In-situ leaching of molybdenum and uranium by percarbonate and chloride-hypochlorite solutions
- 1 — Ph.D., Dr.Sci. Corresponding Member of the Russian Academy of Sciences Khabarovsk Federal Research Centre, Far Eastern Branch of the Russian Academy of Sciences ▪ Orcid ▪ Elibrary ▪ Scopus ▪ ResearcherID
- 2 — Ph.D., Dr.Sci. Deputy Director Mining Institute, Far Eastern Branch of the Russian Academy of Sciences ▪ Orcid ▪ Elibrary ▪ Scopus ▪ ResearcherID
- 3 — Ph.D. Leading Researcher Mining Institute, Far Eastern Branch of the Russian Academy of Sciences ▪ Orcid
Abstract
In-situ leaching of molybdenum and uranium is becoming an increasingly common process. The features of the material composition of ores, leading to a decrease in their filtration properties, were considered. Activation leaching with leaching solutions that have undergone electrophotochemical activation before contact with the ore mass were studied. Activation preparation of leaching solutions promotes the synthesis of clustered water molecules with collectivized protons and hydroxyl ions, as well as active forms of oxygen and hydrogen. Cell leaching of molybdenum from mature tailings of the Shakhtaminsk deposit was studied experimentally. After pre-oxidation with an active carbonate solution, a model borehole leaching was carried out with a chloride-hypochlorite solution. Molybdenum extraction on resin a was 85 % in 30 days. Experiments on the percolation leaching of uranium from the ores of the Uchkuduk and Sugraly deposits confirmed the potential possibility of a significant increase in the extraction of uranium by electrophotoactivated percarbonate solutions relative to aqueous solutions of sodium and ammonium carbonate. When leaching with carbonate solutions without an additional oxidizing agent, the extraction of uranium from the Sugraly deposit ore sample was 52 and 59 % (sodium carbonate and ammonium carbonate). The use of hydrogen peroxide as an oxidizing agent made it possible to achieve 87-88 % extraction into pregnant solutions in 21 days without pre-oxidation. The performed studies confirm the processing capability of extracting uranium and molybdenum by percolation leaching in columns and borehole leaching.
Introduction
During the underground mining of large ore deposits, including molybdenum and uranium, significant reserves of lean and substandard ores remain unextracted in stumps, offshoots, and thin ore bodies [1]. Significant amounts of these metals remain in the underproduced impoverished ore of worked-out blocks, which are difficult to return to [2].
Due to the chemical features of molybdenum and uranium, as well as the minerals containing them, in most cases it is possible to extract them from ores in situ or from accumulations of ore mass in the bottom of spent chambers by leaching [3-6]. The introduction of these methods is constrained by the complexity of assessing the final efficiency of extraction and recovery of uranium in-situ [7].
Features of uranium extraction applying using physicochemical geotechnologies
Uranium, in terms of its solubility in sulphuric acid and carbonate media, has much in common with molybdenum:
The main hydrogeochemical feature of uranium in comparison with molybdenum, as well as other main ore elements, is its radioactivity. It determines the flow of a number of radiochemical processes during the interaction of decay products with a liquid phase and defect formation in a solid (mineral) phase of the leaching solution, ore system. In particular, gamma quanta emitted during the collapse of nuclei of radon-226 atoms, which are the daughters of uranium-238 decay, produce hydrogen peroxide (radiolization effect) in the aquatic environment [8]. Hydrogen peroxide and other strong oxidizing agents intensify uranium leaching [9-11].
In addition, such radiolytic hydrogen peroxide, upon absorption of gamma quanta, disproportionates into two highly active hydroxyl radicals, and upon interaction with ferrous iron, it decomposes into a hydroxyl ion and a hydroxyl radical. The hydroxyl radical not only actively oxidizes minerals, but also forms, as a result of hydration, reactive water clusters that form hydrated shells for complexing agents, thereby increasing their dissolving power with respect to uranium. Due to such radiochemical features, uranium, which is in the ore in the form of a simple oxide in the composition of such minerals as uraninite (U,Th)O2 or pitchblende UO2, is relatively simply leached from the mineral substance, initially in the form of dioxouranium ion UO2+2. The latter then quickly binds with sulphate or carbonate anions to the corresponding complexes, including polyligand ones. If uranium is present in the ore as part of a widespread silicate mineral with a weakly bound hydroxyl group, coffinite U(SiO4)1-x·(OH)4x, its dissolution rate slows down.
