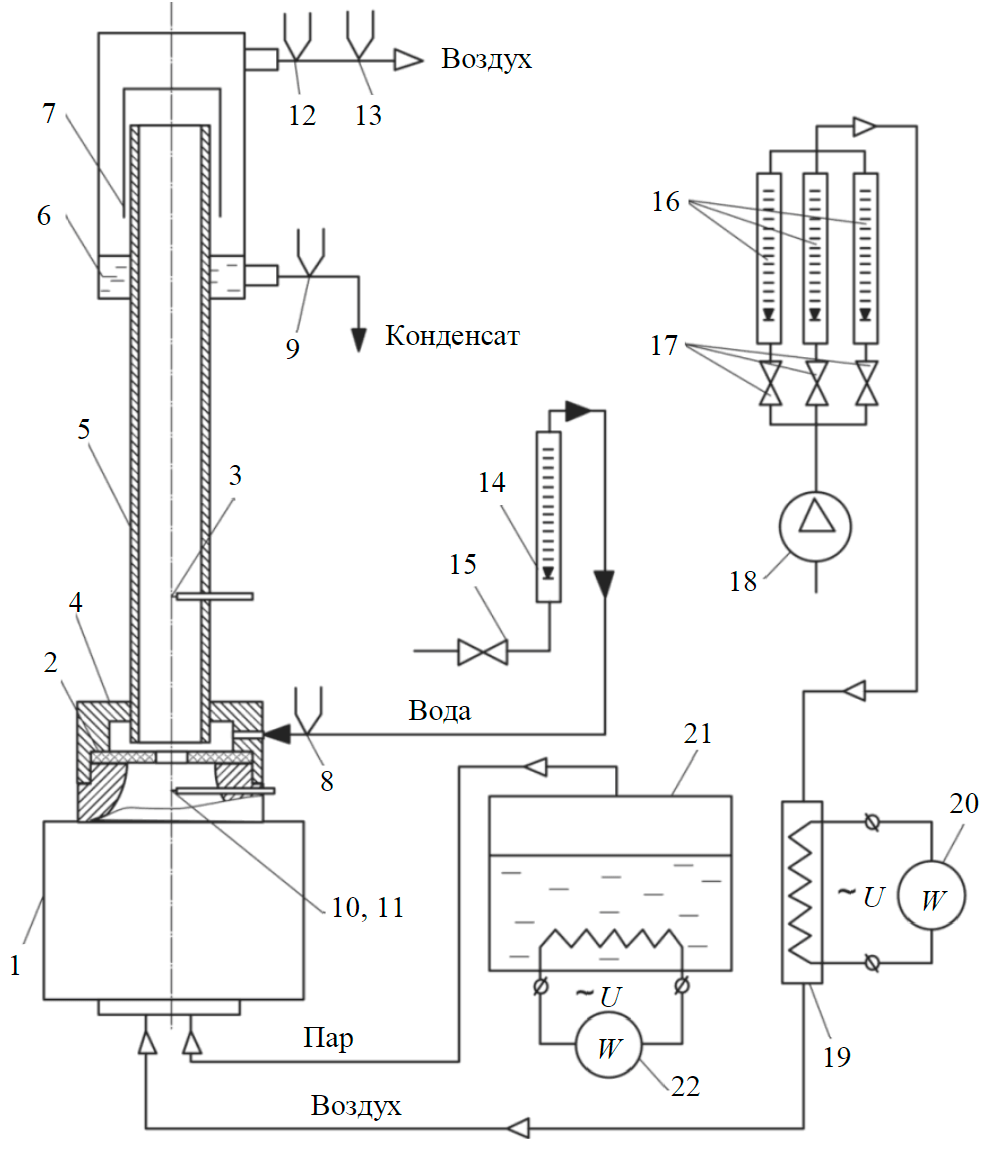
Fig.2. Experimental setup for determining the steam flow 1, 2 – mixer design elements; 3, 8-13 – thermocouple; 4 – water supply chamber with working channel 5; 6 – condensate collector with separator 7; 14, 16 – rotameter with control valves 15, 17; 18 – microcompressor; 19 – electric heater; 20, 22 – wattmeter; 21 – steam generator
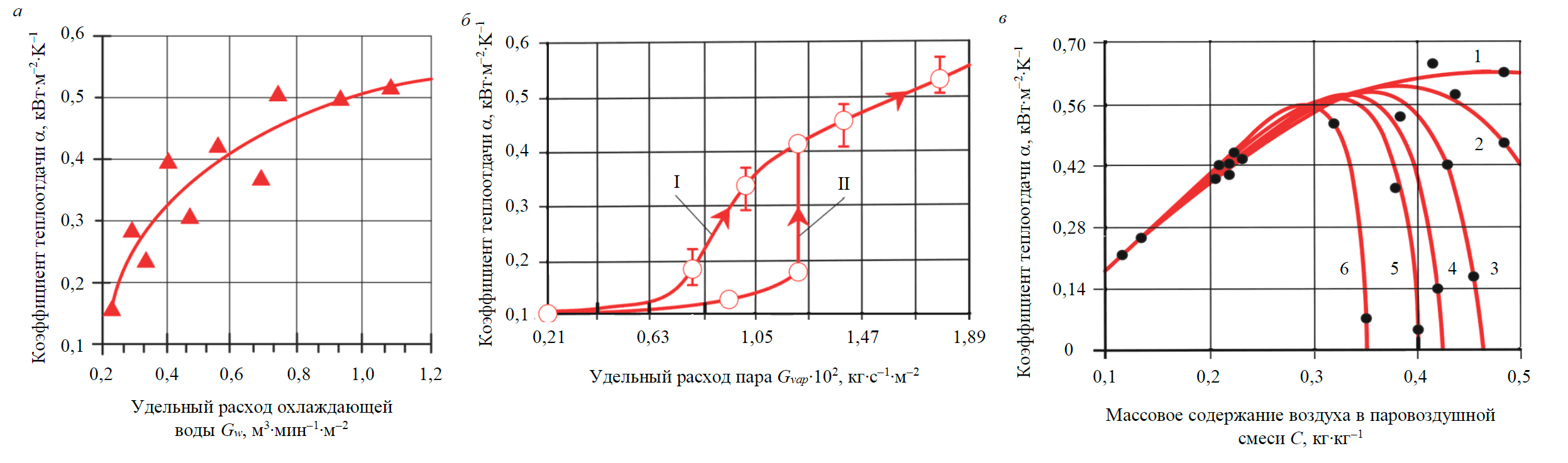
Fig.3. Heat transfer coefficient as a function of specific consumption of cooling water Gw (a), steam Gvap (b) and mass content of air in steam-air mixture С (c) Temperature difference ΔТ, °С: 1 – 70; 2 – 60; 3 – 50; 4 – 40; 5 – 30; 6 – 20
For apatite-nepheline ore flotation the circuit was chosen, in which 1/2 of the feedstock in the feed of rougher flotation process is mixed with rough concentrate (recycled) recovered from another 1/2 of the ore. Such mixing ensures a high concentration of the recovered mineral in the rougher flotation feed with a minimum amount of circulating material (dilution). From the viewpoint of the theory of cascades, in this case, the flotation circuit becomes closer to the ideal cascade, i.e., the probability of an ideal separation of a mixture of minerals increases [25, 26]. After mixing the feedstock with rough concentrate, the flotation with steam-air mixture was run for three minutes.
In the first series of experiments, the impact of two heating agent flows on the heat transfer coefficient was studied: cooling water (simulating pulp flow through the flotation cell) and steam-air mixture (simulating gas used to aerate pulp in the flotation machine). Flow rate of cold heating agent varied from 0.3 to 1.2 m3∙min–1 per 1 m2 of the cell section at a constant flow rate of steam-air mixture (3.52 m3∙min–1 per 1 m2 of the cell section) containing 30.4 vol.% steam. It has been ascertained that the efficiency of heat removal from steam increases with growing consumption of cooling water (Fig.3, a).