The presence of uranophane, a complex calcium hydroxysilicate Ca(UO2)SiO3(OH)2·5H2О, in the ore inhibits uranium leaching to a considerable extent. Therefore, in order to dissolve such mi-nerals with the release of uranyl ion, it is necessary, in addition to radiolytic peroxide and hydroxyl radical, to form in leaching solutions hydrogen peroxides obtained by electrochemical treatment.
During the in-situ leaching of uranium from ores of hydrogen deposits, in addition to its speciation, the content of clay minerals is of great importance. It determines the filtration index value, as well as the content of calcium and magnesium carbonates [12]. The high carbonate module of hydrogenous uranium ore determines not only an increased consumption of sulphuric acid, but also chemical clogging of the pay bed during the transition of calcite and dolomite to gypsum.
The use of surfactants can improve the filtration characteristics of the reservoir [13, 14]. One of the solutions to this problem can be the use of chloride-containing compounds for uranium leaching [15]. Therefore, the recoverability of uranium into a pregnant solution when using borehole sulphuric acid leaching from hydrogenic ores, even with a local increase in the content of calcium and magnesium carbonates, can significantly decrease. In this regard, uranium in-situ leaching is carried out with sulphuric acid or carbonate solutions, depending on the carbonate module of ores, when mining individual “nuclear” areas in ore bodies of hydrogenous deposits or in individual reservoir sections of their limbs. Sulphuric acid solutions for in-situ leaching of uranium are used when the CO2 content in its ores is not more than 2.5 %. Ores with a high content of calcite and/or dolomite are leached by solutions with a carbonate base, including sodium carbonate and bicarbonate, ammonium carbonate and bicarbonate [16]. When CO2 content is more than 2.5 %, it is recommended to switch to carbonate leaching.
Modern technologies for processing molybdenum-containing raw materials and concentrates
Molybdenum from ores with a considerable proportion of powellite and (or) ferrimolybdite is leached with sulphuric acid solutions [17]. For primary ores, in which molybdenum is found only in the composition of molybdenite, alkaline solution of sodium hypochlorite can be used as a leaching solution [18-22].
During hydrometallurgical processing of molybdenum concentrates, soda leaching is used. It is distinguished by a higher degree of molybdenum extraction due to the possible decomposition of some molybdates [23, 24]. The new generation of solvents is fluid CO2 leaching [25]. For mineral raw materials, which contains many insoluble molybdates, soda and ammonia leaching technologies are ineffective. In this case, soda solution with added oxidizing agent can be used to increase molybdenum extraction [26]. So, during autoclave leaching, molybdenum extraction from concentrates of complex composition is more than 98 % [27].
To extract molybdenum from rich ores and concentrates, the most promising method is leaching with electrochemical treatment of the pulp prepared on its basis. Its liquid phase contains sodium chloride and sodium carbonate with concentrations of 10 g/l or more. When it circulates through the electrolytic cell, they are converted in the anode zone into a system of highly active sulphur and molybdenum oxidants. This fact ensures the formation of sulphuric acid, a decrease in pH and its transition from the molybdenite crystal lattice to the liquid phase of the pulp [28].
To extract molybdenum from lean and ordinary ores (when grinding is inapplicable for economic reasons), the electrochemical leaching can also be used, but subject to separate, preliminary preparation of active leaching sulphuric acid or carbonate solutions, i.e., before their interaction with the mineral mass.
Theoretical aspects of activation of leaching solutions
The simplest but rather effective way to increase the activity of leaching solutions used for leaching metals from sulphide minerals is the formation of hydrated forms of diatomic oxygen in them [29, 30]. Saturation of water with oxygen leads to the formation of metastable peroxide compounds, in which hydrogen periodically transforms into an ionized form:
The ionic complex (O·2-2·2H+)·, when interacting with the products of induced dissociation of water molecules surrounding it, becomes the centre of their clustering. The oxygen anion induces the dissociation of water molecules surrounding it and, interacting with the protons formed during their dissociation, forms supramolecular structures with compacted electron shells. In turn, protons in the composition of this complex, when penetrating into the electron shells of oxygen atoms of the nearest water molecules, form hydroxonium ions. Such activated water, with collectivized protons and hydroxyl ions localized in its clustered molecules, interacts more intensively with reagent mole-cules (ions) dissolved in it. The so-called reactive oxygen species, which in modern physical chemi-stry means ozone and the atomic allotropic form, as well as the radical ion and radical compounds of oxygen and hydrogen (peroxide, hydrogen dioxide, hydroxyl radical, etc.), significantly increase the efficiency of leaching of molybdenum and associated valuable components from ores resistant to standard reagent circuits.