During flotation, pulp temperature in a laboratory batch-type flotation machine, depending on mass fraction of steam in the air flow used for pulp aeration, increases with an intensity of 0.3 to 0.5 °С per minute. With increasing temperature difference ΔT = Tvg – Tpal (Tvg, Tpal – temperature of steam-air mixture and pulp), the heat transfer coefficient grows (Fig.3, c).
In the experiments on apatite-nepheline ore flotation, pulp temperature increased from 18-19 °С at the beginning of the experiment and to 18.9-20.5 °С at the end of flotation with steam-air mixture.
Dependence of heat transfer coefficient on mass content of air in the steam-air mixture has a maximum, which flattens out at a temperature difference ΔT = Tvg – Tpal above ~50 °С (Fig.3, c).
This effect can be explained by a change in the contribution of two molecular counter flows – moving towards the interfacial surface (j–) and from it to the center of the air bubble (j+) – to the mass flux density of condensing steam ∑j=(j+)-(j–) At a small temperature difference (ΔТ = 20-50 °С) and mass content of air in steam-air mixture above ~0.3 kg∙kg–1 molecules of non-condensable gas by frequent collisions with steam molecules block their transfer to the condensation surface, and the heat transfer coefficient decreases (Fig.3, c, curves 3-6). At a significant drop of the interphase surface temperature (Fig.3, c, curves 1, 2), an increase in the value of the resulting condensation flow Σj is a consequence of the decreasing flow j+ and, conversely, the improving conditions for delivering steam to the condensation surface due to diffusion. Under these thermophysical conditions, the influence of non-condensable gas on the value of heat transfer coefficient is less noticeable.
Dependences were obtained linking the heat transfer coefficient with specific steam consumption (Fig.3, b).