Since ozone, atomic oxygen, and especially hydroxyl radical recombine rapidly, it is more efficient to produce their hydrated forms directly in the leaching solution. Therefore, the most acceptable method for generating reactive hydrated oxygen species in solution is electrolysis in combination with photolysis. In this case, the molecules of electrolytic gases (primarily oxygen and hydrogen) dispersed in the leaching solution and the water vapour contained in the gas bubbles transform into radicals and radical ions upon absorption of ultraviolet radiation quanta.
The redox potential of the ОН• hydroxyl radical reaches 2.8 V [31], for atomic oxygen it is 2.42 V, for ozone 2.07 V. Therefore, not only the unpaired electron of the oxygen atom, but also the active hydrogen atom or proton formed during the internal dissociation of the hydroxyl radical according to the ionic “mechanism”, not only changes the structural and energy parameters of the electron shells of the water molecules in contact with it but penetrates in them. If there are two active ОН• centres in a water cluster, such a complex will contain clustered 2Н+(2ОН−·nН2О) protons. Solutions, or rather gas-liquid emulsions obtained as a result of the electrochemical treatment of leaching solutions, due to the presence of active oxidizing and complexing components in them, begin to leach molybdenum in the upper layers of molybdenite mineral matrices with the formation of molybdic acid and the oxidation of sulphur anions, passing into elemental form. For the subsequent conversion of sulphur into the sulphate form, it is advisable to use superperoxide compounds of percarbonic acids and alkali metal superoxides. Cluster percarbonic acid compounds can be obtained by electrolysis of bicarbonate or sodium carbonate solutions and photochemical treatment of the anode zone in the reactor. During electrolysis and irradiation with ultraviolet light of a hydro-carbonate (soda) solution in the anode zone (in the gas phase of the resulting emulsion), the following active particles are formed:
During hydration, upon contact with film water surrounding gas bubbles and with water vapour inside them, such dimeric cluster compounds produce percarbonic acid:
Over time, percarbonic acid disproportionates to form monopercarbonic acid and carbon dioxide
Н2C2O6 = Н2CO4 + СO2
or hydrogen peroxide and carbon dioxide
Н2C2O6 = Н2O2 + 2CO2.
The resulting monopercarbonic acid Н2CO4 also disproportionates over time to form hydrogen peroxide and carbonic acid:
Н2СО4 + 2Н2О = Н2СО3 + Н2О + Н2О2.
An important property of percarbonate compounds is their synergetic (together with other complexing agents) effect on metals and oxidizing effect on sulphur and carbonaceous matter. The leaching of molybdenum with such solutions, or rather, water-gas emulsions, will be carried out according to the reactions:
MoS2 + H2C2O6 = H2MoO4 + S2 + 2CO.
Additional hydroxyl radicals in a mineral medium impregnated with active solutions are formed by disproportionation of hydrogen peroxide into a hydroxyl ion and a hydroxyl radical under the catalytic action of Fe2+ (Fenton reaction [32, 33]) and partially due to the absorption of background gamma radiation quanta, the intensity of which for felsic rocks and metasomatic rocks derived from them is quite significant.
Carbon inclusions in ores when reacting with metastable monopercarbonic acid are oxidized to carbon monoxide:
H2СО4 + С = H2СО3 + СО.
Further, carbon monoxide is fully oxidized to CO2 with hydrogen peroxide or a hydroxyl radical:
СО + H2О2 = СО2 + H2О.
Methodology for conducting experimental studies
We propose to perform the electrophotochemical leaching of molybdenum from the mineral mass with peroxide-carbonate solutions in two stages.
Electrochemical synthesis and activation of leaching solutions is carried out in a membrane electrolytic cell with separate cathode and anode spaces. Electrolysis parameters: voltage on the electrode block 15 V, operating current 8 A. Leaching solutions were activated by UV irradiation, wavelength 180-275 nm, DRT-230 lamp, duration 10 min.
At the first stage, to produce sulphate anions and ferrous iron, sulphide iron-containing minerals are oxidized with a catholyte, which is a soda-alkaline solution obtained in the cathode chamber of the electrolyser, containing sodium carbonate, bicarbonate, and hydroxide and hydrogen peroxide. Before introducing the catholyte, it is saturated with oxygen, the concentration of alkali is increased, and subjected to UV irradiation.