Specific steam consumption varied from 0.21∙10–2 to 1.89∙10–2 kg∙s–1 per 1 m2 of the cell section at specific cocurrent air flow consumption 1.11∙10–2 (Fig.3, b, curve I) and 5.69∙10–2 kg∙s–1 per 1 m2 of the cell section (Fig.3, b, curve II). From the experimental data it follows that with a small mass fraction of non-condensable gas (air) in the steam-air flow (Fig.3, b, curve I), the heat transfer coefficient increases monotonically with growing specific steam consumption. However, with an about five-fold increase in mass fraction of air (Fig.3, b, curve II), a noticeable increase in heat exchange of steam with the surrounding aqueous phase occurs only at a specific steam consumption ~1.2∙10–2 kg∙s–1 per 1 m2 of the cell section. Probably, in this case, air molecules are sufficient to create a potential barrier insurmountable for steam molecules at the gas-liquid interface, and an intense heat-mass exchange with the surrounding liquid is possible only with an increase in specific steam consumption to ~1.2∙10 –2 kg∙s–1 per 1 m2 of the cell section.
When testing the developed flotation circuit and mode in laboratory conditions, from the first batch of ore with depression of aluminosilicate flotation with liquid glass (flow rate 50 g/t), apatite was recovered into rough concentrate by a collector as a mixture of reagents. Collector expenditure was 148 g/t including distilled (22 g/t) and crude (43 g/t) tall oil, oxidized petrolatum (4 g/t), surface-active reagent OP-4 (2 g/t), secondary petroleum tar (15 g/t) and fatty acids (62 g/t). Alkalinity of the pulp created by loading of caustic soda (70 g/t) was maintained within the 9.5-9.7 pH range. The emulsifier OP-4 at enterprises processing apatite-nepheline ores is excluded from the reagent flotation modes.
Rough concentrate was mixed with the second batch of ore, and rough concentrate was recovered from the resulting mixture in two steps. First, with a low collector expenditure and the use of steam-air mixture as the gas phase, a selective “head” was isolated for three minutes, then the main part of the collector was loaded, and apatite was refloated.
Rational flow rates of steam (х1) and collector (х2) during isolation of the selective “head” from the mixture of the original ore with rough concentrate of the steam-air mixture were determined by the method of planning the experiment. Constant conditions of the experiment are: steam-air flotation time (3 min); feed pulp temperature (18-19 °С); liquefaction during flotation (R = 2.54). At the first stage, an assumption was made that the results of the experiment can be approximated by the first-order regression equation. By mathematical and statistical processing of the results of the experiments set up following the planning matrix of the first order, a regression equation was obtained:
From the analysis of equation (4) it follows that the coefficient for interactions (b12 = 4.73) exceeds the coefficient for the first factor (b1 = 2.77), and the coefficient for the free term (b0 = 47.47) exceeds the result of “zero” experiment (¯y0=43.43). Consequently, the hypothesis of a linear relationship between the studied factors is incorrect.
To obtain the second-order polynomial, based on results of a series of special experiments, the main levels and intervals of factor variation were determined (Table 1).
Table 1
Boundary conditions (levels) of independent variables
Planning parameter |
Factor xi |
|
Steam consumption х1, |
Collector expenditure х2, g/t |
|
Ground level х0 |
10.7∙10–3 |
60 |
Variability interval Δхi |
2.7∙10–3 |
1.5 |
Variability interval, % from ground level |
25.2 |
25.0 |
Upper level +хi |
13.4∙10–3 |
7.5 |
Lower level –хi |
8.0∙10–3 |
4.5 |
Сonstant conditions of the experiment were the same as in the first stage of the research. A compositional plan for two factors was implemented (Table 2). The number of parallel experiments for each mode is m = 3; the experiments are randomized in time. The response function y is taken as P2O5 recovery into rough concentrate (%) minus the yield (%) of the concentrate. Flotation results are given in Table 2.
Table 2
Planning matrix and experiment results
Number of experiment |
Coded value of the studied factor |
Experimental value of response function |
Design value |
|||||||
x1 |
x2 |
x12 |
x22 |
x1x2 |
y1 |
y2 |
y3 |
¯yc |
yr |
|
1 |
+1 |
+1 |
+1 |
+1 |
+1 |
51.43 |
54.43 |
53.50 |
53.12 |
52.35 |
2 |
–1 |
+1 |
+1 |
+1 |
–1 |
41.36 |
39.50 |
42.80 |
41.22 |
41.95 |
3 |
+1 |
–1 |
+1 |
+1 |
–1 |
55.11 |
55.26 |
55.23 |
55.20 |
54.43 |
4 |
–1 |
–1 |
+1 |
+1 |
+1 |
55.00 |
54.86 |
52.68 |
53.18 |
53.91 |
5 |
+1 |
0 |
+1 |
0 |
0 |
55.20 |
55.43 |
55.27 |
55.30 |
56.83 |
6 |
–1 |
0 |
+1 |
0 |
0 |
50.66 |
53.36 |
54.50 |
52.84 |
51.37 |
7 |
0 |
+1 |
0 |
+1 |
0 |
41.51 |
43.43 |
44.36 |
43.10 |
43.11 |
8 |
0 |
–1 |
0 |
+1 |
0 |
48.43 |
50.46 |
51.38 |
50.09 |
50.13 |
9 |
0 |
0 |
0 |
0 |
0 |
48.50 |
49.61 |
52.28 |
50.13 |
50.06 |
Equiaccuracy of the results obtained in parallel experiments was checked by comparing the largest line rate variances with the sum of all line rate variances according to the Cochrane test. In the coded variables, the dependence of the selected response function y on flotation factors – steam flow (х1) and collector expenditure (х2) when isolating the selective “head” is approximated by the second-order regression equation:
From the results of assessing the statistical significance of regression coefficients (5), it follows that their absolute values are greater than the confidence intervals constructed using Student's t-test at a significance level α = 0.05, i.e., all the coefficients of regression equation (4) are statistically significant.
Ratio of residual variance Sres2=3.32 to reproducibility variance equals Fр = 1.57. For the number of freedom degrees greater than f1 = 21 and smaller variance f2 = 18 and reliability of the estimate α = 0.05, the tabulated value of Fisher’s criterion is F0.05(21.18)=2.20. Thus, the model is adequate.
To assess the nature of the response surface and determine the coordinates of the singular point, a canonical transformation was performed:
The signs of coefficients in equation (6) show that the factorial function is a hyperbolic paraboloid having a minimax at point (x1S, x2S). The best conditions for carrying-out the process correspond to the coordinates of the singular point (center): x1S = –0.164; x2S = –0.569. To increase y value, one should move from the center of the surface in the direction of z2 axis.
Using the formula for the transition between the coded and natural values of the factors, we obtain that the rational steam flow is х1 = 10.3∙10–3 kg/s per 1 m2 of the cell section and the collector expenditure is х2 = 5.2 g/t. Coordinates of the singular point belong to the region of the factor space where the experiment was conducted. The experiments were made on recycled water.
The recommended qualitative-quantitative ore flotation circuit obtained from the results of flotation under the conditions simulating a closed cycle is shown in Fig.4. The experiment consisted of six feedbacks of middlings, at which stabilization of P2O5 content in the final tailings was achieved.
The circuit in Fig.4 can be represented as if from 1/2 of the feedstock (α = 11.7 % P2O5 with a 50 % yield and 50 % recovery) rough concentrate was isolated (β = 19.77 % Р2О5 at 25.71 % yield and 43.44 % recovery) at collector expenditure 148 g/t and mixed with the second 1/2 part of the feedstock. When mixing the feedstock (α = 11.7 % Р2О5 at 50 % yield and 50 %recovery) and rough concentrate (β = 19.77 % P2O5 at 25.71 % yield and 43.44 % recovery), Р2О5 content in the second 1/2 part of the feedstock will be 14.44 % at 75.71 % yield and 93.44 % recovery (6.56 % Р2О5 was lost with tailings-I during recovery of rough concentrate from the first 1/2 part of the feedstock). Р2О5 content in the second 1/2 part of the pulp flow increased by ~23 rel.% – from 11.7 to 14.44 %. An increase in the recovery of the valuable component with its content growth in feed ore was recorded as a result of full circuit sampling of technological circuits for flotation of ores of various valuable components (including apatite [27]). The obtained dependences are approximated by adequate linear [28] and curvilinear [29-31] models.
During the first three minutes of air flotation with addition of hot steam in the working area of one unit, the fast-floating apatite fraction (selective “head”) is actually recovered from the feed ore and the recycled rough concentrate is recleaned. Collector expenditure for these purposes was 5.2 g/t. At a concentration degree of 1.44, P2O5 content in the concentrate increased from 19.77 to 28.44 %. After recovery of the finished rough concentrate (“in two steps”), P2O5 content in the pulp decreased becoming approximately equal to that in feed ore. Moreover, in the depleted mixture, apatite grains are represented by a slowly floated fraction. For its recovery, the main part of the collector (103 g/t) was loaded, and flotation was performed with air without steam addition.
It can be presumed that P2O5 recovery from the mixture of feed ore with recycled rough concentrate is accomplished following the flotation mechanism with a carrier mineral (solid boundary) [32-36] in which apatite grains of the rapidly floating fraction, which have an elevated natural hydrophobicity, stick to apatite grains of recycled rough concentrate hydrophobized by collector. The collector got into the pulp together with liquid and solid phases of recycled rough concentrate. To intensify flotation, a new portion of collector at a rate of х2 = 5.2 g/t was additionally loaded into the pulp by the carrier mineral.
A high selectivity of flotation with steam-air mixture [37, 38] can be accounted for by the value and sign of the phonon component of disjoining pressure [39, 40]. Thus, the free-path length of phonons near the hydrophilic surface is greater than near the hydrophobic one due to a high energy barrier of thermal shocks and a lower mobility of molecules near such a surface. Differences in dynamic structure of liquid in the boundary layer and the structure of bulk fluid [41-44] determine the direction of liquid flow under the action of temperature gradient. Bulk liquid flows into and stabilizes the interphase gap if the enthalpy in it compared to its bulk value is lowered (ΔН < 0) and, on the contrary, it flows out in the case of predominance of positive ΔН > 0 values promoting sticking. An increasing efficiency of apatite-nepheline ore flotation with air-steam mixture is also possible due to a growing solubility of compounds that are the basis of the oxyhydryl collectors used and, as a consequence, an increase in the degree of their dissociation. At 28.40 % yield of saleable (39.50 % P2O5) concentrate, 96.00 % P2O5 were recovered to it.