At the second stage, molybdenum is leached by the anolyte obtained by electrochemical synthesis in the anode chamber of the electrolyser. Anolyte is a water-gas emulsion irradiated with UV light, containing in the bubbles dispersed in the liquid phase carbon dioxide, diatomic oxygen, and water vapour. During absorption of UV radiation quanta, they pass, respectively, into atomic oxygen, ozone, dimeric carboxyl cations (C2O4)+, hydrated hydroxyl radical, and in the liquid phase percarbonic acids, hydrogen peroxide, hydroxyl radical. To increase the yield of reactive oxygen species, sulphuric acid is added to the anode chamber 30-60 min after the start of electrolysis until pH = 3-3.5 is reached, and the anode zone is irradiated with a UV radiation source.
When molybdenum is leached with separately prepared activated solutions, there is no need to circulate the pulp through the electrochemical cell. The proportion of active, molybdenum leaching components synthesized as a result of the combined use of electrochemical and photochemical processes increases.
Hydrometallurgical testing of uranium-containing ores was carried out with electrophotoactivated solutions of sodium carbonate and ammonium carbonate. The percolation leaching method was studied. Potassium permanganate and sodium nitrite were used as an oxidizing agent.
Analysis of feed samples, pregnant solutions, and leaching cakes was performed by atomic absorption spectroscopy with flame atomization (Shimadzu AA-6000).
Materials for this study are beneficiation tailings of the Shakhtaminskoye deposit with molybdenum content 0.01-0.03 %. In the upper layer of the tailing dam, the carrier minerals are represented by ferrimolybdite and povelite. In the lower layers, molybdenum is represented by molybdenite. In the Uchkuduk deposit, the main ore minerals are uraninite and pitchblende, coffinite is present; uranium content is 0.17 %. Ore of the Sugraly deposit contains 0.4 % uranium, uranium mineralization is represented by coffinite and uranophane. The weight of representative samples tested was 23 kg for each experiment.
Results and discussion
Extracting molybdenum from lean technogenic raw materials
Leaching according to the peroxide-carbonate circuit was studied experimentally on mixed samples of mature ore tailings from the Shakhtaminskoye deposit, taken from the surface layer with pronounced hypergenic alterations and visually slightly altered mineral mass. Molybdenum content in the beneficiation tailings of the Shakhtaminskoye deposit varies between 0.01-0.03 %. In the upper layer of the tailing dam, molybdenite is almost completely absent, having transformed into ferrimolybdite and, to a lesser extent, into povelite. Starting from a depth of 1.5-2 m of the tailing dam, molybdenum is mainly found in the composition of molybdenite overground during ore dressing. As the incoming analyses of samples taken from the pits showed, the associate components in the Shakhtaminskoye tailings can be gold, copper, and tungsten.
For the experiment on cell leaching of molybdenum, a representative sample weighing 23 kg was isolated (the cell volume was 20 l). The leaching solution (1.0 % NaHCO3) was activated by electrolysis and bubbling with air to saturate with oxygen in a diaphragm electrochemical reactor for 1 h. After that, sulphuric acid was added to the anode chamber until pH = 3 and reactive hydrated oxygen species formed in the anolyte to increase the yield. The anode zone was irradiated with UV light in the range of 180-275 nm using DRT-230 lamps for 10 min. The resulting active water-gas mixture was used to prepare a viscous suspension (thick pulp) with L:S = 1:3 based on the tailings, kept in a cell for three days, after which a catholyte additionally saturated with oxygen and passed through UV irradiation was added to the pulp. The catholyte was introduced into the pulp until pH = 8.5 and L:S = 1:1.2 were reached, it was bubbled for 2 h, after which a ion-exchange resin selective for molybdenum was introduced into the pulp, and bubbling was continued for another 13 h. After that, the saturated resin was separated on a sieve. Molybdenum recovery on resin was 75 %, which is a fairly high indicator for tailings processing.