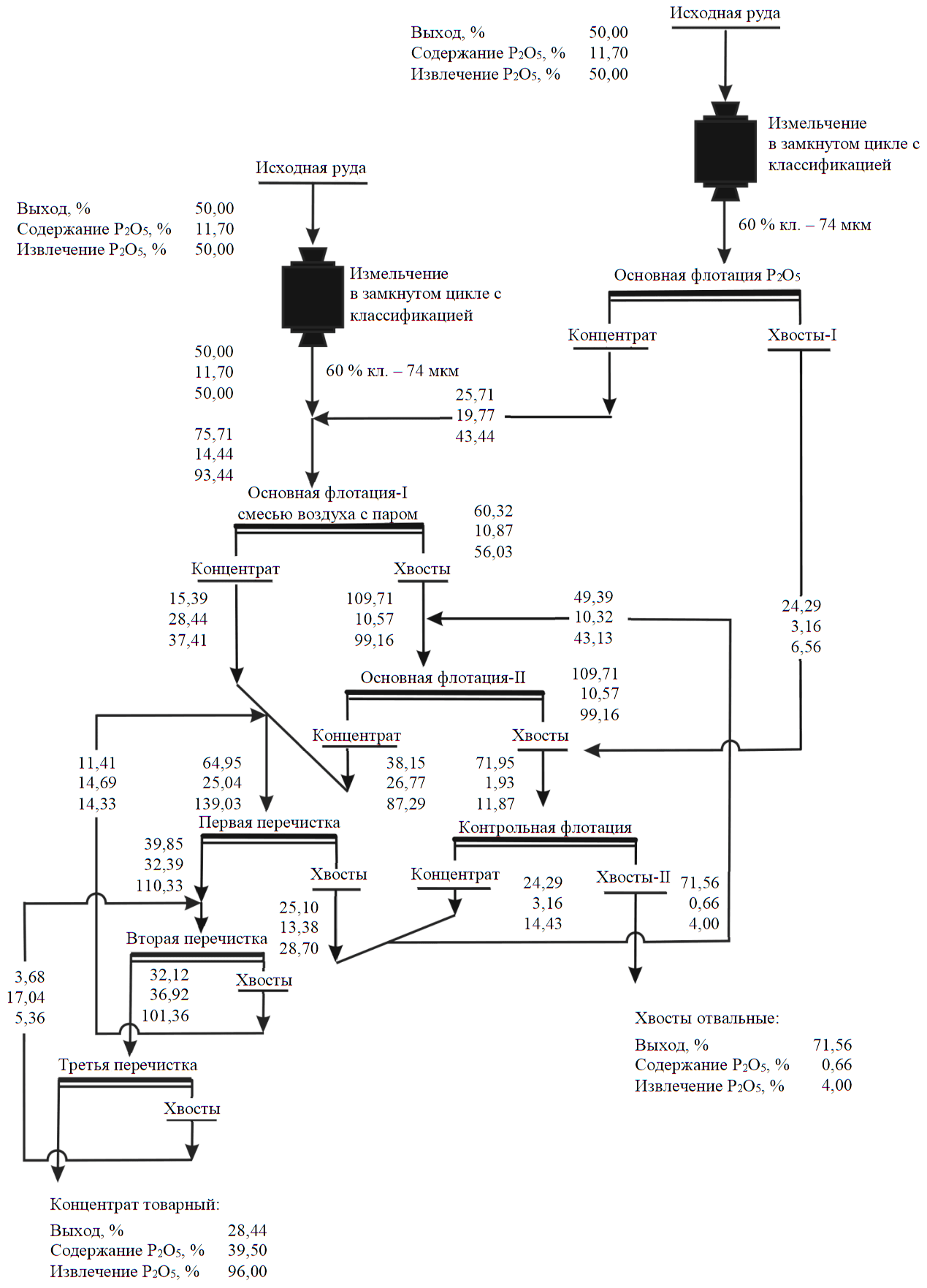
Fig.4. Recommended qualitative and quantitative ore flotation circuit
Experiments were conducted on closed-cycle ore flotation following the “rougher flotation – recleaner flotation – three recleanings of rough concentrate” circuit with the feedback of middlings from subsequent flotation into the previous one. In comparison with results of the experiment performed according to the circuit in Fig.4, P2O5 losses with final tailings increased from 4.0 to 9.94 % due to increase of P2O5 content in them from 0.66 to 1.59 % with almost the same concentrate quality (39.50-39.57 % P2O5).
In case of flotation following the “rougher flotation – recleaner flotation – three recleanings of rough concentrate” circuit, collector expenditure was 148 g/t. During flotation according to the circuit in Fig.4, collector expenditure was 148 g/t in the first 1/2 part of the ore flow and 108.2 g/t in the remaining 1/2 part of the ore flow including 5.2 g/t in rougher flotation-I (isolation of selective “head” for three minutes by steam-air mixture) and 103 g/t in rougher flotation-II (air flotation). In flotation following the circuit in Fig.4, the expenditure of the most expensive distilled (by ~32 % – from 22 to 15 g/t) and crude (by ~30 % – from 43 to 30 g/t) tall oil decreased. Moreover, reducing the collector expenditure is a necessary condition for obtaining a high-quality concentrate.