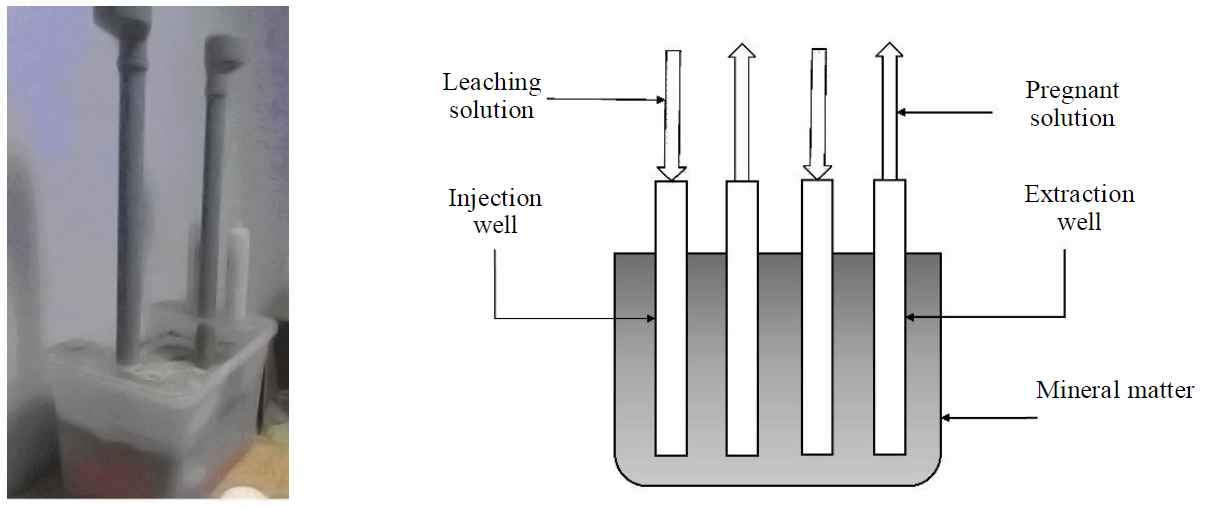
Stand for modelling borehole leaching
Molybdenum agitation leaching in a cell or in vats is effective for processing the mineral mass of the upper part of the tailing dam (to 4-5 m deep); for deeper layers it is advisable to use borehole leaching.
In order to simulate the in-situ molybdenum leaching, the beneficiation tailings of the Shakhtaminskoye deposit in the amount of 23 kg were placed in a plastic cell equipped with two plastic pipes perforated at the bottom (see Figure).
An anolyte obtained by electrochemical treatment of a 1 % soda solution was fed through one of the pipes, simulating the injection well. The solution was prepared by electrolysis and bubbling with air to saturate with oxygen in a diaphragm electrochemical reactor for 1 h, after which sulphuric acid was added to the anode chamber by titration until pH = 5 was reached, and the anolyte was activated by irradiating the anode zone with UV light in the range of 180-300 nm with DRT-230 lamps for 10 min. After 4 h, catholyte, additionally saturated with oxygen and also subjected to UV irradiation, was fed through the same tube. After exposure for three days, a chloride-hypochlorite solution obtained by electrophotochemical treatment according to a patented technology was fed through the tube simulating the injection well [34]. After the appearance of a pregnant solution in the second tube, simulating an extraction well, it was taken and analysed for dissolved elements: molybdenum, gold, and iron. The total consumption of leaching solutions for leaching was S:L = 1:1.7.
Molybdenum extraction in 30 days was 82 %. Extraction was calculated according to the formula
where Сfeed is the content of a valuable component in the feed ore, %; Сcake is the concentration of a valuable component in leaching cakes, %.
Moreover, gold was found in the pregnant solution in commercial (more than 0.3 mg/l) concentration. Thus, both cell and borehole leaching of molybdenum with percarbonate and chloride-hypochlorite solutions containing reactive oxygen species provides an acceptable level of its recovery.
Results of uranium extraction by percolation activation leaching
Numerous experiments on percolation leaching of uranium in columns carried out in the laboratories of the Navoi Mining and Metallurgical Company from the ores of the hydrogenous sedimentary deposits Uchkuduk and Sugraly confirmed the potential possibility of extracting uranium with both sodium carbonate and ammonium carbonate. The content of carbonates and clay minerals in these ore samples is approximately the same. Easily soluble uraninite and pitchblende prevail in the ores of the Uchkuduk deposit, with coffinite subordinately included in the ore paragenesis, with a total uranium content of 0.17 %. In a sample of a significantly richer ore from the Sugraly deposit with uranium content of 0.4 %, coffinite and uranophane are present in a significantly larger amount. Therefore, when leaching with carbonate solutions without an additional oxidizing agent, uranium extraction from the ore sample from the Sugraly deposit was 52 and 59 % (sodium carbonate and ammonium carbonate, respectively) at peak uranium contents in the pregnant solution of 1.5 g/l. Extraction of uranium from the ore sample of the Uchkuduk deposit was 76 and 81 % (sodium carbonate and ammonium carbonate). The use of potassium permanganate as an oxidizing agent at a flow rate of about 2 g/l ensured high levels of uranium recovery from both samples (95 and 96 %, respectively, calculated from the solid phase). Despite the result obtained, the use of such an expensive oxidizing agent as potassium permanganate is not economically justified at current uranium prices. The use of another effective oxidizing agent, sodium nitrite, in the presence of sulphide minerals, primarily pyrite, in the pay bed of the Sugraly deposit, can lead to the hydrogen sulphide release and gas colmatation of the pay bed.