Experiments were performed on steam-air mixture flotation of apatite-nepheline ore without mixing rough concentrate with feed ore. From the analysis of flotation results of a sample of apatite-nepheline ore by two competing methods, it follows that the transition from air flotation to steam-air mixture flotation allows increasing P2O5 content in rough concentrate by 3 % and recovery by ~8 %. Recleaning of rough concentrate in experiments performed according to the process continuity principle allows recovering saleable concentrate from an ore sample with 14.60 % P2O5 content with 92.03 % P2O5 recovery. However, the circuit with feedstock mixing with rough concentrate and using the flotation mode with steam-air mixture for a short time only in rougher flotation operation, in which a high concentration of the recovered mineral is specially created, is technologically more efficient (from an ore sample with 11.7 % Р2О5 content (Fig.4) 96.0 Р2О5 was recovered into saleable concentrate and economically more profitable (steam consumption for performing the flotation process is approximately three times less).
From the condition of heat balance with coupled heat-mass exchange of steam with cold pulp Qn+Qk=Q2, steam consumption in the ore flotation mode with steam-air mixture is 5.08 kg∙t–1 of ore:
where Qn=m1r1 is the amount of heat given off by steam with mass m1 (kg) during condensation; r1 is the heat of vaporization at steam temperature 104 °С, kJ∙kg–1; Qk=m1cp1(t1n-t1k) – the amount of heat given off by the condensate during cooling from temperature t1n to t1k (°С); ср1, ср2 – isobaric mass heat capacity of steam and pulp, respectively, kJ∙kg–1∙deg–1; Q2=m2cp2(t2k-t2n) – the amount of heat received by the pulp with mass m2 (kg) when heated from temperature t2n to t2k (°С).
For producing 1 ton of steam, it will be necessary to burn 96.3 m3 of natural gas (assuming there is no condensate recycling). With the price of natural gas for industrial consumers 5.155 rub for 1.000 m3, the price of 1 Gcal of steam for the technological purposes was 3.500 rub, at which the specific operating costs for steam used as an additive to air for flotation in the steam-air mixture mode are 9.59 rub/t of ore. With concentrate price of 7.300 rub/t, gross proceeds from the sales from processing 1 ton of ore, taking into account steam costs, are 2066.5 and 1944.0 rub, when ore flotation follows the known circuit and mode, i.e., 6.3 % less.
Conclusion
Under laboratory conditions by the example of apatite-nepheline ores, it has been shown that when switching from ore flotation according to the existing circuit to a scheme with recycling of 1/2 part of rough concentrate and using the mixture of air with hot steam as the gas phase, the Р2О5 recovery into saleable concentrate increases from 90.06 to 96.0 % with almost the same concentrate quality. Steam-air flotation process is performed at collector expenditure reduced by ~ 14 %, including the most expensive distilled (by ~32 %) and crude tall oil (by ~30 %). The experiments were made under conditions simulating the closed flotation cycle, the rational mode of which was revealed by mathematical planning of the experiment.
Combining feed ore with a part of rough concentrate gives a mixture with a high level dressability. Recovery of apatite from it begins with the use of the steam-air mixture flotation mode for a short time and ends with transition to air flotation based on technological and economic considerations.
The main effect of a sudden contact of steam-air mixture with pulp is heating of water in the boundary layers of bubbles, which can be one of the causes for decreasing losses of the recovered mineral with flotation tailings. A high selectivity of flotation with steam-air mixture is accounted for by a difference in the influence of the dynamic structure of liquid in the wetting film and bulk liquid on the value and sign of the phonon component of disjoining pressure.
References
- Andreev D.V. Role of the Mining Industry in the Economy of the Country. Moscow economic journal. 2020. N 12, p. 175-185 (in Russian). DOI: 10.24411/2413-046Х-2020-10870
- Tatarkin A.I., Kornilkov S.V., Yakovlev V.L., Orlova E.A. Forecast of technological development in ore mining branches on basis of modernization of technique and technology of mining practice. Economy of regions. 2012. N 4, p. 80-92 (in Russian). DOI: 10.17059/2012-4-7
- Gabdulkhakov R.R., Rudko V.A., Pyagay I.N. Methods for modifying needle coke raw materials by introducing additives of various origin (review). Fuel. 2022. Vol. 310. N 122265. DOI: 10.1016/j.fuel.2021.122265
- Evdokimov S.I., Evdokimov V.S. Increasing gold recovery by co-processing of ore and tails. Fiziko-tekhnicheskie problemy razrabotki poleznykh iskopaemykh. 2017. N 2. p. 160-169 (in Russian).