Replacement of potassium permanganate with less expensive oxidizing agents, in particular pyrolusite or hydrogen peroxide, will not significantly reduce operational costs. The use of chemically pure oxygen supplied to the pay bed through the boreholes, as the “COGEMA” (France) tests on the Sugraly showed, significantly improves the kinetics of uranium leaching and reduces the sulphuric acid consumption but requires an uninterrupted delivery of oxygen equipment or installation of a large oxygen station with high power consumption. Therefore, it is objectively advisable to use an effective oxidizing agent produced directly in the operation site for in-situ uranium leaching but use non-capital-intensive and energy-intensive equipment. We examined and experimentally tested in the central physicochemical laboratory of the Northern Mine Administration of the Navoi Mining and Metallurgical Company a variant of electrophotochemical leaching of uranium from the Sugraly deposit ores by peroxide-carbonate solutions, which were prepared in flow electrochemical reactors. In this case, as for leaching of molybdenum, it is possible to use relatively cheap initial reagent, sodium bicarbonate, during the hydration of the molecules of which metastable monopercarbonic acid is formed in the leaching solution that acts both as an oxidizing and a complexing agent for uranium. Peroxide-carbonate solutions can be obtained onsite during mining operations by electrochemical treatment of initial solution.
Hydrogen peroxide acts as an oxidizing agent, and carbonic acid, when interacting with uranium oxide, acts as a complexing agent, forming a complex compound [UO2(CO3)3]. At the stage of electroactivation treatment of the initial hydrocarbonate solution, the content of dissolved oxygen increased from 5 to 9 mg/l after electrochemical treatment of formation water from the Sugraly deposit, which, during subsequent photochemical treatment of the solution, makes it possible to generate hydrogen peroxide in it. Thus, when using percarbonate and peroxide complexes, uranium is leached quite completely even from such a complexly soluble mineral as uranophane.
Experimental percolation leaching of uranium with peroxidal-carbonate solution obtained by electrophotochemical treatment of the feed hydrocarbonate solution of two parallel ore samples from the Sugraly deposit with a significant share of coffinite and uranophanes in it made it possible to achieve 87-88 % extraction into pregnant solutions in three weeks. Samples were not acidified preliminarily. Calculations according to the hard phase tests showed almost the same result (84.5 % for the first sample, 87.3 % for the second one). Total L:S was 1.7:1. The supply of percarbonate solutions was stopped when the uranium content fell in a pregnant solution to 50 mg/l. Thus, percarbonate solutions can potentially be used in the development of hydrogen uranium ores occurring in sedimentary rocks both in a borehole and other methods of physicochemical geotechnology.
Conclusions
Laboratory experiments and pilot tests of activation leaching of molybdenum and uranium from sedimentary and hydrothermal ores, mineral raw materials industrially transformed with percarbonate and percarbonate-chloride solutions prepared in electrophotochemical reactors were carried out.
75 % extraction on a resin in a cell form (electrophotoactivated carbonate leaching solution conditioned with sulphuric acid) and 82 % extraction of molybdenum when modelling in-situ leaching with a sequential combination of active carbonate and chloride-hypochlorite solutions were reached for the old tailings of the Shakhtaminsk deposit.
For ores of the Sugraly deposit, vat leaching tests showed 52-59 % of uranium recovery. The introduction of an oxidizing agent (KMnO4) made it possible to increase this indicator to 95 %. The modelling of in-situ leaching using an active carbonate solution and hydrogen peroxide as an oxidizing agent made it possible to reach 87-88 % extraction. On ores of the Uchkuduk deposit, the extraction of uranium according to the equal reagent combination at vat leaching was 76 %.
The proposed method for borehole mining of complex deposits of uranium and molybdenum ores with activation leaching will increase the level of development, improve the operational performance of the process, increase the profitability of production and environmental safety.