- Finch J.A., Tan Y.H. A comparison of two flotation circuits. Minerals Engineering. 2021. Vol. 170. N 107002. DOI: 10.1016/j.mineng.2021.107002
- Evdokimov S.I., Gerasimenko T.E. Regime Design for Gold Ore Flotation by Air and Steam Mixture. Journal of Mining Science. 2021. Vol. 57. N 2, p. 327-340. DOI: 10.1134/S1062739121020174
- Jia-Wen Song, Li-Wu Fan. Temperanure dependence of the contact angle of water: A review of research progress, theoretical understanding, and implications for boiling heat transfer. Advances in Colloid and Interface Science. 2021. Vol. 288. N 102339. DOI: 10.1016/j.cis.2020.102339
- Elbendary A., Aleksandrova T., Nikolaeva N. Influence of operating parameters on the flotation of the khibiny apatite-nepheline deposits. Journal of Materials Research and Technology. 2019. Vol. 8. Iss. 6, p. 5080-5090. DOI: 10.1016/j.jmrt.2019.08.027
- Aleksandrova T., Elbendary A., Nikolaeva N. Beneficiation of a low-grade phosphate ore using a reverse flotation technique. Mineral Processing and Extractive Metallurgy Review. 2022. Vol. 43. Iss. 1, p. 22-27. DOI: 10.1080/08827508.2020.1806834
- Belichko D.R., Konstantinova T.E., Volkova G.K. et al.Effects of YSZ ceramics doping with silica and alumina on its structure and properties. Materials Chemistry and Physics. 2022. Vol. 287. N 126237. DOI: 10.1016/j.matchemphys.2022.126237
- Lobacheva O.L. Ion flotation of ytterbium water-salt systems – An innovative aspect of the modern industry. Water. 2021. Vol. 13. Iss. 24. N 3493. DOI: 10.3390/w13243493
- Savchenkov S., Kosov Y., Bazhin V. et al. Microstructural master alloys features of aluminum-erbium system. Crystals. 2021. Vol. 11. Iss. 11. DOI: 10.3390/cryst11111353
- Lobacheva O.L., Dzhevaga N.V. The experimental study of innovative methods regarding the removal of Sm(III). Applied Sciences. 2021. Vol. 11. Iss. 16. N 7726. DOI: 10.3390/app11167726
- Aleksandrova T.N., Orlova A.V., Taranov V.A. Current status of copper-ore processing: A review. Russian Journal of Non-Ferrous Metals. 2021. Vol. 62. Iss. 4, p. 375-381. DOI: 10.3103/S1067821221040027
- Lukyantseva E.S., Sergeev V.V. Increasing the depth of apatite processing by extracting rare-earth elements. E3S Web of Conferences, 31 May – 6 June 2021, Saint Petersburg, Russia. E3S Web of Conferences, 2021. Vol. 266. N 02002. DOI: 10.1051/e3sconf/20212660200
- Kalmykova T.D., Kuznetsov V.V. Kinetic and thermodynamic aspects of flotation beneficiation of polymetallic raw materials. E3S Web of Conferences, 31 May – 6 June 2021, Saint Petersburg, Russia. E3S Web of Conferences, 2021. Vol. 266. N 02015, p. 109-116. DOI: 10.1051/e3sconf/202126602015
- Siziakova E., Ivanov P., Maximova R. Feasibility of applying alkaline-earth metal carboaluminates for bayer process aluminate solution purification from organic impurities. Materials Science Forum. 2021. Vol. 1031. DOI: 10.4028/www.scientific.net/MSF.1031.109
- Ushakov E.K., Alexandrova T.N. On the variability of technological indicators in the extraction of precious metals. E3S Web of Conferences, 31 May – 6 June 2021, Saint Petersburg, Russia. E3S Web of Conferences, 2021. Vol. 266. N 02003. DOI: 10.1051/e3sconf/202126602003
- O’Connor C., Alexandrova T. The geological occurrence, mineralogy, and processing by flotation of platinum group minerals (PGMs) in South Africa and Russia. Minerals. 2021. Vol. 11. Iss. 1, p. 1-15. DOI: 10.3390/min11010054
- 20. Aleksandrova Т.N., Kuskov V.B., Afanasova А.V., Kuznetsov V.V. Improvement of the fine coking coal flotation technology. Obogashchenie Rud. 2021. N 3, p. 9-13 (in Russian). DOI: 10.17580/or.2021.03.02
- Ponomareva M.A., Cheremisina O.V., Mashukova Y.A., Lukyantseva E.S. Increasing the efficiency of rare earth metal recovery from technological solutions during processing of apatite raw materials. Journal of Mining Institute. 2021. Vol. 252, p. 917-926. DOI: 10.31897/PMI.2021.6.13
- Litvinova T.E., Oleynik I.L.Dissolution kinetics of rare earth metal phosphates in carbonate solutions of alkali metals. Journal of Mining Institute. 2021. Vol. 251, p. 712-722. DOI: 10.31897/PMI.2021.5.10
- Aleksandrova T.N., Elbendari A.M. Increasing the efficiency of phosphate ore processing using flotation method. Journal of Mining Institute. 2021. Vol. 248, p. 260-271. DOI: 10.31897/PMI.2021.2.10
- Pelikh V.V., Salov V.M., Burdonov A.E., Lukyanov N.D. Model of baddeleyite recovery from dump products of an apatite-baddeleyite processing plant using a CVD6 concentrator. Journal of Mining Institute. 2021. Vol. 248, p. 281-289. DOI: 10.31897/PMI.2021.2.12
- Barskii L.A., Kozin V.Z. System analysis in mineral beneficiation. Moscow: Nedra, 1978, p. 486 (in Russian).
- Finch J.A., Yue Hua Tan. A comparison of two flotation circuits. Minerals Engineering. 2021. Vol. 170. N 107002. DOI: 10.1016/j.mineng.2021.107002
- Gershenkop A.Sh., Mukhina T.N., Artemev A.V. Use of “jet” flotation for processing poor in apatite ores of the Partomchorr deposit. IX Kongress obogatitelei stran SNG 26-28 fevralya 2013. Moscow: MISiS, 2013. Vol. 1, p. 156-160 (in Russian).
- Tyurin B.A., Zemskii E.V., Purvee Ya., Korablin V.I. Influence of fluorite content in crushed ore on technological parameters of its beneficiation under conditions of “Bor-Undur” Mining and Processing Plant (GOK). Gornyi zhurnal. 2008. N 2, p. 19-21 (in Russian).
- Evdokimov S.I., Gerasimenko T.E. Developing the technology of associated gold recovery when concentrating copper-pyrite ore. News of the Higher Institutions. Mining Journal. 2021. N 7, p. 35-44. DOI: 10.21440/0536-1028-2021-7-35-44
- Petrov S.V. Upon Dependence of Platinum-Group Metals Flotation Recovery on Metals Grade in Ore. Obogashchenie Rud. 2015. N 5, p. 14-19 (in Russian). DOI: 10.17580/or.2015.05.03
- Owusu C., Abreu S.B., Skinner W. et al. The influence of pyrite content on the flotation of chalcopyrite/pyrite mixtures. Minerals Engineering. 2014. Vol. 55, p. 87-95. DOI: 10.1016/j.mineng.2013.09.018
- Jiwei Xue, Dawei Ren, Tong Chen et al. Hydrophobic agglomeration flotation of oxidized digenite fine particles induced by Na2S and butyl xanthate. Minerals Engineering. 2021. Vol. 168. N 106932. DOI: 10.1016/j.mineng.2021.106932
- Bin Yang, Zhanglei Zhu, Haoran Sun et al. Improving flotation separation of apatite from dolomite using PAMS as a novel eco-friendly depressant. Minerals Engineering. 2020. Vol. 156. N 106492. DOI: 10.1016/j.mineng.2020.106492
- Luderitz L.A.C., Klitzing R.V. Interaction forces between silica surfaces in cationic surfactant solutions: An atomic force microscopy study. Journal of Colloid and Interface Science. 2013. Vol. 402, p. 19-26. DOI: 10.1016/j.jcis.2012.11.007
- Hu Y., Qin G., Miller J.D. Hydrodynamic interactions between particles in aggregation and flotation. International Journal of Mineral Processing. 2003. Vol. 70. Iss. 1-4, p. 157-170. DOI: 10.1016/S0301-7516(03)00023-1
- Bryk P., Bryk M. Effective interactions in polydisperse colloidal suspensions investigated using Ornstein-Zernike integral equations. Journal of Colloid and Interface Science. 2009. Vol. 338. Iss. 1, p. 92-98. DOI: 10.1016/j.jcis.2009.05.078
- 37. Evdokimov S.I., Gerasimenko T.E. Combined gravitation-flotation technology for technogenic gold placer concentration. Non-Ferrous Metallurgy. 2021. N 4, p. 4-15 (in Russian). DOI: 10.17073/0021-3438-2021-4-4-15
- Evdokimov S.I., Gerasimenko T.E. Recovery of gold washings from placer beneficiation products by magnetic fluid separation. Izvestiya vuzov. Tsvetnaya metallurgiya. 2017. N 5, p. 4-12 (in Russian). DOI: 10.17073/0021-3438-2017-5-4-12
- Boinovich L.B., Emelyanenko A.M. Forces due to dynamic structure in thin liquid films. Advances in Colloid and Interface Science. 2002. Vol. 96. Iss. 1-3, p. 37-58. DOI: 10.1016/S0001-8686(01)00074-4
- Boinovich L., Emelyanenko A. Wetting and surface forces. Advances in Colloid and Interface Science. 2011. Vol. 165. Iss. 2, p. 60-69. DOI: 10.1016/j.cis.2011.03.002
- Varghese S., Sathian S.P., Kannam S.K., Hansen J.S. Effect of hydrogen bonds on the dielectric properties of interfacial water. Langmuir. 2019. Vol. 35. Iss. 24, p. 8159-8166. DOI: 10.1021/acs.langmuir.9b00543
- Smith A.M., Borkovec M., Trefalt G. Forces between solid surfaces in aqueous electrolyte solutions. Advances in Colloid and Interface Science. 2020. Vol. 275. N 102078. DOI: 10.1016/j.cis.2019.102078
- Yang Yao, Verena Fella, Wei Huang et al. Crystallization and dynamics of water confined in model mesoporous silica particles: two ice nuclei and two fractions of water. Langmuir. 2019. Vol. 35. N 17, p. 5890-5901. DOI: 10.1021/acs.langmuir.9b00496
- Iwasaki Y., Seyama M., Inoue S. et al.Direct measurement of near-wall molecular transport rate in a microchannel and its dependence on diffusivity. Langmuir. 2021. Vol. 37. N 29, p. 8687-8695. DOI: 10.1021/acs.langmuir.1c00561