References
- Balikhin A.V. Uranium mineral-resources: the current state and perspectives for development. Review. Kompleksnoe ispolzovanie mineralnogo syra. N 1, p. 36-50 (in Russian). DOI: 10.31643/2019/6445.05
- Xie H., Zhao J.W., ZhouW. et al. Secondary utilizations and perspectives of mined underground space. Tunnelling and Underground Space Technology. 2020. Vol. 96. N 103129. DOI: 10.1016/j.tust.2019.103129
- Orrego P., Hernandez J., Reyes A. Uranium and molybdenum recovery from copper leaching solutions using, ion exchange. 2019. Vol. 184, p. 116-122. DOI: 10.1016/j.hydromet.2018.12.02
- Oryngozhin E.S., Fedorov E.V., Alisheva Z.N., Mitishova N.A. In-situ leaching technology for uranium deposits. Eurasian Mining. N2, p. 31-35. DOI: 10.17580/em.2021.02.07
- Yipeng Zhou, Guangrong Li, Lingling Xu et al. Uranium recovery from sandstone-type uranium deposit by acid in-situ leaching – an example from the Kujieertai. 2020. Vol. 191. N 105209. DOI: 10.1016/j.hydromet.2019.105209
- Tolstov D.E., Tolstov E.A. Physico-chemical geotechnologies for the development of uranium and gold deposits in the Kyzylkum region. Moscow: Geoinformtsentr, 2002, p. 277 (in Russian).
- Langanay J., Romary T., Freulon et al. Uncertainty quantification for uranium production in mining exploitation by In Situ Recovery. Computational Geosciences. 2021. Vol. 25. N 3, p. 831-850. DOI: 10.1007/s10596-020-10018-x
- Brown S.H. Radiological aspects of in situ uranium recovery. ICEM 2007: Proceedings of the 11th International Conference on Environmental Remediation and Radioactive Waste Management, 2-6 September 2007, Bruges, Belgium. ASME, 2009, p. 1465-1477.
- PanB., Liao W.S., Wai C.M. et al. Carbonate-H2O2 leaching for sequestering uranium from seawater. Dalton Transactions. 2014. Vol. 43. Iss. 28, p. 10713-10718. DOI: 10.1039/c3dt53404a
- Lasheen T.A., El-Ahmady M.E., Hassib H.B., Helal A.S. Oxidative leaching kinetics of molybdenum-uranium ore in H2SO4 using H2O2 as an oxidizing agent. Frontiers of Chemical Science and Engineering. Vol. 7. Iss. 1, p.95-102. DOI: 10.1007/s11705-013-1317-6
- Umanskii A.B., Klyushnikov A.M. Development of NaNO2-O2 system as an oxidant at uranium leaching processes. Journal of Radioanalytical and Nuclear Chemistry. 2012. Vol. 293, p. 193-198. DOI: 10.1007/s10967-012-1658-5
- Qi-Cheng Li, Ju Zhou. Research on character of solute transport in in-situ leaching of uranium in sandstone uranium deposit. International Conference on Design, Manufacturing and Mechatronics (ICDMM2015), 17-18 April 2015, Wuhan, China. World Scientific, 2016, p. 1086-1094.
- Rakishev B., Mataev M., Kenzhetaev et al. Research into leaching of uranium from core samples in tubes using surfactants. Mining of mineral deposits. 2020. Vol. 14. Iss. 4, p. 97-104. DOI: 10.33271/mining14.04.097
- Chunguang Li, Kaixuan Tan, Zhenzhong Liu et al. Prediction model of uranium concentration for in-situ leaching pregnant solution based on uranium chemical fractions of ores. Journal of radioanalytical and nuclear chemistry. Vol. 318. N 2, p.1379-1387. DOI: 10.1007/s10967-018-6190-9
- Titova, Skripchenko S., Smirnov A., Rychkov V. Processing of Chloride-Containing Productive Solutions after Uranium in-situ Leaching by Ion Exchange Method. Indonesian Journal of Chemistry. 2019. Vol. 19. N 1, p. 231-238. DOI: 10.22146/ijc.34460
- Wei Guang Wang, Kai Xuan Tan, Er Ju Xie et al. Supercritical CO2 fluid leaching of uranium from sandstone type ores. Advances in Chemical, Material and Metallurgical Engineering. Vol. 634-638, p. 3517-3521. DOI: 10.4028/www.scientific.net/AMR.634-638.3517
- Valiyev K.K., Bugubayeva A.U., Amandykova A.B., Bulaev A.G. Uranium and molybdenum leaching from the ore of “Vostok” deposit. Izvestija Tulskogo gosudarstvennogo universiteta. Nauki o Zemle. Vol. 4, p. 92-99 (in Russian).
- Fu J.G., Zhong H., Bu X.M., Wang F.L. Electro-oxidation process for molybdenum concentrates. Journal of Central South University of Technology. Vol. 12. N 2, p. 134-139 (in Chinese).
- Weiping Liu, Hui Xu, Xiyun Yang, Xichang Shi. Extraction of molybdenum from low-grade Ni-Mo ore in sodium hypochlorite solution under mechanical activation. Minerals Engineering. Vol. 24. Iss. 14, p. 1580-1585. DOI: 10.1016/j.mineng.2011.08.010
- Warren I.H., Mounsey D.M. Factors influencing the selective leaching of molybdenum with sodium-hypochlorite from copper molybdenum sulfide minerals. 1983. Vol. 10. Iss. 3, p. 343-357. DOI: 10.1016/0304-386X(83)90064-6
- Warren I.H., Mounsey D.M. Fundamentals of the selective leaching with sodium-hypochlorite of molybdenum from copper-molybdenum sulfide concentrations. Journal of Metals. Vol. 31. Iss. 12, p. 84-85.
- Hesami R., Ahmadi A., Hosseini M.R., Torabi M. Effect of mechanical activation on the hypochlorite leaching of Sarcheshmeh molybdenite concentrate. Separation Science and Technology. Vol. 57. Iss. 12, p.1966-1977. DOI: 10.1080/01496395.2021.2018712
- Medvedev A.S., Malochkina N.V., Balgaeva F.Sh. Methods for processing spent catalysts. Tsvetnye metally. 2007. N 6, 78-82 (in Russian).
- Shijie Zhao, Zhiqin Liao, Yu Xie, Xisong Li et al. Extraction of Molybdenum from Spent HDS Catalyst by Pressure Alkaline Leaching. Journal of Sustainable Metallurgy. Vol. 7. Iss. 3, p. 773-782. DOI: 10.1007/s40831-021-00420-9
- Yun Yang, Wenjie Qiu, Zhengbang Liu et al. Quantifying the impact of mineralogical heterogeneity on reactive transport modeling of CO2 + O2 in-situ leaching of uranium. Acta Geochimica. 2022. Vol. 41, p. 50-63. DOI: 1007/s11631-021-00502-1
- Sung-Ho Joo, Young-Uk Kim, Jin-Gu Kang et al. Recovery of Molybdenum and Rhenium Using Selective Precipitation Method from Molybdenite Roasting Dust in Alkali Leaching Solution. Materials Transactions. Vol. 53. N 11, p. 2038-2042. DOI: 10.2320/matertrans.M2012209
- Kaixi Jiang, Yufang Wang, Xiaoping Zou et al. Extraction of Molybdenum from Molybdenite Concentrates with Hydrometallurgical Processing. 2012. Vol. 64. Iss. 11, p. 1285-1289. DOI: 10.1007/s11837-012-0457-3
- Sekisov A.G., Lavrov A.Yu., Rasskazova A.V. Photochemical and electrochemical processes in geotechnology. Chita: Zabaykal'skiy gosudarstvennyy universitet. 2019, p. 306 (in Russian).
- Van Antverp, Ph. Lincoln. Patent N 752.412 USA. Method for recovery of precious metals using Ozone. Publ. 20.07.1987.
- Sekisov A., Rasskazova A. Assessment of the possibility of hydrometallurgical processing of low-grade ores in the oxidation zone of the malmyzh Cu-Au porphyry deposit. Minerals. 2021. Vol. 11. Iss.1. N 69. DOI: 10.3390/min11010069
- Liu Miao, Diao Wei-Li, Wu Di et al. Forming law of hydroxyl radical during electrolysis process. Chemical Journal of Chinese Universities. Vol. 26. Iss. 12, p. 2223-2226.
- Jia Zhishen, Wu Jianmin, Tang Mengcheng. Colorimetric determination of hydroxyl radicals from Fenton reaction. Progress in Biochemistry and Biophysics. Vol. 23. N 2, p. 184-186.
- Ren FL., Wu N., Si SH. Fluorimetry assay of hydroxyl radical by cobalt (II)-hydrogen peroxide-salicylfluorone system. Chinese Journal of Analytical Chemistry. Vol. 29. N 1, p. 60-62.
- Sekisov A.G., Khrunina N.P., Prokhorov K.V., Rasskazova A.V. Patent No. 2689487 RF. Method for extracting precious metals from ores and concentrates. 28.05.2019 (in Russian).